Food grade Teflon tape is a crucial, yet often overlooked, component in ensuring food safety and efficiency across various industries. From bakeries to packaging plants, this specialized tape plays a vital role in preventing contamination and streamlining operations. This exploration dives deep into the world of food grade Teflon tape, uncovering its unique properties, diverse applications, and the essential guidelines for its effective use.
We’ll investigate the materials that set food grade Teflon tape apart, highlighting the certifications and standards it must meet to guarantee safety. Furthermore, we will examine the tape’s remarkable characteristics, including its temperature resistance, non-stick surface, and chemical resilience. Our journey will extend into the food industry, showcasing how this versatile material is used in baking, sealing, and machinery components.
Introduction to Food Grade Teflon Tape
Food grade Teflon tape, also known as PTFE (Polytetrafluoroethylene) tape, is a specialized type of tape designed for use in applications involving direct or indirect contact with food. Its inert and non-reactive properties make it a crucial material for maintaining food safety and preventing contamination. This tape is typically used for sealing, wrapping, and protecting various components within food processing and preparation environments.
Primary Applications of Food Grade Teflon Tape
Food grade Teflon tape serves a multitude of purposes, ensuring food safety and operational efficiency. These applications stem from its unique characteristics.
- Sealing threads on pipes and fittings: Preventing leaks of liquids and gases, which is critical in food processing to maintain hygiene and prevent contamination.
- Wrapping food processing equipment: Protecting surfaces from corrosion and preventing food from sticking.
- Providing a non-stick surface: Facilitating easy cleaning and preventing food buildup on surfaces such as baking sheets and conveyor belts.
- Insulating electrical components: Ensuring safety and preventing electrical hazards in food processing machinery.
Industries Utilizing Food Grade Teflon Tape
Several industries rely heavily on food grade Teflon tape to comply with safety regulations and maintain product quality.
- Food Processing: This includes meat processing, dairy production, bakery operations, and canning facilities.
- Beverage Production: Breweries, wineries, and soft drink manufacturers utilize the tape for sealing and protecting equipment.
- Pharmaceutical Industry: Used in the manufacturing of medications where cleanliness and inertness are paramount.
- Restaurant and Catering: Used in equipment maintenance and food preparation.
- Packaging Industry: Used in sealing and wrapping food packaging.
Key Properties for Food Contact Suitability
Food grade Teflon tape’s suitability for food contact stems from several crucial properties.
- Non-Toxicity: PTFE is inert and does not react with food substances, preventing the leaching of harmful chemicals.
- High Temperature Resistance: It can withstand extreme temperatures, making it suitable for use in ovens, fryers, and other high-heat environments. For example, it can withstand temperatures up to 260°C (500°F) continuously.
- Low Friction: The low friction coefficient prevents food from sticking to surfaces, simplifying cleaning and reducing food waste.
- Chemical Resistance: It is resistant to a wide range of chemicals, ensuring it does not degrade or contaminate food products.
- FDA Compliance: Food grade Teflon tape is manufactured to meet the standards set by the U.S. Food and Drug Administration (FDA) for direct food contact. This ensures its safety and suitability for use in food-related applications.
Materials and Composition
Food grade Teflon tape, essential for sealing in food preparation and handling environments, demands a unique composition and rigorous adherence to safety standards. Unlike standard Teflon tape, its formulation prioritizes the absence of harmful substances that could contaminate food. This section delves into the specific materials, certifications, and manufacturing processes that distinguish food grade Teflon tape.
Materials Used
The primary material in food grade Teflon tape is polytetrafluoroethylene (PTFE). This is the same polymer used in standard Teflon tape, but the critical difference lies in the purity and additives. Food grade tape utilizes only PTFE that meets stringent purity requirements, free from any contaminants or additives that could leach into food.
Certifications and Standards
Food grade Teflon tape must comply with specific certifications and standards to ensure its safety for food contact. These certifications guarantee the tape’s suitability for use in food-related applications.
- FDA Compliance: The U.S. Food and Drug Administration (FDA) sets the standards for materials used in food contact. Food grade Teflon tape must comply with FDA regulations, specifically 21 CFR 177.1550, which addresses PTFE resins and related materials. This regulation specifies the permissible substances and extraction limits.
- Other Certifications: Other relevant certifications might include those from organizations like the NSF International, which tests and certifies products for food safety. NSF certification indicates that the tape has been evaluated and meets specific health and safety requirements.
Manufacturing Process
The manufacturing process of food grade Teflon tape involves several critical steps to ensure food safety. These steps prioritize purity and minimize the risk of contamination.
- Raw Material Selection: The process begins with selecting high-purity PTFE resin. The resin must be sourced from suppliers that adhere to strict quality control measures.
- Extrusion: The PTFE resin is then extruded into a thin tape. This process requires precise temperature control and the use of clean, food-grade equipment.
- Sintering: The extruded tape undergoes sintering, a heating process that fuses the PTFE particles together, giving the tape its strength and durability. This process must be carefully controlled to avoid any degradation of the PTFE.
- Quality Control: Throughout the manufacturing process, rigorous quality control measures are implemented. This includes testing for contaminants, ensuring the tape meets the required physical properties, and verifying compliance with FDA regulations.
- Packaging: The finished tape is packaged in clean, food-grade materials to prevent contamination during storage and transportation.
The entire manufacturing process is designed to minimize the risk of introducing any substances that could compromise the safety of food.
Properties and Characteristics
Food grade Teflon tape possesses unique properties that make it suitable for a wide range of applications in the food processing industry. These characteristics contribute significantly to its effectiveness and safety in direct contact with food products.
Temperature Resistance
Food grade Teflon tape exhibits a broad temperature resistance range, making it adaptable to various cooking and processing methods. This is a crucial factor for its use in diverse food preparation scenarios.The temperature resistance range of food grade Teflon tape typically extends from:
- -268°C (-450°F) to 260°C (500°F).
This wide range allows the tape to withstand both extremely low and high temperatures without degradation or loss of performance. For example, it can be used in cryogenic applications as well as in ovens and on heated surfaces. This thermal stability is a key reason why Teflon tape is preferred in many food processing environments.
Non-Stick Properties
The non-stick nature of food grade Teflon tape is one of its most valuable characteristics, leading to significant benefits in food processing. This property stems from the chemical structure of Teflon, which creates a surface with a very low coefficient of friction.The benefits of the non-stick properties include:
- Reduced food sticking: Prevents food from adhering to surfaces, minimizing waste and simplifying cleaning.
- Easy release: Facilitates the easy release of food products from processing equipment, such as molds, pans, and conveyors.
- Improved efficiency: Reduces downtime for cleaning and maintenance, leading to increased production efficiency.
- Enhanced product quality: Helps maintain the integrity and appearance of food products by preventing damage during processing.
This non-stick surface is particularly useful in applications where food products are prone to sticking, such as baking, grilling, and sealing.
Discover the crucial elements that make chinese food gateway the top choice.
Chemical Resistance
Food grade Teflon tape demonstrates exceptional chemical resistance, making it suitable for use in environments where it may come into contact with various chemicals used in food processing and cleaning. This chemical inertness is a key factor in maintaining the tape’s integrity and preventing contamination of food products.The chemical resistance of food grade Teflon tape can be compared to other materials commonly used in similar applications, such as:
- Stainless Steel: While stainless steel is also resistant to many chemicals, it can be susceptible to corrosion in certain acidic or alkaline environments. Teflon, on the other hand, is virtually unaffected by most acids, bases, and solvents.
- Silicone: Silicone exhibits good temperature resistance and non-stick properties but may be less resistant to certain solvents and chemicals compared to Teflon.
- Polyethylene (PE): PE is a common plastic with good chemical resistance, but it has a lower temperature resistance and may not be suitable for high-temperature applications.
Food grade Teflon tape’s superior chemical resistance ensures its long-term performance and safety in demanding food processing environments.
Applications in the Food Industry
Food grade Teflon tape plays a crucial role in various applications within the food industry due to its inert nature, non-stick properties, and ability to withstand a wide range of temperatures. Its use helps to ensure food safety, improve efficiency, and maintain the quality of food products throughout the manufacturing and preparation processes.
Applications in Baking and Food Preparation
Food grade Teflon tape finds numerous applications in baking and food preparation environments, significantly enhancing efficiency and food safety. Its non-stick surface prevents food from adhering to surfaces, reducing waste and making cleaning easier. The tape’s temperature resistance ensures it remains stable even under high-heat conditions.
Application | Benefit | Example | Notes |
---|---|---|---|
Lining Baking Sheets and Pans | Prevents food from sticking, simplifies removal, and reduces the need for grease. | Used in commercial bakeries to line baking sheets for cookies, pastries, and bread. | This reduces the risk of food tearing or breaking during removal. |
Wrapping Rolling Pins | Provides a non-stick surface for rolling dough, preventing sticking and tearing. | Used by pastry chefs to wrap rolling pins for rolling out fondant, pie crusts, and other doughs. | This makes it easier to handle delicate doughs. |
Sealing Food Packaging | Ensures a tight seal to prevent leaks and maintain freshness. | Used in sealing machines for bags of snacks, frozen foods, and other packaged items. | The tape’s heat resistance is crucial in sealing processes. |
Creating Non-Stick Surfaces for Food Contact | Provides a non-reactive barrier between food and equipment. | Used in conveyor belts, cutting boards, and other food processing surfaces. | This is especially important for acidic foods. |
Applications in Sealing and Packaging Processes
Food grade Teflon tape is extensively used in sealing and packaging processes within the food industry to ensure product integrity and maintain freshness. Its heat resistance and non-stick properties make it ideal for sealing various types of packaging materials, such as plastic films and bags.
- Heat Sealers: Teflon tape is used as a covering for the heating elements in heat sealers. The non-stick surface prevents the packaging material from adhering to the sealing jaws, ensuring a clean and reliable seal. This is crucial for packaging items like chips, snacks, and frozen foods.
- Bag Sealers: In automated bag sealing machines, Teflon tape is often applied to the sealing bars. The tape’s durability and non-stick qualities allow for continuous sealing operations without the packaging material sticking or melting.
- Vacuum Packaging: Used in vacuum sealing machines to create airtight seals. The tape’s ability to withstand high temperatures and pressure is essential for creating effective vacuum seals that extend the shelf life of food products.
Applications in Machinery Components
Food grade Teflon tape is integrated into various machinery components that come into direct contact with food. Its inertness and resistance to chemical reactions make it a safe and effective material for food processing equipment.
- Conveyor Belts: Used to coat conveyor belts in food processing plants. This ensures food products move smoothly without sticking, facilitating efficient processing and reducing the risk of cross-contamination.
- Cutting Surfaces: Applied to cutting surfaces in food processing machines. This creates a non-stick, easy-to-clean surface, which is especially useful for cutting sticky or adhesive foods like candies or cheese.
- Filling Machines: Used in filling machines for liquids and semi-solids. The non-stick properties help to prevent product buildup and ensure accurate dispensing.
Benefits and Advantages
Food grade Teflon tape offers several significant advantages over alternative materials in the food industry, making it a preferred choice for various applications. These benefits range from improved hygiene and operational efficiency to cost savings and enhanced product quality. Its unique properties contribute to its widespread use and effectiveness.
Advantages Over Alternative Materials
Food grade Teflon tape distinguishes itself from other materials commonly used in food processing and handling. The benefits extend beyond just its non-stick properties.
- Superior Non-Stick Surface: Unlike many other materials, Teflon tape provides an exceptionally non-stick surface. This prevents food from adhering to equipment, reducing waste and the need for harsh cleaning chemicals. For example, in baking, this prevents dough from sticking to trays, simplifying removal and reducing product loss.
- Chemical Inertness: Teflon is chemically inert, meaning it does not react with most food products or cleaning agents. This ensures that the tape does not contaminate food or degrade over time, unlike some metals or plastics that can corrode or leach chemicals.
- High-Temperature Resistance: Teflon maintains its properties across a wide temperature range, making it suitable for both high-heat applications (e.g., ovens, grills) and low-temperature environments (e.g., freezers). This versatility is a significant advantage over materials that become brittle or melt at extreme temperatures.
- Low Friction: The low coefficient of friction of Teflon allows for smooth operation of machinery. This reduces wear and tear on equipment, minimizing downtime and maintenance costs. For example, conveyor belts lined with Teflon tape experience less friction, leading to smoother product movement and reduced energy consumption.
- FDA Compliance: Food grade Teflon tape is manufactured to meet stringent FDA (Food and Drug Administration) standards. This ensures its safety for direct food contact, providing assurance to food manufacturers and consumers.
Ease of Cleaning and Maintenance
Food grade Teflon tape significantly simplifies cleaning and maintenance procedures, a critical aspect of food safety and operational efficiency. Its non-stick surface and resistance to chemicals contribute to its ease of care.
- Easy to Clean: The non-stick surface of Teflon tape allows for quick and easy cleaning. Food residue and other contaminants are easily removed with mild detergents and water, unlike materials that require vigorous scrubbing or harsh chemicals.
- Reduced Cleaning Time: The ease of cleaning translates into reduced cleaning time, which is a significant benefit in food processing facilities where time is critical. Less time spent on cleaning increases production time and overall efficiency.
- Resistance to Cleaning Agents: Teflon’s resistance to most cleaning agents means that it can withstand the use of various cleaning chemicals without degrading or being damaged. This ensures thorough sanitation without compromising the tape’s integrity.
- Long Lifespan: When properly maintained, food grade Teflon tape has a long lifespan. Its durability and resistance to wear and tear reduce the need for frequent replacements, leading to cost savings.
Cost-Effectiveness Benefits
The use of food grade Teflon tape results in several cost-effectiveness benefits when compared to alternative materials. These savings stem from reduced waste, lower maintenance costs, and improved operational efficiency.
- Reduced Product Waste: The non-stick properties of Teflon tape minimize food sticking to equipment, which reduces product waste and loss. For instance, in the production of sticky candies, Teflon tape helps prevent the candy from adhering to machinery, leading to higher yields and less product discarded due to sticking.
- Lower Maintenance Costs: The durability and low friction of Teflon tape contribute to lower maintenance costs. Less wear and tear on equipment translates into fewer breakdowns and reduced expenses for repairs and replacements.
- Reduced Downtime: The ease of cleaning and long lifespan of Teflon tape minimize downtime in food processing facilities. This allows for increased production time and higher operational efficiency.
- Energy Savings: The low friction properties of Teflon tape, as seen in conveyor belt applications, can contribute to energy savings. The smoother operation of machinery requires less energy to function.
- Long-Term Durability: While the initial cost might be slightly higher than some alternatives, the long lifespan and durability of Teflon tape make it a cost-effective choice over the long term. It requires less frequent replacement compared to materials that degrade more quickly.
Installation and Usage Guidelines: Food Grade Teflon Tape
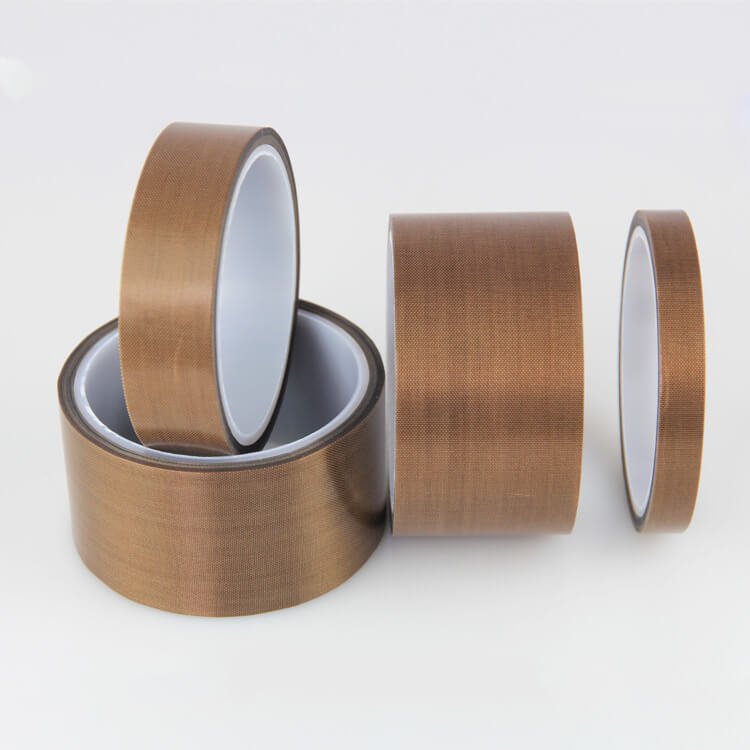
Proper installation and usage of food-grade Teflon tape are crucial for ensuring its effectiveness and preventing contamination. This section provides detailed instructions and recommendations to optimize the tape’s performance and maintain the integrity of food processing equipment.
Step-by-Step Installation for Various Applications
The correct application of food-grade Teflon tape varies depending on the specific use. Following these steps ensures a secure and leak-proof seal, preventing food contamination and equipment malfunction.
- For Pipe Threads:
Clean the pipe threads thoroughly to remove any debris, grease, or old sealant. Start at the beginning of the male thread. Wrap the Teflon tape around the threads, ensuring it lies flat and does not bunch up. Wrap in the direction of the thread, typically clockwise, overlapping each turn by about half the width of the tape. Apply a sufficient amount of tape to create a good seal, usually 2-3 wraps for standard applications.
Cut the tape cleanly and press the end firmly into the threads. Assemble the pipe fitting, tightening it to the manufacturer’s recommended torque.
- For Flange Connections:
Inspect the flange surfaces for any damage or imperfections. Place the Teflon tape around the flange surface, ensuring it covers the entire sealing area. Use a continuous strip of tape or overlap the ends slightly. Align the mating flange and tighten the bolts in a cross-pattern to ensure even pressure. Torque the bolts to the manufacturer’s specifications.
- For Food Processing Equipment:
Disassemble the equipment components that require sealing. Clean the sealing surfaces meticulously. Apply the Teflon tape as directed by the equipment manufacturer, often around threads, joints, or sealing surfaces. Reassemble the equipment, ensuring all components are correctly aligned and tightened according to the manufacturer’s specifications.
Common Mistakes to Avoid During Installation
Avoiding common installation errors is critical to the success of food-grade Teflon tape. Incorrect application can lead to leaks, contamination, and equipment damage.
- Over-tightening Fittings: Over-tightening can damage the Teflon tape, causing it to tear or extrude, leading to leaks. Always use the manufacturer’s recommended torque specifications.
- Using the Wrong Type of Tape: Ensure the tape is specifically food-grade Teflon tape. Other types of Teflon tape may contain additives that are not suitable for food contact.
- Not Cleaning Surfaces: Debris or residue on the sealing surfaces will prevent a proper seal. Always clean the surfaces before applying the tape.
- Wrapping in the Wrong Direction: Wrapping the tape in the wrong direction can cause it to unwind during assembly. Always wrap in the direction of the thread.
- Using Insufficient Tape: Using too little tape may result in an inadequate seal. Ensure sufficient wraps are applied for the application.
Recommended Storage Conditions
Proper storage of food-grade Teflon tape is essential to maintain its quality and prevent degradation. The tape’s performance can be affected by improper storage conditions.
- Temperature: Store the tape in a cool, dry environment, ideally between 10°C and 30°C (50°F and 86°F). Avoid extreme temperatures, which can affect the tape’s adhesive properties and flexibility.
- Humidity: Store the tape in a low-humidity environment to prevent moisture absorption, which can degrade the tape’s performance.
- Direct Sunlight: Protect the tape from direct sunlight, as UV exposure can cause the tape to degrade and become brittle.
- Contamination: Store the tape in its original packaging or a clean, sealed container to prevent contamination from dust, dirt, or other substances.
- Shelf Life: While Teflon tape generally has a long shelf life, it’s best to use the tape within a reasonable timeframe (e.g., 3-5 years) to ensure optimal performance. Check the manufacturer’s recommendations for specific shelf-life guidelines.
Maintenance and Cleaning
Maintaining and cleaning food-grade Teflon tape is crucial for ensuring its longevity and effectiveness in food processing applications. Regular cleaning and inspection practices not only maintain the tape’s performance but also contribute to food safety standards. Proper maintenance helps prevent contamination and ensures the tape continues to meet the stringent requirements of the food industry.
Cleaning Procedures
Cleaning food-grade Teflon tape involves specific methods to remove food residue and maintain its non-stick properties. The cleaning process should be gentle to avoid damaging the tape’s surface.
- Manual Cleaning: For light soiling, manual cleaning is often sufficient. Use a soft cloth or sponge dampened with warm, soapy water. Rinse thoroughly with clean water and allow the tape to air dry or pat it dry with a clean cloth. Avoid using abrasive cleaners or scouring pads, as these can scratch the Teflon surface.
- Mild Detergents: If water alone isn’t enough, a mild detergent specifically designed for food contact surfaces can be used. Dilute the detergent according to the manufacturer’s instructions. After cleaning, rinse the tape meticulously to remove any detergent residue.
- Avoid Harsh Chemicals: Harsh chemicals, solvents, or abrasive cleaners should be strictly avoided, as they can damage the Teflon coating and compromise its food-grade properties. Always refer to the manufacturer’s guidelines for recommended cleaning agents.
- High-Temperature Cleaning: Some food-grade Teflon tapes can withstand high temperatures. In some cases, steam cleaning or washing with hot water may be used, but always check the tape’s specifications to ensure it’s suitable for these methods.
Inspection for Wear and Tear
Regular inspection is essential to identify any signs of damage or wear on food-grade Teflon tape. This allows for timely replacement, preventing potential contamination or equipment malfunction.
- Visual Inspection: Conduct a visual inspection of the tape regularly. Look for signs of scratches, cuts, tears, or any discoloration. These are indicators that the tape may be damaged and could be compromising its functionality.
- Adhesion Testing: Check the tape’s non-stick properties by observing how food or other materials interact with its surface. If food sticks to the tape more than usual, it may indicate degradation of the Teflon coating.
- Thickness Measurement: If possible, measure the tape’s thickness at various points. Significant thinning could indicate wear and tear.
- Edge Examination: Pay close attention to the edges of the tape, as these areas are often more susceptible to damage. Check for fraying, peeling, or any signs of deterioration.
- Replace Damaged Tape: Any tape showing signs of significant damage should be replaced immediately to maintain food safety and prevent equipment issues.
Extending Lifespan Best Practices
Implementing best practices can significantly extend the lifespan of food-grade Teflon tape and minimize replacement frequency.
- Proper Installation: Ensure the tape is installed correctly, following the manufacturer’s instructions. Incorrect installation can lead to premature wear and tear.
- Avoid Sharp Objects: Prevent contact with sharp objects that could scratch or cut the tape’s surface.
- Temperature Control: Operate the tape within its specified temperature range. Excessive heat or cold can damage the Teflon coating.
- Regular Cleaning: Clean the tape regularly, as described above, to remove food residue and prevent buildup.
- Proper Storage: Store unused tape in a clean, dry environment away from direct sunlight and extreme temperatures.
- Prevent Overloading: Avoid overloading equipment that uses Teflon tape, as this can cause excessive stress and wear.
- Use Appropriate Tools: Use only tools and equipment that are compatible with Teflon tape to avoid damage.
- Record Keeping: Maintain a record of the tape’s installation, cleaning, and inspection history to track its performance and identify potential issues.
Sourcing and Purchasing
Finding the right food grade Teflon tape is crucial for ensuring food safety and optimal performance. This section focuses on guiding you through the process of sourcing and purchasing this essential material, covering reputable suppliers, grade comparisons, and application-specific selection.
Identifying Reputable Suppliers of Food Grade Teflon Tape
Choosing a reliable supplier is paramount. This ensures the tape meets the necessary food safety standards and provides consistent quality.
- Reputable Online Retailers: Companies like Amazon often have listings from various suppliers. It is important to check the supplier’s ratings, reviews, and certifications.
- Industrial Supply Companies: These companies specialize in providing materials for various industries, including food processing. They often carry a wide range of Teflon tape products. Examples include Grainger and McMaster-Carr.
- Specialized Sealant and Tape Distributors: These distributors focus specifically on sealants and tapes and often have a deep understanding of the products they offer.
- Manufacturers’ Direct Sales: Purchasing directly from the manufacturer can sometimes offer competitive pricing and direct access to product expertise. Examples include Saint-Gobain and W.L. Gore & Associates.
Comparing the Different Grades and Thicknesses Available for Food Grade Teflon Tape
Food grade Teflon tape comes in various grades and thicknesses, each designed for specific applications. Understanding these differences is essential for selecting the right product.
- Grades:
- Virgin PTFE: This is the purest form of Teflon tape, manufactured from virgin PTFE resin. It is typically the preferred choice for food contact applications due to its high purity and inertness. It is free from additives that could potentially leach into food.
- Filled PTFE: This grade contains fillers such as glass fiber or carbon. While these can improve certain properties, they are less common in food grade applications as the fillers might compromise the inertness.
- Thickness:
- Standard Thicknesses: Common thicknesses range from 0.002 inches (2 mils) to 0.005 inches (5 mils).
- Thicker Tapes: Thicker tapes are used for applications requiring increased durability or to fill larger gaps.
- Choosing the Right Thickness: Consider the application. For example, sealing threads on pipes might require a thinner tape, while sealing larger flanges could benefit from a thicker one.
Providing Guidance on How to Choose the Right Type of Food Grade Teflon Tape for Specific Applications
Selecting the appropriate Teflon tape requires careful consideration of the intended use. Factors such as temperature, pressure, and the type of food product being handled influence the selection process.
- Threaded Connections:
- Application: Sealing threaded pipes and fittings.
- Recommended Type: Virgin PTFE tape in a standard thickness (e.g., 0.003 inches).
- Considerations: Ensure the tape is wrapped correctly to prevent leaks and contamination. Apply the tape in the direction of the threads.
- Flange Seals:
- Application: Sealing flanges in food processing equipment.
- Recommended Type: Virgin PTFE tape, potentially a thicker grade (e.g., 0.004-0.005 inches), or pre-cut gaskets made of food grade PTFE.
- Considerations: The tape must withstand the pressure and temperature of the system.
- Sealing Equipment Components:
- Application: Sealing components in machinery, such as mixers or conveyors.
- Recommended Type: Virgin PTFE tape, selected based on the specific needs of the equipment.
- Considerations: Assess the type of food product, temperature, and pressure. Regular inspections are crucial.
Alternatives to Food Grade Teflon Tape
Food grade Teflon tape is a valuable material in the food industry, but it’s not the only option. Understanding the alternatives, their properties, and their suitability for various applications is crucial for making informed decisions about sealing and insulation. This section explores materials that compete with Teflon tape, examining their advantages and disadvantages in the context of food safety and performance.
Alternative Materials Comparison
Several materials are used in food processing and handling as alternatives to food grade Teflon tape. Each material has its own strengths and weaknesses, impacting its suitability for specific applications.
- Silicone Tape: Silicone tape is another popular option, known for its flexibility and resistance to high temperatures. It is often used for sealing and insulating applications.
- PTFE (Polytetrafluoroethylene) Tape (Non-Food Grade): While food grade Teflon tape is made from PTFE, the non-food grade version may contain additives that are not suitable for food contact. This tape is generally less expensive but poses a risk of contamination in food processing environments.
- EPDM Rubber Tape: EPDM (Ethylene Propylene Diene Monomer) rubber tape offers excellent resistance to weather, ozone, and UV radiation, and is also food grade.
- Viton® (Fluorocarbon Rubber) Tape: Viton® tape is a high-performance synthetic rubber known for its exceptional resistance to chemicals, heat, and solvents. It is often used in demanding environments.
- Fiberglass Tape: Fiberglass tape provides excellent thermal insulation and is often used in high-temperature applications, though it may not be suitable for direct food contact without proper coating.
Pros and Cons of Alternatives
The choice of material depends on the specific application requirements. Here’s a breakdown of the advantages and disadvantages of each alternative:
- Silicone Tape:
- Pros: Flexible, heat-resistant, and generally considered food-safe. It can also be easily applied to various surfaces.
- Cons: May be less resistant to certain chemicals than Teflon and can be more prone to tearing or damage.
- PTFE Tape (Non-Food Grade):
- Pros: Typically less expensive than food grade Teflon tape.
- Cons: May contain additives that are not food-safe and could contaminate food products. It’s crucial to avoid this for any food contact applications.
- EPDM Rubber Tape:
- Pros: Food-grade, excellent resistance to weather and ozone, and suitable for outdoor applications.
- Cons: Not as heat-resistant as Teflon, and may not be suitable for applications involving aggressive chemicals.
- Viton® Tape:
- Pros: Excellent resistance to chemicals and high temperatures.
- Cons: Can be more expensive than other alternatives, and may not be necessary for all applications.
- Fiberglass Tape:
- Pros: Provides excellent thermal insulation and is cost-effective for many high-temperature scenarios.
- Cons: Not typically food-safe without special coatings, and can be abrasive.
Preferred Materials for Specific Scenarios
The selection of an alternative to food grade Teflon tape hinges on the specific operational needs. Several scenarios highlight when alternative materials might be preferred:
- High-Temperature Applications: In situations where extremely high temperatures are involved, such as sealing ovens or industrial cooking equipment, Viton® tape might be preferred due to its superior heat resistance compared to silicone or EPDM.
- Chemical Exposure: For applications involving exposure to aggressive chemicals, such as in cleaning processes, Viton® tape’s chemical resistance makes it a more suitable choice than Teflon tape.
- Outdoor Use: EPDM rubber tape would be favored for outdoor applications due to its resistance to UV radiation and weather elements, which are properties not as strongly associated with Teflon.
- Cost Sensitivity: If cost is a primary concern and the application doesn’t require the specific properties of food grade Teflon tape, non-food grade PTFE tape (with careful consideration of potential contamination) or even silicone tape could be considered, although this must be weighed against the potential risks to food safety.
Troubleshooting and Common Issues
Food grade Teflon tape, while highly effective, is not immune to problems. Understanding common issues and how to resolve them is crucial for ensuring its optimal performance and longevity in food processing applications. This section addresses the most frequently encountered challenges and provides practical solutions.
Improper Sealing
Improper sealing is a common issue that can lead to leaks and contamination. This can be caused by several factors.
- Incorrect Application: Applying the tape incorrectly, such as wrapping it in the wrong direction or with insufficient overlap, can create gaps.
- Damaged Tape: Using damaged or torn tape compromises the seal.
- Incompatible Surfaces: Using Teflon tape on surfaces that are not smooth or clean can prevent a proper seal.
- Over-tightening or Under-tightening: Excessive or insufficient tightening of fittings can also lead to leaks.
To address these issues:
- Re-apply the Tape: Remove the old tape and reapply, ensuring the correct wrapping direction (typically clockwise for right-handed threads) and sufficient overlap (usually covering the threads completely).
- Inspect the Tape: Always use fresh, undamaged tape. Discard any tape that appears torn, creased, or contaminated.
- Prepare Surfaces: Clean and ensure that the threaded surfaces are smooth and free of debris or burrs.
- Tighten Appropriately: Tighten fittings to the manufacturer’s recommended torque specifications. Avoid over-tightening, which can damage the tape and the fitting.
Tape Degradation
Teflon tape can degrade over time, especially under high temperatures, pressure, or exposure to certain chemicals.
- Temperature Extremes: Exposing the tape to temperatures beyond its operating range can cause it to become brittle or lose its sealing properties.
- Chemical Exposure: Certain chemicals can react with the tape, causing it to break down.
- Mechanical Stress: Constant vibration or movement can wear down the tape, leading to leaks.
To mitigate tape degradation:
- Check Temperature Ratings: Ensure the tape is rated for the operating temperature of the application.
- Chemical Compatibility: Verify the tape’s compatibility with the chemicals it will be exposed to. Consult the manufacturer’s guidelines.
- Reduce Vibration: If possible, minimize vibration or movement in the system. Consider using vibration-dampening techniques.
- Regular Inspections: Inspect the tape regularly for signs of degradation, such as cracking, brittleness, or discoloration. Replace the tape if necessary.
Contamination Concerns
While food grade Teflon tape is designed to be inert, improper handling or installation can introduce contamination risks.
- Cross-Contamination: Using non-food grade tape or contaminating the tape during installation can introduce unwanted substances into the food stream.
- Particulate Matter: Tape fragments or particles can detach and contaminate the product if the tape is improperly installed or degraded.
To prevent contamination:
- Use Food Grade Tape: Always use food grade Teflon tape specifically designed for food contact applications.
- Maintain Cleanliness: Handle the tape with clean hands and tools. Avoid contamination from grease, oil, or other substances.
- Proper Installation: Ensure proper installation to prevent tape fragments from entering the system.
- Regular Inspections: Regularly inspect the tape for signs of degradation or damage that could lead to particle release.
Difficult Removal
Removing Teflon tape can sometimes be challenging, especially if it has been exposed to high temperatures or has been in place for an extended period.
- Adhesion: The tape can become tightly adhered to the threads over time.
- Breaking: The tape may tear during removal, leaving fragments behind.
To facilitate removal:
- Use Appropriate Tools: Use a pick or small screwdriver to gently lift and remove the tape.
- Heat Application (Carefully): In some cases, gently heating the fitting can soften the tape and make it easier to remove. Avoid excessive heat.
- Thorough Cleaning: After removing the tape, thoroughly clean the threads to remove any remaining residue.
Frequently Asked Questions
This section addresses common questions related to food grade Teflon tape.
- What is the correct way to wrap Teflon tape? The tape should be wrapped around the male threads in the direction of the thread (typically clockwise for right-handed threads), starting from the end of the thread and overlapping the tape slightly with each wrap. Ensure the tape covers the threads completely.
- How much Teflon tape should I use? The amount of tape needed depends on the size of the fitting and the application. Generally, 2-3 wraps are sufficient. Too much tape can cause the fitting to crack.
- Can I use Teflon tape on gas lines? Yes, but only use a yellow, gas-rated Teflon tape, specifically designed for gas applications. Food grade tape is not appropriate for gas lines.
- Can I reuse Teflon tape? No, Teflon tape is a single-use product. Reusing tape can compromise the seal and lead to leaks.
- How do I store Teflon tape? Store Teflon tape in a cool, dry place, away from direct sunlight and chemicals.
- What is the shelf life of Teflon tape? Teflon tape has a long shelf life if stored properly. However, it’s best to use fresh tape for optimal sealing performance.
- What should I do if I accidentally use the wrong type of Teflon tape? If you’ve used the wrong type of tape (e.g., non-food grade tape in a food application), remove it immediately and replace it with the correct food grade tape. Ensure the system is thoroughly cleaned before resuming use.
- What are the signs of a bad seal? Signs of a bad seal include leaks, pressure drops, and the presence of liquid or gas around the fitting.
- What should I do if my fitting leaks? If your fitting leaks, first tighten the fitting slightly. If the leak persists, disassemble the fitting, remove the old tape, reapply fresh Teflon tape, and reassemble the fitting, ensuring it is properly tightened.
- Can Teflon tape be used with all types of fluids? While Teflon tape is generally inert, its compatibility with fluids should be checked. Refer to the manufacturer’s guidelines for specific fluid compatibility information.
Future Trends and Innovations
The food industry is constantly evolving, and with it, the technologies used to ensure food safety and efficiency. Food-grade Teflon tape is no exception. Ongoing research and development promise to further enhance its capabilities and broaden its applications, offering new solutions for food processing and handling. These advancements are driven by the need for greater hygiene, improved performance, and sustainable practices within the industry.
Enhanced Materials and Formulations
Future innovations will likely focus on improving the base materials and formulations of food-grade Teflon tape. This includes exploring new polymers and additives to enhance specific properties.
- Improved Non-Stick Properties: Research into new fluoropolymers and surface treatments aims to create tapes with even greater non-stick capabilities. This would minimize food residue buildup and facilitate easier cleaning, contributing to enhanced hygiene. The development of nano-coatings on the tape surface could further enhance these properties, making it even more resistant to sticking and easier to clean.
- Increased Durability and Longevity: Scientists are working on strengthening the physical properties of Teflon tape, making it more resistant to wear and tear, temperature fluctuations, and chemical exposure. This would lead to longer lifespans for the tape, reducing the need for frequent replacements and minimizing waste. This involves research into reinforced Teflon tape with added materials to improve tear resistance and overall durability.
- Enhanced Chemical Resistance: Food processing often involves exposure to a wide range of chemicals, including cleaning agents and food ingredients. Future Teflon tapes may be designed with improved resistance to these substances, ensuring their integrity and preventing any potential contamination. This includes developing tapes that are resistant to harsh cleaning solutions and various food acids.
- Biodegradable and Sustainable Options: There is a growing trend towards sustainable practices in the food industry. Research is underway to develop biodegradable or bio-based alternatives to traditional Teflon tape. This would reduce the environmental impact of the product and align with the industry’s commitment to sustainability. The use of bio-based polymers, derived from renewable resources, is a key area of exploration.
Smart and Intelligent Teflon Tape
The integration of smart technologies could revolutionize the way food-grade Teflon tape is used.
- Sensors for Monitoring: Future Teflon tape could incorporate sensors to monitor temperature, pressure, and the presence of contaminants. This would provide real-time data on the conditions within food processing equipment, enabling proactive maintenance and preventing potential food safety hazards. These sensors could detect leaks or contamination early, allowing for immediate corrective action.
- Self-Cleaning Capabilities: Researchers are exploring self-cleaning Teflon tape that utilizes innovative surface treatments or coatings to repel food particles and automatically clean itself. This would significantly reduce the need for manual cleaning and further enhance hygiene standards. This could involve the use of photocatalytic coatings that break down organic matter when exposed to light.
- Traceability and Authentication: Smart Teflon tape could incorporate technologies such as RFID tags or QR codes to enable traceability of the tape throughout the food processing chain. This would help ensure that the tape is authentic and compliant with food safety regulations. This would provide information on the manufacturing date, batch number, and any relevant certifications.
Emerging Applications of Food Grade Teflon Tape
The unique properties of food-grade Teflon tape are opening up new avenues for its application within the food industry.
- 3D Printing of Food: The development of 3D food printing technology presents a new opportunity for Teflon tape. It can be used as a printing surface to ensure the food product does not stick and can be easily removed. This application would also require the tape to withstand high temperatures and provide excellent non-stick properties.
- Advanced Packaging Solutions: Teflon tape can be used in the sealing of food packaging, especially for products requiring airtight seals or high-temperature processing. This includes applications in modified atmosphere packaging (MAP) and retort packaging, where maintaining the integrity of the seal is critical for food safety and shelf life.
- Specialized Baking Applications: The use of Teflon tape in baking continues to evolve, with new applications emerging. This includes its use in baking molds, conveyor belts, and other surfaces where non-stick properties are essential for efficient and hygienic food production. This is crucial in industries like bakery and confectionery where products are prone to sticking.
- Robotics in Food Processing: As automation increases in the food industry, Teflon tape will play a role in robotic systems used for food handling and processing. The tape’s non-stick properties and resistance to chemicals make it suitable for use in grippers, conveyors, and other robotic components that come into contact with food. This is especially relevant in high-volume food production facilities.
Wrap-Up
In conclusion, food grade Teflon tape stands as a testament to innovation in food processing, offering a blend of safety, efficiency, and durability. Understanding its composition, applications, and proper usage is paramount for anyone involved in the food industry. As technology advances, the future of food grade Teflon tape promises even greater advancements, ensuring safer and more efficient food production processes.
Embracing this knowledge is not just about adhering to regulations; it’s about fostering a commitment to excellence in the food industry.