Food wrapper machines, at their heart, embody the sacred act of preserving life’s sustenance. They are not merely instruments of industry, but tools that extend the reach of nourishment, mirroring the universe’s boundless generosity. Each package sealed is a prayer for freshness, a testament to the interconnectedness of all things, from the farmer’s field to the consumer’s table. This journey of packaging is a lesson in mindful action, reminding us to appreciate the effort that goes into providing for ourselves and others.
These machines find their purpose in a myriad of industries, from the comforting aroma of bakeries to the savory delights of the meat and poultry sector. They cradle our favorite treats, ensuring they arrive in perfect condition, reflecting the care we should bestow upon all aspects of life. They embrace various packaging materials, from the simple to the complex, teaching us the value of utilizing resources wisely, echoing the earth’s own careful stewardship.
Introduction to Food Wrapper Machines
Food wrapper machines are indispensable in the modern food industry, playing a critical role in preserving freshness, extending shelf life, and enhancing product presentation. These machines automate the process of wrapping food items in various packaging materials, from simple films to complex multi-layered structures. Their efficiency and versatility make them essential for businesses of all sizes, contributing significantly to the global food supply chain.
Primary Function of a Food Wrapper Machine
The primary function of a food wrapper machine is to enclose food products in protective packaging. This process serves several critical purposes, including:
- Preservation: Packaging acts as a barrier against environmental factors like oxygen, moisture, and light, which can degrade food quality and accelerate spoilage.
- Protection: Packaging shields food products from physical damage during handling, transportation, and storage.
- Presentation: Packaging enhances the visual appeal of food products, attracting consumers and conveying branding information.
- Portion Control: Machines can package food in pre-determined portions, simplifying consumer use and managing inventory.
- Information Delivery: Packaging provides a platform for displaying essential information, such as ingredients, nutritional facts, and expiration dates.
Industries Utilizing Food Wrapper Machines
Food wrapper machines are utilized across a wide range of industries involved in the production, processing, and distribution of food products. Their adaptability and efficiency make them valuable assets in diverse sectors:
- Bakery: Wrapping bread, pastries, cakes, and other baked goods to maintain freshness and prevent contamination.
- Meat and Poultry: Packaging raw and processed meats, poultry, and seafood to ensure food safety and extend shelf life.
- Dairy: Wrapping cheese, butter, and other dairy products to preserve their quality and prevent spoilage.
- Produce: Packaging fruits and vegetables to protect them from damage and maintain their freshness during transport and storage.
- Snack Foods: Wrapping chips, cookies, candies, and other snack items to preserve their crispness and prevent contamination.
- Ready-to-Eat Meals: Packaging prepared meals, salads, and other convenience foods for retail sale and consumer convenience.
- Frozen Foods: Wrapping frozen products like pizzas, vegetables, and ice cream to protect them from freezer burn and maintain quality.
Examples of Common Food Products Packaged by These Machines
Food wrapper machines handle a vast array of food products, each requiring specific packaging techniques and materials. Here are some common examples:
- Bread: Wrapped in plastic film to maintain freshness and prevent drying. A typical bread wrapper machine uses a flow wrapping method.
- Meat: Packaged in trays with overwrap film or vacuum-sealed to extend shelf life and prevent bacterial growth. Modified Atmosphere Packaging (MAP) is often employed for meat products.
- Cheese: Wrapped in plastic film, foil, or wax paper to protect from drying and maintain flavor. Hard cheeses are often vacuum-packed.
- Produce (Apples): Individual apples are often flow-wrapped to prevent bruising and enhance presentation. Clamshell packaging is also common for berries.
- Chips: Packaged in flexible pouches or bags to maintain crispness and prevent oxidation. Nitrogen flushing is frequently used to extend shelf life.
- Candy Bars: Wrapped in foil or plastic film to protect from moisture and maintain freshness. These are commonly flow wrapped.
- Frozen Pizza: Encased in cardboard boxes or wrapped in plastic film to protect from freezer burn and physical damage.
Types of Food Wrapper Machines
Choosing the right food wrapper machine is critical for optimizing packaging efficiency, preserving product freshness, and minimizing waste. The food industry offers a variety of machines, each designed to handle specific product types, packaging materials, and production volumes. Understanding the different types of machines and their capabilities allows businesses to select the most suitable solution for their needs. This decision directly impacts operational costs, product presentation, and ultimately, customer satisfaction.
Horizontal vs. Vertical Form-Fill-Seal Machines
Form-fill-seal (FFS) machines are the workhorses of the food packaging industry, creating packages directly from rolls of flexible film. These machines come in two primary configurations: horizontal and vertical. The choice between horizontal and vertical FFS machines depends on the product’s characteristics, desired package style, and production requirements.The primary difference lies in the orientation of the packaging process. Horizontal FFS machines, also known as flow wrappers, move the product horizontally through the machine.
Vertical FFS machines, on the other hand, move the product vertically. This fundamental difference influences everything from the types of products that can be packaged to the speed and efficiency of the packaging process.Here’s a breakdown of the advantages and disadvantages of each type:* Horizontal Form-Fill-Seal (Flow Wrappers):
Advantages
High-speed operation, ideal for products requiring rapid packaging.
Suitable for a wide variety of products, including solid and individually wrapped items.
Produce attractive, airtight packages with good product visibility.
Generally easier to integrate into existing production lines.
Disadvantages
Not ideal for liquids or products that easily spill.
May require more floor space than vertical machines.
Can be less efficient for products that need to settle during the packaging process.
* Vertical Form-Fill-Seal Machines:
Advantages
Well-suited for granular, powdered, and liquid products.
Compact footprint, saving valuable floor space.
Efficient for products that need to settle during packaging.
Can incorporate features like gas flushing for extended shelf life.
Disadvantages
Slower packaging speeds compared to horizontal machines.
Less suitable for irregularly shaped or fragile products.
May require more complex machinery for certain applications.
Comparing Food Wrapper Machine Types
Selecting the right food wrapper machine involves evaluating several factors, including product type, packaging requirements, and production volume. The following table provides a comparative analysis of three common types of food wrapper machines: Flow Wrappers, Overwrappers, and Tray Sealers. This information will aid in the selection process, providing a quick reference guide to the key features of each type.
Feature | Flow Wrappers | Overwrappers | Tray Sealers |
---|---|---|---|
Packaging Style | Creates a pillow-shaped or fin-sealed package around the product. | Wraps a pre-formed tray or container with film. | Seals a film to a pre-formed tray, creating an airtight seal. |
Product Type | Suitable for solid products, individual items, and multi-packs. | Typically used for products in trays, cartons, or other containers. | Ideal for products packaged in trays, providing a sealed environment. |
Speed | High-speed operation, capable of packaging a large volume of products. | Moderate speed, depending on the complexity of the wrapping process. | Moderate to high speed, depending on the tray sealing requirements. |
Packaging Material | Uses flexible films, such as polypropylene, cellophane, and laminates. | Uses flexible films, such as cellophane, polypropylene, and shrink films. | Uses a variety of films, including lidding films and barrier films. |
Product Protection | Provides good protection against moisture and contaminants. | Offers moderate protection, primarily for aesthetic appeal and tamper evidence. | Provides excellent protection, creating an airtight seal for extended shelf life. |
Applications | Candy bars, baked goods, snacks, produce, and medical devices. | Boxes of chocolates, cosmetics, and pharmaceuticals. | Fresh produce, ready-to-eat meals, and meat products. |
Components and Operation
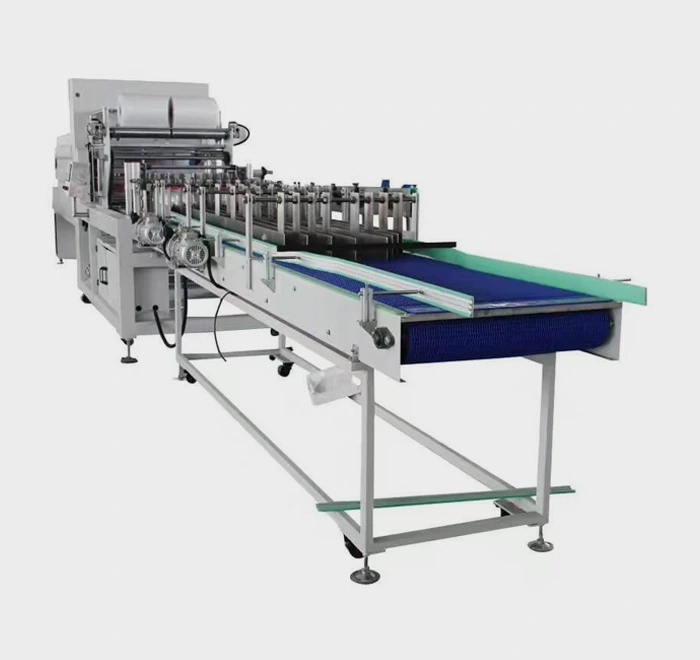
Understanding the inner workings of a food wrapper machine is crucial for optimizing its performance and ensuring efficient packaging. These machines are complex systems comprised of various interconnected components, each playing a vital role in transforming raw product into sealed, ready-to-ship packages. This section delves into the essential elements, their functions, and the step-by-step process of food packaging.
Essential Components of a Food Wrapper Machine
Food wrapper machines, regardless of their specific type, rely on a core set of components to function. These components work in concert to receive, form, fill, and seal packages.
- Product Infeed System: This system is responsible for delivering the food product to the packaging machine. It can range from simple conveyor belts to more sophisticated systems that automatically orient and feed products.
- Forming System: This system shapes the packaging material, typically flexible film, into the desired package form. It often involves folding the film around a forming collar or mandrel.
- Filling System: The filling system accurately dispenses the pre-determined amount of product into the formed package. This system varies depending on the product type, using auger fillers for powders, volumetric fillers for liquids, or weigh-fill systems for solid products.
- Sealing System: The sealing system closes and seals the package, creating an airtight or hermetic seal. This is usually achieved through heat sealing, ultrasonic sealing, or impulse sealing.
- Cutting System: This system separates the individual packages from the continuous web of packaging material. This can involve rotary knives, reciprocating knives, or other cutting mechanisms.
- Control System: A central control system, often a Programmable Logic Controller (PLC), manages and coordinates the operation of all other components, ensuring synchronized operation and package consistency.
- Film Delivery System: This system feeds the packaging film to the forming system. It controls the film’s tension and alignment to ensure proper package formation.
Role of Each Component in the Packaging Process
Each component contributes significantly to the overall packaging process. Their coordinated actions ensure the efficient and accurate creation of packaged food products.
- Product Infeed System: The infeed system prepares the product for packaging. Its efficiency directly impacts the machine’s throughput. For example, a candy bar wrapper might use a vibratory feeder to align and single-file the bars before they enter the forming system.
- Forming System: The forming system creates the package shape. For example, in a horizontal form-fill-seal (HFFS) machine, the film is drawn over a forming collar to create a tube, which is then filled and sealed.
- Filling System: The filling system ensures the correct amount of product is dispensed into each package. The accuracy of the filling system is critical for maintaining product consistency and meeting weight regulations. For instance, a snack food packaging machine uses a volumetric filler to measure the exact amount of chips or crackers.
- Sealing System: The sealing system creates a secure and airtight seal. This seal protects the product from contamination and extends its shelf life. The sealing process parameters (temperature, pressure, and dwell time) are precisely controlled.
- Cutting System: The cutting system separates the individual packages. Precise cutting is essential for producing uniform packages.
- Control System: The control system is the brain of the machine, coordinating all operations. It monitors sensors, adjusts parameters, and ensures the machine operates smoothly and safely.
- Film Delivery System: The film delivery system ensures proper film handling. Correct film tension is critical for the quality of the final package.
Steps Involved in the Packaging Process
The packaging process is a sequential series of steps that transforms bulk product into individually packaged units. The steps are precisely timed and coordinated by the control system.
- Product Infeed: The food product is delivered to the machine via the infeed system. This might involve a conveyor belt, a vibratory feeder, or a robotic arm, depending on the product.
- Film Feeding: The packaging film is unwound from a roll and fed into the machine by the film delivery system.
- Package Forming: The forming system shapes the film into the desired package configuration. This may involve folding the film around a forming collar or using a mold.
- Product Filling: The filling system dispenses the pre-determined amount of product into the formed package.
- Sealing: The sealing system closes and seals the package, creating an airtight seal. This usually involves heat sealing, though other methods like ultrasonic or impulse sealing are used.
- Cutting: The cutting system separates the individual packages from the continuous web of packaging material.
- Package Discharge: The finished packages are discharged from the machine, often onto a conveyor belt for further processing, such as labeling or cartoning.
Diagram of a Horizontal Form-Fill-Seal (HFFS) Machine
The following diagram illustrates the flow of a product through a horizontal form-fill-seal (HFFS) machine, a common type of food wrapper.
Diagram Description:
The diagram depicts a horizontal form-fill-seal (HFFS) machine, illustrating the sequential steps of the packaging process. The machine is oriented horizontally, with the product entering from the left and the finished packages exiting on the right.
1. Product Infeed: On the left, a stream of individual food products (e.g., candy bars) is shown being fed onto a horizontal conveyor belt. Arrows indicate the direction of product flow towards the right.
2. Film Unwinding: Above the conveyor belt, a roll of flexible packaging film is depicted. The film is unwound and fed downwards towards the forming section. Arrows show the direction of film movement.
3. Forming Collar: The film is drawn over a forming collar, which shapes the film into a tube. This collar is located near the product infeed area. The formed tube is then guided along the conveyor.
4. Product Loading: The food products are placed inside the tube of film, usually with the help of a transfer system. The product is carefully positioned within the formed package.
5. Horizontal Sealing Jaws: A pair of horizontal sealing jaws are located downstream from the product loading area. These jaws move together, applying heat and pressure to seal the top and bottom of the package, creating individual pouches.
6. Vertical Sealing Jaws: Vertical sealing jaws seal the ends of the package. These jaws move together, creating the end seals, typically in a fin seal configuration.
7. Cutting Blade: A cutting blade positioned after the sealing jaws cuts the continuous film into individual packages. This is typically a rotary knife. The blade’s position is synchronized with the sealing operation.
8. Finished Packages: On the right, the finished, sealed, and cut packages are shown exiting the machine onto another conveyor. Arrows show the direction of the finished product flow.
9. Overall Flow: The diagram illustrates the continuous flow of product and film, highlighting the coordinated operation of the machine’s components. The entire process is controlled by a PLC, not shown in the diagram.
Materials Used in Food Wrapping
Food wrapper machines are versatile, but their effectiveness hinges on the packaging materials they utilize. The choice of material directly impacts the food’s shelf life, preservation, and presentation. Understanding these materials and their properties is crucial for optimizing the wrapping process and ensuring consumer satisfaction.
Types of Packaging Materials
Food wrapper machines employ a diverse range of materials to suit various food products and their specific requirements. These materials are chosen based on factors like barrier properties, sealability, and cost-effectiveness.
- Flexible Films: These are the most common type, offering flexibility and ease of use. They are typically used for wrapping snacks, candies, and baked goods. Examples include:
- Polyethylene (PE): A widely used thermoplastic polymer known for its excellent moisture barrier properties and flexibility.
- Polypropylene (PP): Offers good clarity, stiffness, and heat resistance, making it suitable for high-speed wrapping applications.
- Polyester (PET): Provides superior strength, clarity, and barrier properties against oxygen and moisture, extending shelf life.
- Laminates: Combining multiple layers of different films, often including foil or metallized films, to enhance barrier properties and provide specific functionalities.
- Paper-Based Materials: Used for eco-friendly packaging solutions and often paired with coatings for enhanced protection. Examples include:
- Waxed Paper: Offers moisture resistance, commonly used for wrapping sandwiches and other foods.
- Paperboard: Provides rigidity and is often used for boxes and trays.
- Coated Paper: Enhanced with coatings like polyethylene to improve barrier properties and sealability.
- Rigid Containers: Though less common in wrapper machines, these can be used in conjunction with them, especially for tray sealing or overwrap applications. Examples include:
- Plastic Trays: Used for pre-packaged foods like fruits, vegetables, and ready meals.
- Aluminum Trays: Offer excellent heat resistance and are suitable for ovenable products.
Properties of Different Films
Each film type possesses unique properties that dictate its suitability for different food products. Understanding these properties is critical for selecting the right material.
- Polyethylene (PE):
- Offers excellent moisture barrier properties, protecting food from humidity.
- Provides good sealability, ensuring the package is airtight.
- Is flexible and relatively inexpensive, making it cost-effective for various applications.
- Is commonly used for wrapping bread, frozen foods, and produce.
- Polypropylene (PP):
- Provides excellent clarity, enhancing product visibility on shelves.
- Offers good stiffness, maintaining the package shape.
- Exhibits high heat resistance, making it suitable for hot-fill applications.
- Is frequently used for wrapping snacks, candies, and confectionery items.
- Laminates:
- Provide enhanced barrier properties by combining different materials.
- Can offer superior protection against oxygen, moisture, and light.
- Often include layers of PET, foil, and PE to create a multi-functional barrier.
- Are used for packaging coffee, snacks, and processed foods to extend shelf life and maintain product quality.
Factors Influencing the Choice of Packaging Material
Several factors influence the selection of the packaging material for food wrapper machines. These factors must be carefully considered to ensure optimal performance and product protection.
- Food Product Characteristics: The type of food product, its moisture content, fat content, and sensitivity to oxygen and light, all influence the choice. For example, products with high fat content require materials with good barrier properties to prevent rancidity.
- Shelf Life Requirements: Longer shelf life necessitates materials with superior barrier properties to protect against spoilage and degradation.
- Packaging Machinery Compatibility: The chosen material must be compatible with the food wrapper machine’s sealing and wrapping mechanisms.
- Cost Considerations: Material cost is a significant factor, as it directly impacts the overall packaging cost.
- Sustainability Goals: Increasing consumer demand for sustainable packaging drives the adoption of eco-friendly materials.
Sustainable Packaging Materials and Their Applications
The food industry is increasingly focused on sustainable packaging solutions. Several innovative materials are emerging to reduce environmental impact.
- Biodegradable Plastics: These plastics are derived from renewable resources, such as corn starch or sugarcane, and break down naturally. They are suitable for wrapping fruits, vegetables, and other perishable items. An example is Polylactic acid (PLA), derived from corn starch.
- Compostable Films: These films are designed to break down in industrial composting facilities, leaving no harmful residues. They are ideal for packaging items like coffee pods or tea bags.
- Recycled Content Materials: Utilizing recycled plastics in packaging reduces the demand for virgin materials and minimizes waste. Recycled PET (rPET) is commonly used for bottles and trays.
- Paper-Based Packaging: Paper and paperboard are renewable and recyclable resources. Coatings can be applied to enhance barrier properties. Examples include:
- Using paper-based trays for ready meals, reducing plastic usage.
- Paper wrappers for sandwiches and baked goods.
Advantages of Using Food Wrapper Machines
Automating the food packaging process with wrapper machines offers a multitude of benefits, transforming how food products are handled, preserved, and presented to consumers. These machines aren’t just about speed; they represent a comprehensive solution that boosts efficiency, reduces costs, and enhances product quality. From small businesses to large-scale manufacturers, the advantages of integrating food wrapper machines are undeniable, contributing to increased profitability and customer satisfaction.
Improved Efficiency and Reduced Labor Costs
Food wrapper machines significantly streamline the packaging process, leading to a substantial increase in operational efficiency. The automation inherent in these machines allows for higher throughput compared to manual packaging methods.The reduction in labor requirements is a direct result of automation. Machines can perform packaging tasks at a rate far exceeding human capabilities, eliminating the need for a large workforce dedicated to packaging.
This frees up human resources to focus on other critical aspects of the business, such as product development, marketing, and customer service. Consider a bakery that previously employed five workers solely for wrapping bread loaves. By investing in an automated wrapper, the bakery can now wrap the same number of loaves with only one or two operators, significantly lowering labor expenses.
Preserving Product Freshness and Extending Shelf Life
Food wrapper machines play a crucial role in maintaining product freshness and extending shelf life. The ability to create airtight seals and control the packaging environment helps to prevent spoilage and degradation.By tightly sealing food products, these machines minimize exposure to oxygen, moisture, and contaminants. Oxygen exposure is a primary cause of food spoilage, leading to oxidation and the growth of microorganisms.
Moisture can promote mold and bacterial growth, while contaminants can compromise the safety and quality of the food. The precise control offered by wrapper machines helps create a barrier against these factors.The use of modified atmosphere packaging (MAP) is a prime example of how wrapper machines extend shelf life. MAP involves replacing the air inside the package with a gas mixture designed to slow down the deterioration process.
This is commonly used for fresh produce, meat, and prepared meals. For instance, pre-packaged salads utilizing MAP can maintain their freshness for several days longer than those packaged without this technology.
Here’s a bulleted list highlighting the key advantages:
- Increased Packaging Speed: Automated machines package products at a significantly faster rate than manual methods.
- Reduced Labor Costs: Fewer human workers are required for packaging operations.
- Enhanced Product Freshness: Airtight seals and controlled environments prevent spoilage.
- Extended Shelf Life: Products stay fresh for longer, reducing waste and increasing marketability.
- Consistent Packaging Quality: Machines ensure uniform packaging, improving product presentation.
- Reduced Material Waste: Precise control over material usage minimizes waste and lowers costs.
- Improved Hygiene: Automated processes minimize human contact, reducing the risk of contamination.
- Increased Production Capacity: Businesses can handle higher volumes of products with existing resources.
- Versatile Packaging Options: Machines can handle a variety of packaging formats and materials.
- Improved Brand Image: Professional-looking packaging enhances the product’s appeal to consumers.
Factors to Consider When Selecting a Machine
Choosing the right food wrapper machine is a crucial decision that directly impacts the efficiency, cost-effectiveness, and overall success of your food packaging operation. A poorly chosen machine can lead to wasted materials, slower production, and ultimately, lost profits. This section will Artikel the key factors to consider when making this important investment.
Production Speed and Throughput
Production speed, measured in packages per minute (PPM) or units per hour (UPH), is a primary determinant of a machine’s suitability for your needs. It must align with your current production volume and anticipated future growth.Consider the following:
- Current Demand: Accurately assess your present packaging requirements. Determine the number of products that need to be wrapped per hour or day.
- Future Growth: Project potential increases in demand over the next 1-3 years. Select a machine with a capacity that exceeds your current needs to accommodate expansion.
- Machine Cycle Time: Understand the time it takes for the machine to complete one packaging cycle. This includes the time for feeding, wrapping, sealing, and discharging the product.
- Line Integration: Evaluate how the machine will integrate with existing production lines. Consider the need for conveyors, feeders, and other equipment to ensure seamless product flow.
Product Size and Shape Compatibility
The dimensions and form of your product significantly influence the type of food wrapper machine you need. Machines are designed to handle specific size ranges and product geometries.Consider the following:
- Product Dimensions: Measure the length, width, and height of your product. Ensure the machine’s specifications accommodate these dimensions, including the minimum and maximum sizes it can handle.
- Product Shape: Determine the shape of your product (e.g., rectangular, cylindrical, irregular). Different machine types are better suited for certain shapes. For instance, flow wrappers are often used for irregularly shaped items, while box wrappers are ideal for rectangular boxes.
- Product Weight: Note the weight of each product, as this affects the machine’s ability to handle and wrap the product efficiently. Heavy products may require more robust machinery.
- Product Stability: Consider the stability of the product during the wrapping process. Unstable products may require special handling features or pre-forming mechanisms.
Packaging Material Compatibility
The type of packaging material you intend to use is another critical factor. Different machines are designed to work with specific materials, and the machine must be compatible with your chosen material.Consider the following:
- Material Type: Determine the packaging material you will use (e.g., plastic films, paper, foil). Ensure the machine is designed to handle the chosen material.
- Material Thickness: The thickness of the packaging material impacts machine performance. Thicker materials may require more powerful sealing mechanisms.
- Material Properties: Consider the material’s sealing properties, such as heat sealability and cold sealability. The machine must be equipped with the appropriate sealing technology.
- Material Roll Size: Determine the maximum roll size the machine can accommodate. This impacts how often you need to change the packaging material rolls.
Machine Reliability and Maintenance Requirements
The reliability and maintenance needs of the machine directly affect your operational uptime and overall costs. A reliable machine minimizes downtime and ensures consistent production.Consider the following:
- Mean Time Between Failures (MTBF): Research the MTBF of the machine. A higher MTBF indicates greater reliability.
- Maintenance Schedule: Review the recommended maintenance schedule and requirements. Ensure you have the resources and expertise to perform the necessary maintenance.
- Spare Parts Availability: Verify the availability of spare parts and the lead time for obtaining them. This is critical to minimizing downtime in case of a breakdown.
- Service and Support: Evaluate the manufacturer’s service and support capabilities. Consider the availability of technical support, training, and on-site service.
Automation and Flexibility
Automation features and the machine’s flexibility impact efficiency and the ability to adapt to changing needs. Highly automated machines can significantly reduce labor costs.Consider the following:
- Level of Automation: Assess the level of automation required. Consider features such as automatic feeding, product handling, and sealing.
- Changeover Time: Determine the time required to switch between different product sizes or packaging materials. Faster changeover times increase flexibility.
- Programmability: Evaluate the machine’s programmability. A programmable machine allows you to easily adjust settings and save recipes for different products.
- Expandability: Consider the machine’s potential for future upgrades and expansion. This allows you to adapt to changing production needs without having to replace the entire machine.
Cost and Return on Investment (ROI)
The initial cost of the machine and its operational costs are significant considerations. Evaluating the ROI helps you make an informed financial decision.Consider the following:
- Initial Purchase Price: Obtain quotes from multiple vendors and compare the initial purchase price of different machines.
- Operational Costs: Factor in ongoing operational costs, such as energy consumption, packaging material costs, and maintenance expenses.
- Labor Costs: Estimate the labor costs associated with operating the machine. Consider the number of operators required and their hourly wages.
- ROI Calculation: Calculate the expected ROI by comparing the cost savings and increased efficiency of the machine against its initial investment and operational costs.
Critical Specifications for Packaging a Box of Cookies:* Product Dimensions: Length: 20 cm, Width: 10 cm, Height: 5 cm
Product Weight
250 grams
Packaging Material
Polypropylene film, heat-sealable
Production Speed
60 packages per minute
Machine Type
Horizontal flow wrapper with automatic infeed system
Sealing Method
Heat sealing
You also can investigate more thoroughly about k foods chicken to enhance your awareness in the field of k foods chicken.
Machine Requirements
Capable of handling rectangular products, precise temperature control for sealing, and reliable performance.
Applications in Different Food Industries
Food wrapper machines are indispensable tools in the modern food industry, playing a crucial role in preserving food quality, extending shelf life, and enhancing product presentation. Their versatility allows them to be adapted to various food types and production scales, leading to significant efficiency gains and reduced waste. Understanding the specific applications across different sectors highlights their importance in the food supply chain.
Applications in the Bakery Industry
The bakery industry extensively utilizes food wrapper machines to package a wide range of products, from bread and pastries to cakes and cookies. These machines ensure freshness, prevent contamination, and provide an attractive presentation for consumers.
- Bread Packaging: Bread wrapper machines are commonly used to wrap loaves of bread, protecting them from air exposure and maintaining their soft texture. The machines can handle various bread sizes and shapes, including sliced and unsliced loaves.
- Pastry Wrapping: Croissants, muffins, and other pastries benefit from individual or grouped packaging. This protects delicate items from damage and keeps them fresh for longer. Flow wrappers are particularly well-suited for these applications.
- Cake and Cookie Packaging: Cakes and cookies are often packaged in trays or boxes, which are then sealed using wrapping machines. This protects the products and enhances their visual appeal. Shrink wrapping is also used for these items to provide a secure seal.
- Dough Products: Packaging machines help in sealing dough products to maintain their freshness.
Applications in the Confectionery Sector
The confectionery sector relies heavily on food wrapper machines to package candies, chocolates, and other sweet treats. These machines contribute to product protection, portion control, and brand recognition.
- Candy Wrapping: Individual candies and candy bars are often wrapped using high-speed flow wrappers or twist wrappers. This process maintains freshness and provides a convenient way for consumers to purchase the products.
- Chocolate Packaging: Chocolates are often packaged in foil or film wrappers to protect them from light, moisture, and temperature changes. Machines can handle a variety of chocolate shapes and sizes.
- Boxed Chocolates: Boxes of chocolates are typically sealed with film to maintain freshness and prevent tampering. These machines can apply labels and other branding elements.
- Gummy and Chewy Candies: Gummy candies are packaged using flow wrappers or pouch-filling machines, providing a sealed package for freshness.
Applications in the Meat and Poultry Processing Industry
The meat and poultry processing industry uses food wrapper machines extensively for packaging fresh, frozen, and processed meat products. This is crucial for food safety, preservation, and consumer convenience.
- Fresh Meat Packaging: Vacuum packaging and modified atmosphere packaging (MAP) are common techniques used to extend the shelf life of fresh meat. These machines remove oxygen or alter the gas composition within the package, inhibiting bacterial growth.
- Processed Meat Packaging: Sausages, bacon, and deli meats are often packaged using flow wrappers or tray sealers. These machines protect the products and provide a convenient way for consumers to purchase them.
- Poultry Packaging: Whole chickens and poultry parts are frequently packaged using shrink wrapping or vacuum packaging. This preserves the product and provides a secure seal.
- Portion Control: Packaging machines can be used to create pre-portioned meat products, making it easier for consumers to manage portion sizes.
Applications in the Snack Food Industry
The snack food industry utilizes food wrapper machines extensively to package chips, crackers, pretzels, and other snack items. These machines are essential for maintaining product freshness, preventing damage, and ensuring portion control.
- Chip Packaging: Flow wrappers are commonly used to package bags of chips. These machines create a sealed package that protects the chips from air and moisture.
- Cracker Packaging: Crackers are often packaged in boxes or trays, which are then sealed using wrapping machines. This preserves the product and provides an attractive presentation.
- Pretzel Packaging: Pretzels are frequently packaged in bags or boxes, using flow wrappers or vertical form-fill-seal machines. This keeps the pretzels fresh and prevents breakage.
- Popcorn Packaging: Popcorn can be packaged in bags or boxes using flow wrappers or vertical form-fill-seal machines, which maintain freshness.
Food Industry | Typical Products Packaged | Common Packaging Methods | Benefits of Using Wrapper Machines |
---|---|---|---|
Bakery | Bread, pastries, cakes, cookies | Flow wrapping, tray sealing, shrink wrapping | Preservation of freshness, protection from damage, enhanced product presentation |
Confectionery | Candies, chocolates, boxed chocolates, gummy candies | Flow wrapping, twist wrapping, foil wrapping, pouch filling | Protection from moisture and light, portion control, brand recognition |
Meat and Poultry | Fresh meat, processed meats, poultry | Vacuum packaging, MAP, shrink wrapping, tray sealing | Extended shelf life, food safety, portion control, prevention of contamination |
Snack Food | Chips, crackers, pretzels, popcorn | Flow wrapping, vertical form-fill-seal | Preservation of freshness, prevention of breakage, portion control, improved consumer convenience |
Maintenance and Troubleshooting
Food wrapper machines, like any sophisticated piece of equipment, require diligent maintenance and proactive troubleshooting to ensure optimal performance and longevity. Neglecting these crucial aspects can lead to costly downtime, reduced efficiency, and potential safety hazards. Regular maintenance, coupled with effective troubleshooting, is essential for maximizing the return on investment in your food wrapping operation.
Routine Maintenance Procedures, Food wrapper machine
Implementing a consistent maintenance schedule is key to preventing unexpected breakdowns and maintaining the machine’s efficiency. This involves a combination of daily, weekly, and monthly tasks.
- Daily Checks: Daily inspections focus on readily observable areas and should be performed before each shift.
- Cleaning: Remove food debris, dust, and any accumulated materials from the machine’s exterior, wrapping area, and sealing components. This prevents contamination and ensures proper sealing.
- Visual Inspection: Check for any loose parts, unusual noises, or signs of wear and tear on belts, chains, and rollers. Look for any leaks of lubricants or hydraulic fluids.
- Film Supply: Verify the film supply is adequate for the day’s production.
- Weekly Maintenance: Weekly tasks involve more in-depth checks and cleaning.
- Lubrication: Lubricate moving parts, such as bearings, chains, and gears, according to the manufacturer’s recommendations. This reduces friction and wear.
- Seal Jaw Inspection: Inspect the sealing jaws for any damage, such as scratches or wear. Clean them thoroughly to ensure a proper seal.
- Film Path Alignment: Check the film path to ensure it is correctly aligned and running smoothly. Misalignment can lead to film jams and poor sealing.
- Monthly Maintenance: Monthly maintenance includes more thorough inspections and potential adjustments.
- Filter Replacement: Replace air filters and any other filters as specified by the manufacturer. This helps maintain air quality and prevent contamination.
- Electrical Component Inspection: Inspect electrical components, such as wiring and connectors, for any signs of damage or wear. Ensure all safety devices are functioning correctly.
- Performance Testing: Run test packages to evaluate the machine’s sealing and wrapping performance. Check for any inconsistencies or defects.
Common Troubleshooting Tips for Operational Issues
Despite regular maintenance, issues can arise. Knowing how to diagnose and address common problems can minimize downtime.
- Machine Won’t Start: If the machine fails to power on, first check the power supply, circuit breakers, and emergency stop button. If these are functioning, consult the machine’s manual for troubleshooting specific to your model.
- Poor Sealing: If the seals are weak or inconsistent, inspect the sealing jaws for damage or contamination. Adjust the sealing temperature, pressure, and dwell time as needed. Ensure the correct film type is being used.
- Film Jams: Film jams are a common problem. Identify the source of the jam, such as incorrect film loading, film misalignment, or a worn-out film knife. Correct the issue by re-threading the film, adjusting the film path, or replacing the knife.
- Inconsistent Wrapping: If packages are not wrapped consistently, check the film tension, the wrapping speed, and the alignment of the wrapping components. Adjust these parameters to achieve consistent results.
- Unusual Noises: Any unusual noises should be investigated immediately. These can indicate worn parts, misalignment, or other issues. Turn off the machine and inspect the area where the noise originates.
Importance of Regular Inspections and Preventative Maintenance
Regular inspections and preventative maintenance are the cornerstones of a well-functioning food wrapping operation. They are critical for several reasons.
- Minimizing Downtime: Regular maintenance helps identify and address potential problems before they escalate into major breakdowns, thus minimizing costly downtime.
- Extending Machine Lifespan: Preventative maintenance helps to extend the lifespan of the machine by reducing wear and tear on components.
- Improving Efficiency: A well-maintained machine operates more efficiently, reducing waste and increasing productivity.
- Ensuring Food Safety: Regular cleaning and maintenance help prevent food contamination, which is critical for food safety.
- Reducing Repair Costs: Addressing small problems early on prevents them from becoming major repairs, ultimately reducing overall maintenance costs.
Guidance on Handling Common Problems: Film Jams and Seal Failures
Film jams and seal failures are among the most frequent issues encountered. Knowing how to handle these problems can significantly reduce downtime.
- Film Jams: When a film jam occurs, first, turn off the machine and disconnect the power. Carefully remove the jammed film, paying attention to the film path. Check for any obstructions or damaged components. Ensure the film is loaded correctly and the film path is aligned. Replace any damaged parts.
- Seal Failures: If the seals are failing, check the sealing jaws for damage, such as scratches or wear. Ensure the correct sealing temperature, pressure, and dwell time are set for the film type being used. Clean the sealing jaws to remove any residue. Check the film for wrinkles or folds that might be interfering with the seal. Consider replacing the sealing jaws if they are worn.
Technological Advancements
The food packaging industry is experiencing a rapid transformation, driven by continuous technological advancements. These innovations are reshaping how food wrapper machines operate, enhancing efficiency, improving product quality, and reducing waste. The integration of cutting-edge technologies is crucial for meeting the evolving demands of consumers and the industry.
Automation and Robotics Integration
Automation and robotics have become integral components of modern food wrapper machines. This integration streamlines processes, boosts productivity, and minimizes human error.
- Robotic arms are now commonly used for picking, placing, and orienting products with speed and precision. These robots can handle a wide range of product sizes and shapes, adapting to various packaging needs.
- Automated guided vehicles (AGVs) transport materials and finished products, optimizing workflow and reducing the need for manual handling. This leads to improved safety and efficiency in the packaging process.
- Automated systems also control sealing, labeling, and inspection, ensuring consistent quality and minimizing the risk of defects. The use of automated systems significantly reduces downtime and labor costs.
Smart Sensors and Data Analytics
Smart sensors and data analytics play a critical role in optimizing food wrapper machine performance. These technologies collect and analyze data to provide valuable insights into the packaging process.
- Sensors monitor various parameters, including temperature, pressure, and material flow, ensuring optimal operating conditions. Data collected from these sensors provides real-time feedback and enables proactive maintenance.
- Data analytics tools analyze the collected data to identify trends, predict potential issues, and optimize machine performance. This data-driven approach helps in making informed decisions and improving overall efficiency.
- Predictive maintenance algorithms use historical data to anticipate equipment failures, reducing downtime and maintenance costs. By identifying potential problems early, manufacturers can prevent costly disruptions.
Impact on Packaging Efficiency and Quality
Technological advancements have significantly improved both the efficiency and the quality of food packaging. These improvements directly benefit manufacturers and consumers alike.
- Increased speed and throughput: Automation and robotics have dramatically increased packaging speeds, allowing manufacturers to meet high-volume demands efficiently. This leads to reduced production times and lower per-unit costs.
- Enhanced precision and accuracy: Smart sensors and automated systems ensure precise sealing, labeling, and product placement, resulting in consistent and high-quality packaging. This reduces waste and minimizes product damage.
- Improved product preservation: Advanced packaging materials and techniques, coupled with precise control over packaging processes, help to extend the shelf life of food products. This minimizes spoilage and waste.
- Real-time monitoring and control: Data analytics and smart sensors enable real-time monitoring of the packaging process, allowing for immediate adjustments and corrections. This ensures optimal performance and consistent product quality.
Futuristic Food Wrapper Machine
Envision a futuristic food wrapper machine that seamlessly integrates advanced technologies to revolutionize the packaging process. This machine would represent the pinnacle of innovation in the food packaging industry.This machine features a modular design, allowing for easy customization and adaptation to different product types and packaging needs. Robotic arms with advanced vision systems handle products with extreme precision, capable of adapting to any shape or size.
The machine utilizes advanced sensors to monitor every aspect of the packaging process, including temperature, humidity, and material properties. These sensors feed data into an AI-powered control system that optimizes the machine’s performance in real time. The machine also incorporates a self-healing capability, where the system can automatically diagnose and repair minor issues. The entire system is connected to a cloud-based platform, allowing for remote monitoring, predictive maintenance, and data analysis.
Furthermore, the machine can create packaging that is fully biodegradable and sustainable. This futuristic food wrapper machine would be a testament to the transformative power of technology in the food industry.
Safety Regulations and Standards
Ensuring the safety of food wrapper machines is paramount, protecting both the operators and the integrity of the food products. Compliance with stringent regulations and standards is crucial for preventing accidents, maintaining hygiene, and guaranteeing consumer safety. This section delves into the key safety aspects of food wrapper machines.
Relevant Safety Regulations and Standards
Food wrapper machines are subject to a variety of safety regulations and standards, varying by region and country. These regulations aim to minimize hazards associated with machine operation and food handling.
- Food and Drug Administration (FDA) (United States): The FDA sets standards for materials that come into contact with food, ensuring they are safe and do not contaminate the product. This includes regulations on the use of food-grade plastics, inks, and adhesives.
- European Food Safety Authority (EFSA) (Europe): EFSA provides scientific advice on risks associated with the food chain, including packaging materials. They establish guidelines and regulations on food contact materials to ensure consumer safety.
- Occupational Safety and Health Administration (OSHA) (United States): OSHA mandates workplace safety standards, covering aspects such as machine guarding, electrical safety, and hazard communication to protect workers from injury.
- Canadian Food Inspection Agency (CFIA) (Canada): The CFIA enforces regulations related to food safety and packaging, including those concerning materials and labeling.
- International Organization for Standardization (ISO): ISO standards, such as ISO 12100 (Safety of machinery – General principles for design), provide guidelines for the design and construction of machinery to minimize risks.
- Underwriters Laboratories (UL) (United States): UL certifications are often sought to ensure electrical safety and compliance with national standards.
Importance of Compliance with Food Safety Regulations
Adherence to food safety regulations is critical for several reasons, directly impacting public health and the operational success of food processing businesses.
- Protecting Public Health: Regulations are designed to prevent foodborne illnesses by ensuring that packaging materials do not contaminate the food. This protects consumers from potentially harmful substances.
- Maintaining Product Integrity: Compliant packaging helps preserve the quality and freshness of food products, extending shelf life and reducing waste.
- Avoiding Legal Penalties: Non-compliance can result in severe penalties, including fines, product recalls, and even legal action, significantly impacting a company’s financial stability and reputation.
- Building Consumer Trust: Adhering to safety regulations demonstrates a commitment to consumer safety and builds trust in the brand, which is essential for long-term success.
- Facilitating International Trade: Compliance with international standards, such as those set by the FDA or EFSA, is often necessary for exporting food products to different markets.
Safety Features Incorporated into Modern Machines
Modern food wrapper machines are engineered with numerous safety features to protect operators and ensure safe operation. These features are constantly evolving to meet the demands of stricter regulations and the need for enhanced workplace safety.
- Protective Guards and Enclosures: Machines are equipped with guards and enclosures around moving parts, such as cutting blades, sealing jaws, and conveyor belts, to prevent accidental contact.
- Emergency Stop Buttons: Easily accessible emergency stop buttons are strategically placed on the machine to allow operators to immediately shut down the machine in case of an emergency.
- Light Curtains and Sensors: Light curtains and sensors are used to detect the presence of an operator in a hazardous area. If an operator enters the area, the machine automatically stops.
- Safety Interlocks: Safety interlocks prevent the machine from operating if a safety guard is not properly closed or secured.
- Material Safety Data Sheets (MSDS): Machines that utilize chemicals or materials that pose a hazard to operators will have MSDS readily available to the operators.
- Temperature Controls: Machines that utilize heat for sealing have temperature controls to prevent overheating and ensure consistent sealing.
- Ergonomic Design: Modern machines are designed with ergonomics in mind, reducing the risk of repetitive strain injuries and improving operator comfort and efficiency.
- Automated Shutdown Systems: These systems automatically shut down the machine in case of malfunctions, such as material jams or power failures.
Key Safety Features Commonly Found in These Machines
The following is a summary of the most crucial safety features typically incorporated into food wrapper machines.
- Machine Guarding: Enclosures and physical barriers to prevent access to moving parts.
- Emergency Stop Mechanisms: Readily accessible buttons to immediately halt machine operation.
- Light Curtains/Sensors: Detect presence in hazardous zones, triggering machine shutdown.
- Safety Interlocks: Prevent operation if safety guards are not properly closed.
- Clear and Accessible Controls: User-friendly interfaces and controls for safe operation.
- Proper Ventilation: Systems to remove fumes and maintain a safe working environment.
- Electrical Safety Features: Grounding, insulation, and overload protection.
- Regular Maintenance and Inspection Schedules: To ensure the machine’s safety features are functioning correctly.
- Training Programs: To educate operators on safe machine operation and hazard awareness.
- Material Compatibility: Use of food-grade materials that are safe for contact with food products.
Ending Remarks
In conclusion, the food wrapper machine stands as a symbol of efficiency and mindful provision. It demonstrates the power of automation to serve humanity’s needs, while reminding us of our responsibility to protect the resources that sustain us. Let us view these machines not just as tools of commerce, but as reflections of our commitment to providing for ourselves and others with care and consideration, embodying the spirit of nourishment and abundance.