Food wrapping machine, a silent guardian of freshness, stands at the crossroads of innovation and sustenance, transforming the way we preserve and present our daily meals. Imagine a world where the simple act of sealing a loaf of bread or encasing a succulent steak holds the key to extending shelf life and minimizing waste. This journey delves into the intricate mechanisms and evolving technologies that define the art of food wrapping, from the earliest hand-wrapped packages to the sophisticated, automated systems of today.
We’ll explore the diverse array of machines, each tailored to specific food types, from flow wrappers that cradle delicate pastries to tray sealers that hug ready-made meals. Discover the materials that shield our food, the films, trays, and labels, each playing a crucial role in safeguarding quality. We will then unravel the inner workings of these machines, examine the components, and the processes that turn raw ingredients into beautifully presented products, ready to grace our tables.
Let us not forget to explore the sectors where these machines are indispensable, from bakeries to meat processing plants, and the benefits they bring to both producers and consumers.
Introduction to Food Wrapping Machines
Food wrapping machines are the unsung heroes of the food industry, silently safeguarding the freshness, safety, and presentation of the products we consume daily. They’re an indispensable component of the modern food supply chain, ensuring that everything from a delicate pastry to a hearty cut of meat arrives at your table in perfect condition. These machines are essential for maintaining product integrity, extending shelf life, and enhancing consumer appeal.These machines utilize a variety of methods, from simple film wrapping to complex modified atmosphere packaging (MAP), to protect food from spoilage, contamination, and physical damage.
The benefits extend beyond mere preservation; efficient wrapping also optimizes storage and transportation, minimizes food waste, and contributes to a more sustainable food system.
Purpose and Significance
The primary function of a food wrapping machine is to enclose food products within a protective barrier, typically a film or other packaging material. This barrier serves several crucial purposes: it shields the food from external contaminants such as bacteria, dust, and insects; it helps to control the exchange of gases like oxygen and carbon dioxide, which can impact the food’s freshness and shelf life; and it prevents physical damage during handling and transportation.The significance of these machines lies in their contribution to food safety, reduced waste, and increased consumer satisfaction.
By extending the shelf life of perishable goods, they allow for wider distribution and reduce the likelihood of products spoiling before they reach consumers. This, in turn, minimizes food waste, a significant global concern. Furthermore, attractive and secure packaging enhances the product’s appeal and builds consumer trust.
Examples of Food Products
Food wrapping machines are incredibly versatile and are used to package a vast array of food products. The types of machines and wrapping methods employed vary depending on the food product’s characteristics and requirements.
- Fresh Produce: Fruits and vegetables, such as apples, bananas, tomatoes, and lettuce, are often wrapped in plastic film to protect them from bruising and maintain their moisture content. The film also helps to control the respiration rate of the produce, extending its shelf life.
- Meat and Poultry: Fresh cuts of meat, poultry, and seafood are frequently wrapped in trays with a plastic film overwrap. This method protects the product from contamination and allows for visual inspection by the consumer. Modified atmosphere packaging (MAP) is often used to further extend shelf life and maintain color and flavor.
- Baked Goods: Bread, pastries, and cakes are commonly wrapped in plastic film or packaged in boxes with a film overwrap to maintain their freshness, prevent them from drying out, and protect them from damage.
- Dairy Products: Cheese, yogurt, and other dairy products are packaged using various methods, including film wrapping, thermoforming, and filling and sealing. The packaging helps to prevent spoilage and maintain the product’s quality.
- Prepared Meals: Ready-to-eat meals, such as salads, sandwiches, and microwaveable dinners, are often packaged in trays or containers with a film seal. This provides convenience for consumers and extends the shelf life of the prepared food.
History and Evolution of Technology
The evolution of food wrapping technology reflects advancements in materials science, engineering, and automation. Early methods involved manual wrapping using simple materials like paper and waxed paper. The introduction of cellophane in the early 20th century marked a significant step forward, providing a transparent and moisture-resistant barrier.
- Early 20th Century: Manual wrapping techniques dominated, with basic materials like paper and waxed paper being used. Cellophane emerged as a revolutionary material, offering transparency and moisture resistance.
- Mid-20th Century: The development of polyethylene and other plastic films brought increased durability, flexibility, and cost-effectiveness. Semi-automatic wrapping machines began to appear, speeding up the process.
- Late 20th Century: Advancements in automation led to the development of high-speed, fully automated wrapping machines. Modified atmosphere packaging (MAP) and vacuum packaging technologies emerged, extending shelf life significantly.
- 21st Century: The focus shifted towards sustainable packaging materials and more efficient, flexible, and user-friendly machines. Innovations include the use of biodegradable films, improved sealing technologies, and integrated systems that combine wrapping with other processes like labeling and inspection.
The invention of the flow wrapper is a pivotal moment in the history of food wrapping. This machine, which encases products in a continuous film, dramatically increased wrapping speeds and efficiency. The introduction of heat sealing further improved the integrity of the packaging, creating a hermetic seal that prevented air and moisture from entering.
“The development of high-speed, automated wrapping machines has been instrumental in meeting the demands of a growing global population and a more complex food supply chain.”
Types of Food Wrapping Machines
Food wrapping machines are indispensable in the food industry, ensuring product freshness, extending shelf life, and enhancing consumer appeal. Understanding the different types of machines available is crucial for selecting the optimal solution for specific packaging needs. This section delves into the various types of food wrapping machines, their operational mechanisms, and their respective strengths and weaknesses, equipping you with the knowledge to make informed decisions.
Flow Wrappers
Flow wrappers, also known as horizontal form-fill-seal (HFFS) machines, are versatile and widely used in food packaging. They excel at wrapping individual items or groups of products in a continuous flow.
- Mechanism: Products are fed into the machine, and a continuous film of packaging material (typically plastic) is formed around them. The film is sealed lengthwise, creating a tube around the product. Then, the tube is sealed and cut to create individual packages. The process is continuous, allowing for high-speed operation.
- Advantages: Flow wrappers offer high-speed packaging capabilities, making them ideal for mass production. They are adaptable to various product sizes and shapes, and the packaging material can be customized with printed graphics for branding. They provide excellent product protection and often extend shelf life by creating a hermetic seal.
- Disadvantages: Flow wrappers may not be suitable for fragile products that require more robust packaging. The initial investment can be higher than for some other types of wrapping machines. While adaptable, they may require adjustments for significant product size changes.
- Examples: Flow wrappers are commonly used for wrapping confectionery items like chocolate bars, baked goods such as bread and pastries, and snack foods like chips and granola bars.
Tray Sealers
Tray sealers, or tray-sealing machines, are designed to seal a film onto a pre-formed tray, often made of plastic or aluminum. This method is particularly well-suited for packaging products in a controlled atmosphere.
- Mechanism: Products are placed in trays, and a film is sealed over the tray’s opening. The sealing process often involves heat sealing, which fuses the film to the tray. Some tray sealers offer modified atmosphere packaging (MAP) capabilities, where the air inside the tray is replaced with a gas mixture to extend shelf life and preserve product quality.
- Advantages: Tray sealers offer excellent product protection and can significantly extend shelf life through MAP. They provide a tamper-evident seal, enhancing food safety. The trays offer a convenient and visually appealing presentation for consumers.
- Disadvantages: Tray sealers require pre-formed trays, which can add to the packaging costs. The speed of tray sealing may be slower than flow wrapping for some applications. They are generally less adaptable to varying product shapes than flow wrappers.
- Examples: Tray sealers are frequently used for packaging fresh meat, poultry, seafood, ready-to-eat meals, and prepared salads.
Shrink Wrappers
Shrink wrappers utilize heat to shrink a film tightly around a product, creating a secure and visually appealing package. This process is effective for bundling multiple items together or providing a tight seal around individual products.
- Mechanism: The product is placed inside a shrink film bag or wrapped in a sheet of shrink film. The film is then exposed to heat, typically from a heat tunnel or a heat gun. The heat causes the film to shrink, conforming tightly to the product’s shape.
- Advantages: Shrink wrapping provides excellent product protection and offers tamper-evident packaging. It is cost-effective and versatile, suitable for a wide range of products. The tight seal can prevent moisture loss and maintain product freshness.
- Disadvantages: The heat involved in shrink wrapping can be a concern for heat-sensitive products. The process may be slower than flow wrapping or tray sealing for large-scale operations. The appearance of the finished package may not be as aesthetically pleasing as flow-wrapped or tray-sealed products in some cases.
- Examples: Shrink wrappers are commonly used for bundling bottled water, packaging CDs and DVDs, and securing boxes of products.
Comparative Specifications of Food Wrapping Machines
The following table compares the specifications of flow wrappers, tray sealers, and shrink wrappers, highlighting key differences and helping you evaluate their suitability for different applications.
Feature | Flow Wrapper | Tray Sealer | Shrink Wrapper |
---|---|---|---|
Speed (Packages per minute) | Up to 300+ | 10-60 (depending on the model and tray size) | 5-30 (depending on the size and type of product) |
Materials Used | Polypropylene (PP), Polyethylene (PE), laminated films | PP, PE, PET, aluminum trays, lidding film | Polyolefin, PVC, and other shrink films |
Size of Products Handled | Highly adaptable, various sizes and shapes | Limited by tray size, generally rectangular or square | Various, suitable for bundling and individual items |
Atmosphere Control | Limited | Excellent (MAP capabilities) | Limited |
Food Wrapping Materials
Ah, the unsung heroes of freshness! Food wrapping materials are more than just pretty packaging; they’re the guardians of flavor, the champions of shelf life, and the silent partners in presentation. From the delicate embrace of a cling film to the sturdy structure of a tray, the right material makes all the difference. Let’s dive into the fascinating world of food wrapping, where science meets sustainability, and where every choice impacts the quality and longevity of the food we love.
Types of Food Wrapping Materials
The realm of food wrapping materials is a diverse landscape, encompassing a variety of options, each tailored to meet specific needs. This section will explore the common categories, highlighting their unique characteristics and applications.
Films
Films are the workhorses of food wrapping, offering a flexible and versatile solution for a wide range of products. Their ability to conform to the shape of the food and provide a protective barrier makes them indispensable.Films are often made of:
- Polyethylene (PE): A widely used plastic film known for its flexibility, moisture resistance, and relatively low cost. It’s a staple for wrapping fresh produce, baked goods, and other items where a good seal is essential. Consider the common cling film you use at home to keep your leftovers fresh.
- Polypropylene (PP): Offering excellent clarity and heat resistance, PP films are ideal for applications where visual appeal is important, such as wrapping snacks, confectionery, and prepared meals. The crisp, transparent wrap around your favorite cookies often uses PP.
- Polyethylene Terephthalate (PET): Known for its strength, barrier properties, and ability to withstand higher temperatures, PET is a popular choice for ovenable trays and films used in ready-to-eat meals. Think of the film sealing a microwaveable lasagna.
- Polyvinyl Chloride (PVC): While offering excellent clarity and stretch, PVC’s use is declining due to environmental concerns. It’s still found in some applications, like wrapping meat and cheese, where its ability to cling tightly is beneficial.
- Modified Atmosphere Packaging (MAP) Films: These are sophisticated films designed to control the gas composition within the package, extending the shelf life of fresh produce and other perishable items. They often incorporate multiple layers of different polymers to achieve specific barrier properties and gas permeability.
Trays
Trays provide a rigid structure for food, offering protection, ease of handling, and presentation advantages. They are essential for packaging everything from meat and poultry to fruits and vegetables.Trays are typically made of:
- Expanded Polystyrene (EPS): A lightweight and cost-effective material, EPS is commonly used for meat and poultry trays. However, due to environmental concerns, alternatives are increasingly being adopted. Consider the classic white tray that holds your supermarket chicken breasts.
- Polyethylene Terephthalate (PET): PET trays offer excellent clarity, strength, and recyclability, making them a popular choice for a variety of food products, including ready-to-eat meals and fruit containers.
- Paperboard: Sustainable and often recyclable, paperboard trays are gaining popularity, especially for baked goods, confectionery, and frozen foods.
- Aluminum: Aluminum trays offer excellent heat conductivity and can be used for both cooking and serving. They are often found in ready-to-bake meals.
Labels
Labels are the information hubs of food packaging, providing essential details about the product, including ingredients, nutritional information, and handling instructions. They also play a crucial role in branding and marketing.Labels are made from:
- Paper: A common and cost-effective option, paper labels are often used for dry goods and products with a shorter shelf life.
- Polypropylene (PP): PP labels offer good moisture resistance and durability, making them suitable for a wide range of applications, including food products that may be exposed to moisture.
- Polyethylene (PE): PE labels provide flexibility and are often used on squeezable containers and flexible packaging.
- Film-Based Labels (e.g., PET): These offer superior durability, tear resistance, and clarity, making them ideal for products that require a premium look and feel.
Properties of Wrapping Materials
The effectiveness of food wrapping materials hinges on their specific properties. These characteristics determine how well the material protects the food from spoilage, maintains its quality, and presents it to the consumer.The key properties to consider include:
- Barrier Properties: This refers to the material’s ability to prevent the passage of gases (like oxygen and carbon dioxide), moisture, and light. Good barrier properties are crucial for extending shelf life and preserving the food’s flavor and nutritional value. For example, a high-barrier film will prevent oxygen from reaching the food, slowing down oxidation and spoilage.
- Sealability: The ability of the material to form a secure and airtight seal is essential for preventing leaks, maintaining freshness, and protecting the food from contamination. A strong seal is critical for products like vacuum-packed meats.
- Clarity: Transparency is important for allowing consumers to see the product inside, influencing their purchasing decisions. Clear films and trays are particularly important for showcasing fresh produce and prepared meals.
- Strength and Durability: The material’s ability to withstand handling, transportation, and storage conditions is essential for preventing damage and maintaining the product’s integrity. A robust tray is crucial for protecting delicate pastries during transit.
- Heat Resistance: For applications like ovenable trays and microwaveable films, heat resistance is critical to ensure the material doesn’t melt or deform during cooking.
- Printability: The ability to print clear and attractive graphics, branding, and information on the material is essential for marketing and regulatory compliance.
Sustainable and Eco-Friendly Food Wrapping Material Options
In today’s world, sustainability is no longer a trend, but a necessity. Consumers are increasingly demanding eco-friendly packaging options, and the food industry is responding with innovative solutions.Here are some sustainable and eco-friendly options:
- Biodegradable Films: Made from renewable resources like cornstarch, sugarcane, or cellulose, these films break down naturally in compostable environments. While offering a promising solution, their performance and cost are still being improved.
- Compostable Trays: Trays made from materials like molded pulp (recycled paper) or plant-based plastics can be composted, reducing landfill waste.
- Recycled Content Materials: Using recycled plastics and paperboard in packaging reduces the demand for virgin materials and minimizes environmental impact.
- Plant-Based Plastics: These plastics, derived from renewable resources, offer a more sustainable alternative to traditional petroleum-based plastics. Examples include PLA (polylactic acid) made from corn starch.
- Reusable Packaging: Encouraging the use of reusable containers and wraps, such as beeswax wraps or silicone bags, can significantly reduce packaging waste. Consider the popularity of reusable coffee cups.
- Reduced Packaging: Minimizing the amount of packaging used, while still ensuring product protection, is a key strategy for sustainability. This can involve optimizing packaging design and using thinner materials.
Benefits of Using Different Food Wrapping Materials
Choosing the right food wrapping material offers a multitude of benefits, impacting everything from food preservation to consumer appeal.Here’s a bullet-pointed list illustrating the benefits:
- Extends Shelf Life: Barrier properties prevent spoilage, preserving freshness and extending the time food can be stored.
- Protects Against Contamination: Creates a barrier against bacteria, pests, and other contaminants, ensuring food safety.
- Maintains Quality and Flavor: Prevents moisture loss, oxidation, and other factors that can degrade food quality and flavor.
- Facilitates Handling and Transportation: Provides a sturdy structure for easy handling, storage, and transportation, minimizing damage.
- Enhances Presentation: Clear films and attractive labels enhance the visual appeal of the product, attracting consumers.
- Provides Information: Labels provide essential information about the product, including ingredients, nutritional facts, and handling instructions.
- Enables Portion Control: Individual wrapping allows for portion control, reducing food waste.
- Allows for Modified Atmosphere Packaging (MAP): MAP films extend shelf life by controlling the gas composition around the food.
- Offers Convenience: Pre-packaged food offers convenience for consumers, saving time and effort.
Machine Components and Operation: Food Wrapping Machine
Ah, let’s delve into the heart of these marvelous machines! Understanding the components and operational dance of food wrapping equipment is key to unlocking their full potential. We’ll explore the inner workings, from the film’s graceful journey to the perfectly sealed package, and even peek into the troubleshooting toolbox. Get ready to become a food wrapping aficionado!
Key Components of a Food Wrapping Machine
Food wrapping machines are intricate systems, each part playing a crucial role in the packaging process. Let’s take a closer look at the essential players.
- Film Feed System: This is where the magic begins. The film feed system, often consisting of rollers and tension controls, precisely guides the wrapping material (like plastic film) from a roll to the wrapping area. Precise control is vital for consistent wrapping and minimal material waste. Imagine a delicate dance, ensuring the film unfurls smoothly and efficiently.
- Forming Section: This section shapes the film around the product. In flow wrappers, for example, the film is often formed into a tube. This is typically achieved by passing the film over a forming plow, a carefully designed mold that guides the film into the desired shape. The product then moves through this formed tube.
- Sealing Mechanism: This is where the package is sealed, creating an airtight and secure enclosure. Sealing mechanisms vary depending on the machine type, but they often involve heat sealing, impulse sealing, or ultrasonic sealing. Heat sealing, a common method, uses heated jaws to melt and fuse the film. The pressure and temperature are carefully controlled to create a strong and reliable seal.
- Cutting System: After sealing, the product needs to be separated from the continuous film. The cutting system precisely cuts the wrapped product from the film web. This can involve rotary knives, reciprocating knives, or other cutting mechanisms, ensuring a clean and consistent cut.
- Product Infeed System: The product infeed system is responsible for delivering the items to be wrapped to the machine. This can be a conveyor belt, a manual loading system, or an automated system, depending on the machine’s design and the product’s characteristics.
- Control Panel/PLC (Programmable Logic Controller): The brain of the operation! The control panel, often featuring a touchscreen interface, allows operators to adjust settings, monitor performance, and troubleshoot issues. The PLC manages the various machine functions, coordinating the movements of different components to ensure smooth and efficient operation.
Operational Steps of a Flow Wrapper
Flow wrappers are a popular choice for wrapping a wide variety of products. Let’s walk through the typical operational steps of a flow wrapper.
- Product Infeed: Products are fed into the machine, typically via a conveyor system. They are spaced apart and positioned for wrapping.
- Film Forming: The wrapping film is drawn from a roll and passed over a forming plow. The plow shapes the film into a tube, ready to enclose the product.
- Product Insertion: As the formed film tube moves along, the product is gently inserted into the tube.
- End Sealing: The leading and trailing ends of the product are sealed. This typically involves heat sealing, creating a secure closure.
- Cutting: The wrapped product is then cut from the continuous film web, separating it from the next package.
- Discharge: The finished, wrapped product is discharged from the machine, ready for the next stage of processing or packaging.
Troubleshooting Common Food Wrapping Machine Issues
Even the most reliable machines can encounter hiccups. Knowing how to troubleshoot common issues can save valuable time and prevent production delays.
- Poor Seals: Weak or inconsistent seals are a common problem.
- Possible Causes: Incorrect temperature settings, damaged sealing jaws, film contamination, or excessive product in the seal area.
- Troubleshooting Steps: Check and adjust the sealing temperature, inspect the sealing jaws for damage, ensure the film is clean, and reduce the product volume if necessary.
- Film Tears or Jams: Film tears or jams can halt production.
- Possible Causes: Incorrect film tension, dull cutting knives, film defects, or obstructions in the film path.
- Troubleshooting Steps: Adjust the film tension, replace dull knives, inspect the film for defects, and clear any obstructions.
- Incorrect Package Size: Inaccurate package dimensions can lead to product waste or customer dissatisfaction.
- Possible Causes: Incorrect machine settings, inaccurate product spacing, or inconsistent product size.
- Troubleshooting Steps: Verify and adjust machine settings, ensure consistent product spacing, and address any product size variations.
- Machine Not Starting: A non-responsive machine can be frustrating.
- Possible Causes: Power supply issues, blown fuses, or faulty sensors.
- Troubleshooting Steps: Check the power supply, replace any blown fuses, and inspect the sensors for proper operation.
Applications in Different Food Industries
Food wrapping machines are indispensable tools in the modern food industry, streamlining processes and ensuring product integrity. Their versatility allows them to cater to the diverse needs of various sectors, from delicate baked goods to robust meat products and fresh produce. Understanding the specific applications of these machines in different food industries is crucial for optimizing operations and maintaining high standards of food safety and presentation.
Bakery Industry Applications
The bakery industry relies heavily on food wrapping machines to preserve the freshness, extend the shelf life, and enhance the visual appeal of its products. This is particularly important for items like bread, pastries, and cakes, where presentation is key to consumer appeal.The applications include:
- Bread Wrapping: High-speed flow wrappers are commonly used to wrap loaves of bread, buns, and rolls, providing a protective barrier against air and moisture. These wrappers often incorporate features like automated loading and sealing to maintain a high throughput.
- Pastry Packaging: Tray sealers and shrink wrappers are employed for packaging pastries, muffins, and other baked goods, often in pre-formed trays. This packaging method not only protects the products but also allows for attractive presentation in retail settings.
- Cake and Dessert Wrapping: Cakes, pies, and individual desserts benefit from shrink wrapping or over wrapping, which provides a secure seal and protects delicate decorations. Clear films allow consumers to view the product, enhancing its visual appeal.
Meat and Poultry Processing Sector Applications
In the meat and poultry industry, food wrapping machines play a critical role in maintaining product safety, hygiene, and extending shelf life. The nature of these products demands robust and efficient packaging solutions that can withstand the demands of handling and transportation.The applications include:
- Meat Tray Sealing: Modified Atmosphere Packaging (MAP) tray sealers are widely used for packaging fresh meat, poultry, and seafood. MAP technology extends shelf life by controlling the gas composition within the package, typically using a combination of oxygen, carbon dioxide, and nitrogen.
- Vacuum Packaging: Vacuum packaging machines remove air from the package before sealing, creating a tight seal that inhibits bacterial growth and reduces spoilage. This method is especially important for preserving the quality of processed meats and sausages.
- Portion Control and Packaging: Portioning machines are often integrated with wrapping systems to accurately portion and package meat products, ensuring consistent weights and reducing waste. This is a key factor in operational efficiency and cost control.
Produce and Fresh Produce Industry Applications
The produce industry benefits greatly from food wrapping machines that protect delicate fruits and vegetables, maintain freshness, and extend shelf life. Proper packaging minimizes damage during transportation and storage, reducing waste and ensuring product quality.The applications include:
- Clamshell Packaging: Clamshell packaging, often made from clear plastic, is widely used for berries, grapes, and cherry tomatoes. These packages protect the produce from bruising and provide excellent visibility for consumers.
- Flow Wrapping: Flow wrappers are used for wrapping individual fruits like apples, pears, and avocados, as well as bundles of vegetables like asparagus and green beans. This method provides a protective barrier while allowing for efficient packaging.
- Stretch Wrapping: Stretch wrapping is used to secure pallets of produce for transportation, protecting the products from damage and maintaining the integrity of the load. This is particularly important for bulk shipments of fruits and vegetables.
Machine Types and Products Handled
The following table summarizes the different types of food wrapping machines and the products they are commonly used for in various food sectors.
Food Sector | Machine Type | Products Handled | Key Benefit |
---|---|---|---|
Bakery | Flow Wrappers | Bread, buns, pastries, cookies | High-speed packaging, freshness preservation |
Meat & Poultry | MAP Tray Sealers | Fresh meat, poultry, seafood | Extended shelf life, controlled atmosphere |
Produce | Clamshell Packaging | Berries, grapes, cherry tomatoes | Protection from bruising, visual appeal |
Bakery & Produce | Shrink Wrappers | Cakes, pies, individual fruits | Secure seal, enhanced presentation |
Advantages of Using Food Wrapping Machines
Food wrapping machines are indispensable in the modern food industry, offering a multitude of benefits that extend far beyond simple packaging. They are a cornerstone of efficiency, preservation, and brand enhancement, contributing significantly to profitability and consumer satisfaction. Let’s delve into the remarkable advantages these machines bring to the table.
Increased Shelf Life and Reduced Food Waste
One of the most significant advantages of food wrapping machines is their ability to extend the shelf life of perishable goods. This is achieved through precise sealing, which creates a barrier against oxygen, moisture, and contaminants, the primary culprits behind food spoilage.
- Controlled Atmosphere Packaging (CAP): Some advanced wrapping machines employ CAP technology. This involves modifying the atmosphere within the package, often by reducing oxygen levels and introducing gases like nitrogen or carbon dioxide. This process significantly slows down the degradation process, keeping food fresher for longer. For instance, a study by the University of California, Davis, showed that using modified atmosphere packaging on fresh-cut produce can extend its shelf life by up to 50%.
- Reduced Spoilage: By minimizing exposure to external elements, wrapping machines drastically reduce the risk of spoilage. This is especially crucial for items like meat, poultry, and seafood, which are highly susceptible to bacterial growth. A food processing plant in Denmark reported a 20% reduction in food waste after implementing automated wrapping systems, demonstrating the tangible impact on reducing waste.
- Enhanced Preservation Techniques: The combination of airtight sealing and, in some cases, the application of preservatives or modified atmosphere packaging, creates an environment that significantly inhibits microbial growth and enzymatic reactions. This helps preserve the nutritional value, taste, and texture of the food product for a more extended period.
Improved Product Presentation and Branding
Beyond preserving food, wrapping machines play a vital role in enhancing product presentation and strengthening brand identity. A well-packaged product immediately catches the consumer’s eye, influencing their purchasing decisions.
Find out about how bethel food bank can deliver the best answers for your issues.
- Professional Appearance: Automated wrapping ensures consistent and professional packaging, eliminating the inconsistencies often associated with manual methods. This consistency translates to a perception of higher quality and attention to detail.
- Branding Opportunities: Wrapping machines provide a perfect platform for branding. Packaging can be customized with logos, colors, and detailed product information, reinforcing brand recognition and communicating essential details to the consumer. Consider the vibrant, eye-catching packaging of pre-packaged salads; this is a direct result of the capabilities of modern wrapping machines.
- Enhanced Product Visibility: Many wrapping machines utilize clear, transparent films that allow consumers to see the product inside. This transparency builds trust and allows customers to assess the quality and freshness of the food before purchasing.
Cost-Effectiveness of Automated Wrapping Versus Manual Wrapping
While the initial investment in a food wrapping machine might seem significant, the long-term cost-effectiveness of automated wrapping far surpasses manual methods. The efficiency gains and reduced waste quickly offset the initial expenses.
- Increased Speed and Efficiency: Automated machines can wrap products at a significantly faster rate than manual labor. This increased throughput translates to higher production volumes and reduced labor costs. A bakery, for example, might see a threefold increase in wrapping speed by switching to an automated system.
- Reduced Labor Costs: Automated wrapping machines require fewer employees compared to manual wrapping, leading to significant savings in labor costs. This is particularly beneficial in industries with high labor turnover or rising wage rates.
- Minimized Material Waste: Automated machines are designed to use packaging materials efficiently, minimizing waste and reducing material costs. Precision in cutting and sealing prevents excessive material usage. For instance, a study by a food processing company revealed a 15% reduction in packaging material waste after automating their wrapping process.
- Consistent Packaging Quality: Automated wrapping ensures uniform packaging, reducing the likelihood of product damage during transportation and handling. This minimizes product returns and associated costs.
Choosing the Right Food Wrapping Machine
Selecting the perfect food wrapping machine is like choosing the right chef for your culinary masterpiece: the success of your product hinges on this critical decision! It’s not just about having a machine; it’s about having theright* machine, one that perfectly complements your food products and your production goals. Let’s delve into the key considerations to ensure you make an informed and advantageous choice.
Factors for Machine Selection
Choosing a food wrapping machine involves a multifaceted evaluation process. Several factors must be considered to ensure the machine meets your specific needs and operational demands.
- Product Size and Shape: The dimensions and form of your food products are paramount. Machines are designed to handle various sizes and shapes, from individual pastries to large trays of prepared meals. A machine designed for small, rectangular items may not be suitable for irregularly shaped or oversized products. For instance, a bakery wrapping individual croissants would need a different machine than one wrapping whole loaves of bread.
- Wrapping Speed (Throughput): Consider your desired production volume. Higher-speed machines are ideal for large-scale operations, while slower machines may suffice for smaller businesses. Evaluate the number of units you need to wrap per minute or hour to determine the necessary machine speed. For example, a machine capable of wrapping 100 units per minute is significantly different from one wrapping 10.
- Budget: Establish a clear budget, encompassing the initial purchase price, installation costs, and ongoing maintenance expenses. Consider both the short-term and long-term costs, including energy consumption and potential repair expenses. Research different models and manufacturers to find the best balance between price and features.
- Wrapping Materials: The type of wrapping material you intend to use (e.g., film, paper, foil) will influence the machine’s compatibility. Ensure the machine is designed to handle the specific materials required for your food products. Some machines are designed for specific film types like polyethylene, polypropylene, or laminates.
- Level of Automation: Determine the level of automation required. Manual, semi-automatic, and fully automatic machines offer different degrees of operator involvement. Fully automated systems require less labor but have a higher initial investment. Semi-automatic machines offer a balance between cost and operator control.
- Machine Footprint and Space Availability: Evaluate the available space in your production facility. Consider the machine’s dimensions, required clearance, and accessibility for maintenance and operation. A compact machine is advantageous in space-constrained environments.
- Ease of Operation and Maintenance: Choose a machine that is user-friendly and easy to operate. Consider the complexity of the control system, the accessibility of components for maintenance, and the availability of technical support. A machine with straightforward operation minimizes training time and reduces downtime.
- Durability and Reliability: Opt for a machine built with high-quality materials and components to ensure durability and reliability. Check the manufacturer’s reputation, warranty, and service network. A robust machine minimizes downtime and extends its lifespan.
Importance of Food Product Type
The type of food product is a crucial determinant in selecting the appropriate wrapping machine. Different food products have unique characteristics that influence the optimal wrapping method.
- Perishability: Highly perishable items, such as fresh produce or meats, require wrapping that provides excellent barrier properties to extend shelf life and prevent spoilage. Modified Atmosphere Packaging (MAP) is a common technique used for these products.
- Product Consistency: The consistency of the food product (solid, liquid, or semi-solid) affects the type of wrapping machine required. Liquid products often require specialized machines designed to handle spills and maintain product integrity.
- Fragility: Delicate food items, such as pastries or baked goods, necessitate gentle handling during the wrapping process to prevent damage. Machines with features like soft-seal technology and adjustable wrapping pressure are beneficial.
- Temperature Sensitivity: Some food products require temperature-controlled wrapping environments to maintain quality. Machines with integrated temperature control systems are suitable for these applications. Consider frozen food, which needs to be wrapped at low temperatures to maintain its quality.
- Packaging Requirements: The desired packaging style (e.g., flow wrap, shrink wrap, tray sealing) influences machine selection. Each style offers different advantages in terms of product presentation, protection, and shelf life. For example, flow wrapping is often used for individual snacks, while shrink wrapping is suitable for bundling multiple items.
Evaluating Machine Performance and Efficiency
Evaluating the performance and efficiency of a food wrapping machine is essential to ensure it meets your production goals and delivers a return on investment.
- Wrapping Speed: Measure the actual wrapping speed under real-world operating conditions. Compare this to the manufacturer’s specifications to identify any discrepancies. Consider any slowdowns caused by product variations or machine malfunctions.
- Wrapping Accuracy: Assess the consistency and precision of the wrapping process. Evaluate the seal integrity, film tension, and overall package appearance. Inspect the packages for defects such as air leaks or loose seals.
- Material Usage: Track the consumption of wrapping materials, such as film or paper. Calculate the material waste generated during the wrapping process. Optimize machine settings to minimize material usage and reduce costs.
- Downtime: Monitor the machine’s downtime due to maintenance, repairs, or product changes. Analyze the causes of downtime and implement measures to reduce its frequency and duration. Downtime directly impacts productivity and profitability.
- Energy Consumption: Measure the machine’s energy consumption over a specific period. Compare the energy usage to the manufacturer’s specifications and identify areas for improvement. Consider using energy-efficient machines to reduce operating costs.
- Operator Training and Productivity: Evaluate the ease of operation and the time required for operator training. Assess the operator’s productivity and efficiency in using the machine. A well-trained operator can maximize the machine’s performance.
- Maintenance Costs: Track the costs associated with machine maintenance, including spare parts, labor, and service contracts. Compare these costs to the machine’s performance and lifespan. Implement a preventative maintenance program to minimize repair expenses.
By carefully considering these factors, you can select a food wrapping machine that will enhance your production efficiency, reduce costs, and ensure the quality and appeal of your food products.
Maintenance and Safety
Maintaining your food wrapping machine is like giving your favorite chef a sharp knife – it ensures everything runs smoothly and efficiently, guaranteeing the quality and safety of your wrapped products. Neglecting maintenance and safety protocols can lead to costly downtime, compromised product integrity, and potential hazards for your team. Let’s delve into the crucial aspects of keeping your machine in top condition and your workplace a safe environment.
Recommended Maintenance Procedures
Regular maintenance is the secret to longevity and consistent performance for your food wrapping machine. Following a structured maintenance schedule not only extends the lifespan of your equipment but also minimizes the risk of unexpected breakdowns and ensures optimal wrapping quality.
- Daily Cleaning: After each shift, thoroughly clean the machine. This includes wiping down all surfaces that come into contact with food or packaging materials. Remove any food debris, dust, or residue that may have accumulated. This is crucial for preventing contamination and maintaining hygiene. Consider using food-grade cleaning agents, and follow the manufacturer’s guidelines.
- Weekly Inspection: Perform a more detailed inspection once a week. Check for any loose parts, worn belts, or damaged components. Lubricate moving parts according to the manufacturer’s instructions. Ensure all safety guards are in place and functioning correctly.
- Monthly Lubrication: Lubrication is essential for reducing friction and wear. Lubricate all moving parts, such as bearings, gears, and chains, using the recommended lubricant. Over-lubrication should be avoided, as it can attract dust and debris. Refer to the machine’s manual for the correct lubrication points and frequency.
- Quarterly Calibration: Calibrate the sealing and cutting mechanisms to ensure accurate and consistent wrapping. Check the temperature settings, sealing pressure, and cutting blade alignment. Incorrect calibration can lead to poor seals, product damage, and material waste.
- Annual Professional Servicing: Schedule an annual service by a qualified technician. This service should include a comprehensive inspection, preventative maintenance, and any necessary repairs. A professional can identify and address potential issues that might be overlooked during routine maintenance.
Importance of Safety Protocols
Operating a food wrapping machine safely is paramount. Safety protocols protect your employees from potential hazards and help maintain a productive and compliant work environment. Ignoring these protocols can lead to serious injuries, equipment damage, and regulatory violations. Prioritizing safety is not just a responsibility; it’s an investment in your team and your business’s success.
Safety Precautions for Operation and Maintenance
Adhering to these safety precautions is vital for preventing accidents and ensuring a safe working environment. Always prioritize safety over speed, and train all operators on these procedures.
- Power Disconnection: Before performing any maintenance or cleaning, always disconnect the machine from the power supply. This prevents accidental starts and electrocution. Lockout/tagout procedures should be followed.
- Protective Gear: Always wear appropriate personal protective equipment (PPE), including gloves, eye protection, and potentially a lab coat or apron. This protects against cuts, burns, and exposure to cleaning chemicals.
- Emergency Stop Buttons: Familiarize yourself with the location and operation of the emergency stop buttons. These buttons should be easily accessible and used immediately in case of any malfunction or emergency.
- Guards and Shields: Ensure all safety guards and shields are in place and functioning correctly before operating the machine. Never bypass or disable safety devices. These guards are designed to protect operators from moving parts and other hazards.
- Proper Training: Ensure all operators are properly trained on the machine’s operation, maintenance, and safety procedures. Training should cover potential hazards and how to respond to emergencies.
- Regular Inspections: Conduct regular inspections of the machine and its surroundings to identify and address any potential hazards. This includes checking for frayed wires, damaged components, and slippery surfaces.
- Material Handling: When handling packaging materials, be careful to avoid cuts or injuries. Store materials properly to prevent them from becoming a tripping hazard.
- Ventilation: Ensure adequate ventilation in the work area to prevent the buildup of fumes from cleaning agents or packaging materials.
- Authorized Personnel: Only authorized and trained personnel should operate or perform maintenance on the machine. Unauthorized access should be restricted.
- Report Issues: Report any malfunctions, safety concerns, or potential hazards immediately to the supervisor.
Innovations and Future Trends
The world of food wrapping is on the cusp of a revolution, driven by technological advancements and a growing demand for sustainability and convenience. As we look ahead, the industry is poised for exciting changes, promising not only enhanced efficiency but also a more responsible approach to food packaging. Let’s delve into the emerging trends shaping the future of food wrapping.
Automation and Smart Packaging
The drive toward automation is reshaping food wrapping processes, leading to increased efficiency and reduced labor costs. Simultaneously, smart packaging is emerging, offering exciting possibilities for enhancing product safety, extending shelf life, and providing valuable consumer information.
- Robotic Integration: Robotic arms are increasingly being used for tasks such as product loading, sealing, and palletizing. This automation reduces human error and increases throughput. For example, a major bakery chain has implemented robotic systems in its packaging lines, increasing production speed by 20% and reducing packaging material waste by 15%.
- Smart Sensors and Data Analytics: Packaging is becoming equipped with sensors that monitor temperature, humidity, and other factors that can affect food quality. This data is then analyzed to optimize storage conditions and predict spoilage. Some companies are using these sensors to provide real-time information to consumers about the freshness of the product via a smartphone app.
- Active Packaging: This involves packaging that actively interacts with the food to extend shelf life. Examples include oxygen scavengers that absorb oxygen to prevent spoilage, and antimicrobial films that inhibit the growth of bacteria. Research suggests that active packaging can extend the shelf life of fresh produce by up to 50% in some cases.
- RFID Technology: Radio-frequency identification (RFID) tags are used to track products throughout the supply chain, providing real-time visibility and improving inventory management. This technology is particularly useful for perishable goods, allowing for quick identification of products nearing their expiration date.
New Materials and Designs
Sustainability is a key driver of innovation in food wrapping, leading to the development of new materials and designs that minimize environmental impact. The focus is on reducing waste, increasing recyclability, and using renewable resources.
- Biodegradable and Compostable Materials: There is a growing shift toward using plant-based materials such as polylactic acid (PLA) and cellulose-based films. These materials break down naturally, reducing the burden on landfills. Several food companies are already using compostable packaging for items like coffee pods and fruit containers.
- Edible Films and Coatings: Research is underway to develop edible films and coatings made from ingredients like seaweed and proteins. These films can be applied directly to food products, reducing the need for traditional packaging. Edible coatings are being tested on fruits and vegetables to extend their shelf life and reduce food waste.
- Innovative Designs: Packaging designs are evolving to improve functionality and reduce material usage. This includes features like resealable closures, portion control packaging, and packaging that can be easily flattened for recycling.
- Modified Atmosphere Packaging (MAP): MAP technology continues to evolve, with new methods to control the gases within packaging to extend shelf life and maintain product quality. This includes the use of advanced gas mixtures and improved sealing techniques.
A futuristic food wrapping machine, envisioned in a sleek, stainless steel design, would be a marvel of automation. It would feature multiple robotic arms working in unison, handling delicate products with precision. Integrated sensors would constantly monitor the product’s condition and the packaging environment, adjusting parameters in real-time to optimize preservation. The machine would utilize advanced materials, including biodegradable films printed with embedded QR codes that link to detailed product information and even recipes. A built-in recycling system would separate and process packaging waste, minimizing environmental impact. The machine’s control panel would be a user-friendly touchscreen interface, allowing for easy customization and monitoring of the entire process. This machine wouldn’t just wrap food; it would be a complete food preservation and information delivery system, seamlessly integrated into the modern food supply chain.
Case Studies
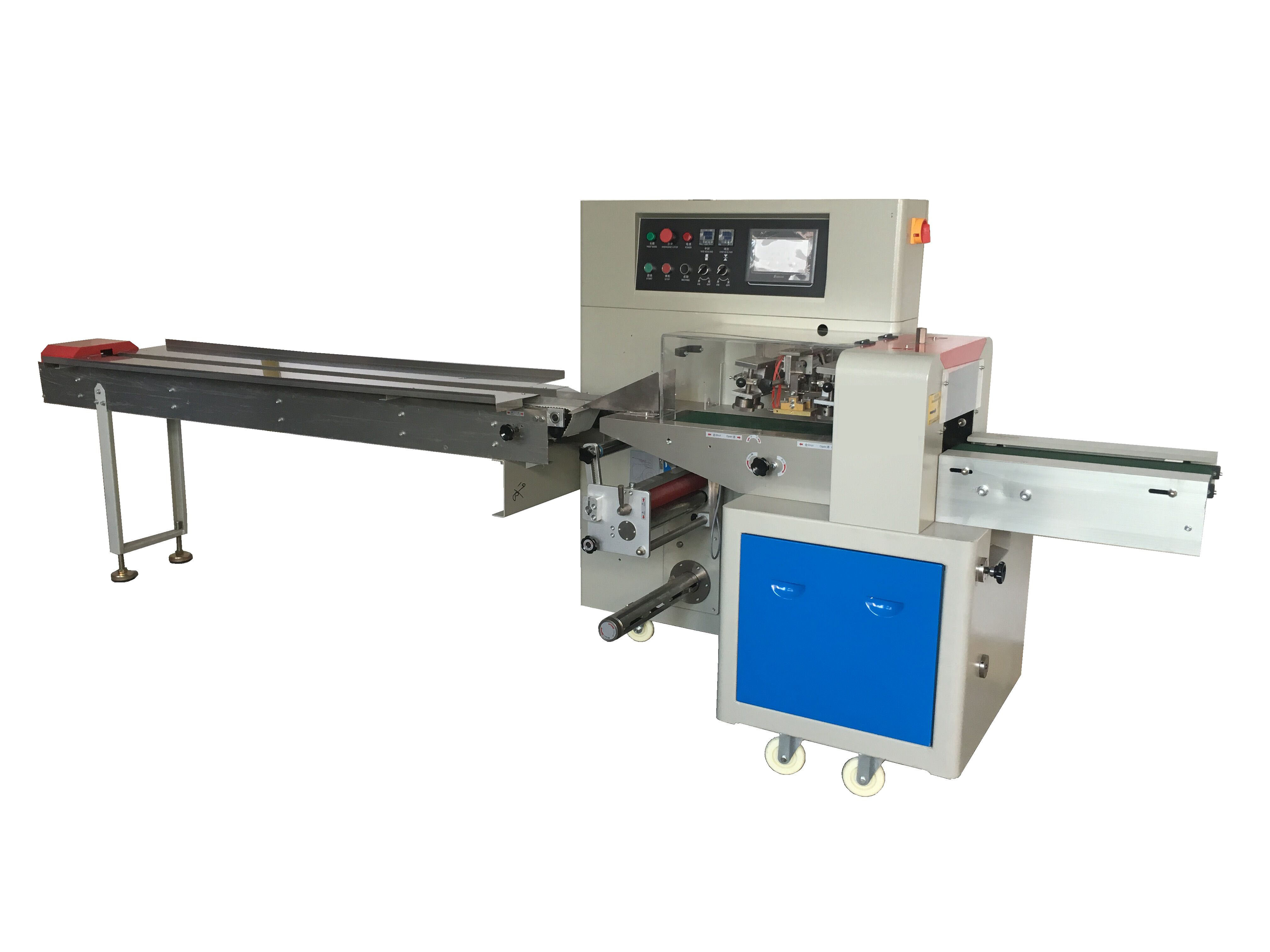
Let’s delve into the real-world impact of food wrapping machines. These case studies illuminate how strategic implementation and the right technology can revolutionize food processing, enhancing both operational efficiency and product excellence. We’ll explore two distinct scenarios, each showcasing a different facet of this transformative technology.
Successful Implementation in a Bakery: Enhancing Efficiency and Quality, Food wrapping machine
This case study highlights the transformation of “Golden Crust Bakery,” a medium-sized bakery specializing in artisan breads and pastries. Before implementing a food wrapping machine, the bakery relied on manual wrapping, a process that was labor-intensive, time-consuming, and inconsistent.To address these challenges, Golden Crust Bakery invested in a high-speed flow wrapping machine capable of handling various bread and pastry sizes.
The machine was specifically chosen for its versatility, allowing it to accommodate the bakery’s diverse product line. The implementation process involved careful integration with the existing production line, ensuring minimal disruption. The bakery also provided comprehensive training to its staff on the machine’s operation and maintenance.The positive impacts were significant:
- Increased Production Efficiency: The automated wrapping process dramatically increased the speed at which products were packaged. Manual wrapping, which took approximately 30 seconds per item, was reduced to a mere 5 seconds per item with the new machine. This resulted in a 600% increase in wrapping speed.
- Improved Product Quality: The machine provided consistent and airtight seals, extending the shelf life of the bakery’s products and reducing food waste. Products arrived to the customers in better condition.
- Reduced Labor Costs: The automation reduced the need for manual labor, freeing up employees to focus on other critical tasks, such as recipe development and quality control. The bakery was able to reallocate three employees to more value-added roles.
- Enhanced Brand Image: The professional and consistent packaging created a more appealing presentation, positively impacting the bakery’s brand image and attracting new customers.
Golden Crust Bakery’s success story is a testament to the transformative power of food wrapping machines. By investing in the right technology and proper training, the bakery significantly improved its operational efficiency, product quality, and overall profitability.
Benefits of a Specific Food Wrapping Solution: Modified Atmosphere Packaging (MAP) for Fresh Produce
This case study examines the implementation of a Modified Atmosphere Packaging (MAP) solution in a fresh produce processing facility, “Green Harvest Farms.” Green Harvest Farms specializes in pre-cut salads and vegetables. The primary challenge was maintaining the freshness and extending the shelf life of their delicate products.The facility adopted a MAP system integrated with a horizontal form-fill-seal machine. This system utilizes specific gas mixtures (typically oxygen, carbon dioxide, and nitrogen) within the packaging to slow down the respiration rate of the produce and inhibit microbial growth.
The system was meticulously calibrated to suit the specific needs of the various types of produce handled by Green Harvest Farms.The results were remarkable:
- Extended Shelf Life: The MAP system significantly extended the shelf life of the pre-cut salads and vegetables. For example, the shelf life of pre-cut lettuce increased from 5 days to 10 days, as verified through independent laboratory testing.
- Reduced Food Waste: By extending the shelf life, the MAP system drastically reduced food waste, both within the facility and throughout the supply chain. This resulted in significant cost savings and a positive environmental impact.
- Improved Product Quality: The controlled atmosphere environment preserved the color, texture, and nutritional value of the produce, resulting in a superior product for consumers. The salads remained crispier and more flavorful for a longer duration.
- Enhanced Market Reach: The extended shelf life enabled Green Harvest Farms to expand its market reach, distributing its products to more distant locations without compromising product quality. The company successfully entered new regional markets.
The success of Green Harvest Farms demonstrates the crucial role of specialized food wrapping solutions in maintaining product quality and minimizing waste. The implementation of MAP technology allowed the company to achieve significant operational and environmental benefits, while simultaneously providing consumers with fresher, higher-quality products.
Final Summary
From the gentle embrace of a flow wrapper to the robust seal of a tray sealer, the food wrapping machine is more than just a tool; it is a testament to human ingenuity. This intricate dance of mechanics, materials, and innovation is a vital component of the modern food industry. As we embrace sustainable practices and seek to minimize waste, the future of food wrapping promises even more advanced solutions.
With smart packaging, eco-friendly materials, and automated processes on the horizon, the food wrapping machine will continue to evolve, ensuring that the food we consume remains fresh, safe, and beautifully presented for generations to come.