Alright, dengar sini! So, you’re thinking about getting a pallet of dog food? Sounds like you’re serious about keeping your furry friends fed! Whether you’re a dog owner with a pack, run a shelter, or just wanna be the neighborhood dog food king, this guide is gonna break down everything you need to know. We’ll cover the whole shebang, from what’s actually on a pallet to how to score the best deals and keep that kibble fresh.
We’re talking sizes, weights, and all the different types of dog food you might find. Then we’ll dig into where to buy, how to save some serious cash, and how to store all that food so it doesn’t go bad before your pups can chow down. Plus, we’ll even touch on shipping, handling, and what to do with all that dog food once it arrives.
Let’s go!
Defining “Pallet of Dog Food”
A “pallet of dog food” refers to a standardized unit of measure used in the warehousing and transportation of dog food products. It represents a collection of individual dog food packages, stacked and secured onto a pallet, facilitating efficient handling, storage, and distribution within the supply chain. Understanding the characteristics of a pallet of dog food is crucial for logistics planning, inventory management, and cost optimization.
Typical Dimensions and Weight of a Standard Pallet Loaded with Dog Food
The dimensions and weight of a pallet of dog food are primarily determined by the pallet’s size, the type and size of the dog food packaging, and the stacking configuration. These factors influence storage capacity, transportation costs, and handling requirements.
A standard pallet of dog food typically adheres to the following characteristics:
- Pallet Dimensions: The most common pallet size used in North America is the Grocery Manufacturers Association (GMA) pallet, measuring 48 inches (121.92 cm) in length and 40 inches (101.6 cm) in width. Other pallet sizes, such as the European standard pallet (Euro pallet), measuring 1200 mm x 800 mm (approximately 47.24 inches x 31.5 inches), might be used depending on the region and distribution network.
- Stacking Height: The height of a loaded pallet of dog food is influenced by the type and size of the dog food packaging and any specific stacking requirements. Generally, the height including the pallet itself, does not exceed 72 inches (182.88 cm) to ensure safe handling and efficient warehouse operations.
- Weight: The weight of a pallet of dog food varies significantly depending on the type of dog food (dry vs. wet), the packaging size, and the number of units stacked. A typical pallet of dry dog food can weigh between 1,500 to 2,500 pounds (680 to 1,134 kg). Wet dog food, due to its higher density and packaging type (cans or pouches), might result in a pallet weight closer to the higher end of this range, or even exceeding it depending on the specific product and packaging configuration.
Different Types of Dog Food Found on a Pallet
Pallets of dog food can contain a variety of products, catering to different dietary needs, life stages, and preferences of dogs. The composition of a pallet often reflects market demand, retailer requirements, and manufacturer’s product offerings.
Pallets can contain different types of dog food, including:
- Dry Kibble: This is the most common type of dog food, characterized by its relatively low moisture content and extended shelf life. Pallets of dry kibble typically contain bags or boxes of various sizes, ranging from small bags for puppies or small breeds to large bags for multiple-dog households.
- Wet Food: Wet dog food comes in cans, pouches, or trays and has a higher moisture content than dry kibble. Pallets of wet food often include cases of individual servings or larger containers, offering a range of flavors, textures, and formulations.
- Specific Diets: Pallets can also include specialized dog food formulations designed for specific dietary needs or health conditions. These might include:
- Grain-free formulas: Designed for dogs with grain sensitivities.
- Weight management formulas: For dogs needing to lose weight.
- Senior dog food: Formulated with ingredients that support the needs of older dogs.
- Hypoallergenic diets: For dogs with food allergies or sensitivities.
- Treats and Supplements: In addition to primary food sources, pallets may also include dog treats, chews, and nutritional supplements. These products are often packaged in smaller quantities and may be integrated with food products to create a comprehensive offering.
Common Pallet Sizes Used for Shipping Dog Food and Their Advantages
The choice of pallet size significantly affects the efficiency of the supply chain. Different pallet sizes offer advantages in terms of space utilization, handling, and transportation costs. The selection is frequently based on the regional standards, warehousing infrastructure, and transportation equipment.
You also can understand valuable knowledge by exploring seafood soul food.
The following table compares common pallet sizes and their advantages in shipping dog food:
Pallet Size | Dimensions (inches) | Advantages | Disadvantages |
---|---|---|---|
GMA Pallet | 48 x 40 |
|
|
Euro Pallet | 47.24 x 31.5 |
|
|
42 x 48 Pallet | 42 x 48 |
|
|
For instance, a large pet food manufacturer with a significant presence in North America might primarily utilize GMA pallets to streamline distribution within its domestic network. Conversely, a company exporting dog food to Europe would likely adopt Euro pallets to comply with European standards and optimize shipping efficiency within the region. The strategic selection of pallet size has direct impact on the efficiency and cost-effectiveness of the dog food supply chain.
Sourcing and Purchasing a Pallet of Dog Food
Procuring a pallet of dog food necessitates a strategic approach, encompassing the identification of reliable suppliers, careful consideration of purchasing factors, and a streamlined ordering process. This section provides a comprehensive guide to navigating the complexities of sourcing and purchasing dog food in bulk quantities.
Identifying Suppliers of Dog Food Pallets
A diverse range of suppliers caters to the demand for dog food pallets. Each offers unique advantages and disadvantages, necessitating a thorough evaluation.
- Online Retailers: Major online retailers, such as Amazon and Chewy, offer a convenient platform for purchasing dog food pallets. These platforms often provide competitive pricing, customer reviews, and subscription services for recurring deliveries. However, availability can vary, and shipping costs may impact the overall price.
- Wholesalers: Wholesalers specialize in bulk sales and frequently offer significant discounts on dog food pallets. They often cater to businesses and organizations, providing a reliable supply chain. Examples include large distribution centers that supply pet stores and other retailers. Minimum order quantities are often a requirement.
- Manufacturers: Purchasing directly from dog food manufacturers can provide access to the lowest possible prices and the freshest product. However, this option typically involves the largest minimum order quantities and may require direct negotiation with the manufacturer.
Factors to Consider When Choosing a Supplier
Selecting the optimal supplier involves a careful assessment of several critical factors that impact cost, quality, and convenience.
- Pricing: Compare prices from multiple suppliers, considering the price per unit (e.g., per bag or can) and the total cost of the pallet. Factor in any applicable discounts for bulk purchases or subscription services.
- Shipping Costs: Shipping costs can significantly impact the overall expense. Obtain quotes from different suppliers and consider factors such as distance, weight, and shipping method. Explore options for free shipping or reduced shipping costs.
- Product Freshness: Ensure the supplier maintains proper storage conditions to preserve product freshness and nutritional value. Inquire about the product’s expiration date and the supplier’s inventory turnover rate. Consider suppliers that prioritize efficient warehousing and distribution.
- Product Variety: Verify that the supplier carries the specific dog food brand and formula required. Evaluate the range of available options, including different sizes, flavors, and dietary formulations.
- Customer Service and Support: Assess the supplier’s responsiveness to inquiries and their willingness to address any issues that may arise. Read customer reviews to gauge their reputation for reliability and customer satisfaction.
The Process of Placing an Order for a Pallet of Dog Food
The ordering process involves several steps, from initial inquiry to final delivery.
- Initial Inquiry: Contact potential suppliers to inquire about the availability of dog food pallets. Request pricing information, shipping costs, and estimated delivery times.
- Order Placement: Once a supplier is selected, place the order, specifying the desired product, quantity, and delivery address. Review the order confirmation for accuracy.
- Payment: Arrange payment according to the supplier’s terms, which may include credit card, check, or wire transfer. Ensure secure payment methods are utilized.
- Delivery and Inspection: Upon delivery, carefully inspect the pallet for any signs of damage or discrepancies. Verify the product’s expiration date and confirm that the correct product was delivered.
- Follow-up: Maintain communication with the supplier to address any issues or concerns that may arise. Establish a system for tracking orders and managing inventory.
Comparison of Dog Food Brands Available in Pallet Quantities, Pallet of dog food
The following table presents a comparison of several dog food brands commonly available in pallet quantities. The data is for illustrative purposes and may vary based on supplier, region, and specific product formulations.
Brand | Price Per Unit (Approximate) | Ingredients (Key Examples) | Customer Ratings (Average) |
---|---|---|---|
Brand A (e.g., Purina Pro Plan) | $30 – $45 (per 30-lb bag) | Chicken, Rice, Corn, Soybean Meal, Brewers Rice, Fish Oil, Vitamins, Minerals | 4.5 out of 5 stars |
Brand B (e.g., Blue Buffalo) | $40 – $60 (per 24-lb bag) | Deboned Chicken, Brown Rice, Oatmeal, Peas, Chicken Fat, Flaxseed, Vitamins, Minerals | 4.3 out of 5 stars |
Brand C (e.g., Royal Canin) | $50 – $70 (per 30-lb bag) | Chicken By-Product Meal, Brewers Rice, Corn, Chicken Fat, Wheat Gluten, Fish Oil, Vitamins, Minerals | 4.2 out of 5 stars |
Brand D (e.g., Hill’s Science Diet) | $45 – $65 (per 33-lb bag) | Chicken Meal, Brewers Rice, Whole Grain Wheat, Corn Gluten Meal, Chicken Fat, Fish Oil, Vitamins, Minerals | 4.4 out of 5 stars |
Note: Pricing and customer ratings are approximate and subject to change. Always verify product information and supplier details before making a purchase.
Cost Analysis and Pricing
Analyzing the cost and establishing a pricing strategy are crucial for maximizing profitability when dealing with a pallet of dog food. This involves meticulous calculation of the per-unit cost, comparison with retail prices, and development of a competitive pricing model. The following sections will delve into these aspects, providing a comprehensive guide to optimizing financial returns.
Calculating the Average Cost Per Unit
Determining the average cost per unit is fundamental to understanding profitability. This calculation provides a baseline for pricing decisions and allows for accurate tracking of profit margins.To calculate the average cost per unit, the following steps are required:
- Determine the total cost of the pallet: This includes the purchase price of the pallet of dog food, including any applicable taxes, shipping costs, and any associated handling fees.
- Determine the number of units per pallet: This refers to the total number of individual bags or cans of dog food contained within the pallet. This information is usually available from the supplier.
- Calculate the average cost per unit: Divide the total cost of the pallet by the number of units.
For example:
If a pallet of dog food costs $1,200 and contains 100 units (bags), the average cost per unit is $12 ($1,200 / 100 = $12).
This cost serves as the foundation for pricing and profit margin calculations.
Comparing Pallet Purchases to Individual Unit Purchases
Comparing the cost of purchasing a pallet of dog food versus buying individual units reveals the potential for significant cost savings. This analysis highlights the benefits of bulk purchasing.The cost difference typically arises from several factors:
- Economies of Scale: Suppliers often offer discounts for larger orders due to reduced handling and shipping costs per unit.
- Reduced Shipping Costs: Shipping a pallet is often more cost-effective per unit than shipping individual bags or cans.
- Wholesale Pricing: Purchasing a pallet allows access to wholesale pricing, which is generally lower than retail pricing.
For example:
Consider a 15kg bag of premium dog food. Individually, it might retail for $45. Purchasing a pallet of 50 bags could cost $1,800, equating to $36 per bag. This represents a $9 saving per bag, or a total saving of $450 on the pallet.
This demonstrates the substantial financial advantages of bulk purchasing.
Demonstrating Potential Savings from Bulk Purchases
The savings achieved through bulk purchases are substantial and directly impact profitability. These savings can be reinvested in the business or passed on to customers to increase competitiveness.The following factors contribute to the overall savings:
- Lower per-unit cost: As demonstrated above, the per-unit cost is significantly reduced when buying a pallet compared to individual units.
- Reduced transportation expenses: Shipping costs are optimized when transporting a large volume of goods.
- Inventory management benefits: Purchasing in bulk can streamline inventory management and reduce the frequency of reordering.
A practical illustration:
A pet store anticipates selling 20 bags of dog food per month. Purchasing individual bags at $45 each would cost $900 monthly. Alternatively, buying a pallet of 100 bags for $3,600 (or $36 per bag) would cover five months of supply. This results in an immediate cash outlay, but the per-bag cost is reduced, and the store saves $9 per bag. Over five months, this equates to $900 in savings, offset by the initial investment.
This example highlights the cash flow considerations and the potential for long-term cost reduction.
Designing a Pricing Strategy for Reselling Individual Units
Developing a sound pricing strategy is critical for reselling individual units of dog food from a pallet. This strategy must consider market demand, competitor pricing, and the desired profit margin.A successful pricing strategy should encompass the following:
- Market Research: Analyze the prices of competitors selling similar dog food brands and sizes in the local market.
- Cost Calculation: Determine the per-unit cost based on the pallet purchase.
- Profit Margin: Decide on a desired profit margin per unit, factoring in operating costs, such as rent, utilities, and marketing expenses.
- Competitive Pricing: Set a price that is competitive with other retailers while still achieving the desired profit margin.
- Promotional Pricing: Consider offering discounts or promotions to attract customers and increase sales.
For instance:
If the per-unit cost is $12, and the market price for a similar product is $25, a retailer might set a price of $22 to remain competitive. This allows for a $10 profit margin per unit, while still being attractive to customers. Implementing a “buy two, get one 10% off” promotion can further increase sales volume. Regularly reviewing and adjusting the pricing strategy based on market conditions and sales data is essential.
This example provides a framework for a practical pricing model.
Storage and Handling
Proper storage and handling are crucial for maintaining the quality, safety, and shelf life of a pallet of dog food. Improper practices can lead to spoilage, pest infestations, and physical damage, resulting in financial losses and potential health risks for pets. This section Artikels the best practices for ensuring the integrity of dog food throughout its storage and handling lifecycle.
Proper Storage Conditions for Dog Food
Maintaining optimal storage conditions is paramount to preserving the nutritional value and palatability of dog food. Factors such as temperature, humidity, and exposure to contaminants significantly impact the product’s shelf life and safety.
- Temperature Control: Dog food should be stored in a cool, dry environment, ideally between 50°F (10°C) and 80°F (27°C). Fluctuations in temperature can lead to condensation inside the packaging, promoting mold growth and spoilage. Exposure to high temperatures can also accelerate the degradation of fats and vitamins, diminishing the nutritional value of the food. Consider a warehouse temperature monitoring system.
- Humidity Control: Humidity levels should be kept below 60%. High humidity can cause the food to absorb moisture, leading to clumping, mold growth, and a reduced shelf life. A dehumidifier or proper ventilation can help regulate humidity levels.
- Protection from Sunlight: Direct sunlight can degrade the vitamins and fats in dog food, leading to rancidity and a loss of nutritional value. Store pallets away from direct sunlight or use opaque coverings to protect the food.
- Ventilation: Ensure adequate ventilation to prevent the buildup of moisture and odors. Proper airflow helps to maintain a consistent temperature and humidity level.
- Cleanliness: The storage area must be kept clean and free from debris, pests, and potential contaminants. Regular cleaning and sanitation are essential to prevent cross-contamination and maintain the hygiene of the dog food.
- Storage Location: Store pallets of dog food off the floor, preferably on pallets, to prevent moisture absorption from the floor and facilitate air circulation. This also prevents potential pest infestations from the ground.
- Rotation: Implement a “First In, First Out” (FIFO) inventory management system. This ensures that older stock is used before newer stock, minimizing the risk of spoilage and maximizing shelf life.
Best Practices for Handling a Pallet of Dog Food
Proper handling techniques are essential to prevent damage to the packaging and the dog food itself, and to ensure the safety of personnel involved in the handling process. This involves using the correct equipment, following established procedures, and prioritizing safety at all times.
- Equipment Selection: Use appropriate equipment, such as forklifts or pallet jacks, to move pallets of dog food. Ensure that the equipment is in good working order and operated by trained personnel.
- Load Stability: Ensure the pallet is properly stacked and stable before moving it. Overhanging or unbalanced loads can be dangerous and increase the risk of the pallet tipping over. Use shrink wrap or strapping to secure the load.
- Safe Lifting Techniques: When manually handling individual bags or boxes, use proper lifting techniques to prevent injuries. Bend at the knees, keep the back straight, and hold the load close to the body.
- Avoid Dragging: Never drag pallets across the floor, as this can damage the packaging and the dog food.
- Avoid Sharp Objects: Exercise caution when handling pallets to avoid puncturing the packaging with sharp objects such as nails, staples, or broken pallet pieces.
- Inspect for Damage: Regularly inspect pallets for any signs of damage, such as tears, punctures, or water damage. Damaged products should be removed from the inventory and assessed for suitability for sale or use.
- Protective Gear: Employees handling dog food should wear appropriate personal protective equipment (PPE), such as gloves and eye protection, to prevent injury and maintain hygiene.
Step-by-Step Procedure for Breaking Down a Pallet of Dog Food
Breaking down a pallet of dog food for individual sale or use requires a systematic approach to ensure accuracy, efficiency, and safety. This process minimizes waste, prevents damage, and facilitates accurate inventory management.
- Preparation: Gather necessary tools and equipment, including a box cutter or utility knife, gloves, and a designated area for the breakdown process. Ensure adequate lighting and ventilation.
- Inspection: Inspect the pallet for any signs of damage or infestation. If any issues are found, isolate the affected products and take appropriate action.
- Documentation: Record the date, pallet identification number, and the number of units on the pallet.
- Cutting the Shrink Wrap: Carefully cut the shrink wrap or strapping, taking care not to damage the bags or boxes.
- Unit Removal: Remove the bags or boxes one at a time, carefully placing them in the designated area.
- Counting and Verification: Count each unit as it is removed to ensure accurate inventory control. Verify the count against the original pallet inventory.
- Storage: Place the individual units in their designated storage locations, following FIFO principles.
- Waste Disposal: Dispose of the shrink wrap, strapping, and other waste materials properly.
- Documentation Update: Update inventory records to reflect the breakdown of the pallet.
Ideal Warehouse Setup for Storing Multiple Pallets of Dog Food
An ideal warehouse setup for storing multiple pallets of dog food should prioritize temperature and humidity control, pest prevention, accessibility, and safety. The design should optimize space utilization while ensuring the integrity of the product and the safety of personnel.
- Building Structure: The warehouse should be constructed with durable, non-porous materials that are easy to clean and maintain. The floor should be level and sealed to prevent moisture absorption and pest entry.
- Temperature Control System: Install a robust HVAC system capable of maintaining a consistent temperature between 50°F (10°C) and 80°F (27°C). This system should include thermostats, sensors, and regular maintenance to ensure proper functionality.
- Humidity Control System: Implement a dehumidification system to maintain humidity levels below 60%. This could involve the use of dehumidifiers, ventilation systems, and moisture barriers.
- Pest Prevention Measures: Implement a comprehensive pest control program, including regular inspections, baiting stations, and sealing of cracks and crevices. Ensure that all doors and windows are screened to prevent pest entry. Regularly inspect the warehouse for signs of pests, such as droppings or gnawing marks.
- Lighting: Provide adequate lighting throughout the warehouse, including both general and task lighting. Use energy-efficient lighting options to minimize energy consumption.
- Racking System: Install a well-designed racking system to maximize storage space and improve accessibility. Consider using selective racking or drive-in racking systems, depending on the volume of inventory and the frequency of access.
- Fire Safety: Install a fire suppression system, such as sprinklers, and ensure that fire extinguishers are readily accessible. Implement fire safety procedures and conduct regular fire drills.
- Accessibility and Layout: Design the warehouse layout to facilitate efficient movement of pallets and personnel. Ensure that aisles are wide enough to accommodate forklifts and pallet jacks. Clearly mark aisles, storage locations, and safety zones. The layout should facilitate the FIFO system.
- Security System: Implement a security system to protect the inventory from theft and unauthorized access. This could include surveillance cameras, alarm systems, and access control measures.
- Cleaning and Sanitation: Establish a regular cleaning and sanitation schedule to maintain a clean and hygienic environment. This includes sweeping, mopping, and disinfecting surfaces.
Shipping and Delivery
The successful acquisition of a pallet of dog food culminates in its safe and timely delivery. This section details the various shipping options, associated costs, necessary documentation, and potential challenges involved in transporting a substantial quantity of pet food. Understanding these aspects is crucial for ensuring the integrity of the product and maintaining customer satisfaction.
Shipping Options for Pallets of Dog Food
Several shipping options are available for transporting a pallet of dog food, each with its own advantages and disadvantages. The choice depends on factors such as distance, budget, and desired delivery time.
- Freight Carriers: Freight carriers are the most common option for shipping pallets. They specialize in transporting large quantities of goods and offer various services, including less-than-truckload (LTL) and full truckload (FTL) options. LTL shipping involves consolidating multiple shipments onto one truck, which can be cost-effective for smaller orders. FTL shipping dedicates an entire truck to a single shipment, providing faster and more direct delivery, but at a higher cost.
- Delivery Services: While less common for entire pallets, some delivery services, particularly those specializing in oversized or heavy goods, might be considered, especially for local or regional deliveries. This option often involves a dedicated vehicle and a higher level of personalized service. However, it might not be as economical as freight carriers for long distances.
- Specialized Carriers: Certain carriers may specialize in transporting food products, including pet food. These carriers often have temperature-controlled options, which are crucial for maintaining the quality and integrity of the dog food, especially during warmer months. They may also possess specific expertise in handling and securing food products to prevent damage or contamination.
Estimated Shipping Times and Costs
Shipping times and costs are influenced by several factors, including distance, shipping method, and carrier. Providing precise figures is challenging due to the variability of these elements, but general estimates can be offered based on industry averages.
- Shipping Times:
- Local Deliveries (within 100 miles): Typically delivered within 1-2 business days.
- Regional Deliveries (100-500 miles): Expected delivery time is 2-5 business days.
- National Deliveries (over 500 miles): Transit times range from 3-7 business days, depending on the specific route and carrier.
- Shipping Costs:
- LTL Shipping: Costs vary significantly based on distance, weight, and freight class (determined by the product’s density and handling requirements). As an example, shipping a pallet of dog food weighing approximately 1,500 pounds a distance of 500 miles could cost between $300 and $700.
- FTL Shipping: FTL costs are generally higher than LTL, reflecting the dedicated use of a truck. A similar pallet shipped FTL over the same distance might cost between $800 and $1,500.
- Additional Charges: Keep in mind that these costs do not include potential additional charges such as fuel surcharges, liftgate service (for deliveries without a loading dock), and residential delivery fees.
Documentation Required for Shipping
Proper documentation is essential for a smooth shipping process and compliance with relevant regulations. Failure to provide the necessary paperwork can result in delays, fines, and even the rejection of the shipment.
- Bill of Lading (BOL): The BOL is the most crucial document. It serves as a receipt of goods, a contract between the shipper and the carrier, and a title to the goods. It contains detailed information about the shipment, including the shipper’s and consignee’s names and addresses, the product description, weight, dimensions, and any special handling instructions.
- Commercial Invoice: This document details the value of the goods, the terms of sale, and other relevant financial information. It is essential for customs clearance if the shipment crosses international borders.
- Packing List: The packing list itemizes the contents of the pallet, including the number of cartons or bags, their individual weights, and any identifying marks or labels. It assists in verifying the shipment’s contents upon arrival.
- Material Safety Data Sheet (MSDS) or Safety Data Sheet (SDS): If the dog food contains any potentially hazardous ingredients (e.g., certain preservatives or additives), an MSDS/SDS may be required. This document provides information about the product’s composition, potential hazards, and safe handling procedures.
- Certificate of Origin: For international shipments, a certificate of origin may be required to verify the country where the dog food was manufactured. This document can affect customs duties and compliance with trade agreements.
Common Shipping Issues and Mitigation Strategies
Shipping a pallet of dog food can present several challenges. Addressing these potential issues proactively is crucial for minimizing delays and damages. Common problems include:
- Damage during transit: Pallets can be damaged due to improper loading, rough handling, or inadequate packaging. To mitigate this, ensure the pallet is properly constructed, the dog food bags or cartons are securely stacked and shrink-wrapped, and that corner boards or edge protectors are used. Label the pallet with “Fragile” or “Handle with Care” if needed.
- Delays: Shipping delays can occur due to traffic congestion, inclement weather, or carrier issues. Choosing a reputable carrier with a good track record of on-time deliveries and providing accurate shipping information can help minimize delays. Consider purchasing shipping insurance to cover any losses.
- Temperature fluctuations: Extreme temperatures can affect the quality and shelf life of dog food. If temperature control is essential, opt for refrigerated or climate-controlled shipping options.
- Lost or misdirected shipments: Proper labeling, tracking, and communication with the carrier are vital to prevent lost or misdirected shipments. Obtain a tracking number and monitor the shipment’s progress regularly. Ensure the consignee’s address is accurate and complete.
Uses and Applications
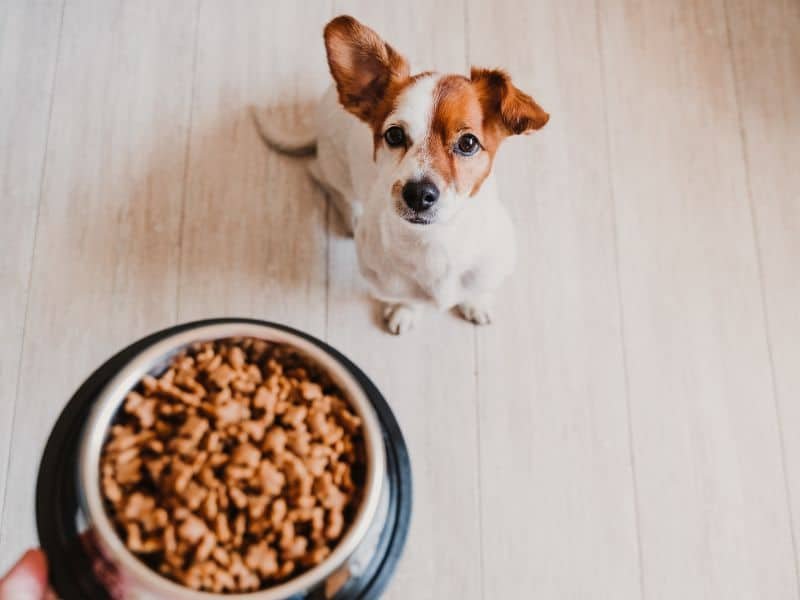
Purchasing a pallet of dog food offers significant advantages for various entities involved in canine care. This section details the practical applications and benefits associated with bulk dog food procurement, providing insights for pet owners, breeders, animal shelters, and rescue organizations.
Applications for Pet Owners and Breeders
Pet owners, particularly those with multiple dogs or specific dietary requirements, can find significant value in buying dog food in bulk. Breeders, managing a larger canine population, can realize substantial cost savings and ensure consistent access to high-quality nutrition.
Purchasing a pallet of dog food can reduce the cost per unit, potentially by up to 30% compared to buying individual bags.
- Cost Efficiency: Buying in bulk significantly lowers the cost per serving, offering long-term financial benefits. This is especially advantageous for owners of large breeds or multiple dogs.
- Dietary Consistency: Maintaining a consistent diet is crucial for canine health. Bulk purchasing minimizes the risk of switching brands or formulations due to supply issues or price fluctuations.
- Convenience: Having a readily available supply of dog food reduces the frequency of shopping trips and ensures food is always on hand. This is especially beneficial for busy pet owners.
- Specialized Diets: Owners of dogs with specific dietary needs (e.g., allergies, sensitivities) can ensure a consistent supply of specialized food formulas.
- Breeding Operations: For breeders, a pallet of dog food guarantees a reliable food supply for the breeding stock and puppies, supporting their health and development.
Applications for Animal Shelters and Rescue Organizations
Animal shelters and rescue organizations rely on a consistent supply of dog food to feed their residents. Bulk purchasing programs can substantially improve their operational efficiency and financial stability.
- Cost Reduction: The primary benefit is the significant reduction in food costs, allowing shelters to allocate resources to other critical areas, such as veterinary care and adoption programs.
- Inventory Management: Bulk purchases streamline inventory management, reducing the need for frequent restocking and minimizing the risk of running out of food.
- Donor Support: Bulk purchases can attract donor support. Donors are often more willing to contribute when they know their donations will be used efficiently.
- Partnerships: Shelters can establish partnerships with dog food manufacturers or distributors, securing discounts or donations.
- Feeding Programs: Shelters can utilize bulk food to provide food assistance programs for low-income pet owners in the community.
Successful Bulk Purchasing Programs
Numerous animal shelters and rescue organizations have successfully implemented bulk purchasing programs. For example, “The Humane Society of the United States” often negotiates contracts with pet food companies to secure large quantities of food at discounted prices for its network of shelters. Similarly, smaller, regional rescue groups frequently pool resources to purchase pallets of dog food, sharing the cost and storage responsibilities.
Pooling resources and forming partnerships can provide greater buying power for smaller organizations.
An example of this is a collaborative effort between several small rescue organizations in a specific region. They collectively purchase a pallet of a specific dog food formula, dividing the food based on their individual needs and storage capacity. This approach allows them to access the benefits of bulk purchasing without the individual burden of storing a full pallet. This strategy also allows for better negotiation with suppliers.
Benefits of Buying a Pallet of Dog Food
Buying a pallet of dog food offers several advantages, impacting financial stability, operational efficiency, and animal welfare. These benefits extend across diverse scenarios, from individual pet owners to large-scale animal care facilities.
- Reduced Cost per Unit: Bulk purchases result in lower per-unit costs compared to buying individual bags or smaller quantities.
- Improved Budgeting: Predictable food costs enable better budgeting and financial planning.
- Consistent Food Supply: Having a pallet of dog food ensures a consistent food supply, reducing the risk of shortages.
- Reduced Shipping Costs: The cost per unit of shipping is significantly lower when shipping a pallet compared to individual bags.
- Convenience and Time Savings: Fewer trips to the store save time and effort.
- Reduced Environmental Impact: Bulk purchasing often reduces packaging waste.
- Enhanced Animal Welfare: Consistent nutrition contributes to the overall health and well-being of the dogs.
Shelf Life and Expiration
The shelf life of dog food, particularly when stored on a pallet, is a critical factor in ensuring its quality, nutritional value, and safety for consumption. Proper understanding and management of expiration dates are essential for minimizing waste, optimizing inventory turnover, and protecting the health of dogs. This section Artikels the key aspects of determining and managing the shelf life of dog food stored on a pallet.
Determining Shelf Life
Determining the shelf life of dog food on a pallet involves understanding the manufacturer’s guidelines and the characteristics of the product. Dog food products typically display a “best by” or “use by” date, which indicates the period during which the food is expected to retain its optimal quality and nutritional value. This date is usually printed on individual bags or cans, and the expiration date for a pallet is derived from the earliest “best by” date of the products contained within.
Factors Affecting Shelf Life
Several factors can significantly affect the shelf life of dog food, potentially leading to spoilage or a decline in nutritional quality. Understanding these factors is crucial for proper storage and handling.
- Type of Food: Dry kibble generally has a longer shelf life than wet or fresh dog food due to its lower moisture content. Kibble can often last for 12-18 months from the manufacturing date if stored properly. Wet food, however, typically has a shorter shelf life, often 12-24 months from the manufacturing date. Fresh or refrigerated dog food has the shortest shelf life, often just a few weeks or months.
- Packaging: Airtight, sealed packaging is essential for preserving the quality of dog food. Damage to packaging, such as tears or punctures, can expose the food to air and moisture, accelerating spoilage.
- Storage Conditions: Proper storage is crucial for extending shelf life. High temperatures, humidity, and exposure to direct sunlight can degrade the food’s nutritional content and lead to the growth of mold or bacteria.
- Ingredients: Dog foods with high fat content may be more susceptible to rancidity over time. The presence of natural or artificial preservatives can significantly impact shelf life.
Strategies for Minimizing Waste
Managing a pallet of dog food to minimize waste due to expiration requires a proactive approach to inventory control and storage practices. Implementing a “first-in, first-out” (FIFO) system is critical.
- Inventory Tracking: Maintain a detailed inventory log that includes the “best by” dates of each product on the pallet. This can be done manually using spreadsheets or with inventory management software.
- FIFO System: Always rotate stock, ensuring that older products are used or sold before newer ones. This reduces the likelihood of products expiring before they are utilized.
- Regular Inspection: Regularly inspect the pallet of dog food for damaged packaging or signs of spoilage, such as changes in color, odor, or texture.
- Proper Storage: Store the pallet of dog food in a cool, dry place away from direct sunlight. Maintain consistent temperature and humidity levels.
- Sales and Promotions: Implement sales or promotional strategies to sell products nearing their expiration dates. This can help reduce waste and recoup some of the investment.
Checking and Organizing Expiration Dates
Checking expiration dates and organizing a pallet of dog food is a systematic process that should be performed regularly. This ensures that the products are used in a timely manner and that any potential issues are identified promptly.The process involves the following steps:
- Gathering Materials: Collect necessary materials, including a flashlight, a clipboard or notebook, a pen or marker, and a pallet jack or forklift for moving the pallet if necessary. Consider wearing gloves for hygiene purposes.
- Visual Inspection: Before beginning, conduct a visual inspection of the pallet. Check for any signs of damage to the packaging, such as tears, punctures, or signs of water damage. Note any damaged bags or cans.
- Date Verification: Systematically examine each bag or can of dog food on the pallet to locate the “best by” or “use by” date. This date is usually printed on the packaging, often near the bottom or on a side panel. Use a flashlight to improve visibility if needed.
- Recording Dates: Record the “best by” dates for each product in the inventory log. Note the product type, size, and the corresponding date.
- Sorting and Organizing: Organize the products on the pallet based on their expiration dates. Place products with the earliest “best by” dates at the front or in a readily accessible location. Consider creating distinct zones or rows for different expiration date ranges. For example, products expiring within three months could be placed in a designated “urgent use” zone.
- Updating Inventory: Update the inventory log to reflect the organized arrangement of products on the pallet. This will assist in the FIFO process during future stock rotations.
- Addressing Damaged Products: Dispose of any damaged products or isolate them for further inspection. If the damage is minor, consider selling the products at a discounted price after a thorough assessment of the food’s integrity.
- Regular Review: Repeat this process regularly, at least monthly or more frequently if inventory turnover is slow. This proactive approach ensures that products are used before they expire and that any potential issues are addressed promptly.
Last Recap: Pallet Of Dog Food
So there you have it, from pallet to plate! Buying a pallet of dog food can be a smart move, especially if you’re in it for the long haul. Remember to do your homework, compare prices, and always think about storage and expiration dates. With a little planning, you can keep those tails wagging and those bellies full without breaking the bank.
Selamat mencoba, and happy feeding!