Food grade hydraulic oil is a critical component in the smooth and safe operation of food processing machinery. Unlike standard hydraulic oils, these specialized lubricants are formulated to meet stringent safety standards, minimizing the risk of contamination in the food production environment. They are designed to withstand the demanding conditions of food processing, where contact with food products is a possibility.
This overview will delve into the purpose, regulations, types, applications, benefits, selection, maintenance, troubleshooting, and future trends related to food grade hydraulic oil. We will explore the critical role these oils play in maintaining food safety, extending equipment lifespan, and optimizing operational efficiency within the food industry. From understanding regulatory compliance to selecting the right lubricant for specific applications, this information will provide a comprehensive understanding of food grade hydraulic oil.
Introduction to Food Grade Hydraulic Oil
Hey there, sun-kissed souls! Ever wondered what keeps those food processing machines humming along smoothly, ensuring your delicious nasi goreng and fresh-pressed juices are made safely? It’s all thanks to a special type of oil: food grade hydraulic oil. This oil is the unsung hero of the food industry, working behind the scenes to keep everything running like a well-oiled Balinese gamelan orchestra.Food grade hydraulic oil is specifically engineered for use in machinery that comes into contact with food products.
Unlike standard hydraulic oils, which might contain ingredients that could be harmful if they contaminate food, food grade oils are formulated to be safe for consumption. This means that even if a small amount of oil accidentally leaks into the food, it won’t pose a health risk. It’s all about keeping those good vibes flowing, from the farm to your plate!
Defining Food Grade Hydraulic Oil
Food grade hydraulic oil is a specialized lubricant designed for use in hydraulic systems within the food and beverage industry. It’s formulated with base oils and additives that meet stringent safety standards, ensuring that the oil is non-toxic and safe for incidental food contact. This is a crucial difference from standard hydraulic oils, which are not designed for this type of application and may contain ingredients that are harmful if ingested.
Key Characteristics of Food Grade Hydraulic Oil
To ensure the safety and performance of food processing equipment, food grade hydraulic oils possess several key characteristics. These features guarantee that the oil not only lubricates machinery effectively but also complies with strict health regulations.
- Safety and Non-Toxicity: Food grade hydraulic oils are formulated with ingredients that are generally recognized as safe (GRAS) by regulatory bodies like the FDA. This means they are designed to be non-toxic and pose no health risks if they accidentally come into contact with food.
- Excellent Lubrication: Despite the stringent safety requirements, these oils must still provide exceptional lubrication to reduce friction, wear, and tear on machinery components. This helps extend the lifespan of equipment and minimize downtime.
- Good Thermal Stability: The oil needs to maintain its lubricating properties and viscosity across a wide range of temperatures. This is especially important in food processing environments where temperatures can fluctuate.
- Resistance to Oxidation: Food grade hydraulic oils are formulated to resist oxidation, which can cause the oil to thicken and degrade over time. This ensures the oil remains effective for an extended period.
- Compatibility with Seals and Materials: The oil must be compatible with the seals, hoses, and other materials used in food processing machinery. Incompatibility can lead to leaks and equipment failure.
Food grade hydraulic oils are crucial for maintaining the safety and efficiency of food processing operations. The specific formulations and characteristics of these oils help to protect both the equipment and the consumer.
Regulations and Standards
Alright, let’s talk about keeping things squeaky clean and safe in the food industry. When it comes to food-grade hydraulic oil, it’s not just about the oil itself; it’s about making sure it’s safe for anyone who might come into contact with it, directly or indirectly. This means sticking to some pretty strict rules and getting the right certifications. Think of it like this: you wouldn’t want to use a dodgy sunscreen, right?
Same goes for the stuff that keeps your food processing machines running smoothly.
Major Regulatory Bodies and Standards
A whole bunch of organizations are in charge of making sure food-grade lubricants are up to snuff. These bodies set the rules and guidelines, and they’re super important for protecting public health. They cover everything from the ingredients used to the manufacturing process.
- NSF International (NSF): NSF is a big player in the food industry. They develop standards and certify products, including food-grade lubricants. Their main program for this is the NSF International Nonfood Compounds Registration Program. NSF uses a system of categories to classify lubricants based on their potential for food contact.
- United States Food and Drug Administration (FDA): The FDA sets the rules for food safety in the US. While they don’t directly certify lubricants, they provide guidance on what’s acceptable in terms of food contact materials. They are responsible for ensuring that food is safe, wholesome, and properly labeled.
- European Union (EU) Regulations: The EU has its own set of regulations, focusing on food safety and materials intended for contact with food. This includes regulations on lubricants and their components. The European Food Safety Authority (EFSA) plays a role in evaluating the safety of substances used in food contact materials.
Specific Requirements and Certifications
To be considered food-grade, hydraulic oils need to meet some very specific criteria. This isn’t just a suggestion; it’s a requirement.
- NSF H1 Certification: This is one of the most common and important certifications. NSF H1 lubricants are safe for incidental food contact. This means they can be used in food processing environments where there’s a chance the lubricant might come into contact with food.
- Ingredients and Formulation: The oil must be made with ingredients that are safe for food contact. This often means using base oils and additives that are specifically approved for food-grade applications. The formulation is carefully designed to minimize any potential risk to food safety.
- Manufacturing Processes: The manufacturing process itself has to be clean and controlled. This helps prevent contamination of the oil during production.
- Testing and Compliance: Lubricants undergo rigorous testing to ensure they meet the required standards. This includes testing for toxicity, performance, and food safety.
Importance of Compliance
Following these standards isn’t just about ticking boxes; it’s crucial for protecting consumers and the business itself. Think of it as an investment in peace of mind.
- Food Safety: The main goal is to prevent food contamination. Using the right oil, certified and compliant, significantly reduces the risk of foodborne illnesses.
- Consumer Protection: By using food-grade lubricants, companies are protecting their customers from potentially harmful substances. This builds trust and loyalty.
- Legal Compliance: Failing to comply with regulations can lead to serious legal consequences, including fines and even shutdowns.
- Brand Reputation: A company’s reputation is everything. Using non-compliant lubricants can damage a brand’s image and lead to lost sales.
- Operational Efficiency: Food-grade lubricants are often designed to provide excellent performance, which can improve the efficiency of food processing equipment and reduce downtime.
Types of Food Grade Hydraulic Oil
Alright, let’s dive into the heart of food-grade hydraulic oils! Think of it like choosing the perfect smoothie base – each type brings its own vibe and benefits to the table. Understanding the different types helps you pick the right one to keep your food processing machinery running smoothly and safely, like a well-oiled coconut on a Bali beach.
Base Oil Types in Food Grade Hydraulic Oils
Food grade hydraulic oils mainly rely on two main types of base oils: mineral oil and synthetic oil. Each has its own unique set of properties that impact its performance in food processing environments. Let’s break down the differences between them.
- Mineral Oil: Derived from refined petroleum, mineral oils are a common and cost-effective option. They are often the starting point for many food-grade hydraulic oil formulations. Think of them as the reliable, classic option, like a traditional nasi goreng.
- Synthetic Oil: These oils are manufactured through chemical processes, offering enhanced performance characteristics. Common types include Polyalphaolefins (PAOs), Polyol Esters (POEs), and Polyalkylene Glycols (PAGs). They’re the more modern, premium choice, like a vegan smoothie with spirulina and goji berries.
- Polyalphaolefins (PAOs): Known for their excellent thermal stability and wide operating temperature range. PAOs are good at maintaining their viscosity even when things get hot, like a sizzling tempeh dish.
- Polyol Esters (POEs): POEs boast superior biodegradability and excellent solvency. This makes them ideal for environments where environmental concerns are paramount, similar to choosing organic ingredients for your meal.
- Polyalkylene Glycols (PAGs): PAGs offer good lubricity and are often used when water resistance is crucial. They are like a waterproof layer protecting your machinery, similar to how you protect yourself from the Bali rain.
Performance Characteristics of Food Grade Hydraulic Oil Formulations
The performance of food-grade hydraulic oils is assessed based on several key characteristics. These factors are critical to ensuring that the oil effectively lubricates the machinery, resists degradation, and protects against wear and tear, all while maintaining food safety.
- Viscosity: This is the oil’s resistance to flow. The right viscosity ensures proper lubrication across a range of operating temperatures.
- Oxidation Stability: Resistance to breaking down due to exposure to oxygen and heat. This prevents the formation of sludge and deposits, which can clog the hydraulic system.
- Wear Protection: The ability of the oil to reduce friction and prevent wear on moving parts, extending the lifespan of the machinery.
- Food Safety: The oil must be non-toxic and comply with food-grade regulations to prevent contamination.
- Biodegradability: The rate at which the oil breaks down in the environment, important for minimizing environmental impact.
Comparison of Base Oil Types
Choosing the right base oil is crucial. Here’s a simple table to compare the advantages and disadvantages:
Base Oil Type | Advantages | Disadvantages | Typical Applications |
---|---|---|---|
Mineral Oil | Cost-effective; Good lubricity; Readily available. | Lower thermal stability; Less biodegradable; Limited operating temperature range. | General-purpose hydraulic systems; Moderate temperature applications. |
Polyalphaolefins (PAOs) | Excellent thermal stability; Wide operating temperature range; Good wear protection. | Can be more expensive than mineral oils; Compatibility concerns with some seals. | High-temperature applications; Systems exposed to extreme conditions. |
Polyol Esters (POEs) | Excellent biodegradability; Good solvency; High flash point. | Can be more expensive; May have compatibility issues with certain seal materials; Water absorption. | Environmentally sensitive applications; Systems where biodegradability is a priority. |
Polyalkylene Glycols (PAGs) | Good lubricity; Excellent water resistance; High flash point. | Not compatible with some seal materials; May not mix well with other oils. | Water-resistant systems; Applications where water contamination is a concern. |
Applications in the Food Industry
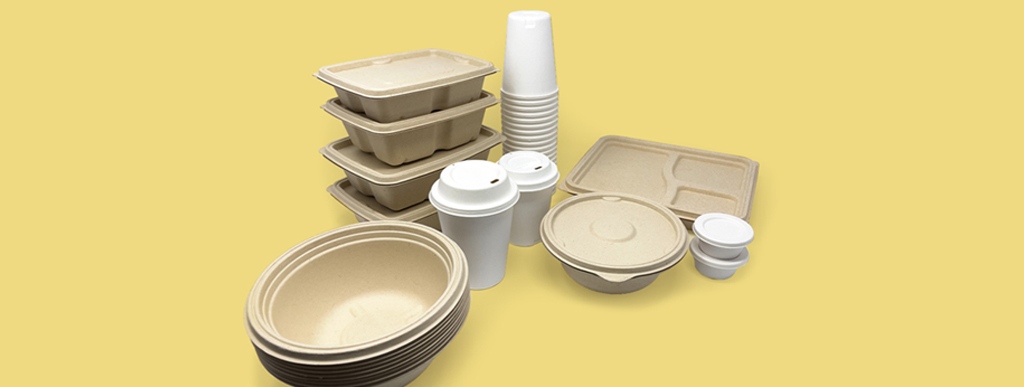
Alright, let’s dive into where food-grade hydraulic oil is absolutely essential in keeping our favorite eats flowing smoothly. Think of it as the unsung hero, quietly working behind the scenes to ensure the food we love is safe and delicious. From the farm to your plate, this special oil plays a crucial role in various processes.This oil isn’t just a lubricant; it’s a safeguard, minimizing the risk of contamination and ensuring the longevity and efficiency of vital food processing equipment.
Using the right food-grade hydraulic oil is critical for maintaining food safety standards, preventing equipment failure, and ultimately, protecting consumer health.
Common Food Processing Applications
Food-grade hydraulic oil finds its place in a wide array of food processing applications. Its versatility and safety profile make it ideal for use in equipment that comes into direct or indirect contact with food products. Here’s a rundown of some common areas:
- Meat Processing: Hydraulic systems power machinery used for cutting, slicing, and packaging meat products.
- Dairy Processing: Essential for equipment like filling machines, homogenizers, and packaging lines.
- Bakery Equipment: Found in mixers, dough dividers, and packaging machines, ensuring smooth operations.
- Beverage Production: Used in bottling lines, filling machines, and labeling equipment.
- Canning and Preserving: Critical for operating canning machinery, sealers, and labeling systems.
- Fruit and Vegetable Processing: Powers equipment used for washing, peeling, cutting, and packaging.
- Confectionery Production: Used in chocolate molding machines, candy forming equipment, and packaging lines.
- Ready-to-Eat Meal Production: Plays a key role in equipment used for portioning, filling, and sealing.
Detailed Application: Meat Slicing
Let’s zoom in on a specific example: meat slicing. Imagine a bustling meat processing plant, where efficiency and hygiene are paramount.
Machinery Involved: Automated meat slicers are a staple. These machines use hydraulic cylinders to precisely control the movement of blades that slice through various meat products (think deli meats, bacon, and roasts). Conveyor systems, also often powered by hydraulics, transport the sliced meat to packaging. The entire process requires consistent power and precise control to ensure uniform slices and high throughput.
Oil’s Function: Food-grade hydraulic oil lubricates the hydraulic cylinders, pumps, and valves within the slicer and conveyor systems. This lubrication minimizes friction, reduces wear and tear on the equipment, and prevents overheating. The oil’s primary function is to facilitate the smooth and reliable operation of the machinery, enabling precise slicing and efficient packaging. Crucially, its food-grade status ensures that even if there’s a leak or accidental contact, the meat product remains safe for consumption.
This minimizes the risk of contamination and ensures the final product meets stringent food safety regulations. The use of food-grade oil also extends the lifespan of the equipment, reducing downtime and maintenance costs.
Benefits of Using Food Grade Hydraulic Oil
Alright, let’s dive into why swapping out your regular hydraulic oil for the food-grade stuff is a total game-changer, especially if you’re vibing in the food processing world. Think of it as leveling up your operation, keeping things smooth, and ensuring everything stays squeaky clean and safe. It’s all about boosting your food safety game, keeping your equipment happy, and ultimately, making your business more efficient.
Enhanced Food Safety and Quality
Food grade hydraulic oils are specifically formulated to minimize any potential contamination of food products. They’re designed to be safe, even if there’s an accidental leak or spill. This is a big deal, because it directly impacts the quality and safety of the food we eat.
- Reduced Contamination Risk: Unlike standard hydraulic oils, food grade options are made with ingredients that are generally recognized as safe (GRAS) by organizations like the FDA. This means that even if there’s a small leak, the risk of harmful chemicals getting into your food is significantly reduced.
- Maintaining Food Integrity: Food grade oils are formulated to prevent the degradation of food products. They don’t contain additives that could alter the taste, smell, or appearance of the food. This ensures that the food maintains its original quality and flavor profile, as it’s meant to be.
- Compliance with Regulations: Using food grade hydraulic oil helps food processing facilities meet strict regulations set by food safety authorities. This includes guidelines from the FDA, USDA, and other regulatory bodies. Meeting these standards is crucial for avoiding costly fines and ensuring consumer trust.
Improved Equipment Lifespan and Operational Efficiency
Food grade hydraulic oils aren’t just about food safety; they also play a crucial role in keeping your machinery running smoothly and efficiently. Using the right oil can extend the life of your equipment and reduce downtime.
- Extended Equipment Life: Many food grade hydraulic oils offer excellent wear protection, which helps to reduce friction and wear on moving parts. This can significantly extend the lifespan of hydraulic pumps, cylinders, and other components.
- Reduced Downtime: By minimizing wear and tear, food grade oils help to reduce the frequency of equipment failures. This translates into less downtime for repairs and maintenance, allowing your operation to run more consistently.
- Enhanced Operational Efficiency: Food grade hydraulic oils are often formulated to provide excellent thermal stability and oxidation resistance. This means they can maintain their lubricating properties even under high temperatures and pressures, contributing to smoother and more efficient operation of the equipment.
Selecting the Right Food Grade Hydraulic Oil
Alright, so you’re ready to dive into the world of food-grade hydraulic oils, eh? Choosing the right one is kinda like picking the perfect surfboard – gotta match the waves (your application) to the board (the oil). Get it wrong, and you’re gonna wipe out. This section is all about making sure you catch the right wave.
Factors for Selecting Food Grade Hydraulic Oil
Choosing the right food-grade hydraulic oil isn’t a one-size-fits-all situation. Several factors need consideration to ensure optimal performance and compliance with food safety standards. Ignoring these can lead to equipment failure, contamination risks, and costly downtime.
- Application Type: What specific equipment are you using? Is it a filling machine, a packaging system, or a conveyor belt? Different applications have different demands. For instance, high-pressure systems require oils with robust anti-wear properties.
- Operating Conditions: Temperature and pressure are crucial. High temperatures can degrade the oil, while high pressures can affect its viscosity. Consider the typical operating range of your machinery.
- Compatibility: Ensure the oil is compatible with all the materials in your system, including seals, hoses, and other components. Incompatibility can lead to leaks and equipment damage.
- Food Safety Regulations: The oil must meet the necessary food safety regulations and certifications, such as those from NSF (National Sanitation Foundation). Look for H1-registered oils, which are safe for incidental food contact.
- Viscosity Requirements: The oil’s viscosity needs to be appropriate for the equipment and operating temperatures. Too low a viscosity can lead to wear, while too high a viscosity can hinder performance.
- Equipment Manufacturer Recommendations: Always consult the manufacturer’s recommendations for the specific equipment. They will specify the required oil type, viscosity grade, and any special requirements.
Viscosity Grades Commonly Used in Food Processing Machinery
Viscosity is a super important property of hydraulic oil. It’s essentially the oil’s resistance to flow. Different viscosity grades are available to suit various operating conditions and equipment types. Think of it like choosing the right sunscreen SPF – gotta match the sun (application) to the protection (viscosity).
Here’s a breakdown of common viscosity grades and their typical uses:
- ISO VG 32: Commonly used in light-duty hydraulic systems and equipment operating at lower temperatures. It offers good flow characteristics in colder environments.
- ISO VG 46: A versatile grade often used in a wide range of food processing equipment. It provides a balance between flow, wear protection, and operating temperature range.
- ISO VG 68: Suitable for heavier-duty applications and equipment operating at higher temperatures. It offers enhanced wear protection and film strength.
- ISO VG 100: Used in very heavy-duty applications or where extreme operating temperatures are present. It provides the highest level of wear protection.
The choice of viscosity grade is critical for efficient and reliable operation. Selecting the wrong viscosity can lead to issues like:
- Poor lubrication: If the viscosity is too low, the oil may not provide sufficient lubrication, leading to increased wear and tear.
- Increased friction: If the viscosity is too high, it can increase friction within the system, reducing efficiency and potentially causing overheating.
- Seal damage: Incorrect viscosity can damage seals and other components, leading to leaks and contamination.
Importance of Considering Equipment Manufacturer Recommendations
Alright, so you’ve got all these choices for your food-grade hydraulic oil. But before you get too excited, remember the golden rule: check the manufacturer’s recommendations. These guys designed the equipment, so they know best. Ignoring their advice is like ignoring the local surf instructor – you might get away with it for a while, but eventually, you’ll regret it.
Here’s why following equipment manufacturer recommendations is super important:
- Warranty Protection: Using the wrong oil can void the equipment’s warranty. Manufacturers often specify the exact oil type and viscosity grade required to maintain warranty coverage.
- Optimal Performance: The manufacturer has tested the equipment with specific oils to ensure optimal performance and efficiency. Using a different oil can lead to reduced performance or even damage.
- Compatibility Assurance: Manufacturers specify oils that are compatible with the materials used in their equipment, minimizing the risk of seal damage, leaks, and other issues.
- Safety Compliance: Manufacturers often provide recommendations to ensure compliance with food safety regulations and certifications.
- Extended Equipment Life: Following the manufacturer’s recommendations can help extend the life of your equipment by providing proper lubrication and protection.
Maintenance and Handling
Alright, so you’ve got your food-grade hydraulic oil, ready to keep those food processing machines humming smoothly. But, just like your favorite surf board needs a little TLC, so does your oil. Proper maintenance and handling are crucial to ensure its effectiveness and, more importantly, to prevent any contamination that could spoil the party (and the food!). Let’s dive into some essential tips to keep things flowing safely and efficiently.
Proper Storage Procedures
Keeping your food-grade hydraulic oil in tip-top shape starts with where you stash it. Think of it like storing your fresh fruit – you wouldn’t leave it out in the sun, would you?To prevent contamination:
- Choose the Right Spot: Store your oil in a cool, dry, and well-ventilated area, away from direct sunlight, heat sources, and potential contaminants like dust, dirt, and moisture. Imagine a shaded spot under a frangipani tree, away from the beach!
- Container Matters: Use dedicated, clearly labeled containers specifically for food-grade hydraulic oil. Make sure these containers are clean and tightly sealed to prevent any outside elements from sneaking in. Consider using containers made of materials compatible with the oil, such as polyethylene or stainless steel.
- Separate and Conquer: Never store food-grade oil near non-food-grade oils, chemicals, or any other substances that could cross-contaminate. Think of it like keeping your organic produce separate from your cleaning supplies.
- Inventory Management: Implement a “first in, first out” (FIFO) system to ensure older oil is used before newer oil. This helps minimize the time the oil sits in storage, reducing the risk of degradation.
- Regular Inspections: Periodically inspect storage containers for any leaks, damage, or signs of contamination. If you spot anything suspicious, address it immediately.
Safe Handling and Disposal
Handling food-grade hydraulic oil safely isn’t just about protecting the food; it’s also about protecting yourself and the environment. Let’s get down to business.Here’s a step-by-step procedure:
- Personal Protective Equipment (PPE): Always wear appropriate PPE, including gloves (nitrile or other oil-resistant material), eye protection (safety glasses or goggles), and protective clothing. Imagine yourself geared up like a seasoned surfer, ready to tackle any wave.
- Prevent Spills: When transferring oil, use funnels, pumps, and other tools to minimize the risk of spills. Have absorbent materials like spill kits readily available to clean up any leaks promptly.
- Proper Disposal: Used food-grade hydraulic oil is considered a hazardous waste. Never pour it down the drain or dispose of it in the regular trash. Instead, follow these steps:
- Collect the used oil in a designated, labeled container.
- Contact a licensed waste disposal company to arrange for proper disposal or recycling.
- Follow all local, state, and federal regulations regarding hazardous waste disposal.
- Documentation: Keep records of all oil handling activities, including the type of oil, date of disposal, and the name of the waste disposal company. This is essential for compliance and traceability.
Monitoring Oil Condition
Keeping an eye on the condition of your food-grade hydraulic oil is like checking the waves before you paddle out. You want to make sure everything is safe and ready to go.Best practices for monitoring the oil condition:
- Regular Sampling: Establish a regular oil sampling schedule, typically every 3 to 6 months, or more frequently depending on the operating conditions of your equipment. Samples should be taken from representative points in the hydraulic system.
- Visual Inspection: Regularly check the oil’s appearance. Look for changes in color, clarity, or the presence of any contaminants like water, sediment, or particulate matter. A healthy oil should be clear and free of any visible impurities.
- Laboratory Analysis: Send oil samples to a certified laboratory for analysis. These tests can provide detailed information about the oil’s condition, including:
- Viscosity: Measures the oil’s resistance to flow. Changes in viscosity can indicate oil degradation.
- Water Content: Excessive water can cause corrosion and reduce the oil’s lubricating properties.
- Particle Count: Determines the level of solid contaminants in the oil. High particle counts can lead to wear and tear on equipment.
- Additive Levels: Checks the concentration of the oil’s additives, which help protect the equipment.
- Acid Number (AN): Indicates the level of oil oxidation.
- Filter Maintenance: Regularly inspect and replace hydraulic filters to remove contaminants and maintain oil cleanliness. The filter type and change frequency will depend on the specific equipment and operating conditions.
- Data Analysis: Review the results of your oil analysis and compare them to the manufacturer’s recommendations and established baselines. This will help you identify any potential problems and take corrective action.
- Trending: Track the oil analysis results over time to identify trends. This allows you to anticipate potential issues and proactively address them before they lead to equipment failure. For example, if you see a gradual increase in particle count over several sampling periods, you might want to investigate the source of the contamination and improve filtration.
Troubleshooting Common Issues
Alright, let’s dive into the nitty-gritty of keeping your food-grade hydraulic systems running smoothly. Even with the best oil, things can go sideways. We’ll explore common problems and how to fix them, so you can keep those delicious eats flowing.
Contamination and Degradation Solutions
Contamination and degradation are enemies of food-grade hydraulic oil. These issues can lead to equipment failure, and nobody wants that. Let’s look at some key solutions.
- Regular Filtration: Install and maintain high-quality filtration systems. This removes solid contaminants like dirt, rust, and wear particles that can accelerate oil degradation. Think of it like a super-powered water filter for your system.
- Proper Storage: Store oil in a clean, dry, and climate-controlled environment. Keep containers sealed tightly to prevent moisture and airborne contaminants from entering. Imagine storing your precious coconut oil in a cool, dark place, away from the sun and humidity.
- Oil Analysis: Implement a regular oil analysis program. This involves sending samples of the oil to a lab for testing. The results provide insights into the oil’s condition, identifying contaminants, and monitoring additive depletion. It’s like a regular health check-up for your equipment.
- Seal Integrity: Inspect and maintain seals to prevent external contaminants like water or food particles from entering the system. Think of seals as the guardians of your system, keeping the bad stuff out and the good stuff in.
- Flushing: Regularly flush the system with fresh oil to remove accumulated contaminants, especially after major maintenance or component replacement. It’s like a deep cleanse for your hydraulic system.
Foaming, Leaks, and Equipment Malfunctions Troubleshooting
Foaming, leaks, and equipment malfunctions can be frustrating, and they can disrupt production. Here’s how to address these issues.
- Foaming: Foaming can reduce lubrication and lead to cavitation. Causes can include air entrainment, contaminated oil, or incorrect oil viscosity.
- Solutions:
- Check the oil level; ensure it’s within the recommended range.
- Inspect the suction line for air leaks.
- Verify the oil’s compatibility with the system.
- Consider using an anti-foam additive, but always check compatibility with the oil.
- Leaks: Leaks are a common problem that can lead to oil loss and contamination.
- Causes: Worn seals, damaged hoses, loose fittings, or excessive pressure.
- Solutions:
- Regularly inspect the system for leaks.
- Replace worn seals and damaged components promptly.
- Ensure all fittings are properly tightened.
- Check the system pressure to avoid exceeding the manufacturer’s recommendations.
- Equipment Malfunctions: Equipment malfunctions can stem from various issues related to the hydraulic oil.
- Causes: Contamination, oil degradation, or improper oil viscosity.
- Solutions:
- Perform oil analysis to identify the root cause of the malfunction.
- Change the oil and filter if necessary.
- Inspect and replace worn components.
- Consult the equipment’s manual for troubleshooting steps.
Innovation and Future Trends
Hey, foodies and tech-lovers! Let’s dive into the future of food-grade hydraulic oil – it’s not just about keeping things running smoothly; it’s about pushing boundaries and making things even better for the planet and our plates. The industry is constantly evolving, with exciting new developments promising to revolutionize how we handle our food.
Emerging Trends in Food Grade Hydraulic Oil Technology
The food industry is seeing a shift towards more sustainable and efficient practices. This impacts everything, including the lubricants we use. Here are some key trends:* Smart Lubrication Systems: These systems use sensors and data analytics to monitor oil condition in real-time. They can predict when maintenance is needed, optimize oil changes, and reduce downtime. Imagine a system that alerts you the moment your hydraulic oil starts to degrade, preventing potential equipment failures.
Additive Advancements
Scientists are developing new additives to enhance the performance of food-grade hydraulic oils. These additives improve properties like anti-wear, corrosion resistance, and oxidation stability, leading to longer oil life and better equipment protection.
Nanotechnology Integration
Nanomaterials are being incorporated into lubricant formulations. These tiny particles can improve friction reduction, enhance wear protection, and boost overall oil performance. This is like giving your oil superpowers!
Latest Advancements in Food Grade Lubricant Formulations
Formulation is key to achieving peak performance. Recent advancements focus on enhancing both the safety and effectiveness of these essential fluids.* Enhanced Biodegradability: There’s a growing focus on developing lubricants with even higher biodegradability rates. This reduces environmental impact if leaks occur.
Improved Oxidation Stability
Formulations are being created that resist oxidation, extending the lifespan of the oil and reducing the frequency of oil changes. This is crucial for maintaining equipment reliability and reducing waste.
Enhanced Wear Protection
Advanced formulations offer superior wear protection, reducing friction and extending the life of equipment components. This is achieved through the use of specialized additives and base oils.
Lower Viscosity Grades
The trend is towards lower viscosity grades to improve energy efficiency.
Lower viscosity oils offer reduced friction, leading to improved energy efficiency in hydraulic systems.
Potential of Bio-Based Food Grade Hydraulic Oils
Bio-based oils are derived from renewable resources, offering a sustainable alternative to traditional petroleum-based lubricants. They’re a big deal in the future.* Sustainability Benefits: Bio-based oils are generally biodegradable and have a lower carbon footprint. This makes them an attractive option for companies aiming to reduce their environmental impact.
Performance Characteristics
Modern bio-based oils are engineered to match or even exceed the performance of conventional lubricants. They offer excellent lubricity, wear protection, and oxidation stability.
Examples of Bio-Based Oils
Vegetable Oils
Oils like canola, sunflower, and soybean are commonly used as base oils. They’re readily available and biodegradable.
Synthetic Esters
Discover how dog food roll has transformed methods in this topic.
These are produced from renewable resources like vegetable oils, but they have enhanced properties like improved thermal stability.
Challenges and Considerations
Cost
Bio-based oils can sometimes be more expensive than conventional oils, although this gap is narrowing.
Compatibility
It’s important to ensure compatibility with existing equipment components, especially seals and elastomers.
Cold-Weather Performance
Some bio-based oils may have poorer cold-weather performance compared to mineral oils, but this is being addressed through formulation improvements.
Illustration: Visual Representation of Food Grade Hydraulic Oil in Action
Alright, let’s get visual! Because sometimes, a picture trulyis* worth a thousand words, especially when we’re talking about something as crucial (and potentially invisible!) as food grade hydraulic oil. We’ll be diving into a few key illustrations to make sure the concepts stick, and you can picture this stuff in action. Think bright, clean, and efficient – just like a well-oiled Balinese food stall!
Food Processing Machine Lubrication
Imagine a vibrant food processing plant, maybe a bustling bakery or a state-of-the-art vegetable processing line. The central focus is a gleaming piece of machinery, perhaps a dough mixer with powerful hydraulic arms or a precision slicer effortlessly handling produce. This isn’t just any machine; it’s designed with food safety at its core. The illustration highlights several key aspects:* The Machine: The machine itself is rendered in a clean, modern style, showcasing smooth, easily-cleaned surfaces.
All components are clearly labeled to identify their function. It’s constructed from food-grade stainless steel, reflecting its hygienic design.
Hydraulic System
A cutaway view reveals the internal hydraulic system. We see the hydraulic cylinders, pumps, and hoses that provide the machine’s power and motion. These components are highlighted in a contrasting color to emphasize their role.
Food Grade Hydraulic Oil Application
The illustration shows the food grade hydraulic oil lubricating critical moving parts. It’s depicted as a clear, colorless liquid, subtly highlighted to emphasize its presence and function. The oil is strategically applied to minimize contact with the food product.
Safety Features
The machine is surrounded by protective guards and enclosures, emphasizing worker safety. The illustration includes safety interlocks and emergency stop buttons, reinforcing the importance of a safe working environment.
Food Contact Prevention
The illustration demonstrates seals and barriers preventing any potential contamination. It highlights the importance of using food-grade components to minimize the risk of food safety hazards.The overall feel is one of efficiency, cleanliness, and precision. It’s a visual representation of how food grade hydraulic oil keeps the food processing process running smoothly, safely, and efficiently, like a well-choreographed Balinese dance.
Oil Filtration and Recycling Process
Now, let’s visualize the lifecycle of the oil itself. This illustration focuses on the importance of maintaining the oil’s purity and extending its lifespan, essential for both food safety and sustainability.* The Cycle: The illustration showcases a closed-loop system. This system ensures the oil is continually cleaned and re-used.
Oil Reservoir
The cycle starts with the oil reservoir, where the oil is stored and ready for use.
Filtration System
The oil is then pumped through a sophisticated filtration system. The illustration details the different stages of filtration, removing contaminants and maintaining oil quality.
Recycling
The illustration depicts the oil being analyzed and treated to remove any potential contaminants or degradation products.
Return to Service
After filtration and treatment, the oil is returned to the reservoir, ready to lubricate the machinery once more.The illustration uses a series of interconnected elements to show the oil’s journey, emphasizing the importance of regular maintenance and responsible practices. This image demonstrates how the oil is continually cleaned and re-used.
Emphasis on Food Safety, Food grade hydraulic oil
This illustration takes a more conceptual approach, focusing on the core principle of food safety. The visual language is clean and minimalist, communicating the essential message in a clear and impactful way.* Central Symbol: The focal point is a stylized representation of a food product, such as a piece of fruit or a loaf of bread.
Protective Shield
Surrounding the food product is a protective shield or barrier, representing the various measures taken to ensure food safety.
Key Elements
Within the shield, the illustration highlights key elements related to food grade hydraulic oil, such as:
Cleanliness
The illustration shows a symbol representing cleanliness and hygiene.
Purity
The illustration includes a symbol representing purity.
Compliance
The illustration may include logos or symbols representing compliance with relevant food safety standards and regulations.
Color Palette
The color palette is clean and inviting, using bright, fresh colors.The overall message is one of protection, assurance, and trust. The illustration emphasizes the crucial role of food grade hydraulic oil in safeguarding the food supply, like a silent guardian ensuring every bite is safe. This visual serves as a reminder of the commitment to quality and safety that defines the food processing industry.
Last Recap
In conclusion, food grade hydraulic oil is indispensable for maintaining food safety, equipment longevity, and operational efficiency in the food processing sector. From understanding regulatory requirements to implementing best practices for maintenance and handling, the effective use of these specialized lubricants ensures the integrity of food products and the smooth functioning of critical machinery. As technology advances, the future of food grade hydraulic oils promises even greater innovation, with bio-based formulations and enhanced performance characteristics set to further elevate their role in the food industry.