Food grade wood filler, a humble yet potent tool, invites us to consider the essence of restoration and renewal. Just as we seek to mend and nourish our bodies with wholesome foods, so too must we approach the surfaces that come into contact with our sustenance. This exploration transcends mere carpentry; it’s a journey of mindful practice, where each application becomes a step towards creating a space that reflects purity and intention.
Imagine the wood as a vessel, holding the potential for connection and nourishment. Food grade wood filler becomes a conduit, bridging gaps and smoothing imperfections. It is about more than just filling cracks; it’s about honoring the wood’s inherent beauty and purpose, much like we honor the divine spark within ourselves. As we delve into its applications, materials, and techniques, we’ll discover how to cultivate a space of safety and harmony, where every touch point contributes to the overall well-being.
Defining Food Grade Wood Filler
Food grade wood filler is a specialized product designed for use in direct or indirect contact with food. Its primary function is to repair or fill imperfections in wooden surfaces that will come into contact with food, ensuring the safety and hygiene of the food supply. The definition extends beyond mere suitability; it involves adhering to strict regulations and using specific materials to prevent contamination and maintain food safety standards.
Components of Food-Grade Wood Filler
The composition of food-grade wood filler is carefully controlled to minimize the risk of harmful substances leaching into food. The materials are selected for their inertness and non-toxicity.
- Binders: These substances hold the filler together and allow it to adhere to the wood. Common binders include:
- Epoxy Resins: Often used for their strong adhesion and resistance to moisture and chemicals. Food-grade epoxy resins are specifically formulated to be non-reactive and to meet the requirements of food safety regulations. An example of a specific formulation might include a resin based on bisphenol A diglycidyl ether (BADGE) but with a low migration rate.
- Polyurethane Resins: Offer flexibility and durability, suitable for applications where the wood may experience movement. These are chosen for their resistance to solvents and ability to form a seamless bond.
- Fillers: Fillers add bulk, improve workability, and reduce shrinkage. These are usually inert materials. Common fillers are:
- Calcium Carbonate: A widely used filler, providing good filling properties and is generally considered safe for food contact.
- Talc: A mineral filler that enhances the filler’s workability and reduces cracking.
- Wood Flour: Finely ground wood particles can be used to match the original wood’s appearance, provided the source wood is also food-safe.
- Curing Agents/Hardener: These components initiate the chemical reaction that causes the filler to harden. Curing agents must also be food-safe. Examples include:
- Amine Hardeners: Certain amine-based hardeners are used, specifically those formulated for food contact applications, ensuring they do not release harmful compounds.
- Polyamide Hardeners: Another type of hardener, selected for their flexibility and chemical resistance, which are compatible with food safety standards.
- Additives: Small amounts of additives can be included to modify the filler’s properties. Additives include:
- Pigments: Used to match the color of the wood. Only food-safe pigments are allowed. For example, titanium dioxide (TiO2) is a common white pigment used, provided it meets purity standards.
- Thickeners: To adjust viscosity for better application.
- Anti-sag agents: To prevent the filler from running or dripping during application.
Regulations and Standards Governing Food-Grade Wood Filler
The production and use of food-grade wood filler are subject to rigorous regulations and standards established by various governmental and international bodies to ensure consumer safety. These standards define the acceptable materials, manufacturing processes, and testing procedures.
- U.S. Food and Drug Administration (FDA): The FDA plays a crucial role in regulating food-grade materials in the United States.
- 21 CFR Part 175.300: This regulation Artikels the requirements for resinous and polymeric coatings used as food contact surfaces. Wood filler that comes into contact with food must comply with this regulation. Compliance often involves detailed testing and documentation.
- Indirect Food Additives: The FDA also regulates indirect food additives, including substances that may migrate from food contact materials into food. Wood filler components must meet the requirements for indirect food additives.
- European Union (EU) Regulations: The EU has its own set of regulations for materials intended for food contact.
- Regulation (EC) No 1935/2004: This framework regulation sets out the general principles for all food contact materials, including wood filler. It mandates that materials must not transfer their constituents to food in quantities that could endanger human health or change the food’s composition, taste, or odor.
- Specific Measures: The EU also has specific measures for certain materials, which might include detailed requirements for epoxy resins and other components.
- Testing and Certification: Compliance often involves third-party testing and certification.
- Migration Testing: This is a crucial test to determine the extent to which substances from the wood filler migrate into food. Tests simulate the conditions of food contact, such as temperature and the types of food.
- Material Safety Data Sheets (MSDS): Manufacturers must provide MSDS detailing the composition of the filler and any potential hazards.
- Certifications: Certifications from organizations like NSF International (formerly the National Sanitation Foundation) provide assurance that a product meets specific standards for food safety. For example, NSF/ANSI/CAN 51 sets requirements for food equipment materials.
Applications of Food Grade Wood Filler
Food-grade wood filler plays a crucial role in maintaining the safety and integrity of food preparation and service environments. Its use extends from repairing damaged surfaces to restoring the aesthetic appeal of wooden elements. This ensures compliance with health regulations and promotes a clean and hygienic atmosphere.
Common Applications in Food Environments
Food-grade wood filler finds extensive application in a variety of settings where food is handled, prepared, or served. Its versatility allows for effective repairs and restorations while adhering to strict food safety standards.
- Repairing Wooden Cutting Boards: Food-grade wood filler can be used to fill cracks, chips, and gouges on wooden cutting boards, extending their lifespan and preventing the accumulation of food particles and bacteria. This application is critical for maintaining hygiene and preventing cross-contamination.
- Restoring Wooden Serving Utensils: Wooden spoons, spatulas, and other serving utensils often develop cracks or splinters over time. Food-grade wood filler can be used to repair these imperfections, ensuring the utensils remain safe for food contact and preventing potential hazards.
- Sealing Wooden Butcher Blocks: Butcher blocks used for meat preparation are susceptible to damage and wear. Sealing cracks and crevices with food-grade wood filler prevents the absorption of liquids and bacteria, maintaining a sanitary surface.
- Repairing Wooden Tables and Counters: In restaurants and food service areas, wooden tables and counters can experience scratches, dents, and other forms of damage. Food-grade wood filler can be used to restore these surfaces, ensuring they are safe for food contact and meet aesthetic standards.
- Fixing Wooden Storage Containers: Wooden storage containers, such as those used for dry goods, can develop cracks or gaps. Food-grade wood filler provides a safe and effective solution for sealing these imperfections, preventing contamination and maintaining the integrity of stored food items.
Scenarios for Repair and Restoration
Food-grade wood filler is invaluable in various repair and restoration scenarios, providing practical solutions for maintaining the functionality and safety of wooden elements in food environments. These scenarios highlight the versatility and importance of this product.
- Restoring Antique Kitchenware: Antique wooden kitchenware, such as bowls and utensils, can be restored using food-grade wood filler. This allows for the preservation of valuable items while ensuring they are safe for food use.
- Repairing Damage from Accidental Impacts: Accidents happen, and wooden surfaces can suffer from dents, scratches, and chips. Food-grade wood filler provides a quick and effective way to repair this damage, preventing further deterioration and maintaining a clean appearance.
- Addressing Wear and Tear Over Time: Regular use leads to wear and tear on wooden surfaces. Food-grade wood filler helps to address this by filling in imperfections and restoring the original condition of the wood, prolonging its lifespan.
- Correcting Imperfections in Newly Constructed Items: Even new wooden items may have minor imperfections. Food-grade wood filler can be used to correct these, ensuring a smooth and sanitary surface from the start.
- Sealing Against Moisture and Bacteria: In environments where moisture and bacteria are a concern, food-grade wood filler provides a barrier that helps to prevent the growth of harmful organisms, safeguarding food safety.
Selecting the Correct Food-Grade Wood Filler
Choosing the appropriate food-grade wood filler is essential for achieving optimal results and maintaining food safety standards. Several factors should be considered when making a selection. The following table provides guidance on selecting the correct filler for specific applications.
Application | Considerations | Recommended Filler Type | Example |
---|---|---|---|
Cutting Boards | Must withstand frequent washing, resist moisture, and be non-toxic. | Epoxy-based, food-safe | A two-part epoxy wood filler specifically formulated for food contact surfaces. |
Serving Utensils | Requires a smooth, non-porous finish and must be safe for direct food contact. | Polyurethane-based, food-safe | A single-component polyurethane wood filler that dries quickly and provides a durable surface. |
Butcher Blocks | Must resist moisture, be easy to clean, and prevent bacterial growth. | Epoxy-based, food-safe | A clear epoxy filler that can be sanded and finished to match the surrounding wood. |
Tables and Counters | Should be durable, resistant to scratches and spills, and easy to maintain. | Acrylic-based, food-safe | An acrylic wood filler that can be tinted to match the existing wood color and provides a hard, durable finish. |
Storage Containers | Needs to seal cracks and gaps effectively, prevent contamination, and be non-toxic. | Epoxy-based or Polyurethane-based, food-safe | A food-grade epoxy or polyurethane filler suitable for sealing cracks and providing a smooth, sanitary surface. |
Materials and Composition
Understanding the materials and composition of food-grade wood filler is crucial for ensuring its safety and effectiveness in applications where it comes into contact with food. The selection of ingredients directly impacts the filler’s performance, its ability to resist moisture and degradation, and most importantly, its compliance with food safety regulations. This section delves into the specific materials used, the different types available, and the critical importance of choosing fillers free from harmful substances.
Components of Food-Grade Wood Fillers
Food-grade wood fillers are formulated with specific materials to meet stringent safety standards. These materials are carefully chosen to minimize the risk of contamination and ensure the filler’s suitability for use in food-related environments. The composition typically includes resins, binders, and various additives.
- Resins: These form the primary binding matrix of the filler. Common resins include:
- Epoxy Resins: Epoxy resins are known for their excellent adhesion, strength, and resistance to chemicals and moisture. Food-grade epoxy resins are often used because of their durability and ability to create a non-porous surface, which is essential for preventing the growth of bacteria. They are usually formulated with specific hardeners that are also food-safe.
An example is the use of epoxy in the repair of wooden cutting boards or butcher blocks.
- Water-Based Resins: Water-based resins, often acrylic or vinyl-acrylic based, offer a lower-odor and lower-VOC (Volatile Organic Compound) alternative. These resins are preferred for their ease of use and environmental friendliness. They typically dry quickly and are suitable for use in environments with moderate moisture exposure. An example is the use of water-based fillers for repairing wooden food storage containers.
- Epoxy Resins: Epoxy resins are known for their excellent adhesion, strength, and resistance to chemicals and moisture. Food-grade epoxy resins are often used because of their durability and ability to create a non-porous surface, which is essential for preventing the growth of bacteria. They are usually formulated with specific hardeners that are also food-safe.
- Binders: Binders help to hold the filler together and provide structural integrity. These materials can vary depending on the type of resin used. For epoxy-based fillers, the binder is often part of the epoxy resin system. For water-based fillers, the binder is often the same as the resin itself, acting as a cohesive agent.
- Additives: Additives are incorporated to enhance specific properties. These include:
- Fillers: Inert materials, such as wood flour or calcium carbonate, are added to increase the volume of the filler and improve its sanding properties. The choice of filler is crucial to ensure it doesn’t leach any harmful substances into the food.
- Pigments: Food-grade pigments can be added to achieve the desired color. These pigments must be non-toxic and comply with food safety regulations.
- Thickeners: Thickeners are used to adjust the viscosity of the filler, making it easier to apply.
- Preservatives: Preservatives are added to prevent the growth of mold and mildew, especially in water-based fillers. These must be food-safe.
Types of Food-Grade Wood Fillers, Food grade wood filler
The choice of food-grade wood filler depends on the specific application, the type of wood, and the desired characteristics. Each type of filler has unique properties that make it suitable for different purposes.
- Epoxy-Based Fillers: Epoxy fillers offer excellent durability, chemical resistance, and water resistance. They are ideal for applications that require a strong, long-lasting repair, such as repairing cracks in butcher blocks or sealing joints in food-processing equipment. These fillers typically consist of two parts: a resin and a hardener, which are mixed together to initiate the curing process. The curing time and final hardness can vary depending on the specific formulation.
- Water-Based Fillers: Water-based fillers are a more environmentally friendly option with lower VOC emissions. They are easy to clean up with water and typically have a lower odor. These fillers are suitable for less demanding applications, such as filling small imperfections in wooden food storage containers or repairing furniture used in dining areas. They generally dry faster than epoxy fillers, but may not be as resistant to moisture and chemicals.
Importance of Selecting Safe Fillers
The selection of a food-grade wood filler that is free of harmful chemicals and solvents is paramount to maintaining food safety. The potential for contamination can have serious consequences.
- Harmful Chemicals and Solvents: Many conventional wood fillers contain volatile organic compounds (VOCs), solvents, and other chemicals that can leach into food and pose health risks. These substances can contaminate food, leading to potential allergic reactions or long-term health problems.
- Regulatory Compliance: Food-grade fillers must comply with regulations set by organizations like the FDA (Food and Drug Administration) in the United States, or similar agencies in other countries. These regulations specify which materials are permissible for use in food contact applications and set limits on the levels of any potentially harmful substances.
- Certification and Testing: Look for fillers that have been tested and certified by independent laboratories to ensure they meet food safety standards. Certifications, such as those from NSF International (National Sanitation Foundation), indicate that the filler has been evaluated and meets specific criteria for food contact.
- Examples of Harmful Substances to Avoid: Fillers should be free of solvents like toluene and xylene, which are known irritants and potential carcinogens. They should also be free of phthalates, which are plasticizers that can leach out of materials and have been linked to various health issues.
Surface Preparation and Application
Proper surface preparation and application are critical to the performance and longevity of food-grade wood filler. This section provides a detailed guide on preparing wood surfaces and applying the filler to achieve a smooth, food-safe finish. Following these steps ensures the filler adheres correctly, resists degradation, and maintains its integrity in a food-contact environment.
Preparing Wood Surfaces
Thorough surface preparation is essential for the successful application of food-grade wood filler. It ensures optimal adhesion and a durable finish. The following steps detail the necessary procedures:Before applying food-grade wood filler, it is important to assess the existing wood condition. This involves identifying any issues such as rot, insect damage, or existing coatings that may need removal.
- Cleaning the Surface: Begin by thoroughly cleaning the wood surface. Remove any dust, dirt, grease, or loose particles. Use a vacuum cleaner with a brush attachment to remove dust from cracks and crevices. For grease or oil, use a mild detergent and water solution, ensuring to rinse thoroughly and allow the wood to dry completely.
- Sanding the Wood: Sand the wood surface to create a smooth and slightly rough texture. This enhances the adhesion of the wood filler. Use sandpaper of progressively finer grits, starting with a coarser grit (e.g., 80-grit) to remove imperfections and then moving to a finer grit (e.g., 120- or 150-grit) for a smooth finish. Ensure the surface is even and free of splinters.
- Removing Old Finishes (if applicable): If the wood has an existing finish (paint, varnish, etc.), it must be removed before applying the filler. Use appropriate methods like chemical strippers, heat guns, or sanding. Always follow the manufacturer’s instructions for any chemical products, and ensure proper ventilation and safety precautions.
- Repairing Damaged Areas: Address any significant damage to the wood, such as deep cracks or missing pieces, before applying the filler. Consider using wood shims or epoxy fillers for structural repairs, depending on the severity of the damage.
- Drying the Wood: Ensure the wood is completely dry before applying the filler. Moisture can prevent proper adhesion and lead to issues such as cracking or bubbling. Allow ample drying time, especially after cleaning or removing finishes.
Applying Food-Grade Wood Filler
The application of food-grade wood filler requires precision to ensure a seamless and food-safe result. This section Artikels a step-by-step guide to the application process, from mixing to curing.The correct application of food-grade wood filler involves a careful mixing process and precise application techniques. The following steps should be followed to ensure optimal results.
- Mixing the Filler: Carefully follow the manufacturer’s instructions for mixing the food-grade wood filler. Generally, this involves combining the filler with a hardener or catalyst in the specified ratio. Use a clean mixing container and a mixing stick. Mix thoroughly until the mixture is homogenous, ensuring no lumps remain. Pay attention to the pot life (the time the filler remains workable) and mix only the amount that can be applied within that timeframe.
- Applying the Filler: Use a putty knife or a similar tool to apply the filler to the prepared wood surface. Apply the filler in thin layers, pressing it firmly into the cracks, holes, or imperfections. Overfilling can lead to difficulty in sanding.
- Leveling the Filler: Once the filler is applied, use the putty knife to level it with the surrounding wood surface. Scrape the excess filler to create a smooth, even finish. This step is crucial for minimizing the sanding required later.
- Drying and Curing: Allow the filler to dry and cure completely according to the manufacturer’s instructions. The curing time depends on the specific product and environmental conditions (temperature, humidity). Avoid disturbing the filled areas during the curing process.
- Sanding the Filled Area: After the filler has completely cured, sand the filled area to achieve a smooth and even surface. Start with a medium-grit sandpaper (e.g., 150-grit) to remove any imperfections and level the filler with the surrounding wood. Progress to finer grits (e.g., 220-grit or higher) to achieve a smooth finish.
- Cleaning the Surface After Sanding: After sanding, remove all sanding dust from the surface. Use a vacuum cleaner, tack cloth, or a slightly damp cloth to ensure the surface is clean before applying any finish.
Achieving a Smooth, Food-Safe Surface
The final step is to ensure that the finished surface is smooth and food-safe. This involves using the correct techniques and materials to achieve the desired outcome.Several techniques are employed to achieve a smooth and food-safe surface. These methods enhance the overall quality and safety of the finished product.
- Using High-Quality Fillers: Select food-grade wood fillers specifically designed for food contact. These fillers are formulated to be non-toxic, resistant to moisture, and compliant with relevant food safety regulations.
- Proper Sanding Techniques: Employ proper sanding techniques to create a smooth surface. Use progressively finer grits of sandpaper, ensuring each pass removes any imperfections left by the previous grit. Apply even pressure and avoid sanding in one spot for too long.
- Avoiding Pores and Cracks: Ensure the filled areas are free of pores and cracks. Multiple thin layers of filler, with sanding in between, may be necessary to achieve a perfectly smooth surface.
- Applying Food-Safe Finishes: Apply food-safe finishes, such as food-grade oils, waxes, or varnishes, to protect the filler and wood from moisture and contaminants. These finishes create a barrier that prevents the filler from direct contact with food. Follow the manufacturer’s instructions for application and curing.
- Regular Maintenance and Inspection: Regularly inspect the filled areas for any signs of wear or damage. Clean the surface regularly with appropriate food-safe cleaners. Reapply finishes as needed to maintain the protective barrier.
Curing and Finishing
The final steps in working with food-grade wood filler are crucial for ensuring its durability, food safety, and aesthetic appeal. Proper curing, sanding, and finishing are essential to create a surface that is both functional and compliant with food safety standards. These processes directly impact the longevity and usability of the filled wood, making them a critical aspect of the overall application.
Curing Process
The curing process is the chemical reaction that hardens the wood filler. Understanding the factors influencing this process is vital for achieving optimal results.The curing time for food-grade wood filler varies depending on the specific product and environmental conditions. Generally, the curing time is indicated on the product packaging. However, several factors influence this time frame:
- Temperature: Higher temperatures generally accelerate the curing process, while lower temperatures slow it down. A common range for optimal curing is between 65°F (18°C) and 75°F (24°C). At temperatures below 50°F (10°C), the curing process can be significantly delayed or even halted. Conversely, excessively high temperatures can cause the filler to cure too quickly, potentially leading to cracking or other defects.
- Humidity: Humidity can also affect the curing process. High humidity levels can sometimes slow down the curing process, especially for water-based fillers, as the water evaporates more slowly. Conversely, extremely low humidity can lead to premature drying of the surface, potentially affecting the filler’s ability to bond properly.
- Ventilation: Adequate ventilation is important, particularly for solvent-based fillers, as it helps to remove solvents and promote proper curing. Good air circulation can also help to regulate temperature and humidity.
- Filler Thickness: The thickness of the filler application impacts curing time. Thicker applications will naturally require more time to cure completely than thinner ones.
It’s crucial to consult the manufacturer’s instructions for the specific filler being used, as these will provide the most accurate guidelines for curing time and environmental considerations. Allow sufficient time for complete curing before proceeding with sanding or finishing. This prevents issues like the filler being soft or not fully bonded.
Sanding and Finishing
Sanding and finishing are the processes that refine the filled surface, creating a smooth and food-safe final product.Before sanding, the filler must be fully cured. Use the following steps to achieve a desirable finish:
- Sanding: Begin with a medium-grit sandpaper (e.g., 120-grit) to remove any excess filler and level the surface. Progress through finer grits (e.g., 180-grit, 220-grit) to achieve a smooth finish. Sand in the direction of the wood grain to minimize scratches. Use a sanding block to ensure an even surface.
- Dust Removal: Thoroughly remove all sanding dust with a vacuum cleaner, tack cloth, or compressed air. Residual dust can interfere with the application of any subsequent finish.
- Inspection: Carefully inspect the sanded surface for any imperfections, such as pinholes or uneven areas. If necessary, apply a small amount of filler to these areas and repeat the sanding process once it is cured.
The finishing process involves applying a protective sealant or coating. The choice of finish depends on the application and desired aesthetic.
Applying Protective Sealant or Coating
Applying a food-safe sealant or coating is an important step to provide a durable, food-safe, and aesthetically pleasing surface.The choice of sealant depends on the specific application and desired finish. Options include:
- Food-Grade Oil: Natural oils like mineral oil or walnut oil are often used. These oils penetrate the wood, providing a water-resistant barrier. Reapplication is typically needed periodically.
- Food-Safe Varnish or Lacquer: These finishes create a hard, protective layer on the surface. Ensure the product is specifically labeled as food-safe.
- Food-Grade Epoxy Resin: Epoxy resins can provide a very durable and waterproof surface. They are often used for butcher blocks and countertops.
The application process typically involves the following steps:
- Surface Preparation: Ensure the sanded surface is clean and free of dust.
- Application: Apply the sealant or coating according to the manufacturer’s instructions. This may involve brushing, spraying, or wiping the product onto the surface.
- Drying and Curing: Allow the sealant or coating to dry and cure completely according to the manufacturer’s recommendations. This may involve multiple coats.
- Inspection: Inspect the finished surface for any imperfections and make necessary repairs.
Safety and Health Considerations
The use of food-grade wood filler is paramount in ensuring the safety of food preparation and storage surfaces. Understanding and adhering to safety guidelines is crucial to protect both the user and the consumer from potential health hazards. This section Artikels the critical safety aspects associated with food-grade wood filler, focusing on the risks of using non-food-grade alternatives, safe handling practices, and proper storage and disposal methods.
Potential Health Risks of Non-Food-Grade Wood Fillers
The selection of the correct wood filler is vital for food safety. Using non-food-grade wood fillers in applications involving food contact can introduce harmful substances into the food supply.Non-food-grade wood fillers may contain chemicals that pose significant health risks. These risks can include:
- Toxicity: Many non-food-grade fillers contain volatile organic compounds (VOCs), solvents, and other chemicals that can be toxic if ingested or inhaled. Exposure to these substances can lead to various health problems, ranging from skin irritation and respiratory issues to more severe conditions such as organ damage or cancer.
- Migration: The chemicals in non-food-grade fillers can migrate from the filler into the food, especially when exposed to heat, moisture, or acidic substances. This process, known as leaching, can contaminate the food and pose a direct threat to consumer health. For instance, the U.S. Food and Drug Administration (FDA) regulates the materials used in food contact applications, establishing limits on the amount of certain substances that can migrate into food.
- Allergic Reactions: Some non-food-grade fillers may contain allergens that can trigger allergic reactions in sensitive individuals. Symptoms can vary from mild skin rashes to severe anaphylactic shock.
- Unintended Consequences: In some cases, the ingredients in non-food-grade fillers are not fully disclosed, making it difficult to assess the potential health risks. This lack of transparency can lead to unforeseen health consequences for consumers.
Importance of Following Safety Guidelines
Adhering to safety guidelines is essential when handling and applying food-grade wood filler to minimize risks and ensure the safety of the user and the consumer. This involves following the manufacturer’s instructions, using appropriate personal protective equipment (PPE), and working in a well-ventilated area.To ensure safety, consider these guidelines:
- Read and Understand the Instructions: Always read and fully understand the manufacturer’s instructions before using food-grade wood filler. These instructions provide critical information on proper application, curing times, and safety precautions.
- Use Personal Protective Equipment (PPE): Appropriate PPE is necessary to minimize exposure to the filler. This typically includes:
- Gloves: Wear chemical-resistant gloves to protect the skin from contact with the filler.
- Eye Protection: Use safety glasses or goggles to prevent eye irritation from splashes or dust.
- Respiratory Protection: In some cases, especially when working in poorly ventilated areas, a respirator may be necessary to prevent inhalation of fumes or dust. Choose a respirator appropriate for the specific filler being used.
- Work in a Well-Ventilated Area: Ensure adequate ventilation when applying food-grade wood filler. This can involve opening windows and doors, or using fans to circulate air. Good ventilation helps to disperse any fumes or vapors released during the application process.
- Avoid Contact with Skin and Eyes: Take precautions to avoid direct contact with the filler. If contact occurs, immediately wash the affected area with soap and water. In case of eye contact, flush the eyes with water for several minutes and seek medical attention if irritation persists.
- Keep Out of Reach of Children and Pets: Store food-grade wood filler in a secure location, away from children and pets. Accidental ingestion can lead to serious health problems.
Safe Storage and Disposal of Food-Grade Wood Filler
Proper storage and disposal of food-grade wood filler are essential for maintaining safety and minimizing environmental impact. This involves storing the product correctly to prevent spoilage and contamination, and disposing of it in a manner that complies with local regulations.Follow these guidelines for safe storage and disposal:
- Storage:
- Keep Tightly Sealed: Store food-grade wood filler in its original, tightly sealed container when not in use. This prevents the filler from drying out or being contaminated.
- Store in a Cool, Dry Place: Protect the filler from extreme temperatures and humidity. Store it in a cool, dry place, away from direct sunlight and heat sources.
- Avoid Freezing: Some food-grade wood fillers may be damaged by freezing. Check the manufacturer’s instructions for specific storage recommendations.
- Keep Away from Food: Store food-grade wood filler separately from food products to prevent cross-contamination.
- Disposal:
- Follow Local Regulations: Dispose of food-grade wood filler in accordance with local regulations. These regulations may vary depending on the specific type of filler and the location.
- Check for Hazardous Waste: Some food-grade wood fillers may be classified as hazardous waste. Check the Safety Data Sheet (SDS) for the product to determine its hazardous waste classification.
- Proper Containerization: When disposing of the filler, place it in a sealed container to prevent spills and leaks.
- Avoid Pouring Down Drains: Do not pour liquid filler down drains or into the environment. This can contaminate water sources and harm wildlife.
- Recycle if Possible: If possible, recycle the empty containers according to local recycling guidelines.
Cleaning and Maintenance
Maintaining the integrity of surfaces repaired with food-grade wood filler is crucial for ensuring food safety and prolonging the lifespan of the repair. Regular cleaning and proper maintenance practices are essential to prevent the buildup of bacteria, mold, and other contaminants, while also preserving the aesthetic appearance and structural soundness of the filled areas. Following the guidelines below will help ensure the continued safety and usability of food-contact surfaces.
Recommended Cleaning Methods
Effective cleaning of food-grade wood filler requires methods that are both thorough and gentle. The goal is to remove food particles and potential contaminants without damaging the filler or the surrounding wood.
- Wiping: For daily cleaning, a simple wipe-down with a clean, damp cloth is often sufficient. This is especially useful for removing surface debris and spills. Ensure the cloth is wrung out well to prevent excess water from penetrating the wood.
- Gentle Scrubbing: For more stubborn stains or residue, a gentle scrubbing action may be necessary. Use a soft-bristled brush or a non-abrasive sponge to avoid scratching the surface.
- Rinsing: After cleaning, rinse the surface thoroughly with clean water to remove any residual cleaning agents. This step is crucial to prevent the buildup of chemicals.
- Drying: Always dry the surface completely after cleaning. Standing water can promote the growth of mold and mildew. Use a clean, dry cloth or allow the surface to air dry.
Safe Cleaning Agents
Selecting appropriate cleaning agents is vital to prevent the contamination of food and the degradation of the wood filler. Avoid harsh chemicals that could leach into food or damage the filler’s protective properties.
- Mild Soap and Water: A solution of mild dish soap and warm water is generally safe and effective for most cleaning tasks. Ensure the soap is thoroughly rinsed away.
- Vinegar Solutions: Diluted white vinegar (a 1:1 solution with water) can be used as a natural disinfectant and degreaser. Vinegar is generally safe for food-contact surfaces.
- Baking Soda Paste: A paste made from baking soda and water can be used to gently scrub away stains and odors. Baking soda is a mild abrasive and a natural deodorizer.
- Avoid Harsh Chemicals: Refrain from using bleach, ammonia, or other strong cleaning agents, as they can damage the wood filler and pose a health risk. Always consult the wood filler’s manufacturer instructions for recommended cleaning products.
Maintenance Schedule
Establishing a regular maintenance schedule is key to preserving the integrity and safety of food-grade wood filler. The frequency of cleaning and inspection should be tailored to the usage of the surface and the types of foods it comes into contact with.
The following is a suggested maintenance schedule:
- Daily Cleaning: Wipe down the surface with a damp cloth after each use to remove food particles and spills.
- Weekly Cleaning: Perform a more thorough cleaning using mild soap and water or a vinegar solution. Inspect the filled areas for any signs of damage, such as cracks or discoloration.
- Monthly Inspection: Conduct a more detailed inspection of the repaired surfaces. Check for any signs of wear, chipping, or degradation of the wood filler. Address any issues promptly.
- Annual Reapplication (if necessary): Depending on the wear and tear, the wood filler may need to be reapplied annually or as needed. Follow the manufacturer’s instructions for reapplication.
Sourcing and Purchasing
Acquiring food-grade wood filler requires careful consideration to ensure product safety and suitability for its intended use. This section Artikels crucial aspects of sourcing and purchasing, guiding you through selecting reputable suppliers and verifying product compliance.
Get the entire information you require about mexican food catering portland or on this page.
Identifying Reputable Manufacturers and Suppliers
Choosing a reliable source for food-grade wood filler is paramount. Several manufacturers and suppliers specialize in products designed to meet stringent food safety standards.
- Reputable Manufacturers: Look for established manufacturers with a proven track record in producing food-safe materials. These companies often have certifications and adhere to rigorous quality control processes. Examples include companies that specialize in epoxy resins, such as those that have experience supplying materials for food processing equipment.
- Authorized Distributors: Purchasing from authorized distributors of reputable manufacturers ensures you receive genuine products and access to technical support. These distributors often have in-depth knowledge of the products they sell.
- Online Marketplaces (with caution): While online marketplaces offer convenience, exercise caution when purchasing food-grade wood filler from these platforms. Verify the seller’s reputation, read reviews, and confirm the product’s certifications before making a purchase. Look for sellers with transparent product information and readily available technical data sheets.
- Industry Trade Shows and Associations: Attending industry trade shows and contacting relevant associations provides opportunities to connect with manufacturers and suppliers directly. These events often showcase the latest products and technologies in food-safe materials.
Factors to Consider When Selecting Food-Grade Wood Filler
Several factors influence the selection of the appropriate food-grade wood filler for a specific application. Considering these aspects ensures the chosen product aligns with your needs and safety requirements.
- Cost: The price of food-grade wood filler varies depending on the manufacturer, the volume purchased, and the specific formulation. While cost is a consideration, prioritize product quality and compliance with food safety standards. Compare prices from different suppliers and consider the long-term value, including durability and ease of maintenance.
- Availability: Ensure the wood filler is readily available from a reliable supplier. Consider lead times, especially for large projects. Check if the supplier offers the desired quantities and packaging options to meet your project’s needs.
- Application Requirements: The specific application dictates the type of wood filler needed. Consider factors such as the type of wood, the environment (e.g., temperature, moisture), and the expected contact with food. For example, a filler for a cutting board will have different requirements than a filler used to seal a food storage container.
- Durability and Performance: Assess the filler’s durability, including its resistance to wear, impact, and chemical exposure. The filler should withstand the cleaning processes and the conditions it will encounter in the food-related environment. Research the filler’s performance characteristics, such as its ability to bond to the wood, its flexibility, and its resistance to cracking or shrinking.
- Regulatory Compliance: Confirm the wood filler complies with relevant food safety regulations, such as those set by the FDA (in the United States) or similar agencies in your region. Look for certifications that indicate compliance with these standards.
Tips for Verifying Food-Grade Standards
Verifying that a product meets food-grade standards is critical to ensuring safety. These steps help confirm the filler’s suitability for food-related applications.
- Review Product Documentation: Carefully examine the product’s technical data sheets (TDS), safety data sheets (SDS), and any available certifications. These documents provide information about the filler’s composition, performance characteristics, and compliance with food safety regulations.
- Check for Certifications: Look for certifications from recognized organizations that assess the safety of materials used in food contact applications. Examples include:
- NSF International: NSF provides certifications for food equipment and materials. NSF/ANSI standards ensure products meet specific requirements for health and safety.
- FDA Compliance: The U.S. Food and Drug Administration (FDA) sets standards for materials that come into contact with food. Look for statements indicating that the product complies with FDA regulations, such as 21 CFR Part 175.300, which pertains to resins used in food packaging.
- Contact the Manufacturer: If you have any doubts, contact the manufacturer directly. Inquire about their quality control processes, certifications, and any specific testing they have conducted to ensure the product’s food safety.
- Request Samples: Request a sample of the wood filler to test it in your specific application. This allows you to evaluate its performance, adhesion, and suitability for your needs.
- Understand the Labeling: Carefully read the product label. The label should clearly state that the product is food-grade, provide information on its intended use, and include any necessary safety precautions.
Alternatives to Food Grade Wood Filler
While food-grade wood filler is specifically designed for use in food-related environments, there are alternative materials that can be considered for repairing wood surfaces. These alternatives offer varying degrees of suitability, and it’s crucial to carefully evaluate their properties, particularly their food safety compliance and durability, before making a selection. The choice of alternative should be guided by the specific application, the type of wood, and the level of exposure to food products.
Comparison of Food-Grade Wood Filler and Alternative Materials
Food-grade wood filler typically comprises a combination of wood flour, a binder (often a modified polymer), and additives. It’s formulated to be non-toxic, odorless, and resistant to moisture and microbial growth, making it ideal for food contact surfaces. Alternative materials may offer different advantages and disadvantages. For example, some materials might offer greater durability or faster curing times, but they might not meet the same food safety standards.
It’s important to remember that any material used in a food environment must not contaminate food products and must be easily cleanable.
Pros and Cons of Alternative Materials
Food-grade epoxy resins can be an alternative. These resins offer excellent durability and water resistance, making them suitable for areas exposed to moisture. However, they can be more expensive and may require more precise application techniques. Some epoxy resins are certified as food-safe, but it is vital to confirm this certification and follow the manufacturer’s instructions meticulously. Specialized wood patching compounds are another option.
These compounds are designed for wood repair and may offer good adhesion and flexibility. However, their food safety may vary, so it is crucial to verify their compliance with food safety regulations before use. The selection depends on the specific requirements of the repair and the level of food contact.
Alternative Solutions for Repairing Wood Surfaces
Here are some alternative solutions for repairing wood surfaces in food-related environments, along with their pros and cons:
- Food-Grade Epoxy Resins:
- Pros: Highly durable, water-resistant, excellent adhesion, can be used in areas with significant wear and tear.
- Cons: Can be more expensive, may require specialized application techniques, some formulations may not be fully food-safe without specific certifications. Always verify the food-safe certification from a recognized authority like NSF International or FDA compliance.
- Specialized Wood Patching Compounds:
- Pros: Designed specifically for wood repair, often offer good adhesion and flexibility, can be easier to apply than epoxy resins.
- Cons: Food safety can vary significantly between products; careful selection and verification of food-grade certification are crucial. Durability may be less than epoxy resins in high-stress areas.
- Wood with Integrated Repairs:
- Pros: In cases where the damage is extensive, replacing the damaged wood section with new, food-safe wood can be a viable alternative. This approach avoids the need for patching compounds altogether, providing a seamless and potentially more durable solution.
- Cons: May require more carpentry skills, can be time-consuming, and may not be feasible for all types of damage or in all locations.
- Stainless Steel or Other Food-Grade Metals:
- Pros: Completely inert and non-reactive, excellent for direct food contact, highly durable, and easy to clean.
- Cons: Not a wood repair material, requires replacing the damaged wood section, can be expensive, and may require specialized fabrication skills.
Troubleshooting Common Issues
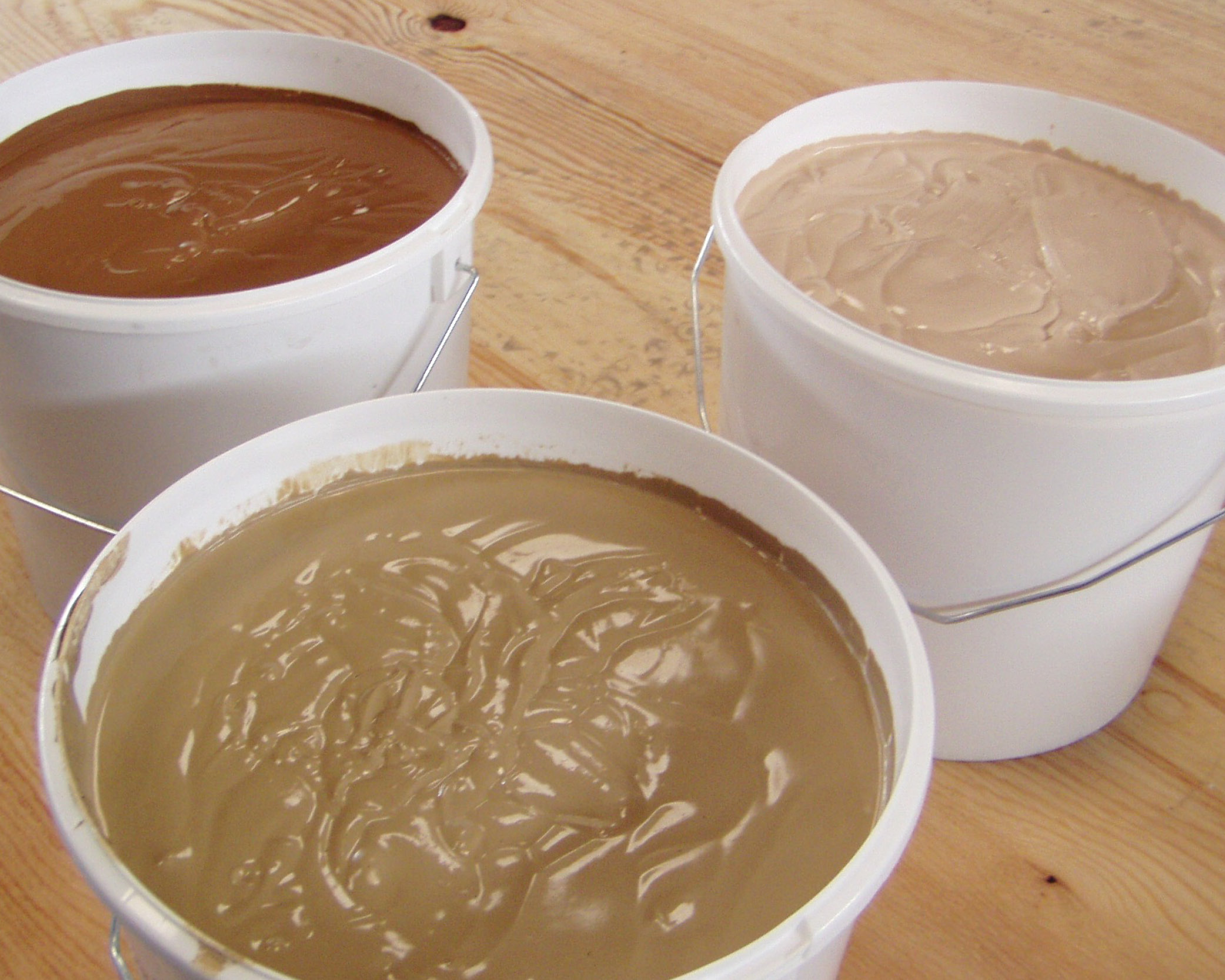
Applying food-grade wood filler, while generally straightforward, can sometimes present challenges. Understanding potential problems and knowing how to address them ensures a successful and food-safe repair or restoration. This section addresses common issues encountered during application, curing, and use, providing practical solutions to achieve optimal results.
Cracking and Shrinking
Cracking and shrinking are among the most frequent problems encountered with wood fillers. These issues often stem from the filler drying too quickly, excessive application, or the natural movement of the wood.
- Causes of Cracking: Rapid drying due to environmental factors like low humidity or high temperatures, application of too thick a layer in a single pass, and the wood expanding and contracting due to changes in moisture content.
- Solutions for Cracking:
- Control the environment by maintaining moderate humidity and temperature levels during application and curing.
- Apply filler in thin, multiple layers, allowing each layer to dry completely before applying the next. This prevents the outer layer from drying and cracking before the inner layer has a chance to cure.
- Consider using a filler with a slightly longer drying time, especially in dry climates.
- Ensure the wood is properly acclimated to its environment before applying the filler to minimize movement.
- Causes of Shrinking: The filler losing volume as it dries and cures, particularly if it contains a high percentage of solvents or water that evaporates during the process.
- Solutions for Shrinking:
- Apply filler in multiple thin coats rather than one thick coat. Each thin coat will shrink less.
- Select a filler with low shrinkage characteristics. Check the product specifications for shrinkage percentages.
- Properly prepare the wood surface to ensure the filler adheres well and doesn’t pull away during the drying process.
Discoloration
Discoloration can occur after the filler has cured, potentially affecting the aesthetic appeal of the repaired surface. This issue may arise from several factors.
- Causes of Discoloration: Reaction between the filler and the wood, exposure to UV light, contamination from previous finishes or treatments, or improper mixing of two-part fillers.
- Solutions for Discoloration:
- Choose a food-grade wood filler that is specifically designed to be compatible with the wood type.
- Apply a food-safe finish that provides UV protection after the filler has completely cured.
- Ensure the wood surface is thoroughly cleaned and free of any old finishes or contaminants before applying the filler.
- Follow the manufacturer’s instructions precisely when mixing two-part fillers to avoid uneven curing and discoloration.
Adhesion and Durability Issues
Ensuring strong adhesion and long-term durability are critical for the effectiveness of food-grade wood filler, especially in areas subject to frequent use and cleaning.
- Causes of Adhesion Failure: Improper surface preparation, contamination of the wood surface, the use of incompatible fillers, or applying filler outside the recommended temperature range.
- Solutions for Adhesion Failure:
- Thoroughly clean and sand the wood surface to remove any dirt, grease, or old finishes.
- Ensure the wood is dry before applying the filler.
- Select a food-grade wood filler specifically designed for the wood type and intended use.
- Apply the filler within the temperature range specified by the manufacturer.
- Consider using a primer recommended by the filler manufacturer to improve adhesion, especially on difficult-to-bond surfaces.
- Causes of Durability Issues: Exposure to excessive moisture, impact damage, the use of an inappropriate filler for the application, or inadequate curing.
- Solutions for Durability Issues:
- Protect the filled area from excessive moisture by applying a food-safe, water-resistant finish.
- Select a food-grade wood filler with high impact resistance if the area is subject to wear and tear.
- Allow the filler to cure completely according to the manufacturer’s instructions before exposing it to use.
- Regularly inspect and maintain the filled area, re-applying filler or finish as needed to address any signs of damage.
Ending Remarks
In closing, food grade wood filler is more than just a product; it’s a practice of mindful creation. By understanding its composition, applications, and care, we become stewards of our environments, fostering spaces that promote health, safety, and a deeper connection to the present moment. Embrace the journey of restoration, knowing that each carefully applied layer is a testament to your dedication to wholeness.
Let the work you do reflect the care you give, and the surfaces you create become a sanctuary for nourishment, both physical and spiritual.