CRC food grade chain lube isn’t just a lubricant; it’s a guardian of food safety and operational efficiency, a silent partner in the bustling world of food processing. Imagine a world where machinery hums with precision, chains glide smoothly, and the risk of contamination is minimized. This is the promise of CRC Food Grade Chain Lube, a product meticulously crafted to meet the stringent demands of the food industry.
From its inception, this lubricant has evolved, embracing technological advancements to become an indispensable asset for businesses prioritizing both productivity and consumer well-being. It’s a story of innovation, compliance, and a commitment to excellence.
This product’s primary purpose is to ensure smooth operation and reduce friction in food processing machinery. This means protecting food products from contamination while extending the life of critical equipment. Unlike standard lubricants, CRC Food Grade Chain Lube is formulated with ingredients that are safe for incidental food contact, complying with rigorous standards such as NSF H
1. The benefits are clear: reduced maintenance costs, minimized downtime, and, above all, enhanced food safety.
This text will delve into its composition, application, and the many ways it contributes to a safer, more efficient food industry.
Introduction to CRC Food Grade Chain Lube
Alright, buckle up buttercups, because we’re about to dive headfirst into the wonderfully greasy world of CRC Food Grade Chain Lube! Think of it as the unsung hero of the food processing industry, the silent guardian, the watchful protector… of your delicious snacks. Without it, well, things could get a little… messy. And by messy, I mean potentially hazardous to your health and your company’s reputation.So, let’s get down to brass tacks (or, perhaps, stainless steel sprockets).
This stuff is designed to keep the gears turning (literally and figuratively) in the food processing world, where cleanliness is next to… well, you know. It’s all about keeping those conveyor belts, chains, and other moving parts lubricated, efficient, and, most importantly, safe for the food they come into contact with.
Primary Purpose and Intended Use
CRC Food Grade Chain Lube is, at its core, a lubricant. But not just any lubricant. This is a lubricant with a PhD in Food Safety. Its primary purpose is to reduce friction and wear on chains, sprockets, and other moving components in food processing equipment. This helps extend the life of the equipment, reduce downtime, and improve overall efficiency.The intended use is, therefore, within the food processing industry.
Think of places where food is being made, packaged, and moved. From bakeries churning out croissants to meatpacking plants slicing and dicing, CRC Food Grade Chain Lube keeps the wheels (or, more accurately, the chains) turning smoothly. This covers a broad range of applications, including:
- Conveyor systems: Moving everything from raw ingredients to finished products.
- Filling and packaging machines: Ensuring smooth operation for efficient packaging.
- Processing equipment: Lubricating machinery that directly handles food products.
- Anywhere that a chain or moving part might come into contact with food.
Brief History and Evolution
The history of food-grade lubricants is less “ancient scrolls” and more “a gradual realization that putting engine oil in a food processor is a bad idea.” The evolution has been driven by the need for safer, more effective, and more compliant solutions.Initially, standard lubricants were used, which worked… until they didn’t. The risks of contamination were, shall we say, significant.
Then, the industry started to realize that things like accidental ingestion of petroleum-based lubricants were a bit of a buzzkill. Thus, the need for food-grade lubricants arose.CRC, being the clever folks they are, recognized this need and developed their Food Grade Chain Lube. This wasn’t a sudden flash of inspiration but rather a process of ongoing improvement. Early versions were good, but the constant drive to improve performance, safety, and regulatory compliance has led to the advanced formula we have today.
It has evolved from basic lubrication to a comprehensive solution that meets the stringent requirements of modern food processing.
Benefits of Food-Grade Lubrication
The benefits of using a food-grade lubricant like CRC Food Grade Chain Lube over a standard lubricant are significant. It’s like the difference between wearing a hazmat suit and wearing a t-shirt in a nuclear reactor – one is clearly a better idea.The key advantages are:
- Safety: The most crucial benefit. Food-grade lubricants are formulated with ingredients that are safe for incidental food contact. This significantly reduces the risk of contamination. If a chain breaks or lubricant drips, the food isn’t ruined or contaminated.
- Compliance: Food-grade lubricants are designed to meet the stringent requirements of regulatory bodies like the NSF (National Sanitation Foundation). NSF registration means that the lubricant has been assessed and certified as safe for use in food processing environments.
- Performance: While safety is paramount, CRC Food Grade Chain Lube doesn’t skimp on performance. It provides excellent lubrication, reduces friction, and protects against wear, rust, and corrosion, extending the life of your equipment.
- Efficiency: Reduced friction means less energy consumption and smoother operation, leading to increased efficiency and reduced downtime.
Consider the case of a large bakery. Imagine a conveyor belt system carrying freshly baked bread. If a standard lubricant were used and a leak occurred, the bread would be contaminated and the entire batch would have to be discarded. With CRC Food Grade Chain Lube, the risk of such a costly and potentially disastrous event is dramatically reduced.
“Food safety isn’t just a good idea; it’s the law.”
Composition and Properties
Alright, buckle up buttercups, because we’re about to dive headfirst into the secret sauce (or rather, the secret lube) that makes CRC Food Grade Chain Lube the superhero it is. Forget capes and tights, this stuff has NSF H1 certification and a whole lotta chemistry! We’ll break down what makes this lubricant tick, from its molecular makeup to its impressive ability to laugh in the face of rust and extreme temperatures.
Get ready to get your geek on (in a fun, food-safe way, of course!).
Key Ingredients and Their Roles
Let’s peek under the hood and see what makes this chain lube so special. It’s not just pixie dust and wishes; it’s a carefully crafted blend of ingredients, each playing a vital role in keeping your machinery running smoothly and, most importantly, safely around food.
- Base Oil: The backbone of the lubricant. It provides the fundamental lubrication, reducing friction between the chain links and preventing wear and tear. The base oil used is often a highly refined, food-grade oil that meets strict purity standards. Think of it as the smooth, silent operator of the team.
- Thickeners: These are the unsung heroes that give the lube its consistency. They prevent it from running off the chain and ensure it stays where it’s needed, even under pressure and at varying temperatures. These are often aluminum complex thickeners.
- Additives: This is where the magic really happens! A cocktail of additives is carefully chosen to boost the lubricant’s performance.
- Anti-wear Additives: They reduce friction and wear. These additives create a protective film on the metal surfaces, minimizing direct contact and extending the life of your chain.
- Anti-corrosion Additives: Rust is the enemy! These additives protect metal surfaces from corrosion, ensuring the chain remains strong and reliable, even in humid environments.
- Antioxidants: They prevent the base oil from breaking down over time, extending the lubricant’s lifespan and maintaining its performance.
- Food-Grade Certification: The entire formulation is meticulously designed to meet stringent food safety standards. That means all ingredients are safe for incidental food contact. No nasty surprises here!
Physical and Chemical Properties
Now, let’s talk about what this stuffdoes*. We’re not just interested in the ingredients; we want to know how they behave under pressure (literally!). This section explores the key physical and chemical characteristics that make CRC Food Grade Chain Lube a champion.
- Viscosity: This is the measure of a fluid’s resistance to flow. CRC Food Grade Chain Lube has a carefully selected viscosity to provide optimal lubrication across a range of operating conditions. It’s like Goldilocks – not too thick, not too thin, but
-just right* for the job. The viscosity will be chosen depending on the chain application, but usually, it will be between ISO VG 100 and ISO VG 220. - Temperature Range: This lube is built to handle the heat (and the cold!). It maintains its lubricating properties over a wide temperature range, ensuring reliable performance in various environments. It usually works between -20°C to 150°C (-4°F to 302°F).
- Corrosion Resistance: Say goodbye to rust! CRC Food Grade Chain Lube provides excellent corrosion protection, safeguarding your chains from the damaging effects of moisture and other environmental factors. This is achieved thanks to the additives included in the formula.
- Water Resistance: It repels water. Water and lubrication do not mix, and CRC Food Grade Chain Lube resists water washout, ensuring the lubricant stays in place and continues to protect the chain.
Food Safety Standards and Certifications
This is where CRC Food Grade Chain Lube really shines. It’s not just a lubricant; it’s acertified* lubricant. Meeting food safety standards is a big deal, and this product has the credentials to prove it.
- NSF H1 Certification: This is the gold standard for food-grade lubricants. It means that the lubricant is approved for incidental food contact, meaning that if a tiny amount of the lubricant accidentally comes into contact with food, it won’t cause any harm.
- Stringent Testing: The formulation undergoes rigorous testing to ensure it meets all the requirements of NSF H1 certification. This includes testing for toxicity, purity, and performance.
- Compliance with Regulations: CRC Food Grade Chain Lube complies with all relevant food safety regulations, giving you peace of mind that you’re using a safe and compliant product.
Applications and Industries
Alright, buckle up buttercups, because we’re about to dive headfirst into the glorious world where CRC Food Grade Chain Lube gets to shine! This isn’t just some fancy oil; it’s the superhero of the food processing industry, the unsung champion of pharmaceutical manufacturing, and the MVP of… well, a whole bunch of other places where things need to run smoothly (and safely!).
Think of it as the secret sauce that keeps the wheels turning, the gears grinding (in a good way!), and the products flowing, all while keeping those pesky food safety regulations happy.This lubricant isn’t just a one-trick pony; it’s a versatile workhorse. From the conveyor belts that whisk your favorite snacks to the packaging machines that neatly wrap them, CRC Food Grade Chain Lube is there, silently doing its job.
Let’s explore some of the key industries and applications where this lubricant is the star of the show.
Specific Industries and Applications
The applications of CRC Food Grade Chain Lube are as diverse as the industries it serves. It’s like a Swiss Army knife of lubrication, tackling a variety of challenges with ease. Here’s a breakdown, served up in a handy-dandy table:
Application | Equipment | Benefits |
---|---|---|
Food Processing | Conveyor belts, packaging machines, filling equipment, slicers, and mixers. | Ensures smooth operation, reduces friction and wear, extends equipment life, and minimizes downtime. Crucially, it maintains food safety by preventing contamination and complying with regulations like those set by the FDA. Think of it as the guardian angel of your morning cereal. |
Beverage Production | Bottle filling lines, labeling machines, capping equipment, and conveyors. | Prevents equipment jams, ensures efficient operation, reduces the risk of product spoilage due to equipment failure, and maintains hygiene standards. Imagine a world without your favorite soda – this lube helps prevent that catastrophe! |
Pharmaceutical Manufacturing | Tablet presses, capsule filling machines, packaging equipment, and blending equipment. | Guarantees equipment reliability, minimizes the risk of cross-contamination, and maintains the integrity of sensitive pharmaceutical products. This is the unsung hero behind the pills that keep us healthy, ensuring they’re produced with the utmost care and precision. |
Meat and Poultry Processing | Slicing machines, grinders, conveyors, and packaging equipment. | Reduces friction, extends equipment lifespan, and minimizes the risk of food contamination. Helps keep the meat processing plant running smoothly, so your burgers and chicken nuggets are always ready for the grill. |
Bakery Production | Mixers, ovens, conveyors, and packaging equipment. | Provides excellent lubrication in high-temperature environments, reduces wear and tear, and prevents product contamination. Ensures your bread, cakes, and pastries are baked to perfection, without any unwanted grease or grime. |
Cannery Operations | Filling machines, sealing equipment, conveyors, and retorts. | Maintains equipment efficiency, prevents rust and corrosion, and reduces the risk of product spoilage. Keeps your canned goods safe and sound, from the factory to your pantry. |
Remember, the use of food-grade lubricants isn’t just about keeping things running smoothly; it’s about protecting consumers and adhering to stringent safety regulations.
Benefits and Advantages: Crc Food Grade Chain Lube
Alright, buckle up buttercups, because we’re about to dive into the glorious perks of slathering your chains with CRC Food Grade Chain Lube! Think of it as a spa day for your machinery, but instead of cucumber slices on your eyes, you get… well, you get longer-lasting chains and less downtime. And who doesn’t love a good spa day, even if it’s for a machine?
Let’s get down to brass tacks (or, you know, chain links).
Extended Chain Life, Reduced Friction, and Improved Efficiency
So, what’s the big deal about using a proper food-grade chain lube? Well, let’s just say it’s the difference between a marathon runner and a couch potato. We’re talking about keeping your chains in tip-top shape, reducing energy bills, and boosting overall productivity. Sounds good, right?
- Extended Chain Life: This isn’t rocket science, folks. CRC Food Grade Chain Lube reduces wear and tear, meaning your chains last longer. Imagine the savings! No more replacing chains every other Tuesday. It’s like a perpetual motion machine, but instead of free energy, you get… well, you get to keep your chains. Let’s put it this way: A well-lubricated chain can last up to
-three times longer* than a poorly lubricated one, according to industry reports.That’s a whole lot of saved dough.
- Reduced Friction: Friction is the enemy! It’s the reason your car gets hot, your gears grind, and your chains… well, they wear out. CRC Food Grade Chain Lube creates a smooth, slippery surface, minimizing friction and allowing your chains to glide effortlessly. Think of it like buttering your toast before you eat it. It just makes everything easier and more enjoyable.
- Improved Efficiency: Less friction equals less energy wasted. Less energy wasted equals a more efficient operation. This means your machines run smoother, faster, and with less strain. It’s like giving your machines a performance-enhancing drug… that’s perfectly legal and safe for food processing. According to a study by the National Association of Manufacturers, optimizing lubrication can lead to a
-10-15% increase in overall equipment efficiency*.Not too shabby!
Economic Benefits: Reduced Maintenance Costs and Downtime, Crc food grade chain lube
Now, let’s talk about the green stuff. We’re not just saving chains; we’re saving you money. Think of CRC Food Grade Chain Lube as an investment in your bottom line. It’s like buying a good insurance policy – you might not see the immediate benefits, but you’ll be darn glad you have it when things go wrong.
- Reduced Maintenance Costs: Fewer chain replacements mean lower costs. Less friction means less wear and tear on other components. CRC Food Grade Chain Lube helps you avoid those unexpected repair bills that always seem to pop up at the worst possible time. Consider the case of a major food processing plant that switched to a high-quality food-grade lubricant. Their chain replacement costs dropped by a whopping
-40%* in the first year! - Reduced Downtime: Downtime is the devil. It costs you money, productivity, and sanity. CRC Food Grade Chain Lube helps keep your machines running smoothly, reducing the risk of breakdowns and minimizing downtime. It’s like having a guardian angel for your machinery. Every hour of downtime can cost a food processing facility thousands of dollars in lost production.
By preventing breakdowns, CRC Food Grade Chain Lube helps you keep the production line humming and your profits soaring.
Contribution to Overall Food Safety and Hygiene
This is where CRC Food Grade Chain Lube really shines. We’re not just talking about efficiency and cost savings; we’re talking about protecting your consumers and your brand reputation.
- Food Safety Compliance: CRC Food Grade Chain Lube is specifically formulated to meet the stringent requirements of food safety regulations. This means it’s non-toxic, odorless, and tasteless, ensuring that it won’t contaminate your food products. This is not just about avoiding fines, it’s about building trust with your customers.
- Preventing Cross-Contamination: With the right food-grade lubricant, the risk of cross-contamination is significantly reduced. This is critical in food processing environments where even small amounts of non-food-grade lubricants can pose a serious health hazard. It’s a preventative measure, like washing your hands before you eat.
- Maintaining Hygiene Standards: CRC Food Grade Chain Lube helps keep your equipment clean and sanitary, contributing to overall hygiene standards. This is essential for preventing the growth of bacteria and other microorganisms that can spoil your products and make people sick. Regular lubrication, using a food-grade product, creates a barrier, preventing contamination and helping to maintain the integrity of your food products.
Application Methods and Procedures
Alright, grease monkeys and chain-wielding warriors! Applying CRC Food Grade Chain Lube isn’t rocket science, but it’s also not a free-for-all. We’re aiming for lubricated nirvana, not a greasy, gloopy disaster. Follow these steps, and your chains will be singing a sweet, frictionless song. Think of this as your chain’s spa day – minus the cucumbers on the links.
Step-by-Step Application to Various Chain Types
Let’s get down to the nitty-gritty of lubricating different chain types. Remember, a little precision goes a long way. We’ll cover the most common chain types, from your bicycle’s delicate dance partner to the industrial behemoths.
For all chain types, the goal is to apply the lubricant
-to the moving parts* (pins, rollers, and bushings) where friction occurs. Avoid spraying directly onto the chain itself, which can lead to excessive waste and mess.
- Bicycle Chains:
Ah, the humble bicycle chain! A critical component for cycling fun, and needs to be kept in good condition. This application process is for your two-wheeled friend:
- Clean the Chain: Before applying any lubricant, clean the chain thoroughly with a chain cleaner and a brush. Remove all the old, grimy lubricant and any dirt.
- Position the Chain: Place the chain in a position where you can easily access the entire length. Using a bike stand or flipping the bike upside down works well.
- Apply the Lube: Hold the CRC Food Grade Chain Lube nozzle near the chain, and slowly rotate the pedals backward (or move the chain by hand). Apply a thin, even stream of lubricant to the
-inside* of the chain, focusing on the rollers and pins. - Wipe Excess: After applying the lubricant, wipe off any excess with a clean cloth. This prevents attracting dirt and grit.
- Wait and Ride: Let the lubricant penetrate the chain for a few minutes before riding. This allows the lubricant to settle in.
- Motorcycle Chains:
These chains endure higher stresses. A different approach is necessary, but the core principles remain the same.
- Chain Cleaning: Clean the chain with a dedicated chain cleaner and a brush. Ensure to remove all dirt and old lubricant.
- Chain Positioning: Use a motorcycle stand to elevate the rear wheel. This allows easy access to the chain.
- Lubricant Application: With the engine off, apply the CRC Food Grade Chain Lube to the
-inside* of the chain while rotating the rear wheel slowly. Focus on the rollers and pins. - Wipe Excess: After applying the lubricant, wipe off any excess with a clean cloth.
- Allow Penetration: Allow the lubricant to penetrate the chain for a few minutes before riding.
- Industrial Chains:
Industrial chains are often the workhorses of industry, and the lubrication method depends on the chain type and application. Some industrial chains have specific lubrication systems, while others require manual application.
- Chain Inspection: Before applying the lubricant, inspect the chain for wear, damage, and cleanliness.
- Cleaning: Clean the chain as thoroughly as possible using a chain cleaner or degreaser, depending on the chain type and the application.
- Lubrication Method: The lubrication method depends on the chain type and application. Some industrial chains have automatic lubrication systems, which apply the lubricant continuously. For chains without automatic systems, apply the CRC Food Grade Chain Lube manually, focusing on the pins, rollers, and bushings.
- Application Rate: The application rate depends on the chain type, load, and operating conditions. Always follow the manufacturer’s recommendations.
- Monitoring: Regularly monitor the chain for wear and lubrication.
Pre-Application Preparation and Post-Application Inspection Checklist
Before you start lubing, and after you’re done, a little preparation and inspection can save you a world of trouble. Think of this as a pre-flight check for your chain.
Here’s a checklist to ensure your lubrication efforts are successful:
Pre-Application Preparation | Post-Application Inspection |
---|---|
Chain Type Identification | Chain Alignment Check |
Gather all necessary tools (cleaner, brush, CRC Food Grade Chain Lube, rags) | Lubricant Coverage Inspection |
Chain Cleaning and Drying | Excess Lubricant Removal |
Safety Gear (gloves, eye protection) | Chain Tension Adjustment (if necessary) |
Workspace Protection (cover surrounding surfaces) | Chain Operation Test |
Common Application Mistakes to Avoid
Even the most experienced chain lubricators make mistakes. Here’s a list of common pitfalls to steer clear of, so you don’t end up with a chain that’s either squeaking like a rusty gate or attracting more dirt than a toddler’s playground.
Avoiding these errors will ensure your chain receives the optimal care it deserves.
- Applying too much lubricant: Over-lubricating is a common mistake. Excess lubricant attracts dirt and grime, forming a sticky, abrasive paste. Aim for a thin, even coat.
- Not cleaning the chain first: Applying lubricant to a dirty chain is like putting makeup on a dirty face. The lubricant won’t penetrate properly and will just trap the dirt.
- Using the wrong type of lubricant: Not all lubricants are created equal. Using the wrong type can lead to premature wear and damage. Always use a food-grade lubricant like CRC Food Grade Chain Lube for food-processing equipment or areas where incidental food contact is possible.
- Ignoring safety precautions: Always wear gloves and eye protection to protect yourself from the lubricant.
- Lubricating a moving chain: Never lubricate a chain while it’s moving. This can be dangerous and can lead to uneven lubrication. Turn off the equipment or bicycle before applying the lubricant.
- Applying the lubricant to the outside of the chain: The lubricant needs to penetrate to the inside of the chain where the pins and rollers are. Applying it to the outside is mostly a waste.
- Not wiping off excess lubricant: After applying the lubricant, wipe off any excess with a clean cloth. This prevents the lubricant from attracting dirt and grime.
Safety and Handling: Because Nobody Wants to End Up in the ER (Unless It’s Taco Tuesday)
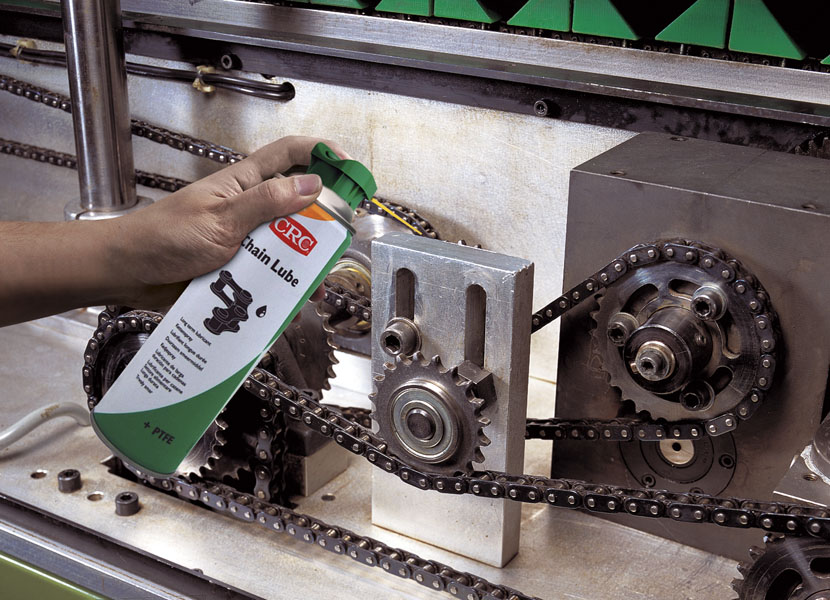
Let’s be honest, nobody enjoys reading about safety. It’s like being told to eat your vegetables – necessary, but not exactly thrilling. However, when it comes to handling CRC Food Grade Chain Lube, playing it safe isn’t just a good idea; it’s the law of not getting your lunch ruined (and potentially ending up with a hefty hospital bill). We’ll cover the nitty-gritty, so you can lube your chains and keep your sanity intact.
Safety Precautions for Handling and Storage
Handling CRC Food Grade Chain Lube demands a bit of common sense and a dash of caution. Think of it like handling a grumpy badger: you want to be respectful and avoid getting swiped at. Here’s how to keep things friendly:
- Protective Gear is Your Wingman: Always wear appropriate personal protective equipment (PPE). This means gloves (think nitrile or similar, not your grandma’s knitting gloves), eye protection (safety glasses or goggles, not your reading glasses), and ideally, a lab coat or apron. You wouldn’t go into a food fight without a shield, would you?
- Ventilation: Breathe Easy, Literally: Use the product in a well-ventilated area. If you’re working indoors, make sure there’s adequate airflow. Think of it as giving the fumes a clear path to escape, like letting the bad guys out of the building.
- Avoid the Fire Hazard: Keep the lube away from heat, sparks, and open flames. It’s flammable, and nobody wants a greasy inferno on their hands. Consider it a very, very grumpy dragon that you don’t want to poke.
- Keep it Contained: Store the lube in its original container, tightly closed, and in a cool, dry place. Think of it as keeping your secret stash of cookies safe from the cookie monster (which, in this case, is you).
- Read the Fine Print (Seriously, Do It): Always refer to the Safety Data Sheet (SDS) for detailed information on hazards, first aid, and handling procedures. It’s like the rulebook for the game of “Don’t Mess Up Your Day.”
First-Aid Measures for Accidental Contact or Ingestion
Accidents happen. Sometimes you get a little enthusiastic with the lube. Here’s what to do if things go sideways:
- Eye Contact: Rinse immediately with plenty of water for at least 15 minutes, holding the eyelids open. Then, consult a doctor. It’s like getting sand in your eyes, but with a slightly different flavor.
- Skin Contact: Wash with soap and water. Remove contaminated clothing and launder before reuse. Think of it as a particularly stubborn stain that needs a good scrubbing.
- Ingestion: DO NOT induce vomiting. If the person is conscious, give them plenty of water to drink. Seek medical attention immediately. This is not a tasty beverage.
- Inhalation: If someone inhales fumes and feels unwell, move them to fresh air and seek medical attention. It’s like getting a lungful of something you shouldn’t have, so breathe deep and then run for help.
Proper Disposal Methods and Environmental Considerations
Disposing of CRC Food Grade Chain Lube responsibly is crucial. Think of it as being a good citizen of Planet Earth. Nobody wants to be
that* person.
- Don’t Dump It: Never pour the product down the drain or into the environment. It’s bad for the ecosystem, and nobody wants to be responsible for a greasy apocalypse.
- Follow Local Regulations: Dispose of the product according to local, state, and federal regulations. These rules are in place for a reason, so don’t be a rebel without a cause (unless the cause is something fun, like ice cream).
- Recycle When Possible: Empty containers can often be recycled. Check with your local recycling center. It’s a small step, but every little bit helps, like contributing a dollar to your favorite charity.
- Waste Management: Dispose of waste in accordance with applicable regulations. Contact your local waste management company for guidance. They’re the experts in dealing with the messy stuff.
Comparison with Competitors
Alright, buckle up, buttercups, because we’re about to dive headfirst into the cutthroat world of food-grade chain lubes! It’s a jungle out there, filled with slippery competitors vying for the coveted title of “Best Chain Lube Ever.” But fear not, because we’re going to dissect the competition and see how CRC Food Grade Chain Lube stacks up. Prepare for some hard-hitting facts, a sprinkle of sass, and maybe a slightly greasy metaphor or two.Let’s get down to brass tacks and pit CRC against the oily titans.
We’ll examine features, benefits, and, of course, those all-important price points. Get ready for a showdown!
Unique Selling Points of CRC Food Grade Chain Lube
CRC Food Grade Chain Lube isn’t just another pretty face (or, uh, spray can). It’s got some serious game. Here’s what sets it apart from the pack:
- NSF H1 Registered: This means it’s safe for incidental food contact. Because nobody wants a side of chain lube with their sausage.
- Excellent Anti-Wear Properties: Keeps your chains running smoothly and extends their lifespan. Think of it as a spa day for your machinery.
- Superior Rust and Corrosion Protection: Shields against the elements, ensuring your equipment stays in tip-top shape. Mother Nature, consider yourself warned!
- Wide Temperature Range: Performs reliably in a variety of conditions, from the freezer to the fryer. Talk about versatility!
- Non-Tacky Formula: Reduces the buildup of dust and debris, keeping things clean and efficient. Less gunk, more grunt!
Comparative Analysis of Features, Benefits, and Price
To really get a feel for how CRC stacks up, let’s put it side-by-side with some of its main rivals. We’ll use a handy-dandy table for easy digestion (pun intended). Remember, prices can fluctuate, so this is a general comparison.
Obtain direct knowledge about the efficiency of portland food festival 2024 through case studies.
Feature | CRC Food Grade Chain Lube | Competitor A (e.g., SuperLube) | Competitor B (e.g., Petro-Canada) | Competitor C (e.g., Molykote) |
---|---|---|---|---|
Food Contact Rating | NSF H1 | NSF H1 | NSF H1 | NSF H1 |
Anti-Wear Performance | Excellent | Good | Good | Very Good |
Rust & Corrosion Protection | Superior | Good | Good | Excellent |
Temperature Range | Wide | Moderate | Moderate | Wide |
Tackiness | Low | Moderate | Moderate | Low |
Typical Price (per can) | $12 – $18 | $10 – $15 | $15 – $20 | $20 – $25 |
Key Benefit | Reliable performance, excellent protection, and good value. | Widely available, decent all-around performance. | Good for specific applications, may offer higher viscosity options. | Excellent wear protection, potentially higher cost. |
Disclaimer: Prices are approximate and may vary based on location and retailer. Performance characteristics are based on typical product specifications and industry data. Always consult product data sheets for specific information.
Maintenance and Storage
Alright, folks, you’ve slathered your chains with the glorious CRC Food Grade Chain Lube. You’ve seen the magic happen, the gears turning smoothly, the food-grade goodness protecting your equipment. But, like any good relationship (or a really,really* good batch of tacos), it requires a little TLC to keep things running smoothly. Let’s talk about how to keep your chains and your lube happy.
Maintaining Chains Lubricated with CRC Food Grade Chain Lube
Keeping your chains happy is like keeping a well-fed gremlin happy – you don’t want to anger it. Regular maintenance is key. Neglecting it is a recipe for premature wear, breakdowns, and potentially, a very grumpy chain. Here’s how to keep that chain purring like a well-oiled kitten:
- Frequency of Application: The frequency depends on your operation. Chains in constant, high-load environments will need more frequent lubrication than those used intermittently. Think of it like this: a busy taco stand needs more salsa than a once-a-week home cook. Inspect your chain regularly. If it looks dry, it’s time for a reapplication.
- Chain Cleaning: Before reapplying the lube, give your chain a good cleaning. This removes dirt, debris, and old lubricant, allowing the new lube to penetrate and work its magic. Use a food-grade chain cleaner (or a damp cloth if you’re feeling minimalist). Think of it as a pre-date shower for your chain.
- Proper Application Technique: Apply the lube to the
-inside* of the chain where the rollers and pins meet. This is where the magic happens. Rotate the chain slowly as you apply the lubricant to ensure even coverage. Don’t just douse it from a distance like you’re spraying for roaches; that’s a waste of product. - Wipe Away Excess: After applying the lubricant, wipe away any excess. Too much lubricant can attract dirt and grime, creating a gritty paste that actually
-hinders* lubrication. Think of it like using just the right amount of cheese on your nachos – enough to be delicious, but not so much that it’s a sloppy mess. - Regular Inspections: Keep an eye on your chain for signs of wear and tear, like stretched links, rust, or damage. Catching problems early can save you from a major headache (and a potential food safety hazard).
Proper Storage Conditions to Preserve the Lubricant’s Effectiveness
Storing CRC Food Grade Chain Lube correctly is crucial to maintaining its effectiveness. Think of it like storing your favorite ice cream – you wouldn’t leave it out in the sun, would you?
- Temperature: Store the lubricant in a cool, dry place. Extreme temperatures can degrade the lubricant’s performance. Aim for a temperature range between 40°F (4°C) and 100°F (38°C). Imagine it’s a Goldilocks situation: not too hot, not too cold, but just right.
- Direct Sunlight: Avoid direct sunlight. UV rays can break down the lubricant’s components, reducing its effectiveness. Keep it tucked away in a storage cabinet or a shaded area.
- Container Integrity: Ensure the container is tightly sealed to prevent contamination and evaporation. A leaky container is like a leaky roof – it lets the good stuff out.
- Away from Contaminants: Store the lubricant away from potential contaminants, such as dust, dirt, and other chemicals. Contamination can compromise the lubricant’s performance and potentially pose a food safety risk.
- Proper Labeling: Always keep the container clearly labeled with the product name and any relevant safety information. This helps prevent mix-ups and ensures proper handling.
Recommended Shelf Life of the Product and Recognizing Signs of Degradation
Even the best lubricants have a shelf life. Knowing the shelf life and how to spot signs of degradation ensures you’re always using a product that’s performing at its peak. It’s like checking the expiration date on your milk – you don’t want any unpleasant surprises.
CRC Food Grade Chain Lube typically has a shelf life of 2-3 years from the date of manufacture when stored under the recommended conditions.
Here’s how to recognize signs of degradation:
- Changes in Appearance: Look for any changes in the lubricant’s appearance, such as cloudiness, separation of components, or the formation of solids. If it looks funky, it probably is.
- Changes in Odor: An unusual or rancid odor can indicate degradation. If it smells off, it’s time to toss it.
- Changes in Consistency: If the lubricant becomes thicker, thinner, or lumpy, it may have degraded.
- Performance Issues: If the lubricant isn’t performing as expected – if your chain is squeaking, wearing out quickly, or showing signs of increased friction – the lubricant may be past its prime.
If you observe any of these signs, it’s best to discard the lubricant and replace it with a fresh container. Don’t risk compromising your equipment or, worse, your food safety!
Troubleshooting
Ah, the glamorous world of chain lubrication! Even with the best food-grade chain lube on the market (ahem, CRC!), things can go a little sideways. Fear not, intrepid grease monkey! This section is your survival guide to common chain lubrication woes. We’ll dive into the usual suspects, from chain wear to lubricant leakage, and arm you with the knowledge to keep your machinery humming like a well-oiled… well, you get the idea.
Common Problems and Solutions
Let’s face it, even the most meticulously maintained equipment can throw a wrench (or a chain link) into your plans. Understanding these potential pitfalls is the first step in conquering them. We’ve compiled a list of common issues you might encounter, along with some handy solutions to get you back on track.
- Chain Wear: This is the most common enemy. Chains wear out, plain and simple. It’s like aging, but for metal.
- Problem: Excessive stretching, stiff links, or visible wear on the rollers and pins.
- Solution: Regular chain inspections are key. Measure the chain stretch using a chain wear indicator. If it’s stretched beyond the manufacturer’s recommendations (usually around 0.75% to 1%), it’s time for a replacement. Also, ensure proper lubrication is applied at the recommended intervals to minimize wear. Consider using a chain tensioner to maintain optimal chain tension.
- Lubricant Leakage: Nobody likes a messy workplace, and leaking lubricant is a cleanliness nightmare.
- Problem: Excess lubricant dripping onto machinery, the floor, or – heaven forbid – your delicious food products.
- Solution: Avoid over-lubrication! Apply the correct amount of CRC Food Grade Chain Lube according to the manufacturer’s instructions. Inspect the chain for proper lubrication and ensure the lubricant has adequate time to penetrate the chain links. Check for worn or damaged seals and replace them if necessary. Consider using a drip pan or absorbent pads to catch any excess lubricant.
- Contamination: Dirt, dust, and other foreign objects are the bane of a well-lubricated chain.
- Problem: Gritty buildup on the chain, reduced lubrication effectiveness, and increased wear.
- Solution: Clean the chain regularly using a food-grade degreaser before re-lubricating. Shield the chain from contaminants as much as possible. This could involve using chain guards or enclosing the chain in a protective housing. Ensure the work environment is as clean as possible, especially around food processing areas.
- Lubricant Drying/Gumming Up: Sometimes, the lube just… vanishes.
- Problem: The lubricant becomes thick, sticky, and loses its lubricating properties, leading to increased friction and wear.
- Solution: This is often a sign of using the wrong lubricant or applying it incorrectly. Ensure you are using the correct CRC Food Grade Chain Lube for your application and following the application instructions. Check the storage conditions of the lubricant; extreme temperatures can affect its properties. Clean the chain thoroughly and re-lubricate.
- Incorrect Lubricant Application: You might be doing everything right, but the application method is off.
- Problem: Inadequate lubrication in specific areas, leading to premature wear or uneven performance.
- Solution: Follow the recommended application methods Artikeld in the “Application Methods and Procedures” section. Ensure the lubricant reaches all critical areas of the chain, such as the pins, rollers, and bushings. Consider using a chain lubrication system for consistent and efficient application. Regularly inspect the chain after lubrication to ensure even coverage.
Product Specifications and Technical Data
Alright, buckle up, buttercups! We’re diving headfirst into the nitty-gritty of CRC Food Grade Chain Lube – the stuff that keeps your food processing equipment humming along, and your lunch from tasting like rusty metal. This section is all about the numbers, the specs, and the technical wizardry that makes this lube a champion. Get ready to have your minds blown (metaphorically, of course.
We’re aiming for safe, not spectacular explosions).
Viscosity and Kinematic Data
Understanding viscosity is key to ensuring the lube does its job effectively. Viscosity, in simple terms, measures a fluid’s resistance to flow. A higher viscosity means the fluid is thicker and flows slower; a lower viscosity means it’s thinner and flows more easily. Think of it like honey versus water – honey has a higher viscosity. CRC Food Grade Chain Lube is formulated to provide optimal lubrication across a range of operating conditions.Here’s the lowdown:
- Viscosity at 40°C (104°F): Typically, this lube boasts a viscosity of around 150-200 cSt (centistokes). This range is chosen because it offers a good balance between film strength and ease of application.
- Viscosity at 100°C (212°F): Expect a viscosity in the range of 15-25 cSt. This ensures the lube maintains its lubricating properties even when things get heated.
- Viscosity Index (VI): This is a measure of how much the viscosity changes with temperature. A higher VI means the viscosity changes less. CRC Food Grade Chain Lube usually has a VI of around 100-120. This indicates a good stability of viscosity across a wide temperature range.
Temperature Range
The temperature range is a critical specification for any lubricant. This tells you the temperatures at which the lube will actually, you know,lubricate*. Using a lube outside its specified temperature range can lead to all sorts of problems, from reduced effectiveness to complete equipment failure. Nobody wants that.
- Operating Temperature Range: CRC Food Grade Chain Lube typically shines within a range of -20°C to 150°C (-4°F to 302°F). This broad range ensures it can handle everything from refrigerated food processing to high-temperature baking applications.
- Flash Point: This is the temperature at which the lube’s vapors ignite when exposed to a flame. CRC Food Grade Chain Lube has a flash point typically above 200°C (392°F), which significantly reduces the risk of fire hazards.
- Pour Point: This is the lowest temperature at which the lube will still flow. A low pour point is essential for applications in cold environments. CRC Food Grade Chain Lube’s pour point is generally below -30°C (-22°F), ensuring smooth operation even in chilly conditions.
Other Relevant Data
Beyond viscosity and temperature, several other factors contribute to the performance and effectiveness of CRC Food Grade Chain Lube. Understanding these details helps in making informed decisions regarding its use.
- Base Oil Type: CRC Food Grade Chain Lube often utilizes a combination of synthetic base oils, such as polyalphaolefins (PAOs) and esters. These base oils offer excellent thermal stability, oxidation resistance, and load-carrying capacity.
- Additives: The formula incorporates various additives to enhance performance. These may include:
- Anti-wear additives: Protect against metal-to-metal contact and reduce friction.
- Rust and corrosion inhibitors: Prevent the formation of rust and corrosion on metal surfaces.
- Antioxidants: Extend the lubricant’s lifespan by preventing degradation.
- Food Grade Certifications: It’s crucial to ensure the lubricant meets the necessary food safety standards. CRC Food Grade Chain Lube is usually NSF H1 registered, meaning it’s safe for incidental food contact. This is critical for food processing environments.
- Density: The density of the lube is typically around 0.85-0.90 g/cm³ at 20°C (68°F).
Detailed Information, Use, and Safety Measures
Imagine a diagram, a detailed illustration of a chain conveyor system in a food processing plant. The image shows the chain itself, glistening with a thin, even layer of CRC Food Grade Chain Lube. Arrows point to key lubrication points on the chain, such as the pins, bushings, and rollers. The background depicts the plant environment – clean, well-lit, and with workers wearing appropriate safety gear.
The diagram also includes small call-out boxes highlighting:
- Proper Application: A detailed explanation of how to apply the lube, whether by spray, brush, or automatic lubrication systems. The text emphasizes the importance of applying a thin, even coat to all moving parts.
- Benefits of Use: Text bubbles around the chain, highlighting benefits such as reduced friction, wear, and noise; extended chain life; and compliance with food safety regulations.
- Safety Precautions: This section is accompanied by an icon showing a pair of safety glasses and gloves. This area includes warnings about avoiding skin contact, proper ventilation, and disposing of the product responsibly.
Last Word
In conclusion, CRC Food Grade Chain Lube is more than just a lubricant; it’s a vital component of a food safety ecosystem. From its carefully selected ingredients to its rigorous testing and compliance, this product exemplifies a commitment to excellence. The advantages are tangible, from extended chain life and reduced friction to economic savings and enhanced hygiene. By understanding its composition, applications, and best practices for use, businesses can unlock the full potential of CRC Food Grade Chain Lube.
Embrace the peace of mind that comes with knowing your machinery is lubricated with a product designed to protect both your operations and the well-being of your consumers. The future of food processing is smoother, safer, and more efficient, thanks to the innovation of CRC Food Grade Chain Lube.