Foam trays for food – Ayo, kita ngomongin soal
-foam trays for food*, wadah makanan yang udah kayak sahabat setia abang-abang nasi uduk sampe restoran bintang lima! Dulu, mah, cuma bungkus nasi uduk, sekarang udah macem-macem, dari ayam geprek sampe steak wagyu. Tapi, emang beneran aman, nih, buat makanan kite? Yuk, kita kulik lebih dalem!
Kita mulai dari sejarahnya, deh. Dulu, mah, plastik nggak se-ngetren sekarang, jadi foam trays ini kayak penyelamat. Trus, kita bahas juga bahan bakunya, cara bikinnya, sampe dampaknya buat lingkungan. Jangan lupa, kita juga bakal ngomongin jenis-jenisnya, dari yang kotak, bulet, sampe yang khusus buat sate kambing. Pokoknya, lengkap dah!
Introduction to Foam Trays for Food
Foam trays have become a ubiquitous presence in the food industry, offering a convenient and cost-effective solution for packaging and presenting a wide array of food products. From fresh meats and produce to prepared meals and bakery items, these trays play a crucial role in maintaining food quality, extending shelf life, and facilitating efficient handling and transportation. Their widespread adoption reflects their versatility and ability to meet the diverse needs of both food producers and consumers.
History of Foam Trays in the Food Industry
The advent of foam trays can be traced back to the mid-20th century, coinciding with advancements in polymer chemistry and manufacturing processes. The development of expanded polystyrene (EPS) foam provided a lightweight, insulating, and moisture-resistant material ideal for food packaging. The initial applications focused on protecting and preserving perishable items, particularly in the meat and poultry sectors. Over time, the use of foam trays expanded to encompass a broader range of food products, driven by factors such as cost-effectiveness, ease of use, and the growing demand for convenient food packaging solutions.
Primary Applications of Foam Trays Across Different Food Sectors
Foam trays find extensive application across various segments of the food industry, serving diverse packaging needs. Their adaptability makes them suitable for a wide range of food products.
- Meat and Poultry: Foam trays are widely used for packaging fresh meat, poultry, and seafood. Their insulating properties help maintain a consistent temperature, reducing spoilage and preserving the product’s quality. The trays also absorb excess fluids, further enhancing freshness and extending shelf life. For example, a study by the University of California, Davis, found that using foam trays in combination with modified atmosphere packaging (MAP) could extend the shelf life of fresh beef by up to 50%.
- Produce: Foam trays are used to package fruits and vegetables, providing cushioning and protection against bruising during handling and transportation. They also help to regulate moisture levels, preventing the produce from drying out or becoming soggy. For example, foam trays are commonly used to package berries, such as strawberries and blueberries, to prevent them from being crushed or damaged.
- Prepared Foods: Foam trays are utilized for packaging ready-to-eat meals, deli items, and bakery products. Their lightweight nature and ease of handling make them ideal for these applications. The trays can be easily sealed with film to maintain freshness and prevent leaks. For instance, many supermarkets use foam trays to package salads, sandwiches, and other prepared food items.
- Dairy Products: Some dairy products, such as cheese slices and butter portions, are packaged on foam trays to maintain their shape and prevent them from sticking together. The trays provide a barrier against moisture and help to preserve the product’s quality.
Advantages of Using Foam Trays
Foam trays offer a number of significant advantages that contribute to their widespread use in the food industry. These advantages are a major factor in their sustained popularity.
- Cost-Effectiveness: Foam trays are generally inexpensive to manufacture, making them an economically attractive option for food packaging. The low cost of production translates into lower overall packaging costs for food producers.
- Lightweight: The lightweight nature of foam trays reduces transportation costs and makes them easy to handle and store. This is particularly beneficial for large-scale food distribution operations.
- Insulation: Foam trays provide good insulation, helping to maintain the temperature of food products and extend their shelf life. This is especially important for perishable items such as meat, poultry, and seafood.
- Moisture Resistance: Foam trays are resistant to moisture, preventing leaks and spills. This helps to maintain the integrity of the food product and prevent spoilage.
- Versatility: Foam trays can be manufactured in a variety of shapes and sizes to accommodate different food products. They can also be easily customized with labels and branding.
- Availability: Foam trays are widely available, making them readily accessible to food producers and retailers. This ensures a consistent supply of packaging materials.
Disadvantages of Using Foam Trays
Despite their numerous advantages, foam trays also have certain disadvantages that must be considered. These disadvantages are a key factor in the ongoing search for alternative packaging solutions.
- Environmental Concerns: Foam trays are typically made from expanded polystyrene (EPS), a non-biodegradable material that can persist in the environment for many years. This contributes to landfill waste and can pose a threat to wildlife.
- Recycling Challenges: Recycling EPS foam can be challenging due to its low density and the presence of food residue. Specialized recycling facilities are often required, and the recycling rate for foam trays remains relatively low.
- Limited Biodegradability: While some biodegradable foam alternatives exist, they are often more expensive than traditional EPS foam. The biodegradability of these alternatives can also vary depending on the composting conditions.
- Potential for Food Contamination: Although generally considered safe, there have been concerns about the potential for chemicals in foam trays to leach into food, especially when exposed to high temperatures or acidic foods. However, regulatory standards are in place to minimize this risk.
- Public Perception: Foam trays have a negative public perception due to their environmental impact. This can lead to consumer pressure on food producers to switch to more sustainable packaging alternatives.
Materials and Manufacturing
Foam trays for food are ubiquitous in the food industry, serving essential roles in packaging, preservation, and transportation. Understanding the materials and manufacturing processes behind these trays is crucial for evaluating their functionality, cost-effectiveness, and environmental impact. This section will delve into the specific materials used, the manufacturing methods employed, and the comparative environmental considerations of different material choices.
Materials Used in Production
The materials used in foam tray production are primarily various types of plastics, chosen for their lightweight properties, insulation capabilities, and cost-effectiveness. These materials are often modified or combined to achieve specific performance characteristics.
- Expanded Polystyrene (EPS): This is the most common material used in foam tray production. EPS is a lightweight, closed-cell foam made from polystyrene beads. It is known for its excellent insulation properties, making it suitable for keeping food items at a stable temperature. EPS is relatively inexpensive and can be easily molded into various shapes. However, it is not biodegradable and poses environmental challenges due to its slow decomposition rate and contribution to landfill waste.
- Expanded Polypropylene (EPP): EPP is another type of foam used, particularly in applications requiring greater durability and resilience. It offers better impact resistance and can withstand higher temperatures compared to EPS. EPP is also recyclable, offering a more environmentally friendly option. EPP trays are often used for hot food items and applications where the tray needs to withstand some physical stress during handling and transport.
- Polyethylene Terephthalate (PET): While not a foam in the same way as EPS or EPP, PET is often used in combination with foam trays or as a component in laminated structures. PET is a clear, strong, and recyclable plastic that provides a barrier against moisture and gases, thus extending the shelf life of food products. It can be used as a top layer to provide a smooth, printable surface or to enhance the overall rigidity of the tray.
- Biodegradable Materials: The growing concern for environmental sustainability has led to the development of foam trays made from biodegradable materials. These materials include:
- Polylactic Acid (PLA): PLA is a bioplastic derived from renewable resources such as corn starch or sugarcane. It is biodegradable under specific composting conditions. PLA trays offer a more sustainable alternative to traditional plastic foams but can be more expensive and may have limitations in terms of heat resistance and moisture barrier properties.
- Cellulose-based foams: These foams are made from plant-based cellulose, offering biodegradability and compostability. Research and development are ongoing to improve their performance characteristics and reduce production costs.
Manufacturing Processes
The manufacturing of foam trays involves several key processes, depending on the material used. These processes are designed to efficiently produce large quantities of trays while maintaining consistent quality.
- EPS Manufacturing: The process typically starts with the pre-expansion of polystyrene beads using steam. This process increases the volume of the beads. The pre-expanded beads are then placed into molds, where they are further expanded using steam and fused together to form the desired tray shape. The molded trays are then cooled, trimmed, and inspected for quality.
- EPP Manufacturing: EPP trays are often produced through a molding process similar to EPS, but the material properties require different parameters. The raw EPP material, in the form of beads, is injected into a mold and expanded using steam. The high impact resistance of EPP makes it suitable for more complex designs and thicker trays.
- Thermoforming (for PET and other plastics): Thermoforming is a process used to shape plastic sheets into trays. A plastic sheet is heated until it becomes pliable, then it is formed over a mold using vacuum or pressure. The formed tray is then cooled and trimmed. This process is often used to create trays with a clear or colored surface, often laminated with foam.
- Extrusion and Lamination: Some foam trays are produced by extruding a foam core and then laminating it with other materials, such as PET, to improve the surface properties and barrier characteristics. This process allows for combining different materials to optimize the performance of the tray.
Environmental Impact Comparison
The environmental impact of foam trays varies significantly depending on the materials used and the end-of-life options available. This section will examine the comparative environmental impacts of different materials, including factors such as resource consumption, waste generation, and recyclability.
- EPS: EPS trays have a significant environmental impact due to their non-biodegradability and low recycling rates. They contribute to landfill waste and can persist in the environment for hundreds of years. The production of EPS also relies on fossil fuels. Efforts to reduce EPS waste include promoting the use of reusable alternatives, encouraging recycling programs, and exploring composting options, although these are limited.
- EPP: EPP offers an improvement over EPS due to its recyclability and greater durability. While EPP still relies on fossil fuels, the ability to recycle EPP reduces its contribution to landfill waste. Recycled EPP can be used in various applications, reducing the demand for virgin materials.
- PET: PET is highly recyclable, and the use of recycled PET (rPET) in foam trays significantly reduces the environmental impact compared to virgin PET. PET also offers a good barrier against moisture and gases, extending the shelf life of food products and potentially reducing food waste.
- Biodegradable Materials (PLA, Cellulose): Biodegradable materials offer the most promising solutions for reducing the environmental impact of foam trays. PLA, derived from renewable resources, can biodegrade under specific composting conditions, reducing landfill waste. Cellulose-based foams are also biodegradable and compostable. However, the widespread adoption of biodegradable trays depends on factors such as cost, performance characteristics, and the availability of composting infrastructure. The challenge lies in creating a closed-loop system where these trays can be effectively composted and the resulting compost used to grow more resources.
Types and Variations
Foam trays for food products are manufactured in a wide variety of shapes, sizes, and specialized designs to meet the diverse needs of the food industry. This variety ensures that different food items, from fresh produce to prepared meals, can be packaged securely and efficiently. The selection of the correct tray type is crucial for maintaining food quality, extending shelf life, and enhancing product presentation.
Shapes and Sizes of Foam Trays
Foam trays are available in a spectrum of dimensions to accommodate various food volumes and packaging requirements. These trays are designed to optimize space utilization during storage, transportation, and display.
- Rectangular Trays: These are the most common and versatile type, suitable for a broad range of products such as meat, poultry, and vegetables. They come in various depths and widths to fit different portion sizes and product dimensions.
- Square Trays: Often used for portioned foods or items that benefit from a compact presentation. They are ideal for items like cheese slices, pre-cut fruits, and small pastries.
- Oval and Round Trays: These are less common but suitable for specific applications, such as presenting deli meats or round-shaped items. They can enhance the visual appeal of the packaged food.
- Custom Shapes: Manufacturers can create custom-shaped trays to fit specific food items with unique geometries. This is particularly useful for products with irregular shapes or those that require a specific presentation, such as seafood or specialty baked goods.
Specialized Foam Trays
Specialized foam trays are designed with specific features to address the unique needs of different food products. These designs enhance the functional benefits of the tray, such as extending shelf life and improving product presentation.
- Absorbent Trays: These trays incorporate an absorbent pad at the bottom to capture excess fluids, primarily used for fresh meat and seafood. This feature helps to maintain the food’s appearance and prevent spoilage by keeping the product dry.
- Compartmentalized Trays: These trays feature multiple compartments, ideal for packaging meal kits, ready-to-eat meals, or items that need to be separated, such as fruits and dips. This design prevents mixing of ingredients and preserves the integrity of each component.
- Deep Trays: Designed to accommodate larger portions or products that have a significant height, these trays are suitable for packaging items like roasted chickens or large cuts of meat.
- Modified Atmosphere Packaging (MAP) Trays: These trays are designed to work with MAP technology, where the air inside the package is modified to extend shelf life. The trays often have a gas barrier property and are sealed with a specific film to maintain the modified atmosphere.
Foam Tray Types, Food Applications, and Key Features
The following table summarizes the different types of foam trays, their common food applications, and key features. This table serves as a quick reference guide for selecting the appropriate tray for a specific food product.
Tray Type | Food Applications | Key Features |
---|---|---|
Rectangular | Meat, poultry, vegetables, fruits | Versatile, various sizes, cost-effective |
Square | Cheese slices, pre-cut fruits, pastries | Compact, ideal for portioned foods, space-saving |
Oval/Round | Deli meats, round-shaped items | Enhances visual appeal, specific applications |
Absorbent | Fresh meat, seafood | Absorbent pad, keeps product dry, extends shelf life |
Compartmentalized | Meal kits, ready-to-eat meals, fruits with dips | Multiple compartments, prevents mixing, preserves integrity |
Deep | Roasted chickens, large cuts of meat | Accommodates larger portions, suitable for tall products |
MAP Trays | Fresh produce, processed meats, ready meals | Gas barrier, compatible with MAP technology, extended shelf life |
Custom Shapes | Seafood, specialty baked goods, products with irregular shapes | Tailored to specific product dimensions, enhances presentation |
Food Safety and Hygiene
Foam trays, while offering convenience and protection for food, necessitate stringent adherence to food safety and hygiene protocols. These measures are crucial to prevent contamination, safeguard consumer health, and maintain the integrity of the food supply chain. Understanding and implementing these practices is paramount for businesses utilizing foam trays.
Food Safety Regulations
Regulations governing the use of foam trays in food packaging are primarily focused on ensuring that the trays do not introduce harmful substances into the food. These regulations vary by region and country but generally address the following key aspects.
- Material Composition and Migration: Regulations specify the types of materials permitted for food contact and set limits on the migration of chemicals from the tray into the food. These limits are determined through rigorous testing and analysis to ensure consumer safety. For example, the U.S. Food and Drug Administration (FDA) has specific regulations for materials used in food packaging, including foam trays.
- Manufacturing Processes: Regulations often dictate acceptable manufacturing processes to minimize the risk of contamination during production. This includes requirements for cleanliness, hygiene, and quality control measures within the manufacturing facility.
- Testing and Certification: Manufacturers are typically required to conduct regular testing to demonstrate compliance with food safety standards. Certifications from recognized organizations, such as the FDA or the European Food Safety Authority (EFSA), are often necessary to verify that the trays meet the required safety standards.
- Labeling and Information: Regulations often require clear labeling on foam trays to indicate the materials used, any potential limitations (e.g., not suitable for microwave use), and manufacturer information. This information helps consumers and food handlers use the trays safely.
Proper Handling and Storage
The proper handling and storage of foam trays are essential to prevent contamination and maintain their integrity. Following these guidelines minimizes the risk of introducing hazards.
- Storage Conditions: Foam trays should be stored in a clean, dry, and well-ventilated area, away from potential sources of contamination such as pests, chemicals, and dust. Direct sunlight and extreme temperatures should be avoided, as they can degrade the tray material.
- Handling Procedures: Food handlers should always wash their hands thoroughly before handling foam trays and should use clean utensils and equipment to transfer food. Trays should be handled carefully to avoid damage, which could create openings for contamination.
- Protection from Contamination: Foam trays should be protected from contact with raw foods, particularly those that may contain pathogens. Separate storage areas and handling procedures should be used for raw and cooked foods.
- Inspection and Quality Control: Regular inspection of foam trays for any signs of damage, contamination, or degradation is essential. Trays that are damaged or contaminated should be discarded immediately.
Potential Contamination Risks and Mitigation Strategies
Foam trays, like any food packaging material, can present potential contamination risks. Implementing effective mitigation strategies is vital to minimizing these risks.
- Cross-Contamination: Cross-contamination can occur when microorganisms or other contaminants are transferred from one food item or surface to another.
- Mitigation: Use separate trays and utensils for raw and cooked foods. Ensure thorough cleaning and sanitization of all surfaces and equipment.
- Chemical Contamination: Chemical contamination can arise from the migration of chemicals from the foam tray into the food, especially if the tray is not designed for the specific food type or if it is exposed to extreme temperatures.
- Mitigation: Use only food-grade foam trays that are approved for the intended food type. Avoid using trays in the microwave unless specifically designed for microwave use.
Follow the manufacturer’s instructions for safe use.
- Mitigation: Use only food-grade foam trays that are approved for the intended food type. Avoid using trays in the microwave unless specifically designed for microwave use.
- Physical Contamination: Physical contamination can occur if fragments of the foam tray break off and enter the food.
- Mitigation: Handle trays carefully to avoid damage. Regularly inspect trays for any signs of degradation or breakage. Discard damaged trays immediately.
- Biological Contamination: Biological contamination, involving microorganisms like bacteria, viruses, or molds, can occur if the trays are not stored or handled properly.
- Mitigation: Store trays in a clean, dry, and pest-free environment. Ensure that food handlers practice good hygiene, including frequent handwashing. Use food-safe sanitizers to clean surfaces that come into contact with the trays.
Example: A restaurant chain that implemented strict hygiene protocols, including the use of dedicated trays and utensils for raw and cooked meats, experienced a significant reduction in foodborne illness incidents. This case highlights the effectiveness of mitigation strategies in preventing cross-contamination.
Packaging and Presentation
Foam trays play a significant role in the presentation and packaging of food products. Their design, coupled with various sealing and display techniques, directly impacts consumer perception and the overall appeal of the food items. Effective packaging not only protects the food but also enhances its visual attractiveness, influencing purchasing decisions and contributing to brand image.
Enhancing Food Presentation with Foam Trays
Foam trays offer several advantages in enhancing food presentation. Their versatility in terms of shape and color allows for creative arrangements and visual appeal.
- Color Contrast and Food Appeal: The neutral color of many foam trays, typically white or light grey, provides a clean backdrop that allows the natural colors of the food to stand out. This contrast is particularly effective for displaying fresh produce, meats, and prepared meals, making them more visually appealing to consumers.
- Shape and Arrangement: Foam trays can be molded into various shapes, accommodating different food items and portion sizes. This flexibility enables businesses to create attractive food arrangements, such as carefully placed sushi pieces or neatly arranged slices of deli meat.
- Compartmentalization: Trays with multiple compartments are available, which allows for the separation of different food components in a meal, preventing cross-contamination of flavors and maintaining visual organization. For example, a meal tray might separate a main course, side dish, and sauce.
- Surface for Labeling and Branding: The flat surface of foam trays provides ample space for labels, branding, and nutritional information. This allows businesses to clearly communicate essential information to consumers, enhancing brand recognition and trust.
Sealing and Packaging Methods for Foam Trays
Various sealing and packaging methods are employed to ensure the freshness, safety, and convenience of food packaged in foam trays. These methods vary depending on the food type, shelf life requirements, and distribution methods.
- Stretch Film Wrapping: This is a common and cost-effective method. The tray is covered with a thin, transparent plastic film that stretches tightly around the food. This provides a barrier against air and moisture, extending shelf life and preventing leakage. The film can be applied manually or using automated machinery.
- Heat Sealing: Heat sealing involves using a heat-sealing machine to bond a film or a lid to the tray. This creates an airtight seal, offering superior protection against contamination and extending the shelf life of perishable foods. Heat-sealed trays are often used for prepared meals, ready-to-eat salads, and other items requiring a longer shelf life.
- Modified Atmosphere Packaging (MAP): MAP involves altering the composition of the air within the tray to slow down the spoilage process. This is typically achieved by flushing the tray with a gas mixture, such as a combination of carbon dioxide, nitrogen, and oxygen. MAP is particularly effective for extending the shelf life of fresh produce, meats, and seafood.
- Lid Applications: Foam trays can be sealed with various types of lids, including snap-on lids and peel-and-seal lids. Snap-on lids provide a secure closure and are often used for items that are consumed quickly. Peel-and-seal lids offer a tamper-evident seal and are suitable for products that require a longer shelf life or require the consumer to easily open and reseal the package.
Visual Description: Foam Tray Display
A visual representation of a foam tray display could showcase the versatility and appeal of foam tray packaging. This description Artikels the elements of such a display:
Overall Scene: The display is set up on a clean, well-lit countertop, possibly in a supermarket or a deli section. The lighting is bright and evenly distributed to highlight the food items.
Tray Arrangement: Several foam trays of varying sizes and shapes are arranged to create a visually appealing presentation. Some trays are rectangular, others are square, and some have multiple compartments. The trays are arranged in a staggered fashion, with some items placed at different heights to add visual interest. The foam trays themselves are white or light grey to provide a neutral background for the food items.
Food Items Displayed:
- Tray 1: A rectangular tray containing sliced deli meats, such as ham, turkey, and salami. The meats are arranged in an overlapping pattern, showcasing their different colors and textures. A small sprig of fresh parsley is placed on top for garnish. The tray is wrapped with clear stretch film.
- Tray 2: A square tray with three compartments, containing a prepared meal. One compartment holds a portion of grilled chicken, another contains a side of roasted vegetables (e.g., broccoli, carrots), and the third compartment holds a small portion of sauce. The tray is heat-sealed with a clear film.
- Tray 3: A multi-compartment tray containing a variety of sushi pieces. The sushi is arranged artfully, showcasing the different colors and textures of the ingredients. A small container of soy sauce and wasabi are placed alongside the sushi. The tray is sealed with a clear, snap-on lid.
- Tray 4: A tray of fresh strawberries. The bright red berries are arranged in a single layer. The tray is covered with a transparent, breathable film to allow for airflow and prevent condensation.
Additional Elements:
- Labels and Signage: Each tray features a clear label with the product name, price, and any relevant nutritional information. A larger sign above the display advertises the variety of products available and any special promotions.
- Accessories: Small serving utensils, such as tongs or forks, are placed near the display to encourage customers to sample the products.
Overall Impression: The display is designed to be inviting and appealing, showcasing the freshness, quality, and convenience of the food items. The use of foam trays enhances the visual presentation, making the products more attractive to consumers and encouraging purchases.
Cost and Economics
The economic viability of foam trays is a crucial consideration for food businesses. This section delves into the cost-effectiveness of foam trays, comparing them to alternatives, outlining the factors influencing their price, and providing a glimpse into supplier pricing structures. Understanding these aspects is essential for making informed packaging decisions that balance cost, functionality, and consumer appeal.
Cost-Effectiveness of Foam Trays Versus Alternative Packaging Options
Foam trays often present a compelling cost advantage compared to other packaging materials, particularly for single-use applications. However, the overall cost-effectiveness depends on various factors, including the type of food, storage requirements, and environmental considerations.
- Cost Advantages: Foam trays are typically less expensive to produce than alternatives like molded pulp, cardboard, or rigid plastics. This lower initial cost can significantly impact the bottom line, especially for high-volume food packaging.
- Material Efficiency: The manufacturing process for foam trays utilizes materials efficiently, often resulting in less waste compared to other packaging methods. This can contribute to lower material costs.
- Weight and Transportation: The lightweight nature of foam trays reduces shipping costs, as less fuel is required to transport the packaged food. This is a crucial factor in long-distance distribution.
- Comparison with Alternatives:
- Molded Pulp: While molded pulp is often perceived as more environmentally friendly, its higher production costs can make it less competitive than foam for certain applications.
- Cardboard: Cardboard boxes offer good structural integrity but may require additional liners to prevent leaks and maintain food freshness, increasing overall costs.
- Rigid Plastics: Rigid plastic containers offer superior protection and reusability, but their higher material costs and potential environmental concerns (depending on the plastic type) can make them less economical for single-use applications.
- Environmental Considerations: The environmental impact of foam trays, primarily due to their non-biodegradable nature, is a significant concern. This can indirectly affect cost-effectiveness if businesses face pressure to adopt more sustainable packaging options, potentially increasing expenses in the long run.
Factors That Influence the Price of Foam Trays
Several key factors influence the final price of foam trays. Understanding these variables allows businesses to optimize their purchasing decisions and potentially negotiate better prices.
- Raw Material Costs: The price of polystyrene (the primary material used in foam tray production) is a significant driver of overall cost. Fluctuations in the price of crude oil, from which polystyrene is derived, directly impact the cost of foam trays.
- Tray Size and Design: Larger trays and those with complex designs require more material and more intricate manufacturing processes, increasing their cost. Customization options also contribute to higher prices.
- Production Volume: Higher production volumes typically result in lower per-unit costs due to economies of scale. Manufacturers often offer volume discounts to incentivize larger orders.
- Manufacturing Process: The efficiency and sophistication of the manufacturing process affect production costs. Automation and advanced technologies can help reduce labor costs and improve material utilization, leading to lower prices.
- Supplier and Location: The geographic location of the supplier and the competitive landscape in that region influence pricing. Shipping costs also vary depending on the supplier’s location relative to the customer.
- Additional Features: Trays with added features, such as absorbent pads or anti-fog coatings, will have a higher cost compared to standard trays.
- Regulations and Taxes: Government regulations, such as taxes on polystyrene products, can affect the final price of foam trays.
Suppliers and General Pricing Tiers for Different Tray Sizes
Pricing for foam trays varies considerably between suppliers and is often influenced by order volume, tray size, and customization options. While specific pricing is subject to change, general pricing tiers can be identified to provide a baseline understanding.
- Supplier Examples (Note: Actual pricing requires direct contact with suppliers):
- Large-Scale Manufacturers: Companies like Dart Container Corporation and Pactiv Evergreen are major players, offering a wide range of standard and custom tray options. They often cater to large-volume customers and can offer competitive pricing for bulk orders.
- Regional Suppliers: Numerous regional suppliers provide foam trays, potentially offering more personalized service and competitive pricing for smaller and medium-sized businesses.
- Online Marketplaces: Online platforms such as Alibaba or Amazon offer various foam tray options from different suppliers, allowing for price comparison and convenient purchasing. However, it is crucial to verify supplier reliability and product quality.
- General Pricing Tiers (Illustrative Examples):
- Small Trays (e.g., for individual portions of meat or produce): Prices can range from $0.02 to $0.05 per tray, depending on the volume purchased and features.
- Medium Trays (e.g., for larger portions of meat or multiple servings of vegetables): Prices might fall between $0.04 and $0.10 per tray.
- Large Trays (e.g., for family-sized portions or catering applications): These can range from $0.08 to $0.20 per tray or more, depending on size, thickness, and any special features.
- Pricing Considerations:
- Minimum Order Quantities (MOQs): Suppliers typically have MOQs, and prices are often significantly lower when orders meet or exceed these thresholds.
- Customization: Custom trays with specific shapes, sizes, or printing options will incur additional costs.
- Negotiation: Businesses should negotiate with suppliers, especially for large orders, to secure the best possible pricing.
Environmental Concerns and Alternatives: Foam Trays For Food
Foam trays, while offering convenience and protection for food products, present significant environmental challenges. These concerns have spurred the development and adoption of various alternative packaging solutions. Understanding these environmental impacts and exploring the available alternatives is crucial for making informed decisions about food packaging.
Environmental Concerns of Foam Tray Disposal
The environmental impact of foam trays stems primarily from their composition and disposal methods. Expanded polystyrene (EPS), the material commonly used in foam tray production, is a petroleum-based plastic that is not readily biodegradable.
- Non-Biodegradability: EPS is extremely slow to decompose in landfills, persisting for hundreds of years. This contributes to the growing problem of landfill space scarcity.
- Landfill Burden: The volume of EPS waste adds significantly to landfill accumulation. Its lightweight nature allows it to take up considerable space relative to its weight.
- Recycling Challenges: Recycling EPS is often difficult and economically unviable. While technically recyclable, the process requires specialized equipment and facilities, which are not widely available. Contamination with food residue further complicates recycling efforts.
- Marine Pollution: Discarded EPS can easily enter waterways and oceans, breaking down into microplastics. These microplastics pose a threat to marine life through ingestion and entanglement.
- Greenhouse Gas Emissions: The production of EPS requires significant energy and releases greenhouse gases, contributing to climate change. Furthermore, the transportation of bulky EPS waste adds to carbon emissions.
- Chemical Leaching: While rare under normal circumstances, some studies suggest that EPS can leach harmful chemicals into the environment over extended periods. This can pose a threat to soil and water quality.
Biodegradable and Compostable Alternatives to Foam Trays
Driven by environmental concerns, the food packaging industry has seen a rise in biodegradable and compostable alternatives to traditional foam trays. These materials offer a more sustainable option by breaking down naturally, reducing landfill waste and minimizing environmental impact.
These alternatives are generally derived from renewable resources, such as plants, and are designed to decompose in specific environments, either in industrial composting facilities or, in some cases, in home composting systems. The choice of material depends on factors such as the type of food being packaged, the desired shelf life, and the availability of composting facilities.
- Paper-Based Trays: These trays are often made from recycled paper or sustainably sourced paperboard. They can be coated with a biodegradable wax or polymer for moisture resistance. Paper trays are widely compostable and offer a good balance of performance and sustainability.
- Molded Pulp Trays: These trays are made from recycled paper pulp or agricultural byproducts like sugarcane bagasse. They are compostable and offer good cushioning and insulation properties. They are suitable for a variety of food items, particularly fruits and vegetables.
- PLA (Polylactic Acid) Trays: PLA is a bioplastic derived from renewable resources such as corn starch or sugarcane. PLA trays are compostable under industrial composting conditions. They offer good clarity and can be used for a wide range of food products. However, they are not suitable for high-temperature applications.
- Starch-Based Trays: These trays are made from starch derived from corn, potatoes, or other plants. They are compostable and can offer good moisture resistance. They are typically used for dry food items or for packaging that requires a short shelf life.
- Mushroom Packaging: This innovative material is made from mycelium (the root structure of mushrooms) combined with agricultural waste. It is a fully compostable and sustainable option that offers excellent cushioning and insulation. It is particularly well-suited for packaging fragile items.
Performance Characteristics of Alternatives
The performance of alternative tray materials varies significantly. It is essential to consider these differences when selecting the most appropriate packaging solution for a specific food product. The following comparison highlights key performance characteristics.
- Biodegradability:
- Paper-Based: Compostable in most home and industrial composting systems.
- Molded Pulp: Compostable in both home and industrial composting systems.
- PLA: Compostable only in industrial composting facilities.
- Starch-Based: Compostable in industrial and some home composting systems, depending on the formulation.
- Mushroom Packaging: Fully compostable in home and industrial settings.
- Moisture Resistance:
- Paper-Based: Can be coated for moisture resistance, but may not be suitable for very wet foods.
- Molded Pulp: Offers moderate moisture resistance.
- PLA: Generally has good moisture resistance.
- Starch-Based: Varies depending on the formulation; some offer good moisture resistance.
- Mushroom Packaging: Naturally moisture-resistant.
- Temperature Resistance:
- Paper-Based: Can withstand moderate temperatures.
- Molded Pulp: Can withstand moderate temperatures.
- PLA: Limited temperature resistance; not suitable for high-temperature applications.
- Starch-Based: Can withstand moderate temperatures.
- Mushroom Packaging: Offers good insulation properties but limited high-temperature resistance.
- Strength and Durability:
- Paper-Based: Can vary depending on the paper and coating used; generally less durable than foam.
- Molded Pulp: Offers good strength and cushioning.
- PLA: Offers moderate strength.
- Starch-Based: Can be less durable than other options.
- Mushroom Packaging: Offers excellent cushioning and shock absorption.
- Cost:
- Paper-Based: Can be cost-competitive, especially with recycled content.
- Molded Pulp: Often cost-effective.
- PLA: Can be more expensive than foam, but costs are decreasing.
- Starch-Based: Can be cost-competitive.
- Mushroom Packaging: Can be more expensive initially, but costs are decreasing as production scales up.
- Availability:
- Paper-Based: Widely available.
- Molded Pulp: Increasingly available.
- PLA: Availability is growing.
- Starch-Based: Availability varies.
- Mushroom Packaging: Availability is increasing, but still limited compared to other options.
Regulations and Compliance
The use and disposal of foam trays for food are subject to a complex web of regulations designed to protect public health and the environment. These regulations vary significantly depending on the region and can have a substantial impact on businesses that utilize these trays. Understanding and adhering to these rules is crucial for legal compliance and sustainable business practices.
Current Regulations Regarding the Use and Disposal of Foam Trays
Regulations governing foam trays address both their production and end-of-life management. These regulations are often multi-faceted, involving different governmental agencies and focusing on various aspects of the product’s lifecycle.
- Production Regulations: Some jurisdictions have outright bans or restrictions on the manufacturing of foam trays, often targeting those containing specific chemicals, such as certain types of polystyrene. These bans are typically driven by environmental concerns, focusing on the difficulty of recycling and the potential for environmental contamination.
- Food Contact Regulations: Foam trays used for food contact must comply with stringent food safety standards. These regulations dictate the materials that can be used in the tray’s construction and the levels of any potential chemical migration into the food. Compliance with these regulations is typically overseen by food safety agencies.
- Disposal Regulations: Disposal regulations are arguably the most widespread and impactful. These regulations often address how foam trays can be disposed of, including options like recycling (where available), landfilling, and incineration. Many regions have implemented bans or restrictions on foam tray disposal in landfills, driving businesses to seek alternative solutions.
- Labeling Requirements: Regulations may also mandate specific labeling requirements for foam trays, such as indicating whether they are recyclable in certain areas or providing information about the materials used in their construction. This information helps consumers make informed decisions about disposal and supports responsible waste management.
Regional and International Variations in Regulations
Regulations regarding foam trays exhibit considerable variation across different regions and countries. This variance reflects differing environmental priorities, waste management infrastructure, and political considerations.
- European Union (EU): The EU has been at the forefront of implementing regulations to reduce plastic waste. The Single-Use Plastics Directive, for example, targets single-use plastic items, including foam trays, with measures like extended producer responsibility schemes and restrictions on certain products. Some member states have already implemented outright bans on foam trays, while others are exploring alternative solutions.
- United States: Regulations in the US are highly variable, with a patchwork of state and local laws. Some states and cities have banned foam trays, while others have not. California, for instance, has implemented a ban on expanded polystyrene (EPS) food containers, while other states have taken a more cautious approach. This variation can create challenges for businesses operating across multiple jurisdictions.
- Canada: Regulations in Canada also vary by province and municipality. Some regions have implemented bans or restrictions on foam trays, while others are still assessing the environmental impact and exploring alternatives. The federal government is also working on initiatives to reduce plastic waste, which could lead to more uniform regulations in the future.
- Asia: Regulations in Asia are becoming increasingly stringent, particularly in countries with significant plastic waste challenges. Some countries, like China, have implemented nationwide bans or restrictions on certain types of single-use plastics, including foam trays. These regulations are often driven by concerns about pollution and the need to improve waste management practices.
Impact of Regulations on Businesses Using Foam Trays, Foam trays for food
Regulations surrounding foam trays have a significant impact on businesses that rely on them for food packaging. This impact can be felt across various aspects of their operations, from sourcing and production to distribution and waste management.
- Increased Costs: Compliance with regulations can lead to increased costs for businesses. This includes the cost of switching to alternative packaging materials, implementing new waste management systems, and potentially paying fees or taxes related to plastic waste. The cost of alternative packaging, such as biodegradable options, can sometimes be higher than the cost of foam trays.
- Supply Chain Disruptions: Bans or restrictions on foam trays can disrupt supply chains, particularly for businesses that rely on these trays for food transport and distribution. Businesses may need to find new suppliers for alternative packaging materials, which can take time and require significant logistical adjustments.
- Operational Changes: Businesses may need to make significant operational changes to comply with regulations. This can involve redesigning packaging, modifying waste management practices, and educating employees about new regulations. These changes can require investment in new equipment, training, and infrastructure.
- Reputational Risks: Non-compliance with regulations can expose businesses to reputational risks. Consumers are increasingly aware of environmental issues and may choose to avoid businesses that are perceived as contributing to plastic waste. This can damage brand image and affect sales.
- Opportunities for Innovation: While regulations can create challenges, they can also spur innovation. Businesses may be incentivized to develop and adopt new packaging materials, such as compostable trays or reusable containers. These innovations can create new business opportunities and contribute to a more sustainable economy. For example, a restaurant chain might partner with a company that offers reusable food containers to reduce its reliance on single-use foam trays.
Innovations and Future Trends
The food packaging industry is constantly evolving, driven by consumer demand, technological advancements, and environmental concerns. Foam trays, despite their established presence, are not immune to these shifts. Innovation is key to ensuring their continued relevance and addressing their environmental impact. This section explores potential innovations in foam tray design and materials, technologies focused on sustainability, and broader food packaging trends that will influence the future of foam tray usage.
Innovations in Foam Tray Design and Materials
Advancements in materials science and manufacturing processes are paving the way for more efficient, functional, and sustainable foam trays. These innovations aim to improve performance, reduce waste, and enhance the overall consumer experience.
- Biodegradable and Compostable Foams: Research and development are actively focused on creating foam trays from renewable resources. Examples include:
- Polylactic Acid (PLA) foams: Derived from corn starch or sugarcane, PLA offers a biodegradable alternative to traditional polystyrene. While PLA has shown promise, challenges remain in terms of cost, moisture resistance, and composting infrastructure availability.
- Mushroom Packaging: Mycelium, the root structure of mushrooms, can be grown into custom shapes, offering a completely biodegradable and compostable option. Companies like Ecovative Design are pioneering this technology, creating trays that are strong, lightweight, and can be grown to fit specific product dimensions.
- Improved Barrier Properties: Enhancements to foam tray materials are being explored to improve barrier properties, such as resistance to moisture, oxygen, and grease. This extends the shelf life of food products and reduces food waste.
- Coating Technologies: Applying thin coatings of biodegradable polymers or barrier films can enhance the performance of foam trays. These coatings can improve moisture resistance and prevent the migration of odors and flavors.
Finish your research with information from bangkok thai food 2.
- Coating Technologies: Applying thin coatings of biodegradable polymers or barrier films can enhance the performance of foam trays. These coatings can improve moisture resistance and prevent the migration of odors and flavors.
- Smart Packaging Integration: The integration of sensors and other technologies into food packaging is gaining traction. This includes:
- Temperature Sensors: Embedded temperature sensors can monitor the storage conditions of food products, providing real-time data on temperature fluctuations that could impact food safety and quality.
- Time-Temperature Indicators (TTIs): These indicators change color in response to temperature exposure over time, providing consumers with a visual cue about the freshness and safety of the food.
- Enhanced Structural Design: Innovations in tray design can improve strength, reduce material usage, and enhance functionality.
- Ribbed Designs: Incorporating ribs or other structural features can increase the strength and rigidity of foam trays, allowing for thinner materials and reduced packaging weight.
- Snap-Fit Closures: Designing trays with integrated snap-fit closures can eliminate the need for separate lids or wrapping, simplifying packaging and reducing material usage.
Technologies Aimed at Improving the Sustainability of Foam Trays
Addressing the environmental impact of foam trays requires a multifaceted approach, including innovations in materials, manufacturing processes, and end-of-life management. Several technologies are being developed to improve the sustainability of foam trays.
- Closed-Loop Recycling Systems: Establishing closed-loop recycling systems is crucial for minimizing waste and maximizing resource utilization.
- Chemical Recycling: Advanced recycling technologies, such as chemical recycling, can break down polystyrene and other plastics into their original monomers, allowing them to be reused in the production of new foam trays or other products. Companies like Agilyx are developing and implementing chemical recycling processes for polystyrene.
- Mechanical Recycling: Improving the efficiency and accessibility of mechanical recycling systems for foam trays can increase the recovery rate of these materials. This involves better sorting technologies, improved collection infrastructure, and advancements in recycling processes to handle contaminated materials.
- Bio-Based Additives: Incorporating bio-based additives into foam tray formulations can reduce the reliance on fossil fuels and improve the biodegradability of the trays.
- Natural Fillers: Using natural fillers, such as wood flour or cellulose fibers, can reduce the amount of synthetic polymers required and enhance the mechanical properties of the trays.
- Life Cycle Assessment (LCA): Conducting comprehensive Life Cycle Assessments (LCAs) is essential for evaluating the environmental impact of foam trays and identifying areas for improvement.
- Impact Analysis: LCA studies assess the environmental impacts of a product throughout its entire life cycle, from raw material extraction and manufacturing to use, disposal, and recycling. This information can guide the development of more sustainable foam tray designs and manufacturing processes.
Future Trends in Food Packaging that Could Impact Foam Tray Usage
Several broader trends in the food packaging industry are likely to influence the future of foam tray usage. These trends present both challenges and opportunities for foam tray manufacturers.
- Increased Demand for Sustainable Packaging: Consumers are increasingly aware of the environmental impact of packaging and are demanding more sustainable options. This trend is driving the adoption of biodegradable, compostable, and recyclable materials, and will put pressure on foam tray manufacturers to innovate.
- Growth of E-commerce and Food Delivery: The rise of e-commerce and food delivery services is changing the way food is packaged and transported. Foam trays will need to adapt to meet the specific requirements of these channels, such as enhanced protection during transit and improved temperature control.
- Focus on Food Waste Reduction: Minimizing food waste is a major priority for the food industry. Packaging plays a critical role in extending shelf life and preventing spoilage. Foam trays that incorporate barrier properties, modified atmosphere packaging, and smart packaging technologies can contribute to food waste reduction.
- Personalized and Customized Packaging: Advances in digital printing and manufacturing technologies are enabling the creation of personalized and customized packaging solutions. This trend could lead to foam trays that are tailored to specific products, consumer preferences, and branding requirements.
- Emphasis on Convenience and Functionality: Consumers value convenience and ease of use. Foam trays that offer features such as easy opening, resealable closures, and microwaveability will be in high demand.
- Regulatory Pressures: Governments and regulatory bodies are implementing stricter regulations on packaging materials, including restrictions on single-use plastics and mandates for recycling and composting. Foam tray manufacturers must comply with these regulations and proactively develop solutions that meet environmental standards.
User Experience and Feedback
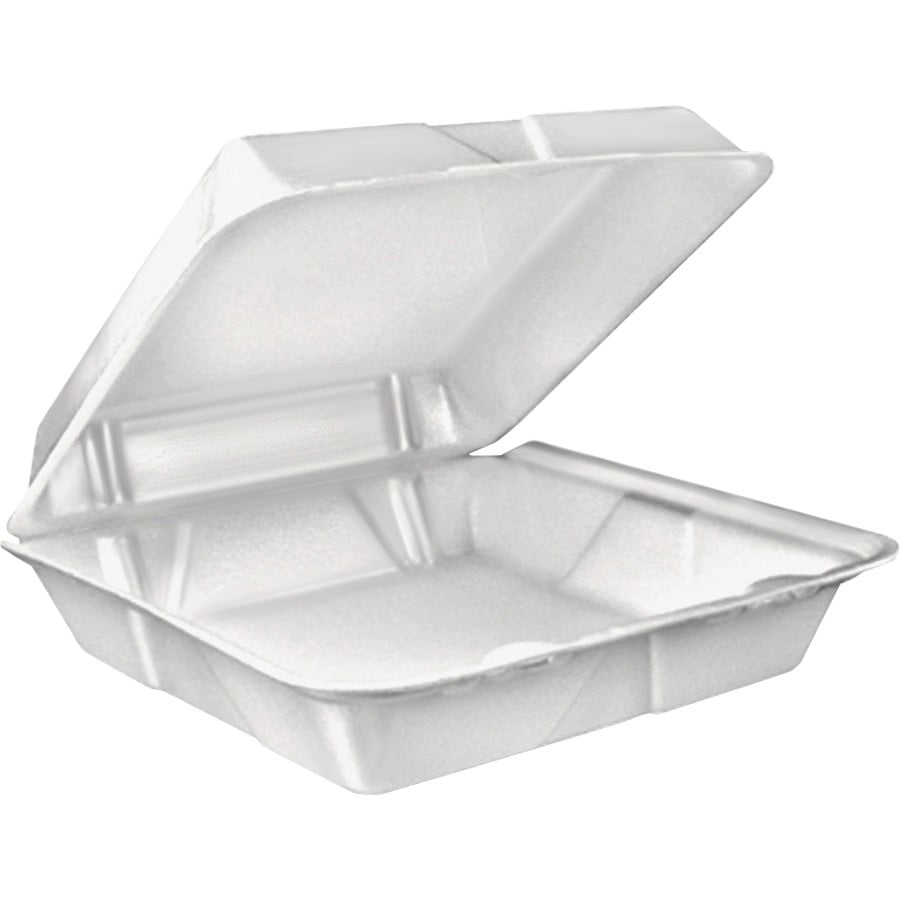
Understanding consumer perceptions and gathering feedback is crucial for optimizing food packaging, including foam trays. This section delves into how consumers view food served in foam trays, explores factors impacting their satisfaction, and provides a sample customer review to illustrate typical sentiments and potential improvements.
Consumer Perceptions of Food Served in Foam Trays
Consumer perceptions of food served in foam trays are often multifaceted, encompassing both positive and negative aspects. While foam trays offer convenience and affordability, they also face criticism regarding their environmental impact and perceived aesthetic appeal.The following factors commonly influence these perceptions:
- Convenience and Affordability: Consumers often appreciate the lightweight nature of foam trays, making them easy to carry and transport. The low cost of foam trays can also translate to lower food prices, a significant advantage for budget-conscious consumers. For example, fast-food chains frequently utilize foam trays to minimize operational costs and offer competitive pricing.
- Food Presentation: The visual appeal of food presented in foam trays is sometimes considered less attractive compared to alternatives like paperboard or plastic containers. The lack of design flexibility can limit the ability to enhance the food’s presentation. A simple example is the contrast between a carefully arranged meal in a paperboard container versus a similar meal in a plain foam tray.
- Food Temperature and Quality: Foam trays can sometimes trap heat, potentially affecting the texture of certain foods, particularly those that require ventilation. Concerns about food safety and hygiene, especially regarding potential leaching of chemicals, can also influence consumer perceptions. Consider, for instance, the difference in perceived quality of a crispy fried item served in a foam tray versus a vented container.
- Environmental Impact: The non-biodegradable nature of foam trays is a major concern for environmentally conscious consumers. The perception of contributing to landfill waste and pollution significantly impacts overall satisfaction. This is exemplified by the growing consumer preference for restaurants that use eco-friendly packaging, as seen in the increasing number of businesses switching to biodegradable alternatives.
Factors Influencing Consumer Satisfaction with Foam Tray Packaging
Several key elements significantly influence consumer satisfaction with food served in foam trays. These factors go beyond the mere functionality of the packaging and encompass aspects of convenience, food quality, and environmental considerations.These factors include:
- Food Freshness and Temperature Maintenance: The ability of the tray to preserve the food’s desired temperature is crucial. Consumers expect hot foods to remain hot and cold foods to stay chilled. This is often related to the material properties of the tray and its ability to insulate or allow for ventilation.
- Leakage Prevention: A major source of dissatisfaction arises from food leaking or spilling during transport. The structural integrity of the tray, including its ability to withstand pressure and prevent liquid seepage, is paramount. A secure lid or closure mechanism further enhances satisfaction.
- Ease of Use: Consumers value packaging that is easy to open, close, and handle. Trays that are difficult to manipulate, especially with one hand, can negatively impact the overall experience. This includes features like easy-to-peel lids and secure closures.
- Portion Control: The size and design of the tray should accommodate appropriate portion sizes. Consumers appreciate trays that offer a suitable amount of food without being wasteful or appearing stingy.
- Environmental Considerations: Consumers increasingly favor packaging that is sustainable and minimizes environmental impact. The use of recyclable or biodegradable foam trays can significantly boost consumer satisfaction, as it aligns with their values and preferences.
- Odor and Taste Neutrality: The packaging should not impart any undesirable odors or flavors to the food. Consumers expect the tray to maintain the food’s original taste and aroma without any interference.
Mock Customer Review and Suggested Improvements
This mock customer review illustrates the types of feedback commonly received and suggests areas for improvement in foam tray packaging.
Customer Review: “I recently ordered a takeout meal from a local diner, and it was served in a foam tray. While the food was delicious and the portion size was perfect, the experience was mixed. On the positive side, the tray was lightweight and easy to carry. However, the fries were a bit soggy by the time I got home, and I’m always concerned about the environmental impact of foam.
Also, the lid wasn’t very secure, and some sauce leaked a bit. I wish there were a more eco-friendly option, maybe something that kept the food hotter and prevented leaks better.”
Based on this review, the following improvements could be considered:
- Material Alternatives: Explore the use of biodegradable or recyclable foam alternatives, or consider using paperboard or plant-based packaging. This directly addresses the environmental concerns raised by the customer.
- Ventilation Design: Implement ventilation features in the lid or tray to prevent food from becoming soggy, particularly for fried items.
- Improved Closure Mechanism: Enhance the lid’s design to provide a more secure seal, preventing leaks during transport.
- Insulation Properties: Improve the tray’s insulation properties to better maintain the food’s temperature, ensuring that hot foods stay hot and cold foods remain chilled.
- Communication: Clearly communicate the packaging’s features and benefits to the customer, including any sustainability efforts.
Summary
Nah, jadi gimana, nih?
-Foam trays for food* itu emang praktis, murah, tapi ya ada plus minusnya juga, ye kan? Sekarang, sih, udah banyak banget pilihan, mulai dari yang ramah lingkungan sampe yang tetep pake plastik. Yang penting, kita sebagai konsumen harus pinter milih, biar makanan enak, lingkungan juga tetep kece. Jangan lupa, buang sampah pada tempatnya, ya, biar Jakarta nggak banjir!