Alright, listen up, yeah? We’re diving headfirst into the world of the food wrap machine. This ain’t just some boring bit of kit; it’s the unsung hero keepin’ your sarnies and snacks lookin’ fly and fresh. From your local bakery to massive food factories, these machines are the real MVPs, making sure your grub stays safe and sound, innit?
We’re gonna break down how these bad boys work, the different types you can get, and all the bits and bobs that make ’em tick. We’ll also be chatting about the film they use, the best ways to keep ’em clean, and even the latest tech advancements. Basically, everything you need to know to become a food wrap machine pro, yeah?
Introduction to Food Wrap Machines
Food wrap machines are essential pieces of equipment in various industries, streamlining the process of packaging food products. These machines provide a protective barrier, extending shelf life and maintaining product freshness. Their versatility and efficiency have made them indispensable in the modern food supply chain.
Basic Functionality of a Food Wrap Machine
Food wrap machines operate by using a variety of methods to seal food items within a protective film or wrap. The core function involves applying a wrapping material, such as plastic film, around a food product and sealing it to create an airtight or modified atmosphere package. This process typically includes the following steps:
- Product Loading: The food product is placed either manually or automatically onto the machine’s wrapping platform.
- Film Dispensing: A roll of wrapping film is fed from a dispenser, often utilizing a pre-made film or creating the film from a roll.
- Wrapping and Sealing: The film is wrapped around the product, and the edges are sealed using heat, pressure, or a combination of both. Heat sealing is a common method, where heat is applied to melt the film edges together, creating a secure seal.
- Cutting (if applicable): In some machines, the wrapped product is then cut from the film roll.
- Product Discharge: The wrapped product is discharged from the machine, ready for further processing or distribution.
Primary Industries Utilizing Food Wrap Machines
Food wrap machines are crucial in numerous industries that deal with food packaging. The use of these machines varies depending on the type of food product, packaging requirements, and production volume. Here are the key industries:
- Food Processing: This industry relies heavily on food wrap machines for packaging a wide range of products, including meat, poultry, seafood, and prepared meals. The machines help to maintain product quality and hygiene, meeting stringent food safety standards.
- Produce: Fresh produce, such as fruits and vegetables, benefits from the protective properties of food wrap machines. Packaging helps to extend shelf life and reduce spoilage.
- Bakery and Confectionery: Bakeries and confectionery businesses use these machines to package baked goods, pastries, and candies, protecting them from contamination and maintaining freshness.
- Dairy: Dairy products, such as cheese and yogurt, are often packaged using food wrap machines to ensure product integrity and prevent spoilage.
- Retail: Supermarkets and grocery stores utilize food wrap machines in their in-store operations for packaging various items like deli meats, cheeses, and pre-packaged foods.
Brief History of Food Wrap Machine Development
The evolution of food wrap machines reflects advancements in packaging technology and the increasing demands of the food industry. Key milestones highlight the transition from manual to automated processes:
- Early 20th Century: The initial methods of food wrapping were largely manual, involving hand-wrapping products with materials like wax paper. This was a labor-intensive process, suitable only for small-scale operations.
- Mid-20th Century: The introduction of cellophane and other plastic films led to the development of basic wrapping machines. These machines automated the wrapping process to a limited extent, improving speed and efficiency compared to manual methods.
- Late 20th Century: Significant advancements occurred with the introduction of heat-sealing technology and the development of more sophisticated wrapping machines. These machines could handle a wider variety of packaging materials and offer greater precision in sealing. Shrink-wrapping technology also became prominent, providing a tight, protective seal around products.
- 21st Century: Modern food wrap machines incorporate advanced features such as automated product loading, precise temperature control, and integrated labeling systems. These machines are designed for high-speed operation, efficiency, and compatibility with various packaging materials, including recyclable options. Innovations in Modified Atmosphere Packaging (MAP) technology further enhance product shelf life. For instance, MAP systems can extend the shelf life of fresh meat products by up to 50% by controlling the levels of oxygen, carbon dioxide, and nitrogen within the packaging.
Types of Food Wrap Machines
Food wrap machines come in various forms, each designed to meet specific needs in food packaging. The selection of a machine depends heavily on factors like production volume, the type of food being wrapped, and budget constraints. Understanding the different types is crucial for optimizing packaging efficiency and ensuring product freshness.
Manual, Semi-Automatic, and Automatic Machines
Food wrap machines can be broadly categorized based on their level of automation. Each type offers a different balance of speed, cost, and labor requirements.
Manual food wrap machines require the operator to perform all steps of the wrapping process, from dispensing the film to sealing the package. Semi-automatic machines automate some steps, such as film dispensing, while the operator still handles aspects like product placement and sealing. Automatic machines perform all wrapping functions without direct operator involvement.
Here’s a comparison of manual, semi-automatic, and automatic food wrap machines:
Feature | Manual | Semi-Automatic | Automatic |
---|---|---|---|
Operation | Operator controls all aspects of wrapping. | Automates some steps (e.g., film dispensing, cutting). Operator handles product placement and sealing. | Fully automated; requires minimal operator intervention. |
Speed | Slowest; dependent on operator skill and speed. | Faster than manual; moderate output. | Fastest; high-volume output. |
Labor Costs | Highest; requires more labor. | Moderate; requires fewer operators than manual. | Lowest; minimal labor required. |
Initial Investment | Lowest; typically the most affordable option. | Moderate; a higher upfront cost than manual. | Highest; most expensive due to advanced technology. |
Suitable For | Low-volume operations, small businesses, specialty products. | Medium-volume operations, supermarkets, delis. | High-volume production, food processing plants, large-scale packaging. |
Specialized Food Wrap Machines
Beyond the basic categories, certain food wrap machines are specifically designed for particular food products. These machines incorporate features tailored to the unique characteristics of the food being wrapped, such as shape, size, and perishability.
Specialized machines are optimized for specific product types. These machines often incorporate features that address the unique characteristics of the food being wrapped.
Here are some examples:
- Bakery Item Wrappers: These machines often feature automated feeding systems and sealing mechanisms to efficiently wrap bread, pastries, and other baked goods. They may also incorporate features to maintain product freshness, such as modified atmosphere packaging (MAP). Consider the needs of a bakery producing a high volume of croissants. An automatic bakery wrapper can significantly increase production speed compared to manual wrapping, potentially reducing labor costs and increasing output by up to 30%.
- Meat Product Wrappers: Designed to handle raw and processed meats, these machines typically use durable materials and sealing methods to ensure hygiene and prevent leakage. Some meat wrappers include vacuum packaging capabilities to extend shelf life and maintain product quality. For example, a meat processing plant that switches from manual wrapping to an automatic meat wrapper can experience a significant reduction in waste due to more consistent sealing and portioning.
- Produce Wrappers: Produce wrappers are engineered to handle various shapes and sizes of fruits and vegetables. They often use breathable films to allow for gas exchange and prevent condensation, thereby extending shelf life. These machines are commonly used in supermarkets and produce distribution centers.
- Tray Sealers: Tray sealers are commonly used for ready-to-eat meals, salads, and other pre-portioned foods. These machines seal a film onto a tray, creating a secure and airtight package. Tray sealers can incorporate MAP technology to extend the shelf life of the product. A food manufacturer utilizing tray sealers can increase the shelf life of pre-packaged meals by up to 50% compared to traditional wrapping methods.
Components and Features
Understanding the components and features of food wrap machines is crucial for both operators and businesses looking to optimize their packaging processes. These machines, whether manual or automatic, rely on a set of core components working in concert to efficiently and effectively wrap food items. This section will break down these essential parts and explore the different film types used, culminating in a visual representation of an automatic food wrap machine’s key elements.
Essential Components of a Typical Food Wrap Machine
Food wrap machines, regardless of their level of automation, share several essential components that enable them to perform their primary function: applying film to food items. The design and sophistication of these components vary based on the machine’s type and intended application.
- Film Dispenser: This component holds and dispenses the roll of wrapping film. It’s designed to control the film’s unwinding process, ensuring a consistent and even feed. Some dispensers include mechanisms to adjust film tension, preventing tearing or wrinkling during wrapping.
- Cutting Mechanism: All food wrap machines must cut the film to the required length. This can be a simple serrated blade for manual machines or a more sophisticated heated wire or blade system in automatic models. The cutting mechanism’s precision directly impacts the neatness and efficiency of the wrapping process.
- Wrapping Platform: The platform provides a stable surface for the food item to be wrapped. It may include heating elements to shrink the film tightly around the product. The platform’s size and design vary depending on the size and shape of the food items being wrapped.
- Sealing System: This component seals the film around the food item, creating a secure package. This could be as simple as a heated plate or a more advanced system involving heat-sealing jaws. The effectiveness of the sealing system is critical for maintaining food freshness and preventing contamination.
- Control Panel (for Automatic Machines): Automatic machines feature a control panel that allows operators to set parameters such as film length, wrapping speed, and sealing temperature. This panel is the interface for monitoring and controlling the machine’s operation.
Film Types Used with Food Wrap Machines
The choice of film used in food wrap machines is crucial, as it directly impacts the product’s preservation, appearance, and shelf life. Several types of films are commonly used, each with its unique properties and applications.
- Polyvinyl Chloride (PVC) Film: PVC film is a widely used option due to its excellent clarity, flexibility, and stretchability. It’s particularly well-suited for wrapping fresh produce, meats, and other perishable items. PVC films are generally cost-effective. However, their use is sometimes restricted due to environmental concerns regarding their disposal.
- Polyethylene (PE) Film: PE film offers good moisture barrier properties and is often used for wrapping bakery items, prepared foods, and frozen products. It is generally considered more environmentally friendly than PVC, as it is recyclable. PE films come in different densities (LDPE, HDPE) that affect their strength and flexibility.
- Stretch Film (Polyolefin): This film is highly stretchable and clings to itself, creating a tight seal without the need for heat. It’s commonly used for wrapping trays of food, such as pre-cut fruits and vegetables. Stretch film provides good clarity and helps to extend the shelf life of the wrapped products.
- Polyester (PET) Film: PET film is known for its strength, excellent barrier properties, and resistance to temperature changes. It is frequently used in modified atmosphere packaging (MAP) applications. This type of film is often combined with other materials to create multilayer films with enhanced performance characteristics.
Diagram of an Automatic Food Wrap Machine’s Key Features
An automatic food wrap machine integrates the essential components described above into a streamlined system. The following diagram illustrates the key features and parts typically found in such a machine:
Diagram Description: The diagram shows a schematic representation of an automatic food wrap machine. The machine is depicted as a rectangular box with several key components labeled and connected by arrows to indicate the workflow.
- Film Roll Holder: A large roll of wrapping film is positioned at the top of the machine. The film is fed down through the machine.
- Film Dispenser/Feed Mechanism: This component controls the unwinding and feeding of the film, ensuring a consistent supply to the wrapping area.
- Product Loading Area: This is the area where the food item (e.g., a tray of chicken breasts) is placed onto the wrapping platform.
- Wrapping Platform: The platform supports the food item during the wrapping process.
- Film Cutting Mechanism: Located near the wrapping platform, this mechanism precisely cuts the film to the required length. A heated wire or blade is commonly used.
- Sealing System: This system seals the film around the product. It may involve heated plates or jaws that apply pressure and heat to create a secure seal.
- Control Panel: A panel is present, enabling the operator to set parameters such as film length and sealing temperature.
- Wrapped Product Exit: The finished, wrapped product exits the machine on a conveyor belt.
- Conveyor Belt (Optional): A conveyor belt may transport the wrapped products away from the machine.
The diagram illustrates the flow of the process: the film unwinds, the product is loaded, the film is cut, the product is wrapped and sealed, and the finished product exits the machine.
Operational Procedures
Operating a food wrap machine efficiently and safely is crucial for maintaining food quality and streamlining production. Understanding the operational procedures for different types of machines, along with troubleshooting common issues, ensures optimal performance and minimizes downtime. This section provides a comprehensive guide to the practical aspects of using food wrap machines.
Operating a Manual Food Wrap Machine
Manual food wrap machines are the simplest type, relying on operator input for each step. Mastering their operation involves understanding the specific actions required for wrapping various food items. This section provides a step-by-step guide.
- Preparation: Ensure the machine is clean and the wrapping film roll is correctly loaded. Position the food item on the wrapping platform. The platform’s size should accommodate the food item comfortably.
- Film Dispensing: Pull the film over the food item, ensuring sufficient overlap on all sides for a secure seal. The overlap amount will vary depending on the size and shape of the item.
- Wrapping: Fold the film tightly around the food item, typically by tucking the edges underneath or using a sealing bar to create a neat package. Proper folding and tucking are key to preventing air pockets and ensuring a tight seal.
- Sealing: Activate the sealing mechanism, which usually involves pressing a heated sealing bar onto the overlapping film edges. This creates a secure seal. Ensure the sealing time is appropriate for the film type to prevent burning or incomplete sealing.
- Cutting: If necessary, use the built-in cutting mechanism to trim excess film. This leaves a clean, professional-looking package.
- Cooling (if applicable): Allow the sealed package to cool briefly before handling to solidify the seal.
Operating Semi-Automatic and Automatic Machines
Semi-automatic and automatic food wrap machines offer increased speed and efficiency compared to manual models. They automate certain steps, reducing operator workload. Understanding their operational differences is crucial.The operational procedures for semi-automatic and automatic machines differ significantly from manual machines due to their automated features. Semi-automatic machines often automate film dispensing and sealing, while automatic machines automate the entire wrapping process.
- Semi-Automatic Machines:
- Loading: Place the food item on the designated platform or conveyor belt.
- Film Dispensing: The machine automatically dispenses the film.
- Wrapping: The operator may need to fold or tuck the film around the food item.
- Sealing: The machine typically seals the wrap automatically.
- Cutting: Some models automatically cut the film; others require manual cutting.
- Automatic Machines:
- Loading: Food items are typically fed onto a conveyor belt.
- Film Dispensing: The machine automatically dispenses the film.
- Wrapping: The machine wraps the food item, often using complex folding mechanisms.
- Sealing: The machine automatically seals the wrap.
- Cutting: The machine automatically cuts the film.
- Ejection: The wrapped product is automatically ejected.
Troubleshooting Common Issues
Food wrap machines, like any equipment, can experience operational issues. Identifying and resolving these issues promptly is essential to maintain productivity. Here are some common problems and their solutions.
Issue | Possible Cause | Solution |
---|---|---|
Film Not Sealing Properly | Incorrect sealing temperature, film type mismatch, damaged sealing element, or film contamination. | Adjust sealing temperature, use the correct film type for the machine, clean or replace the sealing element, ensure the film is clean and free from debris. |
Film Tears or Breaks | Incorrect film tension, film quality, or sharp edges on the food item or machine components. | Adjust film tension, use higher-quality film, inspect the food item and machine for sharp edges and address them. |
Machine Jams | Incorrect loading of the food item, film entanglement, or mechanical failure. | Ensure correct loading procedures, clear any film entanglement, inspect and repair mechanical issues. |
Film Dispensing Issues | Film roll improperly loaded, film sticking, or mechanical failure. | Reload the film roll correctly, clean the film dispensing mechanism, inspect and repair mechanical issues. |
Inconsistent Wraps | Inconsistent operator technique (manual machines), machine malfunction, or incorrect settings. | Provide operator training (manual machines), calibrate and maintain the machine, check and adjust machine settings. |
Advantages and Disadvantages
Food wrap machines offer significant benefits in the food packaging industry, but they also present certain drawbacks. Understanding these advantages and disadvantages is crucial for businesses considering investing in or utilizing these machines. A thorough evaluation ensures that the chosen packaging method aligns with specific operational needs and budgetary constraints.
Advantages of Using Food Wrap Machines
Using food wrap machines presents several advantages for businesses in the food industry. These benefits contribute to increased efficiency, enhanced product presentation, and improved food safety.
- Increased Efficiency and Speed: Food wrap machines automate the packaging process, significantly increasing the speed at which products can be wrapped. This is particularly beneficial for high-volume operations, where manual wrapping would be time-consuming and labor-intensive. For example, a supermarket bakery can wrap hundreds of pastries per hour, a task that would take a team of employees much longer to complete manually.
- Consistent and Professional Presentation: Machines provide consistent and uniform wrapping, which enhances the aesthetic appeal of packaged food products. This contributes to a more professional presentation that attracts customers and reinforces brand image. Products wrapped by machines generally look neater and more visually appealing compared to those wrapped manually.
- Reduced Labor Costs: Automating the wrapping process reduces the need for manual labor, leading to lower labor costs. This cost saving can be substantial, especially for businesses that handle a large volume of food products. The elimination of repetitive tasks also reduces the risk of worker fatigue and potential errors.
- Improved Food Safety and Hygiene: Food wrap machines are designed to maintain a high level of hygiene. They often incorporate features like automated film dispensing and sealing, which minimizes direct human contact with the food. This reduces the risk of contamination and helps to ensure food safety standards are met.
- Extended Shelf Life: Many food wrap machines use films that create a barrier against oxygen, moisture, and other contaminants. This helps to extend the shelf life of food products by slowing down spoilage and preserving freshness. Vacuum sealers, for example, can significantly increase the shelf life of meats and other perishables.
Disadvantages of Using Food Wrap Machines
While food wrap machines offer numerous advantages, there are also some disadvantages to consider. These include the initial investment cost, maintenance requirements, and limitations in flexibility.
- High Initial Investment: The initial cost of purchasing a food wrap machine can be significant, particularly for more advanced models. This can be a barrier for smaller businesses or those with limited capital. The price varies widely depending on the type of machine, its features, and its capacity.
- Maintenance and Repair Costs: Food wrap machines require regular maintenance and occasional repairs, which can add to the overall operating costs. Businesses need to factor in the cost of spare parts, labor for repairs, and downtime when a machine is out of service. Regular maintenance, however, can mitigate some of these costs by preventing major breakdowns.
- Space Requirements: Food wrap machines require dedicated space within a facility. The size of the machine and the space needed for operation, storage of wrapping materials, and maintenance can be a constraint for businesses with limited floor space. Larger, high-speed machines, in particular, can take up a considerable amount of room.
- Limited Flexibility: While machines excel at consistent wrapping, they may offer less flexibility than manual methods. Changing the type of wrap, the size of the product, or the wrapping style might require adjustments to the machine settings or the use of different equipment. Manual wrapping can be more adaptable to unique product shapes or special packaging needs.
- Potential for Training and Skill Requirements: Operating and maintaining food wrap machines often requires specialized training for employees. This can involve initial training costs and ongoing training to keep staff up-to-date with new features or troubleshooting techniques. The complexity of the machine determines the level of expertise required.
Cost-Effectiveness Comparison: Food Wrap Machines vs. Manual Wrapping
The cost-effectiveness of using food wrap machines compared to manual wrapping depends on several factors, including production volume, labor costs, and the cost of materials. The following table provides a four-column comparison:
Feature | Food Wrap Machines | Manual Wrapping | Comparison |
---|---|---|---|
Initial Investment | High (machine cost) | Low (minimal equipment) | Machines require a significant upfront investment, while manual wrapping has lower initial costs. |
Labor Costs | Low (fewer employees needed) | High (more employees needed) | Machines reduce labor costs significantly due to automation; manual wrapping is labor-intensive. |
Wrapping Speed | High (faster wrapping) | Low (slower wrapping) | Machines wrap products much faster, increasing throughput; manual wrapping is slower. |
Wrapping Consistency | High (uniform wrapping) | Low (variability in wrapping) | Machines provide consistent wrapping, improving product presentation; manual wrapping can vary. |
Material Costs | Can be variable, depends on film type and volume | Can be variable, depends on film type and volume | Material costs are similar, although machines may optimize film usage, reducing waste. |
Maintenance Costs | Moderate (repairs and upkeep) | Low (minimal equipment maintenance) | Machines require regular maintenance, which adds to operating costs; manual wrapping has minimal maintenance. |
Throughput | High (greater output) | Low (lower output) | Machines significantly increase the volume of products that can be wrapped per hour. |
Long-Term Cost-Effectiveness | High (especially for high-volume) | Low (suitable for low-volume only) | Machines become more cost-effective as production volume increases; manual wrapping is cost-effective only for low-volume operations. |
The cost-effectiveness analysis often hinges on the volume of products being packaged. For high-volume operations, the labor savings and increased speed of machines typically outweigh the initial investment and maintenance costs. Conversely, for low-volume operations, manual wrapping may be more cost-effective due to the lower initial investment and the flexibility it provides.
Applications in the Food Industry
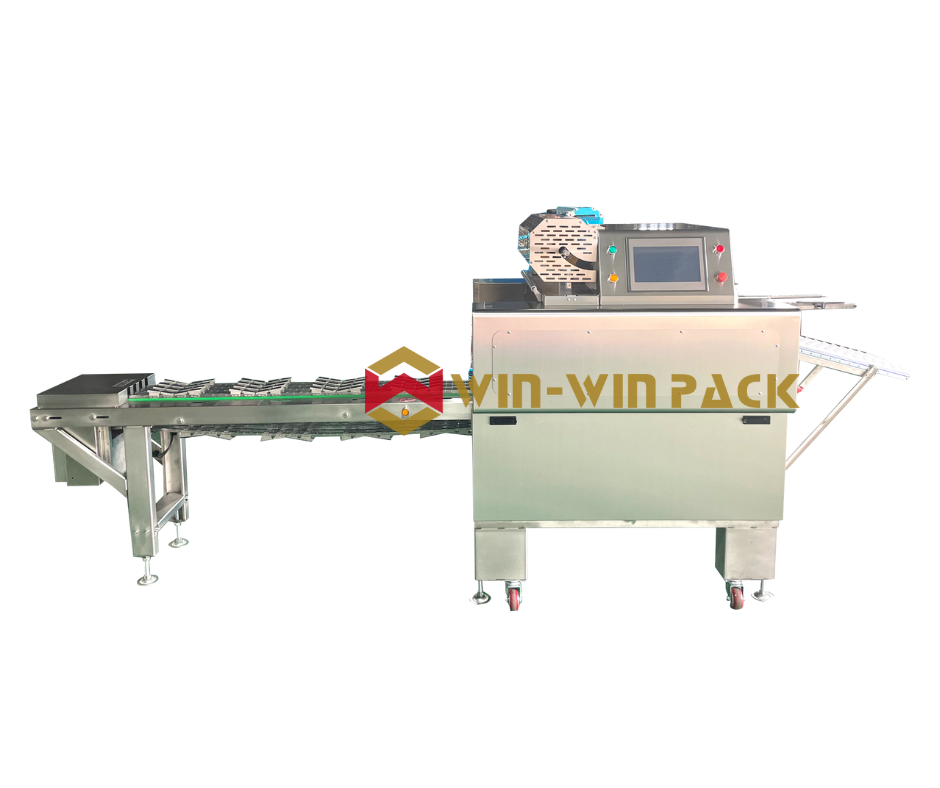
Food wrap machines are indispensable tools in the food industry, streamlining packaging processes and significantly impacting product quality and safety. Their versatility allows them to be applied across a wide range of food products, contributing to efficiency, preservation, and adherence to stringent hygiene standards.
Commonly Packaged Food Products
Food wrap machines are used to package an extensive array of food products, ensuring they are protected, preserved, and presented attractively. This versatility makes them a staple in various food processing and retail environments.
- Fresh Produce: Fruits and vegetables, such as apples, oranges, tomatoes, and cucumbers, are frequently wrapped to prevent bruising, reduce moisture loss, and extend shelf life. For instance, pre-packaged salads benefit from the protective barrier, which minimizes spoilage and maintains visual appeal.
- Meat and Poultry: Meats, including beef, chicken, and pork, are commonly packaged using food wrap machines. This packaging helps to prevent bacterial contamination, control the flow of oxygen, and maintain the product’s color and texture. Vacuum packaging, a specialized application, further extends shelf life by removing air.
- Seafood: Fish and shellfish are frequently wrapped to maintain freshness, prevent odor transfer, and protect against contamination. The packaging helps to preserve the delicate texture and flavor of seafood.
- Baked Goods: Bread, pastries, and other baked goods are often wrapped to retain moisture, prevent staleness, and protect the product from external elements. This packaging contributes to maintaining the freshness and appeal of these products.
- Dairy Products: Cheese, butter, and other dairy products are often wrapped to protect them from contamination and maintain their quality. Wrapping helps to control moisture levels and prevent the growth of unwanted microorganisms.
- Prepared Meals: Ready-to-eat meals, such as sandwiches, salads, and prepared entrees, are commonly packaged using food wrap machines to ensure food safety and convenience. This packaging also helps to extend shelf life and maintain the product’s appearance.
Maintaining Food Freshness and Extending Shelf Life
Food wrap machines play a critical role in preserving food quality and extending its usable life. By providing a protective barrier, these machines mitigate the factors that lead to spoilage, thereby reducing waste and increasing the time products remain marketable.The primary mechanisms through which food wrap machines achieve this are:
- Barrier Protection: The wrapping material creates a physical barrier that prevents the ingress of oxygen, moisture, and other contaminants that accelerate spoilage. This barrier helps to maintain the product’s original qualities.
- Moisture Control: Wrapping can either retain or remove moisture, depending on the product and the packaging material used. This helps to prevent the growth of mold and bacteria, which thrive in humid environments, or to prevent the product from drying out.
- Oxygen Control: Some packaging methods, such as vacuum sealing or modified atmosphere packaging (MAP), reduce or alter the oxygen content within the package. This slows down oxidation processes that can cause discoloration, flavor changes, and the growth of aerobic microorganisms.
- Temperature Regulation: While not a primary function, the wrapping material can sometimes help to regulate the temperature of the food product, slowing down spoilage processes. This effect is particularly noticeable with refrigerated or frozen items.
- Shelf Life Extension: By employing these protective measures, food wrap machines significantly extend the shelf life of various food products. This reduces waste, allows for wider distribution, and provides consumers with fresher products. For example, the use of MAP can extend the shelf life of fresh meat products from a few days to several weeks.
Contribution to Food Safety and Hygiene Standards
Food wrap machines are essential in upholding the stringent food safety and hygiene standards mandated by regulatory bodies. Their use contributes significantly to preventing contamination and ensuring that food products are safe for consumption.Key contributions include:
- Preventing Contamination: The packaging process creates a barrier that prevents the food from coming into contact with external contaminants, such as bacteria, viruses, and physical debris. This reduces the risk of foodborne illnesses.
- Maintaining Product Integrity: Packaging protects the food from physical damage during handling, transportation, and storage, ensuring that the product remains intact and free from spoilage.
- Compliance with Regulations: Food wrap machines enable businesses to comply with food safety regulations, such as those set by the FDA or similar agencies in other countries. These regulations often require that food products are packaged in a way that prevents contamination and maintains their safety.
- Controlled Environments: Many food wrap machines operate in controlled environments, which can further minimize the risk of contamination. These environments often feature temperature control, air filtration, and regular sanitation procedures.
- Traceability and Labeling: Food wrap machines facilitate the application of labels that include essential information, such as expiration dates, ingredients, and nutritional information. This information is crucial for consumer safety and enables product traceability.
- Reduced Cross-Contamination: The use of automated wrapping processes reduces the amount of human handling, which can minimize the risk of cross-contamination. This is particularly important in environments where multiple food products are processed.
Maintenance and Cleaning
Maintaining a food wrap machine is crucial for ensuring its longevity, optimal performance, and, most importantly, the safety of the food products it handles. Neglecting these aspects can lead to equipment failure, reduced efficiency, and potential contamination, which can have severe consequences for both the business and the consumer. Regular maintenance and thorough cleaning are therefore non-negotiable aspects of operating a food wrap machine.
Recommended Maintenance Procedures
Consistent maintenance practices are essential for keeping a food wrap machine operating smoothly and efficiently. These procedures, when followed diligently, minimize downtime and extend the machine’s lifespan.
Regular maintenance typically involves:
- Daily Inspection: Before each use, visually inspect the machine for any signs of damage, such as frayed wires, broken parts, or unusual noises. Check the film roll for proper alignment and any tears or imperfections. Ensure that all safety guards are in place and functioning correctly.
- Lubrication: Lubricate moving parts, such as gears and bearings, according to the manufacturer’s recommendations. This reduces friction and wear, preventing premature failure. The frequency of lubrication depends on the machine model and usage, but it is typically performed weekly or monthly. Use food-grade lubricants to avoid contamination.
- Film Roll Management: Regularly check the film roll for proper tension and alignment. Incorrect tension can lead to film breakage or inconsistent wrapping. Ensure the film is loaded correctly and that the cutting mechanism is functioning smoothly. Replace film rolls before they are completely depleted to avoid machine downtime.
- Belt and Roller Checks: Inspect belts and rollers for wear and tear. Replace worn or damaged components promptly to maintain proper film feeding and wrapping. Check the tension of the belts and adjust as necessary to ensure smooth operation.
- Temperature Control Monitoring: If the machine has temperature control features (e.g., for sealing), monitor the temperature settings to ensure they are accurate and consistent. Regularly calibrate the temperature sensors to maintain the desired sealing temperature.
- Electrical System Checks: Periodically inspect the electrical components, including wiring and connections, for any signs of damage or wear. Ensure that the machine is properly grounded and that all electrical safety features are functioning correctly.
- Preventive Maintenance Schedule: Establish a preventive maintenance schedule based on the manufacturer’s recommendations and the machine’s usage. This schedule should include regular inspections, lubrication, and component replacement. Keep detailed records of all maintenance activities.
Guidelines for Cleaning and Sanitizing
Cleaning and sanitizing food wrap machines are paramount to preventing the growth of bacteria and other microorganisms that can contaminate food. Adhering to a strict cleaning protocol is essential for maintaining food safety standards.
The cleaning and sanitizing process typically involves these steps:
- Preparation: Disconnect the machine from the power supply before cleaning. Gather all necessary cleaning supplies, including appropriate cleaning agents, sanitizers, clean cloths, and brushes. Wear appropriate personal protective equipment (PPE), such as gloves and eye protection.
- Pre-Cleaning: Remove any loose debris, food particles, and film scraps from the machine. Use a soft brush or scraper to remove any stubborn residue.
- Cleaning: Clean all accessible surfaces of the machine with a food-safe cleaning agent. Pay particular attention to areas that come into contact with food, such as the wrapping surface, sealing jaws, and cutting mechanisms. Follow the manufacturer’s instructions for the cleaning agent and the recommended dilution.
- Rinsing: Rinse all cleaned surfaces thoroughly with clean, potable water to remove any traces of the cleaning agent. Ensure that all cleaning agent residue is completely removed.
- Sanitizing: Apply a food-safe sanitizer to all cleaned surfaces. Follow the manufacturer’s instructions for the sanitizer and the recommended contact time. Ensure the sanitizer covers all surfaces.
- Drying: Allow the machine to air dry or use clean, disposable cloths to dry all surfaces. Avoid using cloths that could re-contaminate the machine.
- Film Path Sanitization: Pay special attention to the film path. Some machines might have specific procedures for sanitizing the path that the film travels.
- Frequency: Clean and sanitize the machine at the end of each shift or at least once a day, depending on usage. More frequent cleaning may be required if the machine is used to wrap highly perishable foods or if there is a risk of contamination.
Importance of Regular Maintenance for Machine Longevity and Performance
Regular maintenance is a critical investment that directly impacts the lifespan and performance of a food wrap machine. Ignoring maintenance can lead to costly repairs, reduced efficiency, and, ultimately, the premature replacement of the equipment.
Benefits of a consistent maintenance program include:
- Extended Lifespan: Regular maintenance prevents wear and tear on components, extending the machine’s operational lifespan. By addressing minor issues early on, you can prevent them from escalating into major problems that require costly repairs or replacements.
- Improved Performance: A well-maintained machine operates more efficiently, producing consistent and high-quality wraps. This leads to reduced waste and improved productivity. For example, a machine with properly lubricated moving parts will wrap products more quickly and accurately.
- Reduced Downtime: Preventive maintenance helps identify and address potential problems before they lead to machine breakdowns. This minimizes downtime and ensures continuous operation, allowing businesses to meet production schedules and customer demands.
- Enhanced Food Safety: Regular cleaning and sanitizing, a key component of maintenance, are essential for preventing food contamination. This protects consumers and helps businesses maintain their reputation and avoid costly recalls.
- Cost Savings: While maintenance requires an initial investment, it ultimately saves money by reducing the need for expensive repairs and replacements. It also minimizes waste and improves operational efficiency, leading to lower overall operating costs.
- Compliance with Regulations: Maintaining food wrap machines in good condition helps businesses comply with food safety regulations and standards. Regular maintenance demonstrates a commitment to food safety and helps avoid potential fines or penalties.
Consider this example: A food processing plant that diligently follows a maintenance schedule for its food wrap machines experiences significantly fewer breakdowns compared to a plant that neglects maintenance. The plant with a robust maintenance program consistently produces high-quality wrapped products, experiences minimal downtime, and enjoys a longer lifespan for its equipment, resulting in significant cost savings and enhanced operational efficiency.
This proactive approach minimizes potential disruptions and ensures compliance with stringent food safety regulations, showcasing the tangible benefits of a well-executed maintenance plan.
Safety Considerations
Operating food wrap machines efficiently is crucial, but prioritizing safety is paramount. The fast-paced environment of food processing can present numerous hazards. Understanding and implementing safety protocols ensures a safe working environment, reduces the risk of accidents, and protects employees.
Potential Hazards and Mitigation Strategies
Several potential hazards are associated with the operation of food wrap machines. Implementing preventative measures is essential to minimizing risks and ensuring a safe working environment.
- Moving Parts: Food wrap machines contain various moving parts, such as rollers, blades, and sealing mechanisms. These components can pose a significant risk of entanglement or injury.
- Mitigation: Always ensure that all safety guards and covers are in place and properly secured before operating the machine. Never reach into the machine while it is running. Regular inspections should be conducted to ensure all moving parts are functioning correctly and are free from obstructions.
- Electrical Hazards: Food wrap machines utilize electricity to power their operations. Exposure to electrical components can lead to electric shock or electrocution.
- Mitigation: Ensure that the machine is properly grounded. Regularly inspect electrical cords and connections for damage, such as fraying or exposed wires. Immediately disconnect the machine from the power source before performing any maintenance or repairs.
Only qualified personnel should handle electrical repairs.
- Mitigation: Ensure that the machine is properly grounded. Regularly inspect electrical cords and connections for damage, such as fraying or exposed wires. Immediately disconnect the machine from the power source before performing any maintenance or repairs.
- Sharp Blades and Cutting Mechanisms: Many food wrap machines use sharp blades or cutting mechanisms to trim and seal the wrapping material. These can cause severe cuts and lacerations.
- Mitigation: Always use appropriate personal protective equipment (PPE), such as cut-resistant gloves, when handling blades or working near cutting mechanisms. Be extremely cautious when changing blades or performing maintenance. Follow the manufacturer’s instructions for blade handling and disposal.
- Heat and Burns: Some food wrap machines utilize heat sealing mechanisms. Contact with these heated surfaces can cause burns.
- Mitigation: Allow the machine to cool down completely before performing any maintenance or cleaning. Use heat-resistant gloves when handling heated components. Be aware of the location of heated surfaces and avoid accidental contact.
- Ergonomic Hazards: Repetitive motions and awkward postures can lead to musculoskeletal disorders.
- Mitigation: Arrange the workstation to promote good posture and reduce strain. Provide adjustable chairs and work surfaces. Encourage employees to take regular breaks to stretch and rest. Implement job rotation to vary tasks and reduce repetitive movements.
Safety Checklist for Food Wrap Machine Operators
A comprehensive safety checklist helps ensure that all safety procedures are followed consistently. This checklist should be reviewed and followed before each shift and as needed throughout the day.
- Pre-Operational Inspection:
- Verify that all safety guards and covers are in place and securely fastened.
- Inspect electrical cords and connections for damage.
- Check for any obstructions or foreign objects near the machine.
- Ensure the machine is properly grounded.
- Confirm that all emergency stop buttons are functioning correctly.
- Personal Protective Equipment (PPE):
- Wear appropriate PPE, including cut-resistant gloves, when handling blades or sharp objects.
- Use heat-resistant gloves when handling heated components.
- Wear eye protection to prevent debris from entering the eyes.
- Ensure that clothing is appropriate and does not pose an entanglement hazard.
- Operational Procedures:
- Follow the manufacturer’s instructions for operating the machine.
- Never reach into the machine while it is running.
- Be aware of the location of moving parts and potential pinch points.
- Use the correct wrapping material and settings for the product being wrapped.
- Report any malfunctions or safety concerns immediately.
- Maintenance and Cleaning:
- Disconnect the machine from the power source before performing any maintenance or cleaning.
- Allow the machine to cool down completely before cleaning heated components.
- Use appropriate cleaning agents and follow the manufacturer’s instructions.
- Regularly inspect the machine for wear and tear.
- Schedule and perform preventative maintenance as recommended by the manufacturer.
- Emergency Procedures:
- Know the location of the emergency stop buttons and how to use them.
- Be familiar with the machine’s power shut-off procedures.
- Know the location of the first-aid kit and how to administer basic first aid.
- Report any accidents or injuries immediately to the supervisor.
Technological Advancements
Food wrap machines have undergone significant transformations in recent years, driven by the need for increased efficiency, improved hygiene, and reduced operational costs. These advancements have revolutionized the way food is packaged, leading to enhanced shelf life, reduced food waste, and improved consumer experience. The integration of cutting-edge technologies has played a crucial role in shaping the modern food wrap machine landscape.
Automation and Robotics Integration
The incorporation of automation and robotics is arguably the most impactful technological advancement in food wrap machine design. This integration has streamlined operations, reduced manual labor, and enhanced overall productivity.Robotic arms, for instance, are now commonly used in various stages of the wrapping process. These arms can perform tasks such as:
- Product Loading and Unloading: Robots can efficiently pick and place food items onto the wrapping line, and remove the wrapped products, increasing speed and reducing human error.
- Film Handling: Robotic systems can precisely control the film feed, ensuring accurate wrapping and minimizing film waste. This precision is crucial for maintaining consistent wrap quality.
- Sealing and Cutting: Robots are equipped with advanced sealing and cutting mechanisms, ensuring airtight seals and clean cuts, which is essential for preserving food freshness and preventing contamination.
The benefits of this integration are numerous:
- Increased Speed: Automated systems operate at significantly higher speeds compared to manual processes, leading to higher throughput.
- Reduced Labor Costs: The need for manual labor is drastically reduced, leading to cost savings.
- Improved Accuracy: Automation minimizes human error, ensuring consistent and high-quality wrapping.
- Enhanced Hygiene: Robots can operate in hygienic environments, reducing the risk of contamination.
Impact on Efficiency and Productivity
Technological advancements, particularly automation and robotics, have significantly impacted the efficiency and productivity of food wrap machines. The ability to process more products in less time, with fewer errors, has led to substantial improvements in overall operational performance.For example, consider a large-scale bakery that produces a variety of baked goods.
Before automation, wrapping these goods might have required a team of workers, each manually handling and wrapping individual items. This process would be slow, prone to errors, and labor-intensive.
Browse the multiple elements of chinese food raritan to gain a more broad understanding.
With automated food wrap machines, the bakery can now:
- Increase Production Volume: Automated machines can wrap thousands of products per hour, far exceeding the capacity of manual processes.
- Reduce Waste: Precise film handling and sealing mechanisms minimize film waste, reducing operational costs and environmental impact.
- Improve Product Quality: Consistent wrapping and airtight seals help maintain product freshness and extend shelf life.
- Optimize Labor Allocation: The bakery can reallocate its workforce to other critical tasks, such as quality control and product development.
These advancements translate into higher profitability, reduced operational costs, and improved product quality, ultimately benefiting both food manufacturers and consumers.
Film Materials and Sustainability
The choice of film material for food wrap machines has a significant impact on both the environment and the efficiency of food packaging. Understanding the environmental footprint of different film types and exploring sustainable alternatives is crucial for responsible food packaging practices. This section delves into the environmental impact of various film materials, highlighting sustainable alternatives, and comparing their performance with conventional options.
Environmental Impact of Food Wrap Film Materials
The environmental consequences of food wrap film materials vary considerably depending on their composition and manufacturing processes. The widespread use of certain materials contributes significantly to environmental challenges.* Traditional Plastic Films: These films, often made from polyethylene (PE), polypropylene (PP), and polyvinyl chloride (PVC), are derived from fossil fuels. Their production consumes significant energy and resources.
These plastics are often non-biodegradable, meaning they persist in landfills for hundreds of years, contributing to pollution and taking up valuable space.
The manufacturing process can release greenhouse gases, contributing to climate change.
Plastic waste frequently ends up in oceans, harming marine life.
Aluminum Foil
While aluminum foil offers excellent barrier properties, its production is energy-intensive, requiring significant electricity for the electrolysis process.
Mining bauxite ore, the raw material for aluminum, can lead to deforestation and habitat destruction.
Aluminum foil is often not easily recyclable, further contributing to waste.
Other Films
Various other materials, such as cellophane and coated papers, also have their own environmental impacts. Cellophane, for example, while biodegradable, may require specific composting conditions. Coated papers may contain plastics or other non-recyclable components.
Sustainable and Eco-Friendly Alternatives to Traditional Films
The food packaging industry is increasingly exploring sustainable alternatives to mitigate the environmental impact of traditional films. Several options are gaining traction, offering reduced environmental footprints.* Biodegradable Plastics: These plastics are designed to break down naturally in specific environments.
Polylactic Acid (PLA)
Derived from renewable resources like corn starch or sugarcane, PLA is biodegradable under industrial composting conditions.
Polyhydroxyalkanoates (PHAs)
Produced by microorganisms, PHAs are biodegradable in various environments, including soil and marine environments.
Compostable Films
These films are designed to break down into compost, enriching the soil. These films are often made from plant-based materials and are certified compostable.
Paper-Based Films
Paper can be used as a film or as a component of a film, especially when coated with biodegradable materials.
Paper is a renewable resource and can be recycled.
Edible Films
Edible films are made from materials that can be safely consumed.
These films offer a unique solution for reducing waste, as they are meant to be eaten along with the food. Examples include films made from proteins or polysaccharides.
Comparison of Biodegradable Films with Conventional Plastic Films
The performance characteristics of biodegradable films differ from those of conventional plastic films. The following table provides a comparative analysis:
Feature | Conventional Plastic Films (e.g., PE, PP) | Biodegradable Films (e.g., PLA, PHA) | Notes |
---|---|---|---|
Raw Material Source | Fossil fuels (oil, natural gas) | Renewable resources (corn starch, sugarcane, microorganisms) | Biodegradable films often utilize resources that can be replenished, reducing reliance on finite fossil fuels. |
Biodegradability | Non-biodegradable; persists in landfills | Biodegradable under specific conditions (industrial composting, soil, marine environments) | Biodegradable films offer a potential solution to reduce plastic waste accumulation. However, composting facilities are necessary. |
Barrier Properties (Oxygen, Moisture) | Generally good; can be tailored | May vary; some have lower barrier properties than conventional plastics | Barrier properties are crucial for food preservation. Research and development are focused on improving the barrier properties of biodegradable films. |
Cost | Generally lower cost | Often higher cost, but costs are decreasing with increased production and innovation | The cost of biodegradable films can be a barrier to adoption. However, economies of scale and technological advancements are reducing prices. |
Mechanical Properties (Tensile Strength, Flexibility) | Generally good and well-understood | May vary; some can be less durable than conventional plastics | Mechanical properties affect the performance of the film during wrapping and handling. Research is ongoing to improve these characteristics. |
Environmental Impact (Production) | High greenhouse gas emissions; use of fossil fuels | Generally lower greenhouse gas emissions, especially for PLA; use of renewable resources | The production process of biodegradable films can have a smaller environmental footprint than that of conventional plastics. |
Regulatory Compliance
Food wrap machines operate within a complex legal framework designed to protect consumer health and ensure fair trade practices. Adhering to these regulations is not just a matter of avoiding penalties; it’s fundamentally about safeguarding the food supply chain and maintaining consumer trust. This section delves into the key regulatory aspects governing food packaging and the critical role food wrap machines play in achieving compliance.
Relevant Regulations and Standards Governing Food Packaging
Numerous regulations and standards govern the materials, manufacturing processes, and labeling of food packaging, including those used by food wrap machines. These regulations vary by region, but several key standards are globally recognized.
A crucial set of regulations concerns the materials that come into contact with food, often referred to as Food Contact Materials (FCMs). These regulations aim to prevent the migration of harmful substances from the packaging into the food.
- Food and Drug Administration (FDA) (United States): The FDA sets standards for food packaging materials under the Federal Food, Drug, and Cosmetic Act (FFDCA). This includes regulations for materials like plastics, paper, and coatings used in direct contact with food. Compliance involves premarket approval for new materials and ongoing monitoring for safety. The FDA also regulates the labeling of food packaging, including the required information about the contents and the packaging materials used.
- European Food Safety Authority (EFSA) (European Union): EFSA provides scientific advice and risk assessments on food safety, including food packaging. The Framework Regulation (EC) No 1935/2004 sets out general principles for FCMs, requiring that they are safe and do not transfer their constituents to food in quantities that could endanger human health. Specific regulations exist for different materials, such as plastics (Regulation (EU) No 10/2011).
- Canadian Food Inspection Agency (CFIA) (Canada): The CFIA enforces regulations related to food packaging under the Food and Drugs Act and Regulations. These regulations cover the safety and suitability of packaging materials, as well as labeling requirements. The CFIA’s focus is to ensure that food packaging is safe and does not contaminate food.
- International Organization for Standardization (ISO): ISO standards provide internationally recognized guidelines for various aspects of food packaging, including quality management (ISO 9000 series) and environmental management (ISO 14000 series). While not legally binding, adherence to ISO standards demonstrates a commitment to best practices and can enhance a company’s reputation.
- Global Food Safety Initiative (GFSI): GFSI is a collaborative platform for food safety stakeholders. GFSI-recognized standards, such as those developed by the British Retail Consortium (BRC) and the Safe Quality Food (SQF) Institute, are widely adopted by food manufacturers and retailers. These standards include requirements for packaging materials and processes.
Importance of Adhering to Regulations for Food Safety
Compliance with food packaging regulations is paramount for ensuring food safety and protecting public health. Failure to adhere to these regulations can lead to severe consequences.
The primary reason for regulatory compliance is to prevent the contamination of food with harmful substances. Packaging materials can potentially leach chemicals into the food, posing health risks to consumers. Furthermore, non-compliant packaging can compromise the integrity of the food, leading to spoilage and the potential for bacterial growth.
- Preventing Chemical Migration: Regulations limit the types and amounts of chemicals that can migrate from packaging materials into food. For instance, specific regulations address the use of phthalates, bisphenol A (BPA), and other potentially harmful substances in plastics.
- Ensuring Food Integrity: Packaging must protect food from physical damage, spoilage, and contamination from external sources. Regulations dictate the barrier properties required for different food types, ensuring that packaging materials effectively preserve the food’s quality and safety.
- Protecting Against Microbial Contamination: Packaging materials must not support the growth of microorganisms. Regulations often specify requirements for the cleanliness and hygiene of packaging materials and the manufacturing processes used to create them.
- Consumer Protection: Accurate labeling is crucial for providing consumers with essential information about the food and its packaging. Regulations mandate the disclosure of ingredients, allergens, and other relevant details, empowering consumers to make informed choices.
- Legal and Financial Consequences: Non-compliance with food packaging regulations can result in significant penalties, including fines, product recalls, and legal action. These consequences can damage a company’s reputation and lead to substantial financial losses. For example, a major food manufacturer faced a multi-million dollar recall due to packaging contamination, highlighting the importance of strict adherence to regulations.
Role of Food Wrap Machines in Ensuring Compliance
Food wrap machines play a crucial role in ensuring compliance with food packaging regulations. By using the correct materials and operating within defined parameters, these machines help food manufacturers meet regulatory requirements.
Food wrap machines can be designed and operated to meet specific regulatory requirements. The selection of appropriate film materials, the control of sealing temperatures, and the overall operational procedures all contribute to achieving compliance.
- Material Selection: Food wrap machines can be configured to use packaging films that are compliant with relevant regulations. This includes films that meet FDA, EFSA, and other regional standards. The machine’s specifications often dictate the types of films that can be used, and manufacturers must ensure that the selected films are suitable for the food being packaged.
- Controlled Sealing Parameters: The sealing process is critical for maintaining the integrity of the packaging. Food wrap machines can precisely control sealing temperatures, pressures, and dwell times to ensure a secure seal that prevents contamination and preserves the food’s shelf life. The settings of the machine must be calibrated and monitored to guarantee consistency.
- Hygiene and Sanitation: Food wrap machines are designed to be cleaned and sanitized regularly to prevent the build-up of bacteria and other contaminants. Compliance with hygiene regulations is achieved through routine cleaning protocols, including the use of appropriate sanitizing agents and the adherence to established cleaning schedules.
- Traceability and Documentation: Many food wrap machines can integrate with traceability systems, allowing manufacturers to track packaging materials and processes. This is essential for regulatory compliance, as it enables quick identification and resolution of potential issues. Documentation of machine settings, maintenance, and cleaning procedures is crucial for demonstrating compliance.
- Labeling Integration: Some food wrap machines can apply labels to the packaging, ensuring that the required information, such as ingredients, nutritional facts, and expiration dates, is accurately displayed. The machine’s labeling system must be aligned with labeling regulations.
Market Trends and Future Outlook: Food Wrap Machine
The food wrap machine industry is dynamic, constantly evolving to meet the changing needs of the food industry and consumer demands. Understanding current trends and anticipating future developments is crucial for businesses operating within this sector. This section explores the key market trends, the factors driving demand, and the future trajectory of food wrap machine technology and its applications.
Current Market Trends
Several key trends are shaping the food wrap machine market. These trends reflect shifts in consumer preferences, technological advancements, and regulatory pressures.
- Increased Demand for Sustainable Packaging: Consumers are increasingly concerned about environmental impact, driving demand for eco-friendly packaging solutions. This trend is leading to the adoption of biodegradable films, compostable materials, and machines designed to minimize material waste. For example, the rise of plant-based packaging options and machines capable of handling these materials is a direct response to this trend.
- Automation and Robotics: Automation is becoming more prevalent, particularly in large-scale food processing and packaging facilities. Robotic systems are being integrated to improve efficiency, reduce labor costs, and enhance packaging precision. An example is the use of robotic arms to load and unload food products onto wrapping machines, increasing throughput significantly.
- Smart Packaging Technologies: Smart packaging incorporates technologies like sensors, indicators, and communication devices to provide information about the product’s condition, freshness, and origin. This trend includes the use of modified atmosphere packaging (MAP) to extend shelf life and the integration of RFID tags for tracking and tracing products.
- Customization and Flexibility: Food manufacturers are increasingly seeking machines that offer flexibility in terms of product size, shape, and packaging materials. This allows them to cater to diverse product lines and respond quickly to changing market demands. Modular machine designs and easily adjustable settings are key features in this regard.
- E-commerce and Direct-to-Consumer Sales: The growth of online food sales is influencing packaging requirements. Food wrap machines must now be capable of producing packaging that can withstand the rigors of shipping and maintain product integrity during transit. This includes the use of durable films and packaging designs that protect against damage.
Factors Driving Demand for Food Wrap Machines
Several factors are contributing to the continued growth of the food wrap machine market. These factors highlight the importance of efficient, reliable, and sustainable packaging solutions.
- Rising Global Population: A growing global population translates to increased demand for food, which in turn drives the need for efficient food processing and packaging. This includes a need for machines that can handle large volumes of products quickly and effectively.
- Growing Food Industry: The food industry is expanding, encompassing various sectors such as fresh produce, prepared meals, and snacks. This expansion necessitates advanced packaging solutions to protect, preserve, and transport food products.
- Increasing Focus on Food Safety: Food safety regulations are becoming stricter worldwide, requiring food manufacturers to adopt packaging solutions that protect products from contamination and maintain their quality. This is especially important for perishable items, where proper packaging can prevent spoilage and waste.
- Technological Advancements: Continuous advancements in packaging technology, such as improved film materials, automation, and smart packaging, are driving demand for newer and more efficient food wrap machines. These innovations provide better protection, extend shelf life, and enhance consumer convenience.
- Changing Consumer Preferences: Consumers are increasingly seeking convenience, portion control, and visually appealing packaging. Food wrap machines are adapting to meet these preferences by offering features like easy-open packaging, resealable options, and attractive designs.
Future of Food Wrap Machine Technology and Applications
The future of food wrap machines promises exciting advancements and expanded applications. Several key areas are expected to drive innovation and growth.
- Integration of Artificial Intelligence (AI): AI and machine learning are poised to revolutionize food wrap machines. AI can be used to optimize machine performance, predict maintenance needs, and improve packaging accuracy. AI-powered vision systems can also detect defects and ensure consistent packaging quality.
- Enhanced Sustainability: The focus on sustainability will continue, with increased use of biodegradable films, compostable packaging, and machines designed to minimize waste. Closed-loop systems that recycle packaging materials and reduce environmental impact will become more common.
- Development of Smart Packaging: Smart packaging will become more sophisticated, with the integration of sensors that monitor food freshness, track product location, and provide consumers with valuable information. This includes the use of indicators that change color to signal spoilage or temperature abuse.
- Customization and Personalization: Food wrap machines will offer greater flexibility in terms of packaging design and features, allowing manufacturers to create personalized packaging that meets specific consumer needs. This includes the ability to print customized labels, create unique packaging shapes, and offer variable portion sizes.
- Expanded Applications in Emerging Markets: Food wrap machines will find wider applications in emerging markets, where the demand for packaged food products is growing rapidly. This includes the development of machines that are affordable, easy to operate, and suitable for a variety of packaging needs. For example, small-scale food processors in developing countries will benefit from accessible and efficient packaging solutions.
Final Summary
So there you have it, yeah? Food wrap machines: they’re not just about wrapping food; they’re about keeping things fresh, safe, and lookin’ top-notch. From the simple manual ones to the super-smart automatic ones, they’re essential for the food industry. With all the tech and sustainability stuff, these machines are only gonna get better, so keep an eye out, yeah?
Peace out!