Embarking on the journey of establishing a business in the burgeoning hemp food industry? Navigating the regulations is key, and that starts with understanding the hemp food establishment permit florida requirements. This guide provides a comprehensive overview of the necessary steps, from defining what constitutes a “hemp food establishment” under Florida law to detailing the application process and the specific requirements for operating within the state.
We will explore the various facets of this topic, including facility standards, product regulations, inspection processes, and local ordinances. Furthermore, we will delve into the importance of training, the complexities of the hemp supply chain, and the essential aspects of record-keeping. By providing practical solutions to common challenges, this resource aims to assist both aspiring entrepreneurs and existing businesses in ensuring compliance and fostering success in this evolving sector.
Overview of Hemp Food Establishment Permits in Florida
Understanding the regulatory landscape for hemp food establishments in Florida is essential for businesses seeking to operate within the state. This overview provides a comprehensive look at the key aspects of obtaining and maintaining the necessary permits, ensuring compliance with Florida law.
Legal Definition of a “Hemp Food Establishment”
Florida law, specifically as defined in Chapter 581, Florida Statutes, establishes the parameters for hemp food establishments. The definition focuses on the activities and products involved.
A “hemp food establishment” is defined as any location where hemp food is manufactured, processed, packed, or stored for sale or distribution. This includes facilities that conduct these activities for wholesale or retail purposes.
This definition is broad and encompasses a range of businesses, from large-scale manufacturers to smaller processors and storage facilities. It is crucial to understand this definition to determine whether a permit is required.
Activities Requiring a Permit
Certain activities necessitate a permit to operate as a hemp food establishment in Florida. These activities are subject to inspection and regulation to ensure consumer safety and product quality.
- Manufacturing: This includes the creation of hemp food products from raw materials or ingredients. This could involve mixing, cooking, baking, or other processes.
- Processing: This involves altering the form or characteristics of hemp food products, such as grinding, extracting, or refining.
- Packing: This covers the packaging of hemp food products for sale or distribution. This can include labeling and packaging.
- Storing: Facilities that store hemp food products intended for sale or distribution also require a permit. This includes warehouses and distribution centers.
Primary Governing Bodies Involved in Regulation
Several state agencies play a crucial role in regulating hemp food establishments in Florida. These agencies work together to ensure compliance with all applicable laws and regulations.
- Florida Department of Agriculture and Consumer Services (FDACS): FDACS is the primary regulatory body for hemp food establishments. It is responsible for issuing permits, conducting inspections, and enforcing regulations related to food safety and labeling.
- Florida Department of Health (FDOH): The FDOH may be involved, especially in matters related to food safety standards and consumer health. They often collaborate with FDACS to ensure compliance.
- Local County Health Departments: In some cases, local county health departments may also be involved in inspections and enforcement, especially for smaller establishments. The specifics can vary based on the county.
Permit Application Process
Navigating the permit application process for a hemp food establishment in Florida requires careful attention to detail. Understanding each step and preparing the necessary documentation is crucial for a smooth and successful application. This section provides a comprehensive guide to help you through the process.
Step-by-Step Procedure for Applying
The Florida Department of Agriculture and Consumer Services (FDACS) Artikels a specific procedure for hemp food establishment permit applications. Following these steps will help ensure your application is processed efficiently.
- Application Submission: The first step involves completing and submitting the official application form provided by FDACS. This form requires detailed information about your business, including the nature of your hemp food products, the facility’s location, and operational procedures. The application can typically be submitted online through the FDACS website or by mail.
- Facility Inspection: Once the application is received, FDACS inspectors will schedule a facility inspection. This inspection is conducted to verify that the establishment meets all required safety and sanitation standards. Be prepared to demonstrate compliance with food safety regulations, including proper storage, handling, and processing procedures.
- Plan Review (if applicable): If your establishment involves significant construction or modifications to the facility, a plan review may be required. This involves submitting detailed plans of your facility layout, equipment, and operational processes to FDACS for approval before construction begins.
- Permit Issuance: If the inspection and plan review (if applicable) are successful, and all requirements are met, FDACS will issue the hemp food establishment permit. This permit authorizes you to operate your business within the scope defined in your application.
- Renewal: Permits typically need to be renewed periodically, often annually. You will need to submit a renewal application and may be subject to another inspection to maintain your permit.
Checklist of Required Documents
Gathering all the necessary documents before starting the application process can save time and prevent delays. The following documents are typically required for a hemp food establishment permit application:
- Completed Application Form: The official application form, fully and accurately completed.
- Facility Floor Plan: A detailed floor plan of the establishment, including the layout of all processing areas, storage areas, and restrooms. The plan should show the location of all equipment and fixtures.
- Standard Operating Procedures (SOPs): Written SOPs for all food handling and processing activities. These SOPs should Artikel procedures for receiving, storing, preparing, and serving hemp food products.
- Employee Training Records: Documentation of employee training on food safety, hygiene, and proper handling of hemp products. This should include records of training dates and topics covered.
- Equipment List: A comprehensive list of all equipment used in the establishment, including specifications and maintenance schedules.
- Ingredient List: A detailed list of all ingredients used in hemp food products, including the source and supplier information.
- Hemp Product Certificates of Analysis (COAs): COAs for all hemp products used as ingredients, verifying that they meet the state’s requirements for THC content.
- Water Source Documentation: Documentation verifying the safety of the water source used in the establishment, such as a water test report.
- Proof of Business Registration: Documentation demonstrating that the business is registered with the state of Florida, such as a business license or articles of incorporation.
Typical Processing Time for a Permit Application
The time it takes to process a permit application can vary depending on several factors, including the completeness of the application, the complexity of the facility, and the volume of applications being processed by FDACS. While there is no guaranteed timeframe, understanding the general expectations can help you plan accordingly.Generally, the initial review of an application by FDACS can take between 30 to 60 days.
This time frame is an estimate and can be influenced by factors such as the completeness of the application and any required follow-up communication. After the initial review, the inspection process and any necessary plan reviews can add to the overall processing time. It’s recommended to plan for a total processing time of at least 60 to 90 days, and potentially longer if any issues arise during the review or inspection.For example, a small bakery focusing on hemp-infused cookies, with a straightforward facility layout and complete application, might experience a faster processing time compared to a larger, more complex manufacturing facility producing a variety of hemp-based food products.
It is always a good idea to contact FDACS directly to inquire about the current processing times and any specific requirements.
How to Fill Out the Application Form
Filling out the application form accurately is critical to avoid delays or rejection. This section provides guidance and examples of common mistakes to avoid.The application form typically requires information in several key areas.
- Business Information: This section requires the legal name of the business, the business address, contact information, and the type of business entity (e.g., sole proprietorship, partnership, corporation). Make sure all information matches your official business registration documents.
- Facility Information: This section requires the physical address of the hemp food establishment, including details about the building’s layout and use. Ensure that the facility’s address is accurately listed and matches the address on your lease or property documents.
- Product Information: Provide a detailed description of the hemp food products you intend to manufacture, process, or sell. Include the product names, the types of products (e.g., baked goods, beverages, snacks), and the hemp-derived ingredients used.
- Operational Information: This section addresses your business’s operating procedures, including hours of operation, the number of employees, and how you plan to comply with food safety regulations.
- Applicant Signature and Certification: The application must be signed and dated by the applicant or an authorized representative, certifying that the information provided is true and accurate.
Here are some common mistakes to avoid when filling out the application form:
- Incomplete Information: Failing to provide all required information, such as missing business details or product descriptions, can lead to delays or rejection. Always review the form carefully to ensure that all fields are completed accurately.
- Incorrect Information: Providing inaccurate information, such as the wrong business address or product formulations, can result in serious consequences. Double-check all information against your business records and supporting documents.
- Vague Product Descriptions: Providing unclear or general descriptions of your hemp food products can cause confusion. Be as specific as possible about the product types, ingredients, and intended uses.
- Failure to Include Supporting Documents: Not including all required supporting documents, such as floor plans, SOPs, and COAs, can significantly delay the application process. Always refer to the checklist and ensure that all documents are included with your application.
- Lack of Proper Signatures: Failing to sign and date the application form can invalidate the submission. Ensure that the application is signed by an authorized representative of the business.
For instance, a common mistake is failing to accurately describe the source of hemp ingredients. Instead of simply stating “hemp extract,” the application should specify the type of extract, the concentration of cannabinoids, and the supplier’s name and contact information. Similarly, using an outdated or incorrect business address is another frequent error that can lead to the application being returned.
Discover the crucial elements that make grace place food pantry the top choice.
By carefully reviewing the form and double-checking all information, applicants can significantly increase their chances of a successful and timely permit application.
Requirements for Hemp Food Establishments
Operating a hemp food establishment in Florida necessitates strict adherence to specific requirements to ensure the safety and quality of the products. These requirements cover various aspects, from the physical structure of the facility to the labeling of the final product. Compliance with these regulations is crucial for obtaining and maintaining a permit and, more importantly, for protecting public health.
Facility Requirements
The physical environment of a hemp food establishment must meet stringent standards to prevent contamination and facilitate safe food handling practices. These requirements cover construction, sanitation, and the type of equipment used.The construction of the facility must be durable, easily cleanable, and designed to prevent pest entry. Floors, walls, and ceilings should be constructed of smooth, non-absorbent materials. Adequate lighting and ventilation are also essential.
The layout should facilitate an efficient flow of operations, minimizing the risk of cross-contamination. Handwashing stations must be readily accessible and equipped with hot and cold running water, soap, and single-use towels or hand dryers. Separate areas should be designated for receiving, storage, preparation, and packaging to prevent the mixing of raw and ready-to-eat foods.Sanitation is paramount. Regular cleaning and sanitizing of all food contact surfaces, equipment, and utensils are mandatory.
Proper waste disposal systems must be in place, and pest control measures must be implemented to prevent infestation. The facility must have adequate storage space for food and supplies, with proper temperature control to maintain food safety. For example, refrigerated storage must maintain temperatures at or below 41°F (5°C) for potentially hazardous foods.Equipment used in the hemp food establishment must be food-grade, non-toxic, and easily cleanable.
Equipment should be designed for the specific tasks performed and maintained in good working order. This includes ensuring that all equipment is properly calibrated and functioning correctly. For example, thermometers used to check food temperatures must be accurate to within +/- 2°F (+/- 1°C).
Food Handling and Storage Practices
Proper food handling and storage practices are essential for preventing foodborne illnesses. Both acceptable and unacceptable practices are clearly defined by regulations.Acceptable practices include:* Following proper handwashing procedures, including washing hands thoroughly with soap and water before handling food and after any activity that could contaminate hands.
- Using separate cutting boards and utensils for raw and ready-to-eat foods to prevent cross-contamination.
- Storing food at the correct temperatures.
- Cooking food to the required internal temperatures to kill harmful bacteria.
- Properly labeling and dating food items to track their shelf life.
- Training employees on food safety principles.
Unacceptable practices include:* Failing to wash hands properly.
- Using the same cutting board or utensils for raw and ready-to-eat foods without proper cleaning and sanitizing.
- Storing food at improper temperatures.
- Failing to cook food to the required internal temperatures.
- Using expired or spoiled ingredients.
- Allowing employees with illnesses to handle food.
- Ignoring pest control measures, which can lead to contamination of food products.
Labeling Requirements for Hemp-Infused Food Products
Accurate and informative labeling is crucial for consumer safety and compliance with Florida regulations. Hemp-infused food products must adhere to specific labeling requirements to ensure consumers are informed about the product’s contents and potential effects.The label must include:* The product’s name and a statement of identity.
- The name and address of the manufacturer, packer, or distributor.
- A complete list of ingredients, listed in descending order of predominance by weight.
- The net quantity of contents.
- Nutrition information, including serving size, calories, and macronutrients.
- The amount of total and active cannabinoids per serving and per package. This information is crucial for consumers to understand the potency of the product.
- A statement that the product contains hemp extract.
- Any other required warnings or statements as mandated by Florida law.
A warning statement
“This product contains hemp extract. Keep out of reach of children.”
The label must be clear, legible, and prominently displayed on the product packaging. The information must be presented in a way that is easy for consumers to understand.
Types of Inspections
Florida health officials conduct various types of inspections to ensure compliance with food safety regulations. These inspections help to protect public health by identifying and correcting potential hazards.
Inspection Type | Purpose | Frequency | Focus |
---|---|---|---|
Routine Inspections | To assess overall compliance with food safety regulations. | Varies based on risk level, typically at least annually. | Facility structure, food handling practices, sanitation, equipment, and labeling. |
Follow-up Inspections | To verify that violations identified during a routine inspection have been corrected. | Conducted after a routine inspection where violations were found. | Specific areas where violations were identified. |
Complaint Inspections | To investigate complaints received from consumers or other sources. | Triggered by a specific complaint. | The specific issue raised in the complaint. |
Pre-Operational Inspections | To assess a new establishment’s readiness to operate. | Before a new establishment can open. | Ensuring the facility meets all initial requirements for operation. |
Hemp Food Product Regulations: Hemp Food Establishment Permit Florida
Navigating the regulatory landscape for hemp food products in Florida requires a thorough understanding of the specific rules governing their production, sale, and marketing. These regulations are designed to ensure consumer safety, product quality, and compliance with state and federal laws. The following sections detail key aspects of these regulations.
Permissible THC Levels in Hemp Food Products
The Florida Department of Agriculture and Consumer Services (FDACS) strictly regulates the amount of tetrahydrocannabinol (THC) allowed in hemp food products. This is crucial for ensuring that these products do not produce intoxicating effects and comply with federal regulations.
The current regulations stipulate that hemp food products must contain no more than 0.3% THC on a dry weight basis.
This means that the concentration of THC is measured after the product has been dried to remove moisture. Compliance with this limit is essential for legal sales within the state.
Types of Hemp Food Products Permitted for Sale in Florida
A variety of hemp-derived food products are currently permitted for sale in Florida, providing consumers with diverse options. These products must adhere to all relevant food safety standards and labeling requirements.
- Hemp Seeds and Hemp Seed Products: This includes hemp seeds, hemp seed oil, hemp seed protein powder, and hemp seed-based snacks. These products are valued for their nutritional content, including essential fatty acids and protein.
- Hemp-Infused Foods: Foods that have been infused with hemp extracts, such as CBD-infused edibles (e.g., gummies, chocolates, baked goods), are permitted as long as they meet the THC limits.
- Hemp Flour and Baking Ingredients: Hemp flour and other hemp-based baking ingredients can be used in various food products.
The FDACS regularly updates its list of permitted products, so it is advisable to check the latest guidelines for the most current information.
Restrictions on Advertising and Marketing of Hemp Food Products
The advertising and marketing of hemp food products in Florida are subject to specific restrictions designed to prevent misleading claims and protect consumers. These restrictions apply to various forms of communication, including packaging, labeling, and promotional materials.
- Health Claims: Advertisements cannot make unsubstantiated health claims about hemp food products. Any claims must be supported by scientific evidence and comply with FDA regulations.
- Intoxication Claims: Advertisements must not suggest that hemp food products will produce intoxicating effects.
- Age Restrictions: Advertising and marketing materials should not target minors.
- Packaging and Labeling: Packaging must clearly state the product’s hemp origin and comply with all applicable labeling requirements, including information on THC content and any other relevant ingredients.
For example, a marketing campaign for CBD-infused gummies would need to avoid claims that the product can cure diseases and should clearly state the amount of CBD and THC present in each serving.
Testing Requirements for Hemp Food Products
Rigorous testing is a critical component of ensuring that hemp food products meet regulatory standards and are safe for consumers. These tests verify the accuracy of product labeling and confirm compliance with THC limits.
- THC Content Testing: All hemp food products must undergo testing to verify their THC content. Testing must be performed by a laboratory that is registered with the FDACS and uses validated testing methods.
- Contaminant Testing: Products are tested for the presence of contaminants, such as heavy metals, pesticides, and residual solvents, to ensure they meet safety standards.
- Certificate of Analysis (COA): Each batch of hemp food products must have a Certificate of Analysis (COA) that provides detailed information on the product’s cannabinoid profile and contaminant levels. This COA should be available to consumers upon request.
The FDACS may conduct random inspections and testing of hemp food products to ensure compliance. Businesses found to be in violation of these testing requirements may face penalties, including product recalls and fines.
Inspection and Enforcement
The Florida Department of Agriculture and Consumer Services (FDACS) plays a crucial role in ensuring the safety and compliance of hemp food establishments. This involves a comprehensive inspection and enforcement system designed to protect public health and uphold the integrity of the hemp food industry. Understanding these processes is essential for all establishments operating within the state.
Inspection Process for Hemp Food Establishments
The inspection process is a key element in maintaining the standards for hemp food establishments. FDACS inspectors conduct regular inspections to assess compliance with relevant regulations.The inspectors look for various aspects, including:
- Sanitation: This encompasses the cleanliness of the facility, equipment, and food contact surfaces. Inspectors evaluate the effectiveness of cleaning and sanitizing procedures to prevent contamination.
- Food Handling Practices: Inspectors observe employee practices, such as proper handwashing, glove use, and prevention of cross-contamination. They also assess the storage and handling of hemp food products.
- Product Labeling: Inspectors verify that products are accurately labeled with required information, including the hemp extract content, ingredients, and allergen declarations. They also ensure compliance with labeling requirements for nutritional information.
- Record Keeping: Establishments must maintain accurate records of product processing, sales, and any complaints received. Inspectors review these records to ensure traceability and compliance.
- Pest Control: Facilities must have effective pest control measures to prevent infestation. Inspectors check for evidence of pests and the implementation of pest control programs.
- Equipment and Facilities: Inspectors assess the suitability of equipment and the overall condition of the facility, ensuring they meet the standards for food safety and hygiene.
Common Violations and Potential Penalties
Non-compliance with regulations can lead to various penalties, ranging from warnings to permit revocation. Understanding these potential consequences is vital for establishments.Examples of common violations include:
- Sanitation Violations: Failure to maintain a clean and sanitary environment, including improper cleaning of equipment or surfaces, can result in warnings or fines.
- Improper Food Handling: Practices such as improper handwashing, cross-contamination, or unsafe food storage can lead to penalties.
- Labeling Deficiencies: Inaccurate or incomplete labeling of hemp food products, including missing required information or false claims, may result in warnings, fines, or product seizure.
- Unapproved Ingredients or Processes: Using ingredients or processing methods that are not approved by FDACS can lead to enforcement actions.
- Pest Infestation: Failure to control pests adequately can result in fines and potentially facility closure until the issue is resolved.
Penalties for non-compliance can include:
- Written Warnings: These are issued for minor violations and provide an opportunity for the establishment to correct the issue.
- Fines: Financial penalties can be imposed for more serious violations, with the amount varying depending on the severity and frequency of the violations.
- Permit Suspension: The permit to operate can be temporarily suspended, preventing the establishment from producing or selling hemp food products until the issues are resolved.
- Permit Revocation: In cases of repeated or severe violations, the permit can be permanently revoked, prohibiting the establishment from operating.
Procedures for Appealing an Inspection Finding or Enforcement Action, Hemp food establishment permit florida
Establishments have the right to appeal inspection findings or enforcement actions. Understanding the appeal process is essential to protect their interests.The appeal process typically involves the following steps:
- Notification of the Action: The establishment receives written notification of the inspection findings or enforcement action.
- Filing an Appeal: The establishment must file a written appeal within a specified timeframe, typically within 10-15 days of receiving the notice.
- Review of the Appeal: The FDACS reviews the appeal, which may include a review of the evidence, inspection reports, and any supporting documentation provided by the establishment.
- Hearing (if applicable): Depending on the nature of the appeal, a hearing may be held where the establishment can present its case and provide additional information.
- Decision: The FDACS issues a final decision, which may uphold, modify, or overturn the original inspection finding or enforcement action.
Establishing a clear understanding of the inspection and enforcement process can help hemp food establishments to maintain compliance, protect their business, and contribute to a safe and regulated hemp food industry in Florida.
Local Regulations and Zoning
Understanding and complying with local regulations and zoning ordinances is crucial for the successful establishment and operation of a hemp food establishment in Florida. These local requirements often supplement the state regulations and can significantly impact a business’s feasibility and operational practices. Careful consideration of these local rules can prevent costly delays and ensure smooth operations.
Additional Regulations and Zoning Restrictions
Local jurisdictions, including cities and counties, frequently impose additional regulations and zoning restrictions that specifically address businesses involved in the processing, manufacturing, distribution, or sale of hemp-derived food products. These regulations are implemented to manage land use, public health, and safety within their respective communities.
Specific Local Ordinances Related to Hemp Food Establishments
Examples of local ordinances that may affect hemp food establishments include:
- Zoning Restrictions: Zoning ordinances may restrict where hemp food establishments can be located. Some areas may prohibit such businesses entirely, while others may limit them to specific zones, such as industrial or commercial districts. For instance, a city might require a hemp food processing facility to be located a certain distance from residential areas or schools.
- Permitting Requirements: Local governments may have their own permitting processes in addition to the state permit. These permits could cover aspects such as building codes, fire safety, and environmental health.
- Business Licenses: Local business licenses are almost always required. These licenses often involve annual fees and require businesses to comply with local tax regulations.
- Signage Regulations: Specific guidelines on signage, including size, placement, and content, may be mandated by local ordinances. These regulations help maintain aesthetic standards and ensure public safety.
- Operating Hours: Some jurisdictions might impose restrictions on operating hours, particularly for businesses that sell hemp food products directly to consumers.
- Waste Disposal Regulations: Local ordinances might dictate how hemp food establishments must dispose of waste materials, including packaging and any byproducts from processing.
Researching Local Regulations
Thorough research into local regulations is essential before establishing a hemp food business. This research should be conducted early in the planning process.
- Contacting Local Government: The primary step is to contact the local city or county government’s planning and zoning department. Inquire about specific zoning regulations, permitting requirements, and business license applications relevant to hemp food establishments.
- Reviewing Official Websites: Most local governments have websites that provide access to ordinances, zoning maps, and permitting information. Search for relevant documents related to food establishments, manufacturing, and hemp-related businesses.
- Consulting with Professionals: Engaging a local attorney specializing in business law or a zoning consultant can be invaluable. These professionals can provide expert guidance on navigating local regulations and ensuring compliance.
- Visiting the Local Government Office: Visiting the local government office in person can be beneficial. You can speak directly with officials, ask specific questions, and gain a clearer understanding of the regulations.
- Checking with Neighboring Businesses: Inquire with existing businesses in the area about their experiences with local regulations. They might offer insights into the permitting process and any challenges they have encountered.
Key Considerations for Businesses to Account for Local Regulations
Businesses must consider several key factors to ensure compliance with local regulations.
- Zoning Compliance: Verify that the proposed location is properly zoned for the intended use of a hemp food establishment. This involves reviewing zoning maps and ordinances to confirm the business activities are permitted in that specific zone.
- Permitting and Licensing: Obtain all necessary permits and licenses from the local government. This might include a business license, building permits, health permits, and any other permits specific to the business activities.
- Building Codes and Inspections: Ensure the facility complies with local building codes. This involves meeting requirements for construction, fire safety, and accessibility. Regular inspections may be required.
- Signage and Advertising: Comply with local regulations on signage, including size, placement, and content. Ensure that all advertising materials meet local standards and are truthful and accurate.
- Waste Management: Develop a plan for proper waste disposal that complies with local regulations. This might involve contracts with waste management companies and adherence to specific disposal guidelines.
- Operating Hours and Noise Restrictions: Adhere to any local restrictions on operating hours and noise levels. These regulations are often in place to minimize disturbances to nearby residents.
- Community Engagement: Engage with the local community and address any concerns that residents may have. Building positive relationships with the community can help ensure the business operates smoothly.
Training and Education
Food safety and regulatory compliance are paramount in the hemp food industry. Adequate training and education for all personnel involved in the handling, preparation, and sale of hemp-infused food products are essential for ensuring consumer safety and maintaining the integrity of the industry. This section details the training requirements, resources, and the importance of staying current with regulations.
Training Requirements for Food Handlers
Food handlers in hemp food establishments must receive comprehensive training to understand and implement safe food handling practices. This training is crucial for preventing foodborne illnesses and ensuring that products meet all relevant health and safety standards.
Resources for Food Safety Training and Certification
Several resources offer food safety training and certification programs that are recognized and accepted in Florida. These programs equip food handlers with the knowledge and skills needed to operate safely and comply with state regulations.
- Florida Department of Business and Professional Regulation (DBPR): The DBPR often provides or approves food safety training programs that meet state requirements. Their website and publications offer guidance on approved courses and certification.
- ServSafe: ServSafe is a nationally recognized food safety training program. ServSafe certification is widely accepted and provides comprehensive training on food safety practices, including cross-contamination prevention, proper cooking temperatures, and personal hygiene.
- National Registry of Food Safety Professionals (NRFSP): NRFSP offers a range of food safety training and certification options. Their programs are designed to meet various industry needs and are often recognized by regulatory agencies.
- Local Health Departments: County health departments may offer or recommend food safety training programs, providing localized information and resources.
Importance of Staying Up-to-Date on Changes to Hemp Regulations
The regulatory landscape for hemp and hemp-derived products is constantly evolving. Staying informed about changes to regulations is critical for maintaining compliance and avoiding potential penalties. This includes understanding new rules regarding labeling, testing, and permitted ingredients.
Staying informed ensures the ability to adapt business practices and maintain legal compliance.
Key Topics Covered in Required Training Programs
Required training programs generally cover a range of essential topics related to food safety and handling, ensuring that food handlers are well-prepared to work in hemp food establishments.
- Foodborne Illness Prevention: Understanding the causes of foodborne illnesses, including bacteria, viruses, and parasites, and how to prevent their spread.
- Personal Hygiene: Proper handwashing techniques, the use of gloves, and other personal hygiene practices to prevent contamination.
- Cross-Contamination Prevention: Methods for preventing the transfer of harmful substances from one food item to another, including proper cleaning and sanitization of equipment and surfaces.
- Safe Food Handling Practices: Proper cooking, cooling, reheating, and storage procedures to ensure food safety.
- Allergen Awareness: Understanding common food allergens and how to prevent cross-contact.
- Hemp-Specific Regulations: Knowledge of the specific regulations related to hemp food products, including labeling requirements, testing standards, and permitted ingredients.
- Cleaning and Sanitization: Proper techniques for cleaning and sanitizing food contact surfaces, equipment, and utensils.
- Pest Control: Strategies for preventing and controlling pests in food establishments.
Hemp Source and Supply Chain
Understanding the hemp source and supply chain is crucial for ensuring the safety, quality, and legality of hemp food products in Florida. This involves careful consideration of where the hemp originates, how it’s cultivated, processed, and transported, and how its quality is maintained throughout the process. Compliance with state and federal regulations is paramount, alongside a commitment to transparency and traceability.
Requirements for Sourcing Hemp Used in Food Products
The sourcing of hemp for food products in Florida is governed by specific regulations designed to protect public health and ensure product integrity. These requirements are primarily focused on the origin of the hemp and its compliance with the legal definition of hemp.
- Compliance with Federal and State Laws: Hemp must be sourced from growers licensed under the U.S. Department of Agriculture (USDA) hemp program or a state-approved hemp program. This ensures that the hemp contains no more than 0.3% delta-9 tetrahydrocannabinol (THC) on a dry weight basis.
- Approved Cultivation Practices: Hemp must be cultivated using approved agricultural practices that minimize the risk of contamination from pesticides, heavy metals, and other harmful substances.
- Traceability Documentation: A complete paper trail is necessary, including records of the hemp’s origin, testing results, and transportation. This documentation helps to trace the product back to its source if any issues arise.
- Testing Requirements: Hemp must undergo third-party testing by a DEA-registered laboratory to verify cannabinoid content and screen for contaminants. The testing results must be provided to the hemp food establishment.
- Seed Certification: The origin of the seed must be known, preferably with certification that it is from an approved source, to verify the genetics and ensure it is a legal hemp variety.
Verifying the Origin and Quality of Hemp
Verifying the origin and quality of hemp is a critical step in the process of ensuring that hemp food products are safe and compliant with regulations. Several methods are employed to accomplish this, offering varying levels of assurance.
- Reviewing Grower Licenses and Certifications: Verify the grower’s license and any relevant certifications, such as organic or Good Agricultural Practices (GAP) certifications. This confirms the grower’s adherence to industry standards and regulatory requirements.
- Examining Third-Party Lab Test Results: Request and carefully review third-party lab test results for each batch of hemp. These tests should confirm the THC content is below 0.3% and screen for pesticides, heavy metals, and other contaminants.
- Conducting Site Visits: When feasible, conduct site visits to the hemp farm or processing facility. This allows for direct observation of cultivation, harvesting, and processing practices.
- Requesting Certificates of Analysis (COAs): Obtain COAs from the supplier, ensuring that the lab is accredited and the results are current. The COA should include the date of testing, the name of the lab, and the specific tests performed.
- Evaluating the Supplier’s Reputation: Research the supplier’s reputation and experience in the hemp industry. Consider factors like their history, customer reviews, and adherence to ethical practices.
Best Practices for Managing the Hemp Supply Chain
Effective management of the hemp supply chain involves implementing robust practices to ensure the quality, safety, and traceability of hemp-derived ingredients. These practices help to mitigate risks and maintain compliance.
- Establishing Supplier Agreements: Develop formal agreements with suppliers that Artikel expectations for quality, testing, and compliance with all applicable regulations.
- Implementing a Traceability System: Implement a robust traceability system to track the hemp from its origin to the finished product. This system should document each step in the process, including cultivation, harvesting, processing, and transportation.
- Conducting Regular Audits: Conduct regular audits of suppliers and their facilities to verify compliance with established standards and regulations.
- Maintaining Detailed Records: Maintain detailed records of all aspects of the supply chain, including purchase orders, lab test results, and transportation documents. These records should be readily accessible for inspection.
- Managing Inventory Control: Implement a system for inventory control to ensure that hemp ingredients are used on a first-in, first-out (FIFO) basis, minimizing the risk of degradation and ensuring product freshness.
Hemp Sourcing Options Comparison
The following table provides a comparison of different hemp sourcing options, outlining their key characteristics and considerations.
Sourcing Option | Pros | Cons | Considerations |
---|---|---|---|
Directly from Licensed Growers |
|
|
|
From Hemp Processors/Wholesalers |
|
|
|
Through a Broker |
|
|
|
Vertically Integrated Operations |
|
|
|
Record Keeping and Documentation
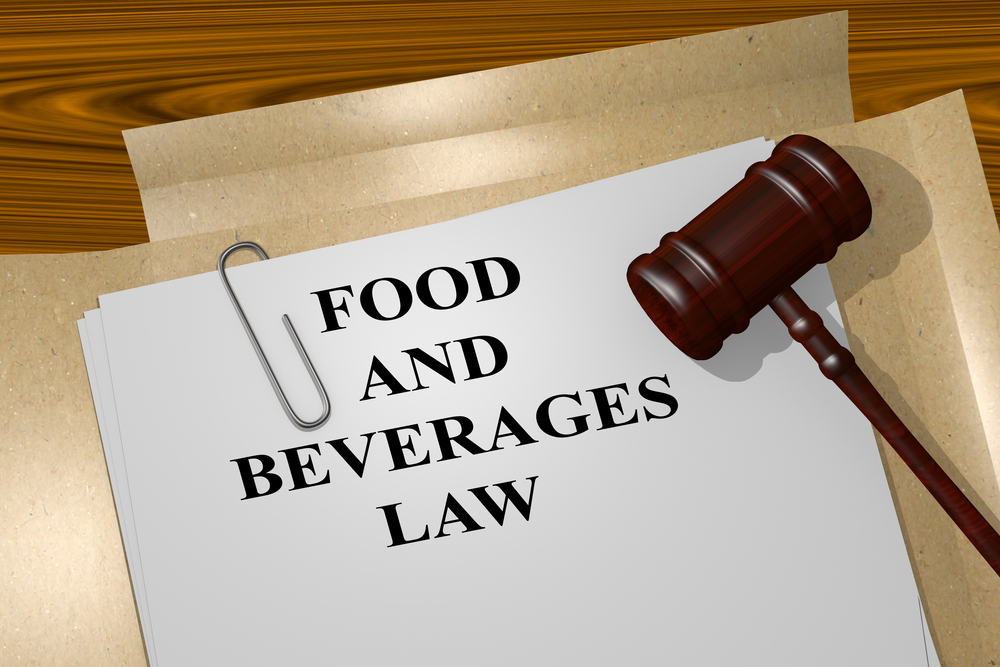
Maintaining meticulous records is crucial for hemp food establishments in Florida. It not only ensures compliance with state regulations but also facilitates efficient operations, aids in traceability, and demonstrates a commitment to food safety. Comprehensive record-keeping is a cornerstone of a successful and legally compliant hemp food business.
Types of Records to Maintain
Several types of records are essential for hemp food establishments. These records provide a comprehensive history of the product from source to sale, enabling effective tracking and accountability.
- Hemp Source Documentation: This includes Certificates of Analysis (COAs) from the hemp supplier, verifying the cannabinoid content (including Delta-9 THC), and confirming that the hemp meets the regulatory requirements for being classified as hemp (0.3% or less Delta-9 THC by dry weight). It should also contain supplier information, purchase orders, and invoices.
- Ingredient Records: Detailed records of all ingredients used in the hemp food products are essential. This encompasses ingredient purchase records, including supplier information, quantities, and dates received. Records should demonstrate adherence to all labeling requirements.
- Production Records: These records document the entire production process. They include batch numbers, production dates, manufacturing procedures, processing parameters (e.g., temperature, time), and any deviations from standard operating procedures (SOPs). They should also include details on the ingredients used in each batch and the finished product’s yield.
- Testing Records: Records of all testing conducted on the finished hemp food products are required. These records should include COAs from accredited laboratories, demonstrating that the products meet all regulatory standards for cannabinoid content, contaminants (pesticides, heavy metals, etc.), and any other required analyses.
- Inventory Records: Accurate inventory records are critical for tracking the movement of hemp and hemp products. They should detail the quantity of hemp and hemp products on hand, including incoming and outgoing shipments, and any waste or disposal.
- Sales Records: Maintain comprehensive sales records, including customer information (if required), product details, quantities sold, dates of sale, and payment information. This helps track product distribution and facilitate potential recalls.
- Employee Training Records: Documentation of all employee training related to food safety, hygiene, and the handling of hemp products is essential. This includes the date of training, the topics covered, and the names of the employees who participated.
- Complaint Records: A system for recording and addressing customer complaints is necessary. These records should include details of the complaint, the investigation conducted, the corrective actions taken, and the resolution.
Examples of Record-Keeping Best Practices
Implementing best practices can significantly improve the efficiency and effectiveness of record-keeping. These practices help ensure accuracy, accessibility, and compliance.
- Use a Consistent System: Establish a standardized record-keeping system, whether manual or electronic, to ensure consistency across all records.
- Maintain Accuracy: Ensure all records are accurate, complete, and legible.
- Date and Time Stamp Records: Always date and time-stamp all records to establish a clear timeline of events.
- Use Unique Identifiers: Assign unique identifiers (e.g., batch numbers, lot numbers) to hemp and hemp products for easy tracking.
- Document Deviations: Any deviations from standard operating procedures (SOPs) or any issues encountered during production should be documented, including the corrective actions taken.
- Regular Audits: Conduct regular internal audits to review record-keeping practices and identify areas for improvement.
- Maintain Records for the Required Time: Florida regulations require that records be maintained for a specific period (e.g., two years). Adhere to these requirements.
Organizing and Storing Records
Proper organization and storage are critical for ensuring records are easily accessible during inspections and for internal management purposes.
- Organize by Category: Group records by type (e.g., COAs, production records, sales records) for easy retrieval.
- Use a Filing System: Implement a clear and organized filing system, whether physical or electronic. Consider using color-coding or labeling to further improve organization.
- Secure Storage: Store records in a secure location to prevent unauthorized access or loss. This might include locked cabinets for physical records or password-protected access for electronic records.
- Backup Electronic Records: Regularly back up electronic records to prevent data loss. Consider off-site backups or cloud storage.
- Accessibility: Ensure that records are easily accessible to authorized personnel, especially during inspections.
Creating a Basic Record-Keeping Template
A well-designed template can streamline the record-keeping process. The following is a simple example that can be adapted to meet the specific needs of a hemp food establishment.
Record Type | Description | Date | Batch/Lot Number | Details | Supplier/Source | Notes/Comments |
---|---|---|---|---|---|---|
Hemp Source (COA) | Certificate of Analysis received | YYYY-MM-DD | [Batch Number] | Delta-9 THC: [Value]%, Pesticides: Pass/Fail, Heavy Metals: Pass/Fail | [Supplier Name] | File location [e.g., Folder/File name] |
Ingredient Purchase | Ingredient received | YYYY-MM-DD | [Batch Number] | Ingredient Name: [Ingredient], Quantity: [Amount] | [Supplier Name] | Purchase Order [Number] |
Production | Batch Production | YYYY-MM-DD | [Batch Number] | Process: [Description], Temp: [Value], Time: [Value] | N/A | SOP Reference [Number] |
Finished Product Testing | Finished Product COA | YYYY-MM-DD | [Batch Number] | Delta-9 THC: [Value]%, Contaminants: Pass/Fail | [Laboratory Name] | COA Number: [Number] |
This is a simplified example. Each establishment should customize the template to include all necessary information specific to its operations and products.
Common Challenges and Solutions
Navigating the hemp food industry in Florida presents unique hurdles for businesses. Understanding these challenges and implementing effective solutions is crucial for success. This section Artikels common obstacles and provides practical strategies to overcome them, fostering a thriving hemp food market.
Navigating Regulatory Compliance
Establishing compliance with Florida’s hemp food regulations can be complex. This requires meticulous attention to detail and a proactive approach.
- Challenge: Staying updated with evolving state and federal regulations. Regulatory changes can occur frequently, impacting product formulations, labeling, and operational procedures.
- Solution: Regularly monitor official government websites, subscribe to industry newsletters, and consult with legal experts specializing in hemp regulations. Maintaining a compliance calendar can help track deadlines and ensure timely adjustments to operations.
- Challenge: Ensuring accurate labeling and product claims. Misleading or inaccurate labeling can lead to product recalls, legal penalties, and damage to brand reputation.
- Solution: Conduct thorough reviews of all product labels, ensuring compliance with Florida Department of Agriculture and Consumer Services (FDACS) guidelines and federal requirements. Utilize third-party laboratories for testing to verify cannabinoid content and purity.
- Challenge: Understanding and adhering to Good Manufacturing Practices (GMP). Implementing GMP standards is critical for food safety and product quality.
- Solution: Develop and implement a comprehensive GMP plan that covers all aspects of production, from sourcing raw materials to packaging and storage. Provide regular training to employees on GMP procedures. Consider seeking GMP certification to demonstrate commitment to quality.
Managing Supply Chain and Sourcing
Securing a reliable and compliant supply chain is vital for the success of any hemp food business. This includes sourcing quality ingredients and ensuring traceability.
- Challenge: Finding reputable hemp suppliers. The quality and legality of hemp products can vary significantly.
- Solution: Conduct thorough due diligence on potential suppliers, including verifying licenses, certifications, and testing results. Establish clear contracts that Artikel quality standards, testing requirements, and supply chain traceability.
- Challenge: Ensuring product traceability. Being able to trace products from seed to sale is essential for compliance and consumer confidence.
- Solution: Implement a robust tracking system that documents the origin, processing, and transportation of all hemp ingredients. Utilize batch numbering and detailed record-keeping to facilitate product recall if necessary.
- Challenge: Managing fluctuations in raw material availability and pricing. The hemp market can be subject to supply and demand dynamics, impacting the cost and availability of ingredients.
- Solution: Diversify sourcing options by establishing relationships with multiple suppliers. Consider long-term contracts to secure favorable pricing and ensure a consistent supply of raw materials. Forecast demand to anticipate potential shortages.
Addressing Market and Consumer Perception
Educating consumers and addressing misconceptions about hemp food products are essential for market success.
- Challenge: Overcoming consumer skepticism and lack of awareness. Many consumers may be unfamiliar with hemp food products or have misconceptions about their effects.
- Solution: Develop informative marketing materials that clearly explain the benefits of hemp food products and address common concerns. Provide educational content on websites and social media platforms. Partner with retailers to offer product samples and demonstrations.
- Challenge: Differentiating products in a competitive market. The hemp food market is becoming increasingly crowded.
- Solution: Focus on product innovation, creating unique formulations and flavors that appeal to specific consumer preferences. Build a strong brand identity and develop compelling marketing campaigns that highlight the unique benefits of the products.
- Challenge: Managing consumer expectations regarding product efficacy. Consumers may have unrealistic expectations about the health benefits of hemp food products.
- Solution: Clearly communicate the potential benefits of the products and avoid making exaggerated health claims. Provide accurate information about the ingredients and their effects. Encourage consumers to consult with healthcare professionals.
The Role of Industry Associations
Industry associations play a vital role in supporting hemp food businesses by providing resources, advocacy, and networking opportunities.
- Benefits:
- Advocacy: Lobbying for favorable legislation and regulations.
- Education: Offering training and educational programs on compliance, best practices, and market trends.
- Networking: Providing opportunities for businesses to connect with suppliers, retailers, and other industry professionals.
- Information Sharing: Disseminating information on regulatory changes, market research, and industry best practices.
“Starting a hemp food business requires dedication, thorough research, and a commitment to compliance. Prioritize quality, transparency, and consumer education to build a successful and sustainable business.”
Conclusion
In conclusion, the hemp food establishment permit florida process is multifaceted, but with diligent preparation and adherence to the Artikeld guidelines, success is attainable. By staying informed on the evolving regulations, understanding the intricacies of facility standards, and maintaining meticulous records, businesses can navigate the challenges and capitalize on the opportunities within the hemp food industry. This guide serves as a valuable resource, helping to foster a compliant and thriving environment for hemp food establishments across Florida.