Food film packaging, yeah? It’s the unsung hero keepin’ your scran fresh, innit? From the corner shop sausage roll to the fancy supermarket sushi, it’s all wrapped up in something. We’re gonna delve deep, yeah? Lookin’ at the different types, the materials, and how they keep your nosh safe and sound.
It’s a proper important bit of kit, this packaging lark.
Think about it: it’s gotta keep the grub from goin’ off, stop the bugs gettin’ in, and look the part on the shelf. We’ll be lookin’ at plastics, bioplastics, laminates – the whole shebang. Plus, we’ll be discussin’ the good bits – like keepin’ your grub edible for longer, protectin’ it from muck, and makin’ it easy to handle. Sounds alright, yeah?
Introduction to Food Film Packaging
Food film packaging serves as a critical interface between food products and their surrounding environment. Its primary function is to maintain the safety, quality, and integrity of food throughout its journey from production to consumption. This is achieved by creating a barrier against various external factors that can degrade food, such as oxygen, moisture, light, and microorganisms. The evolution of food film packaging has significantly impacted the food industry, enabling extended shelf lives, reducing food waste, and improving consumer convenience.
Materials Used in Food Film Packaging
A wide range of materials are utilized in the creation of food film packaging, each offering unique properties and suitability for different food products. These materials are chosen based on their barrier characteristics, mechanical strength, and compatibility with the food product.
- Plastics: Plastics remain the dominant material, with polyethylene (PE), polypropylene (PP), and polyethylene terephthalate (PET) being the most common. PE is known for its flexibility and moisture barrier properties, PP offers good clarity and resistance to heat, and PET provides excellent barrier properties against gases and moisture, along with good mechanical strength. These plastics can be tailored with additives to enhance their performance, such as UV stabilizers to protect against light degradation.
- Bioplastics: Bioplastics, derived from renewable resources like cornstarch or sugarcane, are gaining traction due to their reduced environmental impact. Examples include polylactic acid (PLA), which is often used for packaging fruits and vegetables. However, bioplastics may have limitations in terms of barrier properties and cost compared to conventional plastics. Research continues to improve their performance and broaden their applications.
- Laminates: Laminates are created by combining multiple layers of different materials, such as plastic films, aluminum foil, and paper, to achieve a specific combination of properties. For example, a laminate might consist of a layer of PET for strength, a layer of aluminum foil for a complete barrier against oxygen and light, and a layer of PE for heat sealing.
These structures are commonly used for packaging items such as coffee, snacks, and ready-to-eat meals.
Advantages of Food Film Packaging
The use of food film packaging provides a multitude of benefits, significantly impacting the food supply chain and consumer experience. These advantages are a key factor in the widespread adoption of this packaging method.
- Shelf-Life Extension: Food film packaging significantly extends the shelf life of perishable products by controlling the interaction between the food and its environment. By creating a barrier against oxygen, moisture, and other contaminants, packaging slows down spoilage processes such as oxidation, microbial growth, and enzymatic reactions. For example, modified atmosphere packaging (MAP) utilizes specific gas mixtures within the packaging to further extend shelf life.
Studies have shown that MAP can extend the shelf life of fresh produce by several days or even weeks, reducing food waste and increasing distribution range.
- Protection from Contamination: Packaging acts as a crucial shield, preventing food from being exposed to external contaminants, including physical hazards (e.g., dust, dirt), chemical hazards (e.g., cleaning agents), and biological hazards (e.g., bacteria, molds). The integrity of the packaging is essential in maintaining the safety of the food product. The effectiveness of packaging in protecting against microbial contamination is crucial. For example, a study by the Food Standards Agency revealed that proper packaging significantly reduces the risk of foodborne illnesses.
- Ease of Handling: Film packaging provides convenience in handling, storage, and transportation. The flexibility and lightweight nature of film packaging make it easy to handle and transport, reducing the risk of damage during transit. This ease of handling also translates to consumer convenience, as packaging is often designed for easy opening, resealing, and disposal. Innovations like stand-up pouches and easy-open features have further enhanced the consumer experience.
Materials and Technologies in Food Film
Food film packaging utilizes a diverse range of materials and manufacturing techniques to provide protection, preservation, and presentation for food products. The selection of materials and the chosen manufacturing processes significantly influence the film’s performance characteristics, including its barrier properties, mechanical strength, and overall sustainability. This section details the key materials and technologies employed in food film production.
Polymers and Other Materials in Food Film Packaging
Food film packaging relies primarily on polymers, which are large molecules composed of repeating structural units. Other materials are often incorporated to enhance specific properties.
Find out further about the benefits of chinese food bloomfield nj that can provide significant benefits.
- Polyethylene (PE): A widely used thermoplastic polymer known for its flexibility, low cost, and good water barrier properties. It is available in various densities, including Low-Density Polyethylene (LDPE), Medium-Density Polyethylene (MDPE), and High-Density Polyethylene (HDPE), each offering different properties. LDPE is commonly used for flexible films, while HDPE is often found in rigid packaging.
- Polypropylene (PP): Another thermoplastic polymer, PP offers good clarity, high melting point, and excellent resistance to chemicals. It is frequently used for packaging applications requiring heat resistance, such as microwaveable food containers. Oriented Polypropylene (OPP) provides improved clarity and strength.
- Polyethylene Terephthalate (PET): A strong, clear, and recyclable thermoplastic polymer with excellent barrier properties against gases and moisture. PET is often used for bottles, trays, and films requiring good product visibility and extended shelf life.
- Polyvinyl Chloride (PVC): A versatile thermoplastic polymer with good clarity, flexibility, and barrier properties. PVC is used in a variety of food packaging applications, including cling films, but its use is declining due to environmental concerns.
- Polyamide (PA) or Nylon: A family of polymers offering excellent mechanical strength, puncture resistance, and barrier properties, especially to oxygen. They are often used in multi-layer films to enhance the overall performance.
- Ethylene Vinyl Alcohol Copolymer (EVOH): A copolymer with exceptional barrier properties, particularly against oxygen and aroma compounds. EVOH is frequently used as a barrier layer in multi-layer films to extend shelf life.
- Polyvinylidene Chloride (PVDC): Provides exceptional barrier properties against gases, moisture, and aromas. Historically used in cling films, its use is declining due to environmental concerns.
- Aluminum Foil: Provides an excellent barrier against light, oxygen, moisture, and aromas. Often used in flexible packaging as a layer in multi-layer films.
- Paper and Paperboard: Used in various forms, including waxed paper and coated paperboard, to provide structural support and printability.
- Adhesives: Used in lamination processes to bond different layers of film together.
- Inks: Used for printing graphics and information on the packaging.
Manufacturing Processes of Food Film
The manufacturing processes used to produce food films are critical in determining the final properties of the packaging.
- Extrusion: A process where polymer pellets are melted and forced through a die to create a continuous film. Single-layer films are produced using a single extruder, while multi-layer films are produced using co-extrusion. The thickness of the film is controlled by adjusting the die gap and the extrusion speed. For example, LDPE film for produce bags is often made by extrusion.
- Co-extrusion: A process where multiple layers of different polymers are extruded simultaneously to create a multi-layer film. This allows for combining the desirable properties of different materials, such as barrier, strength, and sealability. The layers are combined in a die before being cooled and solidified. Co-extrusion is commonly used to create films with an EVOH barrier layer to extend the shelf life of packaged foods.
- Lamination: A process where two or more pre-made films are bonded together using adhesives. This allows for combining different materials to achieve specific properties, such as improved barrier performance, printability, and strength. Lamination can be done using solvent-based, solvent-free, or water-based adhesives. For example, a PET film can be laminated to a PE film to improve its barrier properties and printability.
- Orientation: Some films undergo orientation processes (e.g., biaxial orientation) to improve their mechanical properties. The film is stretched in one or two directions, which aligns the polymer chains and increases tensile strength, stiffness, and clarity. Oriented polypropylene (OPP) is a result of this process.
Comparison of Film Material Properties
The following table provides a comparison of the properties of various film materials commonly used in food packaging. The properties are categorized as barrier properties (oxygen and moisture), strength (tensile strength and puncture resistance), cost (relative), and recyclability (relative). This comparison is a general overview and can vary based on specific film formulations and processing methods.
Film Material | Barrier Properties | Strength | Cost | Recyclability |
---|---|---|---|---|
Polyethylene (PE) | Good water barrier, fair oxygen barrier | Good flexibility, moderate tensile strength | Low | Widely recyclable (check local regulations) |
Polypropylene (PP) | Good water barrier, fair oxygen barrier | Good clarity, moderate tensile strength | Low to Medium | Widely recyclable (check local regulations) |
Polyethylene Terephthalate (PET) | Excellent water and oxygen barrier | High tensile strength, good puncture resistance | Medium | Widely recyclable |
Polyvinyl Chloride (PVC) | Good water and oxygen barrier | Good flexibility, moderate strength | Low to Medium | Generally not recyclable |
Polyamide (PA/Nylon) | Good oxygen barrier, fair water barrier | Excellent strength, puncture resistance | Medium to High | Generally not recyclable |
Ethylene Vinyl Alcohol Copolymer (EVOH) | Excellent oxygen barrier, good water barrier | Moderate strength | High | Generally not recyclable as a single layer |
Aluminum Foil | Excellent barrier to all gases and light | Moderate strength | High | Recyclable in some areas (specialized collection) |
Packaging Design and Functionality
Packaging design plays a crucial role in the success of food products, acting as a silent salesperson and a critical component of the overall consumer experience. It encompasses aesthetic elements like graphics and shapes, as well as functional aspects such as material selection and structural integrity. Effective design integrates branding, product protection, and consumer convenience, influencing purchasing decisions and brand loyalty.Packaging design significantly enhances product presentation and consumer experience.
Well-designed packaging communicates the product’s quality, freshness, and value, enticing consumers to choose it over competitors.
Attracting Consumers and Branding Food Products
Packaging design is a fundamental element of branding, influencing consumer perception and brand recognition. The visual elements, including color palettes, typography, and imagery, create a unique brand identity that differentiates the product in a crowded marketplace. The shape and structure of the packaging also contribute to brand recognition, making the product easily identifiable on shelves.Effective packaging design communicates the product’s key attributes, such as health benefits, origin, or flavor profile.
For instance, packaging featuring vibrant colors and playful illustrations may appeal to children, while minimalist designs with premium materials can convey a sense of luxury and sophistication. Furthermore, the incorporation of the brand’s logo, tagline, and other brand elements reinforces brand recognition and loyalty. This consistent branding across various packaging formats helps create a cohesive brand image, increasing consumer trust and driving sales.
Enhancing Product Presentation and Consumer Experience
Food film packaging, in particular, offers numerous opportunities to enhance product presentation and the consumer experience. The clarity and transparency of certain films allow consumers to visually inspect the product, increasing their confidence in its quality and freshness.Consider the example of fresh produce packaging. Transparent films allow consumers to see the vibrant colors and textures of fruits and vegetables, enhancing their appeal and encouraging purchase.
Conversely, opaque or printed films can be used to create a sense of mystery or exclusivity, particularly for premium or specialty food products. Moreover, the choice of film material and its properties, such as flexibility and sealability, directly impact the ease of opening and reclosing the package, contributing to consumer convenience and satisfaction. Films that offer easy-open features or resealable closures improve the user experience and extend product shelf life.
Packaging Functionalities
Food film packaging provides a variety of essential functionalities that ensure product safety, extend shelf life, and enhance consumer convenience. These functionalities are often integrated into the film’s design and material properties.* Barrier Protection: Food film packaging provides a crucial barrier against external elements that can degrade food quality, including oxygen, moisture, light, and contaminants. Oxygen barrier films prevent oxidation, preserving the freshness and flavor of products like coffee and snacks.
Moisture barrier films protect against water absorption or loss, crucial for maintaining the texture and integrity of baked goods and cereals. Light barrier films shield light-sensitive products, such as dairy products and oils, from degradation.* Modified Atmosphere Packaging (MAP): MAP involves altering the composition of the gas inside the package to extend shelf life and preserve product quality. This is often achieved by flushing the package with a gas mixture, typically involving carbon dioxide, nitrogen, and oxygen, to inhibit microbial growth and slow down enzymatic reactions.
For example, MAP is widely used for packaging fresh meat, where a high oxygen atmosphere maintains the red color, while modified atmosphere packaging of leafy greens utilizes a combination of low oxygen and high carbon dioxide to slow respiration and maintain freshness.* Portion Control: Packaging design facilitates portion control, helping consumers manage their food intake and reduce waste.
Individual serving sizes, pre-portioned snacks, and resealable packaging enable consumers to consume the desired amount and store the remaining product safely. For instance, single-serve yogurt cups and pre-portioned snack bags contribute to convenient portion control, supporting healthier eating habits.
Sustainability and Environmental Impact
Food film packaging, while crucial for food preservation and safety, presents significant environmental challenges. The widespread use of plastic films, particularly those derived from fossil fuels, contributes substantially to plastic waste accumulation, pollution of ecosystems, and greenhouse gas emissions. Addressing these issues is paramount to fostering a more sustainable food packaging industry.The environmental burden of food film packaging necessitates a transition towards more sustainable practices.
This involves a multifaceted approach, encompassing the reduction of plastic usage, the adoption of renewable resources, and the implementation of effective waste management strategies. Exploring innovative materials and technologies is essential to minimize the environmental footprint of food packaging.
Environmental Challenges of Food Film Packaging
The environmental impact of food film packaging stems primarily from its material composition and end-of-life management. The vast majority of food films are made from petroleum-based plastics, which are not readily biodegradable. This leads to several significant environmental consequences.
- Plastic Waste Accumulation: The non-biodegradable nature of plastic films results in their accumulation in landfills and natural environments, including oceans. This contributes to the global plastic waste crisis.
- Pollution of Ecosystems: Plastic films can break down into smaller fragments (microplastics) that contaminate soil, water, and air. These microplastics pose a threat to wildlife and can enter the food chain, potentially impacting human health.
- Greenhouse Gas Emissions: The production of plastic films, from the extraction of raw materials to manufacturing processes, consumes significant energy and generates greenhouse gas emissions. Furthermore, the incineration of plastic waste releases harmful pollutants into the atmosphere.
- Resource Depletion: The reliance on fossil fuels for plastic production contributes to the depletion of finite natural resources.
Methods for Reducing the Environmental Footprint
Mitigating the environmental impact of food film packaging requires the implementation of several strategies, including the use of recycled materials, the development of biodegradable films, and the promotion of circular economy principles. These approaches aim to minimize waste, conserve resources, and reduce pollution.
- Using Recycled Materials: Incorporating recycled content into food film packaging reduces the demand for virgin plastics and diverts plastic waste from landfills. Post-consumer recycled (PCR) plastics, such as recycled polyethylene terephthalate (rPET), can be used to produce films for various food applications.
- Promoting Biodegradability: Developing and utilizing biodegradable films made from renewable resources, such as corn starch, cellulose, or polylactic acid (PLA), allows the packaging to break down naturally in composting environments. This reduces the persistence of plastic waste in the environment.
- Optimizing Packaging Design: Reducing the amount of packaging material used and designing films for recyclability or compostability can minimize waste generation. This involves streamlining packaging formats and selecting appropriate materials.
- Implementing Waste Management Systems: Improving waste collection and recycling infrastructure, including composting facilities, facilitates the proper disposal and management of food film packaging waste.
Sustainable Packaging Solutions: Benefits and Drawbacks
The selection of sustainable packaging solutions involves considering their environmental benefits, technical performance, and economic feasibility. The following table provides a comparative analysis of various sustainable packaging options, examining their advantages and disadvantages.
Packaging Solution | Benefits | Drawbacks | Example |
---|---|---|---|
Compostable Films |
|
|
PLA films for fruit and vegetable packaging. |
Reusable Packaging |
|
|
Reusable containers for takeaway food. |
Recycled Content Films |
|
|
Films made from rPET for beverage bottles. |
Bio-based Films |
|
|
Films made from cellulose for food wrapping. |
Regulations and Compliance
Food film packaging operates within a complex regulatory landscape designed to safeguard consumer health and ensure fair market practices. Adherence to these regulations is paramount for manufacturers and suppliers, influencing every stage from material selection and manufacturing processes to labeling and distribution. Non-compliance can result in significant penalties, including product recalls, legal action, and damage to brand reputation.
Relevant Regulations and Standards Governing Food Film Packaging
A wide range of regulations and standards directly impacts food film packaging, varying by region and country. These standards aim to control the materials used, manufacturing processes, and information presented to consumers.
- Food Contact Regulations: These are the cornerstone of food film packaging regulations. They specify which materials are permitted for use in contact with food and set limits on the migration of substances from the packaging into the food.
- United States (FDA): The Food and Drug Administration (FDA) regulates food contact materials under the Federal Food, Drug, and Cosmetic Act. Regulations, such as 21 CFR (Code of Federal Regulations) Part 177, detail the specific substances permitted for use and the conditions under which they can be used.
The FDA also conducts inspections of manufacturing facilities to ensure compliance.
- European Union (EU): The EU has a comprehensive framework for food contact materials, primarily Artikeld in Regulation (EC) No 1935/2004. This framework establishes general requirements for all food contact materials and provides specific regulations for different material types, including plastics (Regulation (EU) No 10/2011). The EU uses a positive list approach, meaning only substances explicitly authorized are permitted.
- Other Regions: Other regions, such as Canada (Health Canada) and various countries in Asia and South America, have their own specific regulations. These regulations often align with international standards but may have unique requirements or specific lists of approved substances.
- United States (FDA): The Food and Drug Administration (FDA) regulates food contact materials under the Federal Food, Drug, and Cosmetic Act. Regulations, such as 21 CFR (Code of Federal Regulations) Part 177, detail the specific substances permitted for use and the conditions under which they can be used.
- Labeling Regulations: These regulations mandate the information that must be displayed on food packaging, including food film packaging. The aim is to provide consumers with accurate and useful information to make informed choices.
- Nutritional Labeling: Regulations such as the Nutrition Labeling and Education Act (NLEA) in the US and the Food Information Regulation (FIR) in the EU require the presentation of nutritional information on packaged foods.
This includes details on serving sizes, calories, macronutrients (fat, carbohydrates, protein), and micronutrients (vitamins and minerals).
- Ingredient Declaration: Ingredients must be listed in descending order of weight. This information helps consumers identify potential allergens and other ingredients they may want to avoid.
- Allergen Information: Specific labeling requirements for allergens are crucial. In the EU, the Food Information Regulation (FIR) requires that 14 major allergens be declared on packaging. In the US, the Food Allergen Labeling and Consumer Protection Act (FALCPA) mandates clear labeling of major food allergens.
- Country of Origin: Consumers may need to know the country where the food or the packaging was produced.
- Nutritional Labeling: Regulations such as the Nutrition Labeling and Education Act (NLEA) in the US and the Food Information Regulation (FIR) in the EU require the presentation of nutritional information on packaged foods.
- Specific Material Regulations: These regulations focus on the specific properties and safety aspects of the packaging materials themselves.
- Plastics: Regulations often focus on the migration of chemicals from plastics into food. Specific migration limits (SMLs) are set for individual substances. Regulations also address the use of recycled plastics and require that they meet stringent purity standards.
- Paper and Board: Regulations may address the use of specific chemicals in paper and board packaging, such as inks and coatings, to prevent migration into food.
- Coatings and Inks: Regulations often set limits on the amount of specific chemicals that can be present in coatings and inks used on food packaging, to minimize the risk of migration.
Types of Information Required on Food Film Packaging Labels
Accurate and comprehensive labeling is a critical component of regulatory compliance and consumer protection. Labels must convey essential information clearly and concisely.
- Product Name and Description: The name of the food product and a brief description of its contents must be clearly stated.
- Ingredient List: All ingredients used in the food product must be listed in descending order of weight.
- Nutritional Information: A nutrition facts panel, including serving size, calories, macronutrients, and micronutrients, is required.
- Allergen Information: Major allergens must be clearly identified, often using bold type or a separate allergen statement.
- Net Quantity: The net weight or volume of the food product must be stated.
- Manufacturer Information: The name and address of the manufacturer or distributor must be provided.
- Country of Origin: The country where the food product was manufactured or packaged must be indicated.
- Date Marking: Best-before or use-by dates are typically required to indicate the shelf life of the product.
- Storage Instructions: Instructions on how to store the product to maintain its quality and safety are often included.
- Recycling Information: Information on the recyclability of the packaging materials is increasingly required, including the recycling symbol and material codes.
Importance of Complying with Regulations
Compliance with food film packaging regulations is not merely a legal obligation; it is crucial for protecting consumer safety and safeguarding brand reputation.
- Consumer Safety: The primary purpose of food packaging regulations is to protect consumer health. By controlling the materials used and the information provided, these regulations minimize the risk of contamination and ensure that consumers can make informed choices about the food they consume.
For example, regulations limiting the migration of phthalates from plastic packaging into food help to reduce potential health risks associated with exposure to these chemicals.
- Preventing Adulteration and Misbranding: Regulations ensure that food products are accurately labeled and do not contain harmful substances. This prevents adulteration (the addition of inferior or harmful substances) and misbranding (false or misleading labeling).
- Protecting Brand Reputation: Compliance with regulations builds trust with consumers. Brands that consistently meet or exceed regulatory standards are seen as more reliable and trustworthy, which can lead to increased sales and customer loyalty. Conversely, non-compliance can result in product recalls, negative publicity, and damage to a brand’s reputation, leading to a significant loss of consumer trust.
- Avoiding Legal and Financial Penalties: Failure to comply with regulations can result in significant financial penalties, including fines and legal action. In severe cases, non-compliance can lead to the seizure of products, the closure of manufacturing facilities, and even criminal charges.
- Facilitating International Trade: Adhering to international food packaging regulations is essential for companies that export their products. Compliance with the regulations of the importing country is often a prerequisite for market access.
Innovation and Future Trends
The food film packaging industry is characterized by continuous innovation, driven by consumer demand for enhanced food safety, extended shelf life, and reduced environmental impact. This section explores emerging trends and technological advancements that are reshaping the landscape of food film packaging, focusing on active and intelligent packaging, and the potential of nanotechnology.
Emerging Trends in Food Film Packaging
The food packaging industry is witnessing a shift towards technologies that go beyond simple containment, offering active functionalities and smart capabilities. These trends aim to improve food quality, reduce waste, and provide consumers with valuable information.
- Active Packaging: Active packaging interacts with the packaged food or the surrounding environment to extend shelf life and enhance food safety. This can involve the release of antimicrobial agents, oxygen scavengers, or moisture absorbers.
- Antimicrobial Films: These films incorporate antimicrobial agents, such as silver nanoparticles or essential oils, to inhibit the growth of spoilage microorganisms. For example, films containing nisin, a naturally occurring bacteriocin, can be used to control the growth of
-Listeria monocytogenes* in meat products. - Oxygen Scavenging Films: These films incorporate oxygen absorbers to reduce the oxygen content within the package, preventing oxidation and extending the shelf life of oxygen-sensitive foods. The reaction typically involves the oxidation of iron powder or ascorbic acid within the film.
- Ethylene Scavenging Films: Specifically designed for fruits and vegetables, these films absorb ethylene gas, a ripening hormone, to slow down the ripening process and extend shelf life. Activated carbon or potassium permanganate are commonly used as ethylene scavengers.
- Antimicrobial Films: These films incorporate antimicrobial agents, such as silver nanoparticles or essential oils, to inhibit the growth of spoilage microorganisms. For example, films containing nisin, a naturally occurring bacteriocin, can be used to control the growth of
- Intelligent Packaging: Intelligent packaging incorporates sensors and indicators to provide information about the condition of the packaged food, such as temperature, freshness, and potential spoilage.
- Time-Temperature Indicators (TTIs): TTIs change color or appearance in response to cumulative temperature exposure, providing a visual indication of the food’s temperature history and helping to assess its quality. These are particularly useful for monitoring the cold chain.
- Gas Sensors: Gas sensors detect the presence of specific gases, such as carbon dioxide or volatile organic compounds (VOCs), that are indicative of food spoilage. These sensors can provide early warning signs of degradation.
- Freshness Indicators: These indicators, often based on pH changes or enzymatic reactions, signal the onset of spoilage by changing color or appearance. For instance, a freshness indicator might change color when the pH in the package shifts due to bacterial growth.
- Edible Films: Edible films are thin layers of edible materials that can be used to package food. They are designed to be consumed along with the food, reducing packaging waste and offering an alternative to traditional plastic films.
- Protein-Based Films: Proteins such as whey protein, casein, and soy protein can be used to create edible films. These films provide good barrier properties to oxygen and carbon dioxide.
- Polysaccharide-Based Films: Polysaccharides like cellulose, starch, and chitosan are used to create edible films. Chitosan films, for example, exhibit antimicrobial properties.
- Lipid-Based Films: Lipids, such as waxes and fatty acids, can be used to create edible films that provide good moisture barrier properties.
Advancements in Technology Impacting Food Film Packaging
Technological advancements are continually improving the performance, sustainability, and functionality of food film packaging. These advancements include the use of new materials, advanced manufacturing techniques, and digital technologies.
- New Materials: The development of new materials with improved barrier properties, mechanical strength, and biodegradability is a key driver of innovation.
- Bio-based Polymers: Polymers derived from renewable resources, such as polylactic acid (PLA), polyhydroxyalkanoates (PHAs), and starch-based polymers, are being increasingly used to reduce the reliance on fossil fuels and improve the biodegradability of packaging.
- Nanocomposites: Incorporating nanoparticles, such as nanoclay or cellulose nanocrystals, into polymer matrices can enhance barrier properties, mechanical strength, and thermal stability.
- Multilayer Films: The development of multilayer films combines different materials to create packaging with tailored properties, such as high barrier to oxygen and moisture, and good mechanical strength.
- Advanced Manufacturing Techniques: These techniques are improving the efficiency and precision of film production.
- 3D Printing: 3D printing allows for the creation of customized packaging with complex geometries and functionalities. This technology can be used to produce packaging with integrated sensors or tailored barrier properties.
- Plasma Treatment: Plasma treatment modifies the surface properties of films, improving their barrier properties, printability, and adhesion.
- Roll-to-Roll Processing: This high-speed manufacturing process is used to produce large volumes of film with consistent quality.
- Digital Technologies: Digital technologies are being integrated into packaging to enhance tracking, traceability, and consumer engagement.
- QR Codes and RFID Tags: These technologies provide consumers with information about the product, such as its origin, ingredients, and shelf life. They also facilitate supply chain tracking and product authentication.
- Smart Printing: Smart printing technologies, such as inkjet printing, allow for the printing of variable data on packaging, enabling personalized marketing and enhanced traceability.
- Blockchain Technology: Blockchain technology can be used to create a secure and transparent supply chain, tracking the product from origin to consumer.
Nanotechnology in Food Film Packaging
Nanotechnology offers significant potential to enhance the performance of food film packaging, particularly in terms of barrier properties and shelf life extension.
- Enhanced Barrier Properties: Nanomaterials, such as nanoclay, metal oxides, and carbon nanotubes, can be incorporated into polymer matrices to create films with improved barrier properties to oxygen, moisture, and other gases.
- Nanoclays: The addition of nanoclays to polymer films can significantly reduce the permeability of oxygen and water vapor, extending the shelf life of oxygen-sensitive foods. For example, films containing montmorillonite nanoclay have shown a significant reduction in oxygen transmission rates.
- Metal Oxides: Nanoparticles of metal oxides, such as titanium dioxide (TiO2) and zinc oxide (ZnO), can improve the barrier properties of films to UV light and oxygen.
- Carbon Nanotubes: Carbon nanotubes can be used to create highly impermeable films with excellent mechanical properties.
- Shelf Life Extension: Nanotechnology can be used to extend the shelf life of food products by inhibiting microbial growth, reducing oxidation, and controlling moisture migration.
- Antimicrobial Nanoparticles: Nanoparticles of silver, copper oxide, and other antimicrobial agents can be incorporated into films to inhibit the growth of spoilage microorganisms. These nanoparticles can be released slowly, providing long-lasting antimicrobial protection.
- Oxygen Scavenging Nanocomposites: Nanocomposites containing oxygen scavengers, such as iron nanoparticles, can be used to reduce the oxygen content within the package, preventing oxidation and extending shelf life.
- Moisture Barrier Nanocomposites: Nanocomposites with improved moisture barrier properties can be used to prevent moisture migration, maintaining the texture and quality of food products.
- Examples of Nanotechnology Applications:
- Active Packaging for Meat: Nanocomposite films containing silver nanoparticles are used to extend the shelf life of fresh meat products by inhibiting the growth of spoilage bacteria.
- Modified Atmosphere Packaging for Fruits and Vegetables: Films containing nanoclay are used to control the gas permeability of packaging, maintaining the optimal atmosphere for fruits and vegetables and extending their shelf life.
- Smart Packaging with Nanosenors: Nanotechnology is used to create sensors that can detect changes in the packaged food, such as temperature fluctuations or the presence of spoilage indicators.
Packaging for Specific Food Products: Food Film Packaging
Food packaging design is highly product-specific, necessitating tailored solutions to preserve quality, extend shelf life, and ensure consumer safety. The diverse characteristics of food products, ranging from fresh produce’s respiration rates to meat’s susceptibility to microbial growth, dictate the need for a nuanced approach to packaging material selection and design. This section explores the unique packaging requirements for various food categories and provides examples of specialized packaging solutions.
Packaging Requirements for Fresh Produce
Fresh produce presents unique challenges due to its inherent biological activity. The primary goals of packaging for fresh produce are to control respiration, minimize moisture loss, and protect against physical damage. Packaging must also allow for the exchange of gases, primarily oxygen and carbon dioxide, to maintain optimal ripening and prevent anaerobic conditions.Packaging solutions often involve:
- Modified Atmosphere Packaging (MAP): This technique alters the gas composition within the package to slow down respiration and enzymatic browning. This typically involves reducing oxygen levels and increasing carbon dioxide concentrations.
- Perforated Films: These films provide controlled gas exchange, allowing for the release of respiratory gases while minimizing moisture loss. The size and number of perforations are crucial and depend on the produce type and storage conditions.
- Absorbent Pads: Placed within the packaging, these pads absorb excess moisture, preventing microbial growth and maintaining product quality.
Packaging Requirements for Meat Products
Meat products are highly perishable and susceptible to spoilage due to microbial growth and oxidation. Packaging must therefore provide a strong barrier against oxygen, moisture, and microorganisms. The specific requirements vary depending on the type of meat, processing method, and intended shelf life.Common packaging strategies include:
- Vacuum Packaging: This method removes oxygen from the package, inhibiting the growth of aerobic bacteria and extending shelf life. It’s widely used for fresh and processed meats.
- Modified Atmosphere Packaging (MAP): In MAP for meat, high concentrations of carbon dioxide and/or nitrogen are often used to inhibit microbial growth and maintain product color.
- Skin Packaging: This technique uses a heat-sealable film that conforms tightly to the product’s shape, providing excellent oxygen barrier properties and enhancing product presentation.
Packaging Requirements for Dairy Products
Dairy products, such as milk, cheese, and yogurt, are sensitive to light, oxygen, and temperature fluctuations. Packaging must protect against these factors to maintain product quality and prevent spoilage. The specific requirements vary depending on the product’s fat content, acidity, and intended shelf life.Typical packaging solutions include:
- Multi-Layer Packaging: For milk and other liquid dairy products, multi-layer cartons or plastic bottles are commonly used. These packages typically incorporate layers of paperboard, polyethylene, and aluminum foil to provide a barrier against light, oxygen, and moisture.
- Modified Atmosphere Packaging (MAP): Some cheeses are packaged in MAP to control microbial growth and maintain texture and flavor.
- Protective Films: Yogurt containers often use films that provide a barrier against oxygen and moisture, as well as protection from light exposure.
Packaging Requirements for Baked Goods
Baked goods are susceptible to staling, moisture loss, and microbial spoilage. Packaging aims to maintain freshness, prevent moisture migration, and protect against physical damage. The specific requirements vary depending on the type of baked good and its intended shelf life.Effective packaging strategies include:
- Moisture Barrier Films: These films prevent moisture loss, which leads to staling. Polypropylene and polyethylene are commonly used for this purpose.
- Modified Atmosphere Packaging (MAP): MAP can extend shelf life by inhibiting mold growth and slowing down staling.
- Controlled Release Films: For some baked goods, packaging might include components that release preservatives or flavor enhancers over time.
Film Properties for Various Food Products
The following table summarizes the specific film properties needed for different food products. This table provides a simplified overview, and the exact requirements can vary depending on specific product formulations, processing methods, and storage conditions.
Food Product | Gas Permeability (O2) | Moisture Barrier | Light Barrier | Other Important Properties |
---|---|---|---|---|
Fresh Produce (e.g., berries) | Controlled (moderate to high) | Moderate to High | Low to Moderate | Puncture Resistance, Anti-fogging |
Fresh Meat | Very Low | High | High | Good Seal Integrity, Puncture Resistance |
Processed Meat (e.g., sliced ham) | Very Low | High | High | Good Seal Integrity, Easy Peelability |
Dairy Products (e.g., milk) | Very Low | High | High | Heat Sealability, Stiffness |
Cheese (e.g., shredded cheese) | Very Low | High | High | Anti-fogging, Seal Integrity |
Baked Goods (e.g., bread) | Moderate to Low | High | Low to Moderate | Heat Sealability, Tear Resistance |
Dry Snacks (e.g., chips) | Very Low | High | High | Good Seal Integrity, Stiffness |
Supply Chain Considerations
Food film packaging plays a crucial role in optimizing the efficiency and sustainability of the food supply chain, impacting every stage from production to consumption. Effective packaging minimizes waste, preserves product quality, and reduces logistical complexities, contributing to overall cost savings and environmental benefits. The selection and design of food film packaging directly influence the efficiency of operations and the integrity of the food products.
Contribution to Food Supply Chain Efficiency
Food film packaging enhances the efficiency of the food supply chain through several mechanisms. It protects food products from physical damage, contamination, and spoilage, thereby reducing food waste, a significant concern in modern supply chains. Furthermore, it facilitates efficient transportation, storage, and distribution, leading to reduced operational costs and improved shelf life. The implementation of advanced packaging technologies, such as modified atmosphere packaging (MAP) and active packaging, further extends shelf life and minimizes the need for preservatives, streamlining processes and improving consumer experience.
Role in Transportation, Storage, and Distribution
Packaging is indispensable throughout the transportation, storage, and distribution phases of the food supply chain. The packaging design must withstand the rigors of transportation, including vibration, temperature fluctuations, and handling.
- Transportation: Packaging protects products during transit, preventing damage and ensuring product integrity. The packaging material’s strength, barrier properties, and sealing effectiveness are critical for withstanding the mechanical stresses and environmental factors encountered during transport. For example, the use of multi-layer films provides superior puncture resistance, reducing the likelihood of leaks or damage during handling and stacking.
- Storage: Proper packaging extends the shelf life of food products by controlling the environment within the package. Barrier films prevent the ingress of oxygen, moisture, and other contaminants that can cause spoilage. Vacuum packaging and MAP techniques are commonly used to create controlled atmospheres, further extending shelf life and preserving food quality. For instance, the storage of fresh produce in modified atmosphere packaging can significantly extend its shelf life from a few days to several weeks, reducing waste and improving availability.
- Distribution: Packaging facilitates efficient distribution by enabling easy handling, stacking, and identification of products. Clear labeling and information on the packaging are crucial for tracking products throughout the supply chain. The packaging design should also consider the ergonomics of handling and distribution, ensuring ease of use for retailers and consumers.
Steps in Packaging Food Products for Global Shipping
Packaging food products for global shipping requires a systematic approach to ensure product safety, quality, and compliance with international regulations. The process involves several key steps:
- Product Assessment: This involves assessing the food product’s characteristics, including its perishability, sensitivity to environmental factors, and regulatory requirements. The assessment guides the selection of appropriate packaging materials and methods.
- Packaging Material Selection: Choosing packaging materials that provide the necessary barrier properties, protection, and durability for the intended shipping conditions is critical. Considerations include the film’s resistance to moisture, oxygen, and light, as well as its ability to withstand temperature fluctuations. Examples of suitable materials include multi-layer films with various barrier layers, vacuum-sealed pouches, and modified atmosphere packaging.
- Packaging Design and Prototyping: The packaging design must protect the product during handling, storage, and transportation, as well as meet the regulatory requirements of the destination countries. Prototyping and testing are essential to ensure the packaging’s performance under simulated shipping conditions.
- Packaging and Sealing: This involves filling the packaging with the food product and sealing it securely. The sealing process must ensure an airtight and leak-proof seal to prevent contamination and maintain product freshness.
- Labeling and Marking: Accurate and compliant labeling is essential for international shipping. Labels must include information required by the destination country’s regulations, such as product name, ingredients, nutritional information, country of origin, and any necessary warnings. Marking the packaging with handling instructions, weight, and dimensions is also crucial for efficient handling and tracking.
- Secondary Packaging and Palletization: Secondary packaging, such as corrugated boxes or shrink wrap, provides additional protection during transportation and facilitates handling. Palletization organizes the packaged products for efficient loading and unloading, as well as ensuring stability during transit.
- Quality Control and Inspection: Rigorous quality control measures are implemented throughout the packaging process to ensure that all packages meet the required standards. This includes inspecting the packaging materials, the sealing integrity, and the labeling accuracy.
- Compliance and Documentation: Compliance with international shipping regulations, including food safety standards and import/export requirements, is essential. Proper documentation, such as packing lists, bills of lading, and certificates of origin, must be prepared.
Consumer Behavior and Preferences
Consumer behavior is a critical driver of food film packaging choices, influencing design, materials, and functionality. Understanding consumer preferences, which are often shaped by cultural norms, demographics, and lifestyle choices, is essential for creating packaging that effectively attracts, informs, and satisfies the target audience. This section will explore how these preferences dictate packaging decisions and impact the overall success of food products.
Influence of Consumer Preferences on Food Film Packaging
Consumer preferences significantly influence the selection and development of food film packaging. Factors such as convenience, sustainability, shelf life, and brand perception are paramount. The packaging must align with these preferences to resonate with consumers and drive purchasing decisions.
- Convenience: Consumers increasingly prioritize convenience. Packaging formats that are easy to open, resealable, portable, and suitable for single servings are highly valued. For example, stand-up pouches with zipper closures are popular for snacks, as they offer both convenience and portion control.
- Sustainability: Environmental concerns are growing, leading to increased demand for sustainable packaging. Consumers favor packaging made from recycled materials, biodegradable films, or those designed for recyclability. The rise of plant-based films and compostable packaging reflects this trend.
- Shelf Life and Food Safety: Maintaining food freshness and safety is crucial. Consumers expect packaging to protect products from spoilage, contamination, and physical damage. Modified atmosphere packaging (MAP) and vacuum packaging are employed to extend shelf life and preserve food quality, thereby meeting consumer expectations.
- Brand Perception: Packaging serves as a critical tool for communicating brand values and differentiating products. Consumers are drawn to packaging that reflects the brand’s identity, whether it emphasizes premium quality, health benefits, or ethical sourcing.
- Information and Transparency: Consumers demand clear and accurate information about the product, including ingredients, nutritional facts, and sourcing details. Packaging that provides this information in a transparent and easily understandable manner is more likely to gain consumer trust and preference.
Impact of Packaging Design on Purchasing Decisions, Food film packaging
Packaging design elements, including aesthetics, functionality, and information presentation, significantly influence consumer purchasing decisions. These elements create the first point of contact with the consumer and play a vital role in attracting attention, conveying product value, and influencing the final purchase.
- Visual Appeal: The visual design of the packaging, including colors, graphics, and typography, is the initial point of contact. Eye-catching designs, use of high-quality imagery, and effective color palettes can attract consumers’ attention on crowded shelves. The packaging should also align with the brand’s visual identity.
- Material and Texture: The materials used in packaging influence the perceived quality of the product. Premium materials, such as high-gloss films or textured surfaces, can convey a sense of luxury and quality. Conversely, sustainable materials like recycled paperboard or bio-based films signal environmental responsibility.
- Shape and Structure: The shape and structure of the packaging impact its functionality and shelf appeal. Innovative shapes and ergonomic designs can improve handling and usability, making the product more attractive to consumers. For instance, bottles with easy-grip features or resealable pouches enhance consumer experience.
- Information Presentation: Clear and concise product information, including nutritional facts, ingredient lists, and usage instructions, is crucial. Effective information design, using legible fonts and well-organized layouts, ensures that consumers can easily access and understand the information they need.
- Shelf Impact: The way packaging performs on the shelf is critical. Packaging that stands out from the competition, whether through unique shapes, colors, or branding, is more likely to capture consumer attention and drive sales. For example, using bold colors or distinctive fonts can differentiate a product from its competitors.
Role of Packaging in Communicating Product Information and Brand Values
Packaging serves as a vital communication tool, conveying product information and brand values to consumers. It facilitates brand recognition, builds trust, and influences consumer perceptions. Packaging communicates key messages about the product and the brand.
- Product Information: Packaging provides essential product information, including ingredients, nutritional facts, and usage instructions. The clarity and accuracy of this information are critical for consumer trust and satisfaction.
- Brand Identity: Packaging visually represents the brand’s identity, including its logo, color palette, and overall design. Consistent branding across all packaging elements helps consumers recognize and remember the brand.
- Brand Values: Packaging communicates brand values, such as sustainability, ethical sourcing, or health benefits. This can be achieved through the use of sustainable materials, certifications, or messaging on the packaging.
- Marketing and Promotion: Packaging can be used for marketing and promotional purposes, such as highlighting special offers, new product features, or seasonal promotions.
- Storytelling: Packaging can be used to tell a story about the product, its origins, or its unique qualities. This can create an emotional connection with consumers and enhance brand loyalty. For instance, using imagery or narratives on packaging that highlight the product’s heritage or the ingredients’ source.
Cost Considerations in Food Film Packaging
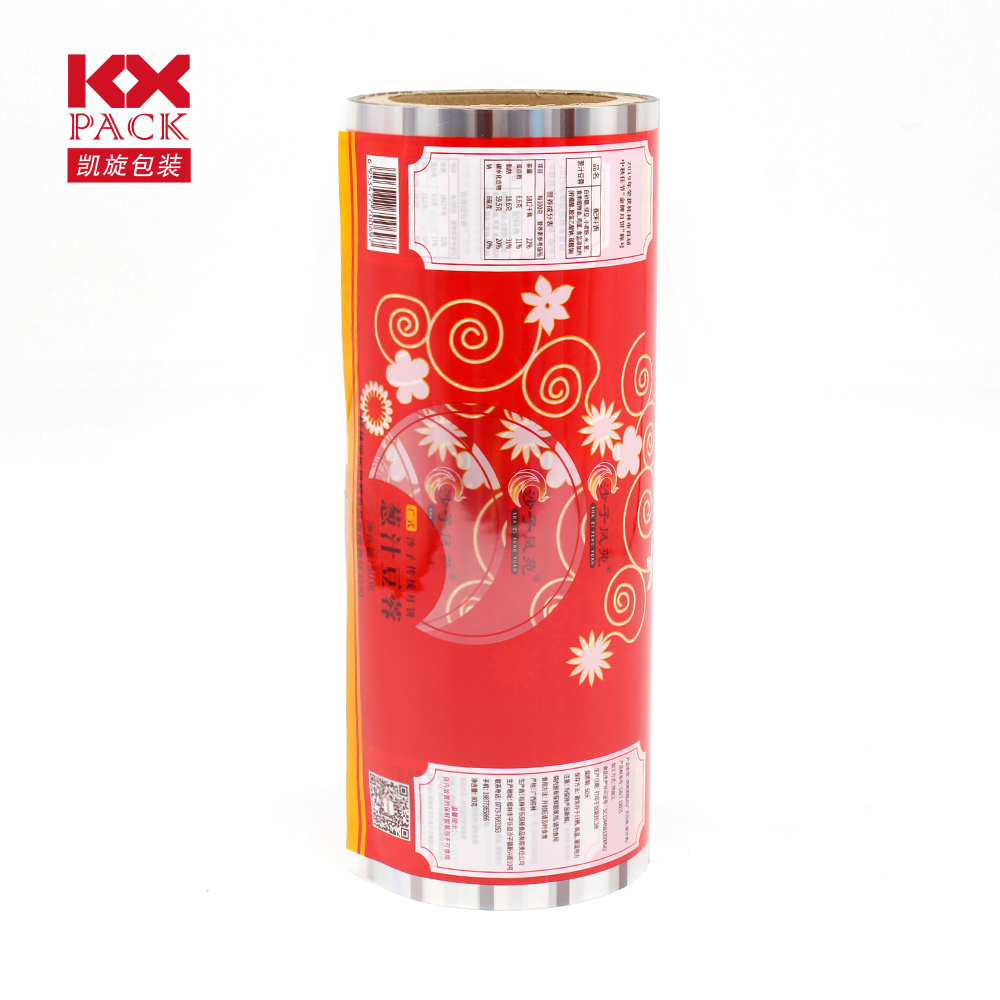
The economic viability of food film packaging is a critical determinant of its adoption and sustainability. Understanding the cost drivers associated with materials, manufacturing processes, and distribution is essential for businesses to make informed decisions. A comprehensive cost analysis allows for the optimization of packaging designs, material selection, and supply chain management, ultimately influencing profitability and competitiveness in the market.
Factors Influencing Food Film Packaging Costs
Several interconnected factors significantly impact the overall cost of food film packaging. These factors span the material composition, manufacturing processes, and the complexities of the supply chain.
- Material Costs: The raw material used in food film production constitutes a significant portion of the overall cost. The type of polymer (e.g., polyethylene, polypropylene, polyester), the presence of barrier layers (e.g., ethylene vinyl alcohol (EVOH), aluminum foil), and the inclusion of additives (e.g., antioxidants, UV stabilizers) directly influence material expenses. Furthermore, the global price of raw materials, influenced by factors such as crude oil prices, supply chain disruptions, and geopolitical events, adds volatility to these costs.
- Manufacturing Processes: The methods employed to convert raw materials into food films play a vital role in cost determination. Extrusion, co-extrusion, lamination, and printing processes each have associated costs related to equipment, energy consumption, labor, and waste management. For instance, complex multi-layer films require sophisticated co-extrusion lines, which involve higher initial investment and operational expenses compared to simpler mono-layer film production.
- Packaging Design: The design of the packaging, including its shape, size, and features (e.g., resealable closures, easy-open features), significantly impacts the material usage and manufacturing complexity. More intricate designs may require specialized equipment and processes, leading to increased production costs. Moreover, the design must consider the product-to-package ratio, which can impact material waste.
- Printing and Graphics: Printing and graphics are essential for branding, product information, and consumer appeal. The type of printing method (e.g., flexography, rotogravure, digital printing), the number of colors used, and the complexity of the artwork affect printing costs. Digital printing, while offering flexibility and reduced setup costs for short runs, may have higher per-unit costs compared to flexography for large-scale production.
- Transportation and Logistics: The cost of transporting raw materials to the manufacturing facility and finished packaging to distribution centers is a crucial component of the overall cost structure. Factors such as distance, mode of transportation (e.g., truck, rail, sea), fuel prices, and warehousing costs contribute to these expenses. Optimized logistics, including efficient route planning and inventory management, are essential to minimize these costs.
- Waste Management and Disposal: The generation of waste during film production and disposal of used packaging contribute to overall costs. Compliance with environmental regulations, the implementation of recycling programs, and the adoption of sustainable packaging materials can mitigate these costs, but they also involve upfront investments and operational adjustments.
- Labor Costs: Labor expenses associated with operating machinery, quality control, and other manufacturing processes are a crucial component. These costs vary depending on geographical location, skill levels, and the level of automation within the production facility. Automation can often reduce labor costs, but requires substantial initial investment.
- Regulatory Compliance: Adherence to food safety regulations, such as those set by the Food and Drug Administration (FDA) or the European Food Safety Authority (EFSA), can increase costs. Compliance often involves testing, documentation, and the use of approved materials, adding to the overall expenses.
Cost-Effectiveness Comparison of Packaging Options
Evaluating the cost-effectiveness of different food packaging options requires a comparative analysis of material costs, manufacturing processes, and performance characteristics. This comparison allows businesses to select the most suitable packaging solution that balances cost considerations with the required level of protection, shelf life, and consumer appeal.
Packaging Option | Material | Material Cost (per unit) | Manufacturing Cost (per unit) | Pros | Cons | Applications |
---|---|---|---|---|---|---|
Mono-layer Polyethylene (PE) Film | Polyethylene | Low | Low | Low cost, good sealability, readily recyclable (depending on the type) | Poor barrier properties, limited shelf life for sensitive products | Fresh produce, baked goods, frozen foods |
Multi-layer Co-extruded Film (PE/EVOH/PE) | Polyethylene, Ethylene Vinyl Alcohol (EVOH) | Medium | Medium | Improved barrier properties (oxygen, moisture), extended shelf life | Higher cost than mono-layer films, more complex recycling | Processed meats, cheese, ready-to-eat meals |
Laminated Film (PET/Aluminum Foil/PE) | Polyethylene Terephthalate (PET), Aluminum Foil, Polyethylene | High | High | Excellent barrier properties, high product protection, good for high-value products | High cost, difficult to recycle, not environmentally friendly | Coffee, snacks, pet food |
Bioplastic Films (PLA) | Polylactic Acid (PLA) | High | Medium to High | Renewable resource, compostable (under specific conditions) | Higher cost than conventional plastics, limited barrier properties, may not be suitable for all food products | Produce, bakery items (where composting is available) |
The material costs are relative, and they can change according to market fluctuations. Manufacturing costs also fluctuate based on factors like energy and labor expenses. The table provides a general overview to guide in cost-effectiveness comparisons.
Optimizing Packaging Design to Reduce Costs
Packaging design optimization is a strategic approach to minimize costs while preserving functionality and safety. Several techniques can be implemented to achieve this balance, focusing on material reduction, process efficiency, and supply chain optimization.
- Material Reduction: Minimizing the amount of packaging material used without compromising product protection is a key cost-saving strategy. This can be achieved through down-gauging films (reducing the thickness of the film), using thinner layers in multi-layer structures, and optimizing the package dimensions to fit the product precisely.
- Design Simplification: Simplifying the packaging design by reducing the number of components, eliminating unnecessary features, and using standard shapes can reduce material waste and manufacturing complexity. For example, opting for a simple pouch design instead of a complex stand-up pouch with multiple closures can reduce material usage and manufacturing steps.
- Process Optimization: Streamlining the manufacturing process can reduce costs. This involves selecting efficient printing methods, optimizing sealing parameters to minimize waste, and implementing automation to increase production speed and reduce labor costs. For instance, using in-line printing during the extrusion process can eliminate the need for separate printing steps.
- Supply Chain Efficiency: Optimizing the supply chain can lead to significant cost savings. This includes sourcing materials from cost-effective suppliers, reducing transportation distances, and implementing just-in-time inventory management to minimize warehousing costs and reduce material waste.
- Material Selection: Choosing cost-effective materials without compromising performance is crucial. For example, using a thinner layer of a high-barrier material can reduce the overall material cost compared to using a thicker layer of a less effective barrier material.
- Design for Recyclability: Designing packaging for recyclability can reduce waste disposal costs and potentially provide access to recycled materials, which can be more cost-effective than virgin materials. This involves using mono-material structures and avoiding complex laminates that are difficult to recycle.
- Collaboration with Suppliers: Collaborating with packaging suppliers to leverage their expertise in material science, design, and manufacturing can lead to cost-effective solutions. Suppliers can provide insights into material alternatives, process optimizations, and innovative packaging designs that reduce costs.
By implementing these strategies, businesses can significantly reduce the cost of food film packaging while maintaining the required level of product protection, shelf life, and consumer appeal.
Ending Remarks
So, there you have it. Food film packaging – it’s more than just a wrapper, yeah? It’s about keepin’ food safe, lookin’ after the planet, and makin’ sure your grub gets from the factory to your gob without goin’ off. From the materials to the design, it’s a proper important part of the whole food game. Remember, the choices we make today about packaging are gonna shape the future, innit?