Right, so, cardboard food container innit? Sounds kinda boring, yeah? Nah, fam, it’s actually proper interesting. We’re talkin’ about the unsung hero of your takeaway, the eco-friendly saviour of your scran, and the canvas for some sick branding. These bad boys are everywhere, from your local chippy to fancy restaurants, keeping your nosh safe and sound.
Basically, it’s a box, a tray, a clamshell – you get the gist. Made from, like, recycled paper and stuff, they’re way better for the planet than those nasty plastic things. We’ll be diving deep into how they’re made, why they’re the bomb, and how they’re shaping the future of the food game. Get ready to have your mind blown (or at least mildly impressed).
Advantages of Using Cardboard Food Containers
Cardboard food containers offer a compelling alternative to traditional packaging, providing a range of benefits that extend beyond mere convenience. Their advantages span environmental sustainability, economic viability, and branding potential, making them an increasingly attractive option for food businesses of all sizes. The following sections will delve into these key advantages, highlighting their practical implications and long-term value.
Environmental Benefits
The environmental advantages of cardboard food containers are significant, primarily stemming from their renewability, biodegradability, and recyclability. This contrasts sharply with the environmental impact of many alternative packaging materials.Cardboard’s primary environmental benefit is its renewability. Unlike plastics derived from fossil fuels, cardboard is made from wood pulp, a renewable resource when sourced from sustainably managed forests. Forests absorb carbon dioxide from the atmosphere, making cardboard a carbon-neutral material when properly managed.
Enhance your insight with the methods and methods of square pet dog food.
This reduces the reliance on finite resources and mitigates the contribution to greenhouse gas emissions.Cardboard is also readily biodegradable. Under the right conditions, it breaks down naturally, returning organic matter to the soil. This contrasts with plastics, which can persist in the environment for hundreds of years, contributing to pollution of land and oceans. The biodegradability of cardboard minimizes landfill waste and reduces the environmental burden associated with waste disposal.Furthermore, cardboard is highly recyclable.
Recycled cardboard can be reprocessed into new cardboard products, creating a closed-loop system that reduces the demand for virgin materials and conserves resources. Recycling cardboard consumes less energy than producing it from raw materials, further minimizing its environmental footprint. The efficiency of cardboard recycling systems is constantly improving, making it an increasingly sustainable option.Consider this: According to the Environmental Protection Agency (EPA), in 2021, the recycling rate for paper and paperboard (which includes cardboard) was 68.2%, significantly higher than the recycling rates for plastics.
This demonstrates the established infrastructure and consumer awareness surrounding cardboard recycling.
Cost-Effectiveness
The cost-effectiveness of cardboard food containers is a crucial factor driving their adoption. Several aspects contribute to their economic appeal, making them a competitive choice for businesses.The initial cost of cardboard containers can be lower than that of alternatives like plastic or foam, particularly when purchasing in bulk. The manufacturing process for cardboard is often less complex and energy-intensive than for other materials, leading to lower production costs.Cardboard containers also offer potential cost savings in terms of transportation and storage.
They are typically lightweight, reducing shipping costs. Their flat-pack design allows for efficient storage, minimizing warehouse space requirements.Moreover, cardboard’s recyclability can lead to cost savings through waste management. Businesses can often reduce their waste disposal fees by recycling cardboard, offsetting the initial investment in containers.While the exact cost varies depending on factors like container size, design, and quantity, the overall cost-effectiveness of cardboard often makes it a financially sound choice, especially for businesses prioritizing both cost and sustainability.For example, a fast-food chain switching from plastic containers to cardboard containers might experience a slightly higher initial cost per unit.
However, the long-term benefits, including reduced waste disposal fees, enhanced brand image (due to the sustainability aspect), and potentially increased customer loyalty, can offset this initial cost difference and ultimately lead to greater profitability.
Printing and Branding Opportunities
Cardboard food containers provide excellent opportunities for printing and branding, enabling businesses to enhance their brand visibility and communicate with customers effectively. The surface of cardboard offers a versatile canvas for various printing techniques and design elements.The ease of printing on cardboard allows for high-quality graphics, logos, and text to be applied. This enables businesses to create visually appealing packaging that reflects their brand identity.Here are some examples of branding opportunities:
- Logo Placement: The prominent display of a company logo on the container enhances brand recognition. A well-designed logo can create a lasting impression on customers.
- Color Printing: Cardboard can be printed with a wide range of colors, allowing businesses to match their packaging with their brand’s color scheme. This creates a cohesive brand experience.
- Informative Content: Containers can include nutritional information, ingredient lists, and preparation instructions, enhancing the customer experience and promoting transparency.
- Promotional Messages: Businesses can print promotional messages, coupons, or QR codes to drive customer engagement and encourage repeat purchases. For example, a QR code can lead to online ordering or loyalty program signup.
- Unique Designs: Custom designs, including illustrations, patterns, and creative layouts, can differentiate a brand from competitors and create a memorable customer experience.
These branding opportunities not only help to attract customers but also reinforce brand loyalty. The ability to print high-quality graphics and informative content on cardboard containers makes them a powerful marketing tool.
Types of Cardboard Food Containers
The versatility of cardboard makes it a popular choice for food packaging, offering a wide array of container types designed to meet diverse needs. The selection of the right container is crucial for preserving food quality, ensuring ease of handling, and presenting the product attractively. Understanding the various types of cardboard food containers and their specific applications allows for informed decisions, leading to optimized packaging solutions.
Container Types and Food Item Suitability
Cardboard food containers come in a variety of forms, each engineered to address specific packaging requirements. The suitability of each type is dictated by factors such as the food’s moisture content, temperature, shape, and the desired level of protection during transport and storage. A careful match between the container and the food item is essential for maintaining freshness, preventing damage, and enhancing the overall consumer experience.
Here’s a breakdown of common cardboard food container types and their suitability for different food items:
- Boxes: These are perhaps the most versatile type, available in numerous sizes and shapes. They are suitable for a wide range of dry and non-liquid foods.
- Suitability: Ideal for cereals, crackers, cookies, pasta, pizza (in a flat, square or rectangular box), and frozen foods. The box provides excellent stacking capabilities.
- Example: Consider the ubiquitous pizza box. Its flat design allows for easy stacking and transportation. The corrugated cardboard offers insulation to keep the pizza warm for a reasonable period, and the vented design (often with small holes) allows steam to escape, preventing the crust from becoming soggy.
- Trays: Open-top containers, often used for presenting food items attractively.
- Suitability: Suitable for fruits, vegetables, baked goods, and pre-prepared meals that don’t require a lid for immediate consumption. They offer easy access to the contents.
- Example: Grocery store produce sections frequently use cardboard trays to display apples, oranges, and other fruits. The tray’s open design allows customers to easily see and select items.
- Clamshells: These containers are hinged, forming a closed unit.
- Suitability: Best suited for items like sandwiches, burgers, salads, and takeout meals. The clamshell provides good protection and is easy to handle.
- Example: Fast-food restaurants frequently use clamshell containers for burgers and sandwiches. The clamshell’s design keeps the food contained, prevents leakage, and allows for easy carrying.
- Folding Cartons: These are often used for products that need to be easily assembled and provide a clean, presentable appearance.
- Suitability: Ideal for dry foods, such as breakfast cereals, cake mixes, and ready-to-eat snacks. They offer a flat surface for printing and branding.
- Example: Breakfast cereal boxes are a classic example of folding cartons. The flat panels allow for vibrant graphics and informative product details.
- Cups/Tubs: These are typically cylindrical or conical containers.
- Suitability: Best for liquids and semi-liquids, such as ice cream, yogurt, and soups. Often lined with a moisture barrier.
- Example: Ice cream tubs are a common application. The cardboard provides insulation, and a wax or plastic lining prevents leakage.
Categorization by Food Application
Container types can be logically categorized based on their primary food applications. This categorization helps in quickly identifying the most appropriate packaging solution for a given food item. The following blockquote summarizes this categorization:
Dry Goods: Boxes, folding cartons (e.g., cereal boxes, pasta boxes, cracker boxes).
Fresh Produce: Trays, open-top boxes (e.g., fruit and vegetable containers).
Prepared Meals & Takeout: Clamshells, boxes, trays (e.g., burger boxes, pizza boxes, salad containers).
Liquid & Semi-Liquid Foods: Cups/Tubs (e.g., ice cream tubs, soup containers).
Baked Goods: Boxes, trays, clamshells (e.g., cake boxes, pastry trays).
Manufacturing Processes
The journey of a cardboard food container from raw material to a consumer-ready product is a sophisticated process, involving several crucial steps designed to ensure both functionality and safety. Understanding these manufacturing processes is key to appreciating the engineering behind these ubiquitous items. The careful selection of materials, precise manufacturing techniques, and rigorous quality control are all vital to creating a product that meets the demands of the food industry and the expectations of consumers.
Raw Material Acquisition and Pulping
The process begins with the sourcing of raw materials, typically wood pulp derived from sustainably managed forests. This is a critical first step, ensuring the long-term availability of the material and minimizing environmental impact.
- Wood Selection: Trees, often softwoods like pine or spruce, are harvested from managed forests. The choice of wood species impacts the final product’s strength and suitability for different applications.
- Debarking and Chipping: The logs are debarked to remove the outer layer and then chipped into small pieces. This process prepares the wood for pulping.
- Pulping: The wood chips are then converted into pulp through either mechanical or chemical pulping methods. Mechanical pulping uses grinding to separate the fibers, yielding a higher yield but a weaker pulp. Chemical pulping, using chemicals like sulfite or sulfate, dissolves the lignin that binds the wood fibers together, producing a stronger pulp. The specific method used depends on the desired characteristics of the final cardboard.
Paperboard Formation
The pulped wood fibers are then transformed into paperboard, the foundational material for cardboard food containers.
- Pulp Preparation: The pulp is mixed with water to create a slurry. This slurry may also include additives such as sizing agents for water resistance, dyes for color, and strengthening agents to enhance the paperboard’s structural integrity.
- Sheet Formation: The slurry is spread onto a moving wire mesh, allowing the water to drain and the fibers to interlock, forming a continuous sheet. This sheet then passes through a series of rollers that press and dry the paperboard.
- Multi-Ply Construction (for Corrugated Cardboard): For corrugated cardboard, multiple layers of paperboard are combined. A corrugated medium, created by passing paperboard through fluted rollers, is glued between two flat linerboards to create the characteristic structure. The flute profile (A, B, C, E, F) affects the cardboard’s strength and cushioning properties.
Coating and Treatment
To ensure food safety, moisture resistance, and grease resistance, the paperboard undergoes various coating and treatment processes. These processes are essential to prevent the cardboard from degrading when it comes into contact with food and liquids.
- Coating Application: Various coatings are applied to the paperboard. Common coatings include:
- Polyethylene (PE) Coating: A common plastic coating that provides a barrier against moisture and grease.
- Polypropylene (PP) Coating: Offers similar properties to PE and can withstand higher temperatures.
- Polylactic Acid (PLA) Coating: A biodegradable and compostable coating derived from renewable resources, gaining popularity for its environmental benefits.
- Wax Coating: Provides excellent moisture resistance, particularly for cold food applications.
- Treatment for Enhanced Properties: Beyond coatings, the paperboard may undergo other treatments:
- Barrier Coatings: Special coatings are used to prevent the migration of substances from the cardboard into the food and vice versa.
- Antimicrobial Treatments: Some containers receive antimicrobial treatments to inhibit the growth of bacteria and fungi.
Printing and Cutting
Once the paperboard is prepared, it can be printed with branding, product information, and other designs. This is followed by cutting the paperboard into the specific shapes required for the food containers.
- Printing: The paperboard is printed using various methods, including flexography and offset printing. The printing process allows for the application of logos, nutritional information, and other branding elements.
- Cutting and Creasing: The printed paperboard is then cut and creased using die-cutting machines. These machines use sharp blades to cut the paperboard into the desired shapes and create creases for folding.
Assembly and Quality Control, Cardboard food container
The final step involves assembling the containers and conducting rigorous quality control checks to ensure that the containers meet all the required standards.
- Container Assembly: The cut and creased paperboard is folded and assembled into the final container shape. This may involve gluing, stapling, or heat-sealing, depending on the container design.
- Quality Control: Quality control checks are performed throughout the manufacturing process, but especially at this stage. These checks include:
- Leak Testing: To ensure the containers are leak-proof.
- Strength Testing: To assess the containers’ ability to withstand pressure and handling.
- Visual Inspection: To check for defects in printing, cutting, and assembly.
- Food Safety Testing: To verify the absence of harmful substances.
Visual Representation of Manufacturing Steps
The image below illustrates the key steps in the manufacturing process of cardboard food containers, from raw material to finished product.
Illustration Description:
The image is a horizontal flow diagram depicting the cardboard food container manufacturing process. The diagram is divided into distinct sections, each representing a key stage in the process. The visual style is clean and informative, suitable for clear understanding.
Section 1: Raw Material Acquisition and Pulping
This section shows:
- A visual representation of a forest with several trees, symbolizing the source of wood pulp.
- A depiction of logs being transported to a factory.
- An illustration of a debarking machine removing the bark from the logs.
- An illustration of a chipping machine converting the debarked logs into wood chips.
- A depiction of a pulping process, showing wood chips being processed with chemicals or mechanically, resulting in pulp.
- Labels indicate each step.
Section 2: Paperboard Formation
This section illustrates:
- A tank with pulp being mixed with water and additives.
- A sheet-forming machine, showing the pulp slurry being spread onto a wire mesh, and the drainage of water, forming a sheet.
- A series of rollers pressing and drying the paperboard sheet.
- An image of a corrugated medium being created by fluted rollers.
- The corrugated medium being glued between two flat linerboards, forming corrugated cardboard.
- Labels indicate each step.
Section 3: Coating and Treatment
This section shows:
- The paperboard being coated with various materials.
- The use of a PE coating machine.
- The use of a PP coating machine.
- The use of a PLA coating machine.
- The application of a wax coating machine.
- Labels indicating each step and coating type.
Section 4: Printing and Cutting
This section illustrates:
- A printing press applying designs and branding to the paperboard.
- A die-cutting machine cutting the paperboard into container shapes.
- Labels indicating each step.
Section 5: Assembly and Quality Control
This section shows:
- The cut and printed paperboard being folded and assembled into a food container.
- A visual representation of the assembled container.
- Quality control processes, including leak testing, strength testing, and visual inspection.
- Labels indicating each step.
Food Safety and Regulations
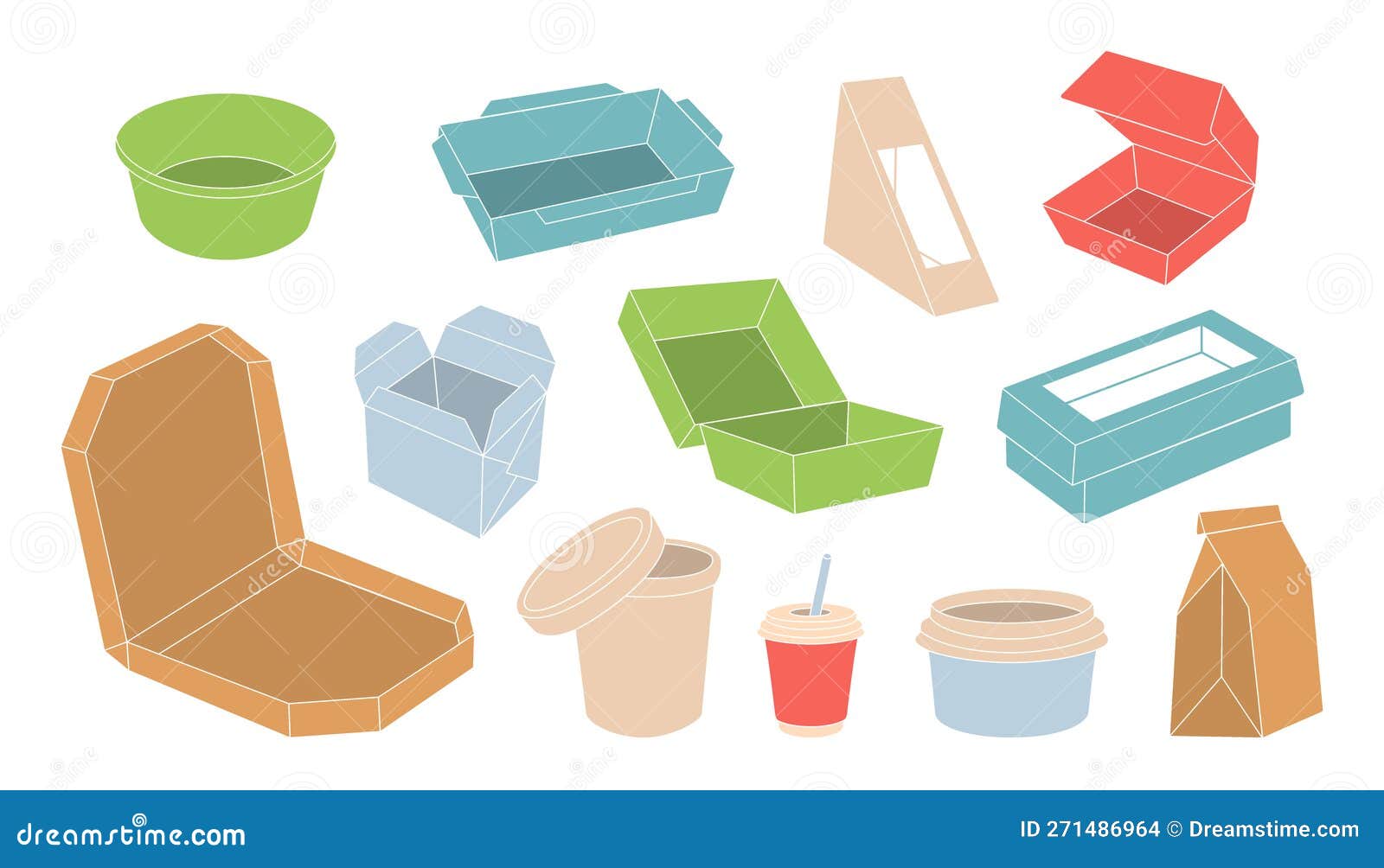
The use of cardboard food containers, while offering numerous advantages, necessitates rigorous adherence to food safety standards and regulations. These guidelines are crucial to protect consumers from potential health hazards arising from the packaging itself. This section delves into the critical aspects of food safety, focusing on the standards, potential risks, and mitigation strategies associated with cardboard food containers.
Food Safety Standards and Regulations
Food safety regulations for cardboard food containers vary by region and country, but several core principles are universally applied. These regulations aim to prevent the migration of harmful substances from the packaging into the food, ensuring the container itself does not contaminate the contents. Compliance typically involves adherence to specific material requirements, manufacturing processes, and testing protocols.Examples of key regulatory bodies and their roles include:
- The Food and Drug Administration (FDA) in the United States: The FDA sets standards for food contact materials, including cardboard. They regulate the substances that can be used in the manufacturing of these containers and require manufacturers to demonstrate the safety of their products. Specifically, the FDA’s regulations in 21 CFR Parts 170-189 detail the requirements for substances that can be used in food packaging.
- The European Food Safety Authority (EFSA): EFSA provides scientific advice on food safety matters, including the safety of food contact materials. They assess the risks associated with substances used in packaging and provide guidance to the European Commission, which then establishes regulations. The Framework Regulation (EC) No 1935/2004 is a key piece of legislation in the EU, setting out the general principles for food contact materials.
- The Canadian Food Inspection Agency (CFIA): The CFIA enforces food safety regulations in Canada, ensuring that food packaging materials meet the required standards. They focus on preventing the contamination of food by packaging materials.
- The International Organization for Standardization (ISO): ISO develops international standards, some of which are relevant to food safety and packaging. While ISO doesn’t have the power to enforce regulations, their standards provide guidelines that are often used by regulatory bodies and industry stakeholders.
These regulations often cover:
- Material Composition: Restrictions on the types of materials that can be used to manufacture the cardboard, including limitations on the use of recycled materials and specific chemicals.
- Migration Limits: Setting maximum permissible levels of substances that can migrate from the container into the food. These limits are determined based on the toxicity of the substances and the potential for consumer exposure.
- Good Manufacturing Practices (GMP): Requirements for the manufacturing process to ensure hygiene and prevent contamination during production. This includes controls on the handling of raw materials, cleaning and sanitation procedures, and employee training.
- Testing and Certification: Requiring manufacturers to conduct testing to demonstrate compliance with the regulations. This often involves simulating the conditions in which the container will be used and analyzing the food for the presence of any migrated substances. Certifications from recognized bodies are often required.
Importance of Food-Grade Cardboard and Inks
The selection of food-grade cardboard and inks is paramount to ensuring the safety of food packaged within. These materials are specifically designed to minimize the risk of contamination and prevent the transfer of harmful substances to the food. The term “food-grade” signifies that the materials have been tested and approved for direct contact with food, meeting stringent safety standards.Key considerations include:
- Cardboard Composition: The cardboard should be manufactured from virgin pulp or recycled materials that meet food safety standards. The use of recycled materials requires careful control to prevent the introduction of contaminants.
- Barrier Coatings: Cardboard often incorporates barrier coatings to protect the food from moisture, grease, and other potential contaminants. These coatings must be food-safe and not leach any harmful substances into the food. Examples include polyethylene (PE) and polylactic acid (PLA) coatings.
- Ink Selection: Inks used for printing on cardboard food containers must be food-safe and free of harmful chemicals such as heavy metals. The inks should also be resistant to migration, meaning they should not bleed into the food. Water-based and UV-curable inks are often preferred due to their lower environmental impact and reduced risk of contamination.
- Adhesives: Adhesives used in the manufacturing process must also be food-safe and not contain any substances that could migrate into the food.
Failure to use food-grade materials can lead to serious health risks. For instance, the presence of heavy metals in inks can cause chronic health problems if ingested over time. Similarly, the migration of volatile organic compounds (VOCs) from non-food-grade materials can affect the taste and odor of the food and potentially pose health hazards.
Potential Contamination Risks and Mitigation
Cardboard food containers are susceptible to several potential contamination risks. Understanding these risks and implementing effective mitigation strategies is crucial to ensuring food safety.Potential contamination risks include:
- Migration of Chemicals: Chemicals from the cardboard, inks, or coatings can migrate into the food. This is particularly likely if the container is exposed to heat, moisture, or acidic foods.
- Microbial Contamination: Cardboard can harbor microorganisms if not properly handled and stored. This is especially concerning if the container comes into contact with food that is not subsequently cooked.
- Cross-Contamination: If the cardboard container is used for both raw and cooked foods, cross-contamination can occur, transferring harmful bacteria from raw foods to cooked foods.
- Physical Contamination: Fragments of cardboard or ink can detach from the container and contaminate the food.
- Contamination from External Sources: Contamination can occur if the cardboard container is not stored or transported in a clean and hygienic environment. Exposure to pests, chemicals, or other contaminants can pose a risk.
Mitigation strategies include:
- Use of Food-Grade Materials: Always use cardboard, inks, and coatings that are specifically designed for food contact.
- Barrier Coatings: Apply barrier coatings to prevent the migration of substances and protect the food from moisture and grease.
- Proper Manufacturing Practices: Implement GMPs to ensure hygiene and prevent contamination during the manufacturing process.
- Controlled Storage and Handling: Store cardboard containers in a clean, dry environment, away from potential contaminants. Handle the containers with clean hands and tools.
- Temperature Control: Minimize exposure to extreme temperatures, which can increase the rate of migration.
- Printing Considerations: Select inks with low migration potential and ensure that the printing process is well-controlled to prevent ink from coming into direct contact with food.
- Regular Testing: Conduct regular testing to monitor the levels of any migrating substances and ensure compliance with regulations.
- Proper Packaging and Sealing: Design the container to effectively seal and protect the food from external contamination.
- Consumer Education: Provide consumers with instructions on how to properly use and dispose of the containers.
An example of a real-world application is the use of microwave-safe cardboard containers for ready-to-eat meals. These containers are often coated with a food-grade barrier to prevent the food from absorbing the cardboard and to withstand the high temperatures of the microwave. They are also tested to ensure that no harmful chemicals migrate into the food during heating. Another example is the use of cardboard packaging for fresh produce.
The packaging is designed to allow for air circulation to extend the shelf life of the produce while also protecting it from physical damage and contamination.
Sustainability and Recycling
The environmental impact of food packaging, including cardboard containers, is a significant concern in the modern era. The shift towards more sustainable practices is driven by consumer demand, regulatory pressures, and a growing awareness of the finite nature of resources. Recyclability, along with other factors like material sourcing and production methods, plays a crucial role in minimizing the ecological footprint of these containers.
Recyclability of Cardboard Food Containers
The recyclability of cardboard food containers is not always straightforward. While cardboard itself is a readily recyclable material, the presence of food residue, coatings (like wax or plastic), and inks can complicate the process. These contaminants can hinder the pulping process, which is the first step in recycling cardboard.
The key challenge lies in separating the cardboard fibers from these contaminants to ensure the resulting pulp is of sufficient quality for reuse.
Many cardboard food containers are considered recyclable, but it is essential to understand the specific requirements of local recycling programs. Some programs may accept containers with minor food residue, while others require thorough cleaning. Containers with significant contamination, like grease or heavy food soiling, may be rejected. The type of coating applied also affects recyclability. Containers with wax coatings are generally less recyclable than those with water-based or compostable coatings.
Methods for Improving the Sustainability of Cardboard Food Containers
Improving the sustainability of cardboard food containers involves a multi-faceted approach, from the sourcing of raw materials to the manufacturing processes and end-of-life management.
- Sustainable Sourcing: Utilizing responsibly sourced paperboard is paramount. This includes obtaining paper from forests certified by organizations like the Forest Stewardship Council (FSC), which ensures sustainable forestry practices. The use of recycled content in the paperboard also reduces the demand for virgin materials and lessens the environmental impact.
- Optimized Production: Manufacturing processes should be optimized to minimize waste and energy consumption. This can involve reducing the amount of material used in container production, implementing efficient cutting and shaping techniques, and utilizing renewable energy sources to power the manufacturing facilities.
- Reducing Coatings and Additives: Minimizing or eliminating the use of non-recyclable coatings and additives is crucial. Exploring alternative coatings like water-based or compostable options can enhance recyclability. Reducing the use of inks and dyes, or opting for environmentally friendly alternatives, also contributes to sustainability.
- Design for Recyclability: Container design plays a significant role. Simple designs with minimal components and coatings are easier to recycle. Clear labeling indicating recyclability and providing instructions for proper disposal can also improve recycling rates.
- Closed-Loop Systems: Implementing closed-loop recycling systems, where used containers are collected, processed, and then used to manufacture new containers, can create a circular economy. This reduces the reliance on virgin materials and minimizes waste.
Comparison of Recycling Programs and Their Effectiveness
The effectiveness of recycling programs varies depending on the infrastructure, regulations, and consumer participation. The following table compares different recycling program types and their effectiveness for cardboard food containers.
Recycling Program Type | Description | Effectiveness for Cardboard Food Containers | Examples |
---|---|---|---|
Curbside Recycling | Residents place recyclable materials at the curb for collection by the local waste management service. | Generally effective for clean, uncontaminated cardboard. Acceptance of food-soiled containers varies widely by municipality. | Most municipalities in North America, Europe, and Australia. |
Drop-Off Recycling Centers | Designated locations where residents can drop off recyclable materials. | Can accept a wider range of materials than curbside, but the cleanliness requirements still apply. Often used for large quantities of cardboard. | Community centers, recycling depots, and waste management facilities. |
Commercial Recycling Programs | Businesses and institutions contract with waste management companies for recycling services. | Highly effective, as these programs often have specialized equipment and protocols for handling large volumes of cardboard and managing contamination. | Restaurants, grocery stores, and food processing plants. |
Extended Producer Responsibility (EPR) Programs | Producers are held responsible for the end-of-life management of their products, including recycling. | Can be very effective in driving innovation and investment in recycling infrastructure and promoting design for recyclability. Often result in higher recycling rates. | Programs in place or being developed in various regions, with differing levels of scope and enforcement. Some European countries, and increasingly, in certain states in the United States. |
Applications in the Food Industry
Cardboard food containers have become ubiquitous across the food industry, offering a versatile and sustainable packaging solution. Their adaptability allows for diverse applications, ranging from individual meal servings to bulk food transport. The increasing demand for eco-friendly alternatives has further propelled their adoption, reshaping packaging practices across various sectors.
Sector-Specific Usage
The application of cardboard food containers varies significantly across different segments of the food industry. Each sector leverages the containers’ attributes, such as portability, insulation, and printability, to meet specific needs.
- Restaurants: Cardboard containers are extensively used in restaurants for takeout and delivery services. They offer a convenient and cost-effective way to package various dishes, from burgers and fries to pasta and salads. Many restaurants customize these containers with their branding, enhancing brand visibility and customer recognition.
- Catering: Catering companies utilize cardboard containers for transporting and serving food at events. These containers are often designed to maintain the temperature of the food and are available in various sizes to accommodate different serving needs. They are particularly useful for buffet-style presentations and individual meal portions.
- Retail: Retail food establishments, including supermarkets and grocery stores, employ cardboard containers for packaging prepared foods, bakery items, and fresh produce. The containers’ ability to be easily labeled and stacked makes them ideal for display and storage. The move towards sustainable packaging has led to an increase in the use of cardboard trays and boxes for fruits, vegetables, and pre-packaged meals.
- Food Delivery Services: The rise of food delivery platforms has significantly increased the demand for cardboard containers. These services rely heavily on the containers to ensure food arrives in good condition. Containers are often designed to be leak-proof and retain heat, ensuring a positive customer experience.
Innovative Container Applications
Beyond standard applications, cardboard containers are continuously being adapted for innovative purposes, meeting the evolving needs of the food industry. These adaptations often focus on enhancing functionality, sustainability, and consumer experience.
- Self-Heating Containers: Some manufacturers are developing cardboard containers integrated with self-heating technology. These containers use a chemical reaction to generate heat, allowing consumers to warm their meals without needing a microwave. This innovation is particularly useful for ready-to-eat meals and on-the-go consumption.
- Containers with Built-in Utensils: To enhance convenience, some cardboard containers incorporate built-in utensils, such as forks or spoons. These containers eliminate the need for separate cutlery, making them ideal for single-serve meals and takeout orders.
- Modular Packaging: Modular cardboard packaging allows for the creation of customized container configurations. This flexibility is particularly useful for meal kits and subscription services, where the container must accommodate a variety of ingredients and components.
- Containers with Augmented Reality (AR) Features: Some cardboard containers now incorporate AR features, which can be accessed through a smartphone. Consumers can scan the container to access recipes, nutritional information, or interactive content, enhancing the overall consumer experience.
Packaging Illustration: Pizza
A detailed description of packaging for a pizza in a cardboard container suitable for creating an image:The image depicts a square cardboard pizza box. The box is predominantly brown, with a natural cardboard texture visible throughout. The top panel features a vibrant, high-resolution print of a whole pizza. The pizza has a golden-brown crust, generously topped with melted mozzarella cheese, pepperoni slices, green bell peppers, and red onion.
The pizza appears fresh and appetizing, with steam subtly rising from the cheese, indicating it is hot.The box is closed and sealed with a rectangular adhesive label. The label features the restaurant’s logo, a stylized image of a chef’s hat with a pizza slice. Below the logo, the restaurant’s name is printed in a bold, modern font, along with the phrase “Freshly Baked.” On the side of the box, there are ventilation holes to allow steam to escape, preventing the pizza from becoming soggy.
The box has reinforced corners for added durability during transportation. The overall design is clean, professional, and conveys a sense of quality and freshness. The color palette is warm and inviting, designed to appeal to the consumer’s appetite. The box’s construction appears sturdy, suggesting it can withstand the rigors of delivery or takeout. The design prioritizes both visual appeal and functionality, ensuring the pizza arrives in optimal condition.
Design and Customization
The design and customization of cardboard food containers are crucial aspects that influence both their practicality and market appeal. A well-designed container not only protects the food but also enhances the brand’s image and provides consumers with a positive experience. This section delves into the key considerations for design, the various customization options available, and the practical steps involved in creating a custom container.
Design Considerations
Effective design in cardboard food containers balances functionality with aesthetics. This involves careful consideration of the container’s purpose, the food it will hold, and the overall user experience.* Functionality: The primary function is to protect the food. Design elements should ensure structural integrity to prevent leaks, spills, and damage during transportation and handling. Considerations include:
Structural Integrity
The container must withstand the weight of the food and any stacking pressures. This often involves choosing the correct board grade and incorporating features like reinforced corners or double-walled construction. For example, a pizza box needs to support significant weight and maintain its shape, while a delicate pastry container demands a different structural approach.
Ease of Use
The container should be easy for consumers to open, close, and handle. Features such as secure closures, easy-tear perforations, and ergonomic designs contribute to user-friendliness. Consider the example of a takeout container with a simple, secure latch versus one that requires multiple steps to open.
Food Preservation
Design should consider the food’s characteristics. For example, containers for hot foods must be able to withstand heat and prevent condensation buildup, while those for cold items should maintain temperature. Some containers may incorporate vents to release steam and prevent sogginess.
Portion Control
The container design can influence portion sizes. Pre-portioned containers help control calorie intake and reduce food waste. For instance, a container for a single serving of ice cream is a clear example of portion control.
Aesthetics
The visual appeal of a cardboard food container significantly impacts brand recognition and consumer perception. This involves considering:
Shape and Size
The shape and size should complement the food item and enhance its presentation. Different shapes cater to different food types, from rectangular boxes for sandwiches to cylindrical containers for beverages. The size must be appropriate for the portion.
Branding
The container serves as a branding opportunity. The design should incorporate the brand’s logo, colors, and messaging to create a consistent and recognizable brand identity. For instance, the iconic red and white stripes of a fast-food chain’s packaging are immediately recognizable.
Visual Appeal
The design should be visually appealing and reflect the quality of the food. This includes the use of attractive graphics, colors, and finishes. A well-designed container enhances the perceived value of the product.
Customization Options
A wide array of customization options allows businesses to create unique and branded cardboard food containers that meet their specific needs.* Printing: Printing is a primary customization method. It allows for the application of logos, graphics, text, and other branding elements.
Printing Techniques
Various printing techniques can be used, including:
Offset Printing
This is a high-quality printing method suitable for large quantities. It produces sharp images and precise color reproduction, ideal for detailed designs and photographs.
Flexographic Printing
This method is cost-effective for large volumes and is well-suited for printing on corrugated cardboard. It can handle uneven surfaces and is often used for simple designs and text.
Digital Printing
This is ideal for short runs and allows for variable data printing, such as personalized messages or unique codes. It offers flexibility and quick turnaround times.
Color Options
Containers can be printed with a wide range of colors, including spot colors (specific premixed inks) and process colors (CMYK). The choice of colors can significantly impact the container’s visual appeal and brand recognition.
Die-Cutting
Die-cutting involves using custom-shaped blades to cut the cardboard into specific shapes and sizes. This allows for unique container designs that go beyond standard shapes.
Shape and Form
Die-cutting enables the creation of containers with complex shapes, such as containers with custom closures, handles, or windows. This can enhance both the functionality and aesthetic appeal of the container.
Examples
Die-cut features can include custom flaps for easy opening, integrated handles for convenient carrying, or windows to showcase the food inside.
Embossing and Debossing
These techniques create raised (embossing) or recessed (debossing) designs on the cardboard surface. This adds a tactile element and a premium feel to the container.
Texture and Depth
Embossing and debossing can be used to create logos, patterns, or other visual elements that add depth and texture to the container.
Effect on Branding
These techniques enhance the brand’s perceived value and can create a memorable impression on consumers.
Procedure for Designing a Custom Cardboard Food Container
Designing a custom cardboard food container is a process that involves several steps, from conceptualization to final production.* Define Requirements: Clearly define the purpose of the container, the type of food it will hold, the desired portion size, and any specific functional requirements (e.g., insulation, venting). Determine the target audience and branding objectives.
Conceptualize the Design
Sketch out initial design ideas, considering shape, size, and functionality. Explore different closure mechanisms, handle options, and structural features. Develop multiple design concepts to evaluate.
Create a Prototype
Develop a physical prototype using materials that simulate the final container. This allows for testing the design’s functionality, usability, and structural integrity. Make adjustments based on feedback. Consider the use of a Computer-Aided Design (CAD) software for precise designs and simulations.
Choose Customization Options
Select printing techniques, colors, die-cutting features, and embossing/debossing options to enhance the design and branding. Consider the cost implications of each option.
Finalize the Design and Specifications
Refine the design based on prototype testing and customization choices. Create detailed specifications, including dimensions, materials, printing instructions, and any special requirements. Prepare artwork files for printing.
Obtain Quotes and Select a Manufacturer
Send the final design specifications to several manufacturers and obtain quotes. Evaluate the manufacturers based on their experience, capabilities, and quality control processes.
Approve a Sample and Proceed with Production
Review a final sample from the chosen manufacturer to ensure it meets all specifications. Approve the sample before proceeding with mass production. This step is critical to avoid costly errors.
Trends and Innovations
The cardboard food container market is dynamic, constantly evolving to meet consumer demands for convenience, sustainability, and aesthetic appeal. Driven by technological advancements and a growing awareness of environmental impact, the industry is witnessing significant shifts in design, materials, and manufacturing. This section explores the current trends, emerging innovations, and future projections shaping the cardboard food container landscape.
Current Trends in Cardboard Food Container Design and Usage
Several key trends are currently defining the cardboard food container market. These trends reflect a move towards greater functionality, improved user experience, and enhanced environmental responsibility.
- Enhanced Convenience and Functionality: Consumers increasingly seek food containers that are easy to use, transport, and store. This has led to designs featuring features like:
- Leak-proof construction: Utilizing coatings and innovative folding techniques to prevent spills and maintain food integrity, especially for liquid-rich dishes like soups and sauces.
- Easy-open and re-closable mechanisms: Facilitating convenient access and preserving food freshness. Consider the rise of peel-and-seal lids or snap-on closures.
- Stackable and space-saving designs: Optimizing storage efficiency for both consumers and food service providers.
- Sustainable and Eco-Friendly Materials: A significant driver of innovation is the demand for sustainable alternatives to traditional plastics. This encompasses:
- Increased use of recycled content: Aiming to reduce reliance on virgin materials and minimize waste.
- Biodegradable and compostable coatings: Replacing conventional plastic coatings with plant-based alternatives, like those derived from cornstarch or seaweed.
- Emphasis on sourcing sustainable paperboard: Utilizing paperboard certified by organizations like the Forest Stewardship Council (FSC) to ensure responsible forestry practices.
- Customization and Branding: Businesses are leveraging cardboard containers as a branding tool. This involves:
- High-quality printing: Employing advanced printing techniques to create visually appealing designs and convey brand messaging.
- Custom shapes and sizes: Tailoring containers to specific food products and brand identities. Think of the unique shapes adopted by fast-food chains for their signature items.
- Integration of QR codes and interactive elements: Providing customers with access to product information, recipes, or promotional offers.
- E-commerce and Delivery Optimization: The growth of online food ordering and delivery services is influencing container design:
- Insulated containers: Maintaining food temperature during transit, using materials like corrugated cardboard with integrated insulation layers or inserts.
- Tamper-evident features: Assuring food safety and security during delivery.
- Optimized packaging for transport: Designing containers that are robust and protect food from damage during handling and shipping.
Emerging Innovations in Materials and Manufacturing Techniques
Technological advancements are fueling innovation in both materials and manufacturing processes, leading to more efficient, sustainable, and functional cardboard food containers.
- Novel Materials: The search for improved materials is ongoing.
- Bio-based coatings: The development of new coatings derived from renewable resources, such as algae, chitosan, and cellulose, is gaining momentum. These coatings offer improved barrier properties and compostability compared to traditional options.
- Advanced paperboard composites: Combining paperboard with other materials, like bio-plastics or innovative films, to enhance performance characteristics like grease resistance, moisture barrier, and heat resistance. For example, the use of thin layers of PLA (polylactic acid) can create a compostable barrier against moisture.
- Nanomaterials: The application of nanomaterials, such as nano-cellulose or nano-clay, to improve the strength, barrier properties, and printability of paperboard.
- Manufacturing Techniques: Innovations in manufacturing are also enhancing container performance and sustainability.
- 3D printing: Enables rapid prototyping and the creation of customized container designs. While not yet widespread for mass production, it allows for faster development cycles and the creation of highly specialized packaging.
- Digital printing: Offers flexibility in design, enabling on-demand printing, variable data printing, and the ability to create personalized packaging. This minimizes waste and allows for smaller production runs.
- Automated assembly: Streamlining the manufacturing process through the use of automated machinery, improving efficiency and reducing labor costs.
- Laser cutting and scoring: Enhancing the precision and complexity of container designs, allowing for intricate folding patterns and customized features.
- Smart Packaging Technologies: Integrating technology into cardboard containers.
- Sensors: Integrating sensors to monitor food temperature, freshness, and potential contamination, providing valuable information to consumers and the food supply chain.
- Near Field Communication (NFC) and RFID tags: Enabling tracking and tracing of containers throughout the supply chain, improving inventory management and ensuring food safety.
Future Developments in the Cardboard Food Container Market
The future of cardboard food containers is likely to be shaped by several key factors, including continued pressure for sustainability, technological advancements, and evolving consumer preferences.
- Increased Adoption of Circular Economy Principles: The industry will increasingly embrace circular economy principles, focusing on reducing waste, reusing materials, and designing containers for recyclability and compostability.
- Design for recyclability: Container designs will be optimized to minimize the use of non-recyclable components and facilitate easy disassembly for recycling.
- Closed-loop recycling systems: Developing systems where cardboard containers are collected, processed, and used to create new containers, creating a closed-loop system.
- Emphasis on compostability: Designing containers that are readily compostable in both industrial and home composting environments.
- Growth of Personalized and Smart Packaging: The integration of technology will become more prevalent.
- Personalized packaging: Containers tailored to individual consumer preferences and dietary needs, enabled by digital printing and data analytics.
- Smart labels and interactive features: Integrating QR codes, NFC tags, and other technologies to provide consumers with information about the food, its origin, and its environmental impact.
- Advancements in Barrier Technologies: Improving the functionality of containers.
- Development of high-performance barrier coatings: Creating coatings that provide superior protection against moisture, grease, and oxygen, while remaining compostable or recyclable.
- Use of active packaging: Integrating materials that extend the shelf life of food by absorbing oxygen, releasing preservatives, or controlling moisture levels.
- Expansion into New Food Categories: Cardboard containers will be increasingly used for a wider range of food products.
- Ready-to-eat meals: Expanding the use of cardboard containers for ready-to-eat meals, including those designed for microwave heating.
- Fresh produce: Developing containers that extend the shelf life of fresh produce, incorporating features like ventilation and moisture control.
- Specialty foods: Customizing containers for specialty foods like gourmet cheeses, artisanal chocolates, and premium baked goods, focusing on presentation and brand appeal.
- Supply Chain Optimization and Automation: The industry will witness increased automation and optimization across the supply chain.
- Robotics and automation in manufacturing: Increasing the speed and efficiency of production processes.
- Data-driven supply chain management: Using data analytics to optimize inventory levels, reduce waste, and improve delivery times.
Sourcing and Purchasing
The procurement of cardboard food containers is a multifaceted process, requiring careful consideration of numerous factors to ensure both cost-effectiveness and suitability for the intended application. Making informed decisions in this area is crucial for businesses of all sizes, from small cafes to large-scale food manufacturers. This section provides a detailed guide to navigate the complexities of sourcing and purchasing cardboard food containers.
Factors to Consider When Sourcing Cardboard Food Containers
Several critical factors must be weighed when selecting cardboard food containers to meet specific needs and objectives. These considerations span a range of aspects, from material composition and performance characteristics to environmental impact and regulatory compliance.
- Material Composition and Performance: The type of cardboard, its thickness (measured in GSM or grams per square meter), and any coatings or treatments applied significantly impact the container’s performance. Consider moisture resistance (essential for preventing leaks), grease resistance (critical for fried foods), and temperature tolerance (necessary for both hot and cold applications). For instance, containers for soups or sauces require robust moisture barriers like polyethylene (PE) or polylactic acid (PLA) coatings.
Evaluate the container’s structural integrity to withstand stacking and handling during transport and storage.
- Food Safety Compliance: Ensure the containers meet all relevant food safety regulations, such as those set by the FDA in the United States or the EFSA in Europe. This includes verifying that the materials used are food-grade and free from harmful chemicals that could leach into the food. Request certificates of compliance from the supplier and review their food safety management systems (e.g., HACCP).
- Container Design and Functionality: The design of the container must align with its intended use. Consider the ease of assembly, closure mechanisms (e.g., tuck-in flaps, snap closures), and any features that enhance the consumer experience, such as carrying handles or vents to prevent condensation. Evaluate the container’s suitability for portion control and ease of serving.
- Environmental Impact and Sustainability: Prioritize containers made from recycled materials, those that are compostable, or those sourced from sustainably managed forests (certified by organizations like the Forest Stewardship Council – FSC). Assess the container’s recyclability and the availability of recycling infrastructure in the target market. Choose suppliers committed to reducing their environmental footprint through efficient manufacturing processes and waste reduction strategies.
- Cost and Volume: Compare pricing from different suppliers, considering the cost per unit, minimum order quantities (MOQs), and shipping costs. Factor in the total cost of ownership, including storage, handling, and potential waste disposal costs. Negotiate prices based on volume, and explore opportunities for bulk purchasing to achieve economies of scale.
- Supplier Reliability and Reputation: Research the supplier’s reputation, experience, and financial stability. Check for certifications and awards that demonstrate their commitment to quality and sustainability. Request references from other customers and assess their responsiveness, communication, and ability to meet deadlines.
- Customization Options: Determine the need for custom printing, branding, or unique container shapes and sizes. Inquire about the supplier’s capabilities in these areas and the associated costs and lead times. Consider the potential impact of customization on minimum order quantities and overall cost.
Guide to Evaluating Suppliers and Comparing Product Offerings
A systematic approach to evaluating suppliers and comparing their offerings is essential for making informed purchasing decisions. This process involves a multi-faceted evaluation of each supplier’s capabilities and product characteristics.
- Request Samples and Conduct Testing: Obtain samples from multiple suppliers and subject them to rigorous testing to assess their performance. Test for leakage, grease resistance, and temperature tolerance under simulated use conditions. Evaluate the ease of assembly and closure mechanisms. Conduct sensory evaluations to ensure the containers do not impart any unwanted odors or flavors to the food.
- Assess Supplier Certifications and Compliance: Verify that suppliers hold relevant certifications, such as ISO 9001 (quality management), ISO 14001 (environmental management), and FSC certification (sustainable forestry). Review their food safety certifications and compliance documentation to ensure adherence to regulatory requirements.
- Compare Pricing and Terms: Obtain detailed price quotes from each supplier, including unit costs, shipping costs, and any additional charges. Compare the payment terms, lead times, and warranty policies offered by each supplier. Negotiate pricing based on volume and payment terms.
- Evaluate Supplier Capabilities and Capacity: Assess the supplier’s manufacturing capacity, their ability to meet your volume requirements, and their responsiveness to your inquiries. Inquire about their quality control processes and their ability to handle any potential issues or complaints. Consider their geographical location and the potential impact on shipping costs and lead times.
- Review Customer Reviews and References: Research the supplier’s reputation by reviewing online reviews, testimonials, and case studies. Contact references provided by the supplier to gather insights into their performance and customer service.
- Conduct a Site Visit (If Possible): For larger orders or critical supply relationships, consider visiting the supplier’s manufacturing facility to assess their operations, quality control processes, and commitment to sustainability. This provides a firsthand perspective on their capabilities and allows you to build a stronger relationship.
Checklist for Purchasing Cardboard Food Containers
This checklist provides a structured approach to the purchasing process, ensuring all critical aspects are addressed.
- Define Requirements:
- Determine the specific food items the containers will hold.
- Specify the required container size, shape, and capacity.
- Establish performance requirements (e.g., moisture resistance, grease resistance, temperature tolerance).
- Identify any branding or customization needs (e.g., printing, labeling).
- Research and Identify Potential Suppliers:
- Search online directories, industry publications, and trade shows to identify potential suppliers.
- Obtain referrals from other businesses or industry contacts.
- Create a shortlist of suppliers based on initial criteria.
- Request Quotes and Samples:
- Send requests for quotes (RFQs) to shortlisted suppliers, including detailed specifications.
- Request samples of containers that meet your requirements.
- Evaluate the samples based on performance, design, and functionality.
- Evaluate Suppliers:
- Assess supplier certifications and compliance with food safety regulations.
- Compare pricing, payment terms, and lead times.
- Evaluate supplier capabilities and capacity.
- Review customer reviews and references.
- Negotiate and Place Order:
- Negotiate pricing and terms with the selected supplier.
- Review and finalize the purchase agreement.
- Place the order, specifying quantities, delivery dates, and shipping instructions.
- Monitor and Evaluate Performance:
- Track order fulfillment and delivery.
- Inspect the containers upon arrival to ensure quality and compliance.
- Provide feedback to the supplier on performance and address any issues.
- Continuously evaluate the supplier’s performance and explore opportunities for improvement.
Wrap-Up
So, there you have it: cardboard food containers, from humble beginnings to eco-friendly champions. They’re not just a box, they’re a statement. They’re a way to eat your food without feeling like a total waster. From the manufacturing process to the latest trends, these containers are constantly evolving. So next time you’re scoffing down a burger, give a nod to the cardboard that’s holding it together – it’s doing its bit for the planet, innit?