Alright, buckle up buttercups, because we’re diving headfirst into the wonderfully utilitarian world of plastic food baskets! Forget boring old containers; these are the unsung heroes of the food industry, holding everything from farm-fresh produce to your late-night takeout feast. From the grocery store aisles to the bustling kitchens of your favorite restaurants, these baskets are quietly, efficiently, and often stylishly, doing their job.
But what exactly makes these plastic wonders so essential? Let’s crack open this picnic basket of knowledge and find out!
We’ll explore their materials, their manufacturing secrets (think injection molding magic!), and their surprising sustainability stories. We’ll uncover the different types, from the humble produce basket to the fancy restaurant-ready carriers. Plus, we’ll delve into the industries that rely on them, the regulations that keep them safe, and the design features that make them so darn useful. Get ready to become a plastic food basket aficionado!
Introduction: Defining Plastic Food Baskets
Plastic food baskets are versatile containers designed primarily for the transportation, storage, and display of food products. They are ubiquitous in various sectors, from supermarkets and farmers’ markets to restaurants and food processing facilities, streamlining food handling processes. These baskets offer a practical and cost-effective solution for managing a wide range of items, enhancing efficiency and ensuring food safety.
Materials Used in Manufacturing
The materials used in manufacturing plastic food baskets are selected based on their durability, food safety compliance, and resistance to environmental factors. These materials ensure the baskets can withstand repeated use and exposure to different temperatures, while also protecting the food products from contamination.
Explore the different advantages of mediterranean food overland park that can change the way you view this issue.
- Polypropylene (PP): This is a common choice due to its high melting point, chemical resistance, and ability to be molded into various shapes. PP baskets are often used for hot food applications as they can withstand higher temperatures without deforming or releasing harmful chemicals.
- High-Density Polyethylene (HDPE): HDPE is another widely used material, known for its strength, rigidity, and resistance to moisture and impact. Baskets made from HDPE are suitable for cold storage and transportation of a variety of food items, including produce and frozen goods.
- Low-Density Polyethylene (LDPE): LDPE offers flexibility and good impact resistance. It is frequently used for applications where a degree of pliability is desired.
- Polycarbonate (PC): Polycarbonate is a clear, strong, and impact-resistant plastic that offers excellent transparency, allowing easy visibility of the contents. While PC is highly durable, its use in food contact applications is carefully regulated due to potential leaching of BPA (Bisphenol A), so it is used less frequently.
- Recycled Plastics: Many manufacturers are now incorporating recycled plastics into their production processes, reducing waste and promoting sustainability. These baskets often utilize a blend of virgin and recycled materials, maintaining performance while minimizing environmental impact.
Sizes and Shapes Available, Plastic food baskets
Plastic food baskets are manufactured in a wide array of sizes and shapes to accommodate different types and quantities of food products. This diversity ensures that businesses can select baskets that are optimally suited for their specific needs, improving efficiency and minimizing waste.
- Rectangular Baskets: These are a standard shape, ideal for stacking and maximizing space utilization. They are available in various sizes, from small baskets for individual portions to large ones for bulk storage and transport. For instance, a typical rectangular basket used in grocery stores might measure 18 x 13 x 6 inches, designed to hold produce like apples or oranges.
- Square Baskets: Square baskets offer a compact design and are often used for displaying items on shelves or in retail settings. Their dimensions are often standardized to fit shelving systems, maximizing display space.
- Round Baskets: Round baskets are commonly used for items like baked goods, fruits, and vegetables. Their shape can be visually appealing, and they may include handles for easy carrying. A round basket might have a diameter of 12 inches and a depth of 4 inches, making it suitable for displaying pastries.
- Specialty Baskets: These are designed for specific food items or applications. Examples include baskets with drainage holes for washing produce, baskets with lids for protecting food during transport, and baskets with handles for easy carrying. Some examples of specialty baskets include those designed to hold specific numbers of eggs (e.g., a 30-egg basket), or those specifically designed for fish, allowing drainage.
- Stackable Baskets: Designed for space-saving storage, stackable baskets often have a lip or groove to securely fit one basket on top of another. This feature is particularly useful in environments with limited storage space.
Applications and Industries
Plastic food baskets, born from the need for efficient and hygienic food handling, have become indispensable across a multitude of sectors. Their versatility, durability, and ease of sanitation have propelled them to the forefront of food logistics, from farm to table. These baskets streamline operations, reduce waste, and ensure the safe delivery of edibles to consumers.
Grocery Store Usage
Grocery stores rely heavily on plastic food baskets for various crucial tasks, enhancing operational efficiency and preserving product quality. These baskets provide a robust solution for managing the vast array of fresh produce, packaged goods, and prepared foods that define the modern supermarket experience.
- Produce Display and Handling: Plastic baskets are frequently used to display fruits and vegetables. Their open design promotes air circulation, extending the shelf life of delicate items like berries and leafy greens. The lightweight nature of these baskets makes them easy for employees to handle during restocking and rotation. Consider a vibrant display of apples, each piece nestled safely in a brightly colored basket, inviting customers to select their perfect fruit.
- Checkout and Customer Convenience: At checkout, plastic baskets provide a convenient way for customers to carry their purchases. Their sturdy construction ensures that groceries remain secure, and their ergonomic design allows for comfortable handling, even when filled with heavy items. Imagine a shopper effortlessly maneuvering a basket overflowing with groceries through the checkout lane.
- Back-of-House Operations: Beyond the customer-facing areas, plastic baskets play a vital role in the back of the house. They are used for storing and transporting goods from the receiving dock to the shelves, ensuring that products are kept organized and protected. Picture rows of neatly stacked plastic baskets filled with various food items, streamlining inventory management.
- Self-Service Areas: In self-service areas, such as salad bars or bulk food sections, plastic baskets allow customers to easily select and portion their desired items. These baskets often feature handles and convenient sizes, allowing for simple portioning.
Food Service Industry Applications
The food service industry, encompassing restaurants, catering businesses, and fast-food establishments, finds plastic food baskets to be an invaluable asset for optimizing operations and ensuring food safety. Their durability, ease of cleaning, and ability to withstand frequent use make them a practical choice in this high-volume environment.
- Restaurant Operations: Restaurants employ plastic food baskets for various tasks, including transporting food from the kitchen to the dining area, organizing ingredients in the kitchen, and storing prepared dishes. These baskets are particularly useful for bussing tables, efficiently collecting dirty dishes and transporting them to the dishwashing area. Imagine a busy restaurant kitchen, where plastic baskets are constantly in motion, efficiently moving food and supplies.
- Catering Services: Catering companies depend on plastic food baskets for transporting and serving food at events. The baskets can be customized with lids and dividers to keep food items separate and at the correct temperature. The ability to stack these baskets allows caterers to transport large quantities of food easily. Consider a catering event where a team of servers uses neatly stacked plastic baskets to deliver hot meals to guests.
- Fast Food Efficiency: Fast-food restaurants utilize plastic baskets for food preparation, storage, and serving. They often use specialized baskets designed to hold specific items, such as french fries or chicken nuggets. This helps standardize portion sizes and streamline the serving process. Visualize a fast-food restaurant where plastic baskets are an integral part of the assembly line.
Agricultural Applications
Plastic food baskets are essential tools in agriculture, particularly during harvesting and transportation. Their resistance to moisture, pests, and temperature fluctuations makes them ideal for handling produce from the field to the processing plant or market.
- Harvesting: During harvest, plastic baskets are used to collect and transport crops from the field. Their sturdy construction protects delicate fruits and vegetables from damage. The lightweight nature of these baskets makes them easy to carry and maneuver in the fields. Picture a field of ripe tomatoes, with workers carefully placing the harvest into durable plastic baskets.
- Transportation: After harvesting, plastic baskets are used to transport crops to processing plants, storage facilities, or markets. The baskets can be stacked and secured on trucks, protecting the produce from damage during transit. The standardized sizes of these baskets make them easy to load and unload. Consider a truckload of fresh peaches, securely packed in plastic baskets, ready for delivery to the grocery store.
- Storage: Plastic baskets are also utilized for storing produce in warehouses and cold storage facilities. Their open design promotes air circulation, helping to maintain the freshness and quality of the stored items. The baskets can be easily cleaned and sanitized, preventing the spread of disease.
- Specific Crop Uses: Different types of plastic baskets are designed for specific crops. For example, strawberry baskets are often shallow and vented to allow for proper air circulation, while potato baskets may be larger and more robust to handle the weight.
Advantages of Plastic Food Baskets
In the realm of food handling and transportation, the choice of container significantly impacts efficiency, hygiene, and cost-effectiveness. Plastic food baskets offer a compelling alternative to traditional materials like cardboard and wood, presenting a suite of benefits that cater to the evolving demands of the food industry. Their inherent advantages extend beyond mere functionality, shaping a more sustainable and streamlined approach to food distribution.
Durability and Reusability Advantages
The longevity of plastic food baskets, compared to their counterparts, offers significant advantages in terms of both cost and environmental impact. Unlike single-use cardboard or the often-fragile nature of wooden crates, plastic baskets are engineered for repeated use, enduring the rigors of frequent handling, transportation, and washing.
- Extended Lifespan: Plastic baskets can withstand numerous cycles of use, lasting for years with proper care. This contrasts sharply with cardboard, which degrades rapidly upon exposure to moisture, and wood, which is susceptible to splintering, rot, and insect infestation. For example, a major produce distributor switched from wooden crates to plastic baskets and reported a 70% reduction in container replacement costs over a five-year period.
- Resistance to Damage: Plastic baskets are resistant to impacts, punctures, and abrasions, protecting the food contents from damage during transit. This minimizes food waste and preserves the quality of the produce or other items being transported.
- Stackability and Space Efficiency: Many plastic food baskets are designed to be stackable, both when full and when empty. This optimizes storage space in warehouses and during transportation, reducing logistical costs and environmental footprint.
- Reduced Packaging Waste: The reusability of plastic baskets significantly reduces the volume of packaging waste compared to single-use options. This aligns with the growing global emphasis on sustainability and waste reduction initiatives.
Ease of Cleaning and Sanitizing
Maintaining impeccable hygiene is paramount in the food industry, and plastic food baskets excel in this regard. Their non-porous surfaces and design facilitate easy and effective cleaning, minimizing the risk of contamination and ensuring food safety.
- Non-Porous Surfaces: Plastic materials are inherently non-porous, preventing the absorption of food particles, bacteria, and odors. This makes them easy to clean and sanitize thoroughly.
- Resistance to Chemicals: Plastic baskets are generally resistant to a wide range of cleaning agents and sanitizers, allowing for the use of effective cleaning protocols without damaging the material.
- Simplified Cleaning Procedures: The smooth surfaces and open designs of many plastic baskets make them easy to clean manually or through automated washing systems. This contrasts with the difficulty of cleaning porous materials like wood, where bacteria can thrive in crevices. A major food processing plant implemented a plastic basket system and reported a 95% reduction in cleaning time compared to their previous wooden crate system.
- High-Temperature Tolerance: Many plastic baskets are designed to withstand high-temperature washing and sanitizing cycles, ensuring effective sterilization and eliminating potential contaminants.
Cost-Effectiveness Over Time
While the initial investment in plastic food baskets may be higher than that of disposable alternatives, their long-term cost-effectiveness becomes evident through reduced replacement costs, minimized waste, and improved operational efficiency.
“The initial cost of plastic food baskets can be offset by their extended lifespan and reduced operational expenses.”
- Reduced Replacement Costs: The durability and reusability of plastic baskets significantly reduce the frequency of replacements compared to single-use containers. This translates into substantial cost savings over time.
- Minimized Waste Disposal Costs: The reusability of plastic baskets drastically reduces the volume of waste that needs to be disposed of, leading to lower waste disposal fees and a smaller environmental footprint.
- Improved Operational Efficiency: The stackability, standardized sizes, and ease of handling of plastic baskets streamline logistics and warehouse operations, reducing labor costs and improving overall efficiency. For instance, a study showed that a large grocery chain that transitioned to plastic baskets for produce distribution saw a 15% reduction in labor costs related to handling and sorting.
- Reduced Food Spoilage: The protection afforded by plastic baskets during transportation minimizes food spoilage, reducing financial losses and ensuring product quality.
Manufacturing Process
The creation of plastic food baskets is a carefully orchestrated process, transforming raw materials into functional and durable products. This journey involves a series of precise steps, from the initial selection of materials to the final inspection and packaging, ensuring the highest quality and safety standards are met. Understanding this process is crucial to appreciating the engineering and innovation behind these everyday items.
General Manufacturing Process
The manufacturing of plastic food baskets typically involves several key stages, each contributing to the final product’s form and functionality. These steps are often streamlined to optimize efficiency and minimize waste.
- Material Preparation: The process begins with selecting and preparing the plastic resin. This involves ensuring the resin meets the required food-grade standards and may include adding colorants, stabilizers, or other additives to enhance its properties.
- Molding: This is the core of the manufacturing process, where the molten plastic is shaped into the desired basket form. Various molding techniques, such as injection molding, are employed based on the design complexity and production volume.
- Cooling and Solidification: After molding, the plastic basket needs to cool and solidify. This step is crucial for maintaining the shape and structural integrity of the product. The cooling process is carefully controlled to prevent warping or deformation.
- Ejection and Trimming: Once cooled, the basket is ejected from the mold. Any excess plastic, such as sprues or flash, is trimmed away. This stage ensures the basket has a clean and finished appearance.
- Quality Control: Rigorous quality control checks are performed throughout the process, from material inspection to final product evaluation. These checks ensure the baskets meet all safety and performance standards.
- Finishing and Packaging: The finished baskets may undergo additional finishing steps, such as surface treatments or labeling. Finally, the baskets are packaged and prepared for distribution.
Common Plastic Molding Techniques
Several plastic molding techniques are commonly used in the production of food baskets, each offering unique advantages depending on the design and required production volume.
- Injection Molding: This is the most prevalent method, especially for high-volume production. Molten plastic is injected into a mold cavity under high pressure, allowing for intricate designs and consistent dimensions. The process allows for the rapid creation of complex shapes with excellent detail. For instance, a manufacturer producing thousands of baskets daily would likely utilize injection molding due to its efficiency and ability to create intricate features like interlocking handles or reinforced corners.
- Blow Molding: While less common for food baskets than injection molding, blow molding might be employed for specific designs, particularly those with hollow sections or handles that need to be integrated. The process involves inflating molten plastic within a mold to create a hollow shape.
- Extrusion Molding: This technique involves forcing molten plastic through a die to create a continuous profile. While less suited for the complete basket, it could be used to create components like handles or reinforcing ribs that are later assembled.
- Rotational Molding: This method involves rotating a mold containing plastic powder or liquid while heating it. The plastic adheres to the mold’s inner surface, creating a hollow part. This technique is suitable for producing large or irregularly shaped baskets in lower volumes.
Steps Involved in Quality Control
Quality control is paramount in the manufacturing of plastic food baskets, ensuring they meet food safety regulations and perform reliably. A multi-faceted approach is employed, integrating inspections at various stages of the production process.
- Raw Material Inspection: Incoming plastic resin is thoroughly inspected to verify its compliance with food-grade standards, including testing for contaminants and ensuring it meets specified physical properties, such as tensile strength and impact resistance.
- Molding Process Monitoring: During the molding process, parameters such as temperature, pressure, and cycle time are continuously monitored and adjusted to maintain consistent product quality. Sensors and automated systems help to identify and address any deviations from the established parameters.
- Dimensional Checks: Baskets are regularly inspected for dimensional accuracy, ensuring they meet the specified size and shape requirements. This involves using precision measuring tools, such as calipers and gauges, to verify critical dimensions like the height, width, and depth of the basket.
- Visual Inspection: Each basket undergoes a visual inspection to identify any defects, such as cracks, warpage, or imperfections in the surface finish. Trained inspectors carefully examine the baskets for any signs of damage or non-conformity.
- Performance Testing: Baskets may undergo performance testing to assess their durability and functionality. This can include drop tests to evaluate impact resistance, load tests to determine weight-bearing capacity, and chemical resistance tests to ensure they can withstand exposure to food and cleaning agents.
- Food Safety Compliance: Baskets are tested to ensure they do not leach harmful chemicals into food. This involves simulating food contact and analyzing the plastic for migration of substances that could pose a health risk.
Visual Representation of the Manufacturing Process
A visual representation of the manufacturing process would illustrate the key stages, using clear and concise imagery to convey the workflow.
Illustration Description:
The illustration depicts a circular diagram, representing the continuous nature of the manufacturing process. The circle is divided into sections, each representing a key stage, with arrows indicating the flow of the process.
The illustration starts at the top with a section labeled “Raw Material Receiving & Inspection,” showcasing a delivery truck unloading pallets of plastic resin, accompanied by a quality control inspector examining a sample.
Moving clockwise, the next section is “Material Preparation & Mixing,” showing a worker operating a machine that blends the resin with additives and colorants.
The subsequent section, “Injection Molding,” is the largest, illustrating an injection molding machine with a mold open, revealing a partially formed plastic basket. Molten plastic is being injected into the mold. The machine is depicted with detailed components such as the clamping unit, injection unit, and ejector pins.
Following injection molding, the “Cooling & Solidification” section shows the basket moving along a conveyor belt through a cooling tunnel, with fans circulating air.
Next is “Ejection & Trimming,” where a robotic arm removes the cooled basket from the mold and another worker trims excess plastic.
The “Quality Control” section displays inspectors performing various tests on the finished baskets.
There is an inspector using calipers, another performing a drop test, and another checking for visual defects.
The “Finishing & Packaging” section shows workers labeling and packaging the baskets for shipment. A forklift is shown loading the packaged baskets onto a pallet.
The final arrow returns to the beginning, symbolizing the continuous cycle of manufacturing.
Materials and Sustainability: Plastic Food Baskets
The journey of a plastic food basket, from its creation to its eventual end-of-life, is inextricably linked to the materials it’s made from and the environmental impact those materials entail. Understanding these aspects is crucial for making informed choices that balance functionality with environmental responsibility. This section delves into the specific plastics used, their environmental footprints, and the evolving landscape of sustainable practices within the industry.
Types of Plastics Used in Food Basket Production
The selection of plastic for food basket production hinges on a delicate balance of properties: durability, food safety, cost-effectiveness, and recyclability. Two primary types of plastics dominate this landscape: polypropylene (PP) and polyethylene (PE).Polypropylene (PP) is a thermoplastic polymer known for its high strength, resistance to heat, and chemical inertness. It’s a common choice for food baskets because it can withstand the rigors of repeated use and cleaning, and it doesn’t leach harmful chemicals into food.
It is often used in applications requiring high durability, such as baskets designed for carrying heavier loads or those subjected to frequent washing.Polyethylene (PE) comes in various densities, each with different characteristics. High-density polyethylene (HDPE) is rigid and offers good resistance to chemicals, making it suitable for baskets designed to hold a variety of food items. Low-density polyethylene (LDPE) is more flexible and is sometimes used for components or coatings in food baskets.
Plastic Type | Properties | Typical Food Basket Applications |
---|---|---|
Polypropylene (PP) | High strength, heat resistance, chemical inertness | Durable baskets, baskets for hot foods, baskets requiring repeated cleaning |
High-Density Polyethylene (HDPE) | Rigid, good chemical resistance | Baskets for a variety of food items, storage containers |
Low-Density Polyethylene (LDPE) | Flexible | Components, coatings |
Environmental Impact of Various Plastic Materials
The environmental impact of plastic food baskets is multifaceted, encompassing factors from raw material extraction to waste management. The carbon footprint of plastic production, the energy consumed during manufacturing, and the potential for plastic pollution all contribute to this impact.The production of plastics relies heavily on fossil fuels, contributing significantly to greenhouse gas emissions. The manufacturing process itself, from the initial polymerization to the molding of the baskets, consumes considerable energy.
Furthermore, the disposal of plastic food baskets, particularly if they end up in landfills or the environment, poses a significant threat.The long lifespan of plastics, which allows them to persist for centuries, contributes to the buildup of plastic waste in landfills and oceans. This persistent pollution can harm wildlife, contaminate ecosystems, and pose risks to human health. The impact varies depending on the type of plastic, with some plastics, like PP and HDPE, being more readily recyclable than others.
Recyclability of Plastic Food Baskets
Recyclability is a critical aspect of mitigating the environmental impact of plastic food baskets. The effectiveness of recycling programs depends on several factors, including the type of plastic, the availability of recycling infrastructure, and consumer behavior.Both polypropylene (PP) and high-density polyethylene (HDPE) are generally considered recyclable. However, the success of recycling efforts is not guaranteed. Contamination with food residue or other materials can render baskets unrecyclable.
Furthermore, the presence of additives or colorants can also complicate the recycling process.The ideal scenario involves a closed-loop system where used food baskets are collected, sorted, cleaned, and reprocessed into new products. This approach minimizes waste and reduces the demand for virgin plastics. However, achieving a truly closed-loop system requires significant investment in recycling infrastructure, as well as public education and participation.
Sustainable Plastic Food Basket Production and Disposal
The pursuit of sustainability in the plastic food basket industry involves a combination of strategies, including the use of recycled materials, the development of bio-based plastics, and the implementation of effective waste management practices.The integration of recycled plastics into food basket production is a key step toward sustainability. Using recycled PP or HDPE reduces the demand for virgin materials and helps to divert plastic waste from landfills.
However, challenges remain, including ensuring the quality and safety of recycled materials, as well as the potential for contamination.Bio-based plastics, derived from renewable resources like cornstarch or sugarcane, offer an alternative to traditional fossil fuel-based plastics. While bio-based plastics can reduce the carbon footprint of production, they also raise concerns about land use and the potential for competition with food crops.Effective waste management practices are crucial for minimizing the environmental impact of plastic food baskets.
This includes promoting source reduction, encouraging reuse and recycling, and developing composting systems for biodegradable plastics. Education and awareness campaigns can play a significant role in influencing consumer behavior and promoting responsible disposal practices.
Regulations and Standards
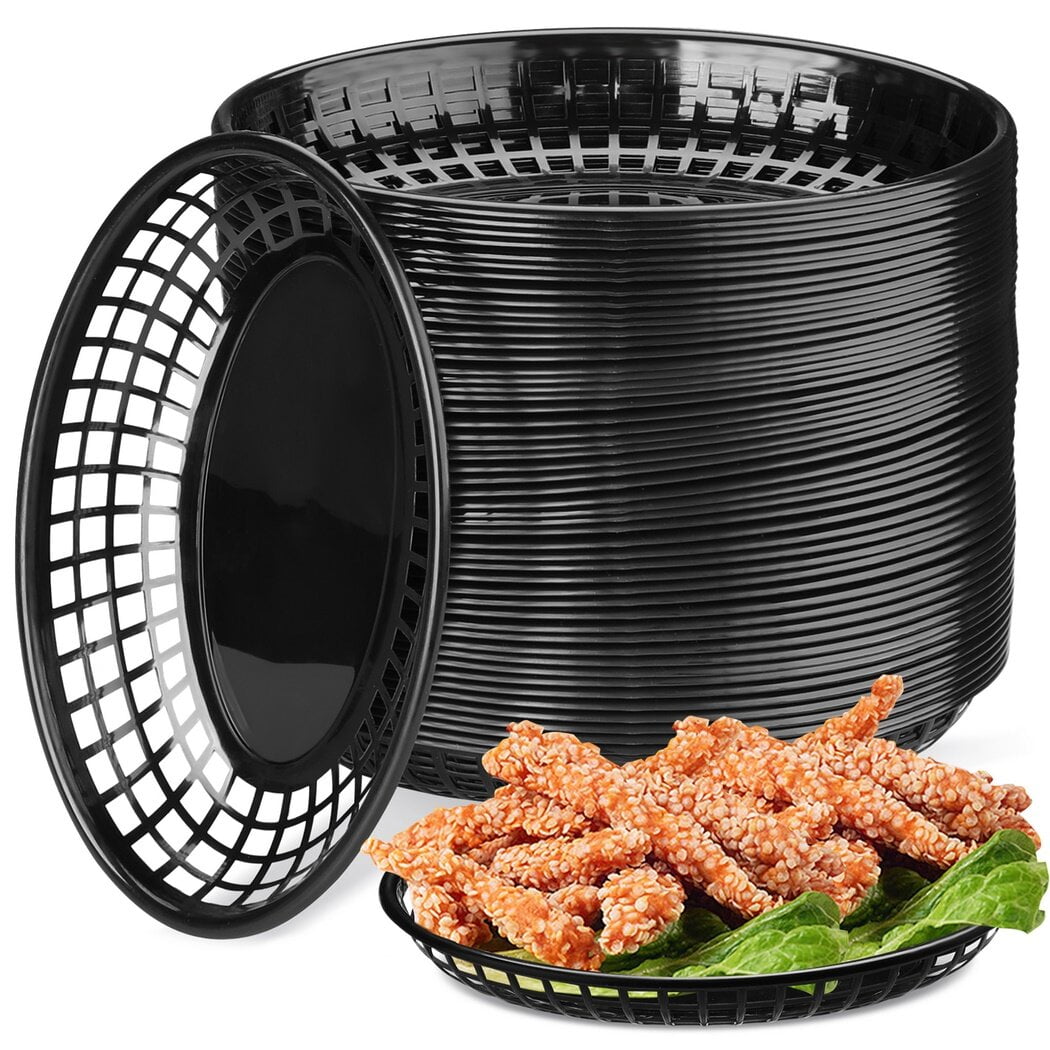
The journey of plastic food baskets, from creation to consumer use, is not a free-for-all. It’s a carefully orchestrated process, guided by a complex web of regulations and standards designed to safeguard public health and ensure product integrity. These guidelines dictate everything from the materials used to the manufacturing processes, guaranteeing that the baskets remain safe for food contact and minimize any potential risks.
Adherence to these regulations is not just a legal requirement; it’s a commitment to consumer trust and product excellence.
Food Safety Regulations for Plastic Food Baskets
Food safety regulations are the bedrock of the food industry, and plastic food baskets are no exception. These regulations aim to prevent contamination of food products and protect consumers from potential health hazards. Compliance is mandatory, and failure to adhere can lead to serious consequences, including product recalls, legal penalties, and damage to a company’s reputation.
- United States: The Food and Drug Administration (FDA) plays a pivotal role in regulating food contact materials, including plastic food baskets. The FDA’s primary regulation is 21 CFR (Code of Federal Regulations) Part 177, which Artikels the specific requirements for polymers used in food contact applications. This regulation covers a wide range of aspects, including the types of polymers that are permitted, the additives that can be used, and the migration limits for substances that could potentially leach into food.
For example, materials must be “Generally Recognized As Safe” (GRAS) or have FDA approval.
- European Union: The European Food Safety Authority (EFSA) sets the standards for food contact materials within the EU. Regulation (EC) No 1935/2004 is the framework regulation, establishing the general principles for all food contact materials. This is supplemented by specific regulations for plastics, such as Regulation (EU) No 10/2011, which details the requirements for plastic materials and articles intended to come into contact with food.
This regulation sets migration limits for substances that can migrate from the plastic into food and provides a positive list of authorized substances.
- Other Regions: Other countries and regions, such as Canada, Australia, and Japan, have their own food safety regulations that are generally aligned with international standards. These regulations often mirror the principles established by the FDA and EFSA, with variations in specific requirements and permitted substances. For example, Health Canada has regulations similar to the FDA, outlining acceptable materials and migration limits.
Standards for Food-Grade Plastics
Food-grade plastics are specially formulated to ensure they are safe for contact with food. These plastics must meet stringent requirements to prevent the migration of harmful substances into food, maintaining the integrity and safety of the food products.
- Material Purity: Food-grade plastics must be manufactured using high-purity raw materials. This means the materials must be free from contaminants and additives that could potentially leach into food. The purity of the materials is essential to prevent any adverse effects on human health.
- Migration Limits: The migration of substances from the plastic into food is a key concern. Regulations set specific migration limits for various substances, ensuring that the amount of any substance that can migrate into food is below a safe threshold. These limits are typically expressed in milligrams per kilogram of food (mg/kg).
- Additives: Only approved additives can be used in the manufacturing of food-grade plastics. These additives may include stabilizers, antioxidants, and colorants, which are carefully evaluated for their safety and compatibility with food. Additives are selected to enhance the plastic’s performance without compromising its safety.
- Manufacturing Processes: The manufacturing process itself must be controlled to prevent contamination. This includes using clean equipment, maintaining a hygienic environment, and implementing quality control measures throughout the production process. Stringent controls minimize the risk of contamination during manufacturing.
- Types of Food-Grade Plastics: Commonly used food-grade plastics include Polyethylene (PE), Polypropylene (PP), Polyethylene Terephthalate (PET), and Polycarbonate (PC). Each plastic has its own unique properties and applications, and the choice of plastic depends on the specific food product and its intended use.
Certifications and Testing Standards for Food Contact Materials
Certifications and testing standards provide independent verification that plastic food baskets meet the required food safety regulations. These certifications give consumers and businesses confidence in the safety and quality of the products.
- FDA Compliance: Manufacturers often seek FDA compliance letters or certifications to demonstrate that their products meet the FDA’s requirements. These documents confirm that the materials used in the basket are compliant with 21 CFR Part 177.
- EU Compliance (Declaration of Compliance): Under EU regulations, manufacturers must provide a Declaration of Compliance (DoC) for their food contact materials. This document confirms that the product complies with the relevant EU regulations, including Regulation (EC) No 1935/2004 and Regulation (EU) No 10/2011.
- Testing Laboratories: Independent testing laboratories, such as SGS, Intertek, and Eurofins, conduct migration testing and other analyses to verify the safety of food contact materials. These laboratories follow standardized testing methods to determine whether the materials meet the required migration limits.
- Testing Methods: Testing methods typically involve simulating the conditions of use, such as the type of food that will be in contact with the basket, the temperature, and the duration of contact. Samples of the plastic are exposed to food simulants, and the amount of any substances that migrate into the simulant is measured.
For example, the EN 1186 series of standards provides a comprehensive set of testing methods for food contact materials in Europe, covering various types of food simulants and test conditions.
- Certification Marks: Some organizations, such as NSF International, provide certification marks that can be displayed on food contact products. These marks indicate that the product has been tested and certified to meet specific safety and performance standards.
Design and Features
The artistry of a plastic food basket lies not just in its utility, but in its thoughtful design. It’s a silent language spoken through curves, textures, and the seamless integration of form and function. The features that define a superior basket go beyond mere aesthetics; they speak to the user experience, efficiency, and sustainability of the product. The design choices influence everything from ease of handling to storage optimization and contribute significantly to its overall value proposition.
Ergonomic Design Importance
Ergonomic design transforms a simple container into an extension of the user’s capabilities. It acknowledges the human form, understanding that the basket will be grasped, lifted, and carried, often under demanding circumstances. A well-designed basket reduces strain, enhances grip, and promotes safer handling practices, ultimately minimizing the risk of injury and boosting user satisfaction. This is particularly crucial in environments where the basket is used repeatedly and for extended periods.
Handle Designs and Benefits
Handle design is a cornerstone of a plastic food basket’s usability. Different handle configurations cater to diverse needs and preferences, each offering unique advantages:
- Integrated Handles: These handles are molded directly into the basket’s structure, creating a seamless and robust design. They offer a clean aesthetic and are often preferred for their durability, especially in heavy-duty applications. The design provides a secure grip, minimizing the chance of breakage under stress.
- Open Handles: Open handles, often rectangular or oval, are easy to grasp and allow for a comfortable grip, even with gloved hands. They offer good ventilation and are generally lighter than integrated handles, making them ideal for lighter loads and frequent handling.
- Folding Handles: Folding handles offer space-saving benefits, allowing the baskets to be stacked or nested more efficiently when not in use. This feature is especially valuable in environments with limited storage space. They can be designed to lock in place when in use, ensuring a secure grip.
- Contoured Handles: Contoured handles, designed to fit the natural curve of the hand, provide superior comfort during prolonged use. This design can reduce fatigue and increase grip security, which is particularly important when carrying heavier items.
Stackability and Nesting Capabilities
Stackability and nesting are vital features that maximize storage efficiency. These design elements are fundamental to streamlining logistics, minimizing storage space requirements, and reducing transportation costs.
- Stackable Baskets: Designed with a rim or lip that allows them to securely stack on top of each other, stackable baskets conserve valuable vertical space. This feature is particularly useful in warehouses, retail environments, and food processing facilities where space is at a premium. The design of the rim and the base of the basket ensures stability and prevents the baskets from sliding during transport.
- Nesting Baskets: Nesting baskets can be inserted inside each other when empty, drastically reducing the space they occupy. This feature is especially beneficial for return logistics and storage, minimizing the volume required for empty containers. The nesting design often incorporates a slight taper in the basket’s walls, allowing them to fit snugly within each other.
Example of a Plastic Food Basket:
Model: Pro-Harvest Basket
Dimensions: 600mm (L) x 400mm (W) x 300mm (H)
Features:
- Integrated, ergonomic handles for comfortable and secure grip.
- Stackable design with reinforced corners for stability.
- Perforated walls for optimal ventilation, crucial for preserving the freshness of produce.
- Made from food-grade polypropylene, ensuring safety and durability.
- Nestable design when empty, saving space during storage and return transport. The basket nests to approximately 20% of its original height.
Application: Ideal for harvesting, storing, and transporting fruits and vegetables in agricultural and distribution settings.
Purchasing and Sourcing
Embarking on the journey of sourcing plastic food baskets is akin to setting sail on a sea of possibilities. The right choice can streamline operations, enhance brand image, and contribute to a sustainable future. This section provides a compass and a map, guiding you through the crucial considerations, processes, and inquiries that will lead you to the perfect supplier for your needs.
Factors for Choosing a Supplier
Selecting a plastic food basket supplier is a strategic decision that warrants careful consideration. Several key factors can influence the success of this partnership.
- Quality and Safety Standards: Prioritize suppliers who adhere to stringent food-grade material standards, such as those set by the FDA (Food and Drug Administration) in the United States or the EFSA (European Food Safety Authority) in Europe. Request certifications and testing reports to verify compliance.
- Manufacturing Capabilities: Assess the supplier’s production capacity, technology, and expertise. Can they handle your order volume and meet your specific design requirements? Do they offer in-house tooling or rely on external vendors?
- Design and Customization Options: Determine if the supplier offers a range of standard basket designs or if they can accommodate custom designs. Explore their capabilities in terms of colors, sizes, branding, and features like handles or lids.
- Lead Times and Delivery: Inquire about the supplier’s lead times for production and delivery. Understand their logistics capabilities and shipping options to ensure timely and cost-effective delivery.
- Pricing and Payment Terms: Compare pricing models from different suppliers, considering factors like material costs, tooling costs, and order quantities. Negotiate payment terms and explore options for bulk discounts.
- Sustainability Practices: Evaluate the supplier’s commitment to sustainability. Do they use recycled materials, implement energy-efficient manufacturing processes, and offer options for basket recycling or disposal?
- Customer Service and Support: Choose a supplier with a responsive and reliable customer service team. They should be readily available to answer your questions, address any concerns, and provide ongoing support.
- Reputation and References: Research the supplier’s reputation in the industry. Request references from other clients to gain insights into their experience with the supplier.
Ordering Custom-Designed Baskets
Custom-designed plastic food baskets offer a unique opportunity to align packaging with specific brand identities and product requirements. The process involves several key steps, starting with a clear vision and ending with the final product.
- Define Your Requirements: Clearly articulate your needs, including the dimensions, shape, material, color, branding elements, and any specific features of the basket. Prepare detailed drawings or sketches.
- Contact Potential Suppliers: Reach out to several suppliers and share your design specifications. Request quotes and inquire about their design capabilities and expertise.
- Design Collaboration: Work closely with the chosen supplier’s design team to refine the design, ensuring it meets your requirements and is manufacturable. This may involve creating prototypes and making adjustments.
- Tooling and Prototyping: The supplier will create molds (tooling) to produce the baskets. They will then produce prototypes for your review and approval.
- Testing and Approval: Thoroughly test the prototypes to ensure they meet your quality standards, functionality requirements, and food safety regulations. Provide feedback and approve the final design.
- Production and Delivery: Once the design is approved, the supplier will begin mass production. They will manage the manufacturing process and arrange for delivery according to the agreed-upon schedule.
Questions to Ask Suppliers
Asking the right questions is crucial to evaluating potential suppliers and ensuring a successful partnership. Here are some essential questions to pose:
- What materials do you use for your food baskets, and what certifications do you have for food safety? This confirms compliance with food-grade standards.
- What is your production capacity, and what are your lead times for standard and custom orders? This ensures they can meet your volume and schedule requirements.
- What design options and customization services do you offer? This helps determine their ability to meet your specific design needs.
- What are your quality control procedures? This provides insight into their commitment to quality.
- What are your pricing models, and what payment terms do you offer? This allows for price comparison and negotiation.
- What are your sustainability practices? This aligns with environmental goals.
- Can you provide references from other clients? This validates their reputation and service.
- What are your warranty and return policies? This protects your investment.
- What are the shipping costs and options? This clarifies delivery logistics.
Pricing Models Comparison
Different plastic food basket suppliers employ varying pricing models. Understanding these models allows for a more informed comparison and helps in negotiating the best possible terms. The following table Artikels common pricing structures:
Pricing Model | Description | Advantages | Disadvantages |
---|---|---|---|
Cost-Plus Pricing | The supplier calculates the cost of materials, labor, and overhead, and then adds a profit margin. | Transparent pricing, easy to understand, potential for negotiation. | May not be the most competitive price, supplier has less incentive to control costs. |
Fixed-Price Pricing | The supplier provides a fixed price for a specific order quantity. | Predictable costs, simplifies budgeting, good for standard orders. | Less flexibility for changes, may not be suitable for complex or custom designs. |
Variable Pricing | The price fluctuates based on factors like material costs, order quantity, or design complexity. | Can be competitive, reflects market changes. | Less predictable costs, requires ongoing monitoring. |
Value-Based Pricing | The price is determined based on the perceived value of the product to the customer, considering factors like brand recognition, design features, and performance. | Potentially higher profit margins, rewards innovation and value-added services. | Requires strong marketing and branding, can be subjective. |
Maintenance and Care
The enduring utility of plastic food baskets hinges not only on their initial quality but also on the diligent care they receive throughout their lifespan. Proper maintenance is paramount, ensuring food safety, extending their service life, and optimizing their overall value. This section provides a comprehensive guide to nurturing and preserving these essential tools, safeguarding both their functionality and the well-being of those who utilize them.
Cleaning and Sanitizing Methods
Maintaining the highest standards of hygiene is crucial when handling food. Plastic food baskets, due to their frequent contact with various food items, require regular and thorough cleaning and sanitizing. Neglecting this can lead to bacterial growth and contamination, potentially posing health risks.To effectively clean and sanitize plastic food baskets, follow these steps:
- Rinse Thoroughly: Begin by rinsing the basket under running water to remove any loose food particles or debris. This initial step is vital for the effectiveness of subsequent cleaning.
- Wash with Soap and Water: Use a mild dish soap and warm water to wash the basket. Scrub all surfaces, including crevices and corners, to eliminate any remaining residue. Avoid abrasive cleaners or scrub brushes that can scratch the plastic.
- Rinse Again: Rinse the basket thoroughly with clean water to remove all traces of soap. Soap residue can affect the taste and safety of food.
- Sanitize: Sanitize the basket using a food-safe sanitizer solution. Follow the manufacturer’s instructions for the specific sanitizer, including dilution ratios and contact time. Common sanitizing agents include:
- Chlorine-based sanitizers: Effective and widely available, but require careful handling and rinsing to remove any residual chlorine odor or taste. The typical concentration is 50-100 ppm (parts per million).
- Quaternary ammonium sanitizers (Quats): These are effective and generally odorless, but require careful rinsing.
- Hot water sanitization: For baskets that can withstand high temperatures, immersion in hot water (at least 170°F or 77°C) for a specified time can be an effective sanitizing method. Ensure the plastic material is suitable for high temperatures.
- Air Dry: Allow the basket to air dry completely. This prevents the growth of mold or bacteria. Avoid using cloths or towels, which can re-contaminate the surface.
Extending the Lifespan
Prolonging the life of plastic food baskets not only reduces replacement costs but also contributes to environmental sustainability by minimizing waste. Careful handling, storage, and adherence to proper usage guidelines are key to achieving this.To extend the lifespan of plastic food baskets:
- Avoid Overloading: Do not exceed the basket’s weight capacity. Overloading can cause the plastic to warp, crack, or break.
- Protect from Extreme Temperatures: Avoid exposing the baskets to extreme heat or cold. High temperatures can cause the plastic to soften and deform, while extreme cold can make it brittle and prone to cracking. For instance, direct sunlight or placement near heat sources (ovens, heaters) should be avoided.
- Handle with Care: Avoid dropping or mishandling the baskets. Impacts can cause cracks or fractures, especially at the corners or edges.
- Use Appropriate Cleaning Agents: Use only mild detergents and avoid harsh chemicals, abrasive cleaners, or solvents, which can damage the plastic.
- Inspect Regularly: Regularly inspect the baskets for signs of wear and tear, such as cracks, chips, or discoloration. Address any issues promptly to prevent further damage.
- Proper Storage: Store the baskets correctly to prevent damage, as detailed below.
Common Issues and Solutions
Plastic food baskets, like any frequently used item, are susceptible to various issues that can compromise their functionality and appearance. Identifying and addressing these problems promptly is essential to maintain their usability and longevity.Common problems and their solutions include:
- Cracking or Breaking: This can result from overloading, impacts, or exposure to extreme temperatures.
- Solution: Discard baskets with significant cracks or breaks. Minor cracks can sometimes be repaired with food-grade epoxy, but this is often a temporary solution.
- Discoloration: Staining can occur from prolonged contact with certain foods or cleaning agents.
- Solution: Clean the basket promptly after use. Baking soda paste can help remove some stains. Consider replacing baskets that are heavily discolored.
- Warping: Exposure to heat can cause the plastic to warp.
- Solution: Avoid exposing baskets to heat sources. If warping is minor, it might not affect usability. However, severely warped baskets should be replaced.
- Scratching: Abrasive cleaners or rough handling can scratch the surface of the plastic.
- Solution: Use soft cloths or sponges and avoid abrasive cleaners. While scratches may not affect functionality, they can harbor bacteria.
- Odor Retention: Certain foods can leave lingering odors in the plastic.
- Solution: Wash the basket thoroughly and try soaking it in a solution of baking soda and water. In some cases, replacing the basket may be necessary.
Storing Plastic Food Baskets
Proper storage is a critical aspect of maintaining the integrity and extending the lifespan of plastic food baskets. Thoughtful storage prevents damage from environmental factors, physical impacts, and ensures their readiness for immediate use.To store plastic food baskets effectively:
- Clean and Dry Thoroughly: Always ensure the baskets are clean and completely dry before storing them. This prevents mold and bacterial growth.
- Stack Neatly: Stack the baskets in a neat and organized manner to save space and prevent damage. If the baskets are designed for nesting, utilize this feature to maximize storage efficiency.
- Store in a Cool, Dry Place: Avoid storing the baskets in areas with extreme temperatures or humidity. A cool, dry environment will help prevent warping, cracking, and the growth of mold or mildew.
- Protect from Direct Sunlight: Direct sunlight can degrade the plastic over time, causing discoloration and brittleness. Store the baskets away from direct sunlight.
- Avoid Heavy Objects: Do not place heavy objects on top of the stacked baskets, as this can cause them to deform or break.
- Regular Inspection: Periodically inspect the stored baskets for any signs of damage or wear. This allows for prompt attention to any issues before they worsen.
Closure
So, there you have it – a whirlwind tour of the amazing plastic food basket! From farm to table, from harvest to home, these often-overlooked workhorses are essential to keeping our food safe, organized, and ready to eat. They’re durable, reusable, and surprisingly eco-friendly (if handled right). Hopefully, this deep dive has given you a newfound appreciation for these plastic powerhouses.
Now, go forth and conquer your food storage challenges, one basket at a time!