Pallets of food are the unsung heroes of the global food supply chain, enabling the efficient and safe transport of sustenance from producers to consumers. This examination delves into the multifaceted world of palletized food, exploring its critical role in maintaining food safety, optimizing logistics, and minimizing waste. From the types of pallets employed to the intricacies of storage and transportation, we will dissect the essential aspects of this vital infrastructure.
The scope of this analysis extends from the fundamental definition of “pallets of food” to the advanced technologies reshaping pallet management. We will examine the regulatory frameworks that govern pallet use, the environmental implications of different pallet materials, and the innovative practices driving sustainability within the industry. This comprehensive exploration aims to provide a clear understanding of the complex processes involved in ensuring food availability worldwide.
Introduction to Pallets of Food
Pallets of food represent a cornerstone of the modern food supply chain, facilitating the efficient movement of goods from producers to consumers. They are essential for maintaining the integrity of food products and ensuring their timely delivery across vast distances. This system streamlines logistics, minimizes handling, and contributes to the overall efficiency of the food industry.
Definition and Purpose of Pallets
Pallets are flat structures, typically made of wood, plastic, or metal, designed to support goods during transport. Their primary purpose is to create a standardized base for stacking, storing, and transporting food items. This standardization allows for easy handling by forklifts and other material-handling equipment, significantly speeding up loading and unloading processes.
Significance in the Food Supply Chain
Pallets play a crucial role in maintaining the efficiency and safety of the food supply chain. They enable the consolidation of various food products into manageable units, reducing the risk of damage and spoilage. The use of pallets also allows for:
- Improved Storage: Pallets facilitate organized storage in warehouses and distribution centers, maximizing space utilization.
- Enhanced Safety: By elevating goods off the ground, pallets minimize the risk of contamination from moisture, pests, and other hazards.
- Faster Transportation: The standardized size and shape of palletized loads enable quick and efficient loading and unloading of trucks, trains, and ships.
- Reduced Labor Costs: The use of forklifts and other automated equipment to handle palletized goods reduces the need for manual labor, lowering costs.
Pallets, therefore, are integral to ensuring the smooth and cost-effective flow of food products from origin to destination.
Types of Food Typically Transported on Pallets
A wide variety of food products are transported on pallets, encompassing both perishable and non-perishable items. The specific type of pallet used often depends on the nature of the food being transported, considering factors such as weight, temperature sensitivity, and shelf life. Common examples include:
- Packaged Goods: Canned goods, boxed cereals, and bottled beverages are frequently palletized for easy handling and distribution.
- Produce: Fruits and vegetables, often transported in crates or containers on pallets, require careful handling to maintain freshness. Consider the transport of fresh strawberries from California to supermarkets across the United States; this is facilitated by palletized shipping.
- Dairy Products: Milk, yogurt, and cheese are often transported on refrigerated pallets to maintain the required temperature during transit.
- Frozen Foods: Frozen pizzas, ice cream, and other frozen products are transported on specialized pallets designed for cold storage and temperature control.
- Bulk Ingredients: Flour, sugar, and other bulk ingredients are often shipped in large bags or containers on pallets.
Food Safety and Pallet Handling: Pallets Of Food
The safe transport of food is paramount, and the humble pallet plays a critical, often overlooked, role. Adherence to stringent food safety protocols in pallet handling and storage is crucial to prevent contamination and ensure consumer health. This section will delve into the regulatory landscape, potential hazards, and best practices necessary to maintain the integrity of food products throughout the supply chain.
Food Safety Regulations and Pallet Use
Regulations governing food safety, such as those Artikeld by the Food and Drug Administration (FDA) in the United States and similar bodies globally, directly impact pallet usage. These regulations mandate that food contact surfaces, including pallets, must be clean, sanitary, and made of materials that do not pose a risk of contamination. The specific requirements vary depending on the type of food, the geographic location, and the specific industry.
Compliance with these regulations is not merely a suggestion; it is a legal obligation with significant consequences for non-compliance, including product recalls, fines, and reputational damage.
Potential Hazards of Improper Pallet Handling and Storage
Improper pallet handling and storage can introduce a multitude of hazards that compromise food safety. These hazards can be broadly categorized as follows:
- Contamination from foreign objects: Pallets can harbor splinters, nails, and other debris that can contaminate food products. Damage to pallets can expose food to these hazards.
- Cross-contamination from previous use: Pallets previously used for non-food products, such as chemicals or hazardous materials, can transfer contaminants to food products if not properly cleaned and sanitized.
- Pest infestation: Pallets stored improperly can attract pests such as rodents and insects, which can contaminate food products with their droppings, urine, and physical presence.
- Mold and mildew growth: Pallets exposed to moisture and improper storage conditions can develop mold and mildew, posing health risks and potentially spoiling food products.
- Structural instability: Damaged or poorly maintained pallets can collapse under the weight of food products, leading to product damage, potential injury to workers, and the introduction of contaminants.
Best Practices for Maintaining Pallet Hygiene, Pallets of food
Maintaining the hygiene of pallets used for food transport requires a multi-faceted approach. The following practices are essential:
- Pallet Selection: Choosing pallets designed specifically for food transport is crucial. These pallets are often made from materials like plastic or treated wood that are easier to clean and sanitize. Avoid using pallets that show signs of significant damage.
- Regular Inspection: Implement a regular inspection program to identify and remove damaged pallets. Inspect pallets for splinters, protruding nails, cracks, and any other damage that could compromise food safety.
- Cleaning and Sanitization: Establish a robust cleaning and sanitization protocol. This should include regular cleaning of pallets using appropriate cleaning agents and sanitizers, particularly after use and before reuse. The frequency of cleaning depends on the type of food being transported and the potential for contamination.
- Proper Storage: Store pallets in a clean, dry environment, away from potential sources of contamination. Elevate pallets off the ground to prevent moisture accumulation and pest infestation.
- Training and Education: Train employees on proper pallet handling and hygiene practices. Ensure that all personnel involved in pallet handling understand the importance of food safety and their role in maintaining it.
- Documentation: Maintain detailed records of pallet inspections, cleaning, and sanitization activities. This documentation is crucial for demonstrating compliance with food safety regulations and for traceability purposes.
- Use of Pallet Wraps: Employing pallet wraps made of food-grade materials can create a barrier between the food product and the pallet surface, minimizing the risk of direct contact and potential contamination.
Types of Pallets Used for Food
The selection of the appropriate pallet type is crucial for ensuring the safety and integrity of food products throughout the supply chain. Different pallet materials and designs offer varying levels of protection, durability, and hygiene, impacting storage, transportation, and overall operational efficiency. Understanding the characteristics of each pallet type allows food businesses to make informed decisions, mitigating risks and optimizing logistical processes.
Pallet Types and Characteristics
A variety of pallet types are employed in the food industry, each with distinct properties influencing their suitability for different applications. The following table Artikels the common types, detailing their materials, dimensions, and load capacities. This information helps in choosing the most appropriate pallet for specific food handling needs.
Pallet Material | Typical Dimensions (inches) | Typical Load Capacity (lbs) | Key Features | Common Food Industry Applications |
---|---|---|---|---|
Wood | 48 x 40 (Standard) | 2,500 – 3,000 (varies) | Cost-effective, readily available, repairable. Susceptible to moisture, pests, and splintering. | Dry goods, non-perishable items. |
Plastic | 48 x 40 (Standard), various sizes | 2,800 – 5,000 (varies) | Durable, washable, resistant to moisture and pests, long lifespan. Higher initial cost. | Refrigerated goods, pharmaceuticals, closed-loop systems. |
Metal (Steel/Aluminum) | 48 x 40 (Standard), custom sizes | 4,000 – 6,000+ (varies) | Extremely durable, high load capacity, hygienic, resistant to extreme temperatures. High initial cost. | Heavy-duty applications, food processing facilities, cleanroom environments. |
Composite | Variable | Varies | Combination of materials (e.g., wood and plastic), offering a balance of cost, durability, and hygiene. | Various applications, often used as a middle-ground solution. |
Comparative Analysis of Pallet Materials
The choice of pallet material significantly impacts the performance and suitability of pallets for food transport. Wooden, plastic, and metal pallets each present unique advantages and disadvantages, influencing their selection based on specific operational requirements.
- Wooden Pallets: Wood pallets are favored for their affordability and widespread availability. Their repairability is a significant advantage, allowing for cost-effective maintenance. However, wood is porous, making it susceptible to moisture absorption, which can promote mold growth and harbor bacteria. Splintering poses a safety hazard and can contaminate food products. Wood pallets also require heat treatment or fumigation to comply with international phytosanitary regulations (ISPM 15), adding to their cost and complexity.
- Plastic Pallets: Plastic pallets excel in hygiene and durability. They are resistant to moisture, chemicals, and pests, and are easily cleaned and sanitized. Their smooth surfaces prevent splintering and reduce the risk of food contamination. While the initial cost of plastic pallets is higher than wood, their longer lifespan and reduced maintenance costs often make them a more economical choice over time, particularly in closed-loop systems.
The consistent dimensions of plastic pallets also facilitate automated handling and warehousing.
- Metal Pallets: Metal pallets, typically constructed from steel or aluminum, offer the highest load capacity and durability. They are ideal for heavy-duty applications and are completely impervious to moisture, pests, and microbial growth. Metal pallets can withstand extreme temperatures, making them suitable for both refrigerated and high-temperature environments. However, their higher initial cost and potential for corrosion (in the case of steel) can be drawbacks.
Pallet Requirements for Different Food Products
The specific characteristics of food products dictate the appropriate pallet requirements. Considerations include temperature sensitivity, hygiene standards, and the potential for contamination. The choice of pallet plays a vital role in maintaining food safety and quality.
- Refrigerated Goods: Refrigerated goods, such as produce, dairy, and meat, necessitate pallets that can withstand cold temperatures and maintain hygiene. Plastic pallets are commonly used due to their resistance to moisture and ease of cleaning. Metal pallets are also suitable, particularly for heavy loads and harsh environments. Pallets must be free from splinters and designed to allow for adequate airflow to maintain product temperature.
An example is the use of plastic pallets in the transport of frozen seafood to prevent contamination and maintain product integrity.
- Dry Goods: Dry goods, including packaged foods, grains, and cereals, often utilize wooden pallets due to their cost-effectiveness. However, the pallets must be well-maintained, free from splinters, and treated to prevent pest infestation. Plastic pallets are also a viable option, especially in facilities with strict hygiene standards. The key is to ensure the pallet material does not contribute to contamination or compromise the packaging of the dry goods.
For instance, the use of treated wooden pallets is common for transporting bulk bags of flour.
Sourcing and Procurement of Food Pallets
The efficient and cost-effective sourcing of pallets is crucial for maintaining the integrity of the food supply chain. Pallet procurement decisions directly impact food safety, transportation costs, and environmental sustainability. A strategic approach to sourcing ensures businesses can meet demand while minimizing risk and maximizing profitability.
Methods for Sourcing Pallets for Food Transport
Businesses have several options for sourcing pallets, each with its own advantages and disadvantages. Understanding these options allows for informed decision-making based on specific needs and priorities.
- New Pallets: New pallets offer the highest level of hygiene and consistency, critical for food safety. They are manufactured to specific dimensions and load-bearing capacities, reducing the risk of pallet failure during transport. While the initial investment is higher, new pallets often have a longer lifespan and can contribute to a lower total cost of ownership over time. For instance, a major food distributor might opt for new, heat-treated pallets to comply with stringent food safety regulations and minimize the risk of contamination.
- Used Pallets: Used pallets present a more economical option, particularly for businesses operating on tight budgets. These pallets are typically inspected, repaired, and reconditioned to meet specific performance standards. The cost savings can be significant, but it’s essential to verify the pallet’s history and condition to ensure it’s suitable for food transport. Proper cleaning and sanitization are critical to eliminate potential contaminants.
A small-scale food manufacturer, for example, might source used pallets to reduce initial capital expenditure, but would need to implement rigorous inspection and cleaning protocols.
- Recycled Pallets: Recycled pallets are an environmentally friendly option, as they reduce waste and conserve resources. These pallets are often sourced from various industries and are disassembled, repaired, and reconstructed. The cost is generally comparable to used pallets, but the quality and consistency can vary. Sourcing from reputable recycling facilities that adhere to strict quality control measures is essential. A company committed to sustainability might prioritize recycled pallets, even if it means accepting some variability in pallet dimensions, as long as safety and performance standards are met.
Designing a Process for Evaluating Pallet Suppliers
Selecting the right pallet supplier is a critical decision that directly impacts operational efficiency and cost management. A robust evaluation process ensures that suppliers meet the required quality standards, offer competitive pricing, and demonstrate a commitment to sustainability.
- Quality Assessment: Evaluate suppliers based on the quality of their pallets. This includes inspecting the materials used, the construction of the pallet, and the overall durability. Consider factors such as load-bearing capacity, resistance to moisture, and the presence of any potential contaminants. Request samples and conduct thorough inspections to assess their suitability for food transport. For instance, a food processing plant might require pallets that meet specific heat treatment standards to comply with ISPM 15 regulations, ensuring that the pallets are free from pests and diseases.
Browse the implementation of hikari koi food in real-world situations to understand its applications.
- Cost Analysis: Compare pricing from different suppliers, considering both the initial purchase price and the long-term costs associated with pallet ownership. Factor in maintenance costs, repair costs, and the lifespan of the pallets. Negotiate pricing based on volume and establish clear payment terms. Request quotes from multiple suppliers to ensure you are receiving the best possible value. A large food retailer might negotiate bulk discounts with a pallet supplier to reduce overall procurement costs.
- Sustainability Evaluation: Assess the supplier’s environmental practices. This includes evaluating their use of sustainable materials, their waste reduction strategies, and their commitment to reducing their carbon footprint. Look for suppliers that offer recycled or renewable pallet options and that have implemented programs to minimize their environmental impact. A company committed to reducing its carbon footprint might select a supplier that utilizes sustainably sourced wood or offers a pallet return program.
Impact of Pallet Choices on the Overall Cost of Food Distribution
The choice of pallets significantly impacts the overall cost of food distribution. From initial procurement to transportation and disposal, pallet decisions influence various cost components.
- Procurement Costs: The initial cost of purchasing pallets varies significantly depending on the type of pallet chosen (new, used, or recycled). While new pallets typically have a higher upfront cost, they may offer a longer lifespan and reduced maintenance expenses, potentially leading to lower total costs over time. Used and recycled pallets can offer cost savings, but they may require more frequent repairs or replacements.
- Transportation Costs: The weight and dimensions of pallets impact transportation costs. Heavier pallets increase fuel consumption and shipping expenses. Consistent pallet dimensions optimize truckload capacity, reducing the number of shipments required. Standardized pallets are essential for efficient loading and unloading, minimizing labor costs and reducing the risk of damage during transit.
- Handling and Storage Costs: Pallet quality affects handling and storage costs. Durable pallets minimize the risk of damage during handling, reducing product losses and the need for repairs. Well-maintained pallets facilitate efficient storage in warehouses and distribution centers. Pallets that meet specific hygiene standards also reduce the risk of contamination, minimizing potential costs associated with product recalls or disposal.
- Maintenance and Repair Costs: Pallet maintenance and repair costs vary depending on the pallet type and the supplier’s services. Regular inspections, timely repairs, and proper handling practices extend pallet life and minimize overall costs. Implementing a pallet management program that includes tracking, inspection, and repair procedures can help reduce these expenses.
- Waste Disposal Costs: Pallet disposal costs can be significant, particularly for businesses that use a large volume of pallets. Recycling or reusing pallets reduces waste disposal expenses. Choosing durable pallets that can withstand multiple trips and minimizing the number of pallets that need to be disposed of can also help control these costs. A food distribution company might implement a pallet return program to reduce waste disposal costs and promote sustainability.
Pallet Loading and Stacking Techniques
Proper pallet loading and stacking are crucial for maintaining food safety, preventing product damage, and ensuring efficient warehouse operations. These techniques are essential for all stages of the supply chain, from the manufacturer to the retailer. Poor practices can lead to costly product loss, safety hazards, and potential regulatory violations.
Step-by-Step Procedure for Safe Pallet Loading
Following a standardized procedure minimizes the risk of accidents and product damage. This process encompasses several key steps, from pallet selection to securing the loaded pallet.
- Select the Appropriate Pallet: Ensure the pallet is the correct size, type, and in good condition for the load. Inspect for any damage, such as broken boards, protruding nails, or pest infestation.
- Inspect the Load: Verify the integrity of the food product packaging. Reject any items with visible damage, such as punctures, tears, or leaks.
- Plan the Load Pattern: Determine the optimal stacking pattern for the specific product. Consider the size, shape, and weight of the items, and aim for a stable and interlocked configuration. Common patterns include the column stack, the interlocking stack, and the bricklay pattern.
- Begin Loading: Start by placing the heaviest items at the bottom of the pallet. Distribute the weight evenly across the pallet surface.
- Build Layers: Build each layer according to the planned pattern. Ensure the items are aligned and tightly packed to minimize shifting.
- Interlock Layers: For increased stability, interlock the layers by shifting the placement of items in each subsequent layer. This helps to bind the load together.
- Maintain Squareness: Ensure the corners of the pallet load remain square. This prevents the load from becoming unstable during handling and transportation.
- Secure the Load: Once the pallet is fully loaded, secure the items using stretch wrap, banding, or other appropriate methods. Ensure the wrapping or banding is tight and evenly distributed to prevent shifting during transit.
- Label the Pallet: Affix clear and accurate labels to the pallet, including product information, handling instructions, and any necessary warnings.
- Inspect the Completed Pallet: Before moving the pallet, conduct a final inspection to ensure it is stable, secure, and properly labeled.
Weight Distribution and Stability
Weight distribution is critical to prevent pallet instability, product damage, and potential safety hazards. An unevenly distributed load can cause the pallet to tip, collapse, or shift during handling and transportation.
The key principles of weight distribution include:
- Center of Gravity: Keep the center of gravity of the loaded pallet as low as possible. This increases stability.
- Even Distribution: Distribute the weight evenly across the entire pallet surface. Avoid concentrating weight on one side or in the center.
- Heavy Items at the Bottom: Place the heaviest items at the bottom of the pallet to provide a stable base.
- Load Limits: Adhere to the pallet’s weight capacity and the weight limits of any handling equipment.
For example, a shipment of canned goods would be loaded with the heavier cases of canned tomatoes at the bottom, followed by lighter items such as canned beans, and finally, the lightest items, like canned fruit cocktail, at the top. This approach ensures the center of gravity remains low and that the load is stable.
Common Mistakes in Pallet Loading and Solutions
Several common mistakes can compromise the safety and efficiency of pallet loading operations. Identifying these errors and implementing corrective measures is essential for maintaining a safe and productive work environment.
Common mistakes and solutions include:
- Overloading the Pallet: Exceeding the pallet’s weight capacity.
- Solution: Strictly adhere to pallet weight limits. Implement a system to weigh each pallet before loading.
- Uneven Weight Distribution: Concentrating weight on one side of the pallet.
- Solution: Plan the loading pattern carefully. Ensure that the weight is distributed evenly across the pallet surface.
- Poor Stacking Patterns: Using unstable stacking patterns.
- Solution: Utilize interlocked or bricklay stacking patterns to improve load stability. Train workers on proper stacking techniques.
- Damaged Pallets: Using pallets with broken boards or other damage.
- Solution: Inspect all pallets before use. Remove and repair or replace any damaged pallets. Implement a pallet management program.
- Inadequate Securing: Failure to properly secure the load.
- Solution: Use stretch wrap, banding, or other appropriate methods to secure the load. Ensure the securing method is applied correctly and tightly.
- Ignoring Product Packaging: Stacking products in a manner that compromises the packaging.
- Solution: Review the manufacturer’s recommendations for stacking the products.
By avoiding these common mistakes and implementing the suggested solutions, food businesses can significantly improve the safety and efficiency of their pallet loading operations, reducing product damage and ensuring regulatory compliance.
Pallet Storage and Warehousing
Efficient and safe storage of food pallets within warehouses and distribution centers is crucial for maintaining product integrity, minimizing waste, and ensuring compliance with food safety regulations. Proper storage practices contribute significantly to the overall supply chain efficiency and profitability. This section provides a comprehensive guide to best practices in this critical area.
Best Practices for Warehouse Food Pallet Storage
Implementing a robust set of practices is paramount for optimizing warehouse operations. These practices cover a range of aspects, from receiving and inspection to inventory management and facility maintenance. Adhering to these guidelines helps to prevent spoilage, contamination, and other issues that can compromise food safety and quality.
- Receiving and Inspection: Upon arrival, all pallets of food should be thoroughly inspected for damage, infestation, or signs of tampering. Verify that the product meets the required temperature specifications and that the packaging is intact. Reject any pallets that do not meet these criteria. Document the inspection process meticulously, including date, time, and findings.
- Inventory Management: Implement a First-In, First-Out (FIFO) inventory system to ensure that older products are used before newer ones. This practice minimizes the risk of spoilage due to prolonged storage. Use a Warehouse Management System (WMS) to track inventory levels, location, and expiration dates. This system provides real-time visibility into the inventory, enabling better decision-making and reducing waste.
- Storage Environment: Maintain a clean and organized storage environment. Regularly clean and sanitize the warehouse to prevent pest infestations and cross-contamination. Ensure proper ventilation to control humidity and temperature. Implement pest control measures, including regular inspections and treatments, to prevent infestations.
- Pallet Handling: Use appropriate equipment, such as forklifts and pallet jacks, to handle pallets safely and efficiently. Train employees on proper pallet handling techniques to prevent accidents and damage to the product. Inspect equipment regularly and maintain it to ensure it is in good working order.
- Rotation and Stocking: Rotate pallets regularly to prevent products from sitting for extended periods. Restock shelves efficiently, ensuring that new products are placed behind older ones. Implement a clear labeling system to identify products and their expiration dates.
- Temperature and Humidity Monitoring: Continuously monitor and record temperature and humidity levels throughout the warehouse. Maintain optimal conditions for each type of food product. Use temperature-controlled storage areas for products that require specific temperature ranges.
- Emergency Preparedness: Develop and implement an emergency plan to address potential issues such as power outages, equipment failures, and natural disasters. This plan should include procedures for protecting food products and ensuring the safety of employees.
- Regular Audits and Inspections: Conduct regular audits and inspections to ensure compliance with food safety regulations and internal procedures. Identify and address any deficiencies promptly. Document all audit findings and corrective actions.
Temperature and Humidity Control in Food Pallet Storage
Controlling temperature and humidity is a critical element in preserving the quality and safety of food stored on pallets. Fluctuations in these environmental factors can lead to spoilage, the growth of harmful microorganisms, and physical degradation of the product. Maintaining the appropriate conditions is therefore essential for extending shelf life and minimizing losses.
- Temperature Requirements: Different food products have specific temperature requirements. Perishable items such as fresh produce, meat, and dairy products require refrigerated or frozen storage. Dry goods, such as grains and canned goods, generally require storage at ambient temperatures.
- Humidity Control: High humidity can promote the growth of mold and bacteria, while low humidity can lead to the drying out of products. The optimal humidity level depends on the type of food product. For example, dry goods generally require lower humidity levels than fresh produce.
- Refrigerated and Frozen Storage: Refrigerated storage typically maintains temperatures between 34°F and 40°F (1°C and 4°C), while frozen storage maintains temperatures at or below 0°F (-18°C). Ensure that refrigeration units are properly maintained and regularly monitored to maintain these temperature ranges.
- Air Circulation: Proper air circulation is essential to maintain consistent temperatures and prevent the formation of hot spots. Use fans to circulate air throughout the storage area. Avoid overcrowding pallets to allow for adequate airflow.
- Monitoring and Recording: Continuously monitor and record temperature and humidity levels using calibrated sensors. Regularly check and maintain these records to identify any deviations from the required conditions. Implement an alert system to notify personnel of any temperature or humidity excursions.
- Insulation: Ensure that the warehouse is properly insulated to minimize temperature fluctuations. Seal any gaps or cracks in the building to prevent air leaks. Consider using insulated doors and loading docks to maintain temperature control during loading and unloading operations.
- Examples: Consider the case of a major produce distributor. They experienced significant spoilage of fresh fruits and vegetables due to inadequate temperature control during storage. After implementing a robust temperature monitoring and control system, including regular calibration of sensors and improved refrigeration maintenance, they reduced spoilage rates by 20% and increased profitability.
Pallet Racking Systems and Storage Efficiency
Pallet racking systems are a key component of efficient warehouse operations, significantly impacting storage capacity, product accessibility, and overall throughput. Various types of racking systems are available, each designed to optimize storage space and meet specific operational needs. The selection of the appropriate system depends on factors such as the type of product, storage volume, and order fulfillment requirements.
- Types of Pallet Racking Systems:
- Selective Racking: This is the most common type, providing direct access to each pallet. It’s ideal for warehouses with a variety of product types and frequent order picking.
- Drive-In/Drive-Thru Racking: This system allows forklifts to drive directly into the racking, maximizing space utilization. It is best suited for storing large quantities of the same product. Drive-thru racking allows access from both sides.
- Push-Back Racking: This system uses a series of carts that are pushed back as new pallets are loaded, allowing for high-density storage.
- Pallet Flow Racking: This system utilizes gravity to move pallets from the loading side to the picking side, facilitating FIFO inventory management.
- Very Narrow Aisle (VNA) Racking: This system uses narrow aisles to maximize space utilization, requiring specialized forklifts.
- Space Utilization: Pallet racking systems significantly increase storage density compared to floor stacking. By utilizing vertical space, warehouses can store more products in the same footprint.
- Accessibility: Racking systems provide easy access to individual pallets, improving order picking efficiency and reducing handling time. Selective racking, for instance, allows direct access to every pallet, while drive-in racking requires more maneuvering.
- Safety: Proper racking systems enhance warehouse safety by providing a stable and organized storage environment. They reduce the risk of product damage and worker injuries.
- Inventory Management: Racking systems, especially those integrated with WMS, improve inventory tracking and control. This helps in managing FIFO inventory and preventing spoilage.
- Cost Considerations: The initial cost of installing a racking system can be significant. However, the long-term benefits, such as increased storage capacity, improved efficiency, and reduced labor costs, often outweigh the initial investment. Consider the cost of equipment, installation, and ongoing maintenance.
- Example: A large distribution center for frozen foods implemented a pallet flow racking system. This system improved their inventory turnover rate by 15% and reduced labor costs associated with order picking by 10%, leading to significant operational efficiencies.
Transportation and Logistics of Food Pallets
Efficient transportation and logistics are critical for preserving the quality and safety of food products throughout the supply chain. The journey from the producer to the consumer involves numerous logistical challenges, necessitating careful planning and execution to minimize spoilage, maintain temperature control, and ensure timely delivery. This section delves into the various modes of transport, crucial securing techniques, and comparative advantages of different shipping methods for palletized food.
Modes of Transport for Food Pallets
Several modes of transportation are employed to move palletized food products, each with its own set of capabilities and limitations. The choice of transport method depends on factors such as distance, product perishability, and cost considerations.
- Trucks: Road transport is the most common method, offering flexibility and door-to-door delivery. Refrigerated trucks, also known as “reefers,” are essential for transporting temperature-sensitive goods, such as fresh produce, dairy products, and frozen foods. Trucks provide the most direct route, minimizing handling and transit times, which is crucial for perishable items. The use of GPS tracking and temperature monitoring systems allows for real-time visibility and control.
However, trucking can be susceptible to traffic delays and fuel price fluctuations, impacting delivery schedules and costs.
- Trains: Rail transport is a cost-effective option for long-distance hauls, particularly for non-perishable items and bulk commodities. Trains can carry large volumes of palletized food, reducing the cost per unit compared to trucking. Specialized railcars, including refrigerated and climate-controlled cars, are available for temperature-sensitive products. The main disadvantage is the lack of flexibility in terms of routes and delivery points, often requiring a transfer to trucks for the “last mile” delivery.
- Ships: Maritime transport is utilized for international shipments of palletized food. Container ships are equipped to carry refrigerated containers (“reefer containers”) that maintain precise temperature controls throughout the voyage. This mode is suitable for long-distance transport of frozen foods, processed goods, and shelf-stable products. Shipping offers the lowest cost per unit for large volumes but is the slowest mode of transport, and susceptible to delays due to weather or port congestion.
- Air Freight: Air freight is the fastest mode of transport, making it suitable for highly perishable goods and time-sensitive deliveries. While it is the most expensive option, it is frequently used for high-value products, such as fresh seafood, exotic fruits, and pharmaceuticals. The speed of air transport minimizes the risk of spoilage and extends shelf life, but requires careful packaging and handling to withstand the higher altitude and pressure changes.
Pallet Wrapping and Securing Techniques for Transportation
Proper pallet wrapping and securing are essential to protect food products from damage, contamination, and shifting during transit. This is particularly important for ensuring food safety and maintaining the integrity of the packaging.
- Stretch Wrapping: Stretch wrapping involves applying a thin, flexible plastic film around the palletized load. This secures the items, preventing them from shifting during handling and transportation. The film also protects against dust, moisture, and minor impacts. Proper tension and overlap are critical to ensure the load remains stable.
- Shrink Wrapping: Shrink wrapping uses a heat-shrinkable film that is applied loosely around the pallet. Heat is then applied, causing the film to shrink tightly around the load. This creates a secure and weather-resistant package. Shrink wrapping is often used for products that require extra protection from the elements or those that are stored outdoors.
- Strapping: Strapping involves using strong bands made of plastic or steel to secure the load to the pallet. Strapping is particularly useful for heavy or irregularly shaped items. It is essential to use the correct type and tension of straps to prevent the load from shifting.
- Edge Protectors: Edge protectors, such as cardboard or plastic corners, are placed on the edges of the palletized load to prevent damage from strapping or wrapping. They also help to distribute the weight evenly.
- Load Restraints: Load restraints, such as nets or straps, are used to prevent the load from shifting during transport. These are especially important for trucks and ships, where movement is more pronounced.
Comparison of Shipping Methods for Palletized Food
The choice of shipping method for palletized food depends on a variety of factors, including the type of product, distance, cost, and time constraints. Each method presents distinct advantages and disadvantages.
Shipping Method | Advantages | Disadvantages | Best Suited For |
---|---|---|---|
Trucking | Flexibility, door-to-door delivery, speed for short distances, real-time tracking. | Susceptible to traffic delays, fuel price fluctuations, limited capacity, higher cost for long distances. | Fresh produce, dairy products, short-haul deliveries, last-mile delivery. |
Rail | Cost-effective for long distances, large capacity, reduced carbon footprint. | Less flexible routes, requires transfer to trucks for final delivery, slower than trucking. | Bulk commodities, non-perishable items, long-distance hauls. |
Shipping | Lowest cost per unit for large volumes, suitable for international transport. | Slowest mode of transport, susceptible to delays, requires specialized equipment (reefer containers). | Frozen foods, processed goods, international trade. |
Air Freight | Fastest mode of transport, ideal for time-sensitive deliveries, minimizes spoilage. | Highest cost, limited capacity, requires specialized handling. | High-value perishables, pharmaceuticals, time-critical deliveries. |
Regulatory Compliance and Standards
The food industry operates under stringent regulations designed to protect consumer health and ensure the safety and integrity of the food supply chain. Pallets, as a critical component of this supply chain, are subject to a range of regulatory requirements and industry standards. Compliance with these standards is essential to prevent contamination, maintain product quality, and avoid costly penalties or recalls.
Key Regulatory Bodies and Standards
Several regulatory bodies and standards play a crucial role in governing the use of pallets in the food industry. Compliance with these regulations is non-negotiable.The primary regulatory bodies include:
- Food and Drug Administration (FDA): In the United States, the FDA is responsible for ensuring the safety of food products. The FDA’s regulations, including those Artikeld in the Food Safety Modernization Act (FSMA), address various aspects of food safety, including the materials used in contact with food. The FDA does not directly regulate pallets but holds food manufacturers responsible for using equipment, including pallets, that do not contaminate food.
- European Food Safety Authority (EFSA): The EFSA provides scientific advice and risk assessments on food safety matters in the European Union. EFSA’s regulations and guidelines influence the standards for materials used in food contact, indirectly affecting pallet requirements.
- Canadian Food Inspection Agency (CFIA): The CFIA enforces food safety regulations in Canada. Similar to the FDA, the CFIA focuses on preventing contamination and ensuring the suitability of materials used in food processing and handling.
- World Health Organization (WHO): The WHO provides international guidelines and recommendations on food safety, including the use of appropriate materials and handling practices. These guidelines inform food safety standards worldwide.
Key standards and certifications include:
- International Plant Protection Convention (IPPC) and ISPM 15: ISPM 15 is an international standard that addresses the treatment of wood packaging material (WPM) used in international trade. The standard mandates heat treatment (HT) or fumigation of wood pallets to eliminate pests like wood-boring insects, which can contaminate food products. Compliance with ISPM 15 is crucial for international shipments. For instance, a food manufacturer exporting products to Australia must ensure its wood pallets meet ISPM 15 standards to prevent the introduction of pests.
- Hazard Analysis and Critical Control Points (HACCP): HACCP is a systematic approach to food safety that identifies and controls hazards. While not specifically a pallet standard, HACCP principles require food manufacturers to assess and mitigate risks associated with all aspects of their operations, including the use of pallets.
- British Retail Consortium (BRC) Global Standard for Food Safety: The BRC standard is a globally recognized food safety standard that covers various aspects of food production and handling. It includes requirements related to the use and maintenance of pallets to prevent contamination.
- Safe Quality Food (SQF) Program: The SQF program is a food safety and quality certification program that requires food businesses to implement rigorous food safety management systems. This includes requirements for pallet management, such as inspection, cleaning, and maintenance.
Importance of Pallet Inspection and Maintenance
Regular pallet inspection and maintenance are critical to ensure compliance with food safety regulations and prevent contamination. This proactive approach helps to minimize risks and maintain product integrity.Pallet inspection should include:
- Visual Inspection: Examining pallets for any signs of damage, such as broken boards, splinters, protruding nails, or evidence of pests.
- Material Assessment: Verifying the pallet material is suitable for food contact and free from harmful chemicals or contaminants.
- Cleanliness Check: Ensuring the pallet is clean and free from debris, dirt, and other contaminants.
Maintenance activities include:
- Cleaning and Sanitization: Regularly cleaning and sanitizing pallets, especially those used in direct contact with food or food packaging. The frequency of cleaning depends on the specific food product and the environment.
- Repair and Replacement: Promptly repairing or replacing damaged pallets to prevent further deterioration and potential contamination.
- Storage Practices: Storing pallets in a clean, dry environment to prevent the growth of mold, mildew, and pest infestations.
For example, a food processing plant that handles raw meat products should have a rigorous pallet inspection and cleaning program in place. Pallets should be inspected daily, cleaned after each use, and repaired or replaced if any damage is detected. This minimizes the risk of cross-contamination.
Role of Traceability and Tracking Systems
Traceability and tracking systems are increasingly important in the food industry to ensure product safety and facilitate efficient recalls if necessary. These systems allow for the tracking of pallets throughout the supply chain, providing valuable information for compliance and risk management.Key elements of traceability and tracking systems include:
- Pallet Identification: Assigning unique identifiers to each pallet, such as bar codes, RFID tags, or QR codes.
- Data Capture: Recording data about each pallet’s journey, including its origin, handling, storage, and transportation. This data can be captured through scanning bar codes, using RFID readers, or manually entering information into a tracking system.
- Data Management: Storing and managing pallet data in a centralized system, allowing for easy access and analysis.
- Recall Management: Using traceability data to quickly identify and isolate pallets associated with a potential food safety issue.
An example of a traceability system is a dairy company that uses RFID tags on its pallets to track the movement of milk products from the farm to the store. If a food safety issue is identified, the company can use the RFID data to quickly locate and recall the affected products, minimizing the impact on consumers and the business.
Another example is a produce distributor that uses a pallet tracking system to monitor the temperature of pallets of fresh produce during transportation. This allows them to ensure the produce stays within the required temperature range, preserving its quality and safety.
Sustainable Practices for Food Pallets
The food industry faces increasing pressure to adopt sustainable practices, and pallet management is no exception. From the environmental impact of materials to the efficiency of handling, every aspect of the supply chain is scrutinized. Embracing sustainability in pallet usage not only benefits the planet but also enhances brand reputation and often leads to cost savings.
Recycling and Reuse Programs
Implementing recycling and reuse programs is crucial for minimizing waste and extending the lifespan of pallets. Effective programs require careful planning and execution, involving strategic partnerships and robust tracking systems.
- Pallet Inspection and Repair: Before reuse, pallets must undergo thorough inspection to assess their structural integrity. Damaged pallets are repaired, which can include replacing broken boards, reinforcing joints, and addressing other wear and tear. This extends the life of the pallet and reduces the need for new materials.
- Pallet Pooling Systems: Pooling systems, where pallets are shared among multiple users, are inherently sustainable. These systems facilitate the tracking, repair, and reuse of pallets, reducing the overall demand for new pallets and the associated environmental impact.
- Closed-Loop Recycling: Closed-loop recycling programs ensure that pallets are recycled into new pallets at the end of their useful life. This creates a circular economy, minimizing waste and conserving resources. For example, CHEP, a global pallet pooling company, operates a closed-loop system where damaged pallets are recycled into new ones.
- Material Recovery Facilities (MRFs): MRFs play a crucial role in processing and sorting discarded pallets. These facilities separate different materials, such as wood, plastic, and metal, for recycling or repurposing. This process reduces landfill waste and recovers valuable resources.
Environmental Impact of Different Pallet Materials
The choice of pallet material significantly impacts the environmental footprint of food supply chains. Evaluating the lifecycle of each material, from sourcing to disposal, is essential for making informed decisions.
- Wood Pallets: Wood pallets are a common choice, but their sustainability depends on the sourcing of timber and the practices used in their production. Sustainably sourced wood, such as that certified by the Forest Stewardship Council (FSC), minimizes deforestation and promotes responsible forest management.
- Plastic Pallets: Plastic pallets can be made from recycled materials and are durable, which can contribute to a longer lifespan and reduced waste. However, the production of plastic often relies on fossil fuels, and the disposal of plastic pallets can pose environmental challenges if not properly managed.
- Composite Pallets: Composite pallets, made from a combination of materials like recycled plastic and wood fibers, offer a balance of performance and sustainability. These pallets can reduce reliance on virgin materials and provide a durable, long-lasting solution.
- Metal Pallets: Metal pallets are highly durable and can be fully recycled. However, their production requires significant energy, and the potential for corrosion can impact their lifespan.
Strategies for Minimizing Waste and Promoting Eco-Friendly Pallet Management
Beyond material selection and reuse programs, several strategies can be employed to minimize waste and promote sustainable pallet management throughout the food supply chain.
- Pallet Design Optimization: Designing pallets for maximum durability and longevity reduces the frequency of replacement. Features like reinforced corners, robust deckboards, and proper construction techniques contribute to extended lifespan.
- Efficient Pallet Handling: Implementing efficient handling practices, such as using forklifts with proper maintenance and training, minimizes damage to pallets. Damage during handling is a major contributor to pallet waste.
- Pallet Tracking Systems: Using tracking systems, such as RFID tags or GPS, helps monitor pallet movements and ensures that pallets are returned to the appropriate locations for reuse or recycling. This reduces the risk of pallets being lost or abandoned.
- Supplier Collaboration: Working with suppliers who prioritize sustainable practices and offer eco-friendly pallet options is crucial. This collaborative approach fosters a shared commitment to environmental responsibility.
- Lifecycle Assessments (LCAs): Conducting LCAs helps businesses understand the environmental impact of their pallet choices throughout their entire lifecycle, from raw material extraction to end-of-life disposal. This data can inform decisions about material selection, handling practices, and recycling programs.
- Regulatory Compliance and Incentives: Adhering to relevant environmental regulations and taking advantage of any available incentives, such as tax credits or rebates for using recycled materials, can further support sustainable pallet management efforts.
Technology and Innovation in Pallet Management
The food industry is undergoing a technological transformation, with pallet management at the forefront of this shift. Integrating technology enhances efficiency, reduces waste, and improves food safety across the supply chain. This evolution involves tracking systems, advanced pallet designs, and automation, ultimately streamlining operations from origin to consumer.
Use of Technology in Pallet Tracking and Management Systems
Modern pallet management relies heavily on technology to track and monitor pallets throughout their lifecycle. This technology provides real-time visibility, optimizes resource allocation, and reduces losses.
- Radio-Frequency Identification (RFID) Technology: RFID tags, embedded within or attached to pallets, transmit data wirelessly to readers. This allows for automated tracking of pallet location, contents, and condition. RFID systems can be used to track pallets in warehouses, distribution centers, and during transportation. For example, a major grocery chain implemented RFID in its distribution network, reducing pallet loss by 20% and improving inventory accuracy.
- Global Positioning System (GPS) Tracking: GPS devices, integrated into pallets, provide precise location data. This is particularly useful for tracking pallets during long-haul transportation. This technology is used to monitor the location of perishable goods and ensure timely delivery.
- Barcode Scanning Systems: Barcodes, traditionally used for inventory management, are still widely used for pallet identification. They provide a cost-effective solution for tracking pallets, especially in smaller operations. Barcode systems are commonly used at loading docks and receiving areas to record pallet movements.
- Data Analytics and Management Software: Specialized software platforms collect and analyze data from various tracking systems. These platforms provide insights into pallet utilization, performance, and potential issues. This data can be used to optimize pallet pool size, reduce turnaround times, and identify areas for improvement.
Examples of Innovative Pallet Designs and Materials
The evolution of pallet design focuses on improving durability, sustainability, and hygiene. This includes exploring alternative materials and innovative designs.
- Plastic Pallets: Plastic pallets are increasingly popular due to their durability, sanitation, and resistance to moisture and pests. They are often used in food processing and pharmaceutical industries. They are easy to clean and can be sanitized, reducing the risk of contamination.
- Composite Pallets: Composite pallets are made from a combination of materials, such as recycled plastic and wood fibers. They offer a balance of strength, durability, and sustainability. Composite pallets are designed to be lightweight, reducing transportation costs.
- Smart Pallets: Smart pallets incorporate sensors and tracking devices to monitor temperature, humidity, and impact during transit. These pallets provide real-time data on the condition of goods, helping to prevent spoilage and damage. They are commonly used for transporting temperature-sensitive products.
- Lightweight Pallets: Lightweight pallets are designed to reduce transportation costs and improve handling efficiency. These are often made from composite materials or engineered wood. They also decrease fuel consumption during transportation.
Potential of Automation and Robotics in Pallet Handling and Distribution
Automation and robotics are transforming pallet handling and distribution processes, leading to increased efficiency and reduced labor costs.
- Automated Guided Vehicles (AGVs): AGVs are driverless vehicles that transport pallets within warehouses and distribution centers. They are programmed to follow specific routes and can handle a variety of tasks, such as moving pallets between storage locations and loading docks. AGVs can operate 24/7, improving productivity.
- Robotic Palletizers and Depalletizers: Robots are used to automatically stack and unstack pallets. These systems can handle a high volume of pallets, reducing the need for manual labor and increasing throughput. Robotic systems can be programmed to handle various pallet sizes and product types.
- Automated Storage and Retrieval Systems (AS/RS): AS/RS are automated systems that store and retrieve pallets from high-density storage areas. These systems optimize space utilization and improve inventory management. AS/RS are often used in cold storage facilities to maintain temperature control.
- Automated Pallet Inspection and Repair: Automated systems can inspect pallets for damage and perform repairs. This reduces the need for manual inspection and ensures that pallets are in good condition. These systems use sensors and cameras to identify and repair damaged pallets.
Closing Notes
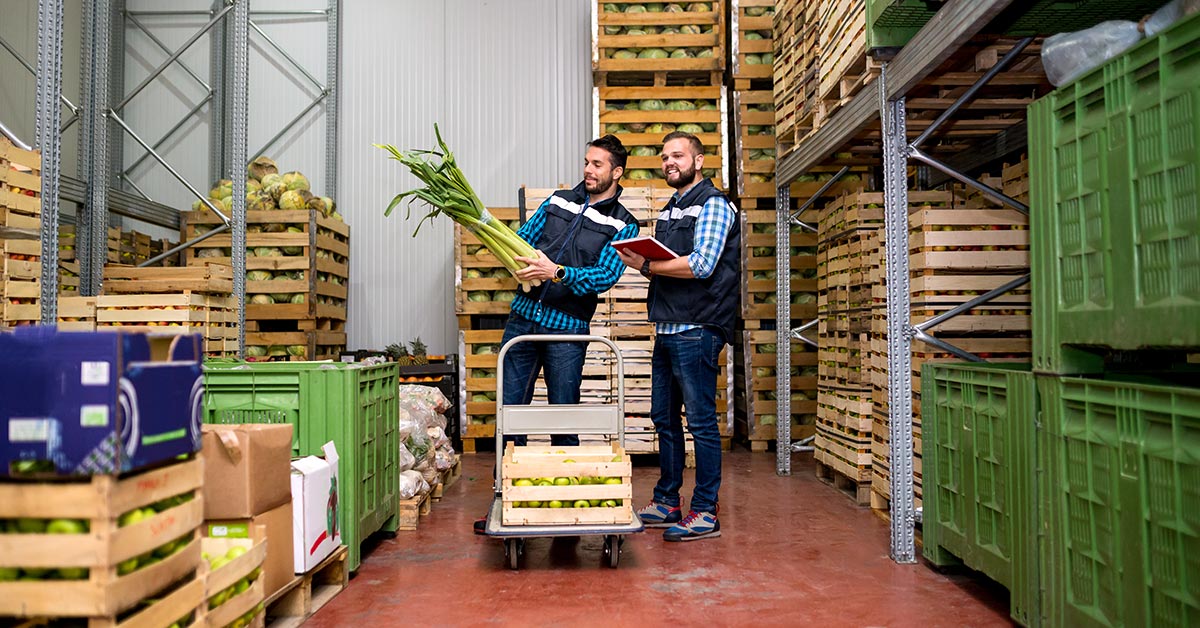
In conclusion, the journey of pallets of food is a testament to the intricate interplay of logistics, safety, and sustainability. By understanding the nuances of pallet selection, handling, and management, we can contribute to a more efficient, resilient, and environmentally responsible food supply chain. The continuous evolution of technology and practices in this domain promises further advancements in food security and resource optimization, underscoring the ongoing importance of this essential component of the global economy.