Shrink wrap machine food, a silent guardian in the bustling world of sustenance, often goes unnoticed, yet its influence is woven into the very fabric of our meals. It’s a paradox, isn’t it? This unassuming technology, this embrace of transparent film, holds within it the power to defy time, to cradle the ephemeral beauty of a perfectly ripe tomato, a glistening cut of meat, or a symphony of pastries.
The shrink wrap machine is more than just a piece of equipment; it is a modern-day alchemist, transforming the vulnerable into the enduring, safeguarding the essence of nourishment.
We will delve into the heart of this fascinating process, exploring the various types of machines, the secrets of the films they employ, and the food products that benefit most from this protective embrace. From the humblest manual machine to the sophisticated automation, each plays a crucial role in delivering freshness and extending shelf life. We’ll also navigate the crucial aspects of food safety and sustainability, unraveling how shrink wrap not only preserves our food but also contributes to a more responsible approach to packaging and waste management.
Imagine a world where the simple act of unwrapping becomes a testament to quality and care, a ritual of anticipation for the delights within.
Introduction to Shrink Wrap Machines for Food
Shrink wrap machines are essential tools in the food packaging industry, designed to tightly encase products in a thin plastic film. This process, known as shrink wrapping, offers significant benefits for food preservation, presentation, and distribution. These machines utilize heat to shrink the film around the food item, creating a secure and often tamper-evident seal.This discussion will delve into the workings of shrink wrap machines, exploring their various types and the advantages they offer to food businesses.
The aim is to provide a comprehensive understanding of how this technology contributes to food safety, shelf life extension, and enhanced product appeal.
Types of Shrink Wrap Machines
Shrink wrap machines are categorized based on their level of automation and operational features. Each type caters to different production volumes and operational needs.
- Manual Shrink Wrap Machines: These machines are the simplest type, often requiring manual loading and sealing of the product. The operator typically places the food item within the film, manually seals the film, and then guides the package through a heat tunnel. They are suitable for low-volume production or small businesses.
- Semi-Automatic Shrink Wrap Machines: Semi-automatic machines automate some aspects of the process, such as sealing or film feeding. Operators may still need to load the product, but the machine handles the sealing and shrinking process. These are ideal for businesses with moderate production demands.
- Automatic Shrink Wrap Machines: Automatic machines offer the highest level of automation, handling the entire packaging process, from film feeding and product loading to sealing and shrinking, with minimal human intervention. These are designed for high-volume production environments, maximizing efficiency and output.
Advantages of Using Shrink Wrap for Food Packaging
Shrink wrapping provides several critical benefits to food packaging, contributing to both product quality and consumer satisfaction.
- Preservation: Shrink wrap creates a barrier against oxygen, moisture, and contaminants, extending the shelf life of perishable food items. This is crucial for maintaining product freshness and reducing food waste.
- Presentation: The tight, clear film enhances the product’s visual appeal, making it more attractive to consumers. It allows for clear product visibility and can be used to create attractive packaging. For example, a shrink-wrapped tray of fruits looks more appealing and protected compared to unwrapped fruits.
- Protection: Shrink wrap provides physical protection, safeguarding food items from damage during handling, transportation, and storage. This reduces the likelihood of spoilage and ensures products reach consumers in optimal condition.
- Tamper-Evident Seal: Shrink wrap can be used to create tamper-evident packaging, providing consumers with confidence that the product has not been opened or compromised. This is particularly important for food safety and consumer trust.
- Cost-Effectiveness: Compared to some other packaging methods, shrink wrapping can be a cost-effective solution, especially for high-volume production. The material costs are often lower, and the process can be highly efficient.
Types of Shrink Wrap Films Used in Food Packaging
Choosing the right shrink wrap film is critical for effective food packaging. The film type directly impacts the product’s shelf life, appearance, and protection. Different films offer varying properties, making some more suitable for specific food applications than others. Understanding these differences allows food producers to select the best option, optimizing both product presentation and preservation.
Common Shrink Wrap Film Types
Several types of shrink wrap films are widely used in the food industry, each with distinct characteristics. These characteristics influence the film’s performance in terms of sealing, clarity, strength, and overall suitability for various food products.
Here is a comparison of some common shrink wrap film types:
Film Type | Common Uses | Pros | Cons |
---|---|---|---|
Polyvinyl Chloride (PVC) | Fresh produce, baked goods, pre-packaged foods (e.g., trays of meat) |
|
|
Polyolefin (POF) | Frozen foods, dairy products, prepared meals, toys, books and other non-food products |
|
|
Polyethylene (PE) | Heavy items, large food containers, bundling multiple products. |
|
|
Polypropylene (PP) | Snack foods, confectionery, some bakery items. |
|
|
Food Products Commonly Packaged with Shrink Wrap
Shrink wrap packaging is a versatile method widely adopted in the food industry to protect and preserve a diverse range of products. Its ability to conform tightly to the shape of the food item offers significant advantages, from extending shelf life to improving presentation. The following sections detail specific food products commonly packaged using shrink wrap, the benefits of this packaging method, and real-world examples demonstrating its impact on food preservation.
Specific Food Products and Their Shrink Wrap Applications
Shrink wrap machines are employed across various sectors of the food industry, from fresh produce to prepared meals. The choice of shrink wrap film and the packaging process are carefully considered to meet the specific requirements of each food item, ensuring optimal protection and presentation.
- Fresh Produce: Vegetables and fruits, such as cucumbers, bell peppers, and apples, are frequently shrink-wrapped. This packaging helps to reduce moisture loss, preventing wilting and maintaining freshness. For instance, individual cucumbers are often shrink-wrapped to extend their shelf life by several days compared to unwrapped produce.
- Meat and Poultry: Shrink wrap is used to package raw meats, poultry, and processed meats like sausages and bacon. This packaging method creates a barrier against oxygen and contaminants, which helps to inhibit bacterial growth and extend the product’s shelf life. Vacuum shrink bags are also employed to tightly encase the meat, minimizing air exposure and reducing freezer burn.
- Dairy Products: Cheeses, especially blocks and wheels, are commonly shrink-wrapped. The tight seal provided by the shrink wrap helps to prevent mold growth and maintain the product’s moisture content. Shrink wrapping also provides a tamper-evident seal, assuring consumers of product safety.
- Baked Goods: Bread, pastries, and other baked goods are often packaged using shrink wrap. This packaging protects the items from drying out, maintains their texture, and prevents contamination. Shrink wrapping also enhances the visual appeal of the product, making it more attractive to consumers.
- Prepared Meals: Ready-to-eat meals, such as pre-packaged sandwiches, salads, and frozen dinners, frequently utilize shrink wrap. The packaging provides portion control, prevents spillage, and offers a convenient, tamper-evident seal. The tight fit also helps to preserve the freshness and flavor of the meal.
- Beverages: Multi-packs of bottled water, soft drinks, and other beverages are often shrink-wrapped together. This bundling method makes the products easier to handle, transport, and store. The shrink wrap also serves as a tamper-evident seal and provides a clean, attractive presentation.
Benefits of Shrink Wrapping Food Products
Shrink wrapping offers several advantages for food products, contributing to improved product quality, safety, and marketability. These benefits are critical for both manufacturers and consumers.
- Portion Control: Shrink wrapping allows for precise portioning of food products. This is particularly beneficial for products like cheese, meats, and prepared meals, where accurate serving sizes are essential.
- Tamper Evidence: The tight seal created by shrink wrapping provides a clear indication if a product has been tampered with. This enhances consumer safety and builds trust in the brand.
- Enhanced Shelf Life: By creating a barrier against oxygen, moisture, and contaminants, shrink wrapping significantly extends the shelf life of food products. This reduces food waste and allows for longer distribution periods.
- Improved Presentation: Shrink wrapping provides a sleek, professional appearance to food products. The tight fit enhances the product’s visual appeal, making it more attractive to consumers.
- Protection from Contamination: Shrink wrap protects food products from external contaminants such as dust, dirt, and bacteria, maintaining the product’s safety and hygiene.
Examples of Shelf Life Enhancement through Shrink Wrapping
The impact of shrink wrapping on shelf life varies depending on the food product and the specific packaging materials used. However, the benefits are often substantial, contributing to reduced waste and increased profitability.
- Example 1: Fresh Meat: Unwrapped ground beef typically has a shelf life of 1-2 days in the refrigerator. However, when shrink-wrapped in a modified atmosphere packaging (MAP) system, this shelf life can extend to 7-10 days. The MAP system replaces the air inside the package with a gas mixture designed to inhibit bacterial growth and maintain the meat’s color and texture.
- Example 2: Cheese: A block of cheddar cheese that is not properly packaged might develop mold within a few weeks. By contrast, shrink-wrapping the same block of cheese can extend its shelf life to several months, even up to a year, when stored under appropriate conditions. The shrink wrap acts as a barrier, preventing the entry of mold spores.
- Example 3: Bakery Products: Sliced bread that is not shrink-wrapped will quickly become stale and dry. Shrink wrapping bread can keep it soft and fresh for several days. This is especially beneficial for specialty breads that are more expensive to produce and require a longer shelf life to justify the cost.
Shrink Wrap Machine Operation and Maintenance
Shrink wrap machines are essential for efficient food packaging, offering protection and presentation benefits. Proper operation and consistent maintenance are critical for maximizing their lifespan, ensuring packaging quality, and maintaining workplace safety. Understanding the operational steps, safety protocols, and maintenance procedures is key to realizing these benefits.
Basic Steps in Operating a Shrink Wrap Machine
Operating a shrink wrap machine involves a series of coordinated steps to ensure effective and consistent packaging. These steps vary slightly depending on the machine type (L-sealer, side sealer, etc.), but the core principles remain the same.
- Preparation: Ensure the machine is properly connected to a power source and preheated to the appropriate temperature for the shrink film being used. Check the film roll, making sure it’s correctly loaded and aligned. Inspect the sealing jaws and conveyor system for any obstructions or damage.
- Product Placement: Position the food product on the sealing area (for L-sealers) or on the conveyor (for automated systems). Ensure the product is centered and positioned correctly for optimal sealing and wrapping.
- Sealing (for L-sealers): If using an L-sealer, close the sealing arm to create a seal around the product. The machine will automatically seal and cut the film. For automated systems, the sealing process is typically integrated.
- Shrinking: Transfer the sealed product into the shrink tunnel. The heat from the tunnel causes the film to shrink tightly around the product. The conveyor speed and tunnel temperature must be adjusted according to the film type and product size.
- Cooling: After exiting the shrink tunnel, allow the packaged product to cool. This step ensures the film sets properly and prevents distortion.
- Inspection: Visually inspect the packaged product for proper sealing, shrinkage, and any defects. Make adjustments to the machine settings as needed to improve packaging quality.
Safety Precautions When Operating Shrink Wrap Machines
Operating a shrink wrap machine involves potential hazards, making safety a top priority. Strict adherence to safety protocols is crucial for preventing injuries and ensuring a safe working environment.
- Personal Protective Equipment (PPE): Always wear appropriate PPE, including safety glasses to protect against flying debris and heat-resistant gloves to handle hot materials.
- Electrical Safety: Ensure the machine is properly grounded and that electrical cords are in good condition. Avoid operating the machine with wet hands or near water.
- Hot Surfaces: Be cautious of hot sealing jaws, shrink tunnels, and other heated components. Allow these parts to cool down before attempting any maintenance or adjustments.
- Film Handling: When handling shrink film, be careful to avoid cuts from sharp edges. Use gloves to protect your hands and ensure the film is properly stored to prevent tearing.
- Ventilation: Ensure adequate ventilation in the workspace to remove fumes generated during the shrinking process.
- Emergency Procedures: Familiarize yourself with the machine’s emergency stop button and other safety features. Know the location of the nearest fire extinguisher and first-aid kit.
Regular Maintenance Procedures for Optimal Machine Condition, Shrink wrap machine food
Regular maintenance is essential for keeping a shrink wrap machine in optimal working condition, extending its lifespan, and ensuring consistent packaging quality. Following a scheduled maintenance routine can prevent costly downtime and ensure efficient operation.
- Daily Cleaning: After each use, clean the sealing jaws, shrink tunnel, and conveyor system to remove any film residue or debris. Use appropriate cleaning agents recommended by the machine manufacturer.
- Weekly Inspection: Inspect the machine for any signs of wear and tear, such as loose belts, worn rollers, or damaged wiring. Lubricate moving parts as specified in the manufacturer’s manual.
- Monthly Calibration: Calibrate the temperature controls and sealing timers to ensure accurate and consistent operation.
- Film Roll Management: Check the film roll for proper alignment and tension. Replace film rolls when they are low or damaged.
- Belt and Roller Check: Examine the conveyor belts and rollers for wear, damage, or alignment issues. Replace any worn parts promptly.
- Professional Servicing: Schedule periodic professional servicing by a qualified technician for more complex maintenance tasks and inspections.
Step-by-Step Guide on Troubleshooting Common Machine Issues
Troubleshooting common issues can help minimize downtime and quickly resolve problems with a shrink wrap machine. A systematic approach to troubleshooting can identify the root cause of a problem and allow for effective solutions.
- Machine Doesn’t Power On:
- Check the power supply: Ensure the machine is plugged in and the power outlet is functioning.
- Inspect the circuit breaker: Verify the circuit breaker has not tripped.
- Examine the power cord: Check the power cord for damage.
- Poor Sealing:
- Check the sealing temperature: Adjust the temperature to the correct setting for the film type.
- Inspect the sealing jaws: Clean the sealing jaws to remove any residue. Check for damage and ensure they are aligned properly.
- Verify the sealing time: Adjust the sealing time to allow for adequate sealing.
- Film Issues: Use the correct film type and ensure it is compatible with the machine.
- Film Doesn’t Shrink Properly:
- Check the shrink tunnel temperature: Adjust the temperature to the correct setting for the film type and product.
- Verify the conveyor speed: Adjust the conveyor speed to allow sufficient time for shrinking.
- Inspect the film: Ensure the film is compatible with the shrink tunnel and is not expired.
- Machine Jams:
- Clear the obstruction: Turn off the machine and carefully remove any product or film that is causing the jam.
- Check the conveyor system: Ensure the conveyor belts and rollers are properly aligned and functioning.
- Uneven Shrinkage:
- Check the tunnel temperature: Ensure the temperature is consistent throughout the shrink tunnel.
- Adjust the product positioning: Ensure the product is centered in the shrink tunnel.
- Inspect the airflow: Check for any obstructions to the airflow within the shrink tunnel.
Factors to Consider When Choosing a Shrink Wrap Machine for Food
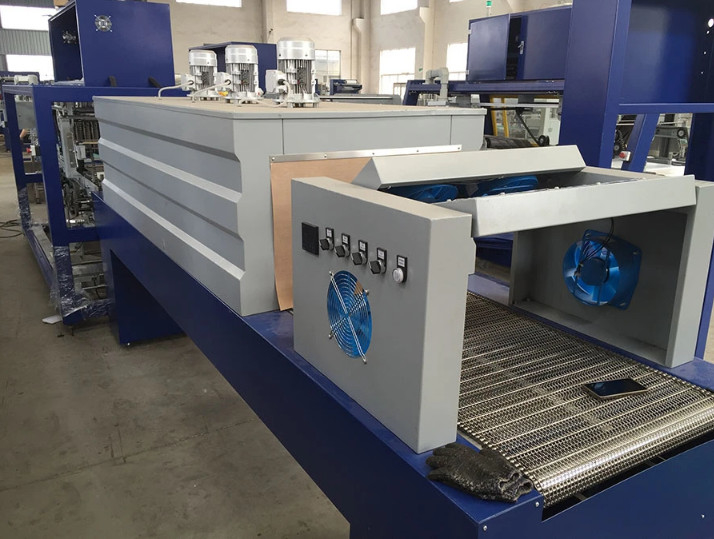
Selecting the right shrink wrap machine is crucial for efficient and safe food packaging. Several factors must be carefully evaluated to ensure the machine meets the specific needs of a food processing operation, impacting everything from packaging speed and product integrity to compliance with food safety regulations. A thoughtful approach to machine selection minimizes waste, maximizes productivity, and protects consumer health.
Machine Speed and Packaging Volume Suitability
The operational speed of a shrink wrap machine is directly related to the volume of food products being packaged. Matching the machine’s capabilities to production demands is critical for avoiding bottlenecks and ensuring efficient workflow.
- Production Volume: Assess the average and peak packaging volume. Consider the number of products packaged per hour, day, or week. A low-volume operation might be well-served by a manual or semi-automatic machine, while high-volume production necessitates a fully automatic, high-speed system.
- Machine Speed Specifications: Review the machine’s stated packaging speed, usually expressed in packages per minute (PPM) or packages per hour (PPH). Verify these figures against actual production runs to ensure the machine can keep pace with the packaging demands.
- Scalability: Consider future growth. Choosing a machine with a slightly higher capacity than current needs allows for expansion without immediate replacement.
- Example: A small bakery producing a few hundred loaves of bread daily might use a semi-automatic L-sealer. In contrast, a large-scale frozen food manufacturer, packaging thousands of meals per hour, would require a high-speed, automated shrink wrap system.
Machine Size, Footprint, and Available Space
The physical dimensions of a shrink wrap machine and the available space in the packaging area are essential considerations. An oversized machine can obstruct workflow, while an undersized one may limit production capacity.
- Footprint: Measure the available space in the packaging area, accounting for the machine’s dimensions and required operating space for operators and material handling.
- Machine Dimensions: Note the machine’s length, width, and height. Consider whether the machine can fit through doorways and maneuver into the packaging area.
- Ergonomics: Ensure sufficient space for operators to move around the machine comfortably and safely.
- Accessibility: Factor in accessibility for maintenance, cleaning, and troubleshooting.
- Example: A compact food stall might require a small, countertop shrink wrap machine, while a large food processing plant has the space for a large-scale, automated system with integrated conveyors and tunnels.
Budget Considerations and Return on Investment (ROI)
The initial investment in a shrink wrap machine, as well as ongoing operational costs, must align with the allocated budget and anticipated return on investment. A cost-benefit analysis is essential.
- Purchase Price: The initial cost of the machine varies widely depending on its features, automation level, and brand.
- Operational Costs: Factor in energy consumption, film costs, labor costs, and maintenance expenses.
- Maintenance and Repair: Consider the costs of routine maintenance, spare parts, and potential repairs. Research the availability and cost of service contracts.
- ROI Calculation: Estimate the payback period by calculating the savings in labor, materials, and waste reduction. Increased production efficiency also contributes to ROI.
- Example: A company invests in an automated shrink wrap system. While the initial cost is higher, the system reduces labor costs, minimizes film waste, and increases production speed, resulting in a quicker return on investment compared to a manual system.
Features for Food Safety and Hygiene
Maintaining strict hygiene standards is paramount in food packaging. The chosen shrink wrap machine must incorporate features that facilitate easy cleaning, prevent contamination, and ensure product safety.
- Food-Grade Materials: Ensure that all components in contact with food are made of food-grade materials, such as stainless steel or food-safe plastics, that are non-toxic, corrosion-resistant, and easy to clean.
- Easy-to-Clean Design: The machine should have a design that minimizes crevices and hard-to-reach areas where food particles and bacteria can accumulate. Removable parts, such as sealing jaws and conveyors, should be easily accessible for cleaning.
- Washdown Capability: Look for machines with washdown capabilities, allowing for thorough cleaning with water and sanitizing agents. This is crucial for maintaining a hygienic environment.
- Sealing Integrity: The machine must provide a reliable seal to prevent contamination and preserve the product’s shelf life.
- Compliance: The machine should comply with relevant food safety regulations and standards, such as those set by the FDA (in the United States) or equivalent bodies in other regions.
- Example: A machine designed for packaging ready-to-eat meals will have smooth, easily cleanable surfaces and a washdown-compatible design to prevent bacterial growth and cross-contamination.
Comparative Features of Shrink Wrap Machines
The following table provides a comparative overview of key features to consider when selecting a shrink wrap machine.
Feature | Manual Machines | Semi-Automatic Machines | Automatic Machines | High-Speed Automatic Machines |
---|---|---|---|---|
Packaging Speed | Low (e.g., <10 PPM) | Moderate (e.g., 10-30 PPM) | High (e.g., 30-60 PPM) | Very High (e.g., >60 PPM) |
Automation Level | Manual sealing and shrinking | Automatic sealing, manual product feeding and shrinking | Automatic sealing, product feeding, and shrinking | Fully automated, including product feeding, sealing, shrinking, and often labeling |
Footprint | Small | Moderate | Large | Very Large |
Labor Requirements | High | Moderate | Low | Very Low |
Initial Cost | Lowest | Moderate | High | Highest |
Suitable for | Low-volume production, small businesses | Medium-volume production, businesses with moderate packaging needs | High-volume production, businesses with large packaging runs | Very high-volume production, industrial-scale food processing plants |
Food Safety Features | Basic, may require manual cleaning | Better cleaning features, may have some washdown capabilities | Improved hygiene, washdown capability, and food-grade materials | Highest hygiene standards, advanced washdown features, and food-grade materials |
Examples | L-sealers, heat guns | L-sealers with shrink tunnels | Continuous motion sealers with shrink tunnels | Inline shrink wrappers with integrated conveyors and labeling systems |
The Role of Shrink Wrap in Food Safety and Hygiene
Shrink wrapping plays a crucial role in maintaining food safety and hygiene standards throughout the food supply chain. By providing a protective barrier, it minimizes the risk of contamination, extends shelf life, and helps ensure that food products reach consumers in optimal condition. This section explores the specific ways shrink wrapping contributes to food safety, detailing its benefits and outlining best practices for its implementation.
Maintaining Food Safety Standards with Shrink Wrap
Shrink wrapping is a key component in adhering to stringent food safety standards. It creates a tamper-evident seal that protects food from external contaminants, such as bacteria, viruses, and physical debris. This protection is critical in preventing foodborne illnesses and maintaining the integrity of the food product.
Preventing Contamination and Spoilage Through Shrink Wrapping
Shrink wrapping acts as a barrier against various factors that can lead to food contamination and spoilage. This includes:
- Physical Contamination: The film provides a physical barrier, preventing the entry of dust, dirt, insects, and other foreign objects that could contaminate the food.
- Microbial Contamination: By sealing the food, shrink wrap limits exposure to microorganisms, such as bacteria and mold, which can cause spoilage and health hazards. This is especially crucial for perishable items.
- Oxygen Exposure: Many shrink wrap films are designed to minimize oxygen permeability. This helps to slow down oxidation processes that can degrade food quality and reduce shelf life.
- Moisture Loss: Shrink wrapping can prevent moisture loss, which is important for maintaining the texture and appearance of certain foods.
Importance of Using Food-Grade Shrink Wrap Materials
The selection of appropriate materials is paramount in food packaging. Using food-grade shrink wrap materials ensures that the packaging itself does not pose a health risk. These materials are specifically designed to be inert and non-toxic, meaning they will not leach harmful chemicals into the food.
Food-grade shrink wrap materials must comply with regulations set by food safety authorities, such as the Food and Drug Administration (FDA) in the United States or the European Food Safety Authority (EFSA).
These regulations specify the types of polymers that are approved for food contact and set limits on the migration of any substances from the packaging into the food. Common food-grade materials include polyethylene (PE), polypropylene (PP), and polyvinyl chloride (PVC).
Adhering to Food Safety Regulations During the Shrink Wrapping Process
To ensure that the shrink wrapping process complies with food safety regulations, several guidelines must be followed:
- Material Selection: Always use food-grade shrink wrap films that are approved for direct food contact.
- Equipment Hygiene: Regularly clean and sanitize the shrink wrap machine to prevent the buildup of food residue and potential cross-contamination.
- Temperature Control: Monitor and maintain the correct sealing and shrinking temperatures to ensure a proper seal without damaging the food or packaging. Excessive heat can degrade the packaging or even the food itself.
- Proper Storage: Store shrink wrap materials in a clean, dry environment, away from potential contaminants.
- Employee Training: Train employees on proper handling procedures, including the use of gloves and other protective equipment, to minimize the risk of contamination.
- Regular Inspections: Conduct regular inspections of the packaging process to identify and address any potential issues, such as improper seals or damaged packaging.
Shrink Wrap Machine Applications in Different Food Sectors: Shrink Wrap Machine Food
Shrink wrap machines offer versatile packaging solutions across various food sectors, providing protection, preservation, and enhanced presentation. Their adaptability makes them a valuable asset for businesses aiming to optimize packaging processes and maintain product quality. The following sections detail specific applications within key food industries.
Shrink wrapping’s ability to create a tight seal around products, protecting them from external contaminants, is especially critical in the food industry, where hygiene and shelf life are paramount. The following sections Artikel the application of shrink wrap machines in several prominent food sectors.
Get the entire information you require about chinese food in tenafly nj on this page.
Shrink Wrap Machine Applications in the Meat and Poultry Industry
In the meat and poultry industry, shrink wrap machines play a crucial role in extending shelf life, preventing freezer burn, and maintaining product integrity. The process typically involves placing meat products on trays or in pre-made containers, then wrapping them with a shrink film. The film is then exposed to heat, which causes it to shrink tightly around the product, creating a secure and visually appealing package.
“Shrink wrapping meat products is a common practice to extend their shelf life and maintain their quality. The tight seal created by the shrink film helps to prevent the growth of bacteria and other microorganisms, which can cause spoilage.”
-Source: Meat Industry Association
Shrink wrap also offers benefits beyond preservation:
- Protection from Contamination: Shrink wrap acts as a barrier against bacteria, dust, and other contaminants during storage and transportation.
- Reduced Oxygen Exposure: Minimizing oxygen exposure helps prevent oxidation, which can lead to discoloration and flavor changes in meat products.
- Enhanced Presentation: The tight, clear wrap enhances the visual appeal of the product, making it more attractive to consumers.
Shrink Wrap Machine Applications in the Bakery and Confectionery Sectors
The bakery and confectionery sectors utilize shrink wrap machines to protect products from damage, maintain freshness, and enhance their visual appeal. From individual pastries to multi-pack bakery items, shrink wrapping provides a cost-effective and efficient packaging solution. This method not only preserves product quality but also helps with portion control and brand presentation.
“Shrink wrapping is crucial for bakery items to preserve their texture and prevent them from drying out. It also protects delicate products from damage during handling and transport.”
-Source: Bakery Packaging Journal
The benefits of shrink wrapping in these sectors include:
- Moisture Retention: Shrink wrap helps to seal in moisture, preventing products like cakes and pastries from drying out.
- Protection from Physical Damage: The wrap provides a layer of protection against bumps and bruises during handling and transportation.
- Improved Shelf Life: Shrink wrapping extends the shelf life of bakery and confectionery items by creating a barrier against air and moisture.
Shrink Wrap Machine Applications in the Produce Industry
The produce industry employs shrink wrap machines to extend the shelf life of fruits and vegetables, maintain freshness, and reduce waste. Shrink wrapping helps to control moisture loss, prevent bruising, and protect produce from external contaminants. This packaging method also allows for easier handling and transportation of delicate items, reducing the risk of damage.
“Shrink wrapping produce can significantly reduce spoilage rates, leading to less waste and increased profitability for growers and retailers.”
-Source: Produce Marketing Association
Key applications in the produce industry include:
- Moisture Control: Shrink wrap helps to regulate moisture levels, preventing wilting and maintaining the crispness of produce.
- Protection from Physical Damage: The wrap provides a protective layer against bruising and other damage during handling and transportation.
- Extended Shelf Life: By slowing down the ripening process and preventing moisture loss, shrink wrapping extends the shelf life of fresh produce.
Shrink Wrap Machine Applications in the Dairy and Cheese Industry
The dairy and cheese industry utilizes shrink wrap machines to protect products from contamination, maintain freshness, and enhance their visual appeal. Shrink wrapping creates a tight seal that helps to prevent the growth of bacteria and other microorganisms, extending the shelf life of perishable dairy products. This method is particularly important for cheese, where the packaging can significantly impact the product’s flavor and texture.
“Shrink wrapping cheese helps to control moisture levels and prevent mold growth, preserving the flavor and quality of the product.”
-Source: Dairy Industry Association
Specific applications in the dairy and cheese industry include:
- Protection from Contamination: The wrap acts as a barrier against bacteria and other contaminants, maintaining product hygiene.
- Moisture Control: Shrink wrapping helps to regulate moisture levels, preventing cheese from drying out or developing unwanted textures.
- Enhanced Presentation: The tight, clear wrap enhances the visual appeal of dairy and cheese products, making them more attractive to consumers.
Shrink Wrap and Sustainability in Food Packaging
The food packaging industry is under increasing pressure to adopt more sustainable practices. Shrink wrap, while offering crucial protection and presentation for food products, has a significant environmental footprint. Understanding the impact of shrink wrap materials and exploring viable alternatives is essential for reducing waste and promoting a circular economy within the food sector.
Environmental Impact of Shrink Wrap Materials
The environmental impact of traditional shrink wrap is primarily tied to the use of petroleum-based plastics. These materials contribute to pollution throughout their lifecycle, from production to disposal.
- Resource Depletion: The extraction of crude oil, the primary raw material for many shrink wrap films, contributes to the depletion of finite natural resources.
- Greenhouse Gas Emissions: The manufacturing of plastic films, including the energy-intensive processes of refining oil and polymerization, releases significant amounts of greenhouse gases, contributing to climate change.
- Waste Generation: Conventional shrink wrap often ends up in landfills, where it can persist for hundreds of years, or in the environment, contributing to plastic pollution in oceans and ecosystems.
- Limited Recyclability: While some shrink wrap films are technically recyclable, the infrastructure for recycling them, especially in the context of food packaging (which often contains food residue), is often lacking. Contamination from food products further complicates the recycling process.
Sustainable Alternatives to Traditional Shrink Wrap Films
Several innovative alternatives to traditional, petroleum-based shrink wrap films are emerging, offering the potential to reduce the environmental impact of food packaging.
- Bio-based Plastics: Films made from renewable resources like cornstarch, sugarcane, or other plant-based materials are becoming increasingly available. These bio-based plastics can be compostable or recyclable, depending on the specific formulation.
- Compostable Films: Certain shrink wrap films are designed to break down in industrial composting facilities, returning organic matter to the soil. These films are often made from bio-based materials. It is crucial to note that home composting is not always suitable for industrial compostable films.
- Recycled Content Films: Some manufacturers are incorporating recycled plastic content into their shrink wrap films, reducing the demand for virgin plastics. This helps to close the loop on plastic waste.
- Paper-Based Alternatives: Research and development are ongoing for paper-based shrink wrap alternatives. While not yet widely available, these options hold promise for reducing the reliance on plastics.
Reducing Waste and Improving Recyclability of Shrink Wrap Packaging
Beyond the use of alternative materials, several strategies can be employed to reduce waste and improve the recyclability of shrink wrap packaging.
- Source Reduction: Optimizing the amount of shrink wrap used in packaging can minimize waste. This can involve using thinner films, designing packaging to fit products more snugly, or reducing the overall size of packaging.
- Design for Recyclability: Packaging can be designed to be easily disassembled and sorted for recycling. This includes avoiding the use of mixed materials and incorporating clear labeling to indicate the type of plastic used.
- Closed-Loop Recycling Programs: Establishing closed-loop recycling programs within the food industry can help to ensure that shrink wrap packaging is collected, processed, and reused in the production of new packaging materials.
- Consumer Education: Educating consumers about proper disposal methods, including the importance of separating recyclable materials and understanding the availability of recycling programs in their area, is critical.
Lifecycle of a Sustainable Shrink Wrap Film (Visual Representation)
The lifecycle of a sustainable shrink wrap film, such as one made from compostable materials, can be illustrated as follows:
1. Production
This stage involves the sourcing of raw materials, such as plant-based starches (e.g., cornstarch, sugarcane). These materials are cultivated, harvested, and processed to extract the starch. The starch is then converted into a polymer, which is used to manufacture the shrink wrap film. The production process utilizes energy, but ideally, the energy source is renewable to minimize the carbon footprint.
The film is manufactured with specific properties for food packaging, ensuring it meets food safety standards.
2. Packaging and Distribution
The sustainable shrink wrap film is used to package food products. The wrapped products are then distributed through the supply chain to retailers and consumers. During this stage, the packaging protects the food, preserves its quality, and helps to extend its shelf life, reducing food waste. Efficient distribution networks are crucial to minimize transportation emissions.
3. Consumption
Consumers purchase the packaged food products. After the food is consumed, the shrink wrap packaging is removed. The packaging is clearly labeled with instructions for disposal, specifying that it should be sent to an industrial composting facility.
4. Disposal and Composting
The used shrink wrap film is collected and transported to an industrial composting facility. At the facility, the film is composted under controlled conditions of temperature, humidity, and aeration. The film breaks down into organic matter, such as water, carbon dioxide, and humus, within a specified timeframe (e.g., 90 days). The resulting compost can then be used as a soil amendment, enriching the soil and supporting plant growth.
5. Benefits and Circularity
The composted material is used to fertilize fields where raw materials for the next generation of compostable films are grown. This completes the circular lifecycle. The benefits include reduced reliance on fossil fuels, reduced landfill waste, and a decrease in greenhouse gas emissions.
Outcome Summary
So, we arrive at the final curtain, the last fold of the film. The journey through the realm of shrink wrap machine food has revealed a world of precision, preservation, and potential. It’s a story of ingenuity, where science and necessity converge to safeguard the essence of our meals. The future beckons, with innovations promising even greater efficiency, sustainability, and a deeper connection to the food we consume.
Remember this: the next time you peel back that protective layer, you’re not just opening a package; you’re unveiling a testament to the power of preservation, a silent promise of quality, and a whisper of the future of food itself.