Paper food containers are more than just disposable packaging; they represent a significant shift towards sustainable food service practices. From humble beginnings, these containers have evolved to meet the diverse needs of the food industry, offering a versatile and eco-friendly alternative to traditional materials. This comprehensive overview delves into the world of paper food containers, exploring their history, various types, manufacturing processes, environmental impact, design considerations, and the regulations governing their use.
This exploration will cover a range of container types, from simple boxes and cups to more complex trays and bowls, each designed for specific food applications. We’ll also examine the materials used, including coatings and liners that enhance functionality and ensure food safety. Moreover, we’ll navigate the intricacies of their production, highlighting the processes, machinery, and quality control measures that ensure these containers meet rigorous standards.
Finally, we’ll discuss the cost implications, market trends, and innovative developments shaping the future of paper food containers.
Introduction to Paper Food Containers
Paper food containers are ubiquitous in modern life, serving as essential packaging for a vast array of food items. From take-out meals and fast food to prepared groceries and bakery goods, these containers provide a practical and hygienic solution for transporting and consuming food. Their versatility and adaptability have made them a cornerstone of the food service industry.
Basic Function of Paper Food Containers
The primary function of paper food containers is to contain and protect food items from external contaminants, physical damage, and temperature fluctuations. They are designed to maintain the food’s integrity, prevent spills, and facilitate easy handling and consumption. Beyond mere containment, these containers often serve to:
- Preserve Food Quality: Many paper containers are designed with features like moisture barriers and insulation to help maintain the food’s freshness, texture, and temperature.
- Provide Convenience: They offer a convenient way for consumers to carry, eat, and dispose of food, particularly in on-the-go scenarios.
- Enable Branding and Information: Paper containers offer a surface for branding, nutritional information, and other important details, enhancing the consumer experience.
History of Paper Food Containers
The development of paper food containers reflects a history of innovation driven by the evolving needs of food service and consumer convenience. The evolution is marked by key milestones:
- Early Beginnings: The earliest forms of paper packaging for food appeared in the late 19th and early 20th centuries. Simple paper bags and wrappers were used for items like candies, bread, and snacks.
- The Rise of Fast Food: The burgeoning fast-food industry in the mid-20th century spurred the development of more specialized containers, such as paper cups, burger boxes, and French fry cartons.
- Technological Advancements: Innovations in paper manufacturing, including the use of coatings like wax and polyethylene, significantly improved the containers’ ability to withstand moisture, grease, and heat. These developments expanded the range of foods that could be packaged in paper.
- Sustainability Concerns: In recent decades, environmental concerns have led to the development of more sustainable paper food containers, including those made from recycled paper, plant-based materials, and compostable options.
Advantages of Using Paper Food Containers
Paper food containers offer several advantages compared to other packaging materials, making them a preferred choice for many food service businesses and consumers. The advantages include:
- Sustainability: Paper is a renewable resource, and paper containers are often recyclable or compostable, reducing their environmental impact. The ability to source paper from sustainably managed forests is also a key advantage.
- Versatility: Paper can be molded into various shapes and sizes to accommodate a wide range of food items. Different paper types and coatings can be used to provide specific functional properties.
- Cost-Effectiveness: Compared to some other packaging materials, paper food containers can be relatively inexpensive to produce, especially when manufactured in large quantities.
- Printability: Paper surfaces readily accept printing, allowing for effective branding, labeling, and communication of important information to consumers.
- Safety: Paper containers are generally considered safe for food contact, especially when manufactured with appropriate coatings and materials.
Types of Paper Food Containers
Paper food containers offer a versatile and sustainable solution for packaging and serving various food items. The diverse range of container types caters to different food types, portion sizes, and consumer needs. Understanding these types, their applications, and the materials used in their construction is crucial for both businesses and consumers seeking practical and eco-friendly food packaging options.
Paper Boxes
Paper boxes are a fundamental type of paper food container, known for their structural integrity and versatility. They are commonly used for packaging items requiring containment and protection.
- Folding Cartons: These are typically made from paperboard and are designed to be folded into shape. They are ideal for dry foods, such as cereals, crackers, and cookies. They also provide a surface for branding and information.
- Clamshells: Often used for takeout meals and fast food, clamshells are hinged boxes that close to contain the food. They are frequently used for burgers, fries, and other quick-service restaurant items.
- Pizza Boxes: Specifically designed to transport pizzas, these boxes are usually made from corrugated cardboard for insulation and strength. The corrugated structure helps to maintain the pizza’s temperature and prevents it from getting soggy.
- Tuck Top Boxes: These boxes are designed with a tuck-in flap for easy opening and closing. They are often used for items like French fries, chicken nuggets, and other grab-and-go foods.
Paper Cups
Paper cups are a ubiquitous type of food container, particularly for beverages and certain food items. They are designed to be disposable and convenient.
- Hot Drink Cups: These cups are typically made from paperboard and are often lined with a polyethylene coating to prevent leaks. They are used for hot beverages like coffee, tea, and hot chocolate. The coating ensures the cup can withstand the heat and moisture.
- Cold Drink Cups: Similar in construction to hot drink cups, cold drink cups may have a polyethylene or a plant-based coating. They are used for beverages like iced coffee, soft drinks, and smoothies. They may also be made with a wax coating to help prevent condensation from weakening the cup.
- Food Cups: These cups are used for serving items like ice cream, yogurt, and small portions of snacks. They can be made from various paper materials and often have a lid for easy transport.
Paper Trays
Paper trays offer a flat surface for serving food, often used in fast food restaurants and for takeout.
- Food Trays: Typically made from paperboard or molded pulp, food trays are used for serving meals such as burgers, fries, and sandwiches. They provide a convenient surface for eating and are easily disposable. They can be coated with a moisture barrier to prevent leaks.
- Compartment Trays: These trays are designed with multiple compartments to separate different food items. They are common in school cafeterias and for pre-packaged meals, providing a convenient way to serve a variety of foods.
Paper Bowls
Paper bowls are designed for holding liquids and semi-liquid foods. They are used for a wide range of foods.
- Soup Bowls: These bowls are designed to hold hot liquids, such as soups and stews. They are usually made from paperboard and coated with a moisture-resistant lining.
- Salad Bowls: Commonly used for salads, these bowls can be made from various paper materials and often have a coating to prevent leaks. They provide a convenient way to serve and consume salads.
- Noodle Bowls: Similar to soup bowls, these are designed for noodle dishes and other similar food items. They need to be resistant to both heat and moisture.
Materials Used in Paper Food Container Construction
The materials used in paper food containers are chosen to provide functionality, durability, and, increasingly, sustainability. Coatings and liners play a crucial role in preventing leaks and maintaining the integrity of the container.
- Paperboard: The primary material used for many paper food containers. Paperboard offers strength and can be molded into various shapes. The thickness and type of paperboard used depend on the intended application of the container.
- Corrugated Cardboard: Often used for pizza boxes and other containers requiring extra strength and insulation. The corrugated structure provides cushioning and helps to maintain the temperature of the food.
- Polyethylene (PE) Coating: A common coating used to make paper containers water-resistant. It is a type of plastic that prevents leaks and keeps the container from becoming soggy.
- Polylactic Acid (PLA) Coating: A bioplastic coating made from renewable resources, such as corn starch. PLA is an alternative to polyethylene and is compostable under specific conditions.
- Wax Coating: Used to provide moisture resistance, especially in older container designs. It can be used on cups and other containers to prevent liquids from soaking through the paper.
- Liners: Used inside containers to add an extra layer of protection against leaks. Liners can be made from various materials, including PE, PLA, or foil, depending on the requirements of the food.
Manufacturing Processes
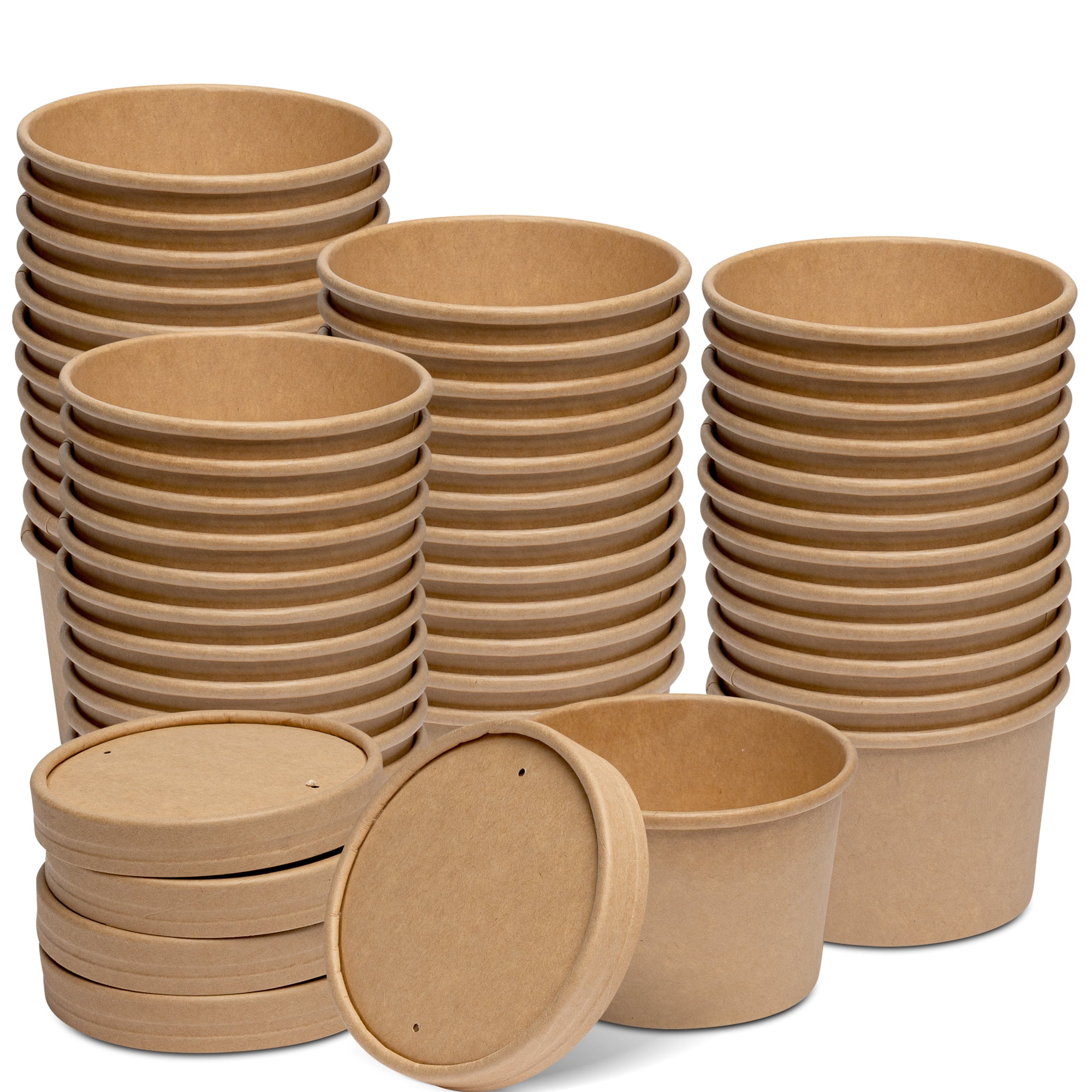
Paper food containers, ubiquitous in modern food service, undergo a sophisticated manufacturing process. This process transforms raw materials into the functional and often aesthetically pleasing containers we use daily. Understanding these processes is crucial to appreciating the innovation and engineering that go into their creation. The efficiency and sustainability of these methods are constantly evolving, reflecting industry demands for eco-friendly solutions and improved performance.
Typical Manufacturing Process for Paper Food Containers
The production of paper food containers typically involves several key stages. These stages are carefully coordinated to ensure product quality, efficiency, and compliance with food safety standards. The process generally begins with the selection of raw materials and concludes with the finished, ready-to-use container.
- Pulping and Paper Production: The process starts with wood pulp, often sourced from sustainable forestry practices. The wood pulp is then processed into paper sheets. This can involve various techniques, including chemical pulping, mechanical pulping, or a combination of both, to create paper with specific properties like strength, thickness, and moisture resistance.
- Coating and Treatment: The paper is often coated with a barrier layer to protect the container from moisture, grease, and other substances. Common coating materials include polyethylene (PE) and, increasingly, more sustainable alternatives like polylactic acid (PLA). This step is critical for the container’s functionality, preventing leakage and maintaining food integrity.
- Printing: The paper is then printed with designs, branding, and nutritional information. This stage utilizes various printing methods, such as flexographic printing, which is commonly used for its efficiency and suitability for large-scale production. The printing process must adhere to strict food safety regulations to ensure that inks and other materials do not contaminate the food.
- Cutting and Forming: The printed and coated paper is cut into the required shapes and sizes. This is followed by the forming process, where the paper is folded, glued, and sealed to create the final container shape. Automated machinery ensures precision and speed in this critical stage.
- Quality Control: Throughout the entire process, rigorous quality control measures are implemented. These measures include checking the paper’s thickness, coating integrity, print quality, and the overall structural integrity of the finished containers. Any defects detected are addressed to maintain product quality and food safety standards.
Step-by-Step Guide: Production of a Paperboard Takeout Box
The production of a paperboard takeout box exemplifies the manufacturing process. This process demonstrates how raw materials are transformed into a functional and convenient food container. The steps Artikeld below highlight the key stages involved.
- Raw Material Selection: High-quality paperboard, often made from virgin or recycled pulp, is selected. The paperboard’s thickness and composition are crucial for the box’s structural integrity. This selection also considers the specific requirements for food contact, such as grease resistance.
- Paperboard Coating: The paperboard is coated with a layer of polyethylene (PE) or a similar food-grade barrier material. This coating provides a barrier against moisture and grease, preventing leaks and maintaining food quality. Alternative coatings, like PLA, are also used to enhance sustainability.
- Printing: The coated paperboard is printed with the desired designs, branding, and nutritional information using flexographic printing. This stage must adhere to strict food safety regulations to ensure that inks and other materials do not contaminate the food.
- Die-Cutting: The printed paperboard is fed into a die-cutting machine, which uses a steel rule die to cut the paperboard into the specific shapes needed for the takeout box. This process ensures accurate and consistent shapes for efficient assembly.
- Creasing and Scoring: Creasing and scoring are applied to the cut paperboard. These lines allow the paperboard to be folded accurately during the box assembly process. The precision of these lines is critical for the box’s structural integrity and ease of use.
- Folding and Gluing: The cut and creased paperboard is then folded into the takeout box shape. Glue is applied to the appropriate areas, and the box components are assembled using automated machinery. This step ensures the box’s structural integrity and secure closure.
- Quality Control and Inspection: Throughout the production process, quality control checks are performed. These checks include verifying the paperboard’s thickness, the integrity of the coating and printing, and the overall dimensions and structural integrity of the finished boxes.
- Packaging and Distribution: The completed takeout boxes are then packaged, typically in bundles or stacks, ready for distribution to food service businesses. Packaging materials must also meet food safety standards to ensure the containers arrive in optimal condition.
Manufacturing Process Table: Paperboard Takeout Box
The table below details the manufacturing process of a paperboard takeout box, outlining each stage, the machinery involved, and the quality control measures applied.
Stage | Description | Machinery Involved | Quality Control Measures |
---|---|---|---|
Raw Material Preparation | Selection and preparation of paperboard and coating materials. | Unwinding machines, coating applicators, and material handling equipment. | Thickness measurement, basis weight testing, and visual inspection of the paperboard and coating for defects. |
Printing | Applying designs, branding, and nutritional information. | Flexographic printing presses, ink handling systems, and plate mounting equipment. | Color matching, print registration checks, and visual inspection for print defects. |
Die-Cutting and Creasing | Cutting the paperboard into shapes and creating fold lines. | Die-cutting machines, creasing and scoring equipment, and waste removal systems. | Dimensional accuracy checks, inspection of cut quality, and alignment checks for creasing lines. |
Folding and Gluing | Assembling the box components. | Folding machines, gluing systems, and automated assembly lines. | Adhesive strength testing, dimensional checks, and visual inspection for proper folding and sealing. |
Environmental Impact and Sustainability
Paper food containers are increasingly recognized as a more environmentally friendly alternative to plastic, playing a crucial role in reducing pollution and promoting sustainable practices. This shift is driven by growing consumer awareness and stricter environmental regulations. The benefits extend beyond simply reducing plastic waste; they encompass a lifecycle analysis that considers resource usage, manufacturing processes, and end-of-life scenarios.
Environmental Benefits of Paper vs. Plastic, Paper food containers
The primary advantage of paper food containers lies in their reduced environmental impact compared to their plastic counterparts. This is primarily due to several factors:
- Reduced Reliance on Fossil Fuels: Plastic production heavily relies on fossil fuels, contributing significantly to greenhouse gas emissions and climate change. Paper, on the other hand, primarily uses renewable resources like wood pulp, which, when sourced sustainably, has a lower carbon footprint.
- Biodegradability and Compostability: Many paper containers are biodegradable and compostable, meaning they can naturally break down and return to the earth, unlike plastic, which persists in the environment for hundreds of years, contributing to landfill waste and ocean pollution.
- Reduced Microplastic Pollution: Plastic containers can break down into microplastics, which contaminate ecosystems and pose a threat to wildlife and human health. Paper containers, even if coated with biodegradable materials, are less likely to contribute to this type of pollution.
- Lower Manufacturing Energy Consumption (Potentially): While manufacturing processes vary, paper production can, in some cases, require less energy than plastic production, especially when considering the energy-intensive processes involved in refining and molding plastics. However, this depends heavily on the specific manufacturing techniques and energy sources used.
Biodegradability and Compostability of Paper Food Container Types
The biodegradability and compostability of paper food containers vary depending on their composition and coatings. Understanding these differences is crucial for proper disposal and maximizing their environmental benefits.
- Uncoated Paper Containers: These are generally the most biodegradable and compostable. They are made solely from paper and can readily break down in composting environments. Examples include simple paper cups and boxes.
- Wax-Coated Paper Containers: Traditionally, wax was used to provide a moisture barrier. While wax is technically biodegradable, its breakdown rate is slower than uncoated paper, and its presence can sometimes hinder the composting process.
- PLA-Coated Paper Containers: PLA (Polylactic Acid) is a bioplastic derived from renewable resources like corn starch. PLA-coated containers are compostable under specific industrial composting conditions. However, they may not readily decompose in home composting setups.
- PE-Coated Paper Containers: PE (Polyethylene) is a type of plastic used for moisture resistance. PE-coated containers are generally
-not* compostable and should be recycled if possible.
Recycling Paper Food Containers
Recycling paper food containers is a crucial step in minimizing their environmental impact and promoting a circular economy. However, the process requires specific steps to ensure the materials are properly processed and reused.
The following Artikels the key steps involved in recycling paper food containers:
- Collection: Paper food containers are collected through various methods, including curbside recycling programs, drop-off centers, and commercial collection services. It is essential to separate them from other waste materials.
- Sorting: Collected containers are sorted to separate them from other recyclables and non-recyclable materials. This is often done at a materials recovery facility (MRF).
- Cleaning: Containers may need to be cleaned to remove food residue, as this can contaminate the recycling process. Some programs accept lightly soiled containers, while others require them to be rinsed.
- Pulping: The paper containers are pulped, which involves breaking them down into a slurry of paper fibers. This process often involves adding water and chemicals to remove any coatings or contaminants.
- Processing: The pulp is then processed to remove any remaining contaminants, such as ink, adhesives, or plastic coatings. This may involve screening, filtering, and bleaching.
- Manufacturing: The cleaned and processed paper pulp is used to create new paper products, such as paperboard, cardboard, or other paper-based packaging.
Design and Functionality
The design of paper food containers plays a crucial role in their overall functionality, directly impacting how effectively they can hold, transport, and protect food. Beyond aesthetics, thoughtful design considerations ensure the containers meet the specific needs of different food types, providing insulation, preventing leaks, and enhancing the user experience. This section explores the intricate relationship between design and functionality in paper food containers, highlighting innovative solutions and design considerations for both hot and cold food applications.
Impact of Design on Functionality
The design of a paper food container directly influences its ability to perform its intended functions. Factors like shape, material thickness, and closure mechanisms are critical for performance.Consider the following aspects:
- Insulation: The design of the container significantly affects its insulation properties. A double-walled container, for example, provides better insulation than a single-walled one, helping to maintain the temperature of the food, whether hot or cold. This design is crucial for preventing heat transfer, keeping hot foods warmer for longer and cold foods colder.
- Leak Resistance: The structural design and the type of closure mechanism are vital for preventing leaks. Containers with tight-fitting lids, folded edges, or specific coatings are designed to minimize the risk of spills, ensuring food remains securely contained during transport.
- Durability: The shape and construction of the container contribute to its durability. Containers with reinforced corners and sturdy bases are less likely to collapse or deform under the weight of the food, ensuring that the food is protected during handling and transportation.
- Ease of Use: Design elements such as handles, easy-open lids, and clear labeling contribute to user convenience. Containers that are easy to open, carry, and dispose of enhance the overall dining experience for consumers.
Innovative Designs for Enhanced User Experience and Convenience
Innovations in paper food container design continually aim to improve user experience and convenience. Several examples showcase these advancements:
- Containers with Built-in Compartments: These designs incorporate separate compartments within a single container, allowing users to keep different food items (e.g., main course and sides) separate, preserving their individual flavors and textures.
- Containers with Tear-Away Sections: Some containers feature tear-away sections that can be used as plates or serving trays, eliminating the need for additional dishware and simplifying the eating process.
- Containers with Vented Lids: These designs incorporate vents in the lids to allow steam to escape, preventing the food from becoming soggy while maintaining its desired texture. This feature is particularly useful for hot foods.
- Containers with Integrated Utensils: Some manufacturers integrate utensils, such as small wooden forks or spoons, directly into the container design. This eliminates the need for separate cutlery and enhances convenience, especially for on-the-go consumption.
- Containers with Customizable Designs: Companies are increasingly offering customizable container designs, allowing businesses to brand their packaging with logos, colors, and other design elements. This enhances brand visibility and creates a more professional presentation.
Design Considerations for Hot and Cold Foods
The design of paper food containers must consider the specific requirements of both hot and cold foods to maintain their quality and safety. Different design features and materials are needed to address these needs.
- Hot Food Containers:
- Insulation: These containers often feature double-walled construction or use materials with high insulation properties to minimize heat transfer and keep food warm.
- Leak Resistance: Designs must prevent leaks, as hot foods often contain liquids. Tight-fitting lids and heat-resistant coatings are common features.
- Ventilation: Vents or breathable materials may be used to release steam and prevent the food from becoming soggy.
- Material: Materials must be able to withstand high temperatures without degrading or leaching harmful chemicals into the food.
- Cold Food Containers:
- Condensation Control: Designs may incorporate features to manage condensation, such as absorbent linings or air gaps, to prevent the container from becoming soggy or compromising its structural integrity.
- Leak Resistance: Leak-proof designs are essential, particularly for items with sauces or dressings.
- Insulation: While less critical than for hot foods, insulation helps maintain the cold temperature of the food.
- Material: The material must be suitable for cold temperatures and resist moisture penetration.
For example, a container designed for hot soup might utilize a double-walled construction with a tight-fitting lid and a vent to release steam. In contrast, a container for a cold salad might use a single-walled design with an absorbent lining to manage condensation and a secure lid to prevent leaks.
Cost Analysis and Market Trends
The economic viability of paper food containers is a critical factor in their widespread adoption. Understanding the cost dynamics, comparing them with alternatives, and analyzing market trends provides a comprehensive view of their current and future prospects. This section delves into these aspects, offering insights into pricing influences and the future outlook for this sustainable packaging solution.
Cost Comparison: Paper vs. Alternatives
Comparing the costs of paper food containers with those made from materials like plastic, styrofoam, and aluminum highlights the economic landscape. The initial cost can vary significantly depending on the material, manufacturing process, and design complexity. While paper containers may sometimes have a higher upfront cost, particularly when considering specialized coatings or features, their lifecycle costs and long-term benefits often provide a more compelling value proposition.
To provide a comparative perspective, here’s a table that Artikels the cost considerations:
Material | Typical Cost per Unit (USD) | Factors Influencing Cost | Additional Considerations |
---|---|---|---|
Paper | $0.05 – $0.50+ | Paper type, coating, design complexity, order volume. | Biodegradability, recyclability, and environmental impact can offset higher initial costs. |
Plastic | $0.03 – $0.40+ | Type of plastic, manufacturing process, and design. | Lower upfront cost, but environmental concerns and regulatory pressures are increasing. |
Styrofoam (Expanded Polystyrene – EPS) | $0.02 – $0.20 | Raw material costs, production volume. | Often the cheapest, but difficult to recycle and has significant environmental drawbacks. |
Aluminum | $0.20 – $1.00+ | Aluminum thickness, design, and finishing. | Excellent barrier properties, but higher cost and environmental impact of aluminum production. |
Plastic containers, especially those made from widely available polymers, often present a lower initial cost. However, the environmental burden associated with plastic production, disposal, and recycling can lead to hidden costs, including cleanup expenses and potential future regulatory fees. Styrofoam is typically the cheapest option initially, but its non-biodegradable nature and recycling challenges create significant environmental concerns. Aluminum containers, while offering excellent barrier properties, tend to be more expensive due to the energy-intensive production process.
Paper containers, with their biodegradable and often recyclable nature, provide a more sustainable option, and the cost is becoming increasingly competitive as manufacturing processes improve and demand grows.
Obtain recommendations related to chinese food on mechanicsville that can assist you today.
Pricing Influences: Size, Material, and Design
Several factors influence the pricing of paper food containers, making each product unique in its cost structure. Container size, the type of material used, and the design complexity all play significant roles in determining the final price.
Here’s a detailed explanation of these influences:
- Container Size: The volume of material required directly impacts the cost. Larger containers naturally require more paper and potentially more complex manufacturing processes, leading to higher prices. For example, a large family-sized pizza box will cost more than a small individual-serving container.
- Material: The type of paper used and any coatings applied significantly affect the price. Kraft paper, a common and relatively inexpensive option, is often used for basic containers. However, containers designed for liquids or greasy foods require specialized coatings like polyethylene (PE) or polylactic acid (PLA), which increase the cost. Recycled paper may be cheaper than virgin paper, but the availability and quality can influence the final price.
- Design: The complexity of the design, including the shape, printing, and any special features, affects the cost. Containers with intricate folds, custom printing, or unique closures will typically be more expensive than simpler designs. For instance, a container with a built-in handle or a custom logo will have a higher price compared to a standard box.
Consider the example of a fast-food chain switching from plastic to paper containers. A simple burger box made from uncoated paper might cost $0.10 per unit, while a similar-sized container with a grease-resistant coating and custom printing could cost $0.25 or more. The design and features influence not only the cost of the container but also the perceived value by the consumer.
Market Trends and Future Outlook
The market for paper food containers is dynamic and evolving, influenced by consumer preferences, environmental regulations, and technological advancements. Several trends shape the current landscape and provide insights into the future of this industry.
Key predictions for the future include:
- Increased Demand: The global demand for paper food containers is expected to grow significantly, driven by the increasing awareness of environmental issues and the growing preference for sustainable packaging solutions. Consumers and businesses are actively seeking alternatives to plastic.
- Technological Advancements: Innovations in materials and manufacturing processes will continue to improve the performance and cost-effectiveness of paper containers. This includes the development of new biodegradable coatings, improved barrier properties, and more efficient production methods.
- Regulatory Influence: Governments worldwide are implementing stricter regulations on single-use plastics, which will further boost the adoption of paper containers. This includes bans on certain types of plastic packaging and incentives for using sustainable alternatives.
- Expansion of Applications: The use of paper food containers will expand beyond traditional applications, such as fast food and takeout, to include a wider range of food products, including frozen foods, ready-to-eat meals, and grocery items.
- Focus on Circular Economy: The industry will increasingly focus on designing containers for recyclability and composting, supporting the principles of a circular economy. This involves using recyclable materials, designing containers that are easy to disassemble, and investing in infrastructure to support recycling programs.
For example, the rise of plant-based packaging is a clear trend. Companies are increasingly using PLA coatings instead of traditional PE coatings, which is a more sustainable option. This shift reflects the industry’s commitment to reducing its environmental footprint and meeting the growing demand for eco-friendly packaging. Another example is the use of molded fiber packaging, which is made from recycled paper and offers excellent strength and durability.
This technology is becoming increasingly popular for packaging fragile items and is a sustainable alternative to polystyrene. These trends demonstrate a dynamic and evolving market, with paper food containers poised to play an increasingly important role in the future of packaging.
Branding and Customization: Paper Food Containers
Paper food containers offer businesses a powerful platform for brand building. Beyond their primary function of holding food, these containers become mobile billboards, communicating brand identity and values to consumers. Effective customization can significantly enhance brand recognition and customer loyalty, transforming a simple packaging element into a strategic marketing asset.
Customization for Branding
Businesses have a variety of options to customize paper food containers to reflect their brand identity. These customizations go beyond just logos and can include specific color palettes, unique typography, and brand messaging, ensuring that the packaging aligns with the overall brand strategy.
- Logo Placement and Design: The logo is the cornerstone of brand recognition. Its placement, size, and design are crucial. The logo should be prominently displayed, easily visible, and consistent with the brand’s visual identity. Consider incorporating the logo on multiple sides of the container to maximize visibility. For example, a fast-food chain might feature its logo prominently on the top and sides of its burger boxes.
- Color Palette and Typography: Consistent use of brand colors and fonts is vital for reinforcing brand recognition. The color palette should be carefully selected to evoke the desired emotions and associations. Typography should be legible and reflect the brand’s personality. A coffee shop, for instance, might use warm colors and a friendly font on its paper cups to create a welcoming atmosphere.
- Brand Messaging and Slogans: Including brand messaging, taglines, or short descriptions on the container can communicate the brand’s values and story. This can be a powerful way to connect with customers and differentiate the brand from competitors. A restaurant focused on sustainability could print a message about its eco-friendly practices on its takeout containers.
- Custom Shapes and Sizes: Beyond standard shapes, businesses can opt for custom-shaped containers to stand out. This can be particularly effective for unique food items or to create a memorable unboxing experience. A bakery might use a specially shaped box for its signature pastries.
- Material Selection: The choice of paper material can also contribute to branding. Using recycled or sustainable paper can communicate a brand’s commitment to environmental responsibility. The texture and finish of the paper can also influence the perceived quality of the product.
Design Options for Printing and Labeling
Various printing and labeling techniques can be used to customize paper food containers. The choice of technique depends on factors like the desired design complexity, production volume, and budget.
- Offset Printing: Offset printing is a high-quality printing method suitable for large production runs. It allows for detailed designs, vibrant colors, and photographic images. This method is commonly used for printing complex logos, detailed illustrations, and multi-color designs on food containers.
- Flexographic Printing: Flexographic printing is a versatile and cost-effective method, particularly suitable for printing on a variety of materials, including paper. It’s ideal for printing simple designs, logos, and text on containers. Flexo printing is often used for food packaging due to its ability to print on curved surfaces and its suitability for food-safe inks.
- Digital Printing: Digital printing is a good option for short runs and personalized designs. It allows for variable data printing, meaning each container can have a unique design. This method is ideal for limited-edition packaging or promotional campaigns.
- Labeling: Labels can be used to add branding, product information, and promotional messages to containers. Labels offer flexibility in terms of design and material and can be applied to various container shapes and sizes.
- Embossing and Debossing: Embossing (raising the design) and debossing (sinking the design) add a tactile element and a premium feel to the packaging. These techniques are particularly effective for highlighting logos or key brand elements.
- Foil Stamping: Foil stamping adds a metallic finish to the design, creating a luxurious and eye-catching effect. This is often used for logos and premium packaging.
Creating a Visually Appealing Design
Creating a visually appealing design involves considering the overall aesthetic, the target audience, and the brand’s message. The design should be both attractive and functional, effectively communicating the brand’s identity while serving its primary purpose.
Illustration: A takeout container for a gourmet burger restaurant. The container is rectangular, made of kraft paper, with a slightly textured surface. The design features the restaurant’s logo, a stylized image of a burger, centered on the top lid. The logo is a combination mark, featuring a custom-designed wordmark in a bold, sans-serif font, colored in a deep, earthy brown.
The burger illustration is placed to the right of the logo and shows a cross-section of the burger, highlighting the fresh ingredients. The color palette consists of the brown from the logo, a creamy white for the text, and the natural color of the kraft paper. The side of the container includes the restaurant’s tagline, “The Perfect Bite,” in the same font as the logo, arranged vertically.
- Color and Imagery: The color palette should be consistent with the brand’s identity and evoke the desired emotions. Imagery should be high-quality, relevant to the product, and visually appealing.
- Typography: The font choices should be legible and reflect the brand’s personality. Different font weights and sizes can be used to create visual hierarchy and guide the viewer’s eye.
- Layout and Composition: The layout should be balanced and organized, with elements placed in a way that is both visually appealing and functional.
- Material and Finish: The choice of paper material and finish can significantly impact the overall look and feel of the packaging.
- Consistency: Maintain a consistent brand identity across all packaging elements to reinforce brand recognition.
Alternative Materials and Innovations
The quest for sustainable packaging has driven significant innovation in the paper food container industry. Beyond traditional paper, manufacturers are exploring alternative materials and technologies to enhance environmental performance, functionality, and consumer appeal. This section explores the use of alternative materials, examines different coating options, and highlights emerging innovations that are reshaping the landscape of paper food containers.
Alternative Materials in Manufacturing
The move towards more sustainable packaging solutions has led to the incorporation of a variety of alternative materials in paper food container manufacturing. These materials aim to reduce reliance on virgin resources, minimize environmental impact, and enhance the overall performance of the containers.
- Plant-Based Coatings: These coatings, derived from renewable resources like cornstarch, sugarcane, or seaweed, offer a biodegradable and compostable alternative to traditional petroleum-based coatings.
- Recycled Paperboard: Utilizing recycled paperboard reduces the demand for virgin paper pulp, conserving forests and decreasing energy consumption in the manufacturing process.
- Bamboo and Bagasse: Bamboo and bagasse (sugarcane fiber) are rapidly renewable resources that can be molded into containers, offering a strong and compostable alternative to conventional paper products.
- Mushroom Packaging: Innovative mushroom packaging uses mycelium (the root structure of mushrooms) to create molded packaging that is fully biodegradable and compostable.
Properties of Coating Options
Different coating options significantly impact the performance, sustainability, and cost-effectiveness of paper food containers. A comparative analysis reveals the advantages and disadvantages of various coating materials.
Material | Advantages | Disadvantages |
---|---|---|
Polyethylene (PE) | Excellent moisture barrier; cost-effective; widely available. | Non-biodegradable; derived from petroleum; difficult to recycle. |
Polylactic Acid (PLA) | Biodegradable and compostable; derived from renewable resources; good barrier properties. | Can be more expensive than PE; requires specific composting conditions; may have lower heat resistance. |
Aquacoat (Water-Based Dispersion) | Water-based, reducing VOC emissions; good barrier properties; can be recyclable. | May not be as effective as PE for some applications; can be more expensive than PE. |
Wax | Renewable resource (soy wax, beeswax); biodegradable; good moisture resistance. | Lower heat resistance; can be susceptible to grease penetration; can alter the taste of the food. |
Emerging Innovations in the Field
The paper food container industry is continuously evolving, with ongoing innovations focused on improving functionality, sustainability, and food preservation.
- Active Packaging: This technology incorporates substances that interact with the food to extend its shelf life. For example, oxygen scavengers can be integrated into the container to reduce oxidation and maintain food freshness.
- Smart Packaging: Smart packaging utilizes sensors and indicators to provide information about the food’s condition. This includes indicators that change color to signal temperature abuse or the presence of spoilage organisms.
- Container Technology for Extended Food Lifespan: Researchers are developing containers with enhanced barrier properties and modified atmosphere packaging (MAP) to slow down food spoilage. This can involve using specialized coatings or incorporating inert gases to reduce microbial growth.
- Edible Coatings: Edible coatings, such as those made from chitosan or alginate, can be applied to the container’s interior to enhance its barrier properties and extend the shelf life of the food.
Challenges and Solutions
The transition to paper food containers, while promising for sustainability, presents several hurdles that must be addressed for widespread adoption. Overcoming these challenges requires a multifaceted approach involving infrastructure improvements, technological advancements, and shifts in consumer and business practices. This section will delve into the key obstacles and explore potential solutions.
Challenges in Adoption
Several factors impede the seamless integration of paper food containers into the food industry. These challenges encompass issues related to cost, performance, and the existing waste management infrastructure.
- Cost Competitiveness: Paper food containers can be more expensive to produce than their plastic counterparts, particularly virgin paper-based options. This cost differential can be a barrier for businesses, especially small and medium-sized enterprises (SMEs) operating on tight margins. This higher initial investment may discourage them from making the switch.
- Performance Limitations: While significant advancements have been made, paper containers can still face limitations in terms of moisture resistance, grease resistance, and durability compared to plastics. This can lead to issues such as leakage, degradation of structural integrity, and compromised food quality, especially when handling hot or oily foods.
- Recycling Infrastructure Deficiencies: A major challenge lies in the existing recycling infrastructure. Many paper food containers are not readily recyclable due to coatings (e.g., wax, plastic) or contamination with food residue. In many regions, the infrastructure to process these containers effectively is either lacking or poorly developed, leading to landfilling instead of recycling.
- Consumer Awareness and Behavior: Consumer understanding of paper container recyclability and proper disposal methods is crucial. Lack of awareness or confusion about recycling guidelines can result in containers being incorrectly disposed of, further hindering recycling efforts. This also includes the perceived convenience of plastic containers.
- Supply Chain Issues: Fluctuations in the price and availability of raw materials, such as paper pulp, can impact the cost and supply of paper containers. Disruptions in the supply chain can create instability and hinder the widespread adoption of paper-based alternatives.
Solutions to Overcome the Challenges
Addressing the challenges requires a comprehensive strategy that includes infrastructure development, technological innovation, and policy support.
- Investing in Recycling Infrastructure: Governments and private sector companies need to invest in robust recycling infrastructure capable of processing paper food containers effectively. This includes:
- Implementing advanced sorting technologies to separate different types of paper containers and remove contaminants.
- Establishing specialized recycling facilities equipped to handle coated and treated paper products.
- Expanding collection programs to include paper food containers in curbside recycling or drop-off locations.
- Technological Advancements in Container Design: Ongoing research and development are crucial for creating more sustainable and functional paper food containers. This involves:
- Developing innovative coating materials that provide superior moisture and grease resistance while remaining recyclable. For example, utilizing bio-based coatings derived from plant-based sources.
- Improving the structural integrity and durability of paper containers to prevent leakage and maintain food quality.
- Designing containers that are easily disassembled for efficient recycling, such as those with detachable lids or liners.
- Promoting Consumer Education and Awareness: Effective communication and education are essential to inform consumers about the benefits of paper containers and proper disposal practices. This includes:
- Launching public awareness campaigns to educate consumers about recycling guidelines and the importance of rinsing and emptying containers before disposal.
- Providing clear and consistent labeling on containers indicating their recyclability and disposal instructions.
- Collaborating with businesses to promote sustainable practices and encourage consumer participation in recycling programs.
- Policy and Regulatory Support: Government policies and regulations can play a significant role in driving the adoption of paper food containers and fostering a circular economy. This includes:
- Implementing extended producer responsibility (EPR) schemes, where manufacturers are responsible for the end-of-life management of their products, including recycling.
- Setting targets for the use of recycled content in paper food containers to stimulate demand and reduce reliance on virgin materials.
- Providing financial incentives, such as tax breaks or subsidies, to businesses that adopt sustainable packaging solutions.
- Collaboration and Partnerships: Collaboration among stakeholders, including businesses, governments, recyclers, and consumers, is essential to accelerate the transition to paper food containers. This involves:
- Forming partnerships between businesses and recycling facilities to ensure proper processing of paper containers.
- Supporting research and development initiatives to advance sustainable packaging technologies.
- Sharing best practices and knowledge across the industry to promote innovation and efficiency.
Recommendations for Businesses Considering a Switch to Paper Food Containers:
- Conduct a thorough cost-benefit analysis, considering the long-term environmental and financial advantages.
- Partner with reliable suppliers who offer sustainable and high-quality paper container options.
- Invest in staff training to ensure proper handling and disposal practices.
- Communicate clearly with customers about your commitment to sustainability.
- Stay informed about evolving recycling guidelines and infrastructure developments in your region.
Final Conclusion
In conclusion, paper food containers offer a compelling blend of functionality, sustainability, and branding opportunities. Their journey from basic packaging to a cornerstone of eco-conscious food service is a testament to innovation and a growing awareness of environmental responsibility. By understanding the various aspects of paper food containers, from their manufacturing and design to their environmental impact and future potential, businesses and consumers alike can make informed choices that support a greener, more sustainable future for the food industry.
The shift towards paper food containers is not just a trend; it’s a vital step toward a more responsible approach to food packaging, offering a tangible way to reduce waste and protect our planet.