Assalamu’alaikum warahmatullahi wabarakatuh, brothers and sisters! Today, let’s delve into the world of something seemingly simple yet incredibly essential: the plastic food container lid. Think about it, how often do we rely on these little guardians to keep our meals fresh and safe? From the humble lunchbox to the restaurant takeout, these lids play a crucial role. But have we ever stopped to consider the science, the design, and the impact behind these everyday objects?
Let’s embark on a journey of discovery together.
We’ll explore the various materials that make up these lids, understanding their strengths and weaknesses. We’ll examine how they are made, from the initial design to the final product, and we’ll learn about the importance of food safety regulations. Furthermore, we will also discuss the durability, environmental impact, and different types of plastic food container lids, ensuring we understand everything from the different closure mechanisms to the best practices for maintaining their performance and longevity.
Materials Used in Plastic Food Container Lids
Plastic food container lids are integral components in preserving food quality and extending shelf life. The selection of appropriate materials for these lids is crucial, directly impacting factors such as food safety, structural integrity, and environmental sustainability. Understanding the diverse range of plastics employed in lid manufacturing, along with their respective properties, is paramount for informed decision-making in food packaging design and material selection.
Types of Plastics Used in Lid Manufacturing
A variety of plastics are utilized in the creation of food container lids, each possessing unique characteristics that render them suitable for specific applications. The most common types include Polypropylene (PP), Polyethylene (PE), Polyethylene Terephthalate (PET), and Polystyrene (PS). The selection of a particular plastic depends on factors such as the food product, the desired level of protection, and the manufacturing process.
- Polypropylene (PP): Polypropylene is a thermoplastic polymer that is frequently used in food container lids due to its excellent resistance to heat, chemicals, and moisture. It offers a good balance of flexibility and rigidity, making it suitable for a wide range of applications. PP is also relatively inexpensive and can be easily molded into various shapes.
- Polyethylene (PE): Polyethylene is another widely used thermoplastic polymer. It comes in various densities, including Low-Density Polyethylene (LDPE) and High-Density Polyethylene (HDPE). LDPE is flexible and is often used for lids that require a degree of conformability, such as those found on yogurt containers. HDPE is more rigid and is often used for lids that need to withstand more stress. Both forms are generally resistant to chemicals and moisture.
- Polyethylene Terephthalate (PET): PET is a strong, lightweight, and transparent plastic commonly used for beverage bottles and food containers. In lid applications, PET offers good barrier properties against gases and moisture, which helps preserve food quality. PET is often chosen when clarity and visual appeal are important.
- Polystyrene (PS): Polystyrene is a versatile thermoplastic polymer available in different forms, including expanded polystyrene (EPS) and high-impact polystyrene (HIPS). While less common for direct food contact lids due to concerns regarding chemical migration, it can be used in specific applications. HIPS provides good impact resistance, while EPS is often used for insulation.
Advantages and Disadvantages of Plastic Types
Each plastic type presents a unique set of advantages and disadvantages concerning food safety, durability, and recyclability. These factors must be carefully weighed when selecting a material for a food container lid.
- Polypropylene (PP): PP is generally considered food-safe and can withstand high temperatures, making it suitable for microwaveable lids. It is durable and resistant to many chemicals. However, its recyclability can vary depending on local infrastructure, and it may not be as transparent as other options like PET.
- Polyethylene (PE): PE is food-safe and offers good flexibility, especially LDPE. It is also relatively inexpensive and readily recyclable in many areas. The main disadvantage is that it may not offer the same level of heat resistance as PP.
- Polyethylene Terephthalate (PET): PET provides excellent clarity and good barrier properties, extending the shelf life of food products. It is also widely recyclable. However, PET is susceptible to degradation at high temperatures, limiting its use in microwave applications, and may not be as impact-resistant as other options.
- Polystyrene (PS): PS is inexpensive and can be molded into various shapes. However, it is often less resistant to chemicals and can leach potentially harmful substances into food, particularly in the presence of fats or oils. Recyclability of PS can be challenging.
Comparison of Lid Material Properties
The following table presents a comparative overview of the properties of the aforementioned plastic materials, highlighting key characteristics relevant to their application in food container lids.
Material | Melting Point (°C) | Flexibility | Chemical Resistance | Typical Applications |
---|---|---|---|---|
Polypropylene (PP) | 130-170 | Moderate | Excellent | Microwaveable lids, general-purpose lids |
Low-Density Polyethylene (LDPE) | 105-115 | High | Good | Flexible lids, squeeze bottle lids |
High-Density Polyethylene (HDPE) | 120-135 | Moderate | Good | Rigid lids, bottle caps |
Polyethylene Terephthalate (PET) | 250-260 | Low | Good | Clear lids, lids requiring barrier properties |
Polystyrene (PS) | 240 | Low | Poor to Moderate | Certain food containers lids, disposable lids |
Role of Additives in Lid Performance
Additives are often incorporated into the plastic materials used in food container lids to enhance their performance characteristics. These additives can significantly impact the lid’s durability, appearance, and safety.
- Plasticizers: Plasticizers are added to increase the flexibility and pliability of the plastic. They are particularly important in applications where the lid needs to be able to seal tightly or conform to the shape of the container. Common examples include phthalates, although there are increasing concerns regarding their potential health impacts, leading to the use of alternative plasticizers.
- UV Stabilizers: UV stabilizers are added to protect the plastic from degradation caused by exposure to ultraviolet (UV) radiation. They are particularly important for lids that are exposed to sunlight, as UV radiation can cause the plastic to become brittle and discolored. Examples include benzophenones and benzotriazoles.
- Colorants: Colorants are used to add color to the lids, enhancing their aesthetic appeal or helping with brand identification. These can range from organic pigments to inorganic pigments.
- Antioxidants: Antioxidants are added to prevent the oxidation of the plastic, which can lead to degradation and embrittlement. They are especially important in high-temperature applications.
Design and Manufacturing of Plastic Food Container Lids
The design and manufacturing of plastic food container lids are crucial for maintaining food safety, preserving freshness, and ensuring consumer convenience. These lids are engineered to provide a secure seal, protect against contamination, and withstand various environmental conditions. Understanding the different design options, manufacturing processes, and sealing mechanisms is essential for producing effective and reliable food packaging solutions.
Different Lid Designs and Applications
Various lid designs cater to specific food types and storage requirements. Each design offers unique advantages in terms of sealing, ease of use, and cost-effectiveness.
- Snap-on Lids: These lids typically feature a rim that snaps onto the container’s edge, creating a tight seal. They are commonly used for containers holding deli meats, prepared salads, and takeout meals. The ease of use and relatively low cost make them a popular choice.
- Screw-on Lids: Screw-on lids employ threads that engage with corresponding threads on the container. This design provides a robust seal, making them suitable for liquids and products requiring a high degree of containment. Jars of sauces, jams, and beverages often utilize screw-on lids.
- Hinged Lids: Hinged lids are permanently attached to the container body, offering convenience and preventing the lid from being misplaced. These are often found on clamshell containers for sandwiches, burgers, and other single-serving items. The integrated design streamlines the packaging process and enhances usability.
Manufacturing Processes for Plastic Lids
The manufacturing of plastic lids involves several processes, each contributing to the final product’s quality and performance. The choice of manufacturing method depends on the lid’s design, material, and production volume.
- Injection Molding: This is the most common method for producing plastic lids. Molten plastic is injected under high pressure into a mold cavity, where it cools and solidifies into the desired shape. Injection molding allows for intricate designs, high production rates, and precise dimensional control.
- Thermoforming: Thermoforming involves heating a plastic sheet and forming it over a mold using vacuum or pressure. This process is often used for producing lids with relatively simple geometries, such as those found on yogurt containers or pre-packaged salads. Thermoforming is generally less expensive than injection molding for lower production volumes.
- Compression Molding: In compression molding, a preheated plastic material is placed into an open mold cavity. The mold is then closed, and pressure is applied to shape the plastic. This method is sometimes used for producing lids from thermoset plastics, such as those used in some food storage containers.
Injection Molding Process for a Snap-on Lid
The injection molding process for a snap-on lid involves several key components working in unison to produce the finished product.
Learn about more about the process of west chester food truck festival in the field.
Diagram Description: The diagram illustrates the injection molding process for a snap-on lid. The diagram depicts a mold assembly with two halves: a stationary half and a movable half. Molten plastic, typically polypropylene or polyethylene, is injected into the mold through a sprue. The sprue channels the plastic to runners, which distribute it to the mold cavities. Within the mold cavities, the plastic solidifies, forming the lid’s shape.
Ejector pins then push the solidified lid out of the mold. The mold is cooled throughout the process to facilitate solidification and maintain dimensional accuracy. The diagram highlights the following key components:
- Injection Unit: This unit melts and injects the plastic material.
- Mold: The mold contains the cavity that shapes the lid.
- Sprue: The primary channel for molten plastic to enter the mold.
- Runners: Channels that distribute the plastic to the mold cavities.
- Mold Cavity: The space where the lid takes shape.
- Ejector Pins: Mechanisms that push the finished lid out of the mold.
- Cooling System: A system of channels that circulate coolant to solidify the plastic.
- Clamping Unit: Holds the mold halves together during injection.
Common Lid Sealing Mechanisms
Effective sealing mechanisms are critical for preventing leaks and maintaining the integrity of the food product. The choice of sealing mechanism depends on the lid design and the type of food being packaged.
- Compression Seals: These seals rely on the compression of a sealing material, such as a gasket or a lip, against the container’s rim. Snap-on lids often utilize compression seals. The effectiveness of the seal depends on the material’s compressibility and the applied pressure.
- Threaded Seals: Screw-on lids create a seal through the tight engagement of threads on the lid and the container. The tightness of the seal is influenced by the thread pitch, the applied torque, and the presence of a sealing liner.
- Heat Seals: Heat sealing involves melting a layer of sealant on the lid and bonding it to the container. This method is commonly used for sealing flexible packaging materials, such as those found in pouches and bags.
- Induction Seals: Induction sealing uses an electromagnetic field to heat a foil seal, which then adheres to the container’s rim. This method provides a tamper-evident and airtight seal, often used for products requiring extended shelf life.
The effectiveness of a seal is often quantified by measuring the leakage rate, typically expressed in terms of the volume of fluid that leaks over a specific period under defined pressure conditions.
Factors Influencing Lid Design
Several factors influence the design of plastic food container lids, ensuring that the lid meets the requirements of the food product and the consumer.
- Food Type: The type of food dictates the required level of protection. For example, liquid products necessitate a more robust seal than dry goods. The lid material must also be compatible with the food to prevent chemical reactions or degradation.
- Storage Requirements: Storage conditions, such as temperature, humidity, and shelf life, influence lid design. Lids for frozen foods must withstand low temperatures without cracking or losing their seal. Products with extended shelf lives require airtight and moisture-resistant lids.
- Consumer Convenience: Ease of opening and closing, reusability, and portability are critical consumer considerations. Features like easy-open tabs, ergonomic designs, and secure closures enhance the user experience.
- Material Selection: The plastic material’s properties, including its barrier properties, flexibility, and chemical resistance, impact the lid’s performance. Polypropylene (PP) and polyethylene (PE) are frequently used due to their food safety and recyclability.
- Cost: Production costs influence material selection, manufacturing processes, and design complexity. The lid design must balance functionality and cost-effectiveness to remain competitive in the market.
Food Safety and Regulations for Plastic Food Container Lids
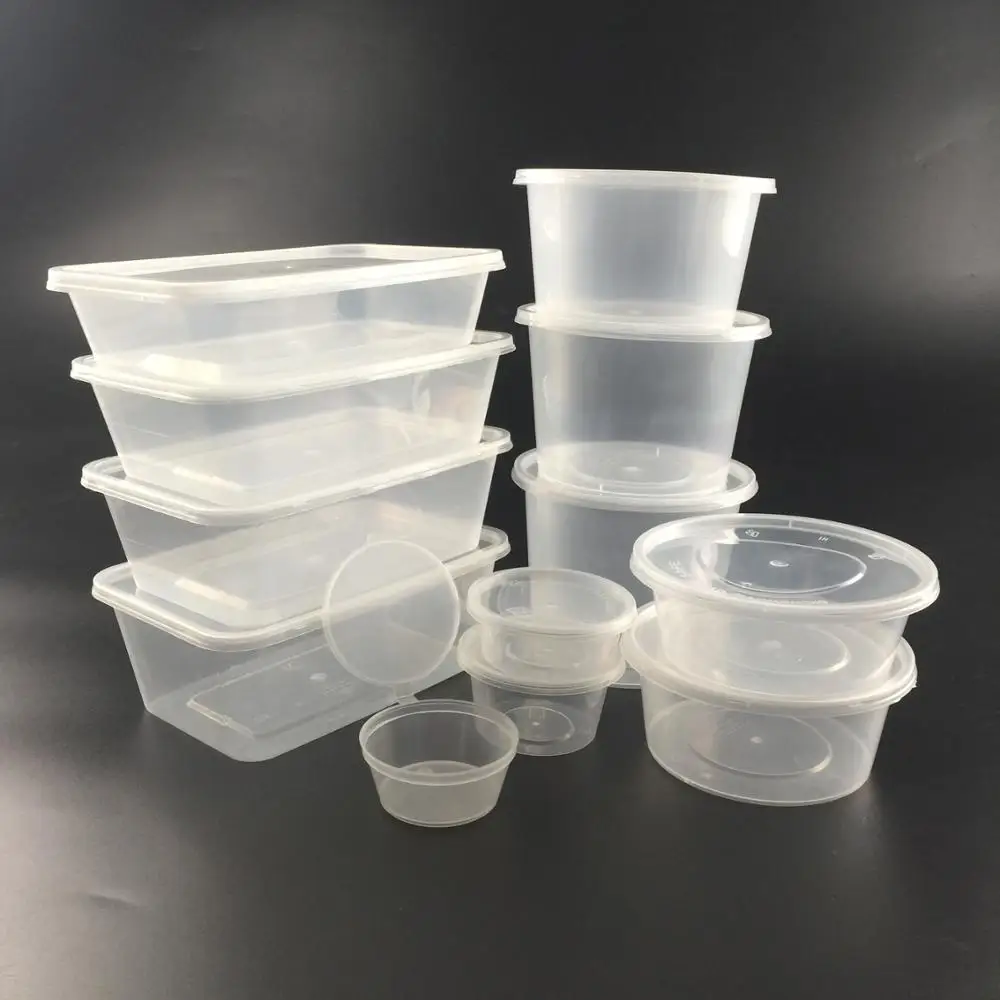
The safety of plastic food container lids is paramount to protect consumer health and maintain the integrity of the food they come into contact with. Food safety regulations and guidelines are essential to ensure that these lids do not leach harmful chemicals into food, thus preventing contamination and ensuring the product’s safety for consumption. Understanding and adhering to these regulations is crucial for manufacturers, distributors, and consumers alike.
Food-Grade Plastics and Contamination Prevention
The selection of appropriate materials is the first and most critical step in ensuring food safety. Food-grade plastics are specifically formulated to be inert and non-reactive when they come into contact with food. This means they are designed not to leach chemicals or additives into the food that could cause harm or alter its taste, odor, or appearance.The use of food-grade plastics is critical for several reasons:
- Preventing Chemical Migration: Food-grade plastics are manufactured to minimize the migration of chemicals from the plastic into the food. This is particularly important for preventing exposure to potentially harmful substances.
- Maintaining Food Integrity: By not reacting with food, food-grade plastics help preserve the food’s original characteristics, including flavor, color, and nutritional value.
- Ensuring Consumer Health: The primary goal is to protect consumers from potential health risks associated with the ingestion of contaminants from non-food-grade plastics.
Overview of Relevant Food Safety Regulations
Numerous regulations and guidelines govern the use of plastics in food contact applications. These regulations are designed to protect public health by setting standards for material composition, manufacturing processes, and labeling requirements.Several key regulatory bodies and their roles include:
- U.S. Food and Drug Administration (FDA): The FDA is the primary regulatory agency in the United States responsible for ensuring the safety of food contact materials, including plastic lids. The FDA sets regulations regarding the types of plastics that can be used, the additives permitted, and the testing required to demonstrate safety. Specific regulations include those Artikeld in 21 CFR (Code of Federal Regulations) Parts 174-189, which detail substances that may be used in food contact materials.
- European Food Safety Authority (EFSA): EFSA provides scientific advice on risks associated with the food chain, including food contact materials. It assesses the safety of substances used in plastic materials and issues opinions on their use. Regulations related to food contact materials in the EU are primarily based on Framework Regulation (EC) No 1935/2004 and specific regulations for plastics, such as Regulation (EU) No 10/2011, which sets out detailed rules for plastic materials and articles intended to come into contact with food.
- Other International Standards: Other countries and regions often have their own specific regulations that align with or are based on the standards set by the FDA and EFSA. These may include guidelines from organizations like the Canadian Food Inspection Agency (CFIA) and various national food safety authorities.
These regulations typically cover aspects such as:
- Material Composition: Permitted substances and additives that can be used in plastic manufacturing.
- Migration Limits: Allowable levels of substances that can migrate from the plastic into food.
- Manufacturing Processes: Requirements for manufacturing practices to prevent contamination.
- Testing and Certification: Testing protocols and certification processes to ensure compliance.
- Labeling Requirements: Information that must be provided on the product label to indicate compliance with regulations.
Identifying Food-Safe Markings and Symbols
Identifying food-safe markings on plastic lids is essential for consumers and businesses. These markings provide assurance that the product has been manufactured in compliance with relevant food safety regulations and is suitable for its intended use.Common markings and symbols include:
- “Food Grade” Symbol: Often represented by a glass and fork symbol. This symbol indicates that the material is safe for food contact.
- Recycling Codes: The recycling code (a number inside a triangle of arrows) can provide information about the type of plastic. While not a direct indicator of food safety, it can help determine the plastic’s properties and potential uses. For example, PETE (1) and HDPE (2) are commonly used for food containers.
- Material Identification: The presence of specific resin codes (e.g., PP for polypropylene) can help identify the type of plastic used. PP is widely considered food-safe.
- Specific Compliance Statements: Manufacturers may include statements such as “BPA-free” or “Complies with FDA regulations” to indicate adherence to specific standards.
These markings should be clearly visible on the lid or container. Consumers should inspect these markings before using the product for food storage.
Risks of Using Non-Food-Grade Plastics
Using non-food-grade plastics for food storage can pose significant health risks due to the potential for chemical migration. These plastics may contain substances that are not safe for human consumption, leading to contamination of the food and potential adverse health effects.The risks associated with non-food-grade plastics include:
- Chemical Leaching: Non-food-grade plastics may leach harmful chemicals, such as phthalates, bisphenol A (BPA), and other additives, into the food. These chemicals can disrupt the endocrine system, cause developmental problems, and increase the risk of certain cancers.
- Toxicity: Some non-food-grade plastics may contain toxic substances that can poison the food, leading to immediate or long-term health problems.
- Altered Food Properties: Non-food-grade plastics can affect the taste, odor, and appearance of the food, making it unpalatable or unsafe to eat.
- Cross-Contamination: These plastics may harbor bacteria or other contaminants that can transfer to the food, increasing the risk of foodborne illnesses.
Using non-food-grade plastics can result in serious health consequences. Consumers should always prioritize food-grade products and avoid using any container that is not specifically labeled as food-safe for food storage.
Steps to Test a Plastic Lid’s Suitability for Food Contact, Plastic food container lid
While not a definitive test, here are steps to help assess a plastic lid’s suitability:
- Visual Inspection: Examine the lid for any markings or symbols indicating food safety.
- Odor Test: Smell the lid. If it has a strong or unusual odor, it may not be food-safe.
- Scratch Test: Gently scratch the surface. If the plastic flakes or the color changes significantly, it might not be suitable for food contact.
- Water Test: Fill the lid with hot water and let it sit for a few minutes. If the water changes color or the plastic becomes cloudy, it may not be food-safe.
- Consult Manufacturer: If unsure, contact the manufacturer for information about the lid’s composition and intended use.
Durability and Performance of Plastic Food Container Lids
The durability and performance of plastic food container lids are critical factors influencing their overall utility and the safety of the food they contain. Lids are subjected to various environmental conditions, mechanical stresses, and repeated use, all of which can compromise their integrity. Understanding these factors is crucial for designing and manufacturing lids that effectively protect food and maintain their functionality over time.
This section will delve into the factors impacting lid durability, compare the performance of different materials, identify common failure modes, and Artikel best practices for maintaining lid integrity.
Factors Affecting Lid Durability
Several factors contribute to the durability of plastic food container lids. These factors influence the lid’s ability to withstand various stresses encountered during its lifecycle, from manufacturing and distribution to consumer use and disposal.* Temperature Changes: Exposure to extreme temperatures, both high and low, significantly impacts the physical properties of plastic lids. High temperatures can cause softening, warping, and degradation of the plastic, potentially leading to leaks or loss of seal.
Conversely, low temperatures can make the plastic brittle, increasing the likelihood of cracking or fracturing upon impact. The thermal expansion and contraction of the plastic material due to temperature fluctuations also contribute to stress, potentially compromising the lid’s fit and sealing ability.* Impact Resistance: The ability of a lid to withstand impacts is essential for its durability. Lids are often subjected to impacts during handling, storage, and transportation.
Impact resistance is determined by the plastic’s inherent properties, such as its tensile strength, elongation at break, and the presence of impact modifiers. A lid with poor impact resistance is prone to cracking or breaking, especially when dropped or subjected to sudden force.* Material Composition: The specific type of plastic used in the lid’s construction plays a crucial role in its durability.
Polypropylene (PP) and polyethylene (PE) are commonly used due to their flexibility, chemical resistance, and ability to withstand temperature variations. However, the addition of additives, such as plasticizers and stabilizers, can also affect durability. For instance, the presence of plasticizers can improve flexibility but may also increase the material’s susceptibility to degradation over time.* Design and Manufacturing Process: The design of the lid, including its shape, thickness, and the presence of any sealing mechanisms, affects its durability.
A lid with a well-designed sealing mechanism, such as a tight-fitting rim or a snap-on closure, will be more resistant to leaks and will maintain its seal better over time. The manufacturing process, including molding techniques and quality control measures, also influences the lid’s durability by ensuring consistency in material properties and dimensional accuracy.
Performance of Different Lid Materials
The performance of plastic lids varies depending on the material used and the conditions they are exposed to. This section compares the performance of common lid materials under various conditions, such as freezer and microwave use.* Polypropylene (PP): PP is a widely used material for food container lids due to its good balance of properties. It exhibits excellent resistance to chemicals, good temperature resistance, and is generally considered safe for food contact.
Freezer Performance
PP lids typically perform well in freezers. They maintain their flexibility and do not become brittle at low temperatures, making them resistant to cracking. However, repeated freeze-thaw cycles can still lead to degradation over time.
Microwave Performance
PP is generally considered microwave-safe, meaning it can withstand the temperatures generated during microwave heating without melting or releasing harmful chemicals. However, it’s important to note that certain foods can reach high temperatures, and lids may warp if they are not designed for microwave use.* Polyethylene (PE): PE is another common material for food container lids. It is known for its flexibility, chemical resistance, and low cost.
Freezer Performance
PE lids also perform well in freezers. They are flexible and do not become brittle at low temperatures.
Microwave Performance
PE is also considered microwave-safe. However, like PP, it’s important to check the specific type of PE used and ensure it is suitable for microwave use.* Polystyrene (PS): PS is sometimes used for lids, but it is less common due to its lower temperature resistance and potential for leaching chemicals.
Freezer Performance
PS lids may become brittle and crack at low temperatures.
Microwave Performance
PS is generally not recommended for microwave use, as it can melt or release harmful chemicals at high temperatures.* Other Materials: Other materials, such as polyethylene terephthalate (PET), are used less frequently for lids but can offer specific advantages, such as high clarity.
Freezer Performance
PET typically performs well in freezers, with good resistance to cracking.
Microwave Performance
Some PET materials are microwave-safe, but it’s essential to check the specific product’s labeling. To illustrate these differences, consider a comparison table: | Material | Freezer Performance | Microwave Performance | Common Uses | | —————- | ————————————————— | ———————————————————— | ——————————————————————————– | | Polypropylene (PP) | Excellent, flexible, resists cracking | Generally safe, may warp with high-temperature foods | Yogurt containers, food storage containers, deli containers | | Polyethylene (PE) | Excellent, flexible, resists cracking | Generally safe, check specific type | Food storage bags, some food containers, deli containers | | Polystyrene (PS) | May become brittle and crack | Generally not recommended, may melt or release chemicals | Rarely used for food container lids due to performance limitations | | Polyethylene Terephthalate (PET) | Good, resistant to cracking | Some are microwave-safe, check product label | Salad containers, some food containers, beverage bottles (with appropriate labeling) |
Common Problems Associated with Lid Failure
Lid failure can manifest in various ways, compromising the container’s ability to protect food and maintain its integrity. Understanding these failure modes is crucial for designing more durable lids.* Cracking: Cracking is a common mode of failure, especially at points of stress, such as corners, hinges, or sealing areas. Cracks can arise from impact, temperature fluctuations, or material degradation.* Warping: Warping occurs when the lid deforms due to heat exposure or uneven stresses.
Warping can lead to a loss of seal, allowing air and contaminants to enter the container.* Loss of Seal: A loss of seal is often a consequence of cracking, warping, or degradation of the sealing mechanism. This failure allows for leaks and potential contamination of the food.* Brittleness: Certain materials, especially those that have degraded due to age or environmental factors, can become brittle.
This makes them susceptible to cracking or breaking upon impact.* Deformation: Deformation can occur under sustained pressure or heat. This can alter the lid’s shape and prevent it from sealing properly.* Discoloration and Degradation: Over time, plastic lids can discolor or degrade due to exposure to UV light, chemicals, or repeated washing. This can affect their appearance and potentially compromise their structural integrity.
Impact of Repeated Use and Washing
Repeated use and washing cycles can significantly impact the integrity of plastic food container lids. The cumulative effects of these processes can accelerate degradation and reduce the lid’s lifespan.* Mechanical Stress: Repeated opening and closing, as well as the physical handling during washing, put mechanical stress on the lid. This can lead to wear and tear on hinges, sealing mechanisms, and the lid’s overall structure.* Chemical Exposure: Washing with detergents and exposure to hot water can degrade the plastic over time.
Harsh detergents can cause chemical reactions that weaken the material, while hot water can accelerate the breakdown of the plastic’s molecular structure.* Abrasion: The abrasive action of washing, especially with abrasive sponges or in dishwashers, can scratch the lid’s surface. These scratches can weaken the material and create points of vulnerability for cracks or leaks.* UV Degradation: Repeated exposure to sunlight or other UV sources can degrade the plastic, leading to discoloration, embrittlement, and a loss of mechanical strength.* Accumulation of Residues: Over time, food residues and other contaminants can accumulate on the lid, potentially leading to the growth of bacteria or mold.
Thorough cleaning and proper storage are crucial to mitigate this issue.
Best Practices for Maintaining Plastic Lid Performance and Longevity
Implementing best practices can significantly extend the lifespan and maintain the performance of plastic food container lids. These practices focus on proper handling, cleaning, and storage.* Avoid extreme temperatures: Prevent exposure to direct sunlight or excessive heat.* Use appropriate cleaning methods: Use mild detergents and avoid abrasive cleaners.* Wash by hand: Handwashing is gentler than machine washing.* Handle with care: Avoid dropping or subjecting lids to excessive force.* Inspect regularly: Check for cracks, warping, or other signs of damage.* Store properly: Store lids in a cool, dry place, away from direct sunlight.* Follow manufacturer’s instructions: Adhere to any specific care instructions provided by the manufacturer.* Replace damaged lids: Discard and replace any lids that show signs of damage.
Environmental Impact and Sustainability of Plastic Food Container Lids
The environmental impact of plastic food container lids is a significant concern, encompassing their production, use, and disposal. The widespread adoption of these lids has led to substantial waste generation and environmental pollution. Understanding these impacts and exploring sustainable alternatives is crucial for mitigating the negative consequences associated with their lifecycle.
Environmental Impact of Plastic Lid Production, Use, and Disposal
The environmental impact of plastic lids spans the entire product lifecycle, from raw material extraction to end-of-life management. This section will explore the different stages and their corresponding effects.
- Production: The manufacturing of plastic lids necessitates the extraction and processing of fossil fuels, primarily crude oil, a non-renewable resource. This process contributes to greenhouse gas emissions, including carbon dioxide (CO2), which exacerbates climate change. Manufacturing also consumes significant amounts of energy and water, further adding to the environmental footprint.
- Use: During use, plastic lids may contribute to microplastic pollution if they degrade or break down. The leaching of chemicals from the plastic into food, especially under heat, is another potential health concern with indirect environmental impacts. Moreover, single-use plastic lids contribute to waste accumulation.
- Disposal: The disposal of plastic lids presents a significant challenge. Landfilling is a common method, but it leads to long-term pollution, as plastic takes hundreds of years to decompose. Incineration, another disposal method, releases pollutants into the atmosphere. Plastic lids often end up in the environment, including oceans, where they contribute to plastic pollution, harming marine life.
Recyclability of Different Types of Plastic Lids and Challenges
The recyclability of plastic lids varies depending on the type of plastic used and the infrastructure available for recycling. This section examines the recyclability of different plastic types and the challenges faced in the recycling process.
- Common Plastic Types: Polypropylene (PP, resin identification code #5) and Polyethylene (PE, resin identification code #2 or #4) are the most common plastics used for food container lids. These plastics are generally recyclable, but the success depends on the local recycling programs.
- Recycling Challenges: Several factors impede the effective recycling of plastic lids:
- Material Complexity: Lids can be made from mixed materials or have additives that complicate the recycling process.
- Contamination: Lids often contain food residue, which can contaminate the recycling stream and reduce the quality of recycled materials.
- Size and Shape: The small size and irregular shapes of lids can make them difficult to sort using automated recycling equipment. They may also fall through the sorting machinery.
- Infrastructure Limitations: Recycling infrastructure varies widely across regions. Many communities lack the necessary facilities to process certain types of plastic or effectively sort small items like lids.
- Impact of Recycling: Effective recycling reduces the demand for virgin plastic, conserving fossil fuels and lowering greenhouse gas emissions. However, the recycling process itself requires energy and water.
Alternative Materials in Lid Manufacturing
The search for more sustainable alternatives to traditional plastics in lid manufacturing is ongoing. This section details several alternative materials and their potential benefits.
- Bioplastics: Bioplastics are derived from renewable resources, such as corn starch, sugarcane, or cellulose. Examples include polylactic acid (PLA) and polyhydroxyalkanoates (PHAs). These materials can potentially reduce the reliance on fossil fuels and lower greenhouse gas emissions. However, the environmental impact of bioplastics depends on their source, production methods, and end-of-life management. For example, the cultivation of crops for bioplastic production can require significant land, water, and fertilizer, which can lead to deforestation and other environmental issues.
- Paper-based materials: Paper-based lids, often coated with a thin layer of a barrier material for moisture resistance, offer a renewable alternative. However, the barrier coatings may contain plastic or other materials that limit their recyclability and compostability.
- Other Materials: Innovations include lids made from recycled plastic, which helps to reduce waste and promote a circular economy. Research is ongoing into materials like mycelium (mushroom root structures) and seaweed-based packaging.
Composting and Biodegradation of Plastic Lids
Composting and biodegradation are crucial aspects of end-of-life management for plastic lids, particularly for those made from bioplastics. This section will describe these processes in the context of plastic lids.
- Composting: Composting is a biological process that breaks down organic materials into nutrient-rich compost. Some bioplastics, like PLA, are compostable under specific conditions in industrial composting facilities. Home composting is often not effective for bioplastics.
- Biodegradation: Biodegradation is the process where materials are broken down by microorganisms into simpler substances, such as water, carbon dioxide, and biomass. The biodegradability of plastic lids varies. Traditional plastics are designed to be durable and are not biodegradable in most environments. Bioplastics are designed to biodegrade, but the rate and extent of biodegradation depend on the material and the environmental conditions.
- Challenges: The lack of widespread access to industrial composting facilities and the potential for bioplastics to contaminate conventional plastic recycling streams are significant challenges. Additionally, some bioplastics may only biodegrade under specific conditions of temperature, humidity, and microbial activity, which are not always present in natural environments.
Comparison of Environmental Impact of Lid Materials
A comparison table is presented below, summarizing the environmental impact of various lid materials. The comparison considers the following factors: raw material source, energy consumption in production, recyclability/compostability, and potential for environmental contamination.
Material | Raw Material Source | Recyclability/Compostability | Potential for Environmental Contamination |
---|---|---|---|
Plastic (e.g., PP, PE) | Fossil fuels (crude oil) | Recyclable (depending on local programs), not biodegradable | High: Microplastic pollution, leaching of chemicals, long-term landfill impact |
Bioplastic (e.g., PLA) | Renewable resources (e.g., corn starch) | Compostable (in industrial facilities), potentially recyclable with limitations | Moderate: Requires specific composting conditions, potential for contamination of recycling streams, land use impact |
Alternative Materials (e.g., Paper-based with coatings) | Renewable resources (e.g., wood pulp) | Recyclable (depending on coating), compostable (depending on coating) | Moderate: Potential for plastic contamination from coatings, waste from production |
Types and Applications of Plastic Food Container Lids
Plastic food container lids are integral components of the food packaging industry, offering a range of functionalities from preserving food freshness to ensuring safe transportation. Their diverse designs and applications reflect the varying needs of different food products and consumer requirements. Understanding the different types of lids and their specific uses is crucial for optimizing food packaging performance and safety.
Lid Types for Take-Out, Storage, and Beverage Containers
The design of plastic food container lids varies significantly depending on their intended use. This diversity allows manufacturers to tailor lid features to the specific requirements of the food product and the intended consumer experience.* Take-Out Container Lids: These lids are typically designed for ease of use and portability. They often feature a snap-on or click-on closure mechanism to ensure a secure seal during transport.
Clear lids are common, allowing consumers to view the contents. The materials used prioritize cost-effectiveness and often incorporate polypropylene (PP) or polyethylene terephthalate (PET) due to their ability to withstand moderate temperatures and provide a degree of flexibility. Examples include lids for disposable containers used in restaurants and food delivery services.* Storage Container Lids: Designed for longer-term food preservation, storage container lids prioritize airtight seals and durability.
They often incorporate features like rubber or silicone gaskets to enhance the seal and prevent leaks. Materials such as polypropylene (PP) are favored for their resistance to chemicals and ability to withstand repeated washing and use. The designs often include features for easy stacking and nesting to optimize storage space.* Beverage Cup Lids: These lids focus on spill prevention and ease of drinking.
They commonly feature a drinking aperture, which may be covered by a sliding or hinged closure. The design considerations include the compatibility of the lid material with hot and cold beverages. Polystyrene (PS) and PET are frequently used for their clarity and ability to be molded into various shapes. The focus is on user convenience and minimizing the risk of spills, especially in on-the-go scenarios.
Specialized Lid Designs for Specific Food Products
Certain food products necessitate specialized lid designs to maintain product integrity and freshness. These designs incorporate specific features tailored to the unique properties of the food being packaged.* Airtight Lids for Liquids: These lids are designed to create a completely sealed environment, preventing leakage and maintaining the product’s freshness. The design typically includes a tight-fitting seal, often achieved through a combination of the lid material and a gasket made of a flexible material like silicone or thermoplastic elastomers (TPE).
The closure mechanisms are robust, such as screw-on or pressure-fit, to ensure a secure seal. Examples include lids for sauces, dressings, and beverages.* Lids with Vents for Microwaving: These lids are designed to release steam during microwave heating. They typically incorporate vents or small openings that allow excess pressure to escape, preventing explosions and ensuring even heating. The vent design can vary, from simple perforations to more complex, adjustable vents.
The materials used must be microwave-safe, such as polypropylene (PP), and designed to withstand the temperatures generated during microwave heating.* Lids with Tamper-Evident Features: These lids are designed to provide assurance that the product has not been opened or compromised after packaging. They often feature a breakable seal or a visible indication of tampering. Examples include lids with tear-off bands or shrink-wrap seals.
These features are critical for ensuring product safety and preventing contamination.
Key Features of Lids Designed for Microwave Use
Lids intended for microwave use must be designed with specific features to withstand the heating process and maintain the integrity of the food and the container.* Material Selection: The primary consideration is the selection of microwave-safe materials. Polypropylene (PP) is a common choice due to its high melting point, chemical resistance, and ability to withstand the temperatures generated during microwave heating.
The material should also be food-grade and not leach harmful chemicals into the food when heated.* Ventilation Design: Proper ventilation is crucial to prevent pressure buildup, which can cause the lid to warp or explode. Lids often incorporate vents or small openings that allow steam to escape during heating. The design of these vents can vary, from simple perforations to adjustable vents that control the amount of steam released.* Heat Resistance: The lid must be able to withstand the temperatures generated during microwave heating without warping or melting.
The design and material selection must ensure that the lid retains its shape and functionality throughout the heating process.* Food Safety: The lid must be designed to prevent the food from splattering or drying out during heating. The design may include features like raised edges or a recessed area to contain the food. The lid material must also be inert and not react with the food or release harmful chemicals when heated.
Advantages and Disadvantages of Different Lid Closure Mechanisms
The closure mechanism of a plastic food container lid plays a crucial role in its functionality, influencing factors such as seal integrity, ease of use, and cost. Different mechanisms offer unique advantages and disadvantages.* Click-On/Snap-On Closures:
Advantages
Easy to use, provide a secure seal, cost-effective, and often allow for visual confirmation of closure.
Disadvantages
Can be prone to accidental opening if not designed properly, seal integrity may be compromised over time with repeated use, and may not be suitable for airtight applications.* Screw-On Closures:
Advantages
Provide a tight, airtight seal, suitable for liquids and products requiring long-term storage, and offer good tamper evidence.
Disadvantages
Can be more difficult to open and close, require a more complex design, and are typically more expensive to manufacture.* Pressure-Fit Closures:
Advantages
Simple design, easy to manufacture, and can provide a reasonably good seal.
Disadvantages
Seal integrity may vary, can be prone to leakage, and may be less durable than other closure mechanisms.* Hinged Closures:
Advantages
Convenient for single-use applications, easy to open and close, and can be integrated into the lid design.
Disadvantages
Seal integrity may be limited, often less durable than other closure mechanisms, and may be more prone to breakage.
Uses of Plastic Food Container Lids Across Different Industries
Plastic food container lids are used in a wide range of industries to package and protect various food products.* Food Service Industry: Lids are used extensively for take-out containers, salad bowls, and beverage cups. They provide a secure and hygienic way to transport food and beverages.
Retail Food Industry
Lids are used for packaging a variety of food products, including deli items, prepared meals, and fresh produce. They help maintain product freshness and extend shelf life.
Beverage Industry
Lids are essential for sealing beverage cups and bottles, preventing spills and maintaining the integrity of the product.
Dairy Industry
Lids are used for packaging yogurt, sour cream, and other dairy products, providing a secure seal and protecting the contents.
Prepared Food Industry
Lids are used for packaging ready-to-eat meals, microwaveable dinners, and other prepared food products, ensuring food safety and convenience.
Pharmaceutical Industry
Lids are used to seal containers for liquid medications and supplements.
Ending Remarks
So, there you have it, a comprehensive look at the plastic food container lid. We’ve journeyed from the raw materials to the final disposal, exploring every aspect of these essential items. Remember, understanding these things helps us make informed choices, both for our health and for the planet. May Allah SWT grant us all knowledge and wisdom. Jazakumullahu Khairan.