My dear friends, let us begin with Frozen Food Express Tracking, a journey into the heart of ensuring your precious cargo arrives fresh and on time. This isn’t just about knowing where your shipment is; it’s about understanding the meticulous care and precision that goes into every mile. Imagine the journey of a delicate ingredient, from the farm to your table, and how this tracking system helps us follow its path with unwavering attention.
We’ll delve into how this tracking system works, the benefits it offers to both those sending and receiving goods, and the wealth of information available at your fingertips. We’ll explore the methods to access this information, from the website to the mobile app, and guide you through the process step by step. Prepare yourselves to learn about the statuses, the common issues, and how to overcome them, all while appreciating the dedication of those who make this possible.
Introduction to Frozen Food Express Tracking
Frozen Food Express (FFE) tracking is a vital service designed to provide real-time visibility into the movement of your temperature-sensitive shipments. This tracking system offers a comprehensive view of your freight’s journey, ensuring peace of mind and enabling proactive management of your supply chain. It’s a critical tool for anyone shipping or receiving perishable goods.The primary objective of FFE tracking is to offer complete transparency regarding the location and status of your frozen food shipments, from the point of origin to their final destination.
This transparency allows both shippers and receivers to stay informed, anticipate potential delays, and take necessary actions to maintain product integrity.
Core Purpose of Tracking Shipments
The core purpose of tracking shipments with Frozen Food Express is to ensure the efficient and secure transport of temperature-controlled freight. It provides a centralized platform for monitoring the location, condition, and estimated time of arrival (ETA) of each shipment. This system is crucial for:
- Maintaining Product Integrity: Tracking helps monitor temperature fluctuations and potential deviations from the required conditions, which is essential for preserving the quality and safety of frozen goods.
- Enhancing Supply Chain Efficiency: By providing real-time updates, the system allows for proactive planning, reducing the risk of delays and ensuring timely deliveries.
- Improving Customer Satisfaction: Accurate and timely information about shipment status enhances customer experience and builds trust.
Benefits for Shippers and Receivers
FFE tracking offers significant advantages for both shippers and receivers, improving operational efficiency and providing critical insights.For Shippers:
- Proactive Monitoring: Shippers can monitor shipments in real-time, allowing them to address potential issues promptly, such as temperature excursions or unexpected delays.
- Improved Inventory Management: The tracking system provides accurate ETAs, enabling shippers to optimize their inventory levels and reduce storage costs.
- Enhanced Communication: Real-time updates facilitate clear and consistent communication with customers, providing them with accurate information about their orders.
For Receivers:
- Accurate Planning: Receivers can plan for the arrival of their shipments with greater accuracy, coordinating staffing and resources effectively.
- Reduced Waste: By monitoring temperature conditions, receivers can identify potential issues that could compromise product quality and prevent spoilage.
- Faster Receiving Process: Knowing the exact location and ETA of a shipment allows receivers to streamline their receiving processes and expedite the movement of goods.
Information Available Through the Tracking System
The FFE tracking system provides a wealth of information, ensuring comprehensive visibility into the status of each shipment. This includes:
- Location Tracking: Real-time GPS location of the trailer or container, showing the current position on a map.
- Temperature Monitoring: Continuous monitoring of the internal temperature of the trailer, with alerts for any deviations from the set parameters.
- ETA and Delivery Updates: Accurate ETAs and updates on the estimated time of delivery, providing timely information to both shippers and receivers.
- Arrival and Departure Notifications: Notifications regarding the arrival and departure of the shipment at various checkpoints, including loading docks and warehouses.
- Detailed Shipment History: A complete history of the shipment, including all stops, temperature readings, and any reported incidents.
Accessing Frozen Food Express Tracking Information
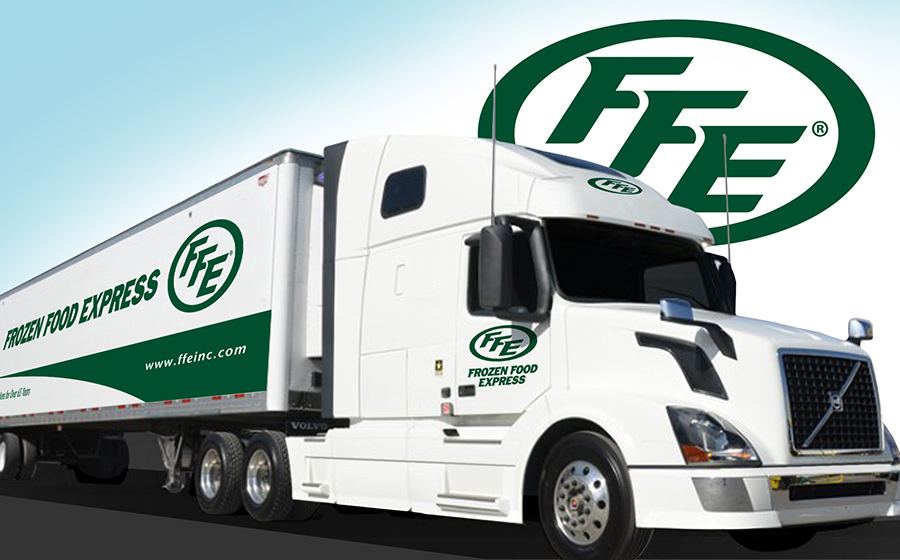
Tracking your Frozen Food Express shipment is a straightforward process, providing real-time updates on your cargo’s journey. Understanding the different methods available and the necessary information ensures you can monitor your shipment effectively and plan accordingly.
Methods for Accessing Tracking Information
Frozen Food Express offers several convenient methods for accessing shipment tracking information, catering to various user preferences and needs. These methods provide flexibility and accessibility, allowing you to stay informed regardless of your location.
- Website: The primary method is through the Frozen Food Express website. This provides a comprehensive tracking experience with detailed information.
- Mobile App: Frozen Food Express likely provides a mobile application, which allows for on-the-go tracking and notifications.
- EDI (Electronic Data Interchange): For high-volume shippers, EDI integration offers automated tracking updates directly into their systems. This is a more advanced method, suitable for businesses.
- Customer Service: If online access is unavailable or if you require personalized assistance, you can contact Frozen Food Express customer service for tracking information.
Tracking a Shipment Using the Frozen Food Express Website
Tracking a shipment through the Frozen Food Express website is a simple, user-friendly process. This guide will help you navigate the website and access the necessary information.
- Access the Website: Open your web browser and navigate to the official Frozen Food Express website.
- Locate the Tracking Section: Look for a tracking section on the homepage, typically found in the navigation menu or as a prominent link. The location might vary slightly depending on the website’s design.
- Enter Tracking Information: The website will prompt you to enter your tracking information. This usually involves entering the PRO number, which is a unique reference number assigned to your shipment.
- Submit the Information: After entering the required information, click the “Track” or “Submit” button to initiate the tracking process.
- View Tracking Details: The website will display the current status of your shipment, including its location, estimated delivery date, and any relevant updates. The information will likely be presented in a clear, concise format.
Requirements for Tracking a Shipment
To successfully track a Frozen Food Express shipment, you’ll need specific information to access the tracking data. This information ensures accurate identification of your shipment within the system.
- PRO Number: The most critical piece of information is the PRO number. This is a unique reference number assigned to each shipment by Frozen Food Express. It is usually provided on the bill of lading or shipping confirmation. This number is essential; without it, tracking is impossible. For example, a PRO number might look like this: 1234567890.
- Order Number (May be Required): In some cases, you may also need your order number, particularly if you are tracking a shipment related to a specific purchase or order. The order number helps to cross-reference the shipment with the original order details.
- Other Information (Less Common): Depending on the specific system and the shipment details, you might occasionally be asked for additional information, such as the shipper’s name or the destination zip code, but this is less common.
Understanding the Tracking Statuses
Knowing how to interpret the tracking statuses provided by Frozen Food Express (FFE) is crucial for both shippers and receivers. This understanding allows for proactive management of shipments, ensuring timely delivery and minimizing potential issues. This section breaks down the common tracking statuses, what they mean, and the appropriate actions to take.
Common Tracking Statuses Used by Frozen Food Express
Understanding the various tracking statuses used by FFE is essential for effectively monitoring your shipment’s journey. These statuses provide real-time updates on the location and progress of your freight.
- In Transit: This status indicates that the shipment is currently en route to its destination. The freight is moving between facilities or is on the road.
- Arrived at Terminal: This status means the shipment has reached a specific FFE terminal or facility along its route. It’s awaiting further processing or transfer.
- Departed Terminal: The shipment has left an FFE terminal and is proceeding to the next destination or delivery point.
- Loaded on Trailer: This status confirms the freight has been loaded onto a trailer for transport.
- Out for Delivery: The shipment is on the final leg of its journey and is scheduled to be delivered to the recipient on the same day.
- Delivered: The shipment has been successfully delivered to the consignee.
- Exception: This status signifies that an issue has occurred with the shipment, potentially causing a delay.
Meaning of Each Tracking Status
Each status update provides vital information about the shipment’s location and progress. Understanding what each status signifies allows for proactive monitoring and prompt responses to potential issues.
Obtain access to best asian food tampa to private resources that are additional.
- In Transit: This status typically means the shipment is in transit between terminals, on a long-haul journey, or being handled at a specific location. For example, a refrigerated trailer might be crossing state lines.
- Arrived at Terminal: The shipment has reached a scheduled stop, such as a cross-docking facility. This could mean that the cargo is being unloaded, inspected, or prepared for the next stage of its journey.
- Departed Terminal: This signifies that the shipment has left a terminal and is moving towards its next designated location. This could mean it is on its way to another terminal, distribution center, or the final delivery point.
- Loaded on Trailer: This indicates the freight has been securely loaded and is ready for the road. This is a crucial step, ensuring that the goods are correctly stowed and protected.
- Out for Delivery: This status means the shipment is scheduled to arrive at the consignee’s location on the same day. The driver is en route to deliver the goods.
- Delivered: This confirms the shipment has been successfully delivered to the recipient, including date, time, and often a proof of delivery.
- Exception: This status alerts shippers and receivers of potential problems. The exception status requires immediate attention. Examples of exceptions include:
- Delay: Weather conditions, traffic congestion, or mechanical issues can cause delays.
- Damage: Damage to the goods can be caused by improper handling or accidents.
- Incorrect Address: The delivery address may be incorrect or incomplete.
- Delivery Refusal: The consignee may refuse delivery for various reasons.
Actions for Shippers and Receivers When Encountering Specific Tracking Statuses
The actions to take depend on the tracking status. Prompt responses can mitigate potential issues and ensure a smooth delivery process.
- In Transit: No immediate action is typically required. However, it’s wise to periodically check the status for updates.
- Arrived at Terminal / Departed Terminal / Loaded on Trailer: These statuses indicate normal progress. Continue monitoring for further updates.
- Out for Delivery: The receiver should be prepared to receive the shipment. Ensure personnel are available to unload the freight. Shippers should confirm the consignee is aware of the delivery.
- Delivered: The receiver should inspect the shipment immediately for any damage. Both shipper and receiver should retain the proof of delivery.
- Exception: This requires immediate action:
- Shippers: Contact FFE’s customer service to understand the cause of the exception and initiate a resolution. Provide necessary information to help resolve the issue.
- Receivers: Contact the shipper and FFE to provide details on the problem. Be prepared to provide documentation or photos.
Troubleshooting Tracking Issues
Tracking your Frozen Food Express shipment is generally straightforward, but occasionally, you might encounter issues. Understanding these potential problems and knowing how to resolve them can save you time and ensure your perishable goods arrive safely and on schedule. This section addresses common tracking difficulties and provides solutions to keep you informed every step of the way.
Common Tracking Problems
Several factors can lead to tracking discrepancies. Recognizing these issues helps you proactively address them and minimize potential delays.
- Delayed Updates: The tracking information might not update in real-time, leading to a perceived delay in the shipment’s progress. This is often due to factors like the time it takes for scanners to transmit data or the volume of shipments being processed.
- Inaccurate Location Data: The location information might be imprecise, showing the shipment in a general area rather than its exact location. This can occur due to GPS limitations or network connectivity issues.
- Missing Information: Certain tracking details, such as estimated delivery dates or specific stop locations, might be missing. This can be due to human error during data entry or system glitches.
- Error Messages: The tracking system might display error messages, such as “Invalid Tracking Number” or “No Information Available.” These errors typically indicate a problem with the tracking number or that the shipment information hasn’t yet been entered into the system.
- Unexpected Delays: Unforeseen circumstances, such as inclement weather, traffic congestion, or mechanical issues, can cause delays in the shipment’s transit, leading to inaccurate tracking information.
Solutions for Tracking Problems
Addressing tracking issues requires a proactive approach. The following solutions can help you resolve common problems and stay informed about your shipment’s status.
- Verify the Tracking Number: Double-check that you have entered the correct tracking number. Errors in the number are a primary cause of tracking failures. Ensure you’re using the exact number provided by Frozen Food Express.
- Allow Time for Updates: Tracking information may not be instantaneous. Give the system some time to update, especially after a shipment has just been picked up or has reached a new terminal.
- Check the Estimated Delivery Date: The estimated delivery date provides a benchmark for when the shipment is expected to arrive. If the tracking information indicates a delay, compare it to the estimated delivery date to assess the severity of the issue.
- Review the Tracking History: Examine the entire tracking history for any patterns or clues about the shipment’s progress. Look for any unusual stops or changes in the route.
- Contact the Shipper: If the tracking information remains inaccurate or you have concerns about your shipment’s status, contact the shipper (the sender of the package) for assistance. They can often provide more detailed information and initiate an investigation if necessary.
Contacting Frozen Food Express Customer Service
When tracking issues persist, contacting Frozen Food Express customer service is essential. They have the resources to investigate and resolve tracking problems efficiently.
- Accessing Contact Information: Frozen Food Express provides various methods to contact their customer service department. Information about phone numbers, email addresses, and online contact forms is available on their official website.
- Preparing Information for Contact: Before contacting customer service, gather all relevant information about your shipment. This includes the tracking number, the date the shipment was sent, and any specific details about the issue you are experiencing.
- Describing the Problem Clearly: When you contact customer service, clearly and concisely describe the tracking problem you are experiencing. Provide specific details, such as the date the last update occurred or the discrepancy in the location information.
- Following Up on Your Inquiry: After contacting customer service, keep track of your inquiry and follow up if you don’t receive a response within a reasonable timeframe. This ensures your issue is addressed promptly.
Features and Functionality of the Tracking System
Frozen Food Express’s tracking system goes beyond basic location updates, offering a suite of features designed to provide you with comprehensive control and visibility over your shipments. These advanced functionalities empower you to proactively manage your deliveries and minimize potential disruptions.
Advanced Features in the Tracking System
The tracking system provides several advanced features to enhance your shipping experience. These features are designed to keep you informed and in control of your freight.
- Notifications: Receive real-time alerts via email or SMS regarding shipment status changes, including pickup, en route, at destination, and delivered. This proactive communication helps you stay informed without constantly checking the tracking portal. For example, you can set up notifications to alert you when a shipment is within 50 miles of its destination, allowing you to prepare for unloading.
- Estimated Delivery Times (EDT): The system provides estimated delivery times based on real-time data, historical performance, and current traffic conditions. These EDTs are dynamically updated to reflect any changes that may affect the delivery schedule.
- Custom Reporting: Generate reports on past shipments, including delivery times, transit times, and any delays experienced. This data can be used to analyze shipping performance and identify areas for improvement in your supply chain.
- Geofencing Capabilities: The system utilizes geofencing to track the location of your shipments within specific geographic areas. This feature allows you to monitor your shipments’ progress and receive alerts when they enter or exit predefined zones. This is particularly useful for sensitive cargo.
Setting Up and Managing Shipment Notifications
Customizing your notification preferences is straightforward and allows you to tailor the system to your specific needs. Here’s how you can configure your alerts:
- Access the Notification Settings: Log in to your Frozen Food Express account and navigate to the tracking section. Look for a “Notifications” or “Alerts” tab or button.
- Choose Your Notification Method: Select your preferred method of receiving notifications: email, SMS (text message), or both.
- Specify Shipment Details: Enter the relevant shipment information, such as the tracking number or bill of lading number, for which you want to receive notifications.
- Select Trigger Events: Choose the specific events that will trigger a notification. Common options include:
- Shipment Picked Up
- Shipment En Route
- Arrival at a Terminal
- Shipment Delayed
- Shipment Out for Delivery
- Shipment Delivered
- Customize Notification Frequency: Determine how often you want to receive notifications. You can choose to receive them for every event, or you can opt for a summary notification at specific intervals.
- Save Your Preferences: Once you have configured your settings, save your preferences. The system will then begin sending you notifications based on your selected criteria.
Interpreting Estimated Delivery Times and Potential Variances
Estimated Delivery Times (EDTs) are valuable tools for planning and managing your logistics, but it’s essential to understand how they are calculated and the factors that can influence their accuracy.
The system calculates EDTs by considering several factors:
- Origin and Destination: The distance between the origin and destination points significantly impacts the EDT.
- Mode of Transportation: The type of transportation used (e.g., over-the-road, intermodal) affects the estimated transit time.
- Historical Performance Data: The system analyzes historical data of past shipments to determine average transit times between specific locations.
- Real-time Traffic and Weather Conditions: The system integrates real-time data on traffic congestion, road closures, and weather conditions to adjust the EDT.
- Terminal Processing Times: The time it takes for a shipment to be processed at terminals and transfer points is factored into the EDT.
Understanding Potential Variances: While the system strives to provide accurate EDTs, several factors can cause variances:
- Traffic Congestion: Unexpected traffic delays can significantly impact delivery times, especially in urban areas.
- Weather Conditions: Severe weather, such as snowstorms or hurricanes, can lead to road closures and delays.
- Unexpected Mechanical Issues: Vehicle breakdowns or other mechanical problems can cause delays.
- Customs Inspections: Shipments crossing international borders may be subject to customs inspections, which can add time to the delivery process.
- Changes in Route: Drivers may need to adjust their routes due to unforeseen circumstances, which could affect the EDT.
Example: A shipment is scheduled to travel from Chicago to Los Angeles, with an EDT of 4 days. However, a severe snowstorm in Denver causes a major road closure. This unforeseen event forces the driver to reroute, adding an extra day to the transit time. The EDT is automatically updated to reflect this change. This highlights the dynamic nature of EDTs and the importance of staying informed through notifications.
Impact of Temperature Control on Tracking
Maintaining the integrity of perishable goods is paramount in the food transportation industry. Frozen Food Express (FFE) understands this crucial aspect, integrating advanced temperature monitoring directly into its tracking system. This ensures that temperature-sensitive products, such as frozen foods, pharmaceuticals, and other commodities, are transported under optimal conditions from origin to destination. The integration of temperature data with tracking information provides customers with real-time insights and proactive alerts, minimizing the risk of spoilage and ensuring product quality.
Temperature Monitoring Integration
FFE’s tracking system seamlessly incorporates temperature monitoring capabilities, providing a comprehensive view of the conditions within the trailer. This integration allows customers to monitor temperature fluctuations alongside the location and estimated time of arrival (ETA) of their shipments.Temperature monitoring is integrated through the following methods:
- Sensor Deployment: Temperature sensors are strategically placed within the trailers, often at multiple points to capture a complete temperature profile. These sensors are designed to withstand the rigors of transportation and accurately measure temperatures across a wide range.
- Real-Time Data Transmission: The sensors continuously transmit temperature data wirelessly to a central tracking system. This data is updated at regular intervals, providing a real-time view of the temperature conditions.
- System Integration: The temperature data is integrated with the GPS location and other tracking information, creating a unified view of the shipment’s status. This combined data is accessible through the FFE tracking portal.
Temperature Data Collection and Sharing
FFE utilizes sophisticated technology to collect and share temperature data with its customers, ensuring transparency and accountability.Temperature data is collected and shared through the following processes:
- Data Collection: Advanced temperature sensors, often using cellular or satellite communication, continuously monitor the temperature inside the trailer. These sensors are calibrated to ensure accuracy and reliability.
- Data Transmission: The collected temperature data is transmitted wirelessly to a central server. This transmission occurs at regular intervals, providing near real-time updates.
- Data Accessibility: Customers can access the temperature data through the FFE tracking portal. This includes current temperature readings, historical temperature logs, and temperature alerts.
- Alerts and Notifications: The system is programmed to generate alerts if the temperature deviates from the pre-defined acceptable range. These alerts are sent to both FFE and the customer, allowing for immediate action.
Identifying and Addressing Temperature-Related Issues
FFE’s system allows for proactive identification and resolution of temperature-related issues during transit.Addressing temperature-related issues involves the following steps:
- Monitoring Temperature Data: Customers can continuously monitor the temperature readings through the tracking portal. They can also review historical temperature logs to identify any anomalies.
- Alerts and Notifications: The system sends automated alerts if the temperature exceeds or falls below the pre-set thresholds. These alerts notify both FFE and the customer of potential issues.
- Proactive Intervention: Upon receiving an alert, FFE’s operations team can take immediate action. This may involve adjusting the trailer’s refrigeration settings, rerouting the shipment to a facility with temperature-controlled storage, or contacting the customer to discuss potential solutions.
- Documentation and Reporting: The system maintains a detailed record of all temperature readings, alerts, and corrective actions taken. This documentation is available to the customer for audit and compliance purposes.
- Example: Consider a shipment of frozen pizzas. The system is programmed to maintain a temperature of -10°F. If the temperature rises above -5°F, an alert is triggered. FFE’s team can then adjust the refrigeration unit or contact the customer to discuss options, such as expediting delivery or re-evaluating the load.
Tracking and Cold Chain Logistics
Maintaining the cold chain is paramount in the frozen food industry, ensuring product safety and quality from origin to consumer. Effective tracking is the backbone of this process, allowing for real-time monitoring and control of temperature-sensitive goods. This visibility is crucial for preventing spoilage, minimizing waste, and upholding consumer trust.
The Role of Tracking in Maintaining Cold Chain Integrity
Tracking plays a vital role in maintaining the integrity of the cold chain. It provides real-time data on the location and condition of goods, enabling proactive intervention when deviations occur. This proactive approach is critical for preserving product quality and safety.
- Temperature Monitoring: Continuous monitoring of temperature throughout the journey is essential. Tracking systems use sensors to record temperature fluctuations, alerting stakeholders to potential issues.
- Location Tracking: GPS tracking provides real-time location data, allowing for efficient route planning and timely delivery. This helps minimize transit times and exposure to temperature variations.
- Alerting and Notifications: Automated alerts are triggered when temperature thresholds are breached or other critical events occur. This enables immediate action to rectify the situation.
- Documentation and Compliance: Tracking systems generate comprehensive records of temperature, location, and handling procedures, ensuring compliance with regulatory requirements and providing a detailed audit trail.
- Reduced Waste: By identifying and addressing potential issues early, tracking helps minimize product spoilage and waste, contributing to cost savings and sustainability.
Comparing Frozen Food Express’s Cold Chain Practices with Industry Standards
Frozen Food Express (FFE) adheres to industry standards in cold chain logistics, employing advanced tracking technologies and rigorous quality control measures. These practices are continuously evaluated and improved to ensure the highest levels of product integrity. The comparison below highlights some key areas:
- Temperature Monitoring: FFE utilizes advanced temperature sensors and monitoring systems to ensure continuous temperature control throughout the transportation process. Industry standards often involve similar technologies but may vary in the frequency of data collection and reporting. FFE’s system allows for real-time monitoring and proactive adjustments, exceeding some basic industry requirements.
- Equipment and Infrastructure: FFE’s fleet and facilities are equipped with temperature-controlled environments, including refrigerated trailers and warehouses. These meet or exceed industry standards for insulation, refrigeration capacity, and maintenance. Regular maintenance and calibration of equipment are crucial to maintaining the cold chain.
- Training and Procedures: FFE provides comprehensive training to its employees on cold chain best practices, including proper handling, loading, and unloading procedures. These training programs are designed to align with industry standards and regulatory requirements. Standard operating procedures (SOPs) are in place to ensure consistency and compliance.
- Data Analysis and Reporting: FFE’s tracking systems generate detailed data reports, providing insights into temperature fluctuations, transit times, and other key performance indicators (KPIs). This data is used to identify areas for improvement and optimize cold chain operations. Industry standards often emphasize data analysis, but the level of detail and frequency of reporting may vary.
Tracking Feature Comparison: Frozen Food Express vs. Competitors
The following table compares the tracking features of Frozen Food Express with two of its competitors, illustrating the capabilities and differences in their offerings. The information presented is for comparative purposes only and based on publicly available information and general industry knowledge. Specific features and functionalities may vary.
Feature | Frozen Food Express | Competitor A | Competitor B |
---|---|---|---|
Real-Time Temperature Monitoring | Yes, with alerts and historical data | Yes, with alerts | Yes, basic monitoring |
GPS Location Tracking | Yes, integrated with temperature data | Yes | Yes |
Geofencing Capabilities | Yes, for proactive monitoring and alerts | Yes | Limited |
Mobile App Access | Yes, for real-time tracking and data access | Yes | Yes, basic tracking information |
Reporting and Analytics | Comprehensive reports with customizable options | Standard reports | Basic reporting features |
Integration with Warehouse Management Systems (WMS) | Yes | Limited | No |
24/7 Customer Support | Yes | Yes | Yes |
Tracking and Claims
Understanding how tracking data supports the claims process is crucial for shippers and receivers of temperature-sensitive freight. Frozen Food Express (FFE) provides robust tracking capabilities to help resolve issues of damaged or lost shipments efficiently. This section details how FFE’s tracking information is utilized in claims and Artikels the necessary steps to initiate a claim.
Tracking Information in the Claims Process
FFE’s tracking system plays a vital role in the claims process. The detailed information it provides is often essential in determining the cause of damage or loss and in supporting a successful claim. The data generated by the tracking system offers a comprehensive view of the shipment’s journey, which is essential when problems arise.
Information Required to File a Claim
To file a claim related to tracking issues, you’ll need to gather specific information, which FFE will use to assess the validity of the claim. This information is critical for a prompt and accurate evaluation.
- Bill of Lading (BOL) Number: This is the primary identifier for the shipment.
- Tracking Number: Provides access to the shipment’s history and location.
- Description of the Damage or Loss: A detailed account of the issue, including the extent of the damage or a statement that the shipment is missing.
- Photos or Videos: Visual evidence of the damage is extremely helpful in the claims process. Take pictures that clearly show the damage to the packaging and the product.
- Date of Delivery or Expected Delivery: Essential for confirming if the shipment arrived on time or if it was delayed.
- Supporting Documentation: Any additional documents that can help support the claim, such as purchase orders, invoices, and packing lists.
Process of Filing a Claim Related to Tracking Issues, Frozen food express tracking
The process of filing a claim, supported by tracking data, follows a structured approach to ensure efficient resolution. Following these steps is critical for a smooth claims process.
- Gather Necessary Information: Collect all required documentation, including the BOL number, tracking number, and a detailed description of the issue, along with supporting evidence such as photographs or videos.
- Contact Frozen Food Express Claims Department: Initiate the claim process by contacting the FFE claims department. Contact information, such as phone numbers and email addresses, is usually available on the FFE website or the BOL.
- Submit the Claim: Provide the collected information and documentation to the claims department. Ensure that all details are accurate and complete to avoid delays.
- Claim Review and Investigation: FFE will review the claim and conduct an investigation based on the tracking data and supporting documentation. This may involve reviewing the shipment’s history, including temperature logs, location data, and any recorded events.
- Claim Resolution: The claims department will communicate the outcome of the investigation and provide a resolution. This may include approving the claim, denying the claim, or requesting additional information.
Future of Tracking in Frozen Food Express
Frozen Food Express (FFE) is constantly evolving to meet the demands of the modern cold chain. The future of tracking promises enhanced visibility, improved efficiency, and increased transparency, ultimately benefiting both FFE and its customers. This section explores potential advancements and provides a glimpse into the future of FFE’s tracking system.
Potential Future Enhancements to the Frozen Food Express Tracking System
FFE is committed to investing in cutting-edge technologies to improve its tracking capabilities. These enhancements will refine operations and provide more comprehensive information to stakeholders.
- Real-time Predictive Analytics: Utilizing advanced algorithms and machine learning to predict potential delays, temperature fluctuations, and other issues before they occur. This allows for proactive intervention and minimizes disruptions. For example, the system could analyze historical data, weather patterns, and traffic conditions to anticipate potential problems on a specific route.
- Enhanced Sensor Technology: Implementing more sophisticated sensors that provide a wider range of data points, including precise temperature readings, humidity levels, shock detection, and even door opening alerts. These sensors will be smaller, more durable, and more energy-efficient.
- Integration with Blockchain Technology: Incorporating blockchain to create a secure and transparent record of the entire cold chain journey, from origin to destination. This will improve traceability, reduce fraud, and ensure the integrity of the products. Every transaction, including temperature readings and location updates, would be recorded on the blockchain, making it immutable and accessible to authorized parties.
- Automated Reporting and Alerts: Developing a system that automatically generates customized reports and alerts based on pre-defined parameters. This will allow customers to receive timely notifications about critical events, such as temperature deviations or unexpected delays.
- Expanded Integration with Customer Systems: Providing seamless integration with customers’ existing supply chain management systems, enabling them to access tracking data directly within their own platforms. This will streamline communication and improve overall efficiency.
Hypothetical Interface for a Future Tracking System
The future tracking interface will prioritize user experience, offering intuitive navigation and easily accessible information. The goal is to provide a clear and concise overview of the shipment’s status at a glance.
The hypothetical interface will feature the following elements:
- Interactive Map: A dynamic map displaying the real-time location of the shipment, along with route information, traffic conditions, and nearby points of interest. Users can zoom in and out, and click on specific points to view detailed information.
- Dashboard: A customizable dashboard providing a summary of key metrics, such as temperature readings, estimated time of arrival (ETA), and any potential issues. The dashboard will allow users to personalize the information displayed based on their specific needs.
- Timeline View: A chronological timeline of the shipment’s journey, highlighting key events, such as loading, unloading, temperature checks, and any deviations from the planned route.
- Alerts and Notifications: A dedicated section for receiving real-time alerts and notifications about critical events, such as temperature excursions or unexpected delays. Users can customize alert preferences based on their needs.
- Reporting and Analytics: A section for generating customized reports and analyzing historical data, providing insights into shipment performance and identifying areas for improvement.
- Mobile Accessibility: A fully responsive design that allows users to access the tracking system from any device, including smartphones and tablets.
Diagram Showcasing the Flow of Information Within the Tracking System
The following diagram illustrates the flow of information within a future tracking system, showcasing the interconnectedness of various components and the flow of data.
The diagram represents the following key elements:
1. Data Sources: Sensors embedded within the refrigerated trailers, GPS devices, and external data sources (e.g., weather services, traffic data providers) collect real-time information.
2. Data Transmission: The data is transmitted wirelessly via cellular networks or satellite communication to a central server.
3. Data Processing and Analysis: The central server processes and analyzes the data, using advanced algorithms and machine learning to identify patterns, predict potential issues, and generate alerts.
4. Database and Storage: The processed data is stored in a secure database, providing a comprehensive record of the shipment’s journey.
5. User Interface: The user interface provides access to the tracking information through a web-based platform and mobile applications.
6. Alerts and Notifications: Automated alerts and notifications are sent to customers and FFE personnel based on pre-defined parameters.
7. Integration with External Systems: The system integrates with customer systems and other external platforms, enabling seamless data exchange.
The diagram highlights the continuous flow of information from the data sources to the user interface, with real-time monitoring, analysis, and proactive intervention.
Ending Remarks: Frozen Food Express Tracking
In closing, my friends, Frozen Food Express Tracking is more than just a tool; it’s a testament to our commitment to quality and reliability. We’ve journeyed together through the various aspects of this system, from understanding the statuses to troubleshooting issues and envisioning its future. Remember, this system helps us maintain the integrity of the cold chain and protect the freshness of every item.
May this knowledge empower you to confidently navigate the world of frozen food transportation and always receive your goods with a smile.