Foam food tray, a ubiquitous presence in the modern food industry, has significantly shaped how we package, transport, and consume food. From its humble beginnings, this versatile packaging solution has evolved to meet the demands of a globalized food supply chain. This presentation will delve into the history, purpose, and manufacturing of foam food trays, exploring their impact on food preservation, cost-effectiveness, and logistical efficiency.
We will explore the diverse types and applications of foam food trays, examining their advantages and disadvantages. This will include a critical assessment of their environmental impact, potential health concerns, and limitations. Furthermore, we will analyze alternative packaging solutions, regulatory frameworks, and the ongoing innovations shaping the future of this essential packaging component.
Introduction to Foam Food Trays
Foam food trays have become ubiquitous in the food industry, serving as a convenient and cost-effective solution for packaging and transporting various food items. Their lightweight nature, coupled with their ability to provide insulation and cushioning, has made them a popular choice for both consumers and businesses. This section will delve into the history, purpose, and materials associated with these widely used trays.
Historical Context of Foam Food Tray Usage
The evolution of foam food trays reflects advancements in material science and packaging technology. The development and adoption of these trays occurred over several decades, driven by a need for more efficient and affordable food packaging solutions.The initial use of foam food trays can be traced back to the mid-20th century, coinciding with the rise of fast-food restaurants and supermarkets.
Early versions were primarily made from polystyrene, a type of plastic known for its insulating properties. The 1960s and 1970s saw a surge in their popularity, particularly in the packaging of meat, poultry, and produce, due to their ability to extend shelf life and reduce spoilage.By the 1980s, concerns regarding the environmental impact of polystyrene began to surface. The material was not easily biodegradable, and its disposal contributed to landfill waste.
This led to a search for alternative materials and manufacturing processes.
Primary Purpose of Foam Food Trays
Foam food trays serve several crucial functions in the food supply chain, primarily centered around preservation, protection, and presentation. Their design facilitates safe and efficient handling from the point of origin to the consumer.
- Food Preservation: The insulating properties of foam trays help maintain the temperature of food items, whether hot or cold. This is particularly important for perishable goods like meat, fish, and prepared meals, as it helps to slow down bacterial growth and extend shelf life. For example, consider a supermarket display of fresh seafood. Foam trays help keep the fish cold, maintaining freshness and preventing spoilage.
- Product Protection: The cushioning effect of foam trays protects food items from physical damage during transportation and handling. This is especially crucial for fragile items like eggs, fruits, and vegetables. For instance, an egg carton made of foam provides a layer of protection that minimizes the risk of breakage during transit from the farm to the grocery store.
- Convenience and Presentation: Foam trays provide a convenient platform for displaying and packaging food items. They can be easily sealed with plastic wrap, making them tamper-evident and enhancing food safety. Furthermore, they contribute to the overall presentation of the food, making it more appealing to consumers. Consider the pre-packaged deli meats or cheeses found in a grocery store; the tray facilitates portioning and labeling.
Common Materials Used in Manufacturing Foam Food Trays
The materials used in the production of foam food trays have evolved over time, reflecting changes in technology, environmental concerns, and regulatory requirements. The primary goal in material selection is to balance functionality, cost-effectiveness, and environmental impact.
- Expanded Polystyrene (EPS): This is the most common material used in foam food trays. EPS is lightweight, inexpensive, and provides excellent insulation and cushioning. However, it is not biodegradable and contributes to landfill waste. It is also known to be difficult to recycle, which has led to restrictions on its use in some regions.
- Expanded Polypropylene (EPP): EPP is a more environmentally friendly alternative to EPS. It is recyclable and can withstand higher temperatures. EPP trays are often used for packaging hot food items. While EPP is more expensive than EPS, its recyclability makes it a more sustainable option.
- Biodegradable Materials: There is a growing trend towards using biodegradable materials in foam food tray manufacturing. These materials include plant-based starches, such as cornstarch and sugarcane. These trays are designed to break down naturally in compost environments. The use of these materials is still limited, as they can be more expensive and may not provide the same level of protection as traditional plastics.
An example would be the tray used for a pre-packaged salad kit, now commonly made of compostable materials.
Types and Varieties
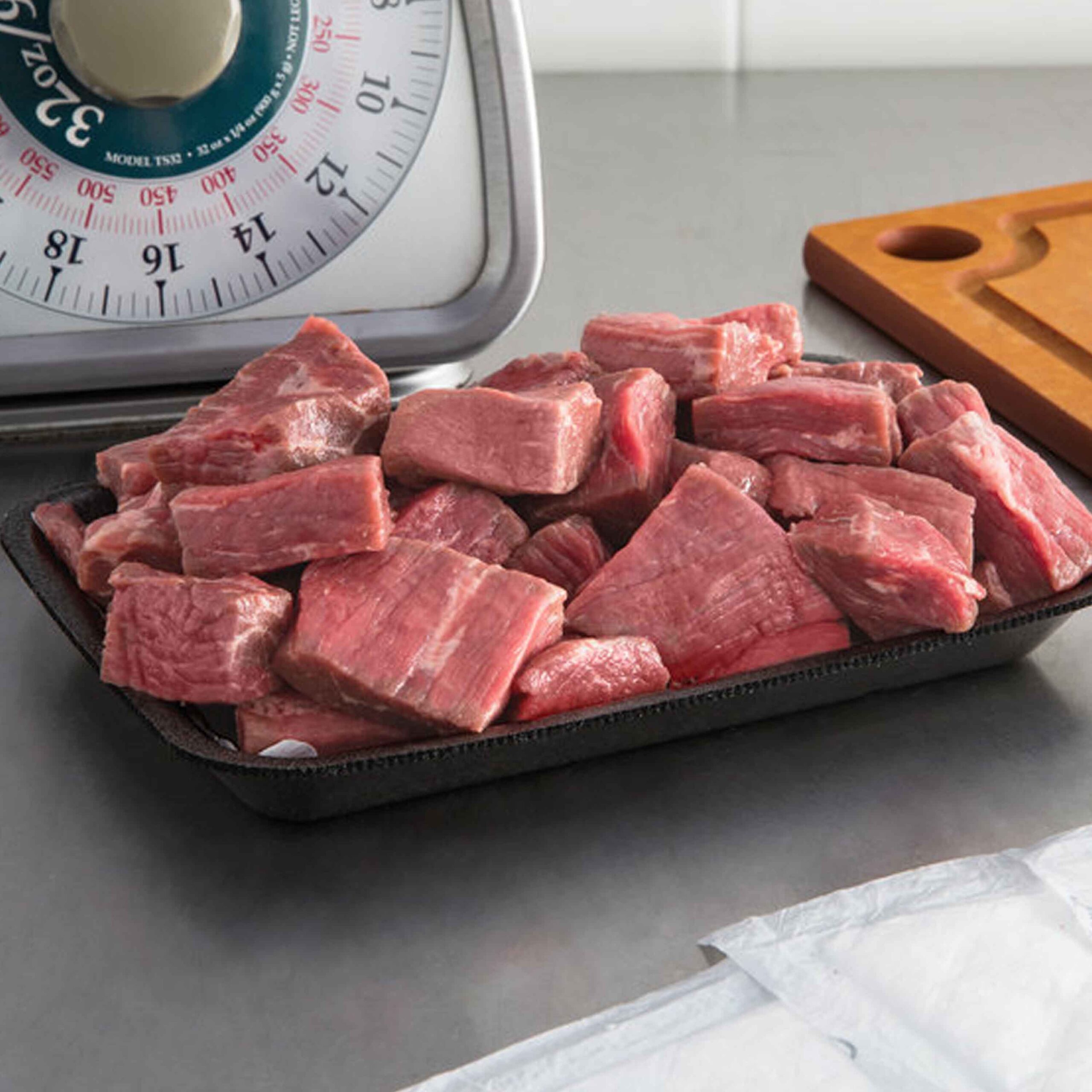
Foam food trays are manufactured in a wide array of shapes, sizes, and densities to accommodate diverse food products and their specific needs. This variety allows for optimized food presentation, preservation, and transportation. The design considerations often depend on the type of food, its intended shelf life, and the demands of the supply chain.
Shapes and Sizes
The dimensions and configurations of foam food trays are highly variable. This flexibility allows manufacturers to cater to a broad spectrum of food items, from small portions to large cuts.
- Rectangular Trays: These are the most common, suitable for packaging meats, poultry, produce, and prepared meals. They offer efficient stacking and storage. Examples include trays sized for a single steak, a pound of ground beef, or a family-sized portion of lasagna.
- Square Trays: Often used for smaller portions, such as individual servings of cookies, slices of cake, or pre-cut vegetables.
- Oval Trays: These trays are commonly seen in the seafood industry, designed to showcase fish fillets or shellfish.
- Compartmentalized Trays: These feature multiple sections within a single tray, ideal for pre-portioned meals with different food components (e.g., a main course, side dish, and dessert).
- Custom Shapes: Manufacturers can create custom tray shapes to fit specific food items or branding requirements. This can include trays designed for specialty bakery items or unique product presentations.
Trays for Specific Food Types
Different food products necessitate specialized tray designs to maximize preservation, presentation, and handling efficiency. These trays are often tailored to meet the specific requirements of the food they contain.
- Meat Trays: Meat trays typically have absorbent pads at the bottom to collect any liquids that might exude from the meat. This helps maintain the meat’s appearance and prevents spoilage. They come in various sizes to accommodate different cuts and weights.
- Produce Trays: Produce trays often feature ventilation holes to allow for air circulation, which helps to reduce moisture buildup and extend the shelf life of fruits and vegetables. They are available in sizes appropriate for berries, grapes, or pre-cut salads.
- Prepared Meal Trays: These trays are frequently designed to be microwave-safe and may have compartments for different food items. They are intended to provide convenience for consumers, offering an easy way to heat and consume pre-made meals.
- Seafood Trays: Seafood trays, as previously mentioned, are often oval or shaped to present seafood aesthetically. They may include absorbent pads to capture liquids.
Foam Densities and Applications
The density of foam used in food trays significantly impacts their performance characteristics, including rigidity, insulation, and cushioning. The selection of foam density is a critical factor in matching the tray to the specific needs of the food product.
- Low-Density Foam: Low-density foam trays are typically more flexible and cost-effective. They are suitable for lighter food items or where cushioning is not a primary concern. Examples include trays for bakery goods or produce.
- Medium-Density Foam: Medium-density foam provides a balance between rigidity and cushioning. These trays are commonly used for meat, poultry, and prepared meals, where a degree of structural integrity is needed.
- High-Density Foam: High-density foam offers greater structural strength and insulation properties. These trays are sometimes used for more delicate or heavier items, or where extended temperature control is required. They can be found in specialized applications.
Advantages of Using Foam Food Trays
Foam food trays offer a multitude of benefits that make them a popular choice in the food industry. These advantages span from preserving food quality and reducing costs to facilitating efficient handling and transportation. Their lightweight nature and insulating properties contribute significantly to their widespread use.
Food Preservation with Foam Trays
Foam food trays are designed to extend the shelf life and maintain the quality of food products. Their structure and composition play a crucial role in this process.The primary function of foam trays in food preservation is their ability to regulate temperature. They provide a layer of insulation, which helps to maintain a consistent temperature, whether the food is hot or cold.
This insulation helps to prevent rapid temperature fluctuations that can degrade food quality. For instance, consider a tray of pre-cooked chicken. A foam tray will help keep the chicken warm for a longer duration, minimizing the chance of bacterial growth and keeping the food safe for consumption.
- Insulation: The cellular structure of foam trays creates air pockets, which act as insulators. This insulation helps to slow down the transfer of heat, keeping cold items cold and hot items hot for extended periods.
- Moisture Control: Foam trays can also help to manage moisture levels. They often absorb excess moisture, preventing condensation that can lead to spoilage. This is especially important for fresh produce and meats.
- Protection from External Factors: Foam trays provide a physical barrier that protects food from external contaminants such as dust, dirt, and physical damage during handling and transportation. This barrier helps to maintain the integrity and appearance of the food.
Cost-Effectiveness of Foam Food Trays
Compared to alternative packaging materials, foam food trays offer a significant cost advantage, particularly for businesses that handle large volumes of food products. Several factors contribute to their cost-effectiveness.The low cost of production is a major factor. The raw materials used to manufacture foam trays are generally inexpensive and readily available. Furthermore, the manufacturing process is relatively simple and efficient, which further reduces production costs.
This translates to lower prices for consumers.
- Lower Material Costs: The materials used to produce foam trays, such as polystyrene, are typically less expensive than alternatives like cardboard or rigid plastics.
- Reduced Transportation Costs: Foam trays are lightweight, which reduces shipping costs. This is especially beneficial for businesses that distribute food products over long distances. For example, a large food distributor might save thousands of dollars annually on shipping costs by using foam trays instead of heavier alternatives.
- Waste Reduction: The design of foam trays often minimizes food waste. Their ability to maintain food quality and extend shelf life means less food is discarded due to spoilage.
- Availability and Accessibility: Foam trays are widely available, making them easy to source and purchase in bulk, contributing to cost savings.
Efficient Food Handling and Transportation with Foam Trays
Foam food trays are designed to facilitate efficient handling and transportation of food products, streamlining operations for food businesses.Their lightweight nature is a key advantage. This makes them easy to handle, load, and unload, reducing labor costs and the risk of worker fatigue. Their stacking capabilities are also a significant benefit. They can be easily stacked, maximizing space utilization during storage and transportation.
- Lightweight Design: The lightweight nature of foam trays simplifies handling, reducing the physical strain on workers and increasing efficiency. This is particularly useful in busy environments like supermarkets and food processing plants.
- Stackability: Foam trays are designed to be stacked, allowing for efficient use of storage space and reducing the amount of space required for transportation. This is especially important for businesses that handle large volumes of food products.
- Durability: While lightweight, foam trays are surprisingly durable. They can withstand the rigors of handling and transportation, protecting the food products from damage.
- Versatility: Foam trays come in a variety of shapes and sizes, making them suitable for a wide range of food products, from delicate pastries to large cuts of meat. This versatility simplifies packaging operations.
Disadvantages and Concerns
While foam food trays offer several advantages, it’s crucial to acknowledge their drawbacks and the potential concerns associated with their use. These disadvantages span environmental, health, and practical considerations. Understanding these limitations is essential for making informed decisions regarding their application and exploring viable alternatives.
In this topic, you find that sun chinese food is very useful.
Environmental Impact of Foam Food Tray Disposal
The environmental impact of foam food trays is significant due to the material’s composition and disposal challenges. Polystyrene, the primary component of foam food trays, is a non-biodegradable plastic. This characteristic leads to long-term environmental consequences.
- Landfill Accumulation: Foam food trays take hundreds of years to decompose, leading to their accumulation in landfills. This contributes to the growing problem of landfill space scarcity and the associated environmental burdens. For example, according to the Environmental Protection Agency (EPA), plastics make up a substantial portion of municipal solid waste, and expanded polystyrene (EPS) is a significant contributor to this waste stream.
- Difficulty in Recycling: Recycling foam food trays is often challenging. Many municipalities lack the infrastructure to effectively recycle EPS due to its low density and the potential for contamination from food residue. This results in a low recycling rate for foam food trays.
- Litter and Marine Pollution: Discarded foam food trays can easily become litter, polluting streets, parks, and waterways. This litter can then make its way into oceans, contributing to marine debris and posing a threat to marine life. Foam breaks down into smaller pieces, becoming microplastics, which can be ingested by marine animals, potentially entering the food chain.
- Manufacturing Emissions: The production of foam food trays involves the use of fossil fuels and the release of greenhouse gases. The manufacturing process contributes to climate change and other environmental issues.
Potential Health Risks Associated with Foam Food Tray Use
The use of foam food trays raises certain health concerns, primarily related to the potential for chemical migration and the impact of heat exposure.
- Chemical Migration: Styrene, the monomer used to produce polystyrene, can potentially leach from foam food trays into food, particularly when the food is hot or contains fats. The FDA has established limits for styrene migration, but concerns remain about long-term exposure.
- Heat Exposure: Heating food in foam food trays can increase the risk of styrene migration. Microwaving food in foam trays is generally not recommended due to the potential for the tray to melt and release chemicals.
- Styrene Exposure: Chronic exposure to styrene has been linked to potential health effects, including nervous system effects and possible carcinogenic effects. The International Agency for Research on Cancer (IARC) has classified styrene as a possible human carcinogen.
- Food Contamination: The porous nature of foam can potentially harbor bacteria if not properly cleaned, increasing the risk of foodborne illnesses. While not directly a chemical risk, it contributes to the health concern associated with the use of foam food trays.
Limitations of Foam Food Trays Regarding Temperature Resistance
Foam food trays have inherent limitations regarding their temperature resistance, affecting their suitability for certain food applications and handling practices.
- Low Melting Point: Foam food trays have a relatively low melting point, typically around 212°F (100°C). This means they can melt or deform when exposed to high temperatures, such as those encountered in ovens, microwaves, or when containing very hot food.
- Microwave Use Restrictions: Due to their low melting point, foam food trays are generally not suitable for microwave use. Microwaving food in these trays can lead to the release of chemicals and potential damage to the tray.
- Limited Hot Food Applications: While foam food trays can be used for some hot food items, their temperature resistance limits their use for foods that are extremely hot or require prolonged heat exposure.
- Storage Considerations: Foam food trays should be stored away from heat sources to prevent deformation or melting. Direct sunlight or proximity to heat-generating appliances can also damage the trays.
Alternatives to Foam Food Trays
Considering the environmental and health concerns associated with foam food trays, exploring viable alternatives is crucial. These alternatives offer various benefits, ranging from biodegradability to reusability, providing options that cater to different needs and priorities. Understanding these alternatives allows for informed decisions that can reduce the reliance on foam and promote more sustainable practices in food packaging.
Biodegradable Alternatives Compared
Several biodegradable materials have emerged as alternatives to foam food trays. These materials aim to decompose naturally, minimizing environmental impact. The following table compares some of the most common biodegradable alternatives, highlighting their advantages, disadvantages, and associated costs.
Material | Advantages | Disadvantages | Cost |
---|---|---|---|
Plant-based Plastics (PLA) |
|
|
Generally more expensive than foam, but costs are decreasing with increased production. |
Molded Pulp (e.g., sugarcane, bamboo) |
|
|
Moderately priced, often comparable to or slightly more expensive than foam. |
Paper-based Products (coated paperboard) |
|
|
Cost-effective, often comparable to or slightly less expensive than foam. |
Other Bio-based materials (e.g., mushroom packaging) |
|
|
Typically more expensive than foam, but prices are decreasing. |
Properties of Paperboard Food Trays
Paperboard food trays offer a versatile alternative to foam, utilizing paper-based materials. They are generally made from paper pulp and can be coated with various substances to enhance their performance.Paperboard trays are commonly used in various applications, including fast food restaurants, grocery stores, and food delivery services. They are often favored for their affordability and the ability to be printed with branding and other information.
These trays can be coated with different materials to provide resistance to grease and moisture, making them suitable for a wide array of food items. For example, wax coatings offer basic moisture resistance, while polyethylene (PE) coatings provide more robust protection. Some paperboard trays are also coated with biodegradable materials, increasing their environmental friendliness. While paperboard trays are generally recyclable, the presence of coatings can affect their recyclability depending on the specific coating used and the recycling infrastructure available.
Use of Reusable Containers
Reusable containers represent a sustainable alternative to single-use foam trays, particularly in settings where food is consumed on-site or frequently transported. These containers are designed to be used multiple times, significantly reducing waste and environmental impact.Reusable containers are commonly made from durable materials such as polypropylene (PP), stainless steel, or glass. These materials are chosen for their ability to withstand repeated use, washing, and handling.
Polypropylene containers are lightweight and often microwave-safe, making them convenient for various applications. Stainless steel offers durability and resistance to staining, while glass provides a non-reactive surface, ideal for food storage.The adoption of reusable containers is often encouraged through incentives like discounts for customers who bring their own containers. Some businesses offer container exchange programs, where customers can swap used containers for clean ones.
These practices promote a circular economy, where materials are kept in use for as long as possible.
Regulations and Standards
The production and use of foam food trays are subject to a complex web of regulations and standards designed to protect public health and the environment. These regulations vary significantly by region, reflecting differing priorities and environmental concerns. Understanding these requirements is crucial for manufacturers, distributors, and businesses using these trays.
Regional Regulations on Production and Use
Regulations concerning foam food trays vary considerably across different geographical areas. Some regions have implemented outright bans, while others impose restrictions or specific requirements.
- United States: Regulations are primarily handled at the state and local levels. Some states, such as California, Maine, and Vermont, have banned polystyrene foam food containers. Many cities and counties also have their own bans or restrictions. The Food and Drug Administration (FDA) regulates the materials used in food packaging, including foam trays, ensuring they are safe for food contact.
The FDA’s focus is primarily on food safety, rather than environmental concerns directly.
- European Union: The EU has taken a more comprehensive approach. In 2018, the EU implemented a ban on single-use plastic items, including polystyrene foam food containers, as part of its strategy to reduce plastic pollution. This ban took effect in July 2021. The focus is on reducing waste and promoting sustainable alternatives.
- Canada: Regulations vary by province and municipality. Some provinces have banned or restricted the use of foam food trays, while others have not. Municipalities often have the authority to implement their own bylaws regarding single-use plastics.
- Asia: Regulations are emerging, with some countries implementing bans or restrictions on foam food trays. China, for example, has implemented regulations to reduce plastic pollution, which may include restrictions on foam containers. The specific regulations and their enforcement vary across different countries within the region.
- Australia: Regulations are also variable, with different states and territories adopting different approaches. Some states and territories have banned or restricted the use of foam food trays. The focus is on reducing waste and promoting sustainable alternatives.
Food Safety Standards for Foam Food Trays
Ensuring the safety of food packaging is paramount. Several standards and regulations govern the materials and manufacturing processes used for foam food trays to prevent the migration of harmful substances into food.
- FDA Regulations (United States): The FDA sets standards for materials that come into contact with food. Foam food trays must comply with these regulations, ensuring that the materials used are safe and do not leach harmful chemicals into the food. This includes requirements for the types of polymers that can be used, the manufacturing processes, and the testing that must be conducted.
- European Food Safety Authority (EFSA) Standards (European Union): EFSA assesses the safety of food contact materials, including foam trays. They set limits on the migration of substances from the packaging into food. These standards are rigorously enforced to protect consumers.
- Testing and Certification: Manufacturers often subject their products to testing by independent laboratories to ensure compliance with food safety standards. These tests can assess the migration of chemicals, the overall safety of the materials, and the suitability of the trays for different types of food.
- Good Manufacturing Practices (GMP): Manufacturers must adhere to GMP to ensure that the production process is controlled and that the products are consistently safe and of good quality. This includes hygiene standards, quality control procedures, and proper documentation.
Labeling Requirements for Foam Food Trays
Proper labeling is crucial for providing consumers with essential information about the product, including its composition, intended use, and disposal instructions. Labeling requirements vary by region and are subject to change.
- Material Identification: Labels typically must identify the material from which the tray is made. For example, it must state “polystyrene foam” or “expanded polystyrene (EPS)”.
- Recycling Symbols: Labels often include recycling symbols, which can vary depending on the region. These symbols indicate whether the tray is recyclable and, if so, how it should be disposed of. For example, the resin identification code (a number inside a triangle of arrows) indicates the type of plastic.
- Food Contact Information: Labels must state that the tray is safe for food contact, or must indicate any specific limitations. This might include information about the types of food that can be safely placed in the tray or temperature limitations.
- Manufacturer Information: Labels typically must include the manufacturer’s name and address, as well as any relevant contact information.
- Compliance Statements: Labels may include statements confirming that the product complies with relevant regulations, such as FDA or EFSA standards.
- Country of Origin: The country of origin must be clearly stated on the label.
Manufacturing Process
The creation of foam food trays is a complex process involving several key stages. This process requires specialized machinery and strict quality control to ensure the trays meet the necessary standards for food safety and functionality. The manufacturing process can be broken down into distinct steps, each playing a crucial role in the final product’s quality.
Raw Material Preparation
The initial step involves preparing the raw materials, primarily polystyrene. This material is usually supplied in the form of small beads.
- Bead Pre-expansion: The polystyrene beads are first pre-expanded using steam. This process increases their volume, creating the foam structure. The steam heats the beads, causing the blowing agent (typically a hydrocarbon gas like pentane) inside them to expand. This expansion makes the beads much larger and lighter. The extent of the expansion determines the density of the final foam tray.
Lower density trays use more expanded beads.
- Bead Aging: After pre-expansion, the beads are allowed to “age” or stabilize. This process typically takes place in large storage silos. During aging, the beads dry out and air replaces some of the blowing agent, which helps stabilize the foam structure and improve its performance during the molding process.
Molding Process
The molding process shapes the foam trays into their final form. This process utilizes specialized machinery.
- Molding Machines: The pre-expanded and aged beads are fed into a molding machine. This machine consists of two halves of a mold, which close to form the tray’s shape. The mold cavities are often complex, designed to accommodate various tray sizes and shapes.
- Steam Injection: Steam is injected into the mold, further expanding the beads and fusing them together. The steam also heats the mold, ensuring the polystyrene softens and conforms to the mold’s shape.
- Cooling: After the steam injection, the mold is cooled, typically using water. This step solidifies the foam structure and allows the tray to retain its shape. The cooling time is crucial; insufficient cooling can lead to warping or deformation.
- Ejection: Once cooled, the mold opens, and the formed foam tray is ejected.
Trimming and Finishing
Following the molding process, the trays undergo trimming and finishing to remove excess material and ensure a consistent product.
- Trimming: Trimming machines remove any excess foam or “flash” (extra material) from the edges of the trays. This ensures the trays have a clean and uniform appearance.
- Inspection: The trays undergo visual inspection to identify any defects, such as holes, cracks, or uneven surfaces. This quality control step is critical for ensuring the trays meet the required standards.
- Stacking and Packaging: The trimmed and inspected trays are then stacked and packaged for shipment. Packaging typically involves wrapping the trays in plastic film or placing them in cardboard boxes to protect them during transportation.
Role of Machinery and Equipment
Various types of machinery are essential for the efficient and effective production of foam food trays. Each machine plays a specific role in the manufacturing process.
- Pre-expanders: These machines use steam to expand the polystyrene beads, increasing their volume. The pre-expansion process determines the density and overall properties of the final product.
- Molding Machines: These machines are the core of the manufacturing process, shaping the expanded beads into the desired tray forms. They employ steam injection, cooling systems, and mold clamping mechanisms.
- Trimming Machines: These machines precisely cut away excess material from the trays, ensuring a consistent shape and size.
- Conveyor Systems: Conveyor belts transport materials and products between different stages of the manufacturing process, optimizing efficiency.
- Quality Control Equipment: This includes inspection stations with visual and sometimes automated inspection systems to identify defects and ensure product quality.
Quality Control Measures
Rigorous quality control measures are implemented throughout the manufacturing process to ensure the foam food trays meet the required standards for food safety and functionality.
- Raw Material Inspection: Incoming polystyrene beads are inspected to ensure they meet the required specifications. This includes checking the bead size, density, and purity.
- Process Monitoring: During the molding process, parameters such as steam pressure, temperature, and cooling time are continuously monitored to ensure consistency and prevent defects.
- Visual Inspection: Trained personnel conduct visual inspections at various stages of the process to identify any defects, such as holes, cracks, or uneven surfaces.
- Dimensional Checks: Trays are regularly checked for dimensional accuracy to ensure they meet the specified size and shape requirements.
- Performance Testing: Finished trays are subjected to performance tests to evaluate their strength, durability, and ability to withstand various temperatures and conditions. This might involve drop tests, load tests, or tests to assess the tray’s resistance to moisture and grease.
- Compliance with Regulations: The manufacturing process adheres to all relevant regulations and standards, such as those related to food contact materials. This includes ensuring the trays are made from approved materials and are manufactured in a clean and sanitary environment.
Usage in the Food Industry
Foam food trays have become an integral part of the food industry, playing a crucial role in packaging, presentation, and distribution. Their versatility and cost-effectiveness have led to widespread adoption across various sectors, from supermarkets to food delivery services. This section will explore the diverse applications of foam food trays within the food industry, highlighting their impact on operational efficiency, food safety, and consumer experience.
Applications in Supermarkets, Restaurants, and Food Delivery
Foam food trays find extensive application across different segments of the food industry, contributing significantly to operational efficiency and consumer convenience.
- Supermarkets: Supermarkets heavily rely on foam trays for packaging fresh produce, meats, and seafood. These trays provide a cost-effective solution for displaying and protecting food items, extending shelf life, and maintaining product quality. Pre-packaged items like sliced meats and cheeses are commonly presented on foam trays, sealed with plastic film to ensure freshness and prevent contamination. For example, a typical supermarket might use foam trays to package approximately 80% of its fresh meat and poultry products.
- Restaurants: Restaurants, particularly those offering takeout or delivery services, utilize foam trays for packaging prepared meals. These trays help to maintain food temperature, prevent spillage, and facilitate convenient handling. Restaurants offering family-style meals often use larger foam trays to accommodate multiple servings. The use of foam trays in restaurants is particularly prevalent in fast-food establishments and casual dining settings, where speed and efficiency are paramount.
- Food Delivery Services: The rise of food delivery services has further increased the demand for foam trays. These trays are essential for transporting meals safely and securely from restaurants to customers’ homes. They provide insulation to maintain food temperature and prevent leaks or damage during transit. The growing popularity of online food ordering has made foam trays a critical component of the food delivery infrastructure.
Role in Portion Control and Food Presentation
Foam food trays play a significant role in portion control and enhancing the visual appeal of food products. Their design allows for precise measurement and presentation, contributing to both operational efficiency and consumer satisfaction.
- Portion Control: Foam trays are available in various sizes and shapes, making them suitable for portioning different food items. By using pre-portioned trays, food service providers can ensure consistent serving sizes, which helps in managing food costs and reducing waste. For example, a restaurant might use specific tray sizes for different entrees to guarantee accurate portioning.
- Food Presentation: Foam trays provide a clean and organized platform for presenting food items. The white color of many foam trays enhances the visual appeal of the food, making it more attractive to consumers. The ability to wrap and seal trays with clear plastic film allows for a clear view of the product, further enhancing its presentation. The use of foam trays in meat and seafood departments, for example, highlights the quality and freshness of the products.
Evolution of Foam Food Tray Designs
The design of foam food trays has evolved over time to meet the changing demands of the food industry, with a focus on improving functionality, sustainability, and consumer experience.
- Enhanced Insulation: Early foam trays primarily focused on structural integrity. Newer designs incorporate improved insulation properties to better maintain food temperature. This is especially crucial for hot food delivery and the preservation of perishable items.
- Leak-Resistant Features: Modern foam trays often feature leak-resistant designs, such as sealed edges and absorbent pads, to prevent spills and maintain food quality during transportation. These features are essential for food delivery services and takeout operations.
- Sustainable Alternatives: The industry is increasingly exploring sustainable alternatives to traditional polystyrene foam, such as trays made from recycled materials or biodegradable materials. These alternatives aim to reduce the environmental impact of foam food trays while maintaining their functionality. For instance, some supermarkets are transitioning to trays made from recycled PET (polyethylene terephthalate) or plant-based materials.
- Customization and Branding: Manufacturers are increasingly offering customized foam trays with branding options. This allows food businesses to enhance their brand identity and provide a more professional presentation. This includes options for printing logos and product information directly onto the trays.
Innovations and Future Trends
The food packaging industry is in constant flux, driven by consumer demand for convenience, safety, and, increasingly, sustainability. Foam food trays, despite their established presence, are also subject to this evolution. Innovations in materials and manufacturing processes are poised to address the environmental concerns associated with traditional foam trays, paving the way for a more sustainable future.
Potential Innovations in Foam Food Tray Materials
Material science advancements are offering promising alternatives and modifications to traditional polystyrene foam. These innovations aim to enhance the environmental profile of foam food trays, focusing on biodegradability, compostability, and the use of renewable resources.
- Bio-based Foams: Researchers are exploring the use of bio-based polymers derived from renewable resources like cornstarch, sugarcane, and algae. These materials can potentially biodegrade under specific composting conditions, reducing reliance on fossil fuels. For example, polylactic acid (PLA), a polymer derived from cornstarch, is already used in some food packaging applications.
- Biodegradable Additives: Incorporating biodegradable additives into traditional polystyrene foam can accelerate its breakdown in specific environments. These additives can break down the polymer chains, making the foam more susceptible to microbial degradation.
- Foams with Recycled Content: Increasing the percentage of recycled materials in foam food tray production is another innovation. This reduces the demand for virgin materials and diverts waste from landfills. This approach requires sophisticated recycling processes to ensure the quality and safety of the final product.
- Nanocomposites: The use of nanocomposites, which involve incorporating nanoparticles into the foam matrix, can improve the mechanical properties and barrier characteristics of the trays. This can lead to thinner, yet stronger, trays, potentially reducing material usage and waste.
- Foams with Enhanced Barrier Properties: Innovations in foam structure and composition can enhance barrier properties, such as moisture and oxygen resistance. This extends the shelf life of food products, minimizing food waste, which is a significant contributor to environmental impact.
Trends in Sustainable Packaging for Food Trays
The push for sustainability is reshaping the food packaging landscape, with a clear trend towards reducing environmental impact throughout the product lifecycle. This involves multiple strategies.
- Compostable Packaging: Compostable food trays are gaining traction, particularly in markets with established composting infrastructure. These trays are designed to break down into nutrient-rich compost under controlled conditions, reducing waste sent to landfills.
- Recyclable Packaging: Even if not compostable, ensuring that food trays are recyclable is crucial. This requires clear labeling, consumer education, and the development of effective recycling programs. The design of the tray itself also plays a role, as simpler designs are often easier to recycle.
- Reduced Material Usage: Optimizing the design of food trays to minimize material usage is a key trend. This can involve thinner materials, lighter structures, and innovative designs that provide the same functionality with less material.
- Use of Renewable Resources: The shift toward bio-based materials is accelerating. This reduces reliance on fossil fuels and can help lower the carbon footprint of food packaging.
- Closed-Loop Systems: Developing closed-loop recycling systems, where trays are collected, recycled, and used to create new trays, is a long-term goal for many companies. This approach minimizes waste and conserves resources.
Hypothetical Foam Food Tray with Improved Environmental Characteristics
Imagine a food tray called “EcoFoam,” designed with sustainability as its core principle. EcoFoam would incorporate several key features to minimize its environmental footprint.
- Material Composition: EcoFoam would be made primarily from a bio-based polymer, such as PLA derived from cornstarch. This material is compostable under industrial composting conditions.
- Additives: Biodegradable additives would be incorporated to further accelerate the breakdown process in composting environments.
- Design: The tray would have a simple, streamlined design to minimize material usage. It would also be designed to be easily stackable, reducing storage space during transportation.
- Manufacturing: The manufacturing process would prioritize energy efficiency and utilize renewable energy sources. The process would be designed to minimize waste and emissions.
- End-of-Life: EcoFoam would be clearly labeled with instructions for composting. The company would also support the development of composting infrastructure in regions where the trays are sold.
- Appearance: The tray would be colored using natural pigments, such as plant-based dyes.
EcoFoam, while hypothetical, exemplifies the direction in which the food packaging industry is heading. The combination of bio-based materials, efficient design, and a focus on end-of-life management offers a pathway toward more sustainable food packaging solutions. This concept highlights the potential for integrating innovation with environmental responsibility to create products that meet both consumer needs and ecological demands.
Disposal and Recycling
Proper disposal and recycling practices are critical for mitigating the environmental impact of foam food trays. These practices help reduce landfill waste, conserve resources, and minimize pollution. Understanding the correct methods for disposing of and recycling these trays is essential for promoting sustainability.
Proper Disposal Methods
The appropriate disposal of foam food trays depends largely on local regulations and the availability of recycling facilities. It is crucial to check with local authorities regarding specific guidelines.
- Landfill Disposal: In areas without recycling programs, foam food trays often end up in landfills. Landfilling is the most common disposal method, though it contributes to the accumulation of waste and the potential for environmental contamination. The trays take a very long time to decompose, contributing to long-term landfill issues.
- Incineration: Incineration, or burning, is another disposal method. This can reduce the volume of waste but may release harmful pollutants into the atmosphere if not done with proper filtration systems. The emissions can include greenhouse gases and other toxic substances.
- Composting (Not Recommended): Foam food trays are generally not compostable. They are made from polystyrene, a plastic that does not break down naturally in composting environments. Attempting to compost them will not result in their degradation.
Recycling Initiatives for Foam Food Trays
Recycling foam food trays is a complex process, but it is possible. Several initiatives are in place to facilitate the recycling of these trays, though their availability varies geographically.
- Drop-Off Recycling Programs: Some municipalities and private companies offer drop-off recycling programs for foam. These programs typically require consumers to clean the trays and remove any food residue. The trays are then collected and transported to recycling facilities.
- Curbside Recycling (Limited): Curbside recycling for foam food trays is less common than drop-off programs due to the challenges of processing and market demand. However, some areas have begun to include foam in their curbside recycling programs, particularly if they have access to specialized recycling facilities.
- Specialized Recycling Facilities: Dedicated facilities are designed to process foam. These facilities often use densification technology to compress the foam, reducing its volume and making it easier to transport and process. The densified foam can then be used to create new products.
- Partnerships and Collaboration: Collaboration between recycling companies, businesses, and local governments is crucial to expand recycling opportunities. These partnerships often involve establishing collection points, educating the public, and investing in recycling infrastructure.
Challenges Associated with Recycling Foam Food Trays
Despite the efforts to recycle foam food trays, several challenges hinder widespread recycling. These challenges include logistical difficulties, economic factors, and technical limitations.
- Contamination: Food residue and other contaminants on the trays can make recycling difficult or impossible. Even small amounts of contamination can render an entire batch of recycled material unusable. Consumers must thoroughly clean the trays before recycling.
- Logistics: The lightweight and bulky nature of foam makes transportation and storage challenging. Transporting large volumes of foam is expensive and inefficient. The need for specialized equipment and processes adds to the logistical complexity.
- Market Demand: The market for recycled foam products can be limited. Demand for products made from recycled foam may be lower than for products made from virgin materials. This lack of demand can make recycling economically unviable.
- Processing Technology: Recycling foam requires specialized equipment and technology. Not all recycling facilities have the infrastructure to process foam efficiently. This technological gap limits the availability of recycling options.
- Economic Viability: The cost of collecting, transporting, and processing foam can be high. The low value of the recycled material may not offset these costs, making recycling economically challenging. Subsidies or other financial incentives may be needed to support recycling programs.
Conclusion: Foam Food Tray
In conclusion, the foam food tray represents a complex intersection of convenience, cost, and environmental responsibility. While offering undeniable benefits in food preservation and distribution, its lifecycle presents significant challenges. As we’ve seen, the industry is actively pursuing innovative solutions, from biodegradable alternatives to improved recycling initiatives. The future of food packaging likely lies in a balanced approach, prioritizing sustainability and minimizing environmental impact while maintaining the functional advantages of foam food trays and exploring new materials and designs.