Tyson Foods closed, marking a significant shift in the meat processing industry. This review examines the recent instances of Tyson Foods plant closures, providing a comprehensive overview of the factors driving these decisions and their far-reaching consequences. From the economic impacts on local communities to the company’s strategic responses, we will delve into the complexities surrounding these closures.
This analysis will explore the history of Tyson Foods, the specific locations affected, and the reasons cited by the company. We’ll investigate the economic repercussions, job losses, and community responses. Furthermore, the role of market conditions, operational efficiency, and industry trends will be scrutinized. Employee and union reactions, financial implications for Tyson Foods, governmental involvement, and the future outlook for the company will also be examined.
This comprehensive review aims to provide a clear understanding of the dynamics at play.
Overview of Tyson Foods Plant Closures
Tyson Foods, a prominent player in the global meat industry, has experienced a series of plant closures in recent years. These closures represent significant operational adjustments with far-reaching consequences for local economies, employee populations, and the overall market dynamics of the food sector. Understanding the factors driving these closures provides crucial insights into the evolving landscape of food production and the challenges faced by large-scale agricultural businesses.
History of Tyson Foods and Its Operations
Tyson Foods, Inc., founded in 1935 by John W. Tyson, began as a small poultry processing business in Springdale, Arkansas. The company initially focused on producing and selling chickens to local markets. Over time, Tyson Foods expanded its operations significantly, diversifying into beef, pork, and prepared foods. Through strategic acquisitions, such as the purchase of IBP (Iowa Beef Packers) in 2001, Tyson Foods solidified its position as one of the world’s largest meat processors and food companies.
Its operations encompass a wide range of activities, including:
- Raising and processing livestock.
- Manufacturing and distributing a variety of food products, including fresh and frozen meats, prepared meals, and snacks.
- Operating a vast network of processing plants, distribution centers, and retail partnerships across North America and internationally.
The company’s vertically integrated model, controlling aspects of the supply chain from animal feed to consumer products, has been a key factor in its growth and market dominance.
Recent Instances of Tyson Foods Plant Closures
In recent years, Tyson Foods has implemented several plant closures, impacting various communities and altering its operational footprint. These closures have been strategically planned, often involving the consolidation of production facilities and the restructuring of operations to optimize efficiency and profitability. Examples of these closures include:
- In 2023, Tyson Foods announced the closure of a poultry plant in Dexter, Missouri, impacting over 1,600 employees.
- A pork processing plant in Perry, Iowa, was also slated for closure in 2023, affecting approximately 1,300 employees.
- The company has also closed facilities in other locations, such as Wilkesboro, North Carolina, and Noel, Missouri, further consolidating its operations.
These closures often involve the transfer of production to other existing facilities or the reduction of overall processing capacity.
Primary Reasons Cited by Tyson Foods for These Closures
Tyson Foods has cited several primary reasons for the plant closures, reflecting broader trends in the meat industry and the challenges of maintaining a competitive advantage. These reasons include:
- Shifting Consumer Demand: Changes in consumer preferences, such as a growing demand for plant-based protein alternatives and evolving dietary trends, have influenced the demand for certain meat products.
- Operational Efficiency: The company aims to optimize its production network by consolidating operations and improving efficiency. This involves closing older, less efficient plants and concentrating production in newer, more technologically advanced facilities.
- Economic Factors: Factors such as rising labor costs, increased transportation expenses, and fluctuations in the cost of raw materials can impact profitability. Plant closures can be a strategic response to mitigate these economic pressures.
- Supply Chain Disruptions: Disruptions to the supply chain, including challenges in sourcing livestock and maintaining a consistent flow of materials, can affect plant operations.
- Market Conditions: Overcapacity in certain regions and shifts in the overall market dynamics can also contribute to closure decisions.
These factors often interact, making the decision-making process complex and necessitating strategic adjustments to maintain competitiveness in the evolving food industry.
Impact on Local Communities
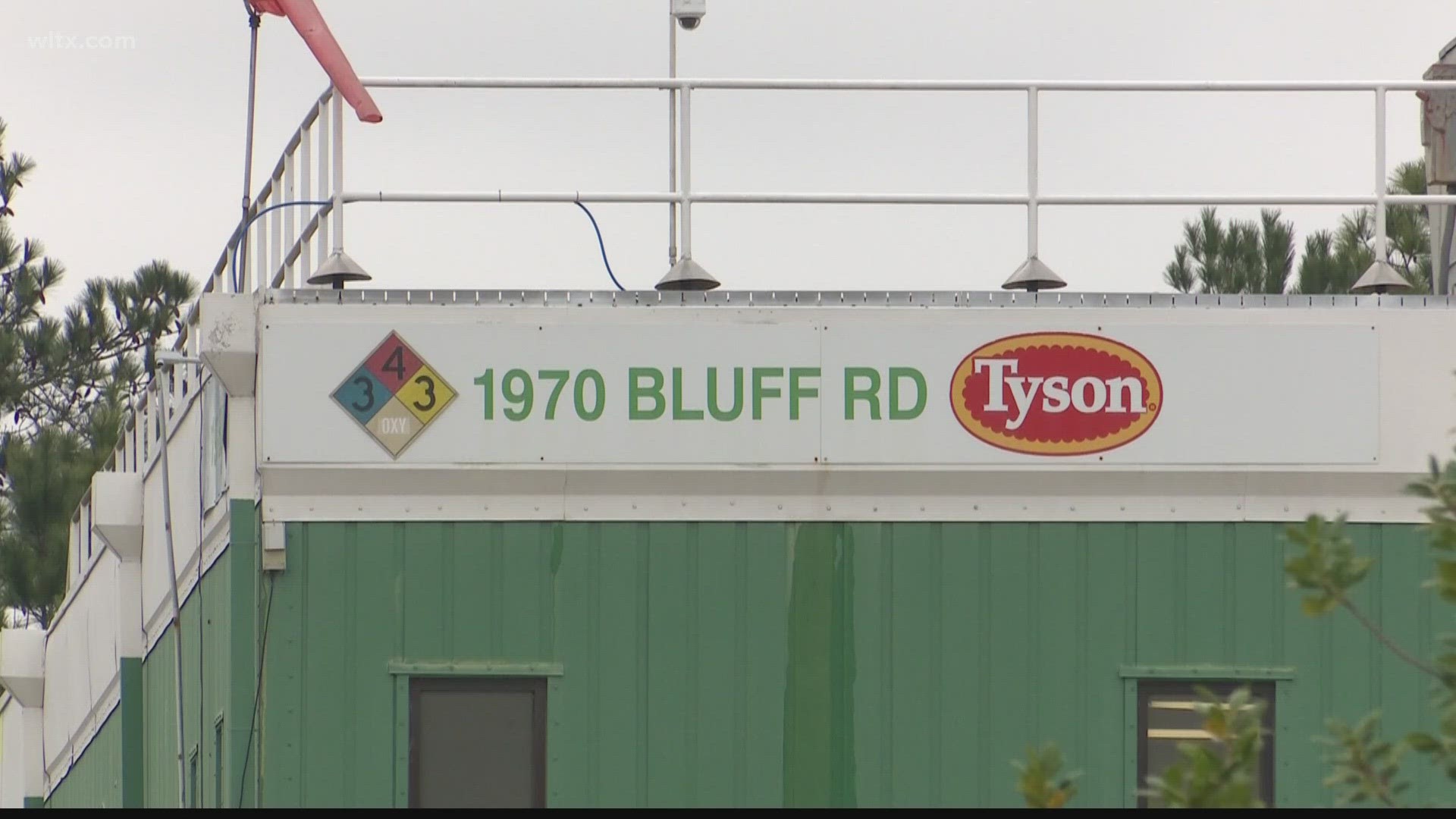
The closure of a major employer like a Tyson Foods plant reverberates throughout the local economy, causing significant disruption. The ripple effects extend beyond the immediate job losses, impacting various sectors and the overall well-being of the community. Understanding these consequences requires a detailed examination of economic indicators, workforce demographics, and community responses.
Economic Consequences of Plant Closures
Plant closures lead to a cascade of economic challenges for the affected communities. The loss of jobs directly reduces household income, leading to decreased consumer spending. This, in turn, impacts local businesses, potentially leading to further job losses and business closures.
Do not overlook explore the latest data about can tetras eat betta food.
- Reduced Tax Revenue: The decline in employment and business activity results in lower tax revenues for local governments. This impacts the funding of essential public services like schools, infrastructure maintenance, and emergency services. A town that relied heavily on property taxes from a now-closed plant may struggle to maintain its services.
- Decreased Property Values: The closure of a major employer often leads to a decrease in property values, as the demand for housing declines. This further impacts the tax base and can lead to a decline in home equity for residents. For example, homes near a closed Tyson plant in a rural area might see a significant drop in market value, making it harder for residents to sell or refinance.
- Strain on Social Services: Increased unemployment puts a strain on social services, such as food banks, unemployment benefits, and healthcare providers. These services often struggle to meet the increased demand with reduced funding. Food banks, for instance, may experience a surge in requests as laid-off workers struggle to afford basic necessities.
- Ripple Effect on Supporting Industries: Businesses that directly or indirectly support the plant, such as transportation companies, suppliers, and maintenance services, also experience significant losses. These companies may be forced to lay off employees or even close down. A trucking company specializing in transporting Tyson products could lose a significant portion of its business.
Job Losses and Affected Workforce Demographics
The workforce impacted by plant closures often reflects the demographic composition of the surrounding area. The characteristics of the workforce are crucial for understanding the long-term implications of job losses and for tailoring support initiatives.
- Employment Statistics: The number of employees directly affected by the plant closure is the most immediate impact. Data from the Bureau of Labor Statistics (BLS) is essential for quantifying these losses. The number of layoffs provides the baseline for understanding the magnitude of the economic disruption.
- Demographic Breakdown: Often, a significant portion of the workforce is comprised of specific demographic groups, including minorities, immigrants, and individuals with limited education. For example, if a plant closure disproportionately affects a community with a large Hispanic population, it may exacerbate existing economic disparities.
- Skill Levels and Wage Data: The skills and wages of the affected workers are crucial in determining the ability of these individuals to find new employment. Workers in the meatpacking industry may possess specialized skills, but these skills may not be easily transferable to other sectors. Lower-skilled, lower-wage workers often face the greatest challenges in finding new jobs.
- Age and Experience: The age and experience of the affected workers also influence their job prospects. Older workers may find it more difficult to secure new employment than younger workers. The loss of experienced workers can also create a knowledge gap within the community.
Community Support Initiatives and Challenges
Communities often respond to plant closures with a variety of support initiatives aimed at mitigating the negative impacts. These initiatives can range from providing job training and placement services to offering financial assistance and mental health support.
- Government Assistance Programs: Federal, state, and local governments often provide assistance to communities affected by plant closures. These programs can include unemployment benefits, job training grants, and economic development loans. For instance, the Trade Adjustment Assistance (TAA) program offers support to workers who have lost their jobs due to foreign competition.
- Job Training and Placement Services: Organizations like local community colleges and workforce development boards often offer job training programs designed to help laid-off workers acquire new skills and find employment. These programs might focus on areas with growing job opportunities, such as healthcare or manufacturing.
- Financial Assistance and Support: Food banks, charities, and religious organizations frequently step in to provide financial assistance, food, and other essential services to affected families. This support can help alleviate the immediate hardships caused by job loss.
- Mental Health Services: The stress and uncertainty associated with job loss can take a toll on mental health. Communities often provide counseling services and support groups to help individuals cope with these challenges.
- Challenges in Implementing Support: Despite the availability of support initiatives, communities often face challenges in implementing them effectively. These challenges can include limited funding, bureaucratic hurdles, and a lack of coordination among different agencies.
Factors Contributing to Closures
The closure of Tyson Foods plants represents a complex interplay of economic and operational factors. Understanding these drivers is crucial for comprehending the strategic shifts within the meat processing industry and their impact on local communities. This analysis will delve into the primary forces behind these closures, examining market dynamics, operational efficiencies, and the role of automation.
Market Conditions and Consumer Demand
Consumer preferences are a significant determinant of the meat industry’s trajectory. Shifts in these preferences can directly influence the viability of specific plant operations. These shifts, often driven by broader societal trends, impact the types of products demanded and the geographic distribution of demand.The evolution of consumer preferences has demonstrably influenced the meat industry. Several factors have contributed to this evolution:
- Changing Dietary Trends: The rising popularity of plant-based diets, flexitarianism, and concerns about the environmental impact of meat production have led to a decrease in demand for certain types of meat products, particularly red meat. For example, the market share of plant-based meat alternatives has steadily increased, putting pressure on traditional meat processors.
- Geographic Shifts in Demand: Demand patterns vary regionally and nationally. For instance, population growth in specific areas might increase demand for certain types of meat, while other areas experience declining demand. The relocation of production facilities often follows these shifts in consumer preferences.
- Evolving Product Preferences: Consumers are increasingly seeking convenience and value-added products. This means a greater demand for pre-packaged, portion-controlled, and ready-to-eat meat products, which can influence the types of processing facilities that remain competitive.
Operational Efficiency and Automation
Operational efficiency and the implementation of automation technologies are critical factors in determining a plant’s long-term viability. Plants that fail to modernize and adapt to these advancements often face significant cost disadvantages.The influence of operational efficiency and automation can be illustrated through several examples:
- Automation in Processing: Automation reduces labor costs, increases throughput, and improves consistency in product quality. Automated systems for tasks like deboning, packaging, and inspection can significantly increase the efficiency of a plant. Older plants with outdated equipment and manual processes are at a competitive disadvantage.
- Supply Chain Optimization: Efficient supply chains are crucial. Plants located closer to feed sources (for livestock) or distribution centers benefit from lower transportation costs and shorter lead times. Plants that are strategically positioned within the supply chain are more likely to survive.
- Scale of Operations: Larger plants often benefit from economies of scale, spreading fixed costs over a larger volume of production. Smaller, less efficient plants may struggle to compete with larger, more automated facilities.
Factors and Impact on Plant Locations
The table below Artikels specific factors and their potential impact on different plant locations. This table illustrates how a combination of market conditions and operational efficiencies can influence the closure of a plant. Note that the impact is a generalization, and specific circumstances can vary.
Factor | Impact on Plant Location A (Example: Rural, older facility) | Impact on Plant Location B (Example: Near major distribution hub) | Impact on Plant Location C (Example: High-automation facility) |
---|---|---|---|
Changing Consumer Demand (e.g., shift to poultry) | Significant negative impact if primarily focused on red meat. Limited flexibility to adapt. | Moderate impact, potentially needing to retool for different product lines or smaller volumes. | Moderate, depending on product mix and ability to quickly adapt to consumer trends. |
Labor Costs | High labor costs can erode profitability, especially if automation is limited. | Labor costs may be higher near a major distribution hub, impacting competitiveness. | Lower labor costs due to automation and more efficient processes. |
Automation and Technology Adoption | Lack of automation makes the plant less competitive, increasing operating costs. | May require investment in automation to remain competitive, but may be better positioned to do so. | High level of automation provides a significant competitive advantage, reducing costs and improving efficiency. |
Supply Chain Efficiency | Higher transportation costs if located far from livestock sources and distribution networks. | Potentially lower transportation costs due to proximity to major transportation routes. | Efficient supply chains are critical; strategic location is important for optimal performance. |
Industry Trends and Competitive Landscape
The meat processing industry is subject to dynamic shifts driven by consumer preferences, economic pressures, and technological advancements. Understanding these broader trends is crucial for analyzing the strategic decisions, including plant closures, made by major players like Tyson Foods. This section examines these trends and compares Tyson’s actions with those of its competitors.
Broader Trends Affecting the Meat Processing Industry
Several overarching trends are significantly impacting the meat processing sector. These factors are influencing production, distribution, and consumer behavior.* Changing Consumer Preferences: There is a noticeable shift towards plant-based protein alternatives and a growing demand for sustainably sourced and ethically produced meat products. Consumers are also increasingly concerned about the environmental impact of their food choices, leading to scrutiny of intensive farming practices.
Labor Challenges
The industry faces persistent labor shortages and rising labor costs. This is further complicated by issues such as worker safety concerns and the need for skilled labor in increasingly automated processing facilities.
Supply Chain Disruptions
Global events, such as pandemics and geopolitical instability, have exposed vulnerabilities in the meat supply chain. These disruptions can lead to fluctuating prices, reduced availability of raw materials, and logistical challenges.
Technological Advancements
Automation, artificial intelligence, and data analytics are being implemented to optimize production processes, improve efficiency, and enhance food safety. These technologies require significant capital investment and can alter the industry’s competitive landscape.
Regulatory Environment
Increasing government regulations regarding food safety, environmental sustainability, and animal welfare are adding to the complexity and cost of operations. Companies must adapt to these evolving standards to maintain compliance and consumer trust.
Comparison of Tyson Foods’ Closures with Competitor Actions
Tyson Foods’ plant closures are not an isolated phenomenon. Competitors are also re-evaluating their production footprints and strategies in response to market dynamics. Examining these actions provides context for understanding Tyson’s decisions.* JBS: JBS, a major global meat processor, has also been adjusting its operations. They have invested heavily in automation and technology to improve efficiency and reduce labor costs.
They have also expanded their presence in the plant-based protein market through acquisitions.
Cargill
Cargill has focused on optimizing its existing facilities and expanding its presence in emerging markets. They are investing in sustainable sourcing practices and exploring new technologies to improve animal welfare and reduce environmental impact.
National Beef Packing Company
National Beef has been concentrating on improving operational efficiency and adapting to shifts in consumer demand. They have made strategic investments in expanding their beef processing capacity.
Strategies Competitors are Employing to Adapt to Market Changes
To remain competitive, meat processing companies are implementing a variety of strategies. These strategies reflect the need to adapt to changing consumer preferences, economic pressures, and technological advancements.* Diversification into Alternative Proteins: Many companies are investing in or acquiring businesses in the plant-based protein sector to cater to the growing demand for meat alternatives. This includes developing their own product lines or partnering with existing plant-based food companies.
Automation and Technological Investments
Competitors are deploying automation, robotics, and artificial intelligence to streamline production processes, reduce labor costs, and improve efficiency. This involves significant investments in advanced equipment and data analytics.
Supply Chain Optimization
Companies are working to strengthen their supply chains by diversifying suppliers, improving logistics, and utilizing technology to track and manage inventory. This includes initiatives to mitigate the impact of supply chain disruptions.
Sustainability Initiatives
There is a growing emphasis on sustainable sourcing, reducing environmental impact, and improving animal welfare practices. This includes implementing programs to reduce greenhouse gas emissions, conserve water, and promote responsible land use.
Focus on Value-Added Products
Companies are increasingly focusing on producing value-added products, such as pre-cooked meals, ready-to-eat products, and specialized cuts of meat, to cater to changing consumer preferences and increase profit margins.
Strategic Partnerships and Acquisitions
Competitors are forming strategic partnerships and making acquisitions to expand their market reach, gain access to new technologies, and strengthen their product portfolios. This includes mergers and acquisitions within the industry and collaborations with technology companies.
Labor Management and Retention Strategies
Companies are implementing strategies to attract and retain workers, including competitive wages, benefits, and improved working conditions. This includes investing in worker training and development programs.
Employee and Union Responses
The closure of Tyson Foods plants triggered a multifaceted response from employees and labor unions, reflecting the significant impact on workers’ livelihoods and the economic stability of the affected communities. These responses ranged from expressions of grief and uncertainty to organized efforts aimed at mitigating job losses and securing worker benefits. Union involvement played a critical role in navigating the complexities of the closures, advocating for employees’ rights, and negotiating severance packages.
Employee Reactions to Plant Closures
The initial reaction from employees was often characterized by shock, disappointment, and anxiety. The sudden loss of a job, particularly in communities heavily reliant on a single employer, created significant personal and financial hardship. Many workers faced immediate concerns about their ability to pay bills, maintain healthcare coverage, and provide for their families. The closure also disrupted established social networks and community ties, as colleagues and friends were forced to relocate or seek alternative employment.
- Emotional Distress: Employees experienced significant stress and anxiety due to job insecurity and the uncertainty surrounding their future. The sudden loss of employment often led to feelings of anger, sadness, and fear.
- Financial Hardship: Many workers faced immediate financial difficulties, including the inability to pay rent or mortgages, cover healthcare costs, and afford basic necessities. The closure often occurred without sufficient notice, leaving employees with limited time to prepare financially.
- Community Impact: The closures not only affected individual workers but also had a ripple effect on the local communities. The loss of jobs reduced consumer spending, impacting local businesses and services.
- Job Search Challenges: Many Tyson Foods employees lacked the skills or experience to readily transition into new jobs, particularly in areas with limited employment opportunities. This often resulted in prolonged periods of unemployment and underemployment.
Union Involvement in Addressing Closures
Labor unions, representing a significant portion of Tyson Foods’ workforce, played a crucial role in responding to the plant closures. Their primary objectives were to protect the rights and interests of their members, negotiate severance packages, and provide support for displaced workers. Unions utilized their collective bargaining power to advocate for fair treatment, secure benefits, and assist employees in navigating the transition to new employment.
- Negotiating Severance Packages: Unions negotiated with Tyson Foods to secure severance packages that included financial compensation, extended healthcare benefits, and outplacement services. These packages were designed to provide a financial cushion and assist workers in their job search.
- Advocating for Worker Rights: Unions ensured that Tyson Foods adhered to labor laws and provided employees with the rights and protections to which they were entitled. This included ensuring fair treatment, preventing discrimination, and upholding safety standards during the closure process.
- Providing Support Services: Unions offered a range of support services to assist displaced workers. These services included career counseling, job training, resume writing assistance, and access to resources for finding new employment.
- Community Engagement: Unions often collaborated with local community organizations and government agencies to provide support to affected workers and address the broader economic impact of the plant closures.
“Our union is committed to ensuring that every member affected by these closures receives fair treatment and the support they need to navigate this difficult transition. We will fight to secure the best possible severance packages, protect worker rights, and provide resources to help our members find new employment.” – Statement from a United Food and Commercial Workers (UFCW) representative.
Financial Implications for Tyson Foods
The closure of Tyson Foods plants represents a significant strategic shift, with considerable financial ramifications for the company. These closures, while potentially streamlining operations in the long run, necessitate immediate costs and ongoing adjustments that directly affect profitability, market valuation, and overall financial health. Understanding the financial implications requires analyzing the immediate costs of closure, the strategies employed to mitigate losses, and the long-term impact on key financial metrics.
Immediate Costs Associated with Plant Closures
The decision to shutter a manufacturing plant entails a cascade of expenses that immediately impact Tyson Foods’ balance sheet. These costs can be substantial and include items such as severance packages, asset write-downs, and environmental remediation.
- Severance and Employee-Related Costs: This constitutes a significant initial outlay. It encompasses severance pay for laid-off employees, outplacement services to assist in job searching, and potential early retirement packages. The magnitude of these costs depends on factors like the number of employees affected, their tenure, and the terms negotiated with labor unions. For example, the closure of a large plant employing several hundred workers could easily result in tens of millions of dollars in severance expenses.
- Asset Write-downs and Impairment Charges: Plants often house specialized equipment and infrastructure. When a plant closes, the book value of these assets must be reassessed. If the fair market value is less than the carrying value on the balance sheet, an impairment charge is recorded. This charge reduces the company’s reported earnings in the period of the closure. The size of this charge depends on the age and condition of the plant’s assets.
Older plants with depreciated equipment might result in lower impairment charges than newer facilities.
- Environmental Remediation and Site Cleanup: Food processing plants can generate environmental liabilities, including wastewater treatment, waste disposal, and potential soil contamination. Closing a plant triggers the need for environmental assessments and remediation activities. These costs can vary widely depending on the location, the extent of contamination, and regulatory requirements.
- Inventory Disposal and Contractual Obligations: Closing a plant also necessitates dealing with existing inventory of raw materials, work-in-progress, and finished goods. These may need to be sold at a discount or disposed of entirely, leading to losses. Furthermore, Tyson Foods may have ongoing contractual obligations, such as supply agreements or lease agreements, that must be addressed, which may involve penalties or settlement payments.
Strategies to Mitigate Financial Losses
To counteract the negative financial impact of plant closures, Tyson Foods implements several strategic measures aimed at minimizing losses and optimizing resource allocation. These include consolidating production, streamlining the supply chain, and seeking government incentives.
- Consolidation of Production: This involves shifting production from closed plants to existing, more efficient facilities. By consolidating production, Tyson Foods can leverage economies of scale, reduce per-unit production costs, and improve overall capacity utilization. This can help to offset the fixed costs associated with the closed plants and improve profitability in the long run.
- Supply Chain Optimization: Streamlining the supply chain is crucial. This involves optimizing the flow of raw materials from suppliers to processing plants and the distribution of finished products to customers. This could involve renegotiating supplier contracts, adjusting transportation routes, and implementing more efficient warehousing practices. The goal is to reduce transportation costs, minimize waste, and improve overall efficiency.
- Cost-Cutting Initiatives: Tyson Foods often implements company-wide cost-cutting measures to offset the financial impact of plant closures. These may include reducing overhead expenses, streamlining administrative processes, and negotiating better terms with suppliers.
- Seeking Government Incentives and Tax Benefits: Plant closures can sometimes trigger eligibility for government incentives, such as tax credits, grants, and workforce development programs. Tyson Foods actively seeks these opportunities to offset closure costs and support affected communities.
- Strategic Asset Sales: The company might choose to sell the closed plant or its assets to other businesses, which can help recover some of the initial investment and reduce the overall financial impact of the closure.
Financial Snapshot: Key Metrics Before and After Closures, Tyson foods closed
Analyzing key financial metrics provides insights into the impact of plant closures on Tyson Foods’ performance. The following table presents a simplified financial snapshot, using hypothetical data to illustrate the potential impact. Actual figures would vary based on the specific closures and market conditions.
Metric | Before Closures (Year 1) | During Closures (Year 2) | After Closures (Year 3) | Notes |
---|---|---|---|---|
Revenue (USD Billion) | 50.0 | 48.0 | 49.0 | Initial decrease due to reduced production capacity, followed by stabilization through consolidation and efficiency gains. |
Cost of Goods Sold (USD Billion) | 40.0 | 39.0 | 39.5 | Initial decrease due to lower production volume, followed by stabilization due to efficient production and cost control. |
Gross Profit (USD Billion) | 10.0 | 9.0 | 9.5 | Reflects revenue and COGS trends. |
Operating Expenses (USD Billion) | 6.0 | 7.0 | 6.5 | Increase during closures due to severance, write-downs, and other related costs. Long-term reduction from efficiency. |
Operating Income (USD Billion) | 4.0 | 2.0 | 3.0 | Significant impact during closures, followed by recovery as efficiencies are realized. |
Net Income (USD Billion) | 2.8 | 1.4 | 2.1 | Reflects impact of operating income and one-time costs. |
Earnings Per Share (EPS) (USD) | 7.75 | 3.87 | 5.80 | Reflects impact of net income and outstanding shares. |
Note: This table is a simplified illustration. Actual results would vary depending on specific plant closures, market conditions, and other factors. It is critical to consult the company’s official financial reports for a comprehensive analysis.
Governmental and Regulatory Oversight: Tyson Foods Closed
The closure of Tyson Foods plants, with their significant economic and social impact, invariably attracts the attention of governmental bodies at various levels. This oversight involves a range of actions, from direct intervention to provide assistance to affected workers and communities to a broader examination of the regulatory environment that may have contributed to the closures. These governmental responses are crucial in mitigating the negative consequences and ensuring a degree of accountability.
Involvement of Governmental Agencies in Response to the Closures
Governmental agencies play a multifaceted role in responding to plant closures. This involvement can range from providing immediate support to displaced workers to conducting investigations into the underlying causes of the closures. The specific agencies involved and the nature of their actions depend on the scale of the closures, the geographic location, and the specific circumstances.
- Federal Agencies: The U.S. Department of Labor (DOL) is often a key player. The DOL, through its Employment and Training Administration (ETA), administers programs designed to assist workers who have lost their jobs due to plant closures. These programs may include providing funds for retraining, job search assistance, and unemployment benefits. The Occupational Safety and Health Administration (OSHA) may also become involved if the closures raise concerns about workplace safety violations.
- State Agencies: State governments, typically through their departments of labor or economic development, are also heavily involved. They often coordinate with federal agencies to provide assistance to affected workers and communities. This can include providing unemployment benefits, connecting workers with job opportunities, and offering resources for retraining. States may also offer financial incentives to companies that create new jobs in the affected areas.
- Local Agencies: Local governments, such as city or county administrations, are directly impacted by plant closures and often take the lead in addressing the immediate needs of affected communities. This might involve providing social services, working with local businesses to find employment opportunities, and assessing the economic impact of the closures.
Regulatory Factors or Policies Influencing the Decisions
Regulatory factors and policies can influence the decisions of food processing companies, including Tyson Foods, regarding plant closures. These factors can range from environmental regulations to labor laws and trade policies. Understanding these influences is crucial to understanding the full context of the closures.
- Environmental Regulations: Stricter environmental regulations, particularly those related to wastewater treatment, air emissions, and waste disposal, can increase the operational costs for food processing plants. Plants that are older or located in areas with more stringent environmental standards may find it more difficult to comply, potentially leading to closures or relocations. For instance, a plant facing significant investment to upgrade its wastewater treatment facilities might find it more cost-effective to close or move to a location with less stringent regulations.
- Labor Laws and Regulations: Labor costs, including wages, benefits, and compliance with labor laws, are significant factors for food processing companies. Regulations regarding minimum wage, overtime pay, and worker safety can impact operational costs. Changes in labor laws, such as increased minimum wage requirements or stricter enforcement of worker safety standards, can influence decisions about plant operations.
- Trade Policies: International trade policies, such as tariffs and trade agreements, can affect the competitive landscape for food processing companies. Changes in trade policies can alter the cost of raw materials or the ability to export products, potentially impacting plant operations. For example, the imposition of tariffs on imported meat products could make domestic production more competitive, while the removal of trade barriers could open up new markets.
- Taxation and Incentives: Tax policies and government incentives can influence the location and operation of food processing plants. Tax breaks, subsidies, and other financial incentives offered by state and local governments can encourage companies to locate or expand operations in certain areas. Conversely, changes in tax policies, such as increased corporate tax rates, can make operations less profitable.
Governmental Assistance Programs for Affected Workers
Governmental assistance programs are designed to provide support to workers who have lost their jobs due to plant closures. These programs aim to mitigate the economic hardship faced by displaced workers and help them find new employment. The specific types of assistance available vary depending on the location, the nature of the closure, and the specific programs offered by federal, state, and local governments.
- Unemployment Benefits: Unemployment insurance provides temporary financial assistance to workers who have lost their jobs through no fault of their own. These benefits are typically funded by employer taxes and are designed to provide a safety net while workers search for new employment. The duration and amount of benefits vary depending on state laws and the worker’s employment history.
- Trade Adjustment Assistance (TAA): TAA is a federal program designed to assist workers who have lost their jobs or whose jobs are threatened as a result of increased imports. TAA provides a range of benefits, including job search assistance, retraining, and income support. To be eligible, workers must typically be employed by a firm that has been certified as being adversely affected by trade.
- Workforce Development and Retraining Programs: These programs provide workers with the skills and training needed to find new employment. They may include classroom instruction, on-the-job training, and vocational programs. These programs are often funded by federal and state governments and are typically offered through local workforce development boards or community colleges. For example, a program might provide training in a high-demand field such as healthcare or information technology.
- Job Placement Services: Government agencies and non-profit organizations often provide job placement services to assist workers in finding new employment. These services may include resume writing assistance, interview skills training, and job search assistance. Job fairs and networking events are also common.
- Financial Counseling and Support Services: Displaced workers often face financial challenges. Governmental programs may provide financial counseling to help workers manage their finances, including budgeting, debt management, and access to financial assistance programs. Support services may also include assistance with accessing healthcare, housing, and other essential needs.
Future Outlook for Tyson Foods
Tyson Foods, like any major player in the food industry, faces a dynamic landscape of evolving consumer preferences, supply chain challenges, and economic pressures. The company’s future trajectory hinges on its ability to adapt and innovate, focusing on strategic restructuring, supply chain optimization, and operational footprint adjustments. These strategies are crucial for maintaining profitability and market share in a competitive environment.
Strategic Plans for Restructuring and Adaptation
Tyson Foods’ restructuring plans are designed to enhance operational efficiency and responsiveness to market demands. These plans often involve strategic divestitures, facility consolidations, and investments in automation and technology. This process aims to streamline operations, reduce costs, and improve overall agility.
- Portfolio Optimization: Tyson regularly assesses its product portfolio to identify underperforming segments or those with limited growth potential. This often leads to the sale of certain brands or product lines, allowing the company to focus on core competencies and high-growth areas such as value-added products and alternative protein sources. An example is the sale of its pet food business in 2023.
- Operational Efficiency: Investments in automation, robotics, and data analytics are critical. This includes upgrading existing facilities and building new, technologically advanced plants. These measures aim to reduce labor costs, improve processing speeds, and enhance product quality.
- Geographic Footprint Adjustments: Facility closures, like those discussed earlier, are part of a broader strategy to optimize the company’s geographic presence. This includes consolidating operations in regions with lower costs and favorable market access, while also expanding in areas with growing consumer demand.
- Innovation and Product Development: Tyson is investing heavily in research and development to create new products that cater to evolving consumer preferences. This includes plant-based protein alternatives, ready-to-eat meals, and products with enhanced nutritional profiles. For instance, Tyson’s acquisition of Keystone Foods focused on value-added products and international expansion.
Supply Chain Management Strategies
Managing the supply chain effectively is paramount for Tyson Foods, given the complexity of sourcing raw materials, processing them, and distributing finished products. The company employs various strategies to mitigate risks, enhance efficiency, and ensure product availability.
- Diversification of Sourcing: To reduce reliance on any single supplier or geographic region, Tyson diversifies its sourcing of raw materials, including livestock, grains, and packaging materials. This helps mitigate risks associated with weather events, disease outbreaks, and geopolitical instability.
- Vertical Integration: Tyson has a degree of vertical integration, particularly in poultry and beef production. This allows the company to control more of its supply chain, from breeding and raising livestock to processing and distribution. This integration improves efficiency and reduces costs.
- Technology Integration: The company utilizes technology, including blockchain, to improve traceability, transparency, and food safety across its supply chain. This technology allows for better tracking of products from origin to consumer, reducing the risk of contamination and enabling faster recall responses.
- Inventory Management: Tyson employs advanced inventory management techniques, such as just-in-time inventory and demand forecasting, to minimize storage costs and ensure products are available when needed. This is particularly important for perishable goods.
- Transportation and Logistics Optimization: Optimizing transportation and logistics is critical for timely delivery and cost efficiency. Tyson leverages data analytics and route optimization software to streamline its distribution network. The use of refrigerated transportation and cold chain management is crucial for maintaining product quality and safety.
Visual Representation of Tyson Foods’ Future Operational Footprint
The future operational footprint of Tyson Foods can be envisioned as a globally distributed network, optimized for efficiency and responsiveness.
Description of the Image:
The image represents a world map, color-coded to depict Tyson Foods’ key operational regions. Each region is visually characterized by circles, the size of which indicates the relative significance of that region’s operations. The circles are divided into two or three colors, indicating various aspects of operations, such as production facilities (processing plants), distribution centers, and research and development facilities.
Production facilities, represented by the largest, centrally located circles, are clustered in regions like North America (primarily the United States) and South America (Brazil, Argentina). These circles are colored with a gradient of greens and blues to represent meat and poultry processing facilities, respectively. Smaller circles, colored orange and purple, indicate distribution centers, strategically placed to serve the production facilities and facilitate the delivery of products to major consumer markets.
Research and development facilities are shown as small yellow circles, strategically positioned near the production and distribution centers to promote innovation and product development. The map also includes arrows to indicate the flow of raw materials from suppliers to production facilities, and finished products from processing plants to distribution centers and consumers. These arrows represent the company’s supply chain. The entire map is designed to illustrate a streamlined, globally integrated operation.
Conclusion
In conclusion, the closure of Tyson Foods plants reflects broader industry shifts and economic realities. The impact on communities, employees, and the company itself is substantial. While Tyson Foods navigates restructuring and adapts to evolving market demands, the future holds uncertainty. This review underscores the importance of understanding these complex challenges and the need for strategic planning and support for those affected by these closures.