Food grade plastic containers, often overlooked, play a critical role in safeguarding our food supply and maintaining its quality. From the simple sandwich bag to the robust storage container, these seemingly ordinary objects are engineered with precision to protect food from contamination and spoilage. But what makes a plastic “food grade”? This exploration delves into the science, regulations, and innovative designs that underpin this essential aspect of modern life, promising a journey of discovery into the unseen world of food preservation.
We’ll journey through the history, from the advent of plastics to today’s sophisticated polymers, examining the various types of food grade plastics – PP, HDPE, PET, and more – and their unique properties. We’ll unpack the complex world of regulations, including the roles of agencies like the FDA and EFSA, and understand the importance of labeling, certifications, and rigorous testing.
Prepare to uncover the manufacturing processes, design features, and sustainability initiatives that shape the food grade plastic container industry.
Types of Food Grade Plastics
The realm of food-grade plastics is a tapestry woven with diverse materials, each possessing unique characteristics that dictate their suitability for various culinary applications. Understanding these plastics, from their inherent properties to their specific advantages and drawbacks, is paramount in ensuring food safety, preservation, and the overall integrity of the consumer experience. This knowledge allows for informed choices, optimizing packaging solutions for freshness, shelf life, and environmental responsibility.
Common Food Grade Plastics and Their Properties
A diverse array of plastics is employed in the food industry, each crafted to meet specific needs. Their properties determine their utility in food storage, transportation, and presentation.
- Polypropylene (PP): A versatile thermoplastic polymer, PP is known for its high melting point, chemical resistance, and flexibility. It is often used in containers for hot foods, microwavable dishes, and yogurt cups. It’s often translucent or opaque.
- High-Density Polyethylene (HDPE): This robust and rigid plastic offers excellent moisture resistance and is a barrier against many chemicals. It’s commonly found in milk jugs, juice bottles, and detergent containers. It’s often opaque, offering good protection from UV light.
- Polyethylene Terephthalate (PET): A clear, strong, and lightweight plastic, PET is favored for its transparency and ability to withstand pressure. It is widely used for soft drink bottles, water bottles, and food jars. PET is recyclable and offers good barrier properties against oxygen and carbon dioxide.
- Low-Density Polyethylene (LDPE): Known for its flexibility, LDPE is used in squeezable bottles, plastic bags, and film wraps. Its flexibility makes it suitable for applications requiring a degree of give. It is also a good moisture barrier.
- Polycarbonate (PC): A transparent and strong plastic, polycarbonate is known for its impact resistance and heat resistance. While it was once popular for baby bottles and reusable water bottles, its use has declined due to concerns about the potential for leaching of BPA (Bisphenol A).
- Polystyrene (PS): Polystyrene can be either rigid or foamed (expanded polystyrene, or EPS). Rigid PS is used in items such as disposable cutlery and CD cases. EPS is commonly used in disposable coffee cups and takeaway containers.
Comparison of Food Grade Plastics for Different Applications
The selection of a food-grade plastic depends heavily on the intended application. The following table provides a comparative analysis, highlighting the critical factors that influence this decision.
Plastic Type | Properties | Advantages | Disadvantages |
---|---|---|---|
PP (Polypropylene) | High melting point, chemical resistance, flexibility, good barrier to moisture. | Suitable for hot foods, microwaveable, recyclable, good impact resistance. | Can become brittle at low temperatures, lower clarity than PET. |
HDPE (High-Density Polyethylene) | Excellent moisture resistance, rigid, good barrier to chemicals. | Strong, durable, recyclable, cost-effective, good barrier to moisture. | Less transparent than PET, can crack under stress. |
PET (Polyethylene Terephthalate) | Clear, strong, lightweight, good barrier to gases. | Transparent, recyclable, strong, shatter-resistant, good barrier properties. | Can absorb flavors, may release antimony in some circumstances. |
LDPE (Low-Density Polyethylene) | Flexible, good moisture barrier. | Flexible, inexpensive, good for squeezing applications, good moisture barrier. | Lower temperature resistance, not as strong as HDPE or PET. |
PC (Polycarbonate) | Strong, transparent, impact resistant, heat resistant. | Durable, reusable, can withstand high temperatures. | May leach BPA (Bisphenol A), not as recyclable as other plastics. |
PS (Polystyrene) | Rigid or foamed, can be clear or opaque, relatively inexpensive. | Inexpensive, can be clear, good for insulation (EPS). | Not as strong as other plastics, can be brittle, EPS is not easily recycled. |
Chemical Composition and Manufacturing Process of Polyethylene Terephthalate (PET)
PET, a cornerstone of the packaging industry, undergoes a meticulously controlled manufacturing process. This process transforms raw materials into a versatile plastic with exceptional properties.
The chemical composition of PET begins with the polymerization of two primary monomers: terephthalic acid (TPA) and ethylene glycol (EG). The process can be summarized by the following reaction:
n HOOC-C6H 4-COOH + n HO-CH 2-CH 2-OH → [(CO-C 6H 4-CO-O-CH 2-CH 2-O)] n + (2n-1)H 2O
This reaction, conducted under high temperatures and vacuum conditions, yields long polymer chains. The specific process involves the following steps:
- Esterification: TPA and EG are reacted to form a monomer called bis(2-hydroxyethyl) terephthalate (BHET). Water is released as a byproduct.
- Polycondensation: BHET monomers undergo polycondensation, where they combine to form long polymer chains. Ethylene glycol is released as a byproduct. Catalysts, such as antimony trioxide or germanium dioxide, are often used to speed up this process.
- Solid-State Polymerization (SSP): After initial polymerization, the PET polymer is often subjected to SSP. This process involves heating the polymer in a controlled environment under vacuum or an inert gas atmosphere. This process increases the molecular weight and crystallinity of the PET, improving its mechanical properties and heat resistance.
- Extrusion and Molding: The molten PET is then extruded and molded into various shapes, such as preforms for bottles or sheets for packaging. Techniques such as injection molding and blow molding are frequently employed.
The final product is a clear, strong, and lightweight plastic ideally suited for containing beverages and food products. The manufacturing process is continually refined to improve efficiency, reduce environmental impact, and enhance the properties of the final product. For example, improvements in catalyst technology have led to faster reaction times and reduced waste. Furthermore, research into bio-based PET, using ethylene glycol derived from renewable resources, is contributing to the sustainability of the process.
Applications of Food Grade Plastic Containers
The embrace of food-grade plastic containers has woven itself into the very fabric of our sustenance, a silent guardian ensuring freshness and safety from farm to table, and beyond. Their versatility allows for a multitude of uses, shaping the way we store, transport, and consume food, influencing both the industrial landscape and the domestic sphere. They are the unsung heroes, preserving the bounty of the earth.The realm of food-grade plastic containers extends far beyond mere storage, encompassing a spectrum of applications that are vital to the modern food system.
From the bustling factories to the quiet corners of our homes, these containers play an indispensable role.
Industrial Applications
The food industry relies heavily on food-grade plastic containers for a multitude of critical functions. These containers, crafted with precision and adhering to rigorous safety standards, ensure the integrity of products throughout the supply chain.* Bulk Storage and Processing: Large-capacity containers, often tanks or vats made from polyethylene or polypropylene, are used for storing and processing ingredients such as liquids (water, juices, oils), powders (flour, sugar), and granular materials.
These containers are designed to withstand varying temperatures and pressures, ensuring the preservation of food quality.* Transportation: Food-grade plastic containers, including crates, pallets, and intermediate bulk containers (IBCs), facilitate the efficient and safe transportation of food products. They are lightweight yet durable, reducing shipping costs and minimizing the risk of damage during transit. For example, reusable plastic crates are extensively used for transporting fruits and vegetables from farms to distribution centers and supermarkets, helping to reduce food waste and ensure product freshness.* Packaging: A vast array of food products are packaged in food-grade plastic containers.
From individual yogurt cups and sandwich bags to large bottles of beverages and jars of sauces, these containers provide a protective barrier against contamination, spoilage, and physical damage. The use of modified atmosphere packaging (MAP) in plastic containers extends the shelf life of fresh produce and processed foods.* Portion Control and Convenience: Single-serve containers, such as those used for condiments, ready-to-eat meals, and snacks, offer portion control and convenience for consumers.
These containers are often designed for easy handling and disposal, catering to the fast-paced lifestyles of modern consumers.
Household Applications
Within the domestic sphere, food-grade plastic containers are indispensable tools for managing food storage and preservation. Their adaptability and ease of use make them a staple in kitchens worldwide.Consider the humble refrigerator, a sanctuary of freshness. Food-grade plastic containers, in various shapes and sizes, play a pivotal role in organizing and preserving the contents within.* Food Storage: Airtight containers made of polypropylene or polyethylene are commonly used to store leftovers, prepped meals, and fresh produce.
These containers help to prevent spoilage, maintain food quality, and extend the shelf life of food items. The ability to stack these containers efficiently maximizes refrigerator space.* Freezing: Freezer-safe containers, often made of polyethylene or polypropylene, allow for the safe storage of food in the freezer. These containers are designed to withstand low temperatures and prevent freezer burn, preserving the flavor and texture of frozen foods.* Lunch Boxes and On-the-Go Meals: Food-grade plastic containers are ideal for packing lunches, snacks, and meals for consumption outside the home.
Their lightweight and durable nature makes them easy to carry, while their airtight seals prevent spills and maintain food freshness.* Meal Prep: Many individuals utilize food-grade plastic containers for meal prepping, portioning out meals and snacks in advance to save time and promote healthy eating habits. These containers allow for easy organization and convenient access to pre-prepared meals throughout the week.
Lifecycle Scenario
Let us trace the journey of a typical food-grade plastic container, a journey from its inception to its eventual fate. Imagine a container designed to hold a serving of yogurt.* Production: The journey begins in a manufacturing facility. Raw plastic resin, often polypropylene, is melted and molded into the desired shape using injection molding or blow molding techniques.
Rigorous quality control measures are in place to ensure the container meets food-grade standards. The container is then labeled and sealed, ready for filling.* Filling and Packaging: The yogurt container is transported to a dairy processing plant. Here, the container is filled with yogurt, sealed with a lid, and packaged with other containers for distribution. The containers are designed to withstand the filling process and maintain the integrity of the product.* Distribution and Retail: The packaged yogurt is transported to retail stores, such as supermarkets.
Remember to click chinese food cambridge ontario to understand more comprehensive aspects of the chinese food cambridge ontario topic.
The containers are designed to withstand the rigors of transportation and handling, ensuring the product arrives in good condition. The containers are prominently displayed on shelves, attracting consumers.* Consumer Use: A consumer purchases the yogurt container and takes it home. The consumer consumes the yogurt. The container, now empty, can be reused for storing other food items, depending on the consumer’s habits and the container’s design.* Disposal or Recycling: The empty container reaches the end of its initial use.
The consumer has two primary options. The consumer can dispose of the container in a waste bin, destined for a landfill. Or, if the consumer is environmentally conscious and the container is accepted by local recycling programs, the container is placed in the recycling bin.* Recycling Process (if applicable): If the container is recycled, it is collected and transported to a recycling facility.
Here, the container is sorted, cleaned, and shredded into small pieces. The shredded plastic is then melted and reprocessed into new plastic products, potentially including new food-grade containers, demonstrating a closed-loop recycling system. However, the effectiveness of recycling programs can vary depending on local infrastructure and consumer participation.* Environmental Impact: If the container ends up in a landfill, it can persist for hundreds of years, slowly breaking down into microplastics and contributing to environmental pollution.
The production of new plastic containers from virgin materials also consumes energy and resources, contributing to greenhouse gas emissions. The lifecycle of a food-grade plastic container underscores the importance of responsible consumption, recycling, and the development of sustainable packaging alternatives.
Safety and Compliance: Food Grade Plastic Containers
In the realm of food storage, where sustenance meets survival, the sanctity of the container is paramount. The vessels that cradle our nourishment must be shields against contamination, silent guardians of health. Neglecting the safety and compliance of food-grade plastic containers can invite insidious threats, turning the very tools of preservation into vectors of peril.
Potential Hazards of Non-Food Grade Plastics
The allure of cost-effectiveness can sometimes blind us to the silent dangers lurking within non-food grade plastics. These materials, often crafted for industrial or non-consumptive purposes, can leach harmful substances into the foods they contain, compromising the integrity of our meals and jeopardizing our well-being.The risks are multifaceted, a tapestry woven with chemical migration and physical degradation:
- Chemical Migration: Non-food grade plastics may contain phthalates, bisphenol A (BPA), and other potentially harmful chemicals. These substances can leach into food, especially when exposed to heat, acidity, or fats. Prolonged exposure can lead to endocrine disruption, developmental problems, and even increased risk of certain cancers. Imagine a plastic container used to store a hot, acidic tomato sauce; the likelihood of chemical migration is significantly heightened.
- Physical Degradation: These plastics may not be designed to withstand the rigors of food handling and storage. They can crack, break, or release microplastics into food. Microplastics, tiny fragments of plastic, are increasingly recognized as a widespread environmental contaminant, and their impact on human health is a growing concern. Think of a container repeatedly washed in a dishwasher; the heat and detergents can accelerate degradation.
- Unregulated Additives: Non-food grade plastics may contain unregulated additives or pigments that are not safe for human consumption. These substances could introduce allergens or toxins into food. Consider a brightly colored container; the dyes used might not be food-safe.
Importance of Labeling and Certifications
Navigating the world of food-grade plastics requires a discerning eye, a commitment to verification. The presence of proper labeling and certifications acts as a beacon, guiding consumers and manufacturers towards safe and compliant products.Proper labeling provides vital information:
- Material Identification: Labels should clearly indicate the type of plastic used (e.g., PET, HDPE, PP) and whether it is food-grade.
- Intended Use: The label should specify the intended use of the container, including whether it is suitable for hot or cold foods, microwave use, and freezer storage.
- Manufacturer Information: The manufacturer’s name and contact information should be provided for accountability and traceability.
- Recycling Codes: Recycling codes (numbers 1-7 within the recycling symbol) can assist in proper disposal and recycling efforts, promoting environmental sustainability.
Certifications provide an extra layer of assurance:
- Third-Party Validation: Certifications from reputable organizations, such as the Food and Drug Administration (FDA) in the United States or the European Food Safety Authority (EFSA), signify that the container has been tested and meets stringent safety standards.
- Compliance Verification: Certifications verify that the container complies with specific regulations regarding chemical migration, material composition, and overall safety.
- Consumer Confidence: Certifications instill consumer confidence, providing reassurance that the product has undergone rigorous scrutiny and is safe for food contact.
Procedures for Testing Food Grade Plastic Containers
Ensuring the safety of food-grade plastic containers requires a multifaceted approach, encompassing rigorous testing procedures designed to identify potential risks and guarantee compliance with established standards. These tests are not mere formalities but essential safeguards that protect the health of consumers.The testing procedures involve a series of evaluations:
- Material Analysis: This involves identifying the chemical composition of the plastic, including the presence of any potentially harmful substances. Techniques like Gas Chromatography-Mass Spectrometry (GC-MS) and Fourier-transform infrared spectroscopy (FTIR) are used to analyze the plastic’s molecular structure and identify any contaminants.
- Migration Testing: This assesses the potential for chemicals to migrate from the plastic into food. Samples of the plastic are exposed to food simulants (e.g., water, acetic acid, olive oil) under various conditions (e.g., temperature, time) to mimic real-world usage. The food simulants are then analyzed for the presence of any migrated substances.
- Sensory Evaluation: This evaluates the impact of the plastic on the food’s taste, odor, and appearance. Trained panelists assess the food stored in the container for any undesirable changes.
- Physical Testing: This evaluates the physical properties of the plastic, such as its strength, durability, and resistance to temperature changes. Tests may include drop tests, tensile strength tests, and heat resistance tests.
- Regulatory Compliance: This ensures that the container meets all relevant regulatory requirements, such as those established by the FDA or EFSA.
The testing process is not a one-time event, but a continuous cycle of evaluation and improvement. Manufacturers regularly conduct testing to ensure that their products continue to meet the required safety standards, demonstrating their unwavering commitment to consumer protection.
Manufacturing Processes
From the molten heart of polymers, shaped by fire and pressure, food-grade plastic containers emerge, each a vessel of preservation, a testament to engineering’s embrace of chemistry. The journey from raw material to finished product is a dance of precision, a symphony of machines orchestrated to meet the stringent demands of food safety and consumer needs.
Common Manufacturing Methods
The creation of food-grade plastic containers relies on several core manufacturing methods, each offering unique advantages in terms of design flexibility, production speed, and material usage. These processes, carefully chosen, dictate the final form and function of the container, ensuring its suitability for its intended purpose.
- Injection Molding: A method where molten plastic is forced under high pressure into a mold cavity. This process is ideal for producing complex shapes and intricate designs with high precision. It is commonly used for creating items like bottle caps, food storage containers, and smaller parts of larger packaging systems. The process allows for rapid production cycles, making it suitable for mass production.
For instance, a mold with multiple cavities can produce hundreds of caps per minute. The plastic is heated to its melting point, injected into the mold, cooled, and then ejected as a finished product.
- Blow Molding: Used to create hollow plastic parts such as bottles and jars. A parison (a tube of molten plastic) is extruded and then inflated with compressed air inside a mold. The plastic expands to fill the mold’s shape, and upon cooling, the mold opens to release the finished container. This method is highly efficient for producing lightweight containers with varying sizes and shapes.
The process can be further divided into Extrusion Blow Molding (EBM) and Injection Blow Molding (IBM). EBM is more suitable for producing larger containers, while IBM offers greater precision and is often used for smaller bottles.
- Thermoforming: Involves heating a plastic sheet to a pliable temperature and then shaping it over a mold using vacuum, pressure, or a combination of both. This method is suitable for producing trays, clamshell containers, and other packaging with relatively shallow depths. Thermoforming offers versatility in material selection, allowing for the use of various plastic types and thicknesses. The process is often used for producing packaging for fresh produce, baked goods, and prepared meals.
The sheet is clamped, heated, and then drawn over the mold.
- Extrusion: A continuous process where plastic is melted and forced through a die of the desired shape. It is commonly used to create films, sheets, and profiles. This method is also used to produce some types of containers, such as tubes and certain types of bottles. The process can be adapted to create multi-layered structures by combining different plastic materials.
This is especially useful for food packaging, as it allows for the incorporation of barrier layers that protect the food from oxygen, moisture, and other contaminants.
Environmental Impact of Different Manufacturing Processes
The environmental footprint of food-grade plastic container manufacturing varies significantly depending on the chosen process and the materials used. Understanding these differences is crucial for promoting sustainable practices and reducing the industry’s impact on the planet. The choice of material, energy consumption, and waste generation all play vital roles in determining the overall environmental impact.
- Energy Consumption: Injection molding often consumes more energy due to the high pressures and temperatures involved, while thermoforming can be relatively energy-efficient for certain applications. Blow molding’s energy consumption depends on the size and complexity of the container.
- Material Waste: Extrusion and blow molding can produce less material waste compared to injection molding, which often generates sprues and runners that must be recycled or disposed of. Thermoforming can generate significant scrap material depending on the shape and design of the container.
- Material Choice: The type of plastic used also impacts the environment. Plastics derived from renewable sources (bioplastics) or those that are easily recyclable are generally more sustainable. The use of recycled plastic in the manufacturing process reduces the demand for virgin materials.
- Emissions: All manufacturing processes generate some level of greenhouse gas emissions. These emissions are linked to energy consumption, the use of refrigerants, and the transportation of raw materials and finished products. Implementing energy-efficient equipment and using renewable energy sources can reduce emissions.
Step-by-Step Guide for the Production of a Specific Type of Food Grade Container
Let us consider the creation of a 1-liter, rectangular, food-grade polypropylene (PP) container with a snap-on lid, a common item found in many kitchens for storing leftovers. The process involves injection molding, a technique that provides the precision needed for the container’s dimensions and the lid’s secure fit.
- Material Preparation: Virgin polypropylene (PP) pellets, chosen for their high heat resistance, chemical inertness, and recyclability, are thoroughly dried to remove any moisture that could affect the molding process. The pellets are then loaded into the injection molding machine’s hopper.
- Melting and Injection: The PP pellets are fed into a heated barrel, where they are melted by a combination of heat and the friction generated by a reciprocating screw. Once molten, the plastic is injected under high pressure into a closed mold cavity that precisely matches the container’s shape.
- Mold Design: The mold itself is a complex assembly of steel or aluminum components, engineered to create the container’s walls, base, and any features like handles or ridges. Cooling channels within the mold circulate water to rapidly solidify the plastic. The mold for this container would have two main parts: one forming the outer shape and one forming the inner shape, with cores for any internal features.
- Cooling and Solidification: The molten plastic fills the mold and begins to cool. The cooling time is crucial for the container’s structural integrity. Cooling is accelerated by the circulating water within the mold. The cooling time is carefully controlled to ensure the plastic solidifies uniformly, preventing warping or distortion.
- Ejection: Once the plastic has solidified, the mold opens, and the container is ejected. Ejector pins, located within the mold, push the container out. The container is then inspected for any defects, such as imperfections in the surface or dimensional inaccuracies.
- Lid Production: A separate injection molding machine is used to create the snap-on lid. The process is similar to the container production, but the mold is designed to create the lid’s shape and the interlocking mechanism that secures it to the container.
- Assembly and Quality Control: The containers and lids are then assembled, often automatically, and undergo rigorous quality control checks. This includes dimensional measurements, leak tests, and visual inspections to ensure that each container meets the required standards for food safety and performance.
- Packaging and Distribution: The finished containers are then packaged and prepared for distribution to retailers and consumers. The packaging is also chosen to protect the containers during shipping and storage, minimizing the risk of damage.
Design and Features
The art of crafting food-grade plastic containers is a delicate dance between form and function, where aesthetics meet the imperative demands of preservation and safety. Each curve, seal, and closure is meticulously engineered, not merely to hold sustenance, but to safeguard its integrity, extending its life, and ensuring the well-being of the consumer. The design is the silent guardian of the contents, a testament to the commitment to quality and a crucial element in the journey from production to consumption.
Key Design Features Enhancing Functionality and Safety
A symphony of design elements orchestrates the performance of food-grade containers. These features work in harmony to provide optimal protection and convenience.
- Airtight Seals: The fortress of freshness. Airtight seals, often achieved through precision-molded lids and rims, create an impenetrable barrier against the outside world. This prevents oxygen ingress, a primary culprit in food spoilage, and helps retain moisture, crucial for the longevity of many food products. The efficacy of an airtight seal can be quantified by measuring its oxygen transmission rate (OTR), which should be exceptionally low for food-grade containers.
For instance, containers designed for highly perishable items like fresh berries might boast an OTR of less than 0.1 cm³/m²/day at standard conditions, showcasing the effectiveness of the seal.
- Tamper-Evident Closures: Guardians of Trust. Tamper-evident closures serve as a visual and physical assurance that the container’s contents remain untouched from the moment of packaging to the consumer’s possession. These can range from shrink bands and induction seals to breakaway tabs and specialized lid designs. A broken seal immediately signals potential tampering, providing an added layer of security. These features are crucial for consumer confidence, particularly for products like baby food or pharmaceuticals.
- Stackable and Nestable Designs: Efficiency in Motion. Strategic container designs allow for efficient stacking and nesting, optimizing storage space in warehouses, retail environments, and even the consumer’s pantry. This design also reduces transportation costs. For example, rectangular containers often offer superior stacking capabilities compared to cylindrical ones.
- Ergonomic Handles and Grip Features: Comfort in Handling. The design considers the user experience, incorporating features like ergonomic handles or textured grips to facilitate easy handling, especially for larger or heavier containers.
- Durable Materials and Construction: Strength and Resilience. Food-grade containers are engineered to withstand the rigors of transportation, storage, and handling. They are constructed from robust materials and engineered to resist impacts, punctures, and temperature fluctuations. The material’s impact resistance is tested through drop tests from specified heights.
Impact of Container Design on Food Preservation and Shelf Life
The design of a food-grade container is directly correlated to the preservation of its contents, affecting shelf life. The features of a container act as a shield against environmental factors that accelerate spoilage.
- Barrier Properties: The container’s ability to act as a barrier is paramount. Different plastics have varying barrier properties against oxygen, moisture, and light. For instance, multi-layer containers, combining different plastic materials, are often used to create a superior barrier against oxygen and moisture, thereby significantly extending shelf life. A study published in the “Journal of Food Science” demonstrated that using a multi-layer plastic container increased the shelf life of a specific type of processed meat by up to 50% compared to a single-layer container.
- Temperature Control: Containers designed for refrigerated or frozen foods often feature insulating properties or are designed to withstand temperature fluctuations. This can prevent temperature abuse and help to maintain the cold chain.
- Light Protection: Opaque or UV-resistant containers protect light-sensitive foods, such as milk or oils, from degradation.
- Shape and Volume Optimization: The container’s shape and volume influence the ratio of surface area to volume, impacting the rate of food degradation. Containers designed with a smaller surface area exposure to air can slow down the spoilage process.
Food Grade Container Design Illustration
Consider a hypothetical 1-liter food-grade container designed for storing a variety of dry goods like cereals or pasta.
The container is a clear, rectangular box made from food-grade Polypropylene (PP). The transparency allows the consumer to see the contents. The dimensions are approximately 20cm (length) x 10cm (width) x 15cm (height).
* Material Specifications:
Body
Polypropylene (PP) with a high impact resistance and excellent chemical resistance. The PP used would be food-grade, meeting FDA (Food and Drug Administration) and EU regulations for food contact materials. The PP is also BPA-free.
Lid
The lid is made from the same food-grade PP as the body, ensuring compatibility and recyclability. The lid is designed with an airtight seal.
Seal
A silicone gasket is embedded within the lid to enhance the airtight seal. The silicone is food-grade and tested for migration.
Design Features
Shape
Rectangular to optimize space utilization in pantries and shelves. The shape also facilitates stacking.
Closure
A snap-on lid with a secure locking mechanism. The lid incorporates a tamper-evident feature in the form of a small tab that breaks if the container has been opened.
Transparency
The container is clear, allowing consumers to easily identify the contents and gauge the amount remaining.
Handle/Grip
The container features recessed grips on the sides to facilitate easy handling and pouring.
Labeling Area
A designated flat area on the front and back for labels containing product information, nutrition facts, and brand details.
Recyclability Symbol
The container prominently displays the recycling symbol and material identification code (PP, resin identification code #5).
Visual Elements
A clear, concise brand logo is embossed on the front of the container.
Measurement markings (e.g., liters, cups) are molded into the side of the container for easy portioning.
The lid is a contrasting color to the body of the container, providing a visual cue and aesthetic appeal.
This design prioritizes functionality, safety, and user experience, reflecting the core principles of food-grade container design. The material selection ensures food safety, while the features extend the shelf life of the dry goods. The design also emphasizes consumer convenience and environmental responsibility.
Sustainability and Recycling
The whisper of plastic, once a marvel of modern convenience, now carries the weight of a troubled conscience. Food grade plastic containers, vital guardians of our sustenance, also contribute to a global tide of waste. The imperative to reconcile our dependence with our responsibility calls for a deep dive into sustainability, recycling, and innovative solutions. The path forward requires a blend of mindful consumption, efficient waste management, and groundbreaking alternatives.
Environmental Concerns of Plastic Waste and the Importance of Recycling
Plastic waste, a phantom limb of modern life, haunts our landscapes and oceans. Its persistence, a testament to its durability, becomes a curse when it lingers for centuries, slowly degrading and leaching harmful chemicals into the environment. The sheer volume of discarded plastics chokes marine life, pollutes ecosystems, and contributes to climate change through the energy-intensive processes of production and disposal.
Recycling, a beacon of hope in this narrative, offers a pathway to mitigate these impacts. It conserves resources, reduces landfill burden, and lowers greenhouse gas emissions by repurposing existing materials instead of relying on virgin resources. The act of recycling transforms a problem into a potential solution, a second life for materials that would otherwise become an environmental burden.
Recycling Codes for Food Grade Plastics and the Recycling Process
The journey of a plastic container from use to reuse is guided by a system of codes and processes. These codes, etched upon the container’s surface, are a language understood by recycling facilities, guiding them in sorting and processing. The process itself is a dance of sorting, cleaning, and transformation.The Society of the Plastics Industry (SPI) resin identification coding system is a standardized set of symbols, often a triangle with a number inside, used to identify the type of plastic resin used in a product.
The most common food-grade plastic codes include:
- #1 PETE (Polyethylene Terephthalate): Commonly used for beverage bottles and food jars. It is widely recycled, making it a good candidate for a circular economy. Recycling processes often involve shredding, cleaning, and melting the plastic into pellets that can be used to make new bottles, fibers for clothing, or other products.
- #2 HDPE (High-Density Polyethylene): Found in milk jugs, detergent bottles, and some food containers. HDPE is relatively easy to recycle and can be transformed into a variety of products, including new containers, pipes, and outdoor furniture.
- #5 PP (Polypropylene): Used for yogurt containers, medicine bottles, and some food storage containers. PP is also recyclable, though the recycling rates are generally lower than PETE and HDPE. Recycled PP can be used to make items like battery cables, brooms, and plastic trays.
The recycling process generally follows these steps:
- Collection: Consumers place recyclable plastic containers in designated bins or drop-off locations.
- Sorting: At a material recovery facility (MRF), the plastics are sorted, often using automated systems and manual labor, based on the resin identification codes.
- Cleaning: The sorted plastics are washed to remove contaminants like food residue and labels.
- Processing: The cleaned plastics are shredded, melted, and sometimes pelletized.
- Manufacturing: The recycled plastic pellets are used to manufacture new products, completing the cycle.
Innovative Methods for Reducing the Environmental Impact of Food Grade Plastic Containers, Including Biodegradable Alternatives
The quest for sustainability in food packaging extends beyond recycling, embracing innovation and the exploration of alternative materials. This includes the design of containers that are easier to recycle, using less material, and exploring materials that can break down naturally, minimizing the long-term environmental burden.
Several innovative methods and materials are emerging:
- Biodegradable Plastics: These plastics are designed to break down into natural substances like water, carbon dioxide, and biomass under specific conditions. They are often made from renewable resources such as corn starch or sugarcane. While promising, their widespread adoption faces challenges, including the need for specific composting facilities and concerns about their degradation in the open environment.
- Compostable Plastics: Compostable plastics are a subset of biodegradable plastics that are designed to break down in industrial composting facilities. They must meet specific standards, such as ASTM D6400, to ensure they completely break down within a specified timeframe.
- Reusable Containers: Encouraging the use of reusable containers is a simple yet effective method to reduce plastic waste. This can include incentivizing the use of reusable containers through discounts or convenience, and also establishing deposit-return systems for food packaging.
- Improved Recycling Technologies: Advancements in recycling technologies, such as chemical recycling, can break down plastics into their basic building blocks, allowing for the creation of new plastics from old ones.
- Reduced Packaging: Optimizing the design of containers to use less material can significantly decrease the overall environmental footprint. This includes exploring lightweighting techniques and eliminating unnecessary packaging layers.
Cleaning and Maintenance
The pristine embrace of food-grade plastic containers, guardians of our sustenance, demands a ritual of care. To ensure their longevity and unwavering protection against unseen foes, a diligent regimen of cleaning and maintenance is paramount. This ensures the safety of the food they hold and preserves their structural integrity, extending their service and minimizing waste. Like a sacred vessel, these containers must be treated with respect and understanding.
Preventing Contamination Through Proper Cleaning
The battle against contamination begins with the simple act of cleaning. Improper cleaning can breed harmful microorganisms, compromising the food and potentially endangering health. A consistent and methodical approach is essential.
- Immediate Post-Use Cleaning: The most effective defense is a swift offense. Rinse containers immediately after use, especially after holding perishable items. This prevents food particles from drying and adhering, becoming breeding grounds for bacteria.
- Washing with Soap and Water: Use warm, soapy water and a soft sponge or cloth. Avoid abrasive scrubbers that can scratch the plastic, creating crevices where bacteria can thrive. Choose a mild, unscented dish soap to avoid transferring unwanted flavors or chemicals to the food.
- Thorough Rinsing: Rinse the containers thoroughly with clean, running water. Ensure all soap residue is removed, as it can affect the taste and potentially react with the food.
- Air Drying: Allow the containers to air dry completely. This is generally preferable to towel drying, which can reintroduce contaminants. Place them upside down on a clean surface to facilitate drainage and airflow.
- Dishwasher Use (If Applicable): Check the manufacturer’s instructions to determine if the containers are dishwasher-safe. If so, place them on the top rack, away from the heating element. Use a dishwasher detergent specifically designed for food contact surfaces.
- Sanitizing (For Enhanced Protection): For an extra layer of defense, sanitize the containers periodically. A solution of diluted bleach (1 teaspoon of unscented bleach per quart of water) or a food-grade sanitizer can be used. Soak the containers for the recommended time, then rinse thoroughly and air dry.
Removing Stains and Odors from Plastic Containers
Despite meticulous care, stains and odors can sometimes cling to plastic containers, remnants of past culinary adventures. Fear not, for solutions exist to restore their pristine state.
- Baking Soda Paste for Stains: For stubborn stains, create a paste of baking soda and water. Apply the paste to the stained areas, let it sit for a few hours, and then scrub gently before rinsing thoroughly. Baking soda is a natural abrasive and odor absorber.
- Vinegar Soak for Odors: To eliminate persistent odors, soak the container in a solution of equal parts white vinegar and water for several hours or overnight. Vinegar is a natural deodorizer. Rinse thoroughly after soaking.
- Sunlight for Odor and Stain Removal: Place the containers in direct sunlight for a few hours. Sunlight can help to fade stains and eliminate odors. The UV rays have a sanitizing effect.
- Activated Charcoal for Odor Absorption: Place a small amount of activated charcoal inside the container and seal it. Activated charcoal is a highly absorbent material that can remove odors effectively. Leave it overnight or for a longer period.
- Boiling Water (Use with Caution): For some types of stains and odors, you may carefully try pouring boiling water into the container and letting it sit for a short time. This method is not recommended for all plastics, so check the container’s specifications first. Ensure the plastic can withstand high temperatures without warping or releasing harmful chemicals.
Safe Practices for Handling and Storing Food Grade Containers
The lifespan of these containers is not just determined by cleaning, but also by the way they are handled and stored. Thoughtful practices can prevent damage and ensure their continued safety.
- Avoid Extreme Temperatures: Food-grade plastic containers should be kept away from extreme temperatures. Avoid placing them near direct heat sources, such as ovens or stovetops, unless specifically designed for high-temperature use. Similarly, protect them from extreme cold, which can make the plastic brittle.
- Proper Stacking: When storing containers, stack them neatly to prevent scratches and damage. Consider using dividers or organizers to keep them separated and easily accessible.
- Avoid Sharp Utensils: Use only soft utensils when scooping food from plastic containers. Sharp knives or forks can scratch the surface, creating areas where bacteria can thrive.
- Inspect Regularly: Regularly inspect the containers for cracks, scratches, or any signs of damage. Discard any containers that show signs of wear and tear, as they may no longer be safe for food storage.
- Consider Container Rotation: Rotate the use of your containers, utilizing older ones first. This will help ensure that all your containers get used and are not left unused for extended periods, potentially leading to degradation.
- Follow Manufacturer’s Instructions: Adhere to the specific guidelines provided by the manufacturer. These guidelines will often include information on the appropriate use, temperature range, and cleaning methods.
Regulations and Standards
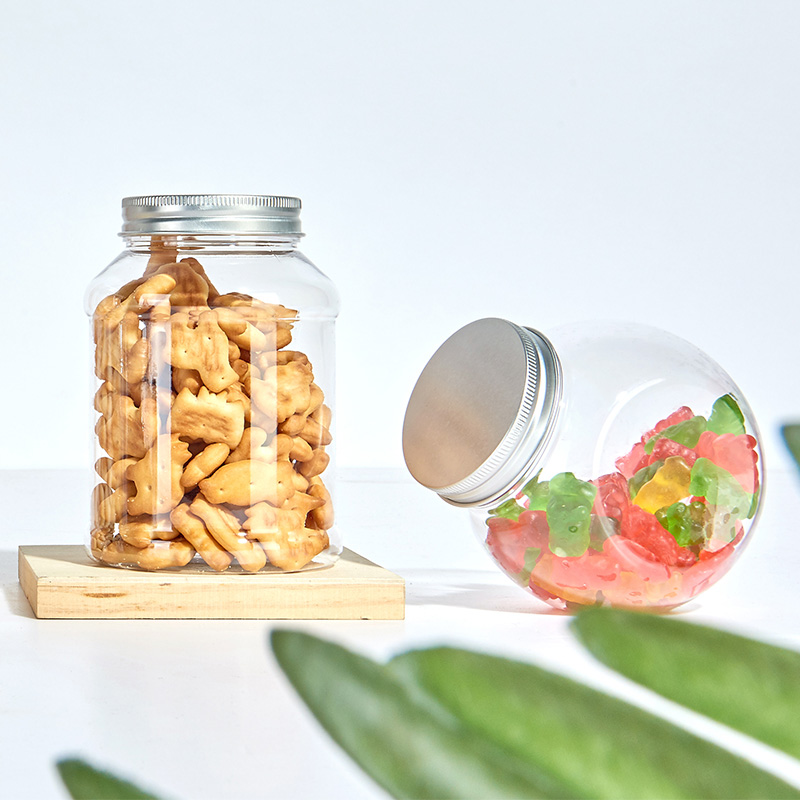
The realm of food-grade plastics, a silent guardian of our sustenance, dances to the tune of intricate regulations and stringent standards. These are not mere guidelines, but the very breath of safety, woven by global bodies to safeguard the health of every consumer. They dictate the composition, manufacture, and use of these containers, ensuring that the purity of our food remains untainted.
This intricate framework, constantly evolving, demands unwavering adherence from manufacturers, shaping the very essence of the industry.
Major Regulatory Bodies and Their Roles
The guardians of food safety are many, each wielding a unique influence over the world of food-grade plastics. Their roles, though distinct, converge on a shared mission: protecting public health.
- The U.S. Food and Drug Administration (FDA): Within the United States, the FDA reigns supreme. It establishes standards for materials that come into contact with food, issuing regulations under the Federal Food, Drug, and Cosmetic Act. The FDA meticulously assesses the safety of plastic materials, scrutinizing their chemical composition and potential for migration of substances into food. It approves substances for use in food contact applications and sets limits on the amount of certain substances that can leach from the plastic.
For instance, the FDA’s regulations define what additives are permitted in plastics and at what levels, ensuring that no harmful chemicals contaminate the food.
- The European Food Safety Authority (EFSA): Across the Atlantic, the EFSA holds sway over the European Union. It provides scientific advice on food safety, including the safety of food contact materials. EFSA evaluates the safety of substances used in plastics and provides opinions that inform the European Commission’s decisions on regulations. The EFSA’s assessments are based on rigorous scientific evaluations, taking into account potential exposure and toxicological data.
EFSA also plays a key role in harmonizing food safety standards across the EU member states.
- Other International Bodies: Beyond these major players, other organizations contribute to the global landscape of food safety. These include national regulatory bodies in countries like Japan, Canada, and Australia, each with its own set of standards and regulations. These bodies often align with international guidelines, contributing to a global effort to ensure the safety of food-grade plastics. The World Health Organization (WHO) also provides guidance and recommendations on food safety, influencing international standards and practices.
Impact of Specific Regulations on the Food Grade Container Industry
Regulations, like the currents of a vast ocean, profoundly shape the food-grade container industry. They influence material choices, manufacturing processes, and the very economics of production. Compliance is not merely an option; it is the price of entry into the market.
- Material Selection: Regulations restrict the use of certain chemicals and materials in food-grade plastics. This forces manufacturers to carefully select the polymers, additives, and colorants they use. For example, the use of phthalates, known for their potential endocrine-disrupting effects, is heavily restricted in many jurisdictions. Manufacturers must therefore choose alternative plasticizers and additives that meet regulatory requirements.
- Manufacturing Processes: Regulations also dictate the manufacturing processes used. They may set limits on the residual monomers in the plastic, the use of recycled materials, and the cleanliness of the production environment. For example, the FDA requires manufacturers to implement good manufacturing practices (GMPs) to ensure that food-grade containers are produced under sanitary conditions, minimizing the risk of contamination.
- Cost Implications: Compliance with regulations often increases the cost of production. The use of safer, but potentially more expensive, materials and the implementation of stringent manufacturing processes can add to the overall cost. Manufacturers may also need to invest in testing and certification to demonstrate compliance. These increased costs can be passed on to consumers, impacting the affordability of food products.
- Innovation and Development: Regulations can also drive innovation. Faced with restrictions on certain materials, manufacturers are spurred to develop new and safer plastics. For instance, the push to reduce the use of petroleum-based plastics has led to the development of bio-based plastics made from renewable resources. This fosters a dynamic environment where companies constantly seek more sustainable and compliant solutions.
Examples of Compliance with Specific Regulations, Food grade plastic containers
Food-grade containers must bear the badge of compliance, showcasing their adherence to the stringent rules that govern their existence. This compliance is demonstrated through labeling, material restrictions, and rigorous testing.
- Labeling: Food-grade containers must often be labeled with information that demonstrates their compliance with specific regulations. This may include a statement indicating that the container is “food grade” or “food safe.” The label might also include the name of the manufacturer, the type of plastic used, and any specific instructions for use. For example, a container may be labeled as “BPA-free” to assure consumers that it does not contain bisphenol A, a chemical that has raised health concerns.
- Material Restrictions: Regulations often restrict the use of certain materials in food-grade containers. This might include the prohibition of specific chemicals or the limitation of the amount of certain substances that can leach from the plastic into food. For example, the FDA has set limits on the amount of vinyl chloride that can be present in PVC plastic used for food packaging.
- Migration Testing: Food-grade containers are subjected to migration testing to ensure that no harmful substances leach into food. This testing simulates the conditions under which the container will be used, such as exposure to different types of food, temperatures, and storage times. For instance, a container intended for hot liquids might be tested at high temperatures to assess the potential for migration of chemicals.
The results of migration testing are used to determine whether the container meets regulatory requirements.
- Material Declarations: Manufacturers often provide material declarations to demonstrate compliance with regulations. These declarations list the components of the plastic and the levels of any regulated substances. They may also include information on the manufacturing processes used. These declarations are used by regulatory agencies and other stakeholders to assess the safety of the container.
- Third-Party Certifications: Many manufacturers seek third-party certifications to demonstrate their compliance with regulations. These certifications are issued by independent organizations that conduct testing and audits of manufacturing processes. For example, the “NSF” mark indicates that a product has been tested and certified by NSF International, a globally recognized certification body. These certifications provide added assurance to consumers and retailers.
Market Trends and Innovations
The food grade plastic container market, a vibrant tapestry woven with threads of consumer demand, technological advancement, and environmental consciousness, is in constant flux. It’s a realm where innovation is not merely a choice, but a necessity, driven by the evolving tastes of the global palate and the pressing need for sustainable practices. The following sections illuminate the current market trends, the exciting innovations reshaping the landscape, and the pivotal role of technology in enhancing both safety and efficiency.
Current Market Trends
The current market trends paint a picture of dynamic growth, influenced by a confluence of factors. These trends dictate the direction of development, shaping the future of food storage and transportation.
- Increased Demand for Convenience and Portability: The fast-paced lifestyles of consumers are driving a surge in demand for ready-to-eat meals and on-the-go snacks. This necessitates lightweight, easily transportable, and single-serve packaging solutions. The rise of meal-kit services, for instance, is heavily reliant on food-grade plastic containers designed for portion control and convenient handling.
- Growing Emphasis on Sustainability: Environmental concerns are paramount, with consumers increasingly favoring eco-friendly packaging options. This trend is pushing manufacturers to explore biodegradable plastics, recycled materials, and designs that minimize waste. The Ellen MacArthur Foundation’s New Plastics Economy initiative is a key driver, encouraging a shift towards a circular economy for plastics.
- Rise of E-commerce and Food Delivery: The exponential growth of online food ordering and delivery services is creating a demand for packaging that can withstand the rigors of transportation while maintaining food safety and freshness. This includes containers designed to prevent leaks, maintain temperature, and resist tampering. The use of insulated shipping containers, often incorporating food-grade plastics, is a common example.
- Expansion of the Ready-to-Drink (RTD) Beverage Market: The RTD beverage market, encompassing everything from juices and smoothies to cold-brewed coffee and kombucha, is experiencing substantial growth. This fuels the demand for plastic bottles and containers that offer excellent barrier properties to preserve product quality and shelf life.
- Growing Focus on Food Safety and Traceability: Heightened consumer awareness of food safety is leading to stricter regulations and increased demand for packaging that provides effective protection against contamination and facilitates traceability. This includes the use of tamper-evident seals, antimicrobial packaging, and technologies like QR codes for product tracking.
Emerging Innovations in Materials and Container Designs
Innovation in materials and container design is a constant pursuit, fueled by the desire to enhance functionality, sustainability, and consumer appeal. These advancements are shaping the future of food packaging.
- Biodegradable and Compostable Plastics: The development of biodegradable and compostable plastics, derived from renewable resources like cornstarch or sugarcane, offers a promising alternative to conventional plastics. These materials break down naturally, reducing environmental impact. Polylactic acid (PLA) is a widely used example, commonly found in cups, cutlery, and food containers.
- Recycled and Recyclable Plastics: Utilizing recycled plastics, such as PET (polyethylene terephthalate) and HDPE (high-density polyethylene), in food packaging is gaining traction. This approach reduces the reliance on virgin materials and contributes to a circular economy. The challenge lies in ensuring the safety and purity of recycled materials for food contact.
- Active Packaging: Active packaging goes beyond simply containing food; it actively interacts with it to extend shelf life and maintain quality. This includes oxygen scavengers, antimicrobial agents, and moisture absorbers. For example, packaging that releases carbon dioxide to preserve the freshness of baked goods.
- Smart Packaging: Smart packaging integrates sensors and indicators to provide information about the condition of the food inside. This can include temperature sensors to monitor cold chain integrity, time-temperature indicators (TTIs) to track freshness, and sensors to detect spoilage.
- Lightweight and Durable Container Designs: Advances in container design are leading to lighter, yet stronger, food-grade plastic containers. This reduces material usage, lowers transportation costs, and minimizes waste. Innovative designs, such as those incorporating ribbing or corrugations, can enhance strength and stacking capabilities.
The Role of Technology in Improving Safety and Efficiency
Technology plays a crucial role in improving the safety and efficiency of food-grade plastic containers, impacting everything from manufacturing to distribution and consumer use.
- Advanced Manufacturing Processes: Technologies like injection molding, blow molding, and thermoforming are continually being refined to produce containers with greater precision, efficiency, and consistency. Automation and robotics are being integrated to streamline production and reduce the risk of human error.
- Quality Control and Inspection Systems: Sophisticated quality control systems, including vision systems and automated inspection equipment, are used to detect defects, ensure dimensional accuracy, and verify the integrity of containers. This helps to prevent contaminated or substandard products from reaching consumers.
- Smart Packaging and Data Analytics: As mentioned before, smart packaging equipped with sensors and data-logging capabilities provides valuable insights into the condition of food throughout the supply chain. This data can be used to optimize logistics, reduce waste, and enhance food safety. For example, real-time temperature monitoring of refrigerated transport vehicles.
- Traceability and Supply Chain Management: Technology facilitates enhanced traceability, allowing for the tracking of containers and their contents from origin to consumer. This is critical for food safety and in the event of a recall. Technologies like blockchain are being explored to improve transparency and accountability.
- Digital Printing and Personalization: Digital printing technology enables the creation of customized packaging designs and the inclusion of interactive elements, such as QR codes that link to product information or promotional content. This enhances consumer engagement and provides opportunities for branding and marketing.
Final Wrap-Up
In conclusion, food grade plastic containers represent more than just packaging; they are integral to our food system’s safety, efficiency, and sustainability. From the initial design to the final recycling process, these containers are a testament to innovation and a commitment to safeguarding our food. By understanding the science, regulations, and future trends, we can appreciate the vital role these containers play in protecting our health and the environment.
The evolution of food grade plastics continues, promising even safer, more sustainable solutions for the future, ensuring the continued preservation of our food supply for generations to come.