Alright, listen up! We’re diving deep into the world of pet can food lids. Yeah, those little metal or plastic circles that keep your furry friend’s grub fresh. This ain’t just about popping open a can, though. We’re talking about the materials, the design, the safety, and even the environmental impact of these tiny but mighty protectors of your pet’s chow.
From peel-off lids to easy-open tabs, we’ll break down all the different styles and materials, like metal, plastic, and even fancy foil. We’ll also get into the nitty-gritty of how these lids are made, how they keep the food safe, and what you should know about recycling them. Get ready to level up your pet food knowledge!
Types of Pet Can Food Lids
Ah, the humble lid. It’s the unsung hero, the gatekeeper of deliciousness, the silent protector of your furry friend’s feast. Without it, we’d have a chaotic mess of kibble and… well, you get the picture. Let’s dive into the fascinating world of pet food can lids, shall we? We’ll explore the materials, the styles, and the often-overlooked genius that keeps our pets fed and happy.
Lid Materials
The material a lid is made from dictates a lot about its performance. It’s like choosing the right outfit for a grand adventure – gotta pick the one that’ll hold up! Here’s a rundown of the main players:
- Metal: Typically steel, sometimes tin-plated for corrosion resistance. These are the workhorses, the dependable ones. They offer a strong barrier against the outside world.
- Advantages: Excellent sealing properties, robust, widely recyclable (though recycling rates vary by region). Provides a good barrier against oxygen and light, which helps preserve the food.
Cost-effective, particularly in large-scale production.
- Disadvantages: Can be prone to rust if the protective coating is damaged. Requires specialized equipment for opening (e.g., can opener).
- Advantages: Excellent sealing properties, robust, widely recyclable (though recycling rates vary by region). Provides a good barrier against oxygen and light, which helps preserve the food.
- Plastic: Often polypropylene (PP) or polyethylene (PE), chosen for their flexibility and resistance to chemicals. Think of them as the flexible friends, always willing to bend a little.
- Advantages: Can be molded into various shapes, including reclosable lids. Relatively lightweight. Often easier to open than metal lids (e.g., peel-off lids).
- Disadvantages: Can be less effective at sealing than metal, potentially leading to faster food degradation. Recyclability varies greatly depending on the plastic type and local recycling infrastructure. May not provide as good a barrier against oxygen and light.
- Foil: Typically aluminum foil, often laminated to a plastic backing for strength. These are the sensitive souls, protecting the precious cargo within.
- Advantages: Excellent barrier properties against oxygen, light, and moisture. Often used for easy-open lids (peel-off). Lightweight.
- Disadvantages: Can be easily punctured or torn. Recyclability can be complicated due to the mixed materials (foil and plastic). Can be more expensive than metal or plastic.
Lid Styles and Functionality
Beyond the material, the design of the lid plays a crucial role. It’s like the choreography of a dance – each movement has a purpose. Let’s examine some popular styles:
- Peel-off Lids: These are the effortless ones, offering convenience with a simple pull. They’re typically made of foil or a combination of foil and plastic. The lid is sealed to the can body, and a tab allows for easy removal.
- Functionality: Easy to open without a can opener. Provides a good seal to prevent leakage and preserve freshness.
- Example: Many wet cat food cans feature peel-off lids, making feeding time a breeze for busy pet owners.
- Easy-Open (Ring-Pull) Lids: These are the classic heroes, the ones you recognize from countless cans. A ring attached to the lid is pulled to tear open the seal.
- Functionality: Relatively easy to open. Provides a good seal.
- Example: Canned dog food often utilizes this style, offering a balance of convenience and security.
- Reclosable Lids: These are the practical ones, designed for portion control and extended freshness. They can be made from plastic or metal, often with a snap-on or screw-on design.
- Functionality: Allows for multiple servings from a single can. Helps maintain freshness by resealing the can.
- Example: Some larger cans of pet food come with plastic reclosable lids, allowing owners to store the remaining food in the refrigerator.
- Standard Metal Lids (with Can Opener): These are the traditional ones, the OGs of the lid world. They require a can opener to remove.
- Functionality: Provides a very secure seal. Cost-effective.
- Example: Some budget-friendly pet food brands still use this type of lid, emphasizing affordability.
Lid Design and Functionality
The design of pet food can lids is a critical aspect of ensuring product integrity, safety, and consumer convenience. Effective lid design encompasses engineering principles that address sealing, opening, and reclosing mechanisms, all while considering manufacturing efficiency. This section delves into these key elements.
Engineering Principles of Lid Sealing
Effective lid sealing is paramount to prevent leaks, maintain food freshness, and ensure a long shelf life for pet food. This relies on several engineering principles, including material science, pressure dynamics, and precise manufacturing.* The sealing process generally involves the application of pressure to deform the lid and the can body, creating a hermetic seal. The type of seal depends on the can and lid material, but the most common type is the double seam.* Double Seam Formation: This process involves curling the lid and can body together in two operations, creating a secure and airtight seal.
The first operation curls the lid flange and can body together, creating a “first operation seam.”
The second operation presses the curled metal tightly together, forming the final double seam, which is crucial for sealing.
* Pressure and Vacuum: The internal pressure within the can influences the sealing process.
The food is typically heated before sealing, which creates steam and increases internal pressure.
After sealing, the can cools, and the steam condenses, creating a vacuum that helps to maintain the seal and preserve the food.
* Material Selection: The choice of materials, typically steel or aluminum for the can and a food-grade sealant, is critical. The sealant fills any microscopic gaps and ensures an airtight seal.
The primary goal is to create a hermetic seal, which is a seal that is airtight and watertight, preventing any ingress or egress of gases or liquids.
Key Design Features for Easy Opening and Reclosing
The design of pet food can lids incorporates features to facilitate easy opening and reclosing, enhancing consumer convenience and product usability. These features are often a blend of mechanical design and material selection.* Easy-Open Lids: These lids often feature a pull-tab mechanism that allows for easy opening without requiring a can opener. The pull tab is usually attached to a scored or weakened area of the lid, allowing it to be peeled back.
The design of the pull tab is important, considering the ergonomics for different users.
* Reclosable Lids: Some pet food cans incorporate reclosable lids, often made of plastic, to preserve the food after opening.
These lids typically snap onto the can, creating a seal that helps to maintain freshness and prevent odors.
The design of the reclosable lid involves a tight fit to the can’s rim, often using a friction or snap-fit mechanism.
* Material Properties: The materials used in the lid, such as the type of metal, plastic, or sealant, influence the ease of opening and reclosing.
For example, the metal’s thickness and flexibility are important in easy-open lids, while the plastic’s flexibility and resilience are critical for reclosable lids.
Manufacturing Processes for Pet Food Can Lids
The manufacturing of pet food can lids involves several steps, utilizing specialized machinery and processes to ensure quality and consistency.* Material Preparation: The process typically starts with the raw material, which is usually steel or aluminum.
The metal is often coated with a protective layer, such as a lacquer or polymer coating, to prevent corrosion and protect the food from contact with the metal.
* Lid Stamping: The metal is then fed into a stamping press, which uses dies to cut and shape the lid.
This process creates the basic lid shape, including the rim and any features for easy opening.
* Seaming and Curling: If it’s a double-seam lid, the lid is curled to fit the can body, a crucial step for sealing.* Printing and Decoration: The lids are often printed with graphics, branding, and product information.
This can be done using various printing techniques, such as lithography or screen printing.
* Inspection and Quality Control: The manufactured lids undergo rigorous inspection to ensure that they meet quality standards.
This may involve visual inspection, testing for leaks, and measurement of dimensions.
* Machinery Used:
Stamping Presses
Used for cutting and shaping the lids.
Seaming Machines
Used to curl the lid and can body together to create the seal.
Printing Machines
Used to apply graphics and product information.
Coating Machines
Used to apply protective coatings to the metal.
Inspection Equipment
Used to check the quality and dimensions of the lids.
Lid Safety and Regulations
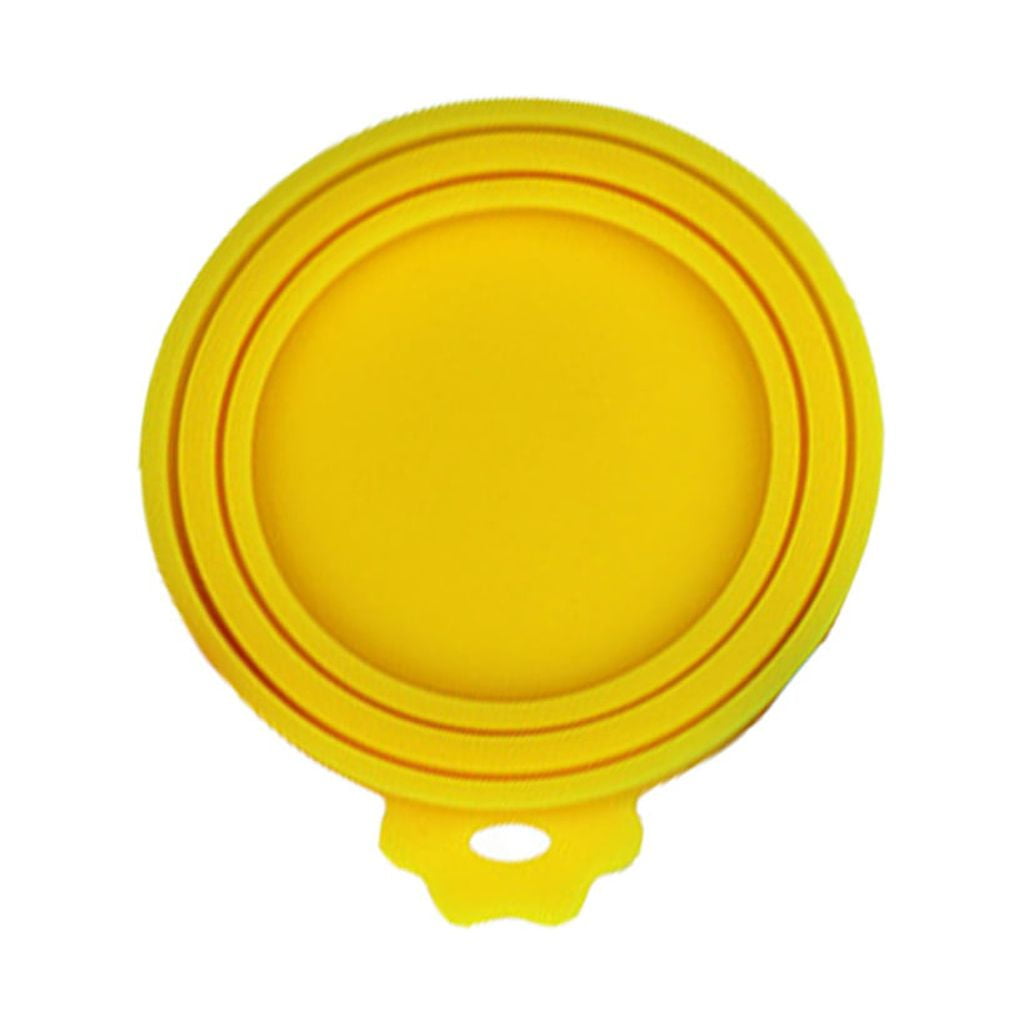
Ah, the humble pet food can lid. It seems so simple, doesn’t it? Just a piece of metal that pops on and off, keeping your furry friend’s dinner fresh. But like all things, there’s a lot more going on behind the scenes than meets the eye, especially when it comes to keeping your beloved companion safe. We’re diving deep into the world of lid safety and the regulations that keep those lids, and your pets, out of harm’s way.
Sharp Edges and Choking Hazards
The quest for a perfect pet food lid, a lid that seals in deliciousness while ensuring your pet’s safety, is a serious one. The devil, as they say, is in the details, and in this case, those details are often found in the sharp edges and the potential for choking.
- The Peril of Sharp Edges: Imagine a lid with a jagged edge. Not a pretty picture, is it? These sharp edges can cause cuts and injuries to both humans and pets during handling. Think about the little paws and noses that might be exploring the discarded can.
- The Choking Menace: The lid itself, or fragments of it, presents a choking hazard. A pet, in its eagerness to get to the tasty food, might accidentally ingest pieces of the lid, leading to a potentially life-threatening situation. This is particularly concerning with smaller pets.
- Mitigation Strategies: Manufacturers employ several strategies to mitigate these risks.
- Rounded Edges: Lids are designed with rounded or smooth edges to minimize the risk of cuts.
- Quality Control: Rigorous quality control processes are in place to identify and remove any lids with imperfections or sharp edges before they reach the consumer.
- Material Selection: The choice of lid material is crucial. Materials that are less prone to splintering or breaking are preferred.
Regulatory Standards and Guidelines for Pet Food Packaging
The pet food industry isn’t a free-for-all. There are rules and regulations in place to ensure that the food and its packaging are safe for your pets. These standards govern everything from the materials used to the labeling requirements.
- Food and Drug Administration (FDA): The FDA plays a crucial role in regulating pet food packaging in the United States. They oversee the safety of the materials used and the labeling of the products.
- Association of American Feed Control Officials (AAFCO): AAFCO is another key player. They develop model regulations for pet food, including guidelines for packaging materials and labeling. While AAFCO doesn’t have the force of law, their recommendations are often adopted by state regulatory agencies.
- Labeling Requirements: Pet food labels must contain specific information, including:
- Product Name and Brand: Clearly identify the product.
- Net Weight: The weight of the food in the can.
- Ingredient List: A list of all ingredients, in descending order by weight.
- Guaranteed Analysis: The minimum percentages of crude protein and crude fat, and the maximum percentages of crude fiber and moisture.
- Manufacturer’s Name and Address: Who made the food.
- Feeding Guidelines: Instructions on how much to feed your pet.
- “Use By” or “Best By” Date: To ensure freshness.
- Packaging Materials: The materials used in pet food packaging must be safe and suitable for contact with food. This means they must not leach harmful chemicals into the food.
BPA and Other Potentially Harmful Substances in Lid Production
The topic of potentially harmful substances in lid production is a sensitive one, especially when considering the health and safety of our pets. The use of Bisphenol A (BPA) and other substances has raised significant concerns.
- BPA’s Past: BPA was commonly used in the production of can linings and some lid coatings to prevent the metal from corroding and to provide a barrier between the food and the metal. However, BPA has been linked to potential health concerns.
- The Controversy: Studies have suggested that BPA can leach from packaging into food, and some studies have raised concerns about its potential effects on hormone disruption.
- Alternatives and Mitigation:
- BPA-Free Alternatives: The pet food industry has largely moved away from BPA in lid production. Manufacturers are increasingly using BPA-free coatings and alternative materials, such as acrylic coatings or epoxy resins.
- Regulations and Consumer Demand: Regulatory pressures and consumer demand for safer products have driven this shift.
- Ongoing Research: Research continues to evaluate the safety of alternative materials and to assess the potential risks of any residual substances.
- Other Concerns: Besides BPA, other substances used in lid production, such as certain solvents or additives, can also pose potential risks. Manufacturers are expected to use materials that are safe for food contact and to adhere to strict safety guidelines.
Impact of Lids on Food Preservation: Pet Can Food Lids
Ah, the humble lid! Often overlooked, yet a silent guardian of your furry friend’s feast. Its role extends far beyond simply keeping the kibble contained. It’s a critical component in preserving the food’s quality, ensuring your pet gets a nutritious and safe meal, bite after delightful bite. Let’s delve into how these little protectors work their magic.
Influence of Lid Design on Shelf Life
The design of a pet food lid, from its material to its sealing mechanism, directly impacts how long the food remains palatable and safe. A well-designed lid acts as a barrier, preventing spoilage and extending the product’s usable life.The effectiveness of a lid in preserving shelf life can be seen in the difference between various lid types:
- Material Matters: Lids made from materials like metal, particularly those with a good sealant, offer superior protection against oxygen and moisture compared to less robust options. Consider the classic can of tuna; its metal lid, sealed with a rubber compound, creates a nearly airtight environment that inhibits bacterial growth and prevents the food from going bad.
- Sealing Strength: The seal itself is paramount. A tight, consistent seal prevents air and contaminants from entering. A poorly sealed can, even with a high-quality lid, will spoil much faster than one with a perfect seal.
- Barrier Properties: The lid’s ability to block external factors is crucial. A lid that blocks light helps to prevent degradation of vitamins and fats.
Role of Lids in Maintaining Nutritional Value
Beyond shelf life, lids play a vital role in safeguarding the nutritional integrity of pet food. They act as a shield against elements that can degrade essential nutrients.The following factors demonstrate how lids preserve food nutrition:
- Preventing Oxidation: Oxygen is the enemy of many nutrients, especially vitamins and fats. Oxidation leads to rancidity and a loss of vitamins. A well-sealed lid minimizes oxygen exposure, preserving these vital components. Imagine opening a bag of chips; within hours, the oils begin to go rancid due to oxidation. A lid on a pet food can, however, slows this process significantly.
- Protecting Against Contamination: Lids prevent external contaminants, such as dust, insects, and other pollutants, from entering the food. This helps to maintain the food’s nutritional value and prevent the introduction of harmful substances.
- Maintaining Moisture Content: Proper sealing also helps maintain the optimal moisture content of the food. Too much or too little moisture can negatively impact the food’s texture, taste, and nutritional stability.
Impact of Proper Lid Sealing on Food Safety
The most critical function of a lid is to ensure food safety. A secure seal is essential for preventing the growth of harmful bacteria and protecting your pet from illness.Here’s how lids contribute to food safety:
- Preventing Bacterial Growth: The airtight seal created by a properly designed and applied lid inhibits the growth of bacteria, such as
-Clostridium botulinum*, which can produce deadly toxins. This is why canned pet food is generally considered safe; the canning process, coupled with a strong seal, eliminates these threats. - Minimizing Contamination Risks: Lids prevent the entry of bacteria, mold, and other microorganisms that can cause food spoilage and pose health risks. This protection is crucial, particularly for wet pet foods, which are more susceptible to microbial growth.
- Ensuring Product Integrity: A robust seal ensures that the food remains intact and prevents leaks, which can attract pests and increase the risk of contamination. This integrity is vital for maintaining food safety throughout the product’s shelf life.
Lid Recycling and Sustainability
Ah, the silent life of the pet food can lid! It seals our furry friends’ meals, a tiny sentinel against spoilage. But its journey doesn’t end at the trash bin. Its ultimate destination, and its impact on our world, is a story we must unravel. This chapter focuses on the lid’s afterlife – its potential for rebirth and the importance of making conscious choices for a greener planet.
Recyclability of Pet Food Can Lid Materials
The materials that form these humble lids dictate their fate in the recycling realm. Some are readily embraced by recycling programs, while others… well, they present a more complex challenge. The following table illuminates the recyclability of common pet food can lid materials, coupled with a nod to the local recycling programs that champion them. Remember, the specifics of what can be recycled vary significantly based on your location.
Always check with your local municipality for the most accurate guidelines.
Material | Recyclability | Common Challenges | Local Program Considerations |
---|---|---|---|
Aluminum | Generally highly recyclable. | May require cleaning to remove food residue. | Most curbside recycling programs accept aluminum cans, including lids. Check if the lid needs to be separated from the can. Some programs may have specific guidelines. |
Steel (Tin-plated Steel) | Also widely recyclable. | Food residue and the presence of coatings can sometimes pose challenges. | Accepted by many recycling programs, often in the same stream as aluminum cans. Confirm if lids need to be separated. Some programs may have different requirements. |
Plastic (e.g., PET, PP) | Recyclability varies significantly based on plastic type and local program capabilities. | Identifying the specific plastic type is crucial. Food contamination can hinder recycling. | Check local guidelines for the specific plastic resin (indicated by a recycling symbol and number). Some programs accept certain types of plastic lids, while others do not. Ensure lids are clean. |
Composite Materials (e.g., Plastic-lined metal) | Generally not recyclable due to the mixed materials. | Separating the different materials is often impossible or economically unfeasible. | Typically, these are not accepted by standard recycling programs. These lids often end up in landfills. |
Methods for Proper Disposal of Pet Food Can Lids
Responsible disposal is the first step towards a sustainable future. Here’s how to bid farewell to those lids with a clear conscience:
- Recycle, Recycle, Recycle: If your local program accepts the lid material, clean it thoroughly to remove food residue. Then, follow the program’s specific instructions for disposal (e.g., separate from the can, place in the recycling bin).
- Check Your Local Guidelines: Recycling rules differ. Always consult your local municipality’s website or call their waste management department to confirm what materials are accepted and any specific preparation requirements.
- Landfill as a Last Resort: If your local program doesn’t accept the lid material, the landfill becomes the unfortunate destination. However, explore alternatives like local recycling centers that may accept a wider range of materials.
- Consider Alternatives: When purchasing pet food, explore brands that use recyclable materials or innovative packaging solutions.
Environmental Impact of Lid Waste and Strategies for Reduction
The environmental footprint of discarded lids, while individually small, accumulates into a significant impact. This impact arises from resource depletion, energy consumption, and the pollution associated with manufacturing, transportation, and disposal. The following strategies aim to mitigate this impact:
- Reduce Consumption: The most impactful strategy is to reduce the number of lids entering the waste stream. Choose pet food brands that offer larger can sizes or those packaged in alternative formats (e.g., pouches) to reduce the frequency of lid disposal.
- Promote Recycling Awareness: Educate yourself and others about the importance of recycling pet food can lids and the proper procedures for doing so. Share information with friends, family, and online communities.
- Support Sustainable Brands: Choose pet food brands that prioritize sustainable packaging. Look for brands that use recycled materials, minimize packaging, or participate in take-back programs.
- Advocate for Improved Recycling Infrastructure: Support policies that promote the development of more comprehensive recycling programs and improved sorting technologies, particularly for challenging materials like composite lids.
- Composting (If Applicable): In some cases, certain lid materials (especially those made of plant-based compostable materials) might be compostable in a home or municipal composting system. Check the lid’s composition and your local composting guidelines.
Innovations in Pet Food Lid Technology
The world of pet food lids is constantly evolving, driven by the desire for enhanced convenience, improved food preservation, and a reduced environmental footprint. Recent technological advancements are transforming how we package and interact with pet food, benefiting both pet owners and the planet.
Smart Lid Integration
Smart lids represent a significant leap forward, incorporating technology to provide pet owners with valuable information and control.
- Real-time freshness monitoring: Some smart lids include sensors that detect changes in food quality, such as temperature fluctuations or gas buildup, indicating spoilage. These sensors can alert pet owners via a smartphone app, preventing the feeding of potentially harmful food. For example, a lid could monitor the oxygen level within the can, triggering an alert if it rises above a certain threshold, signaling a breach in the seal.
- Portion control assistance: Integrated scales within the lid can measure the amount of food dispensed, ensuring accurate portioning and helping to prevent overfeeding. This is especially beneficial for pets with specific dietary needs or those prone to weight gain. A digital display on the lid could show the weight of the food dispensed, along with recommended serving sizes based on the pet’s breed, age, and activity level.
- Inventory management: Smart lids can track the amount of food remaining in a can, providing alerts when it’s time to reorder. This feature can be integrated with online pet food retailers, streamlining the purchasing process. A companion app could even automatically reorder food when the supply runs low, ensuring a consistent food supply.
Innovative Sealing Methods
Beyond smart technology, advancements in sealing methods are also contributing to improved pet food packaging.
- Modified Atmosphere Packaging (MAP): This technique involves altering the gas composition within the can to extend shelf life and preserve food quality. By replacing oxygen with inert gases like nitrogen, MAP inhibits the growth of spoilage microorganisms and reduces oxidation. This results in fresher, more palatable food for pets. For instance, a study demonstrated that pet food packaged with MAP retained higher levels of vitamins and antioxidants compared to food packaged with conventional methods.
- Airtight and Tamper-Evident Seals: These seals provide enhanced protection against contamination and ensure product integrity. They often incorporate features that make it immediately apparent if the lid has been opened or tampered with. These seals are crucial in preventing the introduction of bacteria and maintaining the nutritional value of the food.
- Innovative Materials: The use of new materials is also improving sealing performance. Some manufacturers are experimenting with biodegradable and compostable materials that are both effective at sealing and environmentally friendly.
Potential Benefits for Pet Owners and the Environment
These innovations offer a multitude of benefits.
- For pet owners: Convenience, peace of mind knowing food is fresh, accurate portion control, and reduced food waste.
- For the environment: Reduced food spoilage (less waste in landfills), sustainable materials, and potentially lower transportation emissions due to reduced food waste.
Forecast for Future Trends
The future of pet food lid design and functionality is likely to be characterized by even greater integration of technology and a stronger emphasis on sustainability.
- Personalized Nutrition: Lids may be integrated with systems that can analyze the food’s composition and provide personalized nutritional recommendations for the pet.
- Advanced Material Science: Expect to see the wider adoption of bio-based plastics and compostable materials, reducing reliance on fossil fuels and minimizing environmental impact.
- Data-Driven Packaging: Lids will provide even more data on pet food consumption patterns and food waste, enabling manufacturers and retailers to optimize their products and supply chains.
- Circular Economy: There will be increased emphasis on designing lids that can be easily recycled or repurposed, further promoting a circular economy for pet food packaging.
These trends point to a future where pet food lids are not just containers, but smart, sustainable tools that enhance the pet owner experience and contribute to a healthier planet.
Consumer Experience with Pet Food Lids
Ah, the humble pet food lid! A tiny guardian of kibble and gravy, yet a frequent source of minor daily dramas for pet parents everywhere. From the struggle to pry them open to the frustration of a poorly sealing lid, the consumer experience with these simple closures is often more complex than it appears. This section dives into the world of pet food lids from the consumer’s perspective, exploring common complaints, best practices, and opportunities for improvement.
Common Consumer Complaints Related to Pet Food Can Lids
Let’s face it, not all lid experiences are created equal. Some lids practically leap off the can, while others require a Herculean effort. The following are the most frequent gripes pet owners have with their furry friends’ food lids:
- Difficulty Opening: This is, by far, the most prevalent complaint. Many lids are simply difficult to remove, requiring excessive force, specialized tools, or a good deal of patience. This is especially true for those with arthritis or limited hand strength.
- Sharp Edges: Even when a lid comes off, the edges can be dangerously sharp, posing a risk of cuts to both the consumer and the pet. This is particularly concerning with metal lids.
- Poor Reclosability: Many lids, once opened, are difficult or impossible to reseal effectively. This leads to food spoilage, odor issues, and a general feeling of waste. The need to transfer the food to another container is an added hassle.
- Lid Failure: Occasionally, the lid itself fails, either breaking during opening or detaching completely, making the food inaccessible or potentially dangerous.
- Lack of Clear Labeling: Instructions for opening and reclosing the lid are sometimes unclear or absent, adding to the frustration.
Best Practices for Opening and Handling Pet Food Can Lids Safely and Effectively
Knowing the right techniques can transform the lid-opening experience from a battle to a breeze. Here are some helpful tips for pet owners:
- Use the Right Tool: If you struggle with lids, invest in a good quality can opener specifically designed for pet food. Look for openers with comfortable grips and robust construction.
- Open Away from Yourself: Always open the lid away from your face and body to avoid potential injury from sharp edges or splashing food.
- Inspect the Lid: Before opening, carefully inspect the lid for any damage or defects. Discard the can if the lid appears compromised.
- Wash Your Hands: Thoroughly wash your hands after handling pet food lids, as they may come into contact with bacteria.
- Store Food Properly: If the lid is not reclosable, transfer the remaining food to an airtight container and store it in the refrigerator to maintain freshness and prevent spoilage.
- Consider the Material: Plastic lids, while often easier to open, may not seal as effectively as metal lids. Choose the lid material that best suits your needs and the type of food.
Consumer Feedback on Lid Designs and Functionality
The voice of the consumer is crucial for driving innovation and improvement. Here, pet food companies can gather valuable insights directly from their customers.
Feature | Feedback Options | Example |
---|---|---|
Ease of Opening |
|
“I found the lid very difficult to open. I had to use a can opener, and even then, it was a struggle.” |
Sharpness of Edges |
|
“The edges of the lid were dangerously sharp. I cut myself while trying to open the can.” |
Reclosability |
|
“The lid didn’t reseal properly, and the food dried out quickly.” |
Overall Satisfaction |
|
“I was very dissatisfied with the lid. It was hard to open, and the food spilled everywhere.” |
Additional Comments | Open text field | “I would prefer a lid that is easier to open and reclose, and doesn’t have sharp edges.” |
This feedback could be gathered through surveys, online reviews, or even dedicated feedback sections on product packaging. The information collected would then be used to improve the lid’s design and functionality.
Cost and Production of Pet Food Lids
Ah, the humble pet food lid! Often overlooked, yet a crucial guardian of our furry friends’ meals. Understanding the cost and production intricacies of these lids unveils a fascinating story of materials, manufacturing, and market dynamics. It’s a journey from raw resources to the final, satisfying
thwack* of the lid opening.
Cost Factors in Manufacturing Pet Food Can Lids
The financial landscape of producing pet food lids is a tapestry woven from several key elements. Each thread, from the raw materials to the machinery, contributes to the final price. Let’s delve into the specific components that shape the cost structure.
The following table presents a simplified overview of the cost factors involved in manufacturing pet food can lids. It is important to note that these are general examples, and the actual costs can vary based on factors such as geographic location, supplier relationships, and production volume.
Cost Factor | Description | Example | Percentage of Total Cost (Approximate) |
---|---|---|---|
Materials | The primary expense, encompassing the metal (usually steel or aluminum) and any coatings or sealants. | Steel coils, food-grade epoxy coatings, sealing compounds. | 40-60% |
Labor | Wages for employees involved in all stages of production, from raw material handling to quality control and packaging. | Operators, technicians, quality inspectors, packaging personnel. | 20-30% |
Equipment & Depreciation | Costs associated with the machinery used in the manufacturing process, including stamping presses, coating lines, and inspection equipment, as well as the depreciation of this equipment over time. | Stamping presses, coating lines, inspection systems. | 10-20% |
Overhead & Other Expenses | Encompasses all other associated costs such as utilities, rent, insurance, shipping, marketing, and administrative expenses. | Rent, utilities, insurance, shipping costs, marketing expenses. | 10-20% |
Relationship Between Lid Design Complexity and Production Costs
The more intricate the design, the higher the price. It’s a simple truth, but let’s unpack the nuances of how lid design influences production costs. Consider it like crafting a complex sculpture versus a simple brick.
A complex lid design, requiring multiple steps and specialized equipment, naturally drives up production costs. Conversely, a simpler design can be manufactured more efficiently, reducing expenses. Several design elements significantly impact cost:
- Number of Components: Lids with multiple pieces (e.g., a separate pull tab or a plastic overcap) require more assembly steps, increasing labor and equipment costs.
- Material Complexity: Using specialized materials, such as those with enhanced barrier properties or specific aesthetic finishes, will inevitably raise material costs.
- Precision and Tolerance: Lids demanding tight tolerances in their dimensions necessitate more precise manufacturing processes and quality control measures, adding to the expense.
- Printing and Decoration: Intricate printing, embossing, or other decorative elements require additional equipment and processes, increasing the overall cost. For instance, applying a multi-color design to a lid is considerably more expensive than a single-color print.
For instance, a “peel-off” lid with multiple layers and a complex sealing mechanism is significantly more expensive to produce than a simple, flat lid with a standard pull-tab.
Impact of Economies of Scale on the Price of Pet Food Can Lids
Economies of scale, that beautiful principle where the more you produce, the cheaper it gets per unit, plays a crucial role in the pet food lid industry. It’s a bit like buying in bulk; the per-unit cost decreases as the volume increases.
Larger production runs enable manufacturers to spread their fixed costs (such as equipment setup and administrative expenses) over a greater number of units, thereby reducing the per-unit cost. Here’s how it works:
- Reduced Per-Unit Material Costs: Bulk purchasing of raw materials, like steel or aluminum coils, often results in lower prices from suppliers.
- Efficient Machine Utilization: Running production lines at full capacity minimizes downtime and maximizes output, reducing the cost per lid.
- Lower Labor Costs Per Unit: While total labor costs may increase, the cost per lid decreases as production volume rises.
- Negotiating Power: Larger manufacturers often have more negotiating power with suppliers, allowing them to secure more favorable pricing for materials and services.
Consider a scenario where a lid manufacturer produces 1 million lids per month versus 10 million lids per month. The manufacturer producing 10 million lids will likely have a significantly lower per-unit cost due to the advantages of economies of scale, allowing them to offer more competitive pricing to pet food producers.
Lid Materials and Their Properties
The humble pet food can lid, a seemingly simple disc, is a marvel of material science and engineering. Its performance is critical, ensuring the safety, freshness, and shelf life of the precious contents within. Understanding the specific properties of the materials used is key to appreciating its vital role.
Specific Properties of Lid Materials
The choice of material for a pet food can lid is paramount, and several key properties dictate its effectiveness. These properties work in concert to protect the food from spoilage and contamination.* Tensile Strength: This refers to the material’s ability to withstand pulling forces before breaking. Lids must possess high tensile strength to withstand the pressure exerted during the canning process and the handling during shipping and storage.
For example, a steel lid typically boasts a tensile strength ranging from 276 to 414 MPa (Megapascals), providing the necessary robustness.
Flexibility
A degree of flexibility is essential, particularly for metal lids. This allows the lid to conform slightly to the can’s rim, creating a tight seal. Flexibility also helps the lid absorb impacts without cracking or failing.
Resistance to Corrosion
This is perhaps the most critical property. The lid must resist corrosion from the food contents and the environment. Corrosion can lead to leaks, compromising the food’s safety and allowing spoilage. The coatings and materials are selected to provide excellent corrosion resistance.
Barrier Properties
The lid acts as a barrier, preventing the entry of oxygen, moisture, and microorganisms. This helps maintain the food’s quality and extends its shelf life. Materials like aluminum and steel, combined with protective coatings, excel in this regard.
Formability
The material must be easily shaped into the required lid design. This involves processes like stamping and drawing, which are used to create the lid’s shape and features.
Sealability
The lid must be capable of forming a hermetic (airtight) seal with the can body. This is achieved through the combination of the lid material, the sealing compound, and the seaming process.
Temperature Resistance
Lids must withstand the high temperatures of the sterilization process (typically around 121°C or 250°F) without degradation or compromising the seal.
Impact Resistance
The lid should be able to withstand impacts during handling and transportation without denting or compromising the seal.
Coatings Applied to Metal Lids
To prevent corrosion and ensure food safety, metal lids, particularly those made of steel, are coated with specialized materials. These coatings create a barrier between the metal and the food contents.The coatings commonly applied include:* Epoxy Coatings: These are widely used due to their excellent adhesion, flexibility, and resistance to a broad range of food acids and alkalis.
Epoxy coatings are applied to both the inside and outside of the lid. The inside coating is crucial for preventing the food from directly contacting the metal, while the outside coating protects against environmental factors.
Acrylic Coatings
Acrylic coatings offer good flexibility and resistance to chemicals. They are often used as an alternative to epoxy coatings.
Polyester Coatings
These coatings provide good hardness and scratch resistance. They are often used in conjunction with other coatings to enhance overall performance.
Organosol Coatings
These coatings are solvent-based and offer excellent flexibility and resistance to corrosion. They are commonly used for the exterior of the lid.
Chromium Coatings
While less common now due to environmental concerns, chromium coatings were historically used to enhance corrosion resistance. They often provide a bright, metallic finish.
Tin Plating
A thin layer of tin is applied to steel lids to provide corrosion resistance. This method is less common nowadays due to cost and environmental issues.The choice of coating depends on the specific food being canned, the manufacturing process, and regulatory requirements. For instance, foods with high acidity may require a more robust coating than those with a neutral pH.
Impact of Temperature and Humidity on Lid Performance
Temperature and humidity significantly impact the performance and longevity of pet food can lids. These environmental factors can affect the lid’s ability to maintain a hermetic seal, leading to potential spoilage.* High Temperature: Elevated temperatures can accelerate the degradation of the lid material and the sealing compound. This can lead to a loss of seal integrity, allowing air and contaminants to enter the can.
During storage, excessive heat can cause the food to expand, putting stress on the lid and potentially causing it to fail. For example, if a can of pet food is left in a hot car during summer, the lid could bulge or even burst.
Low Temperature
Extremely low temperatures can cause the lid material to become brittle, making it more susceptible to cracking or damage during handling. The sealing compound may also become less flexible, compromising the seal. While freezing generally does not pose a direct threat to the lid, rapid temperature changes can cause condensation, which can contribute to corrosion.
High Humidity
High humidity can promote corrosion, particularly if the lid’s protective coating is compromised. Moisture can penetrate the coating and react with the metal, leading to rust and eventual failure. Humidity also can affect the adhesive properties of the sealing compound, leading to a weakened seal.
Temperature Fluctuations
Repeated temperature fluctuations can cause the lid to expand and contract, putting stress on the seal. This can lead to fatigue and eventual failure. These fluctuations are especially problematic during transportation and storage in warehouses with varying environmental conditions.To mitigate these effects, pet food manufacturers employ several strategies:* Optimized Coating Selection: Choosing coatings that are resistant to a wide range of temperatures and humidity levels.
Discover more by delving into met food supermarket weekly circular further.
Proper Storage Conditions
Recommending storage in a cool, dry place away from direct sunlight and extreme temperatures.
Quality Control
Implementing rigorous quality control measures to ensure the lids are properly sealed and that the coating is intact.
Material Selection
Utilizing lid materials that are less susceptible to temperature and humidity fluctuations.
Lid Compatibility and Manufacturing Processes
The humble pet food lid, often overlooked, plays a critical role in the overall functionality and consumer experience of canned pet food. Its compatibility with the can, the manufacturing processes used to create it, and the rigorous quality control measures are all intertwined, ensuring both the safety and the integrity of the food within. A poorly designed or manufactured lid can lead to spoilage, consumer dissatisfaction, and even potential health hazards for pets.
Lid Compatibility with Can Sizes and Shapes
Ensuring lids fit a variety of can sizes and shapes is paramount in the pet food industry. This compatibility is not just about aesthetics; it directly impacts the sealing effectiveness and overall shelf life of the product.The following factors influence lid compatibility:
- Can Diameter: The diameter of the can opening must precisely match the lid’s dimensions. Slight variations can compromise the seal, allowing air and contaminants to enter.
- Can Height: While not directly impacting the lid’s seal, the can’s height influences the overall volume of food and, consequently, the lid’s role in preserving the food within that volume.
- Can Shape: While round cans are the most common, some pet food products use rectangular or other specialized shapes. Lids must be designed to accommodate these shapes while maintaining a secure seal. For instance, a rectangular can would require a lid that fits precisely and doesn’t warp under pressure during the sealing process.
- Material Compatibility: The lid material must be compatible with the can material. For example, a steel lid is typically used on steel cans. The materials must interact appropriately during the sealing process to ensure a hermetic seal.
Manufacturing Processes for Different Lid Types, Pet can food lids
The manufacturing processes employed to create pet food lids vary depending on the lid type and the materials used. Each process requires specialized equipment and expertise to ensure the lid meets the necessary performance standards.Here are some common manufacturing processes:
- Stamping: This process is typically used for metal lids. Metal sheets are fed into a stamping machine, where a die cuts and shapes the lid. This is a high-speed, cost-effective method suitable for mass production. The design, including the score lines for easy opening, is incorporated during the stamping process.
- Molding: Plastic lids are often created through injection molding. Molten plastic is injected into a mold, which shapes the lid. This process allows for complex designs and the incorporation of features like pull tabs or reclosable elements. Different types of molds can be used to create various shapes and sizes, as well as different design elements such as logos or text.
- Thermoforming: This process is often used for plastic lids. A plastic sheet is heated and then formed over a mold. Thermoforming is suitable for creating lids with specific contours or features, such as those that are designed to fit snugly over the can’s rim.
- Sealing Processes: After the lid is formed, it is often sealed to the can using a double seam process. This involves rolling the lid and can together to create a secure and airtight seal. The double seam process is a critical step in preserving the food.
Quality Control Measures During Lid Production
Rigorous quality control measures are essential throughout the lid production process to ensure consistency, performance, and safety. These measures help minimize defects and maintain the integrity of the product.Here are some key quality control measures:
- Material Inspection: Raw materials, such as steel sheets or plastic pellets, undergo thorough inspection to ensure they meet the required specifications for thickness, composition, and purity. This inspection helps ensure that the final product meets the necessary performance standards.
- Dimensional Checks: During the manufacturing process, lids are regularly inspected for dimensional accuracy. This includes measuring the diameter, height, and other critical dimensions to ensure they meet the design specifications and will properly fit the cans.
- Seal Integrity Testing: The seal integrity of the lid is tested to ensure it is airtight. This can involve various tests, such as vacuum testing, pressure testing, and leak detection tests. These tests help verify that the lid effectively prevents the entry of air and contaminants.
- Visual Inspection: Lids are visually inspected for defects such as dents, scratches, or imperfections. This helps to identify any issues that could compromise the lid’s performance or appearance.
- Performance Testing: Lids undergo performance testing to evaluate their functionality and durability. This may include tests for opening force, reclosability, and resistance to damage during handling and transportation.
- Coating Adhesion Tests: For metal lids, the adhesion of any coatings, such as lacquers or protective layers, is tested to ensure they remain intact and do not contaminate the food.
The consistency of lid production is not merely about aesthetics; it’s about safeguarding the food within and ensuring the pet’s well-being.
End of Discussion
So, there you have it. From the factory floor to your kitchen counter, we’ve explored the wild world of pet can food lids. They’re more than just a seal; they’re a critical part of keeping our pets happy and healthy. Remember to recycle those lids when you can and stay informed about the latest tech. Peace out!