Food safe epoxy paint, a revolutionary coating, is about to transform how we think about food safety! Get ready to dive into the world of this incredible material, where durability meets hygiene, and where surfaces are not just protected but also made safer for food contact. We’ll explore its fascinating history, from its humble beginnings to its current status as a go-to solution for food-related applications.
Prepare to discover the key benefits that make it a superior choice over other coatings.
This comprehensive guide will illuminate the science behind food safe epoxy paint, detailing the strict standards and certifications that guarantee its safety. We’ll uncover the magic of its chemical composition, explaining why it’s the ultimate shield against contamination and bacterial growth. From kitchen countertops to industrial food processing equipment, we’ll uncover the amazing versatility of food safe epoxy paint and show you how it is used everywhere.
This guide will walk you through everything from choosing the right type, preparing surfaces, and applying the paint to maintaining your epoxy-coated surfaces for years to come. Let’s get started!
Introduction to Food Safe Epoxy Paint
Food safe epoxy paint serves as a crucial protective coating for surfaces that come into contact with food. Its primary function is to create a non-toxic, durable, and easily cleanable barrier, safeguarding food from contamination and preventing the leaching of harmful substances from the underlying material. This specialized paint is engineered to meet stringent health and safety standards, making it ideal for a wide range of food-related applications.The development and application of food safe epoxy paint have evolved significantly over time.
Initially, coatings used in food processing and preparation were often less sophisticated, potentially posing risks of contamination or breakdown. As the food industry prioritized hygiene and safety, the need for more advanced coatings became apparent. The emergence of epoxy resins, known for their exceptional durability and chemical resistance, marked a turning point. Through ongoing research and development, epoxy formulations were refined to eliminate toxic components and meet the stringent requirements of food contact surfaces.
This resulted in the creation of food safe epoxy paint, which has become a standard in food processing facilities, restaurants, and even home kitchens.
Key Benefits of Using Food Safe Epoxy Paint
Food safe epoxy paint offers numerous advantages over other coating options. These benefits contribute to its widespread use and preference in the food industry.
- Superior Hygiene and Safety: Food safe epoxy paint is formulated to be non-toxic and free of harmful chemicals, such as Bisphenol A (BPA), ensuring that it does not leach into food and contaminate it. This is crucial for maintaining food safety standards and preventing health risks. This property is especially important in facilities where food is prepared and handled, where even minor contamination can lead to significant health hazards.
- Exceptional Durability and Chemical Resistance: Epoxy coatings are known for their exceptional resistance to wear and tear, impacts, and abrasion. This durability is crucial in environments where surfaces are subjected to heavy use, such as food processing plants and commercial kitchens. Food safe epoxy paint also resists a wide range of chemicals, including acids, bases, and solvents commonly used in food processing and cleaning, ensuring that the coating remains intact and functional over time.
- Ease of Cleaning and Maintenance: Food safe epoxy paint creates a seamless, non-porous surface that is easy to clean and disinfect. This property is critical for preventing the buildup of bacteria, mold, and other microorganisms that can compromise food safety. The smooth surface of epoxy coatings allows for efficient cleaning and sanitization, reducing the risk of contamination and simplifying maintenance procedures.
- Excellent Adhesion: Epoxy coatings exhibit excellent adhesion to a variety of substrates, including concrete, metal, and wood. This ensures that the coating remains securely bonded to the surface, preventing delamination and maintaining its protective properties. Proper adhesion is essential for the long-term performance and effectiveness of food safe epoxy paint.
- Versatility and Customization: Food safe epoxy paint can be applied to a wide range of surfaces, including floors, walls, and equipment. It is also available in a variety of colors and finishes, allowing for customization to meet specific aesthetic and functional requirements. This versatility makes it suitable for diverse applications within the food industry.
Defining “Food Safe”
The term “food safe” is more than just a marketing buzzword; it represents a rigorous set of standards and regulations designed to protect consumers from harmful chemicals leaching into their food. This involves understanding the specific requirements and certifications that epoxy paints must meet to be considered safe for use in food-contact applications. The definition varies depending on the region and governing body.
Regional Standards and Regulations
Different regions around the world have established their own standards and regulations regarding food safety. These standards dictate the acceptable levels of chemical migration from materials into food products. Understanding these differences is crucial for manufacturers and consumers alike.The primary regulatory bodies setting these standards include:
- United States – FDA (Food and Drug Administration): The FDA regulates food contact materials under the Federal Food, Drug, and Cosmetic Act (FFDCA). Specific regulations, like those Artikeld in 21 CFR (Code of Federal Regulations) Part 175 and 177, detail the acceptable substances and limitations for materials used in food contact. These regulations specify allowable migration limits for various substances. Compliance often involves third-party testing to ensure the paint meets the requirements.
- European Union – EFSA (European Food Safety Authority): The EU employs a comprehensive approach to food safety, with the EFSA providing scientific advice and risk assessments. Regulation (EC) No 1935/2004 is the framework regulation for all food contact materials. The EU also has specific regulations, such as those related to plastics (Regulation (EU) No 10/2011), which cover epoxy resins and their use in food contact applications. These regulations emphasize the importance of ensuring that materials do not transfer substances to food at levels that could endanger human health or change the composition, taste, or odor of the food.
- Other Regions: Other countries and regions, such as Canada (Health Canada) and Australia (Food Standards Australia New Zealand), have their own regulatory frameworks. These often align with or reference the standards set by the FDA and EFSA, adapting them to local conditions and consumer needs. These bodies also conduct inspections and testing to enforce compliance.
Certifications for Food Safe Epoxy Paints
Certifications provide assurance that an epoxy paint has been tested and meets the required food safety standards. Several certifications are commonly associated with food-safe epoxy paints.
- FDA Compliance: While not a formal certification, paints often state “FDA compliant” to indicate that they meet the FDA regulations for food contact materials. This typically means the paint has been formulated with ingredients that are listed as acceptable under 21 CFR.
- NSF International Certification: NSF (formerly the National Sanitation Foundation) is a widely recognized third-party certification organization. NSF/ANSI/CAN 51 is a standard specifically for food equipment materials. Epoxy paints certified to NSF 51 have undergone rigorous testing to ensure they are safe for food contact and do not leach harmful substances. NSF certification is often preferred in the food service industry.
- Other Certifications: Other organizations may offer similar certifications based on specific regional or industry standards. The specific certification required often depends on the intended use of the paint and the regulations of the region where it will be used.
Critical Chemical Components
The composition of food-safe epoxy paints is critical to their safety. The specific chemical components must be carefully selected to minimize the risk of migration into food.
- Resins: The resin component forms the bulk of the paint and provides its protective properties. Food-safe epoxy resins are typically based on bisphenol A diglycidyl ether (BADGE) or similar compounds, but must be formulated to minimize migration. The resin’s chemical structure must be carefully considered to ensure it does not react with or leach into food.
- Hardening Agents: Hardeners initiate the curing process, which solidifies the paint. The choice of hardeners is crucial, as some can contain volatile organic compounds (VOCs) or other potentially harmful substances. Food-safe formulations typically use hardeners with low toxicity and minimal migration potential.
- Pigments: Pigments provide color and opacity to the paint. Only pigments approved for food contact applications should be used. These pigments must be chemically stable and inert to prevent them from reacting with or leaching into food.
- Additives: Various additives are used to enhance the paint’s performance, such as UV stabilizers, flow agents, and defoamers. All additives must be evaluated to ensure they are safe for food contact.
The key to food safety is the absence of harmful chemicals migrating from the paint into the food.
Food safe epoxy paints are formulated to meet stringent regulations, ensuring that they do not pose a risk to human health.
Applications of Food Safe Epoxy Paint
Food safe epoxy paint offers a versatile solution for protecting surfaces in environments where food safety is paramount. Its unique properties make it suitable for a wide array of applications, from commercial kitchens to food processing facilities. This section explores the various applications of this specialized paint, detailing the surfaces it protects and the benefits it provides.
Surfaces and Environments
Food safe epoxy paint is commonly applied to a variety of surfaces that come into contact with food or are located within food-related environments. These surfaces require a durable, non-toxic coating that can withstand frequent cleaning and exposure to various substances.The environments where food safe epoxy paint is frequently utilized include:
- Commercial Kitchens: Restaurants, cafeterias, and other food service establishments.
- Food Processing Plants: Facilities that manufacture, package, or store food products.
- Breweries and Wineries: Environments where beverages are produced and stored.
- Pharmaceutical Manufacturing: Cleanrooms and areas where pharmaceutical products are handled.
- Laboratories: Research facilities where food samples or related materials are analyzed.
- Retail Food Establishments: Bakeries, butcher shops, and grocery stores.
Specific Applications
The adaptability of food safe epoxy paint allows it to be used on a variety of surfaces. The following examples highlight some of the most common applications:
- Countertops: Epoxy paint creates a seamless, non-porous surface on countertops in kitchens and food preparation areas. This makes them easy to clean and resistant to stains and spills. Consider a commercial kitchen countertop; the smooth, durable surface facilitates efficient food preparation while adhering to strict hygiene standards.
- Food Processing Equipment: Food safe epoxy paint is used to coat equipment such as mixers, blenders, and conveyor belts. This coating protects the equipment from corrosion and prevents food particles from accumulating in hard-to-reach areas. This application is particularly important in a meat processing plant, where sanitation is critical.
- Storage Tanks: Epoxy paint provides a protective barrier for storage tanks used to hold food products, such as water, juices, or oils. The coating prevents the tanks from rusting and ensures the stored contents remain uncontaminated. A large-scale example is the storage tanks found in breweries, where the epoxy coating maintains the integrity of the beer.
- Flooring: Epoxy flooring is a common application, especially in commercial kitchens and food processing plants. The seamless, non-porous nature of the coating makes it easy to clean and sanitize, while its durability ensures it can withstand heavy foot traffic and equipment movement. Imagine a bakery, where epoxy flooring withstands the daily activity of bakers and equipment, maintaining a clean and safe environment.
- Walls and Ceilings: Food safe epoxy paint is used on walls and ceilings to create a smooth, easy-to-clean surface. This prevents the accumulation of dirt, grease, and other contaminants. For instance, in a slaughterhouse, the application of epoxy paint on walls and ceilings is crucial for maintaining a hygienic environment, reducing the risk of bacterial contamination.
Protection Against Contamination and Bacterial Growth
Food safe epoxy paint is designed to minimize the risk of contamination and bacterial growth, providing a crucial layer of protection in food-related environments. The properties of the paint contribute significantly to its effectiveness in this regard.The paint’s key protective features include:
- Non-Porous Surface: Epoxy paint creates a seamless surface that does not allow liquids or contaminants to penetrate. This prevents the growth of bacteria and mold, which thrive in porous materials.
- Chemical Resistance: Food safe epoxy paint is resistant to a wide range of chemicals, including cleaning agents and disinfectants. This allows for frequent and thorough cleaning without damaging the coating.
- Easy to Clean: The smooth, non-porous surface of epoxy paint makes it easy to clean and sanitize. This is essential for maintaining a hygienic environment and preventing the spread of bacteria.
- Antimicrobial Properties: Some food safe epoxy paints incorporate antimicrobial additives that actively inhibit the growth of bacteria and other microorganisms. These additives further enhance the paint’s ability to protect against contamination.
The combination of these features makes food safe epoxy paint an effective barrier against contamination and bacterial growth, contributing to a safer and more hygienic environment for food handling and processing.
Types of Food Safe Epoxy Paints
Understanding the different formulations of food safe epoxy paints is crucial for selecting the right product for a specific application. The choice of epoxy paint significantly impacts factors like application ease, curing time, and overall performance. Each type of epoxy paint, whether solvent-based, water-based, or solid epoxy, possesses distinct characteristics that make it suitable for different scenarios.
Finish your research with information from music city food wine festival.
Solvent-Based Epoxy Paints
Solvent-based epoxy paints are formulated using solvents to dissolve the epoxy resins and hardeners. These paints offer excellent adhesion and durability, making them a popular choice for industrial and commercial applications where a robust, chemical-resistant finish is required.
- Advantages: Solvent-based epoxies often provide superior chemical resistance compared to water-based alternatives. They tend to level out well, resulting in a smoother finish. They are generally more resistant to damage during application and curing.
- Disadvantages: The primary drawback of solvent-based epoxies is the presence of volatile organic compounds (VOCs). These VOCs can pose health risks and contribute to environmental pollution. They also have a strong odor, which can be unpleasant. Solvent-based epoxies can also take longer to dry and cure than other formulations.
- Typical Curing Times and Application Methods: Solvent-based epoxy paints typically require a longer curing time, often ranging from several days to a week or more, depending on the specific product and environmental conditions. Application typically involves using spray guns, rollers, or brushes. Proper ventilation is essential during application and curing to minimize exposure to VOCs.
Water-Based Epoxy Paints
Water-based epoxy paints utilize water as the primary solvent, offering a more environmentally friendly alternative to solvent-based formulations. They are often preferred for applications where low VOC emissions and ease of cleaning are important considerations.
- Advantages: Water-based epoxies are low in VOCs, making them safer for the environment and applicators. They generally have a lower odor than solvent-based paints. They are also easier to clean up with water and soap.
- Disadvantages: Water-based epoxies may have slightly lower chemical resistance compared to solvent-based options. They can be more sensitive to temperature and humidity during application and curing, potentially affecting the final finish.
- Typical Curing Times and Application Methods: Water-based epoxy paints usually have shorter curing times compared to solvent-based formulations, often curing within a few days. Application methods are similar to solvent-based paints, using rollers, brushes, or spray equipment. Proper ventilation is still recommended, though the risk of VOC exposure is significantly reduced.
Solid Epoxy Paints
Solid epoxy paints, also known as 100% solids epoxies, contain no solvents. They are composed entirely of epoxy resins and hardeners, offering a highly durable and chemical-resistant coating.
- Advantages: Solid epoxy paints offer exceptional durability and chemical resistance. They have zero VOC emissions, making them the most environmentally friendly option. They provide a thick, seamless coating, ideal for high-traffic areas.
- Disadvantages: Solid epoxy paints can be more challenging to apply, often requiring specialized equipment and techniques. They may have a shorter pot life, meaning they need to be applied quickly after mixing. The application can be more complex, potentially requiring professional expertise.
- Typical Curing Times and Application Methods: Solid epoxy paints typically cure within a few days, although the exact time varies based on the product and environmental factors. Application often involves specialized methods like squeegees or trowels to achieve a uniform thickness. Because of the rapid curing process, it is important to work efficiently.
Surface Preparation: Food Safe Epoxy Paint
Proper surface preparation is paramount for the successful application of food safe epoxy paint. It’s the critical foundation upon which the epoxy adheres, determining the longevity, durability, and overall performance of the coating. Neglecting this crucial step can lead to a host of problems, including poor adhesion, blistering, peeling, and ultimately, a compromised food safety environment. A well-prepared surface ensures a strong bond, allowing the epoxy to perform its protective and aesthetic functions effectively.
Importance of Surface Preparation
Surface preparation is more than just cleaning; it’s a comprehensive process that creates an ideal substrate for the epoxy to bond with. The goal is to remove contaminants, create a profile for mechanical adhesion, and ensure the surface is sound and stable. A poorly prepared surface can lead to the epoxy failing prematurely, rendering the food-safe coating ineffective and potentially hazardous.
Step-by-Step Procedure for Preparing Different Surfaces
The specific steps for surface preparation vary depending on the material being coated. However, the general principles of cleaning, abrasion, and priming remain consistent. Here’s a detailed procedure for preparing concrete, metal, and wood surfaces:
Concrete
Concrete surfaces require careful preparation to ensure proper epoxy adhesion. The presence of laitance (a weak layer of cement dust) and other contaminants can hinder the epoxy’s ability to bond.
- Cleaning: Thoroughly clean the concrete surface to remove dirt, grease, oil, and any loose debris. Use a degreaser specifically designed for concrete, followed by a thorough rinsing with clean water. Ensure the surface is completely dry before proceeding.
- Mechanical Abrasion: This step is crucial for creating a profile that allows the epoxy to mechanically bond with the concrete. Options include:
- Shot Blasting: This method uses abrasive particles propelled at high speed to remove contaminants and create a textured surface. It’s highly effective for large areas. (Imagine a specialized machine, similar to a sandblaster, but enclosed to contain the abrasive material and dust.
The machine blasts small steel balls at the concrete surface, effectively removing the top layer and creating a rough profile.)
- Grinding: Using a concrete grinder with diamond grinding pads is another option. This method is suitable for smaller areas or when shot blasting is not feasible. The grit of the grinding pads should be chosen based on the desired profile. (Picture a large, flat machine with rotating abrasive pads that grind down the concrete surface. Different grit sizes are used to achieve the desired texture.)
- Shot Blasting: This method uses abrasive particles propelled at high speed to remove contaminants and create a textured surface. It’s highly effective for large areas. (Imagine a specialized machine, similar to a sandblaster, but enclosed to contain the abrasive material and dust.
- Surface Repair: Repair any cracks, spalls, or other imperfections in the concrete. Use a concrete patching compound specifically designed for the intended environment. Allow the repairs to cure completely according to the manufacturer’s instructions.
- Priming (Optional, but often recommended): Apply a concrete primer specifically designed for epoxy coatings. Primers enhance adhesion and can help to seal the concrete, preventing outgassing (the release of trapped air and moisture) which can cause bubbles in the epoxy. Follow the primer manufacturer’s instructions for application and drying times.
Metal
Metal surfaces, especially those exposed to the elements, require meticulous preparation to remove rust, corrosion, and any existing coatings.
- Cleaning: Remove any loose rust, scale, or old paint using a wire brush, scraper, or power tool. Clean the metal surface with a metal cleaner or degreaser to remove oil, grease, and other contaminants.
- Abrasion: This is essential for creating a surface profile for epoxy adhesion. Options include:
- Sandblasting: The most effective method for removing rust and creating a rough surface. (Imagine a nozzle blasting abrasive material onto the metal, removing rust and creating a slightly rough texture.)
- Power Tool Abrasion: Using a grinder with a wire wheel or abrasive disc is a viable alternative, especially for smaller areas or when sandblasting is not practical.
- Surface Inspection: Inspect the metal for any remaining rust or imperfections. Address any issues before proceeding.
- Priming (Recommended): Apply a metal primer specifically designed for epoxy coatings. Primers enhance adhesion and provide corrosion resistance. Follow the primer manufacturer’s instructions for application and drying times.
Wood
Wood surfaces require preparation that considers the wood’s porosity and potential for moisture absorption.
- Sanding: Sand the wood surface to remove any existing coatings, smooth out imperfections, and create a slightly rough surface for epoxy adhesion. Start with a coarser grit sandpaper and progress to a finer grit.
- Cleaning: Remove all sanding dust with a tack cloth or vacuum cleaner. Ensure the surface is completely free of dust and debris.
- Moisture Content Check: Verify that the wood’s moisture content is within the acceptable range for the epoxy you are using. Excessive moisture can cause adhesion problems. A moisture meter can be used for this purpose.
- Filling (Optional): Fill any cracks, holes, or imperfections with a wood filler appropriate for the intended use. Allow the filler to dry completely and sand smooth.
- Priming (Recommended): Apply a wood primer specifically designed for epoxy coatings. Primers help to seal the wood, preventing the absorption of epoxy and promoting adhesion. Follow the primer manufacturer’s instructions for application and drying times.
Tools and Materials Required for Surface Preparation
The specific tools and materials will vary depending on the surface being prepared and the chosen methods. However, some common items are essential for all projects.
- Personal Protective Equipment (PPE): Safety glasses, gloves (chemical-resistant for degreasers and solvents), and a respirator (especially during sanding, grinding, and blasting) are crucial for protecting yourself from dust, fumes, and debris.
- Cleaning Supplies: Degreaser, cleaning solutions appropriate for the surface, clean water, and rags or cloths.
- Abrasive Tools: Depending on the method, you may need a concrete grinder, sandblaster, wire brush, scraper, sanding block, or power sander.
- Abrasives: Sandpaper (various grits), grinding pads, or abrasive blasting media.
- Surface Repair Materials: Concrete patching compound, wood filler, or metal filler, as needed.
- Primers: Primers specifically designed for the surface and the epoxy coating you intend to use.
- Mixing and Application Tools: Buckets, mixing sticks, rollers, brushes, or spray equipment, depending on the application method of the primer and epoxy.
Application Methods
Achieving a flawless, food-safe epoxy paint finish relies heavily on the application method. The choice of method significantly impacts the final appearance, durability, and overall performance of the coating. Proper technique, alongside environmental considerations, is paramount for ensuring the epoxy cures correctly and provides the intended protection.
Brushing
Brushing is a versatile application method suitable for smaller areas, detailed work, and projects where precise control is needed. It’s often preferred for edges, corners, and irregular surfaces.
- Equipment: The essential tools for brushing include high-quality brushes specifically designed for epoxy paints. Consider using natural bristle brushes for solvent-based epoxies and synthetic brushes for water-based options. A clean brush, free from loose bristles, is crucial for a smooth finish. Also, have a container for the mixed epoxy, stir sticks, and appropriate personal protective equipment (PPE) such as gloves and eye protection.
- Technique: Begin by thoroughly mixing the epoxy components according to the manufacturer’s instructions. Dip the brush into the epoxy, ensuring not to overload it, as this can lead to drips and an uneven coating. Apply the epoxy in smooth, even strokes, working in the direction of the surface grain, if applicable. Overlap each stroke slightly to avoid leaving brush marks.
Avoid excessive brushing, as this can introduce air bubbles. For vertical surfaces, apply the epoxy from top to bottom to minimize runs and sags.
- Benefits and Limitations: Brushing offers excellent control and is ideal for intricate designs or detailed work. However, it can be time-consuming for larger areas and may leave brush marks if the technique isn’t perfected. The final finish may not be as smooth as with other methods.
Rolling
Rolling is a popular method for applying food-safe epoxy paint to larger, flat surfaces. It offers a good balance of speed and coverage, making it suitable for floors, countertops, and walls.
- Equipment: The essential tools include a roller frame, a roller cover (typically a foam or microfiber roller for epoxy), a paint tray, and a clean container for mixing the epoxy. The roller cover’s nap (thickness) should be chosen based on the surface texture. A short nap roller is generally preferred for smoother surfaces, while a slightly longer nap can be used for textured surfaces.
- Technique: Mix the epoxy thoroughly according to the manufacturer’s instructions. Pour a small amount of the mixed epoxy into the paint tray. Dip the roller cover into the epoxy, ensuring it’s evenly saturated. Roll the roller on the tray’s angled surface to remove excess epoxy. Apply the epoxy to the surface in overlapping rows, maintaining a wet edge to prevent lap marks.
Work in a consistent direction, and avoid excessive pressure, which can cause air bubbles. For optimal results, apply multiple thin coats, allowing each coat to cure according to the manufacturer’s recommendations before applying the next.
- Benefits and Limitations: Rolling is faster than brushing and provides good coverage for large areas. It generally produces a smoother finish than brushing. However, it may not be suitable for intricate details or hard-to-reach areas. Achieving a perfectly smooth, bubble-free finish requires careful technique and attention to detail.
Spraying
Spraying is the most efficient method for applying food-safe epoxy paint, especially for large areas or projects requiring a high-gloss, flawless finish. This method demands careful preparation and expertise.
- Equipment: This method requires a spray gun (e.g., an HVLP or airless sprayer), a compressor (for air-powered sprayers), appropriate nozzles, a respirator, and full PPE. Ensure you have a well-ventilated spray area or booth to minimize exposure to fumes. The spray gun should be compatible with the epoxy paint being used. The type of nozzle and the spray gun settings will depend on the specific epoxy and the desired finish.
- Technique: Thoroughly mix the epoxy components according to the manufacturer’s instructions. Strain the epoxy through a filter to remove any particles that could clog the spray gun. Adjust the spray gun settings (e.g., air pressure, fluid flow) to achieve the desired spray pattern and coverage. Apply the epoxy in thin, even coats, overlapping each pass slightly. Maintain a consistent distance between the spray gun and the surface.
Avoid applying too much epoxy in a single coat, as this can lead to runs, sags, and an uneven finish. Allow each coat to cure completely before applying the next.
- Benefits and Limitations: Spraying provides the smoothest, most even finish and is the fastest method for large areas. It’s ideal for achieving a high-gloss appearance. However, spraying requires specialized equipment, a well-ventilated area, and experience. Overspray can be a concern, and proper masking and protection are essential. It may also be more difficult to control the thickness of the coating, potentially leading to issues like runs or sags if not applied correctly.
Application Process Guide: Temperature and Humidity Considerations
Environmental conditions play a critical role in the successful application and curing of food-safe epoxy paint. Both temperature and humidity can significantly impact the epoxy’s viscosity, working time, cure time, and final appearance.
- Temperature: The ideal temperature range for applying epoxy paint typically falls between 70°F (21°C) and 80°F (27°C). Applying epoxy outside this range can lead to problems. If the temperature is too low, the epoxy may not cure properly, resulting in a soft or tacky finish. If the temperature is too high, the epoxy may cure too quickly, leading to a shorter working time and potentially causing bubbles or other imperfections.
Always consult the manufacturer’s recommendations for the specific epoxy product.
- Humidity: High humidity can also affect the curing process. Excessive moisture in the air can interfere with the epoxy’s ability to cure correctly, potentially leading to a cloudy or uneven finish. Aim for a relative humidity level below 80%. If the humidity is too high, consider using a dehumidifier to reduce the moisture content in the air.
- Process:
- Surface Preparation: Ensure the surface is properly prepared, clean, and dry before applying the epoxy. This includes cleaning, sanding (if necessary), and degreasing.
- Mixing: Thoroughly mix the epoxy components according to the manufacturer’s instructions, paying close attention to the recommended mixing ratio and pot life.
- Application: Choose the appropriate application method (brushing, rolling, or spraying) based on the project’s requirements. Apply the epoxy in thin, even coats, following the recommended techniques for each method.
- Curing: Allow each coat to cure completely according to the manufacturer’s instructions, considering the temperature and humidity levels. Avoid disturbing the surface during the curing process.
- Inspection: After the final coat has cured, inspect the surface for any imperfections. If necessary, sand and reapply the epoxy to achieve the desired finish.
Curing and Drying Process
Proper curing and drying are critical for food safe epoxy paint to achieve its intended properties and ensure its safety for use with food. These processes transform the liquid epoxy into a hard, durable, and non-toxic surface. Failure to cure and dry correctly can compromise the paint’s food-safe status, leading to potential health hazards and reduced performance.
Importance of Proper Curing and Drying
The curing and drying stages are essential for the epoxy paint to reach its full potential.
- Chemical Reaction Completion: Curing allows the epoxy resin and hardener to fully react, creating a strong, cross-linked polymer structure. This process is irreversible and dictates the final properties of the paint. Without complete curing, the paint may remain soft, tacky, and susceptible to damage.
- Solvent Evaporation: Drying involves the evaporation of solvents that are often present in epoxy paint formulations. These solvents must completely evaporate for the paint to harden and become non-toxic. Trapped solvents can affect the paint’s appearance, durability, and food safety.
- Achieving Food-Safe Properties: Proper curing and drying are crucial for the paint to achieve its food-safe characteristics. This includes the paint’s ability to resist leaching of chemicals into food and its resistance to microbial growth.
- Durability and Performance: The curing and drying processes contribute to the paint’s hardness, abrasion resistance, chemical resistance, and overall longevity. These properties are essential for ensuring the paint can withstand the rigors of food handling and cleaning.
Factors Affecting Curing Time, Food safe epoxy paint
Several factors influence the curing time of food safe epoxy paint. Understanding these factors is essential for ensuring the paint cures correctly and achieves optimal performance.
- Temperature: Temperature is a primary factor affecting curing time. Higher temperatures generally accelerate the chemical reaction, shortening the curing time. Conversely, lower temperatures slow down the reaction, extending the curing time. The manufacturer’s instructions usually specify the optimal temperature range for curing. For instance, a typical epoxy paint might cure in 24 hours at 77°F (25°C), but could take several days or even weeks at lower temperatures.
- Humidity: High humidity can also affect the curing process. Excessive moisture in the air can interfere with the chemical reaction, potentially leading to incomplete curing or a cloudy finish. It is important to apply epoxy paint in a well-ventilated area with controlled humidity levels.
- Type of Epoxy: Different epoxy formulations have varying curing times. Some are designed to cure quickly, while others are formulated for slower, more controlled curing. The type of hardener used also plays a role, with some hardeners designed for fast curing and others for slow curing.
- Film Thickness: The thickness of the paint film can impact curing time. Thicker coats generally require more time to cure completely than thinner coats, as the solvents need more time to evaporate.
- Ventilation: Adequate ventilation is essential for removing solvents released during the drying process. Poor ventilation can trap solvents, slowing down the curing process and potentially affecting the paint’s final properties.
Timeline for the Curing Process
The curing process typically involves several stages, each with its own characteristics and expected results.
- Initial Cure (Tack-Free Time): This is the time it takes for the surface to become tack-free, meaning it no longer feels sticky to the touch. This stage usually occurs within a few hours, depending on the temperature and the epoxy formulation. For example, some fast-curing epoxies might become tack-free in as little as 4 hours at 77°F (25°C).
- Handle Time: This is the point at which the coating is hard enough to handle or walk on without causing damage. This stage typically occurs within 24 hours, although this can vary.
- Full Cure: Full cure represents the point at which the epoxy has reached its maximum hardness, chemical resistance, and other performance properties. This stage usually takes several days, or even weeks, to complete. The exact time depends on the factors mentioned above. A food safe epoxy might reach 90% of its full cure within 7 days at 77°F (25°C) but might take 14-21 days for complete curing.
- Complete Drying: Complete drying is the stage when all solvents have evaporated from the coating. While the epoxy might be fully cured before this stage, complete drying ensures the paint is non-toxic and ready for food contact. This process may take up to several weeks.
It is important to consult the manufacturer’s instructions for specific curing times and conditions for the particular food safe epoxy paint being used.
Maintenance and Cleaning
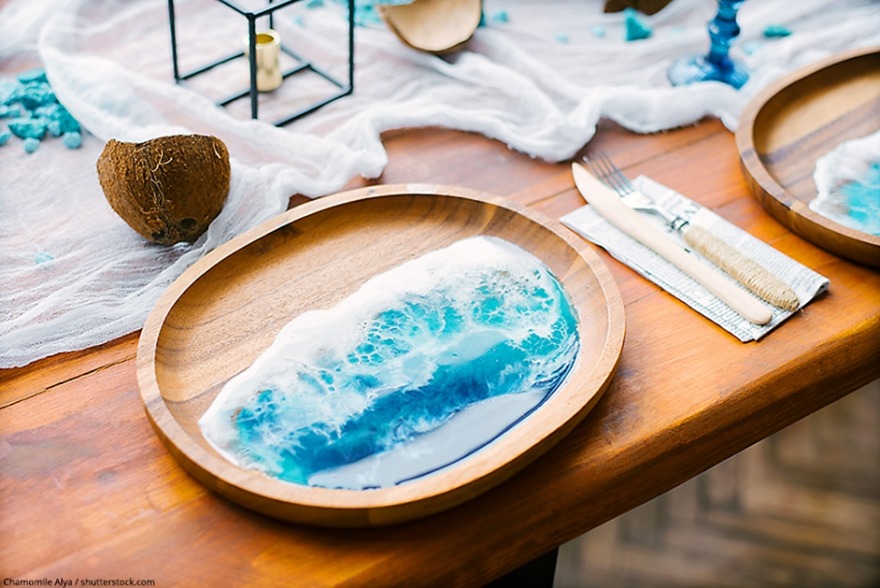
Maintaining surfaces coated with food safe epoxy paint is crucial for preserving their integrity, extending their lifespan, and ensuring continued compliance with food safety regulations. Proper cleaning and maintenance practices prevent the build-up of bacteria, stains, and other contaminants, thus safeguarding the health of consumers and the longevity of the coating. This section provides guidelines for the effective cleaning and maintenance of food safe epoxy painted surfaces.
Cleaning Products and Techniques
Selecting the appropriate cleaning products and employing the correct techniques are essential for maintaining the appearance and functionality of food safe epoxy coatings. Using harsh chemicals or abrasive materials can damage the epoxy surface, leading to discoloration, scratching, and ultimately, a shorter lifespan.
- Recommended Cleaning Products: The best cleaning agents for food safe epoxy coatings are generally mild and pH-neutral. Using these products ensures the coating remains intact and free from damage. Examples include:
- Mild Soap and Water: A solution of warm water and a gentle dish soap is often sufficient for routine cleaning. This is a safe and effective option for most spills and everyday messes.
- Non-Abrasive Cleaners: Avoid abrasive cleaners, as they can scratch the epoxy surface. Instead, opt for non-abrasive cleaners specifically designed for use on epoxy or similar surfaces.
- Diluted Bleach Solution (for disinfection): In situations requiring disinfection, such as after contact with raw meat or other potentially hazardous substances, a diluted bleach solution (e.g., 1 part bleach to 10 parts water) can be used. Rinse thoroughly with clean water after disinfecting.
- Cleaning Techniques: Proper cleaning techniques involve the correct application of cleaning products and the use of appropriate tools.
- Washing: Wash the surface with the chosen cleaning solution using a soft sponge, microfiber cloth, or mop. Avoid using abrasive scrub brushes or scouring pads.
- Rinsing: Rinse the surface thoroughly with clean water to remove any residue from the cleaning solution. Leaving residue can lead to a dull appearance or potential food safety issues.
- Drying: Dry the surface completely with a clean, soft cloth or allow it to air dry. Standing water can leave water spots or contribute to the growth of microorganisms.
- Products to Avoid: Certain cleaning products can damage food safe epoxy coatings.
- Abrasive Cleaners: Scouring powders, abrasive pads, and other abrasive cleaners can scratch the surface, compromising its integrity.
- Solvents: Strong solvents like acetone, paint thinners, and other similar chemicals can dissolve or damage the epoxy coating.
- Acidic Cleaners: Acidic cleaners can etch the surface, leading to discoloration and damage.
Lifespan and Extension Strategies
The lifespan of food safe epoxy paint can vary depending on factors like the quality of the epoxy, the surface preparation, the application process, and the level of use and maintenance. With proper care, these coatings can last for many years, even in high-traffic environments.
- Typical Lifespan: The lifespan of a food safe epoxy coating typically ranges from 5 to 10 years or even longer, depending on the specific application and environmental conditions. Regular cleaning and maintenance significantly extend this period.
- Extending Lifespan: Several strategies can be employed to extend the lifespan of a food safe epoxy coating.
- Regular Cleaning: Frequent cleaning, as described above, prevents the build-up of contaminants that can degrade the coating over time.
- Prompt Spill Cleanup: Immediately cleaning up spills of food, liquids, or other substances prevents staining and potential damage.
- Avoiding Heavy Impacts: Protecting the surface from heavy impacts or sharp objects prevents scratches, chips, and other damage.
- UV Protection (for outdoor applications): If the epoxy coating is exposed to direct sunlight, consider using a UV-resistant topcoat to prevent yellowing and degradation.
- Periodic Inspections: Regularly inspect the coating for signs of wear and tear, such as scratches, chips, or discoloration. Addressing any issues promptly can prevent them from escalating into more significant problems.
- Real-World Examples: In commercial kitchens, where food safe epoxy coatings are common on floors and countertops, coatings properly maintained can last over a decade. Conversely, in environments with heavy traffic and infrequent cleaning, the lifespan can be significantly reduced. For example, a restaurant with a poorly maintained epoxy floor might require recoating within 3-5 years, whereas a well-maintained floor in a similar establishment could last twice as long.
“Proper maintenance is an investment, not an expense.”
Safety Precautions
Working with food-safe epoxy paint requires careful attention to safety to protect yourself and others from potential hazards. Epoxy resins and hardeners can pose health risks if not handled properly. Adhering to safety protocols ensures a safe and successful application process.
Personal Protective Equipment (PPE) Requirements
Employing appropriate PPE is crucial when handling epoxy paints. This equipment acts as a barrier between you and potentially harmful substances.
- Respirator: A respirator is essential to prevent the inhalation of epoxy fumes and dust particles. Use a respirator with an organic vapor cartridge and a particulate filter. Ensure the respirator fits properly and is used in a well-ventilated area. The type of respirator needed depends on the specific epoxy and its volatility; consult the manufacturer’s safety data sheet (SDS) for recommendations.
For instance, if a painter is working in a confined space with poor ventilation, a full-face respirator with a supplied air system might be necessary to ensure adequate respiratory protection.
- Gloves: Wear chemical-resistant gloves, such as nitrile or neoprene, to protect your skin from direct contact with the epoxy and hardener. Epoxy can cause skin irritation and allergic reactions. Gloves should be replaced immediately if they become torn or contaminated. For example, a food service worker applying epoxy to a countertop would need to change gloves frequently to prevent any potential contamination of the food preparation surface.
- Eye Protection: Safety glasses or goggles are mandatory to protect your eyes from splashes, fumes, and dust. Consider using goggles with side shields for maximum protection. A full-face shield offers the best protection if there is a risk of significant splashing. For instance, a contractor working on a large epoxy flooring project might choose a full-face shield to protect against the large volumes of epoxy being applied.
- Protective Clothing: Wear long sleeves, pants, and an apron or coveralls to prevent epoxy from contacting your skin. Consider disposable coveralls for easier cleanup. Choose clothing made of materials that resist epoxy penetration. For example, an individual applying epoxy to a table should wear long sleeves and pants to avoid skin exposure.
Potential Hazards and Mitigation Strategies
Understanding the potential hazards associated with epoxy paints and implementing appropriate mitigation strategies is key to ensuring safety.
- Skin and Eye Irritation: Epoxy resins and hardeners can cause skin irritation, allergic reactions, and eye damage.
- Mitigation: Wear appropriate PPE, including gloves, eye protection, and protective clothing. Avoid direct skin contact. If contact occurs, immediately wash the affected area with soap and water. Flush eyes with water for at least 15 minutes and seek medical attention if irritation persists.
For example, a person experiencing a skin rash after working with epoxy should immediately wash the affected area and consult a doctor if the rash does not subside.
- Mitigation: Wear appropriate PPE, including gloves, eye protection, and protective clothing. Avoid direct skin contact. If contact occurs, immediately wash the affected area with soap and water. Flush eyes with water for at least 15 minutes and seek medical attention if irritation persists.
- Respiratory Irritation: Epoxy fumes can irritate the respiratory system, causing coughing, wheezing, and difficulty breathing.
- Mitigation: Work in a well-ventilated area or use a respirator with an organic vapor cartridge and a particulate filter. Avoid breathing in fumes. If respiratory irritation occurs, move to fresh air and seek medical attention if symptoms worsen. For example, a worker experiencing difficulty breathing while applying epoxy should immediately move to an area with fresh air and seek medical attention if the condition does not improve.
- Flammability: Some epoxy products and their solvents are flammable.
- Mitigation: Keep epoxy products away from heat, sparks, and open flames. Provide adequate ventilation to prevent the buildup of flammable vapors. Store epoxy products in a cool, well-ventilated area, away from sources of ignition. For example, a person should never smoke while working with epoxy, and all potential ignition sources should be eliminated.
- Sensitization: Repeated exposure to epoxy can lead to sensitization, causing allergic reactions.
- Mitigation: Minimize exposure by using proper PPE and working in a well-ventilated area. If you develop an allergic reaction, discontinue use and consult a doctor. For example, if an individual repeatedly experiences skin rashes or respiratory irritation after working with epoxy, they should discontinue use and consult with a medical professional.
- Ingestion: Epoxy products are harmful if swallowed.
- Mitigation: Do not eat, drink, or smoke while working with epoxy. Keep epoxy products out of reach of children and pets. If epoxy is ingested, seek immediate medical attention. For example, if a child accidentally ingests epoxy, call emergency services immediately.
- Improper Disposal: Improper disposal of epoxy waste can harm the environment.
- Mitigation: Follow local regulations for the disposal of epoxy waste. Allow liquid epoxy to fully cure before disposal. Consult the manufacturer’s SDS for disposal instructions. For example, a person should never pour uncured epoxy down the drain; instead, they should follow local regulations and the manufacturer’s guidelines for proper disposal.
Troubleshooting Common Issues
Applying food safe epoxy paint can sometimes present challenges. Understanding and addressing these issues promptly is crucial to achieving a durable, aesthetically pleasing, and, most importantly, safe finish. This section Artikels common problems encountered during application and use, providing solutions and preventative measures to ensure a successful outcome.
Bubbling in Epoxy Paint
Bubbles can appear during epoxy application, marring the surface and potentially compromising the paint’s integrity.The causes of bubbling can be traced to several factors:
- Air Entrapment: Air can be trapped within the epoxy mixture during mixing, especially if mixed too vigorously or with a drill at high speed.
- Surface Porosity: The substrate itself may have tiny pores that release air during the epoxy curing process.
- Temperature Issues: Rapid temperature changes or applying epoxy in excessively hot conditions can accelerate the curing process, trapping air before it can escape.
Solutions for eliminating bubbles include:
- Mixing Techniques: Mix epoxy slowly and deliberately, using a mixing stick to avoid incorporating air. A slow, even mixing action is preferable to a fast, aggressive one.
- De-gassing: Allow the mixed epoxy to sit for a few minutes to allow air bubbles to rise to the surface and dissipate before application. For larger projects, a vacuum chamber can be used to de-gas the mixture before application.
- Surface Preparation: Properly prepare the surface by sealing porous materials before applying epoxy. This prevents air from being released during the curing process.
- Heat Gun or Torch: After application, gently pass a heat gun or propane torch (with a broad, diffused flame) over the surface to pop any remaining bubbles. Keep the heat source moving and avoid concentrating heat in one spot.
Peeling and Delamination
Peeling or delamination occurs when the epoxy paint separates from the substrate. This can compromise both the appearance and the protective qualities of the coating.Common causes include:
- Improper Surface Preparation: Inadequate cleaning, sanding, or priming of the surface before applying epoxy.
- Contamination: The presence of dust, grease, oil, or other contaminants on the surface, which prevents the epoxy from bonding properly.
- Incorrect Mixing Ratio: Using an incorrect ratio of resin to hardener can weaken the epoxy and affect its adhesion.
- Environmental Factors: Applying epoxy in high humidity or extreme temperatures can interfere with the curing process and lead to poor adhesion.
Solutions include:
- Thorough Surface Preparation:
- Clean the surface meticulously to remove any contaminants.
- Sand the surface to create a profile for the epoxy to adhere to.
- Prime the surface if recommended by the epoxy manufacturer.
- Correct Mixing: Carefully measure and mix the resin and hardener according to the manufacturer’s instructions. Use accurate measuring tools.
- Proper Application Conditions: Apply epoxy in a clean, dry environment within the recommended temperature and humidity ranges.
- Multiple Coats: Applying multiple thin coats, allowing each coat to cure fully before applying the next, can improve adhesion and reduce the risk of peeling.
Discoloration and Yellowing
Over time, food safe epoxy paint can sometimes discolor or yellow, diminishing its aesthetic appeal.The causes of discoloration include:
- UV Exposure: Prolonged exposure to ultraviolet (UV) light can cause epoxy to yellow or fade.
- Chemical Exposure: Contact with certain chemicals, solvents, or cleaning agents can also lead to discoloration.
- Incorrect Mixing Ratio: Improper mixing can lead to incomplete curing, which can affect color stability.
- Material Quality: Using low-quality epoxy or products not specifically formulated for food safety and UV resistance.
Solutions include:
- UV Protection: Choose epoxy formulations with UV stabilizers or apply a UV-resistant topcoat, especially for projects exposed to sunlight.
- Avoid Harsh Chemicals: Use mild, pH-neutral cleaning agents to clean epoxy surfaces.
- Proper Mixing: Ensure the resin and hardener are mixed thoroughly and according to the manufacturer’s instructions.
- Quality Materials: Select high-quality, food-safe epoxy products from reputable manufacturers.
Craters and Fish Eyes
Craters, or fish eyes, are small, circular imperfections in the epoxy surface, which can be caused by contamination or surface tension issues.The causes of craters and fish eyes are:
- Surface Contamination: The presence of silicone, oil, wax, or other contaminants on the surface, which prevents the epoxy from flowing evenly.
- Surface Tension: Differences in surface tension between the epoxy and the substrate can also lead to cratering.
Solutions for addressing craters and fish eyes include:
- Surface Cleaning: Clean the surface thoroughly to remove any contaminants before applying epoxy. Use a degreaser or solvent appropriate for the substrate.
- Anti-Cratering Additives: Add a small amount of a fisheye flow additive to the epoxy mixture. These additives reduce surface tension and help the epoxy flow more smoothly.
- Re-coating: If craters appear, allow the epoxy to cure fully, then sand the surface lightly and re-coat with a fresh layer of epoxy.
Cost Considerations
The financial implications of using food safe epoxy paint are a crucial factor in decision-making. Understanding the various cost components, comparing them to alternatives, and performing a cost-benefit analysis allows for informed choices that balance safety, performance, and budget. This section delves into these critical aspects, providing a comprehensive overview of the financial considerations associated with food safe epoxy paint.
Breakdown of Costs
The overall cost of implementing food safe epoxy paint involves several contributing factors, each playing a significant role in determining the total expenditure. A thorough understanding of these elements is essential for accurate budgeting and project planning.
- Materials: This is the most significant cost component, including the epoxy resin, hardener, pigments (if any), and any necessary additives. The price varies based on the brand, quality, and quantity needed. High-quality, food-grade epoxy resins tend to be more expensive than standard epoxy. For example, a gallon of high-quality food-safe epoxy can range from $75 to $200 or more, depending on the specific formulation and manufacturer.
- Labor: Labor costs depend on the project’s complexity, the size of the surface area, and the experience level of the applicator. Professional application will cost more than a DIY approach. Skilled labor is crucial for achieving a flawless finish and ensuring the epoxy meets food safety standards. The labor cost can range from $50 to $150+ per hour, depending on location and expertise.
- Equipment: The equipment needed includes mixing tools (drills with mixing attachments), application tools (rollers, brushes, squeegees), personal protective equipment (PPE) like respirators, gloves, and eye protection, and potentially, surface preparation tools like grinders or sanders. The cost of these items can vary widely. Basic mixing tools and application tools can be relatively inexpensive, while specialized equipment can significantly increase the overall cost.
- Surface Preparation: Proper surface preparation is critical for the epoxy’s adhesion and longevity. This involves cleaning, sanding, and priming the surface. The cost depends on the existing surface condition and the level of preparation required. This can include the cost of cleaning solutions, sandpaper, and primer.
- Overhead and Other Costs: Additional costs may include waste disposal fees, travel expenses (for professionals), and potential contingency funds for unexpected issues. These can add to the overall project budget.
Cost Comparison with Other Coating Options
Food safe epoxy paint is not the only option available for coating surfaces in food-related environments. Comparing its cost with alternative coatings helps to assess its value proposition.
- Stainless Steel: Stainless steel is a highly durable and hygienic option, but it can be more expensive than epoxy, especially for large surfaces or complex shapes. The cost of stainless steel can be significantly higher, depending on the grade and thickness of the material.
- Polyurethane Coatings: Polyurethane coatings offer good chemical resistance and durability. They may be less expensive than food-safe epoxy in some cases, but they might not have the same level of food safety certification.
- Ceramic Tile: Ceramic tiles are a cost-effective and durable option, but grout lines can harbor bacteria. The cost of tiles and installation varies depending on the type and size of the tiles.
- Acrylic Coatings: Acrylic coatings are generally less expensive than epoxy but may not be as durable or resistant to chemicals and abrasion, particularly in high-traffic areas. They are also less likely to be certified as food safe.
To illustrate a comparison, consider the following simplified example for coating a 100 sq. ft. countertop:
Coating Option | Estimated Material Cost | Estimated Labor Cost | Total Estimated Cost | Pros | Cons |
---|---|---|---|---|---|
Food Safe Epoxy | $150 – $300 | $200 – $500 (DIY or Professional) | $350 – $800 | High durability, food-safe certification, seamless finish | Higher material cost, requires careful application |
Polyurethane Coating | $100 – $250 | $150 – $400 (DIY or Professional) | $250 – $650 | Good durability, chemical resistance | May not be fully food-safe certified, potential for off-gassing during application |
Stainless Steel | $500 – $1000+ | $300 – $700+ (Installation) | $800 – $1700+ | Extremely durable, hygienic | High initial cost, complex installation, not seamless |
Cost-Benefit Analysis
A cost-benefit analysis helps to evaluate the long-term value of food safe epoxy paint compared to other options. This involves considering both the initial costs and the ongoing benefits.
- Benefits:
- Durability: Epoxy coatings are highly durable and can withstand heavy use, reducing the need for frequent repairs or replacements. This results in cost savings over time.
- Hygiene: Food-safe epoxy creates a seamless, non-porous surface that is easy to clean and resistant to bacteria growth, reducing the risk of contamination and associated costs.
- Longevity: Epoxy coatings have a long lifespan, reducing the need for frequent recoating, unlike some alternatives that may require more regular maintenance.
- Chemical Resistance: Epoxy’s resistance to chemicals and spills can protect the underlying surface, reducing damage and repair costs.
- Applications:
- Commercial Kitchens: In commercial kitchens, the cost of food-safe epoxy for flooring and countertops is often offset by reduced cleaning costs, improved hygiene, and compliance with health regulations.
- Food Processing Plants: Food processing plants benefit from epoxy’s durability, chemical resistance, and ease of cleaning, which minimizes downtime and maintenance expenses.
- Residential Kitchens: While the initial cost might be higher, the long-term benefits of durability, hygiene, and aesthetic appeal make epoxy a worthwhile investment for homeowners.
- Cost-Benefit Example: Consider a commercial kitchen floor.
- Scenario 1: Epoxy Flooring: The initial cost might be $10 per square foot, totaling $10,000 for a 1,000 sq. ft. kitchen. Over 10 years, cleaning and maintenance costs are minimized, and the floor requires minimal repairs.
- Scenario 2: Tile Flooring: The initial cost might be $5 per square foot, totaling $5,000. However, grout lines require frequent cleaning and maintenance, and the tiles may crack or chip, requiring more frequent repairs. The long-term costs (cleaning, maintenance, and potential repairs) could easily exceed the initial cost difference.
- Formulas:
Net Present Value (NPV) = ∑ (Cash Flow / (1 + Discount Rate)^n)
Initial Investment
Where:
- Cash Flow = Annual cost savings or revenue generated
- Discount Rate = The rate used to reflect the time value of money
- n = The number of years
Return on Investment (ROI) = ((Net Profit / Cost of Investment) – 100)
Finding and Purchasing
Locating and acquiring food-safe epoxy paint is crucial for ensuring the safety and longevity of your projects. Knowing where to look and what to look for will significantly streamline your purchase and guarantee you’re using a product that meets your specific needs and safety standards. This section guides you through the process, from identifying reputable suppliers to selecting the right epoxy paint.
Where to Purchase Food Safe Epoxy Paint
Food-safe epoxy paint can be found through various channels, catering to different project scales and preferences. Knowing where to source your materials ensures you have access to the best products and customer support.
- Online Retailers: Platforms like Amazon, eBay, and specialized epoxy resin websites offer a wide selection of food-safe epoxy paints. They often provide detailed product descriptions, customer reviews, and competitive pricing. However, carefully review seller ratings and product specifications to ensure the paint meets food-safe requirements.
- Hardware Stores: Large hardware stores such as Home Depot and Lowe’s may carry food-safe epoxy paints, particularly those designed for countertops or food preparation surfaces. This offers the advantage of in-person inspection and immediate purchase, but the selection might be more limited than online options.
- Specialty Epoxy Suppliers: Dedicated epoxy resin suppliers, both online and brick-and-mortar, are a primary source. They often provide a more extensive range of products, including specialized formulations, color options, and expert advice. This is a great option for more complex projects or when seeking specific technical support.
- Industrial Supply Stores: Businesses that cater to industrial needs may also carry food-safe epoxy paints, especially those suitable for commercial kitchens or food processing facilities. This option is ideal for large-scale projects or when requiring specific performance characteristics.
Different Brands and Product Options Available
The market offers various food-safe epoxy paint brands, each with its own strengths and specializations. Understanding these options helps in selecting the most suitable product for your specific application.
Brand | Product Options | Key Features | Typical Applications |
---|---|---|---|
Stone Coat Countertops | Food Safe Epoxy, Countertop Epoxy | High-gloss finish, UV resistant, self-leveling | Countertops, bar tops, tabletops |
ProMarine Supplies | Crystal Clear Table Top Epoxy, Food Safe Epoxy Resin | Excellent clarity, bubble-free formula, scratch-resistant | Tabletops, river tables, decorative projects |
TotalBoat | TableTop Epoxy Resin, Food Safe Epoxy | High gloss, UV resistant, easy to apply | Tabletops, bar tops, and other surfaces |
FAS-COAT | Food Safe Epoxy Coating | Chemical resistant, durable, suitable for high-traffic areas | Commercial kitchens, food processing plants, food storage areas |
What to Look for When Choosing a Food Safe Epoxy Paint Product
Selecting the right food-safe epoxy paint involves careful consideration of several factors. These factors directly influence the paint’s performance, safety, and suitability for your intended use.
- Food-Safe Certification: Ensure the product is explicitly labeled as “food safe” and has certifications from reputable organizations, such as the FDA (in the United States). This certification confirms that the epoxy paint has been tested and meets the necessary safety standards for contact with food.
- VOC Content: Low VOC (Volatile Organic Compounds) content is crucial for both environmental and health reasons. Look for products with low or zero VOCs to minimize the release of harmful chemicals during application and curing.
- Durability and Hardness: Consider the paint’s durability and hardness, especially for surfaces subject to heavy use. Epoxy paints are known for their resilience, but the specific properties can vary. Check the product specifications for scratch resistance, impact resistance, and chemical resistance.
- Ease of Application: The application process can influence the final outcome. Some epoxy paints are self-leveling, which simplifies the process, while others may require more experience. Read reviews and consider the application method that best suits your skills and project requirements.
- Color and Finish Options: Epoxy paints are available in a variety of colors and finishes, from clear and transparent to solid colors and metallic effects. Choose a product that offers the aesthetic qualities you desire for your project. Consider how the finish will affect the appearance and functionality of the surface.
- Curing Time: The curing time is an important consideration, especially if you have a deadline. Some epoxy paints cure quickly, while others require several days. Consider the impact of curing time on your project timeline.
Illustrative Examples
Food-safe epoxy paint offers a transformative solution for various food preparation surfaces. This section provides illustrative examples demonstrating its application, the visual changes achieved, and the long-term performance characteristics of the coating. These examples aim to provide a clear understanding of the practical benefits and aesthetic enhancements food-safe epoxy paint delivers.
Transforming a Kitchen Countertop
The renovation of a worn kitchen countertop with food-safe epoxy paint provides a compelling illustration. Consider a countertop constructed of laminate, previously showing signs of wear and tear, including scratches, stains, and minor chipping along the edges. The existing surface, while functional, detracts from the kitchen’s overall aesthetic and poses potential hygiene concerns due to the accumulation of dirt and bacteria in surface imperfections.The application process begins with meticulous surface preparation.
This involves thorough cleaning to remove grease and debris, followed by sanding to create a slightly roughened surface for optimal epoxy adhesion. Any existing damage, such as chips or cracks, is repaired with a suitable filler, leveled, and sanded smooth. The prepared countertop is then primed with a compatible epoxy primer, ensuring proper bonding.The food-safe epoxy paint is applied in several thin, even coats.
The first coat, often tinted with a base color, establishes the foundation. Subsequent coats incorporate decorative elements, such as metallic pigments or color flakes, to achieve the desired aesthetic. Each coat is applied with a specialized roller or trowel, ensuring a smooth, bubble-free finish. The final coat, a clear epoxy sealant, provides a durable, glossy, and food-safe surface.The transformation is visually striking.
The old, damaged countertop is replaced by a seamless, resilient surface with a high-gloss finish. The new surface is resistant to stains, scratches, and heat, enhancing both the functionality and appearance of the kitchen. The application process results in a surface that is easy to clean and maintain, significantly improving the overall hygiene of the food preparation area.
Visual Description of the Application Process
The application of food-safe epoxy paint requires a systematic approach, with each step contributing to the final outcome. The visual description of the application process highlights the key stages and the tools involved.The initial phase involves surface preparation, which is a critical step. The visual representation includes the use of protective gear, such as gloves, safety glasses, and a respirator, emphasizing the importance of safety.
The surface is thoroughly cleaned with a degreasing agent, removing any contaminants. Sanding tools, including orbital sanders and hand-held sanding blocks, are used to abrade the surface, creating microscopic pores that enhance epoxy adhesion. Repairing imperfections is visualized through the application of epoxy filler, followed by sanding to achieve a level surface.The application of the epoxy paint itself is another crucial step.
The visual representation showcases the mixing of the epoxy resin and hardener, following the manufacturer’s instructions precisely. The mixing process is shown with the use of a mixing paddle attached to a drill to ensure complete homogenization. Application tools, such as specialized rollers and squeegees, are used to apply the epoxy in thin, even coats. The visual emphasizes the importance of avoiding air bubbles by carefully spreading the epoxy and using a heat gun to remove any trapped air.
The final coat, a clear epoxy sealant, is applied to provide a glossy, durable finish.The entire process is depicted as a clean, organized, and meticulous operation, emphasizing the importance of attention to detail and proper technique for achieving a successful result. The final visual emphasizes the importance of allowing the epoxy to cure fully, providing the required time for it to harden completely, and achieve its maximum durability.
Long-Term Durability and Appearance
The long-term durability and appearance of a food-safe epoxy-painted surface are key factors in its value proposition. This section describes the expected performance over time, considering factors such as wear, resistance to staining, and ease of maintenance.Over a period of several years, a properly applied food-safe epoxy coating demonstrates exceptional durability. The surface resists scratches and abrasions from daily use, maintaining its smooth, glossy appearance.
Resistance to staining is another significant advantage. Food spills, such as coffee, wine, or sauces, can be easily wiped away without leaving permanent marks. The epoxy’s non-porous nature prevents the absorption of liquids and bacteria, ensuring hygienic food preparation.The coating’s resistance to heat is another key aspect of its durability. While direct exposure to extremely high temperatures should be avoided, the epoxy typically withstands moderate heat, such as that from hot pots and pans, without damage.The ease of maintenance is also notable.
The smooth, seamless surface is easily cleaned with mild soap and water. Harsh chemicals or abrasive cleaners are generally unnecessary, as the epoxy’s inherent properties resist staining and dirt accumulation. Regular cleaning helps maintain the coating’s appearance and prolongs its lifespan.In a typical kitchen environment, a food-safe epoxy-painted countertop can be expected to last for many years, with minimal signs of wear and tear.
The initial investment in materials and application pays off over time through the reduced need for repairs and the long-lasting aesthetic appeal.
Closing Summary
So, there you have it! Food safe epoxy paint isn’t just a coating; it’s a commitment to safety, hygiene, and longevity. From understanding the science to mastering the application, you now possess the knowledge to transform any food preparation surface into a pristine, durable, and safe environment. Embrace the power of food safe epoxy paint and step into a world where food safety is paramount, and your surfaces are protected with the best!