Ah, foam food trays, a humble servant in the grand kitchen of life. From the bustling food service industry to our very homes, these simple vessels hold a silent story. We’ll delve into the world of foam food trays, exploring their purpose, the materials that shape them, and the important roles they play in keeping our meals safe and sound.
These trays, often made from expanded polystyrene, are lightweight and excellent at keeping food at the right temperature. They are used for everything from holding fresh cuts of meat to displaying delectable pastries. We will uncover the secrets of their manufacture, their strengths, and their vulnerabilities.
Introduction to Foam Food Trays
Foam food trays, ubiquitous in the food service landscape, serve as essential packaging for a variety of food items. These lightweight containers are designed to protect, preserve, and present food in a convenient and cost-effective manner. Their widespread use reflects their adaptability and practicality within the fast-paced world of food distribution and consumption.
Definition of Foam Food Trays
Foam food trays are single-use containers primarily made from expanded polystyrene (EPS) or similar materials. They are designed to hold and transport food products, offering a degree of insulation, protection from physical damage, and moisture resistance. These trays are often disposable, catering to the demands of convenience and hygiene in the food industry.
Materials Used in Manufacturing Foam Food Trays
The manufacturing of foam food trays relies on specific materials chosen for their properties.Polystyrene, in its expanded form (EPS), is the most common material. It’s favored for its low cost, lightweight nature, and good insulation properties. The expansion process traps air within the plastic, giving the tray its characteristic cushioning and thermal insulation.Polypropylene foam is another material, often used as an alternative to EPS.
It offers enhanced durability and heat resistance, making it suitable for a wider range of food applications.Other materials can be incorporated to improve performance or provide specialized characteristics. Additives may include colorants, anti-static agents, or stabilizers.
Typical Applications of Foam Food Trays in the Food Service Industry
Foam food trays find extensive application throughout the food service industry, playing a critical role in various sectors.
- Meat and Poultry Packaging: Foam trays are widely used to package fresh meat and poultry products. They provide a stable base, absorb fluids, and protect the products from damage during transportation and display.
- Produce Packaging: Fruits and vegetables are often packaged in foam trays, offering protection from bruising and maintaining freshness. This is particularly important for delicate items.
- Prepared Food Packaging: Ready-to-eat meals, sandwiches, and salads are frequently presented in foam trays. Their lightweight nature and insulation properties make them ideal for these applications.
- Seafood Packaging: Similar to meat and poultry, foam trays provide a suitable environment for seafood, protecting it from damage and maintaining a cold temperature.
- Fast Food and Takeaway: Foam trays are often used to hold burgers, fries, and other fast-food items, offering convenience and insulation to keep food warm.
The applications highlight the versatility and adaptability of foam food trays within the food service ecosystem.
Advantages of Using Foam Food Trays
Foam food trays, often underestimated, offer a compelling suite of advantages that contribute significantly to food safety, cost efficiency, and operational ease within the food industry. Their properties cater to the multifaceted demands of preserving freshness, maintaining optimal temperatures, and simplifying handling processes. The benefits extend beyond mere convenience, impacting food quality and overall profitability.
Food Preservation and Temperature Control
Foam food trays excel in preserving food quality by providing superior insulation. This characteristic is critical for maintaining the desired temperature of food items, whether hot or cold.
Discover the crucial elements that make food handlers permit washington dc the top choice.
- Foam trays act as an effective barrier against external temperature fluctuations. They minimize heat transfer, preventing food from rapidly warming up or cooling down. This is especially important for maintaining the safety of perishable goods.
- For chilled items like meats and seafood, foam trays help to keep them cold for longer periods. This reduces the risk of bacterial growth and extends the shelf life of the products. This is crucial for both retail display and transportation.
- For hot foods, foam trays can retain heat, keeping meals warm for a reasonable duration. This is a significant advantage for takeout and delivery services, ensuring that food arrives at the consumer’s location at an acceptable temperature.
- The insulation properties also help to prevent condensation, which can affect the texture and appearance of certain foods. This is particularly beneficial for items like pastries and fried foods, preserving their crispiness.
Cost-Effectiveness of Foam Food Trays
The cost-effectiveness of foam food trays is a significant factor in their widespread use. When compared to alternative packaging options, foam trays often present a more economically viable solution.
- Foam trays are typically less expensive to manufacture than paper or plastic alternatives. This cost advantage translates into lower packaging expenses for food businesses, which can improve profit margins.
- Their lightweight nature reduces shipping costs. Lighter packaging materials mean lower transportation expenses, especially when dealing with large volumes of food products. This is a critical factor for distributors and retailers.
- The efficient use of materials in the production of foam trays contributes to their cost-effectiveness. Less material is required compared to some other packaging types, resulting in savings in raw material costs.
- Foam trays are often readily available, reducing the need for costly and time-consuming procurement processes. The ease of sourcing translates into fewer logistical challenges for businesses.
Lightweight Properties and Ease of Handling
The lightweight nature of foam food trays significantly contributes to their ease of handling and overall practicality. This characteristic provides numerous benefits for both businesses and consumers.
- The lightweight design makes foam trays easy to handle and transport. This is a considerable advantage for employees in busy food service environments, allowing for efficient packing and unpacking.
- Foam trays reduce the overall weight of packaged food items, which is beneficial for both retail displays and consumer convenience. Consumers appreciate the ease of carrying lighter packages.
- The compact design of foam trays facilitates efficient storage. They can be easily stacked, minimizing the space required for storage in both warehouses and retail settings.
- Their lightweight nature also contributes to lower waste disposal costs. Lighter packaging generally results in lower fees for waste removal services.
Comparative Table: Advantages of Packaging Materials
The following table provides a comparative overview of the advantages of foam food trays, paper trays, and plastic trays.
Feature | Foam Food Trays | Paper Trays | Plastic Trays |
---|---|---|---|
Food Preservation | Excellent insulation, maintaining temperature and freshness. | Moderate insulation, suitable for dry foods. | Good insulation, can be sealed for freshness. |
Cost-Effectiveness | Generally less expensive to manufacture and ship. | Moderate cost, dependent on material and design. | Can be more expensive, depending on the type and features. |
Lightweight Properties | Lightweight and easy to handle, reducing shipping costs. | Lighter than plastic, but can be less durable. | Heavier than foam, can be more robust. |
Environmental Impact | Often criticized for being non-biodegradable, but recyclable in some areas. | Biodegradable options available, but may require specific disposal conditions. | Can be recyclable, but the process depends on the plastic type and local facilities. |
Disadvantages of Foam Food Trays
The seemingly convenient world of foam food trays, while offering certain benefits, casts a long shadow of environmental, health, and logistical challenges. These trays, ubiquitous in the food industry, present a complex web of drawbacks that demand careful consideration. Understanding these disadvantages is crucial to evaluating the true cost of their widespread use.
Environmental Concerns Associated with the Use of Foam Food Trays
The environmental impact of foam food trays is substantial, stemming from their production, disposal, and persistence in the environment. Their non-biodegradable nature poses significant threats to ecosystems worldwide.
The primary environmental concern revolves around the material itself: expanded polystyrene (EPS), often referred to as Styrofoam, which is the most common material used. EPS is derived from petroleum, a non-renewable resource. The manufacturing process releases greenhouse gases, contributing to climate change. Furthermore, the trays’ light weight and bulkiness contribute to litter problems, often ending up in landfills, oceans, and natural habitats.
Consider this: A single foam tray can persist in a landfill for hundreds, perhaps even thousands, of years, slowly breaking down into microplastics that contaminate soil and water. This slow decomposition process releases harmful chemicals into the environment. Animals can ingest these microplastics, leading to health problems and ecological imbalances. The environmental cost of using foam trays extends far beyond their immediate use, impacting the planet for generations to come.
Challenges of Recycling Foam Food Trays
Recycling foam food trays is significantly difficult, contributing to their accumulation in landfills and environmental pollution. The process is complex and often economically unviable.
The primary obstacle to recycling is the nature of the material itself. EPS is mostly air, making it bulky and inefficient to transport. Furthermore, it is often contaminated with food residue, making cleaning necessary. The recycling process requires specialized equipment and facilities, which are not widely available. Even when facilities exist, the low market value of recycled EPS often makes the process financially unattractive.
A case study illustrates the challenges. In many municipalities, foam trays are not accepted in curbside recycling programs. Even where collection programs exist, the trays may be rejected if they are not properly cleaned or if they contain food scraps. This results in a significant portion of foam trays ending up in landfills, compounding the environmental problems associated with their disposal.
Potential Health Risks Associated with Using Foam Food Trays
Beyond environmental concerns, the use of foam food trays raises potential health risks, especially related to the chemicals used in their manufacturing and the possibility of leaching into food.
Styrene, a key component of EPS, is classified as a possible human carcinogen by the International Agency for Research on Cancer (IARC). When heated, as in the case of hot food or beverages, styrene can leach from the tray into the food. This poses a potential health risk to consumers. While the levels of styrene leaching are often considered low, the cumulative effect of exposure over time remains a concern.
Additionally, the manufacturing process can introduce other potentially harmful chemicals. The Food and Drug Administration (FDA) regulates the use of EPS in food packaging, but the potential for migration of chemicals into food remains a subject of ongoing research and debate. Consider the case of a hot coffee served in a foam cup; the longer the contact time and the higher the temperature, the greater the potential for chemical migration into the beverage.
Alternative Materials for Food Trays and Their Drawbacks
Several alternative materials are available for food trays, each with its own set of advantages and disadvantages. The choice of material often involves a trade-off between environmental impact, cost, and functionality.
- Paperboard: Paperboard trays are biodegradable and renewable. However, their production requires significant water and energy resources. They may also require coatings to prevent leaks, which can hinder biodegradability.
- Compostable Plastics (PLA): Made from renewable resources like corn starch, PLA trays are compostable under specific industrial composting conditions. However, they are not readily compostable in home compost piles and may contaminate traditional recycling streams.
- Recycled Cardboard: Recycled cardboard trays reduce the demand for virgin materials. However, they may lack the insulation properties of foam and can be less durable.
- Aluminum: Aluminum trays are recyclable and can withstand high temperatures. However, the production of aluminum is energy-intensive, and its extraction can cause environmental damage.
- Reusable Trays: Reusable trays made of durable plastic or other materials offer the most environmentally friendly option in the long run. They require washing and are not ideal for all food service scenarios.
Each alternative presents its own challenges. Choosing the best option requires careful consideration of the specific application, environmental impact, and economic feasibility. For example, the environmental benefits of compostable plastics can be negated if they end up in landfills, where they will not decompose. Likewise, while reusable trays minimize waste, they may not be practical for large-scale events or situations where washing facilities are limited.
Manufacturing Process of Foam Food Trays
The journey of a foam food tray, from raw material to the familiar shape holding our meals, is a fascinating process. It’s a carefully orchestrated sequence of steps, demanding precision and technological prowess, ensuring that each tray meets the necessary standards for food safety and functionality. Understanding this process reveals the ingenuity behind a seemingly simple product, highlighting the interplay of chemistry, engineering, and quality control.
Step-by-Step Manufacturing Process
The creation of foam food trays involves several crucial stages, each contributing to the final product’s characteristics. These steps, performed in a specific order, transform raw materials into the familiar trays we use daily.
- Raw Material Preparation: The process begins with the selection and preparation of the raw material, typically polystyrene (PS) beads. These beads are often pre-expanded using steam. This initial expansion increases the volume of the beads, reducing the amount of material needed later in the process. The pre-expansion stage is crucial for achieving the desired density and structural properties of the final product.
- Foaming/Extrusion: The pre-expanded polystyrene beads are then mixed with a blowing agent, such as pentane or isobutane. This mixture is fed into an extruder, a machine that melts the polystyrene and forces it through a die. The blowing agent vaporizes during this process, creating the foam structure within the molten plastic. This step is critical for achieving the desired lightweight and insulating properties of the foam.
The die shapes the extruded foam into a continuous sheet.
- Sheet Cooling and Shaping: The extruded foam sheet is cooled and then passes through a series of rollers. These rollers help to maintain the sheet’s thickness and ensure uniform cooling. Once cooled, the sheet is ready for the thermoforming process.
- Thermoforming: In thermoforming, the foam sheet is heated to a specific temperature and then placed over a mold. A vacuum is applied, and/or air pressure is used to force the heated foam into the mold’s shape, creating the tray’s contours. The mold’s design determines the final shape and features of the tray.
- Trimming and Cutting: After thermoforming, the trays are trimmed to remove excess material and cut into individual units. This step ensures that each tray has clean edges and the correct dimensions.
- Quality Control and Inspection: Each tray undergoes a rigorous inspection process to ensure it meets the required quality standards. This includes checking for defects, such as holes, cracks, or uneven thickness.
- Packaging and Shipping: The finished trays are then packaged and prepared for shipping to distributors and end-users. Proper packaging protects the trays during transportation and storage.
Machinery and Equipment Used in Production, Foam food trays
The production of foam food trays relies on specialized machinery and equipment, each designed to perform a specific task in the manufacturing process. These tools are crucial for achieving efficiency, precision, and consistent quality.
- Extruders: Extruders are the heart of the manufacturing process, responsible for melting the polystyrene, mixing it with the blowing agent, and forming the foam sheet. They are equipped with screws and heating elements to achieve the desired temperature and consistency.
- Thermoforming Machines: These machines use molds and vacuum or pressure to shape the foam sheet into the desired tray form. They often include heating elements, cooling systems, and robotic arms for efficient operation.
- Molds: Molds are the key to the final tray’s shape. They are designed with precision and can be customized to create various tray sizes, shapes, and features.
- Cutting and Trimming Equipment: These machines trim the excess material and cut the thermoformed sheet into individual trays, ensuring clean edges and accurate dimensions.
- Quality Control Equipment: Various tools are used to inspect the trays for defects. These include thickness gauges, visual inspection stations, and automated testing systems.
- Material Handling Systems: Conveyor belts, robots, and other automated systems are used to move materials and trays throughout the production process, improving efficiency and reducing manual labor.
Quality Control Measures
Quality control is an integral part of the foam food tray manufacturing process, ensuring that each tray meets the required standards for food safety, durability, and functionality. These measures are implemented at various stages to identify and correct any potential issues.
- Raw Material Inspection: The raw materials, primarily polystyrene beads, undergo thorough inspection before being used in production. This includes checking for purity, consistency, and compliance with food-grade standards.
- Extrusion Monitoring: During the extrusion process, parameters such as temperature, pressure, and foam sheet thickness are continuously monitored to ensure consistent foam quality.
- Thermoforming Inspection: After thermoforming, the trays are visually inspected for defects such as uneven thickness, cracks, and incomplete molding.
- Dimensional Checks: Trays are regularly measured to ensure they meet the specified dimensions and tolerances.
- Performance Testing: Trays may be subjected to various performance tests, such as drop tests, stacking tests, and leak tests, to assess their durability and functionality.
- Food Safety Compliance: Manufacturers must adhere to strict food safety regulations, ensuring that the trays do not leach harmful chemicals into food. This includes testing for migration of substances and using food-grade materials.
Visual Representation of the Foam Food Tray Manufacturing Process
Imagine a cross-sectional illustration, a visual journey through the foam food tray manufacturing process. The image shows a simplified representation, starting from the left.The first frame shows the polystyrene beads, represented as small, white spheres, alongside a container of a blowing agent. Arrows indicate their mixing and entry into an extruder. The extruder, a long, cylindrical machine, is depicted with internal components that melt the polystyrene and mix it with the blowing agent, forming a foamed sheet.The next frame shows the foamed sheet exiting the extruder.
It then passes through a series of cooling rollers, represented as large, cylindrical objects, which control the sheet’s thickness and prepare it for thermoforming.The following frame displays a thermoforming machine. The foamed sheet is positioned over a mold, with a vacuum system beneath it. An arrow indicates the application of vacuum, drawing the heated foam into the mold’s shape, forming the tray.The subsequent frame illustrates the trimming and cutting stage, where excess material is removed, and individual trays are separated.
A cutting machine is shown, with a tray being cut from the larger sheet.The final frame depicts a quality control station, where finished trays are inspected for defects. A person is shown visually inspecting a tray, while measurement tools are present. Finished trays are then shown being packaged and ready for shipment. The entire process is accompanied by labels highlighting each stage, such as “Raw Material Preparation,” “Extrusion,” “Thermoforming,” “Trimming,” “Quality Control,” and “Packaging.” This visual provides a clear, concise overview of the key steps involved in manufacturing foam food trays.
Types and Varieties of Foam Food Trays
The world of foam food trays is a landscape of versatility, molded to meet the diverse needs of the food industry. From the simplest rectangular shape to complex designs tailored for specific items, these trays showcase a spectrum of possibilities. Understanding the available types and their specific applications is crucial for making informed choices that balance functionality, cost-effectiveness, and environmental considerations.
The following sections explore the various facets of this diverse category.
Shapes and Sizes of Foam Food Trays
Foam food trays are manufactured in a vast array of shapes and sizes, each designed to accommodate different food products and packaging requirements. Rectangular and square trays remain the most common, offering simplicity and ease of stacking and handling. However, the market also presents specialized forms to optimize space and presentation.These include:* Rectangular Trays: The ubiquitous standard, perfect for meats, poultry, and produce.
Sizes range from small single-serving portions to large family packs.
Square Trays
Often used for baked goods, sandwiches, and deli items, providing a stable base and minimizing movement during transport.
Oval and Round Trays
Commonly employed for showcasing seafood, prepared salads, and pre-portioned meals, offering an aesthetically pleasing presentation.
Compartmentalized Trays
Designed with built-in dividers to separate different food items within a single tray, ideal for meal kits, bento boxes, and ready-to-eat meals.Size variations are equally extensive, catering to portion control and retail needs. Trays can range from a few inches in length and width for individual servings to over a foot in size for larger family packs or bulk food items.
The specific dimensions are determined by the food product’s size, weight, and the desired visual appeal.
Grades and Densities of Foam
The performance characteristics of foam food trays are profoundly influenced by the grade and density of the foam material used in their production. These factors directly impact the tray’s strength, insulation properties, and overall suitability for various food applications. Different densities cater to specific requirements, ensuring optimal protection and preservation of the packaged food.* Low-Density Foam: Typically used for lighter items like produce or bakery goods.
These trays offer good cushioning and are often more cost-effective.
Medium-Density Foam
Provides a balance of strength and insulation, making them suitable for a wider range of products, including meats, poultry, and prepared meals.
High-Density Foam
Offers superior structural integrity and is used for heavier items or those requiring enhanced protection during transport and handling.The choice of foam grade and density also impacts the tray’s environmental profile. Lower-density trays generally require less material, potentially reducing the environmental impact, while high-density trays might offer increased durability, thus extending their lifespan.
Trays Designed for Specific Food Types
The versatility of foam food trays extends to their ability to be customized for particular food categories. Manufacturers design trays with specific features to enhance the presentation, preservation, and handling of different food items. This specialized approach optimizes the packaging for each food type, ensuring its quality and extending its shelf life.For instance:* Meat Trays: These trays often feature absorbent pads to capture excess juices and maintain the product’s freshness and visual appeal.
They are designed to withstand lower temperatures, crucial for storing raw meats.
Produce Trays
Designed with ventilation holes to allow air circulation, preventing moisture buildup and extending the shelf life of fruits and vegetables. They often come in various shapes and sizes to accommodate different produce items.
Bakery Item Trays
These trays are typically designed to cradle delicate baked goods, preventing damage during handling and transport. They may include features like rounded edges and non-stick surfaces to enhance the product’s presentation.These are a few examples, with each design element contributing to the preservation of the food product.
Types of Foam Food Trays and Their Common Uses
Foam food trays encompass a wide variety of types, each designed to serve specific purposes within the food industry. These diverse trays are tailored to meet various requirements.* Meat Trays: Designed for raw meats, poultry, and seafood, often featuring absorbent pads to contain liquids.
Produce Trays
Used for fruits and vegetables, frequently with ventilation holes to maintain freshness.
Bakery Trays
Suited for baked goods, offering cushioning and often non-stick surfaces to protect delicate items.
Prepared Food Trays
Used for ready-to-eat meals, deli items, and sandwiches, often with compartmentalization for different food components.
Deli Trays
Specifically designed for showcasing deli meats and cheeses.
Egg Trays
Designed with individual compartments for eggs, protecting them from breakage.
Custom Trays
Tailored for unique food items or specific packaging requirements, offering flexibility in design and function.Each type of tray is engineered with specific features to ensure the safe handling, presentation, and preservation of the food it contains, demonstrating the adaptability and versatility of foam food tray technology.
Alternatives to Foam Food Trays
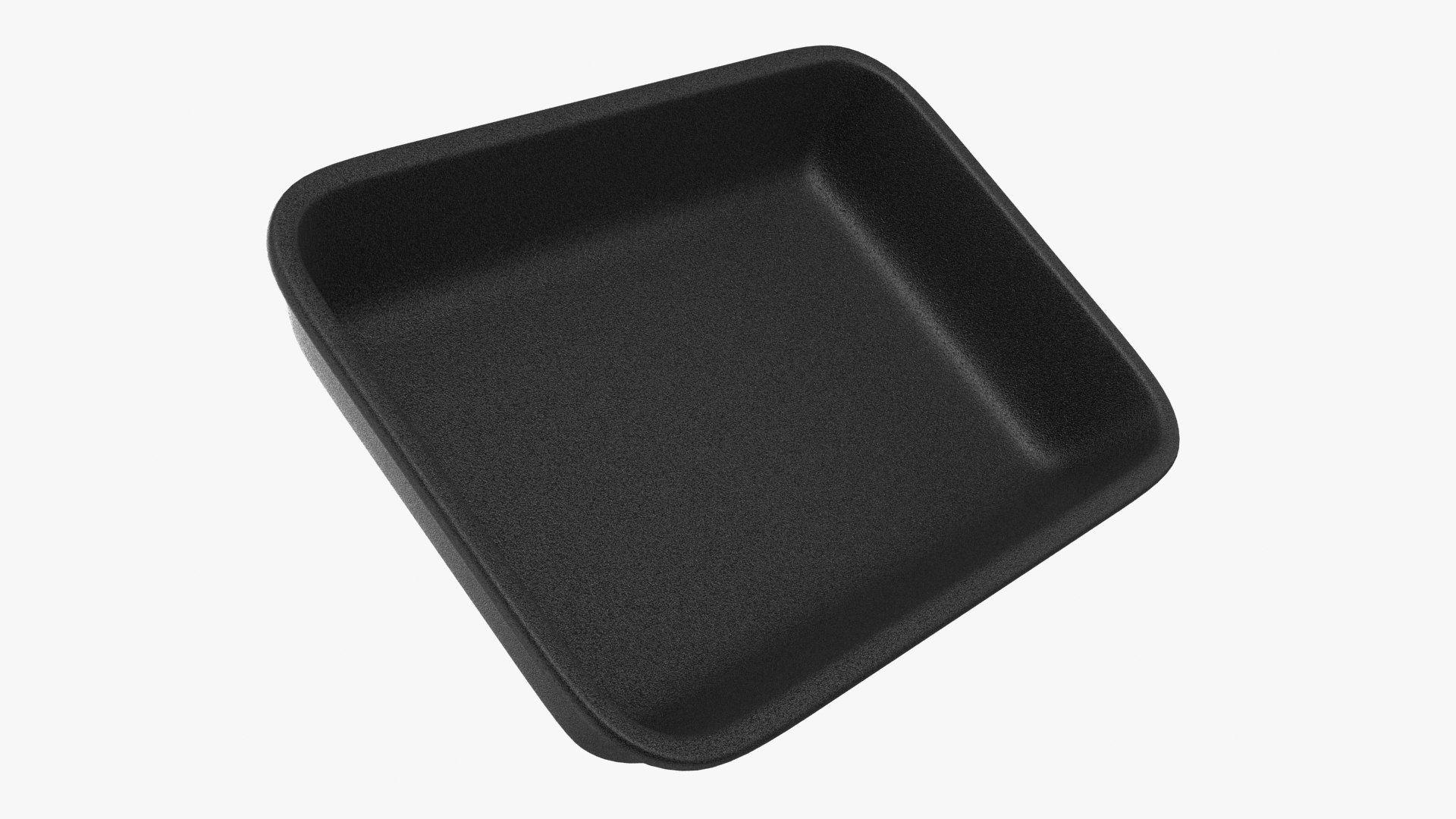
The world is shifting, a subtle but powerful awakening to the fragility of our shared home. Foam food trays, once ubiquitous, are now viewed with a critical eye, their environmental impact a stark reminder of our consumption habits. Fortunately, innovation blossoms in the face of necessity. A diverse array of alternatives offers a chance to nourish ourselves without sacrificing the planet’s well-being.
Sustainable Alternatives to Foam Food Trays
The quest for sustainability in food packaging is multifaceted, demanding solutions that consider not only the material itself but also its lifecycle. The alternatives range from the readily compostable to the meticulously biodegradable, each possessing unique characteristics and environmental footprints.
- Compostable Options: These materials break down into nutrient-rich compost under specific conditions, mirroring nature’s own recycling process. They often include:
- Plant-based plastics (PLA): Derived from renewable resources like corn starch, PLA offers a promising alternative. When properly composted in industrial facilities, it decomposes efficiently. However, it may not break down readily in home composting systems.
- Molded Pulp: Created from recycled paper or agricultural byproducts, molded pulp trays are robust and can be composted. Their textured surface provides a natural aesthetic.
- Sugarcane Bagasse: A byproduct of sugarcane processing, bagasse trays are sturdy, grease-resistant, and readily compostable. They represent a circular economy approach, utilizing waste to create valuable products.
- Biodegradable Options: These materials decompose through natural processes, but the timeframe and conditions for breakdown can vary.
- Paperboard: A classic, paperboard offers a readily available and recyclable option. It can be coated with biodegradable films to enhance its resistance to moisture and grease.
- Certain Bio-plastics: While some bio-plastics are compostable, others are biodegradable under specific conditions, such as marine environments. Research and development are continuously refining these materials.
Comparison of Alternative Materials
The performance of alternative materials hinges on several factors: their ability to withstand handling, their resistance to moisture and temperature, and their suitability for different food types. The choice of material often involves trade-offs, balancing environmental benefits with practical considerations.
- Paperboard: This material offers a good balance of cost and performance. Its recyclability adds to its sustainability. However, it may require coatings to prevent leaks and maintain structural integrity.
- Molded Pulp: Molded pulp excels in durability and its ability to absorb moisture. Its textured surface provides a tactile experience. It may be less aesthetically appealing than other options.
- Plant-based Plastics (PLA): PLA offers excellent clarity and can be molded into various shapes. It’s ideal for displaying food. However, its composting requirements must be carefully managed.
- Sugarcane Bagasse: Bagasse trays are naturally grease-resistant and sturdy. They are a strong contender for sustainability due to their use of agricultural waste.
Environmental Impact of Different Alternative Food Tray Materials
Assessing the environmental impact requires a holistic view, considering factors such as resource consumption, manufacturing processes, and end-of-life scenarios. Life cycle assessments (LCAs) provide a valuable framework for comparing the environmental burdens of different materials.
- Resource Consumption: Plant-based materials utilize renewable resources, reducing reliance on fossil fuels. Molded pulp leverages recycled materials, decreasing the need for virgin resources.
- Manufacturing Processes: The energy consumption and emissions associated with manufacturing vary depending on the material and production methods. The sourcing of raw materials also plays a role.
- End-of-Life: Compostable materials offer a clear advantage in terms of waste reduction. Recyclable materials can be incorporated into new products, extending their lifespan. Biodegradable materials provide an alternative to landfills.
Comparative Table of Alternative Food Tray Materials
The following table summarizes the key characteristics of the alternative food tray materials, offering a comparative view of their cost, sustainability, and performance:
Material | Cost | Sustainability | Performance |
---|---|---|---|
Paperboard | Moderate | Good (Recyclable) | Good (requires coatings for some applications) |
Molded Pulp | Moderate | Excellent (Compostable, made from recycled materials) | Good (durable, absorbent) |
Plant-based Plastics (PLA) | Moderate to High | Good (Compostable in industrial facilities, renewable resources) | Excellent (clarity, moldability) |
Sugarcane Bagasse | Moderate | Excellent (Compostable, made from agricultural waste) | Good (grease-resistant, sturdy) |
Market Trends and Future of Foam Food Trays
The food packaging industry, a relentless engine of commerce and sustenance, is currently undergoing a dramatic metamorphosis. Driven by environmental awareness, evolving consumer demands, and technological advancements, the landscape of food tray materials is in constant flux. The future of foam food trays is intertwined with these shifts, presenting both challenges and opportunities for adaptation and innovation.
Current Market Trends in the Food Packaging Industry
The food packaging industry reflects the broader societal trends of sustainability, convenience, and visual appeal. A complex interplay of factors influences the choices made by manufacturers, retailers, and consumers.
- Rise of Sustainable Packaging: The most prominent trend is the escalating demand for sustainable packaging solutions. Consumers are increasingly aware of the environmental impact of their choices, and they actively seek products packaged in materials that are recyclable, compostable, or made from renewable resources. This shift is putting pressure on manufacturers to move away from traditional, non-biodegradable materials.
- Increased Demand for Convenience: Modern lifestyles demand convenience. Food trays that offer ease of use, portability, and extended shelf life are highly valued. This trend is fueling the growth of ready-to-eat meals and takeout options, further impacting the demand for specific packaging types.
- Emphasis on Food Safety and Preservation: Maintaining food safety and extending shelf life are critical considerations. Packaging materials that provide effective barriers against contaminants and maintain the freshness of food are in high demand. This often leads to the adoption of materials with specific properties, such as oxygen and moisture barriers.
- Growing E-commerce and Food Delivery: The surge in online food ordering and delivery services has created a unique set of packaging requirements. Trays must be durable enough to withstand transportation, maintain food temperature, and prevent leaks and spills.
- Regulatory Pressures and Legislation: Governments worldwide are implementing stricter regulations regarding packaging materials, including bans on single-use plastics and mandates for recycling and composting. These regulations significantly impact the choices available to food producers and retailers.
Future Prospects of Foam Food Trays
The future of foam food trays is complex, shaped by the interplay of environmental concerns, consumer preferences, and technological advancements. While the material faces significant challenges, opportunities for adaptation and innovation exist.
- Challenges from Environmental Concerns: The primary challenge stems from the environmental impact of traditional foam trays, primarily made from expanded polystyrene (EPS). EPS is not easily recyclable and often ends up in landfills or as litter. The negative perception of EPS as a non-biodegradable plastic has led to bans and restrictions in various regions.
- Impact of Consumer Preferences: Consumers are increasingly seeking sustainable packaging options. They are willing to pay a premium for products packaged in environmentally friendly materials. This preference is driving the demand for alternatives to foam trays, such as those made from recycled materials, plant-based materials, or compostable options.
- Opportunities for Innovation: The challenges also present opportunities for innovation. The development of biodegradable foam trays, made from materials like cornstarch or mushroom-based packaging, offers a promising path forward. Another avenue is the use of recycled EPS, though this requires robust recycling infrastructure.
- Adapting to a Circular Economy: The concept of a circular economy, where materials are reused and recycled, is gaining momentum. Foam food tray manufacturers need to embrace this concept by designing products that are easily recyclable or compostable and by supporting the development of recycling infrastructure.
- The Role of Regulations: Regulatory pressures will continue to shape the market. Foam food tray manufacturers must stay informed about evolving regulations and proactively adapt their products and processes to meet compliance requirements.
Innovations and Developments in Foam Food Tray Technology
The foam food tray industry is not standing still. Manufacturers are actively exploring new technologies and materials to address the challenges and meet the demands of the market.
- Biodegradable and Compostable Foam Alternatives: The development of biodegradable and compostable foam trays is a key area of innovation. These trays are made from renewable resources such as cornstarch, sugarcane, or mushroom mycelium. These materials decompose naturally, reducing their environmental impact.
- Recycled Foam Technologies: Another approach is to improve the recyclability of traditional EPS foam. This involves developing technologies to collect, process, and reuse EPS foam, creating a closed-loop system. This can involve new recycling processes that break down the foam into its base components.
- Foam Alternatives Using Plant-Based Materials: Plant-based foams, often derived from agricultural byproducts like wheat straw or bagasse, are gaining traction. These materials offer a more sustainable alternative to traditional foam, and they can be composted.
- Advanced Barrier Technologies: To enhance food safety and shelf life, manufacturers are developing new barrier technologies that can be incorporated into foam trays. These barriers can protect food from moisture, oxygen, and contaminants, extending its usability.
- Smart Packaging Integration: The integration of smart technologies, such as sensors and indicators, is an emerging trend. Smart foam trays can provide information about the food’s freshness, temperature, and potential spoilage, enhancing food safety and reducing waste.
Visual Representation of Market Trends: The Rise and Fall of Food Tray Materials
The following visual representation illustrates the fluctuating popularity of different food tray materials over the past decade, highlighting the shifting market trends.
Descriptive Paragraph: The illustration depicts a line graph charting the market share of various food tray materials from 2014 to 2024. Expanded polystyrene (EPS), represented by a red line, shows a steady decline in market share, reflecting the negative perception and regulatory pressures. Paper-based trays, illustrated by a green line, exhibit a moderate increase, indicating a growing preference for sustainable alternatives.
Recycled PET (rPET), shown by a blue line, experiences a consistent increase, reflecting the growing demand for recycled materials. Plant-based trays, represented by a yellow line, demonstrate a gradual rise, indicating the growing adoption of compostable options. The graph shows the market’s gradual move towards sustainable solutions, with EPS losing ground to more eco-friendly alternatives. The projected data for 2024 highlights the expected continued growth of sustainable options, while EPS continues to decline.
The data shows a dynamic industry in transition.
Final Summary
In the end, the story of foam food trays is a story of choices. We’ve journeyed through their benefits and their drawbacks, seen how they are made, and pondered the future. As we consider the impact of our actions, may we always strive to make choices that honor both our needs and the well-being of our precious world. May this knowledge guide us towards a more thoughtful approach to packaging and its role in our lives.