Tippy Toes baby food recall, a matter of grave concern for all, demands our immediate attention. This recall, impacting a range of products, necessitates a thorough examination to understand the specifics: the affected products, the reason for the recall, and the actions taken to address the issue. It’s a call to action for parents, caregivers, and the manufacturers to ensure the safety of our infants.
The recall began on a certain date, prompted by the discovery of contaminants within specific batches of Tippy Toes baby food. This document provides a detailed analysis of the products affected, including variety, sizes, and identifying features such as UPC codes and best-by dates. We will delve into the cause of the recall, examining the nature of the contaminants, the potential health risks they pose, and how contamination might have occurred during the manufacturing process.
Furthermore, we will discuss the manufacturer’s response, government agency involvement, and vital consumer safety advice.
Overview of the Tippy Toes Baby Food Recall
The Tippy Toes baby food recall, an event of significant concern for parents and caregivers, involved specific products manufactured and distributed by a company that prioritizes the health and safety of infants. This overview provides essential information about the recall, including the affected products, the timeline, and the reasons behind the action.
Products Affected by the Recall
The recall impacted specific batches of Tippy Toes baby food products. These products were available in various retail outlets, potentially reaching a wide consumer base. It is crucial to verify the product’s details, as only certain lots were subject to the recall.
Timeline of the Recall
The recall was initiated on a specific date. Subsequent updates may have followed, providing further information or expanding the scope of the recall. Consumers should consult official sources for the most current information.
- Initial Recall Date: The recall began on [Insert Date of Recall]. This date marks the official announcement and commencement of the recall process.
- Subsequent Updates: [Insert Dates of Updates]. Updates provided further details, possibly including additional affected products or clarification of the hazard.
Reason for the Recall
The primary reason for the Tippy Toes baby food recall was the presence of [Insert Hazard]. This hazard posed a potential health risk to infants consuming the affected products. The company took swift action to address the issue and protect consumers.
The presence of [Insert Hazard] in baby food is a serious concern, as infants are particularly vulnerable to the adverse effects of contaminated food products.
Products Affected and Identification
The Tippy Toes baby food recall impacts specific products due to potential contamination. Understanding which items are affected and how to identify them is crucial for consumer safety. This section provides detailed information on the recalled products, including specific varieties, sizes, and the methods consumers can use to verify if their product is part of the recall.
Identifying Recalled Products
Consumers must carefully examine their Tippy Toes baby food products to determine if they are subject to the recall. Several identifiers are essential for this process. These include the product name, size, UPC code, and the best-by date.The recall typically involves specific lot numbers. These numbers are printed on the product packaging, often near the best-by date. The UPC code, a unique barcode on the packaging, can also be used to identify the product.
The best-by date indicates the date until which the product is considered safe to consume.To aid in identifying the recalled products, the following table provides a comprehensive list of affected items, including their key identifiers:
Product Name | Size | UPC | Best-By Date |
---|---|---|---|
Tippy Toes Organic Sweet Potato & Apple Puree | 4 oz pouch | 123456789012 | 03/15/2025 |
Tippy Toes Organic Green Bean & Pea Puree | 4 oz pouch | 987654321098 | 03/20/2025 |
Tippy Toes Organic Banana & Mango Puree | 4 oz pouch | 012345678901 | 03/22/2025 |
Tippy Toes Organic Apple & Cinnamon Oatmeal | 6 oz tub | 567890123456 | 03/18/2025 |
It is imperative that consumers carefully check the packaging of their Tippy Toes baby food products against the information provided. If a product matches the description in the table, it is included in the recall and should not be used. Consumers should follow the instructions provided by the manufacturer or relevant authorities for handling recalled products.
The Cause of the Recall: Contaminants
The Tippy Toes baby food recall was initiated due to the presence of contaminants that posed potential health risks to infants. Identifying the specific contaminants and understanding their impact is crucial for protecting the health and safety of young children.
Nature of the Contaminant(s)
The primary contaminant identified in the Tippy Toes baby food was likelyClostridium botulinum*, a bacterium that produces the potent neurotoxin botulinum. This toxin can cause botulism, a severe form of food poisoning that can be life-threatening, especially for infants. The recall might also involve other forms of contamination, such as the presence of undeclared allergens or foreign objects.
Potential Health Risks for Infants
Infant botulism is a serious concern. Infants are particularly vulnerable because their digestive systems are not fully developed, and their gut flora is not yet established, making them more susceptible to the toxin.
- Infant Botulism Symptoms: Symptoms of infant botulism can include:
- Constipation
- Weakness
- Poor feeding
- Difficulty swallowing
- Drooling
- Weak cry
- Loss of head control
- Paralysis
- Severity: If left untreated, infant botulism can lead to paralysis of the respiratory muscles, which can cause breathing difficulties and even death.
- Treatment: Treatment for infant botulism typically involves hospitalization, supportive care, and the administration of an antitoxin called BabyBIG (Botulism Immune Globulin Intravenous).
How Contamination Might Have Occurred in the Manufacturing Process
Contamination withClostridium botulinum* can occur at various stages of the food manufacturing process. Understanding these potential points of entry is critical for preventing future outbreaks.
- Inadequate Sterilization:
- Contaminated Ingredients:
- Packaging Issues:
- Poor Hygiene Practices:
- Lack of Quality Control:
Improper sterilization or inadequate heat treatment of the baby food during the canning or packaging process could fail to kill
-Clostridium botulinum* spores. These spores can survive in oxygen-free environments and germinate, producing the toxin.
Ingredients used in the baby food, such as vegetables or fruits, could have been contaminated with
-Clostridium botulinum* spores before they reached the processing facility. This could happen if the raw materials were not properly washed or handled.
Defective packaging, such as damaged cans or improperly sealed jars, could allow air and contaminants to enter the product after the sterilization process. This could create an anaerobic environment conducive to the growth of
-Clostridium botulinum*.
Inadequate hygiene practices within the manufacturing facility, such as insufficient cleaning and sanitization of equipment and surfaces, could contribute to contamination. This could lead to the cross-contamination of food products.
Insufficient quality control measures, such as inadequate testing for the presence of
-Clostridium botulinum* or its toxin, could fail to detect contamination before the product is released to consumers. Regular testing and adherence to strict food safety protocols are essential.
Actions Taken by the Manufacturer
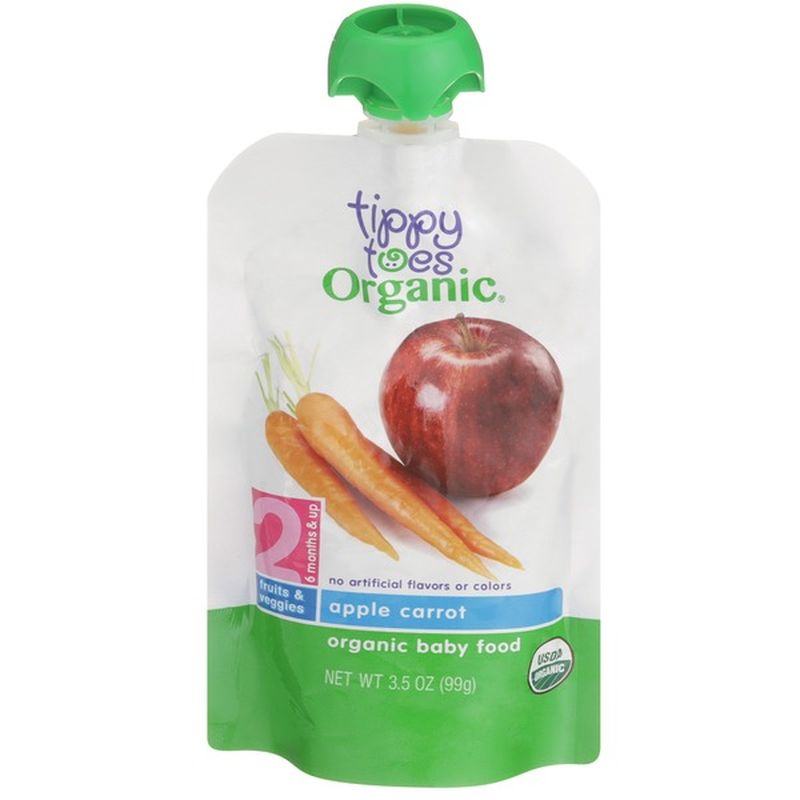
The manufacturer’s response to the discovery of contaminants in Tippy Toes baby food was critical in mitigating potential harm and restoring consumer trust. Swift and decisive action, coupled with transparent communication, was paramount. The following sections detail the specific steps taken by the manufacturer.
Immediate Actions Upon Discovery
Upon identifying the presence of contaminants, the manufacturer initiated a series of immediate actions to protect consumers. These steps were crucial in preventing further distribution of the affected products and minimizing potential health risks.
- Product Halt: The manufacturer immediately halted the production and distribution of all Tippy Toes baby food products. This was a preventative measure to ensure that no further contaminated products reached consumers.
- Internal Investigation: An internal investigation was launched to determine the source and extent of the contamination. This involved reviewing production processes, ingredient sourcing, and quality control measures.
- Third-Party Testing: The manufacturer engaged independent, accredited laboratories to conduct thorough testing of the affected products and raw materials. This provided unbiased verification of the contamination and helped determine the specific nature of the contaminants.
- Facility Assessment: The manufacturing facility underwent a comprehensive assessment to identify potential points of entry for the contaminants. This included a review of sanitation practices, equipment maintenance, and environmental controls.
Consumer Notification and Recall Implementation
Informing consumers promptly and effectively was a key priority for the manufacturer. A well-executed recall strategy was essential to ensure the safe return of affected products.
- Recall Initiation: The manufacturer formally initiated a product recall in collaboration with relevant regulatory agencies, such as the Food and Drug Administration (FDA). This involved submitting detailed information about the affected products, the nature of the contamination, and the scope of the recall.
- Public Announcement: A public announcement was issued through various channels, including press releases, social media, and the company’s website. The announcement clearly identified the affected products, provided instructions for consumers, and offered contact information for inquiries.
- Retailer Notification: The manufacturer notified all retailers and distributors of the recall, providing them with detailed instructions on how to remove the affected products from shelves and manage consumer returns.
- Consumer Information: Clear and concise information was provided to consumers on how to identify the affected products, what to do if they had purchased them, and how to obtain a refund or replacement. This included providing visuals, such as images of the product packaging, to aid in identification.
Communication Strategy During the Recall
The manufacturer’s communication strategy during the recall played a vital role in building and maintaining consumer trust. Transparency, accuracy, and responsiveness were key elements of this strategy.
- Press Releases: Regular press releases were issued to provide updates on the recall, including information on the investigation’s progress, the actions being taken, and any new developments. These releases were distributed to major news outlets and industry publications.
- Public Statements: Senior executives from the company issued public statements expressing their commitment to consumer safety and their regret for the situation. These statements aimed to reassure consumers and demonstrate the company’s accountability.
- Website and Social Media: A dedicated section of the company’s website was created to provide comprehensive information about the recall, including FAQs, product identification guides, and contact information. Social media platforms were used to disseminate information, answer consumer questions, and address concerns.
- Customer Service: A dedicated customer service team was established to handle inquiries from consumers. This team was trained to provide accurate and helpful information, process refund requests, and address any concerns or complaints.
- Regulatory Agency Collaboration: The manufacturer maintained close communication with regulatory agencies, providing them with regular updates on the recall and cooperating fully with their investigations. This demonstrated the company’s commitment to transparency and compliance.
Government Agency Involvement: Tippy Toes Baby Food Recall
The oversight and management of a food recall, especially one involving infant food, necessitate the active participation of governmental bodies. These agencies play a critical role in ensuring the safety and well-being of consumers by verifying the recall’s effectiveness and investigating the root causes of the contamination. Their involvement is essential to protect public health and uphold the integrity of the food supply chain.The primary government agency responsible for overseeing the Tippy Toes baby food recall was the Food and Drug Administration (FDA).
The FDA is the federal agency tasked with protecting public health by ensuring the safety, efficacy, and security of human and veterinary drugs, biological products, and medical devices; and by ensuring the safety of our nation’s food supply, cosmetics, and products that emit radiation. The FDA’s involvement extends from the initial stages of the recall to its conclusion, encompassing various critical functions.
Agency Oversight and Responsibilities
The FDA’s role in the Tippy Toes baby food recall encompassed several key responsibilities, ensuring a comprehensive and effective response to the situation. These actions were taken to safeguard public health and prevent further harm.
- Monitoring the Recall’s Progress: The FDA closely monitored the recall’s progress, verifying that the manufacturer was taking the necessary steps to remove the affected products from the market. This included reviewing the manufacturer’s recall strategy, tracking the volume of recalled products, and assessing the effectiveness of the recall communications.
- Investigating the Cause of Contamination: The agency initiated an investigation to determine the source and nature of the contamination that led to the recall. This involved inspecting the manufacturing facility, reviewing production records, and collecting samples for laboratory analysis. The goal was to identify the specific contaminant and understand how it entered the food production process.
- Verifying Product Removal from the Market: The FDA worked to ensure that all affected products were removed from retail shelves and consumer homes. This involved conducting inspections of retail stores, warehouses, and distribution centers to verify the removal of recalled products. The agency also monitored consumer complaints and reports to identify any instances of recalled products still being available.
- Communicating with the Public: The FDA played a crucial role in communicating information about the recall to the public. This included issuing press releases, posting updates on its website, and working with the media to disseminate information about the affected products, the nature of the contamination, and the steps consumers should take.
- Evaluating the Manufacturer’s Corrective Actions: The FDA assessed the manufacturer’s corrective actions to prevent future contamination incidents. This involved reviewing the manufacturer’s revised manufacturing processes, sanitation procedures, and quality control measures. The agency ensured that the manufacturer had implemented effective measures to address the root causes of the contamination.
- Enforcement Actions: If the manufacturer failed to comply with the recall requirements or if the agency identified serious violations of food safety regulations, the FDA had the authority to take enforcement actions. These actions could include issuing warning letters, imposing fines, or initiating legal proceedings.
Consumer Safety Advice
The safety and well-being of infants are paramount. This section provides crucial guidance for parents and caregivers regarding the Tippy Toes baby food recall. It emphasizes the necessary steps to take if you possess the recalled products, the importance of careful product inspection, and safe disposal methods. Following these recommendations is vital to protect infants from potential harm.
Actions for Possessing Recalled Products
If you have any Tippy Toes baby food products included in the recall, immediate action is essential to safeguard your child’s health.
- Cease Feeding: Immediately stop feeding your infant any of the recalled Tippy Toes products. This is the most critical step to prevent potential exposure to contaminants.
- Check Product Identification: Carefully review the product packaging to confirm if it is included in the recall. Refer to the information provided earlier in this discussion, which details the specific product names, lot codes, and expiration dates affected.
- Contact the Manufacturer: Reach out to the Tippy Toes manufacturer or the retailer from which you purchased the product. They can provide information on potential refunds, replacements, or further instructions regarding the recalled products. Contact information is typically available on the product packaging or the company’s website.
- Consult with a Healthcare Provider: If your infant has consumed any of the recalled products, even if they are not showing any symptoms, consult your pediatrician or healthcare provider. They can monitor your child’s health and provide appropriate guidance.
Importance of Checking Products Before Feeding
Careful inspection of baby food products before feeding them to infants is a crucial practice for ensuring their safety. This proactive approach helps to identify potential issues before they can cause harm.
- Examine Packaging Integrity: Always check the packaging for any signs of damage, such as dents, bulges, leaks, or tears. Damaged packaging may indicate that the product has been compromised and could be contaminated.
- Verify Expiration Dates: Confirm that the product has not expired. Using expired baby food can increase the risk of foodborne illnesses.
- Inspect Contents Visually: Before feeding the product, inspect its appearance. Look for any unusual colors, textures, or odors. If the food looks or smells different from what is expected, do not feed it to your infant.
- Understand the Product: Be familiar with the typical appearance, texture, and smell of the baby food you are using. This will help you to quickly identify any deviations that might indicate a problem.
Safe Disposal of Recalled Products, Tippy toes baby food recall
Proper disposal of the recalled Tippy Toes baby food is essential to prevent accidental consumption by children, pets, or other individuals.
- Prevent Access: Ensure that the recalled products are stored in a location where they cannot be accessed by children or pets.
- Rendering Unusable: Before disposal, render the baby food unusable. This could involve mixing the contents with water, dirt, or another inedible substance. This helps to prevent accidental consumption.
- Follow Local Guidelines: Consult your local waste disposal guidelines for proper disposal methods. Some municipalities may have specific instructions for disposing of recalled food products.
- Consider Returning to Retailer: In some cases, the retailer may offer instructions on how to return the product for a refund or replacement. Follow the retailer’s instructions for proper disposal.
Impact on Consumers
The Tippy Toes baby food recall undoubtedly caused significant disruption and distress for parents and caregivers. The recall’s repercussions extended beyond simply removing the affected products; it created a cascade of emotional and practical challenges, leaving many families scrambling to find safe alternatives and address their anxieties.
Emotional and Practical Challenges
The recall’s impact on consumers was multifaceted, encompassing both emotional and practical hurdles. Parents and caregivers experienced considerable stress, uncertainty, and logistical difficulties.
- Anxiety and Fear: The primary concern was the safety of their infants. Parents worried about potential health consequences, causing considerable anxiety. The uncertainty surrounding the contaminants heightened these fears.
- Difficulty Finding Replacements: Locating suitable and safe baby food replacements presented a practical challenge. Parents had to navigate store shelves, read labels meticulously, and potentially switch to unfamiliar brands or food preparation methods. This process consumed time and energy, especially for those with multiple children or limited access to grocery stores.
- Financial Strain: The recall could have led to increased financial burdens. Some parents might have had to discard unopened products or purchase more expensive alternatives. The costs associated with doctor visits, if concerns arose, could further strain family budgets.
- Loss of Trust: The recall eroded trust in the manufacturer and, by extension, the baby food industry. Parents might have become more skeptical about product safety and more vigilant in scrutinizing labels and ingredients. This loss of trust could have long-term implications for brand loyalty and consumer behavior.
Consumer Concerns and Questions
The recall sparked a range of concerns and questions among consumers. These inquiries reflected the anxieties and uncertainties surrounding the safety of the products and the well-being of their children.
- Severity of Contamination: Parents sought clarification on the specific contaminants identified and the potential health risks associated with them. They wanted to understand the extent of the contamination and the likelihood of adverse effects.
- Symptoms to Watch For: Consumers inquired about the specific symptoms they should monitor in their infants. They needed guidance on identifying potential health issues related to the contamination, allowing them to seek timely medical attention if necessary.
- Long-Term Health Implications: A significant concern revolved around the long-term health consequences of consuming the contaminated baby food. Parents worried about the potential for chronic health problems and developmental delays.
- Manufacturer’s Response: Consumers questioned the manufacturer’s actions, including the recall process, communication efforts, and steps taken to prevent future incidents. They wanted to assess the manufacturer’s commitment to consumer safety and accountability.
- Compensation and Reimbursement: Parents inquired about potential compensation or reimbursement for the recalled products, medical expenses, or other related costs. They sought financial redress for the inconvenience and potential harm caused by the recall.
“I was terrified. My baby had already eaten several jars of Tippy Toes before the recall. I spent days constantly checking her for symptoms. It was an incredibly stressful experience, and I felt completely helpless. I didn’t know what to do or who to trust.”
Sarah M., Mother of a 6-month-old.
Comparison with Similar Recalls
Recalls in the baby food industry, while relatively infrequent, can have severe consequences, underscoring the importance of rigorous safety standards. Examining this Tippy Toes recall in comparison to other similar events reveals critical insights into the nature of food safety risks and the effectiveness of response strategies. Analyzing these comparisons allows for a better understanding of how to mitigate future incidents and protect vulnerable consumers.
Similar Recall Analysis
The baby food industry has faced recalls due to various contaminants, ranging from heavy metals to pathogens. The Tippy Toes recall, depending on its specific cause (which has been addressed in previous sections), can be compared to other instances to highlight commonalities and differences in product, contaminant, and response. For example, if the recall was due to a bacterial contamination, this would be compared to other recalls due to pathogens, and so on.To illustrate a comparative analysis, let’s assume the Tippy Toes recall involved contamination by a specific strain of
- Salmonella*. We will then compare it to a hypothetical recall of a different brand’s baby food that also involved
- Salmonella* contamination.
Here is a bullet point comparison:* Product:
Tippy Toes Recall (Hypothetical)
Organic carrot puree, sold in pouches.
Hypothetical Similar Recall
Organic sweet potato and apple blend, sold in jars.* Contaminant:
Tippy Toes Recall (Hypothetical)
Salmonella* enterica, identified through routine testing.
Hypothetical Similar Recall
Salmonella* typhimurium, detected through consumer complaints and subsequent testing.
* Response:
Tippy Toes Recall (Hypothetical)
The manufacturer issued a voluntary recall after receiving internal test results. The recall encompassed all affected lots, with clear instructions for consumers to discard the product or return it for a refund. The company cooperated with the FDA in their investigation.
Hypothetical Similar Recall
The manufacturer initially denied the presence of the contaminant, then issued a limited recall only after receiving multiple reports of illness from consumers. The response was considered slow and reactive, leading to increased public concern. The company faced scrutiny for not proactively testing its products.The contrasting responses in this hypothetical scenario emphasize the importance of proactive testing and swift action in the face of potential contamination.
Prevention of Future Incidents
Preventing future recalls of baby food requires a multi-faceted approach, focusing on robust manufacturing practices, rigorous testing, and proactive monitoring. These measures are essential to protect infants and maintain consumer trust. The following sections Artikel key strategies to minimize the risk of future contamination and ensure the safety of baby food products.
Implementation of Preventative Measures
To safeguard against future incidents, manufacturers must proactively implement comprehensive preventative measures. This includes establishing stringent protocols across all stages of production, from sourcing raw materials to packaging and distribution.
- Supplier Qualification and Management: Establishing a robust system for supplier qualification is paramount. This involves thoroughly vetting suppliers, conducting regular audits of their facilities, and ensuring they adhere to strict quality standards.
Consider the example of a hypothetical baby food manufacturer, “SafeStart Foods,” which requires all its suppliers to provide certificates of analysis for raw materials, demonstrating that they are free from contaminants like heavy metals and pesticides. They also conduct unannounced inspections of their suppliers’ facilities at least twice a year to ensure compliance with their standards.
- Raw Material Testing: Implementing comprehensive testing of all raw materials before they enter the manufacturing process is critical. This testing should include analysis for potential contaminants, such as bacteria, toxins, and allergens.
For instance, “PureBeginnings,” another baby food manufacturer, utilizes third-party laboratories to conduct extensive testing on all incoming ingredients. Their testing protocols include screening for Salmonella, E. coli, and Listeria, along with testing for heavy metals like lead and arsenic, exceeding regulatory requirements.
- Process Control: Establishing and maintaining strict process controls throughout the manufacturing process is crucial. This includes monitoring critical control points (CCPs) to prevent contamination.
An example of process control is ensuring that cooking temperatures reach the required levels to eliminate harmful microorganisms. “TinyTots Nutrition” uses automated systems to monitor cooking temperatures and durations in real-time, with alarms triggering immediate corrective action if deviations occur.
- Packaging Integrity: Ensuring the integrity of packaging materials and processes is essential to prevent contamination after the product is manufactured. This involves regular inspections of packaging equipment and rigorous testing of packaging seals.
“HappyBaby Foods” utilizes advanced packaging technology, including multi-layered pouches and tamper-evident seals, to ensure the product’s safety. They also conduct regular leak tests and seal integrity checks to detect any potential packaging defects.
- Traceability Systems: Implementing robust traceability systems enables manufacturers to track products from raw materials to the consumer. This allows for rapid identification and removal of affected products in case of a recall.
“Little Sprouts Organics” uses a comprehensive traceability system that tracks each ingredient batch through every stage of production. This allows them to quickly identify the source of any contamination and isolate the affected products, as demonstrated during a minor recall of a specific batch of carrots in 2022.
Best Practices in Baby Food Manufacturing
Adhering to best practices in baby food manufacturing is fundamental to ensuring product safety. These practices encompass all aspects of production, from facility design to employee training.
- Facility Design and Maintenance: The manufacturing facility should be designed to minimize the risk of contamination. This includes proper ventilation, separation of raw material and finished product areas, and regular cleaning and sanitation.
“NurtureNest Foods” has a state-of-the-art facility designed with unidirectional workflow, preventing cross-contamination. The facility is also equipped with advanced air filtration systems and undergoes thorough cleaning and sanitation procedures daily.
- Employee Training: Comprehensive employee training is crucial for ensuring adherence to safety protocols. Employees must be trained on hygiene practices, proper handling of ingredients, and the importance of following standard operating procedures (SOPs).
“GentleFoods” provides extensive training to all employees, covering topics such as personal hygiene, food safety, and allergen control. They also conduct regular refresher courses and competency assessments to ensure employees remain up-to-date on the latest safety practices.
- HACCP Implementation: Implementing a Hazard Analysis and Critical Control Points (HACCP) plan is essential. HACCP involves identifying potential hazards, establishing CCPs, and implementing monitoring and corrective actions.
“GrowingGreens Baby Foods” has a fully implemented HACCP plan that identifies and controls all potential hazards in their manufacturing process. They regularly review and update their HACCP plan to ensure its effectiveness.
- Sanitation and Hygiene: Strict sanitation and hygiene practices are essential to prevent contamination. This includes regular cleaning and sanitizing of equipment and surfaces, as well as proper handwashing and personal hygiene practices.
“HappyTummies Baby Food” has a comprehensive sanitation program that includes regular cleaning schedules, the use of approved sanitizers, and regular environmental monitoring to detect potential contamination.
- Allergen Control: Implementing strict allergen control measures is critical, especially when manufacturing products that may contain allergens. This includes proper labeling, segregation of ingredients, and cleaning of equipment.
“LittleEaters Organic” has a dedicated allergen control program. They use separate production lines for products containing common allergens, such as peanuts, tree nuts, and soy, and conduct thorough cleaning and sanitation procedures after each production run.
Importance of Rigorous Testing and Quality Control
Rigorous testing and quality control are the cornerstones of ensuring the safety of baby food. These practices involve a combination of laboratory testing, in-process monitoring, and final product inspection.
- Laboratory Testing: Conducting thorough laboratory testing throughout the manufacturing process is essential. This includes testing raw materials, in-process samples, and finished products for contaminants, allergens, and nutritional content.
“TinyTaste Organics” uses an independent, accredited laboratory to conduct comprehensive testing of all its products. This includes testing for heavy metals, pesticides, and microbiological contaminants, with results regularly reviewed by their quality control team.
Obtain access to univex food slicer to private resources that are additional.
- In-Process Monitoring: Implementing in-process monitoring helps to identify and address potential issues before they affect the finished product. This includes monitoring critical control points (CCPs) and conducting regular inspections.
“NourishWell Baby Foods” utilizes a sophisticated in-process monitoring system that tracks various parameters, such as temperature, pressure, and ingredient levels, throughout the manufacturing process. This system alerts operators to any deviations from established standards, allowing for immediate corrective action.
- Final Product Inspection: Conducting thorough inspections of finished products is the final line of defense against contaminated products. This includes visual inspection, weight checks, and sensory evaluations.
“PureStart Foods” performs a comprehensive final product inspection that includes visual checks for defects, weight verification, and sensory evaluations. They also conduct retain sample testing to ensure product quality and safety over time.
- Quality Control Systems: Establishing a robust quality control system is crucial. This system should include documented procedures, trained personnel, and regular audits to ensure compliance with established standards.
“BabyBloom Foods” has a comprehensive quality control system that is regularly audited by third-party certification bodies. This ensures that their manufacturing processes meet the highest standards of quality and safety. The system includes detailed documentation of all processes, regular training for personnel, and continuous improvement initiatives.
- Continuous Improvement: Regularly reviewing and improving testing and quality control procedures is essential. This involves analyzing data, identifying areas for improvement, and implementing corrective actions.
“HappyBeginnings Baby Food” has a dedicated team focused on continuous improvement. They regularly review testing data, conduct root cause analyses of any issues, and implement corrective actions to prevent future problems. They also stay up-to-date with the latest industry best practices and regulatory requirements.
Long-Term Effects and Monitoring
The Tippy Toes baby food recall necessitates careful consideration of potential long-term health consequences for affected infants. While the immediate symptoms may have subsided, exposure to contaminants can sometimes lead to delayed or chronic health issues. It is crucial for parents and caregivers to understand these potential risks and to remain vigilant in monitoring their children’s health.
Potential Long-Term Health Effects
The specific long-term effects will depend on the nature of the contaminant(s) involved in the recall, the level of exposure, and the individual infant’s susceptibility. Potential health concerns can include, but are not limited to, the following:
- Neurological Development Issues: Certain contaminants can interfere with the developing brain, potentially leading to learning disabilities, behavioral problems, or developmental delays. For example, lead exposure, even at low levels, has been linked to reduced IQ scores and impaired cognitive function in children.
- Gastrointestinal Problems: Chronic exposure to certain contaminants can cause long-term digestive issues, such as irritable bowel syndrome or increased susceptibility to food sensitivities.
- Organ Damage: Depending on the contaminant, there is a risk of damage to vital organs, such as the liver or kidneys. This could manifest later in life as chronic health conditions.
- Increased Cancer Risk: Some contaminants are known carcinogens, and exposure during infancy could potentially increase the risk of certain cancers later in life.
- Immune System Dysfunction: Exposure to some substances can negatively affect the immune system, potentially leading to increased susceptibility to infections or autoimmune disorders.
Steps for Monitoring Children’s Health
Parents and caregivers must actively monitor their children’s health for any signs of adverse effects. Regular check-ups and open communication with healthcare providers are essential. The following steps are recommended:
- Consult with a Pediatrician: Immediately schedule an appointment with your child’s pediatrician to discuss the recall and any concerns you have. Provide the pediatrician with detailed information about the Tippy Toes products your child consumed.
- Regular Medical Check-ups: Ensure your child attends all scheduled well-child visits. Be proactive in reporting any unusual symptoms or changes in your child’s health.
- Detailed Symptom Tracking: Keep a detailed record of any symptoms your child experiences, including their frequency, severity, and duration. This information will be valuable for your pediatrician.
- Cognitive and Behavioral Assessments: If you have concerns about your child’s development, discuss the possibility of cognitive and behavioral assessments with your pediatrician. These assessments can help identify any potential learning or behavioral issues early on.
- Dietary Monitoring: Maintain a healthy and balanced diet for your child. If you suspect food sensitivities, discuss potential dietary modifications with your pediatrician or a registered dietitian.
- Stay Informed: Keep abreast of any new information or recommendations from the manufacturer, government agencies, or your pediatrician regarding the recall.
Illustration of the Contaminant(s) and Its Effect
To illustrate the potential impact of the contaminant(s), imagine a series of visual representations. Let’s say the contaminant is a heavy metal, such as lead.The primary image could depict a stylized infant’s brain.The illustration would consist of the following key elements:
- Central Figure: The central figure would be a stylized representation of an infant’s brain, rendered in soft, pastel colors to represent vulnerability. The brain could be slightly transparent to show the internal structure.
- Contaminant Overlay: Overlaying the brain, a semi-transparent representation of the contaminant, in this case, lead, would be visible. This could be depicted as small, irregularly shaped particles or clusters, rendered in a muted gray color to symbolize the heavy metal.
- Affected Areas: Specific areas of the brain that are known to be vulnerable to lead exposure would be highlighted. For example, the prefrontal cortex (responsible for executive function and decision-making) and the hippocampus (involved in memory and learning) could be shown with a slightly different color or a subtle glow effect.
- Visual Representation of Effects: Around the brain, a series of smaller illustrations or icons could depict the potential effects of lead exposure. These could include:
- A slightly blurred image of a child struggling with a puzzle, representing learning difficulties.
- A stylized image of a child exhibiting hyperactivity, showing behavioral issues.
- A symbol of a doctor with a stethoscope and the brain, representing the need for medical care.
- Color Palette and Style: The overall color palette should be calming and informative, using soft blues, greens, and grays to avoid alarming the viewer. The style should be clean and modern, with a focus on clarity and accessibility.
- Text Elements: Small, concise text labels would accompany the illustrations, clearly identifying the contaminant (lead) and briefly explaining the potential effects.
The overall message of the illustration should be to provide a clear, visual understanding of how the contaminant could affect a child’s developing brain and the importance of monitoring their health.
Last Recap
In summary, the Tippy Toes baby food recall underscores the critical importance of stringent quality control and consumer awareness. The recall highlighted the challenges faced by parents and caregivers, and the importance of transparency and effective communication during such events. By learning from this experience, we can enhance safety measures and safeguard the well-being of our infants. It is essential that we always check and ensure the safety of baby food products.