Food shrink wrap, a silent guardian, envelops our sustenance in a veil of protection, a dance of material and sustenance. This seemingly simple innovation, born from a whisper of necessity, has reshaped the very landscape of our plates. It’s a journey into the heart of preservation, a story of how thin films of ingenuity safeguard the flavors, textures, and nutritional value of our meals.
From humble beginnings, food shrink wrap has evolved, embracing a multitude of materials, each with its own symphony of properties. PVC, polyolefin, and more, each contribute their unique verses to the song of freshness. The essence of shrink wrap lies in its ability to cling, to embrace, to create a barrier against the relentless march of time and the elements, extending the shelf life of our cherished edibles.
The process, a delicate ballet of heat and precision, transforms flat sheets into snug cocoons, ready to meet the discerning eye of the consumer. It’s a world of applications, from the butcher’s counter to the prepared meals aisle, each product benefiting from the invisible embrace of the shrink wrap.
Introduction to Food Shrink Wrap
Food shrink wrap, a seemingly simple innovation, acts as a guardian for the sustenance that nourishes us. Its primary function is to protect food products from spoilage, contamination, and damage, extending their shelf life and ensuring their safe transport and storage. In a world increasingly reliant on global food distribution, this technology plays a crucial role in minimizing waste and maximizing access to essential resources.
The Evolution of Food Shrink Wrap
The journey of food shrink wrap is a testament to human ingenuity and our relentless pursuit of efficiency. Its development mirrors advancements in materials science and packaging technology, evolving from rudimentary methods to sophisticated systems that meet the demands of a complex food supply chain.Early forms of food preservation involved methods like salting, drying, and smoking. These techniques, while effective to a degree, often altered the food’s texture and flavor.
The introduction of plastic films in the mid-20th century marked a significant turning point. Initially, these films were used primarily for wrapping individual items, offering a barrier against moisture and air. The discovery of polymers with the ability to shrink when heated revolutionized the industry.By the 1960s, the concept of shrink wrapping began to take hold, utilizing materials like polyvinyl chloride (PVC) and polyethylene (PE).
These early iterations offered improved protection and presentation compared to previous methods. Further advancements in the 1980s and beyond led to the development of more sophisticated films with enhanced barrier properties, clarity, and strength. The introduction of materials like polyethylene terephthalate (PET) and various co-polymer blends allowed for improved performance, meeting specific needs.
Different Types of Food Shrink Wrap Materials
A variety of materials are utilized in the production of food shrink wrap, each possessing unique properties that make them suitable for specific applications. The selection of the material depends on factors such as the type of food, desired shelf life, and the environmental conditions the product will encounter.
- Polyvinyl Chloride (PVC): PVC was one of the earliest and most widely used shrink wrap materials. It is known for its excellent clarity, shrink properties, and relatively low cost. However, concerns regarding its environmental impact and the potential for the release of plasticizers (additives used to make the plastic flexible) have led to a decline in its use in certain regions.
PVC is often used for wrapping fresh produce, meat, and baked goods.
- Polyethylene (PE): Polyethylene, particularly low-density polyethylene (LDPE) and linear low-density polyethylene (LLDPE), is a versatile and widely used material. It offers good shrink properties, tear resistance, and moisture barrier. PE is commonly used for wrapping frozen foods, poultry, and prepared meals. It’s a more environmentally friendly option than PVC.
- Polypropylene (PP): Polypropylene is another popular choice due to its clarity, high tensile strength, and excellent resistance to grease and oils. It is often used for wrapping food products where transparency and a glossy appearance are desirable, such as confectionery and snack foods.
- Polyethylene Terephthalate (PET): PET provides exceptional clarity, strength, and a good barrier against gases and moisture. It’s often used for products requiring a longer shelf life and is frequently found in pre-packaged meals and ready-to-eat foods. PET is a recyclable material.
- Polyolefin Films: These films, which include a variety of co-polymer blends, are becoming increasingly popular. They offer a balance of properties, including excellent shrink characteristics, high clarity, and good barrier properties. Polyolefin films are often used as a more sustainable alternative to PVC and are suitable for a wide range of food products. They also offer good sealing properties and can be used with various shrink-wrapping equipment.
The choice of shrink wrap material is a crucial decision, impacting both the product’s quality and its environmental footprint.
Materials and Properties
The journey of food shrink wrap is a journey into the heart of preservation, a testament to human ingenuity’s quest to extend life and minimize waste. Understanding the materials that make up this essential technology is crucial to appreciating its impact. It is through these materials and their inherent properties that the magic of shrink wrapping unfolds, transforming the mundane into the marvelously preserved.
Common Materials for Food Shrink Wrap
The selection of materials for food shrink wrap is not arbitrary; it is a carefully considered process, driven by the specific needs of the food being protected. Each material brings its unique blend of advantages and disadvantages, influencing the final product’s performance. These materials must meet rigorous standards for safety, clarity, and functionality.
- Polyvinyl Chloride (PVC): PVC has long been a staple in shrink wrap applications. It offers excellent clarity, making it ideal for showcasing the product within. However, its use has decreased in some regions due to environmental concerns.
- Polyolefin (PO): Polyolefin is a family of polymers, with the most common being polyethylene and polypropylene. Polyolefin is known for its versatility, offering excellent shrink properties and resistance to punctures. It is often considered a more environmentally friendly alternative to PVC.
Comparative Analysis of Materials
A deeper understanding of the advantages and disadvantages is facilitated by comparing the materials head-to-head. This comparative view allows for informed decisions based on the specific requirements of the food packaging application. The following table highlights the key differences:
Material | Advantages | Disadvantages | Applications |
---|---|---|---|
Polyvinyl Chloride (PVC) | High clarity, low cost, excellent shrink properties. | Environmental concerns regarding chlorine content, can release harmful fumes during sealing, less resistant to extreme temperatures. | Produce, baked goods, non-food items. |
Polyolefin (PO) | Environmentally friendlier, good tear resistance, excellent sealability, versatile shrink characteristics, suitable for food contact. | Higher cost compared to PVC, potentially less clarity depending on the formulation. | Meat, poultry, frozen foods, prepared meals, gift baskets. |
Properties of Shrink Wrap
The functionality of shrink wrap is not simply about the material; it is about the interplay of its properties. Clarity, strength, and sealability are not merely features; they are essential elements that contribute to the overall effectiveness of the packaging.
- Clarity: The ability to see the product is paramount. High clarity allows consumers to view the food, ensuring its visual appeal and demonstrating its freshness. A shrink wrap with good clarity enhances the product’s marketability.
- Strength: The shrink wrap must be strong enough to withstand handling, transportation, and storage. Tear resistance is crucial to prevent damage to the product. This is achieved by the molecular structure of the polymer, where the chains intertwine to create a robust barrier.
- Sealability: The ability to create a secure seal is essential to protect the food from contamination and extend its shelf life. The seal must be airtight to prevent the entry of oxygen and moisture.
Applications in Food Packaging: Food Shrink Wrap
The embrace of food shrink wrap extends far beyond the simple act of containment; it’s a transformative practice, a conscious act of preservation that resonates with the very essence of sustenance. It is a method that honors the inherent vitality of food, extending its journey and allowing us to partake in its bounty across time and distance. This application, a silent guardian, safeguards the integrity and freshness of what nourishes us, a testament to our dedication to minimizing waste and maximizing access to the gifts of the earth.
Diverse Applications Across Food Products
Food shrink wrap, in its multifaceted role, embraces a wide spectrum of food products, each benefiting from its protective embrace. Its versatility allows it to cater to the unique needs of diverse comestibles, from the delicate tenderness of fresh produce to the robust structure of prepared meals. This adaptability underscores its significance as a foundational element in modern food packaging.
- Meat and Poultry: Shrink wrap provides a tight, secure seal around meat and poultry products, preventing the growth of spoilage microorganisms. This protection is crucial, as it combats the degradation that occurs due to oxidation and microbial activity, maintaining the quality and safety of these protein-rich foods.
- Produce: Fruits and vegetables, with their delicate structures and inherent vulnerability to environmental factors, find refuge in shrink wrap. It helps to retain moisture, reducing wilting and maintaining crispness, while also guarding against bruising and physical damage during transport and handling. This ensures the vibrant colors and flavors of fresh produce reach the consumer intact.
- Prepared Meals: Pre-made meals, often complex in their composition, benefit significantly from shrink wrap. It provides a barrier against contamination, and maintains the integrity of the different components, ensuring that the carefully crafted flavors and textures remain as intended, offering convenience without compromising quality.
- Dairy Products: Cheeses and other dairy items, susceptible to moisture loss and bacterial growth, are effectively protected. The tight seal helps to preserve their freshness, preventing unwanted changes in texture and taste, thereby extending their shelf life and enhancing consumer enjoyment.
- Baked Goods: Shrink wrap safeguards the delicate textures of baked goods, preventing them from drying out and preserving their aroma. This also helps maintain their visual appeal, ensuring that consumers are presented with products that are both appetizing and fresh.
Extending Shelf Life
The extended shelf life afforded by food shrink wrap is a testament to its efficacy in slowing down the natural processes of food degradation. By creating a barrier against external factors, shrink wrap allows food products to retain their quality and safety for a longer duration, minimizing waste and increasing accessibility.
- Barrier Against Oxygen: Shrink wrap often acts as a barrier to oxygen, which is a primary cause of oxidation, leading to rancidity in fats and discoloration in meats. By limiting oxygen exposure, the wrap helps to maintain the flavor, color, and nutritional value of the food.
- Moisture Control: Shrink wrap helps to regulate moisture levels, preventing the loss of moisture from food products, especially fresh produce and baked goods. This helps to maintain their texture and prevent them from drying out. In other instances, it prevents the ingress of moisture, which can promote the growth of mold and bacteria.
- Protection from Contaminants: The tight seal created by shrink wrap forms a physical barrier against external contaminants, such as bacteria, dust, and other environmental factors. This protection helps to ensure the safety of food products, preventing spoilage and the spread of foodborne illnesses.
- Temperature Stability: Certain types of shrink wrap offer improved temperature stability, helping to maintain the cold chain for refrigerated or frozen foods. This is especially critical in maintaining the quality and safety of products during transportation and storage.
- Reduced Spoilage: By inhibiting the factors that lead to spoilage, shrink wrap plays a vital role in reducing food waste. This is a critical factor in promoting sustainability and addressing global food security challenges.
Shrink Wrap Process Diagram: Chicken Breast
The process of shrink wrapping a chicken breast is a carefully orchestrated sequence of steps designed to preserve freshness and maintain food safety. The following diagram illustrates each stage.
Step 1: Preparation
Description: The chicken breast is meticulously prepared, ensuring it is trimmed of excess fat and any unwanted parts. It is then carefully placed on a tray or platform suitable for shrink wrapping.
Illustration: A close-up view shows a perfectly trimmed chicken breast resting on a clear plastic tray, ready for the next step.
Step 2: Wrapping
Description: The prepared chicken breast and tray are enveloped in a sheet of shrink wrap film. The film is carefully positioned to ensure complete coverage, leaving no gaps.
Illustration: The chicken breast and tray are shown encased in a clear, transparent film, with excess film extending beyond the tray’s edges.
Step 3: Sealing
Description: The edges of the shrink wrap film are sealed together, creating an airtight enclosure. This step is crucial in preventing air and contaminants from entering the package.
Illustration: A close-up view shows the sealed edges of the shrink wrap, forming a secure, air-tight seal around the tray.
Step 4: Shrinking
Description: The sealed package is then subjected to heat, typically through a heat tunnel or with a heat gun. The heat causes the film to shrink tightly around the chicken breast and tray, conforming to its shape.
Illustration: The chicken breast is shown in a fully shrunk package, the film tightly adhering to the contours of the chicken and tray, resulting in a smooth, wrinkle-free appearance.
Step 5: Cooling and Inspection
Description: After shrinking, the package is allowed to cool. This step is followed by a thorough inspection to ensure the seal is intact and the package is free from defects.
Illustration: The packaged chicken breast is now completely shrink-wrapped, ready for distribution, and the clear film allows a full view of the product.
The Shrink Wrap Process
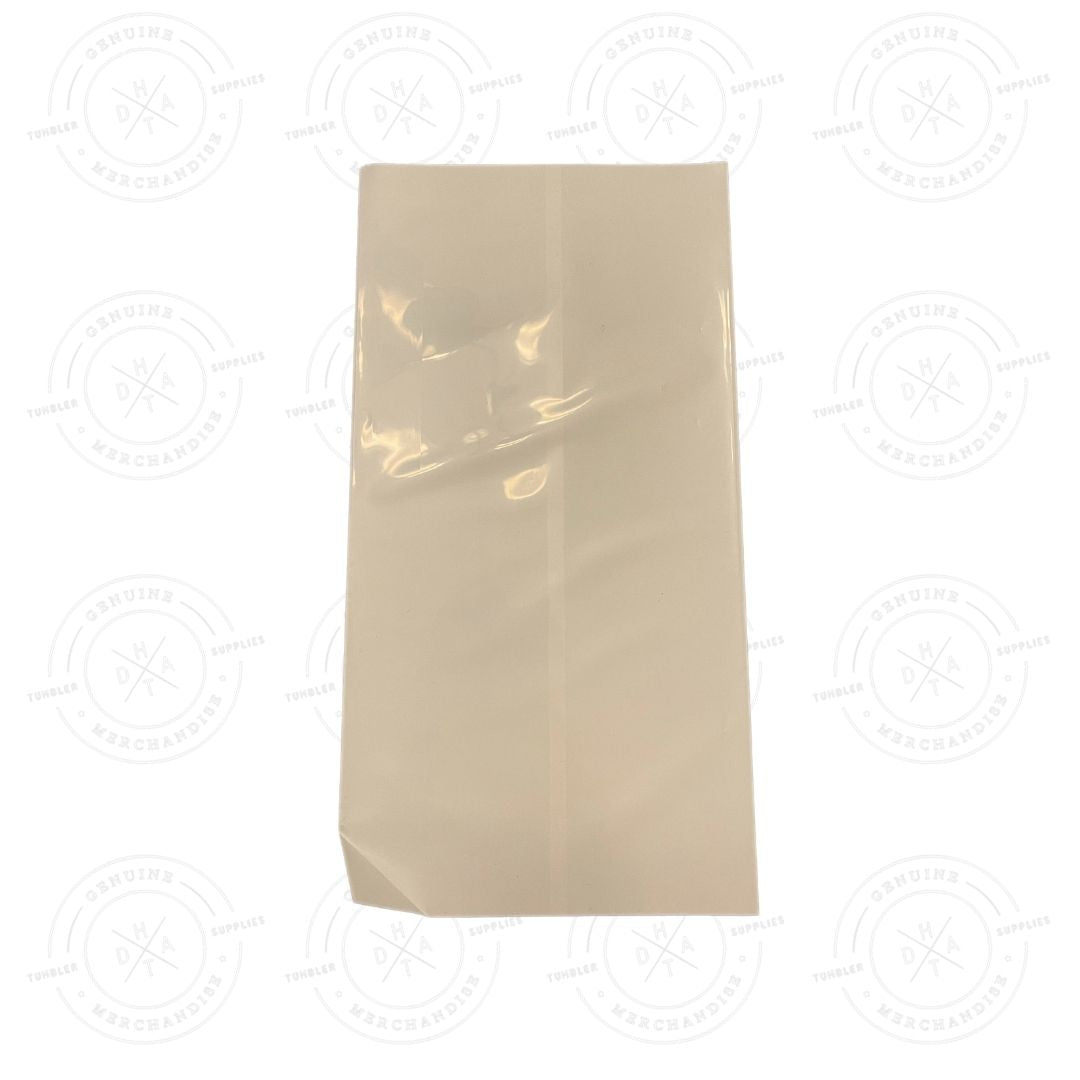
The journey of food shrink wrap, from its initial application to its final seal, is a testament to precision and control. This process, seemingly simple, is a delicate dance of heat, material, and product, ensuring the food within remains protected and preserved. Understanding the steps involved, the equipment utilized, and the best practices employed is paramount to achieving optimal results.
Steps in the Shrink Wrap Process
The following steps Artikel the typical sequence of actions involved in shrink wrapping food products. Each stage is crucial for achieving a secure and effective seal, guaranteeing product integrity.
- Product Preparation: This initial step encompasses the careful cleaning and arrangement of the food items. It involves ensuring the product is free from any contaminants that could affect the seal or the food’s safety. Products are often arranged on trays or in containers, ready for the next stage.
- Film Selection and Measurement: Choosing the correct shrink film is critical. The film must be the right size and type for the product. This involves determining the dimensions of the food item and selecting a film that provides a snug fit without being too tight, which could damage the product. Accurate measurements are vital for efficient film usage and minimizing waste.
- Sealing: This is where the shrink film is sealed around the product. The most common method uses an L-sealer. The product, encased in film, is placed on the sealing surface. The L-sealer uses a heated wire to cut and seal the film simultaneously, creating a three-sided seal. The excess film is then trimmed.
- Shrinking: This stage involves exposing the sealed package to heat. This is typically achieved using a heat tunnel. The tunnel’s temperature and dwell time (the time the package spends inside) are carefully controlled. The heat causes the film to shrink tightly around the product, conforming to its shape and creating a secure seal.
- Cooling: After shrinking, the package is cooled to allow the film to fully set. This step helps the film maintain its shape and prevents the seal from weakening. The cooling process often involves air-cooling or the use of cooling conveyors.
- Inspection: The final step involves a thorough inspection of the wrapped product. This includes checking the seal for integrity, ensuring the film is properly shrunk, and verifying the overall appearance of the package. Any defective packages are removed and either re-wrapped or discarded.
Shrink Wrap Equipment
The equipment used in the shrink wrap process varies depending on the scale of operation and the type of food product. Two primary types of equipment are crucial: sealers and heat tunnels.
L-Seal Sealers: These are among the most common types of sealers. They get their name from the shape of the sealing arm, which resembles an “L.” The product, encased in film, is placed on the sealing surface. The L-sealer uses a heated wire to cut and seal the film simultaneously, creating a three-sided seal. The excess film is then trimmed. L-sealers are suitable for various applications, including wrapping trays of fruits, vegetables, and other food items.
Heat Tunnels: These machines are the heart of the shrinking process. They use controlled heat to shrink the film tightly around the product. Heat tunnels come in different sizes and configurations, ranging from small, tabletop models to large, automated systems. The temperature and dwell time inside the tunnel are adjustable to suit different types of film and products. For example, a heat tunnel used for wrapping poultry might operate at a higher temperature and longer dwell time than one used for wrapping delicate pastries.
Best Practices for Effective and Safe Shrink Wrapping
Adhering to best practices is crucial for ensuring both the effectiveness and safety of the shrink-wrapping process. This includes careful selection of materials, proper equipment operation, and rigorous hygiene protocols.
- Film Selection: Always choose the appropriate shrink film for the food product. Consider factors like the product’s shape, size, and sensitivity to heat. Use films specifically designed for food packaging, as they are typically food-grade and meet the necessary safety standards.
- Temperature Control: Precisely control the temperature of the heat tunnel. Excessive heat can damage the product or the film, while insufficient heat may not shrink the film adequately. The ideal temperature depends on the film type and the product being wrapped.
- Seal Integrity: Ensure the seals are strong and airtight. Regularly inspect the seals for any defects. A weak seal can compromise the product’s protection and lead to spoilage. Use proper sealing techniques and maintain the sealing equipment in good working order.
- Ventilation: Ensure adequate ventilation in the work area. Some shrink films can release fumes when heated, so proper ventilation is essential for the safety of the operators. This is particularly important in enclosed spaces.
- Hygiene: Maintain strict hygiene standards throughout the process. This includes cleaning and sanitizing all equipment, ensuring the work area is clean and free of contaminants, and wearing appropriate protective gear, such as gloves and hairnets.
- Training: Provide comprehensive training to all operators. Training should cover equipment operation, film selection, temperature control, hygiene protocols, and safety procedures. Well-trained operators are crucial for consistent and safe shrink wrapping.
- Equipment Maintenance: Regularly maintain and inspect the shrink-wrapping equipment. This includes cleaning, lubricating, and replacing worn parts. Proper maintenance ensures the equipment operates efficiently and safely, and it extends the lifespan of the equipment.
Benefits of Using Food Shrink Wrap
The embrace of food shrink wrap offers a multitude of advantages, weaving a tapestry of benefits that enhance product preservation, presentation, and economic viability. It’s a testament to the human ingenuity in balancing the needs of commerce, consumption, and the environment, providing a path toward a more efficient and sustainable food system.
Product Protection and Presentation
Food shrink wrap serves as a vigilant guardian, shielding perishable items from the ravages of the external world. It is a transparent barrier, an invisible yet potent shield, that significantly extends shelf life and maintains the integrity of the product.* It creates a tamper-evident seal, bolstering consumer confidence and safety. This is particularly crucial for products where the slightest breach can compromise quality and lead to potential health risks.
- Shrink wrap minimizes moisture loss, preserving the natural textures and flavors of food. Imagine a perfectly ripe avocado, shielded from the drying effects of air, maintaining its creamy consistency and rich taste.
- It provides a barrier against contaminants, protecting food from bacteria, dust, and other external elements. This safeguard is essential in maintaining food safety standards and reducing the risk of spoilage.
- Shrink wrap enhances product presentation, giving a professional and appealing appearance. The tight, form-fitting wrap highlights the product’s shape and color, making it more attractive to consumers.
- It offers an effective method for bundling multiple items together, streamlining packaging and facilitating handling. Consider a package of pre-portioned cheese slices, neatly arranged and easily accessible.
Economic Benefits
Beyond product protection, food shrink wrap contributes to substantial economic advantages, positively impacting both producers and consumers. Its role extends beyond mere packaging, becoming a crucial element in minimizing waste and reducing costs.* Reduced food waste is a significant economic benefit. By extending shelf life and protecting against spoilage, shrink wrap decreases the amount of food that ends up discarded, saving both producers and consumers money.
According to the Food and Agriculture Organization of the United Nations, approximately one-third of all food produced for human consumption is lost or wasted globally, which translates to an estimated $1 trillion in economic losses.
- Lower transportation costs are another key advantage. The secure packaging provided by shrink wrap minimizes damage during shipping, reducing the need for replacements and lowering insurance premiums. This is particularly relevant for fragile or irregularly shaped items, like delicate pastries or irregularly shaped fruits.
- Optimized storage space is achieved through the compact packaging that shrink wrap provides. Products can be stacked more efficiently, maximizing the use of warehouse and retail space. This efficiency translates into reduced storage costs.
- Increased product visibility enhances sales potential. The clear, form-fitting wrap allows consumers to easily view the product, encouraging impulse purchases and boosting overall sales.
- Improved inventory management is facilitated by the clarity and labeling capabilities of shrink wrap. Clear labeling and easy identification of products streamline inventory control, reducing errors and waste.
Environmental Impact and Sustainable Alternatives
The environmental impact of food shrink wrap warrants careful consideration. While it offers undeniable benefits, it also presents environmental challenges that demand innovative solutions. The challenge lies in balancing the advantages of food preservation with the need for environmental stewardship.* The environmental impact of food shrink wrap primarily stems from the use of plastics, which are often derived from fossil fuels.
The production, use, and disposal of these plastics contribute to greenhouse gas emissions and pollution.
- The disposal of shrink wrap can lead to plastic waste accumulation in landfills and oceans, posing a threat to wildlife and ecosystems. The persistent nature of plastic means it can take hundreds of years to decompose, contributing to long-term environmental damage.
- The recycling of shrink wrap can be challenging due to its composition and potential contamination with food residues. This limits the opportunities for recycling and contributes to waste.
To mitigate the environmental impact, sustainable alternatives are being developed and implemented.
Biodegradable shrink wrap
Made from plant-based materials, this type of shrink wrap breaks down naturally, reducing waste accumulation. Research and development in this area are ongoing, with companies exploring various biodegradable polymers.
Compostable shrink wrap
Designed to break down in industrial composting facilities, this option offers a sustainable end-of-life solution for the packaging material.
Recycled content shrink wrap
Incorporating recycled plastics into the manufacturing process reduces the demand for virgin materials and minimizes the environmental footprint.
Reduced plastic usage
Optimizing the thickness and design of shrink wrap can minimize the amount of plastic used without compromising its protective properties.
Reusable packaging systems
Exploring reusable packaging options, such as containers and wraps that can be cleaned and reused, can significantly reduce waste generation.
Regulations and Safety
The journey of food shrink wrap, from creation to its final embrace of sustenance, is guided by a tapestry of regulations and safety protocols. These standards ensure that the packaging, the guardian of our nourishment, remains a silent protector, free from the taint of harm and compliant with the laws of wellness. The pursuit of purity in food packaging is a sacred endeavor, a constant vigil against potential contamination.
Enhance your insight with the methods and methods of indian wedding food.
Food Safety Regulations and Standards
The use of food shrink wrap is subject to a complex web of regulations designed to safeguard public health. These regulations dictate the materials that can be used, the manufacturing processes employed, and the overall safety of the final product.
The core principle underlying these regulations is the protection of the consumer from any potential harm posed by the packaging material itself.
Several key regulatory bodies and standards play a crucial role:
- The Food and Drug Administration (FDA) in the United States: The FDA regulates food contact materials, including shrink wrap, under the Federal Food, Drug, and Cosmetic Act. This includes setting standards for the composition of the film, the additives used, and the overall safety of the packaging. The FDA requires that food packaging materials be “safe for their intended use,” meaning that they must not transfer any substances to the food that could be harmful.
- European Union (EU) Regulations: The EU has comprehensive regulations for food contact materials, including plastic packaging. These regulations, such as Regulation (EC) No 1935/2004, establish general safety requirements for all food contact materials and articles. Specific regulations, like those concerning plastic materials (Regulation (EU) No 10/2011), set limits on the migration of substances from the packaging into the food. These regulations are designed to protect human health and ensure fair trade practices.
- The Canadian Food Inspection Agency (CFIA): The CFIA is responsible for enforcing food safety regulations in Canada, including those related to food packaging. The agency assesses the safety of food contact materials and ensures that they meet the necessary standards.
- International Standards: Organizations such as the International Organization for Standardization (ISO) develop international standards for food packaging materials. While these standards are not legally binding, they provide a framework for best practices and can be used by manufacturers to demonstrate their commitment to quality and safety.
Certifications for Food-Grade Shrink Wrap
Obtaining certifications is a critical step for shrink wrap manufacturers to demonstrate compliance with food safety regulations and build trust with consumers and retailers. These certifications provide independent verification that the packaging materials meet the required standards.The most relevant certifications include:
- FDA Compliance: For shrink wrap sold in the United States, manufacturers must demonstrate compliance with FDA regulations. This often involves providing documentation and test results to show that the materials and additives used are approved for food contact.
- EU Compliance: For shrink wrap sold in the EU, manufacturers must comply with EU regulations, including Regulation (EC) No 1935/2004 and Regulation (EU) No 10/2011. This requires adherence to migration limits and the use of approved substances.
- ISO Certifications: ISO certifications, such as ISO 9001 (quality management) and ISO 22000 (food safety management systems), demonstrate that a manufacturer has implemented robust systems to ensure consistent quality and food safety. ISO 22000 certification is a particularly important indicator of a manufacturer’s commitment to food safety.
- Other Certifications: Depending on the specific application and market, other certifications may be relevant. These can include certifications for specific materials, such as those related to the use of recycled content, or certifications for environmental sustainability.
Importance of Proper Handling and Storage
The integrity of food shrink wrap, and therefore the safety of the food it protects, hinges not only on its initial manufacture but also on its handling and storage. Proper practices are essential to prevent contamination and maintain the film’s protective properties.The following are key considerations:
- Storage Environment: Shrink wrap should be stored in a clean, dry, and well-ventilated environment, away from direct sunlight, extreme temperatures, and potential sources of contamination. Temperature fluctuations can affect the film’s properties, while exposure to contaminants can compromise its safety.
- Handling Practices: Handling shrink wrap should be done with clean hands and in a manner that minimizes the risk of contamination. Protective gloves should be worn to prevent the transfer of oils, dirt, or other substances from the hands to the film. The use of sharp objects near the film should be avoided to prevent tears or punctures.
- Inventory Management: Implementing a “first-in, first-out” (FIFO) inventory system is crucial to ensure that older stock is used before newer stock. This helps to prevent the degradation of the film over time and minimizes the risk of using outdated or compromised packaging.
- Inspection: Regularly inspecting the shrink wrap for any signs of damage, such as tears, punctures, or discoloration, is essential. Damaged film should be discarded immediately to prevent it from being used for food packaging.
Choosing the Right Shrink Wrap
The journey of selecting the perfect shrink wrap is akin to choosing the right garment for the soul – it must fit perfectly to protect and reveal the inner beauty. It’s a process of mindful discernment, ensuring the chosen wrap aligns with the food’s essence and the intended purpose, much like a yogi selects a posture to enhance their energy flow.
This section guides you through the art of selecting the most suitable shrink wrap, considering factors that resonate with the food’s inherent nature and the practicalities of its journey from creation to consumption.
Factors for Selecting Shrink Wrap
Choosing the right shrink wrap involves understanding the food product’s characteristics and the environment it will encounter. It’s a holistic approach, much like assessing the five elements to achieve balance.
- Food Type: The composition of the food dictates the appropriate shrink wrap. Consider the fat content, acidity, and moisture level. For instance, high-fat foods may require specific barriers to prevent rancidity, while acidic foods necessitate wraps resistant to degradation.
- Shelf Life: The desired longevity of the product impacts the selection. A longer shelf life necessitates superior barrier properties to inhibit oxygen and moisture permeation.
- Packaging Environment: Consider the storage and transportation conditions. Exposure to temperature fluctuations, sunlight, and potential physical stress requires a durable and protective wrap.
- Packaging Equipment: The type of shrink wrap machine dictates the film type and thickness. Compatibility between the film and the machine is crucial for efficient and effective sealing.
- Product Aesthetics: The clarity and gloss of the shrink wrap influence the product’s visual appeal. The wrap should showcase the food’s inherent beauty, attracting the consumer’s eye.
- Sustainability: Increasingly, environmentally conscious consumers and regulations favor sustainable options. Consider recyclable or biodegradable shrink wrap alternatives.
Shrink Wrap Gauges and Applications
The gauge, or thickness, of shrink wrap is a critical factor, much like the layers of an onion protecting its core. Different gauges offer varying levels of protection and suitability for different applications.
- Thin Gauges (45-60 gauge): These are often used for lightweight products, such as individual portions or smaller items. They provide a good balance of cost-effectiveness and clarity. Think of a delicate wrapping for a single, perfect fruit.
- Medium Gauges (75-90 gauge): Suitable for a broader range of products, offering enhanced protection against punctures and tears. This is like a protective layer for a collection of pastries, ensuring their integrity during transport.
- Thick Gauges (100 gauge and above): Ideal for heavier items or products requiring superior protection, such as multiple items bundled together or products with sharp edges. Imagine the robust shielding required for a box of frozen goods, safeguarding them from freezer burn.
Consider the example of a bakery:
A bakery producing individual croissants might opt for a thinner gauge for cost efficiency and visual appeal. However, if they are packaging a dozen croissants together for wholesale distribution, a thicker gauge would be essential to prevent damage during transit and ensure product integrity.
Key Features for Shrink Wrap Machines
Selecting the right shrink wrap machine is akin to choosing the right tool for sculpting – it should be efficient, precise, and aligned with your production needs. The machine’s features are the tools of the trade.
- Sealing Capabilities: The machine’s sealing mechanism should be robust and capable of creating airtight seals. Consider the type of sealing required (impulse, continuous) and the maximum seal length.
- Shrink Tunnel Efficiency: The shrink tunnel should provide consistent heat distribution to ensure uniform shrinking. Adjustable temperature and airflow settings are essential for different film types and product sizes.
- Production Speed: The machine’s throughput capacity should align with your production volume. Consider the speed of the sealing and shrinking cycles.
- Automation Features: Automated features, such as product feeding and discharge systems, can significantly enhance efficiency and reduce labor costs.
- Ease of Use and Maintenance: The machine should be user-friendly and easy to maintain, with readily available parts and support.
- Safety Features: Ensure the machine incorporates safety features, such as emergency stops and protective guards, to prevent accidents.
Common Problems and Solutions
The path of food shrink wrap, like any endeavor, is not without its shadows. Obstacles arise, testing the resolve of the practitioner and the integrity of the process. These challenges, however, are not roadblocks, but rather opportunities for deeper understanding and refinement. By embracing these difficulties, we cultivate a more resilient and effective approach to preserving the sacred nourishment we consume.
Seal Failure and Film Tears
Seal failure and film tears represent the most common disruptions in the shrink wrapping journey. These imperfections can compromise the protective barrier, potentially leading to contamination and spoilage. Understanding the root causes and implementing corrective measures is crucial for maintaining the integrity of the process.There are several contributing factors to seal failure, each demanding careful consideration:
- Improper Seal Temperature: If the sealing temperature is too low, the film may not adequately fuse. Conversely, excessive heat can cause the film to melt or distort, weakening the seal. Achieving the correct temperature is paramount for a robust and reliable bond.
Example: A food packaging facility noticed an increase in seal failures when the ambient temperature dropped during winter.
Adjusting the sealing temperature upward, after careful testing, resolved the issue, ensuring consistent seal integrity.
- Contamination of the Seal Area: Any presence of food particles, grease, or moisture on the sealing surface can impede the film’s ability to bond effectively. Maintaining a clean sealing environment is essential.
Example: A bakery experienced seal failures in their shrink-wrapped pastries due to flour dust accumulating on the sealing jaws.
Implementing a regular cleaning schedule for the sealing equipment eliminated the problem.
- Inconsistent Pressure: Insufficient or uneven pressure during the sealing process can lead to weak seals. Ensuring uniform pressure across the sealing surface is vital.
Example: A packaging company found that worn-out sealing jaws caused inconsistent pressure, resulting in seal failures. Replacing the jaws restored consistent seal quality.
- Film Incompatibility: Not all shrink films are created equal. Using an incompatible film with the sealing equipment can lead to poor sealing performance. Selecting the appropriate film type is critical.
Example: Switching to a cheaper, less durable film led to frequent seal failures in a meat processing plant.
Returning to the original film formulation immediately improved the seal reliability.
Film tears, another common ailment, can stem from several causes:
- Incorrect Film Selection: Choosing a film that is too thin or not designed for the specific application can lead to tearing during the shrinking process.
Example: A frozen food manufacturer experienced frequent film tears when using a lightweight film on products with sharp edges.
Switching to a more robust film specifically designed for frozen applications resolved the issue.
- Improper Shrink Tunnel Settings: Excessive heat or insufficient airflow within the shrink tunnel can cause the film to tear. Optimizing the tunnel settings is essential.
Example: A produce packaging facility found that increasing the airflow in the shrink tunnel eliminated film tears, improving packaging efficiency.
- Product Sharp Edges: Products with sharp corners or edges can easily puncture or tear the film. Ensuring the product is properly oriented or protected is crucial.
Example: A company packaging cardboard boxes found that sharp corners were causing film tears. Adding corner protectors resolved the issue, improving packaging efficiency and reducing waste.
- Equipment Malfunction: Faulty equipment, such as a malfunctioning sealing blade or shrink tunnel components, can contribute to film tears. Regular equipment maintenance is vital.
Example: A packaging facility found that a worn-out sealing blade was causing film tears. Replacing the blade immediately improved the seal quality and reduced waste.
Troubleshooting Shrink Wrap-Related Problems
Addressing problems in the shrink-wrapping process demands a systematic approach. Identifying the source of the issue, implementing corrective actions, and continuously monitoring the results are crucial for achieving optimal performance.Here’s a structured approach to troubleshoot common shrink-wrap issues:
- Identify the Problem: Clearly define the specific issue. Is it seal failure, film tears, or something else? Observe the problem closely to determine its nature. Document the frequency and severity of the issue.
- Inspect the Equipment: Check the sealing equipment, shrink tunnel, and any related machinery for any obvious malfunctions or wear and tear. Ensure all components are functioning correctly.
- Examine the Materials: Verify the type and quality of the shrink film being used. Check for any signs of damage or defects in the film. Confirm that the film is compatible with the equipment and the product being packaged.
- Review the Process Parameters: Assess the sealing temperature, pressure, and dwell time. Optimize the shrink tunnel settings, including temperature, airflow, and conveyor speed.
- Test and Adjust: Make incremental adjustments to the equipment settings and observe the results. Document each adjustment and its effect on the packaging process.
- Implement Corrective Actions: Based on the findings, implement the necessary corrective actions. This may involve replacing worn-out parts, adjusting settings, or selecting a different film type.
- Monitor and Evaluate: Continuously monitor the packaging process to ensure that the problem is resolved and does not recur. Track key performance indicators (KPIs) to measure the effectiveness of the corrective actions.
Proper Storage and Maintenance of Shrink Wrap Materials and Equipment
The longevity and effectiveness of shrink wrap materials and equipment depend on proper storage and maintenance. This ensures optimal performance, minimizes waste, and extends the lifespan of the equipment.Proper storage of shrink wrap materials is essential:
- Temperature Control: Store shrink film in a cool, dry environment, away from direct sunlight and extreme temperatures. Maintaining a consistent temperature helps preserve the film’s properties.
Example: A packaging warehouse found that storing film near a loading dock, exposed to fluctuating temperatures, caused the film to become brittle and prone to tearing.
Relocating the film to a climate-controlled storage area solved the problem.
- Humidity Control: Protect the film from excessive moisture. High humidity can degrade the film and affect its sealing characteristics.
Example: A packaging facility found that storing film in a humid warehouse led to seal failures. Using a dehumidifier in the storage area solved the problem.
- Protection from Sunlight: Avoid exposing the film to direct sunlight, as UV rays can degrade the film’s properties.
Example: A company noticed that film stored near a window became discolored and lost its shrink properties. Storing the film in a dark area prevented this issue.
- Proper Handling: Handle the film with care to avoid damage. Avoid dragging or dropping rolls of film. Store rolls vertically to prevent distortion.
Regular maintenance of shrink wrap equipment is equally important:
- Cleaning: Regularly clean the sealing jaws, shrink tunnel, and other equipment components to remove any food particles, grease, or debris.
- Inspection: Inspect the equipment regularly for wear and tear. Check the sealing blades, heating elements, and other components for any signs of damage.
- Lubrication: Lubricate moving parts as recommended by the manufacturer. This helps to ensure smooth operation and prevent premature wear.
- Calibration: Calibrate the sealing equipment and shrink tunnel regularly to ensure accurate temperature and pressure settings.
- Professional Servicing: Schedule regular maintenance and servicing by qualified technicians to ensure optimal performance and longevity of the equipment.
Emerging Trends and Innovations
The realm of food shrink wrap is in constant flux, mirroring the broader evolution of food packaging. Driven by consumer demand for convenience, sustainability, and extended shelf life, the industry is witnessing a surge in innovative approaches. These advancements aim to enhance food preservation, minimize environmental impact, and improve the overall consumer experience. The future promises a convergence of technology and eco-consciousness, leading to packaging solutions that are both effective and responsible.
Latest Trends in Food Shrink Wrap Technology
Several key trends are reshaping the landscape of food shrink wrap, reflecting a shift towards greater efficiency and sustainability. These trends are fueled by technological advancements and evolving consumer preferences.
- Bio-based and Compostable Films: There is a growing adoption of shrink wrap films derived from renewable resources like cornstarch, sugarcane, and other plant-based materials. These films offer a biodegradable alternative to traditional petroleum-based plastics, reducing environmental footprint. For example, companies are actively developing compostable shrink films that can break down in industrial composting facilities, offering a closed-loop packaging solution.
- Smart Packaging: The integration of smart technologies is gaining traction. This includes the incorporation of sensors and indicators to monitor food freshness, temperature, and potential spoilage. These technologies can provide real-time information to consumers and retailers, minimizing food waste. For instance, some shrink wraps now incorporate time-temperature indicators that change color to signal when a product has exceeded a safe temperature threshold.
- Active Packaging: Active packaging goes beyond simply protecting food; it actively interacts with the food to extend shelf life and maintain quality. This can involve incorporating antimicrobial agents, oxygen scavengers, or moisture absorbers within the shrink wrap. A specific example includes shrink wraps infused with natural antimicrobials, such as essential oils, to inhibit the growth of spoilage organisms.
- Improved Barrier Properties: Advances in polymer science are leading to the development of shrink wrap films with enhanced barrier properties. These films offer superior protection against oxygen, moisture, and other environmental factors that can degrade food quality. Multilayer films are being designed with specific layers to provide optimal barrier performance for different food products.
- Thinning and Down-Gauging: Manufacturers are striving to reduce the thickness of shrink wrap films while maintaining or even improving their performance. This leads to reduced material usage and waste, contributing to sustainability goals. Down-gauging is achieved through advancements in film extrusion and processing techniques.
Innovative Applications of Shrink Wrap in the Food Industry
The versatility of shrink wrap is constantly being explored, leading to novel applications across various segments of the food industry. These innovations aim to enhance efficiency, reduce waste, and improve the overall quality of food products.
- Modified Atmosphere Packaging (MAP): Shrink wrap is increasingly used in conjunction with MAP techniques. This involves modifying the gas composition within the package to extend shelf life and preserve the freshness of perishable foods. For example, shrink wrapping fresh produce in a modified atmosphere can significantly reduce the rate of respiration and decay.
- Portion Control Packaging: Shrink wrap is used to create individually portioned food items, catering to the growing demand for convenience and portion control. This application is common for items like cheese slices, pre-cut fruits and vegetables, and single-serving meals.
- Tamper-Evident Packaging: Shrink wrap provides a secure and tamper-evident seal, assuring consumers that the product has not been opened or compromised. This is crucial for ensuring food safety and preventing product tampering. For instance, shrink bands are commonly used on the lids of jars and bottles to provide visual evidence of tampering.
- Automated Packaging Systems: The food industry is increasingly adopting automated packaging systems that utilize shrink wrap. These systems enhance efficiency, reduce labor costs, and improve the consistency of packaging. For example, automated shrink wrapping machines are widely used in meat processing plants to package various cuts of meat.
- Food Bundling: Shrink wrap is employed to bundle multiple food items together for sale, such as multiple cans of beverages or packs of snacks. This is an effective way to create multi-packs and offer promotional deals.
Future Shrink Wrap Technology
The future of food shrink wrap promises even more transformative advancements, driven by the convergence of nanotechnology, biotechnology, and sustainable materials. This future will focus on intelligent, eco-friendly solutions that optimize food preservation and minimize environmental impact.
- Self-Healing Shrink Wrap: Imagine a shrink wrap that can repair minor tears or punctures on its own. This is the promise of self-healing technology, which could be achieved by incorporating microcapsules containing healing agents into the film. Upon damage, these capsules would release the agents, repairing the film and maintaining its protective properties.
- Edible Shrink Wrap: Scientists are exploring the creation of edible shrink wrap films made from natural ingredients like proteins, polysaccharides, and lipids. This would eliminate packaging waste altogether, as the film could be consumed along with the food. These edible films could also be infused with nutrients or flavors to enhance the food product.
- Nanotechnology-Enhanced Films: Nanotechnology will play a crucial role in the future of shrink wrap. Nanomaterials can be incorporated into the film to enhance barrier properties, antimicrobial activity, and mechanical strength. For example, nanoparticles could be used to create films with improved oxygen barrier properties, extending the shelf life of oxygen-sensitive foods.
- Biodegradable and Compostable Films with Enhanced Performance: The trend toward sustainable packaging will continue, with a focus on developing biodegradable and compostable films that offer superior performance compared to existing options. This includes improving the barrier properties, mechanical strength, and heat-sealing characteristics of these films.
- Smart and Interactive Packaging: The integration of smart technologies will become even more sophisticated. This includes incorporating sensors that can detect pathogens, monitor the release of flavors, and provide real-time information about the food’s condition to consumers via their smartphones.
Wrap-Up
As we conclude this exploration, we see food shrink wrap not just as a packaging solution, but as a testament to human ingenuity. It’s a symbol of our dedication to reducing waste, extending shelf life, and ensuring the safety and quality of our food. Emerging trends hint at a future where sustainability takes center stage, where innovation continues to redefine the boundaries of preservation.
The legacy of food shrink wrap is one of transformation, a constant evolution towards a more efficient, safer, and more sustainable food system. The future of food, it seems, is wrapped in a promise of freshness, sealed with a whisper of innovation.