northland foods kalkaska michigan beckons, a siren song of sustenance and story. Imagine a place where the hum of industry intertwines with the quiet grace of the Michigan landscape, where generations have poured their hearts and expertise into crafting culinary delights. This is the realm we’ll explore, a tapestry woven with threads of history, product, and the very essence of community.
We’ll wander through the sprawling Kalkaska facility, a haven of production, and discover the secrets held within its walls.
From its humble beginnings, Northland Foods has blossomed, its roots firmly planted in the fertile soil of innovation. The company’s journey, marked by unwavering dedication and an unyielding commitment to quality, reflects the evolution of the food industry itself. We’ll trace the lineage of key personnel, each a brushstroke in the company’s portrait, and delve into the meticulous processes that transform raw ingredients into delectable offerings, packaged with artistry.
This story is about the products that grace tables, the people who bring them to life, and the dedication that fuels their passion.
Northland Foods Overview
Northland Foods, a significant player in the food manufacturing and distribution sector, has a rich history rooted in Kalkaska, Michigan. This overview will delve into the company’s origins, its key products, and the leadership that guides its operations.
History of Northland Foods
Northland Foods’ journey began in Kalkaska, Michigan. Over the years, the company has grown from its initial operations to become a prominent provider of food products. This expansion has been fueled by a commitment to quality and a focus on meeting the evolving needs of its customers.
Primary Products Manufactured or Distributed by Northland Foods
Northland Foods specializes in the manufacturing and distribution of a variety of food products. These products are designed to cater to different consumer preferences and market demands. The company’s product portfolio is diverse and reflects its ability to adapt to market trends.
- Frozen Foods: A significant portion of Northland Foods’ business involves frozen food products. This includes items like frozen fruits, vegetables, and prepared meals. Variations in these products may involve different packaging sizes, ingredient combinations, and processing methods. For example, a line of frozen vegetables might offer various cuts (diced, sliced, whole) and organic options.
- Canned Goods: Northland Foods also distributes canned goods. These include canned fruits, vegetables, and other preserved food items. Product specifications can vary based on the type of food, canning process, and added ingredients. For instance, canned peaches might be available in light syrup, heavy syrup, or natural juice.
- Prepared Foods: The company manufactures and distributes prepared foods, which could include ready-to-eat meals, side dishes, and other convenience items. These products are designed for ease of use and often cater to busy lifestyles. The variations could involve different cuisines, portion sizes, and dietary considerations (e.g., low-sodium, gluten-free).
Key Personnel and Leadership at Northland Foods
The leadership team at Northland Foods is responsible for overseeing all aspects of the company’s operations, from production to distribution. Their expertise and strategic direction are critical to the company’s success.
- Chief Executive Officer (CEO): The CEO is responsible for the overall strategic direction and management of the company. They set the vision, make key decisions, and ensure the company achieves its goals.
- Chief Operating Officer (COO): The COO oversees the day-to-day operations of the company, including production, supply chain management, and logistics. Their primary focus is on efficiency and operational excellence.
- Chief Financial Officer (CFO): The CFO manages the company’s financial activities, including financial planning, budgeting, and reporting. They ensure the financial health and stability of the organization.
- Head of Sales and Marketing: This individual is responsible for driving sales growth and building the brand. They oversee marketing campaigns, sales strategies, and customer relationship management.
- Head of Production: This role is crucial for managing the manufacturing processes, ensuring product quality, and optimizing production efficiency. They oversee the production teams and ensure that products meet the required standards.
Location and Operations in Kalkaska
Northland Foods’ strategic choice of Kalkaska, Michigan, as a key operational hub underscores the importance of its location and the advantages it provides. This decision reflects a commitment to efficiency, accessibility, and the effective management of the supply chain. The Kalkaska facility serves as a central point for processing and distribution, playing a crucial role in the company’s overall success.
Significance of Kalkaska, Michigan, to Northland Foods’ Operations
Kalkaska’s significance to Northland Foods stems from several key logistical advantages. Its location within Michigan provides access to a robust transportation network and a favorable business environment. These factors contribute significantly to the company’s operational efficiency and its ability to serve its customers effectively.
Kalkaska Facility Size and Layout
The Kalkaska facility is a substantial operation, designed to accommodate significant production capacity and ensure streamlined processes. The layout is carefully planned to maximize efficiency and minimize operational costs.
Production Process at the Kalkaska Plant
The production process at the Kalkaska plant is a well-defined and organized system, designed to convert raw materials into high-quality finished goods. This process is characterized by several key stages, each contributing to the overall efficiency and effectiveness of the operation.
- Raw Material Receiving and Storage: Raw materials are received, inspected for quality, and stored in climate-controlled environments to maintain freshness and integrity. The receiving process includes rigorous checks to ensure compliance with quality standards.
- Preparation and Processing: Raw materials undergo preparation processes such as cleaning, sorting, and cutting. This is followed by various processing steps, which may include cooking, blending, or forming, depending on the specific product. This stage often involves specialized equipment and automated systems to ensure consistency and efficiency.
- Packaging: Processed products are then packaged into various forms, such as containers, pouches, or boxes. Packaging is designed to protect the product, maintain freshness, and provide necessary information to consumers. The packaging process often involves automated filling and sealing equipment.
- Quality Control and Inspection: Throughout the production process, rigorous quality control checks are performed at various stages. This includes testing raw materials, monitoring processing parameters, and inspecting finished products for quality, safety, and compliance with regulations. These checks help ensure that only high-quality products reach consumers.
- Labeling and Coding: Packaged products are labeled with relevant information, including product names, ingredients, nutritional information, and expiration dates. Products also receive batch codes for traceability purposes.
- Storage and Distribution: Finished goods are stored in temperature-controlled warehouses, ready for distribution. The distribution network ensures products are delivered to customers efficiently and on time. This stage involves careful inventory management and logistics planning.
Products and Services
Northland Foods is committed to providing a diverse range of high-quality food products and services to meet the evolving needs of its customers. This commitment extends from sourcing the finest ingredients to offering flexible packaging solutions and private-label opportunities. Their product portfolio is carefully curated to cater to various segments within the food industry, including retail, food service, and industrial applications.
Finish your research with information from proctor silex food chopper.
Product Lines
Northland Foods offers a comprehensive selection of products, categorized into distinct lines to streamline customer selection and cater to specific market needs. These product lines are designed to provide a variety of options, ensuring that customers can find the right products to meet their requirements.* Frozen Fruits: This line includes a variety of individually quick-frozen (IQF) fruits, such as blueberries, cherries, strawberries, and raspberries.
These fruits are ideal for smoothies, baked goods, and other culinary applications.
Frozen Vegetables
A wide assortment of frozen vegetables, including corn, peas, green beans, and mixed vegetable blends. These products are convenient and offer extended shelf life.
Frozen Potato Products
This category encompasses a range of potato-based items, such as french fries, tater tots, and potato wedges. They are a popular choice for food service and retail customers.
Frozen Specialty Items
This product line includes items like frozen soups, sauces, and prepared meals, offering convenience and versatility for various culinary applications.
Dried Fruits
Offers a selection of dried fruits, providing customers with a shelf-stable alternative to fresh produce.
Packaging Options Comparison: Frozen Blueberries
Northland Foods provides flexible packaging options to accommodate the diverse needs of its customers. The following table illustrates the different packaging choices available for frozen blueberries, a popular product within their frozen fruit line. The table compares and contrasts various aspects of each packaging type.
Packaging Type | Size Options | Primary Use Cases | Key Features |
---|---|---|---|
Retail Bags | 10 oz, 1 lb, 2 lb | Retail consumers, small businesses | Convenient, resealable options available, attractive packaging for shelf appeal. |
Bulk Bags | 5 lb, 10 lb, 30 lb | Food service, industrial applications | Economical, designed for high-volume usage, durable for storage and transportation. |
Pails/Tubs | 5 lb, 10 lb | Food service, ingredient supply | Sturdy, easy to stack, suitable for portioning and dispensing. |
Custom Packaging | Varies based on client needs | Private label, specific customer requirements | Flexible, branding opportunities, tailored to specific product and market demands. |
Custom and Private-Label Services
Northland Foods understands the importance of providing customized solutions to its clients. They offer comprehensive private-label services, allowing businesses to market products under their own brand names.* Private Labeling: Northland Foods provides private-label services for a wide range of products. Clients can choose from existing product lines or collaborate on developing new products. This service encompasses packaging design, product formulation, and quality control, providing a comprehensive solution for businesses seeking to expand their product offerings.
Custom Formulations
Beyond private labeling, Northland Foods offers custom formulation services. This enables clients to develop unique products tailored to specific market demands or customer preferences. The company’s team of experts works closely with clients throughout the formulation process, from concept development to production.
Packaging Customization
Northland Foods offers flexibility in packaging options. Clients can choose from a variety of packaging materials, sizes, and designs to align with their branding and marketing objectives. This customization extends to incorporating specific labeling requirements and regulatory compliance standards.
Market Presence and Distribution
Northland Foods’ success is significantly shaped by its strategic market presence and robust distribution network. Understanding the geographic reach of its products, the channels through which they are sold, and the competitive landscape is crucial for evaluating its overall performance and future growth potential.
Geographic Distribution
Northland Foods’ products are distributed across a diverse geographic range, both domestically and internationally. This wide reach allows the company to tap into various consumer markets and mitigate risks associated with regional economic fluctuations.
- Domestic Market: Within the United States, Northland Foods has a strong presence, particularly in the Midwest region, reflecting its Kalkaska, Michigan, location. Distribution extends across various states, targeting both urban and rural areas. The company leverages regional distribution networks to ensure efficient product delivery and cater to local consumer preferences.
- International Market: Northland Foods also exports its products to several international markets. The specific countries served may vary based on market demand, trade agreements, and logistical considerations. The company often focuses on markets with established demand for its product categories and favorable trade environments. Export activities may involve adapting product formulations, packaging, and labeling to meet international regulations and consumer expectations.
Sales and Distribution Channels
Northland Foods utilizes a multi-channel sales and distribution strategy to maximize market penetration and reach a broad customer base. These channels include both traditional and modern approaches, each catering to different segments of the market.
- Retail Channels: A significant portion of Northland Foods’ products is sold through retail channels. This includes partnerships with supermarkets, grocery stores, and specialty food retailers. The company works closely with retailers to ensure product availability, optimal shelf placement, and effective promotional activities. Retail partnerships provide direct access to consumers and facilitate brand recognition.
- Wholesale Channels: Northland Foods also supplies its products to wholesale distributors who, in turn, supply them to smaller retailers, restaurants, and foodservice providers. This channel allows the company to reach a wider network of customers, particularly those operating outside of major metropolitan areas. Wholesale distribution is often characterized by bulk orders and competitive pricing.
- Online Channels: In response to the growing importance of e-commerce, Northland Foods likely has a presence on online platforms. This could involve selling directly through its own website or partnering with online retailers like Amazon or other specialized e-commerce sites. Online channels provide a convenient way for consumers to purchase products and expand the company’s geographic reach.
Major Competitors and Product Offerings
The food industry is highly competitive, with numerous companies offering similar products. Northland Foods faces competition from both large multinational corporations and smaller regional players. Understanding the competitive landscape is essential for developing effective marketing and product development strategies.
Identifying the exact competitors and comparing product offerings requires more specific data on Northland Foods’ product lines. However, we can make some general observations.
- Large Multinational Corporations: These companies often have significant resources, established brands, and extensive distribution networks. Their product offerings may be similar to Northland Foods, but they could have broader product portfolios and greater economies of scale. For example, if Northland Foods specializes in a specific type of frozen food, its competitors may include major frozen food manufacturers. These competitors often have established brand recognition and wider market penetration.
- Regional Competitors: These companies may focus on specific geographic areas or product niches. They might offer similar products to Northland Foods, but they could differentiate themselves through local sourcing, unique flavors, or specialized distribution channels. Regional competitors can be more agile and responsive to local consumer preferences.
Product offerings are often compared based on several factors, including:
- Product Quality: Quality is often measured by ingredients, manufacturing processes, and taste. Northland Foods likely emphasizes high-quality ingredients and production standards to differentiate its products.
- Pricing: Price competitiveness is essential, with companies balancing production costs, distribution expenses, and profit margins.
- Product Variety: A diverse product line caters to different consumer needs and preferences.
- Marketing and Branding: Effective branding and marketing strategies are crucial for creating brand awareness and loyalty.
- Distribution and Availability: The ability to make products readily available to consumers through various channels is critical.
For example, if Northland Foods’ primary product is a premium frozen fruit blend, a major competitor might be a large frozen food company offering a similar product at a slightly lower price point, but Northland Foods might differentiate itself through its use of locally sourced, organic ingredients. This highlights the importance of a clear value proposition.
Sustainability and Community Involvement
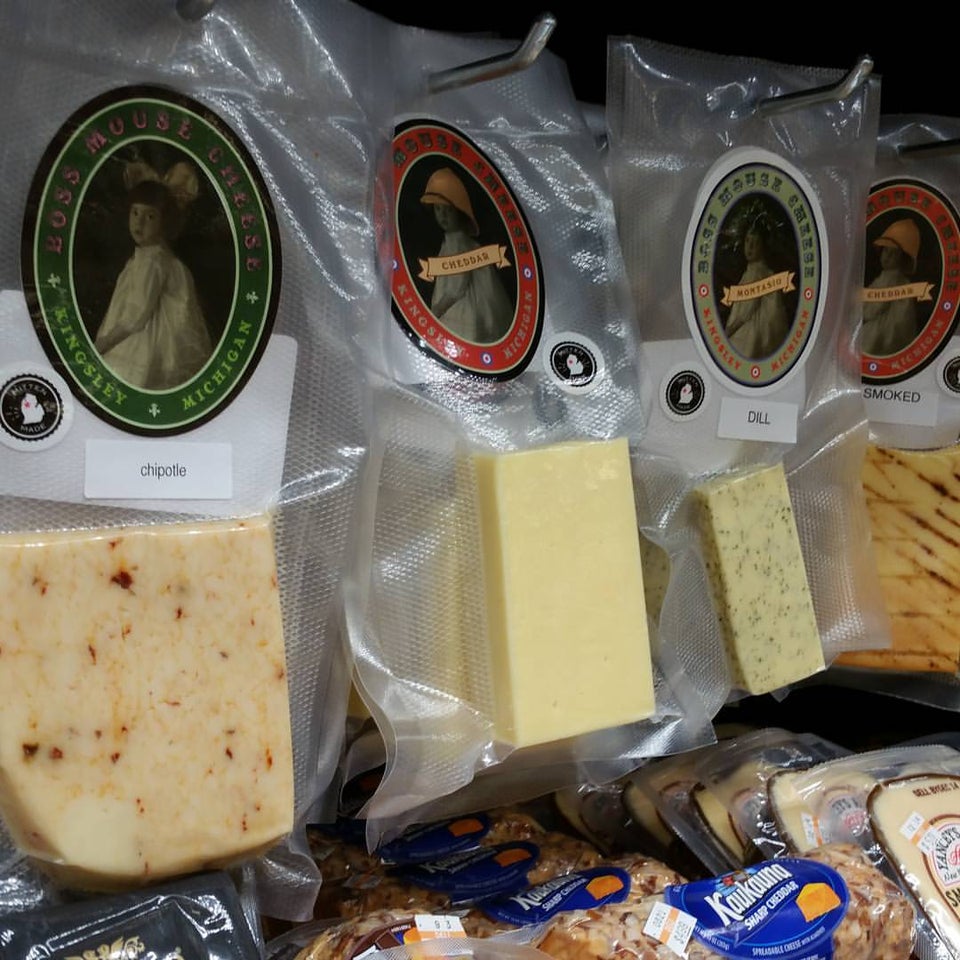
Northland Foods recognizes the importance of operating responsibly, both for the environment and the community it serves. The company is committed to minimizing its environmental footprint and contributing to the well-being of Kalkaska and the surrounding areas. This commitment is reflected in various sustainability initiatives and community engagement programs.
Environmental Practices and Waste Reduction Efforts, Northland foods kalkaska michigan
Northland Foods implements several practices to minimize its impact on the environment and reduce waste. These efforts are integral to their operational philosophy.Northland Foods’ environmental practices include:
- Waste Reduction Programs: Northland Foods actively works to reduce waste generation throughout its operations. This includes implementing strategies for source reduction, reuse, and recycling of materials. They focus on minimizing packaging waste and exploring opportunities to utilize by-products.
- Energy Efficiency: The company invests in energy-efficient equipment and practices to reduce energy consumption. This may involve upgrading lighting systems, optimizing HVAC systems, and implementing energy management systems.
- Water Conservation: Northland Foods aims to conserve water through efficient water usage practices in its processing and sanitation processes. This might include using water-saving equipment and implementing water recycling systems where feasible.
- Sustainable Sourcing: Northland Foods considers the environmental impact of its supply chain by seeking sustainable sourcing options for raw materials. This may involve working with suppliers who adhere to environmentally responsible practices.
Community Involvement
Northland Foods actively engages with the local community through various charitable contributions and partnerships. Their involvement goes beyond simply providing products and services.Northland Foods’ community involvement includes:
- Charitable Contributions: Northland Foods supports local charities and non-profit organizations through financial donations, product donations, and volunteer efforts. These contributions often focus on addressing local needs, such as food security, education, and community development.
- Local Partnerships: The company collaborates with local organizations and businesses to support community initiatives. This can involve partnerships with schools, community centers, and other groups to promote economic development and improve the quality of life in Kalkaska.
- Support for Local Events: Northland Foods participates in and sponsors local events, such as festivals, fairs, and community celebrations. This involvement helps to promote the company’s brand and foster a sense of community.
Certifications and Awards
Northland Foods’ dedication to quality, sustainability, and industry standards is often recognized through certifications and awards. These accolades demonstrate the company’s commitment to excellence.While specific certifications and awards may vary over time, some potential examples include:
- Food Safety Certifications: Certifications such as the Global Food Safety Initiative (GFSI) standards (e.g., BRC, SQF) would highlight the company’s commitment to food safety and quality control throughout its operations. These certifications ensure that the company meets stringent standards for food safety management systems.
- Sustainability Awards: Awards recognizing environmental stewardship or sustainable business practices could be presented to Northland Foods. These awards would acknowledge their efforts to reduce their environmental impact and promote sustainable operations.
- Industry Recognition: Industry-specific awards could be granted to Northland Foods for its products, services, or overall performance. These awards would serve as validation of the company’s quality and dedication to customer satisfaction.
Quality Control and Food Safety
Northland Foods prioritizes the safety and consistency of its products, implementing rigorous quality control measures throughout its operations. These procedures are essential to ensure that all products meet the highest standards, from the selection of raw materials to the final packaging and distribution. This commitment not only protects consumers but also upholds the company’s reputation and complies with stringent industry regulations.
Quality Control Procedures
Northland Foods employs a multi-faceted approach to quality control, encompassing various stages of production. This includes comprehensive testing, meticulous monitoring, and adherence to strict protocols. The goal is to minimize risks and ensure that every product meets or exceeds established quality benchmarks.
- Supplier Approval and Raw Material Inspection: Before any raw materials are used, Northland Foods conducts thorough audits of its suppliers. This includes verifying their adherence to food safety standards and inspecting incoming materials for quality, freshness, and potential contaminants.
- In-Process Monitoring: During the manufacturing process, regular checks are performed at various stages. This involves monitoring critical control points (CCPs) to ensure that parameters like temperature, time, and pressure are within acceptable limits.
- Finished Product Testing: Once production is complete, finished products undergo rigorous testing. This includes sensory evaluations, microbiological analyses, and physical and chemical tests to confirm product safety, nutritional content, and shelf life.
- Traceability Systems: Northland Foods utilizes comprehensive traceability systems. This enables the company to track products from origin to consumer, allowing for rapid identification and recall of any product that may pose a risk.
- Employee Training and Hygiene: All employees receive comprehensive training on food safety practices and hygiene protocols. Regular audits and assessments are conducted to ensure compliance.
Food Safety Certifications and Standards
Northland Foods adheres to a variety of food safety certifications and standards, demonstrating its commitment to producing safe and high-quality products. These certifications are often audited by third-party organizations, providing an independent verification of the company’s food safety practices.
- Good Manufacturing Practices (GMP): Northland Foods adheres to GMP guidelines, which Artikel the minimum sanitary and processing requirements for food production.
- Hazard Analysis and Critical Control Points (HACCP): A HACCP system is implemented to identify and control potential hazards throughout the food production process. This proactive approach helps prevent foodborne illnesses.
- Third-Party Audits: Northland Foods regularly undergoes audits by recognized food safety certification bodies, such as the British Retail Consortium (BRC) or Safe Quality Food (SQF). These audits assess the company’s adherence to food safety standards and best practices.
- Compliance with Regulatory Requirements: Northland Foods complies with all relevant federal, state, and local regulations related to food safety and labeling, including those enforced by the Food and Drug Administration (FDA).
Example Quality Control Procedure: Pasteurization of Milk
- Incoming Milk Inspection: Raw milk is received and tested for temperature, acidity, and the presence of antibiotics.
- Preheating: The milk is preheated to a specific temperature to prepare it for pasteurization.
- Pasteurization: The milk is heated to a specific temperature (e.g., 161°F or 72°C) for a specified time (e.g., 15 seconds). This process eliminates harmful bacteria while preserving the milk’s nutritional value.
- Cooling: The pasteurized milk is rapidly cooled to a temperature below 40°F (4.4°C) to prevent bacterial growth.
- Testing: Samples of the pasteurized milk are tested for bacterial counts and other quality parameters.
- Packaging: The pasteurized milk is packaged in sanitized containers.
- Storage and Distribution: The packaged milk is stored at refrigerated temperatures and distributed to ensure product safety and quality.
Customer Relations and Feedback: Northland Foods Kalkaska Michigan
Northland Foods places a high value on its relationships with customers and actively seeks feedback to improve its products and services. Understanding customer needs and addressing concerns promptly are integral to maintaining customer loyalty and ensuring long-term success. This section Artikels the methods Northland Foods employs to interact with its customers and manage their feedback.
Methods for Customer Interaction and Feedback Collection
Northland Foods utilizes several channels to interact with customers and gather valuable feedback. These methods are designed to be accessible and cater to different customer preferences, ensuring a broad range of perspectives is considered.
- Direct Communication Channels: Northland Foods maintains direct lines of communication, including phone lines and email addresses, specifically dedicated to customer inquiries and feedback. This allows for immediate responses and personalized interactions.
- Website Feedback Forms: A dedicated feedback form is available on the company website. Customers can use this form to submit comments, suggestions, and complaints conveniently. This provides a structured way for customers to share their experiences.
- Social Media Monitoring: Northland Foods actively monitors its presence on social media platforms. This involves tracking mentions, comments, and reviews related to the company and its products. This approach allows for identifying trends and addressing issues in real-time.
- Surveys and Questionnaires: Periodic customer surveys and questionnaires are conducted to gather more in-depth feedback on specific products or aspects of service. These surveys are often distributed via email or included with product shipments. The data gathered helps in making informed decisions about product development and service improvements.
- Retailer Partnerships: Northland Foods collaborates with its retail partners to collect feedback from customers who purchase its products in stores. This includes gathering information from store staff and analyzing customer comments collected by the retailers. This offers an additional perspective on customer experience.
Response to Customer Inquiries and Complaints: Examples
Northland Foods is committed to responding to customer inquiries and complaints promptly and effectively. The company’s customer service team is trained to handle various types of interactions with professionalism and empathy. The following are examples of how Northland Foods addresses customer concerns.
- Product Quality Issues: If a customer reports a quality issue with a product, such as a packaging defect or spoilage, the customer service team will typically request photos or other supporting documentation. The team then investigates the issue, potentially involving the quality control department. Depending on the situation, the customer may receive a replacement product, a refund, or a coupon for a future purchase.
For example, if a customer contacts Northland Foods with concerns about a frozen product arriving thawed, the customer service team would first apologize for the inconvenience, request photographic evidence, and then arrange for a replacement shipment.
- Order Errors: In cases of order errors, such as incorrect items shipped or missing items, the customer service team will verify the order details and take immediate steps to rectify the mistake. This may involve shipping the correct items or issuing a refund for the missing items. For example, if a customer receives the wrong product in their order, Northland Foods will ship the correct product to the customer free of charge and may also include a small complimentary item as a gesture of goodwill.
- Feedback and Suggestions: Customer feedback and suggestions are carefully reviewed by the relevant departments, such as product development or marketing. If a customer suggests a new product flavor or packaging improvement, the feedback is considered in the company’s decision-making process. Northland Foods often acknowledges receipt of feedback and provides updates on how the feedback is being used. For example, a customer suggests a new flavor for a snack product.
The customer service team forwards this feedback to the product development team for consideration, and the customer is informed that their suggestion has been received and will be reviewed.
- General Inquiries: Customer service representatives are available to answer general inquiries about products, ingredients, sourcing, and company policies. These inquiries are handled with accuracy and courtesy.
Customer Service Process Flow Diagram
The customer service process at Northland Foods is designed to be efficient and customer-focused. The following diagram illustrates the steps involved in handling customer inquiries and complaints.
Step 1: Customer Contact
-The customer initiates contact through one of the established channels: phone, email, website form, or social media. The contact includes the nature of the inquiry or complaint.
Step 2: Initial Assessment
-A customer service representative receives the contact and assesses the nature of the issue. This involves gathering relevant information from the customer and reviewing the order details or product information.
Step 3: Information Gathering
-The customer service representative gathers additional information, if needed. This may involve requesting supporting documentation, such as photos or order confirmations. The representative clarifies any unclear details.
Step 4: Issue Resolution
-The customer service representative takes action to resolve the issue. This may involve offering a refund, sending a replacement product, providing information, or forwarding the feedback to the relevant department. The action taken depends on the nature of the issue and company policy.
Step 5: Communication and Follow-Up
-The customer service representative communicates the resolution to the customer, confirming the actions taken and providing any necessary details. Follow-up may be conducted to ensure customer satisfaction and to address any remaining concerns. For example, after sending a replacement product, the customer service team might send a follow-up email to ensure the customer is satisfied.
Step 6: Documentation and Analysis
-All customer interactions are documented in the customer service system. The data collected is then analyzed to identify trends, recurring issues, and areas for improvement. This analysis informs the continuous improvement of customer service processes.
Step 7: Feedback Incorporation
-Customer feedback and complaint data are incorporated into product development, service improvements, and employee training programs. This ensures that customer needs and preferences are considered in all aspects of the business.
Future Plans and Developments
Northland Foods is committed to sustained growth and innovation, constantly seeking opportunities to expand its operations, enhance its product offerings, and adapt to evolving market dynamics. This forward-thinking approach is crucial for maintaining its competitive edge and ensuring long-term success. The company is actively investing in several key areas to secure its future position in the food industry.
Planned Expansions and New Product Developments
Northland Foods is exploring strategic expansions and new product development initiatives to cater to emerging consumer preferences and market demands. These initiatives aim to diversify the product portfolio and increase market share.The company is considering expanding its production capacity through the construction of a new processing facility. This expansion would allow for increased production volume and the introduction of new product lines.
- New Product Lines: Northland Foods plans to introduce several new product lines, including:
- Plant-Based Alternatives: Responding to the growing demand for plant-based protein options, Northland Foods is developing a range of meat-alternative products using ingredients like soy, pea protein, and mushrooms. This includes burgers, sausages, and ground meat substitutes.
- Organic and Locally Sourced Products: Expanding its organic offerings, Northland Foods is partnering with local farmers to source ingredients for a new line of organic products. This will include organic vegetables, fruits, and grains, emphasizing freshness and supporting local agriculture.
- Ready-to-Eat Meals: Northland Foods is developing a line of convenient, ready-to-eat meals designed for busy consumers. These meals will feature a variety of cuisines and dietary options, including vegetarian, vegan, and gluten-free choices.
- Geographic Expansion: Northland Foods is evaluating opportunities to expand its distribution network into new geographic markets, both domestically and internationally. This includes establishing partnerships with new distributors and exploring direct-to-consumer sales channels.
Investment in Technology and Innovation
Northland Foods recognizes the critical role of technology and innovation in driving efficiency, improving product quality, and enhancing customer satisfaction. The company is making significant investments in various technological advancements.
- Automated Processing Systems: Implementing advanced automation in its processing facilities to improve efficiency, reduce labor costs, and enhance food safety. This includes robotic systems for packaging, labeling, and palletizing.
- Data Analytics and Predictive Modeling: Utilizing data analytics to optimize supply chain management, forecast demand, and personalize product offerings. This involves analyzing sales data, consumer preferences, and market trends to make informed decisions.
For example, predictive modeling can help Northland Foods anticipate seasonal fluctuations in demand for specific products, allowing for efficient inventory management and reduced waste.
- Research and Development: Investing in research and development to create innovative food products, improve existing recipes, and explore sustainable packaging solutions. This includes partnering with universities and research institutions to access the latest scientific advancements.
Potential Future Market Trends Impacting Northland Foods
Several emerging market trends have the potential to significantly impact Northland Foods’ future. Understanding and adapting to these trends is crucial for the company’s long-term success.
- Increased Demand for Healthy and Sustainable Food: Consumers are increasingly seeking healthier and more sustainable food options. This trend is driven by growing awareness of the impact of food on health and the environment.
For instance, the popularity of plant-based diets and the demand for sustainably sourced ingredients are expected to continue growing, influencing Northland Foods’ product development and sourcing strategies.
- Growth of E-commerce and Online Food Delivery: The e-commerce and online food delivery market is experiencing rapid growth, presenting both opportunities and challenges for food companies. This trend is driven by consumer convenience and the increasing availability of online food services.
- Northland Foods is actively developing its online presence and exploring partnerships with online food delivery platforms to reach a wider customer base.
- Emphasis on Transparency and Traceability: Consumers are increasingly interested in knowing where their food comes from and how it is produced. This trend is driving demand for greater transparency and traceability in the food supply chain.
- Northland Foods is committed to providing consumers with detailed information about its products, including sourcing information, production processes, and nutritional content.
- Impact of Climate Change and Resource Scarcity: Climate change and resource scarcity are expected to impact the food industry in various ways, including changes in crop yields, increased transportation costs, and the need for sustainable packaging solutions.
- Northland Foods is actively exploring strategies to mitigate the impact of climate change, such as reducing its carbon footprint, conserving water, and sourcing sustainable packaging materials.
Conclusive Thoughts
As our journey nears its end, we find ourselves at a crossroads, contemplating the legacy of northland foods kalkaska michigan. We’ve witnessed the symphony of production, from the dance of ingredients to the final flourish of packaging. The story is one of resilience, of adaptation, and of a deep-seated commitment to the values that have defined the company from its inception.
Northland Foods continues to evolve, poised on the brink of innovation and poised to embrace the future. The echoes of the past resonate with the promise of tomorrow, leaving us with a lasting impression of a company that is more than just a producer of food: it is a cornerstone of community, a purveyor of taste, and a testament to the enduring power of dedication.