Del Monte Foods Toppenish WA presents a compelling case study in food processing, economic impact, and community engagement. This presentation will explore the multifaceted operations of the Del Monte facility in Toppenish, Washington, analyzing its historical significance, current processes, and future prospects. The narrative will delve into the facility’s role in the local economy, its environmental footprint, and its influence on the agricultural landscape of the region.
Furthermore, it will examine the challenges and opportunities facing the plant, providing a comprehensive overview of this vital component of the food industry.
The analysis will encompass a detailed examination of the products manufactured, the technological infrastructure, and the labor practices employed. We will explore the intricacies of the canning process, the distribution networks, and the company’s commitment to sustainability. Moreover, a comparative analysis with competitors and a forward-looking perspective on future developments will be undertaken to provide a complete and nuanced understanding of Del Monte’s Toppenish operations.
Del Monte Foods Toppenish, WA
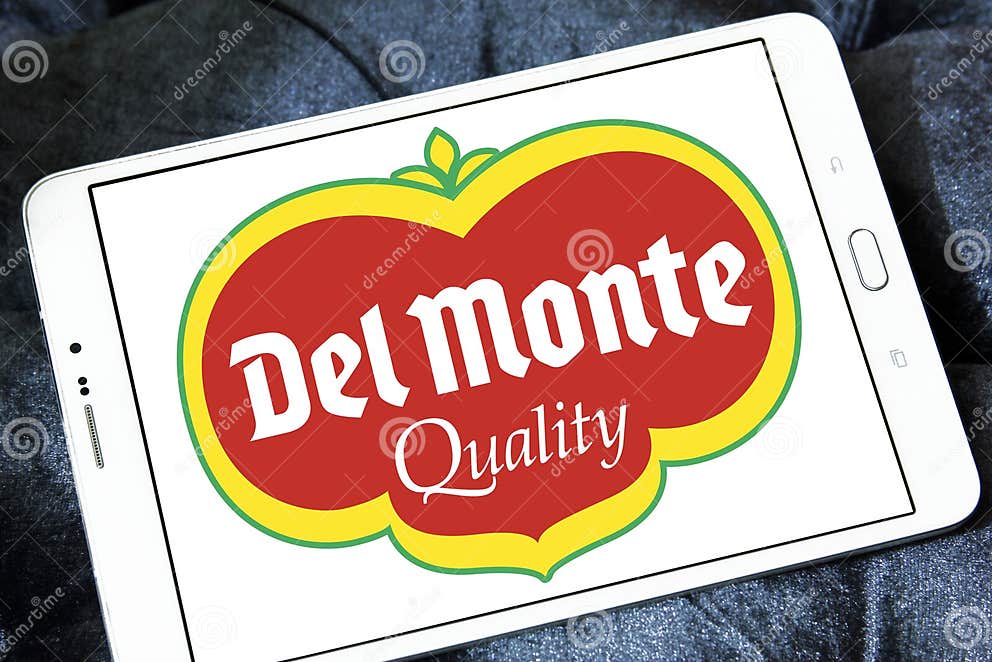
The sun-drenched fields of the Yakima Valley, a tapestry woven with the threads of agriculture, have long been a canvas for the enduring story of Del Monte Foods. Within this fertile landscape, the Toppenish facility stands as a testament to the company’s commitment to preserving the bounty of the land, transforming raw ingredients into shelf-stable staples. Its presence is more than just a factory; it’s an integral part of the community’s economic and social fabric, a place where generations have found employment and built their lives.
History of Del Monte in Toppenish
Del Monte’s roots in Toppenish run deep, mirroring the growth of the region’s agricultural prowess. The facility’s establishment marked a significant milestone, coinciding with the expansion of the area’s farming industry. This expansion was fueled by the availability of irrigation, fertile soil, and a climate conducive to growing a variety of crops. Del Monte saw the potential, recognizing the Yakima Valley as a prime location for processing the fruits and vegetables that would become synonymous with its brand.
The facility quickly became a central hub, processing everything from sweet corn to green beans, transforming them into products that would be enjoyed across the country and beyond.
Products Processed at the Toppenish Facility
The Toppenish facility is a bustling center of food processing, handling a diverse range of agricultural products. The facility focuses primarily on the canning and processing of vegetables.
- Green Beans: These are a cornerstone of the facility’s operations, with vast quantities processed during the harvest season. The beans, sourced from local farms, are carefully selected, trimmed, blanched, and canned to preserve their flavor and nutritional value.
- Sweet Corn: Another significant product, sweet corn, is harvested at its peak ripeness and quickly processed to ensure its sweetness and tenderness are retained. The kernels are either canned whole, creamed, or used in other Del Monte products.
- Peas: Like green beans and corn, peas are also a staple. They are processed with the same precision, ensuring the final product is of the highest quality.
- Other Vegetables: The facility also handles other vegetables, the exact mix varying depending on seasonal availability and market demand. This flexibility allows Del Monte to adapt to changing agricultural conditions and consumer preferences.
The meticulous processes, from field to can, are designed to maintain the quality and freshness of the ingredients. The facility’s commitment to food safety and quality control is paramount, ensuring that every product meets the rigorous standards expected of the Del Monte brand.
Significance to the Local Economy, Del monte foods toppenish wa
The Del Monte facility in Toppenish plays a crucial role in the local economy, providing employment and supporting related industries. The facility’s presence has a ripple effect, influencing various aspects of the community.
- Job Creation: The facility is a major employer in the area, offering a significant number of jobs. These jobs range from processing line workers to skilled maintenance personnel and management positions. The consistent employment opportunities provided by Del Monte contribute to the financial stability of numerous families in the region.
- Support for Local Farmers: Del Monte’s operations rely heavily on local farmers, creating a strong symbiotic relationship. The company provides a reliable market for the farmers’ produce, ensuring a consistent demand for their crops. This partnership helps to sustain the agricultural sector in the Yakima Valley.
- Economic Impact: The facility’s presence generates significant economic activity. This includes the purchase of raw materials, the use of local services, and the payment of taxes. The economic contributions help to fund public services and infrastructure improvements in the community.
- Community Involvement: Del Monte often participates in community events and supports local initiatives. This involvement strengthens the company’s ties with the community and demonstrates its commitment to the well-being of the region.
The presence of Del Monte in Toppenish highlights the crucial role of the food processing industry in supporting both the agricultural sector and the broader economy. The facility is not merely a place of production; it is a cornerstone of the community, providing jobs, supporting local farmers, and contributing to the economic vitality of the Yakima Valley.
Del Monte Toppenish
The Del Monte Foods plant in Toppenish, Washington, stands as a significant hub for agricultural processing in the Yakima Valley. Nestled amidst fertile farmlands, the facility transforms fresh produce into canned goods, contributing to the region’s economic vitality and providing consumers with access to shelf-stable fruits and vegetables. This segment delves into the operational intricacies of the Toppenish plant, focusing on the key agricultural products handled, the canning process, and the rigorous quality control measures employed.
Main Agricultural Products Processed
The Toppenish plant specializes in processing a variety of agricultural products sourced primarily from the surrounding Yakima Valley. These products are selected for their quality and suitability for canning.
- Peaches: Primarily clingstone peaches, known for their firm texture and ability to withstand the canning process, are a staple. The peaches are often packed in syrup or juice.
- Pears: Bartlett pears, prized for their sweet flavor and delicate texture, are another major product. They are prepared in a similar manner to peaches.
- Green Beans: Fresh green beans, both whole and cut, are processed, providing a convenient vegetable option for consumers.
- Corn: Sweet corn is another critical product, often canned as whole kernel or cream-style corn.
Canning Process at the Facility
The canning process at Del Monte’s Toppenish facility is a complex, multi-step operation designed to preserve the produce while maintaining its quality and safety.
- Harvesting and Receiving: The process begins with the harvesting of the agricultural products at their peak ripeness. Produce is transported to the plant and inspected upon arrival for quality and condition.
- Cleaning and Sorting: The produce undergoes thorough cleaning to remove dirt, debris, and any unwanted materials. Sorting ensures that only the highest quality items are selected for canning.
- Preparation: This step varies depending on the product. For peaches and pears, this involves peeling, pitting, and slicing. Green beans are trimmed and cut. Corn is husked and kernels are removed.
- Filling the Cans: Prepared produce is carefully filled into cans. Syrup, juice, or brine is added, depending on the product and desired end result.
- Exhausting: Air is removed from the cans to prevent corrosion and ensure a proper vacuum seal. This can be achieved through steam exhausting or by placing the cans in a hot water bath.
- Sealing: The cans are hermetically sealed, creating an airtight environment that prevents spoilage.
- Sterilization: The sealed cans are then subjected to high-temperature heat treatment in a retort or pressure cooker. This process destroys any microorganisms that could cause spoilage. The specific temperature and time vary depending on the product and can size, but the goal is to achieve commercial sterility. For example, the sterilization process might involve heating the cans to 240-250°F (116-121°C) for a specific duration, such as 30-60 minutes, depending on the product’s density and the can size.
- Cooling: After sterilization, the cans are rapidly cooled to stop the cooking process and prevent overcooking.
- Labeling and Packaging: The cooled cans are labeled with product information and packaged for distribution.
Quality Control Measures Employed
Del Monte places a strong emphasis on quality control throughout the entire production process at its Toppenish facility. This ensures the safety, consistency, and palatability of its canned products.
- Raw Material Inspection: Incoming produce undergoes rigorous inspection to assess quality, maturity, and freedom from defects. This includes visual inspection, grading, and testing for sugar content, firmness, and other relevant parameters.
- Process Monitoring: Continuous monitoring of critical control points (CCPs) is implemented throughout the canning process. This includes monitoring temperatures, pressures, and sealing integrity. Data loggers are used to track these parameters and ensure they remain within specified limits.
- Laboratory Analysis: Samples of raw materials, in-process products, and finished goods are routinely analyzed in the on-site laboratory. These analyses include testing for microbial contamination, pH levels, and nutrient content.
- Metal Detection: Metal detectors are used to identify and remove any metal fragments that might have entered the product during processing. This ensures consumer safety.
- Visual Inspection: Trained inspectors perform visual inspections of the canned products to identify any defects, such as dents, leaks, or improper seals. This visual inspection is done at several points, including after sealing and before labeling.
- Can Integrity Testing: Regular testing is conducted to ensure the integrity of the cans and the seals. This includes vacuum testing and pressure testing to identify any potential leaks.
- Shelf-Life Testing: Samples of finished products are stored under controlled conditions to assess their shelf life and ensure they remain safe and palatable for the duration specified on the label.
Del Monte Toppenish
The Del Monte Foods facility in Toppenish, Washington, serves as a significant production hub for a variety of canned and packaged fruit and vegetable products. This location’s strategic importance lies in its proximity to fertile agricultural lands and efficient transportation networks, enabling the company to process and distribute its products effectively. The following sections delve into the specific products likely manufactured in Toppenish, the distribution strategies employed, and the packaging utilized to deliver these goods to consumers.
Del Monte Toppenish: Products Likely Produced
Del Monte’s Toppenish plant is likely a key location for processing and canning a selection of fruits and vegetables. The region’s agricultural landscape, known for its fruit and vegetable production, allows Del Monte to source raw materials locally. This reduces transportation costs and ensures fresher ingredients for their products.
- Canned peaches: These are a staple Del Monte product, and Toppenish, with its access to peach orchards, is a likely production site. The peaches are processed, peeled, sliced, and canned in syrup or juice.
- Canned pears: Similar to peaches, pears are another fruit commonly canned by Del Monte. The processing involves peeling, coring, slicing, and canning in various liquid mediums.
- Canned green beans: Green beans are a widely consumed vegetable and are often processed at facilities like Toppenish. The beans are typically trimmed, cut, blanched, and canned.
- Canned corn: Corn is another staple vegetable. At Toppenish, the corn is likely shucked, cut from the cob, and canned.
- Canned fruit cocktail: This popular mix of fruits, including peaches, pears, cherries, grapes, and pineapple, is often assembled and canned at facilities like the one in Toppenish.
Del Monte Toppenish: Distribution Network
The distribution network for products manufactured in Toppenish is designed to move goods efficiently from the production facility to consumers across the United States and potentially internationally. This network leverages various transportation methods, including trucks, trains, and ships, to reach different markets.
Trucks are the primary mode of transportation for moving products from the Toppenish plant to distribution centers located throughout the country. These distribution centers act as hubs, receiving large quantities of products and then redistributing them to retail stores, grocery chains, and other outlets. For longer distances, especially to the East Coast or to areas that have established rail infrastructure, Del Monte might utilize rail transport, which is generally more cost-effective for large volumes.
The company also likely partners with logistics providers to manage warehousing and transportation, ensuring timely delivery and efficient inventory management. From distribution centers, products are delivered to retail stores, where consumers can purchase them. The distribution network also supports direct-to-consumer sales through online platforms, allowing consumers to order products directly from Del Monte. For example, if a large order needs to be delivered to a specific retail chain located far from the facility, the products are transported by rail to a distribution center near the retail chain.
From there, trucks take the product to the retail store.
Del Monte Toppenish: Packaging
Packaging plays a crucial role in protecting Del Monte products, preserving their quality, and attracting consumers. The Toppenish facility likely uses a variety of packaging materials, including cans and labels, to package its canned fruits and vegetables.
Cans: The primary packaging for most products from the Toppenish facility is metal cans. These cans are typically made of steel and are designed to withstand the heat processing required for canning. The cans are sealed to create an airtight environment, preventing spoilage and preserving the food’s freshness and shelf life. Cans are often coated internally with a food-grade lacquer to prevent any reaction between the food and the metal.
Labels: Each can is adorned with a label that includes essential information such as the product name, ingredients, nutritional information, net weight, and the Del Monte brand logo. The labels are typically made of paper or a similar material that is resistant to moisture and heat. The labels are printed with vibrant colors and appealing graphics to attract consumers on store shelves.
For instance, a can of peaches might feature a picture of ripe, juicy peaches, alongside the Del Monte logo and the words “Sliced Peaches in Light Syrup.” The packaging ensures the product’s safety, provides essential consumer information, and plays a significant role in brand recognition.
Del Monte Toppenish
The Del Monte Foods facility in Toppenish, Washington, a significant player in the agricultural landscape of the Yakima Valley, has a long-standing presence. This section delves into the environmental and social impacts of the Toppenish plant, examining its sustainability efforts, its influence on local resources, and its engagement with the community.
Del Monte’s Sustainability Initiatives at the Toppenish Facility
Del Monte Toppenish has implemented several sustainability initiatives aimed at reducing its environmental footprint. These efforts are driven by the company’s broader commitment to sustainable practices across its operations.
- Water Conservation: The facility employs water-efficient irrigation systems and wastewater treatment processes. Wastewater is often recycled for non-potable uses, minimizing the demand on freshwater resources.
- Energy Efficiency: Del Monte has invested in energy-efficient equipment and technologies, such as LED lighting and optimized refrigeration systems. These measures aim to reduce energy consumption and greenhouse gas emissions.
- Waste Reduction and Recycling: The Toppenish plant actively participates in waste reduction and recycling programs. This includes composting organic waste from the processing of fruits and vegetables and recycling materials such as cardboard, plastic, and metal.
- Sustainable Sourcing: Del Monte works with local farmers to promote sustainable agricultural practices. This includes encouraging the use of cover crops, reduced pesticide use, and other practices that protect soil health and biodiversity.
Impact of the Facility on Local Water Usage and Conservation Efforts
The Del Monte Toppenish facility, like any large agricultural processing plant, has a significant impact on local water resources. The company’s water usage is tied to both the processing of fruits and vegetables and the maintenance of its operations.
- Water Source: The facility primarily draws water from groundwater sources, as well as potentially from surface water sources, depending on the specific needs and permits.
- Water Usage in Processing: Water is used extensively in various stages of food processing, including washing, blanching, and cooling. Del Monte’s efforts to reduce water consumption include:
Recycling and reusing water within the facility.
- Wastewater Treatment: The facility has a wastewater treatment plant to treat the water used in processing before it is discharged. This treatment process removes pollutants and reduces the impact on local waterways.
- Conservation Efforts: Del Monte actively collaborates with local water authorities and participates in water conservation programs. These efforts may involve implementing water-efficient technologies and supporting initiatives aimed at managing water resources sustainably.
Comparison of Del Monte’s Community Involvement Programs in Toppenish with Similar Programs in Other Locations
Del Monte’s community involvement varies across its locations, reflecting the specific needs and priorities of each community.
- Toppenish Programs: In Toppenish, Del Monte’s community involvement often focuses on supporting local schools, youth programs, and food banks. The company may provide financial contributions, in-kind donations (such as food products), and employee volunteer hours.
- Comparison with Other Locations: In other locations, such as the company’s facility in Modesto, California, Del Monte may have similar community involvement programs, including educational initiatives and support for local non-profit organizations. The scale and focus of these programs may differ based on the size of the facility, the needs of the community, and the specific opportunities available.
- Employee Engagement: Employee volunteerism is a common element in Del Monte’s community involvement efforts across different locations. Employees are encouraged to participate in local events and projects, contributing to the well-being of the community.
- Focus Areas: Common areas of focus for Del Monte’s community involvement include:
Food security, supporting local food banks and initiatives to address hunger.
Education, providing scholarships, supporting school programs, and promoting agricultural education.
Health and wellness, supporting health-related programs and initiatives.
Del Monte Toppenish
The Del Monte Foods facility in Toppenish, Washington, is a significant employer in the Yakima Valley, a region deeply intertwined with agriculture. Its operations, focused on processing fruits and vegetables, create a dynamic employment landscape characterized by seasonal fluctuations and a strong connection to the local community. The facility’s labor practices, including its employment structure and interactions with labor unions, are crucial to understanding its impact on the region.
Employment and Labor Practices
Del Monte Toppenish provides a variety of job opportunities, reflecting the diverse needs of a large-scale food processing plant. These positions vary in skill level and duration, catering to both local residents and individuals seeking seasonal work.The types of jobs available include:
- Production Line Workers: These workers are primarily responsible for tasks such as sorting, cleaning, and packaging fruits and vegetables as they move along the processing lines. This is the most common type of employment at the facility, especially during peak seasons.
- Processing Equipment Operators: Skilled workers operate and maintain the machinery used for canning, freezing, and other processing methods. They require specialized training and experience.
- Maintenance and Repair Personnel: This group ensures the smooth operation of the facility by maintaining and repairing the equipment and infrastructure.
- Quality Control Inspectors: They monitor the quality of the product at various stages of the process, ensuring adherence to food safety standards and company specifications.
- Warehouse and Logistics Staff: They manage the storage and movement of raw materials, finished products, and packaging materials.
- Administrative and Management Staff: This includes positions in human resources, finance, and operations management, providing support and oversight for the facility’s operations.
The plant’s employment patterns are heavily influenced by the agricultural seasons. The peak processing season, often coinciding with the harvests of various crops, typically runs from late summer through early fall. During this period, the workforce significantly expands to accommodate the increased volume of produce.The typical seasonal employment pattern is:
- Peak Season (Late Summer to Early Fall): This is the period of highest employment, with the facility operating at full capacity. Large numbers of temporary workers are hired to handle the influx of fruits and vegetables.
- Shoulder Seasons (Spring and Late Fall): Employment levels are moderate, with some processing activities continuing and preparation for the upcoming peak season.
- Off-Season (Winter): Employment levels are at their lowest, with maintenance and repair activities taking place. Some permanent staff members remain employed.
Labor relations at the Del Monte Toppenish facility have been marked by union activity. The United Food and Commercial Workers International Union (UFCW) often represents the production and maintenance workers. Collective bargaining agreements are in place to address wages, benefits, and working conditions.Significant aspects of labor relations include:
- Union Representation: The UFCW represents a substantial portion of the workforce, negotiating contracts that establish the terms and conditions of employment.
- Collective Bargaining Agreements: These agreements Artikel wages, benefits, working hours, and grievance procedures.
- Past Labor Disputes: In the past, there have been instances of labor disputes, including strikes and work stoppages, related to contract negotiations. These disputes highlight the importance of fair labor practices and worker rights. For example, a strike in 2004 at a Del Monte plant in California, which also processed fruits and vegetables, resulted in improved wages and benefits for the workers.
Del Monte Toppenish
Del Monte Foods’ presence in Toppenish, Washington, represents a significant economic and agricultural component of the region. The facility, a cornerstone of the local food processing industry, contributes to employment, agricultural demand, and the overall vitality of the community. The following sections delve into the specifics of the facility’s infrastructure, offering a glimpse into its operational scale and technological sophistication.
Del Monte Toppenish: Facility Infrastructure
The Del Monte Toppenish facility is a sprawling complex designed to efficiently process and store large volumes of agricultural products. Its layout and operational systems are crucial to its ability to meet production demands and maintain product quality.
Facility Size and Layout
The Toppenish plant occupies a substantial footprint, indicative of its large-scale operations. The layout is strategically designed to optimize the flow of raw materials, the processing stages, and the final product packaging. The facility’s design reflects an emphasis on efficiency and minimizing the distance products travel during processing. Different areas are designated for specific functions, including receiving, washing, sorting, processing, canning/packaging, and warehousing.
The arrangement allows for a continuous flow of product, reducing bottlenecks and maximizing throughput. The location near agricultural fields is another critical element in its design, reducing transportation costs and ensuring the freshness of incoming produce.
Processing Plant Equipment and Technology
The Del Monte Toppenish plant employs advanced equipment and technology to ensure efficient and high-quality food processing. This includes a variety of machinery designed for specific tasks, such as:
- Automated Sorting Systems: These systems utilize optical scanners and sensors to identify and remove defective or substandard produce, ensuring that only the highest quality ingredients are used.
- High-Speed Processing Lines: The facility incorporates high-speed processing lines capable of handling vast quantities of produce. These lines are designed for efficient washing, cutting, cooking, and filling.
- Sterilization and Canning Equipment: The plant features advanced sterilization equipment, including retorts and autoclaves, to ensure the safety and shelf-stability of canned products. Canning lines are automated to maximize throughput and maintain product integrity.
- Robotic Systems: Robotic systems are integrated into various stages of the production process, including packaging and palletizing, to increase efficiency and reduce labor costs.
- Quality Control Systems: Throughout the process, sophisticated quality control systems are employed to monitor product parameters such as temperature, pressure, and fill levels, and to ensure that all products meet stringent quality standards.
Storage and Warehousing Capabilities
Del Monte Toppenish’s storage and warehousing capabilities are designed to accommodate large volumes of finished product, raw materials, and packaging supplies. The facility’s storage solutions include:
- Temperature-Controlled Warehouses: Large-scale, temperature-controlled warehouses are used to store finished canned goods. These warehouses maintain optimal temperatures to preserve product quality and extend shelf life.
- Raw Material Storage: Dedicated areas are allocated for the storage of raw materials, such as fresh produce, packaging materials, and ingredients. Proper storage is essential to prevent spoilage and maintain the quality of these materials.
- Automated Inventory Management: The facility utilizes automated inventory management systems to track product movement, manage stock levels, and optimize storage space utilization. This helps to minimize waste and ensure timely delivery of products.
- Shipping and Receiving Docks: Extensive shipping and receiving docks are designed to handle the efficient loading and unloading of trucks and railcars, ensuring a smooth flow of goods in and out of the facility.
Del Monte Toppenish
The Del Monte Foods facility in Toppenish, Washington, stands as a significant employer and economic driver in the Yakima Valley. Its continued success hinges on navigating a complex landscape of operational hurdles and embracing opportunities for growth. This section delves into the specific challenges and opportunities that shape the plant’s future, while also examining the looming impact of climate change.
Challenges Faced by Del Monte Toppenish
The Toppenish facility, like any large-scale food processing operation, faces a range of challenges that require constant attention and strategic solutions. These challenges can impact profitability, efficiency, and long-term sustainability.
Obtain direct knowledge about the efficiency of chinese food leominster ma through case studies.
- Labor Costs and Availability: Securing and retaining a skilled workforce is a persistent concern. Competition for labor within the agricultural and food processing sectors in the Yakima Valley is fierce, driving up wages and potentially impacting operational costs. The availability of seasonal labor, critical during harvest seasons, is also subject to fluctuations influenced by immigration policies and economic conditions.
- Supply Chain Disruptions: Global events and unforeseen circumstances can disrupt the supply chain. Delays in receiving raw materials, packaging, or spare parts can halt production and impact delivery schedules. The COVID-19 pandemic highlighted the fragility of global supply chains, emphasizing the need for robust contingency plans and diversified sourcing strategies.
- Maintaining Equipment and Infrastructure: The facility relies on aging equipment and infrastructure. Maintaining and upgrading these systems requires significant capital investment. Inadequate maintenance can lead to production downtime, reduced efficiency, and increased repair costs.
- Waste Management and Sustainability: Minimizing waste and implementing sustainable practices are essential. Food processing generates significant waste, including byproducts and wastewater. Managing these waste streams effectively, in compliance with environmental regulations, adds to operational costs. Implementing sustainable practices is not only environmentally responsible but also enhances the company’s reputation.
- Competition: The food processing industry is highly competitive. Del Monte Toppenish competes with other processing plants, both regionally and nationally, as well as with international producers. The ability to maintain competitive pricing, product quality, and efficient production processes is crucial for survival.
Opportunities for Expansion and Innovation
Despite the challenges, the Del Monte Toppenish facility possesses numerous opportunities for expansion and innovation, enabling it to strengthen its market position and ensure long-term viability.
- Product Diversification: Expanding the product line to include new fruit and vegetable varieties, value-added products (such as organic options or ready-to-eat meals), or private-label offerings could attract new customers and increase revenue streams. Market research is crucial to identify consumer preferences and emerging trends.
- Process Optimization: Investing in automation and advanced manufacturing technologies can improve efficiency, reduce labor costs, and enhance product quality. This includes implementing robotics for packaging, automated inspection systems, and data analytics to optimize production processes.
- Sustainable Practices: Embracing sustainable practices, such as reducing water consumption, minimizing waste, and utilizing renewable energy sources, can lower operational costs and enhance the company’s environmental profile. This can involve investing in water recycling systems, composting programs, and solar energy installations.
- Strategic Partnerships: Collaborating with local farmers, research institutions, and technology providers can foster innovation and create new opportunities. Partnering with local growers can ensure a reliable supply of high-quality raw materials. Collaborating with research institutions can facilitate the development of new processing techniques and product formulations.
- Geographic Expansion: Exploring opportunities to expand distribution networks and penetrate new markets can boost sales. This might involve establishing partnerships with new retailers or distributors, or expanding into international markets.
Impact of Climate Change on Operations
Climate change poses a significant threat to the long-term viability of the Del Monte Toppenish facility, particularly due to its reliance on agricultural inputs and water resources. The effects are already being felt, and future impacts are projected to intensify.
- Changes in Crop Yields and Quality: Rising temperatures, altered precipitation patterns, and increased frequency of extreme weather events, such as droughts and floods, can negatively affect crop yields and quality. This can lead to shortages of raw materials and increased production costs. For example, the 2021 heatwave in the Pacific Northwest severely impacted fruit harvests, highlighting the vulnerability of agricultural operations.
- Water Scarcity: Water is a critical resource for both agricultural production and food processing. Climate change is exacerbating water scarcity in the Yakima Valley, putting pressure on irrigation systems and potentially limiting the availability of water for processing. This can lead to increased water costs and necessitate water conservation measures.
- Increased Pest and Disease Pressure: Warmer temperatures and altered weather patterns can favor the proliferation of pests and diseases that affect crops. This can lead to increased crop losses and the need for more intensive pest management practices, which can impact costs and environmental sustainability.
- Infrastructure Damage: Extreme weather events, such as severe storms and floods, can damage the facility’s infrastructure, leading to production downtime and costly repairs. Strengthening infrastructure and implementing measures to mitigate the risks of extreme weather are crucial.
- Need for Adaptation and Resilience: Adapting to the impacts of climate change requires proactive measures. This includes investing in drought-resistant crop varieties, implementing water conservation strategies, and developing contingency plans to address disruptions caused by extreme weather events. Resilience requires a long-term commitment to sustainability and innovation.
Del Monte Toppenish
Del Monte Foods’ Toppenish facility, a significant player in the agricultural processing landscape, faces a complex competitive environment. Understanding its position relative to its rivals is crucial for assessing its performance and future prospects. This section delves into the comparative aspects of the Toppenish plant, examining its product offerings and marketing strategies in relation to its competitors.
Comparison of Del Monte Toppenish with Competitors’ Facilities
The Toppenish facility operates within a competitive landscape dominated by other large food processing companies. A comparative analysis highlights key differences in production capacity, product specialization, and geographic reach. The table below provides a simplified comparison.
Company | Facility Location (Example) | Primary Products | Distinguishing Features |
---|---|---|---|
Del Monte Foods | Toppenish, WA | Canned fruits, vegetables, sauces | Focus on vertically integrated supply chain; significant investment in sustainable practices. |
Conagra Brands | Various (e.g., Hunt’s facilities) | Canned tomatoes, sauces, meals | Extensive product diversification; strong presence in retail and foodservice. |
Seneca Foods | Various (e.g., Prosser, WA) | Canned vegetables, fruit juice | Largest processor of vegetables in North America; strong relationships with growers. |
Goya Foods | Various (e.g., New Jersey) | Canned beans, vegetables, sauces | Focus on Hispanic market; strong brand recognition and distribution network. |
Differentiation of Del Monte’s Product Offerings
Del Monte distinguishes itself through its product offerings in several key ways. These differentiations are critical for capturing market share and building brand loyalty. Del Monte’s product portfolio features a strong emphasis on quality and innovation.
- Brand Reputation: Del Monte has built a long-standing reputation for quality and trust, which translates into consumer loyalty. This is especially true for their canned fruit and vegetable products.
- Product Innovation: Del Monte continuously introduces new product variations, such as low-sodium options, organic lines, and fruit-infused water beverages, catering to evolving consumer preferences. This includes the introduction of products like Fruit Refreshers.
- Sustainable Practices: Del Monte emphasizes sustainable agriculture and sourcing, which appeals to environmentally conscious consumers. This involves initiatives like water conservation and reduced pesticide use.
- Vertical Integration: Del Monte often controls aspects of its supply chain, from sourcing raw materials to processing and distribution, enabling greater quality control and cost management.
Marketing Strategies Employed by Del Monte for Toppenish Products
Del Monte employs various marketing strategies to promote products manufactured at the Toppenish facility. These strategies are designed to reach target consumers and reinforce brand messaging. The core strategies include advertising, promotion, and public relations, all carefully tailored to specific product lines and target demographics.
- Advertising Campaigns: Del Monte utilizes television, print, and digital advertising to build brand awareness and promote its products. Campaigns often highlight the freshness, quality, and convenience of Del Monte products. For example, the use of celebrity endorsements or thematic commercials showcasing the nutritional value of canned goods.
- In-Store Promotions: Del Monte collaborates with retailers to offer in-store promotions, such as coupons, discounts, and product displays. These promotions aim to encourage consumers to purchase Del Monte products.
- Digital Marketing: Del Monte leverages digital channels, including social media, websites, and email marketing, to engage with consumers and promote its products. They often share recipes, nutritional information, and behind-the-scenes content to connect with their audience.
- Partnerships and Sponsorships: Del Monte forms partnerships with organizations and events to increase brand visibility. These partnerships include sponsoring health and wellness initiatives or collaborating with food bloggers.
- Emphasis on Origin: Marketing campaigns may highlight the Toppenish facility’s role in the production process, emphasizing the local sourcing and quality of the products. This can build a connection with consumers who value regional products.
Del Monte Toppenish
The Del Monte Foods plant in Toppenish, Washington, represents a significant economic presence in the Yakima Valley. Its future, however, hinges on strategic planning and adaptability within a rapidly evolving food industry. This section will explore the outlook for the Toppenish facility, considering planned investments, consumer preference adaptation, and long-term viability.
Planned Investments and Upgrades
Del Monte’s commitment to Toppenish’s future is demonstrated through its investment strategies. These investments are crucial for maintaining competitiveness and ensuring operational efficiency.
Investment in modern processing technologies is vital for the plant’s longevity.
- Modernization of Equipment: Investments may include replacing older machinery with more efficient and automated systems. This can encompass upgrades to canning lines, packaging equipment, and processing units, increasing output and reducing waste. For example, a switch to robotic palletizing systems could significantly speed up the packaging process.
- Sustainability Initiatives: Del Monte might invest in sustainable practices to align with consumer and regulatory pressures. This could include implementing water conservation technologies, adopting energy-efficient equipment, and exploring renewable energy sources, such as solar panels on the facility’s roof. The implementation of a closed-loop water system, where water used in processing is recycled and reused, is a good example.
- Facility Expansion: Depending on market demand, expansion of the physical plant may be considered. This could involve adding new processing lines or expanding storage capacity to accommodate increased production volumes. This expansion requires meticulous planning to minimize disruption to existing operations.
Adapting to Changing Consumer Preferences
Consumer preferences are in constant flux, and the Toppenish facility’s ability to adapt to these changes is crucial for its continued success.
Responding to the demand for healthier and more convenient food options is critical.
- Product Diversification: The plant might expand its product portfolio to include healthier options. This could mean increasing the production of low-sugar, organic, or plant-based products. For instance, they could introduce new varieties of canned fruits with no added sugar or develop ready-to-eat vegetable blends.
- Packaging Innovation: The facility could embrace innovative packaging solutions that cater to consumer demands for convenience and sustainability. This includes exploring the use of recyclable or compostable packaging materials, as well as smaller, single-serving options.
- Supply Chain Flexibility: A flexible supply chain allows the plant to respond quickly to changing consumer demands. This could involve diversifying sourcing options for raw materials, improving inventory management, and streamlining distribution channels. The ability to quickly switch between different fruit varieties or vegetable types based on consumer preferences is key.
Long-Term Viability of the Del Monte Plant in Toppenish
The long-term success of the Del Monte plant in Toppenish depends on several interconnected factors. Careful consideration of these factors will determine its future trajectory.
The plant’s future depends on strategic planning, efficient operations, and responsiveness to market trends.
- Economic Factors: The economic climate, including factors such as inflation, labor costs, and commodity prices, will significantly impact the plant’s profitability. The ability to manage these costs effectively is essential. For instance, hedging strategies can mitigate the impact of fluctuating raw material prices.
- Competition: The food processing industry is highly competitive. The Toppenish plant must maintain a competitive edge through operational efficiency, product innovation, and strong relationships with retailers. Continuous improvement is crucial.
- Regulatory Compliance: Adhering to evolving food safety regulations and environmental standards is essential. This includes maintaining certifications, implementing robust quality control measures, and adapting to new regulations. Maintaining compliance helps to preserve the plant’s reputation.
- Community Relations: Strong relationships with the local community are vital. This involves providing employment opportunities, supporting local initiatives, and minimizing environmental impact. Positive community relations can bolster the plant’s image and support its long-term sustainability.
Last Recap: Del Monte Foods Toppenish Wa
In conclusion, the examination of Del Monte Foods Toppenish WA reveals a complex and dynamic entity, deeply intertwined with the economic, environmental, and social fabric of the region. From its historical roots to its current operations and future projections, the facility exemplifies the challenges and opportunities inherent in the food processing industry. Understanding the intricacies of its operations, its impact on the community, and its ability to adapt to evolving circumstances is crucial for appreciating the long-term viability of the plant and its contribution to the broader food system.
The future of Del Monte in Toppenish will likely depend on its capacity for innovation, its commitment to sustainability, and its ability to navigate the ever-changing landscape of consumer preferences and environmental concerns.