Alright, let’s talk about food industry safety shoes. Yeah, those clunky things you see everyone wearing in the kitchen, the factory, and everywhere in between. I bet you never thought about how crucial these things are, right? Wrong! They’re not just some random footwear; they’re the unsung heroes of the food world, saving your toes from becoming a culinary disaster.
Think about it: slippery floors, dropped knives, rogue machinery… it’s a jungle out there, and your feet are the explorers.
This isn’t just about avoiding a toe-related tragedy, either. We’re diving deep into the materials, the standards, and the downright weirdness of shoe designs. We’ll explore the materials that make these shoes indestructible, the standards that make them safe, and the different types of shoes you might need, from the boots that protect you from a flood of milk to the clogs that let you run around the bakery like a pastry-fueled ninja.
Plus, we’ll look at how to keep these bad boys clean, comfortable, and, most importantly, protecting your precious little piggies.
Introduction to Food Industry Safety Footwear
Food processing environments present unique challenges, demanding stringent safety protocols to protect workers and ensure product integrity. Safety footwear plays a critical role in this framework, acting as the first line of defense against a multitude of hazards. From preventing slips and falls to shielding against chemical spills and impact injuries, the right footwear is paramount for a safe and productive workplace.
Its significance extends beyond personal safety, contributing to the overall efficiency and hygiene standards crucial in food production.
Historical Development of Food Industry Safety Footwear
The evolution of safety footwear for food handling reflects the industry’s increasing awareness of workplace hazards and the need for enhanced protection. Early footwear often provided minimal protection, primarily focusing on durability.The need for specialized footwear grew in parallel with the development of food processing technologies and the understanding of workplace risks. Early developments included the incorporation of steel toe caps to protect against falling objects.
The mid-20th century saw the introduction of waterproof materials and slip-resistant soles, addressing the challenges posed by wet and greasy environments. Innovations in materials science further advanced the capabilities of safety footwear. Modern safety shoes incorporate advanced features such as chemical resistance, puncture resistance, and ergonomic designs to maximize comfort and protection. This ongoing development is a testament to the food industry’s commitment to worker safety.
Primary Hazards Mitigated by Safety Shoes in the Food Industry
Food processing environments are fraught with potential dangers, and safety shoes are designed to address a variety of these risks. Effective safety footwear significantly reduces the likelihood of workplace injuries and illnesses.Here are some of the primary hazards that safety shoes mitigate:
- Slips and Falls: The presence of water, oils, and grease on floors creates a significant slip and fall hazard. Safety shoes with slip-resistant soles, often made from specialized rubber or polyurethane compounds, provide superior traction, reducing the risk of accidents.
- Impact and Compression: Heavy objects, such as machinery components or falling food products, pose a risk of foot injuries. Steel-toe or composite-toe safety shoes offer protection against impact and compression, preventing serious foot damage.
- Puncture Wounds: Sharp objects, such as broken glass, metal shards, or bone fragments, can puncture the soles of shoes. Puncture-resistant soles, often made from steel or other durable materials, prevent these injuries.
- Chemical Exposure: Food processing often involves the use of cleaning agents, sanitizers, and other chemicals. Safety shoes made from chemical-resistant materials protect against skin irritation and burns caused by these substances. For example, shoes made from nitrile rubber are often used because of their resistance to oils and chemicals.
- Temperature Extremes: Certain food processing operations, such as freezing or cooking, expose workers to extreme temperatures. Insulated safety shoes provide protection against both cold and heat, preventing frostbite or burns.
- Electrical Hazards: In environments where electrical equipment is used, safety shoes with electrical hazard (EH) protection provide insulation against electric shock. This feature is crucial for worker safety.
Materials and Construction of Food Industry Safety Shoes
The selection of materials and the construction methods employed in food industry safety shoes are critical to ensuring worker safety, hygiene, and comfort. These factors directly impact the shoe’s ability to withstand the harsh environments common in food processing and handling, including exposure to water, chemicals, and extreme temperatures. Understanding the properties of different materials allows for informed decisions, balancing protection, durability, and cost-effectiveness.
Common Materials Used
Several materials are commonly used in the manufacture of food industry safety shoes, each offering distinct advantages and disadvantages. These materials contribute to the overall performance of the shoe, influencing its resistance to hazards, its lifespan, and its ease of maintenance.
- Rubber: Rubber is a popular choice for soles due to its excellent slip resistance and durability. It provides good grip on wet and oily surfaces, minimizing the risk of slips and falls.
- Polyurethane (PU): PU is often used for both soles and midsoles. It offers good shock absorption, lightweight properties, and resistance to oil and chemicals. PU can be molded into complex shapes, allowing for enhanced comfort and ergonomic design.
- Polyvinyl Chloride (PVC): PVC is a cost-effective material used primarily for the uppers of safety shoes. It is waterproof and resistant to many chemicals. However, it may not be as durable or flexible as other materials, especially in extreme temperatures.
- Thermoplastic Polyurethane (TPU): TPU is a thermoplastic elastomer that is often used in soles, offering a balance of flexibility, durability, and abrasion resistance. It is also resistant to oil and many chemicals, making it suitable for various food industry applications.
- Leather: Leather is used for uppers, providing durability and breathability. Treated leather offers resistance to water and certain chemicals. However, it requires regular maintenance and may not be suitable for environments with heavy exposure to liquids or harsh chemicals.
Advantages and Disadvantages of Each Material
Each material used in the construction of food industry safety shoes presents a unique set of benefits and drawbacks. The optimal choice depends on the specific hazards and requirements of the work environment. A thorough understanding of these properties is crucial for selecting the most appropriate footwear.
- Rubber:
- Advantages: Excellent slip resistance, high durability, good abrasion resistance, waterproof.
- Disadvantages: Can be heavy, may degrade in contact with certain chemicals, can be less flexible than other materials.
- Polyurethane (PU):
- Advantages: Lightweight, good shock absorption, resistant to oil and many chemicals, can be molded into complex shapes.
- Disadvantages: Can degrade over time with exposure to water and certain chemicals, may have a shorter lifespan than rubber in some applications.
- Polyvinyl Chloride (PVC):
- Advantages: Waterproof, relatively inexpensive, resistant to many chemicals.
- Disadvantages: Less durable than other materials, less flexible, can crack or become brittle in cold temperatures.
- Thermoplastic Polyurethane (TPU):
- Advantages: Good balance of flexibility and durability, resistant to oil and many chemicals, excellent abrasion resistance.
- Disadvantages: Can be more expensive than PVC, may not offer the same level of slip resistance as rubber in certain conditions.
- Leather:
- Advantages: Durable, breathable, comfortable, can be treated for water resistance.
- Disadvantages: Requires regular maintenance, can be less resistant to water and chemicals compared to synthetic materials, can be more expensive.
Comparison of Shoe Material Properties
The following table compares the durability, slip resistance, and chemical resistance of the materials discussed. The ratings are relative and based on industry standards and typical performance characteristics.
Material | Durability | Slip Resistance | Chemical Resistance |
---|---|---|---|
Rubber | High | Excellent | Good (varies by chemical) |
Polyurethane (PU) | Medium | Good | Good (oil & some chemicals) |
Polyvinyl Chloride (PVC) | Low to Medium | Fair | Good (some chemicals) |
Thermoplastic Polyurethane (TPU) | Medium to High | Good | Good (oil & many chemicals) |
Leather | Medium | Fair | Fair (water & some chemicals) |
Safety Features and Standards
Ensuring worker safety is paramount in the food industry. Safety footwear plays a crucial role in mitigating risks associated with various workplace hazards. This section details the essential safety features, relevant international standards, and the correlation between potential hazards and the protective shoe features designed to address them.
Essential Safety Features
Food industry safety shoes are engineered with specific features to protect workers from a variety of dangers. These features are critical for minimizing the risk of injury and ensuring a safe working environment.
- Toe Protection: This is a fundamental safety feature, typically provided by steel or composite toe caps. They protect the toes from impact and compression injuries caused by falling objects or accidental impacts. For instance, a chef accidentally dropping a heavy pot requires this feature to prevent serious foot trauma.
- Slip Resistance: Slip-resistant outsoles are essential in environments where wet or oily surfaces are common. These outsoles are designed with specific tread patterns and materials to maximize grip and reduce the risk of slips and falls. Consider a food processing plant where water and oil spills are frequent; slip-resistant shoes are vital to prevent accidents.
- Penetration Resistance: This feature, often incorporated through a midsole, protects the foot from punctures caused by sharp objects, such as nails or broken glass. This is crucial in areas where debris may be present, like a loading dock or a kitchen.
- Metatarsal Protection: Some shoes offer metatarsal guards, providing protection to the metatarsal bones in the upper foot from impact and crushing injuries. This is especially important in environments where heavy objects are handled or where machinery is used.
- Electrical Hazard Protection (EH): EH-rated shoes are designed to resist electrical shock. They provide an extra layer of insulation and are essential in environments where electrical hazards exist, such as near electrical equipment or in areas with exposed wiring.
- Chemical Resistance: Food industry environments often involve exposure to various chemicals, including cleaning agents and food processing substances. Chemical-resistant shoes are constructed from materials that resist degradation from these chemicals, protecting the foot from chemical burns and irritations.
International Safety Standards and Certifications
Compliance with international safety standards is crucial for ensuring the effectiveness and reliability of safety footwear. These standards provide a framework for manufacturers to design and test shoes, ensuring they meet specific performance criteria.
- ASTM International (American Society for Testing and Materials): ASTM standards are widely recognized in North America. They define performance requirements for various safety features. For example, ASTM F2413-18 Artikels requirements for protective footwear, including impact resistance, compression resistance, and electrical hazard protection.
- EN ISO (European Norm – International Organization for Standardization): EN ISO standards are prevalent in Europe and other parts of the world. EN ISO 20345 specifies requirements for safety footwear, including toe protection, slip resistance, and penetration resistance. The standard is divided into various categories based on the level of protection provided. For example, S1P footwear offers toe protection, slip resistance, and penetration resistance.
- Certifications: Footwear that meets the requirements of these standards will typically bear a certification mark, such as the ASTM or EN ISO symbol, indicating that the footwear has been tested and certified by an accredited laboratory. This certification provides assurance to the wearer that the footwear meets the required safety standards.
Hazards and Corresponding Shoe Features
The food industry presents various potential hazards, and safety footwear is designed to address these risks effectively. The following table illustrates the relationship between potential hazards and the corresponding shoe features:
Potential Hazard | Corresponding Shoe Feature | Example |
---|---|---|
Falling objects | Toe protection (steel or composite toe cap) | A box of canned goods falling onto a worker’s foot. |
Slippery surfaces | Slip-resistant outsole | Spilled oil or water in a kitchen or processing area. |
Punctures from sharp objects | Penetration-resistant midsole | Stepping on a nail or piece of broken glass. |
Electrical hazards | Electrical hazard (EH) protection | Working near electrical equipment or exposed wiring. |
Chemical exposure | Chemical-resistant materials | Exposure to cleaning agents or food processing chemicals. |
Impact to the metatarsal area | Metatarsal protection | Dropping a heavy object onto the top of the foot. |
Types of Food Industry Safety Shoes
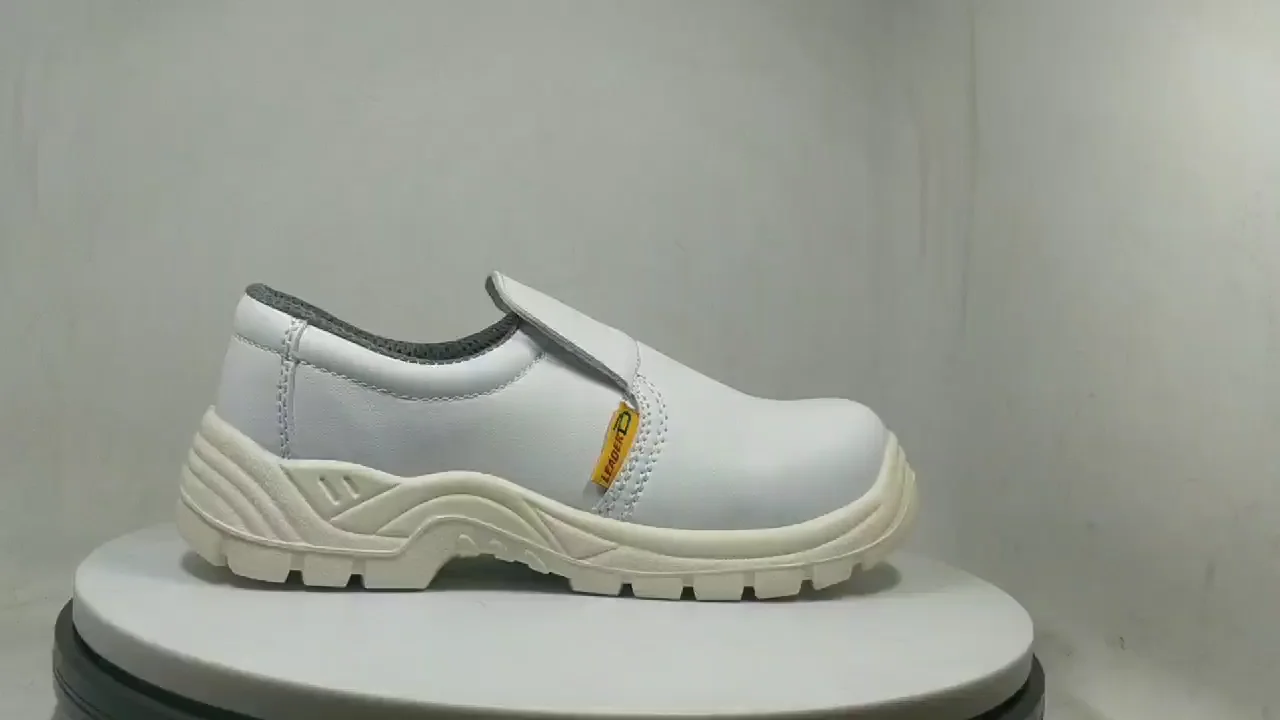
The food industry demands a diverse range of safety footwear to protect workers from various hazards. The choice of shoe type depends heavily on the specific tasks performed and the environment encountered. Selecting the correct footwear is crucial for ensuring worker safety and preventing contamination.
Boots in Food Processing Environments
Boots are a staple in many food processing environments due to their superior protection and coverage. They offer robust defense against spills, impacts, and potential puncture hazards. Boots are available in various materials and designs to meet specific needs.Boots provide:
- Enhanced ankle support, critical in environments with uneven surfaces or heavy lifting.
- Greater protection against liquid ingress, safeguarding feet from exposure to water, chemicals, and food products.
- Often feature higher cut designs to protect the lower leg.
For instance, in meat processing plants, waterproof and slip-resistant boots are essential. Butchers require boots with steel or composite toes to protect against dropped objects and sharp tools. The soles are designed with aggressive tread patterns to provide traction on wet and greasy floors. Boots also often have features like metatarsal guards for added protection.
Clogs in Food Industry Applications
Clogs offer a different approach to safety footwear, prioritizing ease of use and hygiene. They are commonly chosen for tasks requiring frequent movement and where ease of cleaning is paramount. Clogs are often preferred in areas with minimal impact hazards.Consider these features:
- Easy to slip on and off, making them convenient for workers who need to change footwear frequently.
- Typically made from waterproof materials, facilitating easy cleaning and sanitization.
- Often feature closed-toe designs to protect against minor impacts and spills.
Clogs are frequently utilized in food preparation areas, such as kitchens and bakeries. Their easy-to-clean surfaces and slip-resistant soles help maintain hygiene standards. A chef, for example, might choose a clog with a closed toe and arch support for comfort during long hours on their feet. Clogs are also useful in environments where workers move between different areas frequently.
Sneakers in Food Production Settings
Safety sneakers combine the comfort of athletic shoes with the protective features required in food industry environments. They are a popular choice for tasks involving moderate physical activity and where a lighter weight is preferred. Safety sneakers are designed to be both functional and comfortable.The advantages include:
- Providing a more flexible and lightweight option compared to boots.
- Offering good breathability, which can reduce foot fatigue during extended use.
- Featuring slip-resistant soles and often, steel or composite toes for impact protection.
Sneakers are suitable for tasks such as food packaging and light processing duties. For example, a worker in a packaging facility might wear safety sneakers with a steel toe to protect against falling boxes and a slip-resistant sole to prevent falls on slippery surfaces. The breathability of the sneaker can also contribute to comfort during active work.
Slip Resistance and Traction
In the demanding environment of the food industry, where floors are frequently wet, greasy, or contaminated with food substances, slip resistance in safety footwear is paramount. Slips and falls are a leading cause of workplace injuries, resulting in lost productivity, medical expenses, and potential legal liabilities. Therefore, selecting and understanding the slip resistance characteristics of safety shoes is crucial for worker safety and operational efficiency.
Significance of Slip Resistance
The food industry presents a high risk of slips and falls due to the presence of water, oils, fats, and food debris on floors. These contaminants reduce the friction between the shoe sole and the walking surface, increasing the likelihood of slips. Injuries resulting from slips and falls can range from minor bruises and sprains to severe fractures and head injuries.
Beyond the physical harm to workers, these incidents also carry significant financial consequences for businesses.
Factors Contributing to Slip Resistance
Several factors contribute to the slip resistance of safety shoes, primarily focusing on the sole design and the materials used. The interaction between these elements determines the level of grip and traction provided by the footwear.
- Sole Design: The design of the sole is critical for channeling away liquids and providing a gripping surface.
- Tread Pattern: A well-designed tread pattern is essential. Deep, widely spaced treads provide channels for fluids to escape, maximizing contact between the sole and the floor. Patterns with multi-directional grooves offer improved grip in various directions.
- Lug Design: The size, shape, and arrangement of lugs (the raised portions of the sole) influence the shoe’s grip. Lugs with sharp edges and a wide surface area typically provide better traction.
- Sole Material: The material of the sole significantly impacts slip resistance.
- Rubber Compounds: Rubber soles, especially those made from specialized compounds, are known for their excellent grip on wet and oily surfaces. The specific formulation of the rubber can be tailored to optimize performance in various environments.
- Polyurethane (PU): PU soles are also common, offering good slip resistance and durability. However, the specific type of PU and its formulation influence the level of grip.
- Surface Contact Area: The amount of surface area in contact with the floor influences grip. Soles with a larger contact area tend to provide better stability.
- Durometer Hardness: The hardness of the sole material, measured using a durometer, can affect slip resistance. Softer soles often provide better grip on smooth surfaces, while harder soles may be more suitable for rougher environments.
Testing Slip Resistance with a Standardized Procedure
Standardized testing procedures are crucial for evaluating the slip resistance of safety shoes. These tests provide a consistent and objective way to measure the performance of footwear under controlled conditions. A widely recognized standard for slip resistance testing is the ASTM F2913-23, Standard Test Method for Footwear Slip Resistance Measurement Using a Walking Test.
The ASTM F2913-23 involves the following steps:
- Preparation:
- The test surface (e.g., ceramic tile, linoleum) is cleaned and prepared according to the standard.
- A lubricant (e.g., soapy water, vegetable oil) is applied to the test surface to simulate slippery conditions.
- Equipment:
- The test utilizes a walking test machine equipped with sensors to measure the dynamic coefficient of friction (DCOF).
- The machine simulates a walking motion, applying a controlled force to the shoe sample.
- Procedure:
- The safety shoe is securely attached to the test machine.
- The machine performs a series of controlled walking cycles across the lubricated surface.
- The sensors measure the force required to overcome friction during the walking motion.
- Data Analysis:
- The DCOF is calculated based on the force measurements.
- The DCOF value represents the shoe’s slip resistance; a higher DCOF indicates better grip.
- Classification:
- The shoes are then classified based on their DCOF value, which is often used to meet standards such as those set by the Occupational Safety and Health Administration (OSHA).
The DCOF value is a key indicator, and a value of 0.4 or higher is generally considered acceptable for footwear in the food industry, but this can vary depending on the specific requirements and hazards of the workplace.
Hygiene and Cleanliness
Maintaining impeccable hygiene is paramount in the food industry, extending beyond just the food itself to encompass every aspect of the production environment, including footwear. Safety shoes, acting as a crucial barrier between workers and potential hazards, can also become vectors for contamination if not properly managed. This section details the critical importance of hygiene in food industry footwear, outlining effective cleaning and sanitizing procedures, and providing a comprehensive checklist for maintaining optimal cleanliness.
Importance of Hygiene in Food Industry Footwear
Footwear in food processing environments can easily accumulate food particles, spills, and microorganisms, creating a breeding ground for bacteria and fungi. Contaminated footwear can then spread these pathogens throughout the facility, leading to cross-contamination of food products and posing significant risks to consumer health and safety. Moreover, poor hygiene can lead to the deterioration of the shoes themselves, reducing their lifespan and compromising their protective features.
Implementing robust hygiene protocols for safety shoes is therefore essential for minimizing these risks, ensuring food safety, and maintaining a clean and compliant work environment.
Procedures for Cleaning and Sanitizing Food Industry Safety Shoes
Effective cleaning and sanitizing of safety shoes require a systematic approach, utilizing appropriate cleaning agents and following established protocols. The frequency of cleaning will depend on the specific work environment and the level of potential contamination. The following steps Artikel a general procedure:
- Preparation: Before cleaning, ensure the shoes are free of any loose debris. Remove any insoles and laces, cleaning them separately. If the shoes are heavily soiled, consider pre-rinsing them with water to remove excess dirt.
- Cleaning: Use a mild detergent and warm water to wash the shoes. Avoid harsh chemicals that could damage the materials. Apply the detergent with a brush or sponge, paying particular attention to areas prone to contamination, such as the soles, seams, and the upper part of the shoe. Rinse thoroughly with clean water to remove all traces of detergent.
- Sanitizing: After cleaning, sanitize the shoes to eliminate any remaining microorganisms. Use a food-grade sanitizing solution, following the manufacturer’s instructions for dilution and application. Some common sanitizing agents include quaternary ammonium compounds or diluted bleach solutions. Ensure the sanitizing solution comes into contact with all surfaces of the shoe.
- Drying: Allow the shoes to air dry completely in a well-ventilated area. Avoid using direct heat sources, such as dryers or radiators, as this can damage the materials. Reinsert the clean insoles and laces once the shoes are completely dry.
Checklist for Maintaining the Hygiene of Safety Shoes, Food industry safety shoes
Regular maintenance is key to ensuring the long-term hygiene and effectiveness of safety shoes. This checklist provides a framework for establishing a consistent cleaning and sanitizing routine:
Activity | Frequency | Method |
---|---|---|
Inspection for Damage | Daily | Visually inspect shoes for any signs of wear and tear, such as cracks, tears, or loose seams. Replace damaged shoes immediately. |
Removal of Loose Debris | Daily (at the end of each shift) | Brush or wipe down shoes to remove any loose dirt, food particles, or spills. |
Cleaning | Weekly or as needed (more frequently if heavily soiled) | Wash shoes with mild detergent and warm water, scrubbing all surfaces thoroughly. Rinse completely. |
Sanitizing | Weekly or as needed (more frequently if heavily soiled) | Apply a food-grade sanitizing solution to all surfaces of the shoes, following the manufacturer’s instructions. |
Drying | After Cleaning and Sanitizing | Allow shoes to air dry completely in a well-ventilated area. |
Insole and Laces Cleaning/Replacement | Weekly or as needed | Wash insoles and laces separately with detergent and water. Replace if worn or damaged. |
Storage | Daily (when not in use) | Store shoes in a designated area, away from potential sources of contamination. Ensure the storage area is clean and dry. |
Proper hygiene practices, including regular cleaning and sanitizing of safety shoes, are crucial for preventing cross-contamination and maintaining a safe food production environment. Adhering to this checklist and implementing these procedures helps to protect both workers and consumers.
Comfort and Ergonomics
The often-overlooked aspect of food industry safety footwear, comfort and ergonomics, significantly impacts worker well-being, productivity, and, ultimately, safety. Ill-fitting or uncomfortable shoes can lead to a cascade of negative consequences, ranging from minor inconveniences to serious injuries. Prioritizing these factors is not just about employee satisfaction; it’s a crucial investment in operational efficiency and a proactive approach to mitigating workplace hazards.
Impact of Shoe Comfort on Worker Productivity and Safety
Comfortable safety shoes are essential for maintaining worker productivity and ensuring a safe work environment. Uncomfortable footwear can lead to a range of issues that directly affect these crucial aspects.
Investigate the pros of accepting chinese food in hinesville ga in your business strategies.
- Reduced Productivity: Discomfort from poorly designed or ill-fitting shoes can distract workers, making it difficult to concentrate on their tasks. This can slow down work processes and decrease overall output. For example, a study by the National Safety Council found that employees experiencing foot pain were significantly less productive than their pain-free counterparts. This productivity loss can translate into tangible financial consequences for food processing facilities.
- Increased Risk of Accidents: Uncomfortable shoes can alter a worker’s gait and balance, increasing the likelihood of slips, trips, and falls. Pain and fatigue can also impair reaction times, making it more difficult to respond quickly to potential hazards. The Food and Drug Administration (FDA) regularly reports on workplace injuries in food processing facilities, many of which are attributed to slips and falls.
- Musculoskeletal Disorders (MSDs): Prolonged standing and walking in uncomfortable shoes can contribute to the development of MSDs, such as plantar fasciitis, back pain, and knee problems. These conditions can lead to absenteeism, reduced work capacity, and costly medical expenses. The Bureau of Labor Statistics consistently reports that MSDs are a significant cause of workplace injuries in the manufacturing sector, including food processing.
- Employee Morale and Retention: Providing comfortable safety footwear demonstrates a commitment to employee well-being, boosting morale and improving job satisfaction. This, in turn, can lead to reduced employee turnover and lower recruitment costs. A comfortable work environment contributes to a more positive and engaged workforce.
Ergonomic Features that Enhance Comfort and Support in Safety Shoes
Ergonomic design plays a crucial role in enhancing the comfort and support provided by safety shoes. Several features are specifically incorporated to address the unique demands of the food industry, promoting worker well-being and reducing the risk of injury.
- Cushioning and Shock Absorption: Shoes with ample cushioning in the midsole and insole help absorb the impact of walking and standing, reducing stress on the feet, ankles, and knees. Materials like polyurethane or gel inserts are commonly used to provide effective shock absorption. This is particularly important for workers who spend long hours on their feet on hard surfaces.
- Arch Support: Proper arch support helps distribute weight evenly across the foot, preventing overpronation and supination, which can lead to foot pain and fatigue. Safety shoes often incorporate built-in arch supports or removable insoles that can be customized to individual foot types.
- Breathable Materials: The use of breathable materials, such as mesh or perforated uppers, helps to promote airflow and reduce the build-up of heat and moisture inside the shoe. This is crucial for maintaining foot comfort and preventing the growth of bacteria, which can contribute to foot odor and skin irritation.
- Flexible Soles: Soles that are flexible in the forefoot allow for natural foot movement, reducing strain and promoting comfort during walking and bending. This is especially important for workers who frequently squat or kneel.
- Contoured Footbeds: Footbeds that are molded to the shape of the foot provide enhanced support and reduce pressure points. These footbeds often incorporate features like metatarsal support to alleviate stress on the ball of the foot.
- Lightweight Construction: Reducing the overall weight of the shoe can significantly improve comfort and reduce fatigue, particularly for workers who spend long hours on their feet. Modern safety shoes often utilize lightweight materials without compromising on safety features.
Methods for Selecting the Correct Shoe Size and Fit to Optimize Comfort
Choosing the correct shoe size and ensuring a proper fit are fundamental to maximizing the comfort and effectiveness of safety footwear. Several methods and considerations are crucial for achieving the optimal fit.
- Accurate Measurement: The foot should be measured accurately, ideally at the end of the day when the feet are at their largest. Use a Brannock device or a similar tool to measure both length and width.
- Consideration of Sock Thickness: When measuring, wear the type of socks that will be worn with the safety shoes. This will ensure that the shoe size accounts for the extra bulk of the socks.
- Trying On Shoes: Always try on shoes before purchasing them, preferably in the afternoon or evening. Walk around in the shoes to assess the fit and comfort.
- Checking for Adequate Toe Room: There should be approximately a thumb’s width of space between the longest toe and the end of the shoe. This allows for natural foot movement and prevents the toes from being cramped.
- Assessing the Heel Fit: The heel should fit snugly in the shoe, with minimal slippage. The heel counter should provide good support and prevent the foot from moving excessively.
- Width Considerations: The width of the shoe should accommodate the width of the foot without feeling overly tight or constricting. A shoe that is too narrow can cause blisters and other foot problems.
- Utilizing Shoe Charts and Guides: Refer to shoe size charts provided by the manufacturer, as sizing can vary between brands. Consider using online fit guides to assist in the selection process.
- Professional Fitting: Seek professional fitting assistance from a footwear specialist, especially if you have any foot conditions or require custom orthotics.
- Regular Fit Checks: Periodically re-evaluate the fit of the safety shoes, especially if there are changes in foot size or shape. Shoes that fit well initially may not remain comfortable over time.
Footwear for Specific Food Industry Environments
The food industry presents a diverse range of working environments, each with its own unique hazards and challenges. Consequently, selecting the right safety footwear is crucial to protect workers from specific risks. Understanding the specific requirements of each environment, from wet processing areas to extreme temperature conditions, is essential for ensuring worker safety and productivity. This section delves into the specialized footwear needs of various food industry environments.
Footwear Requirements for Wet Processing Areas
Wet processing areas, such as those found in meatpacking plants, seafood processing facilities, and beverage production, pose significant slip and hygiene challenges. The presence of water, cleaning chemicals, and food byproducts creates slippery surfaces, increasing the risk of falls. Moreover, the constant exposure to moisture can compromise the integrity of footwear materials, leading to premature wear and tear.The primary requirements for safety shoes in wet processing areas include:
- Slip Resistance: Footwear must meet or exceed the highest slip resistance standards, typically SRC-rated, to provide maximum grip on wet and oily surfaces. This is achieved through the use of specialized outsole compounds and tread patterns designed to channel water away from the sole.
- Waterproof Construction: Shoes must be fully waterproof to prevent water from penetrating the footwear and reaching the worker’s feet. This often involves the use of waterproof membranes, sealed seams, and water-resistant materials.
- Chemical Resistance: Footwear should be resistant to common cleaning chemicals and food processing byproducts. Materials like polyurethane (PU) and nitrile rubber are frequently used for their resistance to these substances.
- Hygienic Design: Shoes should be easy to clean and sanitize to prevent the buildup of bacteria and contaminants. Features like smooth surfaces, minimal seams, and removable insoles facilitate thorough cleaning.
- Material Considerations: Outsoles made from slip-resistant and chemical-resistant materials like polyurethane (PU) or nitrile rubber are critical. Uppers made from waterproof, non-porous materials such as synthetic leather or certain types of rubber are preferred.
Footwear for Extreme Temperatures
Environments with extreme temperatures, whether cold or hot, demand specialized footwear to protect workers from thermal hazards. These conditions can significantly impact worker comfort and safety, potentially leading to cold stress, heatstroke, or burns. The selection of appropriate footwear is crucial for mitigating these risks. Cold Environments:Cold storage facilities, freezer rooms, and outdoor food processing areas in cold climates necessitate footwear designed to insulate the feet and maintain warmth.
Key considerations include:
- Insulation: Footwear must provide adequate insulation to prevent heat loss and keep feet warm. This is often achieved through the use of insulated linings, such as Thinsulate or similar materials, and thick, insulated insoles.
- Water Resistance: Cold environments often involve moisture, such as condensation or snow. Waterproof construction is essential to prevent water from penetrating the footwear and causing the feet to become cold.
- Traction: Outsoles must provide good grip on cold, potentially icy surfaces. Slip-resistant outsoles with deep treads are crucial.
- Material Considerations: Uppers made from waterproof and insulated materials, such as treated leather or synthetic materials with insulation layers, are common. Outsoles should be made from flexible materials that maintain their grip in cold temperatures.
- Examples: Boots designed for cold storage typically feature thick insulation, waterproof membranes, and slip-resistant outsoles. Some models include features like a built-in vapor barrier to prevent sweat buildup.
Hot Environments:Bakeries, kitchens, and other areas with high ambient temperatures require footwear that protects against heat and potential burns. The focus is on breathability, heat resistance, and protection against spills.
- Heat Resistance: Footwear should be constructed from materials that can withstand high temperatures without melting or degrading.
- Breathability: Breathable materials are essential to prevent the feet from overheating and sweating excessively.
- Protection from Spills: Shoes should offer some level of protection against hot liquids and spills, such as oil or grease.
- Material Considerations: Uppers made from heat-resistant materials, such as leather or flame-retardant fabrics, are important. Outsoles made from heat-resistant rubber or other materials are also necessary.
- Examples: Shoes for bakery environments may feature heat-resistant soles, reinforced toes, and breathable uppers. Some models include metatarsal guards for additional protection against impact.
Safety Shoes for Specific Food Processing Sub-sectors
Different food processing sub-sectors present unique hazards and require tailored safety footwear solutions. Here are examples of footwear considerations for some common sectors: Dairy:The dairy industry often involves wet environments and exposure to milk, cleaning chemicals, and sanitizers.
- Footwear: Waterproof, slip-resistant boots with chemical-resistant soles are crucial. The boots should be easy to clean and sanitize.
- Example: Boots with polyurethane outsoles, waterproof membranes, and a smooth design to prevent bacteria buildup are commonly used.
Bakery:Bakeries involve hot environments, potential for slips, and exposure to flour and other ingredients.
- Footwear: Heat-resistant, slip-resistant shoes with good breathability are essential. Steel or composite toe protection is also important.
- Example: Shoes with heat-resistant outsoles, leather or synthetic uppers, and slip-resistant treads are frequently used.
Meatpacking:Meatpacking plants present wet environments, exposure to blood and meat byproducts, and potential for sharp objects.
- Footwear: Waterproof, slip-resistant boots with puncture-resistant midsoles and steel or composite toes are necessary.
- Example: Boots with polyurethane outsoles, waterproof membranes, puncture-resistant midsoles, and steel toes are common.
Purchasing and Maintenance: Food Industry Safety Shoes
Selecting and maintaining safety footwear is crucial for ensuring worker safety and extending the lifespan of the investment. Proper selection involves considering the specific hazards present in the workplace, while regular maintenance helps to prevent accidents and maintain hygiene standards.
Selecting the Right Safety Shoes for a Food Industry Workplace
The process of choosing appropriate safety shoes for the food industry requires a thorough assessment of the work environment and potential hazards. This involves evaluating factors like the types of food handled, the cleaning protocols, and the physical demands of the job.
- Hazard Assessment: Identify the specific hazards present in the workplace. This includes wet or slippery surfaces, exposure to chemicals or cleaning agents, potential for falling objects, and temperature extremes. For instance, a meat processing plant might require shoes with excellent slip resistance and puncture protection, while a bakery might prioritize heat resistance.
- Material Selection: Choose materials that are appropriate for the identified hazards. Consider waterproof and chemical-resistant materials for wet environments, and insulated materials for temperature control. Polyurethane (PU) and nitrile rubber are common choices due to their durability and resistance to various substances.
- Safety Features: Ensure the shoes meet the necessary safety standards. Steel or composite toe caps protect against impact, while midsole protection shields against punctures. Look for shoes certified to relevant standards, such as EN ISO 20345 or ASTM F2413.
- Fit and Comfort: Proper fit is essential for comfort and preventing foot fatigue. Encourage employees to try on shoes and ensure they have adequate space in the toe box. Consider ergonomic features like arch support and cushioned insoles.
- Work Environment Compatibility: Evaluate the specific requirements of the work environment. For example, in areas with high hygiene standards, choose shoes that are easy to clean and sanitize. In environments with potential for static electricity, consider anti-static footwear.
- Employee Input: Involve employees in the selection process. Their feedback can help ensure the chosen footwear meets their needs and preferences, which can improve compliance and worker satisfaction.
- Trial Period: If possible, provide a trial period for employees to test the selected shoes. This allows them to assess the comfort, fit, and performance in their specific work tasks before a final purchase decision is made.
Proper Shoe Care and Maintenance
Proper shoe care and maintenance are vital for extending the lifespan of safety footwear and maintaining its protective properties. This includes regular cleaning, proper storage, and timely repairs or replacements.
- Cleaning Procedures: Establish a regular cleaning schedule. The frequency of cleaning depends on the work environment. Wipe down shoes after each shift to remove food particles, dirt, and chemicals. Use appropriate cleaning agents and follow the manufacturer’s instructions.
- Drying Methods: Allow shoes to air dry naturally. Avoid placing them near direct heat sources, such as radiators or dryers, as this can damage the materials. If shoes become excessively wet, consider using shoe dryers designed for this purpose.
- Storage Practices: Store shoes in a clean, dry, and well-ventilated area. Avoid storing them in direct sunlight or extreme temperatures. Ensure shoes are stored separately from personal belongings to prevent cross-contamination.
- Inspection for Damage: Regularly inspect shoes for any signs of damage, such as cracks, tears, or worn soles. Check the toe caps, midsoles, and uppers for any defects that could compromise their protective function.
- Repair or Replacement: Repair minor damage promptly. Replace shoes if they are severely damaged or if the safety features are compromised. Adhere to a replacement schedule based on wear and tear and the shoe’s lifespan.
- Specialized Cleaning for Specific Hazards: Consider specialized cleaning methods for specific hazards. For example, shoes exposed to harsh chemicals might require rinsing with specific neutralizing agents.
Maintenance Schedule: Inspection and Replacement Guidelines
Implementing a structured maintenance schedule is crucial for ensuring the continued effectiveness of safety footwear. This schedule should include regular inspections and clear guidelines for replacement.
- Daily Inspection: Conduct a visual inspection of the shoes at the beginning and end of each shift. Check for obvious signs of damage, such as cuts, abrasions, or sole separation. Note any observed issues.
- Weekly Inspection: Perform a more thorough inspection weekly. Examine the soles for wear and tear, the toe caps for dents or damage, and the uppers for any cracks or tears. Check the stitching and seams for integrity.
- Monthly Inspection: Conduct a detailed inspection monthly. This includes checking the inner lining and insoles for wear, assessing the slip resistance of the soles, and evaluating the overall structural integrity of the shoe.
- Replacement Criteria: Establish clear criteria for shoe replacement. Replace shoes when the soles are worn to a point where slip resistance is compromised, when the toe caps are damaged, or when the uppers show significant wear and tear. Replace shoes if they have been exposed to chemicals that have degraded the materials.
- Replacement Schedule based on Usage: Develop a replacement schedule based on the intensity of use and the environment. For example, shoes used in high-hazard environments might need to be replaced more frequently than those used in less demanding settings. Consider replacing shoes every 6-12 months, depending on wear and tear.
- Documentation: Maintain records of inspections, repairs, and replacements. This documentation helps to track the lifespan of shoes, identify potential issues, and ensure compliance with safety regulations. Include the date of purchase, the date of each inspection, and any actions taken, such as repairs or replacement.
Innovations in Food Industry Safety Footwear
The food industry is constantly evolving, and with it, the demands placed on safety footwear. Technological advancements and a heightened awareness of worker well-being have spurred significant innovations in recent years. These innovations aim to enhance protection, comfort, hygiene, and overall performance, leading to safer and more productive work environments.
Recent Technological Advancements in Safety Shoe Design
Modern safety shoe design incorporates several cutting-edge technologies. These advancements focus on improving the overall functionality and protective capabilities of the footwear.
- Advanced Materials: The use of new materials significantly improves durability, protection, and comfort. For instance, composite materials, like carbon fiber and advanced polymers, replace steel in the toe caps and midsoles, reducing weight and enhancing flexibility. These materials maintain the same level of protection as steel while offering superior comfort.
- Ergonomic Design: Computer-aided design (CAD) and 3D printing technologies allow for the creation of shoes that better conform to the foot’s natural shape. This improves fit and reduces pressure points, thereby enhancing comfort and minimizing the risk of musculoskeletal disorders.
- Smart Technology Integration: Some safety shoes now incorporate sensors and data-tracking capabilities. These technologies can monitor foot temperature, pressure, and movement, providing valuable insights into worker health and performance. This data can be used to proactively address potential issues and optimize shoe design.
- Enhanced Breathability: Advanced breathable membranes and ventilation systems are integrated into the shoe’s construction. This helps regulate foot temperature, preventing overheating and reducing the build-up of sweat, thus contributing to increased comfort and hygiene.
Innovative Materials and Features in Current Safety Footwear
The safety footwear industry is witnessing the emergence of several innovative materials and features. These innovations aim to provide enhanced protection, improved comfort, and better hygiene standards.
- Lightweight Composites: As mentioned earlier, the utilization of lightweight composite materials is a prominent trend. These materials, such as carbon fiber and aramid fibers, are used in toe caps, midsoles, and even the shoe’s upper construction. This reduces the overall weight of the shoe, leading to less fatigue during long work hours.
- Antimicrobial and Antibacterial Linings: Many modern safety shoes feature antimicrobial and antibacterial linings. These linings inhibit the growth of bacteria and fungi, reducing odors and minimizing the risk of infections. This is particularly important in the food industry, where hygiene is paramount.
- Self-Cleaning Surfaces: Some manufacturers are incorporating self-cleaning surface treatments. These treatments help to repel water, oils, and other contaminants, making the shoes easier to clean and maintain. This reduces the time and effort required for cleaning and improves the shoe’s overall hygiene.
- Adjustable Fit Systems: Advanced fit systems, such as BOA lacing systems, allow for precise and customized adjustments. These systems provide a more secure and comfortable fit, reducing the risk of slips and falls and improving overall foot support.
- Slip-Resistant Outsoles with Advanced Tread Patterns: The design of outsoles has evolved significantly, with innovative tread patterns and rubber compounds providing superior grip on wet and slippery surfaces. The development of specific rubber compounds for food industry environments is crucial. For example, nitrile rubber is known for its resistance to oils and fats.
Future Trends and Developments in Food Industry Safety Shoe Technology
The future of food industry safety shoe technology promises even greater advancements, driven by a continuous focus on worker safety, comfort, and hygiene. These trends are likely to shape the industry in the coming years.
- 3D Printing for Customization: 3D printing will likely play a more significant role in creating custom-fit safety shoes. This technology allows for the production of footwear tailored to individual foot shapes and needs, maximizing comfort and reducing the risk of injuries. This includes the ability to integrate specific support features for individuals with unique requirements.
- Smart Shoe Integration: The integration of smart technologies will continue to evolve. This could include features such as:
- Pressure mapping sensors: to monitor foot pressure and identify potential issues.
- Temperature sensors: to monitor foot temperature and prevent overheating.
- GPS tracking: to track worker location for safety and accountability.
- Sustainable Materials: The use of sustainable and eco-friendly materials will become increasingly important. This includes the utilization of recycled materials, bio-based polymers, and other environmentally friendly alternatives. The entire lifecycle of the shoe, from production to disposal, will be considered.
- Advanced Slip Resistance Technologies: Research and development efforts will focus on further improving slip resistance. This could involve the development of new outsole materials, tread patterns, and surface treatments. For example, research into nano-materials and their application to improve traction is ongoing.
- Integration with Personal Protective Equipment (PPE): Safety shoes may become more integrated with other PPE, such as work clothing and protective gloves. This could involve the development of integrated communication systems, smart sensors, and other features that enhance overall worker safety and productivity.
Closing Notes
So, there you have it. From understanding the basics of food industry safety shoes to the nitty-gritty of cleaning and maintenance, we’ve covered the whole darn thing. Remember, these shoes aren’t just about compliance; they’re about protecting your feet and your livelihood. So, next time you see someone rocking a pair of these, give them a nod. They’re not just wearing shoes; they’re wearing a shield against the chaos of the food industry.
And hey, if you’re in the food industry, get yourself a good pair. Your feet will thank you, even if they can’t talk.