Disposable food boats, seemingly humble containers, are actually the unsung heroes of the food industry. They’re the silent partners in our fast-paced lives, carrying everything from crispy fries to steaming noodles, often without a second thought. These practical vessels have evolved from simple paper trays to sophisticated designs, adapting to the ever-changing demands of the culinary world and our ever-growing need for convenience.
This article will explore the fascinating world of disposable food boats, dissecting their construction, applications, and the impact they have on both our daily lives and the environment. We’ll dive into the various types, materials, and manufacturing processes, from the familiar paperboard boats to the more modern, eco-conscious alternatives. We’ll also examine their role in different industries, from fast food to food trucks, and how they’ve become indispensable for food vendors and consumers alike.
Get ready for a deep dive into the world of food boats!
Introduction to Disposable Food Boats
Disposable food boats serve as a fundamental element within the food service industry, providing a convenient and sanitary means of containing and transporting food items. Their primary function is to offer a readily available and cost-effective solution for portioning, presenting, and consuming food products, particularly in environments where immediate consumption or portability is prioritized. They have become ubiquitous in various settings, ranging from fast-food restaurants and street vendors to catered events and food delivery services.
Basic Function and Purpose
The core purpose of disposable food boats revolves around containment and presentation. These vessels are designed to hold food items, preventing spills and facilitating easy handling for both the vendor and the consumer. They offer a protective barrier, maintaining the food’s temperature and minimizing direct contact with the user’s hands or external surfaces. Moreover, food boats contribute to portion control, providing a standardized serving size that assists in managing costs and ensuring consistency in food presentation.
They also often incorporate features like grease resistance and structural integrity to maintain the food’s quality and prevent structural failure during handling.
Brief History of Use and Evolution
The evolution of disposable food boats reflects advancements in material science and manufacturing processes, alongside changing consumer habits. Early iterations, predating widespread industrialization, involved rudimentary containers crafted from natural materials.
- Early Forms: Before the advent of mass production, food was often served on leaves, in wooden bowls, or wrapped in paper. These methods were primarily used by street vendors and in informal settings.
- Paper-Based Boats: The late 19th and early 20th centuries saw the emergence of paper-based food containers, coinciding with the rise of fast-food establishments. These paper boats, initially simple in design, provided a more sanitary and convenient alternative to reusable options.
- Wax-Coated Paper and Cardboard: The development of wax-coated paper and cardboard significantly improved the functionality of food boats. The wax coating provided a barrier against grease and moisture, extending the container’s lifespan and enhancing its performance with greasy foods.
- Plastic and Foam: The mid-20th century witnessed the introduction of plastic and expanded polystyrene foam (EPS) as materials for food boats. These materials offered enhanced durability, insulation properties, and cost-effectiveness, leading to their widespread adoption.
- Sustainability Concerns and Modern Innovations: In recent decades, environmental concerns have driven the development of more sustainable food boat alternatives. This has led to the exploration and adoption of compostable materials, such as plant-based plastics, molded pulp, and biodegradable paper.
Typical Materials Used in Construction
The materials used in the construction of disposable food boats have evolved significantly, driven by factors such as cost, performance, and environmental impact.
- Paper and Cardboard: Paper and cardboard are commonly used, often with coatings to enhance their functionality.
- Wax-Coated Paper/Cardboard: Wax coatings provide grease resistance and moisture barriers. The wax seals the paper fibers, preventing oil and water from penetrating the material.
- Polyethylene (PE) Coated Paper/Cardboard: Polyethylene coatings offer similar benefits to wax, with enhanced durability and heat resistance. PE is a thermoplastic polymer that provides a waterproof and grease-resistant barrier.
- Polystyrene Foam (Expanded Polystyrene – EPS): EPS, also known as Styrofoam, provides excellent insulation properties and is lightweight.
- Production: EPS is manufactured by expanding polystyrene beads with a blowing agent, creating a lightweight foam structure.
- Environmental Concerns: EPS is non-biodegradable and contributes to landfill waste. Its production and disposal have raised significant environmental concerns.
- Plastic: Various plastics, such as polypropylene (PP) and polyethylene terephthalate (PET), are utilized for their durability, moisture resistance, and moldability.
- Polypropylene (PP): PP is a thermoplastic polymer known for its high melting point and chemical resistance. It is commonly used in food boats due to its ability to withstand high temperatures.
- Polyethylene Terephthalate (PET): PET is a clear, strong, and recyclable plastic. It is frequently used in clear food containers, allowing for visual inspection of the contents.
- Alternative and Sustainable Materials: Increasing environmental awareness has led to the development and adoption of alternative materials.
- Molded Pulp: Molded pulp is made from recycled paper and plant fibers. It is biodegradable and compostable.
- Polylactic Acid (PLA): PLA is a bioplastic derived from renewable resources like corn starch. It is compostable under specific conditions.
- Bagasse: Bagasse is a byproduct of sugarcane processing. It is a renewable and compostable material used for food boats.
Types and Varieties
Disposable food boats exhibit a diverse range of designs, primarily categorized by shape and size, to accommodate various food types and portion sizes. The materials employed in their construction significantly influence their performance characteristics, including structural integrity, heat resistance, and environmental impact. Understanding these variations is crucial for selecting the most appropriate food boat for a specific application, considering both functionality and sustainability.
Shapes and Sizes
Food boats are manufactured in a spectrum of shapes and sizes to cater to a wide array of food items, from small snacks to larger entrees. This adaptability ensures efficient food presentation and portion control.
- Tapered Boats: These are characterized by a narrow base that widens towards the top. They are commonly used for serving items like french fries, onion rings, and other fried foods. Their design provides a stable base while allowing for easy access to the food. They are also sometimes used for single-serving portions of pasta or rice dishes.
- Boat-Shaped Boats: The classic boat shape features a rounded bottom and slightly flared sides, resembling a small boat. They are well-suited for holding foods with sauces or gravies, such as chili, nachos, or ice cream sundaes. The curved design helps contain liquids and prevents spills.
- Rectangular Boats: These offer a simple, flat-bottomed design that is suitable for serving sandwiches, wraps, or other flat foods. Their rectangular shape maximizes surface area and provides a stable platform.
- Compartmentalized Boats: These boats are divided into multiple sections, allowing for the separation of different food items. They are commonly used in cafeterias or food trucks to serve meals with multiple components, such as a main dish, side dish, and sauce.
Materials Used
The materials used in the construction of disposable food boats dictate their functional properties and environmental footprint. Paper, cardboard, and foam are the most prevalent materials, each with distinct advantages and disadvantages.
The following table compares the key attributes of these materials:
Material | Advantages | Disadvantages | Common Applications |
---|---|---|---|
Paper |
|
|
|
Cardboard |
|
|
|
Foam (Expanded Polystyrene – EPS) |
|
|
|
Applications and Industries
Disposable food boats are ubiquitous in the modern food service landscape, providing a practical and cost-effective solution for food presentation, transportation, and consumption. Their versatility has led to their widespread adoption across a variety of industries, each with specific needs and preferences dictating the type of boat utilized. This adaptability has significantly impacted operational efficiency and customer experience in these sectors.
Primary Industries Utilizing Disposable Food Boats
Several key industries rely heavily on disposable food boats due to their convenience, hygiene, and affordability. The specific types and materials employed vary depending on the industry’s demands and the food items served.
- Fast Food Restaurants: Fast food establishments are among the largest consumers of food boats. These boats are essential for serving a wide range of items quickly and efficiently.
- Food Trucks and Street Vendors: Mobile food businesses benefit greatly from the portability and ease of use that food boats offer. They enable vendors to serve food in various locations with minimal cleanup.
- Concession Stands and Stadiums: Sporting events, concerts, and other large gatherings necessitate efficient food service. Food boats are ideal for handling high volumes of customers and minimizing wait times.
- Catering and Events: Caterers use food boats for presenting and serving food at events. Their disposable nature simplifies cleanup and reduces the need for dishwashing.
- Grocery Stores and Delis: Pre-packaged foods and prepared meals are often sold in disposable food boats, providing a convenient option for consumers.
Food Items Commonly Served in Each Type of Boat
The selection of food boats is closely tied to the type of food being served. Different materials and designs are optimized for specific food items to maintain quality and prevent leaks or degradation.
- Fast Food Restaurants:
- French Fry Boats: Typically made of paperboard or coated paper, these are designed to hold fries and prevent grease absorption.
- Chicken Nugget Boats: Similar to fry boats, but often with a slightly different shape to accommodate nuggets.
- Taco Boats: These are designed to hold tacos or similar items, often made of molded pulp or coated paper to prevent leaks.
- Food Trucks and Street Vendors:
- Taco Boats: Frequently used for tacos, burritos, and similar handheld foods.
- Nachos Boats: Designed to hold nachos, often made from paperboard or molded pulp, to withstand the weight of toppings.
- Hot Dog Boats: Simple boats or trays for holding hot dogs and other similar items.
- Concession Stands and Stadiums:
- Popcorn Containers: Often made of paperboard, these are designed to hold large quantities of popcorn.
- Nachos and Cheese Boats: Similar to those used by food trucks, but potentially larger in size.
- Pretzel Boats: Boats designed to hold pretzels.
- Catering and Events:
- Finger Food Boats: Used for serving appetizers and finger foods, often made from various materials, including paper, molded pulp, or even biodegradable options.
- Miniature Food Boats: Smaller boats for serving individual portions of various dishes.
- Grocery Stores and Delis:
- Salad Containers: Often made of plastic or compostable materials, designed to hold salads and other prepared foods.
- Prepared Meal Containers: Containers for pre-packaged meals, often made of plastic or materials that can be microwaved.
Convenience Offered in Various Settings
The convenience offered by disposable food boats extends beyond simple functionality. They significantly impact operational efficiency, hygiene, and customer experience.
- Operational Efficiency: Disposable food boats streamline food service operations by eliminating the need for dishwashing. This reduces labor costs and increases the speed of service, particularly in high-volume settings.
- Hygiene and Food Safety: Disposable boats provide a hygienic solution by eliminating the risk of cross-contamination. Each serving uses a fresh, clean container, reducing the chances of spreading bacteria or viruses.
- Portability and Ease of Use: Food boats are designed for easy handling and portability, making them ideal for takeout, delivery, and on-the-go consumption. This is particularly important for food trucks, street vendors, and event catering.
- Cost-Effectiveness: While the cost of disposable boats adds to the overall expenses, their convenience and labor-saving benefits often outweigh the initial investment, especially for businesses with high customer turnover.
- Customization and Branding: Disposable food boats can be customized with logos, branding, and promotional messages. This provides an opportunity for businesses to enhance their brand visibility and customer experience. For example, a fast-food restaurant might print its logo and a limited-time offer on its fry boats.
Environmental Impact and Sustainability
The widespread use of disposable food boats presents significant environmental challenges, primarily stemming from the materials used in their production and their subsequent disposal. Addressing these concerns requires a multifaceted approach that considers the entire lifecycle of these products, from resource extraction to end-of-life management. This section explores the environmental consequences of conventional food boats, examines more sustainable alternatives, and proposes strategies to mitigate their impact.
Environmental Concerns Associated with Disposable Food Boats
Disposable food boats, particularly those made from polystyrene foam (Styrofoam) and conventional paper, contribute substantially to environmental pollution. The production processes, material properties, and disposal methods collectively exacerbate these negative impacts.
- Resource Depletion: The manufacturing of these food boats often relies on the extraction of raw materials such as petroleum for polystyrene foam and wood pulp for paper-based products. This extraction process can lead to deforestation, habitat destruction, and the depletion of finite resources. For example, the production of paper requires significant water and energy inputs, further straining environmental resources.
- Greenhouse Gas Emissions: The production of polystyrene foam involves the use of fossil fuels and releases greenhouse gases, contributing to climate change. The manufacturing of paper also releases greenhouse gases due to the energy-intensive processes involved. Furthermore, the transportation of raw materials and finished products adds to the carbon footprint.
- Waste Generation and Landfill Burden: Disposable food boats are frequently discarded after a single use, generating vast amounts of waste. Polystyrene foam is particularly problematic because it is non-biodegradable and can persist in the environment for centuries. Paper-based food boats, while biodegradable under certain conditions, can still contribute to landfill overflow if not properly managed. The sheer volume of these items adds to the burden on landfills, which are often nearing capacity.
- Pollution and Litter: Discarded food boats frequently end up as litter, polluting waterways, landscapes, and oceans. Polystyrene foam breaks down into smaller pieces, known as microplastics, which can be ingested by marine life, posing a threat to ecosystems and potentially entering the human food chain. Paper-based products can also contribute to litter and aesthetic degradation of the environment.
- Toxic Chemicals: The manufacturing of some food boats, particularly those made from bleached paper or containing certain additives, can involve the use of toxic chemicals. These chemicals can leach into the environment during production, use, and disposal, potentially contaminating soil and water sources.
Alternative Materials that are More Eco-Friendly
Several alternative materials offer more sustainable options for disposable food boats, minimizing the environmental footprint compared to conventional materials. These alternatives often emphasize renewable resources, biodegradability, and reduced reliance on fossil fuels.
- Compostable Materials: Food boats made from compostable materials, such as molded pulp (made from recycled paper or plant fibers), are designed to break down naturally in composting facilities or home compost piles. These materials typically meet standards like ASTM D6400, ensuring biodegradability under specific composting conditions. For instance, molded pulp food boats decompose within a few months in a commercial composting facility, returning nutrients to the soil.
- Biodegradable Plastics: Certain plastics, such as polylactic acid (PLA) derived from renewable resources like corn starch, are biodegradable under specific conditions. PLA food boats can be composted in commercial facilities, offering a more sustainable alternative to polystyrene foam. However, it is important to note that PLA may not readily biodegrade in all environments, and proper disposal in a composting facility is crucial.
- Bagasse: Bagasse, a byproduct of sugarcane processing, is a readily available and renewable resource that can be molded into food boats. Bagasse products are compostable and offer excellent insulation properties, making them suitable for hot and cold foods. The use of bagasse also helps reduce waste in the sugarcane industry.
- Bamboo: Bamboo is a rapidly renewable resource that can be harvested sustainably. Bamboo food boats are often biodegradable and compostable, offering a strong and lightweight alternative. Bamboo’s rapid growth rate makes it a sustainable choice for food packaging.
- Reusable Options: While not a material, reusable food boats made from durable materials like stainless steel or polypropylene are a viable solution. These options reduce waste by eliminating the need for single-use items. They can be cleaned and reused multiple times, offering significant environmental benefits.
Design a Plan to Minimize the Environmental Impact of Disposable Food Boats
Minimizing the environmental impact of disposable food boats requires a comprehensive strategy that addresses production, consumption, and disposal. This plan encompasses several key elements.
- Material Selection and Sourcing: Prioritize the use of compostable, biodegradable, and renewable materials. Ensure that these materials are sourced sustainably, with certifications such as Forest Stewardship Council (FSC) for paper products. Invest in materials that have a lower environmental impact during production, such as those with reduced energy and water consumption.
- Design for Disassembly and Recyclability: Design food boats to be easily disassembled and recycled, where possible. Avoid the use of mixed materials that complicate the recycling process. Label products clearly with recycling instructions and composting guidelines.
- Production Efficiency: Implement efficient manufacturing processes to minimize waste and energy consumption. Optimize the use of raw materials to reduce waste generation during production. Consider using renewable energy sources to power manufacturing facilities.
- Consumer Education and Awareness: Educate consumers about the environmental impacts of different food boat materials. Provide clear instructions on proper disposal methods, including composting and recycling guidelines. Promote the use of reusable food boats through educational campaigns and incentives.
- Infrastructure Development: Advocate for the development of composting and recycling infrastructure to support the proper disposal of food boats. Support the establishment of commercial composting facilities in areas where compostable materials are used. Collaborate with local governments to improve waste management systems.
- Extended Producer Responsibility: Advocate for policies that hold producers responsible for the end-of-life management of their products. This can include financial incentives for using sustainable materials and disincentives for using non-recyclable materials.
- Lifecycle Assessment (LCA): Conduct lifecycle assessments to evaluate the environmental impact of different food boat materials and designs. This helps identify areas for improvement and inform decision-making.
- Collaboration and Partnerships: Collaborate with businesses, environmental organizations, and government agencies to implement sustainable practices. Share best practices and work together to develop innovative solutions. For instance, partnerships with restaurants and food vendors to promote the use of compostable packaging.
Design and Features: Disposable Food Boats
Disposable food boats, engineered for the efficient and hygienic transport and presentation of food items, incorporate a variety of design features to optimize functionality, environmental impact, and consumer experience. These features are carefully considered and integrated based on the intended use of the food boat, the type of food it will contain, and the desired level of sustainability. The design process often involves trade-offs between cost, performance, and environmental considerations.
Common Design Features
The design of disposable food boats is driven by several core functional requirements, leading to the incorporation of specific features. These features can be categorized based on their primary purpose: containment, structural integrity, and user experience.
- Containment Features: These features are primarily concerned with preventing leaks and maintaining the integrity of the food contents.
- Coatings: Often, food boats are coated with a barrier layer to prevent grease and moisture from penetrating the material. Common coatings include polyethylene (PE), polylactic acid (PLA) for compostable options, and aqueous dispersions. These coatings are crucial for maintaining the structural integrity of the boat and preventing the food from sticking.
- Seams and Closures: The method used to construct the boat (e.g., folding, gluing, heat sealing) and any integrated closures (e.g., flaps, tabs, or snap-on lids) are critical for preventing spills. The design of the seams and closures must withstand the weight and movement of the food contents.
- Compartments: Many food boats feature compartments to separate different food items, preventing them from mixing and preserving their individual textures and flavors. This is particularly important for items with sauces or condiments.
- Structural Integrity Features: These features are designed to ensure the boat can withstand handling, stacking, and transportation without collapsing or deforming.
- Material Thickness and Density: The thickness and density of the material (e.g., paperboard, molded pulp, or expanded polystyrene) directly impact the boat’s strength and rigidity. Thicker and denser materials generally offer greater structural support.
- Reinforced Edges and Corners: Design elements like folded edges, reinforced corners, and corrugated structures can significantly enhance the boat’s resistance to crushing and bending. These reinforcements distribute the load more effectively.
- Base Design: The base of the boat plays a crucial role in its stability. A wider, flat base provides greater stability, preventing the boat from tipping over.
- User Experience Features: These features focus on ease of use and consumer satisfaction.
- Shape and Ergonomics: The shape of the boat, including its height, width, and the angle of its sides, impacts how easy it is for the consumer to hold and eat from. Rounded edges and comfortable grip areas can enhance the user experience.
- Temperature Resistance: Depending on the food item, the boat may need to withstand high or low temperatures. Materials and coatings must be selected accordingly to prevent warping or degradation.
- Ventilation: Some designs incorporate ventilation holes or slots to prevent condensation buildup and maintain the crispness of the food.
Food Boat Design for a Specific Food Item: French Fries, Disposable food boats
Consider the design of a disposable food boat specifically for serving French fries. This design prioritizes grease resistance, structural integrity, and consumer convenience.The design incorporates the following:
- Material: A paperboard substrate coated with a thin layer of polyethylene (PE) on the interior surface for grease resistance. The paperboard would be sourced from sustainably managed forests, aiming for a balance between functionality and environmental responsibility.
- Dimensions: The boat would be rectangular, with dimensions of 6 inches (15.2 cm) in length, 4 inches (10.2 cm) in width, and 2 inches (5.1 cm) in height. These dimensions provide an appropriate volume for a standard serving of French fries.
- Shape: The boat would have slightly tapered sides to facilitate easy access to the fries. The base would be flat and relatively wide (3.5 inches or 8.9 cm) to provide stability.
- Construction: The boat would be formed from a single piece of paperboard, folded and glued along the seams. The seams would be designed to be strong and leak-resistant.
- Features:
- A small vent hole at the top of the boat to allow steam to escape, preventing the fries from becoming soggy.
- A slightly textured exterior surface to improve grip.
- The option of an integrated flap or lid for transportation.
The design of this French fry boat aims to provide a functional and consumer-friendly experience while minimizing environmental impact through the selection of materials and design choices. The PE coating, for example, prevents grease penetration and maintains structural integrity, allowing the fries to stay crispier for a longer time.
Manufacturing Processes
The production of disposable food boats involves diverse manufacturing techniques, depending on the materials used. Understanding these processes is crucial for evaluating the environmental impact, cost-effectiveness, and performance characteristics of each type of boat. This section will explore the manufacturing of paper, cardboard, and foam food boats, along with the quality control measures implemented throughout the production cycle.
Paper and Cardboard Food Boat Manufacturing
The manufacturing of paper and cardboard food boats is a multi-step process involving pulping, forming, printing, cutting, and assembly. This process utilizes readily available materials and established manufacturing techniques, leading to varying levels of sustainability and performance.The typical manufacturing process involves these stages:
- Pulping: This initial step involves transforming raw materials, such as wood pulp or recycled paper, into a slurry. The pulp is prepared by mechanically or chemically breaking down the fibers. Water and additives, such as binders and strengthening agents, are mixed into the pulp.
- Forming: The pulp slurry is then fed onto a forming machine. The machine spreads the pulp evenly across a moving wire mesh. Water drains through the mesh, leaving a mat of paper fibers. The thickness and density of the paper are controlled at this stage.
- Drying: The paper mat then passes through a series of heated rollers to remove excess moisture. This drying process strengthens the paper and gives it its final form.
- Printing (Optional): If printing is required (for branding, logos, or food-related information), the paper is printed using various methods, such as flexography or offset printing.
- Cutting and Scoring: The printed or plain paper is then cut into the desired shapes and sizes for the food boats. Scoring lines are often added to facilitate folding and assembly.
- Assembly: The cut and scored paper is folded and assembled into the final food boat shape. This may involve gluing, stapling, or other fastening methods.
- Coating (Optional): For enhanced water resistance and grease resistance, the paper or cardboard may be coated with a thin layer of wax, polyethylene (PE), or other barrier coatings.
Foam Boat Manufacturing
Foam food boats, typically made from expanded polystyrene (EPS) or similar materials, employ a different manufacturing process. The process involves several steps, which results in a lightweight and insulating product.The manufacturing process typically involves these steps:
- Pre-expansion: Raw polystyrene beads are pre-expanded using steam. This process increases the volume of the beads and reduces their density.
- Molding: The pre-expanded beads are then placed into a mold that defines the shape of the food boat. Steam is injected into the mold, causing the beads to expand further and fuse together.
- Cooling: After the molding process, the molded foam boat is cooled to stabilize its shape.
- Ejection: The finished foam boat is ejected from the mold.
- Trimming (Optional): Any excess foam or imperfections are trimmed from the boat to ensure a clean and consistent product.
Quality Control Measures
Quality control is crucial in the manufacturing of disposable food boats to ensure product consistency, performance, and safety. These measures are implemented at various stages of the production process.Quality control measures typically include:
- Raw Material Inspection: Before the manufacturing process begins, raw materials, such as paper pulp, cardboard, polystyrene beads, and coatings, are inspected for quality. This includes checking for impurities, consistency, and compliance with material specifications.
- Process Monitoring: Throughout the manufacturing process, parameters such as temperature, pressure, and speed are monitored to ensure they meet the required specifications.
- Dimensional Checks: The dimensions of the food boats are regularly checked to ensure they meet the design specifications. This includes measuring length, width, height, and wall thickness.
- Strength Testing: The strength of the food boats is tested to ensure they can withstand the weight of food and the rigors of handling and transportation. Tests may include compression tests, drop tests, and leak tests.
- Coating Inspection: If the food boats are coated, the coating is inspected for uniformity, coverage, and adhesion. The coating’s resistance to water and grease is also tested.
- Printing Inspection: If printing is involved, the quality of the printing is checked for clarity, color accuracy, and alignment.
- Leak Testing: For boats intended to hold liquids, leak tests are conducted to ensure that the boats are watertight.
- Visual Inspection: Finished food boats are visually inspected for defects, such as cracks, tears, or imperfections in the shape or finish.
- Compliance Testing: Food boats are tested to ensure they comply with relevant food safety regulations and standards, such as those set by the Food and Drug Administration (FDA) in the United States or similar agencies in other countries.
Regulations and Standards
The production and use of disposable food boats are subject to a variety of regulations and standards designed to ensure food safety, environmental protection, and consumer protection. Compliance with these requirements is crucial for manufacturers to legally operate and for consumers to trust the safety and suitability of the products. These regulations vary by region and often encompass multiple aspects of the food boat lifecycle, from material sourcing to disposal.
Browse the implementation of best food festivals in real-world situations to understand its applications.
Food Safety Regulations
Food safety regulations are paramount in governing the production and use of disposable food boats. These regulations are primarily focused on preventing the contamination of food with harmful substances.
- Material Compliance: Regulations often dictate the types of materials that can be used in food contact applications. For example, in the United States, the Food and Drug Administration (FDA) regulates food contact materials under 21 CFR (Code of Federal Regulations). This includes specific requirements for the materials used in disposable food boats, ensuring they are safe and do not leach harmful chemicals into the food.
European Union regulations, such as Regulation (EC) No 1935/2004, set similar standards, with an emphasis on inertness and the prevention of migration of substances into food.
- Manufacturing Processes: The manufacturing process must adhere to stringent guidelines to minimize the risk of contamination. This includes maintaining hygienic conditions in manufacturing facilities, using food-grade lubricants and adhesives, and implementing quality control checks throughout the production process.
- Migration Testing: A critical aspect of food safety regulations involves migration testing. This process assesses the potential for substances from the food boat to migrate into the food itself. The testing is typically conducted under simulated use conditions, such as exposure to different food types (e.g., acidic, fatty) and temperatures. Regulatory limits are established for the maximum allowable migration levels of specific substances.
- Labeling Requirements: Accurate and informative labeling is essential. Regulations specify the information that must be included on food boat packaging, such as material composition, intended use, and any warnings or restrictions. For example, labeling may need to indicate whether the food boat is suitable for microwave use or if it contains any allergens.
Environmental Regulations and Sustainability Standards
Environmental regulations and sustainability standards address the environmental impact of disposable food boats, particularly concerning waste management and resource utilization.
- Material Restrictions: Regulations may restrict or prohibit the use of certain materials, especially those that are difficult to recycle or that contribute to pollution. For instance, some jurisdictions have banned or restricted the use of expanded polystyrene (EPS) foam due to its environmental impact.
- Recycling and Compostability Standards: Standards like those set by the Biodegradable Products Institute (BPI) define requirements for compostable food service products. These standards Artikel the conditions under which a product must biodegrade, ensuring that it breaks down into natural components in a composting environment.
- Extended Producer Responsibility (EPR): EPR schemes hold manufacturers responsible for the end-of-life management of their products. This may involve financing or operating recycling programs, reducing waste, and encouraging the design of more sustainable products.
- Waste Management Regulations: Regulations governing waste disposal and recycling are critical. These may include requirements for sorting and separation of waste, restrictions on landfill disposal, and incentives for recycling.
Certifications for Manufacturers
Manufacturers often seek certifications to demonstrate their compliance with relevant regulations and standards. These certifications provide assurance to consumers and regulatory bodies that the products meet specific criteria.
- ISO Certifications: The International Organization for Standardization (ISO) offers a range of certifications relevant to food boat manufacturing.
- ISO 9001: This certification focuses on quality management systems, ensuring that manufacturers have processes in place to consistently produce high-quality products.
- ISO 14001: This certification focuses on environmental management systems, demonstrating a commitment to reducing environmental impact.
- Food Contact Material Certifications: Certifications like those issued by the FDA (for US market) or similar agencies in other regions, may be required to demonstrate compliance with food contact material regulations. These certifications typically involve third-party testing and audits to verify that materials are safe for use with food.
- Compostability Certifications: Certifications like those from the BPI or similar organizations indicate that a food boat is compostable under specific conditions. These certifications require that the product meets strict standards for biodegradability and disintegration in a composting environment.
- Other Certifications: Depending on the materials used and the target market, manufacturers may obtain certifications related to specific materials, such as Forest Stewardship Council (FSC) certification for paper-based food boats, which ensures that the paper comes from sustainably managed forests.
Cost Analysis
Understanding the cost structure of disposable food boats is crucial for businesses aiming to minimize expenses while maintaining quality and environmental responsibility. A comprehensive cost analysis involves evaluating material costs, manufacturing processes, and external factors. This section provides a detailed examination of the cost dynamics associated with different disposable food boat materials and production methods.
Cost Comparison of Disposable Food Boat Materials
The cost of disposable food boats varies significantly depending on the material used. Each material presents a unique cost profile, influenced by factors such as raw material availability, manufacturing complexity, and transportation expenses. A comparative analysis of the most common materials is presented below.
Material | Typical Cost Range (per unit) | Factors Influencing Cost | Advantages/Disadvantages Related to Cost |
---|---|---|---|
Paperboard | $0.05 – $0.20 |
|
|
Polystyrene (PS) | $0.03 – $0.15 |
|
|
Polypropylene (PP) | $0.04 – $0.18 |
|
|
Polylactic Acid (PLA) | $0.10 – $0.30 |
|
|
Bagasse (Sugarcane Pulp) | $0.08 – $0.25 |
|
|
Factors Influencing the Cost of Production
Numerous factors influence the cost of producing disposable food boats, spanning raw material procurement to distribution. Understanding these elements enables businesses to optimize their production processes and reduce expenses.
- Raw Material Costs: The price of raw materials is a primary driver of production costs. Fluctuations in commodity prices, such as those for oil (for plastics) or pulp (for paper), directly impact material expenses. Supply chain disruptions can also inflate these costs.
- Manufacturing Processes: The chosen manufacturing method significantly affects costs. Thermoforming (for plastics) and molding (for paper-based products) involve varying levels of capital investment, energy consumption, and labor costs. More complex processes generally lead to higher per-unit costs.
- Labor Costs: Wages and salaries for production staff, as well as associated benefits, constitute a substantial portion of the production expenses. Automation and process optimization can help mitigate labor costs, especially in regions with high labor rates.
- Energy Consumption: Energy costs associated with operating machinery, heating, and cooling in manufacturing facilities can be substantial. Energy-efficient equipment and the use of renewable energy sources can reduce these expenses.
- Transportation and Logistics: The cost of transporting raw materials to the manufacturing facility and finished products to distributors or end-users contributes to the overall cost. Strategic location of manufacturing facilities near raw material sources and markets can reduce transportation expenses.
- Waste Management: The disposal of production waste, including trimmings and defective products, incurs costs. Implementing waste reduction strategies, such as recycling or using more efficient manufacturing processes, can minimize waste management expenses.
- Overhead Costs: General overhead expenses, including rent, utilities, insurance, and administrative costs, also contribute to the final product cost. Efficient management of these overheads is essential for cost control.
Ways to Reduce Overall Cost Without Compromising Quality
Businesses can employ various strategies to reduce the overall cost of disposable food boats without sacrificing product quality. These strategies encompass material selection, production optimization, and supply chain management.
- Material Optimization: Selecting the right material for the intended application is crucial. For example, using thinner, yet durable, paperboard can reduce material costs without compromising structural integrity. Similarly, employing a blend of materials (e.g., a paperboard boat with a thin PLA lining for moisture resistance) can balance cost and performance.
- Production Efficiency: Streamlining manufacturing processes can significantly reduce costs. Implementing automation, optimizing machine settings, and reducing waste through efficient cutting and molding techniques can lead to lower production expenses.
- Supply Chain Management: Negotiating favorable contracts with suppliers, bulk purchasing of raw materials, and optimizing transportation routes can reduce supply chain costs. Diversifying suppliers can also mitigate the risk of price fluctuations and supply disruptions.
- Waste Reduction: Implementing waste reduction strategies is essential. This includes recycling production scraps, minimizing material waste during cutting and molding, and using efficient packaging to reduce shipping costs.
- Design Optimization: Optimizing the design of the food boat can reduce material usage. This involves minimizing the amount of material required while maintaining structural integrity and functionality. A well-designed boat can also improve stacking efficiency, reducing storage and transportation costs.
- Energy Efficiency: Investing in energy-efficient equipment and adopting sustainable manufacturing practices can lower energy consumption and associated costs. Utilizing renewable energy sources, such as solar power, can further reduce energy expenses and promote environmental sustainability.
- Collaboration and Partnerships: Forming strategic partnerships with suppliers, distributors, and other stakeholders can lead to cost savings. Joint purchasing agreements, shared transportation resources, and collaborative product development can reduce expenses and improve efficiency.
Future Trends
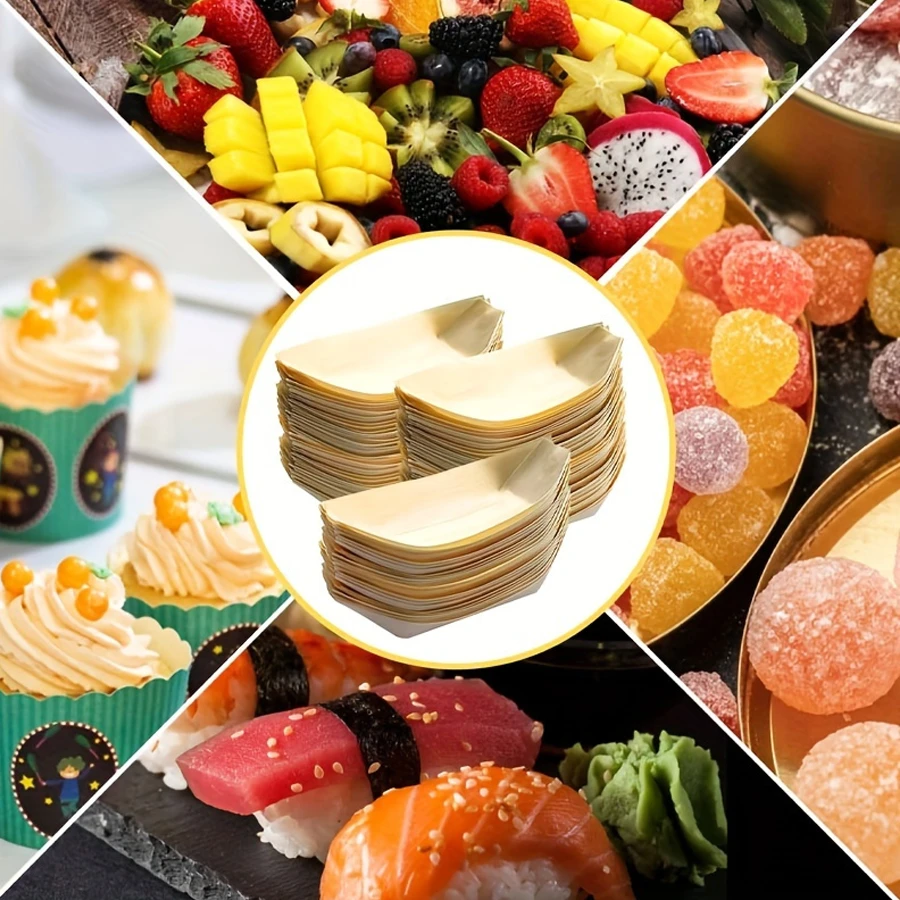
The disposable food boat industry is poised for significant transformation, driven by evolving consumer preferences, stricter environmental regulations, and advancements in material science and manufacturing processes. This section explores the anticipated innovations, materials, and overall vision for the future of disposable food boats.
Potential Innovations in Disposable Food Boat Design
Design innovations will focus on enhancing functionality, sustainability, and consumer experience. These advancements aim to address existing limitations while meeting the demands of a changing market.
- Improved Structural Integrity: Future designs will likely incorporate reinforced structures and novel geometries to enhance the food boats’ ability to withstand handling, transportation, and varying food temperatures. This could involve ribbing, corrugation, or the use of composite materials. For instance, the integration of a “double-wall” design, similar to insulated cups, could significantly improve heat retention and prevent the boat from becoming soggy.
- Enhanced Grease and Leak Resistance: Coatings and treatments are expected to evolve, offering superior barriers against grease, moisture, and potential leaks. These could include biodegradable and compostable alternatives to traditional fluorochemical coatings. Research into bio-based waxes and polymers is ongoing to provide effective and environmentally friendly solutions.
- Modular and Customizable Designs: Manufacturers may offer modular designs allowing for customization to suit specific food types and serving requirements. This flexibility would reduce waste by optimizing the size and shape of the food boat for the intended portion. A modular system might involve interchangeable lids, dividers, and compartments to accommodate various food items in a single container.
- Smart Packaging Integration: Future food boats could incorporate smart technologies, such as QR codes for product information, traceability, and promotional offers. Sensors could also be embedded to monitor food temperature, freshness, and potential spoilage, providing valuable data to both consumers and food service providers.
- Improved Aesthetics and Branding: Design will increasingly focus on visual appeal and brand communication. This may involve the use of vibrant colors, custom printing, and innovative shapes to enhance the consumer experience and create a positive brand image. Digital printing technologies will likely become more prevalent, enabling complex designs and personalization.
New Materials for Future Use
The shift towards sustainability will necessitate the adoption of innovative materials that minimize environmental impact while maintaining performance characteristics.
- Mushroom Packaging (Mycelium): Mycelium, the root structure of mushrooms, can be grown into custom shapes, providing a compostable and biodegradable alternative to traditional plastics. Its natural insulating properties make it suitable for hot food applications.
- Seaweed-Based Materials: Seaweed is a rapidly renewable resource that can be processed into films and sheets for food packaging. These materials are biodegradable, compostable, and offer good barrier properties. Research is ongoing to improve their durability and water resistance.
- Agricultural Waste-Based Materials: Agricultural byproducts such as wheat straw, rice husks, and sugarcane bagasse are being used to create molded pulp and other sustainable packaging materials. These materials are renewable, compostable, and can reduce reliance on virgin resources. The production of molded pulp from sugarcane bagasse, for example, can convert agricultural waste into valuable packaging.
- Polylactic Acid (PLA) and other Bioplastics: PLA, derived from renewable resources like corn starch, is a widely used bioplastic. While it’s compostable under specific conditions, research is ongoing to improve its performance and broaden its application in food packaging. New formulations of bioplastics are also being developed to enhance barrier properties and heat resistance.
- Cellulose-Based Materials: Cellulose, the primary component of plant cell walls, can be processed into various forms for packaging, including films, sheets, and molded pulp. These materials are renewable, biodegradable, and offer excellent printability.
Vision of the Future of Disposable Food Boats
The future of disposable food boats envisions a shift towards a circular economy, where materials are designed for recyclability, compostability, and minimal environmental impact.
- Closed-Loop Systems: Food boats will be designed for easy recycling or composting, and manufacturers will establish closed-loop systems to collect and process used boats. This would involve partnerships with waste management companies and consumers to ensure proper disposal and material recovery.
- Localized Manufacturing: Production may become more localized to reduce transportation emissions and support regional economies. 3D printing and other advanced manufacturing technologies could enable on-demand production and customization, reducing waste and improving efficiency.
- Enhanced Consumer Awareness: Consumers will be educated about the environmental benefits of sustainable packaging and encouraged to participate in recycling and composting programs. Clear labeling and communication will play a crucial role in informing consumers about proper disposal methods.
- Integration of Smart Technologies: Smart packaging features will become commonplace, providing consumers with valuable information about the food and its packaging. This could include tracking food freshness, providing nutritional information, and facilitating recycling.
- Focus on Reduced Waste: Designs will be optimized to minimize material usage and waste generation. This will involve using thinner materials, reducing packaging size, and developing modular designs that can be adapted to various food items. The goal is to move towards a “cradle-to-cradle” approach, where materials are continuously reused and repurposed.
Marketing and Distribution
The effective marketing and distribution of disposable food boats are crucial for their commercial success. This involves understanding the target market, optimizing distribution channels, and employing marketing strategies that highlight the product’s benefits. A well-defined marketing and distribution strategy ensures that the product reaches the end-users efficiently and effectively, maximizing sales and market penetration.
Distribution Channels
Various distribution channels are employed to deliver disposable food boats to end-users, each catering to specific market segments. These channels are selected based on factors such as product volume, target customer, and cost-effectiveness.
- Wholesale Distributors: These distributors purchase large quantities of disposable food boats from manufacturers and then resell them to retailers, restaurants, and catering companies. This channel is efficient for bulk purchases and large-scale distribution.
- Retailers: Retailers, including supermarkets, convenience stores, and online marketplaces, offer disposable food boats directly to consumers. This channel provides convenient access for individual purchases.
- Food Service Distributors: These distributors specialize in supplying food service establishments, such as restaurants, fast-food chains, and catering businesses, with a wide range of disposable food service items, including food boats. This channel is optimized for serving the needs of the food service industry.
- Direct Sales: Manufacturers may sell directly to large customers, bypassing intermediaries. This approach can reduce costs and improve communication but requires significant resources for sales and logistics.
- Online Marketplaces: Platforms like Amazon and Alibaba provide online channels for manufacturers and retailers to sell disposable food boats, reaching a global audience and offering price transparency.
Successful Marketing Strategies
Effective marketing strategies for disposable food boats focus on highlighting their key features and benefits to target audiences. The choice of marketing strategy depends on the specific product, target market, and budget.
- Product Positioning: Defining the product’s unique selling proposition (USP) is critical. This could be based on eco-friendliness, durability, affordability, or specific design features. For example, positioning a food boat as “eco-friendly” made from recycled materials can attract environmentally conscious consumers.
- Content Marketing: Creating informative content, such as blog posts, articles, and videos, that educates consumers about the benefits of disposable food boats. This builds brand awareness and establishes expertise. A video demonstrating the strength and leak-proof qualities of a food boat can influence purchasing decisions.
- Social Media Marketing: Utilizing social media platforms to reach target audiences, share product information, and run advertising campaigns. Platforms like Instagram and Pinterest are effective for showcasing product aesthetics and usage. Visual content highlighting the attractive presentation of food in the boats can be effective.
- Search Engine Optimization (): Optimizing product listings and websites to improve search engine rankings. This ensures that potential customers can easily find the products online. A well-optimized website increases visibility and attracts organic traffic.
- Partnerships and Promotions: Collaborating with food service businesses and other relevant entities to offer promotions and bundled deals. For example, partnering with a fast-food chain to offer a discount on food boats with a meal.
Packaging Methods for Shipping
The packaging of disposable food boats is designed to protect the products during shipping, minimize waste, and optimize storage efficiency. Packaging methods must also comply with shipping regulations and environmental standards.
- Bulk Packaging: Large quantities of food boats are often bundled together using plastic or paper strapping. This method is cost-effective for high-volume shipments. For example, a manufacturer might bundle 5000 food boats together in a corrugated cardboard box.
- Box Packaging: Food boats are placed in corrugated cardboard boxes of varying sizes. The boxes are sealed with tape and labeled with product information and shipping details. This protects the product from damage during transit.
- Shrink Wrapping: Individual stacks or bundles of food boats are wrapped in plastic film and then heat-sealed to create a secure package. This protects the product from moisture and contamination.
- Palletization: Boxes of food boats are stacked on pallets and secured with plastic wrap or strapping. This facilitates efficient handling and transportation by forklifts. Palletization allows for the efficient movement of large quantities of product.
- Sustainable Packaging: Increasingly, manufacturers are using sustainable packaging materials, such as recycled cardboard and biodegradable films, to minimize environmental impact. For example, using a corrugated cardboard box made from recycled materials.
Closing Summary
In conclusion, disposable food boats are more than just simple containers; they are a vital component of the food industry, constantly evolving to meet consumer needs and address environmental concerns. From the initial design to the final disposal, every aspect of their life cycle presents opportunities for innovation and improvement. As we look to the future, the focus will undoubtedly be on sustainability, with the development of new materials and designs that minimize environmental impact.
The journey of the disposable food boat is far from over; it’s a story of adaptation, innovation, and the ongoing quest for a more convenient and environmentally responsible future.