Interbake Foods Jobs offer a gateway into the dynamic world of food manufacturing, presenting a range of opportunities for individuals seeking a fulfilling career. This exploration delves into the core of Interbake Foods, a company with a rich history and a significant presence in the industry. From its founding to its current operations, we’ll uncover the essence of Interbake Foods, examining its product lines, geographical reach, and the vital role it plays in the food supply chain.
Beyond the company’s profile, the focus will shift to the job prospects available. We’ll analyze current openings, the required qualifications, and the application process. Moreover, this examination will cover the workplace culture, employee benefits, and specific job roles, providing a comprehensive view of what it means to work at Interbake Foods. Prepare to learn about the skills needed for success, career advancement pathways, and salary expectations, alongside insights into the interview process and employee testimonials.
Overview of Interbake Foods and its Operations: Interbake Foods Jobs
Interbake Foods, a name synonymous with baked goods, has woven its way into the fabric of American snacking habits. From its humble beginnings to its current stature, the company’s journey is a testament to its enduring commitment to quality and innovation. This exploration delves into the key aspects of Interbake Foods, offering a glimpse into its history, product offerings, and operational footprint.
Founding and Key Milestones
Interbake Foods’ story begins in the realm of baked treats. It has roots in the broader food industry, eventually establishing itself as a prominent player.
- The company’s evolution is marked by strategic acquisitions and expansions. This allowed Interbake Foods to grow its market presence and product portfolio.
- Key milestones include facility expansions, product innovations, and partnerships that have solidified its position in the market. These decisions reflected a focus on efficiency and catering to evolving consumer tastes.
- Over the years, Interbake Foods has adapted to market changes, demonstrating resilience and a commitment to long-term sustainability.
Primary Products Manufactured and Distributed
Interbake Foods is known for a diverse range of baked goods that cater to a wide array of consumer preferences. The product line showcases a balance of classic favorites and innovative offerings.
- The company is particularly recognized for its cookies. These range from traditional recipes to more contemporary flavor profiles.
- Interbake Foods also produces a variety of other baked goods. This includes items like crackers, biscuits, and other snackable treats.
- Distribution channels encompass retail stores, supermarkets, and other outlets. These diverse distribution networks ensure that products are accessible to consumers across different regions.
Geographical Reach of Interbake Foods’ Operations
Interbake Foods’ operational footprint spans across multiple regions, reflecting its broad market reach. The company has established a presence in key locations to facilitate efficient production and distribution.
- Manufacturing facilities are strategically located to optimize logistics and serve different markets.
- Distribution networks extend throughout the United States.
- Interbake Foods also may have a presence in international markets, contributing to its global reach.
Workplace Culture and Employee Benefits
Interbake Foods, much like a well-seasoned recipe, understands that the quality of its final product – its delicious cookies and crackers – is inextricably linked to the environment in which its employees work. The company fosters a culture built on respect, collaboration, and a commitment to excellence. This dedication extends beyond just the production line, permeating all aspects of the employee experience.
Work Environment at Interbake Foods: Values and Principles
The work environment at Interbake Foods is structured around core values that guide daily operations. These values are not just platitudes; they are actively promoted and practiced throughout the organization. They are the ingredients of a successful and satisfying workplace.
Do not overlook the opportunity to discover more about the subject of food pantry green cove springs.
- Integrity: Acting with honesty and transparency in all interactions. This means doing what is right, even when no one is watching, ensuring trust among colleagues and stakeholders.
- Quality: A relentless pursuit of excellence in every product and process. It is a commitment to delivering the best possible baked goods, from the ingredients selected to the final packaging.
- Teamwork: Encouraging collaboration and mutual support among employees. This fosters a sense of community where everyone contributes to a shared goal.
- Innovation: Continuously seeking new and improved methods to enhance efficiency and product offerings. This involves embracing new technologies and ideas to stay ahead in a competitive market.
- Respect: Treating all individuals with dignity and valuing diverse perspectives. This includes fostering an inclusive environment where everyone feels welcomed and appreciated.
The principles guiding the work environment emphasize open communication, employee empowerment, and a commitment to safety. Employees are encouraged to voice their opinions and contribute to process improvements. Safety is paramount, with rigorous training and procedures in place to protect the well-being of all workers.
Employee Benefits Package
Interbake Foods recognizes that attracting and retaining talented employees requires a comprehensive benefits package. This package goes beyond just a paycheck, providing employees with security, support, and opportunities for growth. It is the dough that holds the company together.
- Health Insurance: Comprehensive medical, dental, and vision insurance plans are offered to employees and their families. These plans typically include coverage for doctor visits, hospital stays, prescription medications, and preventative care.
- Retirement Plans: Interbake Foods provides retirement savings options, such as a 401(k) plan, to help employees plan for their financial future. This may include employer matching contributions, encouraging employees to save for retirement.
- Paid Time Off: Employees receive paid time off, including vacation days, sick leave, and holidays. This allows employees to take time away from work to rest, recharge, and attend to personal matters.
- Life Insurance and Disability Coverage: Provides financial protection for employees and their families in the event of unexpected life events.
- Employee Assistance Program (EAP): Access to confidential counseling and support services for employees and their families to address personal and work-related challenges.
- Opportunities for Professional Development: The company invests in employee growth through training programs, workshops, and tuition reimbursement, enabling employees to enhance their skills and advance their careers.
Comparison of Benefits with Similar Companies
Comparing Interbake Foods’ benefits with those of its competitors in the food manufacturing industry reveals a competitive offering. While specific details may vary, the general trends in the industry provide a useful benchmark.
A survey of food manufacturing companies reveals that the benefits offered often include:
- Health Insurance: Most companies provide health insurance, but the specific plans and coverage levels can vary. Interbake Foods’ commitment to comprehensive coverage is a strong point.
- Retirement Plans: 401(k) plans with employer matching are standard. The level of the match and the vesting schedule are key differentiators. Interbake Foods’ offering is competitive.
- Paid Time Off: The amount of paid time off offered is generally in line with industry standards. The flexibility and policies surrounding time off are important.
- Additional Benefits: Some companies offer additional benefits such as wellness programs, employee discounts, and stock options. These benefits can enhance the overall employee experience.
In the competitive landscape of the food manufacturing industry, Interbake Foods’ benefits package appears to be competitive, offering a strong foundation of health insurance, retirement plans, and paid time off. The details of the specific plans and the company culture also contribute to the overall attractiveness of the employment offer.
Specific Job Roles and Responsibilities
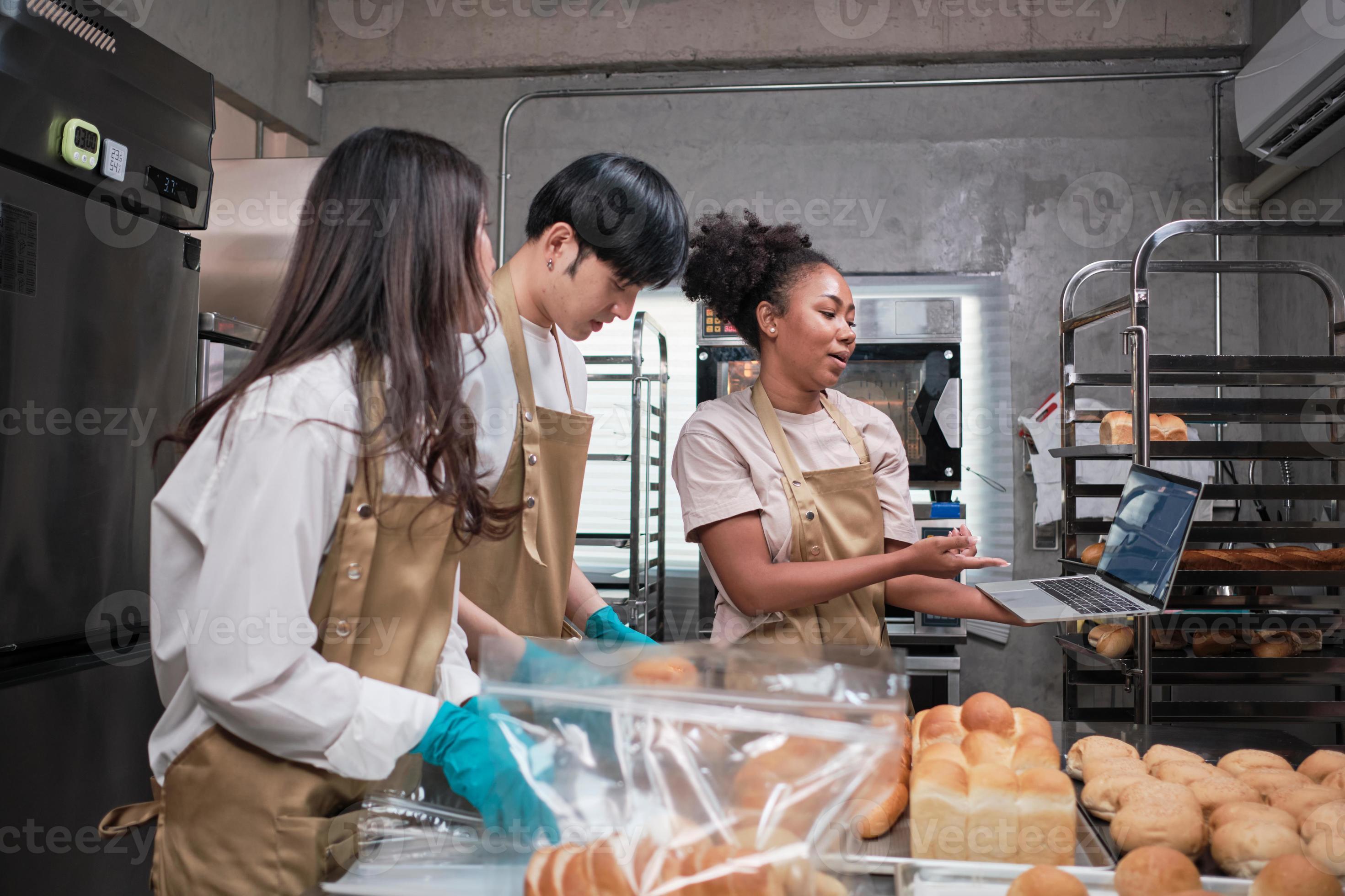
The heart of Interbake Foods’ operations lies in the dedication of its workforce, each member contributing to the seamless production of beloved baked goods. Understanding the specific roles and responsibilities within the company provides insight into the intricate processes that bring these treats to consumers. This section details the roles of a Production Line Worker and a Quality Control Technician, along with a visual representation of the baking process.
Production Line Worker Responsibilities
Production Line Workers are integral to the efficient operation of Interbake Foods’ manufacturing facilities. Their responsibilities are multifaceted and essential for maintaining consistent quality and output.
- Operating Machinery: Production Line Workers operate and monitor various pieces of equipment used in the baking process, such as mixers, ovens, and packaging machines. They ensure that the machinery functions correctly and report any malfunctions to the appropriate personnel.
- Ingredient Handling: They are responsible for accurately measuring and adding ingredients to the production line, following precise recipes and instructions. This includes ensuring the correct quantities and types of ingredients are used.
- Product Inspection: Throughout the production process, Production Line Workers visually inspect products for quality defects, such as incorrect size, shape, or appearance. They remove any defective products from the line.
- Packaging and Labeling: They package finished products according to specifications, ensuring that the correct labels are applied. This includes verifying that the packaging is sealed correctly and meets all regulatory requirements.
- Maintaining Cleanliness: Maintaining a clean and organized work environment is crucial. Production Line Workers are responsible for cleaning their workstations and equipment regularly to prevent contamination and ensure food safety.
- Following Safety Protocols: Adhering to strict safety protocols is paramount. They must follow all safety guidelines, wear appropriate personal protective equipment (PPE), and report any safety hazards to their supervisors.
- Teamwork and Communication: Working collaboratively with other team members and communicating effectively is essential. They communicate any issues or concerns to supervisors and work together to resolve them.
Quality Control Technician Duties
Quality Control Technicians play a vital role in ensuring that all products meet Interbake Foods’ stringent quality standards. Their duties involve meticulous inspection, testing, and analysis throughout the production process.
- Product Testing: Quality Control Technicians conduct various tests on raw materials, in-process products, and finished goods. These tests may include sensory evaluations (taste, smell, appearance), physical tests (weight, size, texture), and chemical analyses.
- Ingredient Verification: They verify the quality and suitability of incoming ingredients. This involves checking certificates of analysis (COAs) and conducting tests to ensure ingredients meet specifications.
- Process Monitoring: They monitor the production process to identify any deviations from established standards. This includes monitoring equipment performance, temperature, and other critical parameters.
- Documentation and Record Keeping: Maintaining accurate records of all testing and inspections is crucial. Quality Control Technicians document test results, deviations, and corrective actions taken.
- Calibration and Maintenance: They calibrate and maintain laboratory equipment to ensure accurate and reliable results. This includes following established calibration procedures and schedules.
- Problem Solving: When quality issues arise, Quality Control Technicians investigate the root cause and recommend corrective actions. This may involve working with production teams to implement process improvements.
- Compliance with Regulations: They ensure that all products comply with relevant food safety regulations and industry standards. This includes staying up-to-date on changes in regulations and implementing necessary adjustments to procedures.
Flowchart of the Baking Process
The baking process at Interbake Foods, while varying slightly depending on the specific product, generally follows a standardized series of steps. The following flowchart illustrates a simplified version of this process.
Step 1: Ingredient Receiving and Storage: Raw materials such as flour, sugar, and shortening are received and inspected for quality. They are then stored in temperature-controlled environments.
Step 2: Ingredient Preparation: Ingredients are measured and prepared according to the specific recipe for the product being made. This may involve sifting flour, melting butter, or mixing ingredients.
Step 3: Mixing: Ingredients are combined in large mixers to form the dough or batter. The mixing time and speed are carefully controlled to achieve the desired consistency.
Step 4: Forming/Shaping: The dough or batter is formed into the desired shape. This can be done manually or using automated equipment.
Step 5: Baking: The shaped dough or batter is baked in industrial ovens at precise temperatures for a specific duration. The baking process transforms the ingredients into the final product.
Step 6: Cooling: Baked products are cooled to a safe temperature to prevent condensation and maintain quality.
Step 7: Inspection: Products are inspected for quality defects such as incorrect size, shape, or appearance.
Step 8: Packaging: The baked products are packaged in appropriate containers or wrappers to maintain freshness and protect them during transportation.
Step 9: Quality Control Checks: Throughout the process, quality control checks are performed at each stage to ensure that the products meet all the requirements.
Step 10: Distribution: Packaged products are then distributed to retailers and consumers.
Skills and Qualifications for Success
To flourish within Interbake Foods, a candidate must possess a blend of technical proficiency, interpersonal skills, and a dedication to the company’s values. Success in this environment demands not only the ability to perform specific job duties but also the capacity to collaborate effectively, adapt to change, and contribute to a culture of safety and quality. This section details the essential skills and qualifications needed to excel at Interbake Foods, along with practical advice on how to demonstrate these attributes during the application and interview processes.
Essential Skills for Manufacturing Success
A successful career at Interbake Foods hinges on several key skill sets. These skills are critical for navigating the fast-paced manufacturing environment and ensuring the production of high-quality baked goods.
- Technical Proficiency: This includes a strong understanding of manufacturing processes, equipment operation, and maintenance. Candidates should demonstrate knowledge of food safety regulations, quality control procedures, and the ability to troubleshoot technical issues.
- Problem-Solving Abilities: The ability to identify, analyze, and resolve issues quickly and effectively is paramount. This involves critical thinking, attention to detail, and the capacity to make sound decisions under pressure.
- Communication Skills: Clear and concise communication is essential for collaborating with team members, reporting issues, and following instructions. This includes both verbal and written communication, as well as active listening skills.
- Teamwork and Collaboration: Manufacturing environments require individuals who can work cooperatively with others to achieve common goals. This involves sharing knowledge, supporting colleagues, and contributing to a positive team dynamic.
- Adaptability and Flexibility: The ability to adapt to changing priorities, learn new skills, and embrace new technologies is crucial. Interbake Foods operates in a dynamic environment, and employees must be able to adjust to evolving demands.
- Attention to Detail: Accuracy and precision are essential in food manufacturing to ensure product quality and safety. Employees must pay close attention to detail in all aspects of their work, from following recipes to operating machinery.
- Safety Consciousness: Prioritizing safety is non-negotiable. Employees must adhere to safety protocols, identify potential hazards, and contribute to a safe working environment.
Showcasing Skills in Applications and Interviews
Demonstrating the required skills during the application and interview phases is vital. Here’s how to effectively present your qualifications:
- Highlight Relevant Experience: In your resume and cover letter, provide specific examples of how you have utilized the essential skills in previous roles. Use action verbs to describe your accomplishments. For instance, instead of saying “Managed a team,” say “Led a team of five employees, successfully increasing production efficiency by 15%.”
- Quantify Achievements: Whenever possible, quantify your achievements to demonstrate your impact. Use numbers and data to illustrate your contributions. For example, “Reduced equipment downtime by 10% through proactive maintenance.”
- Prepare for Behavioral Questions: Interviewers often use behavioral questions to assess your past performance and predict future behavior. Be prepared to provide specific examples of how you have handled different situations in the past.
- Research the Company and the Role: Demonstrate your interest in Interbake Foods by researching the company’s values, products, and recent initiatives. Tailor your application and interview responses to reflect your understanding of the role and the company’s needs.
- Practice the STAR Method: The STAR method (Situation, Task, Action, Result) is a useful framework for answering behavioral questions. Briefly describe the situation, the task you faced, the actions you took, and the results you achieved.
Potential Interview Questions and Effective Responses
Preparing for common interview questions can significantly boost your confidence. Below are examples of questions and suggested responses, demonstrating how to showcase the desired skills.
- Question: “Tell me about a time you had to solve a difficult problem at work.”
- Effective Response: “In my previous role at [Previous Company], we experienced frequent breakdowns of the packaging machine. This was causing significant delays in production. My task was to identify the root cause and implement a solution. I began by thoroughly inspecting the machine, reviewing maintenance logs, and consulting with the maintenance team.
We discovered that a specific component was wearing out prematurely. I then researched potential replacement parts and recommended a more durable option. After implementing the new part, the machine’s downtime was reduced by 40%, significantly improving production efficiency.”
- Effective Response: “In my previous role at [Previous Company], we experienced frequent breakdowns of the packaging machine. This was causing significant delays in production. My task was to identify the root cause and implement a solution. I began by thoroughly inspecting the machine, reviewing maintenance logs, and consulting with the maintenance team.
- Question: “Describe a situation where you had to work as part of a team to achieve a common goal.”
- Effective Response: “During a major product launch at [Previous Company], the production team faced a tight deadline. My role was to oversee the quality control process. We had to ensure all products met stringent standards before shipping. I collaborated closely with the production and packaging teams, sharing my knowledge and expertise.
I also proactively identified potential bottlenecks and offered solutions. For example, when we realized the labeling machine was running slowly, I suggested adjusting the label placement process, which allowed us to increase the labeling speed. The team successfully met the deadline, and we received positive feedback on the product quality.”
- Effective Response: “During a major product launch at [Previous Company], the production team faced a tight deadline. My role was to oversee the quality control process. We had to ensure all products met stringent standards before shipping. I collaborated closely with the production and packaging teams, sharing my knowledge and expertise.
- Question: “How do you handle stress and pressure in a fast-paced environment?”
- Effective Response: “In a fast-paced environment, I prioritize tasks and break down large projects into smaller, manageable steps. I maintain open communication with my team, keeping them informed of progress and any challenges. I also utilize stress-management techniques, such as taking short breaks, practicing deep breathing exercises, and maintaining a positive attitude.
For example, during a recent production surge, I remained calm and focused by creating a detailed schedule and delegating tasks effectively, ensuring all deadlines were met without compromising quality.”
- Effective Response: “In a fast-paced environment, I prioritize tasks and break down large projects into smaller, manageable steps. I maintain open communication with my team, keeping them informed of progress and any challenges. I also utilize stress-management techniques, such as taking short breaks, practicing deep breathing exercises, and maintaining a positive attitude.
- Question: “Tell me about a time you had to adapt to a change in your work environment.”
- Effective Response: “At [Previous Company], we implemented a new software system for tracking inventory. Initially, I was unfamiliar with the software, but I quickly realized its importance. I proactively sought training from the IT department and my colleagues. I also took the initiative to explore the software’s features and functionalities.
I used the software to streamline inventory tracking and improve accuracy, which led to a reduction in waste. My adaptability to the new system significantly contributed to the overall efficiency of the warehouse.”
- Effective Response: “At [Previous Company], we implemented a new software system for tracking inventory. Initially, I was unfamiliar with the software, but I quickly realized its importance. I proactively sought training from the IT department and my colleagues. I also took the initiative to explore the software’s features and functionalities.
- Question: “Why do you want to work at Interbake Foods?”
- Effective Response: “I am drawn to Interbake Foods because of its reputation for quality and innovation in the baking industry. I am particularly impressed by [mention a specific product or initiative]. I am also eager to contribute to a company that values teamwork, safety, and continuous improvement. My skills and experience align well with the requirements of this role, and I am confident that I can make a valuable contribution to your team.”
Career Advancement and Training Programs
The sweet scent of opportunity hangs heavy in the air at Interbake Foods, a fragrance as enticing as the freshly baked cookies that roll off its production lines. Beyond the immediate rewards of employment, a vibrant landscape of career progression and skill development awaits those who choose to build their future within the company. Interbake Foods fosters a culture of growth, recognizing that its employees are the most valuable ingredients in its recipe for success.
Opportunities for Career Progression
Interbake Foods provides structured pathways for employees to climb the career ladder, with advancement opportunities spanning various departments and skill sets. The company champions internal promotion, giving employees a clear advantage over external candidates. These opportunities are not simply promises; they are actively cultivated through performance evaluations, mentorship programs, and a commitment to recognizing and rewarding employee contributions.
Internal Training Programs and Development Initiatives
Interbake Foods understands that its employees’ skills must continuously evolve to meet the dynamic demands of the food manufacturing industry. The company invests heavily in internal training programs designed to equip employees with the knowledge and abilities needed to excel in their current roles and prepare for future advancement. These programs are meticulously crafted to cater to a wide range of employee needs and career goals.
- On-the-Job Training: New hires and employees transitioning to new roles receive comprehensive on-the-job training, often under the guidance of experienced mentors. This hands-on approach allows employees to learn the practical aspects of their jobs while gaining valuable insights from seasoned professionals. The training emphasizes safety protocols, operational procedures, and quality control measures.
- Leadership Development Programs: Aspiring leaders are given the chance to hone their leadership skills through specialized programs that cover topics such as team management, conflict resolution, and strategic decision-making. These programs often incorporate workshops, simulations, and real-world case studies.
- Technical Skills Training: To keep pace with technological advancements, Interbake Foods offers ongoing technical skills training. This includes training on new equipment, software systems, and manufacturing processes. This commitment ensures that employees stay proficient in their respective fields.
- Cross-Functional Training: Employees are often encouraged to participate in cross-functional training programs, which expose them to different departments and roles within the company. This fosters a broader understanding of the company’s operations and helps employees identify potential career paths that align with their interests and abilities.
Advancing Skills and Knowledge Through External Resources, Interbake foods jobs
Recognizing the value of external resources, Interbake Foods supports employees in their pursuit of further education, certifications, and professional development opportunities. This commitment extends beyond internal training programs, allowing employees to access a broader range of expertise and specialized knowledge.
- Tuition Reimbursement: Employees are eligible for tuition reimbursement for relevant coursework and degree programs, including certifications related to food science, engineering, and business administration. This financial support removes a significant barrier to further education, empowering employees to pursue their academic goals.
- Professional Certifications: Interbake Foods encourages employees to obtain industry-recognized certifications, such as those offered by the Food Safety Modernization Act (FSMA) and the Institute of Food Technologists (IFT). The company often covers the costs associated with these certifications.
- Industry Conferences and Seminars: Employees are provided opportunities to attend industry conferences and seminars, where they can learn about the latest trends, technologies, and best practices in the food manufacturing industry. This exposure to external expertise helps employees stay informed and competitive.
- Partnerships with Educational Institutions: Interbake Foods may establish partnerships with local colleges and universities to offer customized training programs or internships. These partnerships provide employees with access to specialized training and educational resources tailored to their specific needs and the company’s operational requirements.
Salary and Compensation Information
Interbake Foods recognizes that competitive compensation is crucial for attracting and retaining top talent. The company’s approach to compensation is designed to reflect the value of each role, the employee’s contributions, and the overall performance of the business. Transparency and fairness are key principles guiding the compensation structure, ensuring employees understand how their pay is determined and how they can advance their earnings.Compensation at Interbake Foods goes beyond a simple salary.
It’s a comprehensive package that includes benefits, incentives, and opportunities for professional development. This holistic approach is designed to create a positive and rewarding work environment where employees feel valued and motivated to excel.
Estimated Salary Ranges for Different Job Roles
The following provides estimated salary ranges for various job roles at Interbake Foods. These figures are approximate and can vary based on experience, skills, and location.
- Production Line Workers: The entry-level salary typically ranges from $30,000 to $40,000 per year. Experienced workers, with specialized skills or supervisory responsibilities, may earn upwards of $50,000 annually.
- Quality Control Technicians: Salaries generally fall between $45,000 and $60,000 per year, reflecting the importance of ensuring product quality and adherence to standards. Senior technicians or those with specialized certifications may earn more.
- Maintenance Technicians: The salary range typically varies from $50,000 to $70,000 annually, depending on the level of experience and the complexity of the machinery maintained. Technicians with advanced skills in areas like electrical or mechanical engineering may command higher salaries.
- Supervisors/Team Leads: Salaries for these roles usually range from $60,000 to $80,000 per year, reflecting the added responsibilities of managing teams and overseeing production processes.
- Managers (various departments): Managerial roles, such as Production Managers or Quality Assurance Managers, typically have a salary range from $80,000 to $120,000 or higher per year, depending on experience, scope of responsibility, and the size of the facility.
- Corporate Roles (e.g., Finance, Marketing): Salaries for corporate positions are generally competitive and depend on the specific role and experience. Ranges can vary widely, but entry-level positions may start around $50,000, while senior-level roles can exceed $150,000 annually.
Comparison of Compensation Packages with Industry Standards
Interbake Foods strives to offer compensation packages that are competitive within the food manufacturing industry. This comparison considers both salary and benefits.
The company benchmarks its compensation against industry standards, considering factors like location, company size, and the specific roles. Benefits packages often include health insurance, retirement plans, paid time off, and other perks. Interbake Foods’ packages often align with or exceed industry norms to attract and retain talent. For example, Interbake Foods might offer a more generous 401(k) matching program or a broader health insurance plan compared to some competitors.
This is to ensure that employees are properly compensated for their work.
Performance-Based Incentives and Bonuses
Interbake Foods incorporates performance-based incentives and bonuses to reward employees for their contributions to the company’s success. These incentives are designed to motivate employees and align their goals with the overall objectives of the business.
Several types of performance-based rewards are offered:
- Production Bonuses: Production line workers may receive bonuses based on meeting or exceeding production targets. These bonuses are often tied to metrics such as units produced per hour, minimizing waste, or maintaining a high level of product quality.
- Quality Assurance Bonuses: Quality control technicians may receive bonuses for maintaining a low rate of product defects or for successfully implementing improvements to quality control processes.
- Sales Bonuses (for relevant roles): Sales representatives or marketing personnel may receive bonuses based on meeting or exceeding sales targets, expanding market share, or launching successful new products.
- Management Bonuses: Managers and supervisors may be eligible for bonuses based on the overall performance of their teams or departments, meeting financial targets, or achieving specific strategic goals.
- Company-Wide Bonuses: In some instances, the company may offer profit-sharing or other bonuses to all employees if the company meets or exceeds its financial targets for a specific period.
These performance-based incentives are regularly reviewed and adjusted to ensure they remain effective in motivating employees and rewarding their contributions. For example, a team that consistently exceeds production goals may receive a higher bonus rate or additional recognition from management.
Company Locations and Contact Information
Interbake Foods, a prominent name in the baking industry, strategically positions its facilities to optimize production and distribution across North America. Understanding the geographical footprint of the company and how to reach its various departments is crucial for anyone seeking employment, partnerships, or information. This section provides a detailed overview of Interbake Foods’ locations and contact information.
Manufacturing Facility Locations
Interbake Foods operates several manufacturing facilities strategically located to serve its diverse customer base efficiently. These facilities are equipped with state-of-the-art technology and adhere to rigorous quality control standards. The locations reflect the company’s commitment to delivering fresh, high-quality baked goods to consumers across the continent.
- Front Royal, Virginia: This facility serves as a significant production hub for various Interbake Foods products. It is known for its large-scale production capabilities and commitment to operational excellence.
- Richmond, Virginia: Another key manufacturing location, the Richmond facility contributes to the company’s extensive production capacity, ensuring a consistent supply of baked goods.
- Oakland, California: This West Coast facility expands Interbake Foods’ reach, enabling efficient distribution to markets in the western United States.
- Montreal, Quebec, Canada: Serving the Canadian market, this facility ensures the availability of Interbake Foods’ products within the country.
Office Locations
Interbake Foods’ corporate and administrative functions are managed from several office locations. These offices house various departments, including human resources, sales, marketing, and executive leadership.
- Corporate Headquarters (Specific Address Unavailable): While the exact address of the corporate headquarters is often not publicly disclosed for security and operational reasons, it is known to be located in the United States. This central hub coordinates all major business functions.
- Sales and Regional Offices (Various Locations): Interbake Foods maintains sales offices in various strategic locations across North America to support its regional sales efforts and customer relationships.
Human Resources Contact Information
Accessing the human resources department is essential for potential employees and current staff alike. While specific contact details can vary, the primary method of contact is generally through the company website.
- Website: The official Interbake Foods website (specific URL unavailable) is the primary source for employment inquiries, job postings, and contact information for the human resources department. Job seekers should regularly check the careers section of the website for the most up-to-date information.
- Application Portal: Most applications are submitted through an online portal, which can be accessed via the company website.
- General Inquiries: General inquiries may be directed to a contact form available on the website or to a generic email address, if provided.
Map Highlighting Interbake Foods Facilities
(Descriptive Illustration of a Map)Imagine a detailed map of North America. The map clearly Artikels the United States and Canada. Within this map, several points are highlighted, each representing an Interbake Foods facility.
- Front Royal, Virginia: A red dot with the name “Front Royal” next to it, signifying the manufacturing plant, is positioned in the central part of Virginia.
- Richmond, Virginia: Another red dot with “Richmond” next to it is located slightly to the southeast of Front Royal, also in Virginia.
- Oakland, California: A red dot with “Oakland” is placed on the western coast of the United States, in California, showing the location of the facility.
- Montreal, Quebec: A red dot with “Montreal” next to it is positioned in the southern part of Quebec, Canada, indicating the location of the Canadian manufacturing facility.
- Corporate Headquarters (US – approximate location): A slightly larger marker, perhaps with a different color or symbol, represents the corporate headquarters, located in the United States. The specific location is not provided, but it’s placed in a central area.
- Sales and Regional Offices: Smaller markers, perhaps in a different color, are scattered across the map, representing sales and regional offices, illustrating the company’s widespread presence.
The map visually communicates the geographical distribution of Interbake Foods’ operations, highlighting its manufacturing capabilities and its strategic locations across the North American continent.
Interview Process and Preparation
The path to a rewarding career at Interbake Foods often begins with a well-structured interview process. Understanding this process and preparing diligently can significantly increase your chances of success. This section provides a comprehensive overview of what to expect and how to excel.
Typical Interview Stages
Interbake Foods typically employs a multi-stage interview process to assess candidates thoroughly. This allows them to evaluate not only skills and experience but also cultural fit and long-term potential.
- Initial Screening: This stage often involves a review of your application materials, including your resume and cover letter. A recruiter may conduct a brief phone screen to assess your basic qualifications and interest in the role.
- First-Round Interview: This is usually a face-to-face interview (or video conference) with a hiring manager or a member of the HR team. The focus is on evaluating your skills, experience, and how they align with the job requirements. Behavioral questions are frequently used to assess past performance and predict future behavior.
- Second-Round Interview (if applicable): Depending on the role and company needs, a second interview may be scheduled. This could involve a panel interview with multiple stakeholders, including team members and senior management. This stage often delves deeper into technical skills, problem-solving abilities, and cultural fit.
- Final Interview (if applicable): This is often the final step in the process and may involve meeting with a senior executive or a member of the leadership team. It’s an opportunity to discuss your long-term career goals and how you see yourself contributing to Interbake Foods’ success.
- Offer and Onboarding: If successful, you will receive a job offer. This is followed by onboarding, which includes completing necessary paperwork and training to prepare you for your role.
Interview Preparation Strategies
Thorough preparation is key to making a positive impression during your interviews. Here’s how to approach the preparation phase:
- Research the Company: Deeply understand Interbake Foods’ history, products, values, and recent news. Review their website, social media, and industry publications. Understanding the company’s mission and goals allows you to tailor your responses and demonstrate your genuine interest.
- Review the Job Description: Carefully analyze the job description and identify the key skills and qualifications required. Prepare specific examples from your experience that showcase how you meet these requirements.
- Practice Common Interview Questions: Prepare answers to common interview questions, such as:
- “Tell me about yourself.”
- “Why are you interested in this position?”
- “What are your strengths and weaknesses?”
- “Describe a time you overcame a challenge.”
- “Where do you see yourself in five years?”
Practice your answers out loud to improve your delivery and ensure you are concise and articulate.
- Prepare Questions to Ask: Asking thoughtful questions demonstrates your engagement and interest. Prepare questions about the role, the team, the company culture, and opportunities for growth. Avoid questions easily answered through research.
- Prepare Examples Using the STAR Method: The STAR method is a structured approach to answering behavioral questions. It stands for:
- Situation: Briefly describe the context.
- Task: Explain the task or challenge you faced.
- Action: Detail the specific actions you took.
- Result: Highlight the positive outcomes of your actions.
- Mock Interviews: Practice interviewing with a friend, family member, or career counselor. This helps you refine your responses, manage your nerves, and receive constructive feedback.
Expected Dress Code and Professional Etiquette
Presenting yourself professionally is crucial for making a positive first impression.
- Dress Code: While the specific dress code may vary depending on the role and the company’s culture, it’s generally advisable to dress in business professional attire for interviews. This typically includes a suit, dress shirt, and tie for men, and a suit or professional separates for women. For less formal roles, business casual attire might be acceptable, but it’s always better to err on the side of formality.
- Punctuality: Arrive on time for your interview. If the interview is in-person, plan your route and allow for traffic or other potential delays. If the interview is virtual, log in a few minutes early to ensure your technology is working correctly.
- Communication: Maintain professional communication throughout the interview process. Respond promptly to emails and phone calls. Use proper grammar and spelling in all written communication.
- Body Language: Maintain good posture, make eye contact, and smile. Show enthusiasm and genuine interest in the opportunity. Avoid fidgeting or distracting behaviors.
- Follow-up: Send a thank-you note to the interviewer within 24 hours of the interview. This reiterates your interest in the position and reinforces your professionalism.
Employee Testimonials and Experiences
Hearing directly from those who shape the daily rhythm of Interbake Foods provides invaluable insight into the company’s true character. These testimonials, gleaned from current and former employees, paint a vivid picture of the workplace environment, highlighting both its strengths and the areas where growth is actively pursued. The following accounts offer a candid perspective on the employee experience at Interbake Foods.
Positive Aspects of Working for Interbake Foods
Employee feedback consistently highlights several positive facets of working at Interbake Foods. These sentiments, echoed across various roles and tenures, reflect a generally positive work environment.
“I appreciate the supportive atmosphere. People genuinely care about each other and the company’s success.”
Sarah M., Production Supervisor
* Many employees praise the company’s commitment to safety, citing comprehensive training programs and a culture that prioritizes employee well-being.
- Opportunities for professional development and career advancement are frequently mentioned. Interbake Foods appears to invest in its employees’ growth through training, mentorship, and internal promotion pathways.
- The collaborative spirit and teamwork are frequently lauded. Employees often describe a workplace where individuals readily support one another to achieve common goals.
- The company’s stability and long-standing presence in the industry contribute to a sense of security and pride among its employees.
Challenges Faced by Employees and Company Responses
While employee experiences are generally positive, feedback also reveals areas where Interbake Foods acknowledges challenges and strives for improvement. The company’s response to these issues demonstrates a commitment to creating a better work environment.
“Initially, the shift schedules were a bit unpredictable. However, the company listened to our feedback and implemented a more structured system.”
David L., Maintenance Technician
* One recurring theme involves the need for clear communication. The company addresses this by improving internal communication channels, including regular updates and feedback sessions.
- Addressing concerns regarding work-life balance is a priority. Interbake Foods has explored options such as flexible scheduling and adjusted workloads to improve employee well-being.
- The company has invested in improving its equipment and processes to reduce physical strain and enhance efficiency. Employee feedback regarding ergonomic improvements has been incorporated into design and implementation.
- Interbake Foods emphasizes regular employee surveys and feedback sessions to gather input, understand concerns, and implement necessary changes to improve the overall work environment. This commitment to continuous improvement is evident in the company’s responsiveness to employee suggestions.
Final Wrap-Up
In conclusion, Interbake Foods Jobs present a compelling option for those eager to embark on or advance their careers in food manufacturing. The company’s dedication to its employees, its commitment to quality, and its opportunities for growth make it a desirable employer. By understanding the company’s operations, available roles, and the skills needed to thrive, potential applicants can confidently navigate the job market and position themselves for success within Interbake Foods.