Food grade plastic sheet, a seemingly simple material, is actually a cornerstone of modern food safety and preservation. It’s the unsung hero, the invisible shield protecting our meals from contamination and extending their shelf life. From the humble sandwich bag to complex food processing machinery, these sheets play a critical role, often without us even realizing their presence.
This isn’t just about wrapping leftovers; it’s a story of material science, rigorous regulations, and the ongoing quest for sustainability. We’ll explore the different types of plastics, the manufacturing processes, and the crucial role these sheets play in ensuring the food we eat is safe, fresh, and delicious. Get ready for a journey through the world of food grade plastic sheets, a world that’s more complex and fascinating than you might imagine.
Introduction to Food Grade Plastic Sheet
Ah, the unsung hero of the culinary world! Food grade plastic sheets are, in essence, the meticulously crafted guardians of our grub, the silent sentinels ensuring our sustenance remains safe and sound. They are the unsung champions, working tirelessly behind the scenes to keep our food fresh, uncontaminated, and ready to grace our plates.These sheets are specifically designed to come into direct contact with food, meaning they’re formulated to be non-toxic, odorless, and, most importantly, to not leach harmful chemicals into the edibles they embrace.
Think of them as the culinary equivalent of a highly trained bodyguard, protecting our precious provisions from all sorts of unsavory characters (and contaminants!).
Definition and Purpose
Food grade plastic sheets are specialized plastic materials manufactured to meet stringent regulatory standards set by organizations like the FDA (Food and Drug Administration) in the United States and similar bodies worldwide. Their primary purpose is to provide a safe and hygienic barrier between food products and their surroundings, safeguarding against contamination, preserving freshness, and extending shelf life.
Common Applications
The versatility of food grade plastic sheets is truly remarkable, making them indispensable in a wide array of applications. They’re like the Swiss Army knife of the food industry, tackling a multitude of tasks with aplomb.
- Food Packaging: This is perhaps the most ubiquitous application. From wrapping sandwiches to forming the containers for ready-made meals, food grade plastic sheets keep our food neatly contained and protected. Imagine a world without the convenience of a pre-packaged salad!
- Food Processing Equipment: These sheets are often used in the construction of cutting boards, conveyor belts, and other equipment that comes into contact with food during processing. Their smooth surfaces and resistance to bacteria make them ideal for maintaining hygiene in food processing plants.
- Food Storage Containers: Tupperware, food storage bags, and other containers that we use in our kitchens and refrigerators are often made from food grade plastic sheets. They help us store leftovers, keep ingredients fresh, and reduce food waste.
- Display Cases: Delicatessens and bakeries frequently utilize food grade plastic sheets to create clear, attractive display cases for their products. This allows customers to see the delectable goods while maintaining a sanitary environment.
Benefits Over Alternative Materials
Food grade plastic sheets offer several advantages over alternative materials, making them a preferred choice for food handling. They’re the champions of convenience, durability, and hygiene.
- Durability and Flexibility: Unlike glass, which can shatter, or certain metals that can dent, food grade plastic sheets are generally quite robust and flexible. They can withstand the rigors of transportation, storage, and repeated use without compromising their integrity.
- Lightweight Nature: This characteristic makes them easy to handle, transport, and store. This is particularly advantageous in food packaging, where reducing weight can lead to cost savings in shipping.
- Resistance to Chemicals and Corrosion: Food grade plastics are often resistant to a wide range of chemicals and corrosive substances that might be present in food or cleaning agents. This ensures they remain safe and effective over time.
- Cost-Effectiveness: Compared to materials like stainless steel or specialized glass, food grade plastic sheets are often more economical to produce and purchase, making them a practical choice for many applications.
- Excellent Barrier Properties: Many food grade plastics provide excellent barriers against moisture, oxygen, and other gases, which helps to preserve the freshness and extend the shelf life of food products. This is crucial for reducing food waste and ensuring product quality.
Food grade plastic sheets are not just about convenience; they are about safeguarding public health and ensuring the integrity of our food supply.
Properties and Characteristics
Ah, the secret sauce! Now we delve into the nitty-gritty of what makes these food-grade plastic sheets the superheroes of the culinary world. We’ll explore their physical prowess, chemical resilience, and how they behave under the influence of heat – because let’s face it, even superheroes have their kryptonite. Buckle up, buttercups!
Physical Properties
These sheets aren’t just pretty faces; they’ve got the goods. Their physical properties are carefully engineered to meet the demands of food handling. Let’s take a peek under the hood:The flexibility of food-grade plastic sheets is a crucial attribute. This allows for easy shaping and molding during manufacturing processes, adapting to various food packaging needs. Their flexibility contributes to the sheets’ resistance to cracking or breaking under stress, ensuring the integrity of the food product.
- Flexibility: Think of it as the plastic sheet’s ability to bend without breaking. This is critical for applications like flexible packaging (think cling film or pouches). The level of flexibility varies depending on the type of plastic. For example, polyethylene (PE) is known for its excellent flexibility, making it ideal for squeeze bottles and flexible containers.
- Strength: These sheets need to be tough enough to withstand handling, stacking, and the general rough and tumble of the food supply chain. The tensile strength (the ability to resist being pulled apart) is a key factor. Polypropylene (PP) offers a good balance of strength and flexibility, often used in containers for yogurt or margarine.
- Clarity: Transparency is a major player, allowing consumers to see the deliciousness within. Clarity is especially important for products like ready-to-eat salads or pre-cut fruits, showcasing their freshness and appeal. Different plastics offer varying degrees of clarity. Polyethylene terephthalate (PET) is renowned for its exceptional clarity, making it the go-to choice for water bottles and clear food containers.
Chemical Resistance
Food-grade plastic sheets are designed to be chemical-resistant, but they’re not invincible. They need to withstand exposure to a variety of substances without degrading or leaching harmful chemicals into the food.
Obtain access to breakfast food truck names to private resources that are additional.
- Resistance to Food Acids: Many foods are naturally acidic (think tomatoes, citrus fruits, and vinegar). Food-grade plastics must resist these acids to prevent degradation and maintain the food’s quality. For example, PET is known for its good resistance to a wide range of acids, making it suitable for storing acidic beverages.
- Resistance to Solvents: Solvents, such as those used in cleaning products or certain food additives, can potentially interact with the plastic. The resistance of the plastic to these solvents is crucial for maintaining its integrity and preventing contamination. The choice of plastic depends on the specific solvents involved. Polypropylene (PP) offers good resistance to many solvents, making it suitable for food packaging exposed to cleaning agents.
Temperature Impact
Temperature is a major player in the performance of food-grade plastic sheets. Heat can cause them to soften, warp, or even melt, while cold temperatures can make them brittle. The specific temperature range a plastic can withstand is crucial for its application.The glass transition temperature (Tg) is the temperature at which a polymer transitions from a hard, glassy state to a rubbery state.
This is a critical property to consider.
- High Temperatures: The ability of the plastic to withstand high temperatures is essential for applications like microwavable containers or hot-fill packaging. Polypropylene (PP) has a relatively high melting point and can withstand temperatures up to 100°C (212°F) for short periods, making it suitable for microwaving. However, it’s essential to check the specific product’s instructions, as not all PP containers are microwave-safe.
- Low Temperatures: Food storage in freezers requires plastics that remain flexible and do not become brittle at low temperatures. Polyethylene (PE) is often used for freezer bags and containers because it retains its flexibility even at very low temperatures.
- Thermal Expansion and Contraction: Plastics expand when heated and contract when cooled. This can affect the dimensional stability of the packaging. Understanding these properties is critical for ensuring the packaging maintains its seal and protects the food product.
Applications in Food Industry
Food grade plastic sheets, the unsung heroes of the culinary world, play a surprisingly diverse role in ensuring our food remains safe, fresh, and readily available. From the farm to our forks, these versatile materials contribute significantly to the efficiency and safety of food production, processing, packaging, and distribution. They are like the silent guardians of our groceries, working tirelessly behind the scenes.
The following sections will explore the myriad ways food grade plastic sheets are employed in the food industry, highlighting their specific applications, the materials used, and the benefits they bring to the table (pun intended!).
Food Grade Plastic Sheet Applications
Food grade plastic sheets are indispensable in a variety of applications within the food industry. Their versatility and ability to meet stringent safety requirements make them a preferred choice for numerous purposes. The following table details some of the most common applications, their descriptions, the materials typically employed, and the associated benefits. Consider it your culinary cheat sheet!
Application | Description | Material Used | Benefits |
---|---|---|---|
Food Packaging | Used to create containers, trays, films, and wraps to protect food products from contamination, spoilage, and physical damage during storage, transportation, and display. | Polyethylene (PE), Polypropylene (PP), Polyethylene Terephthalate (PET), Polyvinyl Chloride (PVC) | Extended shelf life, barrier protection against moisture and gases, enhanced product visibility, tamper evidence, lightweight, and cost-effective. |
Food Processing Equipment | Components in machinery used for food preparation, handling, and processing, such as conveyor belts, cutting boards, and food contact surfaces. | High-Density Polyethylene (HDPE), Polycarbonate (PC), Polyamide (PA) | Durable, resistant to wear and tear, easy to clean, non-reactive with food, reduce friction, and maintain hygiene. |
Food Storage Containers | Manufacture of containers, tubs, and bins used to store raw materials, ingredients, and finished food products in warehouses, restaurants, and homes. | Polypropylene (PP), Polycarbonate (PC) | Stackable, reusable, airtight seals, maintain food freshness, and resist temperature variations. |
Food Service Items | Production of disposable items like plates, cups, cutlery, and food containers used in restaurants, catering, and takeout services. | Polystyrene (PS), Polypropylene (PP), Polylactic Acid (PLA) | Convenient, lightweight, cost-effective, and designed for single-use, ensuring hygiene. Biodegradable options available. |
Dairy Products Packaging | Production of packaging for milk, yogurt, cheese, and other dairy products. | High-Density Polyethylene (HDPE), Polypropylene (PP), Polyethylene Terephthalate (PET) | Maintains freshness, provides a barrier against light and oxygen, and is recyclable. |
Meat and Poultry Packaging | Creation of trays, films, and vacuum packaging for meat and poultry products to extend shelf life and preserve quality. | Polyethylene (PE), Polyvinyl Chloride (PVC), Ethylene Vinyl Alcohol Copolymer (EVOH) | Prevents spoilage, preserves color and texture, and reduces the risk of contamination. |
Bakery Product Packaging | Packaging for bread, pastries, and other baked goods. | Polypropylene (PP), Polyethylene (PE), Oriented Polypropylene (OPP) | Protects against moisture, maintains freshness, and provides a clear view of the product. |
Food Grade Plastic Sheets in Food Packaging
Food packaging is where food grade plastic sheets truly shine, acting as the primary guardians of our edibles. From simple wraps to complex containers, these sheets provide a crucial barrier against external elements, ensuring food safety and extending shelf life. Let’s delve into some specific examples.
Food grade plastic sheets are engineered to offer a variety of benefits, including:
- Barrier Properties: Preventing the passage of oxygen, moisture, and other gases that can cause spoilage.
- Protection: Shielding food from physical damage during handling and transportation.
- Shelf Life Extension: Significantly increasing the time food remains safe and palatable.
- Product Visibility: Allowing consumers to see the product, influencing purchasing decisions.
- Tamper Evidence: Providing a clear indication if a package has been opened or compromised.
Specific Examples:
- Fresh Produce Packaging: Thin, transparent films made from polyethylene (PE) or polypropylene (PP) are used to wrap fruits and vegetables. This packaging helps to maintain the produce’s freshness by controlling the exchange of gases, such as carbon dioxide and oxygen. For example, consider the pre-packaged salad mixes in supermarkets. These often use a modified atmosphere packaging (MAP) system, where the gas composition inside the package is adjusted to slow down the ripening process and extend the shelf life.
- Meat Packaging: Vacuum-sealed packaging, often made from multilayer films including polyethylene (PE) and ethylene vinyl alcohol copolymer (EVOH), is used for meat products. Vacuum sealing removes oxygen, which inhibits the growth of spoilage-causing bacteria and preserves the meat’s color and flavor. This is why you see meat products with a long shelf life in the refrigerated section of the supermarket.
- Dairy Product Containers: Milk jugs and yogurt containers are typically made from high-density polyethylene (HDPE) or polypropylene (PP). These materials are chosen for their durability, resistance to moisture, and ability to withstand the temperature fluctuations during storage and transportation. The opaque nature of HDPE also helps to protect the milk from light, which can degrade its quality.
- Ready-to-Eat Meal Trays: Microwavable meal trays are often made from polypropylene (PP). PP’s high melting point and resistance to chemical reactions make it ideal for this application. These trays allow consumers to heat their meals directly in the packaging, offering convenience and reducing the need for extra dishes.
Food Grade Plastic Sheets in Food Processing Equipment and Machinery
Beyond packaging, food grade plastic sheets play a vital role in the very machinery that processes our food. These sheets are utilized in the construction of equipment, ensuring food safety, hygiene, and efficient operation. They are like the workhorses of the food processing world, quietly contributing to the production of safe and high-quality food products.
Key applications in food processing equipment include:
- Conveyor Belts: Made from materials like polyurethane or polyethylene, these belts transport food products through various stages of processing, from raw ingredients to finished goods. Their smooth surfaces and resistance to wear and tear make them ideal for this demanding application.
- Cutting Boards: High-density polyethylene (HDPE) is a common choice for cutting boards used in food preparation areas. HDPE is durable, easy to clean, and resistant to bacteria growth, ensuring food safety. The smooth, non-porous surface also minimizes the risk of cross-contamination.
- Food Contact Surfaces: Plastic sheets are used to line surfaces that come into direct contact with food, such as in mixing bowls, storage containers, and processing vats. These surfaces are made from food-grade materials like polypropylene (PP) or polycarbonate (PC), which are non-reactive and do not impart any taste or odor to the food.
- Machine Components: Various machine components, such as gears, bearings, and guides, are made from food-grade plastics. These components are selected for their durability, resistance to corrosion, and ability to withstand the harsh conditions of a food processing environment.
The benefits of using food grade plastic sheets in food processing equipment are manifold:
- Hygiene: Non-porous surfaces prevent bacteria from adhering and multiplying, ensuring food safety.
- Durability: Resistance to wear and tear, chemicals, and temperature fluctuations extends the lifespan of the equipment.
- Ease of Cleaning: Smooth surfaces are easy to clean and sanitize, reducing downtime and maintenance costs.
- Cost-Effectiveness: Plastics can be more affordable than alternative materials, such as stainless steel, without compromising performance.
Types of Food Grade Plastic Sheets
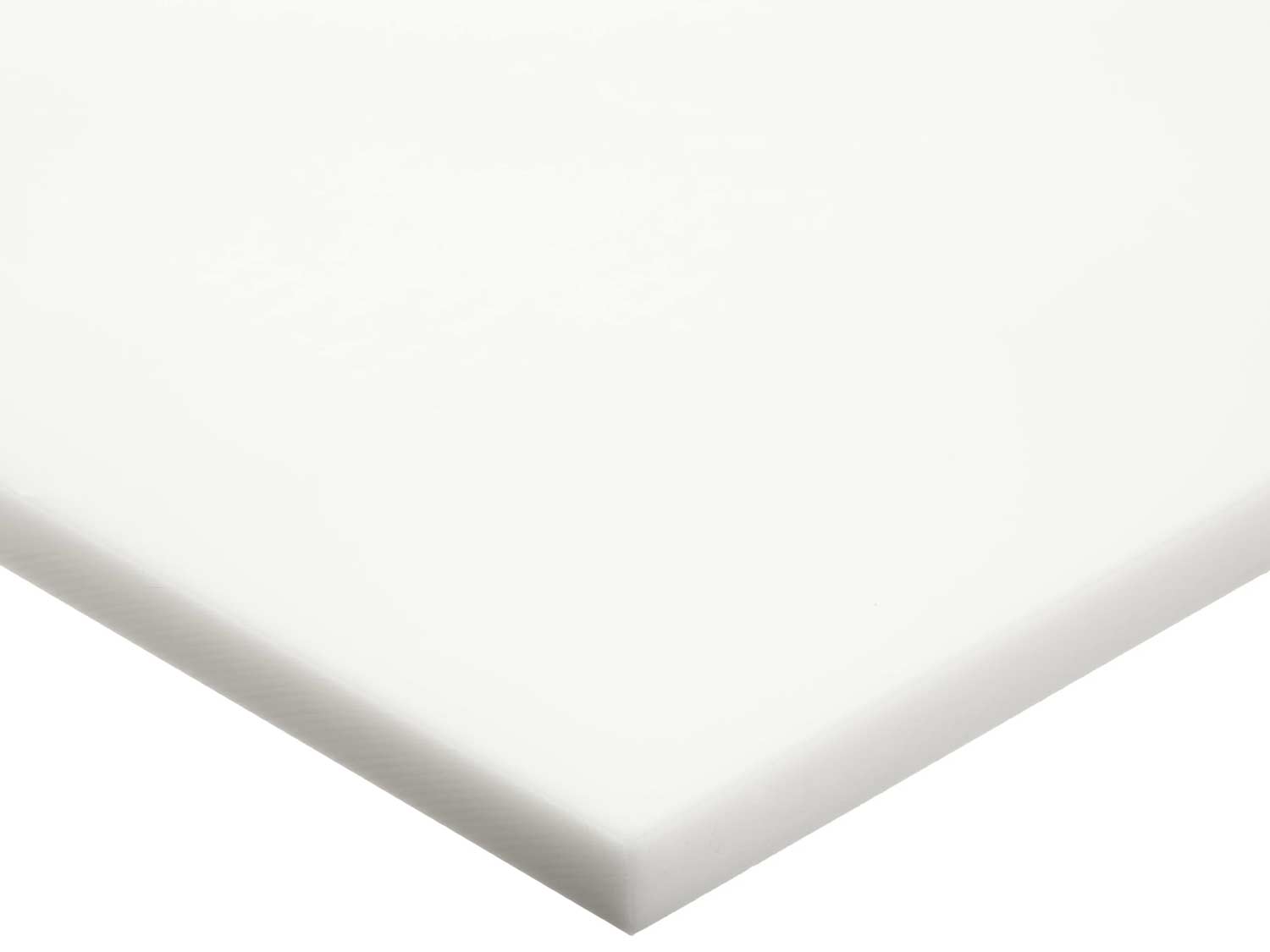
Having explored the realm of food grade plastic sheets, from their fundamental properties to their diverse applications, it’s time to delve into the specific players in this plastic pantheon. These aren’t your run-of-the-mill materials; they’re the champions, the all-stars, the ones that keep our food safe and sound. Understanding their individual strengths and weaknesses is crucial for choosing the right sheet for the job, ensuring both food safety and optimal performance.
Let’s meet the cast of characters.
Food Grade Plastic Sheet Varieties
A variety of food grade plastic sheets are available, each boasting unique characteristics that cater to specific needs within the food industry. From the workhorse PET to the versatile PVC, the options are plentiful. Here’s a quick rundown of some of the most popular types:
- PET (Polyethylene Terephthalate): A widely used thermoplastic polymer known for its excellent clarity, strength, and barrier properties.
- PVC (Polyvinyl Chloride): A versatile plastic known for its durability, resistance to chemicals, and cost-effectiveness.
- Polycarbonate (PC): A strong, transparent plastic known for its impact resistance and ability to withstand high temperatures.
- Polypropylene (PP): A robust plastic known for its high melting point and resistance to chemicals.
- High-Density Polyethylene (HDPE): A durable plastic known for its strength, rigidity, and resistance to moisture.
- Low-Density Polyethylene (LDPE): A flexible plastic known for its transparency, flexibility, and good moisture barrier properties.
Material Properties, Applications, and Advantages
Each type of food grade plastic sheet brings its own set of advantages to the table. The choice of material depends heavily on the specific application and the desired properties. To illustrate this, let’s examine a comparison table outlining the key characteristics of each:
Material | Properties | Applications | Advantages |
---|---|---|---|
PET (Polyethylene Terephthalate) | Excellent clarity, good barrier properties (oxygen, carbon dioxide, water), high tensile strength, recyclable. | Bottles for beverages (water, soft drinks), food containers (salads, fruits), blister packs, trays. | Lightweight, shatter-resistant, maintains freshness, widely recyclable, and offers good design flexibility. For example, a PET bottle can maintain its structural integrity even when dropped, minimizing the risk of contamination. |
PVC (Polyvinyl Chloride) | Durable, rigid, good chemical resistance, can be formulated for flexibility, cost-effective. | Cling film, food packaging trays, meat packaging, blister packs. | Excellent barrier to grease and oils, protects food from spoilage, offers good transparency for product visibility, and is relatively inexpensive to produce. For example, PVC cling film tightly seals food items, preventing air exposure and extending shelf life. |
Polycarbonate (PC) | High impact resistance, transparent, can withstand high temperatures, excellent dimensional stability. | Reusable water bottles, food storage containers, microwave-safe containers, baby bottles. | Durable and reusable, resists cracking and shattering, can be sterilized, and safe for use in microwaves. For instance, polycarbonate baby bottles can withstand repeated sterilization cycles without degrading. |
Polypropylene (PP) | High melting point, good chemical resistance, can be sterilized, flexible, and recyclable. | Food containers (yogurt tubs, margarine tubs), microwave-safe containers, bottle caps, food packaging film. | Resists heat and chemicals, microwave safe, maintains food integrity, and is widely recyclable. For example, a polypropylene container can be safely heated in a microwave without leaching harmful chemicals into the food. |
High-Density Polyethylene (HDPE) | High strength-to-density ratio, good chemical resistance, opaque or translucent, recyclable. | Milk jugs, juice bottles, food storage containers, cutting boards. | Durable, resistant to moisture, cost-effective, and widely recycled. For example, HDPE milk jugs are designed to withstand handling and transportation, maintaining the integrity of the product. |
Low-Density Polyethylene (LDPE) | Flexible, good moisture barrier, transparent, and relatively inexpensive. | Plastic bags (grocery bags, produce bags), squeezable bottles, food wrap. | Flexible and lightweight, excellent moisture barrier, protects food from contamination. For example, LDPE plastic bags are ideal for storing and transporting fresh produce, keeping them fresh and preventing spoilage. |
Selection and Usage: Food Grade Plastic Sheet
Choosing the right food grade plastic sheet is like picking the perfect outfit for a party – you want something that looks good, fits well, and doesn’t make you sick. In this section, we’ll explore the essential factors to consider, ensuring your plastic sheet performs its job flawlessly while keeping food safe and sound. We’ll also delve into the proper care and handling, guaranteeing longevity and preventing any unwanted “plastic-y” surprises in your culinary creations.
Factors in Application Selection
Selecting the appropriate food grade plastic sheet demands careful consideration of several key factors. These factors ensure that the chosen material is both fit-for-purpose and maintains the integrity of the food it comes into contact with. Failing to consider these could lead to a culinary disaster, or worse, a health hazard.
- Food Type: Different plastics react differently to various food types. For example, high-fat foods may cause certain plastics to degrade more quickly. Consider the acidity, oil content, and temperature of the food.
- Temperature Resistance: The sheet’s ability to withstand high or low temperatures is critical. Will it be used in a freezer, oven, or microwave? Ensure the plastic’s temperature range aligns with the application. Using the wrong plastic in a hot oven could lead to melting, deformation, and potentially harmful chemical leaching into the food.
- Durability and Physical Properties: The application may demand varying levels of impact resistance, flexibility, and tear strength. Consider the physical stresses the sheet will endure, such as cutting, handling, and storage.
- Chemical Compatibility: Ensure the plastic is compatible with any cleaning agents or food additives it may encounter. Some chemicals can degrade certain plastics, leading to contamination. Always consult a compatibility chart.
- Regulatory Compliance: Confirm that the plastic sheet meets all relevant food contact regulations, such as those established by the FDA (Food and Drug Administration) in the United States or the EFSA (European Food Safety Authority) in Europe. These regulations set standards for the safety of materials used in contact with food.
- Cost-Effectiveness: Balance the material’s performance characteristics with its cost. Sometimes, a slightly more expensive sheet offers superior performance and longevity, making it a better investment in the long run.
Guidelines for Handling, Storage, and Cleaning
Proper handling, storage, and cleaning are crucial for maintaining the safety and longevity of food grade plastic sheets. Treating these sheets with care minimizes the risk of contamination and ensures they perform as intended. Neglecting these practices can lead to a decline in the sheet’s properties, potentially compromising food safety.
- Handling: Always handle sheets with clean hands and avoid dragging them across surfaces that could contaminate them. Prevent scratches and abrasions, which can harbor bacteria.
- Storage: Store sheets in a clean, dry environment, away from direct sunlight and extreme temperatures. Sunlight can degrade some plastics, and temperature fluctuations can cause warping. Stacking sheets correctly prevents bending and damage. Consider using a dedicated storage rack or cabinet.
- Cleaning: Clean sheets thoroughly after each use. Use appropriate cleaning agents recommended by the manufacturer. Avoid abrasive cleaners or scrub brushes that could scratch the surface. Rinse thoroughly with clean water to remove all traces of cleaning agents.
- Inspection: Regularly inspect sheets for any signs of damage, such as cracks, scratches, or discoloration. Discard damaged sheets immediately, as they may harbor bacteria or leach harmful chemicals.
- Drying: Allow sheets to air dry completely or pat them dry with a clean, lint-free cloth. Ensure no moisture remains, as this can promote bacterial growth.
Best Practices for Longevity and Safety
Implementing best practices is vital for extending the lifespan and ensuring the safety of food grade plastic sheets. These practices help prevent contamination, maintain the sheet’s integrity, and protect the health of consumers. Following these guidelines provides a proactive approach to ensuring that plastic sheets continue to perform their intended function safely and effectively.
- Regular Cleaning Schedule: Establish a consistent cleaning schedule based on the frequency of use and the type of food being handled. This minimizes the buildup of food residue and potential bacterial growth.
- Proper Cutting Techniques: When using sheets for cutting, use appropriate cutting boards or mats to avoid scratching the surface. If cutting directly on the sheet, use sharp knives and avoid excessive force.
- Temperature Control: Adhere to the recommended temperature ranges for each type of plastic sheet. Avoid exposing sheets to temperatures outside their specified limits, as this can lead to degradation.
- Preventing Cross-Contamination: Use separate sheets for different types of food to prevent cross-contamination. For example, use one sheet for raw meat and another for vegetables. Consider color-coding sheets for different applications.
- Documentation and Traceability: Maintain records of cleaning and inspection schedules, and track the use of each sheet. This documentation aids in identifying potential issues and ensuring compliance with food safety regulations.
- Material Selection Based on Application: Always select the most appropriate food grade plastic sheet for the specific application. For example, use a sheet designed for high-temperature applications if the sheet will be used in an oven.
Sustainability and Environmental Impact
Ah, the elephant in the room (or perhaps, the plastic bag in the ocean): the environmental impact of food-grade plastic sheets. While these sheets are busy keeping our edibles safe and sound, they’re also leaving a footprint on our planet. Let’s delve into the complexities of their lifecycle and explore how we can make things a little greener.
Environmental Impact of Food Grade Plastic Sheets
The environmental impact of food-grade plastic sheets is a multifaceted issue, largely determined by their composition and disposal methods. Traditional plastic sheets, often made from petroleum-based polymers, present significant challenges. They contribute to the depletion of fossil fuels during production, and their disposal poses considerable environmental concerns.
- Resource Depletion: The manufacturing of plastic sheets relies heavily on fossil fuels, a non-renewable resource. Extracting and processing these resources requires significant energy, contributing to greenhouse gas emissions and climate change.
- Waste Generation: The vast majority of traditional plastic sheets are not biodegradable. They can persist in landfills for hundreds of years, slowly breaking down into microplastics that contaminate soil and water.
- Ocean Pollution: Plastic waste, including plastic sheets, often finds its way into oceans, posing a severe threat to marine life. Animals can ingest plastic, become entangled in it, or suffer from chemical exposure.
- Greenhouse Gas Emissions: From production to incineration, the lifecycle of plastic sheets releases greenhouse gases, exacerbating climate change. Incineration, while reducing landfill space, can release harmful pollutants into the atmosphere.
Recyclability of Food Grade Plastic Sheets
Recycling food-grade plastic sheets is often more complicated than it seems. The specific recyclability of a sheet depends heavily on the type of plastic it’s made from.
- Common Plastics and Recyclability:
- PET (Polyethylene Terephthalate): Often used for bottles and some food containers, PET is relatively easy to recycle. However, contamination from food residue can hinder the process.
- HDPE (High-Density Polyethylene): Commonly found in milk jugs and some food packaging, HDPE is also widely recyclable.
- PVC (Polyvinyl Chloride): Used less frequently in food packaging due to environmental concerns, PVC is difficult to recycle.
- LDPE (Low-Density Polyethylene): Used in plastic bags and flexible packaging, LDPE is recyclable in some areas, but often ends up in landfills.
- PP (Polypropylene): Used in containers and lids, PP is increasingly recyclable.
- PS (Polystyrene): Includes Styrofoam; it is difficult to recycle and often not accepted by recycling programs.
- Challenges in Recycling:
- Contamination: Food residue can contaminate plastic sheets, making them unsuitable for recycling. Thorough cleaning is essential but not always practical or cost-effective.
- Sorting: Different types of plastics must be sorted correctly for effective recycling. This process can be complex and expensive.
- Infrastructure: Recycling infrastructure varies significantly by location. Some areas lack the facilities to process certain types of plastics.
Initiatives and Innovations for Sustainable Food Grade Plastic Sheets
The quest for more sustainable food-grade plastic sheets is driving innovation and inspiring new initiatives. Companies and researchers are actively exploring ways to reduce the environmental impact of these materials.
- Material Innovation:
- Bio-based Plastics: Plastics derived from renewable resources like cornstarch, sugarcane, or algae are gaining popularity. These materials can reduce reliance on fossil fuels and, in some cases, are biodegradable or compostable.
- Recycled Content: Using recycled plastic in the production of new sheets reduces the demand for virgin materials and diverts waste from landfills.
- Advanced Recycling Technologies: Chemical recycling methods can break down plastics into their basic building blocks, which can then be used to create new plastics. This can enable the recycling of plastics that are not suitable for mechanical recycling.
- Design and Manufacturing Strategies:
- Reducing Material Usage: Designing packaging that uses less plastic without compromising its protective function is a key focus.
- Optimizing Packaging Design: Simplification of packaging design can make it easier to recycle. Avoiding the use of multiple materials or complex structures can also improve recyclability.
- Improving Recycling Infrastructure: Investment in improved sorting technologies and recycling facilities can increase the rate at which plastic sheets are recycled.
- Collaboration and Policy:
- Extended Producer Responsibility (EPR): EPR schemes make producers responsible for the end-of-life management of their products, encouraging them to design for recyclability and reduce waste.
- Government Regulations: Governments are implementing policies to promote the use of recycled content, ban single-use plastics, and incentivize the development of sustainable alternatives.
- Industry Partnerships: Collaboration between companies, research institutions, and government agencies can accelerate innovation and the adoption of sustainable practices.
Biodegradable and Compostable Alternatives to Traditional Food Grade Plastic Sheets
Biodegradable and compostable alternatives offer a promising solution to the environmental challenges posed by traditional plastic sheets. These materials are designed to break down naturally, reducing waste and minimizing their impact on the environment.
- Biodegradable Plastics:
- Definition: Biodegradable plastics break down into water, carbon dioxide, and biomass under specific environmental conditions, typically in industrial composting facilities.
- Examples: PLA (Polylactic Acid) made from cornstarch, and PHA (Polyhydroxyalkanoates) made from bacteria.
- Limitations: Many biodegradable plastics require specific composting conditions to break down effectively. They may not degrade in a home compost pile or in a landfill.
- Compostable Plastics:
- Definition: Compostable plastics are a subset of biodegradable plastics that break down completely in a composting environment, leaving behind no harmful residues.
- Examples: Some formulations of PLA and other bio-based polymers are compostable.
- Benefits: Compostable plastics can be used to create nutrient-rich compost, which can be used to improve soil health.
- Considerations:
- Source of Origin: The source of the raw material is important. For example, corn-based PLA uses land and resources that might be used for food production.
- Composting Infrastructure: Access to industrial composting facilities is essential for the effective composting of biodegradable and compostable plastics.
- Labeling and Certification: Clear labeling is necessary to ensure that consumers can properly dispose of these materials. Certifications like the BPI (Biodegradable Products Institute) help identify compostable products.
Alternatives to Food Grade Plastic Sheets
Food grade plastic sheets, while incredibly useful, aren’t the only game in town when it comes to keeping our edibles safe and sound. The quest for sustainable and eco-friendly food packaging has spawned a whole host of contenders, each with their own strengths, weaknesses, and quirky personalities. Let’s delve into the fascinating world of alternatives, where cardboard boxes and compostable films compete for the crown of culinary containment.
Alternative Materials Used in Food Handling and Packaging
The world of food packaging offers a smorgasbord of options beyond the familiar plastic sheet. These alternatives range from ancient stalwarts to cutting-edge innovations, each vying for a spot on the supermarket shelf. Here’s a culinary tour of the main players:
- Paper and Cardboard: The classic choice, beloved for its recyclability and versatility. Think cereal boxes, pizza containers, and those charming brown paper bags.
- Glass: Elegant and endlessly recyclable, glass jars and bottles have been a food storage staple for centuries.
- Metal: Cans, tins, and foil offer robust protection and are often favored for long-term food preservation.
- Compostable Plastics: Made from renewable resources like cornstarch or sugarcane, these plastics break down naturally, promising a greener future.
- Bioplastics: A broader category encompassing plastics derived from biomass, offering a range of properties and biodegradability levels.
- Aluminum Foil: Lightweight, malleable, and excellent at heat conduction, aluminum foil is a kitchen essential for wrapping and cooking.
- Wood: Used for crates, pallets, and even disposable cutlery, wood offers a natural and renewable packaging solution.
- Plant-Based Films: Derived from materials like cellulose or seaweed, these films are designed to be biodegradable and compostable.
Comparison of Advantages and Disadvantages of Alternative Materials to Food Grade Plastic Sheets
Choosing the right packaging material is a delicate balancing act, a bit like choosing the perfect wine pairing. Each alternative to food grade plastic sheets comes with its own set of pros and cons, creating a complex decision-making process. Let’s compare the key contenders:
Material | Advantages | Disadvantages |
---|---|---|
Paper and Cardboard |
|
|
Glass |
|
|
Metal |
|
|
Compostable Plastics |
|
|
Bioplastics |
|
|
Aluminum Foil |
|
|
Wood |
|
|
Plant-Based Films |
|
|
Situations Where Alternative Materials Might Be Preferred Over Food Grade Plastic Sheets
There are specific scenarios where alternatives to food grade plastic sheets shine, often driven by environmental concerns, specific food characteristics, or consumer preferences. Here’s a look at some prime examples:
- Environmental Consciousness: In situations where sustainability is paramount, compostable plastics, paper, or glass are often favored. For example, many restaurants are switching from plastic straws and takeout containers to paper alternatives to reduce plastic waste.
- Specific Food Types: Glass jars are ideal for preserving acidic foods like pickles and jams, as they won’t react with the food. Metal cans are crucial for long-term storage of shelf-stable items.
- Branding and Aesthetics: Glass and paper offer a premium look and feel that can enhance a brand’s image. High-end food products often use glass jars or beautifully designed cardboard boxes to convey quality.
- Consumer Preferences: Consumers are increasingly demanding eco-friendly packaging options. Products packaged in compostable materials or easily recyclable containers often gain a competitive advantage in the market.
- Short Shelf Life Products: For items like fresh produce, where shelf life is relatively short, paper or compostable films can be a viable option, minimizing the environmental impact.
- High Temperature Applications: Metal containers and aluminum foil are essential for cooking and baking, offering heat resistance that plastic sheets can’t match.
In short, the best packaging material depends on a multitude of factors, from the food product itself to the intended use and the desired environmental footprint. The right choice is a careful blend of functionality, sustainability, and cost-effectiveness, a culinary equation with many delicious solutions.
Future Trends and Innovations
The food grade plastic sheet industry, much like a perpetually hungry Pac-Man, is constantly evolving, gobbling up new technologies and trends to stay ahead of the curve. From biodegradable materials to smart packaging, the future is looking rather exciting, and hopefully, not too plastic-fantastic (pun intended). We’re about to dive into what’s on the menu for tomorrow’s food packaging.
Emerging Trends in Development and Use
The direction of the food grade plastic sheet industry is being shaped by several key trends, driven by consumer demand, regulatory pressures, and technological advancements. These trends are not just whispers in the wind; they’re powerful currents pushing the industry forward.
- Increased Focus on Sustainability: This is no longer a niche concern; it’s a mainstream movement. The industry is actively pursuing bio-based plastics, recycled content, and compostable materials. This is fueled by consumer awareness of environmental issues and governmental regulations. Think of the EU’s Single-Use Plastics Directive, which is pushing for a reduction in single-use plastics.
- Rise of Smart Packaging: Food grade plastic sheets are becoming more than just containers; they’re becoming interactive. Smart packaging incorporates sensors and indicators to monitor food freshness, temperature, and even tampering. This technology can help reduce food waste and enhance consumer safety. An example would be a color-changing indicator on a meat package that alerts consumers when the product is no longer safe to eat.
- Enhanced Barrier Properties: Manufacturers are continually improving the barrier properties of plastic sheets to extend the shelf life of food products. This involves developing new materials and coatings that protect food from oxygen, moisture, and light. This trend is especially crucial for products like coffee, where freshness is paramount.
- Customization and Personalization: The demand for customized packaging solutions is increasing. This means manufacturers are creating plastic sheets that can be tailored to specific food products, sizes, and branding requirements. Consider the rise of subscription boxes and personalized meal kits, which require highly customized packaging.
- Digital Printing Integration: Digital printing technologies are allowing for more flexible and efficient printing on plastic sheets. This enables short-run production, variable data printing (for personalized labels), and more vibrant and detailed graphics. This is a boon for companies wanting to test new designs or offer limited-edition packaging.
Potential Innovations in Manufacturing and Application, Food grade plastic sheet
Innovation in the food grade plastic sheet arena is happening at a rapid pace. It’s a bit like watching a gourmet chef create a masterpiece, only with polymers instead of pastry.
- Development of Bio-Based Plastics: The holy grail of the industry is to find sustainable alternatives to traditional plastics. This involves using renewable resources like corn starch, sugarcane, and algae to create plastic sheets. Polylactic acid (PLA) and polyhydroxyalkanoates (PHAs) are examples of bio-based polymers gaining traction.
- Advanced Recycling Technologies: Chemical recycling, also known as advanced recycling, is a game-changer. This process breaks down plastic waste into its basic components, allowing it to be reused to create new plastic sheets. This addresses the limitations of mechanical recycling, which can degrade the quality of the plastic over time.
- Nanotechnology in Packaging: Nanomaterials can be incorporated into plastic sheets to enhance their barrier properties, mechanical strength, and antimicrobial activity. This is akin to giving the plastic sheets a superhero upgrade. For example, nanoparticles can be added to the plastic to block oxygen and moisture, extending the shelf life of food products.
- Active Packaging Systems: Active packaging goes beyond simply protecting the food; it interacts with it. This includes incorporating oxygen scavengers, antimicrobial agents, and flavor enhancers into the plastic sheets. For example, packaging that releases carbon dioxide to preserve the freshness of fruits and vegetables.
- 3D Printing for Packaging: 3D printing allows for the creation of customized packaging solutions on demand. This could revolutionize the way food products are packaged, particularly for small-batch production or specialized applications. Imagine being able to print a perfectly fitting container for a unique gourmet product.
The Direction of the Food Grade Plastic Sheet Industry
The future of the food grade plastic sheet industry is trending towards sustainability, smart technologies, and customized solutions. This is not a prediction, but a carefully observed trajectory based on market trends and technological advancements.
- Circular Economy Models: The industry is shifting from a linear “take-make-dispose” model to a circular economy, where materials are reused and recycled. This involves designing products for recyclability, investing in recycling infrastructure, and promoting the use of recycled content.
- Increased Regulatory Scrutiny: Governments worldwide are implementing stricter regulations on plastic packaging, including bans on single-use plastics and requirements for recyclability. This will force the industry to innovate and adapt.
- Collaboration and Partnerships: Collaboration between manufacturers, suppliers, retailers, and research institutions is essential to drive innovation and achieve sustainability goals. This includes sharing knowledge, developing new technologies, and creating industry standards.
- Consumer Education and Engagement: Educating consumers about the importance of sustainable packaging and proper recycling practices is crucial. This includes clear labeling, informative campaigns, and engaging consumers in the circular economy.
- Data-Driven Decision Making: The industry is leveraging data analytics to optimize packaging design, material selection, and supply chain management. This allows for more informed decisions and better resource utilization.
Last Point
So, what have we learned? Food grade plastic sheets are more than just wrappers; they’re a testament to innovation, a response to the demands of a growing population, and a constant evolution in the face of environmental concerns. From the factory floor to your kitchen table, these sheets are working hard to keep our food safe and sound. The future of food grade plastic sheets is bright, promising even more sustainable options and innovative applications.
It’s a story that continues to unfold, a story we all participate in every time we reach for that perfectly packaged meal.