Plastic disposable box food liners are a ubiquitous element of modern food packaging, yet their role and impact often go unnoticed. These seemingly simple sheets of plastic play a crucial role in maintaining food freshness, preventing leaks, and ensuring hygiene across a wide range of industries. From the supermarket deli counter to ready-to-eat meals, understanding the function, materials, and implications of these liners is essential for anyone involved in food production, distribution, or consumption.
This discussion delves into the specifics of plastic disposable box food liners, covering their various types, manufacturing processes, and the advantages and disadvantages they present. We’ll explore the materials used, from common plastics like polypropylene and polyethylene to the additives that enhance their performance. The review will also examine the environmental impact of these liners, including waste generation and potential solutions like recycled materials and alternative options.
The narrative will also touch on regulatory compliance, market trends, and practical considerations for their proper use and disposal, providing a well-rounded perspective on this critical aspect of the food industry.
Plastic Disposable Box Food Liners: An Overview
Plastic disposable box food liners are thin, often flexible sheets or containers designed to be placed inside food packaging, such as boxes, trays, or containers, to hold food items. Their primary function is to provide a barrier between the food and the packaging, preventing direct contact and offering several benefits, including hygiene, preservation, and convenience. They are intended for single use and are discarded after the food is consumed.These liners are commonly manufactured from various plastic materials, chosen for their properties such as durability, moisture resistance, and cost-effectiveness.
When investigating detailed guidance, check out chinese food massapequa now.
The selection of the plastic often depends on the food type and intended use, considering factors like temperature, grease content, and the need for gas permeability.
Common Materials Used in Manufacturing
A variety of plastic materials are utilized in the creation of these liners, each possessing unique characteristics suitable for different food applications. The choice of material significantly impacts the liner’s performance in terms of food safety, preservation, and environmental impact.
- Polyethylene (PE): A widely used thermoplastic polymer known for its flexibility, low cost, and moisture resistance. PE liners are frequently employed for packaging items like sandwiches, bakery goods, and fresh produce. It’s available in various densities, including low-density polyethylene (LDPE) and high-density polyethylene (HDPE), offering different levels of flexibility and strength.
- Polypropylene (PP): Another common thermoplastic, PP exhibits higher heat resistance compared to PE, making it suitable for hot foods and microwave applications. It also offers good resistance to grease and oils, which is beneficial for packaging items like fried foods, pasta dishes, and ready meals. PP is often used for containers that hold prepared foods and can be heated.
- Polyethylene Terephthalate (PET): PET is a strong, clear, and recyclable plastic often used for packaging cold foods and beverages. While not as commonly used for liners as PE or PP, PET liners may be employed in certain applications where transparency is desired, allowing consumers to view the food product. PET is also commonly used for clamshell containers.
- Polystyrene (PS): PS is a versatile plastic known for its rigidity and clarity. Expanded polystyrene (EPS), often referred to as Styrofoam, is used for insulation and cushioning. However, it is less common in direct food contact due to environmental concerns, although it is still used in some applications, particularly for disposable trays and containers.
- Biodegradable Plastics: Increasingly, liners are made from biodegradable or compostable plastics, such as polylactic acid (PLA) derived from renewable resources like cornstarch. These offer a more environmentally friendly alternative to traditional plastics, though their use is often limited by cost and performance characteristics, such as heat resistance and barrier properties. These are used where composting is available.
Examples of Food Types Packaged with Liners
Plastic disposable box food liners are utilized across a wide spectrum of food products, catering to various needs in food service, retail, and home consumption. The specific type of liner chosen often depends on the characteristics of the food item and the desired preservation methods.
- Prepared Meals: Liners are frequently used for packaging ready-to-eat meals, such as pasta dishes, stir-fries, and casseroles. These liners help maintain the food’s temperature and prevent leakage during transport and storage.
- Sandwiches and Wraps: Liners, often made from PE or wax-coated paper, are used to wrap sandwiches and wraps, preventing them from drying out and keeping the fillings contained.
- Bakery Goods: Liners are common in packaging pastries, cakes, and cookies. They provide a barrier against moisture and grease, preserving the freshness and appearance of the baked goods.
- Fast Food Items: Liners are used in packaging items like french fries, burgers, and chicken nuggets. They help contain grease and maintain the food’s temperature.
- Fresh Produce: Liners can be used to package items such as salads and pre-cut vegetables. They help maintain freshness and prevent spoilage by providing a barrier against moisture and contaminants.
- Deli Meats and Cheeses: Liners help to prevent the foods from drying out and maintain hygiene.
Types and Varieties of Liners
Plastic disposable box food liners offer a diverse range of options, tailored to meet specific food packaging needs. These variations encompass differences in shape, size, material thickness, and added features. Understanding these types and their respective properties is crucial for selecting the most appropriate liner for a given application, ensuring optimal food preservation and presentation.
Shape and Size Variations
Liners are available in a wide array of shapes and sizes to accommodate various food box dimensions. This ensures a snug fit and effective protection against leaks and spills.The following table summarizes the common shapes and sizes:
Shape | Typical Sizes (Length x Width x Height, in inches) | Common Applications | Notes |
---|---|---|---|
Rectangular | 6x4x2, 8x6x3, 10x8x4, 12x10x5 | Sandwiches, salads, entrees, baked goods | Most versatile shape; easily fits standard box sizes. |
Square | 4x4x2, 6x6x3, 8x8x4 | Burgers, sides, desserts | Ideal for portion control and stacking. |
Round/Oval | Diameter: 6, 8, 10 inches; Depth: 1-3 inches | Soups, stews, pasta dishes | Often used with lids for secure transport. |
Custom | Variable, tailored to specific box dimensions | Specialty food items, unique packaging requirements | Requires custom orders and tooling, offering a perfect fit. |
Thickness and Grade of Plastic
The thickness and grade of plastic used in food liners significantly impact their performance characteristics, including strength, durability, and barrier properties. Different thicknesses are employed to meet specific needs, such as preventing leaks or maintaining food temperature.Common plastic grades include:
- Low-Density Polyethylene (LDPE): Typically used for thinner liners. LDPE offers good flexibility and is suitable for dry or lightly moist foods. It’s often used in liners for sandwiches and bakery items.
- High-Density Polyethylene (HDPE): Provides greater strength and resistance to tearing than LDPE. HDPE liners are well-suited for heavier items and those requiring a higher degree of protection against leakage.
- Polypropylene (PP): Known for its high melting point and excellent barrier properties, PP is often used in liners designed for hot foods. It also offers good resistance to grease and oils.
- Polyethylene Terephthalate (PET): Often used for clear liners, allowing for visibility of the food contents. PET offers good strength and is frequently used in conjunction with other materials.
The thickness of the plastic is typically measured in mils (thousandths of an inch). Common thicknesses range from 1 mil to 4 mils or more, with thicker liners providing greater strength and puncture resistance. Thicker liners are often used for takeout containers and heavy dishes.
Choosing the correct thickness and grade is crucial to ensuring the liner effectively protects the food and prevents spills. For example, a 2-mil HDPE liner might be sufficient for a sandwich, whereas a 4-mil PP liner would be more appropriate for a hot soup.
Features of Liners, Plastic disposable box food liners
Food liners are often enhanced with features that improve their functionality and meet specific requirements. These features can provide added convenience, improve food preservation, and enhance the overall user experience.Common features include:
- Absorbent Pads: Integrated absorbent pads, typically made from cellulose or a similar material, are often placed at the bottom of the liner. They absorb excess moisture and liquids from the food, preventing sogginess and extending the shelf life of items like meat and seafood. For example, a raw chicken breast will benefit from this type of liner.
- Anti-Fog Properties: Anti-fog liners are designed to prevent condensation from forming on the inside surface. This is especially important for displaying prepared foods, such as salads or sandwiches, as it allows customers to see the food clearly. This feature is often used in combination with clear plastic liners, like PET.
- Heat Sealable Properties: Some liners are designed to be heat-sealed to the food box, creating an airtight seal. This helps to preserve the food’s freshness, prevent leaks, and maintain the desired temperature. This is particularly common for pre-packaged meals.
- Printed Liners: Liners can be printed with branding, nutritional information, or other relevant content. This can enhance the visual appeal of the packaging and provide additional information to the consumer.
Materials and Manufacturing Processes
Plastic disposable box food liners, while seemingly simple, represent a complex intersection of material science and manufacturing. Understanding the production processes and material properties is crucial for assessing their performance, cost-effectiveness, and environmental footprint. This section delves into the key aspects of how these liners are made and the implications of the materials used.
Manufacturing Processes
The production of plastic disposable box food liners primarily involves two main manufacturing processes: extrusion and thermoforming. Each process offers different advantages depending on the desired liner properties and application.
- Extrusion: Extrusion is a continuous process where plastic pellets are melted and forced through a die to create a continuous sheet or film. The molten plastic is then cooled and solidified. This process is often used for producing flat sheets that are later cut and shaped into liners. Extrusion offers high throughput and is cost-effective for large-scale production. For example, a food packaging company might use extrusion to produce rolls of polyethylene (PE) film, which are then used to create liners for sandwich boxes.
- Thermoforming: Thermoforming involves heating a plastic sheet until it becomes pliable, and then using a mold to shape it into the desired form. Vacuum or pressure can be applied to force the plastic sheet against the mold. This process is suitable for creating liners with complex shapes, such as those with compartments or raised edges. Thermoforming is commonly used for producing liners that need to conform to specific box designs.
Consider a manufacturer thermoforming polypropylene (PP) sheets to create liners for ready-meal containers, incorporating separate sections for the main course, side dishes, and sauce.
Environmental Impact of Plastic Materials
The environmental impact of plastic disposable box food liners is a significant concern, primarily driven by the type of plastic material used. Different plastics have varying properties that affect their sustainability.
- Polypropylene (PP): PP is a thermoplastic polymer known for its high melting point, chemical resistance, and flexibility. It is often considered a more environmentally friendly option compared to some other plastics because it is recyclable (although recycling rates vary depending on local infrastructure). PP is commonly used for liners that need to withstand higher temperatures, such as those used in microwaveable food containers.
However, its production still contributes to greenhouse gas emissions, and the energy required for recycling can also be significant.
- Polyethylene Terephthalate (PET): PET is a strong, lightweight, and transparent plastic that is widely used for food packaging, including beverage bottles and some food liners. PET is highly recyclable and has a relatively good recycling infrastructure in many regions. The recyclability of PET makes it a better choice than plastics that are not easily recycled. The energy required to recycle PET is generally lower than for other plastics, making it more environmentally friendly.
- Polyethylene (PE): PE is a versatile plastic available in various densities (e.g., LDPE, HDPE). It is flexible, moisture-resistant, and relatively inexpensive. PE is commonly used for food liners and bags. However, PE’s recyclability can be lower than PET, and its decomposition time in landfills is extremely long. The environmental impact of PE depends on the specific type (e.g., high-density PE vs.
low-density PE) and the availability of recycling facilities.
Additives and Coatings
To enhance their performance, plastic disposable box food liners often incorporate various additives and coatings. These additives can improve properties such as barrier protection, heat resistance, and printability.
- Antioxidants: Antioxidants are added to plastics to prevent degradation caused by oxidation, which can lead to changes in color, mechanical properties, and the formation of undesirable compounds. These additives extend the shelf life of the liner and the food it contains.
- UV Stabilizers: UV stabilizers protect the plastic from degradation caused by exposure to ultraviolet (UV) radiation, which can cause the plastic to become brittle and discolored. These are particularly important for liners that may be exposed to sunlight.
- Colorants: Colorants, including pigments and dyes, are used to give the liners a specific color or appearance. They can improve the aesthetics of the packaging and make it more appealing to consumers.
- Coatings: Coatings are applied to the surface of the liners to enhance their barrier properties, improve printability, or provide specific functionalities. For example:
- Barrier Coatings: These coatings, often made from polymers or specialized materials, are used to prevent the migration of moisture, oxygen, or other gases into or out of the food. This extends the shelf life of the food and protects its flavor and quality.
- Printing Coatings: Coatings can be applied to improve the adhesion of inks and provide a smooth surface for printing logos, branding, and product information.
- Heat-Seal Coatings: These coatings are applied to allow for heat sealing of the liners, creating a tight seal to prevent leaks and maintain food freshness.
Advantages and Disadvantages of Using Liners
Plastic disposable box food liners offer a spectrum of benefits, primarily revolving around convenience, hygiene, and food preservation. However, their widespread use also raises significant environmental concerns. Understanding both sides of this equation is crucial for informed decision-making in food packaging practices.
Benefits of Using Plastic Disposable Box Food Liners
The use of plastic disposable box food liners provides several advantages for both food vendors and consumers. These benefits contribute to improved food handling, extended shelf life, and enhanced convenience.
- Enhanced Food Safety and Hygiene: Liners create a barrier between the food and the packaging, minimizing direct contact and reducing the risk of contamination from external sources or the packaging material itself. This is particularly important for preventing the transfer of microorganisms.
- Improved Food Preservation: Certain liners, especially those made from materials like polyethylene or polypropylene, can provide a degree of moisture and gas barrier protection. This helps to slow down spoilage, maintain food freshness, and extend the shelf life of perishable items. For example, pre-packaged salads often utilize liners with modified atmosphere packaging (MAP) capabilities to extend their shelf life by several days.
- Convenience and Efficiency: Liners simplify the process of food packaging and handling. They can be pre-formed and readily inserted into boxes, streamlining the workflow in food service operations. This ease of use also translates to quicker clean-up, as the liner can be discarded with the food waste, reducing the need for extensive washing of the food containers.
- Protection Against Leaks and Spills: Liners act as a protective layer, preventing liquids and sauces from leaking out of the food box. This helps to maintain the integrity of the packaging and prevents messy situations for both the vendor and the consumer, particularly during transport.
- Customization and Branding: Liners can be customized with branding elements, such as logos and product information, providing an additional opportunity for marketing and brand recognition. This can be achieved through printing directly onto the liner material.
Environmental Disadvantages of Using Plastic Disposable Box Food Liners
Despite their advantages, plastic disposable box food liners pose significant environmental challenges due to their reliance on plastic materials. These concerns are primarily related to waste generation, resource depletion, and pollution.
- Contribution to Plastic Waste: The vast majority of plastic liners are single-use items, contributing significantly to the global plastic waste problem. The volume of these liners discarded daily in food service establishments and by consumers is substantial, often ending up in landfills or polluting the environment.
- Non-Biodegradability: Most plastic liners are made from non-biodegradable materials, meaning they do not break down naturally in the environment within a reasonable timeframe. This leads to the accumulation of plastic waste, which can persist for hundreds of years, posing a long-term environmental hazard.
- Resource Depletion: The production of plastic liners requires the extraction and processing of fossil fuels, contributing to the depletion of finite natural resources. This process also involves significant energy consumption, further exacerbating environmental impact.
- Pollution from Manufacturing: The manufacturing of plastic liners releases pollutants into the air and water, contributing to greenhouse gas emissions and environmental degradation. This includes the release of volatile organic compounds (VOCs) and other harmful chemicals.
- Microplastic Formation: As plastic liners degrade over time, they can break down into microplastics, which are tiny plastic particles that can contaminate soil, water, and even enter the food chain, posing potential health risks.
Role of Liners in Food Safety and Hygiene
Plastic disposable box food liners play a crucial role in maintaining food safety and hygiene standards. They act as a barrier, protecting food from contamination and ensuring that food reaches consumers in a safe and sanitary condition.
- Preventing Cross-Contamination: Liners prevent direct contact between food and the box, reducing the risk of cross-contamination from the box itself or from any potential contaminants on the surface of the box. This is particularly important in preventing the spread of foodborne illnesses.
- Minimizing Microbial Growth: By creating a barrier, liners can help to control the environment surrounding the food, reducing the potential for microbial growth. This is especially effective when combined with other food preservation techniques, such as modified atmosphere packaging.
- Protecting Food Integrity: Liners can help to maintain the integrity of the food by preventing it from drying out, absorbing odors, or being exposed to external elements that could compromise its quality.
- Facilitating Safe Handling: Liners simplify the handling of food, reducing the risk of food handlers touching the food directly. This can help to minimize the transfer of bacteria or other contaminants from hands to the food.
- Compliance with Regulations: The use of food-grade liners helps food businesses comply with food safety regulations and standards. Many regulatory bodies mandate the use of food-safe packaging materials to protect public health.
Applications and Industries: Plastic Disposable Box Food Liners
Plastic disposable box food liners find extensive use across various industries due to their convenience, hygiene, and cost-effectiveness. The specific applications and designs of these liners are often tailored to meet the unique requirements of each sector, ensuring optimal food preservation, presentation, and consumer experience.
Primary Industries Utilizing Plastic Disposable Box Food Liners
Several industries heavily rely on plastic disposable box food liners to enhance food safety and presentation. The following industries are among the most significant users of these liners:
- Restaurants and Takeaway Services: This sector is a primary consumer of plastic liners. They are used extensively for packaging takeout and delivery meals.
- Food Processing and Manufacturing: Liners are essential in this industry for protecting food products during storage, transportation, and packaging processes.
- Catering Services: Catering companies frequently use these liners for transporting and serving food at events and gatherings.
- Grocery Stores and Supermarkets: Liners are employed in the prepared foods section and for packaging certain deli items.
Specific Examples of Food Items and Packaging Styles within Each Industry
The application of plastic disposable box food liners varies significantly depending on the food items and packaging styles used in each industry.
- Restaurants and Takeaway Services:
- Food Items: Burgers, fries, pizza slices, salads, sandwiches, and complete meal combinations.
- Packaging Styles: Box-shaped containers, clamshell containers, and trays. The liners are often pre-cut to fit specific container sizes, preventing food from sticking and maintaining the box’s integrity. A burger is placed inside a box lined with a custom-cut sheet, the sheet prevents grease from seeping through.
- Food Processing and Manufacturing:
- Food Items: Ready-to-eat meals, frozen foods, processed meats, and baked goods.
- Packaging Styles: Tray liners for frozen pizzas, bags for processed meats, and box liners for ready-to-eat meals. The liners protect the food from direct contact with the packaging, preventing contamination and maintaining product quality. For example, a frozen lasagna is placed in a tray, and a liner is added before sealing, preventing the lasagna from adhering to the tray.
- Catering Services:
- Food Items: Buffet-style dishes, appetizers, entrees, and desserts.
- Packaging Styles: Large catering trays, disposable serving dishes, and insulated containers. Liners are designed to maintain food temperature and prevent spills during transport and service. A tray of sandwiches is placed inside a large insulated container, with a liner separating the sandwiches from the container’s base.
- Grocery Stores and Supermarkets:
- Food Items: Prepared salads, deli meats, cheeses, and hot food items.
- Packaging Styles: Pre-portioned containers, trays, and take-out boxes. Liners help to maintain food freshness and prevent cross-contamination. A container of prepared salad is placed on a tray, and a liner keeps the salad from touching the plastic.
Variations in Liner Design and Features Based on Industry Needs
The design and features of plastic disposable box food liners are adapted to the specific demands of each industry. These variations ensure that the liners effectively fulfill their intended purposes.
- Material Composition:
- Restaurants: Liners are often made from food-grade polyethylene (PE) or polypropylene (PP) due to their moisture resistance and cost-effectiveness.
- Food Processing: Liners may include specialized barrier films for enhanced oxygen and moisture protection.
- Catering: Liners often feature heat-sealable properties for maintaining food temperature during transport.
- Grocery Stores: Liners may be made from materials suitable for microwave reheating or with anti-fogging properties for better visibility.
- Size and Shape:
- Restaurants: Liners are typically pre-cut to fit standard container sizes used for burgers, fries, and other menu items.
- Food Processing: Custom-sized liners are designed to fit specific product dimensions and packaging requirements.
- Catering: Large-format liners are designed for catering trays and buffet service.
- Grocery Stores: Liners are designed to fit prepared food containers and deli packaging.
- Special Features:
- Restaurants: Some liners are printed with branding elements, serving as a marketing tool.
- Food Processing: Liners can incorporate features such as tear-away strips for easy opening or re-sealable closures.
- Catering: Insulated liners may be used to maintain food temperature.
- Grocery Stores: Anti-fogging liners are used for prepared food containers, improving product visibility.
Regulatory Compliance and Standards
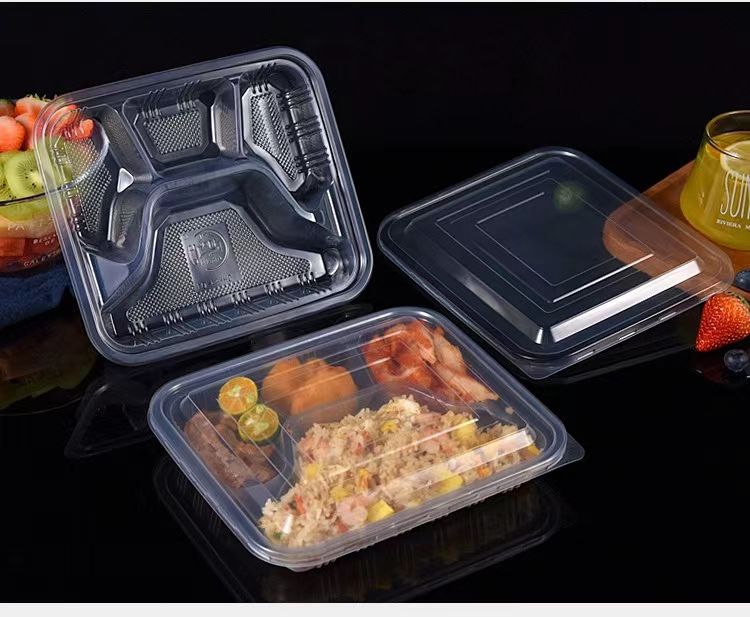
Ensuring the safety and suitability of plastic disposable box food liners requires adherence to stringent regulatory standards and certifications. These regulations and standards are designed to protect public health by minimizing the risk of contamination and ensuring the liners are safe for their intended use. This section Artikels the key compliance aspects.
Food Safety Regulations
Several food safety regulations govern the manufacturing, use, and labeling of plastic disposable box food liners. These regulations are primarily aimed at preventing the migration of harmful substances from the liner into the food it contains.
- United States (FDA): The Food and Drug Administration (FDA) in the United States is a key regulatory body. It establishes standards for materials used in food contact.
- 21 CFR Part 177: This section of the Code of Federal Regulations (CFR) Artikels the regulations for polymers used in food contact applications. It specifies the types of polymers that are approved and the conditions under which they can be used.
For example, it sets limits on the amount of certain substances that can migrate from the plastic liner into the food.
- Food Contact Notifications (FCNs): Manufacturers often submit Food Contact Notifications to the FDA for new food contact substances. These notifications provide information about the material’s composition, intended use, and safety assessments. The FDA reviews these notifications to ensure the material meets the necessary safety standards.
- 21 CFR Part 177: This section of the Code of Federal Regulations (CFR) Artikels the regulations for polymers used in food contact applications. It specifies the types of polymers that are approved and the conditions under which they can be used.
- European Union (EU): The EU has comprehensive regulations regarding food contact materials.
- Regulation (EC) No 1935/2004: This framework regulation sets the general principles for all food contact materials. It mandates that materials must be inert and not transfer substances to food in amounts that could endanger human health or cause unacceptable changes in the food’s composition.
- Regulation (EU) No 10/2011: This regulation specifically addresses plastic materials and articles intended to come into contact with food. It sets out requirements for the composition of plastics, including restrictions on the use of certain substances and migration limits. For instance, it establishes specific migration limits (SMLs) for various substances that can migrate from the plastic into the food.
- Good Manufacturing Practice (GMP): Compliance with GMP is also required. This involves implementing a system of quality control and hygiene measures to ensure the manufacturing process is conducted in a safe and hygienic manner.
- Other International Regulations: Other countries, such as Canada and Australia, have their own food safety regulations that may align with or be based on the standards set by the FDA or the EU.
Certifications and Approvals
Certifications and approvals provide assurance that plastic disposable box food liners meet specific safety and quality standards. These certifications are often awarded by independent third-party organizations.
- FDA Compliance: While the FDA does not issue certifications, manufacturers must demonstrate that their liners comply with FDA regulations. This typically involves providing documentation and testing results to verify that the materials used meet the specified requirements.
- EU Compliance: Compliance with EU regulations requires that the materials and manufacturing processes meet the standards set forth in Regulation (EC) No 1935/2004 and Regulation (EU) No 10/2011.
- Certifications from Third-Party Organizations:
- BfR Recommendations (Germany): The German Federal Institute for Risk Assessment (BfR) provides recommendations for food contact materials. These recommendations are widely recognized and followed in Germany and other European countries.
- ISEGA (Germany): ISEGA is a testing and certification institute that offers certifications for food contact materials, including plastic liners. Their certifications verify compliance with relevant regulations and standards.
- SGS and Intertek: These are global inspection, testing, and certification companies that offer testing and certification services for food contact materials, ensuring compliance with various international standards.
- Testing and Analysis:
- Migration Testing: This involves testing the liner to determine the amount of substances that migrate into food under specific conditions, such as temperature and time.
- Overall Migration Limit (OML) Testing: This test measures the total amount of substances that migrate from the liner into the food.
- Specific Migration Limit (SML) Testing: This test measures the migration of specific substances from the liner.
Labeling Requirements
Proper labeling is crucial to ensure consumers and food handlers are aware of the liner’s intended use, safety features, and any relevant warnings. Labeling requirements vary depending on the region and the specific regulations in place.
- Mandatory Information:
- Material Identification: The label should clearly identify the type of plastic used (e.g., polyethylene, polypropylene).
- Intended Use: The label should state the intended use of the liner (e.g., for cold foods, hot foods, or specific food types).
- Contact Information: The manufacturer’s or distributor’s name and address must be provided.
- Compliance Statements: Statements indicating compliance with relevant regulations (e.g., “Complies with FDA regulations” or “Suitable for food contact”) are often included.
- Optional Information:
- Temperature Range: The label may indicate the safe temperature range for the liner (e.g., “Suitable for temperatures up to 100°C”).
- Storage Instructions: Instructions for proper storage to maintain the liner’s integrity may be provided.
- Recycling Symbols: Recycling symbols and codes may be included to indicate the recyclability of the liner.
- Warnings: Any warnings about the use of the liner, such as “Not suitable for microwave use” or “Avoid contact with strong solvents,” should be clearly stated.
- Examples of Labeling:
- Example 1: A label might state, “Food-grade polypropylene liner. Suitable for cold and hot foods up to 80°C. Manufacturer: ABC Plastics, Anytown, USA. Complies with FDA regulations.”
- Example 2: A label might include, “Made from polyethylene. For single-use food packaging. Do not microwave. Store in a cool, dry place. Manufacturer: XYZ Packaging, London, UK.
Certified by SGS for food contact.”
Environmental Considerations and Sustainability
The widespread use of plastic disposable box food liners, while offering convenience and hygiene, presents significant environmental challenges. Understanding these impacts and exploring sustainable alternatives is crucial for minimizing the ecological footprint of the food packaging industry. This section delves into the environmental consequences, focusing on waste generation, and examines methods to reduce the environmental impact, with a particular emphasis on recyclability and biodegradability.
Environmental Impact of Plastic Disposable Box Food Liners
The primary environmental concern associated with plastic disposable box food liners is waste generation. These liners, often used once and discarded, contribute significantly to landfill accumulation and plastic pollution.
“Plastic waste, particularly single-use items, poses a serious threat to ecosystems and human health.”
United Nations Environment Programme.
- Waste Generation: The sheer volume of liners used daily across various food service sectors results in a substantial amount of non-biodegradable waste. Landfills are rapidly filling up, and the decomposition process for plastic can take hundreds of years, leading to long-term environmental burdens.
- Plastic Pollution: Improper disposal or leakage of plastic liners into the environment leads to plastic pollution in oceans, rivers, and terrestrial ecosystems. This pollution harms wildlife, contaminates water sources, and can enter the food chain through microplastics. A study published in
-Science Advances* estimated that approximately 8 million metric tons of plastic waste enter the ocean annually. - Resource Depletion: The production of plastic liners relies on fossil fuels, contributing to the depletion of non-renewable resources and increasing greenhouse gas emissions. The extraction, refining, and manufacturing processes involved in plastic production have a substantial carbon footprint.
- Greenhouse Gas Emissions: The entire lifecycle of plastic liners, from production to disposal, contributes to greenhouse gas emissions. Incineration of plastic waste releases harmful gases, while the production of virgin plastics consumes significant energy, furthering climate change.
Methods for Reducing Environmental Impact
Several strategies can mitigate the environmental impact of plastic disposable box food liners. These methods aim to reduce waste, promote resource efficiency, and foster a circular economy.
- Using Recycled Materials: Manufacturing liners from recycled plastics reduces the demand for virgin materials and lowers the carbon footprint of production. Post-consumer recycled (PCR) plastics are increasingly available and can be incorporated into liner manufacturing.
- Material Optimization: Designing liners with minimal material usage and optimizing their structure can reduce the overall amount of plastic waste generated. This includes using thinner, yet durable, materials and minimizing unnecessary packaging components.
- Compostable and Biodegradable Alternatives: Switching to liners made from compostable or biodegradable materials, such as plant-based polymers, can significantly reduce landfill waste. These materials break down naturally under specific conditions, returning organic matter to the soil.
- Promoting Reusable Alternatives: Encouraging the use of reusable food containers and liners, particularly in restaurants and food delivery services, can drastically reduce the demand for disposable liners. Implementing deposit-refund systems or offering discounts for using reusable options can incentivize this shift.
- Improved Waste Management: Enhancing waste collection and recycling infrastructure is crucial. Implementing effective recycling programs, providing clear labeling for proper disposal, and educating consumers on waste sorting can increase recycling rates.
- Design for Recyclability: Liners should be designed to be easily recyclable. This includes using compatible materials and avoiding complex designs that hinder the recycling process. Mono-material construction, where the liner is made from a single type of plastic, is ideal for recyclability.
Recyclability and Biodegradability of Different Liner Materials
The environmental performance of plastic disposable box food liners is heavily dependent on the materials used. Understanding the recyclability and biodegradability of different materials is essential for making informed choices.
- Polypropylene (PP): PP is a commonly used plastic for food liners. It is generally recyclable, but the availability of PP recycling varies depending on local infrastructure. Contamination with food residue can reduce its recyclability.
- Polyethylene Terephthalate (PET): PET is another frequently used plastic. It is highly recyclable and widely accepted in recycling programs. PET liners are often clear and can be effectively recycled into new products.
- Polystyrene (PS): PS, including expanded polystyrene (EPS or Styrofoam), is less easily recyclable than PP or PET. Recycling facilities often do not accept PS due to its low density and the challenges in processing.
- Biodegradable Plastics (PLA): Polylactic acid (PLA) is a bioplastic derived from renewable resources like corn starch. PLA is compostable under industrial composting conditions but may not readily biodegrade in home compost piles or landfills.
- Compostable Materials (Paper-Based): Paper-based liners, especially those coated with compostable coatings, are biodegradable and can be composted. These are an excellent option for reducing waste, but their barrier properties might be lower than plastic alternatives.
Alternatives to Plastic Liners
The increasing awareness of plastic’s environmental impact has spurred innovation in food packaging, including the development of alternatives to plastic disposable box food liners. These alternatives aim to provide the same functionality—protection, hygiene, and convenience—while minimizing environmental harm.
Alternative Materials for Food Liners
A variety of materials offer viable alternatives to plastic liners, each with its own set of advantages and disadvantages. These materials can be broadly categorized based on their origin and composition.
- Paper-Based Liners: Paper liners are a widely available and generally biodegradable option. They are often made from virgin or recycled paper and can be treated with coatings to provide grease and moisture resistance. Examples include kraft paper, parchment paper, and waxed paper.
- Plant-Based Liners: Plant-based liners utilize materials derived from renewable resources. These often include materials like sugarcane, cornstarch, or other agricultural byproducts. They can be compostable under specific conditions.
- Aluminum Foil Liners: Aluminum foil provides excellent barrier properties against moisture, grease, and light. It is recyclable but requires significant energy for production.
- Biodegradable Plastic Alternatives: While still technically plastics, these materials are designed to break down more readily in composting environments. They are typically made from renewable resources like cornstarch (PLA – polylactic acid) or other biopolymers.
Performance and Cost-Effectiveness Comparison
The performance and cost-effectiveness of alternative materials vary significantly. A direct comparison highlights these differences, considering factors such as barrier properties, durability, cost, and environmental impact.
Material | Barrier Properties (Grease, Moisture, Oxygen) | Durability | Cost | Environmental Impact | Examples |
---|---|---|---|---|---|
Paper | Varies depending on coating; generally good for grease, moderate for moisture and oxygen. | Moderate; can tear or leak. | Relatively low. | Can be biodegradable/compostable, but production requires resources and coatings may impact recyclability. | Kraft paper, parchment paper, waxed paper. |
Plant-Based | Varies; often similar to paper but with potential for improved performance depending on the specific material and coatings. | Moderate; can be compostable. | Can be higher than paper, depending on the source material and processing. | Potentially low, especially if sourced sustainably; requires industrial composting facilities for optimal breakdown. | Sugarcane, cornstarch-based liners. |
Aluminum Foil | Excellent barrier properties against all elements. | High; resistant to tearing and punctures. | Higher than paper or some plant-based options. | Recyclable but energy-intensive to produce; can contribute to landfill waste if not recycled. | Foil liners for specific food applications. |
Biodegradable Plastic Alternatives (PLA) | Can vary; PLA offers good barrier properties, but may have limitations in high-temperature applications. | Moderate; may degrade under high temperatures or in the presence of moisture. | Higher than conventional plastics and paper. | Compostable under specific conditions (industrial composting). | PLA liners. |
Advantages and Disadvantages of Alternative Materials
Choosing the right food liner material involves balancing various factors. Each alternative material offers a unique set of advantages and disadvantages that must be considered based on the specific application.
- Paper-Based Liners:
- Advantages: Widely available, relatively inexpensive, biodegradable/compostable (depending on coatings), printable.
- Disadvantages: Can lack sufficient barrier properties for grease or moisture without coatings, may tear easily, some coatings can hinder recyclability.
- Plant-Based Liners:
- Advantages: Renewable resource, can be compostable, potentially lower carbon footprint.
- Disadvantages: Can be more expensive than paper, requires industrial composting, performance can vary depending on the material.
- Aluminum Foil Liners:
- Advantages: Excellent barrier properties, recyclable, can withstand high temperatures.
- Disadvantages: High energy input for production, not biodegradable, can be expensive.
- Biodegradable Plastic Alternatives (PLA):
- Advantages: Compostable under specific conditions, derived from renewable resources, can mimic the performance of conventional plastics.
- Disadvantages: Requires industrial composting, can be more expensive, may have limited high-temperature resistance.
Market Trends and Innovations
The market for plastic disposable box food liners is dynamic, shaped by evolving consumer preferences, environmental concerns, and technological advancements. Understanding these trends and innovations is crucial for businesses operating within the food packaging industry.
Current Market Trends
Several key trends are currently influencing the plastic disposable box food liner market. These trends reflect a shift towards greater convenience, sustainability, and food safety.
- Increased Demand for Convenience: Busy lifestyles are driving the demand for ready-to-eat meals and takeout food. This, in turn, increases the need for disposable food containers and liners that are easy to use, transport, and dispose of. This trend is particularly noticeable in urban areas and regions with a high concentration of fast-food restaurants and food delivery services.
- Focus on Food Safety and Hygiene: Consumers are increasingly concerned about food safety. Plastic liners provide a barrier against contamination, ensuring the food remains fresh and protected during transportation and storage. This is particularly important for perishable items. The COVID-19 pandemic further amplified this trend, leading to a heightened focus on hygiene in all aspects of food handling.
- Rising Awareness of Environmental Issues: The environmental impact of plastic waste is a major concern. Consumers and regulatory bodies are pushing for more sustainable packaging solutions, including liners made from recycled materials or biodegradable alternatives. This trend is prompting manufacturers to explore innovative materials and designs that minimize environmental impact.
- Growth in E-commerce and Food Delivery: The rapid expansion of online food ordering and delivery services has fueled the demand for disposable food containers and liners. These liners play a crucial role in maintaining food quality and preventing leaks or spills during transit. This growth is particularly pronounced in countries with high internet penetration and a strong food delivery culture.
- Customization and Branding: Businesses are increasingly using food packaging, including liners, as a branding tool. Custom-printed liners with logos, messages, or artwork can enhance brand recognition and create a positive customer experience. This trend is leading to the development of more sophisticated printing techniques and design options for liners.
Recent Innovations in Materials and Design
The industry is witnessing significant innovations in materials and design to address the challenges and opportunities presented by the market trends. These innovations aim to improve sustainability, functionality, and consumer appeal.
- Biodegradable and Compostable Materials: The development of liners made from biodegradable and compostable materials is gaining momentum. These materials, such as polylactic acid (PLA) derived from cornstarch, offer a more environmentally friendly alternative to traditional plastics. They break down naturally in composting environments, reducing landfill waste. The challenge lies in scaling up production and ensuring these materials meet the necessary performance standards for food safety and durability.
- Recycled Content Plastics: Using recycled plastics in liner production is another key innovation. This reduces the reliance on virgin materials and helps to divert plastic waste from landfills. Post-consumer recycled (PCR) plastics are being increasingly incorporated into liner manufacturing. The quality and performance of liners made with PCR plastics are continuously improving.
- Improved Barrier Properties: Innovations in liner design are focused on enhancing barrier properties to protect food from moisture, oxygen, and other contaminants. This extends the shelf life of food products and reduces food waste. Coating technologies and multi-layer films are being developed to provide superior barrier protection.
- Smart Packaging Features: Smart packaging technologies, such as temperature sensors and freshness indicators, are being integrated into liners. These features provide consumers with valuable information about the food’s condition and safety. While still in their early stages, these technologies have the potential to revolutionize food packaging.
- Sustainable Coatings: Research and development are focused on creating sustainable coatings that can replace traditional plastic coatings. These coatings improve the liner’s performance, such as resistance to grease and water, while being environmentally friendly. They are made from renewable resources and designed to break down more easily.
Future Trends and Developments
The future of the plastic disposable box food liner industry is likely to be shaped by ongoing technological advancements, regulatory changes, and evolving consumer preferences. Several key trends are expected to drive future developments.
- Circular Economy Models: The adoption of circular economy models, where materials are reused and recycled, will become increasingly important. This will involve designing liners for recyclability, implementing closed-loop recycling systems, and exploring innovative material recovery technologies. The focus will be on minimizing waste and maximizing resource utilization.
- Increased Regulation and Policy: Governments worldwide are implementing stricter regulations on plastic packaging, including bans on single-use plastics and mandates for recycled content. These regulations will drive innovation and the adoption of more sustainable packaging solutions. The industry will need to adapt to evolving regulatory landscapes.
- Advanced Manufacturing Technologies: Advanced manufacturing technologies, such as 3D printing, are expected to play a role in liner production. 3D printing can enable customized designs, rapid prototyping, and on-demand manufacturing, reducing waste and improving efficiency. The application of these technologies will become more widespread.
- Bio-based Polymers and Composites: The development of bio-based polymers and composite materials will continue to grow. These materials offer a sustainable alternative to traditional plastics and can be tailored to meet specific performance requirements. The focus will be on improving the performance and cost-effectiveness of these materials.
- Data-Driven Packaging Solutions: Data analytics will play a greater role in the design and optimization of food packaging. By analyzing consumer behavior, supply chain data, and environmental impact, manufacturers can create more effective and sustainable packaging solutions. The use of data will drive innovation and improve decision-making.
Proper Use and Handling
Plastic disposable box food liners, while convenient, require careful handling to ensure food safety and prevent environmental harm. Proper usage extends the liner’s utility and minimizes its negative impact. Understanding and adhering to these guidelines is crucial for all users.
Storage Guidelines
Proper storage is critical to maintain the integrity and hygiene of plastic disposable box food liners. Following these practices will help preserve their functionality and prevent contamination.
- Store in a cool, dry place: Avoid exposure to direct sunlight, excessive heat, and moisture. These conditions can degrade the plastic, making it brittle or altering its chemical composition, potentially affecting food safety.
- Keep away from contaminants: Store liners away from chemicals, cleaning agents, and strong odors. Plastic can absorb these substances, which could then transfer to the food.
- Maintain organized inventory: Implement a “first-in, first-out” (FIFO) system to ensure that older liners are used before newer ones. This minimizes the risk of using expired or degraded liners.
- Protect from pests: Store liners in sealed containers or cabinets to prevent access by insects and rodents. These pests can contaminate the liners, making them unsuitable for food contact.
Use and Handling Procedures
Correct use of plastic disposable box food liners is vital for food safety and to prevent liner damage or contamination. Proper handling ensures the liner effectively protects the food and maintains hygiene standards.
- Wash hands thoroughly: Before handling the liners, wash hands with soap and water for at least 20 seconds. This removes potential contaminants that could transfer to the liners and subsequently to the food.
- Inspect for damage: Before use, examine each liner for any tears, holes, or signs of degradation. Discard any damaged liners, as they may not provide adequate protection or could contaminate the food.
- Handle with clean utensils: Use tongs, spatulas, or gloves to handle the liners, especially when placing them in food boxes. This minimizes direct hand contact and reduces the risk of contamination.
- Avoid overfilling: Do not overfill the liners with food, as this can lead to tearing or leakage. The food should fit comfortably within the liner without straining the material.
- Use appropriate liners for food types: Select liners specifically designed for the type of food being served. For example, liners intended for hot foods may not be suitable for cold foods, and vice versa. Check the liner’s temperature range.
Disposal Protocols
Proper disposal of plastic disposable box food liners is essential for environmental responsibility. These guidelines aim to minimize the environmental impact and promote responsible waste management.
- Check local regulations: Familiarize yourself with local waste disposal regulations. Some areas may have specific guidelines for plastic waste, including recycling programs or landfill restrictions.
- Separate from food waste: Remove any food residue from the liners before disposal. This can prevent contamination of other recyclables and reduce odors.
- Consider recycling options: Determine if the liners are recyclable in your area. If they are, follow local recycling guidelines. Rinse the liners if necessary, before placing them in the appropriate recycling bin.
- Properly dispose of non-recyclable liners: If the liners are not recyclable, place them in a designated trash receptacle. Ensure the trash bags are securely sealed to prevent littering.
- Educate staff and customers: Provide clear instructions to staff and customers regarding proper disposal procedures. This helps to ensure consistent and responsible waste management practices.
Visual Guide: Proper Handling of Plastic Disposable Box Food Liners
The following describes a visual guide illustrating the proper handling of plastic disposable box food liners.
Scene 1: Storage
The scene depicts a clean, organized storage area. A shelf holds stacks of neatly arranged plastic disposable box food liners. The liners are in their original packaging, sealed to protect them from dust and contaminants. A thermometer shows the temperature is within the recommended range (below 25°C). A sign is present that says “Store in a Cool, Dry Place.”
Scene 2: Hand Washing
A person is shown thoroughly washing their hands at a sink. They are using soap and water and are washing for at least 20 seconds. The water is running, and the person is scrubbing their hands, including between their fingers and under their nails. A sign above the sink reads, “Wash Hands Before Handling Liners.”
Scene 3: Liner Inspection
A person is holding a plastic disposable box food liner and visually inspecting it. They are checking for any tears, holes, or signs of damage. The liner is held up to the light to ensure no imperfections are present. A magnifying glass is nearby for closer examination. The person is discarding a liner with a small tear.
The liner is labeled “Damaged – Do Not Use.”
Scene 4: Liner Placement
A person is using clean tongs to place a plastic disposable box food liner into a food container. They are careful not to touch the inside of the liner with their hands. The liner fits perfectly inside the box. The person is wearing disposable gloves to further ensure cleanliness. The tongs are stainless steel, and the box is clean.
Scene 5: Food Placement
The scene shows a filled food box with the plastic disposable liner. The food is neatly arranged inside the liner, and the liner is not overfilled. The food is visually appealing, and the liner is holding the food securely. The box is closed with a lid. A label indicates the contents and date of preparation.
Scene 6: Disposal
A person is shown disposing of a used plastic disposable box food liner. The liner is empty of food residue and placed in a clearly marked recycling bin. A sign above the bin indicates “Recycle – Plastic Liners” or “Landfill – Non-Recyclable Liners.” Another bin is available for food waste.
Final Review
In conclusion, plastic disposable box food liners represent a complex interplay of convenience, functionality, and environmental impact. While they offer significant benefits in terms of food preservation and hygiene, the challenges associated with plastic waste and sustainability cannot be ignored. As the industry evolves, exploring alternative materials, improving recycling processes, and adhering to stringent regulations will be crucial. Ultimately, a balanced approach that considers both the practical advantages and the environmental costs is necessary to ensure a responsible and sustainable future for these essential food packaging components.
The ongoing innovations and market shifts suggest a dynamic future for plastic disposable box food liners, requiring continuous evaluation and adaptation.