Food grade plastic barrels are essential components in the modern food industry, playing a critical role in the safe storage and transportation of a wide array of consumables. These unassuming containers are far more complex than they appear, representing a confluence of material science, manufacturing precision, and stringent regulatory compliance. From the humble beginnings of food preservation to the sophisticated systems of today, the evolution of these barrels reflects the advancements in our understanding of food safety and the demands of a globalized food supply chain.
This exploration delves into every facet of food grade plastic barrels, starting with their fundamental purpose and tracing their historical development. We’ll unpack the materials used, examining their properties and comparing their suitability for various applications. We will navigate the intricate manufacturing processes, the regulatory landscape that governs them, and the diverse industries that rely on them. Furthermore, the discussion will encompass best practices for cleaning, maintenance, and responsible disposal, all while considering the environmental impact and the latest innovations in design and market trends.
Introduction to Food Grade Plastic Barrels
Food-grade plastic barrels are essential containers in the food and beverage industry, designed specifically for the safe storage and transportation of consumables. These barrels are engineered to meet stringent safety standards, ensuring that the contents remain uncontaminated and maintain their quality throughout the supply chain. Their versatility and durability have made them indispensable for various applications, from storing bulk ingredients to facilitating the distribution of finished products.The importance of using food-grade materials cannot be overstated, as it directly impacts public health and product integrity.
These materials are chosen for their inertness and resistance to chemical reactions, ensuring that the stored substances do not interact with the container and remain safe for consumption. This introduction explores the core aspects of these essential containers, examining their history, applications, and the critical role they play in the food industry.
Fundamental Purpose and Application
Food-grade plastic barrels serve a critical function: providing a safe and reliable means of storing and transporting a wide array of food and beverage products. Their primary purpose is to protect the contents from external contaminants, maintain product quality, and facilitate efficient handling and distribution. These barrels are used throughout the food supply chain, from the initial processing stages to the final delivery to consumers.Here are some common applications:
- Bulk Storage of Ingredients: Barrels are used to store raw materials like syrups, oils, and flavorings. For example, a large brewery might use food-grade barrels to store malt extract.
- Transportation of Liquids: Liquids such as water, juices, and milk are frequently transported in food-grade barrels, ensuring that these products arrive at their destination in a safe and sanitary condition.
- Fermentation and Aging: In the winemaking and brewing industries, these barrels can be used for fermentation and aging processes. This allows for controlled environmental conditions.
- Food Processing: Food-grade barrels can be used in various food processing operations, such as mixing, blending, and storage of intermediate products.
History of Food-Grade Plastic Barrels
The evolution of food-grade plastic barrels reflects advancements in material science and manufacturing processes, driven by the need for safer and more efficient food storage solutions. Early iterations were primarily made from materials like wood and metal, but these had limitations in terms of sanitation, durability, and cost-effectiveness. The introduction of plastics revolutionized the industry.Key developments include:
- Early Plastics (Mid-20th Century): The initial use of plastics in food storage focused on materials like polyethylene and polypropylene. These materials offered improved resistance to chemicals and were lighter and more cost-effective than traditional options.
- Advancements in Polymer Technology: Over time, polymer technology advanced, leading to the development of more specialized food-grade plastics. This allowed for better barrier properties to prevent contamination and preserve the quality of stored products.
- Regulatory Standards and Certifications: The establishment of regulatory standards and certifications, such as those from the Food and Drug Administration (FDA) in the United States and similar bodies worldwide, played a crucial role. These standards ensure that the materials used in food-grade barrels meet specific safety and purity requirements.
- Sustainable Practices: Recent years have seen a growing focus on sustainability, leading to the development of food-grade barrels made from recycled plastics and bio-based materials.
Significance of Using Food-Grade Materials
The use of food-grade materials is paramount in the food and beverage industry, directly impacting consumer health and product quality. These materials are selected based on their inertness, which means they do not react with the stored food or beverage products. This prevents the leaching of harmful chemicals into the contents, ensuring that the final product is safe for consumption.The significance can be illustrated by these points:
- Preventing Contamination: Food-grade materials are designed to create a barrier against external contaminants such as bacteria, mold, and other microorganisms. This helps to extend the shelf life of the product and maintain its safety.
- Maintaining Product Quality: The use of appropriate materials ensures that the taste, color, and nutritional value of the food or beverage are preserved. The materials are resistant to degradation and do not impart any off-flavors or odors to the contents.
- Regulatory Compliance: The food and beverage industry is subject to strict regulations, and using food-grade materials is a key aspect of compliance. Non-compliance can lead to product recalls, legal issues, and damage to brand reputation.
- Consumer Trust: Consumers rely on food manufacturers to provide safe and high-quality products. Using food-grade materials is essential for building and maintaining consumer trust.
Materials Used in Food Grade Barrels
Food-grade plastic barrels are essential for storing and transporting a wide variety of food products. The safety and integrity of these barrels depend heavily on the materials they are made from. Choosing the right plastic is crucial to ensure that the food remains uncontaminated, maintains its quality, and the barrel itself withstands the rigors of handling and storage. Understanding the different types of plastics used, their properties, and their limitations is vital for both manufacturers and end-users.
Common Plastics Used in Food Grade Barrels
Several types of plastics are commonly employed in the manufacturing of food-grade barrels, each offering a unique set of characteristics suitable for different applications. These plastics are chosen for their inertness, meaning they don’t react with food, and their ability to withstand various environmental conditions.
- High-Density Polyethylene (HDPE): This is one of the most widely used plastics for food-grade barrels. It is known for its excellent chemical resistance, high strength-to-density ratio, and ability to withstand a wide range of temperatures. HDPE is often used for storing liquids, powders, and solids.
- Polypropylene (PP): PP is another common choice, offering good resistance to chemicals, fatigue, and heat. It’s a lighter plastic compared to HDPE, and it is often used in barrels designed for hot-fill applications, where the product is poured into the container while still hot.
- Polyethylene Terephthalate (PET): While PET is more commonly used for bottles, it can also be found in some barrel applications, particularly for products that require a clear or translucent container. PET offers good clarity, strength, and barrier properties against gases and moisture.
- Low-Density Polyethylene (LDPE): LDPE is more flexible than HDPE and PP. It’s sometimes used for liners or smaller barrels due to its flexibility and good chemical resistance, though it’s less common for large-scale barrel manufacturing.
Properties of Plastics in Food Grade Barrels
The properties of the plastics used in food-grade barrels determine their suitability for different applications. These properties directly impact the safety, durability, and performance of the barrels.
- Durability: The durability of a barrel is its ability to withstand physical stress, such as impacts, drops, and stacking. HDPE and PP generally offer high durability, making them suitable for rough handling.
- Chemical Resistance: Chemical resistance refers to the ability of the plastic to resist degradation when exposed to various chemicals, including acids, bases, and solvents. HDPE and PP are known for their excellent chemical resistance, which is crucial for storing a wide range of food products.
- Temperature Tolerance: Temperature tolerance refers to the range of temperatures the plastic can withstand without losing its structural integrity or releasing harmful chemicals. PP has a higher temperature tolerance than HDPE, making it suitable for hot-fill applications.
- Barrier Properties: Barrier properties refer to the plastic’s ability to prevent the passage of gases, moisture, and other substances. PET offers good barrier properties, helping to preserve the freshness and quality of the food product.
Comparison of Plastic Materials
The selection of the appropriate plastic for a food-grade barrel involves a careful consideration of the specific requirements of the application. The following table provides a comparison of the pros and cons of the different plastic materials commonly used.
Material | Pros | Cons |
---|---|---|
HDPE (High-Density Polyethylene) | Excellent chemical resistance; High strength-to-density ratio; Durable; Relatively inexpensive; Recyclable. | Lower temperature tolerance compared to PP; Can be less clear than PET; May be susceptible to stress cracking. |
PP (Polypropylene) | Good chemical resistance; High temperature tolerance; Lightweight; Fatigue resistance; Recyclable. | Lower impact strength than HDPE; Can be more expensive than HDPE; Susceptible to oxidation with prolonged UV exposure. |
PET (Polyethylene Terephthalate) | Excellent clarity; Good barrier properties; High strength; Recyclable. | Lower chemical resistance compared to HDPE and PP; Can be more expensive than HDPE; Less impact resistant than HDPE. |
LDPE (Low-Density Polyethylene) | Flexible; Good chemical resistance; Relatively inexpensive. | Lower strength and durability than HDPE and PP; Not suitable for high-temperature applications; Less common for large barrels. |
Manufacturing Process
The creation of food-grade plastic barrels is a carefully orchestrated process, demanding precision and adherence to stringent quality control measures. This ensures the final product meets the high standards required for food safety and storage. The manufacturing journey involves several key stages, each contributing to the barrel’s integrity and suitability for its intended purpose.
Injection Molding Process
The most common method for producing food-grade plastic barrels is injection molding. This process involves melting plastic resin and injecting it into a mold to form the barrel’s shape. The choice of plastic resin, such as high-density polyethylene (HDPE), is crucial for food safety and durability.
- Material Preparation: Raw plastic resin, typically in pellet form, is thoroughly inspected to ensure it meets the required food-grade specifications. This includes verifying its chemical composition and ensuring it’s free from contaminants. The resin is then dried to remove any moisture that could affect the molding process.
- Melting and Injection: The dried plastic pellets are fed into an injection molding machine, where they are heated and melted into a molten state. This molten plastic is then injected under high pressure into a mold that is shaped like the barrel. The pressure ensures the plastic fills every detail of the mold, resulting in a uniform product.
- Cooling and Solidification: Once the mold is filled, the plastic is allowed to cool and solidify. Cooling times are carefully controlled to prevent warping or distortion of the barrel. The cooling process also affects the barrel’s mechanical properties, such as its strength and impact resistance.
- Ejection and Finishing: After the plastic has solidified, the mold opens, and the barrel is ejected. The barrel then undergoes finishing processes, which may include trimming any excess plastic (flash) and removing any imperfections. This ensures a smooth surface and consistent dimensions.
Blow Molding Process
Blow molding is another technique used, particularly for barrels with complex shapes or features. This method involves inflating a molten plastic tube inside a mold, forcing it to take the shape of the mold cavity.
- Parison Formation: A tube of molten plastic, called a parison, is extruded downwards. The parison’s dimensions are carefully controlled to determine the barrel’s wall thickness and overall size.
- Mold Closure: The mold, which is shaped like the barrel, closes around the parison, sealing the top and bottom.
- Inflation: Air is injected into the parison, causing it to expand and conform to the shape of the mold. The pressure is carefully controlled to ensure uniform wall thickness and prevent weak spots.
- Cooling and Ejection: The plastic is allowed to cool and solidify within the mold. Once cooled, the mold opens, and the finished barrel is ejected.
Quality Control Measures
Quality control is paramount throughout the manufacturing process to guarantee that the barrels meet the required food safety standards and performance criteria. These measures are implemented at every stage, from material selection to final inspection.
- Material Testing: Raw materials are subjected to rigorous testing to verify their purity, chemical composition, and compliance with food-grade regulations. This includes tests for migration of substances into food, as specified by organizations like the FDA and EFSA.
- Process Monitoring: Manufacturing parameters, such as temperature, pressure, and cooling times, are continuously monitored and controlled to ensure consistency and prevent defects. This includes using statistical process control (SPC) to identify and correct any deviations from the target values.
- Visual Inspection: Finished barrels undergo thorough visual inspections to detect any imperfections, such as cracks, dents, or contamination. Inspectors check for proper dimensions, consistent wall thickness, and the absence of any foreign materials.
- Leak Testing: Barrels are subjected to leak tests to ensure they are airtight and will not allow any leakage of contents. This can involve filling the barrels with water or air and checking for any loss of pressure.
- Performance Testing: Barrels are tested for their mechanical properties, such as impact resistance, tensile strength, and stacking strength. These tests ensure the barrels can withstand the stresses of handling, transportation, and storage.
Food Safety Regulations Compliance
Food-grade plastic barrels are designed to meet stringent food safety regulations, such as those set by the U.S. Food and Drug Administration (FDA) and the European Food Safety Authority (EFSA). These regulations ensure that the barrels do not contaminate the food they contain. The design and manufacturing process are geared towards meeting these standards.
- Material Selection: Only food-grade plastics, such as HDPE and polypropylene (PP), are used. These materials are chemically inert and do not react with food. The specific grade of plastic is selected based on its suitability for the intended food product.
- Barrier Properties: The barrels are designed to have good barrier properties, preventing the migration of substances from the barrel into the food and vice versa. This is crucial for preserving the food’s quality and safety.
- No Additives: The plastic used does not contain any additives that could leach into the food and pose a health risk. This includes the absence of phthalates and bisphenol A (BPA).
- Surface Finish: The barrels have a smooth, non-porous surface that is easy to clean and sanitize. This prevents the buildup of bacteria and other contaminants.
- Traceability: Manufacturers maintain detailed records of the materials used and the manufacturing process to ensure traceability. This allows for quick identification and resolution of any issues that may arise.
Regulatory Compliance and Standards
Food-grade plastic barrels are subject to rigorous regulatory scrutiny to ensure the safety of the food they contain. Compliance with these standards is crucial for manufacturers and distributors to avoid legal repercussions and maintain consumer trust. This section Artikels the key regulatory bodies, certification processes, and the consequences of non-compliance.
Key Regulatory Bodies and Standards
Several international and national bodies establish and enforce standards for food-grade plastic materials. These regulations are designed to prevent the migration of harmful substances from the plastic into the food, thus safeguarding public health.The primary regulatory bodies include:* United States Food and Drug Administration (FDA): The FDA sets standards for materials that come into contact with food in the United States. Specifically, the FDA’s regulations under 21 CFR (Code of Federal Regulations) Artikel requirements for food contact substances.
For example, 21 CFR 177.1520 covers polyolefins, a common plastic used in barrels. Compliance involves ensuring that the plastic materials used are approved for food contact and that the manufacturing processes meet FDA guidelines.* European Union (EU): The EU has comprehensive regulations, primarily through the European Food Safety Authority (EFSA), that govern food contact materials. Regulation (EC) No 1935/2004 is the overarching framework, setting out general requirements.
Specific regulations, such as those related to plastic materials (e.g., Regulation (EU) No 10/2011), detail the permitted substances, migration limits, and testing procedures.* Other International Standards: Other regions and countries often adopt or align with these major standards. For instance, in Canada, the Canadian Food Inspection Agency (CFIA) enforces regulations, often referencing FDA and EU standards. Similarly, in Australia and New Zealand, food contact materials are assessed based on similar principles, often incorporating elements from the FDA and EU guidelines.
Certification Processes and Markings
Achieving and maintaining compliance with food-grade standards involves rigorous certification processes and the use of specific markings on the barrels. These processes and markings provide assurance to consumers and regulatory bodies that the barrels meet the required safety criteria.The certification process typically involves:* Material Testing: Plastic materials are tested by accredited laboratories to ensure they meet migration limits and other safety requirements.
These tests determine if any chemicals from the plastic can leach into the food.* Manufacturing Process Audits: Manufacturers undergo audits to ensure that their production processes are compliant. This includes controlling the raw materials used, the manufacturing environment, and the quality control procedures.* Documentation and Traceability: Comprehensive documentation is maintained to trace the materials used, the manufacturing process, and the testing results.
This documentation is essential for demonstrating compliance and for product recalls if necessary.Certified food-grade barrels are often marked with specific symbols and information:* “Food Grade” Symbol: A symbol, often a glass and fork symbol, indicates that the barrel is suitable for food contact. This symbol is a visual cue for consumers and handlers.* Material Identification: The type of plastic material used (e.g., HDPE, PP) is usually indicated.* Manufacturer Information: The manufacturer’s name or identification mark is included for traceability.* Date Codes: Date codes are frequently used to indicate the date of manufacture, allowing for tracking and recall management.
Implications of Non-Compliance
Failure to comply with food-grade regulations can have serious consequences for manufacturers and distributors. These consequences range from financial penalties to damage to brand reputation and potential health risks.The implications of non-compliance include:* Product Recalls: Non-compliant barrels may lead to product recalls if contamination is detected. This is a costly process that can damage a company’s reputation and erode consumer trust.
Fines and Legal Penalties
Regulatory bodies can impose significant fines and other legal penalties for violations. The amount of the fine depends on the severity of the violation and the specific regulations in place.
Seizure of Products
Non-compliant barrels and the food products they contain can be seized by regulatory authorities, leading to financial losses.
Damage to Brand Reputation
Learn about more about the process of food processor blades in the field.
Non-compliance can severely damage a company’s reputation, leading to a loss of customers and market share. Negative publicity can be difficult to overcome.
Health Risks
The most serious consequence of non-compliance is the potential for health risks to consumers. Migration of harmful substances from the plastic into the food can cause illness and other health problems.
Loss of Business
In extreme cases, repeated or serious violations can lead to the closure of a manufacturing facility or the loss of the right to manufacture or distribute food-grade products.
Applications of Food Grade Barrels
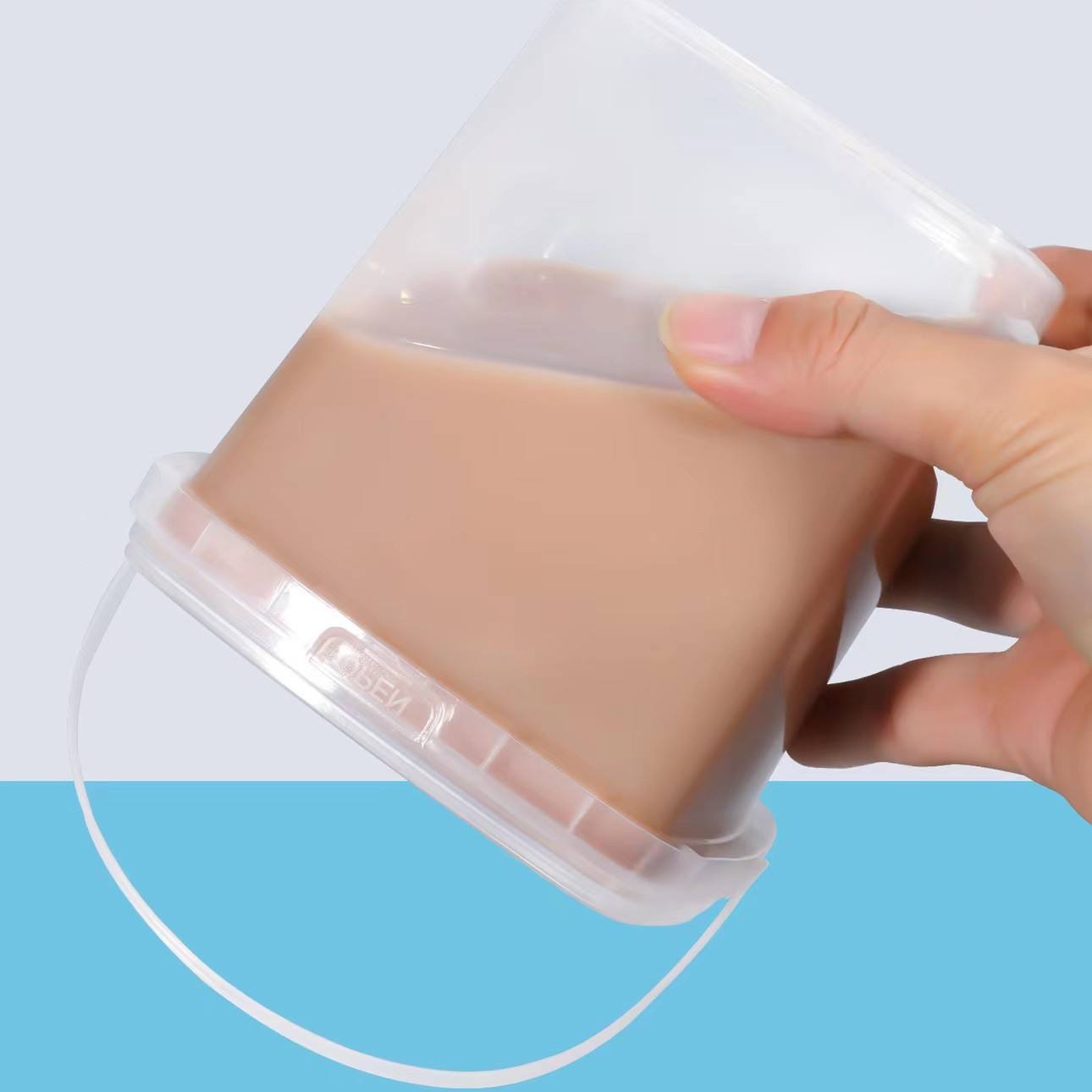
Food-grade plastic barrels are indispensable across a multitude of industries, providing a safe, efficient, and cost-effective solution for the storage, transportation, and handling of various food products. Their versatility, coupled with their compliance with stringent safety regulations, makes them a preferred choice for businesses of all sizes. The applications are diverse, spanning from the farm to the consumer, impacting the food supply chain in significant ways.
Industries Utilizing Food Grade Barrels
Numerous industries depend on food-grade plastic barrels to maintain product integrity and safety. These barrels are particularly valuable where hygiene and regulatory compliance are paramount.
- Food Processing: Food processing plants use barrels extensively for ingredients, intermediate products, and finished goods.
- Beverage Production: Breweries, wineries, and soft drink manufacturers utilize these barrels for fermentation, storage, and transportation of liquids.
- Dairy Industry: The dairy industry relies on barrels for milk, cream, yogurt, and other dairy products.
- Agriculture: Farms and agricultural businesses use barrels for storing and transporting ingredients such as animal feed and agricultural chemicals.
- Pharmaceuticals: The pharmaceutical industry often uses these barrels for ingredients that are sensitive to contamination.
- Food Service and Retail: Restaurants, caterers, and retailers employ barrels for bulk storage and distribution.
- Chemical Industry: While not directly food-related, certain chemicals used in food production and sanitation are stored in these barrels.
Specific Examples of Food Products Stored and Transported
Food-grade barrels are designed to handle a wide array of food products, offering protection from contamination and maintaining product quality.
- Liquids: Water, fruit juices, syrups, edible oils, and liquid flavorings are commonly stored and transported in these barrels.
- Dry Goods: Grains, flour, sugar, salt, spices, and various powdered ingredients are frequently stored in barrels.
- Semi-Liquids: Sauces, purees, jams, and condiments are also suitable for storage in these barrels.
- Fermented Products: Wine, beer, and other fermented products are frequently stored during the fermentation and aging process.
- Dairy Products: Milk, cream, yogurt, and other dairy products.
Case Studies: Practical Application and Benefits
Real-world examples demonstrate the effectiveness and advantages of using food-grade plastic barrels. These cases illustrate how these barrels contribute to efficiency, cost savings, and improved food safety.
Case Study 1: A Large-Scale Brewery
A large brewery switched from stainless steel tanks to food-grade plastic barrels for its fermentation process. The plastic barrels offered several advantages:
“The switch to plastic barrels reduced initial investment costs significantly, as plastic barrels are less expensive than stainless steel tanks. Furthermore, the lightweight nature of the barrels made them easier to handle and transport within the brewery, improving operational efficiency. The ease of cleaning and sanitizing also decreased downtime, allowing for more frequent production runs. The brewery reported a 15% increase in production capacity due to these improvements.”
Case Study 2: A Dairy Farm
A dairy farm adopted food-grade plastic barrels for storing and transporting raw milk. The barrels offered several benefits:
“The use of food-grade barrels ensured that the milk remained free from contamination, which is crucial for meeting stringent hygiene standards. The airtight seals on the barrels prevented spoilage and extended the shelf life of the milk. The durable plastic construction protected the milk from damage during transport, reducing waste and improving the farm’s profitability. The farm saw a 10% reduction in milk spoilage and waste, leading to increased revenue.”
Case Study 3: A Food Ingredient Supplier
A food ingredient supplier utilized food-grade barrels for the storage and distribution of various powdered ingredients, such as flour and sugar. This strategy proved beneficial:
“The airtight and moisture-resistant nature of the barrels protected the ingredients from spoilage and contamination. The standardized barrel sizes simplified inventory management and streamlined the supply chain. The robust construction of the barrels allowed for efficient stacking and storage, maximizing warehouse space. The supplier noted a 8% reduction in ingredient spoilage and improved inventory control.”
Cleaning and Maintenance
Maintaining the cleanliness and structural integrity of food-grade plastic barrels is paramount for food safety and preventing contamination. Regular cleaning and proper handling are essential to ensure the barrels meet the stringent requirements for food storage and transportation. This section details the recommended cleaning methods, storage practices, and potential hazards associated with neglecting these crucial aspects.
Recommended Cleaning and Sanitizing Methods
Proper cleaning and sanitizing of food-grade plastic barrels are essential to remove residues and prevent the growth of harmful microorganisms. The cleaning process typically involves several steps, each playing a critical role in maintaining hygiene.
Here’s a step-by-step guide to cleaning and sanitizing food-grade plastic barrels:
- Rinsing: Begin by thoroughly rinsing the barrel with potable water to remove any loose debris or residues. This initial rinse helps to loosen and remove larger particles, preparing the surface for the cleaning solution.
- Cleaning with Detergent: Use a food-grade detergent specifically designed for cleaning plastic surfaces. Follow the manufacturer’s instructions for dilution and application. Apply the detergent to all surfaces, ensuring complete coverage. Allow the detergent to sit for the recommended contact time to effectively break down any remaining contaminants.
- Scrubbing: Scrub the interior and exterior surfaces of the barrel using a soft-bristled brush or sponge. Pay particular attention to areas that may accumulate residues, such as seams, corners, and the inside of the lid. Thorough scrubbing ensures that all surfaces are cleaned effectively.
- Rinsing Again: Rinse the barrel thoroughly with potable water to remove all traces of the detergent. Ensure that no detergent residue remains, as it can affect the taste or quality of the food products stored in the barrel.
- Sanitizing: Apply a food-grade sanitizer solution to the barrel’s interior and exterior surfaces. Common sanitizing agents include chlorine-based solutions, quaternary ammonium compounds, and peracetic acid. Follow the manufacturer’s instructions for the correct concentration and contact time. Sanitizers are crucial for eliminating any remaining bacteria, viruses, and other microorganisms.
- Final Rinse: After the sanitizer has been in contact with the barrel for the recommended time, rinse it again with potable water to remove any sanitizer residue. This step ensures that the barrel is safe for food storage.
- Drying: Allow the barrel to air dry completely or use clean, food-grade towels to dry it. Proper drying prevents the growth of mold and mildew.
Example: Consider a brewery using food-grade plastic barrels for storing beer. After each batch, they follow these steps meticulously, using a chlorine-based sanitizer at a concentration of 200 ppm for a 10-minute contact time, followed by thorough rinsing. This rigorous cleaning protocol ensures that each batch of beer is free from contamination and maintains its desired flavor profile.
Importance of Proper Storage and Handling
Proper storage and handling of food-grade plastic barrels are crucial for preserving their integrity and preventing contamination. The way barrels are stored and handled can significantly impact their lifespan and effectiveness in maintaining food safety.
Here are key aspects of proper storage and handling:
- Storage Location: Store barrels in a clean, dry, and well-ventilated area. Avoid direct sunlight, extreme temperatures, and exposure to chemicals. Exposure to sunlight can degrade the plastic, making it brittle.
- Stacking: Follow the manufacturer’s recommendations for stacking barrels. Over-stacking can lead to deformation and damage, potentially compromising the barrel’s seal and structural integrity.
- Handling: Handle barrels with care to prevent damage. Avoid dragging them across rough surfaces, which can cause scratches and abrasions that harbor bacteria. Use appropriate lifting equipment when necessary.
- Inspection: Regularly inspect barrels for any signs of damage, such as cracks, leaks, or deformation. Damaged barrels should be removed from service immediately.
- Protection from Contamination: Keep barrels away from potential sources of contamination, such as pesticides, fertilizers, and other chemicals. These substances can leach into the plastic and contaminate the food products.
Example: A large food processing plant stores its food-grade plastic barrels indoors, away from direct sunlight and extreme temperatures. They implement a strict protocol for handling, including using forklifts to move the barrels and regular inspections to identify any damage. This careful approach extends the lifespan of the barrels and ensures food safety.
Potential Hazards Associated with Improper Cleaning and Maintenance
Failure to properly clean and maintain food-grade plastic barrels can lead to several significant hazards, posing risks to food safety, consumer health, and business operations. Understanding these risks is essential for implementing effective cleaning and maintenance protocols.
- Microbial Contamination: Improper cleaning can lead to the growth of bacteria, mold, and other microorganisms within the barrel. This can contaminate the food products stored in the barrel, leading to spoilage and potential foodborne illnesses.
- Chemical Contamination: Residues from previous contents or cleaning agents can contaminate food products. For example, using an inappropriate detergent or failing to rinse thoroughly can leave chemical residues.
- Cross-Contamination: Using the same barrel for different food products without proper cleaning can lead to cross-contamination, where allergens or flavors from one product transfer to another.
- Barrel Degradation: Neglecting proper cleaning and maintenance can accelerate the degradation of the plastic material. This can lead to cracks, leaks, and other forms of damage that compromise the barrel’s ability to contain food products safely.
- Regulatory Non-Compliance: Failure to meet food safety standards can result in regulatory penalties, including fines, product recalls, and damage to the business’s reputation.
Example: A company that stores fruit juice in food-grade plastic barrels fails to properly clean the barrels between batches. As a result, bacteria grow inside the barrels, leading to spoilage of the juice and a product recall. This incident not only causes financial losses but also damages the company’s reputation and erodes consumer trust.
Choosing the Right Barrel
Selecting the appropriate food-grade plastic barrel is crucial for ensuring the safety, integrity, and longevity of stored food products. This decision impacts everything from preventing contamination to optimizing storage space. A well-informed choice safeguards against potential risks and maximizes the efficiency of your operations.
Factors to Consider When Selecting a Food-Grade Plastic Barrel
Several key factors must be evaluated to determine the most suitable food-grade plastic barrel for a specific application. Understanding these elements will help users make informed decisions.
- The Intended Application: Determine the specific food product to be stored. This will influence the choice of material, size, and features. For example, storing liquids requires different considerations than storing dry goods.
- The Type of Food: Different foods have different characteristics that affect barrel selection. Consider the food’s acidity, alkalinity, fat content, and potential for chemical reactions. For instance, highly acidic foods may require barrels made from more chemically resistant plastics.
- Storage Environment: Evaluate the storage conditions, including temperature fluctuations, exposure to sunlight, and potential for physical impact. Barrels exposed to extreme temperatures or sunlight may require UV-resistant materials.
- Storage Duration: The length of time the food will be stored impacts the barrel’s durability and airtightness requirements. Longer storage periods may necessitate barrels with enhanced sealing capabilities.
- Transportation Needs: If the barrel will be transported, consider its dimensions, weight, and the availability of appropriate handling equipment. Barrels designed for transport often have features like reinforced rims or stacking capabilities.
- Regulatory Compliance: Ensure the barrel meets all relevant food safety regulations and standards, such as those set by the FDA or other governing bodies in the region of use. Look for certifications that confirm compliance.
- Budget: Establish a budget to guide the selection process. Barrel prices vary depending on size, material, and features. Balancing cost with the necessary performance characteristics is crucial.
Importance of Barrel Size, Shape, and Lid Type
The dimensions and design of a food-grade plastic barrel play a vital role in its functionality, storage efficiency, and ease of use. Selecting the correct size, shape, and lid type significantly impacts the overall effectiveness of the storage solution.
- Barrel Size: The capacity of the barrel must align with the volume of food to be stored. Consider the anticipated filling level, allowing for headspace to prevent spills and accommodate potential expansion or settling. A barrel that is too small will lead to overcrowding, while one that is too large may waste space and increase costs.
- Barrel Shape: The shape influences storage efficiency and handling. Cylindrical barrels are common and offer good stacking capabilities. Square or rectangular barrels may maximize space utilization in warehouses or storage areas.
- Lid Type: The lid design impacts the airtightness, ease of access, and security of the contents. Options include:
- Screw-on Lids: Offer a secure seal, ideal for liquids and products requiring a high degree of airtightness.
- Clamp-on Lids: Provide a tight seal and are often used for dry goods.
- Snap-on Lids: Offer quick access but may not provide the same level of airtightness as other options.
Decision-Making Process for Choosing the Right Barrel
A systematic decision-making process helps users choose the most appropriate food-grade plastic barrel for their specific needs. This structured approach minimizes the risk of errors and ensures a well-informed selection.
- Define Requirements:
- Identify the food product and its characteristics (e.g., liquid, solid, acidic, etc.).
- Determine the required storage volume.
- Assess the storage environment and potential hazards.
- Specify any transportation needs.
- Research and Evaluate Options:
- Identify potential barrel materials (e.g., HDPE, Polypropylene).
- Research available sizes, shapes, and lid types.
- Review product specifications and certifications.
- Compare prices and evaluate suppliers.
- Assess Regulatory Compliance:
- Verify that the barrel meets all relevant food safety regulations.
- Confirm the presence of necessary certifications (e.g., FDA).
- Consider Durability and Features:
- Evaluate the barrel’s resistance to chemicals, temperature fluctuations, and physical impacts.
- Assess the ease of cleaning and maintenance.
- Consider any additional features, such as handles, spouts, or stacking capabilities.
- Make a Final Selection:
- Choose the barrel that best meets the defined requirements, considering all factors.
- Place an order with a reputable supplier.
- Review the barrel upon arrival to ensure it meets the specifications.
Sustainability and Environmental Considerations: Food Grade Plastic Barrels
Food-grade plastic barrels, while essential for various industries, present environmental challenges that necessitate careful consideration. Understanding the impact of these barrels and adopting sustainable practices is crucial for minimizing their footprint and promoting responsible waste management. This section delves into the environmental implications, recycling and reuse strategies, and responsible disposal methods for food-grade plastic barrels.
Environmental Impact of Food-Grade Plastic Barrels
The widespread use of food-grade plastic barrels contributes to several environmental concerns. Primarily, the production of the plastics used in these barrels, often polyethylene (PE) or polypropylene (PP), relies on fossil fuels, contributing to greenhouse gas emissions and climate change. The disposal of these barrels, particularly in landfills, poses further issues. Plastic takes hundreds of years to decompose, leading to land and water pollution, as well as the potential for microplastics to enter the environment.
Furthermore, the transportation of barrels, both filled and empty, contributes to carbon emissions, increasing the overall environmental impact. The lifespan of a barrel and its ability to be reused, recycled or repurposed plays a crucial role in determining its environmental impact.
Recycling and Reusing Food-Grade Plastic Barrels, Food grade plastic barrels
Recycling and reusing food-grade plastic barrels are vital steps in mitigating their environmental impact. Effective recycling reduces the demand for virgin plastic production, conserving resources and lowering energy consumption. Reusing barrels, on the other hand, extends their lifespan and delays their entry into the waste stream. However, the success of these practices hinges on proper implementation and adherence to regulations.The recycling process typically involves the following steps:
- Collection: Barrels are collected from various sources, including businesses and waste management facilities.
- Cleaning: Thorough cleaning is essential to remove any remaining food residue or contaminants. This step is crucial to prevent cross-contamination during the recycling process.
- Sorting: Barrels are sorted based on the type of plastic (e.g., PE, PP) to ensure compatibility in the recycling process.
- Shredding: The barrels are shredded into smaller pieces to facilitate processing.
- Melting and Reprocessing: The shredded plastic is melted and reprocessed into pellets or new products.
Reusing barrels offers a direct way to reduce waste. Businesses can implement systems to track and manage their barrels, facilitating their return for reuse. Barrels can be used for a variety of purposes, such as storing non-food items, collecting rainwater, or creating planters.
Responsible Disposal and Repurposing of Food-Grade Plastic Barrels
When recycling or reuse is not feasible, responsible disposal or repurposing becomes crucial. The following guide provides practical advice:
- Check Local Regulations: Before disposing of or repurposing any barrel, consult local waste management guidelines. Regulations regarding plastic waste disposal vary by location.
- Cleaning is Key: Thoroughly clean the barrel to remove all food residue. This prevents contamination and makes repurposing safer.
- Repurposing Options: Consider repurposing the barrel for various uses:
- Water Storage: Use the barrel to collect rainwater for gardening or other non-potable uses.
- Composting: Create a compost bin by modifying the barrel.
- Storage: Utilize the barrel for storing non-food items in a garage, shed, or storage unit.
- Planters: Cut the barrel to create planters for flowers, vegetables, or herbs.
- Recycling Facilities: If repurposing is not an option, identify local recycling facilities that accept the specific type of plastic used in the barrel (usually PE or PP).
- Landfill as a Last Resort: As a final option, and if recycling or repurposing is impossible, dispose of the barrel at a designated landfill. Ensure it complies with local regulations.
Innovations in Barrel Design
The food-grade plastic barrel industry is constantly evolving, driven by the need for enhanced safety, efficiency, and sustainability. Recent innovations focus on improving durability, user-friendliness, and environmental impact, reflecting a commitment to meeting the ever-changing demands of the food and beverage sector. These advancements not only optimize performance but also contribute to a more sustainable and responsible approach to food storage and transportation.
Enhanced Durability and Material Science
Significant advancements have been made in materials and manufacturing processes to increase the lifespan and resilience of food-grade plastic barrels. These innovations aim to withstand the rigors of transportation, storage, and repeated use.The incorporation of reinforced materials is a key advancement. For instance, some barrels now utilize a blend of high-density polyethylene (HDPE) with additives like carbon fiber or specific polymers to enhance impact resistance.
This results in barrels that are less prone to cracking or deformation, even under extreme conditions. Consider the “Ultra-Durability Barrel,” designed with a triple-layer construction. The outer layer features a UV-resistant HDPE to protect against sunlight degradation, while the middle layer incorporates a blend of impact-resistant polymers. The inner layer uses food-grade virgin HDPE.
This multi-layered approach extends the barrel’s lifespan by up to 30% compared to standard single-layer designs, according to a study by the Plastic Packaging Association.
The design also includes reinforced ribbing on the exterior and a thicker base for improved load-bearing capacity. The barrel’s exterior could feature a series of vertical ribs that extend from the base to the top rim. These ribs would be spaced evenly around the barrel’s circumference, and they would be slightly thicker than the barrel’s main body. The base of the barrel would be noticeably thicker, with a circular pattern of reinforcing ribs on the underside.
Improved Accessibility and Ease of Use
Modern barrel designs prioritize user convenience, making handling, filling, and emptying processes more efficient and safer.
- Ergonomic Handles: Traditional handles are often replaced with more ergonomic designs. Integrated handles, molded directly into the barrel’s body, offer a more secure grip and reduce the risk of breakage. A good example is the “Easy-Grip Barrel,” which has recessed handles that are shaped to fit the natural curve of a hand. These handles are wider and have a textured surface to prevent slippage, even when wet.
The barrel’s design would also incorporate a slightly tapered shape to make it easier to lift and maneuver.
- Wide Openings: Larger bung openings or fully removable lids are becoming more common. This facilitates easier filling, cleaning, and access to the contents. The “Wide-Mouth Barrel” is designed with a lid that opens completely, allowing for easy scooping or pouring of ingredients. The lid is secured with a quick-release clamping mechanism, and a gasket ensures a tight seal.
- Integrated Measuring Systems: Some barrels incorporate graduated markings or sight gauges to help users accurately measure the contents. The “Precision-Fill Barrel” has a transparent side panel with volume markings in liters and gallons. This allows for easy monitoring of the fill level. The barrel also features a built-in valve for controlled dispensing.
Modular and Customizable Designs
Modular designs offer greater flexibility and adaptability to various needs.
- Stackable Barrels: Stackable barrels optimize storage space, especially in warehouses or transportation vehicles. The “Stack-Safe Barrel” is designed with interlocking features that allow barrels to be stacked securely without the need for additional securing mechanisms. The bottom of the barrel features a series of raised rings that fit into corresponding grooves on the lid of the barrel below.
- Customizable Options: Manufacturers are increasingly offering barrels with customizable features, such as color-coding, labeling, and the ability to integrate sensors for monitoring temperature or pressure. A “Smart Barrel” might be equipped with a Bluetooth-enabled sensor that transmits data on the contents’ temperature and fill level to a mobile app. The barrel’s exterior could be customized with the company’s logo and product information.
Sustainability and Recyclability
The focus on environmental responsibility is driving innovation in materials and manufacturing.
- Recycled Materials: An increasing number of barrels are made from recycled plastics, reducing the demand for virgin materials. The “Eco-Barrel” is constructed from post-consumer recycled HDPE. The barrel’s color may vary slightly due to the use of recycled materials.
- Biodegradable Plastics: Research and development are underway to incorporate biodegradable plastics into barrel designs, though this is still in its early stages for large-scale applications. The “Bio-Barrel” concept could utilize a blend of biodegradable polymers derived from renewable resources, such as cornstarch or sugarcane.
- Design for Disassembly: Some barrels are designed to be easily disassembled for recycling, with components that can be separated and processed individually. The “Modular Recycling Barrel” features a design where the lid, body, and base can be separated without tools. Each component is clearly marked with recycling symbols.
Cost Analysis and Market Trends
Understanding the cost dynamics and market trajectory of food-grade plastic barrels is crucial for businesses involved in food processing, storage, and transportation. This section delves into the average costs, factors influencing pricing, and future market predictions for these essential containers.
Average Cost of Food-Grade Plastic Barrels
The cost of food-grade plastic barrels varies considerably based on several factors, including size, material, and manufacturer. Generally, smaller barrels, such as those with a 15-gallon capacity, may cost between $20 and $50. Larger barrels, such as 55-gallon drums, can range from $50 to $150 or more. Prices also fluctuate based on the specific features, such as the presence of lids, spigots, or reinforced construction.
Bulk purchases often lead to lower per-unit costs.
Factors Influencing the Price of Food-Grade Plastic Barrels
Several factors significantly influence the final price of food-grade plastic barrels. These elements affect both the manufacturing costs and the overall market pricing.
- Material Costs: The type of plastic used, typically high-density polyethylene (HDPE) or polypropylene (PP), significantly impacts the cost. Fluctuations in the price of raw materials, such as petroleum, directly affect the production costs.
- Manufacturing Process: The complexity of the manufacturing process, including the use of specialized molds, injection molding techniques, and any post-processing steps, can increase costs.
- Barrel Size and Design: Larger barrels and those with complex designs, such as custom shapes or reinforced structures, are generally more expensive due to increased material usage and manufacturing complexity.
- Regulatory Compliance: Barrels that meet stringent food-grade standards and certifications, such as those from the FDA or other regulatory bodies, may have higher costs due to the need for specialized materials, testing, and quality control.
- Market Demand and Competition: The level of demand for food-grade barrels and the competitive landscape within the market can influence pricing. High demand or limited competition may lead to higher prices.
- Shipping and Transportation: The cost of shipping the barrels, especially over long distances, can add significantly to the final price, particularly for larger quantities.
Current Market Trends and Future Outlook for Food-Grade Plastic Barrels
The food-grade plastic barrel market is influenced by evolving consumer preferences, environmental concerns, and technological advancements. Understanding these trends provides insights into the future trajectory of the industry.
- Increasing Demand for Sustainable Packaging: Growing consumer awareness of environmental issues is driving demand for more sustainable packaging solutions. This includes a focus on barrels made from recycled materials or those that are easily recyclable themselves. The trend is supported by governmental regulations and initiatives promoting sustainable practices. For example, the European Union’s packaging waste directives are pushing manufacturers to adopt eco-friendly materials.
- Growth in E-commerce and Food Delivery: The expansion of e-commerce and food delivery services is increasing the need for durable and reliable packaging for food products. Food-grade plastic barrels are well-suited for these applications, ensuring the safe transportation and storage of food items. This trend is exemplified by the increased use of these barrels in the logistics of meal-kit delivery services.
- Technological Advancements in Barrel Design: Innovations in barrel design, such as improved sealing mechanisms, integrated monitoring systems, and enhanced durability, are enhancing their performance and appeal. These advancements cater to specific industry needs, like the storage of temperature-sensitive foods or the monitoring of product conditions during transport. An example is the development of barrels with built-in sensors that track temperature and humidity levels.
- Focus on Regulatory Compliance: Stricter food safety regulations and standards worldwide are increasing the importance of using certified food-grade barrels. Manufacturers must adhere to stringent guidelines, driving the need for barrels that meet these requirements. This is especially relevant in markets like North America and Europe, where food safety regulations are particularly robust.
- Market Expansion in Emerging Economies: The growing middle class and increasing urbanization in emerging economies are fueling demand for packaged foods and beverages. This trend is expected to drive the expansion of the food-grade plastic barrel market in regions such as Asia-Pacific and Latin America.
Wrap-Up
In conclusion, food grade plastic barrels are indispensable for the safe and efficient handling of food products. They represent a convergence of material innovation, manufacturing excellence, and regulatory oversight. Understanding the intricacies of these barrels—from material selection and manufacturing processes to cleaning protocols and sustainability initiatives—is paramount for ensuring food safety and environmental responsibility. As the food industry evolves, so too will the design and functionality of these essential containers, continuing to shape the future of food storage and transport.