Food safe cardstock is an essential material in the food industry, playing a crucial role in packaging and presenting various food items. This specialized paper product is designed to come into direct contact with food, ensuring that it remains safe for consumption. This involves adhering to strict regulations and manufacturing processes to prevent contamination and maintain food integrity. Understanding the properties, applications, and regulations surrounding food safe cardstock is critical for both manufacturers and consumers.
The following discussion will explore the definition, applications, manufacturing processes, properties, types, printing considerations, sourcing, regulations, testing, and sustainability aspects of food safe cardstock. This comprehensive overview aims to provide a detailed understanding of the material, its significance in the food industry, and its impact on food safety and environmental sustainability.
Applications of Food Safe Cardstock
Food safe cardstock offers a versatile and essential solution for numerous applications within the food industry, providing a safe, aesthetically pleasing, and often cost-effective way to package, present, and serve food items. Its ability to come into direct contact with food, without compromising safety or flavor, makes it a preferred choice for various food businesses. This adaptability extends beyond mere packaging, encompassing a range of creative uses that enhance the consumer experience.
Packaging and Presentation
The primary application of food safe cardstock lies in the packaging and presentation of food items. From small-scale bakeries to large-scale food manufacturers, businesses utilize food safe cardstock for a variety of purposes. The material’s ability to be customized with printing, die-cutting, and various finishes adds to its appeal, allowing businesses to create branded packaging that enhances their product’s visual appeal.
- Food Boxes and Cartons: Food safe cardstock is widely used for creating boxes and cartons for items such as pizza, pastries, and takeout meals. These boxes protect the food during transport and maintain its temperature.
- Trays and Plates: Cardstock serves as a convenient and hygienic option for disposable plates and trays, particularly at events, food stalls, and in the fast-food sector.
- Cupcake and Muffin Wrappers: These wrappers are designed to protect the baked goods and prevent them from sticking to the packaging.
- Sandwich and Burger Wrappers: Cardstock is often used to wrap sandwiches and burgers, providing a protective barrier while allowing for easy handling and consumption.
- Takeout Containers: Restaurants and food vendors frequently utilize cardstock containers for takeout orders, providing a convenient and eco-friendly option.
Specialized Applications
Beyond basic packaging, food safe cardstock finds application in more specialized areas, often involving direct contact with food. These uses leverage the material’s safety and versatility to enhance the overall dining experience.
- Cupcake Toppers and Cake Decorations: Food safe cardstock is ideal for creating decorative elements that come into direct contact with cakes and cupcakes, adding visual appeal.
- Placemats and Table Linens: Restaurants can use food safe cardstock to create disposable placemats, offering a hygienic surface for diners and allowing for branding opportunities.
- Food Labels and Tags: Cardstock is used to create labels and tags for food products, providing information such as ingredients, nutritional facts, and branding.
- Menu Inserts and Flyers: Food safe cardstock can be used for menu inserts or promotional flyers that come into contact with food, particularly in cafes and restaurants.
Cardstock Thickness and Application Suitability
The thickness of the food safe cardstock significantly impacts its suitability for different applications. Thicker cardstock provides greater durability and structural integrity, making it suitable for heavier items or packaging that requires more robust protection. Thinner cardstock, on the other hand, is often preferred for items where flexibility and ease of use are paramount. The following table illustrates the relationship between cardstock thickness and its appropriate applications:
Cardstock Thickness (Points) | Common Weight (gsm) | Typical Applications | Examples |
---|---|---|---|
10-14 | 120-170 | Sandwich Wrappers, Flyers, Menu Inserts | A thin, flexible cardstock suitable for wrapping sandwiches or creating inserts for menus in restaurants. |
16-18 | 200-250 | Cupcake Wrappers, Food Labels, Cake Toppers | This weight provides enough stiffness for decorative elements and labels while remaining easy to handle. |
20-24 | 280-350 | Food Boxes (e.g., for pastries), Placemats | Provides the necessary strength and durability for small food boxes and disposable placemats. |
28+ | 350+ | Food Cartons, Trays | This thicker cardstock is used for creating sturdy food cartons and trays designed to hold heavier items. For example, a pizza box or a tray for carrying multiple food items. |
Manufacturing Processes for Food Safe Cardstock
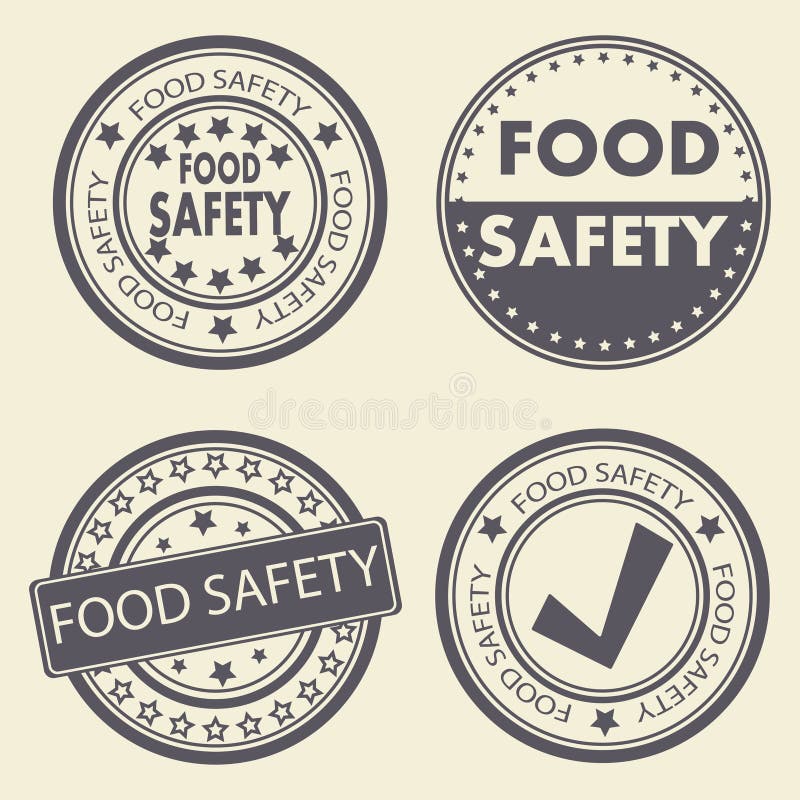
Crafting food-safe cardstock is a meticulous process, demanding precision at every stage. From sourcing raw materials to final inspection, each step contributes to the integrity of the finished product, ensuring it meets stringent safety regulations and protects consumers. This intricate process differentiates food-safe cardstock from its conventional counterparts.
Raw Material Selection and Preparation
The foundation of food-safe cardstock lies in the careful selection of raw materials. The pulp, typically derived from wood fibers, must be sourced from sustainable forests and undergo rigorous testing to ensure the absence of harmful contaminants. This selection process guarantees that the base material meets the highest standards for food contact applications.
- Pulp Sourcing: Only virgin pulp, often bleached to achieve the desired whiteness, is used. Recycled paper is generally avoided due to potential contamination risks.
- Pulp Treatment: The pulp is thoroughly cleaned and screened to remove any impurities, such as dirt, ink, and other debris. This step is crucial for preventing the transfer of unwanted substances to food.
- Chemical Additives: Food-grade additives are incorporated to enhance the paper’s properties. These can include sizing agents to control liquid absorption, and strengthening agents to improve durability. All additives must be approved for food contact.
Paper Formation and Drying
The prepared pulp is then transformed into paper through a sophisticated manufacturing process. This involves the controlled dispersion of pulp fibers, followed by drying and calendaring to achieve the desired thickness, smoothness, and density.
- Sheet Formation: The pulp slurry is spread evenly onto a moving wire mesh, allowing water to drain away, leaving behind a mat of intertwined fibers.
- Pressing: The wet paper sheet is passed through rollers to squeeze out excess water and compact the fibers, increasing density.
- Drying: The paper is dried using heated rollers or air dryers to remove moisture, stabilizing the sheet.
- Calendering: The dried paper is passed through calendaring rollers to smooth the surface and achieve the desired finish. This step is critical for printability and overall appearance.
Printing Methods for Food Safe Cardstock
Selecting the right printing method is vital for food safety. Each method has its strengths and weaknesses in terms of ink compatibility, potential for contamination, and overall suitability for food contact applications.
- Offset Printing: A widely used method, offset printing uses ink transferred from a plate to a rubber blanket, and then to the paper. For food-safe applications, only food-grade inks and varnishes are employed. The printing process must be carefully monitored to prevent ink migration.
- Digital Printing: Digital printing, including inkjet and laser printing, offers flexibility and speed, making it suitable for short runs and customized packaging. However, ensuring the inks are food-safe and resistant to migration is essential. Special low-migration inks are often used.
- Flexographic Printing: Flexography is a high-speed printing method using flexible relief plates. It is well-suited for printing on various materials, including cardstock. Food-safe flexographic inks and coatings are readily available.
- Considerations: The choice of printing method depends on factors like print volume, design complexity, and budget. The printing process must adhere to strict guidelines to prevent the transfer of inks or other substances to the food.
Post-Printing Treatments and Finishing
After printing, cardstock undergoes post-printing treatments to enhance its protective properties and ensure food safety. These treatments create a barrier between the printed surface and the food, minimizing the risk of contamination.
- Coating: Applying a food-grade coating, such as a varnish or lacquer, provides a barrier against moisture, grease, and ink migration. The coating also improves the cardstock’s appearance and durability.
- Lamination: Lamination involves bonding a transparent film to the cardstock surface. This provides an excellent barrier against contaminants and enhances the cardstock’s strength.
- Drying and Curing: The printed and coated cardstock must be thoroughly dried and cured to ensure that the inks and coatings are fully set and that no volatile organic compounds (VOCs) remain.
Food Safety Standards Compliance and Testing
Meeting food safety standards is paramount. Cardstock manufacturers must adhere to strict regulations and conduct thorough testing to verify the safety of their products.
- Regulatory Compliance: Food-safe cardstock must comply with regulations like those established by the FDA (in the US) or similar bodies in other regions. These regulations specify permissible materials and testing protocols.
- Migration Testing: Migration testing is a crucial step to determine if any ink components or other substances migrate from the cardstock into food. This testing simulates real-world conditions and ensures that the cardstock is safe for its intended use.
- Quality Control: Manufacturers implement rigorous quality control procedures throughout the manufacturing process. This includes regular inspections, testing of raw materials, and final product evaluations to ensure consistent quality and compliance.
Properties and Characteristics
Food safe cardstock is engineered to meet stringent requirements, ensuring that it not only protects food products but also maintains their integrity and appearance. Understanding its core properties is essential for making informed decisions in packaging and food service applications. These characteristics are critical for maintaining both food safety and presentation.
Resistance to Contaminants, Food safe cardstock
Food safe cardstock is designed to act as a barrier, protecting food from a variety of external threats. This includes the ability to resist grease, moisture, and other potential contaminants.The cardstock’s resistance to grease is achieved through specialized coatings or treatments applied during the manufacturing process. These coatings, often based on fluorochemicals or other polymers, create a hydrophobic surface that prevents oil and grease from penetrating the paper fibers.
This is especially important for packaging items like fried foods, pastries, and other products with high-fat content. A coating effectively prevents the grease from migrating through the cardstock, which would lead to unsightly stains and potential weakening of the packaging.Moisture resistance is another critical property. The cardstock is designed to withstand a certain level of humidity and prevent moisture from compromising the structural integrity of the packaging.
This is achieved through the use of moisture-resistant coatings or treatments, such as wax or polyethylene. These coatings create a barrier that prevents water from being absorbed into the paper fibers, which could lead to the cardstock becoming soggy and losing its shape. This is especially important for packaging items like sandwiches, salads, and other products with high-moisture content.Furthermore, food safe cardstock must resist the penetration of other potential contaminants, such as inks, adhesives, and microorganisms.
The materials used in the cardstock, including the inks and adhesives, must be food-grade and free of harmful chemicals that could migrate into the food. This is typically achieved through the use of specialized inks and adhesives that are specifically designed for food packaging applications. The cardstock must also be manufactured in a clean environment to minimize the risk of contamination from microorganisms.
Impact of Manufacturing on Color and Print Quality
The manufacturing process significantly influences the color and print quality of food safe cardstock. The choice of pulp, coatings, and printing methods all play a crucial role in determining the final appearance of the packaging.The type of pulp used in the cardstock’s production affects its color. Bleached pulps, for example, result in a brighter, whiter cardstock, which is often preferred for high-end packaging.
Unbleached pulps, on the other hand, produce a more natural, off-white or brown color. The choice of pulp also impacts the cardstock’s opacity, which affects how well the printed design will show through.The coatings applied to the cardstock also impact color and print quality. Coatings can enhance the brightness, smoothness, and printability of the cardstock. For instance, a glossy coating will make the colors appear more vibrant and the print sharper.
A matte coating, on the other hand, will provide a more subdued appearance.Printing methods also affect the final outcome. Offset printing is a widely used method that provides high-quality results, especially for complex designs and photographic images. Flexographic printing is another common method, which is particularly well-suited for printing on cardstock. The choice of ink also plays a crucial role.
Explore the different advantages of mickey mouse party food labels that can change the way you view this issue.
Food-grade inks must be used to ensure that they do not contaminate the food. These inks are specifically designed to meet stringent safety regulations and provide excellent print quality.
Benefits of Food Safe Cardstock
Food safe cardstock offers numerous advantages over non-food-safe alternatives. The following benefits highlight the critical role it plays in ensuring food safety and enhancing the consumer experience:
- Enhanced Food Safety: Food safe cardstock minimizes the risk of food contamination by acting as a barrier against grease, moisture, and other potential hazards. This helps to prevent foodborne illnesses and maintain the integrity of the food products.
- Improved Product Presentation: The cardstock’s ability to maintain its structural integrity and resist stains contributes to a more appealing product presentation. This is crucial for attracting customers and enhancing brand perception.
- Compliance with Regulations: Food safe cardstock is manufactured to meet stringent food safety regulations, ensuring that the packaging complies with industry standards and legal requirements. This is essential for businesses operating in the food industry.
- Extended Shelf Life: By protecting food from external contaminants, food safe cardstock can help to extend the shelf life of products. This is especially important for perishable items.
- Versatility: Food safe cardstock is available in a wide range of sizes, shapes, and finishes, making it suitable for a variety of packaging applications. It can be customized with various printing options to meet specific branding requirements.
- Sustainability: Many food safe cardstock options are available, including those made from recycled materials or sourced from sustainably managed forests. This allows businesses to reduce their environmental impact.
Types of Food Safe Cardstock
Food safe cardstock offers a versatile range of options, each tailored to meet specific packaging needs. Understanding the nuances between coated, uncoated, and specialty cardstocks is crucial for selecting the right material to ensure both product safety and optimal presentation. This section explores the various types, comparing their characteristics and highlighting their suitability for diverse food applications.
Coated Food Safe Cardstock
Coated cardstock features a layer of coating applied to the base paper. This coating significantly alters the paper’s properties, impacting its suitability for food packaging. It is designed to improve printability, provide a barrier against moisture and grease, and enhance the overall appearance of the packaging.The key characteristics of coated food safe cardstock include:
- Enhanced Printability: The smooth surface of coated cardstock provides superior ink adhesion, resulting in sharper images, brighter colors, and finer details in printing. This makes it ideal for packaging that requires high-quality graphics and branding.
- Moisture Resistance: The coating acts as a barrier, reducing the absorption of moisture from the environment or from the food itself. This is crucial for extending the shelf life of food products and maintaining the integrity of the packaging.
- Grease Resistance: Coated cardstock often includes a grease-resistant component, preventing oils and fats from penetrating the paper. This is particularly important for packaging items like pastries, fried foods, and snacks.
- Improved Aesthetics: The coating can give the cardstock a glossy, matte, or satin finish, enhancing the visual appeal of the packaging and making it more attractive to consumers.
Coated cardstock is commonly used for:
- Food Boxes: Boxes for pizza, french fries, and other takeaway foods often utilize coated cardstock for its grease resistance and printability.
- Cereal Boxes: The interior of cereal boxes frequently employs a coated cardstock to provide a moisture barrier and protect the cereal from spoilage.
- Frozen Food Packaging: Coated cardstock can withstand the cold temperatures and prevent freezer burn, making it suitable for frozen food packaging.
Uncoated Food Safe Cardstock
Uncoated food safe cardstock is the base paper without any additional coatings. It maintains the natural texture and absorbency of the paper, which offers specific advantages for certain food packaging applications.Key characteristics of uncoated food safe cardstock:
- Natural Texture: The rougher surface of uncoated cardstock provides a tactile experience, giving packaging a more organic and authentic feel.
- High Absorbency: Uncoated cardstock readily absorbs liquids and moisture, which can be advantageous in certain situations, such as absorbing excess oil from food.
- Biodegradability: Uncoated cardstock is often considered more environmentally friendly due to its simpler manufacturing process and greater biodegradability.
- Printability: While not as sharp as coated cardstock, uncoated cardstock still offers acceptable print quality, especially for simpler designs and text.
Uncoated cardstock is used for:
- Baking Cups: Baking cups are often made from uncoated cardstock to absorb grease and provide a non-stick surface for baked goods.
- Wrapping Paper: Uncoated cardstock is sometimes used as wrapping paper for sandwiches and other food items.
- Food Tray Liners: Liners for food trays can be uncoated to absorb excess moisture or oil.
Specialty Food Safe Cardstock
Specialty food safe cardstock encompasses a wide range of materials designed to meet specific packaging needs. These cardstocks may incorporate unique features like enhanced barrier properties, specific textures, or sustainable attributes.Different types of specialty food safe cardstock include:
- Barrier Cardstock: This type incorporates a special coating or lamination to provide enhanced protection against moisture, grease, and oxygen. It is commonly used for packaging items that require extended shelf life or protection from external elements.
- Recycled Cardstock: This type is made from recycled paper, offering an environmentally friendly option. It’s crucial to ensure the recycled material is food-grade and meets all safety standards.
- Kraft Cardstock: Known for its natural brown color and strength, kraft cardstock is a popular choice for packaging due to its rustic aesthetic and durability. It is often used for bags, boxes, and wraps.
- Metallic Cardstock: This adds a metallic finish to the packaging, providing a premium and eye-catching appearance.
Examples of specialty cardstock applications:
- Barrier Cardstock for Coffee Packaging: Barrier cardstock is used in coffee packaging to protect the coffee beans from oxygen and moisture, preserving freshness and aroma.
- Recycled Cardstock for Eco-Friendly Food Containers: Recycled cardstock is utilized in food containers to reduce environmental impact and appeal to environmentally conscious consumers.
- Kraft Cardstock for Sandwich Wraps: Kraft cardstock is a common choice for wrapping sandwiches, providing a sturdy and aesthetically pleasing packaging solution.
Printing on Food Safe Cardstock
Printing on food safe cardstock requires careful consideration to maintain the cardstock’s food-safe properties. The inks and printing processes used must be specifically designed for this purpose to prevent the migration of harmful substances into food. This section details the compatible printing methods, safety guidelines, and best practices to ensure printed food safe cardstock remains safe for its intended use.
Compatible Inks and Printing Processes
Selecting the correct ink and printing process is paramount for maintaining food safety. Inks must be formulated to meet stringent regulations, and the printing method should ensure proper ink adhesion and curing.
- Ink Types:
Several ink types are suitable for printing on food safe cardstock. These inks are formulated with specific components to minimize the risk of contamination.
- UV-Curable Inks: These inks cure instantly when exposed to ultraviolet light, offering excellent adhesion and resistance to migration. They are popular due to their quick drying times and ability to print on various substrates. They typically contain low-migration components, minimizing the potential for ink transfer.
- Water-Based Inks: These inks are a preferred choice for food packaging due to their low toxicity and environmental friendliness. They use water as a solvent and often incorporate pigments that are safe for food contact. They require careful drying processes to ensure complete curing.
- Soy-Based Inks: Derived from soybeans, these inks are a sustainable and environmentally friendly alternative. They are often used in offset printing and are considered a safer option compared to petroleum-based inks. They offer good color quality and are relatively low in volatile organic compounds (VOCs).
- Printing Processes:
The printing process significantly impacts the final product’s safety. Each method has advantages and disadvantages regarding ink application, drying, and overall food safety.
- Offset Printing: A widely used method, offset printing can utilize soy-based inks effectively. It offers high-quality printing but requires careful monitoring of ink migration and drying processes.
- Flexography: This process is well-suited for printing on various substrates, including cardstock. It often uses water-based inks and is capable of high-volume production. The key is to ensure proper ink curing and adherence to food safety guidelines.
- Digital Printing: Digital printing, particularly inkjet, offers flexibility for short runs and variable data printing. UV-curable inks are frequently employed in digital printing for food safe cardstock, providing quick drying and excellent adhesion.
Ensuring Print Safety: A Comprehensive Guide
Ensuring print safety involves meticulous attention to detail, from ink selection to the final drying process. Following these guidelines will minimize the risk of ink migration and ensure the printed cardstock is suitable for food contact.
- Ink Selection: Always choose inks specifically formulated for food contact applications. Look for certifications such as those from organizations that set food safety standards. These certifications ensure that the ink components are safe for use with food.
- Drying Times: Adequate drying times are crucial for preventing ink migration. The specific drying time depends on the ink type and printing process. For UV-curable inks, complete curing under UV light is necessary. Water-based inks require sufficient time for the water to evaporate completely, often aided by heat or air drying. The goal is to ensure the ink is fully set and bonded to the cardstock.
- Testing and Compliance: Before mass production, conduct thorough testing to ensure the printed cardstock meets all relevant food safety regulations. This may involve migration testing, which assesses whether ink components migrate into food. Compliance with regulations like those set by the FDA (in the US) and similar bodies in other regions is essential.
- Substrate Compatibility: Ensure the ink is compatible with the food safe cardstock. Different cardstock types may have different surface properties, affecting ink adhesion and drying. Always consult the ink and cardstock manufacturers for compatibility recommendations.
- Storage and Handling: Properly store and handle printed cardstock to prevent contamination. Keep the printed materials away from potential sources of contamination, such as solvents or other chemicals. Store them in a clean, dry environment to preserve the integrity of the print and the cardstock.
Best Practices for Printing on Food Safe Cardstock:
- Ink Selection: Use inks specifically formulated for food contact.
- Drying: Ensure thorough drying and curing according to ink specifications.
- Testing: Conduct migration testing to verify food safety.
- Compliance: Adhere to all relevant food safety regulations and certifications.
- Handling: Store and handle printed materials to prevent contamination.
Sourcing and Purchasing
The journey of acquiring food safe cardstock, from identifying reputable suppliers to making the final purchase, is crucial for ensuring product safety and compliance. Navigating this process requires a strategic approach, encompassing thorough research, careful comparison, and a clear understanding of your specific needs. This section provides a comprehensive guide to help you source and purchase the right food safe cardstock for your applications.
Sourcing Food Safe Cardstock from Reliable Suppliers
Finding trustworthy suppliers is the cornerstone of a successful food packaging operation. It’s not just about finding the cheapest option; it’s about establishing a partnership with a company that prioritizes quality, safety, and compliance.
- Industry-Specific Directories and Associations: Leverage industry directories and associations, such as those related to packaging or food safety, to identify potential suppliers. These resources often vet members and provide a level of assurance regarding their credibility.
- Online Marketplaces and Platforms: Explore online marketplaces specializing in packaging materials. However, exercise caution and verify supplier credentials thoroughly before making a purchase. Look for established sellers with positive reviews and transparent information about their products and certifications.
- Trade Shows and Exhibitions: Attend relevant trade shows and exhibitions. These events offer a direct opportunity to meet potential suppliers, examine their products firsthand, and discuss your specific requirements. This face-to-face interaction can be invaluable in building trust and assessing their capabilities.
- Supplier Websites and Catalogs: Carefully review supplier websites and catalogs. Look for detailed product specifications, certifications, and information about their manufacturing processes. A reputable supplier will be transparent about their commitment to quality and safety.
- Requesting Samples and Technical Data Sheets: Always request samples of the cardstock and technical data sheets. This allows you to evaluate the material’s suitability for your intended use and verify its compliance with relevant regulations. The technical data sheets provide crucial information about the material’s composition, properties, and performance characteristics.
- Verifying Certifications and Compliance: Ensure that the supplier can provide documentation of relevant certifications, such as those from the FDA or other food safety agencies. This documentation demonstrates their commitment to meeting industry standards.
Comparing and Contrasting Pricing from Different Suppliers
Pricing for food safe cardstock can vary significantly depending on the type of cardstock, the supplier, the order quantity, and any special requirements. A thorough comparison is essential to ensure you get the best value for your investment.
To effectively compare prices, create a spreadsheet that includes the following columns:
Supplier | Type of Cardstock | Thickness (gsm or point) | Order Quantity | Price per Unit | Shipping Costs | Total Cost | Certifications | Lead Time |
---|---|---|---|---|---|---|---|---|
Supplier A | Bleached Kraft | 250 gsm | 10,000 sheets | $0.15 per sheet | $50 | $1550 | FDA, FSC | 2 weeks |
Supplier B | SBS Board | 230 gsm | 10,000 sheets | $0.18 per sheet | $75 | $1875 | FDA | 3 weeks |
Supplier C | Recycled Cardstock | 240 gsm | 10,000 sheets | $0.17 per sheet | $60 | $1760 | FDA, Recycled Content Certified | 4 weeks |
Example Scenario: Based on the table above, Supplier A offers the lowest total cost. However, consider the lead time. If you need the cardstock quickly, Supplier A might be the best choice, despite the slightly higher per-sheet price. If sustainability is a priority, Supplier C might be preferable, even with a longer lead time.
- Obtaining Quotes: Request detailed quotes from multiple suppliers, specifying the exact type of cardstock, thickness, size, and quantity you require. Ensure the quotes include all costs, such as shipping, handling, and any applicable taxes.
- Comparing Like-for-Like: Compare quotes for identical or very similar specifications. Variations in thickness, coating, or other features can significantly impact the price.
- Considering Order Quantities: Inquire about price breaks for larger order quantities. Purchasing in bulk can often result in significant cost savings.
- Evaluating Shipping Costs: Shipping costs can vary greatly depending on the supplier’s location, the shipping method, and the order weight. Factor these costs into your overall comparison.
- Negotiating Prices: Don’t hesitate to negotiate prices, especially for larger orders. Suppliers are often willing to offer discounts to secure your business.
- Assessing Payment Terms: Review the supplier’s payment terms, such as net 30 or upfront payment requirements. Consider these terms when evaluating the overall cost.
Factors to Consider When Purchasing Food Safe Cardstock
Making informed purchasing decisions requires a comprehensive understanding of the factors that influence the suitability of the cardstock for its intended use.
- Certifications: Prioritize suppliers that provide certifications from reputable food safety organizations, such as the FDA. These certifications demonstrate that the cardstock meets the required standards for food contact.
- Material Composition: Carefully review the material composition of the cardstock. Ensure that all materials used are food-grade and safe for their intended purpose. Avoid cardstock containing harmful chemicals or additives.
- Intended Use: Consider the specific application for the cardstock. For example, cardstock used for direct food contact, such as food trays, requires different properties than cardstock used for outer packaging.
- Barrier Properties: If the cardstock will be used to package foods that need protection from moisture, grease, or oxygen, consider cardstock with appropriate barrier properties.
- Printability: If you plan to print on the cardstock, assess its printability characteristics. Consider factors such as ink absorption, color reproduction, and suitability for different printing methods.
- Thickness and Weight: Choose the appropriate thickness and weight of the cardstock based on the product’s weight and the desired level of protection. Heavier cardstock offers greater durability.
- Sustainability: Consider the environmental impact of the cardstock. Look for options that are made from recycled materials, are sustainably sourced, or are compostable.
- Cost: Balance the cost of the cardstock with its performance characteristics and compliance requirements. Consider the total cost, including shipping and handling.
- Lead Time and Availability: Factor in the lead time for the supplier to fulfill your order. Ensure that the cardstock will be available when you need it.
- Supplier Reputation: Choose a supplier with a good reputation for quality, reliability, and customer service. Read reviews and check references to assess their performance.
Testing and Quality Control
Ensuring the food safety of cardstock requires rigorous testing and meticulous quality control throughout the manufacturing process. This involves employing a variety of testing methods to verify the absence of harmful substances and implementing stringent quality control measures to maintain consistency and safety. The following sections delve into the specifics of these crucial processes.
Testing Methods for Food Safety Verification
The verification of food safety in cardstock hinges on employing a range of testing methods designed to detect potential contaminants and ensure compliance with regulatory standards. These tests are crucial for guaranteeing that the cardstock is safe for its intended use, such as food packaging.The methods used to verify food safety include:
- Migration Testing: This assesses the potential for substances from the cardstock to migrate into the food. It involves simulating the conditions the cardstock will encounter during food contact, such as temperature and contact time. This is often performed using food simulants that mimic the characteristics of various food types (e.g., water, acetic acid, olive oil). The food simulant is in contact with the cardstock under controlled conditions, and then analyzed to identify any migrated substances.
For example, a manufacturer might test cardstock intended for pizza boxes with olive oil at 100°C for 2 hours to assess the migration of any potential contaminants.
- Heavy Metal Testing: This analysis checks for the presence of heavy metals, such as lead, cadmium, and mercury, which can be harmful if they leach into food. Techniques like Inductively Coupled Plasma Mass Spectrometry (ICP-MS) are frequently employed for highly sensitive detection. The cardstock is typically digested in a solution, and the resulting liquid is analyzed.
- Specific Substance Testing: This involves testing for specific substances of concern, such as phthalates, bisphenol A (BPA), or certain inks and coatings. The testing method depends on the substance. For instance, gas chromatography-mass spectrometry (GC-MS) may be used to detect the presence of phthalates, while high-performance liquid chromatography (HPLC) can be used for BPA.
- Microbiological Testing: This verifies that the cardstock is free from harmful microorganisms, such as bacteria and fungi. This is important, especially for cardstock that will come into direct contact with food. Tests include swabbing the surface of the cardstock and culturing the samples in a laboratory to check for the presence of microorganisms.
- Odor and Taste Testing: Sensory evaluations are often performed to ensure that the cardstock does not impart any undesirable odors or tastes to the food. Trained panelists assess the cardstock’s impact on the sensory characteristics of the food.
Quality Control Measures in Manufacturing
Manufacturers of food-safe cardstock employ a comprehensive quality control system to ensure the consistency and safety of their products. These measures encompass every stage of the manufacturing process, from raw material sourcing to finished product inspection.Key quality control measures include:
- Raw Material Inspection: All raw materials, including paper pulp, coatings, and inks, are thoroughly inspected upon arrival. This involves checking for compliance with specifications, verifying the absence of prohibited substances, and ensuring the materials meet the required purity standards. For example, a supplier might provide a Certificate of Analysis (CoA) for the paper pulp, detailing its composition and confirming it meets the necessary food safety requirements.
- Process Control: Strict control over the manufacturing processes is essential. This includes monitoring parameters like temperature, pressure, and coating thickness. Regular checks are performed to ensure that these parameters are within the specified ranges.
- Regular Audits and Inspections: Internal and external audits are conducted to verify compliance with quality standards and regulations. Inspections are performed at various stages of production to identify and correct any deviations from the established procedures.
- Traceability Systems: Implementing a robust traceability system is critical. This allows manufacturers to track the origin of raw materials and the processing history of each batch of cardstock. This is important in case of any product recalls or quality issues.
- Documentation and Record Keeping: Comprehensive documentation of all quality control activities, including testing results, inspection reports, and corrective actions, is maintained. This documentation provides a complete record of the manufacturing process and ensures accountability.
Examples of Quality Control Tests and Their Significance
Quality control tests play a vital role in ensuring that food-safe cardstock meets the required safety standards. These tests provide tangible evidence of the cardstock’s compliance and its suitability for food contact applications.Here are some examples of quality control tests and their significance:
- Basis Weight Measurement: This test determines the weight of the cardstock per unit area (e.g., grams per square meter or GSM). It ensures the cardstock meets the required thickness and strength specifications. The basis weight directly impacts the cardstock’s durability and its ability to protect the food product.
- Tensile Strength Testing: This measures the cardstock’s resistance to tearing and breaking under tension. It is important for cardstock used in packaging applications to withstand the stresses of handling, filling, and transportation.
- Moisture Content Determination: This assesses the amount of moisture present in the cardstock. Excessive moisture can affect the cardstock’s performance and potentially lead to the growth of microorganisms.
- Surface Smoothness Testing: This measures the smoothness of the cardstock’s surface. A smooth surface is important for printability and can affect the visual appeal of the packaging.
- Color Consistency Testing: This ensures that the color of the cardstock is consistent across different batches. Color variations can affect the appearance of the packaging and the brand image.
- Printing Quality Inspection: This verifies the quality of any printing applied to the cardstock, including the accuracy of the images, text, and color registration. This is critical for branding and consumer information.
Sustainability and Food Safe Cardstock
The rising consumer awareness of environmental impact is reshaping the food packaging industry. Sustainability is no longer a trend, but a crucial expectation. Food safe cardstock, at the intersection of food safety and environmental responsibility, is adapting to meet this demand. Examining the sustainability of food safe cardstock involves understanding its lifecycle, from sourcing raw materials to end-of-life management, and identifying opportunities for improvement.
Environmental Considerations for Food Safe Cardstock
The environmental impact of food safe cardstock stems primarily from its sourcing and recyclability. Conventional cardstock production often relies on virgin wood pulp, which can contribute to deforestation and habitat loss if not managed sustainably. Additionally, the manufacturing process may involve energy-intensive operations and the use of chemicals. The recyclability of the cardstock is also a critical factor, influencing its environmental footprint.
Effective recycling programs are essential to divert cardstock from landfills and reduce the need for virgin materials.
Sustainable and Eco-Friendly Options
The market offers several sustainable and eco-friendly options for food safe cardstock. These alternatives are designed to minimize environmental impact while maintaining the necessary functionality and safety standards. The selection of sustainable cardstock often depends on the specific application and required performance characteristics.
Sustainable Practices in Production and Use
The following bulleted list highlights sustainable practices related to the production and use of food safe cardstock. These practices collectively contribute to a reduced environmental footprint and support a more circular economy.
- Sourcing Certified Wood Pulp: Utilizing cardstock produced from sustainably managed forests, certified by organizations like the Forest Stewardship Council (FSC), ensures responsible forestry practices. FSC certification guarantees that the wood pulp originates from forests managed in an environmentally appropriate, socially beneficial, and economically viable manner. This minimizes deforestation and promotes biodiversity.
- Using Recycled Cardstock: Employing cardstock made from recycled fibers reduces the demand for virgin wood pulp and conserves natural resources. Recycled cardstock often requires less energy and water to produce compared to virgin cardstock, contributing to lower greenhouse gas emissions.
- Implementing Renewable Energy: Manufacturing facilities can reduce their carbon footprint by utilizing renewable energy sources, such as solar, wind, or hydroelectric power. This reduces reliance on fossil fuels and lowers emissions associated with cardstock production.
- Minimizing Chemical Use: Employing eco-friendly chemicals and processes in the manufacturing of cardstock reduces environmental pollution. This includes using chlorine-free bleaching methods and reducing the use of harmful dyes and coatings.
- Optimizing Manufacturing Processes: Improving manufacturing efficiency, such as reducing waste and conserving water, helps minimize the environmental impact. Implementing lean manufacturing principles can streamline processes and reduce resource consumption.
- Designing for Recyclability: Designing food safe cardstock products that are easily recyclable is crucial. This involves avoiding coatings or additives that contaminate the recycling stream. Using simple, easily separable designs also enhances recyclability.
- Promoting Compostable Options: Exploring and utilizing compostable food safe cardstock options, particularly for applications where food contamination is likely, provides a biodegradable alternative to traditional cardstock. Compostable cardstock breaks down naturally, returning nutrients to the soil.
- Supporting Local Sourcing: Sourcing cardstock from local suppliers reduces transportation emissions and supports regional economies. Shorter supply chains contribute to a smaller carbon footprint.
- Educating Consumers: Informing consumers about the sustainability of food safe cardstock and providing clear recycling instructions encourages responsible disposal. Consumer awareness plays a critical role in achieving circularity.
- Implementing Closed-Loop Systems: Implementing closed-loop systems, where waste materials are recycled back into the production process, maximizes resource efficiency and minimizes waste. This approach supports a circular economy model.
End of Discussion
In conclusion, food safe cardstock represents a critical component of the food industry, offering a safe and reliable solution for packaging and presenting food products. From stringent manufacturing processes and regulatory compliance to sustainable practices, food safe cardstock ensures consumer safety and environmental responsibility. The selection and use of appropriate food safe cardstock is crucial for maintaining food quality, preventing contamination, and supporting sustainable practices within the food supply chain.