Assalamu’alaikum Warahmatullahi Wabarakatuh. Brothers and sisters, today we embark on a journey to understand the vital operations within Riceland Foods Dispatch. It is a world of coordination, where every grain of rice, every delivery, and every driver’s journey is carefully planned and executed. Just like in our lives, everything needs proper planning and execution.
We will explore the heart of Riceland Foods, where the dispatch team works tirelessly, like the angels, managing the flow of goods from the fields to your tables. We’ll uncover the daily routines, the technological tools, the communication methods, and the emergency protocols that ensure smooth and efficient delivery. Like the Prophet Muhammad, peace be upon him, who emphasized the importance of honesty and integrity in all transactions, the dispatch team ensures that the deliveries are on time and in good condition.
Riceland Foods Dispatch Overview
The Riceland Foods dispatch department plays a crucial role in the efficient movement of rice products from processing facilities to distribution centers and ultimately to customers. This overview details the primary functions, daily operations, and key performance indicators (KPIs) that define the effectiveness of this vital department.
Primary Functions of the Riceland Foods Dispatch Department
The dispatch department’s primary responsibility is to coordinate and manage the transportation of goods. This encompasses several key functions, each critical to maintaining supply chain efficiency.
- Order Fulfillment and Load Planning: The dispatch team receives orders from various sources and plans the optimal loading of trucks to maximize efficiency and minimize transportation costs. This involves considering factors such as product type, quantity, destination, and delivery deadlines.
- Driver Communication and Routing: Dispatchers communicate with drivers, providing them with routes, delivery instructions, and updates on any changes or delays. They utilize real-time tracking systems to monitor the location of vehicles and ensure adherence to schedules.
- Carrier Management: The dispatch department manages relationships with both internal and external carriers, negotiating rates, scheduling pickups and deliveries, and ensuring compliance with all relevant regulations. This involves managing a network of transportation providers.
- Issue Resolution: Dispatchers are responsible for addressing any issues that arise during the transportation process, such as delivery delays, damaged goods, or driver-related problems. They work to resolve these issues promptly and efficiently to minimize disruptions.
- Compliance and Documentation: Maintaining accurate records of all shipments, including bills of lading, proof of delivery, and other required documentation, is a crucial function. The department ensures compliance with all applicable federal, state, and local regulations related to transportation.
Typical Daily Operations within the Dispatch Center
A typical day in the Riceland Foods dispatch center is characterized by a high degree of coordination and responsiveness. The operations are structured to ensure the smooth flow of products.
- Order Review and Preparation: The day begins with a review of all incoming orders. Dispatchers analyze the orders, confirming product availability, determining shipping requirements, and assigning them to available trucks or carriers.
- Route Optimization and Dispatching: Utilizing routing software, dispatchers optimize routes for drivers, considering factors such as traffic conditions, delivery windows, and fuel efficiency. Drivers are then dispatched with specific instructions.
- Real-Time Monitoring and Communication: Throughout the day, dispatchers monitor the progress of shipments in real-time using GPS tracking and communication systems. They maintain constant communication with drivers, providing updates and addressing any issues that may arise.
- Problem Solving and Issue Management: Unexpected events, such as truck breakdowns or delivery delays, require immediate attention. Dispatchers work to resolve these issues by coordinating with drivers, customers, and other stakeholders to minimize disruptions.
- Documentation and Reporting: At the end of the day, dispatchers compile reports on key metrics, such as on-time delivery rates, fuel consumption, and driver performance. They also ensure all necessary documentation is completed and filed.
Key Performance Indicators (KPIs) Used to Measure Dispatch Effectiveness
To ensure efficiency and effectiveness, the Riceland Foods dispatch department utilizes a range of KPIs. These metrics provide valuable insights into the department’s performance and highlight areas for improvement.
- On-Time Delivery Rate: This KPI measures the percentage of deliveries that are completed within the agreed-upon timeframe. A high on-time delivery rate indicates efficient planning and execution. For example, a target might be 98% on-time delivery.
- Cost per Shipment: This metric tracks the total cost associated with each shipment, including fuel, labor, and carrier fees. Monitoring this KPI helps to identify opportunities to reduce transportation costs.
- Utilization Rate: This KPI measures the percentage of truck capacity that is used for each shipment. A high utilization rate indicates efficient loading and minimizes wasted space.
- Driver Performance: Tracking driver performance, including metrics like hours of service compliance, fuel efficiency, and adherence to routes, helps to ensure safety and efficiency.
- Customer Satisfaction: Feedback from customers is used to gauge their satisfaction with the delivery process. This can be measured through surveys or direct feedback mechanisms.
- Claims Rate: This KPI tracks the number of claims related to damaged or lost goods. A low claims rate indicates effective handling and transportation of products.
Technology and Systems Used in Dispatch
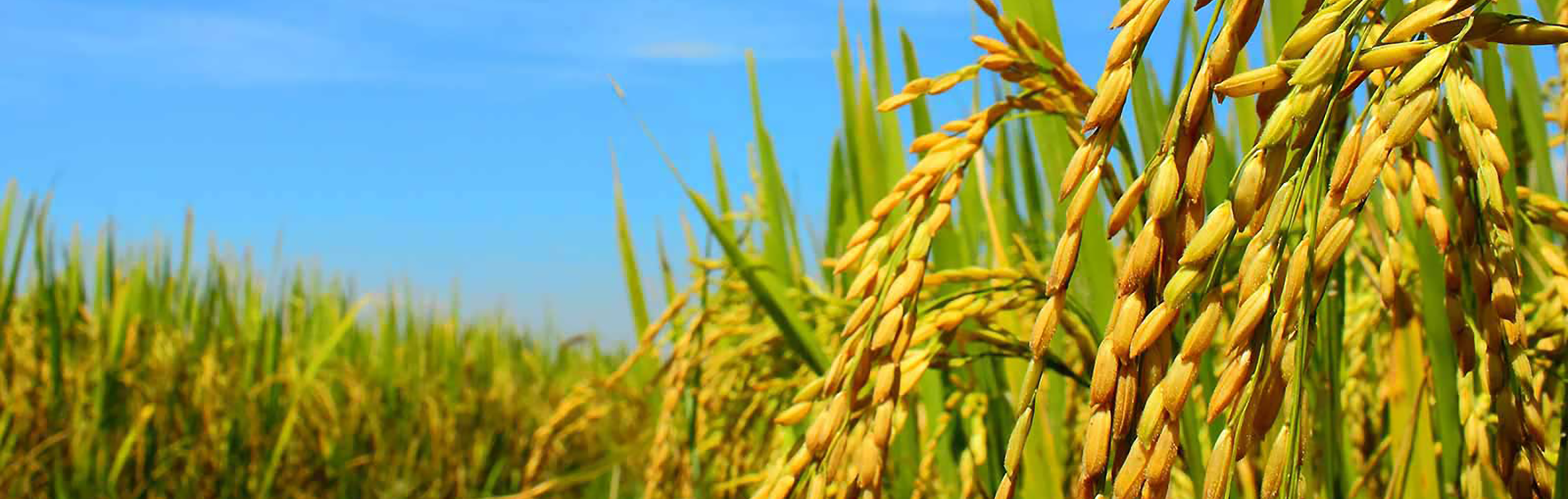
The efficiency of Riceland Foods’ dispatch operations hinges on the integration of various technological systems. These systems streamline communication, enhance real-time tracking, and optimize resource allocation. This section explores the specific software and hardware utilized, the role of GPS tracking, and the overall impact of technology on the dispatch process.
Software and Hardware Systems
Riceland Foods relies on a combination of software and hardware to manage its dispatch operations effectively. These systems are interconnected to provide a comprehensive view of the fleet and facilitate seamless communication.
- Transportation Management System (TMS): A central TMS manages the entire transportation lifecycle, from order entry and route planning to dispatching and freight payment. The TMS at Riceland likely handles tasks such as load optimization, carrier selection, and performance reporting. This system integrates data from various sources to provide real-time visibility into the status of shipments.
- Fleet Management Software: This software monitors vehicle performance, maintenance schedules, and driver behavior. Fleet management software provides insights into fuel consumption, vehicle diagnostics, and driver safety metrics. This enables proactive maintenance and contributes to cost savings and improved safety.
- Communication Systems: Reliable communication is crucial. This includes mobile devices (tablets or smartphones) for drivers, allowing them to receive dispatch instructions, communicate with dispatchers, and report issues. Two-way radio systems may also be employed, especially in areas with limited cellular coverage, for immediate voice communication.
- Hardware: The hardware component includes GPS tracking devices installed in vehicles, servers to host the software applications, and network infrastructure to ensure data transmission. Ruggedized devices are likely used in the vehicles to withstand the rigors of daily operations.
Integration of GPS Tracking
GPS tracking is a fundamental element of Riceland Foods’ dispatch operations, providing real-time location data for all vehicles. This data is integrated into the TMS and fleet management software, enabling improved visibility and control.
- Real-Time Location Monitoring: Dispatchers can pinpoint the exact location of each vehicle at any time. This allows for proactive management of delays, rerouting of vehicles in response to changing conditions, and accurate estimated time of arrival (ETA) predictions.
- Geofencing: Geofencing involves setting up virtual boundaries around specific locations, such as warehouses, distribution centers, or customer sites. When a vehicle enters or exits a geofence, the system automatically generates alerts, providing valuable insights into arrival and departure times.
- Route Optimization: GPS data combined with route planning software allows dispatchers to optimize routes, considering factors such as traffic conditions, road closures, and delivery deadlines. This leads to reduced fuel consumption, minimized travel times, and improved on-time delivery performance.
- Data Analysis: GPS data provides valuable insights into driver behavior, such as speeding, idling, and harsh braking. This information can be used to identify areas for improvement in driver training and to promote safer driving practices.
Impact of Technology on Dispatch Efficiency
The implementation of technology has significantly impacted the efficiency of Riceland Foods’ dispatch operations. However, like any technological advancement, there are both advantages and disadvantages.
Advantages:
- Increased Efficiency: Automation of tasks, such as route planning and dispatching, reduces manual effort and accelerates the overall process.
- Improved Communication: Real-time communication between dispatchers and drivers minimizes delays and enhances responsiveness.
- Enhanced Visibility: Real-time tracking of vehicles provides complete visibility into the status of shipments, enabling proactive management of issues.
- Reduced Costs: Route optimization, fuel efficiency, and proactive maintenance contribute to significant cost savings.
- Improved Customer Service: Accurate ETAs and timely delivery notifications enhance customer satisfaction.
Disadvantages:
- Implementation Costs: Initial investment in software, hardware, and training can be substantial.
- Technical Issues: Systems can be vulnerable to technical glitches, requiring robust support and maintenance.
- Data Security: Protecting sensitive data from cyber threats is critical.
- Dependence on Technology: Over-reliance on technology can lead to inefficiencies if systems fail or are unavailable.
- Training Requirements: Employees require adequate training to effectively utilize and maintain the technology.
Communication Protocols in Dispatch
Effective communication is the cornerstone of efficient dispatch operations at Riceland Foods. Seamless information flow between dispatchers, drivers, and other stakeholders is crucial for timely deliveries, optimized resource allocation, and overall operational success. This section details the communication methods, best practices, and escalation procedures implemented within Riceland Foods’ dispatch system to ensure clear and consistent communication.
Communication Methods Employed by Riceland Foods Dispatchers
Riceland Foods utilizes a multifaceted approach to communication, employing various methods to ensure that information reaches the appropriate parties promptly and reliably. The selection of a particular method often depends on the urgency of the information, the location of the recipient, and the nature of the message.
- Phone: Direct phone calls remain a primary method for real-time communication. Dispatchers use phones to contact drivers for immediate instructions, address urgent issues, and provide updates on delivery schedules. Phone calls are also used to communicate with customers and vendors regarding delivery status, delays, or changes to orders.
- Radio: Two-way radio communication provides a reliable means for dispatchers to communicate with drivers, especially when drivers are in areas with limited cellular coverage. Radios facilitate instant communication and are particularly useful in coordinating operations within the company’s distribution centers and during emergency situations.
- Email: Email is used for non-urgent communication, documentation, and the dissemination of information to a wider audience. Dispatchers use email to send delivery confirmations, provide route updates, share operational procedures, and communicate with other departments. Email is also used to maintain a record of communications and to provide a paper trail for accountability.
- Mobile Applications and Tracking Systems: Riceland Foods leverages mobile applications and GPS tracking systems. These systems allow for real-time tracking of vehicles, providing dispatchers with immediate visibility into driver locations and estimated arrival times. Drivers can use the applications to receive dispatch instructions, update delivery statuses, and communicate with dispatchers through integrated messaging features.
Best Practices for Effective Communication
To maintain clear and efficient communication, Riceland Foods emphasizes the following best practices:
- Clarity and Conciseness: Messages should be clear, concise, and to the point, avoiding jargon and ambiguous language. Dispatchers and drivers are trained to communicate effectively, ensuring that information is understood correctly the first time.
- Active Listening: Dispatchers are trained to listen actively to drivers and other stakeholders, paying attention to both verbal and non-verbal cues. This ensures that all relevant information is captured and that any concerns are addressed promptly.
- Verification and Confirmation: Dispatchers should always verify information received from drivers and other stakeholders, confirming details such as delivery addresses, times, and quantities. This minimizes errors and ensures accuracy. Drivers are encouraged to confirm receipt of instructions.
- Timeliness: Information should be communicated in a timely manner, especially during urgent situations. Dispatchers and drivers are expected to respond promptly to communications and to provide updates on any changes to delivery schedules or routes.
- Professionalism: All communications should be conducted in a professional and respectful manner. Dispatchers and drivers are expected to maintain a positive attitude and to treat each other with courtesy, even during stressful situations.
Escalation Procedures for Communication Issues
To ensure that communication issues are resolved quickly and efficiently, Riceland Foods has established clear escalation procedures. These procedures Artikel the steps to be taken when communication problems arise, ensuring that the appropriate personnel are notified and that corrective actions are implemented. The following table illustrates the escalation procedures.
Issue | Initial Action | Escalation Level 1 | Escalation Level 2 |
---|---|---|---|
Driver Unable to Contact Dispatch | Attempt to contact the driver via radio, then phone. Check driver’s mobile app status. | Contact driver’s supervisor. Review communication logs. Attempt to contact the driver via alternate methods (e.g., email, satellite communication if available). | Contact the Operations Manager. Investigate the root cause (e.g., equipment malfunction, coverage issue). Initiate a formal incident report. |
Dispatcher Unable to Contact Driver | Attempt to contact the driver via radio, then phone. Check the driver’s status in the tracking system. | Contact the driver’s supervisor. Review the driver’s schedule and route. Attempt to contact the driver via alternate methods (e.g., text message). | Contact the Safety Manager. Investigate the driver’s location and any potential safety concerns. Initiate a welfare check if necessary. |
Communication Interference/Disruption | Attempt to re-establish communication. Identify the source of the interference. | Contact the IT department or radio maintenance personnel. Troubleshoot the issue (e.g., adjust radio settings, relocate the vehicle). | Contact the Operations Manager and IT Director. Implement a backup communication plan (e.g., switch to phone calls). Evaluate and implement a permanent solution. |
Driver Management and Coordination: Riceland Foods Dispatch
Effective driver management and coordination are critical components of a successful dispatch operation at Riceland Foods. This involves the strategic assignment of drivers, efficient route planning, and proactive resolution of logistical challenges. The dispatch team serves as the central hub, ensuring that drivers are deployed effectively, deliveries are completed on time, and operational efficiency is maximized.
Driver Assignment and Route Planning
Dispatch plays a pivotal role in driver assignment and route planning, optimizing the use of available resources. This involves matching drivers to specific loads based on factors such as driver availability, vehicle type, load capacity, and delivery location. Route planning software, integrated with real-time traffic data, is employed to determine the most efficient routes, considering factors like distance, road conditions, and potential delays.
Investigate the pros of accepting goat food supplements in your business strategies.
This process aims to minimize fuel consumption, reduce delivery times, and enhance overall operational efficiency.
Handling Driver Requests and Resolving Logistical Challenges
Dispatchers are constantly managing driver requests and resolving a variety of logistical challenges. For example, a driver might encounter unexpected traffic congestion, mechanical issues with the vehicle, or changes in delivery schedules. Dispatchers respond by:
- Re-routing drivers to avoid delays, leveraging real-time traffic information and alternative route suggestions.
- Coordinating with maintenance teams to address vehicle breakdowns, ensuring prompt repairs or vehicle replacements to minimize downtime.
- Communicating with customers regarding any delivery schedule adjustments, providing timely updates and managing expectations.
- Addressing unexpected changes in delivery locations or load requirements, adjusting routes and driver assignments as needed.
These actions highlight the dispatcher’s role as a problem-solver and facilitator, ensuring smooth operations despite unforeseen circumstances.
Common Challenges and Potential Solutions
Dispatchers face various challenges in coordinating with drivers. Addressing these challenges effectively is vital for maintaining operational efficiency and driver satisfaction.
Here are common challenges faced by dispatchers and potential solutions:
- Communication Barriers: Difficulties in clear and timely communication between dispatchers and drivers can lead to misunderstandings, delays, and errors.
- Solution: Implement standardized communication protocols, utilize reliable communication systems (e.g., two-way radios, mobile apps), and provide regular training on effective communication techniques.
- Driver Fatigue and Hours of Service (HOS) Compliance: Managing driver fatigue and ensuring compliance with HOS regulations is crucial for safety and legal compliance.
- Solution: Utilize electronic logging devices (ELDs) to monitor driver hours, integrate HOS data into route planning to avoid scheduling conflicts, and establish policies that encourage drivers to take breaks and rest periods.
- Traffic Congestion and Unforeseen Delays: Unexpected traffic incidents, road closures, or other delays can disrupt delivery schedules and impact efficiency.
- Solution: Use real-time traffic data and route optimization software to identify and avoid congested areas, establish contingency plans for dealing with delays (e.g., alternative routes, customer communication), and provide drivers with regular updates on traffic conditions.
- Vehicle Maintenance and Breakdowns: Mechanical issues and vehicle breakdowns can cause significant delays and disruptions.
- Solution: Implement a proactive vehicle maintenance program to prevent breakdowns, establish a rapid response plan for addressing breakdowns (e.g., roadside assistance, spare vehicles), and provide drivers with training on basic vehicle troubleshooting.
- Driver Availability and Unexpected Absences: Unforeseen driver absences can disrupt dispatch operations.
- Solution: Maintain a pool of backup drivers, develop flexible scheduling options, and provide clear policies regarding driver absences and call-offs.
Emergency Procedures and Incident Response
The safety and well-being of Riceland Foods’ drivers, cargo, and the public are paramount. The dispatch team plays a critical role in managing emergencies and incidents, ensuring a swift and coordinated response to mitigate risks and minimize potential damage. This section Artikels the established procedures and protocols followed by the dispatch team during emergency situations.
Emergency Response Procedures
The dispatch team adheres to a comprehensive set of procedures to handle various emergencies. These procedures are regularly reviewed and updated to reflect best practices and regulatory requirements.
- Initial Notification and Verification: Upon receiving a report of an incident, whether from a driver, the public, or another source, the dispatch team immediately verifies the information. This involves confirming the location, nature of the incident (e.g., accident, mechanical failure, cargo issue), and the parties involved.
- Assessment and Prioritization: The dispatch team assesses the severity of the incident based on the information gathered. Incidents are prioritized based on the potential for harm to life, property, and the environment. This assessment informs the subsequent response actions.
- Communication and Coordination: The dispatch team initiates communication with relevant parties, including the driver, emergency services (police, fire, ambulance), and internal stakeholders (safety department, maintenance). Communication is maintained throughout the incident to ensure a coordinated response.
- Resource Allocation: Based on the nature of the incident, the dispatch team allocates necessary resources. This may include directing other drivers to provide assistance, contacting roadside assistance, or coordinating the deployment of specialized equipment.
- Documentation and Reporting: The dispatch team meticulously documents all aspects of the incident, including communication logs, actions taken, and the outcome. This documentation is essential for post-incident analysis, insurance claims, and regulatory compliance.
Coordination with Emergency Services
Effective coordination with emergency services is crucial for ensuring a timely and appropriate response. The dispatch team maintains established protocols for communicating with these services.
- Contact Protocols: The dispatch team has established contact protocols with local and regional emergency services, including pre-determined contact numbers and communication channels.
- Information Sharing: The dispatch team provides emergency services with essential information, including the location of the incident, the nature of the cargo (if applicable), the number of vehicles involved, and any known hazards.
- On-Scene Support: The dispatch team may provide support to emergency services on-scene, such as directing traffic, providing information about the vehicle’s specifications, or assisting with cargo handling (if safe and appropriate).
- Regular Training and Drills: The dispatch team participates in regular training exercises and drills with emergency services to enhance coordination and improve response times.
Driver and Cargo Safety Measures
The safety of drivers and cargo is a top priority. The dispatch team implements specific measures to ensure safety in the event of an accident or other incident.
- Driver Contact and Support: The dispatch team maintains contact with the affected driver(s) to assess their condition and provide support. This may include offering reassurance, contacting family members, and coordinating medical assistance.
- Cargo Protection: In the event of an accident involving hazardous materials, the dispatch team coordinates with hazmat teams to ensure the safe containment and cleanup of the cargo. For non-hazardous cargo, the team assesses the condition of the cargo and takes steps to prevent further damage or theft.
- Vehicle Recovery and Inspection: The dispatch team coordinates the recovery of damaged vehicles and arranges for inspections to determine the cause of the incident and identify any necessary repairs.
- Post-Incident Review: After each incident, the dispatch team conducts a post-incident review to identify areas for improvement in procedures and training. This review process contributes to continuous improvement in safety performance.
Load Planning and Scheduling
Load planning and scheduling are critical functions within Riceland Foods’ dispatch operations, directly impacting efficiency, cost-effectiveness, and customer satisfaction. This process involves strategically organizing shipments, optimizing routes, and assigning drivers to ensure timely and cost-efficient delivery of agricultural products. Effective load planning minimizes empty miles, reduces fuel consumption, and improves overall operational productivity.
Process of Load Planning and Scheduling
The process of load planning and scheduling at Riceland Foods is a multi-step procedure. This process requires a combination of technological tools and human expertise to achieve optimal results.The following steps are crucial:
- Order Intake and Analysis: All incoming orders are received and analyzed. This involves assessing the quantity of product, the destination, delivery deadlines, and any special handling requirements. Data is pulled from the sales and inventory management systems.
- Load Building: Based on the order analysis, loads are built. This involves grouping orders that can be transported together, considering factors such as product compatibility, weight limits, and delivery locations. The objective is to maximize trailer utilization.
- Route Optimization: Sophisticated routing software is used to determine the most efficient routes for each load. The software considers factors such as distance, traffic conditions, road restrictions, and driver availability.
- Driver Assignment: Once the routes are optimized, drivers are assigned to the loads. This takes into account driver availability, hours of service regulations, and driver experience with specific types of loads.
- Communication and Dispatch: The dispatch team communicates load details, routes, and any special instructions to the assigned drivers. Real-time tracking systems are used to monitor the progress of each load.
- Monitoring and Adjustment: The dispatch team continuously monitors the progress of the loads and makes adjustments as needed. This may involve rerouting due to unforeseen circumstances, contacting customers, or coordinating with other departments.
Optimizing Routes to Reduce Transportation Costs
Riceland Foods employs several strategies to optimize routes and minimize transportation costs. Route optimization is not a one-time event but a continuous process of analysis and improvement.Key strategies include:
- Using Route Optimization Software: Sophisticated software analyzes various factors such as distance, traffic, and road conditions to determine the most efficient routes. The software also considers the type of vehicle, its capacity, and fuel efficiency.
- Consolidating Shipments: Combining multiple smaller orders into a single, larger shipment reduces the number of trips and minimizes empty miles. This is particularly effective for shipments to the same destination or along the same route.
- Backhauling: Arranging for trucks to pick up goods on their return trips from deliveries. This reduces empty miles and generates revenue for the return journey.
- Negotiating Fuel Prices: Riceland Foods leverages its volume purchasing power to negotiate favorable fuel prices with suppliers. This can significantly reduce fuel costs, which is a major component of transportation expenses.
- Monitoring Driver Performance: Tracking driver performance metrics, such as fuel efficiency and adherence to routes, helps identify areas for improvement. Driver training and incentives can be used to promote better driving practices.
“Effective route optimization can lead to a 10-15% reduction in transportation costs, depending on the specific circumstances and the technology employed.”
Types of Loads and Requirements
Riceland Foods handles various types of loads, each with specific requirements that influence load planning and scheduling. Understanding these requirements is crucial for ensuring safe, efficient, and compliant transportation.The following table Artikels the different types of loads handled and their specific requirements:
Load Type | Product Characteristics | Handling Requirements | Scheduling Considerations |
---|---|---|---|
Bulk Grain (e.g., Rice, Soybeans) | High volume, free-flowing, can be sensitive to moisture. | Requires specialized trailers (e.g., hopper-bottom trailers), protection from the elements, and careful loading/unloading to prevent spillage. | Seasonal variations in demand, quick turnaround times at elevators and processing plants, coordination with harvest schedules. |
Packaged Rice Products | Palletized, various package sizes, susceptible to damage if improperly handled. | Requires enclosed trailers, proper palletization and securement, and careful handling during loading and unloading to prevent damage. | Adherence to delivery appointments, efficient loading and unloading procedures at distribution centers and retail locations, and managing order fulfillment. |
Fertilizers and Crop Protection Products | Can be hazardous, requiring specific handling and transportation regulations. | Requires compliance with DOT regulations for hazardous materials, specialized equipment (e.g., tank trucks), and trained drivers. | Strict adherence to safety protocols, ensuring proper documentation, and coordinating with regulatory agencies. |
Ingredients for Food Processing | Variety of ingredients, may require temperature control or special storage. | May require refrigerated trailers, careful handling to prevent contamination, and adherence to food safety standards. | Coordination with production schedules, timely deliveries to processing plants, and monitoring of temperature-sensitive products. |
Compliance and Regulatory Adherence
The Riceland Foods dispatch department plays a critical role in ensuring adherence to a complex web of transportation regulations. This responsibility safeguards the company from legal penalties, protects its drivers, and contributes to the overall safety of the supply chain. Compliance is not merely a procedural necessity but a cornerstone of responsible business practices, reflecting Riceland Foods’ commitment to ethical operations and public safety.
Dispatch Department’s Role in Regulatory Compliance
The dispatch department acts as the primary interface between the company and the regulatory environment, specifically concerning driver operations and vehicle movements. Dispatchers are responsible for proactively managing and monitoring activities to ensure that all operations comply with federal, state, and local regulations. This involves a multi-faceted approach, from initial driver qualification checks to ongoing monitoring of driver hours and vehicle maintenance schedules.
They also serve as the point of contact for roadside inspections and audits, providing necessary documentation and facilitating communication with regulatory agencies. Furthermore, dispatchers must stay informed of evolving regulations and adapt dispatching practices accordingly.
Monitoring Driver Hours of Service (HOS)
A key aspect of compliance involves meticulously monitoring driver hours of service (HOS) to prevent fatigue-related accidents and ensure adherence to regulations established by the Federal Motor Carrier Safety Administration (FMCSA). Dispatchers employ various methods to monitor HOS, including electronic logging devices (ELDs), which automatically record a driver’s driving time and other activities.
- ELD Data Review: Dispatchers regularly review ELD data to verify drivers are compliant with HOS regulations, including the 11-hour driving limit, the 14-hour on-duty limit, and mandatory rest periods. They analyze this data to identify potential violations and take corrective actions.
- Proactive Scheduling: Dispatchers plan routes and schedules with HOS regulations in mind. This includes accounting for travel time, loading and unloading times, and potential delays. They proactively communicate with drivers regarding upcoming HOS limits to avoid violations.
- Driver Communication: Dispatchers maintain open communication with drivers, encouraging them to report any issues or potential violations. This fosters a culture of compliance and enables dispatchers to make necessary adjustments to schedules.
- Alert Systems: Dispatch systems are often integrated with alert mechanisms that notify dispatchers when a driver is approaching their HOS limits. These alerts allow dispatchers to intervene and prevent violations.
- Record Keeping: Dispatchers maintain detailed records of driver HOS data, including ELD reports, inspection reports, and any corrective actions taken. These records are essential for audits and compliance reviews.
Key Regulatory Requirements Impacting Riceland Foods Dispatch Operations
Riceland Foods dispatch operations are subject to a range of regulatory requirements, with significant impact on daily operations. These regulations address various aspects of transportation, including driver qualifications, vehicle safety, and operational procedures.
- Hours of Service (HOS) Regulations: The FMCSA sets limits on the number of hours drivers can work and drive. These regulations include the 11-hour driving limit, the 14-hour on-duty limit, and mandatory rest periods. These rules are designed to prevent driver fatigue and reduce the risk of accidents. Riceland Foods must ensure its dispatchers are well-versed in these regulations and use them to schedule drivers.
- Commercial Driver’s License (CDL) Requirements: Drivers must hold a valid CDL and meet specific medical and physical requirements. Dispatchers are responsible for verifying that drivers possess the necessary licenses and that their medical certifications are current.
- Electronic Logging Device (ELD) Mandate: The ELD mandate requires most commercial drivers to use ELDs to record their hours of service. Dispatchers must be trained in ELD management and data review to ensure compliance. The data from ELDs is used to verify HOS compliance.
- Vehicle Maintenance and Safety Standards: Vehicles must meet specific safety standards and undergo regular inspections. Dispatchers must coordinate maintenance schedules and ensure vehicles are compliant with federal and state regulations.
- Drug and Alcohol Testing: The FMCSA requires commercial drivers to undergo drug and alcohol testing. Dispatchers are responsible for ensuring that drivers are compliant with these testing requirements and for coordinating testing programs.
- Hazardous Materials Regulations: If Riceland Foods transports hazardous materials, it must comply with the Department of Transportation (DOT) regulations for transporting hazardous materials. This includes specific training requirements, packaging and labeling requirements, and emergency response procedures.
- CSA (Compliance, Safety, Accountability) Program: The CSA program is a data-driven program that scores motor carriers on their safety performance. Dispatchers must understand how their actions affect the CSA scores and work to improve them. The CSA program focuses on several areas, including unsafe driving, hours-of-service compliance, and vehicle maintenance.
Training and Development for Dispatchers
Riceland Foods recognizes that a highly skilled and well-trained dispatch team is critical to the efficient and safe operation of its transportation network. Investing in comprehensive training and ongoing development programs is a core tenet of Riceland’s operational strategy, ensuring dispatchers are equipped with the knowledge, skills, and abilities to manage complex logistical challenges effectively. This commitment directly contributes to minimizing downtime, optimizing resource allocation, and maintaining the highest standards of safety and compliance.
Training Programs Provided to Dispatch Personnel
Riceland Foods provides a multifaceted training program for its dispatch personnel, incorporating both initial onboarding and ongoing professional development. These programs are designed to cover all aspects of dispatch operations, from fundamental skills to advanced techniques, and are continuously updated to reflect industry best practices and technological advancements.
- Initial Onboarding Training: This comprehensive program is the foundation for all new dispatchers. It typically lasts for several weeks and combines classroom instruction, hands-on simulations, and mentorship from experienced dispatchers. The curriculum covers the following key areas:
- Company Policies and Procedures: This module covers Riceland’s specific operational protocols, safety regulations, and ethical guidelines.
- Dispatch Software Training: New dispatchers receive in-depth training on the company’s Transportation Management System (TMS) and any other software applications used for dispatching, including load planning, tracking, and communication tools. This includes how to use the system, troubleshoot issues, and generate reports.
- Communication Skills: Dispatchers are trained in effective communication techniques, including active listening, clear and concise verbal and written communication, and conflict resolution. This training focuses on communicating with drivers, customers, and other stakeholders.
- Load Planning and Scheduling: This module covers the principles of load planning, including route optimization, driver assignment, and load balancing.
- Emergency Procedures: Training on emergency response protocols, including accident reporting, incident management, and communication with emergency services.
- Compliance and Regulatory Adherence: This training ensures that dispatchers understand and adhere to all relevant regulations, including hours-of-service (HOS) rules, Department of Transportation (DOT) regulations, and other legal requirements.
- Ongoing Professional Development: Beyond initial training, Riceland offers continuous professional development opportunities to keep dispatchers’ skills sharp and to promote career advancement. These include:
- Refresher Courses: Periodic refreshers on key topics such as safety, regulatory updates, and new software features.
- Advanced Training Modules: Specialized training in areas such as route optimization, advanced load planning, and conflict resolution.
- Industry Certifications: Support for dispatchers to obtain industry-recognized certifications, such as the Certified Transportation Professional (CTP) designation.
- Mentorship Programs: Pairing experienced dispatchers with newer team members to provide guidance and support.
- Technology Upgrades: Training on any new technologies or software updates implemented within the dispatch system.
Skills and Competencies Required for Successful Dispatching
Successful dispatching requires a blend of technical skills, interpersonal abilities, and problem-solving capabilities. Riceland Foods actively cultivates these skills within its dispatch team to ensure operational efficiency and customer satisfaction.
- Technical Skills:
- Proficiency in Transportation Management Systems (TMS): Dispatchers must be adept at using the company’s TMS to manage loads, track vehicles, communicate with drivers, and generate reports.
- Data Analysis: The ability to analyze data to identify trends, optimize routes, and improve operational efficiency.
- Geographic Information Systems (GIS) knowledge: Understanding of mapping software and route planning tools.
- Computer Literacy: Basic computer skills, including proficiency in Microsoft Office Suite (Word, Excel, Outlook).
- Interpersonal Skills:
- Communication Skills: Excellent verbal and written communication skills, including the ability to communicate clearly and concisely with drivers, customers, and other stakeholders.
- Active Listening: The ability to listen attentively to drivers’ concerns and provide appropriate solutions.
- Conflict Resolution: The ability to resolve conflicts and de-escalate tense situations.
- Teamwork: The ability to work effectively as part of a team and collaborate with other departments.
- Problem-Solving and Decision-Making Skills:
- Critical Thinking: The ability to analyze situations, identify problems, and develop effective solutions.
- Decision-Making: The ability to make sound decisions under pressure, including in emergency situations.
- Time Management: The ability to prioritize tasks, manage time effectively, and meet deadlines.
- Adaptability: The ability to adapt to changing situations and handle unexpected events.
- Knowledge of Regulations and Compliance:
- Understanding of DOT Regulations: Comprehensive knowledge of hours-of-service (HOS) rules, vehicle maintenance requirements, and other relevant regulations.
- Safety Awareness: Commitment to safety protocols and procedures.
- Compliance with Company Policies: Adherence to all company policies and ethical guidelines.
Process of Onboarding a New Dispatcher
Riceland Foods has a structured onboarding process to integrate new dispatchers into the team seamlessly. This process ensures that new hires are well-prepared for their roles and understand the company’s culture and expectations.
- Recruitment and Selection: This initial phase involves the recruitment process, including job postings, resume screening, interviews, and background checks. Candidates are assessed based on their skills, experience, and suitability for the role.
- Offer and Onboarding Documentation: Once a candidate is selected, an offer of employment is extended, and the necessary paperwork is completed, including employment contracts, benefits enrollment, and required compliance documents.
- Initial Orientation: New dispatchers are introduced to the company culture, values, and mission. They receive an overview of the company’s structure, departments, and key personnel.
- Training and Development (as detailed above): The new dispatcher begins the comprehensive training program, which includes classroom instruction, hands-on simulations, and mentorship. This training covers all aspects of dispatch operations, from software training to communication skills.
- Mentorship and Shadowing: New dispatchers are paired with experienced mentors who provide guidance and support. They shadow experienced dispatchers to observe their daily routines and learn from their expertise.
- Performance Evaluation: Regular performance evaluations are conducted to assess the new dispatcher’s progress and provide feedback. These evaluations help identify areas for improvement and ensure that the dispatcher is meeting performance expectations.
- Ongoing Support and Development: The onboarding process is ongoing, with continuous support and development opportunities available to help the dispatcher grow and advance in their career.
Metrics and Reporting in Dispatch
Monitoring and evaluating the performance of a dispatch operation is crucial for continuous improvement and ensuring efficient resource allocation. This involves tracking key performance indicators (KPIs) and generating reports that provide insights into operational effectiveness, identify areas for improvement, and support data-driven decision-making. Effective reporting mechanisms are essential for Riceland Foods to optimize its dispatch operations, enhance customer satisfaction, and maintain a competitive edge.
Reporting Mechanisms for Tracking Dispatch Performance
A variety of reporting mechanisms are employed to monitor and evaluate dispatch performance. These mechanisms collect and analyze data from various sources, providing a comprehensive view of operational efficiency.
- Real-time Dashboards: Real-time dashboards display key metrics, such as the number of active drivers, delivery status, and potential delays. These dashboards provide immediate visibility into current operations, allowing dispatchers to proactively address issues as they arise. For example, a dashboard might show a live map with the location of all delivery vehicles, color-coded to indicate their status (e.g., en route, delayed, completed).
- Automated Reporting Systems: Automated reporting systems generate periodic reports on pre-defined KPIs. These systems often utilize software that automatically pulls data from dispatch software, GPS tracking systems, and other relevant sources. Reports can be generated daily, weekly, or monthly, depending on the specific needs of the operation.
- Customizable Reporting Tools: Dispatch operations often utilize customizable reporting tools that allow users to create ad-hoc reports based on specific needs. These tools enable users to filter data, create visualizations, and analyze trends.
- Data Warehousing: Data warehousing involves storing large volumes of historical dispatch data in a centralized repository. This allows for long-term trend analysis and the identification of patterns over time. For example, Riceland Foods could use data warehousing to analyze delivery times over several years, identifying seasonal variations or the impact of new routes.
- Exception Reporting: Exception reporting focuses on identifying and highlighting deviations from established norms. This might include reports on late deliveries, driver incidents, or vehicle maintenance issues. Exception reports enable dispatchers to quickly address problem areas.
Utilization of Dispatch Data for Improving Operational Efficiency
Dispatch data provides valuable insights that can be used to drive improvements in operational efficiency. Analyzing this data allows Riceland Foods to optimize resource allocation, streamline processes, and enhance overall performance.
- Route Optimization: Dispatch data, including GPS tracking information and delivery times, can be used to optimize delivery routes. Software algorithms can analyze this data to identify the most efficient routes, minimizing travel time and fuel consumption. For instance, historical data can reveal that a specific route consistently experiences delays due to traffic congestion, prompting a route adjustment.
- Resource Allocation: Data on delivery volumes, driver availability, and vehicle capacity can be used to optimize resource allocation. This includes ensuring that the right number of drivers and vehicles are available to meet demand, minimizing idle time, and maximizing utilization rates. For example, data may reveal that more drivers are needed during peak delivery hours.
- Performance Monitoring: Dispatch data enables the tracking of individual driver and vehicle performance. KPIs such as on-time delivery rates, fuel efficiency, and incident rates can be monitored to identify areas for improvement.
- Process Improvement: Analyzing dispatch data can help identify bottlenecks and inefficiencies in the delivery process. For example, data may reveal that a significant amount of time is spent on loading and unloading, prompting process improvements.
- Predictive Analytics: Utilizing historical dispatch data, predictive analytics can forecast future demand, allowing for proactive resource planning. For instance, historical data can be analyzed to anticipate increases in delivery volumes during certain seasons or events, allowing Riceland Foods to prepare its dispatch operations accordingly.
Process of Generating Reports on Key Dispatch Metrics
Generating reports on key dispatch metrics involves a structured process that includes data collection, analysis, and presentation. This process ensures that the reports are accurate, reliable, and provide actionable insights.
- Data Collection: The first step is to collect data from various sources, including dispatch software, GPS tracking systems, and driver logs. This data should be accurate, complete, and reliable.
- Data Processing and Cleaning: The collected data is then processed and cleaned to ensure consistency and accuracy. This may involve removing duplicate entries, correcting errors, and standardizing data formats.
- Metric Calculation: Key dispatch metrics are calculated based on the processed data. These metrics might include on-time delivery rate, average delivery time, fuel efficiency, and driver utilization.
- Report Generation: Reports are generated using reporting tools or software. These reports typically include charts, graphs, and tables that visualize the key metrics.
- Report Distribution and Review: The generated reports are distributed to relevant stakeholders, such as dispatchers, managers, and executives. The reports are then reviewed to identify trends, patterns, and areas for improvement.
- Action and Follow-up: Based on the insights gained from the reports, actions are taken to improve dispatch operations. This might include route optimization, resource reallocation, or process improvements. The effectiveness of these actions is then monitored through subsequent reports.
Impact of External Factors on Dispatch
External factors significantly influence the efficiency and effectiveness of dispatch operations. These factors, ranging from unpredictable weather patterns to fluctuating market demands, necessitate adaptable strategies and proactive planning to maintain operational continuity and meet service level agreements. The ability to anticipate and respond to these external pressures is critical for Riceland Foods to optimize its logistics and distribution network.
Weather’s Influence on Dispatch Operations
Weather conditions present considerable challenges to dispatch operations. Adverse weather can disrupt delivery schedules, increase transit times, and pose safety risks to drivers and equipment. Dispatch teams must continuously monitor weather forecasts and adjust plans accordingly.
- Impact of Severe Weather: Severe weather events, such as hurricanes, blizzards, or floods, can lead to road closures, power outages, and damage to infrastructure. These events can halt or severely delay deliveries. For example, a major snowstorm could force the rerouting of trucks to alternative routes, increasing travel times and fuel consumption.
- Adaptation Strategies: Dispatchers utilize various strategies to mitigate weather-related impacts. This includes:
- Route Optimization: Re-routing trucks to avoid areas affected by weather conditions.
- Proactive Communication: Informing drivers about potential hazards and providing real-time updates on road conditions.
- Load Adjustments: Adjusting load sizes to account for potential delays or reduced speed limits.
- Emergency Planning: Having contingency plans in place for severe weather events, including backup routes, driver accommodations, and communication protocols.
- Data-Driven Decision Making: Leveraging weather data from reliable sources, such as the National Weather Service, allows dispatchers to make informed decisions. This data can be integrated with route planning software to identify and avoid weather-impacted areas.
Adaptation to Changes in Supply and Demand
Fluctuations in supply and demand necessitate flexibility and responsiveness within dispatch operations. Understanding market trends and consumer behavior allows Riceland Foods to optimize its distribution network to meet changing needs.
- Impact of Demand Fluctuations: Changes in consumer demand, influenced by seasonal factors, promotional events, or economic conditions, directly affect the volume of orders and the required transportation capacity. For instance, an increase in demand for rice during a holiday season necessitates increased truck availability and efficient route planning.
- Supply Chain Considerations: Dispatch operations must consider supply chain disruptions that affect the availability of raw materials or finished goods. Delays in sourcing or production can impact delivery schedules and require adjustments to the dispatch plan.
- Demand Forecasting and Planning: Accurate demand forecasting is crucial for proactive dispatch planning. This involves analyzing historical sales data, market trends, and external factors to predict future demand.
Accurate forecasting enables the dispatch team to proactively allocate resources, such as trucks and drivers, to meet anticipated demand.
- Examples of Adaptation:
- Increased Truck Capacity: During peak demand periods, dispatch teams may utilize additional trucks, contract with third-party carriers, or optimize truckload utilization to transport a higher volume of goods.
- Flexible Scheduling: Dispatchers adjust driver schedules and delivery routes to accommodate changing demand patterns. This may involve extending operating hours or implementing staggered delivery times.
- Inventory Management: Effective inventory management helps mitigate the impact of demand fluctuations. By maintaining adequate stock levels, Riceland Foods can meet customer orders promptly, even during peak demand periods.
Seasonal Fluctuations and Demand Planning
Seasonal variations in demand require proactive planning and resource allocation. Riceland Foods experiences seasonal demand shifts, particularly during harvest seasons and holiday periods.
- Harvest Season Preparation: The harvest season significantly impacts the demand for transportation services. Increased grain production necessitates the efficient movement of harvested rice from farms to processing facilities and distribution centers. Dispatch teams must plan for increased truckloads, optimized routes, and extended operating hours during this period.
- Holiday Season Planning: Holiday seasons often lead to increased consumer demand for rice and related products. Dispatch teams must prepare for higher order volumes, increased delivery frequency, and potential congestion on transportation networks.
- Proactive Planning Measures:
- Capacity Planning: Ensuring sufficient truck capacity and driver availability to handle increased demand. This may involve leasing additional trucks, contracting with third-party carriers, or optimizing truckload utilization.
- Route Optimization: Optimizing delivery routes to minimize transit times and ensure timely deliveries. This includes considering traffic patterns, road closures, and other potential delays.
- Communication and Coordination: Maintaining effective communication with drivers, customers, and other stakeholders to ensure smooth operations. This includes providing real-time updates on delivery status, addressing any issues or delays promptly, and coordinating with loading and unloading facilities.
- Performance Monitoring: Dispatch teams continuously monitor key performance indicators (KPIs) during seasonal fluctuations to assess operational efficiency. This includes tracking on-time delivery rates, transit times, and customer satisfaction levels. The analysis of KPIs helps identify areas for improvement and informs future planning efforts.
Outcome Summary
In conclusion, my brothers and sisters, the Riceland Foods Dispatch is a testament to the power of organization, technology, and human effort. From the initial planning to the final delivery, every step is crucial. Remember, just as the dispatch team ensures the smooth flow of goods, we, too, must strive to streamline our lives with good planning and execution. May Allah guide us in all our endeavors.
Jazakumullahu Khairan.