Cardboard containers for food represent a critical segment within the packaging industry, offering a versatile and sustainable solution for food storage, transportation, and presentation. These containers, essentially crafted from paper-based materials, serve a multitude of purposes across the food supply chain. Their applications range from simple food packaging to complex protective systems, directly influencing food safety, shelf life, and consumer experience.
This exploration delves into the historical context, diverse types, material compositions, and regulatory standards associated with cardboard food containers, providing a thorough understanding of their significance.
The evolution of cardboard food packaging reflects a continuous adaptation to meet changing consumer demands and environmental concerns. Initially utilized for basic containment, cardboard containers have undergone significant advancements, incorporating specialized coatings, enhanced structural designs, and sustainable sourcing practices. This evolution has been driven by the need to maintain food integrity, reduce waste, and minimize environmental impact. The following sections will provide a comprehensive overview of the various aspects, including materials, manufacturing processes, food safety regulations, sustainability considerations, design and functionality, cost analysis, market trends, and future innovations.
Introduction to Cardboard Containers for Food
Cardboard containers have become ubiquitous in the food industry, providing a versatile and sustainable packaging solution. These containers serve a multitude of purposes, from transporting raw ingredients to presenting finished products to consumers. Their adaptability and eco-friendly attributes have cemented their place as a vital element of the modern food supply chain.
Definition of Cardboard Containers for Food
Cardboard containers for food are primarily fabricated from paper-based materials, specifically corrugated fiberboard or paperboard. These materials are engineered to provide a protective barrier for food products during storage, transportation, and display. The construction typically involves multiple layers of paper, with a fluted inner layer in corrugated cardboard adding strength and cushioning. The surfaces are often treated with coatings to improve resistance to moisture, grease, and other potential contaminants.
Primary Applications of Cardboard Containers in the Food Industry
Cardboard containers are utilized across a wide spectrum of food industry applications, offering a balance of protection, cost-effectiveness, and environmental considerations.
- Food Transportation: Corrugated cardboard boxes are the workhorses of the food supply chain. They securely transport fresh produce, frozen foods, and dry goods from farms, processing plants, and distribution centers to retailers and restaurants. A box of apples, for example, is held within a brown, rectangular container, typically with ventilation holes, ensuring the apples are kept safe during their journey.
- Retail Packaging: Cardboard packaging presents food products attractively on store shelves. Cereal boxes, frozen pizza cartons, and ready-meal containers are all examples. A cereal box, illustrated with colorful graphics and product information, stands upright on a shelf, drawing the consumer’s eye.
- Food Service Packaging: Restaurants and food vendors use cardboard containers for takeout and delivery services. Pizza boxes, burger boxes, and French fry containers are standard. A pizza box, square and sturdy, with a grease-resistant interior, keeps the pizza warm and intact during transport.
- Specialty Food Packaging: Cardboard also caters to niche markets, like artisanal baked goods and gourmet snacks. These often feature custom designs and premium finishes. A box of handcrafted chocolates, for instance, might be a sleek, elegant container with a glossy finish.
Historical Evolution of Cardboard Food Packaging
The use of cardboard in food packaging has a history marked by continuous innovation, responding to the needs of a growing population and evolving distribution methods.
- Early Days: In the late 19th and early 20th centuries, cardboard began to replace wooden crates and other less efficient packaging materials. Early examples were primarily used for shipping and less for consumer-facing packaging.
- The Rise of Mass Production: The advent of mass production and the rise of supermarkets fueled the need for efficient and attractive packaging. Cardboard boxes became essential for packaging and marketing cereals, crackers, and other dry goods.
- Mid-20th Century Innovations: Innovations in coating technologies and printing techniques improved cardboard’s durability and visual appeal. Wax coatings and printed graphics allowed for better protection and branding.
- Late 20th and 21st Century Developments: The emphasis shifted toward sustainability. Recycled cardboard, biodegradable coatings, and innovative designs to minimize material usage have become prominent. Today, cardboard packaging is often designed for recyclability, with clear instructions printed on the container.
Types of Cardboard Food Containers
Cardboard food containers offer a diverse range of designs, each tailored to meet specific food packaging needs. Understanding the different types of containers and their suitability for various food items is crucial for effective food preservation, transportation, and presentation. These containers provide a sustainable and practical solution for a wide array of food products.
Box Containers
Box containers represent a fundamental type of cardboard packaging, known for their versatility and structural integrity. They come in numerous shapes and sizes, designed to accommodate a broad spectrum of food products.
- Folding Cartons: These are the most common type, often used for dry goods like cereals, crackers, and pasta. They typically feature a hinged lid and are easily assembled.
- Rigid Boxes: Constructed from thicker cardboard, these boxes offer superior strength and are suitable for heavier items or those requiring greater protection, such as frozen pizzas or ready meals. They may also incorporate inserts for product organization.
- Shipping Boxes: Designed for transportation, these boxes are durable and capable of withstanding the rigors of shipping and handling. They are often corrugated for added strength and are used for bulk food items, such as packaged snacks or ingredients.
Tray Containers
Tray containers provide an open-top packaging solution, ideal for displaying and accessing food items. They are particularly suited for products that benefit from visual presentation.
- Clamshell Trays: These trays consist of two hinged halves that enclose the food item, offering protection and visibility. They are frequently used for fruits, vegetables, and bakery items. Imagine a clear, transparent clamshell containing vibrant red strawberries, showcasing their freshness and appeal.
- Open Trays: These are simple, shallow trays, often used for fast food, takeout meals, and prepared foods. They allow for easy access to the food and can be paired with a lid for transport. Consider a rectangular open tray filled with a delicious portion of fries, ready for consumption.
- Compartmentalized Trays: These trays feature dividers, separating different food items within a single container. They are commonly found in ready-to-eat meals, offering a convenient way to package a complete meal. Picture a tray with sections for a main course, side dish, and dessert, all neatly arranged.
Sleeve Containers
Sleeve containers are designed to wrap around a product, providing a protective layer and branding opportunity. They are frequently used for items like sandwiches, wraps, and prepared meals.
- Wrap-Around Sleeves: These sleeves completely encircle the food item, offering protection and branding space. Imagine a sleeve elegantly wrapped around a gourmet sandwich, displaying the restaurant’s logo and menu details.
- Partial Sleeves: These sleeves cover only a portion of the product, often leaving the top or bottom exposed. They are commonly used for items like ice cream cones or individual pastries. Picture an ice cream cone nestled in a partial sleeve, protecting the cone while allowing the delicious treat to be seen.
Container Suitability and Design Comparison
The selection of a cardboard food container depends on factors such as the food item’s nature, size, weight, and the desired level of protection. The following table compares the advantages and disadvantages of various container designs:
Container Type | Best Suited For | Advantages | Disadvantages |
---|---|---|---|
Folding Cartons | Dry goods (cereals, crackers), small retail items | Lightweight, cost-effective, easy to assemble, excellent for branding. | Limited protection against moisture, less suitable for heavy items. |
Rigid Boxes | Frozen pizzas, ready meals, heavier items | Durable, provides good protection, can incorporate inserts for organization. | More expensive than folding cartons, requires more storage space. |
Clamshell Trays | Fruits, vegetables, bakery items | Provides good visibility, easy access, protects from crushing. | May not be suitable for items with high moisture content, can be less secure without proper sealing. |
Open Trays | Fast food, takeout meals, prepared foods | Easy access, good for presentation, often paired with lids for transport. | Offers limited protection, can be prone to spills without a lid. |
Materials and Construction
Cardboard food containers, crucial for protecting and presenting food, are engineered through a combination of carefully selected materials and precise manufacturing processes. The integrity of these containers relies heavily on the types of cardboard used, the methods of construction, and the protective coatings applied to ensure food safety and container durability. Understanding these aspects is vital for appreciating the sophisticated design of these seemingly simple items.
Types of Cardboard Used
The selection of cardboard type significantly influences a food container’s performance characteristics. Different types of cardboard are chosen based on the specific application, considering factors such as the weight of the food, the need for insulation, and the desired level of moisture resistance.Corrugated cardboard is a popular choice for its strength and cushioning properties. It consists of one or more layers of fluted corrugated medium (the wavy layer) glued between flat linerboards.
The flute profile (A, B, C, E, F, etc.) dictates the board’s strength, cushioning, and stacking capabilities. For example, A-flute provides excellent stacking strength, while E-flute offers a thinner profile suitable for printing and retail packaging. The choice of flute type is critical for ensuring the container can withstand the rigors of transportation and handling.Paperboard, on the other hand, refers to a broad category of thick paper stock.
It is generally less robust than corrugated cardboard but offers excellent printability and is often used for food containers where aesthetics are important. There are several types of paperboard used in food packaging:
- Solid Bleached Sulfate (SBS) paperboard: Known for its bright white appearance and excellent printability. It’s often used for ice cream containers, fast-food boxes, and other applications where a high-quality print surface is desired. The smooth surface is ideal for showcasing branding and graphics.
- Solid Unbleached Sulfate (SUS) paperboard: Provides good strength and is naturally resistant to moisture. Often used for packaging frozen foods or items requiring some level of moisture protection. The unbleached nature provides a natural, earthy appearance.
- Clay-Coated Newsback (CCNB) paperboard: Made from recycled paper and coated with clay to improve printability. This is a cost-effective option often used for cereal boxes and other packaging where a glossy finish is not critical. The recycled content makes it a sustainable choice.
Manufacturing Process of Cardboard Food Containers
The manufacturing of cardboard food containers involves several key steps, from raw material preparation to the final assembly. The process is highly automated, ensuring efficiency and consistency in the production of large volumes of containers.The process begins with the creation of the cardboard itself. In the case of corrugated cardboard, this involves the corrugation of the fluted medium and the lamination of the linerboards.
Paperboard is typically manufactured in large rolls, ready for conversion into containers.
- Printing and Cutting: The cardboard is then printed with the necessary graphics, branding, and informational labels. This is often done using flexographic printing, which is efficient and cost-effective for large print runs. After printing, the cardboard is cut into the desired shapes using die-cutting machines.
- Folding and Gluing: The cut cardboard is then folded and glued to form the final container shape. Specialized machinery is used to apply adhesive precisely and ensure secure seams. The accuracy of folding and gluing is crucial for the structural integrity of the container.
- Assembly and Quality Control: Some containers, like those for beverages, might involve additional steps like the application of lids or closures. A thorough quality control process is implemented to check for any defects, such as misprints, incorrect dimensions, or insufficient gluing.
Coatings and Treatments Applied to Cardboard for Food Safety and Moisture Resistance
To ensure food safety and protect against moisture and grease, cardboard food containers often undergo various coatings and treatments. These coatings are applied to create a barrier between the food and the cardboard, preventing contamination and maintaining the container’s structural integrity.Coatings provide crucial protection against various challenges. They act as a barrier against grease, moisture, and microbial contamination, extending the shelf life of the food and preserving its quality.
These coatings are also crucial for preventing the cardboard from becoming soggy and losing its shape.
- Polyethylene (PE) Coating: A common coating that provides excellent moisture resistance. PE coatings are applied as a thin layer to the inside of containers, making them suitable for holding liquids and preventing leaks. PE-coated containers are widely used for items like coffee cups and soup containers.
- Wax Coating: Historically, wax coatings were a standard for moisture resistance. They are still used in some applications, but have limitations. Wax coatings are effective at repelling water and grease but can be less durable than other options and may not be suitable for high-temperature applications.
- Fluorochemical Coatings: These coatings provide excellent grease resistance and are often used in food packaging that comes into direct contact with greasy foods, such as pizza boxes or fast-food containers. They can help to prevent oil from penetrating the cardboard and causing stains or weakening the structure.
- Biodegradable Coatings: In response to growing environmental concerns, there is a rise in the use of biodegradable coatings. These coatings are made from plant-based materials and are designed to break down naturally, reducing the environmental impact of the containers. Examples include coatings made from polylactic acid (PLA).
Food Safety and Regulations
Cardboard containers used for food must adhere to stringent food safety regulations to protect consumers from contamination and ensure product integrity. The following sections detail the critical aspects of food-grade cardboard, regulatory standards, and contamination prevention strategies. This information is crucial for manufacturers, distributors, and consumers alike.
Importance of Food-Grade Cardboard
Food-grade cardboard is specifically manufactured to meet the rigorous demands of direct food contact. Unlike standard cardboard, it is designed to prevent the transfer of harmful substances and maintain food safety. The cardboard’s composition and manufacturing processes are tightly controlled.
- Barrier Properties: Food-grade cardboard often includes a barrier coating, like polyethylene (PE) or other food-safe coatings, to prevent the migration of inks, adhesives, and other contaminants from the cardboard into the food. Imagine a thin, transparent layer, like a very fine film, applied to the inside of a pizza box. This coating acts as a shield, ensuring that the pizza, with its cheesy, saucy goodness, doesn’t come into contact with the cardboard directly.
Do not overlook the opportunity to discover more about the subject of key food supermarket weekly ad.
- Low Odor and Taste Transfer: Food-grade materials are selected to minimize the transfer of undesirable odors or tastes to the food. Consider the difference between a fresh, warm croissant and one stored in a cardboard box that smells of glue or chemicals. The food-grade box ensures the croissant’s delicate flavor is preserved.
- Microbial Control: The manufacturing process of food-grade cardboard minimizes the risk of microbial contamination. This includes using clean raw materials, controlling humidity, and ensuring proper drying to inhibit mold and bacteria growth. Think of a cleanroom environment, where everything is sanitized and controlled to prevent any form of contamination.
- Compliance with Regulations: Food-grade cardboard must comply with all relevant food safety regulations, such as those set by the FDA in the United States and the European Union’s (EU) regulations. This ensures that the materials used are safe for food contact and that the manufacturing processes are compliant.
Regulatory Standards and Certifications
Cardboard food packaging is subject to a variety of regulatory standards and certifications that vary depending on the region. These standards are designed to ensure the safety and suitability of the packaging materials for food contact. Compliance with these regulations is crucial for businesses involved in food packaging.
- United States (FDA): The Food and Drug Administration (FDA) in the United States regulates food packaging materials under the Federal Food, Drug, and Cosmetic Act. Specifically, the FDA requires that packaging materials be “generally recognized as safe” (GRAS) or have specific approvals for food contact. For example, the FDA has regulations detailing the acceptable substances that can be used in food packaging and the conditions under which they can be used.
- European Union (EU): The EU has comprehensive regulations for food contact materials. These regulations, including Framework Regulation (EC) No 1935/2004 and specific measures for materials like paper and board, require that materials do not transfer their constituents to food in amounts that could endanger human health or change the composition, taste, or odor of the food. For instance, manufacturers must provide a Declaration of Compliance (DoC) for food contact materials, demonstrating that their products meet these standards.
- Other Regulations and Certifications:
- Global Food Safety Initiative (GFSI): The GFSI provides a benchmark for food safety standards, and many food packaging manufacturers seek certification under GFSI-recognized schemes.
- Good Manufacturing Practices (GMP): GMP guidelines provide a framework for manufacturing practices to ensure the production of safe and consistent products.
- Specific Material Regulations: Beyond general regulations, there are often specific regulations for the materials used in cardboard food packaging, such as inks, adhesives, and coatings. For example, regulations may limit the use of certain chemicals or require specific testing to ensure their safety.
Preventing Contamination and Maintaining Food Safety
Maintaining food safety in cardboard containers requires a multi-faceted approach that includes careful material selection, controlled manufacturing processes, and proper handling throughout the supply chain.
- Material Selection: The choice of raw materials is crucial. Only food-grade cardboard and inks, adhesives, and coatings approved for food contact should be used. Consider a manufacturer who chooses to use inks containing heavy metals for printing on pizza boxes. This would be a violation of regulations and could pose a serious health risk.
- Manufacturing Processes: The manufacturing environment should be clean and controlled to prevent contamination. This includes regular cleaning of equipment, pest control, and measures to minimize the risk of cross-contamination. Imagine a factory where workers wear cleanroom attire, and the production area is regularly sanitized.
- Storage and Handling: Cardboard containers should be stored in a clean, dry environment, away from potential sources of contamination. Proper handling during transport and storage is essential to prevent damage that could compromise the packaging’s integrity. For instance, a warehouse where food packaging is stored alongside cleaning chemicals is a high-risk scenario.
- Testing and Quality Control: Regular testing of the finished cardboard containers should be conducted to ensure compliance with food safety standards. This may include migration testing to ensure that no harmful substances are transferred to the food.
- Traceability: Establishing a robust traceability system allows for the tracking of packaging materials throughout the supply chain. In the event of a contamination issue, this enables quick identification and recall of affected products.
- Examples of Prevention:
- Ink Migration: Using food-grade inks and ensuring they are properly cured to prevent ink migration into the food. Imagine a pizza box printed with food-grade inks. The printing process is carefully controlled to ensure the ink dries properly and doesn’t bleed onto the pizza.
- Odor Transfer: Avoiding the use of adhesives or coatings that can impart undesirable odors or tastes to the food. For example, choosing a glue that is odorless and tasteless is essential.
- Microbial Growth: Ensuring proper drying of the cardboard during manufacturing to prevent mold and bacteria growth. Consider a situation where a bakery receives cardboard boxes that have been stored in a damp environment. This could lead to mold growth, which would contaminate the baked goods.
Sustainability and Environmental Impact
Cardboard food containers offer a compelling alternative to traditional packaging, especially when considering their environmental footprint. The shift towards sustainable practices is increasingly crucial, and cardboard plays a significant role in reducing waste and conserving resources. Understanding the lifecycle of these containers, from sourcing to disposal, reveals their environmental benefits and potential for further improvement.
Recyclability of Cardboard Food Containers
The recyclability of cardboard food containers is a key factor in their sustainability. Properly recycled cardboard helps conserve natural resources, reduces landfill waste, and lowers energy consumption compared to producing new cardboard from virgin materials. However, the recyclability depends on several factors.
- Contamination: Food residue, grease, and other contaminants can hinder the recycling process. Containers heavily soiled with food waste are often rejected by recycling facilities. Imagine a container stained with pizza grease, a common contaminant that can render the entire batch of cardboard unrecyclable.
- Coatings and Liners: Some cardboard containers have coatings (e.g., wax, plastic) or liners (e.g., plastic films) to provide moisture resistance or grease barriers. These coatings can complicate the recycling process, as they may need to be separated from the cardboard fibers. Consider a coffee cup lined with plastic; the separation process can be complex and costly.
- Recycling Infrastructure: Access to recycling programs and the infrastructure to process cardboard effectively varies geographically. Some communities may not have the facilities to handle all types of cardboard containers. For instance, a rural community might lack a specialized facility to process waxed cardboard.
- Consumer Awareness: Consumers play a crucial role in ensuring proper recycling. Educating consumers about how to prepare cardboard containers for recycling (e.g., removing food residue, separating liners) is vital. Think of a clear label on a takeout container explaining how to prepare it for recycling, including removing any plastic lids or liners.
Sustainable Sourcing and Manufacturing Practices
Sustainable sourcing and manufacturing are integral to minimizing the environmental impact of cardboard food containers. This involves responsible forestry practices and efficient production processes.
- Forest Stewardship Council (FSC) Certification: FSC certification ensures that the wood used to make cardboard comes from responsibly managed forests. These forests are managed to protect biodiversity, water resources, and the rights of indigenous peoples. Visualize a tree with the FSC logo stamped on it, signifying its sustainable origin.
- Recycled Content: Utilizing recycled paper fibers in the manufacturing process reduces the demand for virgin wood pulp. This helps conserve forests and reduces energy consumption. Imagine a cardboard box proudly displaying a label stating it contains 75% recycled content.
- Energy Efficiency: Manufacturers are increasingly adopting energy-efficient production methods to reduce their carbon footprint. This includes using renewable energy sources and optimizing processes to minimize waste. Picture a factory powered by solar panels, demonstrating a commitment to renewable energy.
- Water Conservation: Water is a crucial resource in the paper manufacturing process. Implementing water-saving technologies and recycling water can significantly reduce water consumption. Consider a facility with a closed-loop water system, minimizing water usage and wastewater discharge.
- Reduced Chemical Use: Minimizing the use of chemicals in the manufacturing process is essential. This includes using alternative bleaching methods and reducing the discharge of harmful substances into the environment. Visualize a facility using oxygen-based bleaching methods, a less environmentally damaging alternative.
Environmental Benefits of Using Cardboard Over Other Packaging Materials
Cardboard offers several environmental advantages compared to other packaging materials, such as plastics and expanded polystyrene (Styrofoam).
- Renewable Resource: Cardboard is made from wood, a renewable resource when sourced from sustainably managed forests. Plastics, on the other hand, are derived from fossil fuels, a finite resource. Imagine a forest teeming with trees, contrasted with a dwindling oil reserve.
- Biodegradability: Cardboard is biodegradable, meaning it can break down naturally over time. Plastics can persist in the environment for hundreds of years, leading to pollution and harming wildlife. Consider a discarded cardboard box decomposing in a compost pile versus a plastic bottle littering a beach.
- Lower Carbon Footprint: The production of cardboard generally has a lower carbon footprint than the production of plastics, particularly when recycled content is used. This is because the manufacturing process of plastics often requires more energy and releases more greenhouse gases. Consider a graph comparing the carbon emissions of cardboard production with those of plastic production, highlighting the lower emissions of cardboard.
- Reduced Landfill Waste: Cardboard is more likely to be recycled than plastics, reducing the amount of waste sent to landfills. Landfills contribute to environmental problems, including greenhouse gas emissions and soil contamination. Imagine a landfill overflowing with plastic waste versus a recycling center efficiently processing cardboard.
- Ease of Recycling: Cardboard is widely accepted in recycling programs, making it easier for consumers to dispose of it responsibly. While some plastics are recyclable, the variety of plastic types and the complexity of recycling infrastructure can make it challenging. Consider a community with a comprehensive recycling program that readily accepts cardboard, promoting a circular economy.
Design and Functionality
The design of cardboard food containers is crucial for both consumer experience and operational efficiency. Thoughtful design choices directly impact ease of use, food preservation, and the overall appeal of the product. Furthermore, well-designed containers contribute to streamlined logistics, from production to delivery and consumer handling. The following sections detail key aspects of design and functionality for cardboard food containers.
User Experience Enhancements
Optimizing the user experience is paramount in food packaging design. This encompasses ease of opening and closing, comfortable handling, and clear communication of product information.
- Ergonomic Features: Consider the shape and size of the container for comfortable handling. Curved edges on takeaway boxes can prevent cuts and make them easier to hold. Recessed handles, integrated into the container’s structure, provide a secure grip, especially for larger or heavier items.
- Ease of Opening and Closing: Implement intuitive opening mechanisms. Perforated tear strips allow for easy access to the food. Secure closures, like interlocking flaps or snap-fit lids, prevent spills during transport. A tab-and-slot closure, for instance, allows for secure closing without requiring adhesives, which is ideal for environmentally conscious consumers.
- Visual Appeal: Design containers that are visually appealing to enhance the consumer experience. Use high-quality printing to display attractive graphics, clear product information, and branding elements. Consider the color palette and overall design to reflect the brand identity and appeal to the target audience. For example, a container for gourmet pastries might feature elegant fonts and sophisticated color schemes, while a container for children’s snacks might incorporate bright colors and playful illustrations.
- Food Presentation: Design elements to enhance the presentation of the food. Containers with clear windows or transparent lids allow consumers to view the contents, increasing the perceived value of the product. Compartmentalized containers can separate different food items, preventing them from mixing and preserving their individual flavors and textures.
Optimizing for Stacking, Storage, and Transportation
Efficient design is essential for logistical considerations, impacting storage space, transport costs, and overall supply chain efficiency.
- Stackability: Design containers with features that facilitate stable stacking. Interlocking lids or bases prevent containers from sliding during transport. Recessed areas on the top of the container can nest into the base of the container above, creating a secure and stable stack.
- Storage Efficiency: Consider the storage requirements of the containers. Containers that can be shipped flat and assembled on-site reduce storage space. Collapsible designs also optimize storage space, both before and after use.
- Transportation Durability: The containers must withstand the rigors of transportation. Use robust materials and construction techniques to prevent damage during transit. Reinforced corners and edges add strength to the structure. Consider the impact of temperature and humidity during transportation and choose materials accordingly. For instance, corrugated cardboard offers excellent strength-to-weight ratio, ideal for withstanding stacking and handling forces.
- Dimensional Optimization: Design containers to fit standard pallet sizes. This optimizes space utilization during transport and warehousing. Consider the weight of the container and the food contents to ensure they are within safe handling limits and comply with shipping regulations.
Incorporating Branding and Informational Labels
Effective branding and clear communication are critical for building brand recognition and providing essential information to consumers.
- Branding Elements: Incorporate branding elements that are consistent with the brand’s identity. This includes the logo, brand colors, and unique design features. Consider the placement of branding elements to ensure they are visible and eye-catching.
- Informational Labels: Clearly display essential information on the container. This includes the product name, ingredients, nutritional information, and allergen warnings. The font size and style should be legible and meet regulatory requirements.
- Printing Techniques: Utilize appropriate printing techniques to ensure high-quality branding and labeling. Flexographic printing is a cost-effective option for large-scale production. Offset printing provides high-resolution graphics. Digital printing allows for customization and short print runs.
- Label Placement: Strategic placement of labels can improve visibility and readability. The primary display panel (PDP) is the most visible area and is ideal for the brand name and product image. Side panels can be used for nutritional information and ingredient lists.
- QR Codes and Augmented Reality: Integrate QR codes to provide consumers with additional information, such as recipes, product details, or company information. Consider augmented reality (AR) experiences to enhance engagement. For example, a QR code on a pizza box could launch an AR experience that shows the ingredients and preparation steps.
Cost Analysis and Market Trends
The economic viability and market trajectory of cardboard food containers are critical aspects influencing their adoption and evolution. Understanding the cost dynamics relative to alternatives, alongside the prevailing trends and future innovations, provides a comprehensive perspective on the industry’s potential and challenges. This section analyzes these elements to offer a clear picture of the cardboard container market.
Cost Comparison with Other Packaging Materials, Cardboard containers for food
Comparing the cost of cardboard containers with other packaging materials reveals important trade-offs. Factors such as material sourcing, manufacturing processes, transportation, and end-of-life disposal significantly influence the final price.
Packaging Material | Cost Factors | Advantages | Disadvantages |
---|---|---|---|
Cardboard |
|
|
|
Plastic (e.g., PET, PP) |
|
|
|
Aluminum |
|
|
|
The cost-effectiveness of cardboard containers often hinges on factors such as bulk purchasing, efficient manufacturing processes, and robust recycling infrastructure. For instance, a fast-food chain opting for cardboard packaging might find the initial material cost slightly higher than some plastic alternatives. However, the reduced disposal costs and positive brand image associated with recyclability can offset this difference, resulting in long-term savings and enhanced consumer perception.
Current Market Trends in the Cardboard Food Container Industry
Several key trends are currently shaping the cardboard food container market. These trends reflect consumer preferences, regulatory pressures, and technological advancements.
- Increased Demand for Sustainable Packaging: Consumers are increasingly prioritizing environmentally friendly options. This drives demand for recyclable, compostable, and biodegradable cardboard containers. For example, major food retailers are actively switching from plastic to cardboard packaging to meet consumer demand and reduce their environmental footprint.
- Growth in E-commerce and Food Delivery: The surge in online food ordering and delivery services has boosted the need for robust and reliable packaging solutions. Cardboard containers are well-suited for this purpose, offering protection during transit while being relatively lightweight.
- Customization and Branding: Brands are leveraging cardboard packaging for enhanced branding opportunities. High-quality printing and custom designs on cardboard containers help differentiate products and enhance shelf appeal. This includes the use of vibrant colors, intricate graphics, and informative labeling.
- Focus on Food Safety: Ensuring food safety is paramount. This has led to innovations in cardboard container coatings and liners that prevent grease and moisture leakage while maintaining food integrity. Research into using bio-based coatings, such as those derived from seaweed or plant starches, is also gaining momentum.
- Regulatory Influences: Governments worldwide are implementing stricter regulations on packaging waste and promoting recycling initiatives. These regulations encourage the adoption of sustainable packaging materials like cardboard, creating a favorable market environment.
These trends collectively point towards a dynamic and evolving market where cardboard containers are poised for continued growth.
Forecast Future Innovations and Developments in this Area
The cardboard food container industry is expected to witness significant innovations and developments in the coming years. These advancements will focus on enhancing sustainability, functionality, and cost-effectiveness.
- Advanced Coating Technologies: Expect the development of more effective and environmentally friendly coatings. These will improve barrier properties, making cardboard containers suitable for a wider range of food applications, including those with high grease or moisture content. One example is the development of compostable coatings derived from natural polymers.
- Integration of Smart Technologies: The integration of smart technologies, such as QR codes and RFID tags, into cardboard packaging will become more prevalent. These technologies can provide consumers with information about product origin, recycling instructions, and brand engagement opportunities.
- Enhanced Recyclability and Compostability: Innovations will focus on improving the recyclability and compostability of cardboard containers. This includes the development of easily separable components and the use of materials that break down naturally. Research is underway to create cardboard containers that are fully compostable in home composting systems.
- Lightweighting and Material Optimization: Efforts will be made to optimize the design and material composition of cardboard containers to reduce weight and minimize material usage. This can lead to cost savings and reduced environmental impact through efficient transportation.
- Development of Functional Packaging: Expect to see more specialized cardboard containers with enhanced functionality, such as built-in compartments, portion control features, and easy-to-open designs. This is particularly relevant for ready-to-eat meals and convenience foods.
These future innovations will solidify the position of cardboard containers as a leading packaging solution, driving sustainability and meeting evolving consumer demands.
Examples of Cardboard Containers in Use: Cardboard Containers For Food
Cardboard food containers have evolved beyond simple packaging; they are now integral components of the food industry, showcasing innovation and adaptability. Their versatility allows for a wide range of applications, from preserving freshness to enhancing brand presentation. This section explores real-world examples, highlighting their diverse applications across various food sectors.Cardboard’s success in the food industry stems from its ability to be customized, providing both functionality and an effective branding platform.
Its lightweight nature reduces shipping costs and environmental impact compared to heavier alternatives.
Fast Food Packaging Applications
The fast-food industry extensively utilizes cardboard containers, driven by the need for efficient, portable, and visually appealing packaging. These containers are designed for convenience, ease of handling, and maintaining food quality during transport.
McDonald’s, for example, employs various cardboard containers for its menu items, from the iconic Happy Meal boxes to burger cartons and fry containers. These boxes are often printed with vibrant graphics, reinforcing brand recognition and creating a memorable customer experience.
* Burger Boxes: These are designed to hold burgers securely, preventing them from being crushed and maintaining their temperature. They often feature a clamshell design for easy opening and closing.
Fry Containers
Typically, these are shaped to allow for easy access to fries while preventing them from spilling. They may include features like a small opening for dipping sauces.
Happy Meal Boxes
These are brightly colored and often include interactive elements or games, enhancing the overall customer experience, especially for children.
Bakery and Pastry Applications
Bakeries and pastry shops rely heavily on cardboard containers to showcase and protect their delicate products. These containers are crafted to preserve freshness, prevent damage, and present the baked goods in an attractive manner.
A local bakery may use cardboard boxes with transparent windows to display cakes or pastries, allowing customers to see the product without opening the container. This enhances visual appeal and increases the likelihood of a purchase.
* Cake Boxes: These boxes come in various sizes and shapes, often with handles for easy carrying. They are designed to prevent cakes from shifting during transport and typically feature a secure closure.
Pastry Boxes
Designed for individual pastries or assortments, these boxes often include dividers to keep items separate and prevent them from sticking together. They may also have a grease-resistant coating.
Donut Boxes
Donuts are commonly packaged in boxes that accommodate the shape and size of the donuts. These boxes can range from simple, single-donut containers to larger boxes for a dozen or more donuts.
Produce Packaging Applications
The fresh produce sector utilizes cardboard containers for their breathability, structural integrity, and ability to protect delicate fruits and vegetables during transport. Cardboard helps extend the shelf life of the produce by allowing for air circulation.
Grocery stores often receive produce in cardboard boxes designed for stacking and efficient handling. These boxes are frequently labeled with information about the product, including origin, variety, and best-before dates.
* Fruit Crates: These are sturdy boxes designed to hold various fruits, such as apples, oranges, and berries. They are often vented to allow for air circulation and prevent moisture buildup.
Vegetable Boxes
Used for transporting vegetables like tomatoes, peppers, and leafy greens, these boxes must be strong enough to withstand weight and handling. They may include features like moisture-resistant coatings.
Produce Trays
These trays are often used for pre-packaged produce, such as pre-cut vegetables or fruit salads. They are designed to be visually appealing and allow customers to easily view the product.
Challenges and Considerations
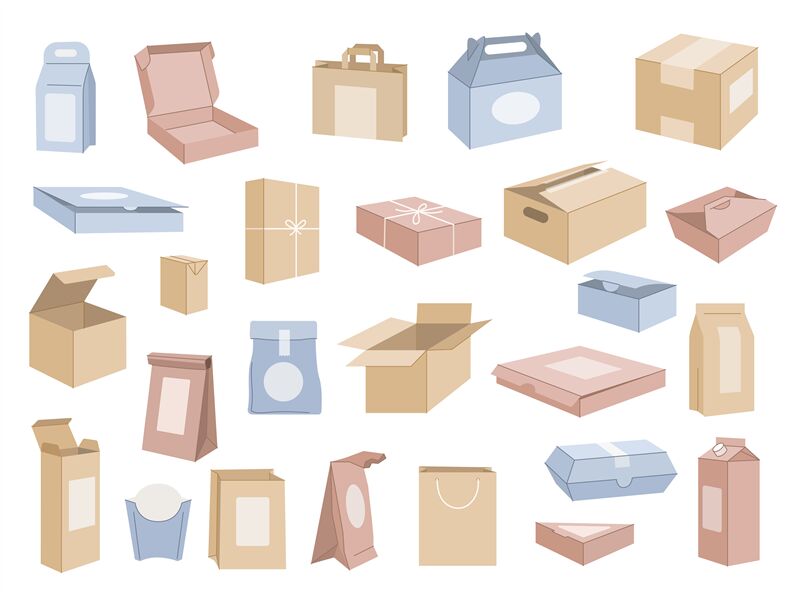
Cardboard containers, while offering numerous benefits, present certain challenges that must be carefully considered to ensure their effective and safe use for food packaging. These challenges relate to the material’s inherent properties and its interaction with various food types and storage conditions. Understanding these limitations is crucial for optimizing the design, manufacturing, and application of cardboard food containers.
Moisture and Grease Resistance
Cardboard’s primary weakness lies in its susceptibility to moisture and grease. These substances can compromise the structural integrity of the container, leading to:
- Weakening of the fibers: Moisture causes the cardboard fibers to swell and lose their rigidity, making the container prone to collapse or tearing. Imagine a paper towel left out in the rain; the same principle applies.
- Grease penetration: Grease can seep through the cardboard, creating unsightly stains, potentially contaminating the food, and reducing the container’s barrier properties. Visualize a greasy pizza box; the grease eventually soaks through.
- Loss of barrier properties: Moisture and grease can degrade the barrier coatings or treatments applied to the cardboard, reducing their effectiveness in preventing the passage of gases, odors, and contaminants.
To mitigate these issues, several strategies are employed:
- Coatings and treatments: Applying wax, polyethylene (PE), or other barrier coatings to the cardboard surface creates a protective layer. These coatings prevent moisture and grease from penetrating the cardboard.
- Lamination: Laminating the cardboard with films, such as PET or foil, provides a superior barrier against moisture, grease, and gases. This method is particularly effective for packaging foods that require extended shelf life.
- Specialized cardboard grades: Using cardboard specifically designed for food packaging, which often includes enhanced moisture and grease resistance properties, can improve performance.
Temperature Sensitivity
Cardboard’s performance can be affected by extreme temperatures.
- High temperatures: Prolonged exposure to high temperatures, such as those encountered during hot food delivery or in ovens (if the container is not designed for it), can cause the cardboard to dry out, become brittle, and potentially ignite. Consider the safety hazard of a pizza box catching fire in a poorly designed oven.
- Low temperatures: Freezing temperatures can also affect cardboard. While the cardboard itself may not degrade significantly, the condensation that forms when frozen food thaws can compromise the container’s structural integrity. Think about a frozen meal container that becomes soggy after thawing.
To address temperature-related challenges:
- Material selection: Choosing cardboard grades with suitable temperature resistance is crucial. For example, cardboard used for oven-safe containers must withstand high temperatures without degrading.
- Coating and design: Employing heat-resistant coatings and designs that minimize direct contact with heat sources can improve performance.
- User instructions: Providing clear instructions on the container regarding temperature limitations (e.g., “Do not microwave” or “Oven safe up to X degrees”) is essential for consumer safety.
Food Compatibility and Migration
Ensuring the compatibility of cardboard containers with the food they hold is paramount to prevent contamination and maintain food safety.
- Migration of substances: Certain substances from the cardboard, such as inks, adhesives, or even components of the cardboard itself, can potentially migrate into the food. This poses a health risk if these substances are not food-grade or are present in excessive amounts.
- Odor transfer: Cardboard can sometimes impart odors or flavors to the food, especially if it’s not properly treated or stored. This can detract from the food’s sensory appeal.
- Chemical reactions: Some foods, particularly those that are acidic or oily, can react with the cardboard, leading to container degradation or the formation of undesirable byproducts.
To ensure food compatibility:
- Food-grade materials: Using only food-grade inks, adhesives, and coatings is crucial. These materials are specifically formulated to minimize the risk of migration.
- Barrier layers: Applying barrier layers, such as PE or foil, between the cardboard and the food can prevent direct contact and reduce the risk of migration.
- Testing and regulations: Adhering to food safety regulations, such as those established by the FDA (in the US) or EFSA (in Europe), and conducting migration testing is essential to ensure compliance and consumer safety.
Structural Integrity and Durability
The structural integrity of cardboard containers must be robust enough to withstand the rigors of handling, transportation, and storage.
- Crushing and deformation: Cardboard containers can be easily crushed or deformed, especially when stacked or subjected to heavy loads. This can damage the food and compromise the container’s functionality.
- Tearing and puncturing: The container may be prone to tearing or puncturing, particularly at corners, seams, or edges. This can lead to spills and contamination.
- Seam failure: Poorly designed or manufactured seams can fail, causing the container to collapse or leak.
To improve structural integrity and durability:
- Cardboard grade and thickness: Selecting a suitable cardboard grade and thickness is essential. Heavier-duty cardboard is better suited for containers that will experience significant handling or stacking.
- Design and construction: Employing robust designs, such as corrugated cardboard with multiple layers, can enhance strength. The design should consider the container’s intended use and the weight of the food it will hold.
- Seam construction: Utilizing strong and reliable seam construction methods, such as proper gluing or stapling, is critical to prevent failure.
Sustainability Considerations
While cardboard is generally considered a sustainable packaging material, certain aspects can impact its environmental footprint.
- Resource consumption: The production of cardboard requires the use of trees, water, and energy. The sustainability of the cardboard depends on responsible forestry practices.
- Recycling challenges: Contamination with food residue, coatings, or other materials can hinder the recycling process. The presence of grease or other non-paper components can make recycling more difficult.
- Waste management: Improper disposal of cardboard containers can contribute to landfill waste. Proper recycling practices are essential to minimize environmental impact.
To enhance sustainability:
- Sourcing and production: Choosing cardboard made from sustainably managed forests (e.g., certified by the Forest Stewardship Council – FSC) and using efficient manufacturing processes can reduce environmental impact.
- Recyclability: Designing containers for recyclability, avoiding non-recyclable coatings or components, and providing clear recycling instructions can facilitate the recycling process.
- Composting: Exploring compostable options, such as compostable coatings or adhesives, can further enhance the environmental benefits of cardboard containers.
Future of Cardboard Food Packaging
The future of cardboard food packaging is poised for significant evolution, driven by technological advancements, shifting consumer demands, and an increasing focus on sustainability. This evolution promises to redefine the way food is packaged, transported, and consumed, impacting both the industry and the environment. The following sections will delve into anticipated innovations, the influence of consumer preferences, and the role of technology in shaping the future of this crucial packaging material.
Forecast Future Innovations in the Design and Use of Cardboard Containers
The landscape of cardboard food packaging is expected to undergo substantial transformations, fueled by innovation. These innovations aim to improve functionality, sustainability, and consumer experience.
- Smart Packaging Integration: Imagine a pizza box that monitors the internal temperature, humidity, and even the freshness of the pizza inside. This is the promise of smart packaging. Sensors embedded within the cardboard could communicate this data to the consumer via a smartphone app, ensuring food safety and quality. Further, incorporating NFC (Near Field Communication) tags could allow for enhanced product information, recipes, and even loyalty program integration.
- Enhanced Barrier Properties: Current cardboard packaging often requires additional coatings or liners to provide effective barriers against moisture, grease, and oxygen. Future innovations will likely focus on developing cardboard materials with inherent barrier properties, reducing the need for these often non-recyclable additions. This could involve utilizing new materials like biodegradable coatings or modifying the cardboard’s structure at the nanoscale to create effective barriers.
- Active Packaging Technologies: Active packaging goes beyond simply protecting the food; it actively interacts with it. For example, cardboard could be infused with antimicrobial agents to extend shelf life, or with oxygen scavengers to prevent spoilage. These technologies will be particularly valuable for perishable goods, reducing food waste and improving consumer convenience.
- Customization and Personalization: With advances in digital printing and flexible manufacturing, cardboard packaging will become increasingly customizable. Brands can create packaging tailored to specific products, target audiences, and even individual consumers. This personalization could extend to incorporating interactive elements, such as QR codes that link to augmented reality experiences or personalized offers.
- Modular and Reusable Designs: Future designs might prioritize modularity, allowing consumers to easily reconfigure or repurpose cardboard containers. Reusable cardboard containers, perhaps with durable coatings and designs that facilitate easy cleaning, could become more prevalent, reducing waste and promoting a circular economy.
Predict the Impact of Changing Consumer Preferences on Cardboard Packaging
Consumer preferences are a driving force in the evolution of packaging, and the future of cardboard food containers will be significantly shaped by these changing demands.
- Sustainability as a Core Value: Consumers are increasingly concerned about the environmental impact of their purchases. This will drive demand for cardboard packaging made from recycled materials, sourced sustainably, and designed for recyclability. Brands will need to demonstrate their commitment to sustainability through transparent sourcing, clear labeling, and packaging designs that minimize waste.
- Convenience and Functionality: While sustainability is crucial, consumers also expect packaging to be convenient and functional. Cardboard containers will need to be easy to open, resealable, and designed to protect food during transport and storage. This will involve innovations such as improved closures, ergonomic designs, and features that enhance the user experience.
- Transparency and Information: Consumers want to know what they are buying, including the ingredients, nutritional information, and the environmental impact of the packaging. Cardboard packaging will need to provide clear and comprehensive information, potentially through QR codes or other interactive elements. This transparency builds trust and empowers consumers to make informed choices.
- Demand for Eco-Friendly Alternatives to Plastics: A significant shift towards reducing plastic consumption is underway. Cardboard offers a viable, renewable, and often more sustainable alternative to plastic packaging for a wide range of food products. This trend will accelerate the adoption of cardboard in areas traditionally dominated by plastics, like take-out containers, food trays, and beverage carriers.
- Influence of E-commerce: The growth of online food delivery and grocery shopping will significantly impact packaging design. Cardboard containers will need to be robust enough to withstand the rigors of shipping, while also maintaining food quality and appearance. This will necessitate innovations in packaging materials, cushioning, and sealing to ensure products arrive in perfect condition.
Illustrate the Role of Technology in Enhancing Cardboard Container Functionality
Technology plays a pivotal role in transforming cardboard food containers, enhancing their functionality, and creating new possibilities for the industry.
- Digital Printing and Design: Advanced digital printing technologies allow for high-resolution graphics, intricate designs, and on-demand customization of cardboard packaging. This enables brands to create visually appealing packaging that communicates their message effectively and can be tailored to specific marketing campaigns or product lines. Digital printing also reduces waste by eliminating the need for large print runs.
- Material Science and Engineering: Innovations in material science are leading to the development of new cardboard materials with enhanced properties. This includes the use of bio-based coatings, nanotechnology for improved barrier performance, and engineered cardboard structures for increased strength and durability. These advancements improve the performance and sustainability of cardboard packaging.
- Automation and Robotics: Automation and robotics are transforming the manufacturing processes of cardboard containers. Robots can efficiently handle tasks such as cutting, folding, gluing, and assembling packaging, increasing production speed, reducing labor costs, and improving consistency. This allows for more complex and innovative packaging designs.
- Data Analytics and Optimization: Data analytics can be used to optimize the design, production, and distribution of cardboard packaging. By analyzing data on consumer behavior, supply chain efficiency, and environmental impact, companies can make informed decisions to improve their packaging strategies, reduce waste, and enhance sustainability.
- Smart Packaging and IoT Integration: As mentioned earlier, the integration of smart technologies like sensors, NFC tags, and QR codes is revolutionizing cardboard packaging. These technologies provide valuable data on product condition, track and trace capabilities, and opportunities for enhanced consumer engagement. This integration creates a more connected and intelligent packaging ecosystem.
Closing Summary
In conclusion, cardboard containers for food have emerged as a pivotal element in the food industry, balancing functionality, cost-effectiveness, and environmental responsibility. The adaptability of cardboard, coupled with advancements in materials science and manufacturing, positions these containers for continued growth and innovation. By understanding the complexities of their design, materials, and regulatory landscape, stakeholders can leverage cardboard’s potential to enhance food safety, promote sustainability, and cater to evolving consumer preferences.
The future of cardboard packaging appears promising, with ongoing developments aimed at optimizing performance and reducing environmental impact, ensuring its sustained relevance in a dynamic market.