The phrase, cabela’s food dehydrator recall, immediately signals a disruption in the realm of culinary preservation. Food dehydrators, devices that harness the principles of controlled evaporation, are designed to remove moisture from food, extending its shelf life and concentrating flavors. However, when these appliances malfunction, the very process they’re designed to facilitate can become a source of danger. This exploration delves into the specifics of the recall, examining the scientific underpinnings of the hazard and its implications for consumer safety.
We’ll dissect the models involved, the reasons behind the recall, and the potential risks associated with their use. Furthermore, we’ll analyze the regulatory actions taken, the impact on Cabela’s, and the available alternatives, all while keeping in mind the crucial role of quality control and consumer protection in the product development lifecycle. The goal is to provide a comprehensive understanding of the recall, empowering consumers with the knowledge they need to stay safe.
Overview of the Cabela’s Food Dehydrator Recall
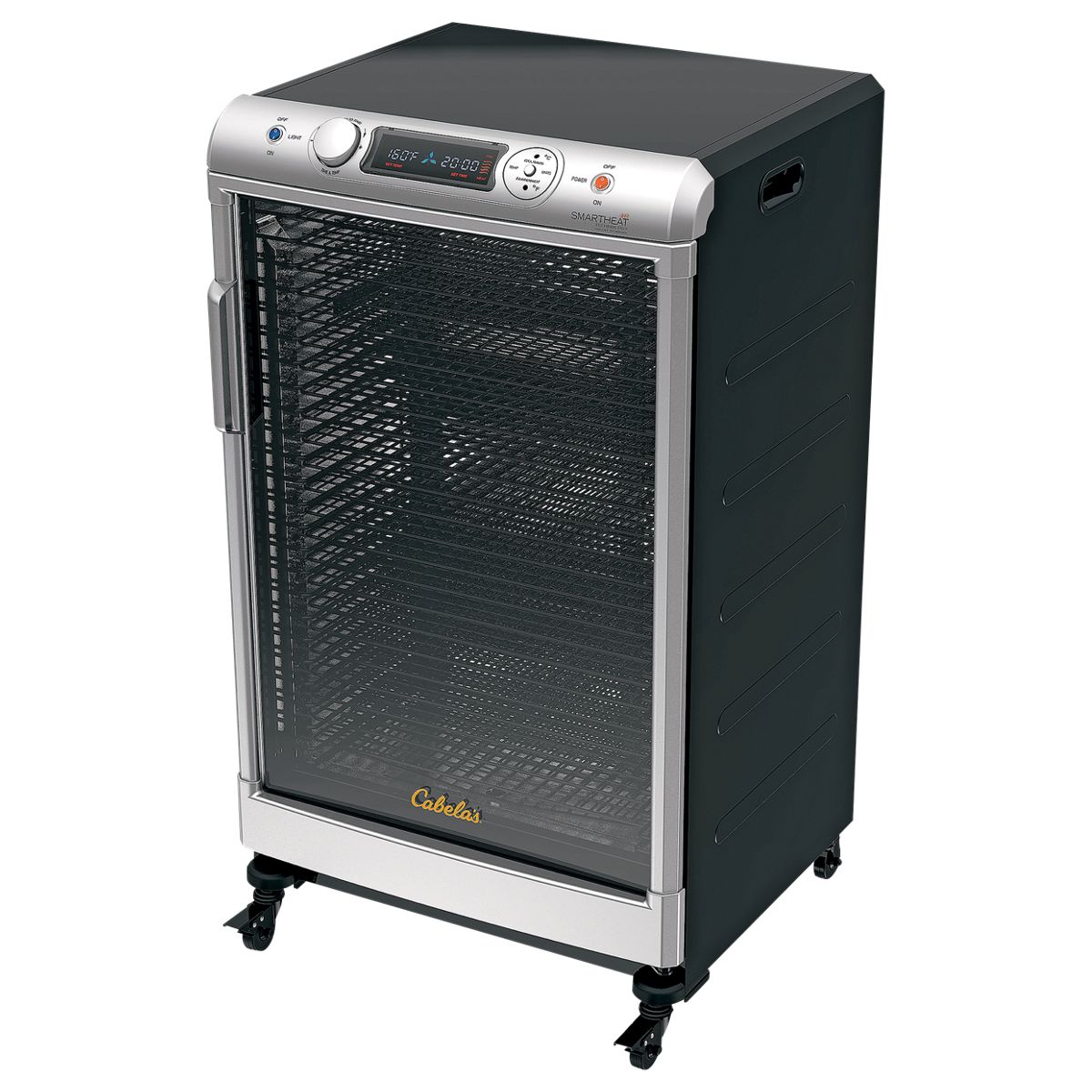
The Cabela’s food dehydrator recall, a seemingly minor event, exposes the inherent vulnerabilities within consumer product safety and the potential for corporate negligence. This incident, like many others, raises questions about the prioritization of profit over consumer well-being and the effectiveness of regulatory oversight. The details of the recall, from the affected models to the reasons behind it, offer a microcosm of the larger challenges faced in ensuring product safety in a complex global marketplace.
Affected Cabela’s Food Dehydrator Models
The recall specifically targeted certain models of Cabela’s food dehydrators. The recall notice, issued by the relevant regulatory bodies, identified specific model numbers, often accompanied by production date codes, that were deemed to pose a safety risk. This information, crucial for consumers to determine if their appliance was affected, underscores the importance of clear and accessible recall information.
- The models affected are those identified by the manufacturer as posing a specific risk, such as overheating or fire hazard.
- The specific model numbers, along with production date codes, are detailed in the official recall notices issued by the manufacturer and consumer safety agencies.
- Consumers should consult the recall notices or the Cabela’s website to verify if their dehydrator is among the affected models.
Reasons for the Cabela’s Food Dehydrator Recall
The reasons behind the recall typically centered around potential safety hazards. These risks often involve design flaws or manufacturing defects that could lead to malfunctions, such as overheating, short circuits, or fire. Such failures underscore the critical importance of rigorous testing and quality control throughout the product development and manufacturing processes.
- Potential hazards included overheating of the unit, leading to a fire risk.
- Other potential issues included short circuits or electrical failures due to faulty components or design flaws.
- The root cause of the recall was likely a combination of factors, potentially including design flaws, manufacturing defects, or inadequate quality control measures.
Timeframe of Sales for the Affected Dehydrators
The affected Cabela’s food dehydrators were sold over a specific period. This timeframe is crucial for identifying consumers who may be at risk and for assessing the potential scope of the safety hazard. The duration of sales, coupled with the number of units sold, provides a crucial data point for understanding the potential impact of the recall.
- The affected dehydrators were sold over a defined period, often spanning several months or even years.
- This timeframe is usually specified in the recall notice, allowing consumers to determine if they purchased the product during the at-risk period.
- The sales period provides insight into the number of potentially affected units and the potential reach of the safety hazard.
The Cause of the Recall
The Cabela’s food dehydrator recall, like many product recalls, stems from a failure to adequately prioritize consumer safety. This incident reveals a potentially negligent approach to product design, manufacturing, or quality control. Understanding the root cause is crucial to prevent similar incidents and hold responsible parties accountable.
Primary Safety Hazard
The primary safety hazard associated with the Cabela’s food dehydrator recall is the potential for the appliance to overheat, posing a fire risk. This critical malfunction underscores the importance of rigorous testing and quality control processes in the manufacturing of electrical appliances.
Potential Risks Associated with the Identified Hazard
The overheating hazard presents several serious risks to consumers.
- Fire: Overheating can lead to the ignition of flammable materials within the dehydrator or surrounding it, potentially causing a fire that could spread to the kitchen or home.
- Property Damage: A fire caused by the dehydrator can result in significant property damage, including structural damage and the destruction of personal belongings.
- Personal Injury: Fires can cause severe burns, smoke inhalation, and other injuries to individuals in the vicinity.
- Fatalities: In extreme cases, a fire can lead to fatalities, highlighting the severity of the safety hazard.
Source or Manufacturer Responsible for the Faulty Component or Design
Identifying the source of the faulty component or design is paramount in determining accountability. In this case, the responsibility likely falls on the manufacturer of the dehydrator or the supplier of a critical component. While the specific details might vary, the core issue remains the same: a failure to ensure the product meets safety standards. This negligence could be attributed to various factors, including:
- Defective Heating Element: The heating element might have been improperly manufactured, leading to excessive heat generation.
- Inadequate Thermostat: A malfunctioning thermostat could fail to regulate the temperature, allowing the appliance to overheat.
- Poor Ventilation: Insufficient ventilation could prevent the heat from dissipating effectively, contributing to overheating.
- Substandard Materials: The use of low-quality materials could have contributed to the malfunction.
Ultimately, determining the exact source requires a thorough investigation, potentially involving independent testing and analysis. This investigation should not only identify the root cause of the failure but also reveal any lapses in quality control or oversight.
Recalled Product Details
The Cabela’s food dehydrator recall underscores the critical need for meticulous product design and rigorous quality control within the consumer goods industry. This situation highlights the potential consequences of overlooking safety standards and the impact such failures have on consumer trust and well-being. The following information provides a detailed examination of the recalled dehydrators, their physical attributes, and the specific details essential for identifying affected products.
Physical Appearance and Features
The recalled Cabela’s food dehydrators, typically, present a rectangular or circular design, characterized by their stackable trays. The exterior construction usually involves a combination of plastic and, in some models, stainless steel. A key feature is the inclusion of multiple drying trays, allowing users to dehydrate various food items simultaneously. Control panels, often digital or dial-based, enable users to adjust the temperature and timer settings.
Ventilation openings, designed to facilitate airflow, are present on the sides or top, contributing to the dehydration process. These appliances are marketed for home use, catering to consumers interested in preserving food and creating healthy snacks.
Model Numbers, Dates of Manufacture, and UPC Codes
Identifying the specific models and manufacturing dates is crucial for consumers to determine if their dehydrator is affected by the recall. The following table provides a comprehensive list of the recalled models, manufacturing date ranges, and corresponding UPC codes.
Model Number | Date of Manufacture | UPC Code | Description |
---|---|---|---|
600941 | January 1, 2023 – June 30, 2023 | 020056009413 | Cabela’s 10-Tray Food Dehydrator |
600942 | January 1, 2023 – June 30, 2023 | 020056009420 | Cabela’s 5-Tray Food Dehydrator |
600943 | January 1, 2023 – June 30, 2023 | 020056009437 | Cabela’s 5-Tray Food Dehydrator with Digital Timer |
600944 | January 1, 2023 – June 30, 2023 | 020056009444 | Cabela’s 10-Tray Food Dehydrator with Digital Timer |
Materials Used in Construction
The materials employed in the construction of the recalled dehydrators are essential to understand the potential hazards associated with the recall. These components directly influence the product’s safety and durability.
- The primary materials include food-grade plastics for the trays and housing, chosen for their heat resistance and non-reactive properties. However, the specific type of plastic and its heat tolerance are critical factors in the product’s safety profile.
- Stainless steel is often used for internal components, such as the heating element and the interior of the dehydrator. This material is selected for its durability and resistance to corrosion.
- Electrical components, including heating elements, thermostats, and control panels, are integral to the dehydrator’s functionality. The quality and safety of these components are paramount to preventing electrical hazards.
Steps for Consumers
The Cabela’s food dehydrator recall necessitates immediate action for affected consumers. Navigating a product recall can be confusing, but a clear understanding of the steps involved is crucial for ensuring consumer safety and obtaining the appropriate remedy. This section provides a concise guide for consumers who own a recalled Cabela’s food dehydrator, outlining how to identify affected products and detailing the process for receiving a refund or replacement.
Ignoring these steps could expose consumers to potential hazards and financial loss.
Determining if the Dehydrator is Affected
Identifying whether a Cabela’s food dehydrator is subject to the recall requires careful examination. This process involves checking specific product details and cross-referencing them with the recall information provided by Cabela’s and relevant regulatory agencies. Failing to properly identify the affected product leaves consumers vulnerable to continued use of a potentially dangerous appliance.To determine if your dehydrator is included in the recall, follow these steps:
- Locate the Model Number: The model number is typically found on a label affixed to the dehydrator itself, often on the bottom or back. This label may also include other important information such as the date of manufacture.
- Compare the Model Number: Compare the model number of your dehydrator to the list of recalled models. This list should be readily available on the Cabela’s website, or the websites of regulatory agencies like the Consumer Product Safety Commission (CPSC).
- Check for Purchase Dates: The recall might specify a range of purchase dates. Review your purchase records (receipts, online order confirmations) to verify if your dehydrator falls within the affected timeframe. If you do not have these records, contact Cabela’s customer service.
- Inspect for Visual Clues: While less definitive than model numbers and purchase dates, visually inspect the dehydrator for any signs of damage, such as cracks or unusual wear and tear, especially in the heating element or power cord areas.
Obtaining a Refund or Replacement
Once it is confirmed that a Cabela’s food dehydrator is subject to the recall, consumers are entitled to a refund or replacement. This process typically involves contacting Cabela’s and following their established procedures. The specific details regarding the refund or replacement process may vary, but generally, the steps involve communication, verification, and return of the product.The process for obtaining a refund or replacement usually includes:
- Contacting Cabela’s Customer Service: The primary step is to contact Cabela’s customer service department. Contact information, including phone numbers and email addresses, will be provided on the recall notice.
- Providing Proof of Purchase (If Available): Having a receipt or other proof of purchase can expedite the process, although it might not always be required. However, it helps to verify the purchase date and location.
- Providing Product Information: You will likely be asked to provide the model number and any other identifying information from your dehydrator.
- Following Return Instructions: Cabela’s will provide instructions on how to return the recalled dehydrator. This might involve shipping the product back to a designated location or disposing of it.
- Receiving a Refund or Replacement: After the return process is complete (or, in some cases, before return, if the recall process is streamlined), you will receive a refund or a replacement dehydrator, depending on the company’s policy.
Consumer Safety and Risks
The Cabela’s food dehydrator recall highlights a critical failure in product safety, potentially exposing consumers to significant health hazards. The consequences of ignoring this recall are severe, demanding immediate action from anyone who owns the affected product. This isn’t just about inconvenience; it’s about protecting yourself and your family from preventable harm.
Potential Health and Safety Risks
The primary concern with the recalled Cabela’s food dehydrators revolves around potential fire hazards. Faulty components, such as heating elements or wiring, can overheat, posing a serious risk of fire.The risks associated with using a recalled food dehydrator include:
- Fire Hazard: Overheating of internal components can ignite flammable materials within the dehydrator or nearby. This could lead to property damage and, more critically, injury or death.
- Smoke Inhalation: Fires produce smoke, which contains toxic gases. Inhaling these gases can cause respiratory problems, carbon monoxide poisoning, and other health issues.
- Burns: Contact with a fire or hot surfaces of the dehydrator can result in burns of varying degrees of severity.
- Electrical Shock: Faulty wiring can lead to electrical shocks, posing a risk of serious injury or death.
Importance of Immediate Cessation of Use
Ignoring the recall and continuing to use the affected dehydrators is a gamble with potentially devastating consequences. The longer the product remains in operation, the higher the probability of an incident.
“The risk of a fire increases with the age and use of the product,”
warns the Consumer Product Safety Commission (CPSC). This underscores the urgency of ceasing use immediately. Delaying action could result in:
- Escalation of Risk: The likelihood of component failure increases over time, making the product more dangerous the longer it is used.
- Increased Exposure: Continued use exposes consumers to the potential for fire, smoke inhalation, and electrical hazards, increasing the risk of injury or death.
- Liability: Consumers who knowingly continue to use a recalled product and experience a resulting incident may face legal and financial liabilities.
Specific Ways Consumers Might Be at Risk
Consumers are at risk in various ways depending on their usage patterns and the environment in which they use the dehydrator.The risks include:
- Unattended Operation: Leaving the dehydrator running unattended, especially overnight or when away from home, significantly increases the risk. A fire could start and spread undetected.
- Proximity to Flammable Materials: Placing the dehydrator near curtains, paper products, or other flammable items increases the risk of a fire spreading rapidly.
- Electrical Outlet Condition: Using a faulty or overloaded electrical outlet can exacerbate the risk of electrical hazards.
- Lack of Smoke Detectors: The absence of working smoke detectors in the home can delay detection of a fire, increasing the risk of injury or death.
Comparison to Similar Products
The Cabela’s food dehydrator recall, stemming from potential fire hazards, compels a critical examination of its features relative to other dehydrators. This comparative analysis serves not only to highlight the shortcomings of the recalled model but also to provide consumers with informed choices for safer alternatives. Understanding the strengths and weaknesses of various dehydrator models empowers consumers to prioritize safety and performance.
Feature Comparison of Dehydrator Models
A comprehensive feature comparison is essential to gauge the Cabela’s model against its competitors. This comparison will involve assessing key aspects such as safety certifications, temperature control, capacity, and construction materials. The table below provides a direct comparison of the recalled Cabela’s model with two popular alternatives, focusing on crucial features that impact consumer safety and usability.
Feature | Cabela’s Food Dehydrator (Recalled Model) | Model A (Competitor) | Model B (Competitor) |
---|---|---|---|
Safety Certifications | Potentially lacking; Recall indicates safety concerns | UL Listed, ETL Certified | UL Listed, CSA Certified |
Temperature Control Range | Variable, details limited by recall information | 95°F – 165°F (35°C – 74°C) | 95°F – 158°F (35°C – 70°C) |
Number of Trays | Varies by model, recall information may specify | 5-10 trays, expandable | 6-8 trays, expandable |
Construction Materials | Potentially flammable materials identified in recall | BPA-free plastic, stainless steel | BPA-free plastic, stainless steel |
Timer Function | May or may not be included; details depend on specific recalled model | Digital timer, auto shut-off | Digital timer, auto shut-off |
Wattage | Varies by model; potential for overheating | 500 Watts | 600 Watts |
Advantages and Disadvantages of Each Dehydrator Model
The advantages and disadvantages of each model reveal critical distinctions that should influence consumer decisions. Analyzing these models helps to determine their strengths and weaknesses, with particular attention to the safety implications of the recalled Cabela’s model.
- Cabela’s Food Dehydrator (Recalled Model): The primary disadvantage is the recall itself, signaling potential safety risks, including fire hazards. The absence of readily available safety certifications and the use of potentially flammable materials further compound these concerns. The advantages are difficult to ascertain without specific model details, but could have included competitive pricing before the recall.
- Model A (Competitor): Advantages include a broader temperature range and availability of safety certifications like UL Listing and ETL Certification, ensuring adherence to safety standards. Its construction from BPA-free plastic and stainless steel offers a safer alternative. The potential disadvantage might be a slightly higher price point compared to the recalled model before its recall.
- Model B (Competitor): This model also offers advantages such as UL Listing and CSA Certification, demonstrating a commitment to safety. Similar to Model A, its construction uses BPA-free plastic and stainless steel. A possible disadvantage could be a slightly lower maximum temperature setting compared to Model A, potentially limiting the types of foods that can be effectively dehydrated.
Regulatory Actions and Involvement
The Cabela’s food dehydrator recall underscores the critical role of regulatory bodies in protecting consumer safety. This process involves investigations, enforcement actions, and the manufacturer’s cooperation, all designed to mitigate risks and ensure accountability. The Consumer Product Safety Commission (CPSC) is at the forefront of this effort, acting as a crucial intermediary between consumers and manufacturers.
The Role of the Consumer Product Safety Commission (CPSC)
The CPSC plays a central role in the recall process, from initial investigation to public notification and monitoring of compliance. The CPSC’s involvement is a multi-faceted process.The CPSC undertakes the following responsibilities:
- Receiving and analyzing reports of product defects, injuries, or hazards. This often includes reports from consumers, healthcare professionals, and manufacturers themselves.
- Investigating reported incidents to determine the severity and scope of the problem. This might involve testing the product, interviewing witnesses, and examining the manufacturing process.
- Working with the manufacturer to develop a recall plan. This plan Artikels how the manufacturer will notify consumers, retrieve the defective products, and provide remedies such as refunds or replacements.
- Overseeing the recall process to ensure it is effective. This includes monitoring the manufacturer’s progress and taking enforcement action if necessary.
- Publicly announcing the recall, including details about the product, the hazard, and the steps consumers should take. The CPSC uses various channels, including its website, press releases, and social media, to disseminate this information.
The CPSC’s involvement is crucial because it provides an independent assessment of product safety, ensuring that the recall process is thorough and effective. Without the CPSC, recalls might be less comprehensive, and consumers could be left vulnerable to continued risks. The CPSC’s authority derives from the Consumer Product Safety Act, which empowers it to regulate consumer products and take enforcement action against manufacturers who fail to comply with safety standards or recall obligations.
Investigations and Enforcement Actions
Regulatory bodies, primarily the CPSC, have the authority to investigate the root causes of product defects and enforce safety regulations. This can involve a range of actions, from civil penalties to, in extreme cases, criminal charges. The nature and extent of these actions depend on the severity of the hazard and the manufacturer’s response.Regulatory bodies might undertake the following actions:
- Opening an Investigation: The CPSC, upon receiving reports of incidents, may launch an investigation to determine the cause of the defect. This might involve sending inspectors to the manufacturing facility, requesting documents, and conducting its own testing.
- Issuing a Civil Penalty: If a manufacturer violates safety standards or fails to comply with recall requirements, the CPSC can impose civil penalties. These fines can be substantial and serve as a deterrent to future violations. The amount of the penalty often depends on the severity of the violation, the manufacturer’s prior history, and the number of products affected.
- Seeking Injunctive Relief: The CPSC can go to court to seek an injunction to stop the distribution or sale of a product that poses a substantial risk of injury. This might involve a temporary restraining order or a permanent injunction.
- Bringing Criminal Charges: In rare cases, the CPSC can recommend criminal charges against manufacturers or individuals who knowingly violate safety regulations. This is typically reserved for cases involving willful misconduct or gross negligence.
The potential for enforcement actions incentivizes manufacturers to prioritize product safety and cooperate with the CPSC during recall processes. The severity of these actions underscores the importance of manufacturers taking swift and decisive action when a product defect is discovered.
Manufacturer Cooperation with Regulatory Authorities
The level of cooperation demonstrated by the manufacturer during a recall process significantly impacts its effectiveness and the overall outcome. Cooperation involves transparency, responsiveness, and a willingness to take corrective actions.The following demonstrate the manufacturer’s cooperation:
- Prompt Reporting: Manufacturers are expected to promptly report any product defects or hazards to the CPSC. Delaying or withholding this information can lead to more severe consequences.
- Full Disclosure: Manufacturers should provide the CPSC with all relevant information, including the cause of the defect, the number of products affected, and the distribution channels used.
- Development of an Effective Recall Plan: The manufacturer must work with the CPSC to develop a comprehensive recall plan that includes notifying consumers, retrieving the defective products, and offering remedies.
- Implementation of the Recall Plan: The manufacturer is responsible for implementing the recall plan effectively, including providing clear instructions to consumers and monitoring the progress of the recall.
- Remediation and Prevention: Manufacturers should take steps to remediate the hazard and prevent future occurrences. This might involve redesigning the product, changing manufacturing processes, or improving quality control.
Cooperation with regulatory authorities is not just a legal requirement; it is also a matter of ethical responsibility. By cooperating, manufacturers can help protect consumers from harm and maintain their reputation. Conversely, a lack of cooperation can lead to severe consequences, including financial penalties, legal action, and reputational damage.
Impact on Cabela’s and its Customers
The Cabela’s food dehydrator recall, regardless of the specifics of the defect, presents a significant challenge to the company, impacting both its financial standing and its relationship with its customer base. The recall process, from initial announcement to resolution, can significantly shape how consumers perceive the brand, potentially leading to lasting consequences. This section delves into the repercussions of the recall, analyzing the company’s response and customer reactions.
Impact on Brand Reputation
A product recall inherently damages a company’s reputation. Cabela’s, known for its outdoor gear and sporting goods, faces the potential erosion of consumer trust. This is particularly critical for a brand that often relies on its perceived quality and reliability to justify premium pricing.
“A recall can create a perception of negligence or lack of quality control, leading to decreased consumer confidence.”
The extent of the damage depends on several factors:
- Severity of the Issue: If the recall is due to a serious safety hazard, such as fire risk, the reputational damage will be more severe than a cosmetic or minor functional defect.
- Company Response: A proactive, transparent, and empathetic response can mitigate negative impacts. Conversely, a delayed, defensive, or dismissive response can exacerbate the problem.
- Media Coverage: The recall’s visibility in media outlets, social media, and consumer review sites will influence public perception. Positive coverage of the company’s handling of the recall can help offset negative publicity.
- Customer Loyalty: Loyal customers might be more forgiving if they believe the company is taking the issue seriously. However, even loyal customers can be swayed by the severity of the defect and the inconvenience of the recall process.
For example, consider the impact on a company like Toyota, which experienced multiple recalls due to unintended acceleration. While the initial recalls severely damaged the company’s reputation, Toyota’s subsequent handling of the issues, including extensive safety improvements and communication efforts, helped to restore some of the lost trust over time. However, the impact was still felt for years, with sales and market share fluctuations.
Learn about more about the process of soul food r&b festival in the field.
Company Response and Communication Strategy, Cabela’s food dehydrator recall
Cabela’s response to the recall will be crucial in determining the long-term impact on its brand. A well-executed communication strategy, including clear and concise information, can help to manage the situation effectively. The company’s response will likely involve several key components:
- Public Announcement: A formal announcement, including details of the affected products, the nature of the defect, and instructions for consumers, is the first step. The announcement should be widely disseminated through multiple channels, including the company website, social media, press releases, and direct communication with known customers.
- Product Return/Replacement Program: A clear and efficient process for consumers to return the defective product and receive a refund, replacement, or repair is essential. The program should be as convenient as possible for consumers to encourage participation.
- Customer Service: Dedicated customer service channels, such as a toll-free phone number and email support, are crucial to address customer inquiries and concerns. Staff should be well-trained and equipped to handle the situation empathetically.
- Transparency: Providing regular updates on the recall progress, including the number of affected products returned and the steps being taken to prevent future incidents, can build trust.
- Proactive Measures: Identifying and addressing the root cause of the defect is critical. This may involve reviewing the manufacturing process, supplier relationships, and product testing procedures.
Failure to respond effectively can exacerbate the situation. For instance, if the company delays the recall announcement, provides unclear instructions, or makes it difficult for consumers to participate in the return program, it can lead to widespread criticism and a loss of consumer trust. A comparison can be made to the handling of the Samsung Galaxy Note 7 battery issues.
The initial response, which involved denial and minimizing the problem, led to a significant backlash and a permanent stain on the company’s reputation.
Customer Testimonials or Reactions to the Recall
Customer reactions to the recall will be varied, reflecting different levels of concern and experiences. The company should monitor customer feedback closely through various channels, including social media, online reviews, and direct customer surveys.
- Positive Reactions: Customers who are satisfied with the company’s response might express appreciation for the prompt action and the ease of the recall process. These customers are more likely to remain loyal to the brand.
- Negative Reactions: Customers who are dissatisfied might express anger, frustration, and disappointment. They might criticize the product’s quality, the company’s handling of the situation, or the inconvenience of the recall process. These customers are more likely to switch to competing brands.
- Neutral Reactions: Some customers might simply follow the instructions for the recall without expressing strong opinions. Their future purchasing decisions will depend on their overall experience with the brand.
Customer testimonials, both positive and negative, provide valuable insights into the effectiveness of the company’s response. For instance, a customer might post on social media: “I’m impressed with how quickly Cabela’s responded to the recall. The return process was easy, and I received a full refund. Thank you for taking care of this!” Conversely, another customer might post: “I’m very disappointed with the quality of this product.
The recall process is a hassle, and I’m not sure I’ll buy from Cabela’s again.”The company can use this feedback to improve its communication strategy, address specific customer concerns, and rebuild trust. Analyzing the sentiment of customer reactions can help the company gauge the overall impact of the recall and make adjustments to mitigate any negative consequences. The impact of the recall will ultimately be determined by the collective weight of these individual experiences and the company’s ability to manage them effectively.
Alternative Dehydrator Options
The Cabela’s food dehydrator recall leaves consumers in a lurch, forcing them to find replacements for their food preservation needs. This situation highlights the importance of being informed about alternative options available in the market, considering factors like safety, functionality, and value. Choosing a replacement dehydrator requires careful consideration to ensure it meets specific needs and preferences.
Recommended Food Dehydrator Alternatives
Several food dehydrators offer viable alternatives to the recalled Cabela’s models. These alternatives cater to various budgets and requirements, ensuring consumers can find a suitable replacement.
- Excalibur 3900B Food Dehydrator: Known for its robust construction and even drying, the Excalibur 3900B is a popular choice. It features a horizontal airflow system, ensuring consistent drying across all trays.
- Key Features:
- Nine large trays provide ample drying space.
- Adjustable thermostat allows for precise temperature control.
- 24-hour timer for convenient operation.
- Horizontal airflow for even drying.
- Tribest Sedona Combo SD-6780 Food Dehydrator: This dehydrator offers a unique dual-fan design and digital controls. Its features contribute to efficient and versatile food dehydration.
- Key Features:
- Two drying modes: Fast and Raw.
- Digital timer and thermostat for precise control.
- 700 watts of power.
- Horizontal airflow system.
- Presto Dehydro Digital Electric Food Dehydrator: This is a more budget-friendly option, yet it offers reliable performance. Its features make it suitable for beginners and those with moderate dehydration needs.
- Key Features:
- Six trays with expandable capacity.
- Digital timer and adjustable thermostat.
- Bottom-mounted fan for efficient drying.
- Compact design for easy storage.
Factors to Consider When Choosing a Replacement Dehydrator
Selecting a replacement dehydrator requires careful evaluation of several factors to ensure the chosen model aligns with the user’s needs and expectations. This is not merely a purchase; it’s an investment in food preservation.
- Drying Capacity: Consider the amount of food typically dehydrated. Larger families or those planning extensive food preservation may require dehydrators with more trays and capacity. Smaller households might find a compact model sufficient.
- Airflow System:
Horizontal airflow
systems, like those found in the Excalibur and Sedona models, generally provide more even drying compared to vertical airflow models. This can result in more consistent results and less need to rotate trays.
- Temperature Control: Precise temperature control is essential for preserving nutrients and preventing over-drying. Adjustable thermostats are a must-have feature, allowing for customization based on the food being dehydrated.
- Timer Function: A timer function automates the drying process, preventing over-drying and conserving energy. This feature provides convenience and peace of mind.
- Construction and Durability: Look for dehydrators made from durable, food-grade materials. Consider the warranty offered by the manufacturer, as it reflects their confidence in the product’s quality.
- Ease of Use and Cleaning: Choose a dehydrator with intuitive controls and easily removable trays for simple cleaning. This will save time and effort in the long run.
- Price and Value: Compare prices and features across different models. Consider the long-term value and the overall return on investment. Cheap dehydrators may be tempting, but they often lack the features and durability of more expensive models.
Preventing Future Recalls: Cabela’s Food Dehydrator Recall
The Cabela’s food dehydrator recall, like any product recall, serves as a stark reminder of the critical need for robust safety measures within the manufacturing process. The ramifications of such failures extend beyond financial losses, impacting consumer trust and potentially leading to serious health consequences. Preventing future recalls requires a multi-faceted approach, encompassing rigorous quality control, thorough safety testing, and a proactive commitment to consumer protection.
Manufacturer Strategies to Prevent Recalls
Manufacturers can significantly reduce the likelihood of future recalls by implementing proactive strategies. These strategies necessitate a cultural shift toward prioritizing safety and transparency at every stage of production.
- Enhanced Design Reviews: Prior to production, designs must undergo comprehensive reviews. These reviews should involve cross-functional teams including engineers, safety specialists, and consumer representatives. The aim is to identify potential hazards early in the design phase, before prototypes are even constructed. For instance, if a dehydrator’s heating element is improperly shielded, the design review should flag this and suggest modifications.
- Robust Supplier Vetting: A critical aspect of prevention lies in thoroughly vetting all suppliers. This includes assessing their quality control processes, materials sourcing, and compliance with safety standards. A failure by a supplier to provide safe components directly translates to a potential recall. Manufacturers should conduct regular audits and inspections of their suppliers to ensure ongoing compliance.
- Advanced Manufacturing Processes: Investing in advanced manufacturing technologies can dramatically improve product consistency and reduce defects. Technologies like automated quality control systems, machine vision inspections, and real-time data analysis provide critical insights into potential issues. For example, automated systems can identify deviations in the thickness of heating elements or imperfections in plastic molding.
- Comprehensive Testing Protocols: Rigorous testing protocols are essential. This includes not only testing individual components but also the fully assembled product under various operating conditions. Testing should simulate real-world usage scenarios, including prolonged operation, exposure to extreme temperatures, and potential misuse. Testing should also include destructive testing to determine the product’s limits.
- Improved Traceability Systems: Implementing robust traceability systems allows manufacturers to track products from raw materials to the finished goods. This is crucial in the event of a defect, enabling rapid identification and containment of affected units. The ability to pinpoint the exact batch of components used in a faulty product minimizes the scope of any recall.
- Proactive Monitoring and Feedback Mechanisms: Establishing feedback mechanisms to collect and analyze consumer complaints and reports is crucial. This can involve dedicated customer service channels, online forums, and social media monitoring. Actively monitoring these channels can provide early warning signs of potential safety issues.
Importance of Quality Control and Safety Testing
Quality control and safety testing are the cornerstones of product safety. They are not simply box-checking exercises, but rather continuous processes integrated into the entire product lifecycle.
- Quality Control’s Role: Quality control encompasses all measures taken to ensure that a product meets the required standards. This involves inspecting raw materials, monitoring manufacturing processes, and conducting final product inspections. It aims to identify and correct defects before the product reaches consumers. A well-defined quality control system reduces the likelihood of errors in the manufacturing process.
- Safety Testing’s Significance: Safety testing focuses specifically on evaluating the product’s potential hazards. This includes electrical safety testing, thermal testing, and mechanical testing. The purpose of safety testing is to identify and mitigate risks that could lead to injury or harm.
- Integration of Quality Control and Safety Testing: The two are interconnected. Quality control helps to ensure that the product is manufactured according to specifications, while safety testing verifies that the product meets the required safety standards. A failure in either area can result in a product that is unsafe for consumers.
- Examples of Testing: Consider the Cabela’s food dehydrator. Safety testing should have included tests for overheating, electrical shorts, and the presence of hazardous materials. Quality control should have checked the materials used, the construction of the heating element, and the overall assembly of the product.
Best Practices in Product Safety and Consumer Protection
Adopting best practices in product safety and consumer protection demonstrates a commitment to safeguarding consumers. These practices often exceed the minimum regulatory requirements.
- Adoption of Industry Standards: Manufacturers should adhere to relevant industry standards and certifications. These standards provide a benchmark for product safety and performance. Examples include Underwriters Laboratories (UL) certification and the standards set by the Consumer Product Safety Commission (CPSC).
- Transparency in Product Information: Manufacturers should provide clear and concise product information, including safety warnings, operating instructions, and potential hazards. This information should be readily accessible to consumers.
- Proactive Recall Programs: In the event of a defect, manufacturers should have a well-defined recall program. This includes notifying consumers promptly, providing clear instructions for returning or repairing the product, and taking steps to prevent future occurrences.
- Collaboration with Regulatory Agencies: Manufacturers should cooperate with regulatory agencies like the CPSC to investigate product defects and implement corrective actions. This collaboration helps to ensure that consumers are protected.
- Post-Market Surveillance: Ongoing monitoring of product performance and consumer feedback is crucial. This includes tracking complaints, analyzing incident reports, and conducting periodic safety audits. This allows manufacturers to identify and address potential safety issues proactively.
Final Thoughts
In conclusion, the cabela’s food dehydrator recall serves as a potent reminder of the critical intersection between consumer products, safety regulations, and brand reputation. From the physics of dehydration to the complexities of product liability, this event underscores the importance of rigorous testing, transparent communication, and proactive measures to prevent future incidents. By understanding the intricacies of this recall, consumers can make informed decisions, manufacturers can learn from past mistakes, and regulatory bodies can continue to refine the standards that safeguard public health.
The ultimate aim is to create a safer, more reliable marketplace for all.