Lawrence Foods Inc. Logistics Center, a sprawling heart of commerce, beats with the rhythm of movement, the constant dance of goods in transit. It is here, in this concrete and steel leviathan, that the lifeblood of Lawrence Foods – its products, its promises – flows, from the moment of arrival to the point of departure, destined for kitchens and tables far beyond the warehouse walls.
This is not merely a storage facility; it is a meticulously orchestrated ecosystem, a place where forklifts pirouette with conveyors, and technology whispers secrets of efficiency and optimization.
We will delve into the very sinews of this logistical behemoth. We will witness the receiving process, a careful dance of inspection and placement, the order fulfillment, where digital commands translate into physical reality, and the shipping, a final push that propels the goods toward their ultimate destination. We will scrutinize the infrastructure, the technologies, and the human element that makes this operation hum.
Moreover, we’ll explore the challenges, the solutions, and the vision for the future, a future where sustainability and innovation are not just buzzwords but the very fabric of operations.
Overview of Lawrence Foods Inc. Logistics Center
Lawrence Foods Inc., a prominent player in the food industry, specializes in the manufacturing and distribution of a wide range of baked goods, fillings, and toppings. The company caters to both retail and foodservice sectors, supplying products to supermarkets, restaurants, and other food-related businesses. Their commitment to quality and efficient operations is crucial to their success.The Lawrence Foods Inc. Logistics Center serves as a vital hub in the company’s supply chain, ensuring the timely and efficient movement of goods from production facilities to customers.
This includes receiving raw materials, storing finished products, managing inventory, and coordinating the distribution process. The logistics center is designed to maintain the integrity and freshness of the products while optimizing delivery schedules and minimizing costs.
Core Functions of the Logistics Center
The logistics center performs several critical functions to support Lawrence Foods Inc.’s operations. These functions work in concert to ensure a smooth and efficient flow of products from the factory to the consumer.
- Receiving and Inventory Management: Upon arrival, raw materials and finished goods are received, inspected for quality, and recorded in the inventory system. This includes verifying quantities, checking for damage, and assigning storage locations. Accurate inventory management is crucial for tracking stock levels, preventing spoilage, and fulfilling orders efficiently.
- Storage and Warehousing: The logistics center provides climate-controlled storage for various products, including refrigerated and frozen storage areas to maintain product integrity. This ensures that the baked goods, fillings, and toppings remain fresh and safe for consumption. Proper storage also involves implementing First-In, First-Out (FIFO) inventory management to minimize waste.
- Order Fulfillment and Processing: When orders are received from customers, the logistics center’s team picks, packs, and prepares the products for shipment. This process involves selecting the correct items from storage, assembling the orders, and ensuring proper packaging to prevent damage during transit.
- Transportation and Distribution: The logistics center coordinates the transportation of finished goods to customers. This may involve utilizing a fleet of trucks, partnering with third-party logistics providers, or a combination of both. Efficient transportation planning is essential to meet delivery deadlines and minimize transportation costs.
Size and Location of the Logistics Center
The Lawrence Foods Inc. Logistics Center is strategically located to facilitate efficient distribution.
While the exact square footage of the logistics center can vary based on expansion and operational needs, a typical facility of this type in the food industry might range from 100,000 to 500,000 square feet or more, depending on the volume of goods handled. Consider, for example, the distribution centers of large bakery companies. These facilities often require extensive space for storage, order processing, and cross-docking activities.
The location of the logistics center is also crucial for minimizing transportation costs and ensuring timely deliveries. The facility is generally situated near major transportation routes, such as highways and interstates, to facilitate efficient distribution across a wide geographical area. Proximity to major cities and customer markets is also a key consideration.
The strategic placement and size of the logistics center are vital for Lawrence Foods Inc. to maintain its competitive edge in the food industry, enabling them to meet the demands of their customers effectively.
Logistics Center Infrastructure and Capabilities
The Lawrence Foods Inc. Logistics Center is a critical component of the company’s supply chain, designed to efficiently manage the flow of goods from suppliers to customers. This section delves into the physical infrastructure, the types of goods handled, and the technologies that underpin its operations, showcasing the center’s capacity to meet the demands of a dynamic market.
Physical Infrastructure of the Logistics Center, Lawrence foods inc. logistics center
The logistics center boasts a robust physical infrastructure designed for optimal operational efficiency. This includes a significant warehouse space, strategically positioned loading docks, and a range of equipment to facilitate the movement and storage of goods.The warehouse itself provides a substantial area for storing a diverse range of products. This space is carefully organized to maximize storage capacity while ensuring easy access for order fulfillment.
The loading docks are equipped to handle a high volume of inbound and outbound shipments. They are strategically placed to minimize the time required for loading and unloading trucks, contributing to faster turnaround times. The layout and design are compliant with all relevant safety regulations, prioritizing the well-being of the staff and the integrity of the stored goods.
You also will receive the benefits of visiting food fight sound effect nyt today.
Types of Goods Handled and Stored
The logistics center handles a variety of goods, reflecting the diverse product portfolio of Lawrence Foods Inc. Understanding the nature of these goods is crucial for efficient handling and storage.Lawrence Foods Inc. typically handles a variety of food products. These include both ambient and refrigerated/frozen items. The center must be equipped to handle goods with different temperature requirements, which may include dry goods, canned goods, packaged foods, and potentially some raw ingredients depending on the supply chain needs.
The center is designed to manage various product formats, from individual packages to bulk containers, ensuring flexibility and adaptability.
Inventory Management Technologies
Efficient inventory management is paramount to the smooth operation of the logistics center. The center leverages advanced technologies to track and manage inventory effectively.A Warehouse Management System (WMS) is likely employed to oversee all aspects of warehouse operations, from receiving and putaway to picking and shipping. A WMS allows for real-time visibility into inventory levels, locations, and movements, improving accuracy and reducing errors.
Furthermore, a Transportation Management System (TMS) could be used to optimize transportation routes, manage carrier relationships, and track shipments. The integration of WMS and TMS streamlines the entire supply chain, providing end-to-end visibility and control. These systems are often integrated with other enterprise resource planning (ERP) systems to provide a comprehensive view of the business operations.
Equipment Used in the Logistics Center
The logistics center utilizes a diverse range of equipment to facilitate the efficient handling of goods. This equipment is essential for moving, storing, and retrieving products within the facility. The selection and deployment of this equipment are key to optimizing operational efficiency and ensuring the safety of employees.The following table illustrates the types of equipment used in the logistics center, detailing their function, manufacturer (hypothetical example), and key features:
Equipment Type | Function | Manufacturer (Example) | Key Features |
---|---|---|---|
Forklifts | Lifting and transporting pallets of goods. | Toyota | Various lifting capacities, electric and gas-powered models, ergonomic design for operator comfort and safety. |
Conveyors | Moving goods horizontally within the warehouse, from receiving to storage or from picking to shipping. | Interroll | Roller conveyors, belt conveyors, and gravity conveyors are used, optimizing the movement of goods throughout the facility, customizable configurations. |
Automated Guided Vehicles (AGVs) | Transporting materials autonomously within the warehouse, often following pre-programmed routes. | Dematic | Laser-guided or vision-guided navigation, integrated with WMS for real-time inventory tracking, increasing efficiency and reducing labor costs. |
Reach Trucks | Used for high-density storage, enabling the warehouse to stack pallets at higher levels, providing greater storage capacity. | Crown | Extended reach capabilities, narrow aisle operation, enhanced visibility for safe operation. |
Supply Chain Operations and Processes
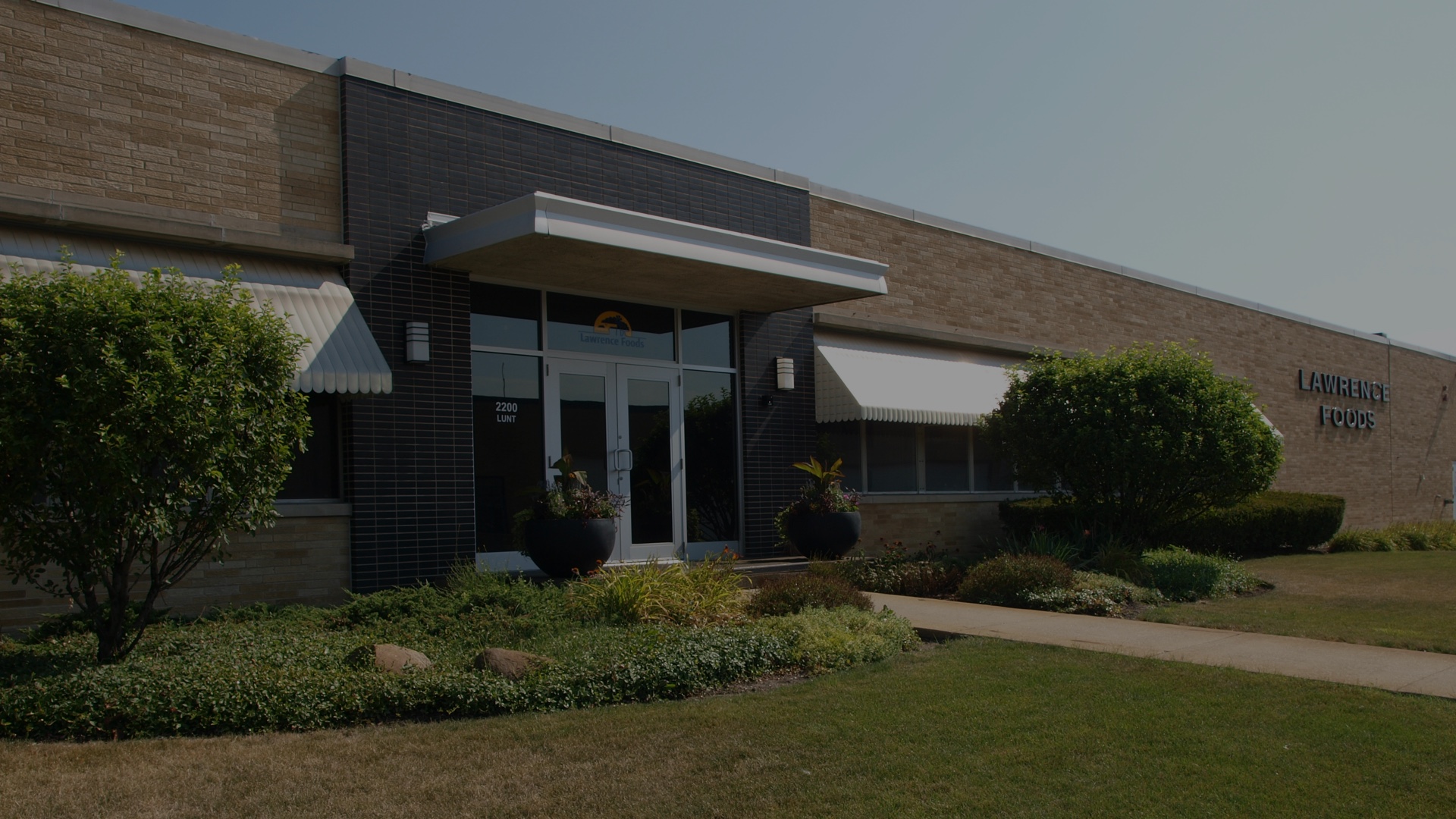
Lawrence Foods Inc.’s Logistics Center operates as a crucial link in the company’s supply chain, ensuring the efficient and timely movement of goods from suppliers to customers. This section details the intricate processes that govern the flow of products, from receiving raw materials to delivering finished goods. The effectiveness of these operations directly impacts customer satisfaction and the overall profitability of the business.
Receiving Process
The receiving process at Lawrence Foods Inc. is a multi-step operation designed to ensure the accurate and efficient intake of inbound goods. This process is critical for maintaining inventory accuracy and preventing disruptions in downstream operations.The inbound logistics process begins with the advance notification of shipments. Suppliers are required to provide detailed shipping information, including packing lists and expected arrival times, which is integrated into the warehouse management system (WMS).
Upon arrival, the following steps are executed:
- Inbound Logistics: Trucks or other delivery vehicles are scheduled and directed to designated receiving docks. Trained personnel are responsible for verifying the seal integrity of the trucks and ensuring that all documentation is in order.
- Inspection: Upon unloading, a visual inspection is conducted to identify any signs of damage or discrepancies between the delivered goods and the accompanying paperwork. Items are checked against the packing list to confirm the quantity and type of goods received. Any issues are immediately documented.
- Put-Away Procedures: After inspection, accepted goods are prepared for put-away. This involves assigning each item a unique location within the warehouse, based on factors like product type, storage requirements, and inventory management strategies. The WMS guides warehouse staff to the designated storage locations. The system ensures that the products are stored in optimal conditions, such as temperature-controlled environments for perishable items.
Order Fulfillment Process
The order fulfillment process at Lawrence Foods Inc. is a complex operation that encompasses the steps from when an order is placed by a customer to when it is prepared for shipment. This process is crucial for meeting customer expectations and maintaining a competitive edge.The process begins with order entry, where orders received through various channels, such as online platforms, sales representatives, and EDI (Electronic Data Interchange), are entered into the WMS.
The system then automatically manages the following:
- Order Entry: Orders are received and entered into the WMS, capturing all relevant information, including product details, quantities, customer information, and delivery preferences.
- Order Processing and Allocation: The WMS checks inventory availability and allocates the necessary products to fulfill the order. If items are out of stock, the system may trigger backorder procedures or suggest alternative products.
- Picking: Warehouse staff, guided by the WMS, pick the required items from their designated storage locations. This process often utilizes technologies like barcode scanning or voice picking to ensure accuracy and speed.
- Packing: Once the items are picked, they are packed securely, considering factors such as product fragility and shipping requirements. Packaging materials are selected to protect the goods during transit.
- Shipping Labeling and Manifesting: Packed orders are labeled with shipping information, including the customer’s address, tracking number, and any special handling instructions. The WMS generates a shipping manifest, which details the contents of each shipment.
- Shipment Preparation: Orders are consolidated, and the manifest is provided to the shipping carrier for final preparation for transportation.
Shipping and Distribution Methods
Lawrence Foods Inc. utilizes a multifaceted shipping and distribution strategy to ensure efficient and timely delivery of its products. The company leverages a combination of transportation partners and route optimization to meet the diverse needs of its customer base.The company relies on various transportation partners, including national and regional carriers, to handle different types of shipments and delivery requirements. This allows for flexibility and cost optimization.
Route optimization tools and software are utilized to plan the most efficient delivery routes, considering factors such as distance, traffic conditions, and delivery time windows.The selection of shipping and distribution methods depends on factors such as the product type, order size, delivery location, and customer requirements. The following are examples:
- Transportation Partners: Strategic partnerships with national and regional trucking companies, as well as parcel carriers, enable the company to handle a wide range of shipment sizes and destinations.
- Transportation Modes: The company employs various modes of transportation, including over-the-road trucking (for larger shipments), parcel services (for smaller packages), and potentially rail or intermodal transport for long-distance or bulk shipments.
- Routes: The company optimizes routes using software that considers factors like distance, traffic, and delivery time windows, to ensure the most efficient and cost-effective delivery.
- Examples: For example, a large shipment of frozen goods destined for a major retail chain might be transported via refrigerated trucks, utilizing specific routes to maintain product integrity. Smaller orders to individual customers might be handled by parcel carriers.
Typical Order Fulfillment Process Steps
The following bulleted list summarizes the key steps involved in a typical order fulfillment process at the Lawrence Foods Inc. Logistics Center.
- Order Receipt: The order is received through various channels.
- Order Processing: The order is processed and validated.
- Inventory Check: Inventory availability is checked.
- Allocation: Products are allocated to the order.
- Picking: Items are picked from storage locations.
- Packing: Items are packed securely.
- Labeling: Shipping labels are generated and applied.
- Manifesting: A shipping manifest is created.
- Shipping: The order is prepared for shipment and handed over to the carrier.
- Delivery: The order is delivered to the customer.
Inventory Management and Control: Lawrence Foods Inc. Logistics Center
Effective inventory management is crucial for Lawrence Foods Inc.’s Logistics Center, directly impacting operational efficiency, cost control, and customer satisfaction. This section delves into the specific strategies, methods, and analytical tools employed to maintain optimal inventory levels and ensure a smooth flow of goods.
Inventory Control Strategies
Lawrence Foods Inc. utilizes a multi-faceted approach to inventory control, selecting strategies based on product characteristics, shelf life, and demand patterns. These strategies aim to minimize waste, reduce holding costs, and ensure product availability.
- First-In, First-Out (FIFO): FIFO is the primary method used for perishable goods, such as certain food ingredients and finished products. This ensures that the oldest inventory is used or shipped first, minimizing the risk of spoilage and obsolescence.
- Last-In, First-Out (LIFO): LIFO is generally not used for physical inventory management at Lawrence Foods Inc., particularly for food products, due to its potential to lead to spoilage. However, it may be considered for certain accounting purposes, though this would depend on accounting practices and tax regulations.
- First-Expired, First-Out (FEFO): FEFO is critical for managing products with expiration dates. This strategy prioritizes the use or shipment of items closest to their expiration dates, regardless of when they were received. This is particularly vital for products like sauces, dressings, and other items with a limited shelf life.
Inventory Tracking and Level Management
Accurate and real-time inventory tracking is paramount for preventing stockouts and overstock situations. Lawrence Foods Inc. employs a combination of technological and operational methods to achieve this.
- Warehouse Management System (WMS): A sophisticated WMS is at the core of inventory tracking. The WMS provides real-time visibility into inventory levels, locations, and movements within the warehouse. This includes tracking goods from receiving, through storage, order fulfillment, and shipping.
- Barcoding and RFID Technology: Barcodes and Radio-Frequency Identification (RFID) tags are used to identify and track individual items or batches of items. This allows for quick and accurate scanning during receiving, put-away, picking, and shipping processes. RFID is particularly useful for tracking large volumes of inventory quickly.
- Cycle Counting: Regular cycle counts are conducted to verify the accuracy of inventory records. This involves physically counting a small portion of the inventory on a regular basis and comparing the count to the WMS records. Discrepancies are investigated and corrected to maintain data integrity.
- Safety Stock Levels: Safety stock is maintained for each product to buffer against unexpected demand fluctuations or supply chain disruptions. These levels are determined based on historical demand data, lead times, and service level requirements.
- Reorder Points: Reorder points are established for each product to trigger a replenishment order when the inventory level falls below a certain threshold. This ensures that sufficient inventory is available to meet demand before the stock is depleted.
Data Analytics in Inventory Optimization
Data analytics plays a critical role in optimizing inventory management at Lawrence Foods Inc. By analyzing historical data and market trends, the company can make data-driven decisions to improve inventory accuracy, reduce costs, and enhance customer service.
- Demand Forecasting: Statistical forecasting models are used to predict future demand for each product. These models consider historical sales data, seasonality, promotional activities, and market trends. Accurate forecasting is essential for setting optimal inventory levels and avoiding stockouts or overstock situations.
- ABC Analysis: ABC analysis categorizes inventory items based on their value and volume. “A” items are high-value, high-volume items that require the most attention and control. “B” items are medium-value, medium-volume items, and “C” items are low-value, low-volume items. This analysis helps prioritize inventory management efforts.
- Inventory Turnover Analysis: Inventory turnover rates are calculated for each product to measure how quickly inventory is sold and replenished. High turnover rates indicate efficient inventory management, while low turnover rates may signal overstocking or slow-moving items.
- Lead Time Analysis: Lead times, which are the time it takes to receive a new order, are monitored and analyzed. This information is used to optimize reorder points and safety stock levels.
- Supplier Performance Analysis: Data is collected on supplier performance, including on-time delivery rates and order accuracy. This information is used to select and manage suppliers effectively.
Example of a Data Visualization: Inventory Turnover Rate
Inventory turnover rate is a key performance indicator (KPI) for assessing inventory efficiency. The following example illustrates how this data can be visualized to provide actionable insights.
A line graph is used to visualize the inventory turnover rate for a specific product (e.g., “Classic Marinara Sauce”) over a period of 12 months.
- X-axis (Horizontal): Represents the months (January through December).
- Y-axis (Vertical): Represents the inventory turnover rate, expressed as the number of times the inventory is sold and replenished during the month.
Description of the Graph’s Features:
The graph displays a line that fluctuates over the 12-month period.
- Trend: An upward trend in the line from January to May, indicating an increasing inventory turnover rate. This suggests that sales are improving, and inventory is being managed efficiently.
- Peaks and Valleys: Peaks in the turnover rate often coincide with periods of high demand, such as during promotional campaigns or seasonal events (e.g., a peak in June for a summer promotion). Valleys might appear during periods of slower sales or supply chain disruptions.
- Data Points: Individual data points on the line represent the inventory turnover rate for each specific month. For instance, the turnover rate might be 2.5 in January, increase to 3.8 in May, drop to 3.0 in July, and increase again to 4.2 in December.
Insights and Actions:
- High Turnover: High turnover rates (e.g., above 4) indicate efficient inventory management and strong sales.
- Low Turnover: Low turnover rates (e.g., below 2) might indicate overstocking or slow-moving items, which could lead to spoilage or increased holding costs.
- Actionable Insights:
- Analyze the reasons for fluctuations: Investigate why turnover rates are high or low during specific periods.
- Adjust inventory levels: Increase or decrease inventory levels based on the observed trends and forecasts.
- Optimize marketing and sales strategies: Promote products with low turnover rates to increase sales.
This data visualization enables Lawrence Foods Inc. to monitor inventory performance, identify areas for improvement, and make informed decisions to optimize inventory levels and enhance operational efficiency.
Technology and Automation in the Logistics Center
The Lawrence Foods Inc. Logistics Center leverages cutting-edge technology and automation to optimize its operations, ensuring efficiency, accuracy, and responsiveness to meet the evolving demands of the food industry. Automation plays a pivotal role in streamlining various processes, from order fulfillment to inventory management, ultimately contributing to a more agile and cost-effective supply chain.
Role of Automation in the Logistics Center
Automation is integral to the Lawrence Foods Inc. Logistics Center, providing a significant competitive advantage. It encompasses a wide range of technologies and systems designed to perform tasks with minimal human intervention, enhancing speed, reducing errors, and optimizing resource utilization. This approach supports both cost savings and improved customer satisfaction.
Robotics and Automated Systems
Robotics and automated systems are employed strategically throughout the Lawrence Foods Inc. Logistics Center to enhance productivity and precision. These systems handle repetitive and labor-intensive tasks, freeing up human employees for more complex and value-added activities.
- Automated Guided Vehicles (AGVs): AGVs transport materials and products throughout the warehouse, optimizing the movement of goods between receiving, storage, and shipping areas. For example, AGVs may transport pallets of ingredients from the receiving dock to the designated storage locations within the refrigerated sections, ensuring the proper temperature maintenance of perishable goods.
- Automated Storage and Retrieval Systems (AS/RS): AS/RS are used for high-density storage and retrieval of inventory. These systems utilize automated cranes and shuttles to move pallets or totes into and out of storage locations, minimizing the need for manual handling and maximizing warehouse space utilization. Imagine a scenario where AS/RS swiftly retrieve specific ingredients needed for a batch of ready-to-eat meals, based on real-time production schedules.
- Automated Picking Systems: These systems, including robotic arms and automated picking stations, are used for order fulfillment. Robotic arms can pick individual items from storage locations and place them into shipping containers, reducing picking errors and accelerating the order fulfillment process. Consider a scenario where a robotic arm picks up packages of cookies for an order.
- Automated Sorting Systems: Automated sorting systems utilize conveyors and sorters to direct packages to the correct shipping lanes based on destination. This process ensures efficient and accurate order fulfillment, minimizing the risk of shipping errors.
Integration of Technology with Business Processes
The Lawrence Foods Inc. Logistics Center integrates technology seamlessly with other business processes to create a unified and efficient operational ecosystem. This integration extends beyond warehouse operations, encompassing order management, accounting, and other critical functions.
- Order Management System (OMS) Integration: The OMS is integrated with the warehouse management system (WMS) to automate the order fulfillment process. When an order is placed, it is automatically transmitted to the WMS, triggering the picking, packing, and shipping processes. The OMS also provides real-time visibility into order status, allowing customers to track their orders and providing valuable data for internal analysis.
- Enterprise Resource Planning (ERP) System Integration: The ERP system, which handles accounting, financial management, and other business functions, is integrated with the WMS to streamline data flow and provide a comprehensive view of the entire supply chain. This integration allows for accurate inventory tracking, cost analysis, and performance reporting.
- Transportation Management System (TMS) Integration: The TMS is integrated with the WMS to optimize transportation and logistics operations. The TMS helps to select the most cost-effective shipping methods, track shipments, and manage carrier relationships.
Impact of Technology on Efficiency and Accuracy
The implementation of technology has significantly impacted the efficiency and accuracy of the Lawrence Foods Inc. Logistics Center, leading to measurable improvements in key performance indicators (KPIs). These improvements contribute to better resource utilization, reduced operational costs, and enhanced customer satisfaction.
- Increased Order Fulfillment Speed: Automation reduces the time required to fulfill orders. Robotic picking and packing systems, coupled with optimized warehouse layouts, accelerate the order fulfillment process. Consider a scenario where the order fulfillment time is reduced by 30%, from 24 hours to 16 hours, due to the implementation of robotic systems.
- Reduced Picking Errors: Automated picking systems minimize human error, leading to a significant reduction in picking errors. The use of barcode scanners and other technologies ensures that the correct items are picked and packed for each order. The reduction in picking errors leads to a decrease in the number of returned goods and associated costs.
- Improved Inventory Accuracy: Real-time inventory tracking and automated data capture provide accurate and up-to-date inventory information. This helps to prevent stockouts, reduce overstocking, and optimize inventory levels.
- Enhanced Labor Productivity: Automation frees up human employees to focus on more complex tasks, improving overall labor productivity. Employees can be reassigned to tasks such as quality control, customer service, and strategic planning.
- Cost Reduction: Automation reduces labor costs, minimizes errors, and optimizes resource utilization, resulting in overall cost savings. The reduced operating costs can be passed on to customers or reinvested in the business.
Challenges and Solutions in Logistics
The Lawrence Foods Inc. logistics center, like any complex operation, encounters a variety of challenges. These obstacles, if not addressed effectively, can impact efficiency, costs, and ultimately, customer satisfaction. This section will delve into some of the most significant hurdles faced and the strategies employed to overcome them, focusing on ensuring the smooth flow of goods and the safety of all involved.
Common Logistics Challenges
The logistics center grapples with several recurring challenges that require constant attention and proactive management. These challenges range from external factors like market volatility to internal operational issues.
- Supply Chain Disruptions: Unexpected events, such as natural disasters, geopolitical instability, or supplier issues, can severely disrupt the flow of goods. These disruptions can lead to delays, increased costs, and potential shortages. For example, a major hurricane in a region where a key ingredient is sourced could halt production and distribution.
- Inventory Management Complexity: Maintaining the optimal level of inventory is a constant balancing act. Too much inventory ties up capital and increases storage costs, while too little can lead to stockouts and lost sales. Forecasting demand accurately, managing expiration dates (especially crucial for food products), and optimizing storage space are all critical components.
- Transportation and Delivery Issues: Efficient transportation is vital. This includes challenges such as fluctuating fuel prices, driver shortages, traffic congestion, and the need to maintain the integrity of perishable goods during transit. Delays in delivery can damage customer relationships and lead to financial losses.
- Labor Management: The logistics industry is often labor-intensive. Attracting and retaining a skilled workforce, managing labor costs, and ensuring worker safety are significant ongoing concerns. This is particularly relevant during peak seasons when demand surges.
- Data Management and Visibility: Effectively managing and utilizing the vast amount of data generated within a logistics center is critical. This includes tracking inventory levels, monitoring transportation routes, and analyzing operational performance. A lack of real-time visibility into these areas can hinder decision-making and responsiveness.
Solutions Implemented to Overcome Challenges
Lawrence Foods Inc. has implemented a variety of solutions to address the challenges Artikeld above, focusing on process improvements, technological advancements, and strategic partnerships.
- Supply Chain Resilience Strategies: To mitigate the impact of disruptions, the company has diversified its supplier base, established backup sourcing options, and implemented robust risk management plans. This includes closely monitoring global events and proactively adjusting supply chain strategies. For example, they may pre-position inventory in multiple locations to reduce the impact of a localized disruption.
- Advanced Inventory Management Systems: Implementing sophisticated inventory management software allows for real-time tracking of inventory levels, automated reordering processes, and improved demand forecasting. This reduces the risk of stockouts and minimizes waste due to spoilage. The use of just-in-time inventory management, where applicable, further optimizes inventory levels.
- Optimized Transportation and Logistics Network: The company leverages route optimization software to plan the most efficient delivery routes, minimizing travel time and fuel consumption. They may also partner with multiple transportation providers to ensure flexibility and redundancy. Investing in temperature-controlled transportation is essential for maintaining the quality of perishable goods.
- Labor Optimization and Training Programs: Lawrence Foods Inc. focuses on creating a positive work environment, offering competitive wages and benefits, and investing in comprehensive training programs. This helps to attract and retain skilled workers. Automation, such as automated guided vehicles (AGVs) and robotic picking systems, can also reduce the reliance on manual labor.
- Technology and Data Analytics: The company utilizes warehouse management systems (WMS), transportation management systems (TMS), and business intelligence tools to gain real-time visibility into all aspects of its operations. Data analytics are used to identify trends, optimize processes, and make data-driven decisions. Implementing a robust tracking system provides insights into the entire supply chain.
Measures for Safety and Security
The safety and security of both goods and personnel are paramount at the Lawrence Foods Inc. logistics center. Several measures are in place to ensure a secure and safe working environment.
- Physical Security: The facility is equipped with a comprehensive security system, including surveillance cameras, access control systems, and perimeter security measures. Security personnel are present 24/7 to monitor the facility and respond to any security breaches.
- Food Safety Protocols: Strict food safety protocols are implemented to prevent contamination and ensure the integrity of food products. This includes regular inspections, temperature monitoring, and adherence to stringent hygiene standards. All employees are trained in food safety procedures.
- Worker Safety Programs: Comprehensive worker safety programs are in place to prevent accidents and injuries. This includes providing personal protective equipment (PPE), conducting regular safety training, and implementing ergonomic improvements to workstations. Regular safety audits are conducted to identify and address potential hazards.
- Cybersecurity Measures: The company has implemented robust cybersecurity measures to protect its data and systems from cyber threats. This includes firewalls, intrusion detection systems, and regular security audits. Employee training on cybersecurity best practices is also provided.
- Emergency Preparedness: The logistics center has a comprehensive emergency preparedness plan that Artikels procedures for various scenarios, such as fire, natural disasters, and security breaches. Regular drills are conducted to ensure that all employees are familiar with the plan and can respond effectively in an emergency.
Top 3 Challenges and Solutions:
- Challenge: Supply Chain Disruptions. Solution: Diversified supplier base, backup sourcing, and risk management plans.
- Challenge: Inventory Management Complexity. Solution: Advanced inventory management systems and demand forecasting.
- Challenge: Transportation and Delivery Issues. Solution: Route optimization software and partnerships with multiple transportation providers.
Sustainability and Environmental Practices
Lawrence Foods Inc. is committed to minimizing its environmental impact and promoting sustainable practices throughout its logistics operations. This commitment is reflected in a variety of initiatives designed to reduce waste, conserve resources, and operate in an environmentally responsible manner. These efforts not only benefit the environment but also contribute to the long-term efficiency and cost-effectiveness of the logistics center.
Sustainability Initiatives
Lawrence Foods Inc. has implemented several key sustainability initiatives to reduce its environmental footprint. These initiatives encompass various aspects of the logistics center’s operations, from energy consumption to waste management.
- Energy Efficiency Measures: The logistics center incorporates energy-efficient technologies and practices to reduce its energy consumption. This includes the use of LED lighting throughout the facility, which consumes significantly less energy than traditional lighting. Smart building management systems are also utilized to optimize energy usage based on real-time needs and occupancy. These systems can automatically adjust lighting and temperature settings to conserve energy when areas are unoccupied.
- Waste Reduction and Recycling Programs: A comprehensive waste reduction and recycling program is in place to minimize waste sent to landfills. This includes the separation and recycling of various materials, such as cardboard, plastics, and paper. Lawrence Foods Inc. actively works with recycling partners to ensure that materials are properly processed and reused. Furthermore, the company strives to reduce packaging waste by optimizing packaging designs and sourcing sustainable packaging materials.
- Water Conservation Strategies: Water conservation is another key area of focus. The logistics center utilizes water-efficient fixtures and practices to minimize water usage. This includes the installation of low-flow toilets and faucets, as well as implementing water-wise landscaping practices. The company also monitors water usage regularly to identify areas for improvement and ensure efficient water management.
- Sustainable Transportation Practices: The company is actively exploring and implementing sustainable transportation options. This involves the use of electric vehicles (EVs) for on-site operations, such as forklift trucks and other material handling equipment. Furthermore, Lawrence Foods Inc. is evaluating the feasibility of using alternative fuel vehicles for its transportation fleet. The company also encourages its employees to carpool and use public transportation to reduce emissions.
- Sustainable Sourcing: Lawrence Foods Inc. prioritizes sustainable sourcing practices for its products and materials. This involves working with suppliers who share the company’s commitment to environmental responsibility. The company seeks to source materials from suppliers who utilize sustainable practices, such as using recycled materials and minimizing waste in their own operations.
Certifications and Awards
Lawrence Foods Inc. actively seeks certifications and awards that recognize its commitment to sustainability. These accolades serve as external validation of the company’s environmental efforts and demonstrate its dedication to responsible business practices.
- LEED Certification: The logistics center may be pursuing or have already achieved LEED (Leadership in Energy and Environmental Design) certification. LEED certification is a globally recognized symbol of sustainability achievement and indicates that the facility meets stringent standards for energy efficiency, water conservation, and sustainable site development.
- Industry Awards: Lawrence Foods Inc. may have received industry awards for its sustainability initiatives. These awards recognize the company’s efforts in areas such as waste reduction, energy conservation, and the implementation of sustainable practices. Such recognition showcases the company’s commitment to environmental stewardship and its positive impact on the community.
- Partnerships with Environmental Organizations: The company may have established partnerships with environmental organizations to further its sustainability goals. These partnerships may involve collaborative projects, such as tree planting initiatives or community outreach programs, that support environmental conservation efforts.
Image Description: The Logistics Center – A Sustainable Vision
The image depicts the Lawrence Foods Inc. logistics center as a modern, sustainable facility seamlessly integrated with its environment. The building itself is a large, modern structure with a sleek design. The roof is covered with a vast array of solar panels, angled to maximize sunlight capture and generate renewable energy for the facility.
In the foreground, several electric vehicle (EV) charging stations are visible.
These charging stations are designed to power a fleet of electric vehicles used for on-site operations and potentially for employee use. The charging stations are modern and efficient, contributing to the reduction of carbon emissions.
Surrounding the logistics center is a meticulously planned green landscaping plan. The landscape incorporates native plants and trees, providing natural habitats for local wildlife and contributing to biodiversity.
The landscaping also includes features like rainwater harvesting systems, which collect and reuse rainwater for irrigation and other non-potable uses. The overall effect is a harmonious blend of industrial functionality and environmental responsibility, demonstrating Lawrence Foods Inc.’s commitment to sustainability. The image illustrates a forward-thinking approach to logistics, where environmental considerations are integral to the design and operation of the facility.
Future Trends and Developments
Lawrence Foods Inc. is constantly evaluating the evolving landscape of logistics to ensure it remains at the forefront of efficiency, sustainability, and customer satisfaction. This forward-thinking approach involves anticipating future trends, planning strategic expansions, and embracing cutting-edge technologies. The goal is to create a logistics center that not only meets current demands but is also resilient and adaptable to future challenges and opportunities.
Potential Future Trends in Logistics Impacting Lawrence Foods Inc.
Several key trends are poised to significantly impact Lawrence Foods Inc.’s logistics operations. Understanding and proactively adapting to these trends is crucial for maintaining a competitive edge.
- Increased Automation and Robotics: The adoption of automated guided vehicles (AGVs), automated storage and retrieval systems (AS/RS), and robotic picking and packing will continue to grow, leading to increased efficiency and reduced labor costs. For instance, Amazon’s widespread use of Kiva robots in its fulfillment centers provides a concrete example of this trend.
- Data Analytics and Predictive Modeling: Leveraging big data and advanced analytics to predict demand, optimize routes, and proactively manage potential disruptions will become even more critical. Companies like UPS utilize predictive analytics to forecast package volumes and optimize delivery routes, demonstrating the practical application of this trend.
- E-commerce Growth and Last-Mile Delivery Challenges: The continued expansion of e-commerce will necessitate faster and more efficient last-mile delivery solutions, including exploring options like drone delivery and micro-fulfillment centers. The rapid growth of online grocery shopping, with companies like Instacart and Amazon Fresh, illustrates the increasing importance of efficient last-mile logistics.
- Sustainability and Green Logistics: Growing consumer and regulatory pressure will drive the adoption of sustainable practices, such as using electric vehicles (EVs), optimizing packaging, and reducing carbon emissions. The increasing adoption of EVs in the delivery fleets of companies like FedEx highlights the shift towards green logistics.
- Supply Chain Resilience and Diversification: Building more resilient supply chains by diversifying sourcing, utilizing multiple transportation modes, and investing in risk management strategies will become paramount to mitigate disruptions. The disruptions caused by the COVID-19 pandemic underscored the importance of supply chain resilience.
Planned Expansions, Upgrades, and Technology Implementations
Lawrence Foods Inc. has concrete plans to expand its logistics capabilities and incorporate advanced technologies. These investments are designed to improve operational efficiency, enhance customer service, and minimize environmental impact.
- Warehouse Expansion: Expanding warehouse capacity to accommodate growing order volumes and product lines is a key priority. This will involve adding new square footage to the existing facility.
- Automated Storage and Retrieval System (AS/RS): Implementing an AS/RS will optimize storage space, reduce labor costs, and improve picking accuracy. This system will utilize automated cranes and shelving to store and retrieve inventory.
- Warehouse Management System (WMS) Upgrade: Upgrading the existing WMS to a more advanced platform will enhance real-time inventory tracking, improve order fulfillment accuracy, and provide better visibility across the supply chain. This will include integration with other systems, such as transportation management systems (TMS).
- Electric Vehicle (EV) Fleet: Transitioning to an EV fleet for local deliveries will reduce carbon emissions and lower fuel costs. This initiative will involve procuring electric trucks and establishing charging infrastructure.
- Advanced Analytics Platform: Implementing an advanced analytics platform to analyze supply chain data, predict demand, and optimize operations. This platform will use machine learning algorithms to identify trends and patterns.
Vision for the Future of the Logistics Center
The vision for the future of the Lawrence Foods Inc. Logistics Center is to become a model of efficiency, sustainability, and technological innovation. It’s about creating a smart, agile, and resilient operation that can adapt to changing market conditions and meet the evolving needs of customers. The center will leverage data-driven insights to continuously improve performance, minimize environmental impact, and provide exceptional service.
Future Developments for the Logistics Center
The following table Artikels the planned future developments for the Lawrence Foods Inc. Logistics Center.
Development Area | Description | Timeline | Expected Benefits |
---|---|---|---|
New Technologies | Implementation of AI-powered demand forecasting and route optimization software. | Q4 2024 | Improved forecast accuracy, reduced transportation costs, and optimized delivery times. |
Expansions | Construction of a new 50,000 sq. ft. warehouse expansion, incorporating automated storage and retrieval systems (AS/RS). | Q1 2025 | Increased storage capacity, reduced labor costs, and faster order fulfillment. |
Sustainability Initiatives | Deployment of a solar panel array on the warehouse roof and the purchase of additional electric delivery vehicles. | Ongoing (2024-2026) | Reduced carbon footprint, lower energy costs, and enhanced brand reputation. |
Training Programs | Comprehensive training programs for employees on new technologies and processes, including robotics operation and data analysis. | Continuous | Enhanced employee skills, improved operational efficiency, and increased employee engagement. |
Supply Chain Resilience | Diversification of suppliers and implementation of a multi-modal transportation strategy. | Q2 2025 | Reduced supply chain disruptions and improved delivery reliability. |
Ending Remarks
And so, we come to the end of our journey through the Lawrence Foods Inc. Logistics Center. We have seen the inner workings, the complexities, and the constant striving for improvement. From the initial receiving dock to the final loading bay, the center stands as a testament to the power of efficient supply chain management. It is a place where food finds its way to tables, where innovation meets necessity, and where the future of logistics is constantly being written.
As we depart, the echo of forklifts, the hum of machinery, and the scent of the world’s provisions linger in the air, a reminder of the essential role this center plays in the world, one delivery at a time.