Food import group operations form the intricate backbone of global food supply chains, facilitating the movement of essential sustenance across borders. These groups are vital for ensuring diverse food availability and meeting consumer demands worldwide. Their responsibilities span a broad spectrum, encompassing regulatory compliance, quality control, logistics management, and risk mitigation. This comprehensive overview delves into the multifaceted world of food import groups, exploring their functions, stakeholders, and the challenges they navigate in the dynamic landscape of international food trade.
The scope of a food import group extends far beyond simply bringing food into a country. They are responsible for understanding and adhering to complex legal and regulatory frameworks, which can vary significantly depending on the origin and destination countries. Different organizational structures, from small independent importers to large multinational corporations, exist within the industry. Furthermore, the success of a food import group hinges on effective collaboration with a diverse range of stakeholders, including customs brokers, exporters, regulatory agencies, and transportation providers.
Each of these entities plays a crucial role in the smooth and safe passage of food products across international boundaries.
Overview of Food Import Groups
Food import groups play a critical role in global food supply chains, ensuring that diverse food products reach consumers across international borders. These organizations are responsible for navigating complex logistical, regulatory, and financial hurdles to bring food items from producers to markets. Their activities are essential for meeting consumer demand, providing access to a wider variety of foods, and contributing to economic growth through international trade.
Primary Functions and Responsibilities of Food Import Groups
Food import groups have several core functions, each vital to the successful movement of food products. These responsibilities encompass a wide range of activities, from initial sourcing to final delivery.
- Sourcing and Procurement: Identifying and establishing relationships with food producers in various countries. This involves evaluating suppliers based on quality, safety, and compliance with international standards. The import group negotiates contracts, prices, and delivery schedules.
- Compliance and Regulatory Affairs: Ensuring that all imported food products meet the legal requirements of the importing country. This includes obtaining necessary permits, licenses, and certifications. The group must stay informed about changing regulations related to food safety, labeling, and tariffs.
- Logistics and Transportation: Managing the movement of food products from the point of origin to the destination. This involves selecting appropriate modes of transportation (e.g., sea, air, land), coordinating shipping schedules, and overseeing customs clearance procedures. Proper temperature control and handling are critical, especially for perishable goods.
- Quality Control and Inspection: Implementing quality control measures throughout the import process. This includes inspecting products upon arrival to ensure they meet quality standards and are free from contamination. The group may conduct laboratory testing and collaborate with third-party inspection agencies.
- Distribution and Sales: Distributing imported food products to retailers, wholesalers, and food service providers. This may involve warehousing, inventory management, and sales and marketing activities. The group often establishes distribution networks and manages relationships with key customers.
- Financial Management: Handling financial aspects of the import process, including currency exchange, payment of duties and taxes, and managing credit lines. They also manage risks associated with fluctuations in currency exchange rates and commodity prices.
Types of Food Import Groups Based on Organizational Structure
Food import groups can be structured in various ways, each with its own advantages and disadvantages depending on the scale and scope of their operations. The organizational structure often reflects the size of the company, the types of products imported, and the target market.
- Independent Importers: These are stand-alone businesses that specialize in importing food products. They typically focus on specific product categories or regions and manage all aspects of the import process, from sourcing to distribution. Their size can vary from small family-owned businesses to large corporations.
- Subsidiaries of Multinational Corporations: Large food companies often establish subsidiaries in different countries to handle import operations. This structure allows for greater control over the supply chain and integration with the parent company’s global operations. For example, a multinational food manufacturer might establish a subsidiary in the United States to import ingredients or finished products from its facilities in other countries.
- Trading Companies: These companies act as intermediaries between food producers and buyers. They may handle the import process on behalf of clients or trade food products directly. Trading companies often have extensive networks and expertise in international trade.
- Wholesalers with Import Divisions: Some wholesalers have dedicated import divisions that handle the import of food products for their distribution network. This structure allows wholesalers to expand their product offerings and source products directly from international suppliers.
- Retailer-Owned Import Groups: Large retailers may establish their own import groups to source products directly from overseas suppliers. This can provide greater control over the supply chain, reduce costs, and ensure product quality and consistency. For example, a major supermarket chain might have an import group that sources fresh produce from various countries.
Legal and Regulatory Framework Governing Food Import Groups in the United States
The import of food into the United States is subject to a complex legal and regulatory framework designed to protect public health and ensure food safety. Several federal agencies are involved in overseeing food imports, with the Food and Drug Administration (FDA) playing a central role.
- Food and Drug Administration (FDA): The FDA is the primary agency responsible for regulating food imports. It enforces the Federal Food, Drug, and Cosmetic Act (FD&C Act), which sets standards for food safety, labeling, and packaging. The FDA inspects imported food products, conducts laboratory testing, and can take enforcement actions against products that violate the FD&C Act.
- U.S. Customs and Border Protection (CBP): CBP is responsible for enforcing customs laws and collecting duties on imported goods. It works closely with the FDA to ensure that imported food products meet all import requirements. CBP inspects shipments, verifies documentation, and can detain or refuse entry to products that do not comply with regulations.
- Food Safety Modernization Act (FSMA): The FSMA, enacted in 2011, significantly enhanced the FDA’s authority to regulate food safety. It introduced new requirements for importers, including:
- Foreign Supplier Verification Program (FSVP): Importers must verify that their foreign suppliers are producing food in a manner that meets U.S. food safety standards. This includes conducting hazard analyses, implementing preventive controls, and monitoring supplier performance.
- Preventive Controls for Human Food and Animal Food: These regulations require food facilities, including those importing food, to implement preventive controls to minimize food safety hazards.
- Produce Safety Rule: This rule sets standards for the safe production and harvesting of fruits and vegetables.
- Import Requirements: Food import groups must comply with several import requirements, including:
- Prior Notice: Importers must provide the FDA with advance notice of imported food shipments.
- Registration: Food facilities, including those that manufacture, process, pack, or hold food for human or animal consumption in the United States, must register with the FDA.
- Labeling: Imported food products must be labeled in accordance with FDA regulations, including accurate ingredient lists, nutrition information, and country of origin labeling.
- Detention and Refusal of Admission: The FDA can detain or refuse entry to imported food products that are adulterated, misbranded, or otherwise in violation of the FD&C Act.
Key Players and Stakeholders
The intricate dance of food imports involves a diverse cast of characters, each playing a vital role in ensuring that safe and desirable food products reach consumers across borders. Understanding the roles and responsibilities of these key players, along with the potential conflicts that can arise, is crucial for navigating the complexities of the global food trade. This section will illuminate the key stakeholders, their duties, and the strategies employed to manage potential conflicts, all grounded in scientific and regulatory principles.
Importers
Importers are the primary drivers of the food import process, acting as the bridge between foreign suppliers and domestic consumers. They are responsible for procuring food products from exporters, ensuring compliance with all relevant import regulations, and ultimately bringing the food into the importing country.
- Sourcing and Procurement: Importers identify and establish relationships with reliable exporters, often conducting due diligence to assess the quality and safety of the products and the exporter’s adherence to food safety standards, such as those set by the World Health Organization (WHO) or the Food and Agriculture Organization (FAO). This involves assessing the exporter’s facilities, processes, and food safety management systems, often through audits or inspections.
- Regulatory Compliance: Importers must navigate a complex web of regulations, including those related to labeling, packaging, food additives, and permitted ingredients. They are responsible for ensuring that the imported food meets the standards of the importing country, such as those enforced by the Food and Drug Administration (FDA) in the United States or the European Food Safety Authority (EFSA) in Europe.
This includes providing necessary documentation, such as import permits, health certificates, and certificates of origin.
- Logistics and Transportation: Importers manage the transportation of food products from the exporter’s facility to the final destination, which involves coordinating shipping, insurance, and warehousing. They must consider factors such as temperature control, storage conditions, and transit times to maintain the quality and safety of the food. The use of refrigerated containers for perishable goods is a critical example of this, adhering to the principles of cold chain management to prevent spoilage and microbial growth.
- Financial Transactions: Importers handle the financial aspects of the import process, including payment to the exporter, duties, taxes, and other associated costs. They may utilize various financial instruments, such as letters of credit, to mitigate financial risks.
Exporters
Exporters are the suppliers of food products in the international trade, providing the goods to importers and ensuring they meet the agreed-upon specifications and quality standards. Their role is critical in maintaining the integrity and safety of the food supply chain.
- Production and Quality Control: Exporters are responsible for producing or sourcing food products that meet the requirements of the importing country, including quality, safety, and labeling standards. They must implement robust quality control systems, such as Hazard Analysis and Critical Control Points (HACCP), to identify and control potential hazards throughout the production process.
- Documentation and Certification: Exporters must provide all necessary documentation required by the importing country, including health certificates, certificates of origin, and other relevant paperwork. They may also be required to obtain certifications, such as those related to organic farming or food safety management systems.
- Packaging and Labeling: Exporters must ensure that the food products are packaged and labeled in accordance with the regulations of the importing country. This includes providing accurate information about ingredients, nutritional content, and any potential allergens.
- Shipping and Logistics: Exporters coordinate the shipment of food products to the importer, including selecting appropriate shipping methods, arranging for transportation, and ensuring that the products are properly handled during transit. They are responsible for complying with international shipping regulations, such as those set by the International Maritime Organization (IMO).
Customs Brokers
Customs brokers are licensed professionals who act as intermediaries between importers and customs authorities. They are experts in customs regulations and procedures, facilitating the smooth and efficient clearance of imported goods.
- Customs Clearance: Customs brokers prepare and submit all necessary documentation to customs authorities, including import declarations, invoices, and packing lists. They ensure that all information is accurate and complete, and that the goods comply with all relevant regulations.
- Duty and Tax Calculation: Customs brokers calculate and pay the duties, taxes, and other fees associated with the import of food products. They are responsible for classifying goods correctly according to the Harmonized System (HS) code, which determines the applicable tariff rates.
- Compliance and Regulation: Customs brokers stay up-to-date on the latest customs regulations and ensure that importers comply with all relevant requirements. They advise importers on issues such as import restrictions, quotas, and other trade barriers.
- Communication and Liaison: Customs brokers serve as a point of contact between importers and customs authorities, handling communications and resolving any issues that may arise during the customs clearance process. They often have established relationships with customs officials, which can expedite the clearance process.
Regulatory Agencies
Regulatory agencies play a crucial role in overseeing the food import process, ensuring the safety and quality of imported food products and protecting public health. Their responsibilities include setting standards, enforcing regulations, and conducting inspections.
- Setting Standards: Regulatory agencies establish food safety standards, including those related to food additives, pesticide residues, and microbiological contamination. These standards are often based on scientific risk assessments and international guidelines, such as those developed by the Codex Alimentarius Commission.
- Inspections and Audits: Regulatory agencies conduct inspections of food processing facilities and import facilities to verify compliance with food safety regulations. They may also conduct audits of food safety management systems, such as HACCP plans.
- Import Controls: Regulatory agencies implement import controls, such as import permits, inspections at the border, and laboratory testing of imported food products. They may also impose restrictions on the import of certain products, such as those that pose a health risk.
- Enforcement: Regulatory agencies enforce food safety regulations, which may involve issuing warnings, imposing fines, or seizing or destroying non-compliant products. They may also initiate legal action against companies that violate food safety laws.
Potential Conflicts of Interest and Management Strategies
Conflicts of interest can arise between stakeholders in the food import process, potentially compromising food safety or creating unfair trade practices.
- Importers and Exporters: A conflict can occur if an importer prioritizes cost-cutting over food safety, potentially pressuring an exporter to cut corners in production or quality control. This is managed through robust contracts that define clear quality and safety standards, third-party audits, and the implementation of food safety management systems like HACCP.
- Customs Brokers and Importers: A conflict may arise if a customs broker, under pressure from an importer, misclassifies goods to reduce duties or taxes. This is mitigated through strict ethical guidelines for customs brokers, audits by customs authorities, and the imposition of penalties for non-compliance.
- Regulatory Agencies and Importers/Exporters: A potential conflict exists if regulatory agencies are perceived as being influenced by the industry. To address this, regulatory agencies maintain independence through transparent decision-making processes, the use of scientific evidence, and public consultation.
The management of conflicts of interest is essential for maintaining the integrity of the food import process and ensuring the safety and quality of imported food.
Import Procedures and Documentation
Importing food is a complex process governed by international regulations and national laws. Understanding these procedures and the required documentation is crucial for ensuring smooth and compliant trade, protecting consumer safety, and preventing delays or rejections at the border. This section Artikels the standard import procedures, provides a checklist of essential documents, and illustrates the step-by-step process through a flowchart.
Standard Import Procedures for Food Products
The import of food products typically follows a standardized set of procedures, although specific requirements may vary depending on the origin, type of food, and destination country. These procedures generally involve several key stages, beginning with pre-shipment activities and concluding with customs clearance and delivery.
- Pre-Shipment Activities: This stage involves all the preparation before the goods are shipped. Importers must first determine the specific import requirements of the destination country, including any specific permits, licenses, or certifications required for the food product. They must also ensure the food product meets all relevant health and safety standards, such as those set by food safety agencies like the Food and Drug Administration (FDA) in the United States or the European Food Safety Authority (EFSA) in Europe.
A contract with a supplier is established, and the goods are inspected at the origin to verify that they comply with the import requirements.
- Shipping and Transportation: Once the pre-shipment activities are completed, the food product is shipped to the destination country. This involves selecting a suitable mode of transport (sea, air, or land), arranging for shipping documentation, and obtaining necessary insurance. The importer is responsible for ensuring the goods are properly packaged and handled to prevent spoilage or damage during transit. Temperature-controlled shipping, for example, is crucial for perishable items like fresh produce or frozen seafood, and can significantly affect the import process.
- Arrival and Customs Clearance: Upon arrival at the destination country, the food product undergoes customs clearance. The importer or their customs broker submits the required documentation to the customs authorities. This documentation is thoroughly reviewed to verify compliance with import regulations, including tariff classifications, duties, and taxes. The customs authorities may inspect the goods physically or through sampling to ensure they meet safety and quality standards.
This process is usually governed by the World Customs Organization (WCO) and the specific regulations of the importing country.
- Inspection and Testing: Depending on the type of food and the regulations of the importing country, the goods may be subject to inspection and testing by food safety authorities. This may involve laboratory analysis to check for contaminants, pathogens, or compliance with labeling requirements. For example, the United States Department of Agriculture (USDA) inspects meat and poultry imports to ensure they meet the same standards as domestically produced products.
- Release and Delivery: If the food product passes all inspections and meets all import requirements, customs authorities release the goods. The importer can then take possession of the goods and arrange for their delivery to their final destination. This final stage includes storage and distribution, often involving a cold chain to maintain the product’s quality and safety.
Essential Documents Required for Importing Food
A wide array of documents is necessary for the successful import of food products. These documents serve various purposes, from verifying the origin and composition of the product to ensuring compliance with health and safety regulations. The specific documents required can vary depending on the product, the origin, and the destination country. However, a standard set of documents is usually required.
- Commercial Invoice: This document provides details about the transaction, including the seller and buyer information, a description of the goods, quantity, price, and payment terms.
- Packing List: This document lists the contents of each package, including the weight, dimensions, and any special handling instructions.
- Bill of Lading (for sea) or Air Waybill (for air): These documents serve as a receipt for the goods and evidence of the contract of carriage. They also act as a title document, enabling the importer to take possession of the goods.
- Import Permit or License: Depending on the product and the destination country, an import permit or license may be required. This document authorizes the importer to bring the food product into the country.
- Certificate of Origin: This document certifies the country of origin of the food product. It may be required to determine the applicable tariffs and duties.
- Health Certificate or Phytosanitary Certificate: These certificates, issued by the exporting country’s health or agriculture authorities, certify that the food product meets the importing country’s health and safety standards. For example, a phytosanitary certificate is often required for fruits and vegetables to certify that they are free from pests and diseases.
- Food Safety Certificates: These certificates, such as those issued by the FDA or EFSA, verify that the food product complies with the food safety regulations of the importing country.
- Labelling and Ingredient Declaration: The importer must ensure the food product is properly labeled with all required information, including ingredients, nutritional information, and any warnings or allergen information.
- Insurance Certificate: This document proves that the goods are insured against loss or damage during transit.
Flowchart Illustrating the Step-by-Step Process of Food Import, from Origin to Destination
The following flowchart illustrates the typical step-by-step process of importing food products, from the point of origin to the final destination. Each stage is presented in a logical sequence, highlighting the key activities and decision points.
+---------------------------------------+ +-------------------------------------+ +--------------------------------------+ | 1. Pre-Shipment Activities: |----->| 2. Shipping and Transportation: |----->| 3. Arrival and Customs Clearance: | | -Determine Import Requirements | | -Select Mode of Transport | | -Submit Documentation | | -Ensure Compliance with Standards | | -Arrange Shipping Documentation | | -Pay Duties and Taxes | | -Contract with Supplier | | -Obtain Insurance | | -Inspection by Customs | | -Inspection at Origin | | -Packaging and Handling | +--------------------------------------+ +---------------------------------------+ +-------------------------------------+ | | | V +--------------------------------------+ | 4.Inspection and Testing: | | -Inspection by Food Safety Agency | | -Laboratory Analysis | | -Compliance with Labeling | +--------------------------------------+ | | V +--------------------------------------+ | 5.
Release and Delivery: | | -Customs Release | | -Delivery to Final Destination | | -Storage and Distribution | +--------------------------------------+
The flowchart begins with the pre-shipment activities, including determining import requirements, ensuring compliance with standards, contracting with a supplier, and conducting an inspection at the origin.
These activities set the foundation for a successful import process. Next, the food product is shipped, involving the selection of the mode of transport, arranging shipping documentation, obtaining insurance, and proper packaging and handling. Upon arrival, the product undergoes customs clearance, where documentation is submitted, duties and taxes are paid, and customs inspections are conducted. Following customs clearance, the food product may be subject to inspection and testing by food safety agencies, including laboratory analysis and checks for compliance with labeling requirements.
Finally, if all requirements are met, the product is released, and delivery to the final destination takes place, including storage and distribution. Each stage in the flowchart represents a critical step in the import process, and any failure to comply with the requirements at any stage can result in delays, rejections, or other penalties. For example, if a shipment of seafood fails inspection due to the presence of harmful bacteria, it may be destroyed or returned to the origin, resulting in significant financial losses for the importer.
Sourcing and Supplier Selection
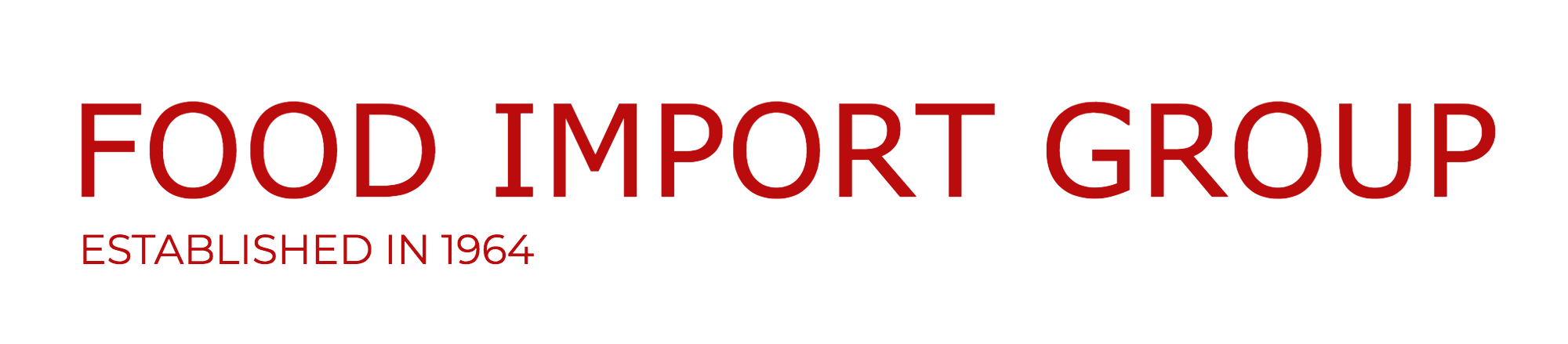.png?format=1500w)
The success of any food import group hinges on the reliability and quality of its suppliers. Sourcing and supplier selection are critical processes, demanding meticulous attention to detail and a proactive approach to risk management. This section delves into the strategies employed by food import groups to identify and vet potential suppliers, ensuring the integrity and safety of the imported food products.
Methods for Sourcing Suppliers
Food import groups employ a multifaceted approach to identify potential suppliers, leveraging a combination of traditional and modern methods. These strategies aim to cast a wide net, ensuring access to a diverse range of suppliers and products while maintaining a high degree of control over the sourcing process.
- Trade Shows and Exhibitions: Attending international food trade shows and exhibitions is a common practice. These events provide opportunities to meet with numerous suppliers, sample products, and assess their operations firsthand. The presence of industry experts and regulatory bodies at these events can also facilitate initial due diligence. For example, the SIAL Paris and the Foodex Japan are significant platforms for global food sourcing, offering opportunities to connect with suppliers from various regions.
- Online Marketplaces and Databases: Utilizing online platforms dedicated to food suppliers allows import groups to search for specific products, compare pricing, and review supplier profiles. Platforms like Alibaba.com and specialized food industry directories offer extensive databases of potential suppliers. This method enables efficient identification of suppliers based on specific criteria, such as certifications, product types, and geographical location.
- Direct Contact and Networking: Building relationships with existing suppliers and leveraging industry contacts is crucial. Direct contact involves reaching out to potential suppliers through email, phone calls, or in-person visits. Networking with industry professionals, such as distributors, brokers, and consultants, can also provide valuable leads and insights into reputable suppliers.
- Supplier Referrals and Recommendations: Seeking referrals from trusted sources, such as existing customers, industry peers, or regulatory agencies, can be an effective way to identify reliable suppliers. Recommendations often come with implicit endorsements, reducing the initial risk associated with supplier selection.
- Country-Specific Trade Organizations and Embassies: Collaborating with trade organizations and embassies of the countries where the import group intends to source food products can offer access to a vetted list of suppliers and facilitate communication. These organizations often have established relationships with local businesses and can provide valuable insights into local regulations and business practices.
Criteria for Evaluating Potential Food Suppliers
Evaluating potential food suppliers involves a comprehensive assessment of their capabilities and adherence to quality, safety, and compliance standards. This evaluation process typically encompasses a range of criteria designed to mitigate risks and ensure the delivery of safe and high-quality food products.
- Product Quality and Consistency: Assessing the quality of the food products is paramount. This involves evaluating factors such as taste, appearance, texture, and nutritional content. Consistent product quality is also critical, ensuring that each shipment meets the required standards. This assessment often includes sensory evaluations, laboratory testing, and adherence to established food standards like those set by the Codex Alimentarius.
- Food Safety Practices and Certifications: Verifying the supplier’s adherence to food safety practices is crucial. This includes assessing their food safety management systems, hygiene practices, and the presence of relevant certifications, such as Hazard Analysis and Critical Control Points (HACCP), Good Manufacturing Practices (GMP), and International Organization for Standardization (ISO) 22000. These certifications provide assurance that the supplier has implemented effective food safety controls.
- Compliance with Regulations and Standards: Ensuring compliance with all relevant regulations and standards is essential. This involves verifying that the supplier meets all legal requirements for food production, labeling, and packaging in both the exporting country and the importing country. This includes adhering to regulations set by agencies such as the Food and Drug Administration (FDA) in the United States or the European Food Safety Authority (EFSA).
- Supplier Capacity and Capability: Assessing the supplier’s capacity to meet the import group’s volume and delivery requirements is crucial. This involves evaluating their production capacity, storage facilities, and logistical capabilities. A supplier’s ability to consistently meet demand and deliver products on time is critical for maintaining a smooth supply chain.
- Financial Stability and Reputation: Evaluating the supplier’s financial stability and reputation is important to minimize the risk of business disruption. This involves reviewing their financial statements, assessing their creditworthiness, and checking their reputation within the industry. A financially stable and reputable supplier is more likely to be reliable and sustainable in the long term.
- Traceability and Recall Procedures: Ensuring that the supplier has a robust traceability system in place is essential for tracking products throughout the supply chain. This enables quick identification and recall of products in case of food safety issues. A well-defined recall procedure demonstrates the supplier’s commitment to food safety and consumer protection.
Due Diligence Procedures for Verifying Supplier Credentials
Due diligence procedures are implemented to verify the credentials of potential food suppliers and to assess their ability to meet the import group’s requirements. These procedures are designed to mitigate risks and to ensure that the selected suppliers are reliable and compliant.
Obtain a comprehensive document about the application of elyria food pantries that is effective.
- Document Review: This involves reviewing a wide range of documents, including supplier profiles, certifications, licenses, food safety plans, and quality control manuals. These documents provide evidence of the supplier’s capabilities and compliance with relevant standards.
- On-Site Audits: Conducting on-site audits of the supplier’s facilities is a crucial step in the due diligence process. Audits involve a thorough inspection of the production processes, storage facilities, and hygiene practices. These audits can be performed by the import group’s personnel, third-party auditors, or a combination of both.
- Laboratory Testing: Performing laboratory testing of the supplier’s products is essential to verify their quality and safety. This involves testing for contaminants, such as pesticides, heavy metals, and microorganisms, as well as assessing nutritional content and compliance with labeling requirements.
- Reference Checks: Contacting the supplier’s existing customers and requesting references can provide valuable insights into their performance and reliability. This helps to assess the supplier’s reputation and track record.
- Review of Past Performance: Analyzing the supplier’s past performance, including their delivery history, complaint records, and audit findings, can help to identify any potential issues or risks. This information can be used to make informed decisions about supplier selection.
- Verification of Certifications: Verifying the authenticity of the supplier’s certifications is essential. This involves checking the certification bodies’ websites or databases to confirm that the certifications are valid and up-to-date.
Quality Control and Food Safety
The import of food products necessitates a rigorous commitment to quality control and food safety. This commitment is not merely a regulatory obligation but a fundamental principle to protect public health, maintain consumer trust, and uphold the reputation of the importing company. Failing to ensure quality and safety can lead to severe consequences, including product recalls, legal liabilities, and significant financial losses.
Implementing robust quality control measures and adhering to food safety standards are, therefore, paramount for the success and sustainability of any food import operation.
Importance of Quality Control and Food Safety
Quality control and food safety are integral to the food import process for several critical reasons. They safeguard consumers from potential health risks, ensure the integrity of the food supply chain, and support the economic viability of the importing business. Effective quality control verifies that imported products meet the specified standards, while food safety focuses on preventing hazards that could cause illness or injury.
- Protecting Public Health: Foodborne illnesses, caused by bacteria, viruses, parasites, or chemical contaminants, can have devastating health consequences, including hospitalization and even death. Rigorous quality control and food safety measures are essential to minimize these risks. For example, in 2018, a multistate outbreak of E. coli infections linked to romaine lettuce prompted a widespread recall and investigations by the U.S. Food and Drug Administration (FDA), highlighting the importance of tracing food sources and implementing effective control measures.
- Maintaining Consumer Trust: Consumers rely on the safety and quality of the food they consume. Consistent adherence to quality control and food safety standards builds trust in the brand and its products. Loss of consumer trust, due to a food safety incident, can lead to a significant decline in sales and damage the company’s reputation.
- Ensuring Regulatory Compliance: Food imports are subject to strict regulations and standards set by government agencies in the importing country. Non-compliance can result in product rejection, fines, and legal action. Compliance with these regulations is non-negotiable for legal operation.
- Minimizing Financial Risks: Food safety incidents can lead to costly product recalls, legal fees, and lost sales. Investing in quality control and food safety measures upfront is a cost-effective strategy to mitigate these risks.
- Supporting the Food Supply Chain: By ensuring the safety and quality of imported food, importers contribute to the overall integrity and stability of the global food supply chain. This includes ensuring the traceability of products, the integrity of packaging, and the validity of labeling.
Methods for Implementing Effective Quality Control Measures
Implementing effective quality control measures requires a multi-faceted approach, encompassing various stages of the import process, from supplier selection to product storage and distribution. This approach should be systematic and documented to ensure consistency and traceability.
- Supplier Audits and Selection: Thoroughly evaluate potential suppliers, considering their food safety certifications, manufacturing practices, and quality control systems. Conduct audits, either in-person or remotely, to verify compliance with relevant standards, such as those established by the Global Food Safety Initiative (GFSI). For instance, a company importing seafood might require suppliers to be certified under the Marine Stewardship Council (MSC) or the Aquaculture Stewardship Council (ASC) standards.
- Product Testing and Inspection: Implement a robust product testing program, including laboratory analysis for contaminants, pathogens, and nutritional content. Conduct regular inspections of incoming shipments to assess product quality, packaging integrity, and labeling accuracy. The frequency and type of testing should be based on the product’s risk profile and regulatory requirements.
- Establishment of Critical Control Points (CCPs): Identify critical control points (CCPs) in the import process where hazards can be controlled. Implement monitoring procedures at each CCP to ensure that critical limits are met. For example, in the import of frozen meat, the CCP might be the temperature during storage and transportation.
- Traceability Systems: Implement a traceability system to track products throughout the supply chain, from the source to the consumer. This enables rapid identification and recall of products in the event of a food safety issue. Utilize lot coding, batch numbers, and electronic tracking systems to maintain detailed records of product movement.
- Proper Storage and Handling: Ensure that imported products are stored and handled under appropriate conditions to prevent contamination and spoilage. This includes maintaining correct temperature and humidity levels, preventing cross-contamination, and adhering to proper sanitation practices. For example, perishable goods should be stored in refrigerated or frozen storage facilities.
- Employee Training: Provide comprehensive training to all employees involved in the import process, covering food safety principles, quality control procedures, and hygiene practices. Regular training updates are essential to keep employees informed about the latest food safety regulations and best practices.
- Documentation and Record Keeping: Maintain detailed records of all quality control activities, including supplier audits, product testing results, inspection reports, and corrective actions. These records are crucial for demonstrating compliance with regulations and for investigating food safety incidents.
- Recall Plans: Develop and maintain a comprehensive recall plan to effectively manage product recalls in the event of a food safety issue. The plan should Artikel procedures for identifying and removing affected products from the market, notifying consumers, and communicating with regulatory authorities.
Common Food Safety Hazards and Control Measures
Food safety hazards can be biological, chemical, or physical in nature. Effective control measures are necessary to mitigate these hazards and ensure the safety of imported food products. The following table provides examples of common food safety hazards and corresponding control measures.
Hazard | Description | Potential Sources | Control Measures |
---|---|---|---|
Biological Hazards | Microorganisms that can cause foodborne illnesses. | Contaminated water, soil, or raw materials; poor hygiene practices; improper food handling. | Supplier audits; testing for pathogens (e.g., Salmonella, E. coli); proper cooking and storage temperatures; employee hygiene training; sanitation protocols. |
Chemical Hazards | Toxic substances that can contaminate food. | Pesticides, heavy metals, cleaning agents, food additives, allergens. | Supplier verification; testing for contaminants; adherence to approved additive lists; proper labeling; allergen control programs; residue testing. |
Physical Hazards | Foreign objects that can cause injury. | Glass, metal, plastic, stones, insects. | Supplier verification; inspection of raw materials; use of sieves and filters; metal detectors; employee training; pest control programs; proper packaging. |
Allergens | Proteins that can cause allergic reactions in sensitive individuals. | Presence of allergenic ingredients (e.g., peanuts, tree nuts, milk, eggs, soy, wheat, fish, shellfish). | Ingredient labeling; allergen control programs; segregation of allergenic ingredients; cleaning and sanitation protocols; employee training. |
Mycotoxins | Toxic substances produced by fungi. | Contaminated grains, nuts, and dried fruits; improper storage conditions. | Supplier audits; testing for mycotoxins (e.g., aflatoxins); proper storage conditions (temperature and humidity control); inspection of raw materials. |
Logistics and Transportation
The efficient movement of imported food products from origin to destination is crucial for maintaining their quality, safety, and shelf life. This involves a complex network of transportation, storage, and handling, often spanning vast distances and diverse environments. The selection of appropriate logistics and transportation methods significantly impacts the final cost and the integrity of the food products.
Modes of Transportation
Food imports rely on a variety of transportation modes, each with its own advantages and disadvantages depending on the type of food, distance, and urgency. Understanding these modes and their characteristics is vital for making informed logistical decisions.
- Sea Freight: This is the most common mode for long-distance food imports, particularly for bulk commodities and non-perishable goods. Ships offer high capacity and relatively low costs per unit. However, transit times are generally longer compared to other modes. Consider that the International Maritime Organization (IMO) has established regulations to ensure the safety and environmental protection of shipping, including the transportation of food products.
For example, refrigerated containers (reefers) are commonly used for transporting temperature-sensitive goods like frozen seafood or fresh produce.
- Air Freight: Air freight is ideal for time-sensitive and high-value food products, such as fresh fruits, vegetables, and specialty items. It offers significantly faster transit times compared to sea freight, minimizing the risk of spoilage. However, air freight is considerably more expensive and has limitations on the size and weight of shipments. The Federal Aviation Administration (FAA) in the United States, and similar organizations globally, regulate the transportation of food products by air, including packaging and labeling requirements.
- Land Transportation: Land transportation encompasses road and rail transport, and is typically used for domestic distribution after the food product has arrived at a port or airport. Road transport offers flexibility and door-to-door delivery, while rail transport is often more cost-effective for long distances and large volumes. Refrigerated trucks and railcars are essential for maintaining the cold chain for temperature-sensitive goods.
Consider that the European Union (EU) has specific regulations, like the Food Hygiene Package, that set out the requirements for the hygienic transport of food.
Selecting the Appropriate Mode of Transport
The selection of the most suitable mode of transport is a critical decision that depends on several factors. These factors should be carefully evaluated to minimize risks and ensure the food product arrives in optimal condition.
- Type of Food: Perishable goods, such as fresh produce, require refrigerated transport (reefers) by sea or air, depending on the distance and urgency. Non-perishable goods, like grains or canned foods, can be transported by less temperature-controlled methods.
- Destination: The destination’s infrastructure, including port facilities, road networks, and customs clearance procedures, influences the choice of transport mode. Remote locations may necessitate a combination of transport modes.
- Distance: Long distances generally favor sea freight for cost-effectiveness, while shorter distances might utilize land transport or air freight for faster delivery.
- Time Sensitivity: The shelf life of the food product dictates the required speed of transport. Perishable goods with short shelf lives demand faster modes like air freight or expedited sea freight.
- Cost: The total cost, including freight charges, insurance, and handling fees, must be considered. Balancing cost with the need for timely and safe delivery is crucial.
- Regulations: Compliance with international and national regulations, including food safety standards and import/export requirements, is essential for selecting the appropriate mode of transport and associated documentation.
Managing Cold Chain Logistics
Maintaining the cold chain is paramount for preserving the quality, safety, and shelf life of temperature-sensitive food products. This involves a continuous and unbroken series of refrigerated operations, from the point of origin to the final consumer.
- Temperature Control: Strict temperature control throughout the supply chain is critical. This includes pre-cooling at the origin, using refrigerated storage and transport, and monitoring temperatures at all stages. The temperature range must be appropriate for the specific food product, as specified by the manufacturer and regulatory bodies. For example, frozen foods must be kept at -18°C (0°F) or below to prevent bacterial growth and maintain quality.
- Refrigerated Equipment: Using reliable refrigerated containers (reefers), trucks, and storage facilities is essential. Regular maintenance and calibration of refrigeration equipment are crucial to ensure accurate temperature control.
- Monitoring and Recording: Continuous temperature monitoring and recording are necessary to track the cold chain integrity. Temperature data loggers are used to monitor and record temperatures throughout the journey. Any deviations from the required temperature range must be addressed immediately.
- Packaging: Proper packaging, including insulated containers and appropriate refrigerants, is essential to maintain the cold chain during transport. The packaging should protect the food from temperature fluctuations and physical damage.
- Coordination and Communication: Effective communication and coordination between all stakeholders in the supply chain, including suppliers, transporters, and storage facilities, are vital for maintaining the cold chain. Clear protocols and procedures must be established to address any potential issues.
- Examples and Data:
Consider the case of avocado imports from Mexico to the United States. A study by the University of California, Davis, showed that maintaining a consistent temperature of 5°C (41°F) throughout the cold chain significantly extended the shelf life of avocados, reducing spoilage and waste. This highlights the importance of cold chain management in ensuring food quality and minimizing economic losses.
Customs Clearance and Compliance
Navigating the intricate world of customs clearance is a critical step in the food import process. Compliance with regulations ensures the safe and legal entry of food products into a country. Understanding the role of key players, anticipating potential challenges, and implementing best practices are essential for a smooth and efficient import experience.
The Role of Customs Brokers in the Food Import Process
Customs brokers act as intermediaries between importers and customs authorities, facilitating the clearance of imported goods. Their expertise in customs regulations, documentation, and procedures makes them invaluable to food importers.
The primary responsibilities of a customs broker include:
- Document Preparation and Submission: Brokers prepare and submit all necessary documentation, such as import declarations, commercial invoices, packing lists, and certificates of origin. They ensure accuracy and completeness to avoid delays or penalties.
- Duty and Tax Calculation: They calculate the duties, taxes, and fees owed on the imported food products based on their classification and value.
- Compliance with Regulations: Brokers stay abreast of constantly evolving customs regulations and ensure that the imported food products comply with all relevant requirements, including food safety standards and labeling regulations.
- Liaison with Customs Authorities: They act as the primary point of contact with customs officials, responding to inquiries, resolving any issues, and facilitating inspections or examinations.
- Bonding and Surety: Customs brokers often provide or assist with obtaining the necessary bonds and surety required by customs authorities.
For example, consider a food importer bringing in a shipment of frozen shrimp. The customs broker would be responsible for accurately classifying the shrimp under the Harmonized System (HS) code, determining the applicable duty rate, and ensuring that the shipment complies with the importing country’s food safety regulations, such as those set by the Food and Drug Administration (FDA) in the United States or the Food Standards Agency (FSA) in the United Kingdom.
The broker would also handle all communication with customs officials, including any necessary inspections or examinations of the shrimp.
Common Challenges Encountered During Customs Clearance
Customs clearance can be a complex process, and food importers often encounter various challenges that can lead to delays, increased costs, or even rejection of their shipments.
Common challenges include:
- Incorrect Documentation: Inaccurate or incomplete documentation is a leading cause of delays. This can include errors in the commercial invoice, packing list, or certificates of origin.
- Product Classification Errors: Misclassifying food products under the wrong HS code can result in incorrect duty rates and potential penalties.
- Non-Compliance with Food Safety Regulations: Failure to meet food safety standards, such as those related to labeling, ingredients, or contaminants, can lead to rejection of the shipment.
- Delays in Inspection: Customs inspections can cause significant delays, particularly if the inspection process is thorough or if the authorities require additional information or testing.
- Changes in Regulations: Customs regulations are subject to change, and importers must stay informed of any updates to ensure compliance.
- Port Congestion: High traffic volume at ports can lead to delays in processing shipments, including customs clearance.
For instance, a food importer might face delays if the commercial invoice for a shipment of imported coffee beans incorrectly states the country of origin, or if the labeling on a container of imported olive oil does not meet the requirements for the country of import. These errors can trigger further inspections and may require corrections, leading to delays and potential storage fees.
In some cases, the importer may be required to re-label the product, which can be costly and time-consuming.
Tips for Ensuring Smooth Customs Clearance and Compliance with Regulations
Proactive measures can significantly improve the chances of a smooth customs clearance process and ensure compliance with regulations.
Strategies for smooth customs clearance:
- Partner with a Reputable Customs Broker: Selecting a knowledgeable and experienced customs broker is crucial. The broker should have a strong understanding of the specific regulations related to food imports and a proven track record of successful clearances.
- Ensure Accurate and Complete Documentation: Meticulous attention to detail is essential. Importers should verify the accuracy of all documentation, including invoices, packing lists, and certificates of origin, before submitting them to customs.
- Proper Product Classification: Correctly classifying food products under the appropriate HS codes is critical for accurate duty calculations and compliance. Importers should consult with their customs broker or other experts to ensure proper classification.
- Comply with Food Safety Regulations: Food importers must adhere to all relevant food safety standards and labeling requirements. This includes ensuring that the products are safe for consumption, properly labeled, and free from prohibited substances.
- Conduct Pre-Import Inspections: Consider conducting pre-import inspections of food products at the origin country to identify and address any potential issues before shipment.
- Stay Informed of Regulatory Changes: Customs regulations are subject to change, so importers must stay up-to-date on the latest requirements and updates.
- Maintain Clear Communication: Effective communication with the customs broker, suppliers, and other stakeholders is essential for resolving any issues that may arise during the clearance process.
- Utilize Technology: Implement technology solutions, such as electronic data interchange (EDI) systems, to streamline the documentation process and improve communication with customs authorities.
For example, consider a food importer who is bringing in a shipment of organic tea. To ensure smooth customs clearance, the importer should work closely with a customs broker who specializes in food imports and is familiar with the specific regulations related to organic products. The importer should also provide the broker with all necessary documentation, including certificates of origin, organic certification, and detailed product information.
Before shipment, the importer could arrange for a pre-import inspection to verify that the tea meets all relevant organic standards and labeling requirements. By following these steps, the importer can minimize the risk of delays and ensure that the shipment is cleared quickly and efficiently.
Risk Management and Mitigation
Food import groups operate in a complex and dynamic environment, subject to a multitude of risks that can significantly impact profitability, supply chain integrity, and consumer safety. Proactive risk management is crucial for ensuring business continuity and minimizing potential losses. This section delves into the various risks inherent in food imports and Artikels effective strategies for mitigating them.
Potential Risks Associated with Food Imports
Food import groups face a spectrum of risks, originating from various sources. These risks can be broadly categorized into several key areas. Understanding these risks is the first step toward effective mitigation.
- Supply Chain Disruptions: Disruptions can arise from natural disasters, political instability, infrastructure failures, and global pandemics. These events can lead to delays, shortages, and increased costs. For instance, the COVID-19 pandemic exposed the fragility of global food supply chains, with significant impacts on the availability and price of imported goods.
- Currency Fluctuations: Exchange rate volatility can significantly impact the cost of imported goods. A weakening domestic currency makes imports more expensive, reducing profit margins. Conversely, a strengthening currency can make exports less competitive. For example, a 10% devaluation of a country’s currency against the exporter’s currency directly translates to a 10% increase in the import cost.
- Regulatory Changes: Changes in import regulations, such as tariffs, quotas, and food safety standards, can disrupt import operations. These changes can lead to increased compliance costs, delays, and even the inability to import certain products. For example, new food labeling requirements can necessitate re-labeling products, incurring additional expenses and potentially causing delays in product distribution.
- Political and Economic Instability: Political unrest, trade wars, and economic downturns in exporting countries can disrupt supply chains and increase costs. Sanctions and trade restrictions can also limit access to certain products or markets. The impact of political instability can be seen in countries with ongoing conflicts, which often experience severe disruptions in agricultural production and export capabilities.
- Quality and Safety Issues: Contamination, spoilage, and non-compliance with food safety standards pose significant risks. These issues can lead to product recalls, legal liabilities, and damage to brand reputation. The 2018 romaine lettuce E. coli outbreak in the United States, linked to contaminated imports, is a clear example of the potential consequences.
- Transportation and Logistics Challenges: Issues such as port congestion, shipping delays, and transportation infrastructure limitations can disrupt the timely delivery of goods. The Suez Canal blockage in 2021, for example, caused significant delays and increased shipping costs worldwide.
Strategies for Mitigating Risks
Effective risk mitigation requires a proactive and multi-faceted approach. Several strategies can be employed to reduce the impact of the identified risks.
- Diversification of Suppliers and Sources: Sourcing from multiple suppliers and countries reduces dependence on any single source, mitigating the impact of supply chain disruptions. Diversification also allows for price negotiation and access to a wider range of products.
- Hedging Against Currency Fluctuations: Utilizing financial instruments like forward contracts and currency options can protect against adverse currency movements. These instruments allow importers to lock in exchange rates, ensuring predictable costs.
- Comprehensive Insurance Coverage: Obtaining appropriate insurance policies, including marine cargo insurance, political risk insurance, and product liability insurance, can protect against financial losses.
- Strong Supplier Relationships and Audits: Building strong relationships with suppliers and conducting regular audits to ensure compliance with quality and safety standards are critical. These actions help identify and address potential issues before they impact imports.
- Detailed Contingency Planning: Developing comprehensive contingency plans to address potential disruptions, including alternative sourcing options, transportation routes, and storage facilities, is essential for business continuity.
- Compliance and Regulatory Expertise: Maintaining a thorough understanding of import regulations and engaging with regulatory experts helps ensure compliance and minimizes the risk of non-compliance penalties.
- Real-Time Supply Chain Visibility: Implementing tracking systems and monitoring supply chain activities in real-time allows for prompt identification and response to potential disruptions.
Insurance Options for Food Import Groups
Insurance plays a vital role in protecting food import groups against various risks. A range of insurance options are available to address specific threats.
- Marine Cargo Insurance: This insurance protects against loss or damage to goods during transit, covering risks such as accidents, theft, and natural disasters. The policy covers the cost of goods, freight charges, and import duties.
- Political Risk Insurance: This insurance protects against losses resulting from political instability in exporting countries, including expropriation, war, and civil unrest. It safeguards investments and ensures business continuity.
- Product Liability Insurance: This insurance covers legal liabilities arising from product defects or food safety issues, including consumer claims, recalls, and legal expenses.
- Business Interruption Insurance: This insurance provides financial protection for lost income and ongoing expenses in the event of a business interruption caused by covered events, such as supply chain disruptions or natural disasters.
- Currency Fluctuation Insurance: While not a standard insurance product, some specialized financial institutions offer insurance or hedging solutions to mitigate the impact of currency fluctuations on import costs. This helps stabilize profit margins.
- Trade Credit Insurance: This insurance protects against the risk of non-payment by customers, covering losses resulting from customer insolvency or protracted default.
Market Trends and Opportunities
The global food import market is a dynamic landscape, constantly reshaped by consumer demand, technological advancements, and evolving geopolitical factors. Understanding these trends and the emerging opportunities is crucial for food import groups to thrive. This section will delve into the key market trends, highlight promising opportunities, and analyze the influence of consumer preferences and dietary habits on the industry.
Current Trends in the Global Food Import Market
Several significant trends are currently shaping the global food import market, creating both challenges and opportunities for businesses. These trends are interconnected and influence each other, leading to a complex and rapidly changing environment.
- Increased Demand for Convenience Foods: The fast-paced lifestyles of consumers worldwide have fueled a surge in demand for convenient food products. This includes ready-to-eat meals, pre-cut vegetables, and other prepared food items. According to a report by Mordor Intelligence, the global convenience food market was valued at USD 616.78 billion in 2022 and is projected to reach USD 875.93 billion by 2028, registering a CAGR of 6.03% during the forecast period (2023-2028).
This trend is particularly pronounced in urban areas where time is often a constraint. Food import groups can capitalize on this trend by importing ingredients and finished products that cater to this demand, such as frozen meals, instant noodles, and processed snacks.
- Growing Popularity of Plant-Based Foods: Consumer awareness of the environmental and health benefits of plant-based diets is driving a significant shift in food preferences. The market for plant-based alternatives to meat and dairy products is experiencing rapid growth. Data from the Good Food Institute indicates that the plant-based food market reached $7.4 billion in sales in 2021, up 6.2% from the previous year. This creates opportunities for food import groups to source and import plant-based ingredients, such as soy protein, pea protein, and various types of plant-based milks, as well as finished plant-based products.
- Rise of E-commerce and Online Food Delivery: The expansion of e-commerce and online food delivery platforms has significantly impacted the food import market. Consumers can now easily access a wider variety of imported food products from the comfort of their homes. The global online food delivery market is projected to reach $1.79 trillion by 2027, growing at a CAGR of 11.78% from 2020 to 2027, according to a report by Grand View Research.
This trend requires food import groups to adapt their logistics and distribution strategies to meet the demands of online retail, including efficient cold chain management and smaller order quantities.
- Emphasis on Sustainability and Ethical Sourcing: Consumers are increasingly concerned about the environmental and social impact of their food choices. This has led to a growing demand for sustainably sourced and ethically produced food products. Food import groups must prioritize sourcing from suppliers who adhere to sustainable practices, such as reducing carbon emissions, conserving water resources, and promoting fair labor practices. Certifications like Fair Trade and organic labels are becoming increasingly important for attracting consumers.
- Increased Scrutiny of Food Safety and Traceability: Food safety is a paramount concern for consumers and regulators alike. Traceability systems, which allow for tracking food products from origin to consumer, are becoming essential. Food import groups need to implement robust food safety protocols and traceability systems to ensure the safety and quality of their imported products and to comply with regulations. Technologies like blockchain are being used to enhance traceability and transparency in the supply chain.
Examples of Emerging Opportunities for Food Import Groups
New opportunities are constantly arising for food import groups to diversify their offerings and expand their market reach. These opportunities often arise from changing consumer preferences, technological advancements, and evolving trade regulations.
- Specialty and Ethnic Foods: The growing diversity of populations and increased travel experiences have fueled demand for specialty and ethnic foods. Food import groups can capitalize on this trend by importing authentic ingredients and finished products from various regions around the world. This includes items such as exotic fruits, spices, and traditional dishes. The global ethnic foods market is expected to reach USD 60.8 billion by 2027, according to a report by Market Research Future.
- Functional Foods and Nutraceuticals: Consumers are increasingly seeking foods with added health benefits, leading to a surge in demand for functional foods and nutraceuticals. These products often contain ingredients that provide specific health benefits, such as vitamins, minerals, and antioxidants. Food import groups can source and import ingredients like superfoods (e.g., chia seeds, quinoa), probiotics, and omega-3 fatty acids to meet this growing demand.
- Organic and Natural Foods: The market for organic and natural foods continues to grow as consumers prioritize health and wellness. Food import groups can focus on importing certified organic products and ingredients that meet stringent quality standards. This includes fruits, vegetables, grains, and other raw materials. The global organic food market is projected to reach $278.8 billion by 2027, according to a report by Allied Market Research.
- Frozen and Refrigerated Foods: Advancements in freezing and refrigeration technologies have expanded the possibilities for importing perishable goods. Food import groups can import a wider range of frozen and refrigerated foods, including fruits, vegetables, seafood, and prepared meals. This requires efficient cold chain management and adherence to strict food safety regulations.
- Personalized Nutrition: Advances in technology and data analytics are enabling personalized nutrition approaches. Food import groups can explore opportunities to import ingredients and products that cater to specific dietary needs and preferences, such as gluten-free, lactose-free, and allergen-free foods. This may involve sourcing specialized ingredients or partnering with companies that offer personalized nutrition solutions.
Impact of Consumer Preferences and Changing Dietary Habits on the Food Import Industry
Consumer preferences and dietary habits are major drivers of change in the food import industry. The evolving needs and desires of consumers directly influence the types of products that are imported, the sourcing strategies employed, and the marketing approaches used.
- Health and Wellness Focus: Consumers are increasingly focused on health and wellness, leading to a demand for healthier food options. This includes products that are low in sugar, fat, and sodium, as well as those that are rich in nutrients and antioxidants. Food import groups must respond to this trend by importing healthier ingredients and products, such as fruits, vegetables, whole grains, and lean proteins.
- Demand for Transparency and Traceability: Consumers want to know where their food comes from and how it is produced. This demand for transparency has led to a greater emphasis on traceability and ethical sourcing. Food import groups need to provide information about the origin of their products, the farming practices used, and the social and environmental impact of their supply chains. This includes providing certifications and labels.
- Rise of Vegetarian and Vegan Diets: The growing popularity of vegetarian and vegan diets has created a significant demand for plant-based foods. Food import groups must adapt by importing a wider variety of plant-based ingredients and finished products, such as plant-based meats, dairy alternatives, and vegan snacks. This involves sourcing ingredients like soy protein, pea protein, and various types of plant-based milks.
- Growing Interest in Ethnic Cuisines: The increasing diversity of populations and increased travel experiences have led to a growing interest in ethnic cuisines. Food import groups can capitalize on this trend by importing authentic ingredients and finished products from various regions around the world. This includes items such as spices, sauces, and traditional dishes.
- Influence of Social Media and Food Trends: Social media platforms and food bloggers play a significant role in shaping consumer preferences and driving food trends. Food import groups need to stay informed about the latest food trends and adapt their product offerings accordingly. This may involve sourcing new and innovative ingredients or developing products that align with popular dietary trends.
Technology and Innovation
The food import industry, traditionally reliant on manual processes and paper-based documentation, is undergoing a significant transformation driven by technological advancements. These innovations are streamlining operations, enhancing efficiency, and improving food safety across the supply chain. From automated documentation to predictive analytics, technology is reshaping how food import groups operate and compete in the global market.
Streamlining the Food Import Process
Technology plays a pivotal role in optimizing various stages of the food import process. This optimization encompasses aspects such as documentation, communication, and traceability, ultimately leading to reduced costs, faster processing times, and enhanced compliance.
- Automated Documentation: Digital platforms automate the creation, submission, and management of import documents. This includes customs declarations, bills of lading, and certificates of origin. Automation minimizes manual errors, accelerates processing, and ensures compliance with regulations. For example, electronic data interchange (EDI) systems allow for the seamless exchange of information between importers, customs agencies, and other stakeholders.
- Enhanced Communication: Real-time communication tools, such as cloud-based platforms and mobile applications, facilitate seamless information exchange between importers, suppliers, freight forwarders, and customs brokers. This improves coordination, reduces delays, and enables faster responses to issues. For example, blockchain technology can be used to create a secure and transparent record of transactions, allowing all parties involved to access the same information simultaneously.
- Improved Traceability: Technologies like radio-frequency identification (RFID) tags and barcode scanning enable comprehensive tracking of food products throughout the supply chain. This facilitates quick identification of the source of a product, allowing for rapid response in case of a food safety incident. This traceability also supports effective recall management and helps build consumer trust. For instance, in the case of a foodborne illness outbreak, tracing the product back to its origin can minimize the impact and prevent further spread.
- Data Analytics and Predictive Modeling: Analyzing historical data on import volumes, customs clearance times, and market trends enables food import groups to make informed decisions. Predictive models can forecast demand, optimize inventory levels, and anticipate potential disruptions in the supply chain. For example, using data on weather patterns, crop yields, and consumer preferences can help importers optimize their sourcing strategies and reduce the risk of supply shortages.
Innovative Technologies Used by Food Import Groups
Several innovative technologies are being adopted by food import groups to improve efficiency, reduce costs, and enhance food safety. These technologies are transforming various aspects of the import process, from sourcing to distribution.
- Blockchain Technology: This technology provides a secure, transparent, and immutable record of transactions, which can be used to track food products from origin to consumer. This increases transparency, improves traceability, and reduces the risk of fraud.
- Artificial Intelligence (AI): AI-powered systems are used for various tasks, including demand forecasting, supply chain optimization, and risk assessment. AI can analyze vast amounts of data to identify patterns, predict trends, and automate decision-making processes. For instance, AI algorithms can analyze historical import data, market trends, and consumer preferences to optimize inventory levels and reduce waste.
- Internet of Things (IoT): IoT devices, such as sensors and trackers, are used to monitor the condition of food products during transportation and storage. This includes monitoring temperature, humidity, and location, which is crucial for maintaining food quality and safety. For example, refrigerated containers equipped with IoT sensors can continuously monitor the temperature of perishable goods, ensuring that they are stored and transported within the required temperature range.
- Robotics and Automation: Robots and automated systems are used for various tasks, including warehousing, packaging, and labeling. This increases efficiency, reduces labor costs, and minimizes the risk of human error.
Technology: Blockchain-based Traceability System
Description: A system that utilizes blockchain technology to create a transparent and immutable record of a food product’s journey from its origin to the consumer. This system typically involves capturing data at various stages of the supply chain, such as farm, processing facility, transportation, and retail. This data is then recorded on a distributed ledger, making it accessible to all authorized parties.
Benefits:
- Enhanced traceability, allowing for quick identification of the source of a product in case of a food safety issue.
- Increased transparency, as all stakeholders have access to the same information.
- Reduced risk of fraud and counterfeiting.
- Improved efficiency in supply chain management.
Limitations:
- High implementation costs, including the need for specialized hardware and software.
- Requires the cooperation of all stakeholders in the supply chain.
- Data privacy concerns, as sensitive information may be stored on the blockchain.
- Scalability challenges, as the system needs to handle large volumes of data.
Wrap-Up: Food Import Group
In conclusion, the food import group plays a pivotal role in the modern global economy, connecting producers and consumers across vast distances. From understanding complex regulations to managing intricate logistics, their responsibilities are immense. The industry continues to evolve with the integration of new technologies and shifts in consumer preferences. By understanding the key players, procedures, and challenges within this industry, stakeholders can navigate the complexities of global food trade more effectively, ensuring the availability of safe, high-quality food for consumers worldwide.
The future of the food import group will be defined by innovation, adaptability, and a commitment to sustainable practices, ultimately shaping the global food landscape for years to come.