Seaboard Foods Load Info, the lifeblood of their logistics operations, is a deep dive into how this information is managed, tracked, and utilized. From the moment products leave their origin to their final destination, precise load information is critical. This comprehensive guide explores the intricate details of managing load data, ensuring efficient supply chain management and maximizing operational effectiveness.
We’ll examine the different facets of load information, from the various types of data handled to the systems and processes used to access, track, and analyze it. We’ll also cover how Seaboard Foods ensures data accuracy, security, and integration with other key systems. Furthermore, we’ll delve into common challenges, troubleshooting tips, and future advancements in this vital area.
Overview of Seaboard Foods Load Information
Seaboard Foods relies heavily on the efficient management of load information to ensure the seamless flow of its products from origin to destination. Accurate and readily available data regarding each shipment is critical for optimizing the supply chain and maintaining the quality of the products. This information is crucial for various aspects of the business, from production planning to customer delivery.
Types of Load Information Managed
Seaboard Foods manages a diverse range of load information to track and control its products. This information encompasses several key areas, each playing a vital role in the overall operational efficiency.
- Product Information: This includes detailed data about the products being shipped, such as:
- Product type (e.g., pork bellies, loin, ribs).
- Grade and quality specifications.
- Quantity (e.g., number of cases, weight in pounds or kilograms).
- Packaging details (e.g., type of container, palletization).
- Production date and lot codes for traceability.
- Origin Information: This specifies the source of the product:
- Production facility (e.g., specific processing plant).
- Location of origin (e.g., farm, warehouse).
- Shipping date and time.
- Destination Information: This defines where the product is headed:
- Customer location (e.g., distribution center, retail store).
- Delivery address.
- Expected delivery date and time.
- Transportation Information: This data is critical for tracking the shipment’s journey:
- Carrier information (e.g., trucking company, rail provider).
- Truck or container number.
- Tracking number.
- Shipping route.
Importance of Accurate Load Information
Accurate load information is the backbone of Seaboard Foods’ efficient supply chain. It allows for proactive management of the movement of goods, minimizing delays and ensuring product integrity.
- Supply Chain Optimization: Accurate data enables Seaboard Foods to:
- Optimize transportation routes and schedules, reducing transit times and costs.
- Improve warehouse utilization by predicting arrival times and managing space effectively.
- Enhance communication and collaboration with carriers and customers.
- Quality Control: Detailed information helps maintain product quality:
- Monitoring temperature-controlled shipments to prevent spoilage.
- Ensuring adherence to cold chain protocols.
- Facilitating rapid response to potential issues.
- Regulatory Compliance: Accurate records are crucial for:
- Meeting food safety regulations and traceability requirements.
- Providing proof of origin and handling practices.
- Facilitating product recalls, if necessary.
Load Information and Inventory Management, Seaboard foods load info
Load information is intrinsically linked to effective inventory management at Seaboard Foods. The ability to track products throughout the supply chain provides crucial insights into stock levels, demand, and potential bottlenecks.
- Demand Forecasting: Analyzing historical load data helps predict future demand. For example, if sales of pork ribs consistently increase during the summer months, Seaboard Foods can anticipate this trend and adjust production and shipping accordingly.
- Inventory Visibility: Load information provides real-time visibility into the location and status of inventory. This allows for:
- Proactive management of stock levels.
- Reduced risk of stockouts.
- Minimization of waste due to spoilage.
- Warehouse Optimization: Load data helps optimize warehouse operations by:
- Efficiently allocating storage space.
- Streamlining order fulfillment processes.
- Improving the accuracy of inventory counts.
Accessing Load Information Systems
Accessing load information is crucial for efficient operations at Seaboard Foods, enabling timely delivery, accurate tracking, and effective resource management. Several systems and methods are employed to ensure that relevant data is readily available to authorized personnel. Understanding these systems and access protocols is essential for all employees involved in the logistics and transportation processes.
When investigating detailed guidance, check out brier creek food truck festival now.
Primary Methods for Accessing Load Information
Seaboard Foods utilizes a combination of systems to provide access to load information, catering to the diverse needs of its employees. These systems are designed to be user-friendly and provide real-time updates.
- Web Portals: Dedicated web portals serve as the primary interface for accessing load details. These portals are accessible from any device with an internet connection and provide a centralized location for viewing, searching, and managing load information. They often feature dashboards that display key metrics and alerts.
- Internal Systems: Several internal systems, integrated with the web portals, provide more detailed load information. These systems often manage specific aspects of the logistics process, such as dispatching, route optimization, and inventory management. Access to these systems is typically role-based.
- Mobile Applications: Mobile applications provide real-time access to load information for drivers and field personnel. These apps allow for updates on load status, communication with dispatchers, and documentation of deliveries.
- EDI (Electronic Data Interchange): For larger partners and carriers, Seaboard Foods utilizes EDI to exchange load information. This allows for automated data transfer, reducing manual entry and potential errors.
Step-by-Step Guide for Retrieving Load Details Using the Web Portal
The web portal is the most common system for accessing load information. The following steps Artikel the process for a new user:
- Access the Portal: Open a web browser and navigate to the Seaboard Foods load information portal. The specific URL will be provided upon onboarding.
- Login: Enter your username and password. If you have forgotten your password, use the “Forgot Password” link to reset it.
- Navigate to the Load Search Section: Once logged in, locate the “Load Search” or “Tracking” section of the portal. This section is usually easily accessible from the main menu or dashboard.
- Enter Search Criteria: Use the search filters to find the specific load you are looking for. Common search criteria include:
- Load Number
- Purchase Order Number
- Shipper Name
- Consignee Name
- Delivery Date
- View Load Details: Once you have entered your search criteria, the system will display a list of matching loads. Click on the load number or a similar identifier to view detailed information.
- Review Information: The load details page will provide comprehensive information, including:
- Origin and Destination Addresses
- Shipping Dates and Times
- Commodity and Quantity
- Carrier Information
- Status Updates (e.g., In Transit, Delivered)
- Documents (e.g., Bill of Lading, Proof of Delivery)
- Download Documents (if needed): Some load details pages provide the ability to download associated documents. Click on the appropriate link to download the required documents.
- Log Out: When finished, log out of the portal to protect your account.
User Roles and Access Levels to Load Information
Access to load information is controlled based on user roles, ensuring that employees only have access to the data necessary for their job functions. This approach helps to maintain data security and integrity.
Below are some examples of user roles and their typical access levels:
- Dispatchers: Full access to all load information, including the ability to create, modify, and track loads. They also have access to carrier and driver information.
- Transportation Managers: Access to load information for their respective areas of responsibility. They can generate reports and analyze load performance.
- Drivers: Access to load information related to their assigned loads, including delivery instructions, pickup and delivery times, and communication tools. They typically update load statuses and upload proof of delivery.
- Receiving Personnel: Access to load information related to incoming shipments, including expected delivery times and the contents of the shipment. They often use this information to prepare for unloading and receiving.
- Sales Representatives: Access to load information related to their customers’ shipments, including tracking information and estimated delivery dates. This information helps them to keep customers informed about their orders.
- Finance/Accounting: Access to load information required for invoicing and payment processing, which may include details of the load, carrier, and rates.
Access levels are typically managed through an administrative system, with each role assigned specific permissions to view, edit, and download information. This ensures that the right people have access to the right data, minimizing the risk of data breaches and unauthorized access.
Data Fields and Structure
Understanding the structure of Seaboard Foods’ load information is crucial for efficient tracking, analysis, and management of the supply chain. This section details the key data fields, their formats, and provides a sample data representation. The consistency and accuracy of these data fields are essential for minimizing errors and ensuring smooth operations.
Key Data Fields
The load information records at Seaboard Foods contain a comprehensive set of data fields that describe each shipment.
- Product Code: A unique identifier for the specific product being shipped. This could be a SKU (Stock Keeping Unit) or a similar internal code.
- Product Description: A brief textual description of the product. This helps in quickly identifying the product without needing to reference a separate product catalog.
- Quantity: The amount of the product being shipped, typically measured in units like pounds (lbs), kilograms (kg), or pieces.
- Unit of Measure: Specifies the unit used for the quantity (e.g., lbs, kg, count).
- Load Date: The date the load was created or scheduled.
- Ship Date: The date the load is scheduled to be shipped from the origin location.
- Origin Location: The point of origin for the load, usually a plant or distribution center. This could include the plant’s name, location, or a specific code.
- Destination Location: The final destination for the load, typically a distribution center, customer location, or another processing facility. This also includes location details or codes.
- Expected Delivery Date: The date the load is expected to arrive at the destination location.
- Carrier Information: Details about the transportation carrier, including the carrier’s name and potentially the tracking number.
- Shipping Method: Specifies the method of transportation (e.g., truck, rail).
- Status: Indicates the current status of the load (e.g., created, shipped, in transit, delivered).
Data Formats
Each data field is structured using specific formats to ensure data consistency and accuracy. Proper data formatting is critical for automated data processing and reporting.
- Product Codes: Typically alphanumeric, with a defined length and structure (e.g., “PF-12345-001”).
- Product Descriptions: Free-text fields, but often standardized to ensure consistency.
- Quantity: Numerical values, often with decimal precision (e.g., 1234.56).
- Unit of Measure: Textual abbreviations (e.g., lbs, kg, CT for count).
- Dates: Commonly formatted as YYYY-MM-DD (e.g., 2024-10-27) or MM/DD/YYYY.
- Locations: Textual descriptions, potentially with standardized codes or addresses.
- Carrier Information: Free-text or coded information, depending on the carrier’s systems.
- Shipping Method: Textual, using standardized terms.
- Status: Uses predefined status codes or textual descriptions.
Sample Load Data
The following table illustrates a sample load record, demonstrating how the various data fields are organized and presented. This provides a practical example of the data structure.
Product | Quantity | Destination | Expected Delivery Date |
---|---|---|---|
Pork Loin – 1234 | 2500 lbs | Kansas City DC | 2024-10-29 |
Bacon – 5678 | 1500 lbs | Omaha Retailer | 2024-10-30 |
Sausage – 9101 | 1000 CT | Denver Retailer | 2024-10-31 |
Ham – 1121 | 1800 lbs | Chicago DC | 2024-11-01 |
Load Tracking and Monitoring
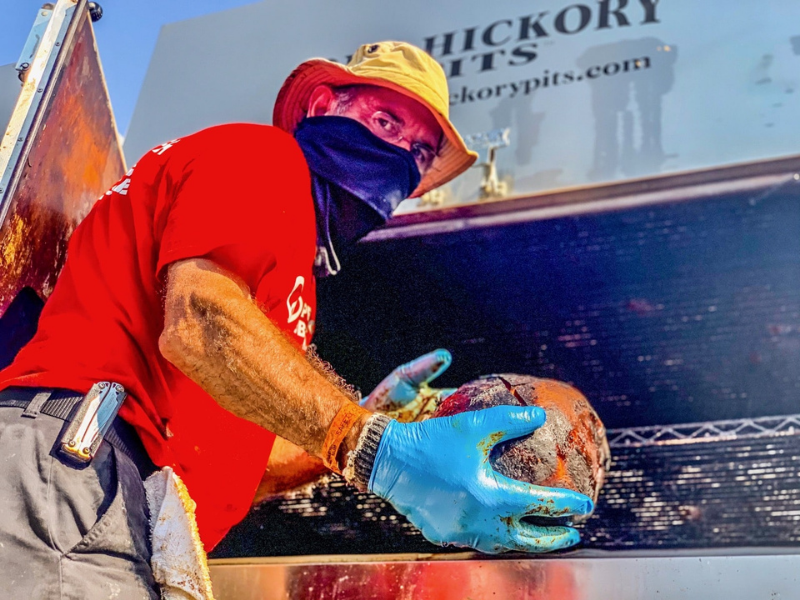
Load tracking and monitoring are critical components of Seaboard Foods’ logistics operations, ensuring the timely and efficient delivery of goods. Real-time visibility into the location and status of each load allows for proactive management, minimizing disruptions and optimizing resource allocation. This section will delve into the specific tools, procedures, and escalation protocols used to track and manage Seaboard Foods loads effectively.
Real-Time Tracking Capabilities
Seaboard Foods utilizes several technologies to provide real-time tracking of its loads. This capability allows for continuous monitoring of a load’s progress from origin to destination.
- GPS Tracking: All Seaboard Foods’ owned and contracted trucks are equipped with GPS tracking devices. These devices transmit location data at regular intervals, providing up-to-the-minute information on the truck’s position. This data is accessible through the company’s transportation management system (TMS).
- Electronic Logging Devices (ELDs): ELDs not only track driving hours as mandated by regulations but also often integrate with GPS systems, providing an additional layer of location data and real-time status updates. This information is automatically fed into the TMS.
- Integration with Carrier Systems: For loads transported by third-party carriers, Seaboard Foods integrates with their systems whenever possible. This integration provides access to the carrier’s tracking data, offering a consolidated view of all loads in transit.
- Temperature and Condition Monitoring: For temperature-sensitive products, such as fresh pork, refrigerated trailers are equipped with sensors that continuously monitor the internal temperature. These sensors transmit data in real-time, alerting dispatchers and stakeholders to any deviations from the required temperature range.
Monitoring Load Progress and Alerts
Seaboard Foods’ TMS provides several mechanisms for monitoring load progress and receiving alerts. These mechanisms help ensure that loads are on schedule and any potential issues are addressed promptly.
- Geofencing: The TMS utilizes geofencing, which involves setting up virtual boundaries around key locations such as origin, destination, and intermediate stops. When a truck enters or exits a geofence, the system automatically triggers an alert.
- Automated ETA Calculations: The system calculates estimated times of arrival (ETAs) based on real-time GPS data, traffic conditions, and planned routes. These ETAs are continuously updated, providing accurate projections of when a load will arrive at its destination.
- Alert Notifications: The TMS is configured to generate alerts for various events, including:
- Delays: If a truck is behind schedule, the system sends an alert to dispatchers and relevant stakeholders.
- Route Deviations: If a truck deviates from its planned route, an alert is triggered.
- Temperature Excursions: For refrigerated loads, alerts are generated if the temperature exceeds or falls below the specified range.
- Unscheduled Stops: Alerts are generated for any stops that were not pre-planned.
- Customizable Dashboards: Users can create customized dashboards within the TMS to monitor specific loads, track key performance indicators (KPIs), and receive real-time updates on load status.
Procedures for Escalating Load Tracking Issues
When issues arise with load tracking, it’s important to have clear escalation procedures in place. These procedures ensure that problems are addressed promptly and efficiently.
- Initial Contact: The first point of contact for load tracking issues is typically the Seaboard Foods’ Transportation Department or the relevant logistics coordinator. They can access the TMS and review the real-time tracking data to assess the situation.
- Information Required: When reporting a load tracking issue, provide the following information:
- Load Number: The unique identifier for the load.
- Truck Number/Carrier Name: The identification of the truck or carrier transporting the load.
- Origin and Destination: The locations of origin and destination.
- Description of the Issue: A clear explanation of the problem, such as a delay, route deviation, or missing tracking data.
- Supporting Documentation: Any relevant documents, such as bills of lading or proof of delivery.
- Escalation Process: If the issue cannot be resolved by the initial contact, the following escalation process is typically followed:
- Level 1: Transportation Department/Logistics Coordinator. They will attempt to resolve the issue by contacting the driver, carrier, or other relevant parties.
- Level 2: Transportation Manager/Senior Logistics Personnel. If the issue persists, it is escalated to the manager level, who can authorize more significant interventions.
- Level 3: Director of Transportation/Supply Chain Management. For critical issues that impact delivery schedules or product quality, the issue is escalated to the highest level of management.
- Communication Protocol: Throughout the escalation process, clear and concise communication is crucial. Regularly update stakeholders on the progress of the issue and any actions taken to resolve it. Document all communication and actions taken in the TMS.
Load Information Integration
Integrating load information within Seaboard Foods is crucial for operational efficiency, data-driven decision-making, and overall supply chain optimization. Seamless integration allows for a holistic view of the movement of goods, from origin to destination, enabling better coordination and resource allocation. This integration facilitates a more responsive and resilient supply chain, capable of adapting to changing market demands and unforeseen disruptions.
Comparison of Load Information Integration with Other Systems
The effective integration of load information with warehousing and transportation management systems is fundamental to Seaboard Foods’ operational success. This integration creates a cohesive data flow that streamlines operations and provides enhanced visibility across the supply chain.
- Warehousing Integration: Integrating load information with warehousing systems, such as Warehouse Management Systems (WMS), provides real-time visibility into inventory levels and storage locations. This integration enables:
- Advanced Shipment Notifications (ASN): Automatically generated ASNs based on load data, informing warehouses about incoming shipments, allowing them to prepare for receiving and storage.
- Inventory Tracking: Accurate tracking of inventory as it moves through the warehouse, from receiving to put-away, storage, and order fulfillment. This minimizes errors and improves inventory accuracy.
- Space Optimization: Better utilization of warehouse space by optimizing the placement of incoming loads based on their dimensions, weight, and storage requirements.
- Cross-Docking Efficiency: Facilitating cross-docking operations by quickly identifying and routing loads that require minimal storage time, improving speed and reducing handling costs.
- Transportation Management Integration: Integrating load information with Transportation Management Systems (TMS) is essential for optimizing transportation planning and execution. This includes:
- Route Optimization: Using load data, such as origin, destination, and delivery requirements, to optimize transportation routes, reducing transit times and fuel costs.
- Carrier Selection: Automated carrier selection based on load characteristics, delivery deadlines, and carrier performance metrics, ensuring the most cost-effective and reliable transportation options.
- Real-Time Tracking: Providing real-time tracking of loads in transit, using GPS data and other tracking technologies, allowing for proactive management of potential delays or issues.
- Freight Cost Analysis: Analyzing freight costs associated with each load, enabling better budgeting and cost control.
Data Utilization for KPI Report Generation
Load data plays a vital role in generating reports on key performance indicators (KPIs) that are critical for evaluating supply chain performance. These KPIs provide actionable insights for continuous improvement and strategic decision-making.
- On-Time Delivery Performance: The percentage of loads delivered within the agreed-upon timeframe.
KPI Calculation: (Number of Loads Delivered On-Time / Total Number of Loads)
– 100This KPI is essential for assessing the reliability of the supply chain and ensuring customer satisfaction. A consistently high on-time delivery rate reflects a well-managed and efficient operation.
- Transportation Cost per Load: The total cost associated with transporting a load, including fuel, labor, and carrier fees.
KPI Calculation: Total Transportation Costs / Total Number of Loads
This KPI is critical for monitoring and controlling transportation expenses. Analyzing this data over time helps identify cost-saving opportunities, such as negotiating better rates with carriers or optimizing routes.
- Warehouse Throughput: The number of loads processed through the warehouse within a specific time period.
KPI Calculation: Number of Loads Processed / Time Period (e.g., per day, per week)
This KPI reflects the efficiency of warehouse operations. Higher throughput indicates improved productivity and the ability to handle a larger volume of goods.
- Inventory Turnover Rate: The frequency with which inventory is sold and replaced over a specific period.
KPI Calculation: Cost of Goods Sold / Average Inventory Value
This KPI measures the efficiency of inventory management. A higher turnover rate generally indicates that inventory is being sold quickly, minimizing storage costs and the risk of obsolescence.
- Load Utilization Rate: The percentage of a trailer’s or container’s capacity that is utilized by a load.
KPI Calculation: (Total Volume or Weight of Goods / Total Capacity of Trailer/Container)
– 100This KPI assesses how effectively transportation resources are being used. High load utilization rates reduce transportation costs per unit and improve overall efficiency. For example, if a trailer with a capacity of 40,000 lbs is transporting a load of 36,000 lbs, the load utilization rate is 90%.
System Design for Automated Data Updates
An automated system for updating the load information database from various sources is crucial for maintaining data accuracy and timeliness. This system should be designed to efficiently collect, process, and integrate data from multiple sources.
- Data Sources: The system must integrate data from various sources, including:
- Warehouse Management Systems (WMS): Providing data on receiving, put-away, storage, and order fulfillment activities.
- Transportation Management Systems (TMS): Providing data on transportation planning, execution, and tracking.
- Enterprise Resource Planning (ERP) Systems: Providing data on order management, inventory levels, and financial transactions.
- Carrier Systems: Providing real-time tracking data and delivery updates.
- IoT Devices: Utilizing data from sensors (e.g., temperature sensors in refrigerated trucks) to monitor the condition of goods during transit.
- Data Transformation and Validation:
- Data Extraction, Transformation, and Loading (ETL): A robust ETL process is necessary to extract data from different sources, transform it into a consistent format, and load it into the load information database.
- Data Validation: Implement data validation rules to ensure the accuracy and integrity of the data. This includes checking for missing values, data type errors, and inconsistencies.
- Data Cleansing: Develop processes to cleanse the data by removing duplicates, correcting errors, and standardizing data formats.
- System Architecture:
- Data Integration Platform: Use a data integration platform (e.g., Informatica, MuleSoft) to manage the data flow and transformations.
- API Integration: Implement APIs (Application Programming Interfaces) to facilitate data exchange between different systems.
- Message Queues: Utilize message queues (e.g., Kafka, RabbitMQ) to handle asynchronous data updates and improve system performance.
- Database Design: Design a relational database (e.g., PostgreSQL, MySQL) or a data warehouse (e.g., Snowflake, Amazon Redshift) to store the load information.
- Automated Updates:
- Scheduled Data Loads: Schedule automated data loads at regular intervals (e.g., hourly, daily) to update the load information database.
- Real-Time Data Streaming: Implement real-time data streaming from certain sources (e.g., carrier tracking systems) to provide up-to-the-minute information.
- Alerting and Notifications: Configure alerts and notifications to notify users of any data integration issues or anomalies.
- Security and Access Control:
- Data Encryption: Encrypt sensitive data to protect it from unauthorized access.
- Access Control: Implement role-based access control to restrict access to data based on user roles and responsibilities.
- Audit Trails: Maintain audit trails to track data changes and user activities.
Common Issues and Troubleshooting
Maintaining accurate and accessible load information is crucial for the smooth operation of Seaboard Foods’ supply chain. However, like any complex system, the load information systems are prone to occasional issues. This section identifies the most common problems encountered, provides troubleshooting steps, and offers answers to frequently asked questions to facilitate quick resolution and prevent disruptions.
Data Entry Errors
Data entry errors are a frequent source of problems in load information systems. These errors can arise from manual input, automated data transfers, or system integrations. Inaccurate data can lead to misallocation of resources, delays, and financial losses.The following are common types of data entry errors:
- Incorrect Product Codes: Entering the wrong product code can lead to the wrong product being loaded, shipped, or invoiced. For example, a typo in the product code (e.g., ‘PORKCHOP’ instead of ‘PORCKOP’) can result in incorrect inventory tracking and order fulfillment.
- Inaccurate Weight or Quantity: Errors in weight or quantity data can impact inventory management, shipping costs, and customer invoicing. For instance, a misreported weight of a pallet can lead to incorrect freight charges.
- Wrong Destination or Origin Information: Incorrectly entered origin or destination information can cause shipments to be routed incorrectly, leading to delays and increased transportation costs. For example, a wrong zip code can result in deliveries to the wrong location.
- Mismatched Dates and Times: Inaccurate dates and times for loading, shipping, or delivery can create discrepancies in tracking and reporting. For example, if the loading date is incorrect, it can throw off the entire timeline of the shipment.
System Glitches and Technical Issues
System glitches and technical issues can disrupt the flow of load information, leading to data loss, system downtime, and operational inefficiencies. These problems can stem from software bugs, hardware failures, or network connectivity problems.Common system glitches include:
- System Crashes: Unexpected system crashes can interrupt data entry, retrieval, and processing, potentially leading to lost data and delays. For example, a server outage during a critical loading period can halt operations.
- Software Bugs: Bugs in the software can cause inaccurate data, system errors, and unexpected behavior. For example, a bug in the load tracking software might prevent updates to the location of a shipment.
- Network Connectivity Issues: Problems with network connectivity can prevent access to load information systems, hindering data synchronization and communication. For example, a disruption in internet service can prevent drivers from updating their load status.
- Integration Failures: Failures in the integration between different systems can lead to data inconsistencies and communication breakdowns. For example, a failure in the integration between the load information system and the accounting system can result in incorrect invoices.
Troubleshooting Data Inconsistencies
When data inconsistencies arise, prompt and effective troubleshooting is essential. The following steps can help resolve these issues:
- Identify the Problem: Clearly define the nature of the data inconsistency. Is it related to product codes, quantities, destinations, or other data fields? Determine the scope of the problem. Is it affecting a single load, or multiple loads?
- Verify Data Sources: Check the original data sources to confirm the accuracy of the information. This may involve reviewing packing slips, purchase orders, shipping documents, and other relevant records.
- Isolate the Cause: Determine the root cause of the inconsistency. Was it a manual data entry error, a system glitch, or an integration issue?
- Correct the Data: Rectify the data errors. Update the affected records with the correct information. Make sure that all related systems are updated as well.
- Implement Preventative Measures: Take steps to prevent similar issues from recurring. This might include improving data entry procedures, implementing data validation checks, or enhancing system monitoring.
- Document the Issue and Resolution: Keep a record of the data inconsistency, the steps taken to resolve it, and any preventative measures implemented. This documentation can be helpful for future troubleshooting and process improvements.
Frequently Asked Questions (FAQs)
Addressing frequently asked questions can provide quick solutions and enhance user understanding of the load information systems. The following FAQs cover common inquiries:
- What should I do if I encounter a data entry error?
- Immediately notify the appropriate personnel (e.g., supervisor, data administrator).
- Provide details about the error, including the load number, data field affected, and the correct information.
- Follow the established procedures for data correction.
- How can I track the status of a shipment?
- Access the load tracking system using your authorized credentials.
- Enter the load number or other relevant tracking information.
- View the shipment’s current status, location, and estimated delivery time.
- What if the load information system is down?
- Contact the IT support team immediately.
- Report the issue and provide any relevant error messages.
- Follow the instructions provided by the IT support team to regain access to the system.
- How can I report a system bug?
- Document the steps you took that led to the bug.
- Note any error messages that appeared.
- Report the bug to the IT support team, providing detailed information.
- Who do I contact for technical support?
- Refer to the company’s internal resources (e.g., help desk, IT support team) for contact information.
- Contact the designated support channel for technical assistance.
Security and Data Integrity: Seaboard Foods Load Info
Maintaining the security and integrity of load information is paramount for Seaboard Foods. This section Artikels the measures taken to protect sensitive data from unauthorized access, ensuring data accuracy, and mitigating potential risks associated with data breaches. Protecting load data safeguards operational efficiency, financial stability, and the company’s reputation.
Security Measures for Load Information
Seaboard Foods employs a multi-layered security approach to protect load information. This approach includes robust access controls, encryption, and regular security audits.
- Access Control: Access to load information systems is strictly controlled through role-based access control (RBAC). Only authorized personnel with specific job functions can access the data relevant to their roles. This limits the potential impact of any security breaches by restricting access to sensitive information. For instance, a warehouse supervisor might have access to real-time tracking data, while a finance team member might have access to load cost information.
- Encryption: All sensitive data, both in transit and at rest, is encrypted. Data in transit, such as data transmitted between different systems or over the internet, is protected using Transport Layer Security (TLS) or Secure Sockets Layer (SSL) protocols. Data at rest, stored in databases and servers, is encrypted using industry-standard encryption algorithms like Advanced Encryption Standard (AES). This protects data even if the storage devices are compromised.
- Authentication and Authorization: Strong authentication methods, including multi-factor authentication (MFA), are implemented to verify user identities before granting access to load information systems. Authorization policies define what actions each user is permitted to perform within the system.
- Firewalls and Intrusion Detection Systems (IDS): Firewalls are deployed to monitor and control network traffic, blocking unauthorized access attempts. IDS are used to detect and alert security personnel to suspicious activities, such as unusual login attempts or data access patterns.
- Regular Security Audits and Penetration Testing: Seaboard Foods conducts regular security audits and penetration testing to identify vulnerabilities in its systems and networks. These audits are performed by both internal security teams and external security firms. The results of these audits are used to remediate identified vulnerabilities and strengthen the security posture.
- Security Awareness Training: Employees are regularly trained on security best practices, including password management, phishing awareness, and data handling procedures. This training helps to reduce the risk of human error, which is a common cause of security breaches.
Data Validation Processes
To ensure the accuracy and integrity of load data, Seaboard Foods employs comprehensive data validation processes. These processes include data cleansing, automated validation checks, and regular data audits.
- Data Cleansing: Data cleansing involves identifying and correcting errors in load data. This includes correcting typos, standardizing formats, and removing duplicate entries.
- Automated Validation Checks: Automated validation checks are implemented at various points in the data entry and processing workflows. These checks verify the data against predefined rules and constraints. For example:
- Range Checks: Ensuring that numerical data, such as weight and quantity, falls within acceptable ranges.
- Format Checks: Validating that data conforms to predefined formats, such as date formats or postal codes.
- Consistency Checks: Ensuring that data is consistent across different data fields. For example, the origin and destination locations of a load should be consistent with the carrier’s information.
- Data Audits: Regular data audits are conducted to verify the accuracy and completeness of load data. These audits involve reviewing a sample of data entries, comparing them against source documents, and identifying any discrepancies.
- Data Backup and Recovery: Regular data backups are performed to ensure that load data can be recovered in the event of a system failure or data loss incident. Backup data is stored in a secure location and is tested regularly to ensure that it can be restored successfully.
Impact of Data Breaches
Data breaches related to load information can have significant negative consequences for Seaboard Foods. The impacts extend beyond financial losses and can severely damage the company’s reputation.
- Financial Loss: Data breaches can result in significant financial losses, including:
- Legal and Regulatory Fines: Failure to protect sensitive data can lead to fines and penalties from regulatory bodies.
- Notification Costs: Companies are often required to notify affected individuals or entities of a data breach, which can be costly.
- Remediation Costs: Remediation efforts, such as incident response, forensic investigations, and system upgrades, can be expensive.
- Lost Revenue: Data breaches can disrupt operations, leading to delays in deliveries, lost sales, and reduced productivity.
- Operational Disruption: A data breach can disrupt operations in several ways:
- Delivery Delays: If load tracking and management systems are compromised, deliveries may be delayed or misdirected.
- Supply Chain Disruptions: A breach could compromise sensitive supply chain data, affecting relationships with carriers, suppliers, and customers.
- System Downtime: Systems may need to be taken offline for investigation and remediation, causing downtime and hindering business operations.
- Reputational Damage: A data breach can severely damage Seaboard Foods’ reputation:
- Loss of Customer Trust: Customers may lose trust in the company if their data is compromised.
- Negative Media Coverage: Data breaches often attract negative media attention, which can damage the company’s brand image.
- Damage to Stakeholder Relationships: Relationships with suppliers, carriers, and other stakeholders may be strained if data breaches compromise their information.
- Competitive Disadvantage: A data breach could expose sensitive competitive information:
- Pricing Data: Competitors could gain access to pricing information, potentially impacting Seaboard Foods’ market share.
- Logistics Strategies: Access to load data could reveal logistics strategies and operational efficiencies, which could be used by competitors to gain an advantage.
Reporting and Analytics
The ability to generate reports and perform analytics is crucial for Seaboard Foods to optimize its logistics operations, improve efficiency, and make data-driven decisions. Load information data provides the foundation for a variety of reports and analyses, offering valuable insights into various aspects of the supply chain. This section will explore the standard reports generated, the analytical tools utilized, and provide an example of data visualization.
Standard Reports Generated from Load Information Data
Standard reports provide a structured overview of key performance indicators (KPIs) and operational metrics. These reports are typically generated on a daily, weekly, or monthly basis, depending on the specific needs of the business.
- Load Volume Reports: These reports track the total number of loads transported over a specific period. They are essential for understanding overall activity and identifying trends in demand. They might also be segmented by origin, destination, or product type.
- On-Time Delivery Reports: These reports measure the percentage of loads delivered within the agreed-upon timeframe. On-time delivery is a critical KPI for customer satisfaction and supply chain efficiency.
- Transportation Cost Reports: These reports provide a breakdown of transportation costs, including fuel, driver wages, and other expenses. They are used to monitor and control transportation expenses. They are also useful for identifying cost-saving opportunities, such as optimizing routes or negotiating better rates with carriers.
- Load Status Reports: These reports provide real-time or near real-time visibility into the status of each load, including its location, estimated time of arrival (ETA), and any delays or issues encountered. They are essential for proactive issue resolution and customer communication.
- Carrier Performance Reports: These reports evaluate the performance of individual carriers based on metrics such as on-time delivery, cost, and damage rates. They are used to manage carrier relationships and ensure that Seaboard Foods is working with reliable and cost-effective partners.
- Damage and Loss Reports: These reports track the number and value of damaged or lost goods. They help identify potential areas for improvement in packaging, handling, and transportation.
Analytical Tools Used to Derive Insights from Load Data
Various analytical tools are employed to extract meaningful insights from load data, supporting data-driven decision-making. These tools enable the identification of trends, patterns, and anomalies that might not be apparent from standard reports alone.
- Business Intelligence (BI) Platforms: BI platforms such as Tableau, Power BI, and Qlik Sense are used to create interactive dashboards and visualizations. They allow users to explore data from various angles and gain a deeper understanding of the business.
- Data Warehousing: Data warehousing solutions consolidate data from multiple sources, including load information systems, into a central repository. This provides a single source of truth for reporting and analysis.
- Statistical Analysis Software: Statistical analysis software, such as R or Python, is used for more advanced analysis, including regression analysis, forecasting, and predictive modeling.
- Geospatial Analysis Tools: Geospatial analysis tools are used to visualize load data on maps, enabling the identification of geographical patterns and the optimization of routes.
- Machine Learning Algorithms: Machine learning algorithms can be used to predict future demand, optimize routes, and identify potential risks in the supply chain. For example, algorithms can predict which routes are most susceptible to delays based on historical data.
Example of a Data Visualization: Load Volume Over Time
To illustrate the power of data visualization, consider a bar chart depicting load volume over a six-month period. This chart can help identify seasonal trends, peak periods, and potential anomalies in load activity.
Description of the Bar Chart: The bar chart displays the total number of loads transported by Seaboard Foods each month from January to June. The X-axis represents the months (January, February, March, April, May, June), and the Y-axis represents the number of loads. Each month is represented by a bar, with the height of the bar corresponding to the total number of loads transported during that month.
The chart provides a clear visual representation of load volume trends over time, allowing for easy identification of fluctuations and patterns. The data is as follows:
Data for the Chart:
- January: 1200 loads
- February: 1150 loads
- March: 1300 loads
- April: 1450 loads
- May: 1600 loads
- June: 1500 loads
Analysis: Based on this data, the load volume generally increased from January to May, with a slight decrease in June. This could indicate a seasonal increase in demand during the spring and early summer months. The data visualization allows for a quick understanding of these trends, enabling proactive planning and resource allocation.
Load Information for Specific Products
Seaboard Foods’ commitment to quality and safety necessitates a sophisticated approach to load information, particularly when handling diverse product types. The requirements for tracking and managing loads differ significantly based on the nature of the goods being transported. This section explores the specific load information protocols for various product categories, emphasizing the crucial role of data accuracy in maintaining product integrity and regulatory compliance.
Perishable Goods Versus Non-Perishable Goods Requirements
The handling of perishable goods, such as pork products, demands significantly more stringent load information protocols compared to non-perishable items. These differences are primarily driven by the need to maintain product quality, safety, and compliance with food safety regulations.
- Temperature Monitoring and Control: Perishable goods require continuous temperature monitoring throughout the transportation process. This includes:
- Real-time temperature sensors within the refrigerated trailers.
- Automated alerts triggered by temperature deviations outside the acceptable range.
- Detailed records of temperature readings at various points in the journey (loading, transit, unloading).
Non-perishable goods, while potentially requiring some environmental control, are less sensitive to temperature fluctuations.
- Transportation Time and Routing: Perishable goods have a limited shelf life, necessitating optimized transportation routes and schedules.
- Load information includes precise delivery deadlines.
- Real-time tracking to ensure on-time delivery.
- Contingency plans for potential delays, such as rerouting or expedited shipping.
Non-perishable goods have greater flexibility in terms of transportation time.
- Sanitation and Hygiene Protocols: Perishable goods require stringent sanitation and hygiene protocols for trailers and handling equipment.
- Pre-trip inspections to ensure cleanliness.
- Regular cleaning and sanitization of trailers between loads.
- Documentation of cleaning and sanitization activities within the load information system.
Non-perishable goods may have less rigorous sanitation requirements.
- Product Handling Instructions: Perishable goods require specific handling instructions to maintain product quality.
- Detailed loading and unloading procedures.
- Guidelines for stacking and securing products.
- Information on proper storage conditions.
Non-perishable goods may have simpler handling instructions.
Handling of Load Information for Temperature-Controlled Shipments
Temperature-controlled shipments are a critical component of Seaboard Foods’ logistics, particularly for maintaining the quality and safety of perishable pork products. The load information system plays a central role in managing and monitoring these shipments.
- Real-time Temperature Monitoring Systems: The system integrates with temperature sensors embedded within refrigerated trailers. These sensors continuously transmit temperature data to the central system. The system also tracks humidity levels when required.
- Alerting and Notification: The system automatically generates alerts if the temperature deviates from the pre-defined acceptable range. These alerts are sent to relevant personnel, including dispatchers, drivers, and quality control staff.
- Temperature Data Logging and Reporting: The system logs temperature data at regular intervals throughout the journey. This data is used to generate detailed temperature reports for each shipment. The reports are essential for compliance with food safety regulations and for investigating any potential quality issues.
- Trailer Pre-Cooling Verification: Load information includes verification that the refrigerated trailer has been pre-cooled to the appropriate temperature before loading. This verification ensures that the products are loaded into a suitable environment.
- Load Planning and Route Optimization: The load information system is integrated with route planning software to optimize routes and minimize transit times. This is particularly important for temperature-controlled shipments to reduce the risk of temperature excursions.
- Compliance with Food Safety Regulations: Temperature data is stored securely and is readily available for audits and inspections. The system helps ensure compliance with regulations like the Food Safety Modernization Act (FSMA).
Specific Load Information for Traceability and Food Safety
Traceability and food safety are paramount at Seaboard Foods. The load information system is designed to provide comprehensive traceability for all products, enabling rapid identification and isolation of any potential food safety issues.
- Lot Code Tracking: Each product is assigned a unique lot code, which is linked to all relevant load information. This allows for precise tracking of the product’s origin, processing date, and destination.
- Production Information: Load information includes data on the production facility, processing date, and any relevant quality control checks performed during production.
- Ingredient Information: For processed products, the system tracks the ingredients used, including supplier information and lot codes.
- Shipping and Receiving Documentation: The system generates and stores shipping and receiving documentation, including bills of lading, packing lists, and inspection reports.
- Chain of Custody: The system maintains a complete chain of custody, documenting the movement of products from origin to destination. This includes information on each handler, the time of transfer, and the condition of the product.
- Recall Management: In the event of a recall, the load information system can be used to quickly identify and locate affected products. The system can then generate a list of customers who received the product, enabling prompt notification and removal of the product from the market.
Example: If a specific lot of pork chops is identified as having a potential contamination issue, the system can immediately pinpoint all shipments containing that lot, the delivery locations, and the customer contact information. This enables a rapid and targeted recall, minimizing the impact on consumers and the business.
- Auditing and Compliance: The system supports regular audits and ensures compliance with food safety regulations. All load information is readily available for inspection by regulatory agencies.
Future Trends and Improvements
The landscape of load information management is constantly evolving, driven by technological advancements and the need for greater efficiency and transparency. Anticipating and adapting to these trends is crucial for Seaboard Foods to maintain a competitive edge and optimize its operations. This section explores potential future advancements, suggests improvements for current systems, and Artikels features to enhance user experience and data efficiency.
Potential Future Advancements in Load Information Management
The future of load information management promises significant advancements, leveraging technologies to create more intelligent, responsive, and interconnected systems. These advancements will likely revolve around enhanced data analytics, automation, and real-time visibility.
- Artificial Intelligence (AI) and Machine Learning (ML): AI and ML algorithms can analyze vast datasets to predict potential disruptions, optimize routing, and identify inefficiencies. For example, predictive maintenance algorithms could analyze sensor data from refrigerated trailers to anticipate equipment failures, preventing spoilage and delays. AI could also be used to automate tasks such as load planning and documentation, reducing human error and improving speed. Consider the potential to forecast demand based on historical sales data, weather patterns, and market trends, optimizing load scheduling and reducing waste.
- Blockchain Technology: Blockchain can enhance transparency and security in the supply chain by providing an immutable record of each load’s journey. This technology can track a product from origin to destination, verifying its authenticity and preventing tampering. Each transaction is recorded in a distributed ledger, making it difficult to alter or manipulate data. This is especially crucial for ensuring the integrity of perishable goods and verifying compliance with food safety regulations.
- Internet of Things (IoT) Integration: The increasing adoption of IoT devices, such as sensors in trailers, will provide real-time data on temperature, location, and other critical factors. This data can be used to monitor the condition of goods throughout the transportation process, ensuring that products are delivered in optimal condition. The integration of IoT will provide unprecedented visibility into the supply chain, allowing for proactive intervention and improved decision-making.
For example, real-time temperature monitoring can alert dispatchers to a malfunctioning refrigeration unit, allowing them to reroute the load or make repairs before spoilage occurs.
- Autonomous Vehicles and Drones: The development of autonomous vehicles and drones could revolutionize load transportation. Autonomous trucks could handle long-haul routes, reducing labor costs and improving efficiency. Drones could be used for last-mile delivery, especially in areas with difficult terrain. These technologies could significantly impact delivery times and costs, but also introduce new challenges related to safety and infrastructure.
- Enhanced Data Analytics and Visualization: More sophisticated data analytics tools will be essential for extracting actionable insights from the growing volume of load information. Advanced visualization techniques, such as interactive dashboards and heatmaps, will enable users to quickly identify trends, patterns, and anomalies. This will allow for data-driven decision-making and improved operational performance. The ability to track key performance indicators (KPIs) in real-time and identify areas for improvement will become increasingly important.
Suggestions for Improving Current Load Information Systems at Seaboard Foods
Improving current systems involves addressing existing pain points and leveraging available technologies to enhance functionality, user experience, and data integrity. These suggestions are focused on incremental improvements that can be implemented relatively quickly.
- Enhanced Integration with Existing Systems: Seamless integration between load information systems and other internal systems, such as Enterprise Resource Planning (ERP) and Warehouse Management Systems (WMS), is essential. This integration will streamline data flow, reduce manual data entry, and improve data accuracy. Consider developing APIs (Application Programming Interfaces) to facilitate data exchange between different systems.
- Mobile Accessibility: Providing mobile access to load information systems will empower employees to access critical data from anywhere, at any time. This is especially important for drivers, dispatchers, and warehouse personnel who need real-time information on the go. Mobile applications can provide access to load details, tracking information, and communication tools.
- Improved User Interface (UI) and User Experience (UX): A user-friendly interface is crucial for ensuring that employees can easily access and understand the information they need. The UI should be intuitive and easy to navigate, with clear visual cues and customizable dashboards. Regular user feedback should be collected and incorporated into UI/UX design updates.
- Automated Reporting and Alerts: Implementing automated reporting and alert systems will help identify and address potential issues proactively. The system should generate reports on key performance indicators (KPIs), such as on-time delivery rates, fuel consumption, and trailer utilization. Alerts should be triggered when critical events occur, such as temperature deviations or delays.
- Enhanced Data Validation and Error Handling: Robust data validation and error handling mechanisms are essential for ensuring data accuracy. The system should automatically validate data entered by users and flag any errors or inconsistencies. Implementing data quality checks will help prevent incorrect information from propagating throughout the system.
Features to Enhance User Experience and Data Efficiency
Adding new features to the system will improve the user experience and increase the efficiency of operations. These features are designed to provide more comprehensive data and enhance the usability of the system.
- Real-time Tracking and Tracing: Implement a real-time tracking and tracing system that provides up-to-the-minute information on the location and status of each load. This can be achieved through GPS tracking, sensor data, and integration with carrier systems. Users should be able to view the location of their loads on a map and receive alerts when a load deviates from its planned route or schedule.
- Predictive ETA (Estimated Time of Arrival): Develop an algorithm that predicts the estimated time of arrival (ETA) for each load, taking into account factors such as traffic, weather, and road conditions. This will allow for more accurate planning and scheduling. The ETA should be regularly updated based on real-time data.
- Interactive Dashboards and Reporting: Create interactive dashboards that provide users with a visual overview of key performance indicators (KPIs) and other relevant data. Users should be able to customize the dashboards to display the information that is most important to them. Reporting tools should allow users to generate custom reports and analyze data trends.
- Advanced Search and Filtering: Implement advanced search and filtering capabilities that allow users to quickly find the information they need. Users should be able to search by multiple criteria, such as load number, product, origin, destination, and date range. The system should also support advanced filtering options, such as filtering by status or location.
- Collaboration and Communication Tools: Integrate collaboration and communication tools that allow users to easily communicate with each other and with external partners, such as carriers and customers. This could include features such as instant messaging, email notifications, and document sharing. These tools should streamline communication and improve coordination.
- Integration with Customer Portals: Integrate load information with customer portals to provide customers with real-time access to the status of their orders. Customers should be able to track their shipments, view estimated delivery times, and receive notifications about any delays or changes. This will improve customer satisfaction and build trust.
Epilogue
In conclusion, Seaboard Foods Load Info plays a pivotal role in the company’s success. By understanding the intricacies of load data management, from its initial capture to its final analysis, Seaboard Foods can optimize its supply chain, improve operational efficiency, and ensure the delivery of high-quality products. The continuous refinement of these processes, along with embracing future technological advancements, will solidify Seaboard Foods’ position as a leader in the food industry.