Small batch dog food recall is a critical issue that demands attention from every pet owner. This guide delves into the specifics of these recalls, which, unlike those from massive corporations, often affect niche brands and specialized formulas. Understanding the nuances of small batch production, the common triggers for recalls, and the agencies involved is the first step in safeguarding your furry friend’s health.
We’ll explore the reasons behind these recalls, ranging from bacterial contamination and mold to undeclared ingredients, and the impact they have on our canine companions. This comprehensive guide covers everything from identifying affected products and recognizing potential health risks to navigating the recall process and taking preventative measures. We’ll also examine how manufacturers and regulatory bodies respond to these situations, emphasizing the importance of transparency and consumer safety.
Overview of the ‘Small Batch Dog Food Recall’
Dog food recalls, even those affecting “small batch” producers, are serious events. They highlight the critical importance of food safety for our canine companions. Understanding the nuances of these recalls, including their causes, scope, and the regulatory landscape, is essential for responsible pet ownership. This information helps owners make informed decisions and protect their dogs from potential health risks.
Defining a “Small Batch” Dog Food Recall
A “small batch” dog food recall differs significantly from those issued by large, national or multinational manufacturers. These recalls typically involve products produced in limited quantities, often with a focus on specific ingredients or recipes.The contrast lies in several key areas:* Production Volume: Small batch producers operate on a smaller scale. This means they produce and distribute far fewer units of food compared to larger companies.
A recall, therefore, affects a smaller geographic area and fewer dogs, statistically.
Distribution Network
Small batch brands frequently rely on direct sales, local pet stores, and online retailers with a more limited reach. Larger manufacturers have extensive distribution networks, including national chain stores, potentially exposing a recall to a much broader consumer base.
Manufacturing Processes
Small batch operations might utilize more hands-on, less automated manufacturing processes. While this can sometimes allow for greater control over ingredient sourcing and quality, it can also increase the risk of human error or contamination if proper protocols are not strictly followed. Larger manufacturers often have highly automated systems designed to minimize these risks.
Traceability
Due to the smaller scale, small batch producers might have an easier time tracing the source of a problem ingredient or batch. This can lead to more targeted recalls. However, they might lack the sophisticated tracking systems employed by larger companies, making it harder to pinpoint the exact affected products.
Reasons for Small Batch Dog Food Recalls
Several factors commonly trigger recalls for small batch dog food. These reasons often mirror those affecting larger manufacturers, but the scale and specific circumstances can vary.Common causes include:* Contamination with Harmful Bacteria: This is a significant concern, with
- Salmonella*,
- Listeria monocytogenes*, and
- E. coli* being among the most frequently cited culprits. These bacteria can cause serious illness in dogs, ranging from mild gastrointestinal upset to severe, life-threatening infections.
- Salmonella* is often associated with raw or undercooked ingredients. Symptoms can include vomiting, diarrhea, fever, and lethargy.
- Listeria monocytogenes* can cause listeriosis, a serious infection that can affect the nervous system.
- E. coli* contamination can lead to bloody diarrhea and kidney failure.
Presence of Toxins
Aflatoxins, produced by molds that can grow on grains, are a common concern. These toxins can cause liver damage. Mycotoxins, in general, can be present in grains and other ingredients if not properly stored.
Ingredient Issues
Mislabeling or Undeclared Ingredients
This can be due to accidental inclusion of ingredients not listed on the label, or a deliberate omission. This is a problem for dogs with allergies or sensitivities.
Contamination with Foreign Objects
Small pieces of plastic, metal, or other foreign materials can find their way into the food during processing.
Ingredient Sourcing Problems
The quality of ingredients is critical. If a supplier provides contaminated or substandard ingredients, it can lead to a recall.
Manufacturing Errors
Mistakes during the manufacturing process can also trigger recalls.
Incorrect Formulation
Using the wrong proportions of ingredients can lead to nutritional imbalances or the presence of harmful substances.
Packaging Problems
Faulty packaging can lead to contamination or spoilage.
Regulatory Violations
Failure to Meet Nutritional Standards
Dog food must meet specific nutritional requirements set by organizations like the Association of American Feed Control Officials (AAFCO).
Improper Labeling
Incorrect or misleading labeling can lead to recalls.
Regulatory Bodies and Agencies Involved
Several regulatory bodies and agencies play a role in overseeing and announcing dog food recalls, including those involving small batch producers.Key players include:* The Food and Drug Administration (FDA): The FDA is the primary federal agency responsible for regulating pet food in the United States. The FDA’s Center for Veterinary Medicine (CVM) monitors the pet food industry, investigates reports of problems, and issues recalls when necessary.
The FDA can inspect pet food manufacturing facilities and take enforcement actions against companies that violate regulations. The FDA also maintains a database of recalls.
State Departments of Agriculture
State agencies often work in collaboration with the FDA, particularly in the inspection and monitoring of pet food facilities within their jurisdictions. They may also issue recalls based on their own findings or in coordination with the FDA.
Find out about how changezi food mart can deliver the best answers for your issues.
The Association of American Feed Control Officials (AAFCO)
AAFCO is a voluntary membership association of state and federal officials. AAFCO develops model regulations and standards for animal feed, including pet food. While AAFCO itself doesn’t have enforcement power, its guidelines are widely adopted by state and federal regulatory agencies. AAFCO’s work is critical for establishing nutritional standards and ingredient definitions.
The Pet Food Industry
While not a regulatory body, the pet food industry itself plays a role in recalls. Manufacturers are responsible for ensuring the safety of their products and initiating recalls when necessary. The Pet Food Institute (PFI) is a trade association that represents pet food manufacturers and works to promote pet food safety and quality.
Identifying Affected Products
Navigating a dog food recall can be stressful, but understanding how to identify potentially affected products is crucial for your dog’s safety. This involves recognizing common product types susceptible to recalls, deciphering product labels, and knowing where to find reliable information.
Common Product Types
Several types of dog food products are frequently subject to recall, often due to manufacturing issues or contamination concerns.
- Dry Food: Kibble is a staple in many dogs’ diets. Recalls of dry food can stem from various problems, including bacterial contamination (like Salmonella), mold growth, or the presence of foreign objects. For instance, in 2021, several brands recalled dry food due to elevated levels of Vitamin D, leading to potential health complications in dogs.
- Wet Food: Canned or pouched wet food is another common category. Recalls in this area often relate to issues with packaging integrity (leading to spoilage), contamination, or formulation errors. A notable example includes recalls due to the presence of pentobarbital, a euthanasia drug, found in some canned dog food products.
- Treats: Dog treats, ranging from biscuits to chews, are also prone to recalls. These can be recalled for similar reasons as dry food, including contamination, undeclared ingredients, or issues with manufacturing processes.
- Raw Food: Raw food diets, which are becoming increasingly popular, present unique challenges. Recalls in this area are often related to bacterial contamination (like E. coli or Salmonella) due to the nature of the product.
Product Label Information
Understanding the information on a dog food label is essential to identify if a product is part of a recall. Recalled products typically have specific identifiers that consumers should check.
- Brand Name and Product Name: The brand name and specific product name are the primary identifiers. Recalls usually target specific products, not entire brands.
- Lot Code or Lot Number: This is a crucial piece of information. The lot code is a unique identifier assigned to a batch of food produced at a specific time. Recalls often specify which lot codes are affected.
- Best-By Date or Expiration Date: This date helps determine if your product falls within the recall timeframe.
- UPC Code: The Universal Product Code (UPC) can also be included in recall notices.
- Manufacturing Date: The date the product was manufactured may be provided in the recall notice.
Confirming Recall Information
Verifying if a specific product is part of a recall requires checking reliable sources.
- The Manufacturer’s Website: Most manufacturers will post recall information on their official website. This is often the first place to check.
- The Food and Drug Administration (FDA): The FDA maintains a database of pet food recalls. You can search by brand name, product name, or other identifiers.
- The Association of American Feed Control Officials (AAFCO): AAFCO often provides information on recalls.
- Pet Food Retailers: Many pet food retailers will post recall notices in their stores or on their websites.
- Local Veterinarian: Veterinarians are often informed of recalls and can provide guidance.
Common Causes of Recalls: Small Batch Dog Food Recall
Understanding why dog food is recalled is crucial for pet owners. Recalls happen for a variety of reasons, stemming from issues during ingredient sourcing, manufacturing, or packaging. These issues can pose significant health risks to dogs. Being informed about the common culprits helps pet owners make safer choices.
Frequent Contaminants and Issues
The most frequent causes of small batch dog food recalls are typically related to contamination or ingredient problems. These issues can arise at any stage of the production process, from the raw materials to the final product.
- Bacterial Contamination: This is a significant concern. Common culprits include Salmonella, Listeria monocytogenes, and E. coli. These bacteria can cause severe gastrointestinal distress, including vomiting, diarrhea, and in severe cases, sepsis. Recalls due to bacterial contamination are often widespread because the contamination can affect multiple batches.
- Mold and Mycotoxins: Mold growth, particularly in stored grains or ingredients, can produce mycotoxins. Aflatoxins are a type of mycotoxin that is particularly dangerous, as they can cause liver damage and even cancer. Regular testing of ingredients and finished products is essential to prevent this.
- Presence of Foreign Objects: This can range from small pieces of plastic or metal to other materials that shouldn’t be present in the food. While not always as immediately life-threatening as bacterial contamination, these objects can cause internal injuries.
- Incorrect Ingredient Ratios or Nutritional Imbalances: Small batch producers, while often focused on quality, can sometimes make errors in formulation. This can lead to foods that are deficient or excessive in certain nutrients, potentially causing long-term health problems.
- Chemical Contamination: This may involve the presence of pesticides, herbicides, or other chemicals that have been introduced during the growing or processing of ingredients.
Impact Comparison: Bacterial vs. Other Contaminants
The impact of different contaminants varies. Bacterial contamination often leads to acute, rapidly developing symptoms. Other contaminants might have more chronic, long-term effects.
Bacterial contamination, such as Salmonella, often presents with immediate and noticeable symptoms like vomiting and diarrhea. In contrast, mycotoxin exposure might lead to gradual liver damage.
Potential Health Effects
The table below Artikels potential health effects associated with various recall causes.
Recall Cause | Potential Health Effects | Severity | Example |
---|---|---|---|
Salmonella (Bacterial) | Vomiting, diarrhea, fever, lethargy, loss of appetite | High (can be fatal) | A 2018 recall affected multiple brands and caused widespread illness. |
Aflatoxins (Mycotoxins) | Liver damage, jaundice, loss of appetite, lethargy, cancer (long-term) | High (can be fatal) | In 2005, a large-scale recall involved many brands due to aflatoxin contamination in corn. |
Foreign Objects (e.g., plastic) | Choking, internal injuries, gastrointestinal obstruction | Variable (can be life-threatening) | A 2022 recall involved sharp plastic pieces. |
Nutritional Imbalances | Deficiencies or excesses of certain nutrients, leading to various health problems depending on the specific imbalance. | Variable (depends on the specific imbalance) | A deficiency in vitamin D can lead to bone problems. |
Impact on Consumers
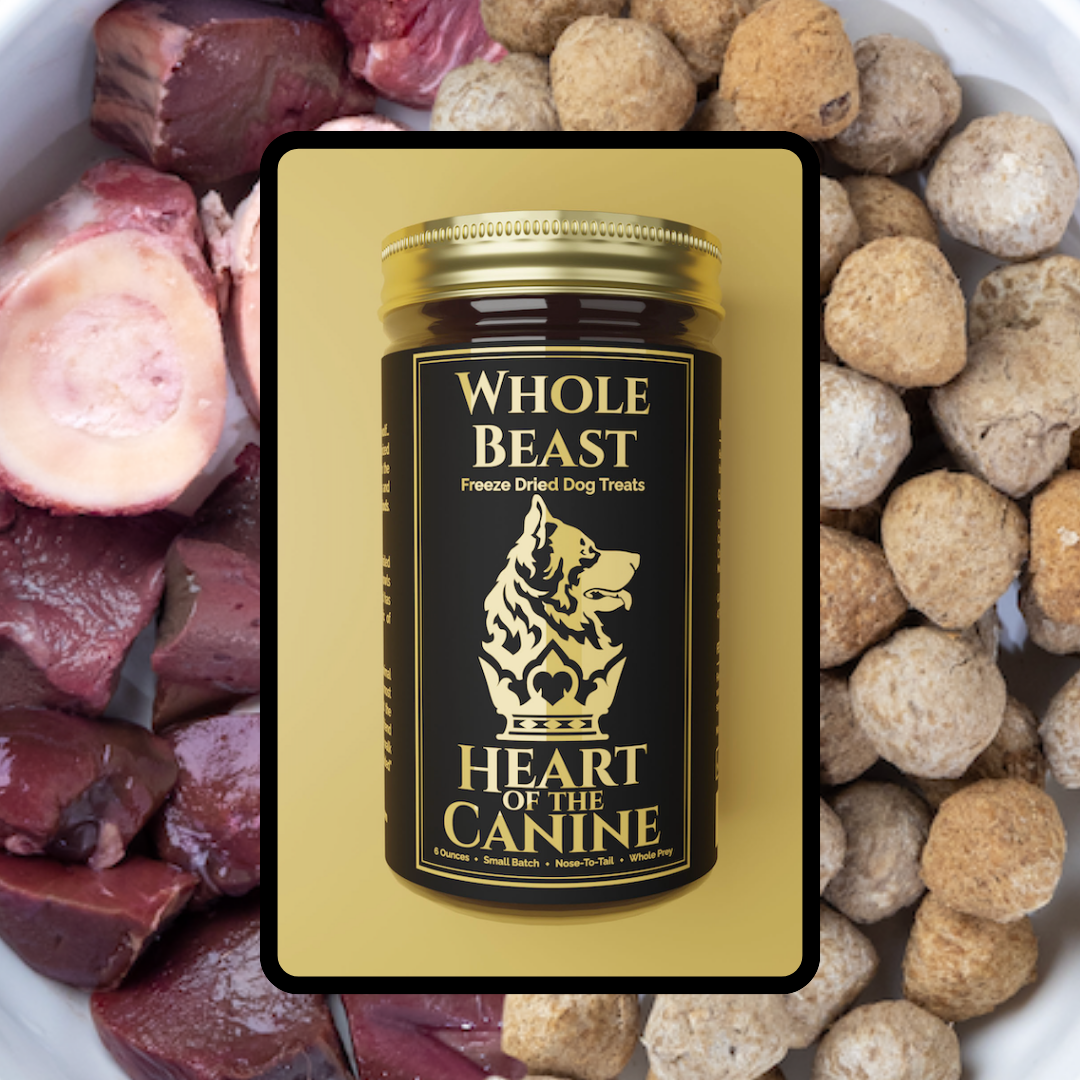
A dog food recall can be a stressful experience for pet owners. It’s essential to understand the potential consequences and know the immediate steps to take to protect your dog’s health and your own peace of mind. This section provides a practical guide to navigate the impact of a recall.
Immediate Actions for Pet Owners
Upon learning about a dog food recall affecting your dog’s food, swift action is crucial. This helps minimize any potential harm to your pet and allows you to take appropriate steps to mitigate the situation.
- Stop Feeding the Food: Immediately discontinue feeding the recalled product to your dog. This is the most important step to prevent further exposure to potentially harmful ingredients.
- Check the Product Code and Lot Number: Verify if the food you have matches the recalled product details. Carefully examine the packaging for the product name, brand, lot number, and “best by” or expiration date. Compare this information with the recall notice provided by the manufacturer or the FDA.
- Assess Your Dog’s Condition: Monitor your dog for any signs of illness. Symptoms can vary depending on the contaminant or issue causing the recall, but common signs include vomiting, diarrhea, lethargy, loss of appetite, and changes in behavior. If your dog exhibits any concerning symptoms, contact your veterinarian immediately.
- Gather Documentation: Keep records of the recalled food, including the packaging, receipts, and any communication with the manufacturer or retailer. This documentation will be useful for refunds or exchanges.
- Inform Others: Share the recall information with other dog owners you know, especially if they feed their dogs the same brand or product. Spreading awareness can help prevent other pets from being affected.
Handling and Disposing of Recalled Dog Food
Proper handling and disposal of recalled dog food are critical to prevent accidental consumption by other animals or humans and to minimize environmental impact.
- Safe Handling: Wear gloves when handling the recalled food to avoid direct contact with potentially contaminated material. Wash your hands thoroughly with soap and water after handling the food and any surfaces that have come into contact with it.
- Storage: Store the recalled food in a secure location, away from children, other pets, and areas where food is prepared. This prevents accidental ingestion.
- Disposal Methods: The best method for disposing of the food depends on the specific recall and the manufacturer’s instructions.
- Sealed Disposal: If the food is in its original, sealed packaging, you may be able to dispose of it in a sealed trash bag, ensuring it cannot be accessed by animals or scavengers.
- Unsealed Disposal: If the packaging is open, or if instructed by the manufacturer, you may need to render the food inedible before disposal. This can be done by mixing it with water, bleach (use a small amount and follow safety precautions), or other non-toxic substances to deter consumption. Then, place it in a sealed trash bag.
- Manufacturer Instructions: Always follow the manufacturer’s specific instructions for disposal, as they may have specific guidelines depending on the nature of the recall.
- Contact Local Authorities: In some cases, local waste management authorities may have specific guidelines for disposing of contaminated materials. Check with your local authorities for any specific regulations.
Contacting the Manufacturer or Retailer for Refunds or Exchanges
Navigating the refund or exchange process can help you recoup your losses and ensure you can continue providing safe food for your dog. Following a checklist can help streamline the process.
- Gather Necessary Information: Collect the product name, lot number, “best by” date, and any purchase receipts. Have these details ready when you contact the manufacturer or retailer.
- Contact the Manufacturer: Locate the manufacturer’s contact information, usually found on the product packaging or their website. Contact them via phone, email, or the contact form. Explain the situation and provide the necessary information.
Example: “Hello, I am contacting you regarding the recall of [Product Name]. I have a bag with lot number [Lot Number] and the “best by” date is [Date]. I would like to inquire about a refund or exchange.”
- Contact the Retailer: If you purchased the food from a retailer, contact them as well. Many retailers will offer refunds or exchanges for recalled products. Provide them with the product information and your receipt.
- Follow Instructions: Carefully follow the instructions provided by the manufacturer or retailer. They may require you to return the product, provide proof of purchase, or complete a claim form.
- Keep Records of Communication: Document all communications, including the date, time, method, and the name of the person you spoke with. Keep copies of emails and any other written correspondence.
- Check for Updates: Monitor the manufacturer’s website or social media for updates regarding the recall and the refund or exchange process.
Investigating the Recall
Navigating a pet food recall is a complex process, demanding swift action and thorough investigation. Understanding the steps involved for both the manufacturer and regulatory agencies is crucial for protecting animal health and maintaining consumer trust. This section Artikels the key procedures undertaken during a recall investigation.
Manufacturer’s Recall Initiation Steps
When a pet food manufacturer identifies a potential issue requiring a recall, a structured approach is essential. These steps ensure a coordinated and effective response:The process begins with identifying the problem and assessing its severity. This often involves reviewing consumer complaints, internal testing results, and supply chain information. Once a potential hazard is confirmed, the manufacturer initiates the following steps:
- Notification of Regulatory Agencies: The manufacturer must immediately notify the relevant regulatory agencies, such as the Food and Drug Administration (FDA) in the United States. This notification should include details about the affected product, the nature of the problem, and the estimated scope of the recall.
- Product Identification and Traceability: A comprehensive investigation into the product’s history is conducted. This involves tracing the ingredients, manufacturing processes, and distribution channels. Accurate records are vital for pinpointing the affected batches and preventing further distribution of the contaminated product.
- Public Notification: The manufacturer must issue a public announcement to inform consumers about the recall. This usually involves press releases, website postings, and social media updates. The announcement should clearly identify the affected products, provide instructions for consumers, and offer contact information for inquiries.
- Product Retrieval and Disposal: The manufacturer is responsible for retrieving the recalled product from retailers and consumers. This may involve providing instructions for returning the product or offering refunds. The recalled product must be properly disposed of to prevent further harm.
- Root Cause Analysis: A thorough investigation is conducted to determine the root cause of the problem. This may involve analyzing ingredient sources, manufacturing processes, and storage conditions. Identifying the root cause is crucial for preventing future incidents.
- Corrective Actions: Based on the root cause analysis, the manufacturer must implement corrective actions to prevent recurrence. These actions may include changes to manufacturing processes, supplier agreements, or product testing procedures.
Regulatory Agency Investigation Procedures
Regulatory agencies play a critical role in investigating pet food recalls, ensuring consumer safety and compliance with regulations. Their investigations involve a series of detailed steps:The FDA, for example, has a structured approach to investigating pet food recalls. Their investigation typically includes the following:
- Review of Manufacturer’s Information: The agency begins by reviewing the information provided by the manufacturer, including the recall plan, product details, and the nature of the problem.
- Inspection of Manufacturing Facilities: FDA investigators may inspect the manufacturing facility to assess the production process, identify potential sources of contamination, and verify the manufacturer’s corrective actions.
- Product Sampling and Testing: The agency collects samples of the recalled product and potentially ingredients for laboratory testing. This testing is crucial for confirming the presence of contaminants, such as bacteria, toxins, or undeclared ingredients.
- Traceback Investigation: The agency conducts a traceback investigation to determine the source of the problem. This involves tracing the ingredients, manufacturing processes, and distribution channels to identify the origin of the contamination.
- Evaluation of Corrective Actions: The agency evaluates the manufacturer’s corrective actions to ensure they are effective in preventing future incidents. This may involve reviewing changes to manufacturing processes, supplier agreements, and product testing procedures.
- Public Communication: The agency communicates its findings to the public through press releases, website postings, and other channels. This ensures transparency and informs consumers about the recall and any associated risks.
Tracing the Source of Contamination
Tracing the source of contamination in a small batch recall can be a complex undertaking. This process requires meticulous record-keeping and a systematic approach to identify the origin of the problem.
Consider a scenario where a small batch of dog food is found to be contaminated with Salmonella. The manufacturer, working with the FDA, would follow these steps to trace the source:
- Batch Identification: The manufacturer identifies the specific batch of dog food affected by the contamination, using lot numbers, production dates, and other identifying information.
- Ingredient Traceback: The manufacturer traces the ingredients used in the affected batch back to their sources. This involves reviewing supplier records, ingredient testing results, and other relevant documentation.
- Manufacturing Process Review: The manufacturer reviews the manufacturing process to identify potential points of contamination. This includes examining equipment, sanitation practices, and employee handling procedures.
- Environmental Sampling: The manufacturer and regulatory agencies may collect environmental samples from the manufacturing facility to test for the presence of Salmonella. This helps to identify potential sources of contamination within the facility.
- Supply Chain Investigation: The manufacturer and regulatory agencies investigate the supply chain to identify potential sources of contamination. This may involve contacting suppliers, reviewing their records, and conducting inspections of their facilities.
- Root Cause Determination: Based on the findings of the investigation, the manufacturer and regulatory agencies determine the root cause of the contamination. This may involve identifying a contaminated ingredient, a failure in the manufacturing process, or a breakdown in sanitation practices.
Prevention and Mitigation
Dealing with a dog food recall is stressful, but proactive measures can significantly reduce the risk and mitigate the impact. This section provides practical advice for pet owners and manufacturers, focusing on preventing future incidents and ensuring the safety of our canine companions.
Minimizing Risk for Pet Owners
Pet owners can take several steps to minimize the chances of feeding their dogs recalled food. It’s about being informed, vigilant, and making smart choices.
- Stay Informed: Regularly check the FDA and your country’s equivalent for pet food recalls. Subscribe to email alerts from these agencies and follow reputable pet food news sources. This proactive approach helps you stay ahead of potential issues.
- Read Labels Carefully: Scrutinize ingredient lists and manufacturing dates. Look for clear labeling, including the manufacturer’s contact information. Avoid products with vague ingredient descriptions.
- Choose Reputable Brands: Opt for brands with a strong track record and a commitment to quality control. Research the brand’s history and read reviews from other pet owners.
- Store Food Properly: Store dog food in a cool, dry place, following the manufacturer’s instructions. This helps maintain freshness and prevents contamination.
- Rotate Food Supplies: Use the “first in, first out” method. Ensure older bags of food are used before newer ones. This reduces the risk of feeding your dog expired food.
- Monitor Your Dog: Pay close attention to your dog’s health. Report any unusual symptoms, such as vomiting, diarrhea, or loss of appetite, to your veterinarian promptly. Early detection is crucial.
Questions to Ask When Selecting Dog Food Brands, Small batch dog food recall
Choosing the right dog food brand is crucial for your dog’s health. Asking the right questions can help you make an informed decision. Transparency and a commitment to safety are key indicators of a reliable brand.
- What are the sourcing practices for ingredients? A good brand should be able to provide details about where their ingredients come from, including the origin of the protein sources and any testing performed. This transparency helps you understand the quality and safety of the ingredients.
- What quality control measures are in place? Ask about the brand’s testing protocols for contaminants, such as bacteria, mycotoxins, and heavy metals. The more rigorous the testing, the safer the food is likely to be.
- What is the manufacturing process? Inquire about the facility where the food is produced and the processes used to ensure safety and consistency. Does the brand own its manufacturing facility or use a co-packer?
- Does the brand have a history of recalls? While past recalls don’t necessarily indicate a future problem, understanding a brand’s history can provide insights into its commitment to safety and its response to issues.
- What is the brand’s customer service like? A responsive and helpful customer service team can be a good indicator of the brand’s overall commitment to its customers. They should be able to answer your questions and address your concerns promptly.
- Are the ingredients human-grade? While not always necessary, using human-grade ingredients often indicates a higher level of quality control and safety standards.
Manufacturer Steps to Prevent Recalls
Manufacturers play a critical role in preventing recalls. Implementing robust quality control measures and a commitment to transparency are essential.
- Establish a Comprehensive Quality Control System: Implement a robust quality control system that includes regular testing of raw materials and finished products for contaminants, such as Salmonella, E. coli, and mycotoxins.
- Implement Hazard Analysis and Critical Control Points (HACCP): This systematic approach identifies and controls hazards throughout the manufacturing process, from ingredient sourcing to packaging.
- Maintain Detailed Records: Keep accurate records of all ingredients, manufacturing processes, and testing results. This documentation is crucial for traceability and rapid response in case of a problem.
- Conduct Regular Audits: Conduct regular audits of manufacturing facilities and suppliers to ensure compliance with safety standards. These audits should be performed by independent third parties.
- Traceability Systems: Implement a robust traceability system that allows manufacturers to track ingredients from their source to the finished product. This enables quick identification and isolation of contaminated products.
- Supplier Verification: Thoroughly vet and verify all suppliers to ensure they meet quality and safety standards. This includes conducting regular inspections and audits of supplier facilities.
- Employee Training: Provide comprehensive training to all employees on food safety procedures and quality control measures. This training should be ongoing and updated regularly.
- Invest in Research and Development: Invest in research and development to improve food safety practices and develop new technologies for detecting contaminants.
- Recall Plan: Develop and maintain a detailed recall plan that Artikels the steps to be taken in the event of a recall. This plan should include procedures for notifying customers, retrieving products, and communicating with regulatory agencies.
- Transparency: Be transparent with consumers about ingredients, manufacturing processes, and any potential risks. This builds trust and allows consumers to make informed decisions.
Comparing Recall Data
Understanding the landscape of pet food recalls requires a close examination of the data. This allows us to differentiate between the risks associated with small-batch producers and large manufacturers, identify industry trends, and ultimately, assess the impact on consumer trust. Analyzing recall data provides valuable insights for both consumers and the pet food industry.
Frequency of Recalls: Small Batch vs. Large Manufacturers
The frequency of recalls varies significantly between small-batch dog food producers and large manufacturers. These differences often reflect variations in production processes, quality control measures, and supply chain complexities.The following bullet points highlight key distinctions in recall frequency:
- Recall Volume: Large manufacturers typically handle a much higher volume of product. Therefore, even with robust quality control systems, they may experience more frequent recalls in terms of the total number of products affected, due to the sheer scale of their operations. Small-batch producers, producing significantly less product, may have fewer recalls overall.
- Recall Scope: Recalls initiated by large manufacturers can often involve a broader distribution network, potentially impacting consumers across multiple states or even countries. Small-batch recalls are often localized, affecting a smaller geographic area.
- Cause of Recalls: The root causes of recalls can differ. Large manufacturers might face recalls related to ingredients sourced from complex, global supply chains, increasing the risk of contamination or adulteration. Small-batch producers may experience recalls related to issues with ingredient sourcing from local suppliers, or manufacturing processes.
- Severity of Impact: While recall frequency may vary, the severity of the impact on consumer health and the brand’s reputation can be significant for both types of producers. Any instance of a pet falling ill or, tragically, passing away due to contaminated food can lead to serious legal ramifications, financial losses, and damage to the brand’s image.
- Transparency and Response: Large manufacturers often have established protocols and resources for managing recalls, including dedicated teams, communication channels, and relationships with regulatory agencies. Small-batch producers might have fewer resources, potentially leading to a different approach to recall management, which can affect public perception.
Data Collection and Analysis for Industry Trends
Recall data is collected and analyzed systematically to identify trends within the pet food industry. This process helps to understand the underlying causes of recalls and to develop preventative measures.The process of data collection and analysis typically involves the following steps:
- Data Sources: Data is gathered from multiple sources, including the Food and Drug Administration (FDA), the Association of American Feed Control Officials (AAFCO), and the manufacturers themselves. Public announcements, press releases, and consumer reports also contribute to the data pool.
- Categorization of Recalls: Recalls are categorized based on various factors, such as the type of product (e.g., dry food, wet food, treats), the reason for the recall (e.g., Salmonella contamination, foreign objects, ingredient issues), and the manufacturer.
- Trend Identification: Statistical analysis is performed to identify trends over time. This involves looking for patterns in the frequency of recalls, the specific causes, and the manufacturers involved. The use of data visualization tools, such as charts and graphs, helps to communicate these trends effectively.
- Root Cause Analysis: A deep dive into the recall data helps to pinpoint the underlying causes. This might involve examining the manufacturing processes, ingredient sourcing, and quality control measures of the affected companies.
- Risk Assessment: The collected data is used to assess the risk of future recalls. This includes identifying potential vulnerabilities in the supply chain, manufacturing processes, and product formulations.
Impact on Consumer Trust and Brand Reputation
Recall data significantly impacts consumer trust and brand reputation. The way a company handles a recall, including its communication strategy, transparency, and responsiveness, plays a crucial role in mitigating the damage to its reputation.Here’s how recall data influences consumer trust and brand reputation:
- Erosion of Trust: Any recall, regardless of the size of the producer, can erode consumer trust. If a consumer’s pet becomes ill after eating a recalled product, the damage can be significant.
- Reputational Damage: Recalls can negatively affect a brand’s image. Negative publicity, social media backlash, and consumer complaints can tarnish a brand’s reputation.
- Financial Impact: Recalls can lead to significant financial losses, including the cost of product retrieval, legal fees, potential lawsuits, and decreased sales.
- Example: In 2007, the pet food industry experienced a large-scale recall involving melamine contamination. Several major brands were affected. This incident led to widespread consumer distrust and a significant decline in sales for many companies. The industry responded with increased safety measures and improved transparency to rebuild trust.
- Impact of Transparency: Companies that are transparent about their recalls and take swift action to address the issues are more likely to maintain consumer trust. Conversely, companies that attempt to hide information or downplay the severity of the situation often face greater reputational damage.
- Impact of Response: A timely and effective response to a recall is essential. This includes communicating clearly with consumers, providing refunds or replacements, and taking steps to prevent future incidents. A slow or inadequate response can exacerbate the damage to a brand’s reputation.
The Role of Transparency
During a pet food recall, the level of transparency exhibited by the manufacturer can significantly impact consumer trust and the overall handling of the crisis. Clear and open communication is crucial for regaining confidence and ensuring pet owners have the information they need to protect their animals. Transparency fosters trust and facilitates a more effective response to the situation.
Importance of Transparency from Pet Food Manufacturers
Pet food manufacturers play a vital role in providing accurate and timely information during a recall. This commitment to transparency helps pet owners make informed decisions and demonstrates the company’s dedication to animal welfare.Transparency involves:
- Providing clear and concise information about the affected products, including product names, lot numbers, and expiration dates.
- Disclosing the specific reason for the recall, whether it’s a contamination issue, a labeling error, or a manufacturing defect.
- Offering readily accessible updates on the recall’s progress, including steps taken to address the issue and prevent future occurrences.
- Being open and honest about the investigation process, including collaborating with regulatory agencies and sharing findings with the public.
- Providing clear instructions on what pet owners should do with the recalled products, such as where to return them and how to obtain a refund.
Effective Communication Strategies During Recalls
Effective communication strategies are essential for manufacturers to manage a recall successfully. These strategies aim to provide clear, concise, and timely information to affected pet owners and the public.Some effective communication strategies include:
- Prompt announcements: Issuing recall notices as soon as the issue is identified, without delay.
- Multiple communication channels: Utilizing various channels, such as the company website, social media, email, and traditional media, to reach a broad audience.
- Dedicated recall websites or pages: Creating a specific section on the company website solely dedicated to recall information.
- Customer service support: Providing a dedicated phone number and email address to address customer inquiries and concerns.
- Proactive updates: Regularly updating the public on the progress of the recall, including investigation findings and corrective actions.
Hypothetical Company Website Displaying Recall Information
Imagine a pet food company, “Happy Paws,” facing a recall. Their website would feature a dedicated section for recall information, designed for clarity and ease of access.Here’s a description of the “Recall Information” page:
The main navigation bar at the top of the page would include a clear link labeled “Recall Information” or “Recalls.” Clicking this link would lead directly to a dedicated page.
The page would begin with a prominent headline, such as “Important Recall Information: Happy Paws [Product Name].” Underneath the headline, there would be a brief, concise summary of the recall, stating the product name, the reason for the recall (e.g., potential salmonella contamination), and the date of the announcement.
The page would then include a detailed table listing all affected products.
The table would have the following columns:
- Product Name: The specific name of the recalled product (e.g., “Happy Paws Chicken Recipe”).
- Lot Number: The lot numbers affected by the recall.
- Expiration Date: The expiration dates of the recalled products.
- UPC Code: The UPC code found on the product packaging.
- Image of the Product: A clear, high-resolution image of the product packaging, allowing pet owners to easily identify the affected items. The image would clearly display the product name, lot number, and expiration date.
Below the table, there would be a section titled “Reason for Recall.” This section would provide a detailed explanation of the reason for the recall, including the specific contaminant or issue and any relevant scientific data or findings.
Following the “Reason for Recall” section, there would be a section titled “What to Do.” This section would provide clear, step-by-step instructions for pet owners.
The page would also feature a “Frequently Asked Questions” (FAQ) section addressing common concerns, such as “What if my pet has already eaten the product?” and “How do I get a refund?”.
Finally, the page would include contact information for customer service, including a dedicated phone number and email address, ensuring pet owners can easily reach out for assistance. The company would prominently display a statement reaffirming its commitment to pet safety and the measures it’s taking to prevent future recalls.
Wrap-Up
In conclusion, navigating the landscape of small batch dog food recalls requires vigilance, informed decision-making, and proactive measures. By understanding the causes, recognizing the signs, and knowing how to respond, pet owners can significantly minimize the risks to their dogs. From scrutinizing product labels to asking the right questions and staying informed about industry trends, you can help protect your dog. Remember that transparency from manufacturers and a commitment to quality control are crucial elements in fostering a safe and trustworthy pet food market.