Food tray lids, unassuming guardians of culinary creations, stand as silent sentinels between your meal and the outside world. Imagine a steaming lasagna, its cheesy surface glistening under the kitchen lights, awaiting its journey. Now picture it nestled securely within a food tray, sealed with a lid, a barrier of clear plastic or perhaps sturdy paperboard, protecting its warmth and flavor.
These lids, often overlooked, are essential components in the intricate dance of food preparation, preservation, and presentation. From the bustling kitchens of restaurants to the neatly arranged shelves of supermarkets, food tray lids play a crucial role.
Delving into the world of food tray lids unveils a fascinating array of designs, materials, and manufacturing processes. We’ll explore the hinged lids that swing open with a satisfying click, the snap-on varieties that create a tight seal, and the peel-off options offering easy access. We’ll examine the properties of plastics, paperboard, and aluminum foil, each with its unique strengths and environmental considerations.
Furthermore, the processes that shape these lids, from the precision of injection molding to the efficiency of thermoforming, will be uncovered, revealing the ingenuity behind their creation. From the simple function of containment to the complex interplay of design and sustainability, this exploration promises to be a revealing journey.
Food Tray Lid
Food tray lids are an essential component of food packaging, playing a critical role in preserving food quality, extending shelf life, and ensuring safe food handling. They are designed to seal food trays, protecting the contents from external contaminants and maintaining optimal conditions for storage and transportation.
Primary Function of a Food Tray Lid
The main purpose of a food tray lid is to provide a protective barrier for the food contained within the tray. This protection encompasses several key aspects, including preventing contamination from airborne particles, bacteria, and other potential hazards. The lid also helps to maintain the food’s temperature, moisture levels, and overall freshness. Furthermore, it contributes to the secure containment of the food, preventing spills and leaks during handling, storage, and transportation.
Different Materials Used for Food Tray Lids
Food tray lids are manufactured from a variety of materials, each offering unique properties and benefits. The selection of the material depends on factors such as the type of food being packaged, the required level of protection, and the desired environmental impact.
- Plastic: Plastic lids are widely used due to their versatility, cost-effectiveness, and ability to be molded into various shapes and sizes. Common plastic materials include:
- Polypropylene (PP): Known for its high melting point, making it suitable for hot-fill applications.
- Polyethylene Terephthalate (PET): Offers excellent clarity and barrier properties, often used for ready-to-eat meals.
- Polystyrene (PS): Provides good insulation and is often used for disposable containers.
- Aluminum Foil: Aluminum foil lids provide a superior barrier against oxygen, light, and moisture, making them ideal for preserving food quality and extending shelf life. They are commonly used for ready meals and dairy products.
- Paperboard: Paperboard lids offer a sustainable alternative to plastic. They can be coated with a food-grade barrier to provide moisture resistance and are often used for bakery items and other dry foods.
- PLA (Polylactic Acid): PLA is a biodegradable plastic derived from renewable resources like cornstarch. It is increasingly used for food tray lids as a more environmentally friendly option.
Benefits of Using Food Tray Lids
Food tray lids offer a range of advantages that contribute to food safety, quality, and efficiency in the food supply chain.
- Enhanced Food Safety: Lids create a physical barrier against contaminants, reducing the risk of foodborne illnesses. This is especially critical for perishable foods.
- Extended Shelf Life: By sealing the food tray, lids help to slow down spoilage and maintain the freshness of the food for a longer period. This is achieved by controlling the environment inside the tray, reducing oxygen exposure, and preventing moisture loss.
- Improved Food Quality: Lids help to retain the flavor, aroma, and texture of the food. They also protect the food from physical damage during handling and transportation.
- Convenience and Portability: Lids make food trays easy to handle, transport, and store. They are particularly important for takeout meals and ready-to-eat products.
- Reduced Food Waste: By extending shelf life and protecting food from spoilage, lids contribute to reducing food waste, which has significant environmental and economic benefits.
Industries Commonly Using Food Tray Lids
Food tray lids are utilized across a wide spectrum of industries involved in the production, distribution, and sale of food products.
- Restaurants and Food Service: For takeout and delivery meals, food tray lids are essential for keeping food warm, preventing spills, and ensuring safe transport.
- Supermarkets and Grocery Stores: Pre-packaged meals, deli items, and prepared foods are often sealed with lids to maintain freshness and display the product attractively.
- Food Manufacturers: Food manufacturers use lids to package a variety of products, including ready-to-eat meals, frozen foods, and dairy products, to protect them during the production, storage, and distribution processes.
- Catering Companies: Catering businesses rely on lids to transport and serve food at events, maintaining the quality and appearance of the meals.
- Healthcare Facilities: Hospitals and nursing homes use food tray lids to serve meals to patients, ensuring food safety and portion control.
- Airlines: Airlines utilize food tray lids to serve meals to passengers during flights, which must maintain food safety and minimize spills.
Types of Food Tray Lids
Food tray lids are essential for preserving food freshness, maintaining temperature, and ensuring hygiene during storage and transportation. Choosing the right lid type is crucial for optimizing food safety and presentation. The selection depends on factors like the type of food, desired shelf life, and operational needs.
Hinged Lids, Food tray lid
Hinged lids are attached to the food tray, offering convenience and ease of use. They typically swing open and closed, providing easy access to the food.
- Advantages:
- Convenient one-piece design, eliminating the need for separate lids.
- Often reusable, reducing waste.
- Provide a secure seal when closed.
- Disadvantages:
- Can be bulky, taking up more storage space.
- The hinge mechanism can be prone to breakage with repeated use.
- May not offer as tight a seal as other types.
Snap-on Lids
Snap-on lids are designed to securely attach to the food tray, creating a tight seal. They are a popular choice for various food applications.
- Advantages:
- Provide a secure and airtight seal, preventing leaks and spills.
- Easy to apply and remove.
- Available in various materials and designs.
- Disadvantages:
- Can be difficult to remove without the proper technique, especially with a tight seal.
- May require specific tray designs for optimal fit.
- Can be less convenient for frequent access compared to hinged lids.
Peel-off Lids
Peel-off lids are designed to be easily removed by peeling back a layer, typically a film or foil, from the food tray. They are commonly used for single-serve portions and ready-to-eat meals.
- Advantages:
- Provide a tamper-evident seal, ensuring food safety.
- Offer excellent barrier properties, extending shelf life.
- Easy to open and consume the food directly from the tray.
- Disadvantages:
- Generally not reusable.
- Can be more expensive than other lid types.
- May require specialized equipment for sealing.
Lid Type Comparison Table
The following table compares the different types of food tray lids, highlighting their materials, design features, pros, and cons.
Material | Design | Pros | Cons |
---|---|---|---|
Plastic (e.g., PP, PET) | Hinged | Convenient, reusable, secure seal. | Bulky, hinge prone to breakage, may not have the tightest seal. |
Plastic (e.g., PP, PET) | Snap-on | Secure, airtight seal, easy to apply. | Can be difficult to remove, requires specific tray designs. |
Film/Foil (e.g., PET, Aluminum) | Peel-off | Tamper-evident, excellent barrier properties, easy to open. | Not reusable, can be more expensive, requires specialized equipment. |
Paperboard/Cardboard | Snap-on/Hinged | Sustainable option, good for insulation | Can be less resistant to moisture, may require a coating. |
Materials Used for Food Tray Lids
The choice of material for food tray lids significantly impacts the functionality, safety, and environmental footprint of food packaging. Understanding the properties, manufacturing processes, and environmental implications of various materials is crucial for making informed decisions. This section explores the common materials used for food tray lids, providing insights into their characteristics and considerations.
Plastic
Plastic lids are widely used due to their versatility, cost-effectiveness, and ability to provide a barrier against moisture and oxygen. Various types of plastics are employed, each with distinct properties.
- Polypropylene (PP): Known for its high melting point, PP is often used for hot-fill applications and microwaveable lids. It offers good chemical resistance and is relatively lightweight.
- Polyethylene Terephthalate (PET): PET is a clear, strong plastic commonly used for cold food applications. It provides excellent clarity and barrier properties, making it suitable for showcasing food.
- Polystyrene (PS): PS is a more brittle plastic often used for disposable lids. It is generally less expensive than PP or PET but may not be suitable for high-temperature applications.
The environmental impact of plastic lids is a significant concern. Plastic production consumes fossil fuels and can contribute to greenhouse gas emissions. Many plastic lids are not readily recyclable, leading to landfill accumulation and potential environmental pollution. However, advancements in recycling technologies and the development of bioplastics are beginning to address these challenges.Food safety considerations for plastic lids include the potential for chemical migration from the plastic into the food.
The Food and Drug Administration (FDA) regulates the materials used in food contact applications to ensure they are safe for human consumption. Manufacturers must adhere to strict guidelines regarding the composition and use of plastics to prevent contamination.
Manufacturing Process of Plastic Lids:
- Injection Molding: This process involves injecting molten plastic into a mold, where it cools and solidifies to form the lid. Injection molding is suitable for mass production and complex designs.
- Thermoforming: In thermoforming, a plastic sheet is heated and then shaped over a mold using vacuum or pressure. This method is often used for producing lids with specific contours or shapes.
- Extrusion: Plastic is melted and forced through a die to create a continuous profile, which is then cut into lids. This process is typically used for producing simpler lid designs.
Paperboard
Paperboard lids offer a more sustainable alternative to plastic, particularly when sourced from responsibly managed forests. They are biodegradable and often recyclable.
- Properties: Paperboard lids are typically made from thick paper or cardboard. They offer good printability, allowing for branding and informational labeling. They can be coated with a barrier layer (e.g., polyethylene) to provide moisture resistance.
- Environmental Impact: Paperboard is a renewable resource, and its production can have a lower environmental impact compared to plastic. However, the manufacturing process requires energy and water, and the use of chemicals for pulping and bleaching can be of concern. The recyclability of paperboard lids depends on the presence of coatings and adhesives.
- Food Safety: Paperboard lids must be manufactured using food-grade materials. Coatings and adhesives used on the paperboard must be safe for food contact and should not leach into the food.
Manufacturing Process of Paperboard Lids:
- Pulping: Wood pulp is produced from wood fibers. The wood is mechanically or chemically processed to separate the fibers.
- Sheet Formation: The pulp is mixed with water and then spread onto a wire mesh, where the water drains away, and the fibers interlock to form a sheet.
- Coating and Finishing: The paperboard may be coated with a barrier layer (e.g., polyethylene) to provide moisture resistance. It is then cut and shaped into lids. Printing and branding can also be added at this stage.
Aluminum Foil
Aluminum foil lids provide an excellent barrier against moisture, oxygen, and light, making them ideal for preserving food quality and extending shelf life.
- Properties: Aluminum foil is lightweight, flexible, and can be molded into various shapes. It is a good conductor of heat and can be used for both hot and cold food applications.
- Environmental Impact: The production of aluminum requires significant energy, and the mining of bauxite ore can have environmental consequences. However, aluminum is infinitely recyclable, and the recycling process requires significantly less energy than producing new aluminum.
- Food Safety: Aluminum foil is generally considered safe for food contact. However, acidic foods can react with aluminum over time, potentially affecting the food’s taste and appearance. Food-grade aluminum foil is specifically designed to minimize this reaction.
Manufacturing Process of Aluminum Foil Lids:
- Casting: Molten aluminum is cast into large ingots.
- Hot Rolling: The ingots are heated and passed through rollers to reduce their thickness.
- Cold Rolling: The aluminum is further thinned through cold rolling, which involves multiple passes through rollers to achieve the desired foil thickness.
- Slitting and Finishing: The foil is slit into rolls of the desired width. It may be coated with a sealant or lacquer to improve its performance and appearance.
Manufacturing Processes
Food tray lids are produced using a variety of sophisticated manufacturing processes. These processes are carefully chosen based on the materials used, the desired lid design, and the required production volume. Understanding these methods is crucial for appreciating the quality, cost-effectiveness, and sustainability of the final product.
Injection Molding Process for Plastic Lids
Injection molding is a widely used manufacturing process for creating plastic food tray lids. This process offers high precision, rapid production rates, and the ability to create complex designs.The injection molding process involves several key steps:
- Material Preparation: Plastic pellets, often made from polypropylene (PP), polyethylene terephthalate (PET), or other food-grade polymers, are fed into a hopper. The material may be pre-colored or require colorants to be added.
- Melting and Injection: The plastic pellets are heated to their melting point inside a barrel. A reciprocating screw then forces the molten plastic into a closed mold under high pressure. The mold cavity is the negative of the desired lid shape.
- Cooling and Solidification: The molten plastic fills the mold cavity and cools, solidifying into the shape of the lid. Cooling time depends on the plastic type and lid thickness.
- Ejection: Once the plastic has solidified, the mold opens, and the finished lid is ejected. Ejection mechanisms, such as ejector pins, ensure the lid is released without damage.
- Trimming and Finishing: The ejected lid may undergo trimming to remove any excess material (e.g., sprue, runners) and finishing operations, such as adding features like vents or tabs.
Injection molding is particularly well-suited for high-volume production, making it an economical choice for disposable food tray lids. The process allows for intricate designs, including features like snap-on closures or stacking capabilities.
Die-Cutting Process for Paperboard Lids
Die-cutting is a process used to manufacture paperboard food tray lids. It’s a cost-effective method, especially for medium to high production runs, and it allows for intricate shapes and designs.The die-cutting process generally involves the following steps:
- Material Preparation: Paperboard sheets, typically made from coated paperboard or recycled materials, are fed into the die-cutting machine. The paperboard may be pre-printed with graphics or branding.
- Die Creation: A die, which is a custom-made tool containing sharp blades, is created to the exact shape of the lid. The die is mounted in the die-cutting machine.
- Cutting: The paperboard sheets are fed under the die. The sharp blades of the die cut through the paperboard, creating the lid shape. Creasing blades may be included to create fold lines for lid construction.
- Waste Removal: After cutting, the waste material (the areas not part of the lid) is removed. This can be done manually or automatically, depending on the complexity of the design and the production volume.
- Finishing: The cut lids may undergo additional finishing steps, such as scoring for folding, gluing, or applying a coating for moisture resistance.
The die-cutting process is versatile, allowing for various lid designs, including those with windows or intricate shapes. It’s also a sustainable option, as paperboard is a renewable and often recyclable material.
Thermoforming Plastic Lids
Thermoforming is a manufacturing process used to create plastic food tray lids by heating a plastic sheet and forming it over a mold. This method is often used for lids with relatively simple shapes and moderate production volumes.The thermoforming process generally involves the following steps:
- Material Preparation: A plastic sheet, often made from materials like PET, PP, or polystyrene (PS), is clamped into a frame. The plastic sheet is pre-cut to the appropriate size.
- Heating: The plastic sheet is heated to its softening point using radiant heaters. The heating process ensures the plastic becomes pliable and moldable.
- Forming: Once the plastic is soft, a mold (either male or female) is pressed into the heated plastic sheet. This forces the plastic to conform to the shape of the mold. Vacuum pressure can be applied to enhance the forming process.
- Cooling: The formed plastic is allowed to cool and solidify while it remains in contact with the mold. This ensures the lid retains its shape.
- Trimming: The formed lid is trimmed to remove any excess plastic, such as the flange or rim. This can be done using a trimming die or a CNC (Computer Numerical Control) cutting machine.
Thermoforming is a flexible process that can accommodate various lid designs, including those with rounded corners or shallow contours. It is a cost-effective solution for producing lids with moderate volumes and complex designs.
Food Tray Lid Features
Food tray lids are more than just covers; they are integral components that enhance the functionality, safety, and presentation of packaged food. Their design incorporates various features tailored to meet specific needs, from maintaining food quality to ensuring consumer safety. The following sections detail key features and their benefits.
Vents in Food Tray Lids
Vents play a crucial role in managing the environment within a food tray, especially for hot foods. They facilitate the release of steam and prevent condensation buildup, which can negatively impact food texture and appearance.Vents offer several advantages:
- Preventing Soggy Food: Steam buildup inside the container can lead to condensation, making foods like fried items or baked goods soggy. Vents allow steam to escape, preserving the intended texture.
- Maintaining Crispness: For foods that require a crispy exterior, vents help to prevent moisture from softening the crust.
- Reducing Pressure: Vents can release pressure that builds up from hot foods, preventing lid deformation or even the lid popping open during transport.
- Extending Shelf Life: By controlling moisture levels, vents can contribute to a longer shelf life for certain foods, especially those that are prone to spoilage due to excess humidity.
Anti-Fog Coatings for Clarity
Anti-fog coatings are applied to food tray lids to maintain clarity, ensuring that the food inside is visible to the consumer. This is particularly important for ready-to-eat meals and prepared foods sold in retail settings.These coatings work by:
- Reducing Surface Tension: Anti-fog coatings reduce the surface tension of the lid’s material, causing water droplets to spread out into a thin, transparent film rather than forming opaque fog.
- Enhancing Product Visibility: By preventing fogging, these coatings ensure that the food inside the tray is clearly visible, which is essential for product appeal and consumer confidence.
- Improving Presentation: A clear lid enhances the presentation of the food, making it more appealing to potential buyers.
- Increasing Sales: The ability to see the food can significantly increase sales, as consumers are more likely to purchase items they can visually assess.
Tamper-Evident Seals for Security
Tamper-evident seals are designed to provide assurance that the food tray has not been opened or compromised after it has been sealed by the manufacturer. These seals are crucial for food safety and consumer trust.Common types of tamper-evident seals include:
- Breakable Seals: These seals are designed to break or tear if the lid is opened, providing a clear indication of tampering.
- Shrink Bands: A band of heat-shrinkable material is placed around the lid and container, shrinking to create a secure seal. Any attempt to open the container will visibly damage or break the band.
- Security Labels: These labels can be affixed to the lid and container, and if the lid is opened, the label is damaged or leaves a residue, showing evidence of tampering.
- Sealed Packaging: The entire package is sealed in a way that any breach is immediately noticeable.
Tamper-evident seals are essential for maintaining food safety, preventing contamination, and building consumer trust in the brand.
Features for Aesthetic Appeal
The aesthetic appeal of a food tray lid is essential for attracting customers and conveying a sense of quality. Several features can be incorporated to enhance its visual impact.Features that improve the aesthetic appeal include:
- Clear Materials: Using transparent materials, such as PET or polypropylene, allows consumers to see the food inside, increasing its appeal.
- Attractive Shapes and Designs: Lids can be designed with unique shapes and contours to create a visually appealing presentation.
- Color and Printing: Custom colors, logos, and branding elements can be printed directly on the lid to enhance brand recognition and visual appeal.
- Embossing and Debossing: Adding raised or recessed designs can give the lid a premium look and feel.
- Surface Finishes: Different surface finishes, such as matte or glossy, can be used to create a specific aesthetic.
Features for Better Food Preservation
Food tray lids can incorporate features to enhance food preservation, extending shelf life and maintaining food quality. These features focus on controlling the environment within the package.Methods to incorporate features for better food preservation include:
- Modified Atmosphere Packaging (MAP): This technique involves flushing the package with a gas mixture (e.g., nitrogen, carbon dioxide) to replace oxygen, which slows down spoilage.
- Oxygen Barrier Films: Using materials with a low oxygen permeability helps to prevent oxidation, which can degrade food quality.
- Moisture Barriers: Lids can be designed to create a moisture barrier, preventing the loss of moisture from the food or the ingress of moisture from the environment.
- UV Protection: Certain lids are designed to block UV light, which can degrade food quality and cause discoloration.
- Temperature Control: Lids can be designed with insulating properties to help maintain the temperature of the food, especially for hot or cold items.
Applications and Industries
Food tray lids are indispensable across a wide array of industries, playing a critical role in food preservation, presentation, and transportation. Their versatility makes them a staple in sectors ranging from quick-service restaurants to large-scale food manufacturing. The specific applications and requirements vary depending on the industry and the type of food being handled.
Industries Utilizing Food Tray Lids
Food tray lids are utilized across numerous sectors within the food industry. These include, but are not limited to:* Restaurants: From fast-food establishments to fine dining restaurants, food tray lids are used for takeout, delivery, and food preparation.
Catering Services
Catering companies rely heavily on food tray lids to transport and serve food at events, ensuring food safety and maintaining presentation.
Supermarkets and Grocery Stores
Pre-packaged meals, deli items, and prepared foods are often packaged with food tray lids to extend shelf life and protect the food.
Food Manufacturers
Large-scale food production facilities use food tray lids for packaging and distributing products to retail outlets and other businesses.
Meal Kit Services
These services depend on food tray lids to package individual ingredients and meals, ensuring freshness and ease of preparation.
Institutional Food Service
Hospitals, schools, and correctional facilities utilize food tray lids for portion control, food safety, and efficient service.
Convenience Stores
Ready-to-eat meals and snacks in convenience stores frequently utilize food tray lids for packaging and presentation.
Specific Applications Within Each Industry
The applications of food tray lids vary widely depending on the specific needs of each industry.* Restaurants: Takeout containers for burgers and fries, pizza boxes with clear lids for visibility, and lids for salad containers.
Catering Services
Trays with lids for hot and cold buffets, disposable containers for individual meals, and lids to maintain food temperature during transport.
Supermarkets and Grocery Stores
Containers for deli meats and cheeses, pre-packaged salads and prepared meals, and lids for bakery items to maintain freshness.
Food Manufacturers
Sealing and packaging of frozen meals, ready-to-eat entrees, and portioned food items.
Meal Kit Services
Compartmentalized trays with lids to separate ingredients, ensure freshness, and facilitate easy meal preparation.
Institutional Food Service
Tray covers for patient meals in hospitals, portioned meal trays in schools, and secure containers in correctional facilities.
Convenience Stores
Containers for pre-made sandwiches, salads, and ready-to-eat snacks.
For descriptions on additional topics like paint for ceramics food safe, please visit the available paint for ceramics food safe.
Food Tray Lids in Meal Kits
Meal kits have revolutionized the way people prepare and consume food, and food tray lids are integral to their success. These lids serve several key functions in the meal kit industry:* Ingredient Separation: Compartmentalized trays, often with multiple sections, allow for the separation of ingredients, preventing cross-contamination and maintaining freshness.
Portion Control
Lids often help in portioning the food items, ensuring that the correct amount of each ingredient is included in the meal kit.
Freshness Preservation
Lids create a seal that helps to maintain the freshness of the ingredients by preventing air exposure and reducing the risk of spoilage.
Convenience
Lids make it easier to transport and store the meal kits, as they keep the ingredients secure and prevent spills.
Branding and Information
Lids often feature branding elements and information about the meal, including instructions and nutritional facts.
How Food Tray Lids Improve Food Presentation
Food presentation is crucial in the food industry, and food tray lids play a significant role in enhancing the visual appeal of meals. Here’s how:* Transparency: Clear lids allow customers to view the food inside, increasing visual appeal and encouraging purchase decisions.
Protection
Lids protect food from external elements such as dust and debris, maintaining its pristine appearance.
Stackability
Lids often enable trays to be stacked, allowing for efficient storage and display in restaurants, supermarkets, and catering events.
Compartmentalization
Lids with multiple compartments can separate different food items, preventing them from mixing and maintaining a visually organized presentation.
Customization
Lids can be customized with logos, colors, and designs to enhance branding and create a more appealing visual experience.
Regulations and Standards
Ensuring the safety and suitability of food tray lids is paramount for consumer health and product integrity. This section details the crucial regulations and standards governing their manufacture and use, highlighting the importance of compliance and recycling practices.
Applicable Regulations and Standards
A variety of regulations and standards govern the production and use of food tray lids, ensuring they are safe for contact with food. Compliance with these standards is mandatory for manufacturers and suppliers to legally market their products.
- Food and Drug Administration (FDA) Regulations (US): The FDA sets standards for materials used in food contact applications. Specifically, 21 CFR (Code of Federal Regulations) Part 177 Artikels regulations for polymers, including those used in the production of food tray lids. These regulations cover the types of materials permitted, the acceptable levels of additives, and the testing procedures required to ensure safety. For instance, a food tray lid made of polypropylene (PP) must comply with the specific requirements for PP as Artikeld in 21 CFR 177.1520.
- European Union (EU) Regulations: The EU’s primary regulation for food contact materials is Regulation (EC) No 1935/2004, which sets out general requirements for all food contact materials. Specific regulations, such as Regulation (EU) No 10/2011, detail the requirements for plastic materials and articles intended to come into contact with food. This includes migration limits for substances from the lid into the food. The EU also has regulations for specific materials, such as those for recycled plastics.
- Other International Standards: Various other countries and regions have their own regulations, often mirroring or aligning with FDA and EU standards. These may include national standards organizations that provide testing and certification services, such as the British Retail Consortium (BRC) in the UK or the Japanese Ministry of Health, Labour and Welfare (MHLW).
Food Safety Certifications
Food safety certifications provide assurance that food tray lids meet specific safety and quality standards. These certifications are often a requirement for businesses to operate within the food industry and demonstrate their commitment to consumer safety.
- FDA Compliance: While not a formal certification, FDA compliance is essential. Manufacturers must ensure their materials and manufacturing processes meet the FDA’s requirements. This involves rigorous testing and documentation to demonstrate that the lids are safe for food contact.
- EU Compliance and Declarations of Compliance (DoC): Similar to the FDA, manufacturers must comply with EU regulations and provide a Declaration of Compliance (DoC). This document certifies that the food tray lid meets the relevant EU requirements, including migration limits and the use of authorized substances.
- ISO 22000: ISO 22000 is an international standard that specifies the requirements for a food safety management system. Certification to ISO 22000 demonstrates a company’s ability to control food safety hazards and ensure the production of safe food contact materials.
- BRCGS Packaging Materials Certification: The BRCGS (Brand Reputation Compliance Global Standards) standard is a global standard for packaging and packaging materials. Certification to this standard demonstrates that a manufacturer has implemented a robust system for ensuring the safety, legality, and quality of their packaging materials.
- Other Certifications: Depending on the region and target market, other certifications might be necessary. These may include national food safety certifications or specific certifications required by major retailers or food service providers.
Importance of Compliance with Food Contact Regulations
Compliance with food contact regulations is critical for several reasons, all of which contribute to public health and business success.
- Protecting Public Health: The primary purpose of food contact regulations is to safeguard consumer health. These regulations limit the migration of harmful substances from the lid into the food, preventing potential health risks such as chemical contamination.
- Maintaining Food Quality and Safety: Compliance ensures that food tray lids do not compromise the quality or safety of the food they contain. This includes preventing the transfer of odors, flavors, or other substances that could alter the food’s taste or cause spoilage.
- Legal Requirements and Avoiding Penalties: Adhering to regulations is a legal requirement. Failure to comply can result in significant penalties, including product recalls, fines, and legal action. This can damage a company’s reputation and lead to substantial financial losses.
- Building Consumer Trust: Consumers are increasingly concerned about food safety. Compliance with regulations and obtaining certifications demonstrates a commitment to providing safe and high-quality products, building consumer trust and loyalty.
- Facilitating Market Access: Compliance is often a prerequisite for selling food tray lids in certain markets. Meeting the required standards allows manufacturers to access broader markets and expand their business opportunities.
Recycling Guidelines for Different Lid Materials
Recycling food tray lids is essential for environmental sustainability. Recycling guidelines vary depending on the material of the lid, and proper disposal is crucial for effective recycling.
- Polypropylene (PP): PP is one of the most commonly used plastics for food tray lids due to its heat resistance and flexibility. PP lids are generally recyclable, and the “5” symbol (a triangle with the number 5 inside) is often used to indicate this. However, recycling infrastructure varies by location. Consumers should check local guidelines to ensure proper disposal.
- Polyethylene Terephthalate (PET or PETE): PET is another common plastic used for food tray lids, particularly for clear, rigid lids. PET is widely recyclable, indicated by the “1” symbol. PET recycling is well-established in many regions, and PET lids should be disposed of in designated recycling bins.
- Polystyrene (PS): PS, including both expanded polystyrene (EPS or Styrofoam) and rigid PS, is sometimes used for food tray lids. However, PS recycling can be more complex. While PS is technically recyclable, recycling facilities may not always accept it due to the difficulty and cost of processing. Consumers should consult local recycling guidelines to determine if PS lids are accepted.
- Other Materials: Other materials, such as paperboard or biodegradable plastics, may be used for food tray lids. Recycling guidelines for these materials vary. Paperboard lids should typically be recycled with paper products, while biodegradable lids should be composted if local facilities support this.
- General Recycling Advice:
- Clean the Lids: Always rinse food tray lids to remove food residue before recycling.
- Check Local Guidelines: Recycling guidelines vary by location. Consult local authorities for specific instructions.
- Remove Labels: Remove any labels or adhesives that could contaminate the recycling stream.
- Separate Materials: Separate lids from other packaging materials to ensure proper processing.
Design and Aesthetics
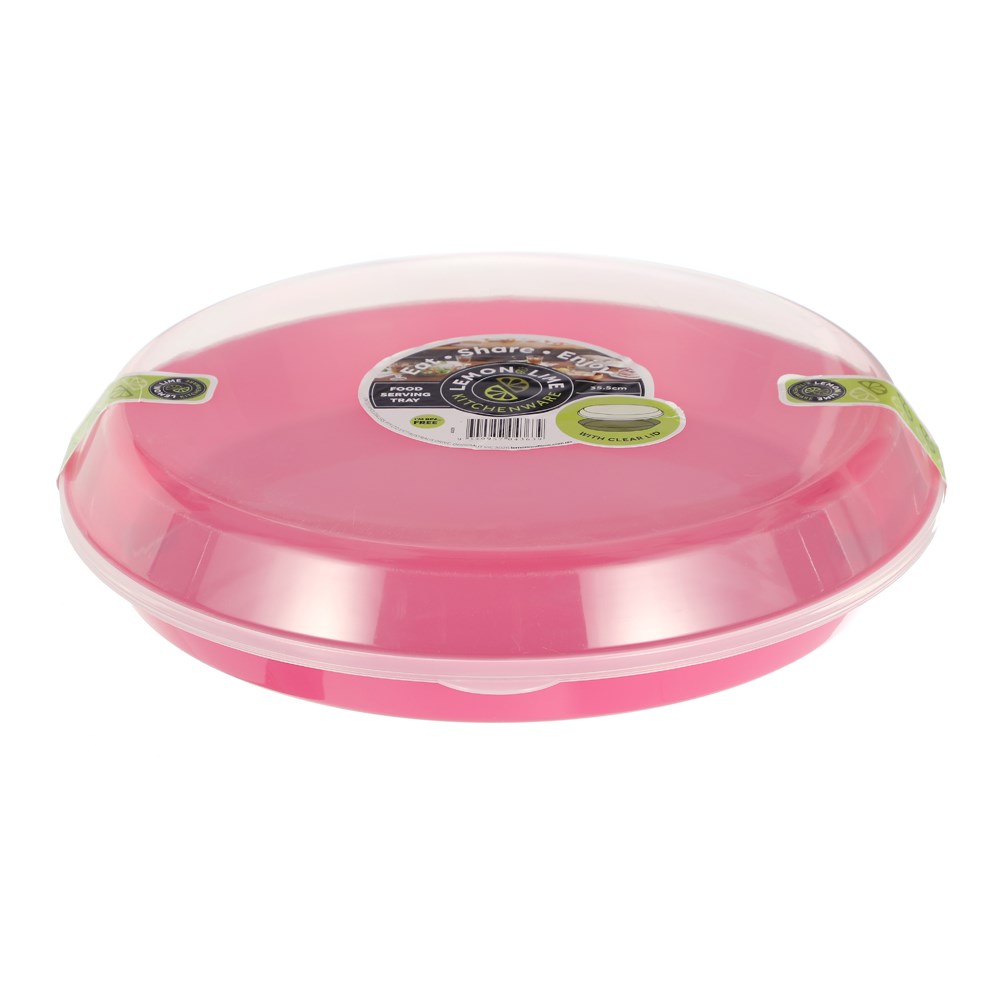
The visual presentation of food tray lids significantly impacts consumer perception and brand recognition. A well-designed lid not only protects the food but also enhances its appeal, influencing purchasing decisions and reinforcing brand identity. Strategic design considerations are crucial for creating lids that are both functional and visually engaging.
Designing Food Tray Lids for Visual Appeal
Creating visually appealing food tray lids involves a multifaceted approach, encompassing color, texture, shape, and branding elements. These elements work in concert to communicate the quality, freshness, and value of the food product. The goal is to attract the consumer’s attention and create a positive association with the brand.Color palettes should align with the product and brand identity. For example, fresh produce might utilize vibrant greens and reds, while a premium dessert could employ elegant blacks and golds.
Textures can range from smooth and glossy to matte or textured, depending on the desired aesthetic. The shape of the lid, whether rectangular, circular, or custom-designed, should complement the food tray and enhance its visual impact.
Branding and Labeling on Food Tray Lids
Branding and labeling are critical components of food tray lid design, serving to communicate essential information and reinforce brand identity. Effective branding integrates the logo, brand colors, and messaging to create a cohesive and recognizable brand presence. Clear and concise labeling is equally important, providing consumers with crucial details about the product.Effective branding strategies include:
- Logo Placement: Strategically positioning the logo in a prominent location ensures brand visibility.
- Color Consistency: Maintaining consistent brand colors throughout the lid design reinforces brand recognition.
- Messaging: Incorporating concise and impactful messaging, such as “Freshly Made” or “Premium Quality,” enhances consumer appeal.
- Labeling Requirements: Compliance with food labeling regulations is essential.
- Ingredient Lists: Providing a clear and legible ingredient list ensures transparency and consumer trust.
- Nutritional Information: Including nutritional information allows consumers to make informed choices.
- Barcode Placement: Strategically placing the barcode facilitates efficient scanning at the point of sale.
Considerations for Lid Shape and Size
The shape and size of a food tray lid are critical factors influencing both functionality and aesthetics. The lid must securely fit the tray, providing a proper seal to maintain food freshness and prevent leaks. The dimensions of the lid should also consider the overall presentation of the food and the space available for branding and labeling.Key considerations for lid shape and size:
- Tray Compatibility: The lid must precisely match the shape and dimensions of the food tray.
- Food Volume: The lid’s height should accommodate the volume of food contained within the tray.
- Sealing Mechanisms: The lid design should incorporate effective sealing mechanisms, such as snap-on closures or heat seals, to ensure food safety.
- Stackability: Lids should be designed to be stackable for efficient storage and display.
- Material Selection: The material of the lid affects its rigidity, flexibility, and ability to maintain its shape.
- Transportation Requirements: The lid must withstand handling and transportation.
Illustrative Design: Gourmet Salad Lid
Consider a food tray lid designed for a gourmet salad. The lid is rectangular, made from clear, recyclable PET plastic, offering a clear view of the vibrant salad within. The shape is slightly domed to accommodate the salad’s ingredients, preventing crushing.The color palette uses a combination of crisp white and a deep forest green. The white serves as the primary background for the brand logo and product information, ensuring legibility and a clean aesthetic.
The deep forest green is used for a subtle border along the edge of the lid and as the background color for the brand name, creating a premium feel and subtly referencing the fresh, natural ingredients of the salad. The lid’s surface has a subtle, matte finish to reduce glare and provide a tactile experience.The brand logo is prominently displayed in the center of the lid, using a modern sans-serif font in a dark green color.
Product information, including the salad name and key ingredients, is printed below the logo in the same font, but in a smaller size. A small, circular sticker indicating “Gluten-Free” is placed in the corner of the lid. The overall design communicates freshness, quality, and health-consciousness, appealing to the target consumer. The lid also incorporates a series of small, recessed areas to provide ventilation, maintaining the salad’s freshness.
Sustainability and Eco-Friendliness
The food packaging industry is under increasing pressure to reduce its environmental footprint. Food tray lids, a crucial component of food packaging, significantly contribute to this footprint. Consumers and regulatory bodies alike are demanding more sustainable and eco-friendly solutions. Understanding the environmental impact, exploring sustainable material options, and implementing waste reduction strategies are essential for creating a more responsible and circular economy for food packaging.
Environmental Impact of Food Tray Lids
The environmental impact of food tray lids stems primarily from the materials used, the manufacturing processes, and their end-of-life management. Traditional plastic lids, often made from petroleum-based polymers, contribute to several environmental concerns.
- Resource Depletion: The extraction of fossil fuels for plastic production depletes natural resources and contributes to habitat destruction.
- Greenhouse Gas Emissions: The manufacturing and transportation of plastic lids release greenhouse gases, contributing to climate change.
- Waste Generation: Plastic lids often end up in landfills or, worse, as litter in the environment, where they can persist for hundreds of years, polluting ecosystems and harming wildlife.
- Microplastic Pollution: The breakdown of plastic lids into microplastics further contaminates the environment, posing risks to human and animal health.
Sustainable Lid Materials
Several sustainable materials are available for food tray lids, offering alternatives to traditional plastics. These materials are designed to minimize environmental impact through various means, including using renewable resources, reducing waste, and improving recyclability or compostability.
- Plant-Based Plastics (Bioplastics): These plastics are derived from renewable resources such as corn starch, sugarcane, or cellulose. They can be compostable or recyclable, depending on the specific type. Examples include PLA (polylactic acid) and PHA (polyhydroxyalkanoates).
- Recycled Plastics: Utilizing recycled plastics, such as rPET (recycled polyethylene terephthalate), reduces the demand for virgin plastics and helps to close the loop on plastic waste.
- Paperboard: Paperboard lids are made from sustainably sourced paper and are often recyclable and compostable. They can be coated with plant-based coatings for improved barrier properties.
- Molded Pulp: Molded pulp lids are made from recycled paper fibers and are compostable. They offer good cushioning and are suitable for various food products.
- Aluminum: Aluminum is a highly recyclable material that can be recycled repeatedly without losing its properties. Aluminum lids offer excellent barrier properties and are often used for food packaging.
Strategies for Reducing Waste from Food Tray Lids
Reducing waste from food tray lids requires a multi-faceted approach that includes material selection, design considerations, and end-of-life management strategies.
- Design for Recyclability: Lids should be designed to be easily recyclable, using materials and designs that are compatible with existing recycling infrastructure.
- Reduce Material Usage: Minimizing the amount of material used in lid production can reduce waste. Lightweight designs and optimized material distribution are key.
- Promote Compostability: Utilizing compostable materials allows for the decomposition of lids in composting facilities, reducing landfill waste.
- Implement Extended Producer Responsibility (EPR) Programs: EPR programs hold manufacturers responsible for the end-of-life management of their products, encouraging the development of more sustainable packaging solutions.
- Consumer Education: Educating consumers about proper disposal methods, such as recycling and composting, is crucial for ensuring that lids are managed appropriately.
Eco-Friendly Lid Options
This table provides a comparison of different eco-friendly lid options, highlighting their material composition, recyclability, and environmental impact.
Material | Material Composition | Recyclability | Environmental Impact |
---|---|---|---|
PLA (Polylactic Acid) | Derived from renewable resources like corn starch | Compostable in industrial composting facilities; may not be accepted in all municipal recycling programs. | Lower carbon footprint than traditional plastics; requires proper composting infrastructure. |
rPET (Recycled Polyethylene Terephthalate) | Made from recycled PET bottles and containers | Widely recyclable in many municipal recycling programs. | Reduces the demand for virgin plastic; lowers energy consumption compared to virgin plastic production. |
Paperboard | Made from sustainably sourced paper, often with plant-based coatings | Generally recyclable; compostable depending on the coating. | Renewable resource; reduces reliance on fossil fuels; can be composted. |
Molded Pulp | Made from recycled paper fibers | Compostable. | Utilizes recycled materials; reduces landfill waste; biodegradable. |
Aluminum | Aluminum | Highly recyclable; can be recycled repeatedly. | Mining can have environmental impacts; reduces reliance on virgin materials; can be recycled indefinitely. |
Cost Considerations: Food Tray Lid
Understanding the cost implications of food tray lids is crucial for businesses aiming to optimize their packaging budget while maintaining product quality and safety. Several factors influence the final price, and making informed decisions requires a careful assessment of material choices, design complexities, and manufacturing processes. This section delves into the various cost aspects associated with food tray lids, providing insights to help businesses make economically sound choices.
Factors Influencing the Cost of Food Tray Lids
The cost of food tray lids is determined by a multitude of factors, impacting both the initial purchase price and the long-term operational expenses. These factors range from the raw materials used to the complexity of the manufacturing process.
- Material Costs: The type of material is a primary cost driver. Materials like PET and PP are generally less expensive than specialized barrier films or bio-based alternatives. Fluctuations in the price of raw materials, such as oil for plastics, also directly affect the cost.
- Manufacturing Process: The method of production, such as thermoforming, injection molding, or die-cutting, influences the cost. Complex designs and intricate features necessitate more sophisticated and potentially more expensive manufacturing techniques.
- Design Complexity: Lids with custom shapes, unique closures, or integrated features (e.g., vents, tamper-evident seals) add to the production cost due to increased tooling and manufacturing time.
- Volume of Production: Larger order quantities typically result in lower per-unit costs due to economies of scale. Manufacturers can spread fixed costs, such as tooling setup, over a greater number of units.
- Material Thickness: Thicker lids provide greater protection but require more material, thereby increasing costs. Finding the right balance between protection and cost is essential.
- Transportation and Storage: Shipping costs depend on the weight and volume of the lids, as well as the distance they need to travel. Efficient storage solutions can help minimize warehousing costs.
- Regulations and Standards: Compliance with food safety regulations and environmental standards can impact costs. For example, using food-grade materials or implementing specific recycling programs may add to the overall expense.
Pricing of Different Lid Materials
The price of food tray lids varies significantly based on the materials used. Choosing the right material involves balancing cost considerations with performance requirements.
- Polypropylene (PP): PP is a widely used and cost-effective option, known for its versatility and suitability for various food applications. Its cost is typically lower compared to materials with specialized properties. For example, the average cost of a PP lid might range from $0.02 to $0.05 per unit, depending on size, thickness, and design complexity.
- Polyethylene Terephthalate (PET): PET offers excellent clarity and barrier properties, making it suitable for displaying food items. While generally more expensive than PP, PET lids remain a popular choice. The price can vary from $0.03 to $0.07 per unit.
- Polystyrene (PS): PS is used for its rigidity and cost-effectiveness. However, environmental concerns and regulatory restrictions are driving its decline in popularity. The price is comparable to PP.
- Barrier Films: Lids made from specialized barrier films, designed to extend shelf life and protect food from oxygen and moisture, are more expensive. The price can range from $0.08 to $0.20 per unit or more, depending on the film’s complexity.
- Bio-Based Materials: Lids made from compostable or biodegradable materials like PLA (polylactic acid) are typically more expensive than traditional plastics. The premium for these eco-friendly options can range from 20% to 50% or higher, depending on the material and production scale. For instance, a PLA lid might cost $0.06 to $0.10 per unit.
Cost-Effectiveness of Various Lid Designs
The design of a food tray lid significantly impacts its cost-effectiveness, affecting material usage, manufacturing processes, and overall performance.
- Simple, Flat Lids: These designs are the most cost-effective due to their straightforward manufacturing process and minimal material usage. They are ideal for applications where aesthetics are not a primary concern.
- Snap-on Lids: Snap-on lids are generally more cost-effective than more complex closure mechanisms, providing a secure seal without requiring elaborate tooling.
- Hinged Lids: Hinged lids offer convenience but may increase costs due to the added complexity of the hinge mechanism and manufacturing.
- Lids with Vents: Adding vents can improve the performance of the lid, but this can add to the cost due to the extra manufacturing step.
- Tamper-Evident Lids: Tamper-evident features add to the cost but provide an important layer of security.
- Custom Designs: While custom designs can be more expensive, they can improve brand recognition and differentiate products.
Reducing the Overall Cost of Using Food Tray Lids
Several strategies can be employed to reduce the overall cost of using food tray lids, from optimizing material selection to streamlining procurement processes.
- Material Optimization: Evaluate whether a less expensive material can meet the performance requirements. For example, using a thinner lid or switching to a different polymer could reduce costs without compromising functionality.
- Design Simplification: Simplify the lid design to reduce manufacturing complexity. Removing unnecessary features or standardizing shapes can lower production costs.
- Bulk Ordering: Purchasing lids in larger quantities often results in lower per-unit costs due to economies of scale.
- Supplier Negotiation: Regularly compare prices from different suppliers and negotiate for better rates.
- Supply Chain Efficiency: Optimize the supply chain to reduce transportation and storage costs. This includes consolidating shipments and using efficient warehousing solutions.
- Automation: Automating the lid application process can reduce labor costs and improve efficiency.
- Waste Reduction: Minimize waste during manufacturing and usage. Implementing recycling programs and using recyclable materials can also reduce waste disposal costs.
- Life Cycle Assessment: Evaluate the environmental impact of different lid options, considering both production and disposal costs.
Final Conclusion
In conclusion, the food tray lid, far from being a mere afterthought, emerges as a vital player in the food industry. From preserving freshness and ensuring food safety to enhancing visual appeal and promoting sustainability, the lid’s influence is profound. As we navigate the evolving landscape of food packaging, with increasing emphasis on eco-friendliness and consumer convenience, the design, materials, and functionality of food tray lids will continue to evolve.
The journey from the factory floor to the dining table highlights the lid’s crucial role, leaving a lasting impact on the way we experience and enjoy our meals. Therefore, consider the lid not just as a cover, but as an integral part of the complete culinary experience.