Food trailer flooring is more than just a surface; it’s the foundation of your mobile food business. Choosing the right flooring is critical, impacting everything from food safety and hygiene to the longevity of your trailer and the efficiency of your operations. This guide dives deep into the world of food trailer flooring, helping you navigate the complexities and make informed decisions.
We’ll explore various flooring material options, weighing their pros and cons based on durability, cost, and cleaning ease. You’ll discover the crucial factors influencing your selection, from adhering to local health codes to ensuring slip resistance. Furthermore, this guide will help you understand the installation and maintenance procedures, budget effectively, and ensure your chosen flooring complements your food trailer’s design and aesthetic.
Introduction to Food Trailer Flooring
Food trailer flooring refers to the surface material installed within a mobile food unit, serving as the primary walking and working surface. Its purpose is to provide a durable, safe, and sanitary environment for food preparation, service, and general operations. The flooring must withstand heavy foot traffic, equipment movement, spills, and regular cleaning.The selection of appropriate flooring is critical for a food trailer’s success.
It directly impacts the trailer’s hygiene, safety, longevity, and compliance with health regulations. Poor flooring choices can lead to slip-and-fall accidents, bacterial contamination, structural damage, and ultimately, business interruptions and financial losses.
Common Challenges in Flooring Selection
Several challenges arise when selecting flooring for a mobile food business. These considerations must be carefully assessed to ensure optimal performance and compliance.
- Durability and Wear Resistance: Food trailer flooring experiences significant wear and tear due to heavy foot traffic, the movement of equipment such as ovens and refrigerators, and the potential for dropped items. The flooring material must be able to withstand these stresses without significant damage like cracks, gouges, or delamination. For example, a flooring system used in a busy burger trailer should be able to withstand the equivalent of several years of residential use in a single year, considering the concentrated wear in specific areas.
- Slip Resistance: Maintaining a slip-resistant surface is crucial to prevent accidents. Spills of grease, water, and food products are common in food trailers. Flooring materials should have a high coefficient of friction, even when wet, to minimize the risk of slips and falls. This is often achieved through textured surfaces or the incorporation of slip-resistant additives.
- Sanitation and Cleanability: Food trailers are subject to strict hygiene standards. Flooring must be non-porous, easy to clean, and resistant to bacterial growth. Seamless flooring systems, such as epoxy or poured polyurethane, are preferred because they eliminate crevices where bacteria can thrive. Regular and effective cleaning protocols are essential, and the flooring material should withstand frequent washing with detergents and sanitizers without degradation.
- Chemical Resistance: Food trailers often use cleaning agents, cooking oils, and food acids. The flooring material must be resistant to these chemicals to prevent degradation, staining, and swelling. Epoxy and certain types of vinyl flooring offer good chemical resistance. The specific chemicals used in the trailer’s operations should be considered when selecting the flooring.
- Moisture Resistance: Food trailers are prone to moisture exposure from spills, cleaning, and condensation. The flooring must be waterproof or highly water-resistant to prevent water damage, mold growth, and the deterioration of the subfloor. Proper sealing and installation techniques are critical to ensure a watertight system.
- Temperature Fluctuations: Food trailers experience significant temperature variations depending on the season and location. The flooring material should be able to withstand these fluctuations without expanding, contracting, or cracking. The coefficient of thermal expansion of the chosen material is an important factor.
- Weight and Load Bearing Capacity: Food trailers have weight restrictions. The flooring material should be lightweight enough to minimize the overall weight of the trailer. The flooring system must also be able to support the weight of heavy equipment, such as cooking ranges and refrigeration units, without deformation or damage.
- Cost and Installation: The cost of flooring, including materials and installation, is a significant factor. The initial investment should be balanced against the long-term benefits of durability, ease of maintenance, and compliance with regulations. Installation costs can vary depending on the complexity of the system and the labor involved.
- Compliance with Regulations: Food trailer flooring must comply with local and state health regulations. These regulations often specify requirements for sanitation, slip resistance, and material composition. Failure to comply can result in fines or the closure of the business. Inspectors often look for flooring that is smooth, non-absorbent, and easy to clean.
Flooring Material Options
Selecting the appropriate flooring material is crucial for the operational efficiency, hygiene, and longevity of a food trailer. The chosen material must withstand heavy foot traffic, spills, temperature fluctuations, and rigorous cleaning protocols. Several flooring options are available, each possessing unique characteristics impacting performance, cost, and maintenance.
Flooring Material Types and Characteristics
Understanding the properties of different flooring materials allows for informed decision-making. The following options represent common choices, each with distinct advantages and disadvantages.
- Vinyl Flooring: Vinyl flooring is a popular choice due to its affordability, water resistance, and ease of installation. It’s available in sheet, tile, and plank formats, offering design flexibility. Vinyl is composed of synthetic materials, typically polyvinyl chloride (PVC), combined with plasticizers, stabilizers, and pigments. The thickness and composition influence its durability and resistance to wear. However, some vinyl products can be susceptible to punctures or tears, and may require more frequent replacement compared to other options.
- Epoxy Flooring: Epoxy flooring involves applying a resin-based coating directly to the concrete subfloor. This creates a seamless, durable, and highly resistant surface. Epoxy is known for its excellent chemical resistance, making it ideal for handling food spills and cleaning agents. It also offers a wide range of design options, including color customization and the addition of decorative flakes. The installation process requires careful surface preparation and can be time-consuming, and the material is susceptible to UV degradation, which can cause yellowing or fading.
- Stainless Steel Flooring: Stainless steel flooring is the most durable and hygienic option, commonly used in commercial kitchens. It’s exceptionally resistant to water, stains, and bacteria, making it easy to clean and sanitize. Stainless steel is typically fabricated from an alloy containing chromium, which forms a passive layer that protects the underlying metal from corrosion. However, it is a high-cost option, can be slippery when wet, and requires specialized installation.
- Rubber Flooring: Rubber flooring, particularly vulcanized rubber, offers excellent slip resistance, cushioning, and impact absorption. It is also relatively easy to clean and maintain. Rubber is made from natural or synthetic rubber compounds, which are often reinforced with fillers and pigments. Its resilience makes it comfortable for staff who spend long hours on their feet. The initial cost can be higher than vinyl, and it may require specific cleaning agents to avoid degradation.
- Concrete Flooring: Concrete flooring, often sealed or coated, provides a durable and cost-effective base. Concrete is a composite material composed of cement, aggregates (sand, gravel), and water. It can be customized with various finishes, including stains and sealers, to enhance its appearance and protect it from wear and tear. While concrete is durable, it can be porous and susceptible to staining if not properly sealed.
Cracks can also develop over time.
Flooring Material Comparison Table
The following table provides a comparative analysis of the key characteristics of each flooring material, aiding in the selection process.
Material Type | Cost (per sq. ft.) | Durability | Cleaning Requirements | Maintenance |
---|---|---|---|---|
Vinyl | $2 – $7 | Moderate | Sweeping, mopping with mild detergent | Periodic waxing or sealing may be required. |
Epoxy | $3 – $12 | High | Sweeping, mopping with appropriate epoxy cleaner | Minor repairs may be needed; re-coating may be necessary after several years. |
Stainless Steel | $15 – $40 | Exceptional | Sweeping, mopping with stainless steel cleaner | Requires professional installation; minimal maintenance, but can scratch. |
Rubber | $4 – $15 | High | Sweeping, mopping with pH-neutral cleaner | Periodic cleaning and maintenance with appropriate rubber care products are needed. |
Concrete (Sealed/Coated) | $2 – $10 | Moderate to High | Sweeping, mopping with appropriate cleaner | Resealing may be required every few years. |
Considerations for Food Trailer Flooring
Selecting the appropriate flooring for a food trailer is a critical decision that impacts food safety, worker safety, and operational efficiency. This selection process necessitates a thorough understanding of various factors, including regulatory requirements, slip resistance, and weight-bearing capacity. A well-considered flooring choice will contribute to a safe and compliant work environment while ensuring the longevity of the food trailer’s infrastructure.
Food Safety Regulations and Local Health Codes
Food trailer flooring must adhere to stringent food safety regulations and local health codes to prevent contamination and facilitate proper cleaning and sanitation. These regulations vary by jurisdiction, but generally, they share common principles.
- Material Compliance: Flooring materials must be non-absorbent, non-toxic, and resistant to grease, chemicals, and staining. Common acceptable materials include commercial-grade vinyl, epoxy, and sealed concrete. Porous materials are generally prohibited because they can harbor bacteria and are difficult to sanitize effectively.
- Smooth and Impervious Surfaces: The flooring surface must be smooth and free of cracks, crevices, and imperfections that could trap food particles and promote bacterial growth. Impervious surfaces prevent the penetration of liquids, making cleaning and sanitation easier and more effective.
- Coving and Transitions: Coving, the gradual curving of the floor up the walls, eliminates sharp corners where dirt and bacteria can accumulate. Transitions between the floor and equipment or walls should be sealed to prevent the accumulation of debris and moisture.
- Cleaning and Sanitization Protocols: Flooring must be designed to withstand frequent cleaning and sanitization procedures, including the use of approved cleaning agents and disinfectants. The choice of flooring material should consider the specific cleaning products required and their potential impact on the floor’s integrity.
- Local Health Department Inspections: Food trailers are subject to regular inspections by local health departments to ensure compliance with all applicable regulations. Failure to meet these standards can result in fines, operational restrictions, or even closure. Consult with local health authorities to understand the specific requirements in your area.
Slip Resistance in Food Trailer Flooring
Slip resistance is a crucial safety consideration in food trailer flooring, as spills of water, grease, and food products are common occurrences. A slip-resistant floor minimizes the risk of falls, protecting workers from injuries and potential liability.
- Coefficient of Friction: Slip resistance is typically measured by the coefficient of friction (COF). A higher COF indicates greater slip resistance. The Occupational Safety and Health Administration (OSHA) recommends a minimum COF of 0.5 for walking surfaces.
- Achieving Slip Resistance: Several methods can be employed to achieve slip resistance in food trailer flooring.
- Textured Surfaces: Flooring materials with textured surfaces, such as embossed vinyl or epoxy coatings with added aggregates, provide increased friction.
- Aggregates: Incorporating aggregates like silica sand or aluminum oxide into epoxy or other coatings enhances slip resistance. The size and density of the aggregates can be adjusted to achieve the desired level of traction.
- Anti-Slip Additives: Some flooring products contain anti-slip additives that increase the COF.
- Proper Maintenance: Regular cleaning and maintenance are essential to maintain slip resistance. Grease and spills should be cleaned up promptly.
- Material Selection: The choice of flooring material significantly impacts slip resistance. For instance, polished concrete is generally less slip-resistant than textured vinyl or epoxy with added aggregates.
- Testing and Certification: Flooring products can be tested and certified for slip resistance by independent laboratories. Look for products that meet or exceed industry standards and regulations.
Weight-Bearing Capacity for Food Trailer Floors
The weight-bearing capacity of a food trailer floor must be carefully assessed to ensure it can safely support the weight of equipment, supplies, and foot traffic. Overloading the floor can lead to structural damage, safety hazards, and costly repairs.
- Equipment Weight: Calculate the total weight of all equipment, including ovens, refrigerators, freezers, grills, fryers, and food preparation tables. Consider the weight of fully loaded equipment, such as a refrigerator filled with food and beverages.
- Supply Weight: Estimate the weight of supplies, including food inventory, beverages, packaging materials, and cleaning supplies. This weight can fluctuate significantly depending on the volume of business.
- Foot Traffic: Consider the number of employees and customers who will be present in the trailer at any given time. While the weight of individuals is generally less than that of equipment, it contributes to the overall load on the floor.
- Weight Distribution: Pay attention to how weight is distributed across the floor. Concentrated loads, such as heavy equipment placed on a small area, can exert more stress than distributed loads.
- Floor Construction: The floor’s construction, including the subfloor material, thickness, and support structure, determines its weight-bearing capacity. Common subfloor materials include plywood and steel.
- Calculating Load Capacity: It is crucial to understand the load capacity of the floor. This information is typically provided by the trailer manufacturer or flooring installer. The total weight of equipment, supplies, and anticipated foot traffic should not exceed the floor’s rated capacity.
- Example Scenario: Consider a food trailer equipped with a commercial-grade oven weighing 500 lbs, a refrigerator weighing 300 lbs, and various other equipment and supplies adding up to 700 lbs. If the trailer typically has three employees (averaging 150 lbs each), the total load would be 1650 lbs. The floor must be rated to handle this weight, plus a safety margin to account for unexpected loads or future equipment additions.
If the manufacturer specifies a load capacity of 2000 lbs, this provides an adequate safety margin.
Installation and Maintenance
Proper installation and diligent maintenance are crucial for extending the lifespan of food trailer flooring and ensuring a hygienic and safe working environment. Neglecting these aspects can lead to premature wear, costly repairs, and potential health hazards. This section details the installation processes for common flooring types and provides guidelines for effective cleaning and maintenance practices.
Installation of Different Flooring Types
The installation process varies significantly depending on the chosen flooring material. Each material requires specific tools and techniques to ensure proper adhesion, sealing, and overall durability. Understanding these requirements is paramount for a successful installation.
- Vinyl Sheet Flooring: This is often chosen for its water resistance and ease of cleaning. The installation involves several key steps. First, the subfloor must be thoroughly cleaned, leveled, and dried. Any imperfections in the subfloor will telegraph through the vinyl, so meticulous preparation is essential. Next, the vinyl sheet is cut to the trailer’s dimensions, allowing for a small amount of overlap at the edges.
The vinyl is then adhered to the subfloor using a specific adhesive, typically a pressure-sensitive or a spread adhesive. The adhesive is applied according to the manufacturer’s instructions, ensuring uniform coverage. Once the vinyl is in place, it’s crucial to use a roller to remove any air bubbles and ensure proper adhesion. Seams, if any, are heat-welded or cold-welded, creating a watertight seal.
Finally, the edges are sealed with a sealant compatible with the vinyl to prevent water ingress. This process requires a utility knife, a notched trowel (for adhesive application), a roller, and potentially a heat gun or cold-welding kit.
- Commercial-Grade Tile Flooring (e.g., Ceramic, Porcelain): These tiles offer superior durability and aesthetic appeal. The installation begins with a prepared and level subfloor, similar to vinyl. A mortar bed, usually a thin-set mortar, is applied to the subfloor using a notched trowel. The tiles are then carefully placed onto the mortar, ensuring even spacing and alignment. Tile spacers are used to maintain consistent grout lines.
Once all tiles are in place, they are allowed to cure according to the mortar manufacturer’s instructions, usually for 24-72 hours. After curing, the grout is applied, filling the spaces between the tiles. Excess grout is removed, and the grout is allowed to set. Finally, the tiles are cleaned, and a sealant is applied to the grout lines to protect against stains and water penetration.
Essential tools include a tile cutter, a notched trowel, tile spacers, a grout float, and a sealant applicator. The accuracy of the mortar mixing ratio is critical; too much or too little water can compromise the mortar’s strength and adhesion.
- Epoxy Flooring: Epoxy flooring creates a seamless, highly durable, and chemically resistant surface. The installation is a multi-step process. First, the subfloor must be thoroughly prepared, including grinding or shot blasting to create a profile for the epoxy to adhere to. Any cracks or imperfections are repaired. Next, a primer is applied to the subfloor to enhance adhesion.
After the primer cures, the epoxy resin and hardener are mixed according to the manufacturer’s instructions. The mixture is then poured onto the floor and spread evenly using a squeegee or notched trowel. Air bubbles are removed using a spiked roller. Several coats may be applied, depending on the desired thickness and features, such as decorative flakes. The final coat can include a clear topcoat for added durability and UV resistance.
This process demands precision in mixing and application. Tools include a grinder or shot blaster, a squeegee or notched trowel, a spiked roller, and protective gear. The ambient temperature and humidity significantly affect the curing time of the epoxy; hence, environmental control is essential.
- Rubber Flooring: Rubber flooring provides excellent slip resistance and shock absorption. The installation process depends on the type of rubber flooring. Rubber mats are generally easy to install; they are simply laid on the prepared subfloor. Rubber tiles may require adhesive, similar to vinyl. The subfloor should be clean, dry, and level.
Adhesive is applied to the subfloor and the back of the tiles (if necessary). The tiles are then placed and pressed firmly to ensure proper adhesion. Rubber flooring seams can be sealed with a seam sealer or adhesive to prevent water ingress. Proper ventilation is important during installation to remove the volatile organic compounds (VOCs) released by the adhesive. Tools required include a utility knife, adhesive, and a roller.
Proper Maintenance and Cleaning of Different Flooring Materials
Regular and appropriate cleaning and maintenance are critical for preserving the appearance and extending the lifespan of food trailer flooring. Different materials require specific cleaning agents and techniques to prevent damage and maintain hygiene.
- Vinyl Sheet Flooring: Regular sweeping or vacuuming removes loose dirt and debris. For spills, immediately wipe them up with a damp cloth or mop. For general cleaning, use a mild detergent mixed with warm water. Avoid abrasive cleaners, solvents, and harsh chemicals, as they can damage the vinyl’s surface. Rinse the floor thoroughly with clean water after cleaning and allow it to air dry or use a clean mop.
Routine cleaning with a pH-neutral cleaner is recommended to prevent the build-up of grime and grease. Consider using a floor cleaner specifically designed for vinyl flooring.
- Commercial-Grade Tile Flooring: Sweep or vacuum regularly to remove dirt and grit. Mop with a mild detergent and warm water. For stubborn stains, use a pH-neutral cleaner or a cleaner specifically designed for ceramic or porcelain tile. Avoid abrasive cleaners and acidic solutions, as they can damage the grout and the tile surface. Rinse thoroughly with clean water after cleaning.
Periodically, the grout lines should be cleaned and sealed to maintain their integrity and prevent staining. Consider using a grout brush for deeper cleaning of grout lines.
- Epoxy Flooring: Sweep or vacuum regularly to remove debris. For general cleaning, use a mild detergent and warm water. Avoid abrasive cleaners, solvents, and harsh chemicals, as they can dull or damage the epoxy surface. Spills should be wiped up immediately. For more persistent stains, a specialized epoxy cleaner may be required.
Rinse thoroughly with clean water after cleaning. Regular waxing or polishing can help maintain the epoxy’s shine and protect against wear. Always test cleaning solutions in an inconspicuous area first.
- Rubber Flooring: Sweep or vacuum regularly. Mop with a mild detergent and warm water. Avoid harsh chemicals and abrasive cleaners, as they can degrade the rubber. Rinse thoroughly with clean water after cleaning. For stubborn stains, a specialized rubber cleaner may be necessary.
In high-traffic areas, consider using a rubber floor protector to prevent wear and tear. Regularly inspect the flooring for damage and address any issues promptly.
Best Practices for Preventing Common Flooring Issues
Implementing preventive measures can significantly reduce the likelihood of common flooring problems, such as water damage, stains, and wear and tear.
- Water Damage Prevention: Immediately address any water leaks or spills. Ensure all plumbing fixtures and appliances are properly sealed. Use floor mats at entrances to trap moisture. Consider installing a waterproof membrane beneath the flooring, especially in areas prone to water exposure. Regularly inspect the flooring for any signs of water damage, such as discoloration, warping, or mold growth.
- Stain Prevention: Wipe up spills immediately to prevent staining. Use floor mats in high-traffic areas and under food preparation stations. Consider using stain-resistant flooring materials. Employ a regular cleaning schedule to remove potential staining agents before they can penetrate the flooring surface. Use appropriate cleaning agents for each flooring material, as incorrect cleaning can cause staining.
- Wear and Tear Prevention: Use floor mats in high-traffic areas. Avoid dragging heavy objects across the floor. Implement a regular cleaning and maintenance schedule to remove abrasive particles. Consider using protective coatings or sealants on the flooring surface. Choose durable flooring materials suitable for the trailer’s usage.
Regularly inspect the flooring for signs of wear and tear and address any issues promptly.
Flooring for Specific Food Trailer Types
The optimal flooring solution for a food trailer is highly dependent on the type of food service it provides. Different operational demands, from the potential for grease spills to the frequency of heavy equipment movement, necessitate tailored material selections. Careful consideration of these factors ensures both safety and operational efficiency, directly impacting the long-term profitability and sustainability of the business.
Pizza Trailers
Pizza trailers present a unique set of challenges due to the prevalence of high heat, grease, and potential for food spills. The flooring must withstand these conditions while maintaining a safe and sanitary environment.
- Material Selection: Epoxy coatings or commercial-grade vinyl are frequently chosen. Epoxy provides excellent resistance to heat, chemicals, and abrasion, crucial for withstanding dropped pizza pans and high foot traffic. Vinyl offers a more cost-effective option with similar hygienic properties and ease of cleaning.
- Workflow Impact: The flooring choice directly influences workflow. A non-slip surface minimizes the risk of accidents when handling hot pizzas or operating near ovens. Ease of cleaning is paramount; spills must be addressed quickly to prevent slip hazards and maintain food safety standards.
- Durability Considerations: The constant movement of heavy pizza ovens and the potential for dropped items demand a highly durable flooring material. This durability translates to a longer lifespan, reducing the frequency and cost of replacements.
Coffee Carts
Coffee carts often experience high foot traffic and frequent spills of coffee, milk, and syrups. The flooring must be resistant to staining and easy to clean to maintain a professional appearance.
Obtain access to food pantry wilson nc to private resources that are additional.
- Material Selection: Commercial-grade vinyl or sheet flooring are commonly used. These materials are water-resistant, easy to clean, and available in various designs to complement the cart’s aesthetic.
- Workflow Impact: The ease of cleaning directly impacts the speed and efficiency of daily operations. A floor that can be quickly wiped down allows baristas to maintain a clean workspace between customers.
- Aesthetic Considerations: The flooring contributes to the overall ambiance of the coffee cart. The choice of color and pattern can enhance the customer experience, reflecting the brand’s image.
Ice Cream Trucks
Ice cream trucks face unique challenges due to the constant presence of moisture, potential for ice cream spills, and the need for insulation.
- Material Selection: Waterproof vinyl sheet flooring is a practical choice. It resists water damage, is easy to clean, and provides a non-slip surface. Another option is rubber flooring, which offers excellent traction and cushioning, which can be beneficial for the employees.
- Workflow Impact: The non-slip properties are crucial for preventing accidents, especially when dealing with melting ice cream. The ease of cleaning is essential for maintaining a sanitary environment and complying with food safety regulations.
- Insulation Considerations: While the primary focus is often on the surface, the flooring can also contribute to insulation. Certain flooring materials can help to maintain a consistent temperature inside the truck, which can be especially important for preserving the quality of the ice cream.
Case Studies
Case Study 1: “Pizza Perfection”
-A Mobile Pizza BusinessThis trailer, operating in a busy urban environment, selected an epoxy flooring system. The owners chose this due to the high heat generated by the pizza oven, the potential for grease spills, and the need for a highly durable surface. The epoxy, professionally installed, provided a seamless, non-porous surface that was easy to clean and resistant to stains and abrasions.
This flooring choice contributed significantly to the trailer’s operational efficiency and helped them maintain their high food safety standards.
Case Study 2: “The Daily Grind”
-A Coffee CartThis coffee cart chose commercial-grade vinyl flooring. The owners prioritized ease of cleaning and aesthetic appeal. The vinyl’s water resistance was crucial for dealing with spills. The flooring was selected in a neutral color with a subtle pattern, creating a clean and inviting atmosphere. The vinyl’s affordability also allowed the owners to invest in other aspects of their business.
The cart experienced a significant reduction in cleaning time and enhanced customer perception.
Case Study 3: “Sweet Surrender”
-An Ice Cream TruckThis ice cream truck utilized waterproof vinyl sheet flooring. This choice was driven by the constant presence of moisture and the need for a non-slip surface to prevent accidents. The flooring was installed with sealed seams to prevent water penetration. The ease of cleaning and the non-slip properties contributed to the truck’s overall safety and efficiency. This flooring choice has contributed to a noticeable reduction in maintenance costs and has helped maintain the truck’s compliance with health and safety regulations.
Cost and Budgeting: Food Trailer Flooring
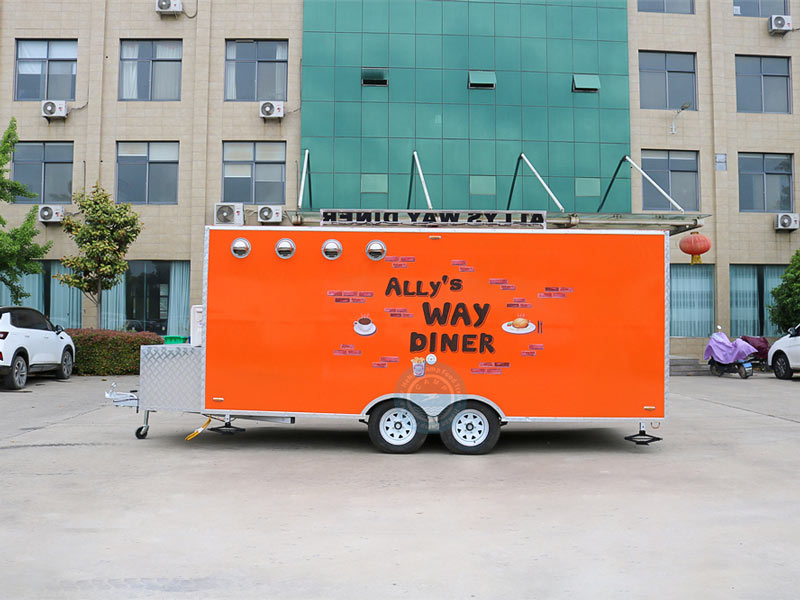
Budgeting for food trailer flooring is a critical aspect of the overall financial planning for your mobile food business. Accurate cost estimations, encompassing both upfront investments and ongoing maintenance expenses, are essential to ensure the long-term viability and profitability of your venture. Understanding the cost implications associated with different flooring materials, installation processes, and maintenance requirements allows for informed decision-making and effective resource allocation.
Estimating Average Costs for Flooring Materials and Installation
The cost of food trailer flooring varies significantly depending on the material chosen, the size of the trailer, and the complexity of the installation. Factors like geographic location, the need for subfloor preparation, and labor rates also contribute to the final price.To illustrate the cost differences, let’s examine several common flooring options. Note that these are
approximate* costs and can fluctuate based on the factors mentioned above
- Commercial Vinyl Sheet Flooring: This is often a more economical choice. The material cost can range from $2 to $6 per square foot. Installation, including subfloor preparation, can add an additional $3 to $8 per square foot, totaling between $5 and $14 per square foot. For a typical 8ft x 20ft food trailer (160 square feet), this translates to a total cost of approximately $800 to $2240.
- Commercial Vinyl Tile Flooring: Vinyl tiles offer a balance between cost-effectiveness and durability. Material costs are usually between $3 and $7 per square foot. Installation costs, including adhesive and labor, typically range from $4 to $9 per square foot, leading to a total cost of around $7 to $16 per square foot. For the same 160 square foot trailer, the estimated cost would be $1120 to $2560.
- Epoxy Flooring: Epoxy flooring provides a seamless and highly durable surface. The material cost is typically higher, ranging from $5 to $12 per square foot, and the installation is more complex. Installation costs, including surface preparation and multiple coats, can range from $8 to $15 per square foot, for a total cost of $13 to $27 per square foot. For a 160 square foot trailer, this equates to $2080 to $4320.
- Rubber Flooring: Rubber flooring is known for its slip resistance and impact absorption. The material cost is usually between $4 and $10 per square foot. Installation costs can range from $5 to $12 per square foot, depending on the type of rubber and installation complexity, resulting in a total cost of $9 to $22 per square foot. For the example trailer, the total cost could be $1440 to $3520.
- Aluminum Diamond Plate: While durable, aluminum diamond plate can be expensive. Material costs range from $8 to $15 per square foot, with installation adding $6 to $10 per square foot. This puts the total cost between $14 and $25 per square foot. For the 160-square-foot trailer, this results in a cost of $2240 to $4000.
These estimates do not include potential costs for removing existing flooring, subfloor repairs, or additional materials like cove base. It’s crucial to obtain detailed quotes from multiple flooring providers to get an accurate assessment for your specific needs.
Budgeting for Food Trailer Flooring: Initial Costs and Ongoing Maintenance
A comprehensive budget should consider both the initial investment and the long-term maintenance expenses associated with food trailer flooring. This approach ensures financial stability and minimizes unexpected costs over the lifespan of the flooring system.Initial costs are primarily comprised of the flooring material, installation labor, and any necessary subfloor preparation or repairs. To build a robust budget:
- Research and compare material costs: Obtain quotes from various suppliers, comparing not only the material price per square foot but also the warranty and expected lifespan.
- Obtain multiple installation quotes: Get quotes from several experienced installers. Ensure the quotes are detailed, including labor, materials, and any additional fees.
- Allocate a contingency fund: Unexpected issues, such as subfloor damage, can arise during installation. Include a contingency (typically 10-15% of the total estimated cost) to cover these potential expenses.
Ongoing maintenance involves the costs associated with cleaning, repairs, and eventual replacement. To account for these, consider:
- Cleaning supplies: Factor in the cost of cleaning products recommended for your chosen flooring material.
- Preventative maintenance: Implementing a regular cleaning schedule and addressing minor repairs promptly can extend the flooring’s lifespan and reduce future costs.
- Repair budget: Allocate funds for potential repairs, such as patching damaged areas or replacing worn tiles.
- Replacement timeline: Research the expected lifespan of your chosen flooring material. Create a sinking fund or savings plan to cover the eventual replacement cost. For instance, if your epoxy floor is expected to last 10 years and cost $3000 to replace, you should save $300 per year.
By incorporating both initial and ongoing costs, your budget will provide a realistic financial framework for your food trailer flooring.
Comparing Quotes and Understanding Flooring Contracts
When soliciting quotes from flooring providers, it is essential to have a standardized approach to ensure a fair comparison. Carefully evaluating the details of each quote and understanding the terms Artikeld in the contract is vital to protect your investment.To compare quotes effectively:
- Request detailed quotes: Each quote should specify the material type, the square footage covered, the installation process, the labor costs, and the cost of any additional materials (e.g., adhesives, sealants).
- Compare “apples to apples”: Ensure that all quotes include the same scope of work. If one quote includes subfloor preparation and another doesn’t, the comparison is skewed.
- Evaluate warranties: Compare the warranties offered by each provider. A longer warranty often indicates greater confidence in the product and installation quality. Pay attention to what is covered (e.g., material defects, labor, water damage) and any exclusions.
- Check references: Ask for references from previous customers. Contact these references to inquire about the provider’s reliability, quality of work, and adherence to deadlines.
The flooring contract is a legally binding document that Artikels the terms and conditions of the project. Carefully review the contract before signing. Key aspects to examine:
- Scope of work: The contract should clearly define the specific tasks the provider will perform, including surface preparation, flooring installation, and any cleanup.
- Payment schedule: The contract should Artikel the payment terms, including the deposit amount, the payment schedule, and the final payment upon completion. Avoid large upfront payments.
- Timeline and deadlines: The contract should specify the project start and completion dates. Include penalties for delays.
- Materials and specifications: The contract should detail the flooring material type, color, and any specific requirements.
- Warranty information: The contract should clearly state the warranty terms, including the duration, coverage, and any limitations.
- Change order process: The contract should describe the process for making changes to the project scope and the associated costs.
- Insurance and licensing: Ensure the contractor is properly licensed and insured. Request proof of insurance (e.g., general liability and workers’ compensation).
- Termination clause: Understand the conditions under which either party can terminate the contract.
Thoroughly evaluating quotes and meticulously reviewing the contract terms will help you choose a reliable flooring provider and protect your investment.
Regulations and Compliance
Adhering to health and safety regulations is paramount in the food trailer industry. Compliance ensures the safety of food products, protects consumers, and safeguards the business from potential legal ramifications. Understanding and implementing these regulations, particularly those concerning flooring, is a crucial step in establishing a successful and compliant food trailer operation.
Relevant Health and Safety Regulations for Food Trailer Flooring
Food trailer flooring regulations are primarily governed by local and regional health departments, with some federal guidelines influencing the standards. These regulations are designed to prevent contamination, facilitate cleaning, and ensure a safe working environment.
- Food and Drug Administration (FDA) Guidance: While the FDA primarily focuses on food safety, it provides guidance on general sanitation practices applicable to food establishments, including flooring. These guidelines emphasize the importance of non-absorbent, easily cleanable surfaces to prevent bacterial growth and contamination. The FDA’s Food Code serves as a model for many state and local health departments.
- State and Local Health Department Codes: These codes are the primary regulatory documents for food trailer flooring. They often specify acceptable flooring materials, installation methods, and cleaning protocols. These codes may vary significantly between jurisdictions. For example, some regions might mandate seamless flooring to eliminate crevices where bacteria can thrive, while others may allow for interlocking tiles with specific requirements.
- Americans with Disabilities Act (ADA) Compliance: Depending on the specific local regulations, food trailers may need to comply with ADA standards regarding accessibility. This can impact flooring choices, particularly regarding slip resistance and level changes to ensure ease of access for individuals with disabilities. Flooring materials must provide sufficient traction to prevent slips and falls, especially in wet conditions.
- Fire Safety Regulations: Fire codes often address flooring materials, requiring them to be non-combustible or have a specific fire-resistance rating. This is particularly important for trailers that use propane or other flammable materials.
Ensuring Flooring Choices Comply with Local Health Codes and Inspection Requirements
Achieving compliance involves a multi-faceted approach, from material selection to installation and maintenance. Understanding the specifics of local regulations is the first step.
- Researching Local Health Codes: Begin by contacting the local health department in the area where the food trailer will operate. Obtain a copy of the food safety regulations, paying close attention to sections related to flooring, surfaces, and sanitation. Many health departments provide online resources, including the specific codes and guidelines.
- Selecting Approved Flooring Materials: Choose flooring materials that are explicitly approved by the local health department. Common approved materials include:
- Commercial-Grade Vinyl: Known for its durability, water resistance, and ease of cleaning.
- Epoxy Resin: Creates a seamless, non-porous surface, ideal for preventing bacterial growth.
- Quarry Tile: A durable and slip-resistant option, often used in commercial kitchens.
- Following Installation Guidelines: Adhere strictly to the installation guidelines specified by the health department and the flooring manufacturer. This might include:
- Proper sealing of seams and edges to prevent water penetration.
- Ensuring a smooth, level surface without cracks or crevices.
- Using approved adhesives and sealants.
- Regular Inspections and Maintenance: Regular inspections and maintenance are crucial for maintaining compliance. This involves:
- Cleaning the floor daily with appropriate cleaning agents.
- Inspecting for damage, such as cracks, chips, or peeling.
- Repairing any damage promptly.
- Conducting periodic professional cleaning and maintenance as needed.
- Documentation: Maintain records of all cleaning, maintenance, and repairs. This documentation can be requested during health inspections.
Guide to Finding and Understanding Local Health Code Requirements for Food Trailer Flooring
Navigating the regulatory landscape can be simplified by following a structured approach. This guide Artikels the key steps to ensure compliance.
- Identify the Jurisdiction: Determine the specific city, county, or region where the food trailer will operate. This is crucial because regulations vary significantly between jurisdictions.
- Contact the Local Health Department: The local health department is the primary source of information on food safety regulations. Contact them directly via phone, email, or in person. Ask for specific information regarding flooring requirements for food trailers.
- Search Online Resources: Many health departments have websites with downloadable documents, including food safety codes, guidelines, and inspection checklists. Use search engines to find the local health department’s website. Search terms such as “[City/County] Health Department Food Safety” or “[State] Food Trailer Regulations” can be helpful.
- Review the Food Safety Code: Carefully review the food safety code, focusing on sections related to:
- Flooring materials
- Floor construction and installation
- Cleaning and sanitation requirements
- Accessibility (ADA) requirements, if applicable
- Attend Health Department Workshops or Training: Some health departments offer workshops or training sessions on food safety regulations. Attending these sessions can provide valuable insights and clarification.
- Consult with a Flooring Professional: A flooring professional experienced in food trailer installations can provide guidance on selecting compliant materials and ensuring proper installation. They are familiar with local regulations and can help navigate the requirements.
- Prepare for Inspections: Food trailers will undergo regular inspections by health department officials. Ensure the flooring meets all requirements before the inspection to avoid penalties or operational delays. Prepare documentation of cleaning, maintenance, and repairs.
Design and Aesthetics
The flooring of a food trailer is a significant element in shaping its overall design and aesthetic appeal. It contributes to the ambiance and branding of the establishment, impacting the customer experience and reflecting the trailer’s operational style. Careful consideration of flooring choices allows for the creation of a cohesive and visually appealing space that aligns with the food trailer’s concept.
Impact of Flooring on Overall Design
The selection of flooring significantly influences the visual impact of a food trailer. The color, texture, and pattern of the flooring can create a variety of effects, from enhancing a sense of spaciousness to establishing a specific brand identity. Different flooring materials possess unique characteristics that impact the overall design. For instance, polished concrete offers a modern, industrial look, while wood-look vinyl planks provide a warmer, more inviting atmosphere.
The flooring choice directly influences the perceived cleanliness, professionalism, and overall attractiveness of the food trailer.
Integrating Flooring with Other Design Elements
Successful food trailer design integrates flooring with other design elements to achieve a cohesive and visually appealing aesthetic. This involves considering how the flooring complements or contrasts with the colors, materials, and styles of the walls, countertops, equipment, and branding elements.
- Color Coordination: Matching or contrasting the flooring color with the trailer’s exterior and interior color scheme creates visual harmony. For example, a trailer with a bright red exterior could feature a black and white checkered floor for a classic diner look, or a grey concrete-look floor for a more contemporary feel.
- Material Synergy: Choosing flooring materials that complement the other materials used in the trailer enhances the overall design. If stainless steel equipment and surfaces are prominent, a flooring material like epoxy or polished concrete would create a consistent industrial aesthetic. Conversely, if the trailer uses a lot of wood or wood-look elements, vinyl planks or luxury vinyl tile (LVT) with a wood grain appearance would provide a cohesive feel.
- Branding Integration: Flooring can be customized to reflect the food trailer’s brand identity. This could involve incorporating the brand’s logo or colors into the flooring design. For example, a coffee shop could use a custom-designed epoxy floor with the company logo embedded in the surface.
- Lighting Effects: The type of lighting used in the food trailer interacts with the flooring. Darker flooring materials absorb more light, requiring brighter interior lighting. Lighter-colored floors reflect more light, creating a brighter and more spacious environment. Consider the effect of different lighting types (e.g., warm vs. cool) on the flooring color.
Detailed Descriptions for Image Generation, Food trailer flooring
Here are detailed descriptions for generating illustrations/images showcasing various flooring designs and color schemes for food trailers:
- Image 1: Modern Food Trailer with Polished Concrete Flooring.
The image depicts a food trailer with a sleek, modern design. The exterior is painted a matte charcoal gray. The main feature is the polished concrete flooring, which has a smooth, reflective surface with subtle variations in gray tones. The floor reflects the overhead lighting, creating a sense of depth and spaciousness.
Stainless steel equipment and countertops are visible, reflecting the lighting and the floor. The walls are painted a clean white, and the overall aesthetic is minimalist and contemporary. The trailer serves gourmet burgers, and the branding is simple, using bold, sans-serif fonts.
- Image 2: Retro Diner Food Trailer with Checkered Flooring.
The image presents a classic diner-style food trailer. The exterior is a vibrant red with chrome accents. The flooring is a black and white checkered pattern, creating a nostalgic and playful vibe. The counter is made of polished stainless steel, and red vinyl booths are placed against the walls. Neon signs illuminate the interior, and classic diner-style equipment, such as a milkshake machine and a grill, are visible.
The overall aesthetic is reminiscent of a 1950s diner. The trailer serves classic American fare.
- Image 3: Rustic Food Trailer with Wood-Look Vinyl Plank Flooring.
The image illustrates a food trailer with a rustic and inviting design. The exterior is clad in reclaimed wood siding, giving it a weathered appearance. The flooring is composed of wood-look vinyl planks with a warm, natural wood grain pattern. The walls are painted a soft cream color, and Edison bulb string lights hang from the ceiling.
The counter is made of a dark-stained wood, and there are touches of greenery throughout the trailer. The trailer serves artisan pizzas, and the branding emphasizes natural and handcrafted ingredients.
- Image 4: Food Trailer with Epoxy Flooring and Custom Branding.
The image showcases a food trailer with an epoxy floor that incorporates custom branding. The trailer’s exterior is a vibrant teal color. The flooring is a seamless epoxy coating with a glossy finish. Embedded in the floor is the company’s logo, a stylized coffee bean, and the brand name. The walls are painted a neutral gray, and the equipment is primarily stainless steel.
The overall design is modern and professional, reflecting the brand’s identity as a high-quality coffee provider.
Conclusion
In conclusion, selecting the right food trailer flooring is a multifaceted decision with significant implications for your business. By understanding the various materials, regulations, and design considerations, you can create a safe, efficient, and visually appealing space. This guide provides the knowledge you need to make the best choices for your mobile food venture, ensuring your flooring stands up to the demands of the food service industry and helps you thrive.